
4 minute read
A sustainable investment for the next half-century
The world’s widest containerboard line, at the Aalen-Neukochen mill in Germany, represents an investment by Papierfabrik Palm that will pay off with sustainable high-quality product for the next 50 years. Report by Marika Mattila and Pauliina Purola.
The PM5 containerboard line at Papierfabrik Palm’s mill at AalenNeukochen in Germany is the largest of its type in the world. Delivered and started up by Valmet in July 2021, it is 10.9 metres wide, runs at up to 2,000 metres per minute and has capacity to yearly produce 750,000 tonnes of very lightweight corrugated case material made from 100 per cent recycled fibres.
Advertisement
The location of the line is significant for Papierfabrik Palm, which operates five paper mills, 29 corrugated board plants and two recycling plants in Europe.
The Aalen-Neukochen mill is where Palm was established in 1872 when Adolf Palm laid the foundation stone for the family business on the Kocher River.
The PM5 production line comprises many novel paper making innovations, including a mill-wide automation system.
It is a true showcase of carbon dioxide-efficient board production. The new production line replaced three old machines at the mill.
Ready for future changes
“There’s a clear trend – even pressure – to be more sustainable in everything we do in the
The Palm mill is located at Aalen-Neukochen, the headquarters of the family-owned company in Germany. Valmet’s scope of delivery for PM5 included a complete containerboard production line from headbox to winder, with a wide scope of automation market. If we didn’t react to these demands, we’d probably quickly go out of business. I strongly believe that PM5 has a sustainable lifetime that is much longer than 50 years,” says Dr Wolfgang Palm, owner and chief executive of Papierfabrik Palm. “Corrugated boxes only have a great future as a packaging material if you can reduce carbon dioxide emissions further in the production process. One way to do this is to reduce the basis weight. We worked closely with Valmet to design a board machine that could produce more lightweight containerboard than any other board machine in the world,” continues Dr Palm.
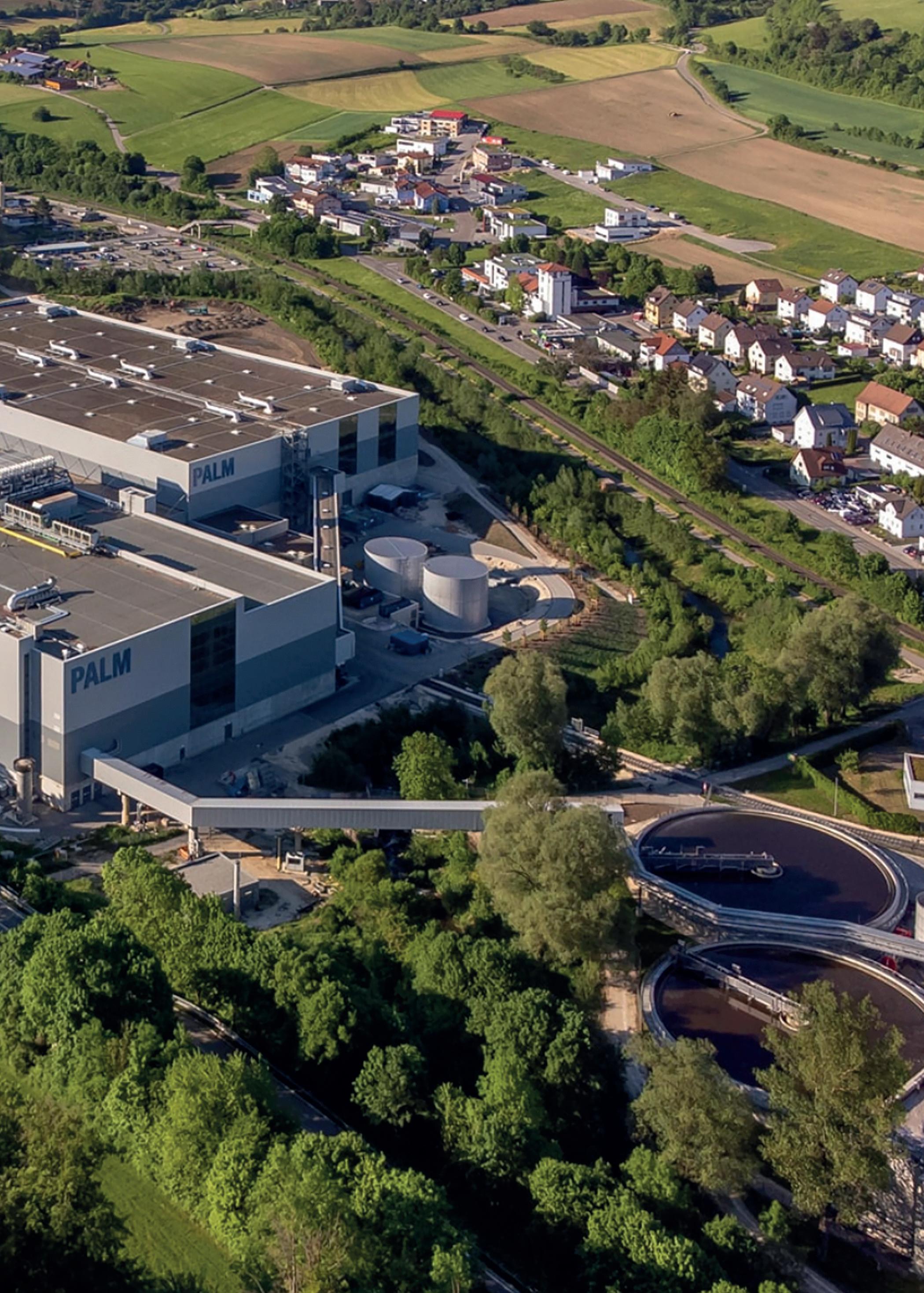
Novel innovations for sustainable board making
“PM5 features many technological innovations, which were tested and proven at Valmet’s pilot plants in Finland,” says
Stephan Gruber, managing director and chief technical officer of Papierfabrik Palm. “An outstanding highlight is Valmet’s Sleeve roll technology in the forming section, which enables high water removal capacity without using any vacuum. We’ve already reached our dryness 4 target, and we would absolutely install this unique technology again.
