
24 minute read
Façades and Fenestration Fire Mitigation Measures
Fire-Safe Aluminium Cladding and Fenestration
The correct fenestration designs can solve a multitude of challenges. As the face of the building design and construction industry is changing rapidly, safety and security measures have become non-negotiable in the building design and construction industry. As a result, there is an increasing need to ensure the various safety measures to make projects viable.
Advertisement
The safety parameters for buildings comprise fire safety measures, structural safety, withstanding harsh weather conditions, safety for accident-prone zones, etc. While many of these measures can be a post-construction add-on, a few should be considered right at the conceptual stage.
Fire safety is one such factor which is segregated into three broad categories that one should look at: • Efficient building design to incorporate passive measures • Provision of systems and equipment for active safety measures • Safe and secure evacuation process for occupants
Using façade and fenestration systems to mitigate fire-related hazards
Fenestration and its Role in Fire Safety Measures Systems such as fire alarms, sprinklers, and fire extinguishers are incorporated
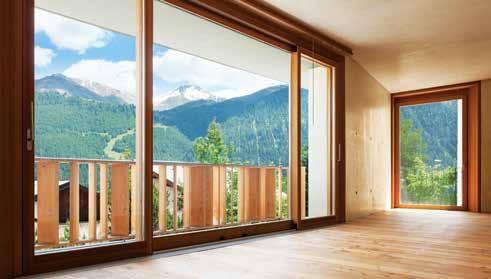
Designing the layout in accordance with fire safety measures
at the construction stage and sometimes after completion. However, architects should integrate specific measures while designing the structure to ensure enough evacuation space for occupants. It also includes making spatial arrangements for housing the fire-fighting systems, strategically using fire-resistant materials, etc. When it comes to fenestration, with technological advancements, it is possible to provide fire-safe solutions that contribute to the safety of the building.
Fenestration, as we know, takes up a significant portion of the building façade. While it dictates the quality of light and ventilation within the building, it can also significantly impact its safety. Besides catering to the appropriateness of material, function, building typology, architectural language and style, providing fire safety is of utmost importance. Fenestration and cladding help with external insulation, which can be a crucial fire deterrent. In order to achieve an efficient building envelope, it is advisable to opt for fire-resistant cladding materials and check them for their safety.
Fire-Safe Aluminium Cladding Options Available Today Aluminium Composite Panel or ACP was previously a popular choice amongst architects and builders because of the numerous advantages aluminium offers. However, the panel has a core of polyethene which is highly combustible in nature, which is a serious disadvantage of ACP. It is a known cause of fire incidents witnessed by the construction industry.
An alternative to ACP is Aluminium Composite Materials or ACM, which are fitted with a non-combustible core sandwiched between two aluminium panels, making the cladding fire safe. As a result, it has a lower environmental impact and is versatile and cost-effective.
FR ACP or Fire Retardant ACP is also a byproduct of the fire safety measures taken for aluminium-based cladding materials.


Using high performance and energy-efficient glass Ensuring evacuation pathways and other safety measures
Similar to ACM, they involve a fireresistant core between two aluminium panels.
Role of Glass and Fenestration in Fire Safety Glass is widely used as an insulating material in fenestrations. Glass technology has undergone tremendous research, resulting in various alternatives for increased fire resistance.
High-performance glass also contributes to a lower heat gain within the building by deflecting a large portion of the solar radiation. It is a viable option for achieving energy efficiency while prioritising a lower environmental impact. Parametric design has enabled the proper selection and arrangement of efficient fenestration systems that can play an integral role in mitigating fire hazards.
How can Fenestration Help in Fire Safety? Apart from the materials used, the functioning of fenestration systems has a huge impact on the fire safety of a building. For example, openable shutters or vents in places where smoke is likely to occur are a much safer choice than fixed casement panels. This ensures that the smoke has a pathway for release and thus isn’t hazardous for the occupants.
Another critical role that fenestration can play is to aid the evacuation of the residents of the building. Fenestration systems should allow for easy access to fire-fighting systems during evacuation and should also prioritise speedy evacuation of the occupants. Systems installed near refuge areas and higher storeys should be carefully designed to meet these needs.
