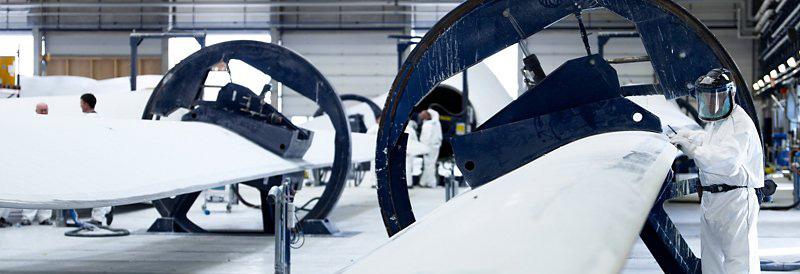
3 minute read
IN BRIEF
OCI Solar Power has now originated more than 3 GW of utility-scale solar projects in Texas, USA.
In 2021, Buckeye Partners acquired OCI Solar Power’s construction-ready Project Parker. The 200 MWac project located in Falls County is now supplying electricity to the ERCOT electrical grid. And in 2022, OCI Solar Power sold its construction-ready Project SunRay to Israel-based Arava Power and Paz Oil. It is now under construction on 1800 acres of privately-owned land in Uvalde County.OCI Solar Power had previously developed 500 MWac in collaboration with CPS Energy, the nation’s largest public power, natural gas, and electric company. These projects began operations between 2012 and 2019. In addition, OCI Solar Power has established a development pipeline in excess of 2 GW of projects located n Bell, Dickens, Falls, Hill, Kent, La Salle, McClennan, and Wharton counties.
Advertisement
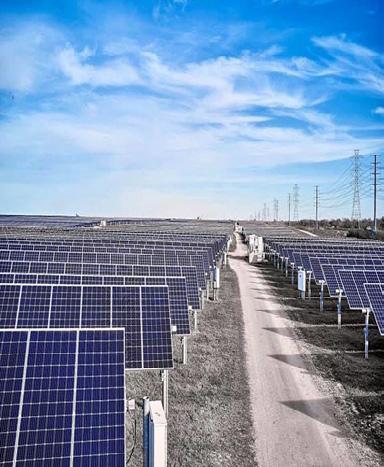
TURBINE TECHNOLOGY ELIMINATES THE NEED FOR BLADE REDESIGN, SAYS MANUFACTURER
A new solution which brings bring epoxy-based turbine blades into a circular economy, without the need for changing the design or composition of blade material is a game-changer, says Vestas, and will effectively eliminate the ‘landfill’ solution for end-of-life blades.
Combining newly discovered chemical technology developed within the CETEC initiative, and partnerships with Olin and Stena Recycling, the solution can be applied to blades currently in operation, says the company. Once matured, this technology is expected to eliminate the need for blade redesign, or landfill disposal of epoxy-based blades when they are decommissioned.
Lisa Ekstrand, VP and head of Sustainability at Vestas, comments: “Until now, the wind industry has believed that turbine blade material calls for a new approach to design and manufacture to be either recyclable, or beyond this, circular, at end of life. Going forward, we can now view old epoxy-based blades as a source of raw material.
“Once this new technology is implemented at scale, legacy blade material currently sitting in landfill, as well as blade material in active windfarms, can be disassembled, and re-used. This signals a new era for the wind industry, and accelerates our journey towards achieving circularity.” Turbine blades have been difficult to recycle owing to the chemical properties of epoxy resin, a substance once believed by manufacturers to be impossible to break down into completely usable components.
Amokabel has clinched a deal with a Sydney company to establish the local production of new-generation covered conductor which provides network resilience and bushfire protection on overhead electrical lines.
