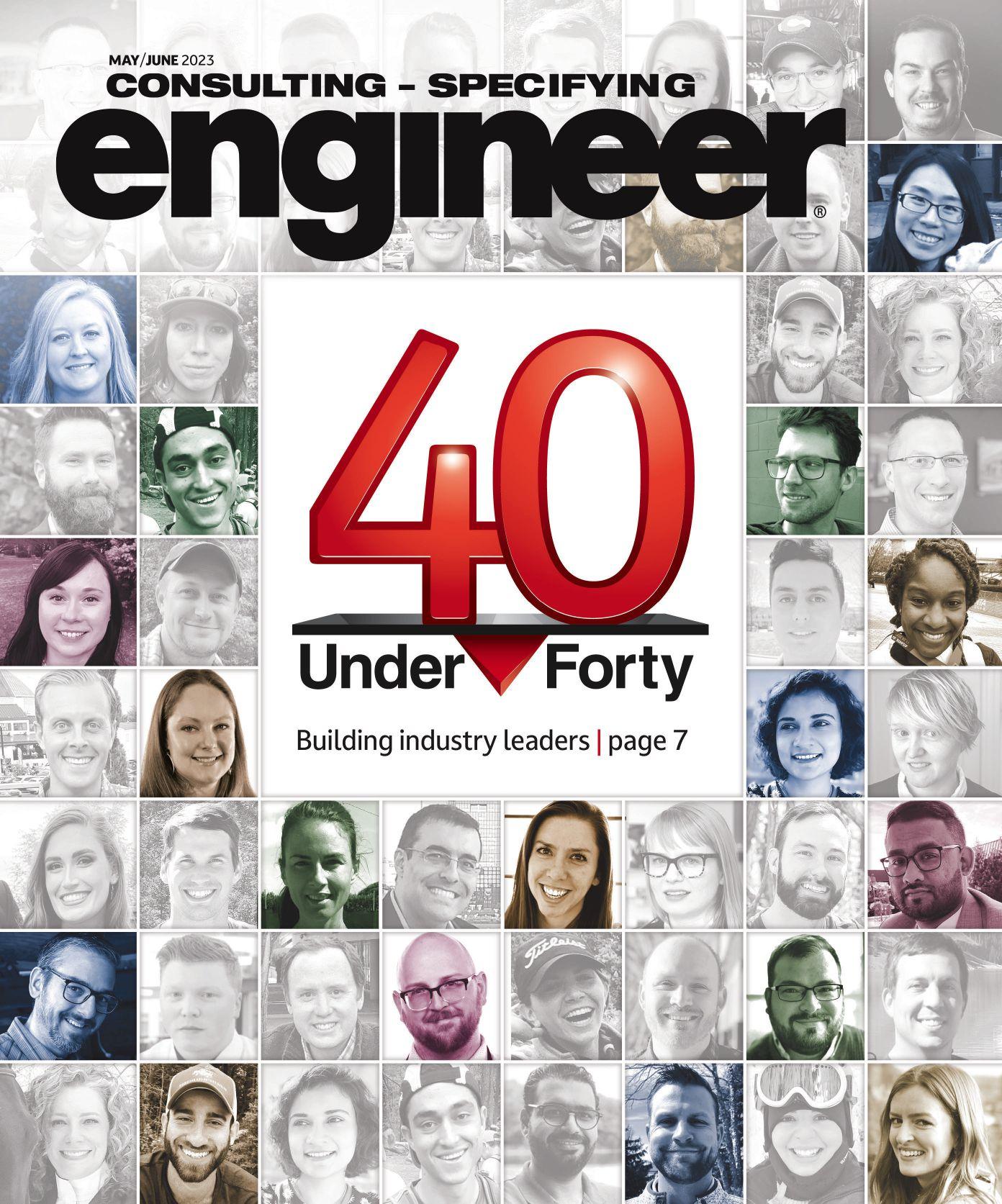
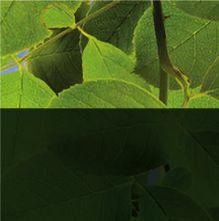
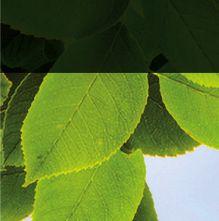
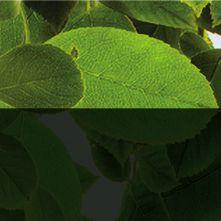
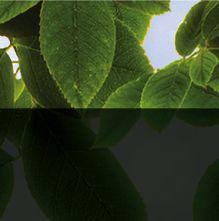
According to the World Green Building Council, we spend 90 percent of our time indoors. Given that statistic, it’s clear the quality of the air we breathe in buildings can dramatically impact our health and well-being. At Reliable Controls we believe sustainable buildings are a key component to reducing the health and environmental impacts of indoor and outdoor air pollution.
Learn more reliablecontrols.com/IAQ
Delivering more flexibility and power in less space!
Get the ultimate in comfort integration with a high-capacity unified platform, for commercial and light commercial applications.
• Expanded outdoor unit capacity, from 6 to 36 Ton
• Larger single module outdoor units – up to 16 Ton
• Up to 26% less space with larger single module outdoor units
• Both Heat Pump and Heat Recovery operation available from one unit
• Increased number of connectable indoor units
• Extended ambient air temperature operating range from -15°F to 126°F
• Intelligent refrigerant control optimizes individual zone comfort
Unified VRF outdoor units allow for heat pump or heat recovery operation for the ultimate in application flexibility.
When your data is critical so is the motor you choose
Baldor-Reliance ® Critical Cooling motors are designed to reliably increase uptime and decrease maintenance of critical HVAC applications in data centers, hospitals, and commercial and industrial buildings.
Courtesy: CFE Media and Technology
The building industry
It
As health care projects become more patient oriented, human-centric lighting design and lighting controls are taking center stage
| Learn the pros and cons of centralized and decentralized generator systems
Centralized, remote and distributed standby generator designs are all options for power systems. Which one is best?
60 | What do you need to know about designing data centers? Will data centers get larger? More efficient? Use less water? Learn about the trends here
AMARA ROZGUS, Editor-in-Chief/Content Strategy Leader ARozgus@CFEMedia.com
CHRIS VAVRA, Web Content Manager CVavra@CFEMedia.com
AMANDA PELLICCIONE, Director of Research APelliccione@CFEMedia.com
MICHAEL SMITH, Creative Director MSmith@CFEmedia.com
DARREN BRUCE, PE, LEED AP BD+C, Director of Strategic Planning, Mid-Atlantic Region, NV5, Arlington, Va.
MICHAEL CHOW, PE, CEM, CXA, LEED AP BD+C, Principal, Metro CD Engineering LLC, Columbus, Ohio
TOM DIVINE, PE, Senior Electrical Engineer, Johnston, LLC, Houston
CORY DUGGIN, PE, LEED AP BD+C, BEMP, Energy Modeling Wizard, TLC Engineering Solutions, Brentwood, Tenn.
ROBERT J. GARRA JR., PE, CDT, Vice President, Electrical Engineer, CannonDesign, Grand Island, N.Y.
JASON GERKE, PE, LEED AP BD+C, CXA, Mechanical Engineer, GRAEF, Milwaukee
JOSHUA D. GREENE, PE, Associate Principal, Simpson Gumpertz & Heger, Waltham, Mass.
RAYMOND GRILL, PE, FSFPE, LEED AP, Principal, Ray Grill Consulting, PLLC, Clifton, Va.
DANNA JENSEN, PE, LEED AP BD+C, Principal, Certus, Carrollton, Texas
WILLIAM KOFFEL, PE, FSFPE, President, Koffel Associates Inc., Columbia, Md.
WILLIAM KOSIK, PE, CEM, LEED AP BD+C, BEMP, Senior Energy Engineer, Oak Park Ill.
KENNETH KUTSMEDA, PE, LEED AP, Engineering Manager, Jacobs, Philadelphia
JULIANNE LAUE, PE, LEED AP BD+C, BEMP, Director of Building Performance, Mortenson, Minneapolis
DAVID LOWREY, Chief Fire Marshal, Boulder (Colo.) Fire Rescue
JASON MAJERUS, PE, CEM, LEED AP, Principal, DLR Group, Cleveland
BRIAN MARTIN, PE, Senior Electrical Technologist, Jacobs, Portland, Ore.
BEN OLEJNICZAK, PE, Senior Project Engineer, Mechanical, ESD, Chicago
GREGORY QUINN, PE, NCEES, LEED AP, Principal, Health Care Market Leader, Affiliated Engineers Inc., Madison, Wis.
BRIAN A. RENER, PE, LEED AP, Principal, Electrical Discipline Leader, SmithGroup, Chicago
SUNONDO ROY, PE, LEED AP, Director, Design Group, Romeoville, Ill.
JONATHAN SAJDAK, PE, Senior Associate/Fire Protection Engineer, Page, Houston
RANDY SCHRECENGOST, PE, CEM, Austin Operations Group Manager/Senior Mechanical Engineer, Stanley Consultants, Austin, Texas
MATT SHORT, PE, Project Manager/Mechanical Engineer, Smith Seckman Reid, Houston
MARIO VECCHIARELLO, PE, CEM, GBE, Senior Vice President, CDM Smith Inc., Boston
RICHARD VEDVIK, PE, Senior Electrical Engineer and Acoustics Engineer, IMEG Corp., Rock Island, Ill.
TOBY WHITE, PE, LEED AP, Associate, Boston Fire & Life Safety Leader, Arup, Boston
APRIL WOODS, PE, LEED AP BD+C, Vice President, WSP USA, Orlando, Fla.
JOHN YOON, PE, LEED AP ID+C, Lead Electrical Engineer, McGuire Engineers Inc., Chicago
Can being competitive in the workplace be just as beneficial as being competitive in sports?
Athletic competition and professional workplace competition share a lot of similarities. I was reminded of that recently while competing in a team athletic competition.
In both cases, the goal is to come out on top and achieve success through hard work, dedication and skill. Whether it's on the field or in the office, competition pushes people to be their best selves and strive for excellence.
Amara Rozgus, Editor-in-Chief
Just like in sports, being competitive in the building engineering field can help you win awards and accolades. Companies often have performance metrics in place and those who excel in their roles are often recognized with bonuses, promotions or other rewards. The same goes for athletics, where top performers are celebrated with awards, medals and recognition from their peers.
One of the most important aspects of competition is the drive to improve. In sports, athletes are constantly training, refining their skills and seeking new ways to get faster or stronger. The same is true for professionals who want to succeed in their careers. They are always looking for ways to improve their skills and knowledge, whether it's through on-the-job experience, additional degrees or continuing education.
Perhaps the most significant similarity is the importance of mental toughness. Athletes need to be mentally strong to perform at their best and the same is true for professionals. Whether it's dealing with pressure, overcoming obstacles or pushing through a difficult engineering project, mental toughness is essential for success in both athletics and the workplace. Being competitive in the workplace can also help you stand out from the crowd. Engineering firms are always looking for employees who are dedicated, hardworking and willing to go the extra mile. By being competitive and striving for excellence, you can demonstrate these qualities to your employer and increase your chances of being recognized for your contributions.
This content was enhanced with ChatGPT. Due to the limitations of AI tools, all content was edited and reviewed by our content team. cse
Look familiar?
If your power infrastructure includes renewables, battery storage and/or EV charging, a microgrid may be the missing piece you need to bring it all together.
At the heart of such a system is an intelligent microgrid controller that maintains overall system stability and dynamically manages
generating assets and loads to optimize power flow based on user-defined goals.
Eaton’s Power Xpert microgrid solutions provide reliable power that delivers operational resilience, minimizes carbon emissions and reduces energy costs.
To learn more go to: Eaton.com/microgrid
It brings us great pride to sponsor Consulting-Specifying Engineer’s 2023 40 Under 40 program, recognizing the most talented young individuals across the engineering community. Your dedication and ingenuity in providing designs incorporating environmental, economic, and sustainable solutions will electrify all industries in building a better tomorrow.
It is both an exciting and challenging time to be an engineer. Our building systems are being revolutionized by integrating new digital and sustainable technologies, fueled by some of the largest US infrastructure investments in decades. With all of these opportunities for growth also comes a need for more educational resources, online tools, and creative design approaches to help navigate the challenges associated with today’s construction projects. These 40 Under 40 winners have embraced these challenges and clearly demonstrate that the future of engineering is in great hands.
At Eaton, we are committed to supporting this building revolution and your needs along the way. We will continue to develop industry-led training and educational programs to provide you with technical know-how needed to navigate this rapidly changing industry. We will continue introducing new products and technologies that raise the bar on safety, ef ciency, intelligence, and sustainability. And, we will be here to support you in building the very foundation the world relies on.
On behalf of everyone at Eaton, I congratulate the winners on this signi cant recognition and cannot wait to see your leadership in action as you continue to revolutionize the engineering industry.
Chris M. Finen, P.E. Manager, National Application Engineers Eaton
Rebecca Birmingham....... 10
Martina Botturi............ 10
Carrie Cremin 10
Bryan Derr 10
Zara Fahim................ 11
Ari Greenberg ............. 11
Miles Grubbs.............. 11
Andy Guthrie.............. 11
Doug Heineke 12
Qini Meko Huang 12
Amir Ibraheem 12
Kevin Jayne ............... 12
Tyler Kelleher ............. 13
Britt Kern 13
Laura Maddux............. 13
Jerry Manavalan........... 13
Thomas Martin 14
Roger Maybrier............ 14
Danny McGrail ............ 14
Brendan McGrath.......... 14
William McGugan.......... 15
Courtney Myers 15
Ian O'Connor 15
Benjamin Olejniczak........ 15
Erin Popa ................. 16
Aric Reed ................. 16
Emily Royal 16
Mehran Salehi............. 16
Corey Sanders............. 17
Michael Scott ............. 17
Kristen Spina.............. 17
Gavin Stewart ............. 17
Michael Stewart 18
Kori Terray 18
Steve Torre................ 18
Usha Tyson................ 18
Catie VanWormer.......... 19
Giselle Villar .............. 19
Kiersten Washle 19
Mark Wassif 19
DAVID
SWhat makes a 40 Under 40 winner? Determination, ambition and a lot of creativity
everal of the 2023 40 Under 40 award winners knew from a young age that they’d make a difference, though not necessarily how. Now they’re expert engineers, designers of complex systems, industry leaders and community supporters. They share technical knowledge with work colleagues and at professional events. They play a role in the direction of their firm’s progress, with an eye toward sustainability. They are also competitive athletes, nature enthusiasts, keen musicians or music lovers and eager travelers. To sum it up, they are all dedicated to making a difference.
Ventures Lead; IP + Digital Counsel, Arup; JD, Brooklyn Law School
How can great ideas be scaled to positively influence the built environment? For some insight, look at Birmingham’s career. Birmingham is the Ventures lead for the Americas region for global sustainable development consultancy Arup, as well as intellectual property and digital counsel in its New York office. She helps Arup and its collaborators realize the potential of innovation to improve the built environment. Graduating from New York University’s Gallatin School with a degree in interdisciplinary studies, Birmingham’s focus was on how technology advances influence the perception of art and architecture. At Brooklyn Law School, Birmingham studied intellectual property law, including built environment and art law. Birmingham joined Arup in 2018 to build upon its legacy of innovation with a scalable commercial lens. She helped develop the Americas region strategy for Ventures, Arup’s in-house ideation, incubation and acceleration program. A major part of her role as Ventures lead is supporting external collaborations, understanding how to solve critical challenges and finding ways to influence the built environment alongside others. Birmingham’s leadership roles also give her the opportunity to help guide internal training efforts and initiatives, ensuring Arup members are engaged in the firm’s goal of digital transformation. Away from work, Birmingham is a music historian and record collector, with an emphasis on midcentury recordings. She occasionally DJs at events around the world. Birmingham also enjoys a good tapas crawl, true to her Catalunya roots.