“We selected a three nip press concept with Transfer beltsystem to remove open draw from the press to the drying section with an excellent dryness level.
This has proved an excellent combination with the OptiDry Twin impingement dryer, which increases dryness and sheet temperature before entering the drying section.
“OptiDry Twin enables a very low deposit level at the beginning of the cylinder drying, and the drying section’s runnability components stay absolutely clean. There are no stickies or dusting at the pre-dryer section. In the drying section, the reliable and compact geometry of the Valmet Hirun Compact runnability system works very well to even further improve both runnability and cleanliness. We believe that selecting these innovations was the right decision.”
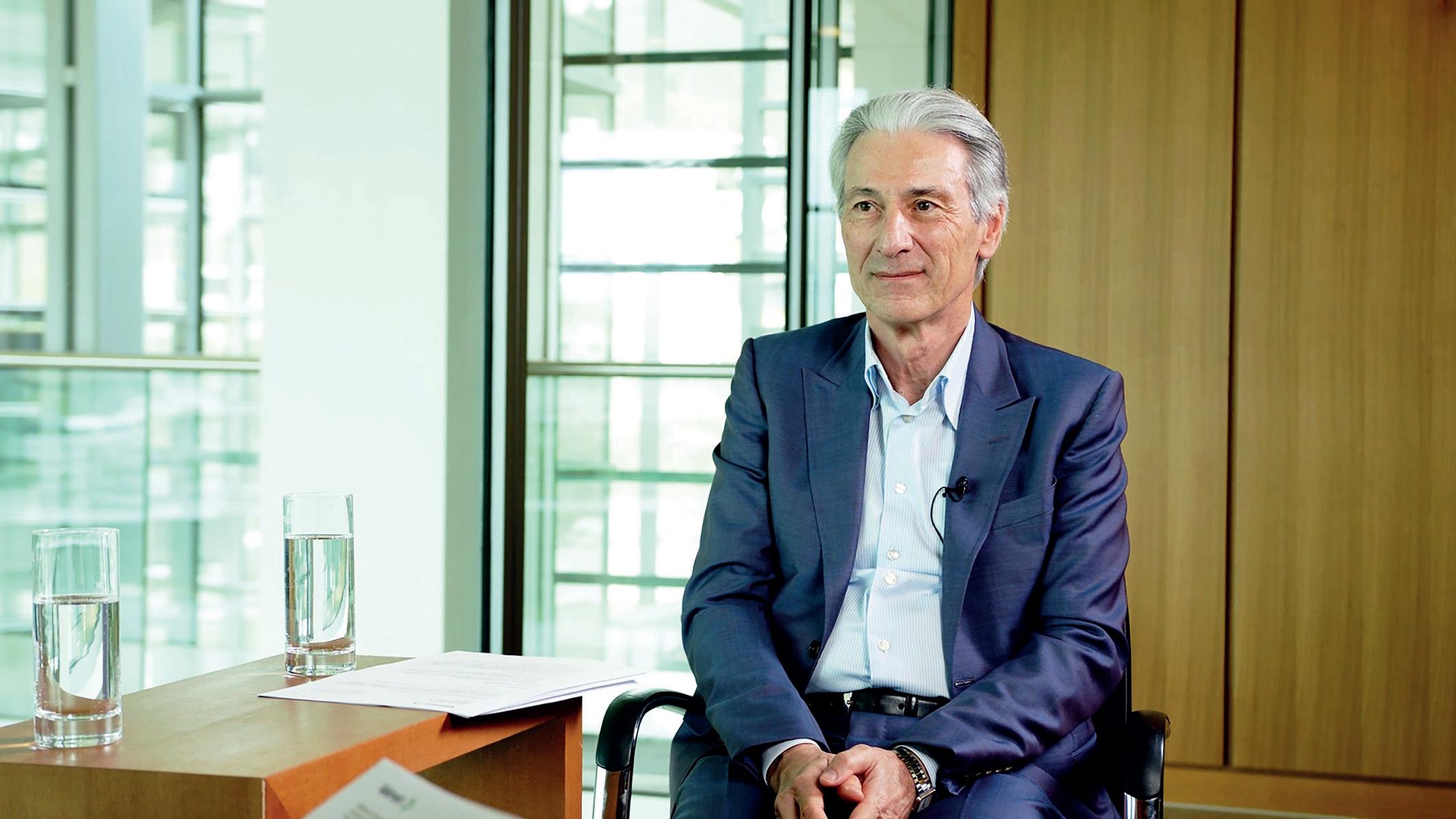
PM5 features novel OptiSizer Hard surface sizing technology for improved runnability, higher strength properties, the cleaning of starch in the recirculation, and lower operating costs than conventional film sizing.
“The hard nip sizing is working really well, with excellent runnability. This is the right solution for low basis weight production with a low draw, high sheet stability and savings in starch consumption. Because the spray size application is contactless, the recirculated starch is never in contact with recycled fibres,” continues Gruber.
