

eVtoL future
wing designs Airbus accelerates with the help of software platforms
The aircraft maker’s Wing of Tomorrow program leverages 3DExperience tools to cut months from the development cycle.
Tereza Pultarova
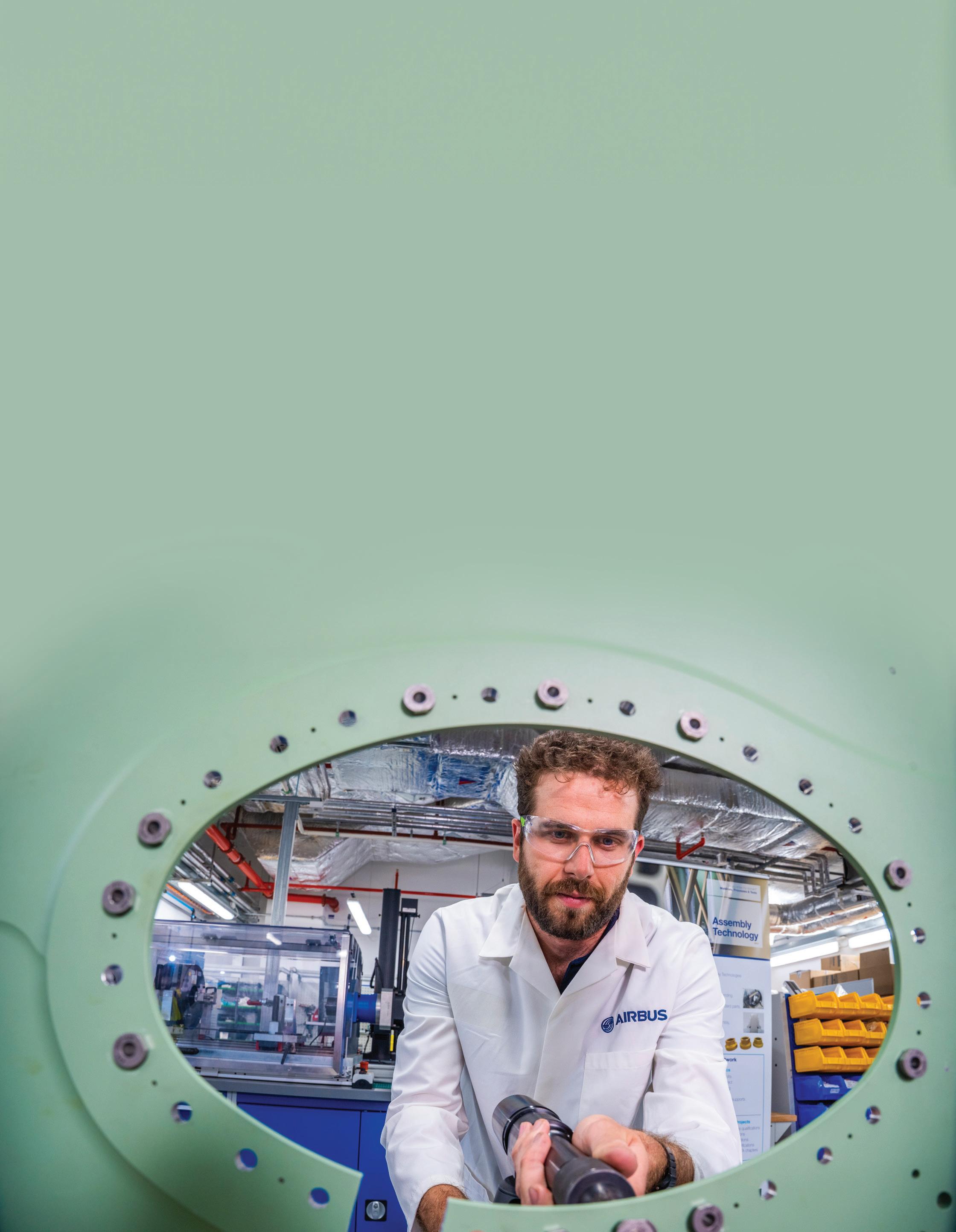
Airbus is reinventing the wing to make it fit for the age of carbon-neutral aviation. The company’s engineers are taking advantage of a 3D digital “co-architecture” environment that enables them to optimize the wing design and the manufacturing process in one go.
Since 2016, teams at the European aerospace giant’s Wing Technology Development Centre (WTDC) in Filton, U.K., have been playing with unconventional ideas that could change how aircraft-makers approach wing design. Pressed by the need to eliminate the carbon footprint of aviation by 2050, in line with international commitments to fight climate change, Airbus is experimenting with lighter composite materials to reduce weight. The company also wants to make wings longer and leaner to increase lift and lower fuel consumption. The goal of the research program, called the Wing of Tomorrow, is to offer a menu of different technology solutions “to enable the development of the next-generation wings,” Airbus says. The work has already produced results, and the first demonstrators are being built to undergo testing next year.
Yann Lewis, the Wing of Tomorrow’s head of engineering, says Airbus has built the demonstrators using a novel approach that relies on advanced digital tools
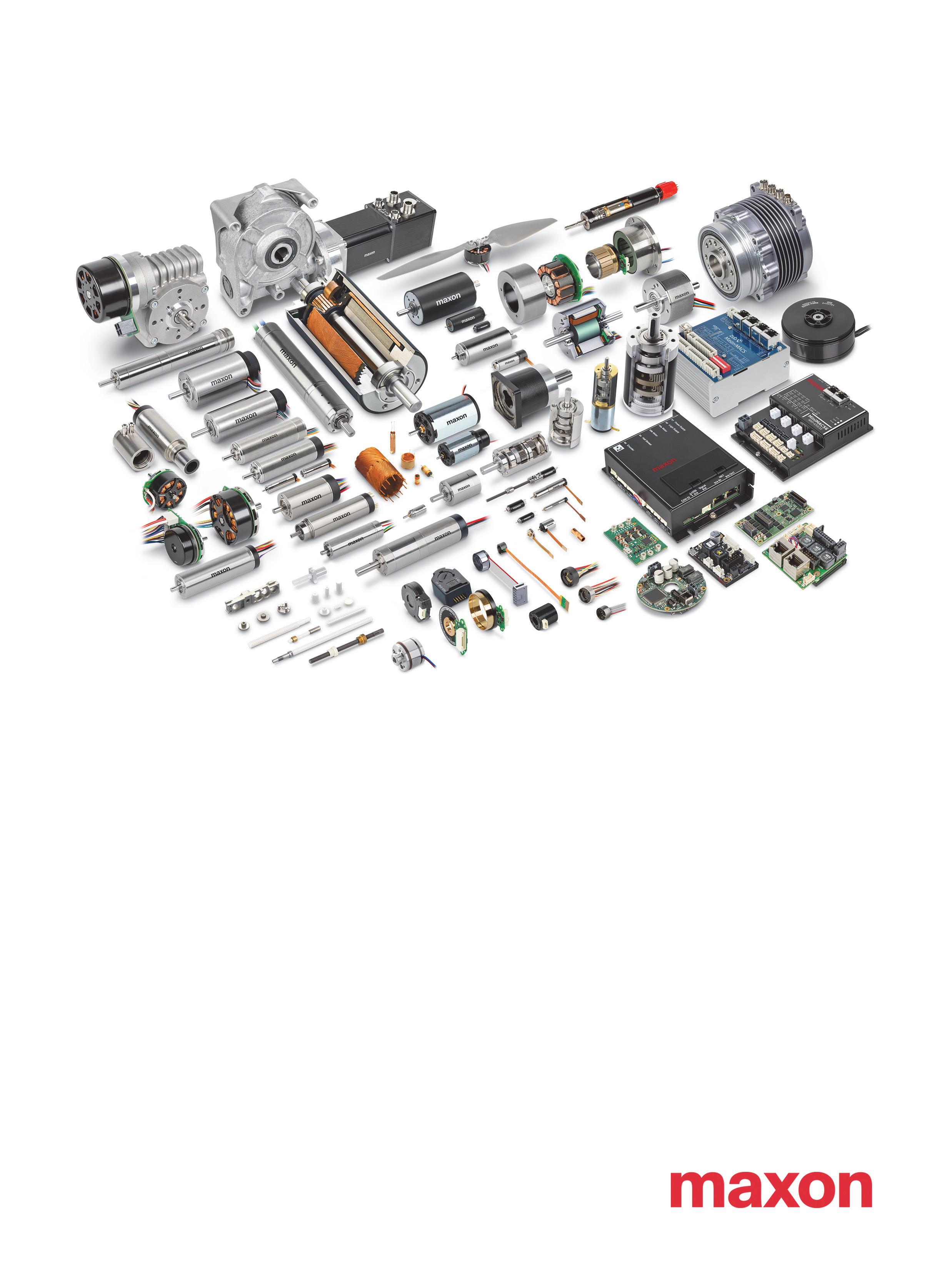




allowing engineers, designers, and manufacturing experts to interact with each other in the same 3D digital environment in real time.