Principal, AKF; BS, Mechanical Engineering, Cooper Union
Associate Principal, Electrical Designer, BR+A; MS, Engineering and Architecture, Sapienza University of Rome
After graduating summa cum laude from the Sapienza University of Rome in her home country, Botturi moved to U.S. at age 26 where she joined BR+A to focus on designing proton therapy centers. Throughout her 10 years at BR+A, Botturi's expertise as electrical engineer has led to the successful completion of more than 30 proton therapy facilities in the U.S., Asia, Europe and Africa. Her work includes the Mayo Clinic Proton Therapy Building in Jacksonville, the Australian Bragg Centre for Proton Therapy and Research in Adelaide and Clinica Universidad de Navarra Proton Center in Madrid. Botturi has presented at the National Association for Proton Therapy national conference and is well-regarded in her field. She is hands-on during construction and highly communicative during the design phase. Her in-depth knowledge of proton and particle therapy combined with her ability to communicate effectively with clients and partners all over the world are her strong suits. Her colleagues say it is Botturi's ability to work with global teams, understand cultural sensitivities and reconcile differences when professional challenges occur that have been an invaluable asset in bringing these projects to completion. Botturi recently relocated to California to establish BR+A's presence on the West Coast. Outside of work, Martina maintains a strong connection with her family and friends in Italy, where she visits annually. She prioritizes a healthy lifestyle, enjoying tennis, biking and spending quality time with her husband and two children. Traveling is her favorite pastime and Amsterdam her favorite place to bike.
s a principal, Cremin plays a key leadership role at AKF and has been integral to the firm’s success. She is an experienced, trusted project manager and plumbing engineer with a focus in the health care sector. She works personally with clients and the design team to achieve solutions. She has presented on her COVID-19 emergency efforts, her experience responding to the need for expedited field hospital design and with adapting existing HVAC and plumbing systems to meet patient requirements. Cremin is a proactive, take-charge professional who is highly regarded as an excellent communicator and team leader. Her meticulous attention to detail and project management skills make her sought after on some of the firm’s most demanding projects. Recognized by industry professionals and her peers as a leader in engineering design, Cremin served a two-year term as president of the American Society of Sanitary Engineering New York Chapter. She also serves on the board of directors of the Salvadori Center, an organization dedicated to teaching science, technology, engineering, arts/architecture and math to K-12 students through a collaborative, project-based approach that uses the built environment. Cremin is a passionate mentor to younger engineers and students thinking of pursuing a career in the architecture, engineering or construction industry. Outside of her work at AKF, Cremin is an avid world traveler. Some of her most memorable trips include cave snorkeling in Tulum, Mexico, hiking the highlands of Scotland and seeing the northern lights from the Blue Lagoon in Grindavik, Iceland.
Principal, Coffman Engineers; BS, Fire Protection Engineer, University of Maryland
The architecture, engineering and construction teammates Derr collaborates with share that, although he is an excellent engineer with a robust client following, they most value his professional contributions. At work, Derr was instrumental in development of the Coffman Washington, D.C., metro office, which started with three staff members in 2017 and has grown to 17. Since leaving his alma mater, Derr has continued his association with the University of Maryland, being instrumental in the development of an entrepreneurial course and serving as an industry resource to the faculty. Derr gives back to the fire protection community through his involvement with the Society of Fire Protection Engineers. He also serves as the main point of contact for Coffman when recruiting new fire protection engineers from various universities. In that role, he delivers presentations to students on an introduction to engineering and consulting, maintaining work/life balance, technical issues and provides mentorship to rising engineers. Derr has also been active in the Design Build Institute of America and the Society of American Military Engineers, attending conferences, meetings and social events. In recognition of his dedication and contributions, Derr was selected as a partner in Coffman, which is a high bar to reach — especially at his age. Both at work and outside of work, Derr finds himself always looking for competition. That sense of competition was likely derived by being the youngest of three active boys. He and his brothers grew up to be fire protection engineers working at three separate organizations. Outside of work his competitive nature is primarily exercised on the golf course.
Senior Energy Engineer, Arup; MS, Mechanical Engineering, University of Illinois at Urbana-Champaign
Acore member of Arup’s energy team, Fahim is responsible for energy and sustainability consulting for a range of complex projects across the commercial property, public utility, education and other key sectors. Having joined the firm in 2008, Fahim has more than a decade of experience providing services for decarbonization, energy feasibility studies on microgrids, campus utility masterplans, cogeneration plants and solar projects. Equipped with the knowledge of mechanical systems design, she enjoys the diversity of projects she works on. As an advocate for equitable decarbonization, Fahim’s focus is on existing building projects ranging from retro-commissioning, energy auditing, decarbonization studies, commissioning, LEED, microgrid feasibility studies, campus masterplans and post-occupancy assessments of buildings. Digitally focused, she is proficient at energy modeling in software like IES, Trane Trace, EnergyPro and eQUEST. Fahim is also interested in net zero design and decarbonization strategies and supports the use and development of in-house and external tools to streamline her work and processes on these types of projects. She has lectured and delivered presentations on a range of subjects including sustainability, net zero energy and carbon neutral design. In her free time, Fahim loves cooking and hosting friends and family. She often cooks traditional Pakistani cuisine, but also enjoys trying foods of all kinds. She engages in various activities such as hiking, sightseeing and almost anything involving nature. Fahim also is an avid traveler and is looking forward to taking international trips with her family.
Lead Mechanical Engineer, Little Diversified Architectural Consulting Inc.; BS, Mechanical Engineering, North Carolina State University
Senior Associate, HVAC & Sustainable Design, BR+A; BSE, Mechanical Engineering, Princeton University
St work, colleagues and clients say Grubbs is recognized as a knowledgeable resource, mentor and thought leader. With a decadeplus design experience, Grubbs understands how a building environment impacts occupants, writing publications on sustainability and engineering topics. He co-wrote an article on COVID-19 and presented on the same topic at industry conferences, including PENC, USGBC Carolinas, the Building Performance Analysis Conference and the AIA Research Triangle Building Enclosure Council. Leading the Durham mechanical engineering practice, Grubbs has given numerous firmwide presentations on engineering basics, along with many “Revit 411” recurring training seminars. Grubbs serves as the vice chair for the Town of Cary Environmental Development Committee. He’s also an active member of Little’s sustainability steering committee, Sustain@Little. He was named an associate in 2018 and senior associate in 2021. His projects have been recognized within several prestigious awards programs including from AIA, Design Build Institute of America, Learning by Design, ASID, USGBC and CoreNet Carolinas. When not at work, Grubbs can be found at home, likely cooking and trying to entice his 5-year-old into adventuresome eating. Lately, he has been trying his hand at vegan and vegetarian cooking. On weekends, Grubbs enjoys cycling. Most of his rides end with a beer from a local brewery. However, his competitive side really comes out when playing a board game or table-top role-playing game with friends.
ince he was 12, Greenberg has been in love with buildings. Growing up in a family-run residential construction company, he worked summers and got his hands dirty. Fast-forward to now and Greenberg serves as an integrated member of the HVAC design and sustainability consulting teams at BR+A. A graduate of Princeton University, Greenberg holds a bachelor’s in mechanical engineering with a certificate in sustainable energy. His work focuses on efficiency and electrification for hard-to-heat and high-energy buildings in the health care, research, commercial and institutional sectors. Greenberg is the primary project manager for various deep energy design projects, including net zero buildings and master plans. He also leads energy efficiency and electrification efforts for dozens of projects, delivering analysis and educating designers and clients. His technical expertise includes HVAC design, energy modeling, life cycle cost analysis and system optimization. In addition to his design and consulting duties, Greenberg’s role at BR+A includes teaching both internally and externally. He provides dynamic in-person and online training sessions on topics including electrification, energy codes, sustainability trends and more. As an outdoorsman, Greenberg’s passion for sustainability is more than just professional. His time in nature during his off-the-clock hours has motivated him to promote technologies that will help preserve the environment. When he isn’t working, Greenberg can be found backpacking with his wife and dog, renovating their 1950s fixer-upper or wrenching on his 1973 Volkswagen Beetle.
Associate, Acoustic and Audiovisual Consulting, Arup; Ph.D., Architectural Acoustics, Rensselaer Polytechnic Institute
Guthrie is a part of Arup’s Technical Services portfolio, applying the latest technologies in acoustics and audiovisual (AV) design across complex projects within health care, transit, education and arts and culture. Having joined Arup in 2009, Guthrie is a leader on the AV and acoustic teams, where they leverage their background in analysis and mitigation of structure-borne noise and vibration; room acoustics and sound isolation design for performing arts centers; AV systems for higher education, corporate and aviation; and sound art projects. Since joining the firm, Guthrie has been a contributor to the development and improvement of Arup SoundLab standards across the United States. They contributed to the implementation of a wave field synthesis system and a higher-resolution spatial audio protocol that allows for a more immersive sonic experience based on more informed design decisions. Guthrie has represented Arup at industry conferences including the Audiovisual and Integrated Experience Association, the Acoustical Society of America, the International Symposium on Room Acoustics and the Institute of Acoustics. Guthrie is a classically trained French horn player and composer active in San Francisco’s contemporary music scene. Given the varied interests and skills both within and outside work, Guthrie thrives as a creative and resourceful leader, insightful and committed to mentoring others while striving to develop the most efficient solutions. Working at the intersection of technical sound design and art, Guthrie makes an impact on the built environment. Guthrie identifies as nonbinary and enjoys going for hikes and camping with their 6-year-old.
Senior Project Manager, Mott MacDonald; BA, Communications, University of Massachusetts, Amherst
Heineke’s background in communications has led him to develop an inherently practical approach to project management. Over the course of his 13-year tenure at Mott MacDonald, Heineke has managed a diverse collection of projects across the fields of education, transportation, construction and digital technologies. He has an excellent track record of delivering successful and profitable projects and has played a key role in developing business and collaborative working relationships with clients, partners and associates. Heineke’s recent Boston-area transit projects include major construction at a vehicle maintenance facility, traction power upgrades design and various station improvements projects. He is recognized for his interpersonal skills and emotional intelligence, having managed and mentored staff and fosters a pragmatic and empathetic approach to working collaboratively with colleagues, whether as a leader or a team member. Heineke obtained his Project Management Professional certification in 2019 and always endeavors to broaden his knowledge and enhance his personal effectiveness by learning from colleagues and maintaining a growth mindset. His curiosity also extends outside of work. He and his wife are avid hikers and recently became members of the Massachusetts Audubon Society, which protects more than 100 wildlife sanctuaries across the state — weekend plans in the Heineke household invariably include a jaunt to at least one Audubon spot. He is also a keen acoustic guitar player with a penchant for mahogany Martins.
Senior Project Engineer – Mechanical, Mott MacDonald; BS, Mechanical Systems, Faculty of Engineering, Cairo University
Ibraheem has experience in the technical aspects and management of complex multidisciplinary projects, with emphasis on underground construction and mechanical, fire/ life safety and tunnel ventilation systems design. He has also been involved in the design and development of technical specifications for mechanical, fire/life safety and tunnel ventilation projects from schematic design through construction document phases. Recent projects include a $3.5 billion expansion for a line on Boston’s public transportation system, in which he managed complex mechanical systems/design. Ibraheem co-chairs the mechanical standard committee for Mott MacDonald’s FEL department and provides technical support to various corporate steering group sub-committees. One of Ibraheem’s roles leading the mechanical standard committee is to provide a standard practice to the company’s mechanical engineers, helping deliver high quality and consistent submissions to clients. He also mentors younger staff to help them become a valuable asset to the company. For example, he gave a presentation to team members on fundamentals of acoustics to assist with ongoing education. His can-do, positive attitude has earned him companywide accolades and awards. Ibraheem was able to bring an innovation tool to lead the team to create a digital solution for asset management. The digital solution enabled colleagues to perform accurate data collection and asset inspections in any environment. In his free time, Ibraheem enjoys spending time with his wife and his two children, as well as traveling around the world. He especially appreciates snorkeling and fishing, two of his favorite activities.
Senior Lighting Designer, Arcadis IBI Group; University Bachelor, Computer Science, Navy Commanders Academy of People's Liberation Army of China
Huang lives and breathes lighting design both on and off the clock. Known by friends and family for critiquing the lighting at hotels, shopping malls and just about anywhere else she sets foot, Huang has more than 15 years of passionate experience in lighting design and management for projects within Canada and internationally. Her work serves a broad range of industries, including architecture, transportation, infrastructure, hospitality, entertainment, manufacturing and landscaping. Holding a degree in computer science, Huang brings technical expertise as well as strong aesthetic sensibilities to her role. Major projects she has worked on include exterior lighting for the Toronto Pearson International Airport and the Lady Gaga Coachella Valley Music and Arts Festival in 2017. In addition, she volunteers with the membership committee of the International Association of Lighting Designers and is on the lighting control and transportation committee of the Illuminating Engineering Society. According to her friends and colleagues, Huang is personable and community-oriented. At Arcadis, she has organized “lunch and fun” groups to cultivate stronger relationships between co-workers and maintains involvement in neighborhood municipal affairs near her residence. Outside of work, Huang is a lighting designer and DJ for musical events. In addition, skiing and yoga are her great passions. Remarking on the difference between the two activities, Huang says that life needs a balance of fast and slow, up and down, bitter and sweet experiences.
Project Manager, Affiliated Engineers Inc.; BS, Mechanical Engineering, University of Wisconsin-Madison
Jayne began his career with AEI promptly after graduating college and quickly narrowed his focus to the health care market. As a member of AEI’s mechanical engineering team, he evaluates all relevant project information to establish design criteria for complex building projects. Over time, his expertise led to advancing his career to both a senior position within AEI and founding member of AEI’s Denver office. He actively promotes progressive and innovative health care design strategies at greenfield site hospitals up and down the Colorado Front Range. According to his peers, Jayne’s ability to balance technical knowledge with soft skills consistently allows him to manage and exceed client expectations. Moreover, his genuine desire to understand problems and develop innovative long-term solutions allows him to balance his clients’ best interests against project limitations, budgets and other challenges. Most notably, Jayne’s peers say his compassion makes him an exemplary individual and role model for younger professionals. Since arriving in Denver, he has participated in community outreach through ongoing contributions to Denver Extreme Community Makeover, which undertakes projects such as graffiti removal, landscaping, painting and yard work; and Food for Thought Denver, which seeks to addresses food insecurity for local schoolchildren. In his free time, Jayne enjoys golf, skiing and music, especially with his two sons. He took many years of piano lessons in his youth and continues to play guitar. He met his wife in their high school band class and music remains a steady constant in their household since.
Senior Associate, Electrical Engineer, BR+A Consulting Engineers; MS, Architecture, Wentworth Institute of Technology
Though his degrees came in architecture, Kelleher found his passion for electrical design with the niche work done at BR+A Consulting Engineers in the life science and health care design fields. Kelleher has worked at BR+A for 11 years in a full-time capacity; he also worked for the firm for two years as an intern during college. With his background in architecture, it provided a bridge to client relations with many former classmates and teachers working at Boston architecture firms where those connections opened doors to grow more relationships at those companies. Kelleher continues his work with Wentworth Institute of Technology by leading the co-op recruitment for BR+A for electrical interns. He believes it is important to continue to find the next great designers and help students discover this field of electrical engineering. Besides recruiting from Wentworth, he has established recruiting at other local colleges and colleges outside of New England. Kelleher is proud to say that several people were first hired by him as co-ops who then went on to become full-time employees. Kelleher knows how important mentors are; he started out working on markups being mentored from more senior designers at BR+A. Within the past few years, he has begun leading the electrical design on projects and mentoring a team that works on these projects under his guidance. With this expanded role, Kelleher was recently promoted to a senior associate. When he isn’t working, Kelleher enjoys photography and taking walks around Boston, trying to capture moments and the architecture that makes this city a beautiful place to call home.
Electrical Department Facilitator, Affiliated Engineers
Inc.; BS, Electrical Engineering, Texas A&M University
Senior Mechanical Engineer, GPI; MA, Architectural Engineering, Pennsylvania State University
Kern began his career at META as a summer intern in 2011 and quickly rose through the ranks to become a project manager and technical lead in the mechanical department. Kern’s former duties at Bala | META included numerous interactions with clients including proposal writing, facility assessment, basis of design documentation, construction documentation, bidding assistance and construction administration. He has been a member of ASHRAE since his senior year in college and frequently attends industry events. He is also an avid public speaker, giving presentations on indoor grow facilities for medical cannabis. As a designer, he tries to think outside the box and seeks to keep sustainability and responsible stewardship of the environment in mind when working on projects. According to his peers, he is a natural born leader whose calm and confident approach helps draw others toward him. Many of Bala | META’s younger engineers enjoyed receiving help from Kern because of his approachability and constructive teaching methods. He is also involved in community service outside his industry role. Last year, he volunteered to build flower beds for a farm to promote the health of the local honeybee population. In addition, during COVID-19, he regularly grocery-shopped for his elderly, high-risk neighbor. Although busy, Kern still finds time to enjoy an active lifestyle outside the office. Over the past 11.5 years, he has competed in 35 registered marathons and ultras, including the 100-mile C&O Canal race. In addition to his endurance pursuits, he also dabbles in playing music and is an avid chess player.
addux is an electrical engineer who contributes to designs, performs condition assessments and completes inspections of complex electrical, lighting and fire alarm systems. Specializing in the design of low- and medium-voltage distribution, she is well-versed in electrical power systems, including emergency power, uninterrupted power sources, lighting and fire alarm. Her project work encompasses markets such as health care, science and technology with an emphasis on laboratories, higher education and government. With a love for math and passion for understanding how things work, Maddux knew she wanted to be an engineer from a young age. Her interest in circuits and electricity made electrical engineering a natural fit. After she graduated from Texas A&M University, she started off managing smaller-scale health care projects. After joining AEI, she quickly adapted to large-scale projects and technical complexity found across the globe — Europe, Middle East, United States and beyond — and all the different voltages, power distribution systems and codes that come with it. Clients, architects and other engineers respond positively to her leadership, demonstrated by her growth into a lead engineer role, where she is the main point of contact for clients. In the AEI Houston office, she serves as department facilitator, where she manages employee workload, project staffing, mentoring and performing employee reviews. When not at work, she helps one of her four sons with beekeeping, including honey harvesting. She and her children love to travel and have been to all 50 states.