Testing and Certification for Fire Safety: Testing for fire safety ensures that the materials, systems and processes under consideration fulfil the minimum requirements of the applicable building code or local authority.
All buildings in India, for instance, must adhere to the norms of the National Building Code. Apart from generic tests and audits, any other recommended tests should also be carried out to guarantee the safety of occupants. Additionally, one must obtain the necessary certifications to affirm quality control for extraordinary materials or systems that need to be installed for the project.
It is critical to carry out fire safety tests to examine specific hazards or issues concerned with the project. For example, in factories or storage facilities that house flammable materials, there are additional tests and certifications that one must obtain to ensure that the building is firesafe.
Before commencing construction, it is important to check if the selected
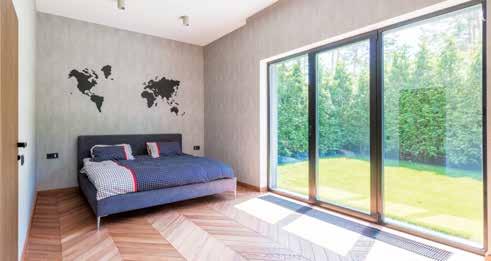
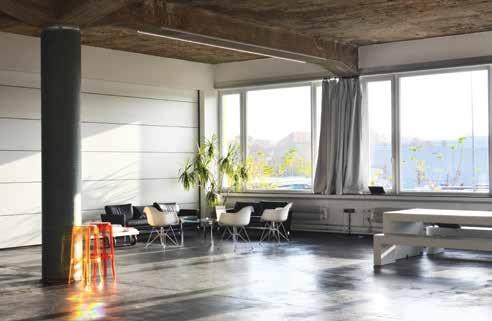
Choosing fire safe exterior cladding and fenestration
materials are approved for fire safety for their purpose. Builders should prioritise the use of prescribed materials that comply with fire safety norms and offer high performance.
A few examples of fire testing for products and systems are: • ASTM E84 Standard Test Method for the surface burning characteristics of building materials, also known as the
Steiner Tunnel Test • DIN 4102 Part 1 fire behaviour of building materials and building components – Part 1: Building materials; concepts, requirements and tests. • Test Houses performing the said tests are Exova Warrington U.K,
PSB Singapore, and Thomas Bell
Wright Associates Dubai, to name a few. can ensure that one can implement fire safety measures properly. Fire safety is an integral consideration right from the conception of the fenestration system design and cladding – rather than an afterthought.
Insulation is an important factor to consider when designing aluminium façades. Whether it’s for composite cladding or fenestration systems, insulation can largely affect the quality of a building. Other than that, one must ensure that the quality standards are met while also considering that an economical approach is ideal in façade design for fire protection. The installation of these systems should not present any fire hazards. These façades should also look at curbing the spread of fire by acting as a barrier.
Façade and fenestration play an important role in the fire safety of a building and significantly contribute to the occupants’ wellbeing. Looking at aluminium-cladding and fenestration systems holistically can enable designers to enhance the safety measures for the project right from the planning stage.
In addition to testing prior to construction, it is also advisable to carry out timely fire safety audits to ensure the workability of the installed systems.
Designing Aluminium Façades that Ensure Fire Safety Working closely with fenestration experts and consultants on projects NITIN MEHTA
Co-Founder and Executive Director,
ALCOI
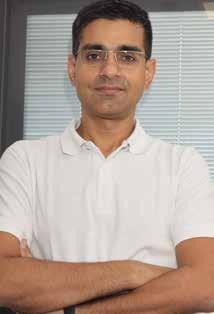
ABOUT THE AUTHOR Nitin Mehta is the Co-Founder and Executive Director of ALCOI, one of India’s leading suppliers of eco-friendly high–performance fenestration solutions. With his futuristic outlook and innovative leadership, Nitin has led the growth of ALCOI into an industry leader in the realm of premium fenestrations. Under his leadership, ALCOI has transformed into a one-stop solutions provider for the design, manufacturing, installation and servicing of precision-engineered fenestration systems in India and abroad.