“When we came to assemble the Wing of Tomorrow wing boxes, we had very few instances where there was a clash with manufacturing requirements,” Lewis said. “We were able to get it right the first time, which I haven’t seen in many other Airbus programs before. That’s of great value because in any sort of serial production environment, if something doesn’t work right the first time, it takes a long time to fix it.”
Finding paths for automation
A wing box is the load-bearing structure of an aircraft wing to which other components, such as flaps and wingtip devices, attach. Assembling these structures has traditionally been a tedious, manual process, says Lewis. Technicians must at times climb inside tight fuel tanks located inside the wing boxes to install fasteners and fuel pipes. In the future, Airbus hopes to make the assembly process more automated to speed it up and make it more comfortable for the personnel. The collaborative digital design approach trialed as part of the Wing of Tomorrow program helps the engineers identify which tasks could be taken over by robots and how to redesign the factory to optimize workflow.
“If you look at the wing assembly process of the single-aisle A320
The Wing Technology Development Centre’s goal is to develop a menu of technology solutions that can feed new wing designs.
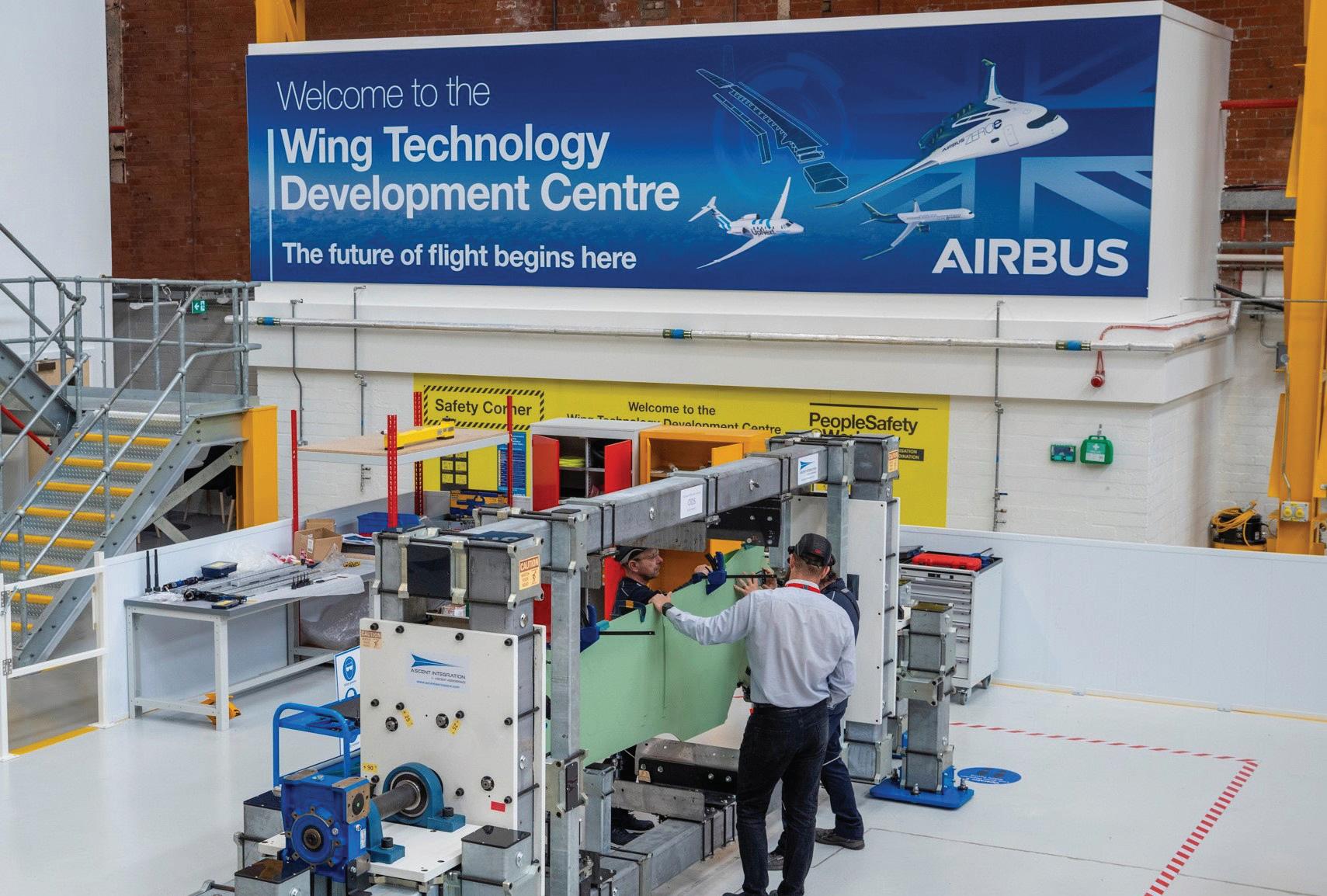
aircraft [Airbus’s flagship narrow-body aircraft manufactured since 1984], it’s very manual,” said Lewis. “As part of the Wing of Tomorrow program, we are looking for opportunities for automation, the use of robots for positioning parts, clamping parts, drilling. It’s quite a big step change.”
Lewis added that although the design changes may seem subtle, the engineers wouldn’t be able to identify them without working in a common environment with the manufacturing experts from the start.
“We would likely have encountered problems or clashes between robots and structure later on during the build when it is too late to change the design,” he said.
AExxxPGA Family
Ultra-low Loss Power Inductors
This step change in the way aircraft are built is called for. According to the International Civil Aviation Organization, demand for air transport is on the rise and will continue to grow over the next 20 years at a rate of 4.3% per year. For Airbus, currently the world’s biggest manufacturer of passenger planes, that means the need to build more aircraft and build them faster, in addition to ensuring that this new aircraft produces less carbon emissions
A platform for possibilities Airbus has been using computer-aided design (CAD) and computer-aided engineering (CAE) tools for more than four decades, pretty much since the technology was introduced in the 1970s.
• Offer up to 40% lower DCR than previous best-in-class inductors
• Meet NASA low outgassing specifications
• Pass vibration testing to 80 G and shock testing to 1000 G
• Currently offered in eight sizes with inductance values from 0.11 to 47 µH and current ratings up to 38 A
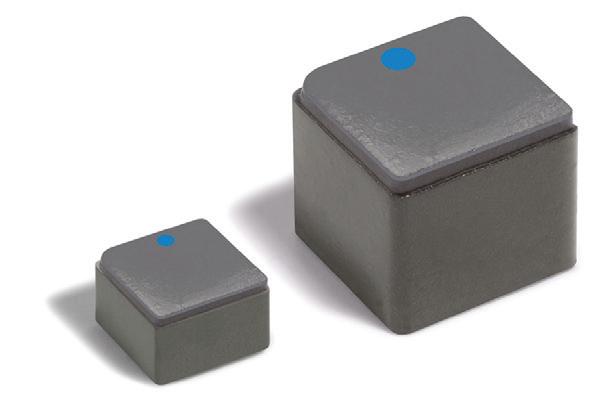
| Airbus / Neil Phillips Photo and Film Ltd.
For more than twenty years, the firm has been relying mostly on the Catia CAD and CAE software suite developed by French company Dassault Systèmes. However, Airbus’s adoption of Dassault’s 3DExperience software platform, which integrates Catia with Delmia (manufacturing), Enovia (PLM) and other tools, opened new possibilities for Airbus.
“We can collaborate and come up with designs that are lightweight, efficient, and perform well structurally,” said Lewis. But we can also be more sympathetic to the manufacturing process. We can visualise the proposed solution and model the type of tooling that we might need to create certain attachments, see whether there is enough space and whether it’s going to be ergonomic.”
The simulations are instantly fed data from completed hardware tests to compare accuracy of the predictions with real-life performance and, in turn, improve fidelity of future simulations. The 3D CAD model also automatically links with the finite element analysis (FEA) model that engineers use to analyze the resiliency of the assembled wing boxes. The linking of the CAD and FEA models means that any updates in the design are immediately reflected in the simulation, shortening the development cycle by “months of time,” said Lewis.
“We’re able to run and show the results of any simulations within the same environment, as well as capture data from the tests that we do and any manufacturing steps that we have,” said Lewis. “We can pull all that data into the same environment, which means that we have a much better understanding not only of how to design [the product] in the first place, but also as we move it through the design and manufacturing cycle”
Simulation advances wing testing
In early 2025, the team at Filton plans to take one of their perfected wing boxes and attempt to break it. Attached to a test airframe inside a giant hangar, the wing will be pulled up and down by a system of levers with a gradually increasing force until it cracks. Before breaking the wing for real, the engineers will simulate each of the 12 tested load scenarios digitally.