“The reel and winder area are streamlined and highly automated, and roll movement is minimised, making it very operator friendly. The winder is like a robot that performs better and better every day. There aren’t any quality issues with the finished rolls.”
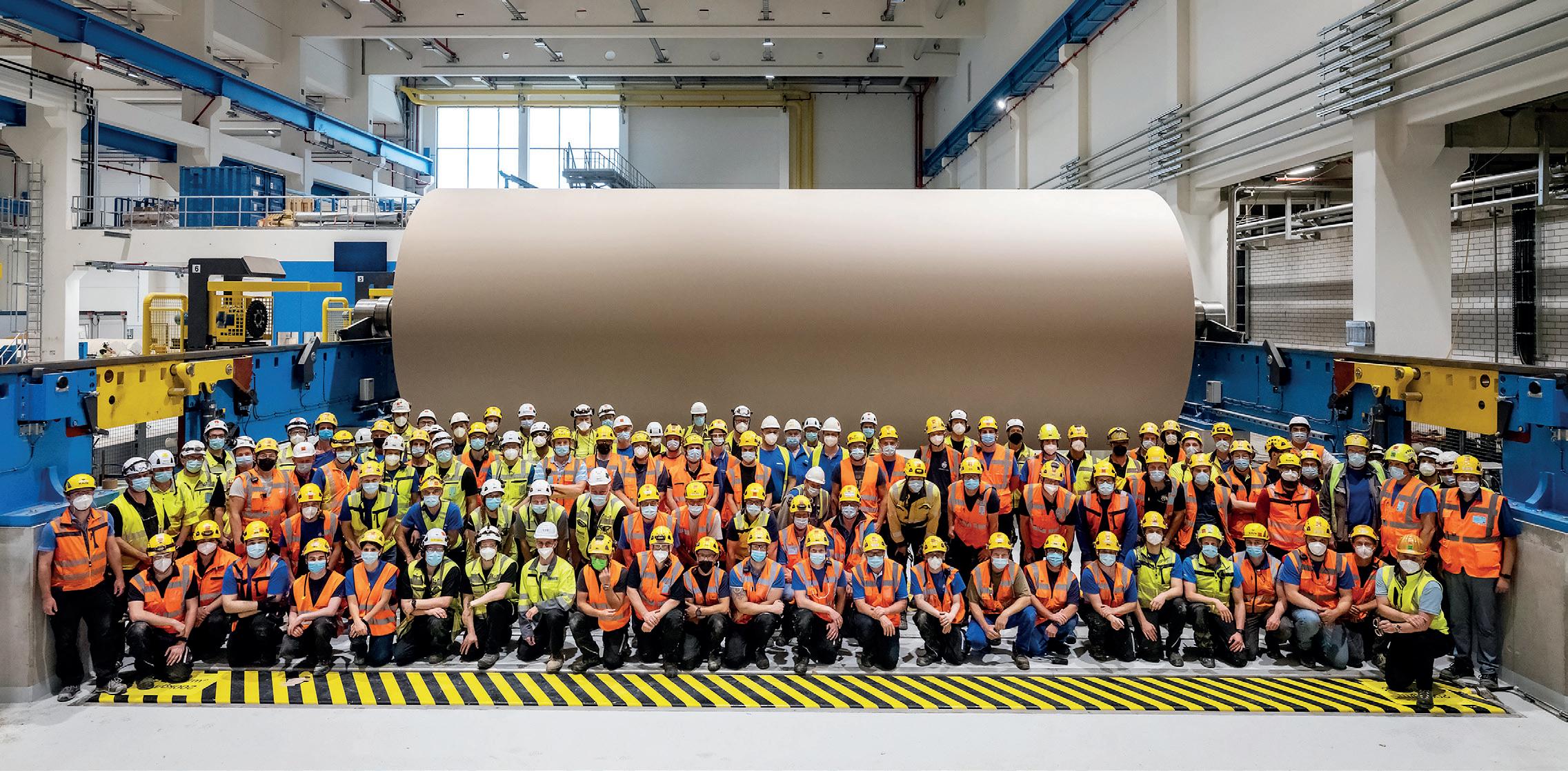
Mill-wide automation as one platform
Industry-leading control systems for distribution (DCS), quality (QCS), machines (MCS), analysers and measurements were selected for PM5 to improve process performance and achieve savings in fibres, chemicals and energy.
Dr Palm explains: “We’ve had very good experiences with the Valmet DNA Automation System, which is utilised mill-wide from the power plant and wastewater treatment system through to the stock preparation and paper machine to the winder.

Gruber adds: “We see clear advantages for both operators and maintenance getting the mill-wide automation system from one supplier. The Valmet platform is very reliable, and there’ve been no issues with the start-up.”
Production line performance reinforced with the latest Industrial Internet solutions
The PM5 line was started up during the Covid-19 restrictions. Valmet’s data-driven Industrial Internet applications with remote connections worked as a valuable support to achieve a world-class start-up.