An engineer by education from Punjab Technical University, Nitin integrates cutting-edge technology with his experience in the metal industry, leading the design and development of high-performance products in-line with market requirements. ALCOI is a leader in the AEC industry, with a unique product portfolio that blends aesthetics with material innovation and sustainability
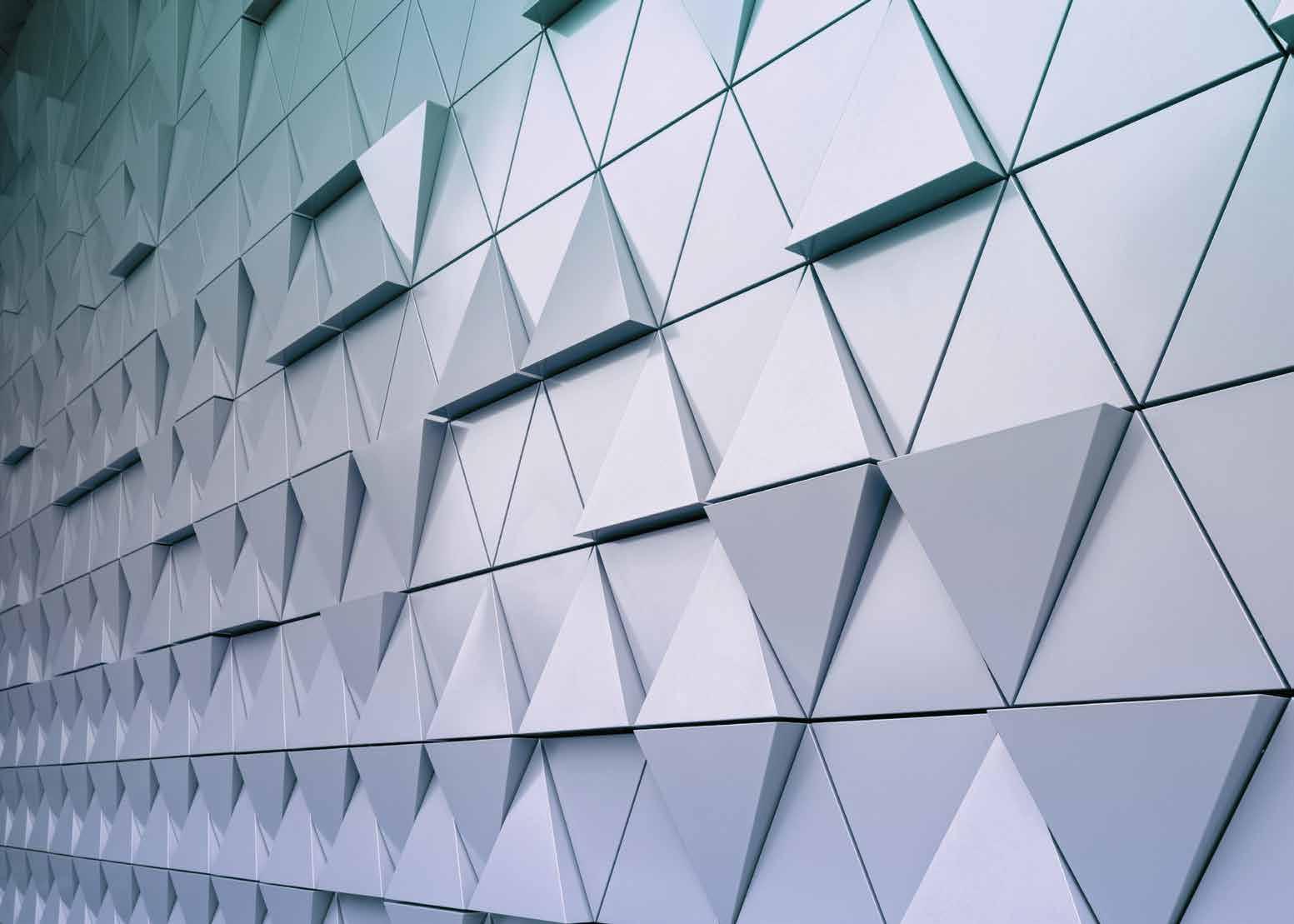
Façades and Fenestration Fire Mitigation Measures
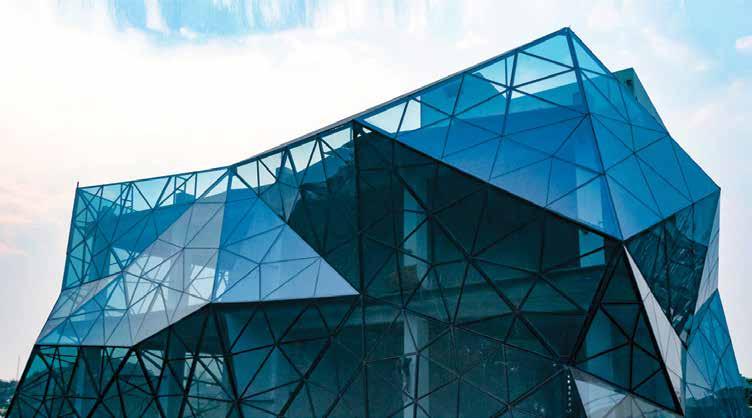
Introduction The concept of façade for buildings was introduced in India in 1990. Before that, high-rise structures were erected in conventional brick and mortar for external wall masonry. Mumbai is the first megacity which was exposed to the highrise culture in the country due to land constraints. Local building bye-laws play an important role in the construction of building in India, however, the majority of these bye-laws have been influenced by the National Building Codes (NBC) which is the backbone of most of the building bye-laws. Before 2106, the NBC was silent about the façade construction beside the fire safety of the façade of buildings.
The use of glass façades in buildings has started gaining momentum due
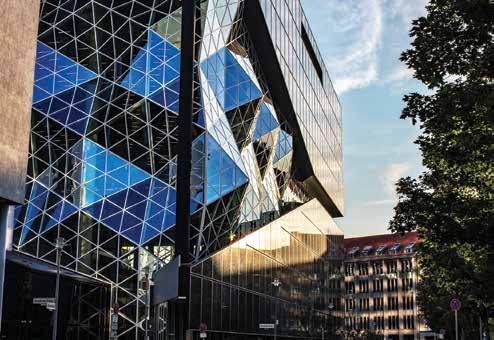
to its transparency and relative ease in installation and maintenance besides the aesthetic value added to the building. The modern construction practices started giving more emphasis on “Green Buildings” and then there was a constant pressure to construct green or sustainable buildings that have benefits environmentally through promoting not only the low-cost of construction but also reducing the recurring expenditure by using the latest techniques of recycling, energyefficiency, and