“Thanks to the simulation, we have a first confident view of how that wing is going to behave during the test,” said Lewis. “That means we can identify areas of interest where something interesting is going to happen on a particular load case. That allows us to put the right instrumentation onto the test specimen to monitor and capture the behavior.”
Over the years, the engineers have conducted many smaller-scale test, the results of which were captured by simulation software, giving the team high confidence in the results of the simulations. Such experiments have been part of Airbus’ testing procedures for decades, but only recent advances in computer technology allowed them to model the entire wing-breaking process.
“It started off with pitifully small and simple models,” said Lewis. “Like three or four rib bases, because we didn’t have the computing power to resolve more. Now we have a simulation model that covers the whole of the wing in a way that predicts the types of behavior that in the past were limited to those smaller models.”
Lewis says that simulations will never fully replace hardware tests but will reshape the “testing pyramid” in a way that proves various design solutions more quickly and earlier in the process.
“You can do more and more quickly, explore a wider design space and also compress some of the timescales,” said Lewis.
In the future, Lewis foresees many of the tasks performed by engineers today being taken over by artificial intelligence. Data collected in the collaborative simulation environment could help Airbus begin experiments and train algorithms that could be used to design wings beyond the Wing of Tomorrow program.
The demonstrators developed as part of the Wing of Tomorrow project are not yet intended for any existing or planned aircraft line and might take decades to take to the skies. The engineers are proposing, for example, to add four-meter-long folding wing tips to the wing boxes to increase their lift while at the same time maintaining the aircraft’s dimensions within the limits required by existing airport infrastructure. AD
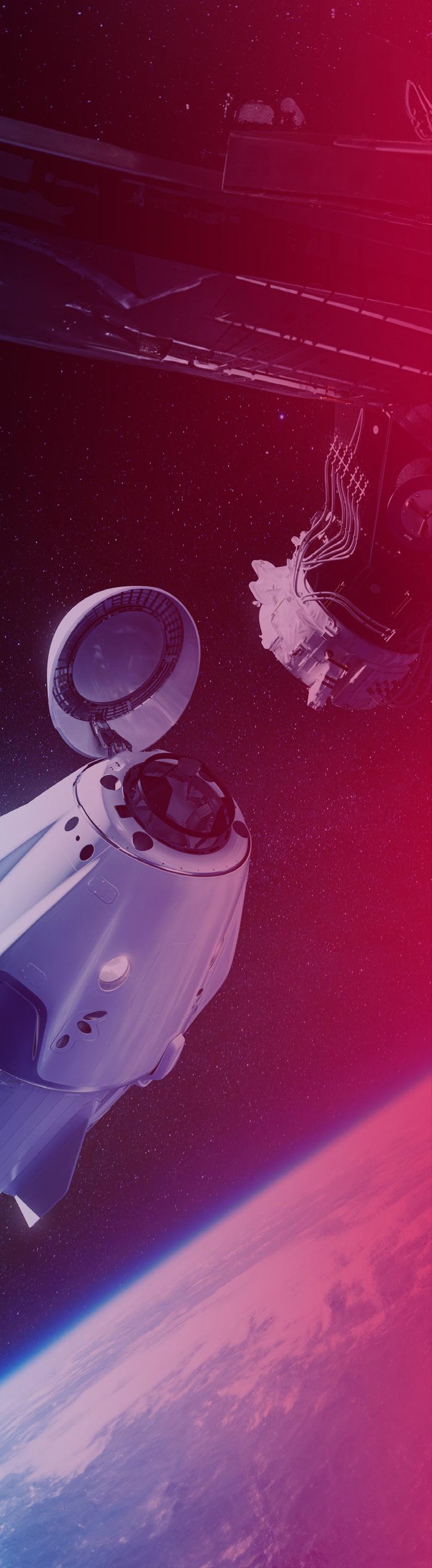
CONNECT TECHNOLOGY WITH CONFIDENCE
and temperature range rigorously tested.
OUR QUALITY,
SUPPORT, AND HIGHLY RELIABLE PRODUCTS, YOU CAN DEPEND ON
Harwin’s connector products are proven to perform in extreme conditions, with shock, vibration
HARWIN.
How Joby Aviation created its
low-noise flying taxi
The eVTOL diminishes its decibels one rotor blade at a time.
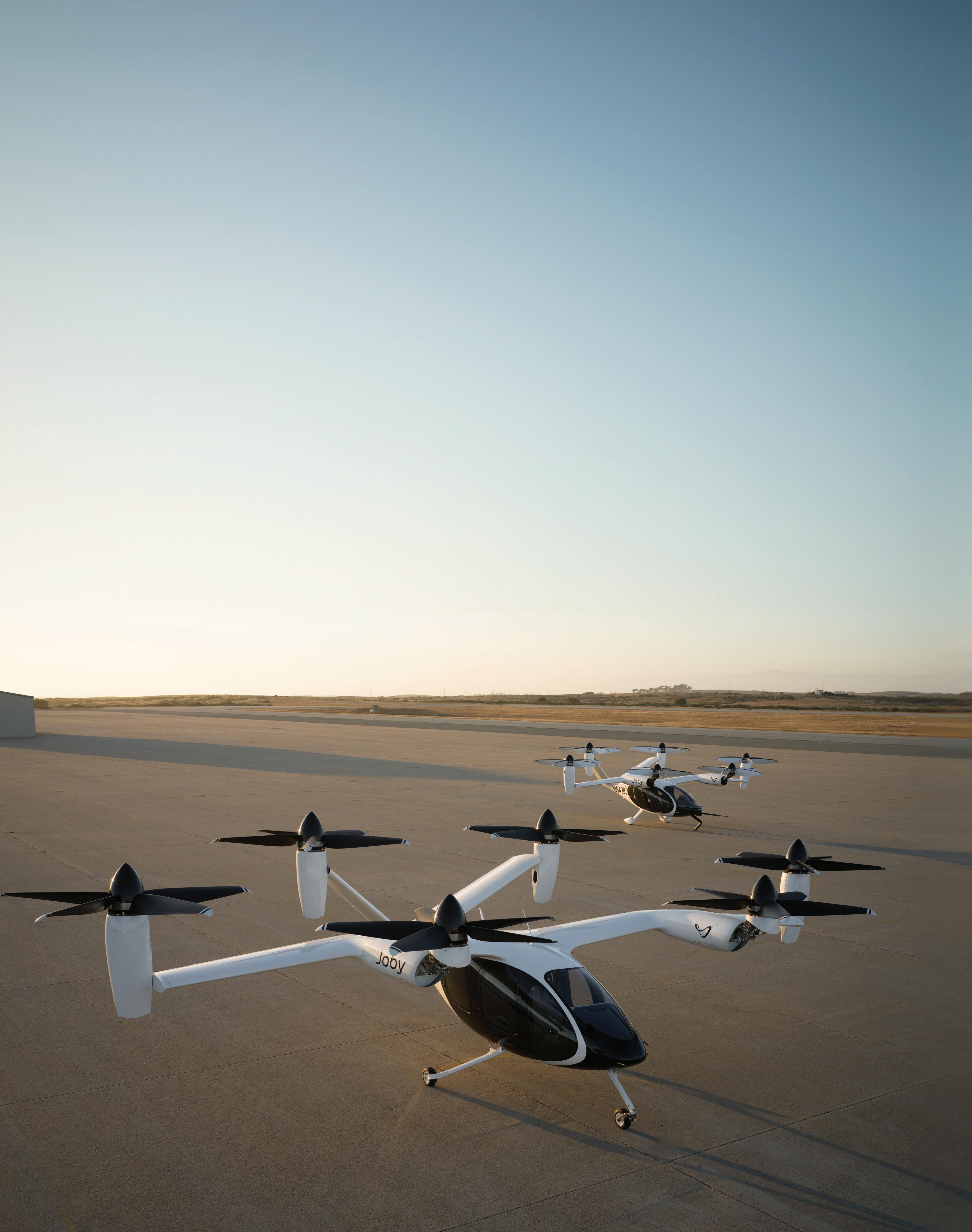
Joby Aviation’s eVTOL is 100 times quieter than a helicopter of similar mass, thanks in part to its propeller design. | Joby Aviation
Tereza Pultarova
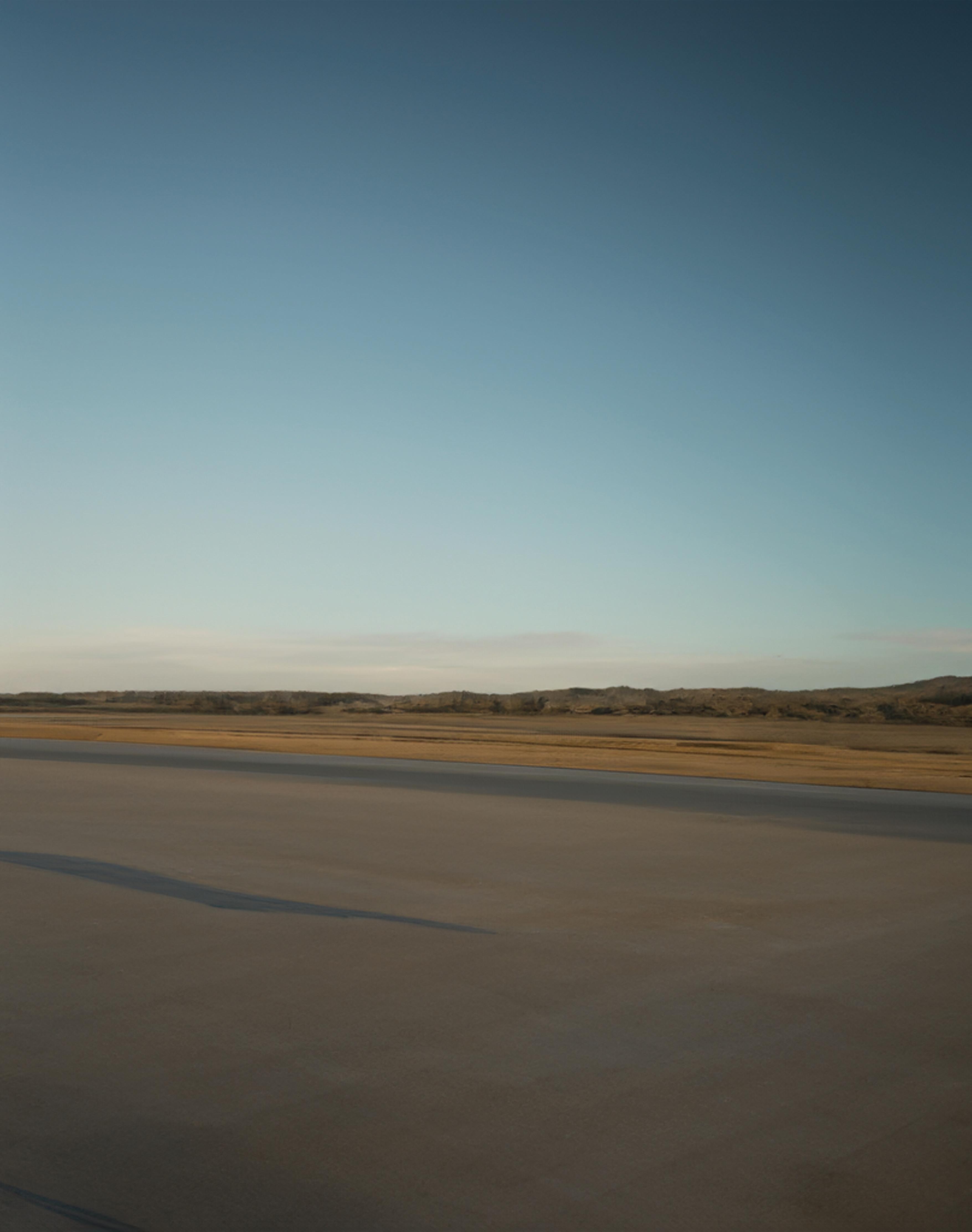
Flyingcars have been a staple of science fiction for decades. Soon, they might be whisking wealthy city dwellers from point to point while common folk idle in traffic jams below.
California-based Joby Aviation hopes to obtain a license from the Federal Aviation Administration (FAA) for its hexacopter-like vehicle to shuttle paying passengers around America’s busiest cities as early as next year.
The electric vertical take-off and landing (eVTOL) aircraft can carry four passengers and a pilot, fly 100 miles on one battery charge and reach speeds of 200 mph. During the aircraft's 15 years of development, Joby engineers had a major problem: making the aircraft so quiet that it wouldn’t bother city dwellers.
“From day one, we considered a low acoustic footprint to be a core design requirement for the Joby aircraft,” said Didier Papadopoulos, president of Joby’s Aircraft OEM division. “We knew that in order for electric flight to become an accepted mobility tool in and around cities, our aircraft would have to be orders of magnitude quieter than today’s helicopters – and that is exactly what we’ve achieved.”
As quiet as a conversation
There's no missing a helicopter hovering above a city. The noise of its rotor blades interacting with the surrounding air thunders compared to the background noise of an urban environment.