Associate, Senior Electrical Engineer, Kohler Ronan LLC Consulting Engineers; BE, Electrical Engineering, Manhattan College
Growing up in Yonkers, New York, Manavalan exhibited an aptitude for math and science from an early age. He attended a science-focused high school where he participated in the ACE (architecture, construction and engineering) Mentor Program before studying electrical engineering. Upon graduation from Manhattan College, he joined Kohler Ronan where he has worked on electrical systems for landmarks and historical buildings such as the Metropolitan Museum of Art in New York City and the Thomas Jefferson Rotunda at the University of Virginia. According to his peers, Manavalan approaches each project with a creative outlook and is always proactive in proposing additional thoughts and ideas on how best to limit the visual and material impact of implementing new building systems into historic spaces, structures and sites. Moreover, he is a natural leader whose innate curiosity and spirit of teamwork have resulted in well-coordinated, multidisciplinary design strategies and successful construction projects. Outside of work, Manavalan is engaged in substantial community outreach. He is now a guest mentor in the same ACE program in which he participated during his younger years. As a mentor, Manavalan guides and instructs groups of approximately 20 students, as they workshop ideas resulting in the simulated design and construction of a building project. In addition to working with ACE, Manavalan volunteers as a mentor with the Connecticut chapter of Professional Women in Construction. Manavalan attributes his success to the quality and support of his wife, parents, family, friends and colleagues.
Senior Associate, Sustainable Design, BR+A Consulting Engineers; BS, Mechanical Engineering Technology, Wentworth Institute of Technology
Passionate about the complex challenges of climate change and global warming, Martin uses his background in engineering and building simulation to provide holistic, sustainable solutions for complex projects. In 2011, Martin shifted his time to focus more on sustainable design rather than HVAC design. Designing low-carbon, high-energy-use buildings such as laboratories and hospitals requires creative thinking and innovation. Project experience includes colleges and universities, mostly school science buildings. A project for a large hospital currently in construction includes a novel approach that will allow the facility to be 100% electric in the future. One key design element uses dedicated outdoor air systems with enthalpy wheels serving air handling units with an active cooling of dedicated exhaust air. Martin’s innovative approach goes back years. In 2014, he was the energy engineer on BR+A’s first zero net energy project, a teaching laboratory for Bristol Community College. The zero net energy building design was $200,000 lower than the projected high-performance design by focusing on load reduction strategies to reduce construction cost to pay for electrification systems such as geothermal and air-to-water heat pumps. The construction cost reduction strategy combined with a hybrid heating and cooling plant was a forward-thinking and innovative concept at that time. Martin enjoys traveling with his wife to new international destinations. Some of his favorite trips include recent visits to Paris and London and two weeks spent in Australia and New Zealand.
Science & Technology Practice Director, Henderson Engineers; BS, Architectural Engineering, Kansas State University
Partner, CMTA Inc.; BS, Mechanical Engineering, University of Kentucky
Maybrier has been interested in engineering from a young age. Even as a child, his parents often discovered disassembled radios, VCRs and other small appliances in his room. He joined CMTA as a project manager in 2016 where he has participated in projects across various building sectors, including education, health care and manufacturing. Recent projects include implementing energy conservation measures for Jasper County Schools and central heating plant decentralization for the Kentucky Transportation Cabinet and State Office Building. Among his peers, Maybrier is viewed as a leader, technical expert and educator. He is always willing to stop what he is doing to answer questions and take the time to share his industry knowledge with anyone eager to learn. In addition, he is consistently able to overcome the obstacles that emerge during a complex construction project and is known for his strong dedication to his clients. Maybrier ensures that all clients have his cell number and advises them to call whenever they need help with their buildings, even if they are not part of one of his projects. He also participates in and donates to the Annual Golfer’s Gauntlet, which benefits the Epilepsy Foundation of Kentuckiana. The foundation services 153,000 Kentucky and Southern Indiana residents in their fight against epilepsy. When he’s not with his wife and three dogs, Maybrier enjoys fishing, camping and time in his garage, which provides him with a place to tinker without the stress of cold buildings, late equipment delivery or project budgets.
n seven years with Henderson, McGrail has climbed his way up the ladder from project manager to practice leader and eventually to practice director. He is the youngest practice director companywide. Recent projects include a Food and Drug Administration facility and laboratory and a university computing facility. Outside of work, he dedicates time to various pursuits within the business and philanthropic community in the Kansas City region. He is a longtime member ASHRAE, serving on a variety of committees for the local chapter during the past decade. He is a respected leader within The Heart of America Chapter of the International Institute of Sustainable Laboratories, currently serving as the organization’s treasurer following a successful tenure as its secretary. McGrail took part in the Pillars leadership program with AIA Kansas City, a coveted honor bestowed upon emerging leaders within the region’s competitive architecture, engineering and construction industry. In addition to volunteering for various charitable causes alongside his Henderson colleagues, he has taken part in Habitat for Humanity building projects for the past six years, using his professional skillset to help provide new homes for the underprivileged. With most of McGrail’s time spent using technology for work and personal pursuits, he enjoys setting aside time to unplug. Sports are a favorite pastime and they allow him to relax by spending time in nature. McGrail picked up golf in his final year of college before taking a brief hiatus and rediscovering his love for the game several years ago.
Southeast Commissioning Team Leader, AKF; BS, Environmental Engineering, University of Florida
As a commissioning engineer, McGrath is responsible for performance verification of building systems throughout all stages of a building’s life. He specializes not only in new construction commissioning, but also retro-commissioning and energy audits. In his role at AKF he was a key member of the team that designed the Morris and Gwendolyn Cafritz Foundation Environmental center, the 13th project in the world to achieve full Living Building Certification from the International Living Future Institute. According to his clients, McGrath always meets any challenge that is presented to him, no matter how great, which has earned him the respect of the consultants and contractors he works with. In addition to his position at AKF, McGrath is an adjunct professor at Drexel University where he teaches three building system classes with the architecture program. Previously, he was an adjunct professor at Philadelphia University teaching sustainable systems. McGrath also volunteers in his local community, where he is a founding member of the Living Futures Philadelphia Collaborative and serves on the board of directors of the Clementine Montessori School in Philadelphia as well as heading the facilities committee. In his free time, he enjoys mountain biking in Philadelphia’s Fairmount Park. In particular, he appreciates sharing time outdoors as a family with his wife and 6-year-old son. McGrath is also a certified weekend warrior, working on DIY projects ranging from full bathroom renovations to small carpentry projects. He fills the gaps with mountain biking or playing basketball.
Electrical Engineer, CDM Smith; ME, Electrical Engineering, Worcester Polytechnic University
Aspecialist in the design, testing and analysis of electric power systems for a wide variety of clients, McGugan originally joined CDM Smith in the Cambridge, Massachusetts, office. In 2019, he transferred to Raleigh, North Carolina, where he has been since. McGugan’s time at CDM Smith has been split between power systems analyses and design/construction services. Clients include small wastewater pumping stations, large industrial complexes and military bases in the U.S. and overseas. As a power systems analyst, McGugan has led and performed projects that include the standard components of an arc flash study as well as harmonic studies, transfer timing studies, load flow studies and reliability studies. He has furthered the power systems practice within the electrical engineering discipline by mentoring junior engineers, writing articles, giving presentations to clients and staff, starting a power systems analysis subcommittee and co-leading internal standards development efforts. One of the most challenging power systems analyses McGugan led was for Naval Station Norfolk in Virginia, which is the largest naval base in the world. This project was challenging due to its size, combination of different types and ages of electrical systems and overall complexity. McGugan is also a member of IEEE and has served on the P1459 Working Group. He lives in North Carolina with his wife and two children. The family enjoys spending time together outdoors, especially by hiking in the foothills and mountains of North Carolina, swimming at the beach and kayaking or canoeing, most commonly on the Lumber River. He also enjoys the challenge of woodworking. One of his professional goals: to work in Antarctica.
Senior Energy Engineer, Cyclone Energy Group; BS, Industrial and Systems Engineering, University of Florida
Fire Protection Engineer, Jensen Hughes; BS, Fire Protection Engineering, University of Maryland
As a student at the University of Maryland, Myers was one of four people selected from the undergraduate fire protection engineering department to research Xtralis’ open-area smoke imaging detection devices. After graduating, she began her tenure with Jensen Hughes as an intern before advancing to become a full-time employee. Her role involves providing fire protection, fire alarm, smoke and egress modeling and life safety code consultation and design services for various types of facilities, including multifamily residential, commercial office, historic landmarks, government facilities and large assembly buildings. According to her peers, she is a versatile and sought after team member, who is not only highly technical and knowledgeable, but an integral member of Jensen Hughes’ office where she is involved in the Women in Technology group, as well as regularly assisting and mentoring younger engineers. Outside of work, Myers serves as a board member for the Arlington County Local Board of Building Code Appeals where she hears appeals from county residents on various topics regarding building code violation notices. According to Myers, this position has allowed her to improve her interpersonal skills by working closely with the panel to make informed decisions that honestly serves the county and its residents. In her leisure time, she can be found enjoying a good book, particularly in the historical fiction, mystery and thriller genres. She also enjoys traveling, having visited South Africa, Thailand, Costa Rica, Spain, Italy, the United Arab Emirates, Mexico and the Dominican Republic in the past few years.
’Connor joined the Cyclone Energy Group team in 2021, having previously worked for Aramark Engineering and Asset Solutions. He made an impact on the energy engineering team and the company, widening the diversity of knowledge and strengthening the collective experience. He was challenged early to learn a new method of retro-commissioning and monitoring-based commissioning. O’Connor accepted the challenge and has delivered on major projects including the monitoring-based commissioning of three shopping centers for Brookfield Properties. Soon after joining the team, the energy efficiency program manager at ComEd — a regional utility — reached out to Cyclone Energy Group and asked for substantial savings across multiple projects in a highly accelerated timeframe to help them reach their program goals. The Cyclone Energy Group team was awarded the “Clutch Performer” award for their efforts, in which O’Connor was instrumental. To give back to the industry, O’Connor is serving as a technical session monitor to assist with checking ASHRAE members into sessions and assist presenters with any inquiries they may have during presentation setups. In his free time, he enjoys biking to explore the great outdoors. Cooking is another creative outlet for O’Connor and he enjoys experimenting to see what he can create with what is already in the refrigerator. He even crafts his own hot sauce. O’Connor enjoys applying his engineering intuition and ability to learn quickly to home improvement projects. The project he is most proud of is the half-bath renovation, which brought a 1970s-style bathroom more in line with 21st century tastes.
Senior Project Engineer, ESD; BS, Mechanical Engineering, Valparaiso University
Olejniczak joined ESD after completing an internship program with the company and became a staff engineer. He quickly advanced, first serving as a project engineer and then as the de facto mechanical lead for ESD’s largest client. His combination of design, work ethic and credibility with clients has positioned him as a key leader for one of the company’s largest hyperscale data center clients. When a client challenge arises, he first addresses client needs, then performs research and engages others with unique experience to gain insight before crafting an informed solution. His dedication, creativity and personal integrity are all highly valued qualities appreciated by clients and colleagues alike. This high degree of professionalism was recognized by ESD in May 2022 when he became an inaugural recipient of the ESD Leadership Award. Olejniczak is also dedicated to fostering the next generation of building professionals. In 2019, he volunteered with the Chicago Architecture Center’s Engineering Festival. He also is generous with the time he dedicates to professional organizations such as ASHRAE. He is an active thought leader, publishing and presenting to professional organizations and peers. Olejniczak has been committed to making a difference in the lives of young people in his community, which he now extends to his three children. He and his wife also enjoy traveling, hiking, exploring new restaurants and spending time with extended family. He also enjoys the solitude of a walk through the woods or an afternoon of fishing, particularly with his two older children.
Associate Principal, HVAC Engineer, BR+A Consulting Engineers; MAE, Architectural Engineering, Penn State University
Apowerhouse in the industry, Popa has been making a difference since college. Popa graduated from Penn State University with an integrated bachelor’s and master’s of architectural engineering and an architectural studies minor from the Pantheon Institute in Rome. As a project manager at BR+A, it is role to lead external and internal mechanical, electrical and plumbing (MEP) communication and coordination among trades with architects, owners, contractors and other project consultants to deliver high-performing MEP designs that align with schedule, budget and building performance goals. In addition to project manager, Popa is the leading HVAC engineer for the projects and works with other staff members to develop HVAC system designs that are both environmentally responsible and resilient for the critical operation and function of the buildings. Key projects include several college/university buildings, health care facilities and research laboratories. As an associate principal, Popa works with her colleagues and senior management at BR+A to improve internal processes including the training of younger and new staff, developing project delivery and design standards and promoting company moral and camaraderie. Outside of the office, Popa enjoys walking 18 holes with her push-cart while talking to her fellow golf friends, working out or running every day and trying new recipes to host her friends and family for dinner parties.
Technical Service Leader, Electrical Engineering, BG Buildingworks; MS, Architectural Engineering, University of Kansas
Senior Project Executive, Bernhard; BS, Kansas State University
Having completed his studies, Reed’s first goal was to become a licensed professional mechanical engineer. After passing the exam on his first attempt, he is a licensed engineer in seven states. Co-workers say his greatest talent is an ability to communicate effectively with individuals at any level of knowledge or experience. He is consistently requested by owners and architectural clients to lead projects. Reed continues to expand his leadership skills by continued use of assessments including: Clifton Strengths, DiSC training, SLII leadership training, enneagram tests and ASHRAE YEA Leadership Weekends. He is an active participant and mentor in Bernhard’s internal young professional mentorship program. Reed was elected the Northwest Arkansas ASHRAE section president. Originally just a section of the Arkansas chapter (operated by leadership in Little Rock), Reed was offered the opportunity to lead the official charter of the Northwest Arkansas section to become its own standalone chapter. In just 11 years, Reed has attained an executive level role with Bernhard. He has led designs of more than a dozen different HVAC system types, including projects for sports arenas, performing arts centers, dormitories, hospitals and many others. Reed is an advocate for a healthy work-life balance. He encourages team members to spend time with their families, schedule breaks away from their desks during the day and coordinate personal appointments so that the stress of work and deadlines can be mitigated. He and his wife love travel, both nationally and abroad. His love of golf allows him to spend time outdoors and to build professional relationships.
oyal is always on the go, those who know her say, whether it’s her academic pursuits, personal interests or being a steward helping others. As an experienced senior project engineer, Royal manages multiple projects while collaborating with internal and external teams. She is often requested by clients for projects and to facilitate interaction with multidisciplinary teams. She has developed power and lighting designs, performed site surveys and provided construction administration services. Royal has also been an adjunct lecturer and is currently pursuing her doctorate in electrical engineering. As the electrical services leader, Royal oversees the electrical engineering elements the firm provides for its clients. She continuously hones her abilities through a hands-on learning approach to building systems and their real-world applications. As a consultant, Royal focuses on relationship building and ethical business practices. She has presented multiple times for internal and external teams including lunch and learns, continuing education, staff retreats and conferences. While at college, Royal was a Division I athlete where she threw shot put and javelin. It was also during her collegiate years she discovered that she loved jumping out of perfectly good airplanes. This love developed into the pursuit of skydiving world records. Royal looks forward to a future as an adjunct professor, hoping to help bridge the gap between academia and real-life engineering experience. Alongside her husband, Royal enjoys traveling and spending time with their boys and furry felines.