efficient use of resources. A well-designed building should meet all design objectives such as usability, aesthetics, the potential for a redesign for alternative uses, and fire safety. The purpose of writing this article is to discuss the mitigation measures of façade fires.
Fire safety of building design focused on prevention of ignitions, smoke management, detection and warning of occupants, providing for safe egress, control and preventing rapid spread of fire. Therefore, it is essential that the façades of the building should also meet the expectation of a fire-safe building design. It’s very important that the material used for the façade system should comply with the minimum fire resistance requirement for an exterior envelope. Façade design needs to be done in a manner that it doesn’t allow fire and smoke to penetrate from one compartment to another. A façade system should not fail when a fire occurs from its integrity, stability and insulation. Based on the past experience, there has been a substantial improvement in façade design to ensure exceptional structure performance in terms of energy efficacy and requirements on aesthetic appeal. These changes primarily alter the behaviour of modern façades in fire and pose a threat to structure safety and financial loss in the event of a fire.
Structures with non-compliant façades pose a threat to occupant safety and may cause considerable economic loss in the event of a fire. The Grenfell Tower fire being the latest significant incident, which occurred on the 14th of June, 2017 and resulted in at least 80 fatalities, has established how vulnerable existing façades may be to fires and how this vulnerability directly affects the safety of occupants which unfolds into catastrophic events.