The sound of an air ambulance rushing to save a life, a police chopper on the hunt for a fugitive or the occasional politician on their way to a high-profile event is considered a fact of life in the city. But hundreds of helicopters carrying people across the city solely for convenience will almost surely spark public outrage. Furthermore, transport noise pollution is a significant health hazard, with studies showing that exposure to consistently elevated levels of noise frequently causes disturbed sleep and stress, increasing the risk of heart disease and diabetes.
Joby, therefore, set out to make its eVTOLs barely perceptible “against
the ambient environment of cities.” That goal was achieved two years ago when a NASA-led test campaign proved that the sleek air produces sound of about 45 weighted decibels (the relative loudness perceived by a human ear) when flying overhead at a distance of 500 meters. That’s quieter than a regular human conversation. An average helicopter hovering 300 meters away generates nearly 80 dB, nearly a thousand times louder than the Joby aircraft. Papadopoulos says Joby’s aircraft is 100 times quieter than a helicopter of a similar weight. The company compares its sound to the rustle of leaves in a breeze.
“Our aircraft’s low noise profile is the result of more than 10 years of hard engineering focused on acoustics, ranging from the design of our motors and propellers to the overall architecture of the aircraft,” Papadopoulos says. “There are numerous aspects of the aircraft’s design that have been selected and optimized to both reduce the magnitude of the sound produced during flight and improve the quality of that sound.”
Minimizing blade-vortex interaction
The Joby aircraft can be piloted remotely, but the company plans to fly passengers with a pilot on board to improve comfort and safety. The eVTOL's six propellers are arranged roughly hexagonally and draw power from four battery packs similar to those used in electric cars, with each motor drawing power from two of the packs to reduce the chance of failure.
But Papadopoulos said that swapping an internal combustion engine for an electric one doesn't solve the helicopter noise problem because most noise results from the rotor blades moving through the air. Joby's engineering team countered this by perfecting the design and positioning of the six propellers and each of their blades.
“Many aspects of Joby’s configuration were carefully selected to minimize or eliminate noisy adverse interactions between air flows produced by our six propellers in all stages of flight,” said Papadopoulos. “This
includes maximizing the distance between each propeller, the placement of propellers relative to the airframe, and the raised tail rotors."
Each propeller can also independently adjust its rotation speed, tilt, and the pitch of its blades. That, Papadopoulos explains, enables the aircraft to minimize the interactions between the blade tips of one propeller and the aerial vortices caused by the blade tips of another. Since the rotor blade tips slice the air at half the speed of sound, suppressing these vortices is extremely important.
The amount of noise each blade produces is also proportional to the weight it lifts. “We made careful decisions around the number of propellers our aircraft has — six larger propellers instead of more, smaller propellers — and five large-area blades per propeller,” Papadopoulos said. “This directly correlates to noise through the tip speeds of the rotor blades.”
However, the Joby vehicle is not purely a giant drone. The aircraft also features an 11.6-meter wing that takes over most of the lifting work once the vehicle is aloft. According to Papadopoulos, that means the propellers must provide only about a tenth of the force needed by a helicopter of a similar size when in cruise mode.
NASA and DARPA tools aided blade design
Joby has been flight-testing its first full-scale prototype aircraft since 2017. At that time, the noise generated by the prototype was considerably lower than that by a conventional helicopter –but the engineers believed it could be lower still. They began fine-tuning the propulsion system, focusing especially on the shape of the blades.
“We started with a CAD design of the blades,” Papadopoulos said. “We then used rapid composite prototyping to build the blades, test them, process the results, and design a new blade. We build many blades to improve our understanding of the noise sources to design new, quieter blades.”