Building Environmental Science Associate, Harris Co.; Ph.D., Philosophy in Mechanical Engineering, University of Toledo
Salehi uses thermal and flow simulations to create efficient project designs. He is motivated to continuously innovate and improve those designs to ensure projects meet or exceed expectations. Since joining the industry in 2016, Salehi has used his extensive knowledge to predict failure scenarios and reduce costs. He relies on his experience with computational fluid dynamics, fluid mechanics and energy modeling to optimize heating and cooling requirements within health care facilities and commercial buildings. He is also an adjunct professor at George Mason University. Salehi developed his interest in design and computer-based simulations during undergraduate studies at Isfahan University of Technology in Iran. Salehi achieved his master’s in mechanical engineering from the University Technology Malaysia. He then moved to the U.S where he received his doctorate from the University of Toledo. His focus for both theses considered advanced turbulent air flow characteristics and how micro particles spread within complex micro and macro environments. This helped Salehi years later when he was designing HVAC systems for clean spaces like operating rooms and clinical centers. Recent projects include pharmaceutical facilities, hospitals and health care buildings and data centers. He’s been an active member of ASHRAE for several years and has published and presented papers at different conferences. Outside of work, Salehi spends his free time outdoors. He belongs to a local hiking club and recently started skiing. He values this connection with nature and enjoys sharing his outdoor experiences with co-workers.
Senior Associate Engineer, IMEG Corp.; BS, Electrical Engineering, University of Wisconsin, Platteville
The first electrical engineering projects Sanders worked on exposed him to the fact that the client relationship can be as important as the actual engineering skills needed to complete a project. This led him to accept a position as an entry-level engineer at KJWW, now IMEG, where he would continuously be engaged with clients and the personal side of engineering. To start, Sanders had no direct consulting or construction responsibility. However, his experience in the Army National Guard working as a heavy construction equipment operator helped him understand the field side of consulting. Sanders’ people skills, developed through the military, also have served him well. His first long-term collaboration was with a health care client where he served as a design engineer on a larger team. He developed into the lead contact for that client, working with the hospital president, head facility manager and team of electricians. Sanders believes the best way to learn is to teach. He developed technical skills in his early years learning from a mentor and is now mentoring new engineers. He volunteered to develop educational modules for IMEG and now represents the Madison, Wisconsin, office for the technical operations group. Sanders routinely participates in team-building exercises and office outings. He is also the Madison office electrical team supervisor. Part of his free time is spent at church as a confirmation mentor and as a camp counselor. He also spends quality time playing with his three children, ages 11, 8 and 1. His motorcycle hobby and board game collection are a passion.
Senior Electrical Engineer, IMEG Corp.; BS, Electrical Engineering, Iowa State University
As a child, Spina always thought she would go into veterinary science. However, looking back she can see the telltale signs of a budding interest in engineering in the number of phones and other electronics she dismantled. As an electrical engineer with IMEG, Spina has amassed experience in energy management, power distribution, lighting, voice and data cabling, fire alarm, security, CCTV and uninterruptible power supply system design. Her work has served buildings in the educational, commercial, industrial and residential spaces. According to Spina’s peers, she is a team player who has consistently provided well-researched recommendations and thoughtful feedback when taking on new challenges and helping her clients grow their organizations’ capabilities. In addition, she is passionate about helping her local community. As a leading member of IMEG’s Community Involvement Committee, Spina is tasked with allocating funds and organizing events that allow employees to support local charities. She is also an emergency foster for a nationwide animal rescue for Papillon dogs. In this role, Spina helps to transfer dogs who have been adopted or are moving to a new rescue facility. When she isn’t working or volunteering, she can be found competing in monthly agility competitions with her Border Collie, Monty, or with her two children. She is also an avid runner and has participated in five half marathons. She also finds time to be a Girl Scout troop co-leader, organizing two or three meetings each month and planning events for the troop members, including visits to Disney on Ice, Iowa State Women’s basketball games and camping outings.
Associate, WSP USA; BS, Mechanical Engineering, Texas A&M University
Scott is a technical leader in mechanical systems and building automation control systems with experience in mechanical, electrical and plumbing (MEP) design engineering, commissioning, facility assessments, energy audits and project management. Scott’s experience includes new and existing hospitals, high-rise, laboratories, pharmacies, higher education, hospitality, municipal, multifamily and mixed-use commercial. Scott successfully engages with owners, design teams, contractors and facilities personnel with the goal of improving the final product. Outside of project work, Scott presents at national conferences, writes engineering articles, develops office-standard specifications and tools and hosts training events. While working as a mechanical engineer, Scott was both MEP project manager and lead mechanical engineer for major hospital projects. Now, he leads commissioning teams and provides technical oversight for commissioning of new projects, retro-commissioning, facility assessments and energy audits across the country. Scott’s experience includes designing 200,000+ square-foot hospitals, full replacements of 5,000+ ton central plants, writing custom control logic for unique applications and testing renovated central plants in operating hospitals. Scott regularly volunteers with OnRamp DFW, which provides reliable vehicles to people who need a helping hand. Scott also has participated in various events with Habitat for Humanity, Feed My Starving Children and Oxford Glen Memory Care at Sachse. When time allows after taking care of his three children, he likes to play board games, brew beer and scuba dive.
Associate, Senior Mechanical Engineer, SMS Engineering; BS, Mechanical Engineering, University of Manitoba
'We need another Gavin” is the phrase commonly used when hiring at SMS Engineering. Initially hired to help with plumbing design, Stewart quickly became proficient in HVAC, fire and hydronics. Stewart is often requested by clients. His personable style is easy to spot, but most impressively, it is his ability to address complex challenges with cost-effective, user-friendly solutions that amazes clients and other designers. He is dedicated to the SMS team, to his profession and to the consulting engineering industry. He possesses a rare talent of being a brilliant designer and businessperson who can apply solutions so the client and company benefit. He’s dedicated to his client base, ensuring they receive the service and return on investment needed. Stewart has been assigned to many renovation projects for his ability to imagine possibilities and then figure out a way to achieve the intended results. His work on the RBC Convention Centre Expansion & Redevelopment challenged him in combining a massive existing structure to that of a new build. Stewart has also been part of many health care renovation projects ranging from air handler replacements to large additions. An active volunteer in the ASHRAE Manitoba chapter, Stewart has served in all the executive positions of the Manitoba Board of Governors since 2012, including president. He also has presented at various conferences. Volleyball has been a passion since high school and he still plays on two teams. In his spare time, he listens to a variety of music types. He is married and has one young daughter.
Partner, Electrical Engineer, CMTA; BS, Electrical Engineering, University of Kentucky
Principal, CMTA; BS, Mechanical Engineering, University of Maryland
Like so many, Torre’s path through the engineering industry has been long and winding.
tewart has been passionate about electrical engineering since he was a child when his grandfather and uncle, both electricians themselves, encouraged his curiosity and allowed him to tinker in their garages. Today, with more than 18 years of electrical engineering experience, his responsibilities have covered all aspects of electrical design for education, health care, commercial and military facilities. For the last six years Stewart has been focused on leading a team of technology designers overseeing audiovisual, information technology and electronic safety and security design. Several of his projects include the Samsung Solutions Center in Washington, D.C., the Department for Homeland Security in Ashburn, Virginia, and Baptist Health in Lexington, Kentucky. Stewart prides himself in always being available at the drop of a hat; on one occasion in which surveillance cameras were added to a site very late, Stewart and his team drove an hour to the jobsite to pull cabling themselves. Outside of his role with CMTA, Stewart has served on the engineering alumni board at the University of Kentucky where he oversaw various activities and philanthropic efforts, including speaking at engineering-related programs and participating in “Root Beer with an Engineer,” a program that allows college of engineering faculty, engineering alumni and industry leaders to share their wisdom with students over a root beer float. He also plays an active role helping with the audiovisual equipment and IT network at First Christian Church Frankfort, his hometown church. Stewart lives with his wife and two young sons on 20 acres in the country. Together, they enjoy sports, trips to Lake Cumberland in Kentucky and working on home improvement projects.
Moving between the design and the project management side of the business has taught him that while mathematics and engineering knowledge are essential, people, relationships and leadership are what really drive the industry. As a principal at CMTA, Torre brings 18 years of experience in the commercial, education, health care, life sciences and government sectors to his role. He has worked on projects ranging from the U.S. Consulate Compound in Mumbai, India, to High Performance Corporate Headquarters and R&D facilities, net zero K-12 schools and laboratory work at the National Institutes of Health. According to his peers, Torre has seemingly endless passion and energy that radiates through to his team. Beyond his work with CMTA, he is also engaged in substantial community outreach. Along with his teammates at CMTA, he volunteers at Washington, D.C.’s Capital Area Food Bank. Torre also donates to the Make-A-Wish Foundation, the National Multiple Sclerosis Society and the Giving Tree and Angel Child programs, local church initiatives that buy and deliver toys to children in need during the holiday season. In his free time, Torre enjoys ice hockey, which he has been playing since the age of five, as well as cooking, art and music. Torre is a family man first and recently put his art skills to work completing a series of canvas murals for his young daughters’ rooms.
Senior Electrical Engineer, Richardson Engineering; BS, Electrical Engineering, Northeastern University
Terray’s interest in engineering started in high school, where her teacher recognized her interest in STEM and recommended her for a Women in Engineering program. She has 13 years of experience and has worked on the design and construction services of a wide variety of projects. In addition to design work, she has had the opportunity throughout her career to mentor others, including being a group leader at Fitzemeyer and Tocci Associates where she ensured her staff was well trained and up to date with code requirements as well as industry standards and trends. She enjoys being a resource to others and always makes certain they receive the support they need to succeed.
Terray started at Richardson Engineering in October 2021 as a senior project engineer where she has worked on solar photovoltaic installations, power systems studies, medium-voltage distribution systems, fire alarm systems, health care, residential, commercial and industrial wastewater and water treatment facilities. Terray consistently works to improve accuracy and efficiency for the company and clients. In her time at Richardson Engineering, Terray has improved standards and updated templates to streamline and ensure consistency as the company grows. She is always excited to tackle a new problem and thrives on challenging designs. Terray has volunteered with several groups, including recently volunteering to co-host a math competition for middle schoolers. Outside of work, Terray enjoys traveling with her husband, most recently visiting Montana, and being active, having completed half marathons, 5Ks and Ragnar (a 200-mile overnight relay race). She hopes to continue being active both as an engineer and runner for many years.
Director, Jensen Hughes; BS, Fire Protection Engineering, University of Maryland
An interest in math and science, the intro to fire protection engineering class and the loss of a college friend to a fire pushed Tyson to success. Tyson is a director for the Atlanta office of Jensen Hughes, responsible for supervising staff on fire protection and code consulting projects. As an engineer with 17 years of experience, she is a trusted adviser to clients seeking technical guidance and project oversight. She employs a servant leadership style to support and grow an exceptional team. She has extensive experience in fire alarm and life safety design, fire alarm inspection and testing, evaluation and review of automatic sprinkler design, building code analysis and negotiations with local authorities having jurisdiction. Tyson’s thinking provides an advantage to clients exploring performance-based design approaches in lieu of a code prescriptive approach. Her project experience includes airports, high-rise mixed-use facilities, education buildings, large-scale residential buildings, office buildings and government facilities. Throughout her career at Jensen Hughes, Tyson has worked her way up from intern to director. As part of the University of Maryland alumni group, which has a large presence in Atlanta, she spends her time volunteering as a part of the organization. Volunteering has included helping at the Atlanta Food Bank. Tyson spends her free time on trails with her senior poodle-mix, walking, running and reading. She loves to travel; her favorite travel partner is her mom. They’ve traveled within the U.S. and to Greece, Iceland, Egypt, India and Dubai. Tyson has also traveled to China, Thailand, the Maldives and the Caribbean.
Director of Hydronics, Cleaver-Brooks; BS, Mechanical Engineering, Michigan Technological University
Starting as a mechanical engineer at a consulting firm, VanWormer moved to Cleaver-Brooks to serve in mechanical and sales engineering roles and in engineering management. She also has worked as a product sales manager where she co-developed an award-wining hydronic boiler. Not only is VanWormer a talented engineer, she also is a leader and a teacher. She is a knowledgeable, dedicated and trusted mentor to her colleagues and others in the industry. She has the ability to communicate highly technical content in an easy-to-comprehend manner. She has contributed content and articles to a host of industry publications and is a regular presenter for Cleaver-Brooks webinars. VanWormer also travels, speaking at ASHRAE chapters, AHR events and with specifying engineers and mechanical contractors. She works with owners, architects, engineers, contractors and manufacturers’ representatives on project specifications and selection. She sits at the crossroads of the hydronics and steam industry and is qualified to listen to the needs and wants of each stakeholder, then works to develop and build innovative products and solutions or make upgrades to existing ones. VanWormer embraces challenges in all aspects of her life. For example, she recently started running and enjoys the mental and physical challenges associated with it. She has finished several 5K races as well as her first 10K race and is training to compete in longer distances. VanWormer is a life-long horseback rider who is getting back into showing horses. She credits riding with teaching her many skills, most notably hard work, responsibility and sportsmanship.
Building Science Engineer, CMTA; MS, Engineering Management, George Washington University
Automation Engineer, CDM Smith; BS, Engineering Science and Mechanics, Virginia Polytechnic Institute
Villar has five years of experience in water and wastewater treatment facility design and applications engineering services for SCADA systems. She is a registered engineer in training and she is working toward her professional engineering license this year. Villar has experience with various SCADA software applications and she is known for her ability to work well with clients and peers. She is the first point of contact for local clients whose SCADA systems she supports, thanks to her critical thinking skills and ability to propose effective solutions to complex problems. During her first year with CDM Smith, Villar recognized the need for early automation education and fundamentals. She took the initiative to develop a library of resources that could be used as coursework for CDM Smith University, a platform for professional development within the company. Villar then created the automation young professional group, a place for young automation professionals to discuss topics related to technical and professional development. Team members from 11 offices across the U.S. and India collaborate and network on a monthly call. Villar is also active in her industry outside of work. She has presented her work at conferences at the state and national levels. She is a member of the joint Virginia American Water Works Association (AWWA) and Virginia Water Environment Association Technology Services Committee. Additionally, she is the incoming chair for the national AWWA Operational Technology Committee and hopes to engage young professionals in various educational activities. Outside of work, Villar enjoys spending time boxing or weightlifting at the gym with her husband and friends.
exed by dryer lint at a young age, the passion to use waste byproducts and make systems more sustainable pushed Washle into a career in green buildings. Her goal is to bring the built environment into harmony with the natural one. Washle’s education in both business and engineering allows her to see more sides of the problem and make the case for sustainability to clients. She works with owners to give them the tools and data to make buildings high-performing. She walks them through the environmental impacts of different HVAC systems and the effects of building design decisions on parameters like energy use intensity and carbon footprint. The business side of her gives them perspective concerning required funds, paybacks, available incentives and return on investment. Personally and professionally, she strives to create opportunities for people to live more sustainably. For instance, when she moved to Massachusetts and found out her town wasn’t a part of the National Buy Nothing project, she started a local group. She is also active in several professional organizations, such as the Association of Energy Engineers. She is secretary and sustainability chair for the Boston ASHRAE chapter and has served on the board of CWEEL and BE+. She hosts monthly eco events, one of which compared the footprint of personal digital files to the energy required to run data centers. She’s engaged with the Keep Nature Wild Wildkeeper program, with a goal of helping to collect 1 million pounds of litter. In her spare time, she meets friends for a book club brunch.
Assistant Vice President, Design Services, MTA Construction and Development; MS, Electrical, New York University
Wassif said the skills developed the past 20 years in the engineering industry serve him well in his current role as a design compliance executive at the MTA. Having worked in design services the past two years, Wassif has assumed leadership roles in managing the architectural and engineering design processes to conform to MTA and industry standards. Under design services, he worked with a team from legal to establish and issue guidance on types of drawings to be used for certain projects and provide consistencies within language in specifications and bridging documents. He served on selection committees and currently is the assigned project manager for various consultant scopes of work. Wassif played an integral role in the development and testing of a lessons learned information system to ensure the application followed developed procedures. He has prepared and presented training sessions to MTA business units on design compliance in projects, design coordination and lessons learned. Wassif has built a good relationship with various user departments in the agency as well as management and staff on establishing various processes, procedures and guidelines that assist in the development of designs and ensure consistent approaches. Aside from work, he enjoys spending time with his wife and two children and serving in his community activities. He mentors youth at home, work and in the church community to instill the practices of hard work and commitment. He serves as church deacon and enjoys prepping fun activities and youth retreats.