1. Study Conducted in India A study was carried out to understand the mechanisms of fire spread in façade systems, external and internal spread of fire and smoke propagation, glass-break and fire stop material behaviour in a real fire scenario, the smoke and obscuration levels, the fire spread behaviour, fire behaviour with ACP/MDF being used with glass, utility of existing smoke alarms, the behaviour of masonry wall, the impact of fire spread on structural components (beams, columns), the performance of locally available fireproofing material (cement boards), and ambient conditions in adjacent compartments during a fire.
The goal of the study was to emphasise the urgent need for developing performance-based codes and to align norms governing fire safety with countryspecific standards.
Experimental investigation of fire behaviour carried out by IIT Gandhinagar and Underwriters Laboratories on glass façade systems reveals that a gap is always provided between the curtain wall and the building to avoid crashing of glass in case of unwanted vibrations arising from passing of heavy vehicles and/or minor earthquakes and also to mitigate effects of thermal expansion. This gap is filled with appropriate fire stop material (e.g., Rockwool). The performance of the façade as well as the fire stop material is crucial for the overall performance of the façade system.

2. Major Façade Fires In all building façade fire cases, it is noticed that the material used in the exterior surface cladding was highly combustive and supported rapid-fire propagation. In a few of the structures where sprinklers were installed, still, external fire spread could not be averted. A few ill-famed façade fire examples are: -
S.NO
1
2
3 DETAILS
Fire at Kalina Building, Santacruz (Mumbai), Diamond Square- April 8th , 2011- A major fire broke out in a six-storey commercial building in the afternoon. The fire was initiated by the left-wing and completely ruined the left façade of the building.
First Information Financial Centre (FIFC) Mumbai, Sep 8th, 2012- A major fire broke out on the 12th floor of the FIFC Building at BKC on Friday. The fire raised for over two hours. The fire travelled from the 12ththe to the 13th floor from the exterior of the buildings.
Lotus Business Park, Mumbai- According to officials, the blaze started on the 21st floor of the building around 11:30 am and soon spread to the 20th floor.
4
Grenfell Tower, 14th of June, 2017- The installation of a new façade system on the Grenfell Tower was completed in 2016. A novel chance exists to learn from the Grenfell Tower fire to avoid similar occurrences around the world.
PICTURES

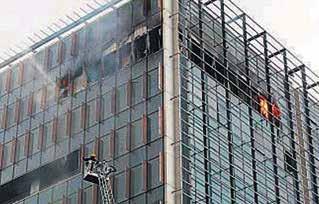
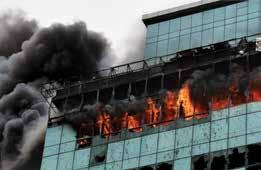
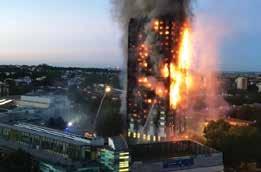
3. Mechanism of Fire Spread in Façade Conduction - Fire can spread via heat transfer of materials, such as metals, which can absorb and transfer heat and are called thermal conductors which are primarily used as a frame in the façade structures.
Convection - Ceilings trap hot air of burning materials and prevent it from moving any higher, which then causes everything to build up heat and can cause a fire to spread. If there is adequate heat, fuel and oxygen accumulation in the area other combustible materials will start igniting and fire away from the original one will start. Once this happens, the fire will quickly engulf a whole room in seconds. This phenomenon is also observed in façade fires.
Radiation - A high-intensity fire will give off more heat. Heat can be transferred through electromagnetic waves just like Sun. There is every possibility for the fire to spread through this mechanism to the building structures nearby.
The Chimney Effect - is where heated surfaces create thermal zones that include upward air movement, which in turn sucks hot gases and flames in its direction. This effect is attributed to the spread of fire upward through shafts, and also the spread of fire upward through available openings between the floor slab edge and therefore in the curtain wall. Subsequently, a need has been felt to fill the penetration through fire stop materials.