The team used a range of highfidelity tools developed by NASA
Joby Aviation’s commercial air-taxi operation should be off the ground in Dubai by late 2025, said CEO JoeBen Bevirt on an earnings call in August 2024. | Joby Aviation
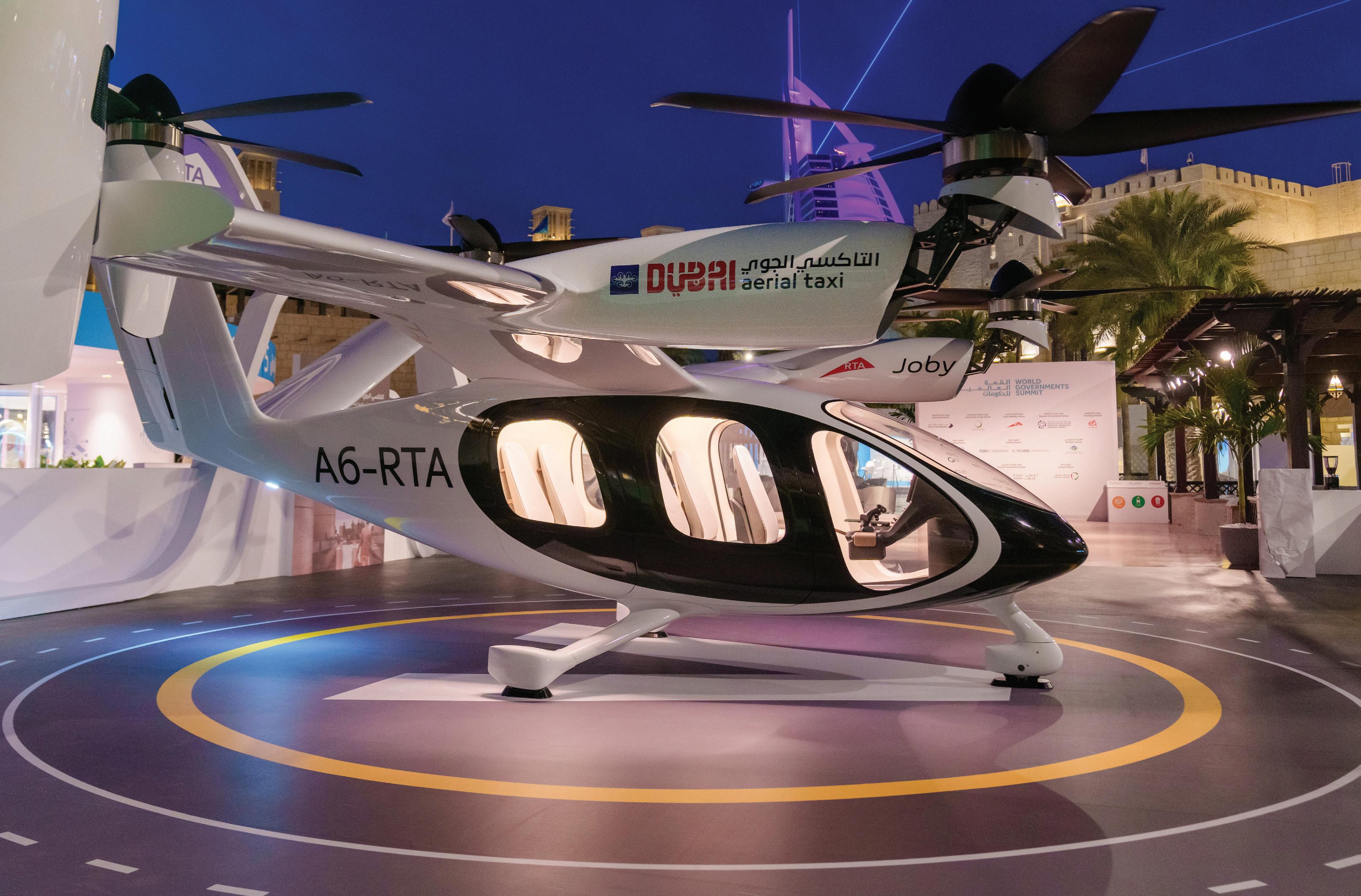
Brushless Motors
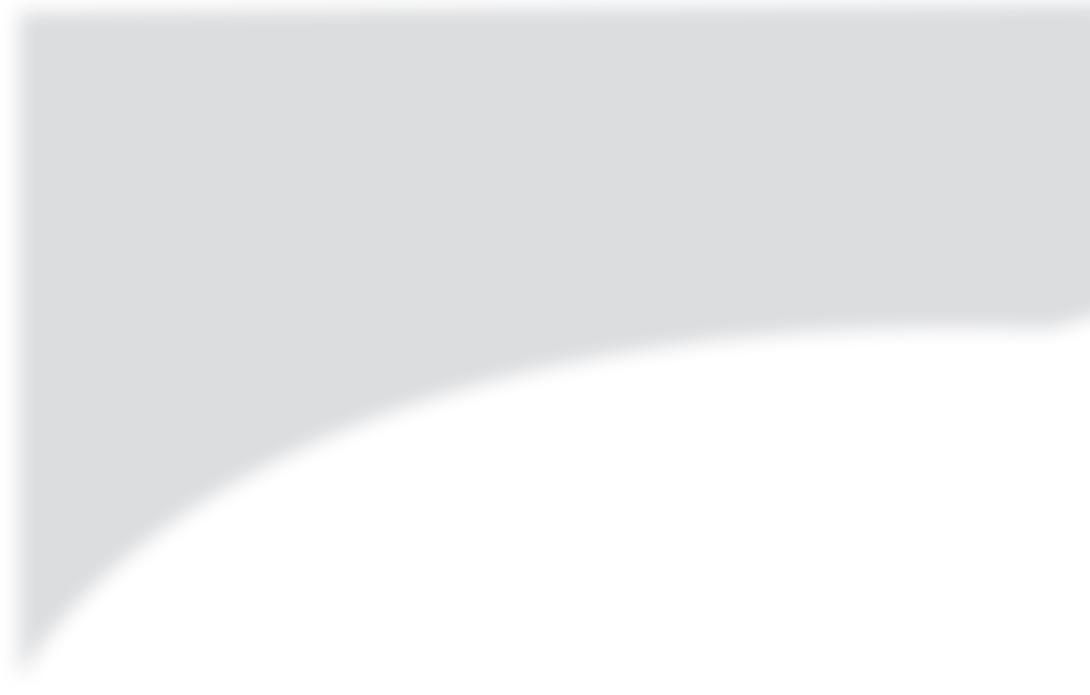
•
Solid or hollow shaft, high performance, housed and frameless, brushless motors and matching drives for demanding applications.
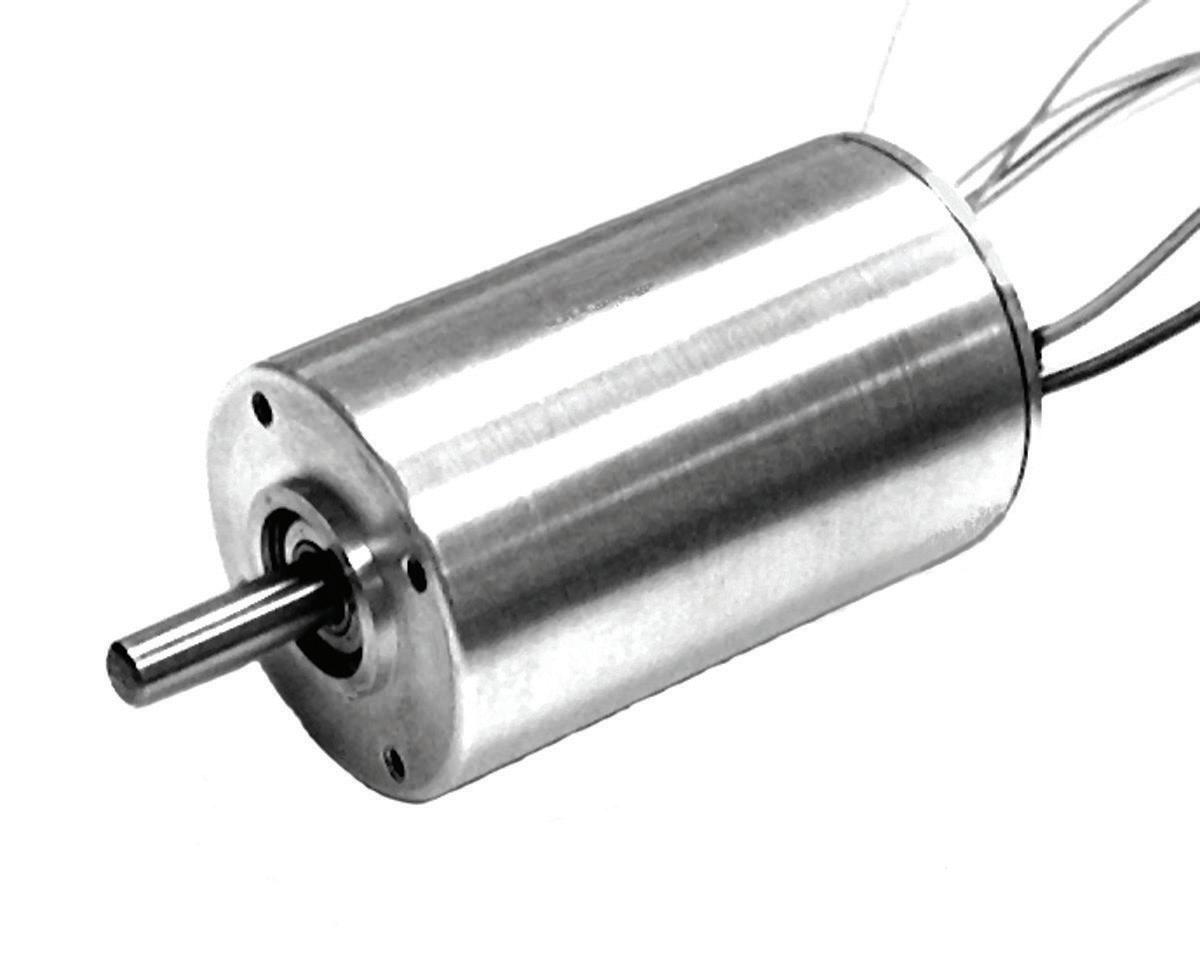
Hall or sensorless motors and drives for surgical tools, aerospace, military, and scientific instrument applications.