Make us your easy button.
Congress has approved $370B for climate and energy tax credits, specifically expanding investment tax credit eligibility to include microgrid controllers and energy storage. Let Eaton experts help design, deploy and even finance your microgrid project from
end-to-end without any up-front capital costs. And leverage available stimulus funding to help pay for your project.
Eaton o ers a seamless solution with trusted finance partners.
To learn more go to: Eaton.com/microgrid
Bill Kosik, PE, CEM, BEMP, DNV, Oak Park, Illinois
Decarbonization efforts are a critical part in meeting the goals pledged by President Biden during the 2021 Leaders Summit on Climate — reducing the nation’s greenhouse gas emissions 50% by 2030 and net-zero by 2050 (2005 emissions as basis).
• Discover what role commercial buildings have in carbon dioxide emissions and the resulting impact on climate change.
• Understand how state energy plans are structured and learn about energy-efficiency incentive programs.
• Get a more in-depth understanding of the different approaches on using technical resources manuals and the energyefficiency measures.
• Learn about specific energy-efficiency measures used in incentive programs for air handling systems and equipment.
The U.S. Department of Energy decarbonization roadmap is a set of strategies including energy efficiency, clean energy supply, clean fuel sources and direct air capture of carbon. Of these strategies, energy efficiency is the “beginning of the pipe,” improving efficiency which reduces the need for clean energy and fuel and results in lower carbon emissions. Energy efficiency is vital in the world’s journey to net zero and keeping global warming at 1.5 degrees Celsius. The International Energy Agency (IEA), nicknamed it “the first fuel.”
To develop actional processes and to reinforce the importance of energy efficiency, the New Building Institute (NBI) published the “Existing Building Decarbonization Code.” According to the NBI, the code is “… a new way for jurisdictions to reduce carbon emissions and meet Climate Action Plan and public health and equity goals. The need to address existing building stock is great, with 5.9 million existing commercial buildings in the U.S. comprising 97 billion square feet”.
Electrification is a strategy that falls under the decarbonization umbrella. It can play a major role in reducing the carbon emissions from commercial
buildings when the source grid is sufficiently clean. In 2020, the American Council for an Energy-Efficient Economy produced a study that showed commercial buildings that replace their gas-burning heating systems with electric heat pumps could reduce their total greenhouse emissions by 44%.
Commercial buildings account for 35% of all electricity use in the U.S and 16% of carbon dioxide (CO2) emissions. And according to the U.S. Department of Energy (DOE), 30% of the energy used in commercial buildings is wasted. Furthermore, in commercial office buildings, the heating and cooling systems, including air handling equipment, consume more energy for air conditioning than any other building type.
The good news is that energy use in commercial buildings continues to drop. The data show that from 2018 the energy use intensity has decreased by 12% (see Figure 1).
Air conditioning systems are one of largest electricity consumers in commercial buildings. Across the buildings sector, purchased electricity accounted for 94% of delivered energy for air conditioning in 2019. These systems range from central built-up systems to packaged rooftop units. Breaking down a typical heating, ventilation and air conditioning (HVAC) system into smaller categories, ventilation, cooling and heating systems are the largest energy consumer of all the other sub-systems. When building owners are looking for ways to reduce energy consumption, implementing energy efficiency measures (EEM) specifically for air handling equipment can yield significant savings.
Small- and medium-sized businesses may have difficulty finding capital funds or using cash reserves for HVAC system upgrades, but there are options for funding that can reduce the need for securing loans. Most states have energy efficiency policies, which are generally managed by the state’s public utility commission. Electric and natural gas utilities are responsible for developing a ratepayer funded energy efficiency program.
The programs are designed to incentivize residential, commercial and industrial customers as they implement energy reduction projects. Depending on the scope of the customer’s project, the incentives can provide a significant funding source for capital-intensive air-handling unit (AHU) upgrade projects.
This article has four primary purposes:
• Provide examples of processes developed by state energy efficiency programs used to estimate and validate energy savings required by ratepayer funded, utility managed incentive energy programs.
• Present high-level technical information based on the state efficiency measures, used to reduce energy consumption by improving the efficiency of air handling units.
• Provide an overview of how a proposed energy savings project is vetted and validated. This includes examples of engineering analysis and calculations developed by state or territory energy programs that are specific to AHUs.
• Discuss the important role of federal and state government in developing and funding programs that incentivize end-users to implement energy efficiency improvements.
Regulatory policy can have a significant impact on investments for improving energy efficiency in commercial, institutional and industrial buildings. Electric and natural gas utilities have a key role in making sure the end use of the energy is efficient, with the goal of lowering energy demand (electricity and natural gas). State utility regulators use a variety of incentives to address the inherent conflict that exists — lowering energy use can have an adverse financial impact on the utility. Policies enacted by the state encourage the utility to play a role in lowering overall energy consumption and set a foundation for implementing cost-effective EEM.
The state public utility commission (PUC) is responsible for the developing and updating the
FIGURE 1: In the reference case, commercial buildings will expand by 34% on a square footage basis. Office buildings consume more energy for air conditioning than any other building type, accounting for 25% of the energy consumed for air conditioning in the U.S. commercial sector in 2050. Courtesy: Bill Kosik
technical reference manual (TRM). The technical parameters and calculation steps in the TRM are essential for state regulators, utilities, program administrators and implementation teams for estimating and validating the energy and demand savings of end-use EEM. TRMs can be used exclusively by a state, by utilities or shared with other states and alliances.
Some TRMs include requirements to validate nonenergy impacts (such as water use and secondary CO2 emissions). Some measures include processes and calculations to validate the costeffectiveness of a measures focusing on the useful life of equipment intended to be replaced.
The state PUC approves the TRMs, giving it a legal framework. For example, in Illinois, the PUC approves the contract of an independent thirdparty organization whose primary responsibility is administering the TRC. In this scenario the thirdparty organization works for and is paid by the utility. But ultimately, the PUC has the final say.
In simple terms, the TRM is the “rulebook” for ratepayer-funded energy efficiency programs. When examining different EEMs, many are straightforward with little math required. Others are more complex using a series of calculations that include multiple variables such as age and capacity of existing equipment, type of flow control, location of project, operating characteristics and others. All these details ensure that requirements are
‘ Electrification can play a major role in reducing the carbon emissions from commercial buildings when the source grid is sufficiently clean.’
FIGURE 2: Air handling systems can have wide variances in energy consumption based on climate and system type. Illustration based on data from Commercial Building Energy Consumption Survey (CBECS) Table C16. Electricity expenditures by census region, 2018. Courtesy: Energy Information Administration
‘ Measures for HVAC efficiency upgrades use different methods to calculate energy savings. These types of measures generally use a more detailed approach to determine energy use reduction. ’
consistent and fair since the different utilities may use the same TRM for programs in other service areas.
When comparing AHU measures from different TRMs, weather data and hours of operation are two common values used in calculating savings. The TRM provides instruction on how to obtain these and other variables. For outside sources, the measure lists the technical reference that must be used (e.g., ASHRAE). In other cases, the values are defined in the TRM.
The TRM measures discussed in this article are classified “deemed” or “partially deemed.” Typically, deemed measures are thoroughly vetted and reviewed on a regular interval by the utility’s third-party evaluator and the utility commission
and updated as necessary. The authors of the measures are required to use reliable and transparent data sources and established analytical methods to calculate energy savings. Some of the measures (such as lighting upgrades) have minimal calculations and might use fixture count to determine energy savings, as an example.
Deemed savings measures have different components:
• Deemed variables: Examples of a deemed variable included weather assumptions and hours of operation
• Deemed factors: These include factors are dependent on the measure, such as measure cost and effective useful life.
• Deemed calculations: These include stipulated calculations for determine the economic aspects and energy impacts of the measure.
However, measures for HVAC efficiency upgrades use different methods to calculate energy savings. These types of measures generally use a more detailed approach to determine energy use reduction. Some of these measures are used for straightforward efficiency projects such as onefor-one equipment replacement — AHUs, chillers, pumps, split-system A/C units and motors are some common examples.
Deemed measures are used to ensure uniformity in documenting energy efficiency. As such, the engineer uses a pre-defined roadmap that determines the energy savings. This method allows the use of the TRM across cities, states or regions and creates a level playing field when determining incentives for the building owner.
Measures for more complex AHU efficiency upgrades, depending on the jurisdiction, require the engineer to demonstrate savings using a predefined set of calculations and assumptions. These measures are defined as partially deemed. Although these require deeper analysis, the measures contain pre-defined specific calculation steps and requirements for documenting savings. Although this method to generate savings is more clear-cut, the engineer must understand what the calculation steps mean and if the energy savings is realistic base on the project criteria.
Although not discussed in this article, custom measures require fully documented energy savings calculations with little guidance from the TRM compared to a deemed measure. Custom measures are calculation-intensive and the engineer must define (and defend) their approach in detail. It must be noted that TRMs present challenges that must be overcome. TRMs do not eliminate the need for applying fundamental engineering principals and investigation of the data presented in the TRM. Also, the energy savings generated from the calculations in the TRM must be validated to ensure accuracy.
For air-handling equipment and systems, the measures in the TRMs apply to replacing existing equipment with high-efficiency systems, mostly for packaged AHUs. Additionally, there are measures for each item such as economizers, airflow control and advanced control strategies. Depending on the situation, more than one of these measures can be used to determine energy savings. Also, energy-efficient products with low market penetration are used to stimulate the marketplace and stay ahead of future codes that require efficiency increases.
Knowing that a measure can span several pages in a TRM and include very detailed energy efficiency compliance requirements, the data presented
‘ There is not one uniform energy efficiency program across the U.S. And the programs that are in place also will vary considerably from state to state. ’
here is a summary only. The reader is encouraged to review a specific TRM for more information. To illustrate how measures are structured, examples relating to AHUs and ancillary equipment are outlined in this article.
In general, the measures from different TRMs have a similar structure, but there are differences. The content will vary based on state- and region-specific factors such as policy, location, climate, economy and utility involvement. These items have an impact on the current and recommended practices because each state or territory has a different energy efficiency baseline.
There is not one uniform energy efficiency program across the U.S. And the programs that are in place also will vary considerably from state to state. There are also programs that cross multiple states and territories and have a governing body that represents the member-states. In this case, a state government will play a different role than it does with a state TRM.
Another common approach used in developing a TRMs for an energy-efficiency program is to reference other state’s TRMs. This happens quite frequently and allows for a small degree of consistency among the TRMs.
The items listed below, taken from various TRMs, are an example of the basic structure, content and methodology of an EEM.
• Ancillary fossil fuel and electricity savings impacts.
• Baseline efficiencies for electric heating and cooling air-handling equipment (like ASHRAE 90.1 equipment efficiency tables).
• Calculations/algorithms.
• Coincidence factor definition.
csemag.com
u Commercial buildings account for 35% of all electricity use in the U.S and 16% of carbon dioxide (CO2) emissions. And according to the U.S. Environmental Protection Agency, 30% of the energy used in commercial buildings is wasted.
u Furthermore, in commercial office buildings the heating and cooling systems, a majority of which consists of airhandling equipment, more energy for air conditioning is consumed than any other building type.
‘ The type of air-handling systems will determine which (if any) energy efficiency measures can be used to calculate energy savings. ’
• Compliance efficiency to determine incentive amount (10% above code as an example).
• Data sources and basis for terms and variables.
• Definitions of terms and variables used in calculations.
• Example calculations.
• Guidelines on early retirement of equipment and remaining useful life.
• Measure description.
• Method of calculating annual energy and summer peak coincident demand savings.
• Operating hours (typical listed in TRM appendix).
• Procedures for determining energy savings including reference to mandated codes and standards.
• Same baselines for HVAC, but for natural gas heating air-handling equipment.
• References (mainly U.S.DOE, California DEER, AHRI, ASHRAE and published university research).
State energy efficiency programs are location specific. Certain measures from a state’s TRM are not applicable to other states. In states that have a cold climate, there is a focus on improving insulation in residences and commercial building and improving efficiency of heating systems. These climates, especially in a residential application,
improving efficiency of air conditioning system may not be a priority.
An AHU is an integrated collection of components that are sized to provide the required heating and cooling based on the relevant building code, engineering calculations and the design requirements of the end user. Some examples are peak demand cooling/heating load, filtration, volumetric flow rate, temperature and moisture levels.
The term “air handling unit” encompasses equipment for many different applications. AHUs range in size and complexity from small, rooftop-mounted units providing HVAC to a shop or small office. This type of equipment has basic components for heating/cooling and controls: dampers, filters and a fan with little or no control other than a wall-mounted thermostat.
In contrast, AHU equipment serving buildings such as hospitals, data centers, laboratories and specialized manufacturing facilities have extremely precise setpoint parameters, multiple levels of filtration, redundant fans and motors and very complex control and instrumentation systems.
The type of air-handling systems will determine which (if any) EEM can be used to calculate energy savings.
• AHU type (rooftop unit, heat pump, packaged indoor AHU).
• Heating source (electric resistance, direct/ indirect gas, hot water, reverse cycle).
• Type of cooling (compressors, chilled water, reverse cycle).
Measures don’t have to apply to the entire AHU. Many are written for sub-systems of the air handling equipment, for example:
• Integrated control of dampers for optimizing discharge air temperature, demand-controlled ventilation and outdoor air economizer:
• Outside air damper: Damper for bringing outside air; depends on control strategy for ventilation, pressurization and economization.
• Return air damper: Damper for controlling airflow back to the AHU.
• Exhaust damper: Damper to control amount of exhaust air.
Based on the existing type of filtration, there could be opportunities to reduce pressure drop across the filter section:
• Filtration: Study the feasibility to remove existing filters and install low-pressure drop filters using polarized media.
• Investigate application of advanced controls (especially for rooftop units) to control fan speed, damper positions, indoor air quality and optimized start-stop:
• Supply fan: Ensures proper airflow rates.
• Return or return/exhaust fan: Works in conjunction with supply fan to return/exhaust.
• Exhaust fan: A dedicated fan to extract air from the building to maintain ventilation and pressurization requirements.
While the items listed above are presented as induvial items, some measures are based on an integrated approach, taking many of the elements in total. It just depends on the measure.
Compressors are the primary component in the refrigeration cycle. They are used are used in residential, commercial, institutional and industrial cooling processes. Yet all AHUs that rely on compressorized systems are based on the same basic concept. A compressed refrigerant cools air or other fluids as required by the specific process. The outdoor temperature and relative humidity have a big impact on the energy use of the process and will vary considerably depending on the climate zone.
In hot climates (dry and humid) air conditioning is one of the primary energy consumers especially in commercial buildings. Energy-efficiency programs in these states have a much greater focus on air conditioning systems including compressor power and fan energy. This is an opportunity
for end-users to apply for utility programs and get partial funding for system upgrades.
Installing heat pumps can result in lower heating and cooling costs. This technology hinges on the climate and the savings will differ depending on the location of the installation. A measure that is based on replacing packaged AHUs with heat pumps may be applicable to warmer climates and locations due to the ambient limitations of heat pumps.
There are other measures use in the efficiency programs that do not involve compressors.
• Demand-controlled ventilation: The goal of this design strategy is to provide the appropriate amount of outside air to a facility as the occupancy demands, typically based on measuring CO2 concentration. In this application CO2 is a proxy measure for people in the building or a certain room within the building such as a large conference or meeting room.
• Outside air economizer: This is another very effective strategy found in many TRMs. Generally, package AHUs have fixed amount of outside air regardless of the outdoor temperature and humidity. Even in the cooler weather, the AHU will maintain a fixed outdoor air and compressors will continue to operate to maintain the required setpoints. An outside air economizer will bring in more outdoor air, based on temperature and
‘ In
energy efficiency programs, individual building owners have a tremendous opportunity to receive capital funds to replace inefficient, outdated equipment.
’
humidity, to cool the building using less compressor horsepower. It is akin to opening a window on a mild day and turning off the air conditioner.
While the energy used by compressors in AHUs is a large part of the overall consumption, the energy required to drive fans can be equal to or greater than the compressors. The fans use energy to drive the air to the end use and return it back to the AHU. Different air-handling equipment have different types and arrangements of fans, for supply, return and exhaust air.
There are several ways to reduce fan energy that are used as a deemed measure in TRMs:
• Matching the fan operation to the required air flow: This is accomplished using variable speed drives or electronically commutated motors. This is a common measure in many TRMs because it can be implemented with minimal down time and lit-
tle reconfiguration of the AHU. This can also be accomplished replacing a packaged AHU with a higher efficiency model that uses variable airflow.