Leapfrog effect - This effect is clear in high-rise building fires where flames blaring out through perimeter façades ultimately spread back in through the façade above and still spread vertically to upper floors. Once the heat release rate of the fire is high enough, between 50-100 kW/m2, the window of the room above the room of origin will fall out. Flames eject from a window, breaking the window above causing ignition on the floor above (leap-frogging), secondary interior fires and level to level fire spread. Heat causing degradation/ separation of non-combustible protective skin resulting in flame spread to combustible elements internal to the wall system. Hence, the façade design must prevent the leapfrog effect.
4. Mumbai Fire Brigade Initiatives After a few fire accidents in Mumbai and India, Mumbai Fire Brigade in September 2016 has initiated the proposal to incorporate fire safety provisions for the façade buildings which is accepted and approved by the Municipal Corporation of Greater Mumbai and incorporated into the fire safety measures with the orders that the occupiers/owners of such buildings shall comply all these fire safety requirements within 120 days of the publishing of the appeal and submit compliance. 1. The smoke seal/barriers between the building wall and the façade shall be provided at every floor level in the form of non-combustible material/ vermiculate cement. 2. Glass façade blocking the area of a staircase, lift lobby and corridor shall be kept openable. If the staircase/lift lobby is pressurised the pressurisation system shall be synchronised with the glass façade window opening mechanism.

Leap From Effect
3. Minimum of 2.5% of the floor area of each compartment on each floor shall be kept openable. 4. Refuge area shall be kept open above the height of 1.20 meters from the flooring level. However, if already covered with a glass façade all the glass panels shall be openable (either left or right hinge) both from inside as well as outside.
5. Comparison of Building Code Requirements for Fire Resistive Design of Façades
5.1) Changes in NBC
Based on the fire safety adopted by the Mumbai Fire Brigade and the NBC has adopted the following in 2016:
1. The glazing shall be by Part 6.
Structural Design, Section 8 Glass and Glazing. The entire glazing assembly shall be rated to that type of construction “Fire Resistance
Ratings of Structural and Non-
Structural Elements” of NBC. This shall be applicable along with other provisions of this Part related to respective uses as specified therein. The use of glass shall not be permitted for enclosures of exits and exit passageways. 2. Glass façade shall be in accordance with the following:

ASTM Test Assembly Picture
NOTE: Panelling (lining) shall be permitted in a limited area. It shall not be permitted in a vestibule.
• For fully sprinklered buildings having fire separation of 9 m or more, tempered glass in a non-combustible assembly, with the ability to hold the glass in place, shall be provided. It shall be ensured that sprinklers are located within 600 mm of the glass façade providing full coverage to the glass. • All gaps between floor slabs and façade assembly shall be sealed at all levels by approved fire-resistant sealant material of equal fire rating as that of the floor slab to prevent fire and smoke propagation from one floor to another. • Openable panels shall be provided on each floor and shall be spaced not more than 10 m apart measured along the external wall from centreto-centre of the access openings.
Such openings shall be operable at a height between 1.2 m and 1.5 m from the floor, and shall be in the form of openable panels (fire access panels) of size not less than 1 000 mm × 1 000 mm opening outwards.
The wordings, “FIRE OPENABLE
PANEL, OPEN IN CASE OF FIRE, DO
NOT OBSTRUCT” of at least 25 mm letter height shall be marked on the internal side. Such panels shall be suitably distributed on each floor based on occupant concentration. These shall not be limited to cubicle areas and shall be also located in common areas/corridors to facilitate the access by the building occupants and fire personnel for smoke exhaust in times of distress.
3. Surface Interior Finishes: • The use of combustible surface finishes on walls (including the façade of the building) and ceilings affects the safety of the occupants of a building. Such finishes tend to spread the fire and even though the structural elements may be adequately fire-resistant, danger to life may result. It is, therefore, essential to have adequate precautions to minimise the spread of flame on walls, façades of buildings and ceiling
surfaces. The finishing materials used for various surfaces and decor shall be such that they shall not generate toxic smoke/fumes. • The susceptibility of various types of wall surfaces to fire is determined in terms of the rate of spread of flame.
