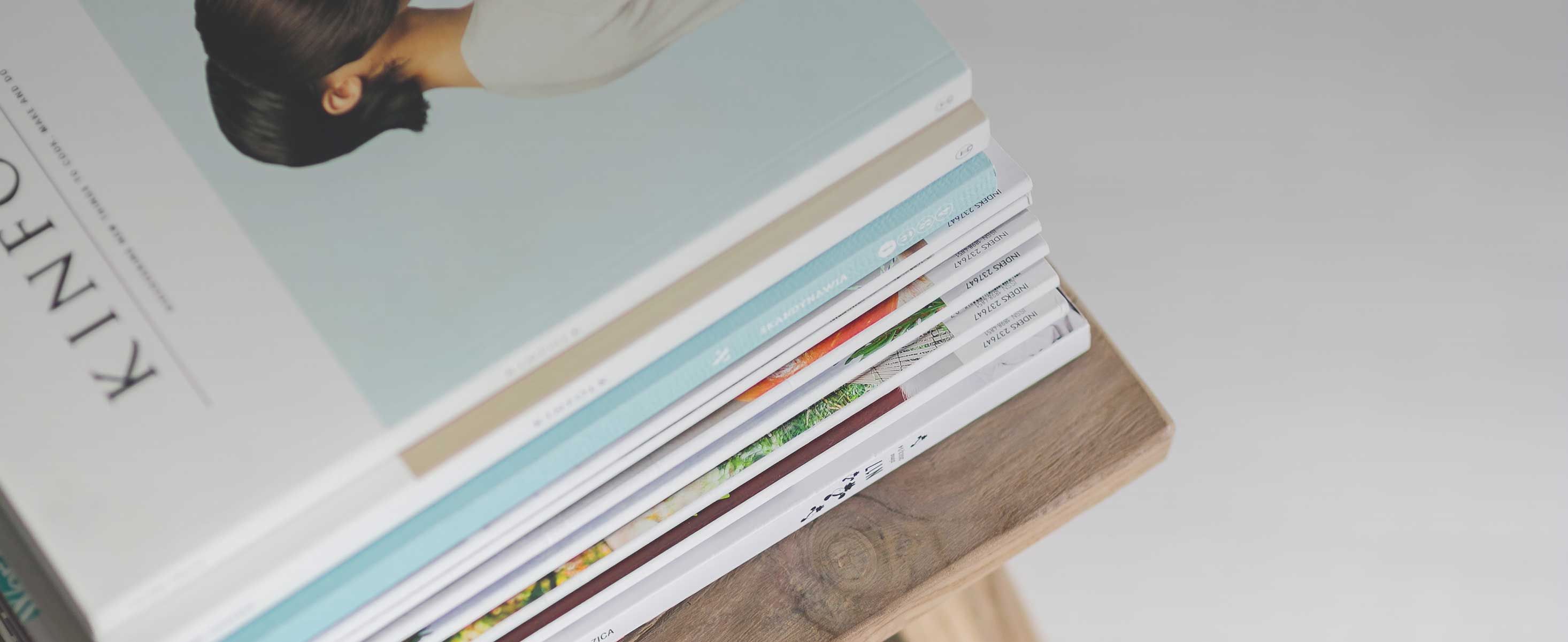
7 minute read
Installation
WPC? SPC? LVT? SVT? VET? VCT? Clarifying vinyl options
Christopher Capobianco I spoke at a presentation for a large flooring contractor recently about a variety of flooring in the resilient category, especially vinyl and rubber. After the meeting, one of the industry veterans in the group pulled me aside. “Christopher, we have a lot of new people here, and they may be shy about asking a lot of questions. I think a lot of the lingo around vinyl flooring is unfamiliar to them. You should put together a short course like Vinyl Tile 101 to clarify it all.” A few weeks later, I was asked to clarify the difference between WPC and SPC and I realized this may be a good subject for me. I am a long-time member of ASTM Committee F.06 on Resilient Flooring, where the industry standards for this category are created. As such, I am a bit of a terminology geek and these days, the terminology around “Vinyl Tile” has never been more confusing.
Advertisement
Let’s start with glue-down products and the ubiquitous marketing term Luxury Vinyl Tile (LVT). There are two ASTM product standards; Vinyl Composition Floor Tile (VCT) and Solid Vinyl Floor Tile (SVT). There is no category called LVT, a term that is sometimes applied to products that are VCT and sometimes as SVT. The difference? SVT has a higher vinyl content and thus, different performance characteristics than VCT. SVT is less porous, which makes for easier maintenance, but also requires a different adhesive because they have a vinyl back. Regardless of which resilient flooring you work with, most of the rules are the same — site conditions, product acclimation, and substrate preparation/testing don’t change from one product to another.
An area where I still see a lot of mistakes being made is adhesive selection, application and open time. Follow the rules for adhesive selection and
proper trowel notch; it’s easy to assume that the same adhesive works on similar looking products, but that often is not the case because of differences in product backings.