• Advanced control systems: This type of system looks at the AHU in its entirety and makes decisions to change parameters that effect energy consumption (and indoor air quality). This system is the master controller of fan speed, air temperatures and humidity (indoor and outdoor), damper positions, economizer functions, etc. It can be a part of implementing other measures, such as economizer, fan speed, compressor power and demand-controlled ventilation.
• Low-pressure drop filtration: Filters in AHUs can incur a considerable pressure drop as the air flows through the filters. As the filter becomes loaded with particulate, the pressure drop will increase. The pressure drop has a direct impact on the fan energy use. Using filters that have a lower initial pressure drop and last longer between cleaning or replacement, will reduce energy consumption of the fans.
Incentive-based, ratepayer-funded energy efficiency programs are at the core of motivating building owners to take a close look at the energy consuming parts of their facility. Trying to understand the magnitude of energy consumption of air handling equipment, owners can make informed decisions based on utility-provided energy audits. The data provided in the audit will clarify the costs associated with the building systems.
Based on the outcome of the audit and the building owner’s situation, the next step is to determine the types of financial incentives that are available to partially offset the cost of upgrading components or replace the equipment entirely.
In energy efficiency programs, individual building owners have a tremendous opportunity to receive capital funds to replace inefficient, outdated equipment. This is a first cost and an operating cost benefit to the building owner.
However, there is a much broader and overarching principle energy efficiency programs reduce energy use, which allows for lower energy generation, in consumption and demand. This can result in less reliance on inefficient sources of electricity generation.
Finally, energy efficiency improvements are a key piece to decarbonization, which includes electrification building systems. Ultimately all these strategies will increase the demand and generation capability of renewable energy sources. cse
Bill Kosik, PE, CEM, BEMP, is a senior energy engineer at DNV. He specializes in modeling and analysis of energy use in commercial buildings. He is a member of the Consulting-Specifying Engineer editorial advisory board.
NFPA 13 requires the addition of an air vent on each wet pipe re sprinkler system that utilizes metallic pipe to help mitigate internal pipe corrosion. PURGENVENT valves come in a variety of styles. The 7910MAV is a manual air vent that has the smallest footprint on the market. The M7900AAV features an 7900V automatic air vent that releases excess air while the system is in operation. It also includes an isolation valve and purge valve. The purge valve helps air exit the system faster when lling, and it can be used as a vacuum break when draining the system. The vacuum break helps the system drain faster and protects gaskets from being dislodged on other system components when draining. The M7930ECA includes a pipe cap for easy installation, and the M7950ILV features an air separation chamber that installs into the main branch line for applications with dif cult to reach system high-points.
Our electrical conduit helps data centers keep the information flowing.
> No burn-through eliminates elbow repairs
> Low coefficient of friction allows for smooth pulls
> Fault resistance makes repairing cable easy
> Available with lower material and installation costs
> Corrosion resistant
DOWNLOAD THE CASE STUDY
Chris McDaniel, PE, LEED AP; Jordan & Skala Engineers, Washington, D.C.; and Sven Peulen, PE, LEED AP BD+C; Jordan & Skala Engineers, Atlanta
In the past several years, the building industry has seen a significant shift toward sustainability initiatives, such as green rooftops and using electricity for energy
Over the past 15 years, the architecture/engineering/construction (AEC) industry has seen a significant shift toward sustainability and environmental, social and governance (ESG) initiatives. As a part of that, there has been a notable trend toward green rooftops, as well as using electricity for energy, rather than traditionally used fossil fuels. The term for this process is called electrification — and over the next decade, the movement toward using sustainable and clean energy will become more prevalent.
• The reader will understand what electrification is and how it applies to the architecture/engineering/ construction industry, specifically in rooftop units and HVAC system technologies.
As a part of this movement, self-contained units and rooftop units (RTUs) used for heating and cooling a building are moving away from ozonedepleting refrigerants and greenhouse gas-producing fossil fuels to clean, efficient energy. Although the electrification of heating, ventilation and air conditioning (HVAC) systems has many impactful benefits, it doesn’t come without its challenges in terms of cost impact, the required electric infrastructure and adjustment to comfort.
• The reader will understand both the pros and cons of moving toward sustainable fuel sources and away from fossil fuels for the heating of a building.
• The reader will learn about the limitations of the power grid and how it will be affected as more electrified buildings come “online.”
The movement toward sustainable building design and construction is necessary as younger generations, including millennial and Generation Z, see green practices as critical to reducing negative impacts on the environment and climate change. Buildings and developments that are not environmentally friendly will see slower leasing rates and decreased revenue as a result.
FIGURE 1: Residential and commercial buildings are responsible for 6.9 million tons of greenhouse gas emissions annually. Courtesy: Jordan & Skala Engineers
Electrification is the use of electricity — distributed by the local power grid — to power devices that typically require a fossil fuel energy source, such as oil, natural gas and coal. In the AEC industry, electrification is typically seen throughout mechanical equipment and infrastructure, such as in self-contained systems.
Residential and commercial buildings’ contributions to greenhouse gas emissions is a growing global topic. In 2021, a utility provider in British Columbia produced a report citing that 6.9 million tons of B.C.’s greenhouse gas emissions were from buildings and homes. By evaluating how we heat and cool buildings and considering alternative
clean energy options, such as renewable electricity, hydrogen fuel cells or hydroelectricity, the AEC industry can significantly reduce these emissions.
It is anticipated that in the nearer future, we will see a national mandate toward electrification. Currently, in most regions of the country, owners and developers have a choice of using current technology to heat and cool their buildings or using electrified RTUs. There are few exceptions to this, as some local jurisdictions — such as Denver and Washington, D.C. — require that buildings designed and constructed moving forward do not use fossil fuels. It is anticipated that more local jurisdictions will follow suit in the nearer future.
Burning fossil fuels for electricity releases greenhouse gases, primarily carbon dioxide. In turn, these gases trap heat within the atmosphere and cause the planet’s temperature to rise. Improvements in HVAC systems technology are being made in order to reduce ozone-depleting chemical emissions.
Refrigerant, a liquid or gaseous chemical compound required for HVAC systems to cool or heat incoming air has historically contained a significant amount of harmful gas, known as hydrochlorofluorocarbons (R-22) and hydrofluorocarbons (R-410A) that negatively affect the ozone layer. The HVAC manufacturing industry has moved away from the ozone-depleting R-22 (which became illegal to produce in the United States in 2010) to a cleaner and more efficient R-410A.
In recent years, manufacturers have been quickly transitioning to an even cleaner R-454B and R-32, which contains almost zero hydrofluorocarbons and have a very low global warming potential — almost two-thirds the amount of R-410A. Plans to phase out R-410A and transition to R-32 will be complete by 2030.
FIGURE 2: As of 2023, the Department of Energy has enacted a new nationwide efficiency mandate for HVAC equipment — referred to as SEER2. It is estimated that 70% of current products in the base tier of HVAC equipment will not meet the 2023 minimum efficiency requirement. Courtesy: Jordan & Skala Engineers
energy efficiency minimums requiring HVAC manufactures to innovate equipment design to meet or exceed these minimums.
In addition to the energy code requirements, the U.S. Department of Energy (DOE) mandates minimum system efficiencies although not in concert with the energy standards and code. The DOE mandates a system’s seasonal energy efficiency rating (SEER2, formerly SEER), which is calculated
‘ In the AEC industry, electrification is typically seen throughout mechanical equipment and infrastructure, such as in self-contained systems. ’
Improvements in sustainability are also being made by increasingly more stringent energy standards and codes. Energy standards and code, primarily ASHRAE Standard 90.1: Energy Standard for Buildings Except Low-Rise Residential Buildings and International Energy Conservation Code are recognized benchmarks of the industry. These have become increasingly more stringent regarding
as follows: the total heat removed from the conditioned space during the annual cooling season, British thermal unit (Btu), divided by the total electrical energy, watt-hour, consumed by the air conditioner or heat pump during the same season Btu/ watt-hour. The higher the SEER2 rating is, the better the system’s efficiencies.
While SEER ratings have been required by the DOE since 2007, further strides are being made to reduce overall energy consumption. As of Jan. 1, 2023, the DOE has enacted a new nationwide efficiency mandate for HVAC equipment — referred to
developers should be aware of before design and construction.
In general, electrification is a more expensive method (in terms of upfront capital costs) of heating and cooling a building than using fossil fuels as energy. Currently, electricity rates (specifically on a unit energy cost basis) are significantly higher than that of natural gas, so the overall operating and utility costs of a building are naturally going to be higher with electrified HVAC units.
In addition to the overall increase in the cost of energy, as the heating and cooling manufacturers transition from R-410A to a more efficient and environmentally friendly R-454B or R-32 refrigerant, there are some additional costs that should be considered during the schematic design of a building. Although at an individual level, R-454B and R-32 refrigerant is more energy efficient than both R-410A and R-22, equipment costs will be higher than that of current equipment.
as the aforementioned SEER2 — based on nationwide regions (ranging from a rating of 14 to 15).
It is estimated that 70% of current products in the base tier of HVAC equipment will not meet the 2023 minimum efficiency requirement. This new mandate has pushed manufacturers to develop more efficient equipment.
Heat pumps that exist now are, in general, much more efficient. Systems have chipsets installed that have robust logic and learning abilities with variable speed fans that can increase or decrease airflow based on capacity demand and, in turn, use less energy; legacy mechanical equipment ran at a constant speed without the ability to adjust, potentially using more energy.
Further HVAC system efficiency can be gained by the use of energy recovery equipment that reduces cooling and heating demand by recovering waste heat from the airstream. According to the DOE, energy recovery equipment can provide energy savings of 15% or more.
Although electrification has an overall significant positive impact on the environment, there are some cost considerations that building owners and
Another significant cost impact will be the increased electrical distribution infrastructure. Because the main electrical room and sub-electrical rooms will be larger throughout a building, there will be increased costs associated with the larger equipment. Consequently, the larger rooms will take away valuable rentable square footage within a development.
Due to the increased infrastructure requirements and electrical service size, it is important for the design team to understand what type of heating and cooling system will be desired before beginning design. Some additional design considerations for electrified RTUs include that larger transformers will be required on the project site, the number and size of electrical rooms will increase (potentially doubling or tripling) and additional space may be needed on the exterior of the building.
A positive long-term cost impact will be when the property is sold later, the value of an electrified building will be notably higher than that of one that uses fossil fuels for energy, as investors recognize the value in future-proofed developments.
Specifying an intelligent HVAC system can assist with significant energy savings as they relate to the system’s sequence of operations and controls via the building management system. The control
IN THIS CASE STUDY, a hybrid HVAC system was used to achieve energy efficiency goals
While the architecture/engineering/ construction industry is seeing both a significant and rapid shift toward fully electrified systems, there are still instances where electrified systems are not able to meet the unique needs of a project — but there are several hybrid and custom options that can both meet environmental and project goals if full electrification is not an option. As technology and local municipalities continue to shift toward full electrification, we expect to see more innovation and greater use cases for a fully electrified system.
assisting with energy savings goals and efficiency.
It was imperative to the owner that their mechanical systems included energy recovery for outside air, specifically due to the outside air dampers — which was not possible using a fully electrified system.
and is included as a part of the vendor’s standard available systems. As a part of the custom heating, ventilation and air conditioning (HVAC) system’s design, Jordan & Skala’s sustainability team ran energy models to calculate the exact energy consumption and operational loads that each distribution center will be using (as the mechanical system requirements vary from project site to project site).
Over the past 10 years, Jordan & Skala Engineers has worked with a leading international big box retailer to design customized hybrid rooftop units (RTUs) for massive industrial distribution and warehouse facilities, keeping in mind both the specific needs of the owner, as well as the overall impact on the environment.
FIGURE 5: Intelligent thermostats “learn” from historical patterns and “remember” energy requirements from days and weeks prior, allowing the thermostat to adjust which times it runs to reach the desired temperature and deploy temperature setbacks during unoccupied hours. Courtesy: Jordan & Skala Engineers
This major retailer has large distribution centers across the globe, averaging about 5 million square feet per facility. With square footage this significant, it was imperative to the owner to maximize energy usage and use as least amount of energy as possible.
In the instance of this owner, using fully electrified mechanical systems did not meet the retailer’s goals, therefore the design team worked diligently with their project team to design a custom variable refrigerant flow hybrid system that met their needs while still
The Jordan & Skala Engineers team worked with the owner and manufacturer to create a hybrid, custom system that included direct expansion cooling and heat pump heating for cold climates. When the facilities reached below a specific temperature, the system would switch to full heat pump mode, which was particularly helpful for locations in the north that reached freezing temperatures in the winter months.
At the time of the system’s design, it was cutting-edge technology and therefore, the very first of its kind. Jordan & Skala worked directly with the manufacturer to achieve the owner’s goals; this system is now being manufactured
In addition to the actual design and type of the mechanical system, a robust controls strategy was also key to this retailer’s energy management and savings. As a part of this, learned controlling with schedules to operate the heat pumps — was implemented into each of the packaged units.
For example, if the system stays on a bit longer than anticipated, it will trigger load shedding. The massive controls system is operated by service stats, meaning that each distribution facility has a remote building operation system, available for virtual adjustment and monitoring 24/7, across all 200+ project sites. This type of remote controls system can be thought of like the smart thermostats that are used in households throughout the U.S., where the device uses machine learning algorithms to determine energy usage peaks and dips.
Smart controls, such as the system implemented by this owner, assist with maintaining a specific custom temperature for employees within the distribution center, keeping the owner in compliance with the Occupational Safety and Health Administration regulations.
‘ Buildings that implement sustainable practices or green building programs (such as U.S. Green Building Council LEED, Fitwel or WELL) benefit from better leasing rates and higher property values over time.’
sequence of operations — essentially, how the system in place should operate and control a given space — on a smart HVAC system does not incur any additional costs, but could save building owners and developers 15% on their overall energy bill. By using thermal storage loading and unloading (the opening and closing of a RTU’s valves to use energy that’s been absorbed by the building throughout the day via furniture, windows, walls, etc.), the heating and cooling system can use stored energy before its necessary to power on the system and create additional energy. Smart building controls are automated to maximize and optimize how energy is flowing in and out of the building and, therefore, do not require the tenant to manually adjust the thermostat.
FIGURE 4: Statistically, seven out of 10 millennials agree that prioritizing the climate is key to providing a sustainable planet for future generations — with 81% of millennial adults believing that alternative energy sources should be a national priority. Courtesy: Jordan & Skala Engineers
Intelligent thermostats “learn” from historical patterns and “remember” energy requirements from days and weeks prior, allowing the thermostat to adjust which times it runs to reach the desired temperature and deploy temperature setbacks during unoccupied hours. Additionally, smart thermostats can adjust based on a specific floor’s required heating and cooling.
For example, in some building types, because heat rises, the top floor of a building retains more heat than the lower floors and because the top floor may only need 50% of the heat required to maintain temperature as the bottom floor, the extra capacity/energy can be distributed to other floors where needed.
As high-performing and energy-efficiency buildings are increasingly more desirable by millennials and Generation Z, this, in turn, makes an owner/developer’s property more marketable and attractive to potential tenants. Statistically, seven out of 10 millennials agree that prioritizing the climate is key to providing a sustainable planet for future generations — with 81% of millennial adults believing that alternative energy sources should be a national priority.
Additionally, buildings that implement sustainable practices or green building programs (such as U.S. Green Building Council LEED, Fitwel or WELL) benefit from better leasing rates and higher property values over time.
From a marketing perspective, the AEC industry has seen a huge shift in prioritizing energy-efficient buildings. For example, in a large metropolitan area, a LEED certified (or similar) building had a competitive advantage against other similar properties; however, if you do not have a sustainable building, you will rent out significantly more poorly than surrounding properties.
In the current market, sustainability and green initiatives are no longer viewed as a “check box”; environmentally friendly practices, such as electrification and energy-efficient HVAC systems, are both required and expected.
Additionally, developers with sustainable developments as a part of their portfolio are typically more attractive to investors.
Decarbonizing the grid — generating energy from renewable sources — is a primary goal of
the Biden administration; a governmental pledge was made to achieve a carbon-free power sector by 2035. Many local governments are offering incentives for developers to electrify their buildings, with some local jurisdictions, such as Washington, D.C., mandating that by 2030, all buildings — new and existing — will need to use an energy source other than natural gas.
Energy generation and power plants will need to be more centralized and all energy will be from a renewable source; everything will be completely reliant on the grid. As more local jurisdictions are moving toward 100% electrification and as local and national energy codes continue toward clean energy, there will be a drastic increase in the usage of the power grid.