Based on the rate of spread of flame, surfacing material shall be considered as divided into four classes as follows1. Class 1 Surfaces of very low flame spread. 2. Class 2 Surfaces of low flame spread. 3. Class 3 Surfaces of medium flame spread. 4. Class 4 Surfaces of rapid flame spread. • The uses for which surface materials falling into various classes shall be adopted in building construction are given below:
CLASS 1 CLASS 2 May be used in any situation May be used in any situation, except on walls, façade of the building, staircase and corridors May be used only in living rooms and bedrooms (but not in rooms on the roof) and only as a lining to solid walls and partitions; not on staircases or corridors or façade of the building.
CLASS 3
• Materials of Class 4 which include untreated wood fibreboards may be used with due fire-retardant treatment as ceiling lining, provided the ceiling is at least, 2.4 m from the top surface of the floor below, and the wall surfaces conform to the requirements of class 4 materials shall not be used in kitchens, corridors and staircases. Some materials contain bitumen and, in addition to the risk of spread of fire, emit dense smoke on burning; such materials shall be excluded from use under these conditions and shall also not be used for the construction of ceilings where the plenum is used for return air in air-conditioned buildings.
• When frames, walls, partitions or floors are lined with combustible materials, the surfaces on both sides of the materials shall conform to the appropriate class because there is considerable danger from fire starting and rapidly spreading within the concealed cavity unknown to the occupants whose escape may be hampered thereby. For detailed information on materials and details of construction with their fire-resistance rating, reference may be made to good practice.
4. Part- 6 Section 8.2.1 of NBC i) Performance Criteriaw The performance criteria to be satisfied by the glazing system are structural stability and safety, energy efficiency (performance), visual comfort (light transmittance and reflection), fire protection (ability to resist/ withstand fire), sound insulation, air infiltration (wind pressure, stack pressure, fan pressure), and water penetration (static, dynamic and cyclic pressures).
ii) Movements The glazing system (and its framing elements) shall be able to accommodate the movements caused due to wind loads, seismic loads, live loads, dead load deflection, thermal expansion and contraction of members, slab deflection, etc. iii) Types of Structural Frame Materials For the framed/semi-framed systems, materials such as aluminium, stainless steel, uPVC and timber, which are commonly employed are listed hereunder. • Aluminium Alloy- is commonly used for higher strength. • Stainless Steel- is employed for its mechanical properties as they are highly corrosion resistant for all normal exposures. • uPVC- A relatively flexible material,
PVC which is internally reinforced with steel or aluminium to give it the required strength and stiffness may also be used. • Timber- Timber frames are relatively stiff and are adopted for their inherent thermal insulation property, lightweight and improved sound insulation.
5.2) National Construction Code Australia Standards Australia has developed an additional Australian Standard (AS 51132016 (Standards Australia 2016) on “Fire propagation testing and classification of external walls of buildings”, that offers procedures for the fire propagation testing and classification of external walls of buildings conferring on their tendency to limit the spread of fire via the external wall and between adjacent buildings. This standard has been developed based on international practice and is consistent with the testing criteria prescribed in ISO 13785 (International Organisation for Standardisation 2002) and BS 8414 (British Standard Institute 2015) Parts 1 and 2. National Construction Code (NCC) Australia expects a certain performance requirement from the external cladding of a building (The Australian Building Codes Board 2016). There are two paths to meet the specified performance criteria; deemed-to-satisfy solution and performance solution. Where a deemed-to-satisfy solution is proposed, performance requirements which are categorised in the order from CP1 to CP9 should be satisfied depending on the type of construction. Where a performance solution is proposed, it requires a report from a qualified fire engineer. The report should be based on full-scale façade tests carried out in accordance with BS 8414 (British Standard Institute 2015), ISO 13785 (International Organisation for Standardisation 2002), and NFPA 285 (National fire protection association 2012), or any equivalent international standard. Standards Australia has released AS 5113, a full-scale façade test based on BS 8414 and ISO 13785.
