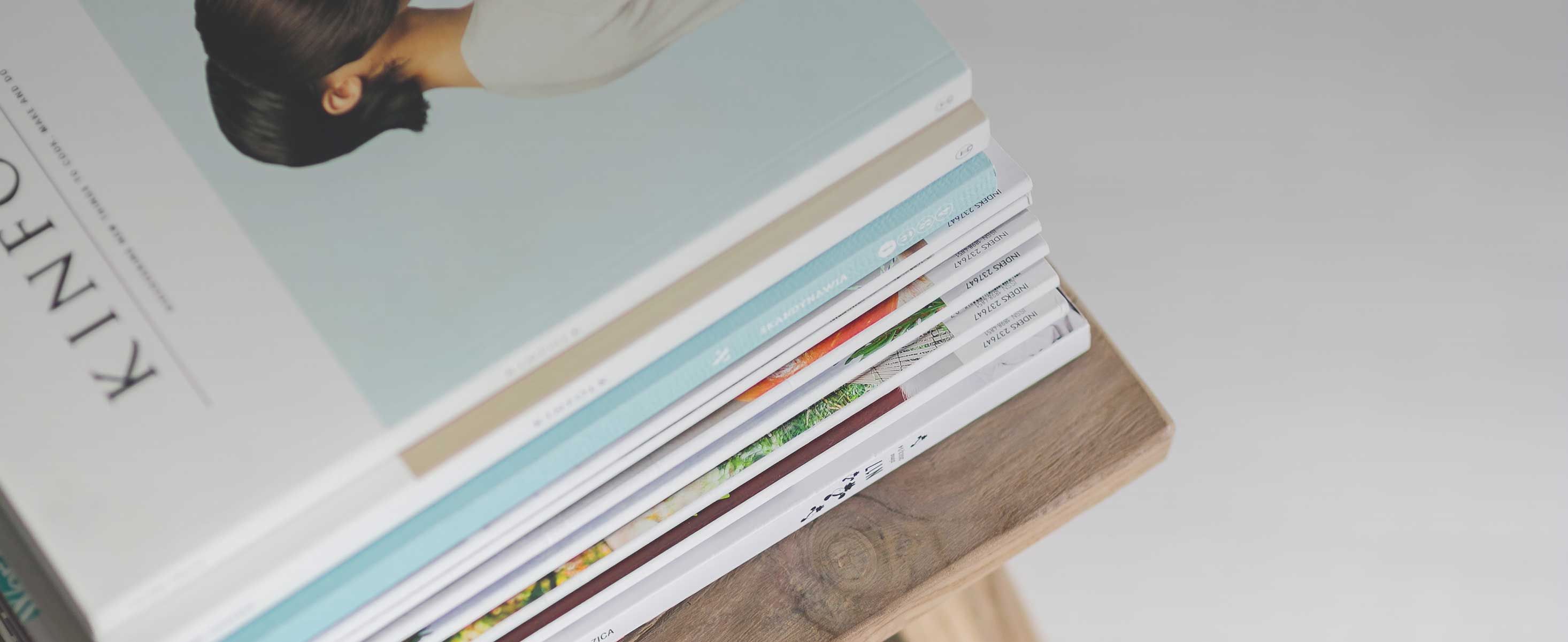
2 minute read
Going strong: More than 1,000 winders and 50 Dual Unwind systems around the world
Winders and their development have a long history at Valmet. The engineering company has already delivered more than 1,000 winders and 50 Dual Unwind systems, but their development is far from complete. The 1,000th winder delivered to Papierfabrik Palm PM5 showcases all the great features it offers.
Palm values its gigantic winder: “It’s not just a winder for us – it’s a robot. Just one winder manages all the paper from PM 5,” says Stephan Gruber, managing director and chief technical officer of Papierfabrik Palm. Having just one winder is a clear benefit for Palm: “It has reduced our investment cost compared to two winders, and it also reduces our personnel costs, because we need only two winder operators,” Gruber continues.
Advertisement
“The two key features of the winder at Aalen are the Valmet Industrial Internet (VII) and the Dual Unwind system to achieve high throughput,” Gruber says. Valmet developed the Dual Unwind system more than 10 years ago with the idea of having two unwinds at the winder. The innovation reduced the parent roll change time from ten to six minutes, improving winder capacity by as much as 50 per cent. More than 50 Valmet customers are already enjoying the benefits of their Dual Unwind systems. The VII provides completely new opportunities to optimise winder production and maintenance. For example, it can give detailed insights into winding performance, with data-driven analytics to avoid unplanned stops and increase end product quality.
Automation has always been an important part of improving winder capacity, usability and roll quality. When combined with a reel and automatic transfer rails, the entire reeling and winding process can be operated with a minimum of personnel safely and effectively, while providing higher production levels. The winder at Aalen is equipped with a Valmet DNA automation system to maximise its high performance.
Although Valmet is proud of its past and the 1,000 delivered winders, this is not the end of the story. Valmet’s two pilot winders are used to continually develop new innovations. And the culture of innovation will drive Valmet to create even better winding solutions in the future.
Valmet offers several technologies that enable the production of lighter board products without compromising on quality or visual properties. This is achieved with light weighting, which allows board and packaging producers to optimise raw material use, board quality and production capacity. The benefits of light weighting expand to each stage of the value chain: Packaging producers need less board for their products; transporting lighter products decreases the environmental impact, less energy is needed at every stage; and less waste is created thanks to recycling.
Palm’s PM5 produces ultra-lightweight board in basis weights down to 60 grams per square metre, which means a raw material reduction of at least 15 per cent, with comparable performance. In addition, old corrugated containers as 100 per cent recycled raw material contributes to the conservation of natural resources.
The PM5 replaces three old production machines, and it is equipped with the latest energy-efficient technological solutions, enabling substantial energy savings.
Further environmental benefits are achieved through mill-wide automation, which improves process performance while enabling savings in fibres, chemicals and energy.