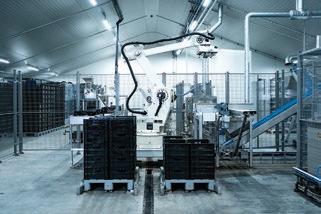
5 minute read
Three African Cities
TABLE 4.5 Value of BSFL Converting Fecal Sludge into Different
End Products in Three African Cities
End product Dakar, Senegal Accra, Ghana Kampala, Uganda
dry fecal sludge legally discharged per day (tons, thousands) value of bsFl converting this sludge to protein for animal feed (us$, thousands) value of bsFl converting sludge to fuel-biogas and selling the remaining residue as biofertilizer (us$, thousands) value of bsFl converting sludge to biofertilizer (us$, thousands) 6 26 16
40,000 235,000–255,000 129,000
— 248,000–258,000 159,000
12,000 54,000–134,000 81,000
Source: Diener et al. 2014. Note: BSFL = black soldier fly larvae; — = not available.
(temperature and humidity) in which it is grown. BSFL are high in protein and chitin. The fat and protein contents of harvested BSFL also depend on the substrate and, possibly, the time of harvest and different genetic traits (Wang and Shelomi 2017), but this has not been standardized across BSLF feeding studies. Wang and Shelomi (2017) found that BSFL, on average, produced 37 to 45 percent (40.8 ± 3.8 percent) protein (dry weight) and 20 to 36 percent (28.6 ± 8.6 percent) fat (dry weight) across 22 studies. This relatively high fat content is a general biological characteristic of insect larvae. The protein content is on par with other animal feeds like fishmeal (Shumo et al. 2019). BSFL, like all insects, also contain chitin, which originates from the insect’s exoskeleton. Chitin is functionally regarded as a dietary fiber, although studies suggest that it may also have probiotic properties benefiting animals’ gut health (Selenius et al. 2018).
BSFL production can be carried out in fully or semi-managed systems. In general, BSFL production includes three phases: (1) egg production, (2) egg hatching and larva growth, and (3) harvesting. BSF breeding and egg laying— called oviposition—require a netted cage in which the adult flies swarm and mate. After mating, the eggs are mixed with an organic substrate and hatch after four days. Next, the larvae grow for about 12 to 14 days. Typically, this process takes place in a stacked crate system (see photo 4.3 for examples of BSF production systems). Last, the BSFL farmers harvest the larvae by removing them from the unconsumed substrate. Alternatively, BSFL can be reared in simpler, semi-managed systems with open containers of organic substrate that attract wild BSF (Nyakeri et al. 2016). However, in unmanaged systems, the BSFL will “self-harvest,” or naturally separate from the substrate at the prepupal stage. This characteristic skips the step of separating the larvae from the substrate;
PHOTO 4.3 Examples of BSF Production Systems
a. Automated system in Denmark b. Automated stacked crate system in the Republic of Korea
c. Net-breeding system in Kenya d. Small-scale system in Kenya

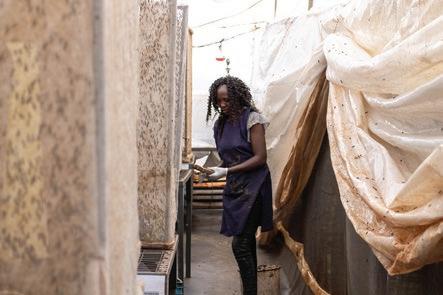
Photographs (panel a) © Mathilde Kræmer / ENROM BioFactory A/S. Used with the permission of Mathilde Kræmer. Further permission required for reuse. (panels b and d) © Nanna Roos / University of Copenhagen. Used with the permission of Nanna Roos. Further permission required for reuse. (panel c) © Talash Hubers / InsectiPro. Used with the permission of Talash Hubers. Further permission required for reuse.
however, leaving the larvae to grow unmanaged to the prepupae stage is not optimal because only some larvae will leave the substrate. Furthermore, the prepupae will have lost mass and have a more sclerotized cuticle. As a result, fully managed systems are more efficient for producing BSFL.
Breeding BSF is difficult, but new methods are making it easier. Managing the BSF’s full life cycle is challenging because it is hard to control the adult flies (Sheppard et al. 2002). Flies will mate only in daylight, and oviposition requires a suitable material to attract the flies during a narrow time frame in their short life span. Researchers and commercial producers have developed various models to overcome these challenges, including using artificial light to replace daylight, identifying alternative substrates to attract flies to stimulate
oviposition, and designing containment structures that are optimal for egg laying and hatching rates.
BSFL are being commercialized at an industrial scale. The advancements in controlling BSF breeding have made large-scale production systems possible. Globally, several companies have invested in large-scale BSFL production. New technologies for industrial-scale BSFL production are emerging quickly. The World Intellectual Property Organization’s portal for patents shows that there are 259 entries for “black soldier fly.”4 Industrial-scale production plants with semi- or fully automated production can handle up to 1,000 tons of organic waste per day. The first large-scale industrial production system for BSFL was established in 2015 (Drew and Pieterse 2015). However, production capacity is largely unknown because companies have not made this information public nor do any independent organizations seek to compile these data. That said, some market analysis companies have attempted to map the BSFL sector and rank the leading companies by the estimated production capacity (Persistence Market Research 2019). This research shows that several producers have invested in industrial-scale BSFL production facilities in recent years, including Protifarm (the Netherlands), AgriProtein (South Africa/United Kingdom), Ynsect (France), Protix (the Netherlands), C.I.E.F. (Korea), and Enterra (Canada) (see table 3.7). Other companies have established the capital investments needed to reach industrial production capacity, including Enviroflight (United States), Nutrition Technologies (Malaysia), Goterra (Australia), and ENORM (Denmark).
BSFL’s main market is animal feed. BSFL can be processed into meals that are fed to animals. In Europe, Canada, and the United States, initial efforts to market BSFL were made in aquaculture, or as a feed ingredient for selected fish species. More recent efforts have expanded the market to pet foods in the European Union and poultry in Canada and the United States. Pet and poultry markets support higher price points than the aquaculture market, making BSFL-based meals economically viable for BSFL producers. Moreover, fishmeal prices are rising, and if this continues, the viability of BSFL meal replacing fishmeal will become more realistic. A female farmer in Kenya commented, “Feed makes up 60 to 70 percent of the cost of animal production and the cost of protein makes up 70 percent of the cost of feed. So, we started looking at alternative options for protein and landed on the black soldier fly. We started in November 2018 with 2 kilograms of BSF and are now [November 2019] at 3 tons of daily production.” In Africa, BSFL substitutes for animal feed ingredients, like fishmeal, are more viable than in Europe. In Kenya, BSFL meal is competitive with both fishmeal and soybean meal on a protein per unit price basis (table 4.6). And since BSFL production systems in Africa are less automated than those in Europe and North America, start-up and production costs can be lower, translating into higher profit margins initially.
BSFL processing can separate elements of the insect for different purposes (figure 4.9). Maintaining the oil fat in BSFL increases BSFL meal’s rancidity