When cladding is part of the external wall, it should be non-combustible for buildings which have more than 3 storeys (The Australian Building Codes Board 2016). The combustibility of the material should be determined by testing in accordance with AS 1530. For laminated products, the test should be carried out with individual layers and a stack of laminates similar to the end-use condition. NCC prescribes the non-combustible requirements for bonded laminated elements as follows (Australian Building Codes Board 2016; The Australian Building Codes Board 2016): • Each laminate is non-combustible in accordance with AS 1530 • Each adhesive layer does not exceed 1 mm in thickness; and • The total thickness of the adhesive layers does not exceed 2 mm; and • The Spread-of-Flame Index and the Smoke-Developed Index of the laminated material as a whole do not exceed 0 and 3 respectively in accordance with AS 1530.
However, if one or more laminates are combustible, it violates noncombustibility requirements and therefore cannot be used as part of a deemed-to-satisfy solution where a noncombustible material is required in façade (Australian Building Codes Board 2016).
In addition to external claddings, other elements such as framing, spandrels,
insulation and internal lining (e.g., plasterboard) are often considered as part of an external wall. The external wall can be load-bearing or non-load bearing. Depending on the load-bearing condition and the distance from the fire source, NCC also specifies fire resistance level (FRL) in minutes for buildings of more than 3 levels for the three main performance criteria; structural adequacy, integrity and insulation (The Australian Building Codes Board 2016) (see Table).
Building element Class of building – FRL: (in minutes) Structural adequacy/Integrity/Insulation
2,3 or 4 parts 5,7a or 9 6 7b or 8
External wall (including any column and other building element incorporated therein) or other external buil ding element, where the distance from any fire-source feature to which it is exposed is—
For load-bearing parts-
Less than 1.5m
1.5m to less than 3m
3m or more
For non-loadbearing parts- Less than 1.5m
1.5m to less than 3m
3m or more 90/ 90/ 90
90/ 60/ 60
90/ 60/ 30 120/120/120
120/120/90
120/60/30 180/180/180
180/180/120
180/120/190
-/ 90/ 90
-/ 60/ 60 -/120/120
-/ 90/ 90
Table- Type A Construction: FRL of building elements -/180/180
-/180/120 180/180/180
180/180/120
180/120/190
-/240/240
-/240/180
When cladding is considered to be an attachment to the external wall, combustible material can be used, given that it satisfies certain conditions of not impairing with the external wall fire resistance. The material should meet the fire hazard properties. The combustible cladding should not be located near or directly above an exit and it should not constitute an undue risk of fire spread via the façade of the building. The attachment should also meet the required FRL for that construction type (refer to Table above).
However, NCC also specifies exceptions for combustible materials or containing combustible components such as fibres. These exclusions can be plasterboard, perforated gypsum lath with a normal paper finish, fibrous-plaster sheet, fibre-reinforced cement sheeting and pre-finished metal sheeting having a combustible surface finish not exceeding 1 mm thickness and where the Spread-ofFlame Index of the product is not greater than 0.
5.3) Approved Document B - UK Approved Document B (ADB) (Department of Communities and Local Government 2010) is used as the guideline under building regulations to determine fire safety. While ADB specifies certain conditions to be satisfied for the cladding to be fire-resistive, it also gives provision to alternate means of compliance by testing according to British Standard 8414 and assessment in accordance with Centre for Window and Cladding Technology BR 135 (2017). Fire-resistance of the wall should be dealt with EN 1364-4 (European Committee for Standardisation 2014). As this article is more focused on the façade fire, the guidelines that apply primarily to façades will be discussed in detail.
If the building contains a floor more than 18m above ground level, the following set of conditions applies for the installation of façades.
• Any insulation product, filler material (not including gaskets, sealants and similar) etc. used in the external wall construction should be of limited combustibility and meet the requirement of Euro class A2 materials; • External surface above 18m should be Class B; • External surface below 18m can be Class C provided distance from boundary exceeds 1m. Combustibility of materials is classified in accordance with EN 13501-1 (European Committee for Standardisation 2009) as A1, A2, B, C, D, E and F with A1 being the highest performance and F being the lowest. Table- Combustibility class of materials used in ADB (Centre for Window and Cladding Technology 2017; Department of Communities and Local Government 2010).