Custom drive programing and designs available.
Motors up to 95% efficient, power up to 1,500 watts.
Highest power density in the industry.
Operating temperatures from -73C to 150C
Slotless and slotted designs. Available with encoders and gearheads and separate or integral electronics.
Quantities 1 to 5,000.
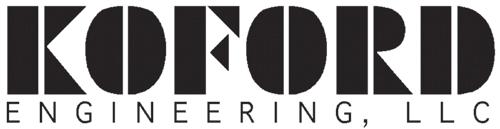
and the U.S. Defense Advanced Research Projects Agency (DARPA) to model the acoustic behavior of the propellers. They then tested the prototypes in a wind tunnel and on a special test circuit they built near Joby’s headquarters in Santa Cruz, Calif. Nicknamed the Whirly, the test track allows the engineers to send a propeller attached to a rig around at a speed similar to the Joby aircraft's cruising speed and measure its aerodynamic behavior in conditions akin to those of an actual flight.
The experiments showed, for example, that wide blades produce less noise than narrow ones. Subsequent flight tests showed the redesign further reduced the loudness of the propulsion system by 3 dB while delivering the same thrust.
“Generally speaking, our blades have much more surface area than helicopter blades, allowing for lower tip speeds, but not too much area, which can increase other noise sources,” said Papadopoulos. “We have found that careful optimization of the airfoil design and blade shape can balance the noise sources, allowing for a sound that more closely resembles leaves in a breeze than the strong whopwhop of a helicopter.
Joby Aviation's commercial air-taxi operation should be off the ground in Dubai by late 2025, said CEO JoeBen Bevirt on an earnings call in August 2024. (Image: Joby Aviation)
In May, Joby announced the completion of more than 1,500 flights covering more than 33,000 miles, including 31 flights in partnership with the FAA to demonstrate “the aircraft’s operational characteristics and precision landing capabilities.” Pilots were on board for more than 100 of those flights.
The company plans to commence further testing with the FAA soon to obtain final certification to start commercial operations. If all goes well, Joby could ferry its first paying customers in 2025. AD www.koford.com Contact us at mail@koford.com
Scott Miller • Director of Product Management • Cinch Connectivity Solutions
eVtoL future The is counting on interconnect
For a sky full of flying cars to become reality, they’ll have to lighten up. Smart selection of cables and connectors will play a big role.
Whenit comes to getting from one place to another, current modes of transportation cover almost all environments, whether by land, sea, or air. Despite these vectors being conquered, numerous emerging technologies provide new options. One such method of transportation takes its inspiration from quadcopter drone technologies, which show extraordinary amounts of freedom, safety, and potential for automation.
Electric vertical takeoff and landing vehicles, or eVTOLs, can fly like common commercial drones, taking off and landing without requiring long airstrips. While drones typically have blades affixed to motors pointing directly upward, more modern eVTOLs can take advantage of movable engines
that allow for more forward thrust, thereby improving efficiency. Cables and connectors play a surprisingly important role in the viability of eVTOLs and their impact on overall mass. Knowing how the right connectors and cables will aid in design can help engineers create viable and sustainable eVTOLs.
Compared to helicopters, which are notoriously difficult to pilot, such vehicles are far easier to manage due to simplified controls. Additionally, the vast amount of software and hardware already developed to create autonomous drones means that eVTOLs are ripe for deploying autonomous flight systems, thus eliminating pilot error.
Most airspace above urban zones is virtually unused, so eVTOLs could move around at high speed, significantly
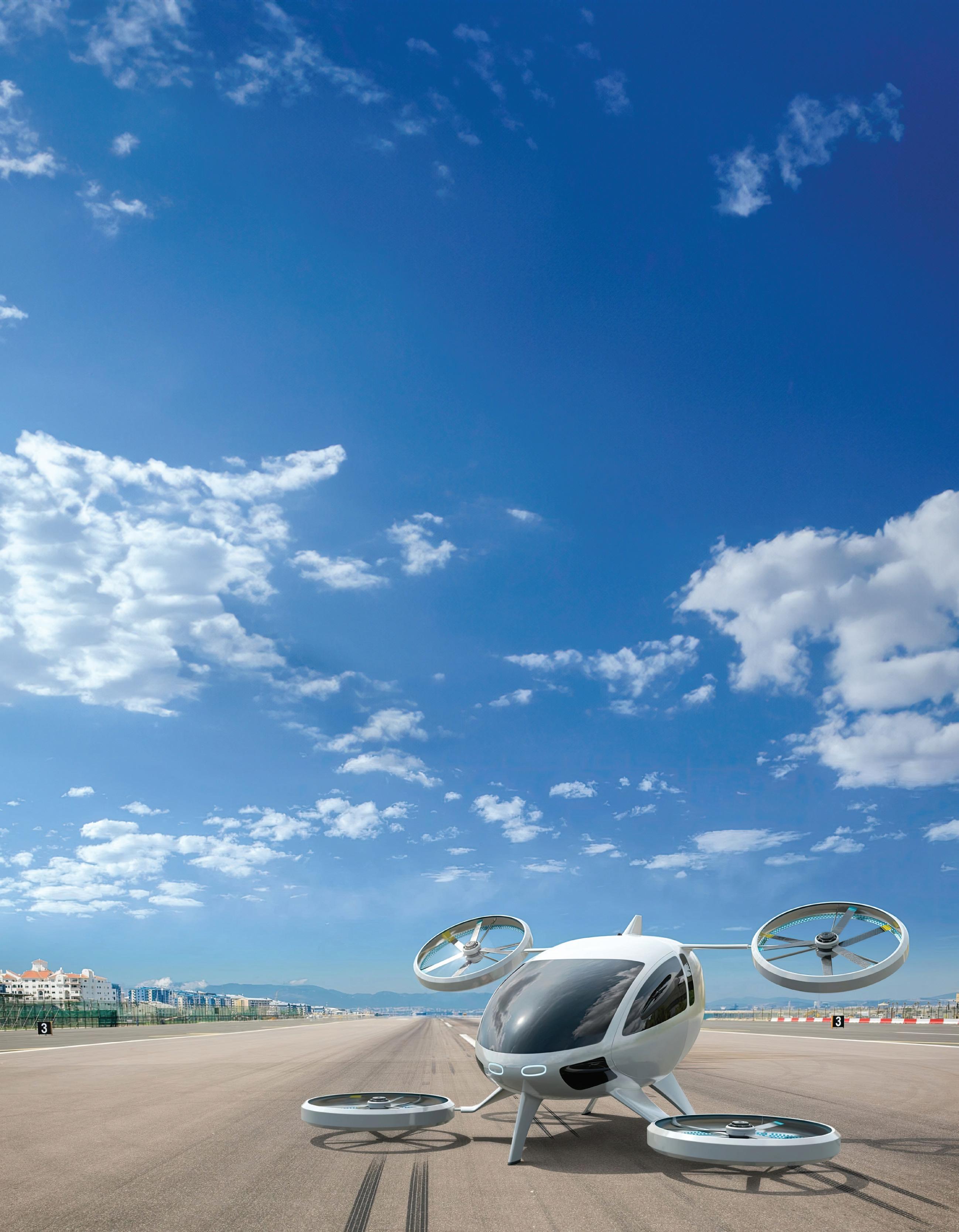
reducing transportation times between locations. Thus, eVTOLs could ferry people and cargo within urban environments, reducing road dependency and making highways more ideal for transporting heavy goods.
Bridges and tunnels can increase road and rail traffic capacity, but the massive infrastructure cost makes such projects hard to justify. eVTOLs would merely need landing pads and charging stations. This not only reduces costs for taxpayers but also lowers maintenance expenses, as roads will experience less traffic if pedestrians use eVTOLs.
While they offer many benefits, eVTOLs face many design challenges if they are to become an effective mode
of transportation. In this article, we’ll discuss these challenges while focusing on the interconnect design and its importance in the development of efficient and effective eVTOLs.
What challenges do eVTOLs face?
Despite all the advantages that eVTOLs present, they are still more of a concept than an actual solution that can be deployed in a commercial environment, and this reality comes down to numerous challenges that they face.
The first, and arguably the most critical factor, is weight. Because eVTOLs are entirely electric, they must carry hefty batteries. Compared to fossil fuels, batteries have far less energy density, meaning that any battery is far heavier than a tank of gasoline with the same energy capacity. For comparison, the energy density of gasoline is 47.5MJ/kg compared to lithium-ion batteries at 0.3MJ/kg.
