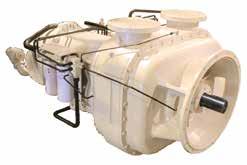
2 minute read
Tamrotor (Ingersoll Rand
The world leader for compressor solutions for mining applications
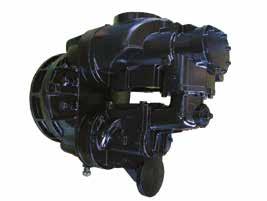
Advertisement
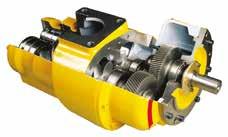
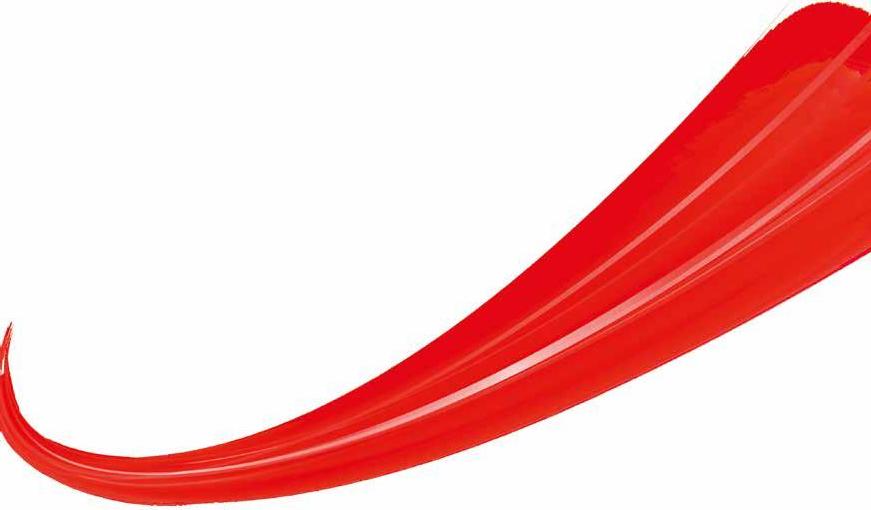
4,000 CFM / 115 m3/min High flow with high performance #1 in reliabilty and durability 500 PSI / 35 BAR For when you need high pressure
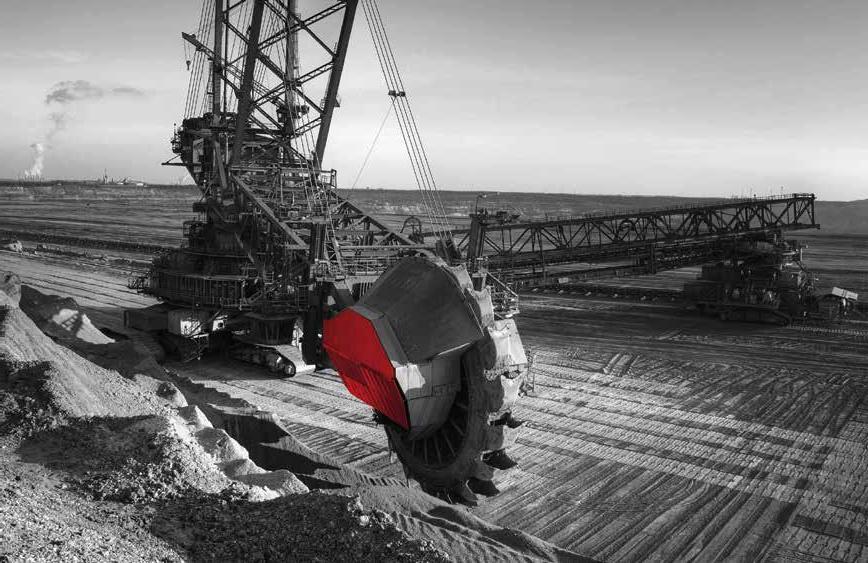
Ingersoll Rand has served the mining industry for over 150 years. Our OEM brands include Ingersoll Rand, GHH RAND and Tamrotor, making us the global leading manufacturer of the screw airends and compressor packages. Whether you manufacture drill rigs or have an aftermarket need, lean on us to make your life better.
www.oem-solutions.ingersollrand.com
Part of the Ingersoll Rand family
Adding the Tamrotor offering of airends and compact compressor packages perfectly complements the Ingersoll Rand and GHH RAND brands, giving us the most complete OEM offering - whatever your application is, we have the solution.
Oil injected single stage air ends Enduro Series Integrated air ends Tempest Series Compact compressor packages for mobile applications CT Series
news

ABB has launched ABB Ability™ Condition Monitoring for belts, an advanced digital service to enable mine operators to track speed, misalignment, damage, thickness and wear, slippage and temperature of conveyor belts in real time, and therefore anticipate maintenance, avoid unplanned downtime and improve belt reliability and lifetime.
The technology is based on sensors installed at strategic points of the conveyor belt equipment and is specifically designed to withstand harsh environments while monitoring asset health and condition.
“Real time monitoring of the actual belt performance prompts the necessary corrective actions ahead of failure or further and more costly damage,” said Eduardo Botelho, Global Material Handling Service Product Manager, ABB. “With equipment condition continuously assessed, operators can plan necessary maintenance only when certain indicators give the signal that the equipment is deteriorating, and the probability of failure is increasing. It will consistently catch misalignment or speed issues online, long before failure, and pre-empt issues such as falling material, energy waste, excessive belt wear, rupture or fire.” The solution can work as a stand-alone option or can be integrated into any control system, being interoperable with existing maintenance tools and infrastructure. KPIs can be customized, based on customer’s needs or pain points.
Purepoint Uranium starts diamond drill program at Red Willow Project
Purepoint Uranium is drilling its 100%-owned Red Willow project in the eastern uranium mine district of the Athabasca Basin, Saskatchewan, Canada.
By far the company’s largest project, Red Willow is located close to several uranium deposits including Orano Resources Canada’s JEB mine, approximately 10 kilometres to the southwest, and Cameco’s Eagle Point mine approximately10 kilometres due south. “This will prove to be a very busy year in the field,” said Scott Frostad, Purepoint’s VP Exploration. “The spring drill program will allow us to begin reprioritizing many of the exploration targets we have previously defined across this large land package.” The Red Willow project consists of 17 claims covering 40,116 hectares on the eastern side of the Athabasca Basin. Beginning at the Osprey Zone, Purepoint intends to drill approximately 1,200 metres at Red Willow during this program. Depending on conditions and results, the company hopes also to test the Geneva and 333 Zones.