Amokabel, the Swedish specialist cable producer, has acquired Euro-Tech Cables Pty, a Sydney manufacturer of high-quality signal and communication cables. The deal completed in December 2022 has established a manufacturing footprint in Australia for Amokabel, with the long-term goal of producing covered conductor. Amokabel’s new-generation covered conductor is the most cost-effective technology that enables distribution network operators (DNOs) to increase their network resilience and vastly reduce the risk of bushfires starting when electrical lines come into contact with dry vegetation. This was the primary cause of the Black Saturday fires in 2009.
According to the Commonwealth Scientific and Industrial Research Organisation (CSIRO), covered conductor reduces the risk of ignition by 98 percent. It can be easily retrofitted to existing poles and infrastructure with minimal changes. As a lightweight technology, covered conductor ensures that virtually eliminates ‘interpoling’, which is the practice of adding additional poles to support the weight of older styles of covered conductors. It also brings many other benefits, such as increased public and wildlife safety.
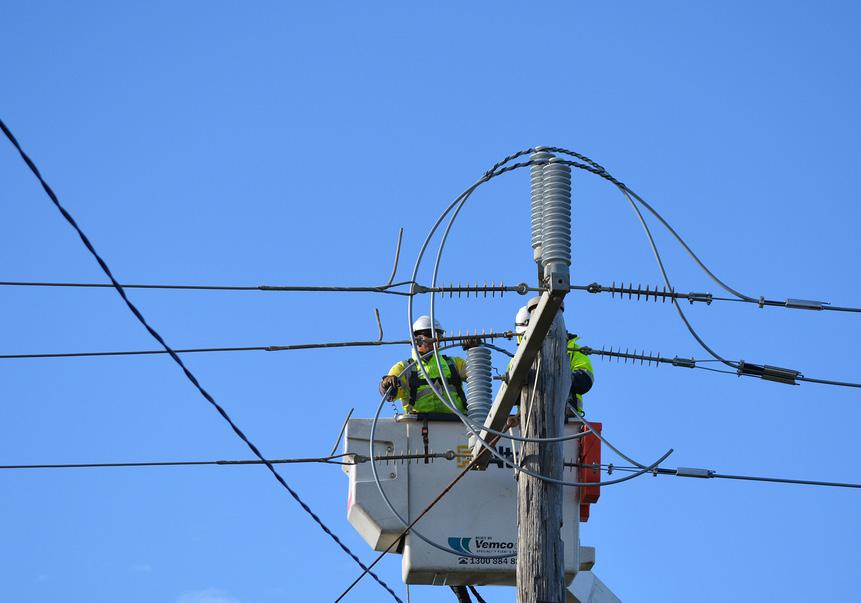
Having established its Australian subsidiary in 2021, Amokabel has been supplying DNOs with covered conductor and accessories from Sweden via a warehouse in Australia. However, demand is growing and it wanted to show its long-term commitment to the market by developing local production.
CEP Renewables, CS Energy, Terrasmart, Lindsay Precast and NJR Clean Energy Ventures have jointly announced that they have completed the largest landfill solar project in North America. This 25.6 MW solar project is located in Mount Olive, New Jersey and has enabled the township to recoup nearly US$2.3 million in past taxes while at the same time transforming the former Combe Fill North Landfill Superfund site into a revenue-generating, clean energy asset.
Chris Ichter, executive vice president at CEP Renewables, commented: “There are over 10 000 closed landfills in the United States, yet only a small fraction of these parcels have been redeveloped.
“Transitioning more of these landfill sites into solar projects will create more local tax revenue, jobs, cleaner air, and affordable energy for residents throughout the country.”
According to the EPA, there has been an 80 % increase i the number of landfill solar projects in the USA over the last five years.
As these landfills have existed for several decades, the key driver of this recent trend is said to be the landfill expertise developed by companies such as CEP Renewables.
CEP has extensive experience in the redevelopment of environmentally impaired sites, and CS Energy has completed 216 MW of landfill solar projects since 2011.
The Mount Olive project is also notable in that it involved the purchasing of the landfill by way of the redevelopment and tax lien foreclosure process.