Due to the need for heavy batteries, the rest of an eVTOL needs to be as light as possible. While modern materials such as carbon fiber can achieve this, they come at an added price and design complexity.
If eVTOLs become autonomous, communication between each eVTOL will be essential due to the severity of possible collisions. eVTOLs will need to be able to see the flight path of all other vehicles and plot a safe route accordingly. Such a network would need to handle vast amounts of data in real time with significantly reduced latency. According to researchers at KAUST, latencies down to 10 ms will be needed for autonomous flight control.
At a minimum, an eVTOL network would need to work on top of a 5G network, using edge computing to have data immediately routed to other vehicles (i.e., not pass through ISPs). However, integrating cellular communication systems and onboard artificial intelligence for autonomous flight introduces additional systems and components, further increasing weight and reducing the energy available to the craft for flight. Energy efficiency is of paramount importance, and designers must reduce the weight of any and every component. Depending on the size and complexity of the
High-density modular connectors like those in Cinch’s C-ENX series reduce the footprint and weight of RF, power, digital, and optical connections.
| Cinch Connectivity Solutions
vehicle, electronics typically account for 10-20% of an eVTOL’s total weight.
What’s the role of connectors and cables?
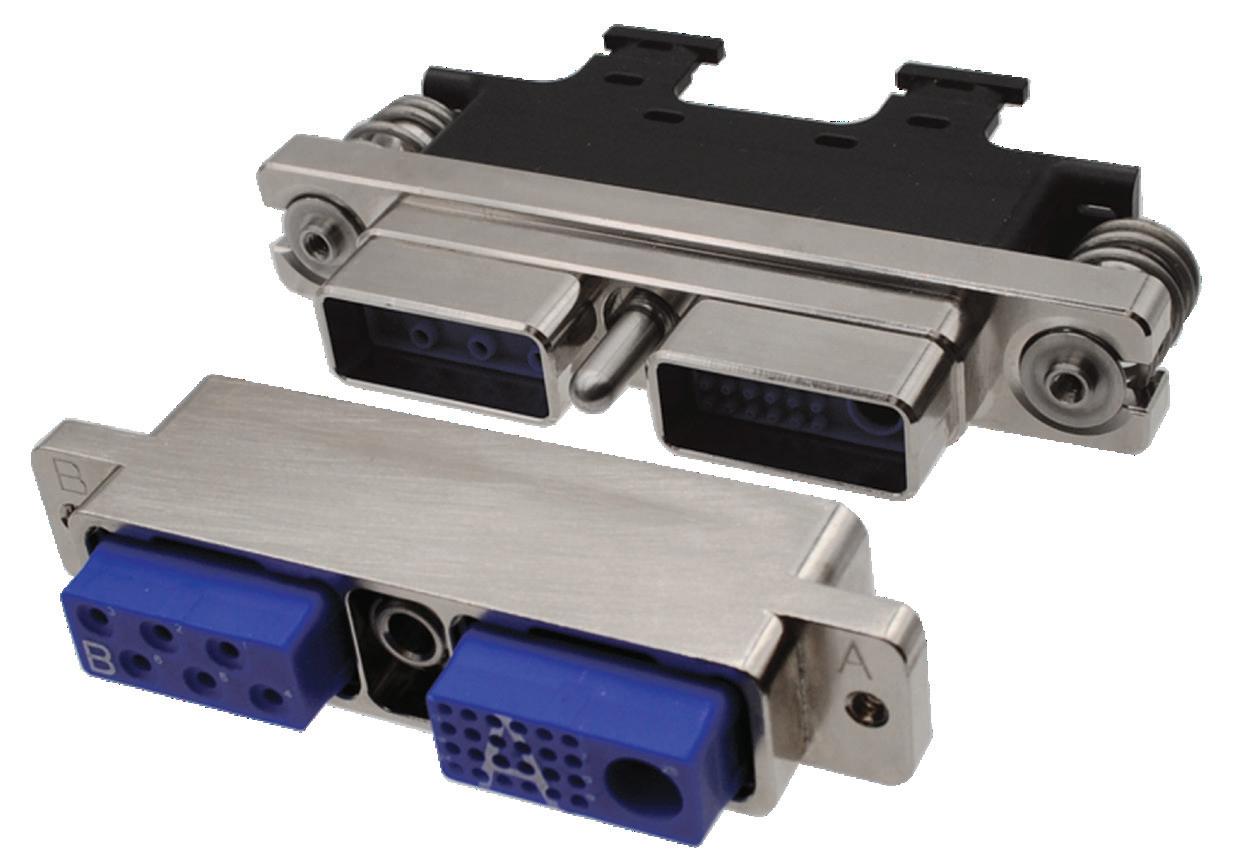
Cables and connectors may not seem as critical as other components in the design of eVTOLs, but their importance is quickly realized when exploring each aspect.
Connecting and powering the various eVTOL systems requires long cabling lengths, sometimes adding up to miles, which can account for a significant portion of the aircraft’s total weight. Power cables alone can account for close to 1% of the total weight of a 5,000-lb. craft. The signal and data cables further increase this number. Power cable weight is seen as such a significant weight contributor that aerospace engineers at NASA have studied how the design of power cables can be optimized to minimize weight.
Since eVTOLs are entirely based on electricity, electrical stress can be extremely high, with high voltages and currents present. This means that any cable and connector used to deliver power from the batteries to the motors needs to handle such power levels safely and have sufficient insulation to provide adequate protection, which tends to lead to large, bulky cables. Ensuring the optimal conductor and insulation materials can help limit power cables’ impact on overall weight. Many engineers designing eVTOLs opt for solutions commonly found in aviation platforms, including aluminum cables that are designed with these concerns in mind.
Whether high voltage or current is chosen, the final cable and connector choice must reduce weight as much as possible. Any extra weight in an eVTOL will increase the difficulty of takeoff and limit its range.
Such connectors must operate safely in extended temperature ranges while retaining a high IP rating to prevent damage during poor weather conditions. Consider, for example, the connectors found in the landing gear, rotary motors, antenna systems for GPS, and radar for eVTOLs. Most of these systems have some or much exposure to the environment. When landing in cities such as Dubai these connections may face weather conditions that include sandstorms, extreme temperature changes, sudden torrential rain, and high winds.
Finally, as all these connectors and cables are being used in an environment subjected to shock and vibration generated by motors and landing/ takeoff, any connector used must resist accidental disconnects over extended use. As such, simple screw terminals or clips will likely be insufficient, requiring locking nuts, press-fit connections, and unique mating mechanisms.
How can RF connectors help power the future of eVTOLs?
A wide range of compact RF connector styles and mounting options is available to satisfy the various RF needs of an EVTOL. This includes connectors down to 1.0 mm, which can operate at frequencies up to 110 GHz. This makes them suitable for all aviation tracking systems, including ADS-B and Pilot Aware. They can also be used with cellular systems, including 4G, 5G, and mmWave bands of 5G.
For designs that require communication speeds beyond copper’s capabilities, a range of optical connectors can help engineers achieve
extremely high inter-device speeds across the entire eVTOL and do so at significantly reduced weight due to the use of tiny fiber-option cables. Such cables are also immune to electromagnetic interference, making them far safer for use in autonomous environments where sensor data cannot be compromised.
Not all connectors can be replaced with RF or fiber optics. For such applications, micro-D connectors become invaluable. Their design allows for either shielded or unshielded cables to be used. In cases where EMI is not a concern, the absence of shielding can help reduce size, weight, and cost. Their specific D shape also makes them polarized. Compared to standard D-sub connectors, micro-D connectors are significantly lighter and take up to 80% less space while offering the same performance in the harshest environments.
Conclusion
While there is a lot of hype surrounding eVTOLs, they are still in their infancy, and any existing systems are more of a concept than an actual viable design that could be supported economically. The extreme technical challenges faced by eVTOLs and endless amounts of legislation present numerous roadblocks to engineers when trying to get such ideas to take off. However, the industry has growing confidence that the necessary infrastructure can be built and that technological roadblocks, such as battery density, will be overcome.
Scott Miller is the Director of Product Management at Cinch Connectivity Solutions. For much of his 25-plus-year career in electronic components, Scott has worked with manufacturers of interconnect devices for harsh environments.
Micro-D connectors can maintain secure connections under severe shock and vibration.
| Cinch Connectivity Solutions

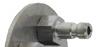


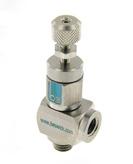

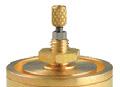
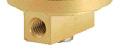
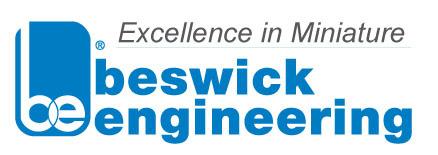

Introducing Harwin’s Gecko-MT, the compact yet powerful micro-miniature connector designed for demanding applications. Ideal for aerospace, defense, and other highreliability industries, Gecko-MT ensures robust performance even in the most challenging environments.