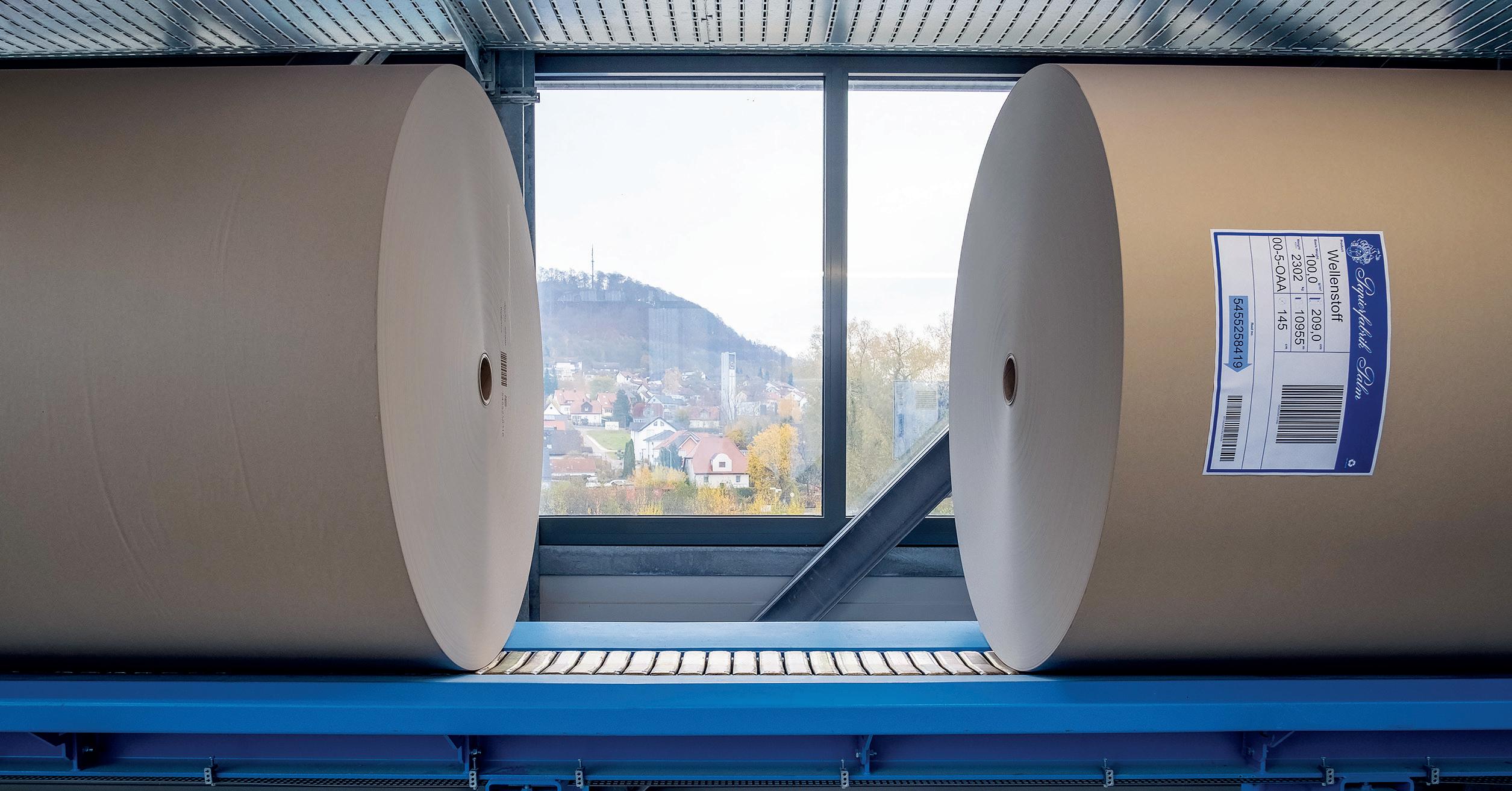
“Industrial Internet applications help us a lot, because Valmet’s specialists can very quickly connect to our process directly from Finland.
Industrial Internet solutions are part of our daily routine – for example, in-strength development with Valmet experts,” says Gruber.
High-quality ultralightweight packaging material with low operating costs
The market for recycled containerboard has good prospects, especially due to its sustainability as a packaging material: it is renewable and recyclable.
Containerboard production needs to deliver high efficiency and advantages in sustainability. Producing packaging grades with a low basis weight while maintaining high strength and excellent printing properties is always a challenge for board makers. Palm overcame this challenge with Valmet’s experts and the right solutions.
“If you produce ultralightweight board, you must achieve two things: you need to produce it efficiently and – even more important – economically. This means you have to increase the board machine’s speed much further. Our target was simply to have the fastest running containerboard machine in the world,” says Dr Palm. “We’ve seen strong demand for ultra-lightweight containerboard, much higher than we anticipated. Our ultralightweight board strategy really is a major success.”
Gruber concludes: “We produce ultra-lightweight high-quality containerboard for strong packaging purposes, which means the same strength properties and more square metres in a roll than in conventional containerboard grades.
“The whole value chain starts from PM5 and ends in households through e-commerce, for example. This means a much more sustainable supply chain.”
More information from: Tomi Tissari, project manager. Tel: 358 4076 5392. Email: tomi. tissari@valmet.com