The U.S. electrical grid has already experienced an increased strain since 2020 due to a large majority of people working from home due to the COVID-19 pandemic. Additionally, climate change has caused stress on the energy grid, as well. Today, the already-aging grid is increasingly more vulnerable to weather conditions, as temperatures and natural disasters have reached an unprecedented extreme that has not been historically experienced.
One major issue that the energy grid is facing is that the average life of all power lines is approximately 30 years old; therefore, the current electrical grid in totality was designed and built for a very different world than what we live in— one that experienced a stable climate and with significantly less demand and digitization than we experience.
With the aging infrastructure of the grid, increased power demand caused by new building technology — such as air conditioning/RTUs — could result in a power overload causing blackouts. The current electrical grid cannot support 100% of all buildings to be heated and cooled using solely electricity. It will take an improved, more sophisticated power grid with significantly increased reliability and capacity in order to support 100% of all buildings to be electrified.
A recent example of this occurred when a vote against the gas ban occurred within Washington, D.C’s Construction Codes Coordinating Board due to the concern that the electrical grid would not have capacity.” The state — with lobbying from the local power company — had originally anticipat-
ed eventually moving to fully electric, but once the study was complete and the statistics were released, it was learned that the entire grid would shut down if only a portion of the buildings achieved this. Maryland decided to take a slow, phased approach in which certain types of facilities can go fully electric during certain time frames in order to stagger the number of buildings coming online at one time to not overwhelm the grid.
Another item that building owners and developers should consider is that occupants of their building will notice a difference between heating produced by a gas furnace versus that of electric heat. In general, people associate the warm feeling and audible hum of a gas furnace with warmth and comfort; overall, heating a building via a natural gas furnace is typically a positive experience for those within the building.
Owners and developers should be aware that there is an educational component to heating using electricity that should be taken into consideration. As more local jurisdictions adopt electrification and more buildings use clean energy, the need to educate will decrease. Tenants will begin to adjust to the standard results of using an electric heating system.
As the AEC industry continues to focus on green and ESG initiatives, it is valuable to consider all sustainable options. Whether you choose to go fully electric or take a hybrid approach with your HVAC systems, future-proofing your client’s building with sustainable systems will help attract tenants and investors, attain an overall healthier environment, as well as potentially achieve a compelling return on investment. cse
Chris McDaniel, PE, LEED AP, is a principal at Jordan & Skala Engineers, where he oversees all Washington, D.C.-area projects for the firm. He has more than 25 years of proficiency in mechanical engineering and project management, as well as 11 years of mechanical system installation experience.
Sven Peulen, PE, LEED AP BD+C, is mechanical discipline leader at Jordan & Skala Engineers. He has been with the company for 12 years and has more than 17 years of mechanical engineering experience.
u The architecture/ engineering/ construction (AEC) industry is shifting toward sustainability and environmental, social and governance (ESG) initiatives, with a trend toward electrification, green rooftops and clean energy.
u This movement is necessary to reduce negative impacts on the environment and climate change, as younger generations see green practices as critical.
u The AEC industry is making improvements in sustainability through the electrification of air conditioning units and green rooftop units, as well as by increasing efficiencies of heating and cooling systems to meet stricter energy efficiency mandates in building codes.
Jack DeVine, EIT, Arup, Boston
In situations where building compartmentalization strategies using fire-resistance rated glass may not be an option, it may be possible to use sprinklers to design a code-compliant passive fire protection solution
Building compartmentalization plays a pivotal role in the building’s overall fire and life safety strategy. With fire-resistance rated construction, buildings can be effectively separated into multiple areas that limit the spread of fire and/or smoke from one compartmentalized area to another. This can keep occupants and building contents protected for a longer duration in a fire event, which allows more time for a safe evacuation, allows more time for first responders to arrive and mitigate the fire’s effects and can keep critical parts of a building safe and functional.
Traditional walls with a fire-resistance rating have been given that rating after undergoing an ASTM E119: Standard Test Methods for Fire Tests of Building Construction and Materials test. This test exposes one side of the barrier to fire following the ASTM E119 time-temperature fire curve while closely monitoring the temperature on the other side of the wall and the structural integrity of the wall.
The fire rating of these walls is typically provided through noncombustible materials on the outside of the wall assembly with insulating materials on the inside. Passive fire protection like this is seen in a vast majority of buildings.
However, in buildings or spaces where certain architectural visions may be desired, the use of traditional fire-rated construction may not be appropriate or preferred. Interior glass paneling is frequently used to separate different rooms. Without any additional protection, it is expected that unrated glass paneling would be compromised due to an adjacent fire, which would render the partitions useless in providing the required fire-resistant separation between the adjacent spaces.
Atrium spaces are required to be separated from adjacent, nonatrium spaces by either a onehour fire barrier or a horizontal assembly per the 2021 edition of the International Building Code (IBC Section 404.6). This boundary separating the atrium is required to aid a smoke control system (also typically required for atriums by the IBC) in exhausting smoke from just the atrium space and protect occupants located throughout the rest of the building. In most cases, the use of a one-hour fire barrier does not present an issue. However, in cases where glass partitions are used as barriers, a possible issue can arise. There is quite a significant cost difference between an unrated interior glass partition and a one-hour rated glass partition that would be compliant with IBC Section 404.6. As such, in cases where a glass partition is used along the boundary of an atrium, IBC Section 404.6, Exception 1 details the prescriptive path to code compliancy.
In lieu of a one-hour fire barrier, a glass partition forming a smoke partition can be used. If an unrated glass partition is desired, then it needs to comply with the following:
• Automatic sprinklers shall be provided on both sides of the separation wall and doors (or only on the room side if there is not a walkway on the atrium side). These sprinklers shall be between 4 and 12 inches from the glass and no more than 6 feet apart from each other. The system shall be designed such that the entire surface of the glass is wet upon activation of the adjacent sprinkler (i.e., no mullions).
• The glass partition shall be installed in a gasketed frame such that the frame deflects without breaking before operation of the sprinkler system.
FIGURE 2: A noncompliant sprinkler installation along glass partitions; one sprinkler is only sufficient to protect 6 feet of glass partition. Courtesy: Arup
FIGURE 3: A noncompliant sprinkler installation along a glass partition. Though the two sprinklers are adequate to protect the length of glass, both sprinklers are located too close to the adjacent wall. Courtesy: Arup
• All glass doors provided along the glass partition shall either be self-closing or automatic-closing.
From a fire protection standpoint, the first clause is an incredibly rigid set of design parameters. IBC requires sprinklers along an atrium boundary to be no more than 6 feet apart. However, NFPA 13: Standard for the Installation of Sprinkler Systems Section 10.2.5.4 sets the minimum distance between sprinklers to 6 feet. That means the distance between sprinklers along the atrium boundary must be exactly 6 feet unless baffles are provided to prevent cold-soldering between sprinklers. Because of these stringent requirements, the architect and other engineers need to coordinate their design around the sprinklers along the atrium boundary. Additionally, the requirement that sprinklers are a minimum of 4 inches laterally
• Learn how to use sprinklers to maintain fire-resistance rated boundary around an atrium.
• Learn how to use sprinklers to maintain fire-resistance rated boundaries around other fireresistance rated elements.
• Understand the importance of coordinating the use of active fire protection in lieu of passive fire protection early in the design phase of a project.
from an adjacent wall (NFPA 13 Section 10.2.5.3) can compound the issue. Consider a length of unrated glass along an atrium boundary that is 6 feet, 6 inches in length. One sprinkler is not sufficient to protect this length of glass — one sprinkler can only protect a maximum of 6 feet (see Figure 2).
Therefore, two sprinklers are sufficient to protect the length of glass, however, note that sprinklers need to be 6 feet apart per NFPA requirements to prevent cold soldering. That means that one or both sprinklers will be placed within 4 inches of the adjacent wall, which is no longer compliant with NFPA 13 (see Figure 3).
This leaves two options that will be code compliant. Option 1 is to install a baffle between the two sprinklers in accordance with NFPA 13 Section 10.2.5.4.2 (see Figure 4). Though this is technically an option, it may not be aesthetically preferable to
install a baffle in this area and may be a deal breaker from an architectural standpoint. If the installation of a baffle is not an option, then the only option that is left is to increase the length of glass to a minimum of 6 feet, 8 inches or to shorten the length of glass to a maximum of 6 feet (see Figure 7). To facilitate a code-compliant design, it is best to bring this up earlier rather than later in the course of a project to give others ample time to react and assure the design is compliant with IBC and NFPA.
Another item to consider is the provision that “the entire surface of the glass is wet upon activation of the adjacent sprinkler.” It is this clause that helps the glass partition perform like a one-hour fire-rated assembly. This clause does not detail exactly how the entire surface should be wet upon sprinkler activation.
A RESEARCH LAB fire and life safety design team determined the use of sprinklers would be used where possible
A new research laboratory building is currently under construction in Massachusetts. This building contains seven stories above grade, six of which are connected by an atrium in the center of the building. Because this is a research laboratory, there are relatively high amounts of hazardous materials that may be present in the building.
As such, the building owner and architect chose to separate the building into multiple control areas. Please note that the complete design of this building is not yet available to the public and, as such, images and figures of this building will be diagrammatic by nature.
The figures show a very simplified version of how each floor is separated. The floor is generally separated into three separate control areas (see Figure 5). Control area 1 is a nonlaboratory space and is also shared across floors (as it encompasses the six-sto-
FIGURE 5: Typical control area layout for a new research laboratory in Massachusetts. Courtesy: Arup
ry atrium). Control areas 2 and 3 on each floor are the laboratory spaces where most of the hazardous materials are expected to be found.
The floor is also separated into spaces that are and are not a part of the atrium (see Figure 6). Some of the separations between the control areas and the separation between the atrium spaces and nonatrium spaces entirely consist partially of glass paneling.
The presence of an atrium and multiple control areas in the building, compound-
ed by the vast amount of glass paneling, made this a complex situation from a life safety and fire protection standpoint. It was determined early in the building design that the use of sprinklers would be used where possible in lieu of common passive fire protection measures to achieve the required fire resistance ratings.
The most basic part of the design for this space was the fire-resistance rated separation between control areas 2 and 3. The boundary between these two spaces did not consist of any glass paneling with the exception of a few glass doors. The glass doors were required to be made of rated glass because window sprinklers cannot be used for operable openings.
The remainder of the separation between the spaces was provided by the standard fire-resistance rated fire barriers, with no need for additional protection by the automatic sprinkler system.
For the separation between nonatrium and atrium regions encompassed within control area 1, the closely spaced sprinkler rule detailed by International Build-
However, IBC commentary notes that curtain rods, draperies and similar fixtures would impede the wetting of the entire surface; as such, any of those fixtures should be located at least 12 inches from the window surface.
Furthermore, the presence of mullions along the glass paneling may obstruct water spray and could prevent the wetting of the entire surface. As such, the use of mullions should be closely examined by the design team to confirm that the system still meets the intent of the code. It is also important to take note of manufacturer specific guidelines pertaining to obstructions to sprinkler spray, like vertical and horizontal mullions in a glass panel wall.
Lastly, the use of closely spaced sprinklers along atriums does not classify the boundary as a onehour fire barrier in all other situations. Rather, it is an alternate approach for providing code allowed
atrium separation. As such, the glass partition with closely spaced sprinklers cannot be used as a firerated wall/barrier/partition in any other situations where needed.
In lieu of unrated glass paneling walls with closely spaced sprinklers, standard fire-rated barriers should be used as enclosures for fire pump rooms, exit passageways, shaft enclosures and control area separations among others.
FIGURE 4: Option 1 for a compliant sprinkler installation along a glass partition: a baffle separates the two sprinklers located less than 6 feet apart. Courtesy: Arup
ing Code Section 404.6, Exception 1 was applied. The glass doors along the boundary were specified to be self-closing and gypsum soffits were provided along the glass boundary so that concealed pendent sprinklers could be spaced every 6 feet along the boundary. These sprinklers are installed within 4 to 12 inches of the glass they are protecting.
Though the design and installation requirements for these closely spaces sprinklers are quite rigid, it was determined that this was the significantly more cost-effective and aesthetically desirable than the use of rated glass partitions.
Lastly, the most complex part of the design was the boundary between the atrium and the lab spaces. Practically the entire boundary between these two spaces consisted of glass paneling. Though it is an eye-catching design, it obviously presents issues when it comes to compartmentalization and separation. The glass paneling makes up the boundary between atrium and nonatrium spaces. However, it is not correct to use the same rules from IBC Section 404.6,
FIGURE 6: Typical atrium separation for a new research laboratory in Massachusetts. Courtesy: Arup
Exception 1 because the control area separation requirement is more stringent than the atrium separation. Separation between control areas does not allow for the same sprinkler alternative that is accepted for atrium separations with closely spaced sprinklers.
As such, the window sprinklers that provide a listed two-hour fire-resistance rating were used instead. The two-hour fire-resistance rating of these sprinklers provided a sufficient fire-resistance rating to separate adjacent control areas, and
exceed the minimum required one-hour fire-resistance rated atrium separation. On the ground level, window sprinklers were designed to wet both sides of the glass surface. On higher levels, the window sprinklers only had to wet the entire surface of the lab (nonatrium) side of the glass, as there were no occupiable walkways on the atrium side. Having no occupiable walkways mean that there does not exist the reasonable threat of a fire on the atrium side to the glass, which would have already been mitigated by the window sprinklers on the lowest level. This approach was specific to the variance associated with this atrium protection. Because the use of window sprinklers to achieve a fire-resistance rating is not a prescriptively compliant approach in Massachusetts, a variance application was submitted and accepted to confirm this approach with the authority having jurisdiction as providing an equivalent level of fire protection and life safety intended by the code.
FIGURE 7: Option 2 for a compliant sprinkler installation along a glass partition: the glass partition has been lengthened to 6 feet, 8 inches to allow compliant distance between sprinklers and between a sprinkler and the adjacent wall. Courtesy: Arup
csemag.com
Fire protection
uThis article will teach how active fire protection (in this case an automatic sprinkler system) with unrated glass paneling can achieve a fire-resistance rating or a code compliant alternative to a fireresistance rating.
uNFPA 13: Standard for the Installation of Sprinkler Systems defines design requirements for fire sprinkler systems.
Atriums are not the only features that need to be separated by fire-rated assemblies in buildings. Fire-resistance rated walls, partitions and barriers, along with smoke partitions and barriers, are found in practically every building. If one is trying to use a sprinkler system to achieve a proper fire-resistance rating, then these fire-rated elements need to be analyzed differently when not located along an atrium boundary. If unrated glass partitions are being used along an element of fire-rated construction (which could be seen along control area separation, exit passageways, walls separating the building into multiple alarm zones and along horizontal exits, etc.), then a different approach is required.
There is a solution that can be used to provide a true fire rating to otherwise unrated glass paneling. Special application sprinklers can be used so that, when activated, water discharges directly onto the glass it is protecting. When installed in accordance with the manufacturer's precise design criteria, these sprinklers wet the entire surface of the adjacent glass and can provide a two-hour fire-resistance rating to the glass panel. This assembly with the special application window sprinklers requires testing and passing of the ASTM E119 test, the same test that typical rated assemblies must go through.
As mentioned above, the installation requirements for window application sprinklers are very strict, far stricter than those prescribed for closely spaced sprinklers by IBC. Though the specific requirements vary between manufacturers, there are some general criteria that need to be followed. There are a few less stringent requirements for sprinkler spacing for window sprinklers than closely spaced sprinklers, such as manufacturers allowing 6 feet and to up to 12 feet between the sprinklers. Also, depending on the manufacturer, the sprinklers need to be between 4 and 12 inches from the glass.
When designing for the use of window sprinklers, it is important to coordinate the details of
the glass paneling with architects. Vertical mullions within the glass paneling create an obstruction of water spray on the glass. If not accounted for in the design, vertical mullions may prevent the wetting of the entire glass surface, therefore compromising the integrity of the fire-rated assembly. Vertical mullions are still allowed on the glass paneling, but each individual section of glass between the mullions needs to be protected individually.
Horizontal mullions, on the other hand, are not permitted within the rated assembly, as there is no feasible way for water to wet the entire surface. Window sprinklers are required to be within a certain distance of the protected glass as well. There is also a maximum height of the glass partition that is allowed, as well as glass type characteristics that need to be followed.
To mitigate the risk of a fire compromising the atrium boundary before the sprinklers can activate, there is also a manufacturer’s requirement to prevent the buildup of combustibles along the glass partition. Manufacturers recommend the use of a 36-inch pony wall up against the glass; however, other methods could be considered acceptable to the authority having jurisdiction (AHJ). All of these stipulations should be discussed with the architect to make sure that their design is copacetic with the window sprinkler requirements.