Key Features:
• Compact Size: Signal pins on a 1.25mm pitch reduce connector size
• Impressive power: 10A per contact power contacts
• High Reliability: Withstands extreme vibrations and temperatures, ensuring secure connections in harsh conditions
• Versatile Configurations: Available in a variety of mixed signal and power layouts
• EMI Shielding: EMI protection available with the inclusion of aluminum backshells for secure signal integrity
• Lightweight: Reduces overall system weight without compromising durability
Other useful features include jackscrews for secure mating, polarization features built into the housings and excellent outgassing properties.
For more information, visit harwin.com
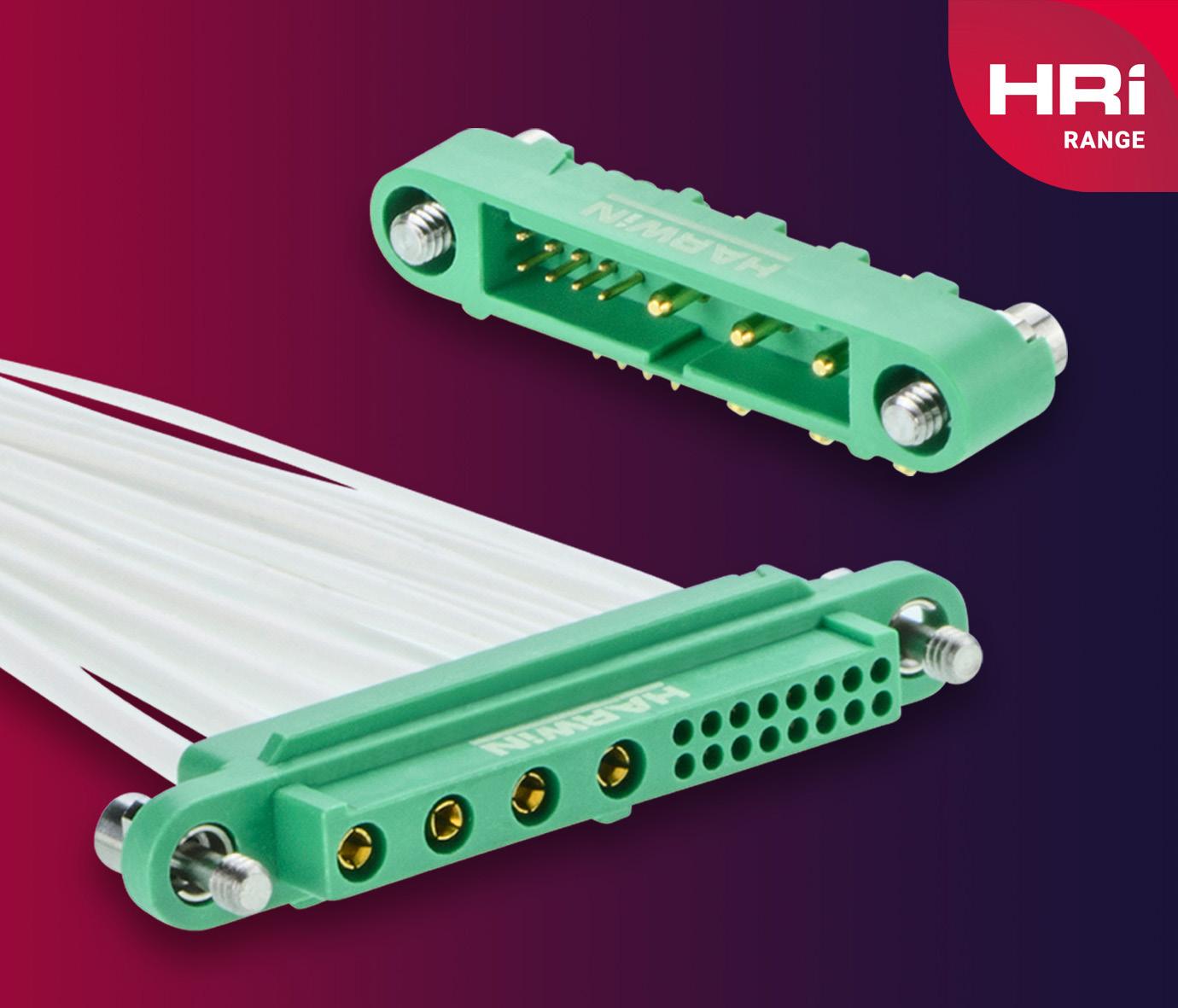
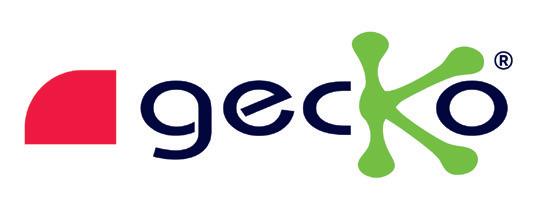
Reliable, high-performance drives for challenging environments
When it comes to drives systems for the aerospace industry, look to maxon for uncompromised quality, innovative technology, and thousands of flight hours. Our aim is to be the most reliable partner in the skies. Electric drive systems from maxon for the aerospace industry assist pilots in the cockpit and power drones, satellites, and rovers on Mars.
maxon’s products have been developed for the most demanding of applications and satisfy the strictest environmental, quality, and regulatory requirements. Offering specific assembly solutions for linear actuators to expand the boundaries for challenging environments, and demanding applications such as speed and weight. Features include:
• Wide range of seals, IP54 to IP66
• Corrosion resistance
• Temperature resistance from -40 °C to +95 °C
• Resistance to vibration/shocks
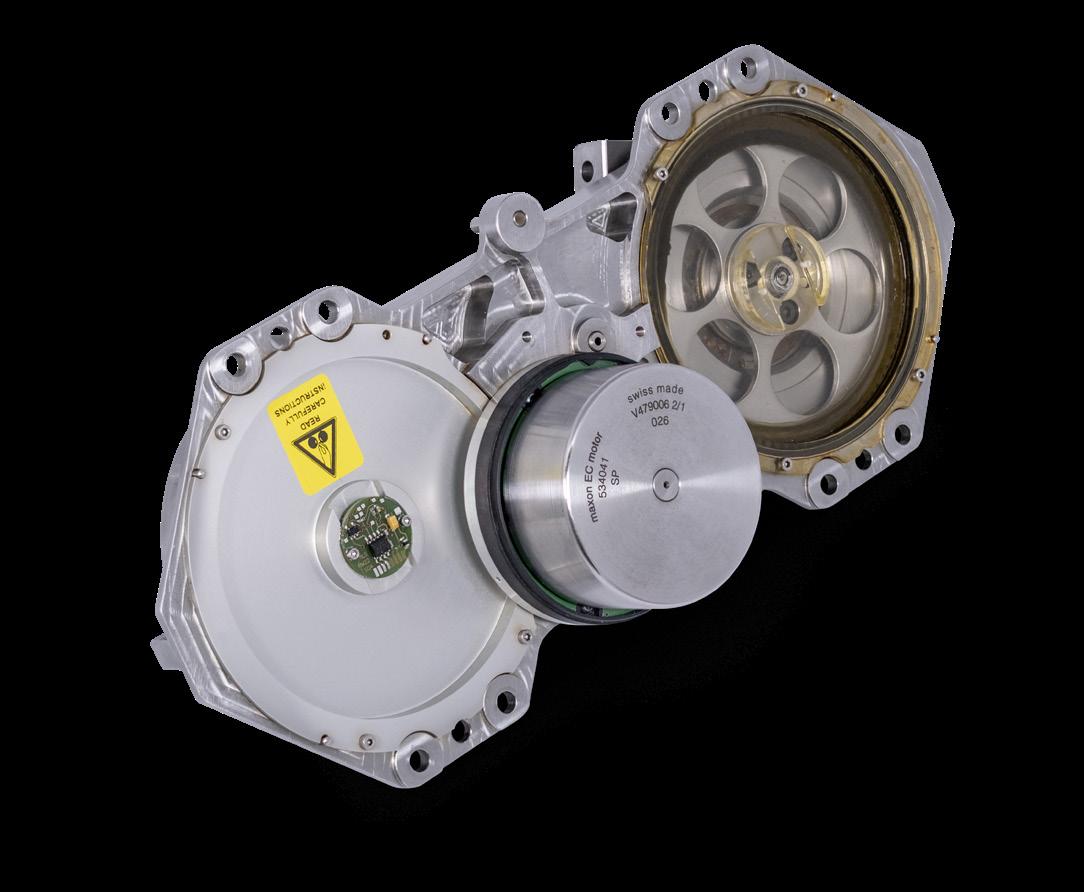

maxon
125 Dever Drive Taunton, MA 02780 www.maxongroup.us 508-677-0520