Pressure sensitive adhesive (PSA) is the most commonly used adhesive for vinyl. Back in the day, we had “clear thinspread” for VCT when the industry was moving away from black, “cutback” adhesive. Installers like PSA for the long open time and working time that allow adhesive to be spread in a large area, turn clear and tack-up so the installer can work on top of the newly installed tile without any risk of tile shifting or adhesive oozing. SVT products can sometimes be installed with a PSA, but don’t be tempted to use VCT adhesive on SVT. It’s a different formulation that doesn’t always work on vinylback products.
Another method is wet-set — adhesives with short open time, so the tile is set while the adhesive is still wet. Homogeneous SVT often requires this type and vinyl back tile and plank in high traffic areas may also. Although harder to work with, they set very hard, which keeps the tile in place over the long term. In even more extreme conditions, twopart reactive adhesives such as epoxy or polyurethane work best in areas with high rolling loads or point loads, surface moisture or wide temperature variations.
An option that I prefer for vinyl-back tile and plank is semi-wet- or tacky-set adhesive that is left open long enough that it develops some tack, is still somewhat wet, but is not open long enough to turn clear. The best way to tell it’s ready is to touch it lightly with a finger. If you get a smudge on your finger, it is not ready. If you see lines from the trowel notching, it is. This method still gives some very good bond strength to the finished floor, but is easier to do than wet-set. Finally, I’ll stress one more time that the proper trowel is critical. READ THE CAN to see what size notch you need and replace the trowels as they wear down. A good trowel costs pennies per square foot and that is an important investment.
The category of “floating” products has really exploded in recent years. In the mid 1990s, laminate floors became popular because they required so much less floor preparation than
vinyl. The early products were a tongue-in-groove construction with adhesive applied at the joint. Later, clever inventors in Europe gave us “click” products: a unique, tonguein-groove design allowed the planks or tiles to fit together without adhesive, and this type of construction started to be used in engineered wood and bamboo, in addition to laminates. Then other products with HDF (high-density fiberboard) cores came out with different such materials on top as cork, and later, linoleum and vinyl.
About 12 years ago, I saw the first “click” vinyl, which looked like a typical vinyl plank, but thicker, so the core of the material could be produced with the “click” tongue-in-groove joint. Then came WPC (wood-plastic composite), and things really started to take off as these products started getting marketed as “waterproof.”
WPC refers to the core of the material. This is a mixture of plastic and wood or bamboo powder, sometimes called woodplastic core or waterproof core, but the correct term is wood plastic composite. These products generally have four layers — a cork backing, WPC core, printed film vinyl layer and clear wearlayer. The attached backing makes for easier installation compared to laminates that require a separate underlayment. They have great acoustic characteristics that have made them very popular for high-rise residential projects.
More recently a category called SPC arrived, which is similar to WPC but with a different core and a syntheticcushioned backing instead of cork. Both of these variations in construction make this product generally less expensive than WPC, but there are some performance differences as well. SPC stands for Stone Plastic Composite, or Stone Polymer Composite, which is basically pulverized limestone and vinyl resin, similar to VCT. WPC is softer under foot than SPC and has better acoustic performance. SPC and WPC products often get grouped together as rigid-core. I covered this category in my column Waterproof Floors last July. The important points for me are flatness and dryness. The term waterproof can be dangerous if you are going over a damp concrete floor and assume there will not be an issue. The material may be waterproof but there can be problems with trapped moisture under the floor and elevated alkalinity levels that come with it. Substrate flatness continues to be an issue for click floors of all kinds because if there is a dip in the substrate that causes the floor covering to move up and down, the tongue of the click joint can break and cause the floor to fail. Another point I learned since last July is that some products have very specific requirements for the direction of installation. I had a problem on a floor that was installed backwards with work progressing from right-to-left instead of left-to-right as per the installation guidelines.
Lastly, the category known as loose-lay vinyl is starting to gain in popularity because of ease of installing and removing the tile, and smoother transitions to adjacent carpets. As opposed to multilayer click products, these are square-edge vinyl tile and plank products that are thicker and heavier than glue-down products and have a textured backing to hold the tile in place. Most are adhered around the perimeter or in a grid and the remainder of the tile is laid loose. Sometimes, installers adhere the entire floor and some new products have a backing of microscopic suction cups that hold the tile in place with no adhesive at all.
It’s hard to keep up with the new products that seem to come at us all the time. As dealers and installers, it’s your job to do so — so take the time to learn these products before you take on any work.
Don’t make assumptions; some homework up front can help make the job go smoothly. I suggest you ask for a small mockup in cases of new products you’re not familiar with. Most suppliers will be happy to give you a few full tiles or planks to try.
Christopher Capobianco has been in the floor covering industry since the 1970s in various roles including retail and commercial sales, technical support, consulting, journalism, education and volunteer work. He currently is part of the sales team for Spartan Surfaces in New York City. You can reach him via christopher@SpartanSurfaces.com.