The long list of requirements for window sprinkler installation should not deter one from specifying their use in spaces where they may be necessary.
However, because of the amount of coordination needed between the fire protection engineer and the architect, code consultant, AHJ and others, it is vital that this topic is brought up early in the design process. The earlier this topic is discussed and resolved, the less stressful the late stages of design will be.
Additionally, it is important to note that this approach is not allowed prescriptively unless it is specifically approved by the AHJ through the means of an alternate means and methods request per IBC Section 104.10. cse
Jack DeVine, EIT, is a fire engineer at Arup. He has growing experience in fire protection system design, code consulting and performance-based design through fire, smoke and evacuation modeling.
Air control solutions from Ruskin® give the freedom to do more. With innovative damper, louver and air measuring systems, Ruskin continues to lead the industry with solutions to meet the most demanding air handler requirements.
Brandon Stanley, PE, LEED AP BD+C, IES, SmithGroup, Chicago
As a complement to other ANSI/IES lighting practice standards, LP-16 provides a roadmap for documenting lighting control intent and sequence of operations throughout the design process
ANSI/IES LP-16-22, Lighting Practice: Documenting Control Intent Narratives (CIN) and Sequences of Operations (SOO), as its primary objective, provides a standard for documenting lighting control design intent. Once that intent is developed by the designer, in coordination with the owner, user and/or architect, it needs to be translated into contractually enforceable and buildable construction documents that are clear and easy to understand by the contractor, manufacturer and installer.
• Understand the difference between the control intent narrative and the sequence of operations and how they are used.
• Identify different standardized control strategies and learn to integrate their requirements into design and construction documents.
• Understand how to use a lighting control matrix to simplify lighting control sequence of operations.
The inaugural 2022 edition of LP-16, developed in collaboration between the American National Standards Institute (ANSI) and the Illuminating Engineering Society (IES), is not intended to be a standalone document or a design manual. In coordination with ANSI/IES LP-6, Lighting Practice: Lighting Control Systems – Properties, Selection and Specification and ANSI/IES LP-8, Lighting Practice: The Commissioning Process Applied to Lighting and Control Systems, LP-16 is intended to be a reference of best practices for developing and documenting the functionality of the lighting controls systems.
As a result, owners and occupants will be provided with a lighting system that functions as intended with less confusion and errors during the construction process.
ANSI/IES LP-16 outlines two documents that define the lighting controls system.
The CIN is meant to outline the requirements of the project and should be written in a format that is easily understood by all parties. The CIN should start with how the project owners and/or users intend the lighting controls system to operate including how the users will interact with the system and how the system should respond to inputs. If the overall lighting controls system is made up of multiple connected systems, the CIN should define how these systems will interact with each other.
The CIN should be written in complete sentences and in plain language and should complement the owner’s project requirements (OPR), conveying how the needs of the owners and/or users will be met by the lighting controls system. For example, electrical room lighting narrative might include:
“Electrical rooms should have two manual switches and should not rely solely on automatic shut-off. Normal lighting should be controlled by manual switch and occupancy sensor. Emergency lighting should be controlled by a separate manual switch and shall turn on to 100% upon loss of normal power.”
The SOO is meant to be a part of the construction documents and is intended to outline in precise terms and instructions how the lighting controls system shall perform and respond to inputs from individual occupants and connected systems and sensors. The SOO is an enforceable
Install example showing wall controls and combination occupancy sensor/photocell.
Courtesy: SmithGroup
contract document and shall be written in unambiguous instructions to the contractor, integrator and/or commissioning agent.
An example that might be found in the SOO as it relates to electrical room lighting is as follows:
“A manual switch shall be provided to control all normal lights in the space. Ceiling occupancy sensors shall be provided such that all spaces within the room are within the minor motion range of the sensor, on all sides of free-standing equipment and shall be connected to the manual switch. Normal lighting shall turn off after 30 minutes of vacancy. Emergency lighting shall be controlled through a separate manual switch and shall be provided with a UL 924 relay. Emergency lighting shall turn on to 100% upon loss of normal power.”
It is important that the design of the lighting control system be considered at all phases of a project. Often, design of lighting controls is deferred to the later phases of the design process. This could lead to missed opportunities for integration or deviations from client or owner preferences outlined in earlier stages of design.
ANSI/IES LP-16 outlines ideal steps to consider at each major design milestone, including review and approval by applicable parties. Both the CIN
‘ It is important that the design of the lighting control system be considered at all phases of a project.’
and the SOO should be developed at different levels depending on the design phase as outlined below.
The CIN should start its development during the schematic design (SD) phase. Developed in conjunction with the OPR, the CIN should translate the overall needs of the owners and/or users into a space-by-space description of the lighting controls system. If the owner and/or user needs remote control or integration with heating, ventilation and air-conditioning (HVAC) or audiovisual (AV) systems, those requirements should be included in the CIN during this phase.
Local codes, standards and certification standards that will affect the design of the lighting control system should also be noted in the CIN at this time. Particular attention should be given to the locally adopted energy code. Although the two primary standards adopted as local energy codes, namely ASHRAE Standard 90.1: Energy Standard for Build-
u By referencing a standard practice, design and documentation can be simplified to reduce confusion and errors during construction, commissioning and use of lighting control systems.
u ANSI/IES LP-16-22 provides a standard for documenting lighting control design intent.
u The control intent narrative and the sequence of operations are two documents outlined in ANSI/IES LP-16-22 that define lighting controls system.
ings Except Low-Rise Residential Buildings and the International Energy Conservation Code, are aligning version by version, understanding the minimum requirements of the adopted version can have significant effects on control devices requirements, control strategies and sequences of operation.
At the end of the SD phase, the CIN should be a thorough outline of the system and the design team should solicit feedback and approval of the approach by the owners and/or users. The SOO is typically not defined during this design phase.
The design development (DD) phase is the most critical time in the development of both the CIN and the SOO. During this time, the designer will detail out all the spaces in the project and may further describe each space’s intent. During SD, the CIN may indicate that conference room lighting controls shall integrate with the mechanical systems.
During the DD phase, this requirement may be refined to indicate that the office lighting controls shall integrate to the building’s building automation system (BAS) through occupancy sensor dry contacts for demand control ventilation. The CIN may also detail the differences between large and small conference rooms as well as ones that have integration with shades and AV systems. If the conference room has multiple zones, such as general lighting, conference table pendant and perimeter wall-wash, the designer should detail out how those different zones may be triggered.
DD is also the phase when the SOO starts to detail the system requirements as outlined in the CIN. Each space within the CIN should have a corresponding space in the SOO. At this stage in the design, it may be too early to define exact thresh-
olds and setpoints, but the structure of the SOO should be set up to easily include those later.
In the above multiple zone conference room example (see Table 1), the SOO may define each zone with multiple setpoints and use a placeholder for the precise values:
• General lighting: a: 0%; b: x%, c: y%; d: z%; e: 100%.
• Conference table pendant: a: 0%; b: x%, c: y%; d: z%; e: 100%.
• Perimeter wall-wash: a: 0%; b: x%, c: y%; d: z%; e: 100%.
Just as during the SD phase, it is important that the owners and/or users review and provide feedback and ideally approval, of both the CIN and SOO. If the design team works closely with the owners and/or users during SD and DD, the CIN should be essentially complete at this point and the SOO should not need major revisions.
In the construction documents (CD) phase, the SOO turns into a contractually enforceable document. At this point, the exact requirements for each space shall be detailed and aligned with all other documentation such as the specifications, system diagrams, zoning requirements and panel or relay schedules.
If the design team has worked closely with the owners and/or users, this phase should mostly consist of further detailing out each space. If major changes arise during the CD phase, it is important that the OPR is referenced for compliance and the CIN is updated to align with the new direction.
A LIGHTING CONTROL matrix can be a valuable tool for documenting control intent and a sequence of operations. Often it is easier for contractors, lighting controls manufacturers and design team members to track lighting control requirements on a roomby-room or space type basis through information indicated on the drawings. Although its best to include detailed sequences for spaces with complicated or atypical requirements in the specifications, having a quick reference right on the drawings will save time across the board.
On a recent medium-sized, multifloor office tenant improvement project for a confidential client, SmithGroup elected to simplify the controls documentation down to a lighting controls matrix on a space type basis. Because the client didn’t have a standard for lighting control systems, the specification was written on a performance basis and was limited to systems that were familiar to the client and successfully installed at other office sites around the country.
control strategy. Directly from this matrix, the designer and the contractor can determine which spaces need switches, dimmers, occupancy sensors, photosensors, HVAC contacts, etc.
‘ The matrix also lists the
illumination target and the manual control device type, as well as a basic sequence of operation.
In addition to what devices are present, the matrix also lists the illumination target and the manual control device type, as well as a basic sequence of operation. The contractor can see what the intent is for each control device, whether it is a simple dimmer, a multizone device with presets or a combination control device with integral occupancy sensor. By indicating the switch type in the matrix, the designer can easily confirm that all similar rooms have similar control devices and can clean up the drawings to make more room for other critical information useful to the contractor, like zoning and circuiting (see Figure 3).
’
Because the allowable systems had different design requirements like some systems with standalone daylight photosensors and others with combination occupancy sensor and daylight photosensors and different device performance limitations like different occupancy sensor range and room coverage, the lighting control matrix became the primary documentation for what devices were required in the various spaces. The only devices indicated on the plans were the coordinated location of manual control devices (see Figure 2).
If you take a look at Table 1, you can see that each room is indicated and combined with other rooms of the same space type and
During the bid phase, the bidding contractors reached out to the local representing agencies of the approved manufacturers. The agencies developed preliminary shop drawings as part of their quote to the contractor. The agency representatives had no issues understanding the matrix and were easily able to quote a complete system based on the spaceby-space control intent without supporting plans indicating device quantity and location.
Documenting control requirements through a matrix was particularly helpful in the open office areas where sensor range and quantity varied between the approved manufacturers. Instead of quoting the number of devices on the drawings, the agencies quoted the number of devices required to meet the sequence of operations.
FIGURE 2: Example lighting control matrix. Courtesy: SmithGroup
The CD phase is also the last chance to verify that all sequences meet the minimum requirements of the locally adopted energy code. At the end of the CD phase, the CIN, SOO, drawings and specifications shall be in full alignment and the owners and/or users shall approve the complete set of documents before bid and construction.
Section 5 of ANSI/IES LP-16-22 details several common control strategies, both by strategy and by space type. Within the text, examples are provided for both the CIN and the SOO. It is not the intent of the standard for a designer to copy these examples verbatim but use them as a reference and to tailor them to a specific project.
By reviewing the examples, a designer can understand the difference in language and level of detail between the CIN and SOO. Although not exhaustive, the standard does reference several control strategies, such as high-end/low-end trim, emergen-
BECAUSE of the performance-based approach, the controls package was aligned with the luminaire package by the awarded contractor and both were procured together to allow for bulk pricing from the local agency. This resulted in a cost savings for the owner.
During the construction phase, the selected manufacturer’s local representing agency provided shop drawings of the lighting controls as a part of the submittal review and approval process. The design team was able to easily verify the control intent was met by comparing the provided shop drawing layouts against the lighting control matrix.
FIGURE 3: Defining setpoints for single-zone spaces via drawing details.
Courtesy: SmithGroup
The agency also included the control matrix on each plan of the shop drawings, further simplifying the review and approval process. As a result, the submittals were reviewed quickly and returned promptly with only a few minor comments and there were zero requests for information related to the lighting control system during the construction phase.
cy response, room partitioning and spectrum adjustment that may not be found in every project type and therefore provide a level of detail that a designer may not arrive at when first considering how to develop those strategies into the CIN and SOO.
For this reason, it is important to reference the standard for guidance and examples on each new project.
As lighting control systems become more sophisticated, some can control or interface with other building systems such as AV, HVAC, security systems or motorized window shade controllers. This interface often involves multiple contractors working together to realize the design intent.
Components that allow for communication with the lighting control system and implementation of the lighting control SOO are not part of the lighting control package, such as touch-panels, thermostats, network switches or communication gateways. When components that interface with other systems are part of the lighting control package, the contractor and integrator need to fully understand what needs to be communicated and how, to achieve the desired functionality.
Clear, concise and complete documentation is necessary, to ensure that all parties understand their scope of work and how the systems need to communicate to achieve the desired result. Section 6 of ANSI/IES LP-16-22 provides examples of how these other systems may integrate with the lighting control system, which system initiates an operation and how each system shall respond.
For large projects with complex control strategies or significant quantities of differently controlled spaces, a written SOO included in the specifications may be the best way to document the lighting control functionality. For many projects, however, having as much information in the drawing set is the best approach to ensure the contractor, manufacturer and integrator have the complete picture. This is where a lighting control matrix can provide a complete and concise representation of the design intent.
The lighting control matrix should still consider all the elements of the SOO. This may
Paul Daniel, LC, LEED AP, HDR, Philadelphia
As health care projects become more patient oriented, human-centric lighting design and lighting controls are taking center stage
o achieve the best lighting control strategies, it is imperative to look at each type of space separately and define criteria that is useful for the design. For example, a health care environment involves a plethora of different programs and the individuality of each space affects the lighting control strategy dramatically.
• Learn about three different lighting experiences in a health care environment.
• Understand how to apply humancentric lighting controls to health care projects.
• Observe the challenges in achieving human-centric lighting controls and corresponding solutions.
As an electrical engineer or a lighting designer start on a new project, they are usually faced with comments from clients and users about the importance of lighting controls in a health care environment. The ease of controlling lighting is imperative for a great patient experience.
In some existing facilities, the lighting can be harsh and directional. The ability to control the lighting while in bed can be nonexistent. Patients can struggle to walk through a crowded room with the IV pole just to turn the lights on and off. Human-centric lighting design could lead to a positive patient experience in health care facilities. As building designers embrace technology and the need for net zero, the careful balance between cost, comfort and energy efficiency is the way to the future. Simply providing a lighting controls solution that meets minimum code requirements might not be the best approach, especially when designing state-of-the-art health care facilities.
How can a lighting designer achieve a human-centric experience using lighting controls? The client and the users must be on board with the design and in tune with the future facility. A health care project involves the interactions of multiple experiences including the patient, visitor and staff experiences. Each experience type carries a diverse set of requirements from the code perspective, and also from the human or user’s side.
These requirements should be tailored to the needs of each facility. The complexity of the design requires the proper layering of lighting and lighting controls to achieve maximum comfort for
the patient while maintaining a highly technical and functional space for the caregiver.
Let’s study each category individually: Patient experience: It’s important for a patient to feel comfortable when coming into a hospital environment. Proper lighting design can play a key role in patient outcomes, which is augmented by the lighting control experience. When a patient has personal control, they can feel less stressed in an already-stressful situation. In fact, ANSI/IES RP-29-22: Recommended Practice: Lighting Hospital and Health Care Facilities reinforces the need for flexible patient controls to assure patient comfort and satisfaction.
Increasing patient satisfaction is one important metric hospitals look for to achieve the total performance score (TPS) managed and rated by The Centers for Medicare & Medicaid Services. A low TPS can reduce Medicare payments to a hospital due to poor satisfaction under the “person and community engagement domain” and due to frequent re-admissions. Body of evidence referenced by ANSI/IES RP-29-22 concluded that patient comfort also aids in faster healing and a quick turnaround. This in turn leads to better infection control as the patients’ stay in the hospital shortens.
Visitor experience: A visitor’s experience is similar, as the goal of controls for that category is to provide intuitive, easy-to-use controls. Providing care for a loved one should not come with the frustration of operating multiple keypads and complicated controls. Incorporating intuitive localized controls into the lighting design for the visitor zone provides localized lighting to the area without disturbing the patient’s sleep and respite. This helps reduce the trial-and-error efforts for a visitor to adjust the lighting in the visitor zone.
Staff experience: Staff controls can be used to help increase their efficiency and accuracy. For instance, lighting controls that turn on controlled beam task lights at staff work zones are strongly desirable. These controls should be clearly defined and located near their tasks as well as near the entrance to decrease the need for staff to find the proper switches. Touchless controls for task lighting are also strongly encouraged to reduce staff contamination as described in the ANSI/IES RP-29-22 Lighting Controls Systems section.
To achieve the best lighting control strategies, a health care case study will be used: Penn Medicine’s Pavilion at the Hospital of the University of Pennsylvania. The state-of-the-art facility was designed and constructed by the integrated project delivery (IPD) team PennFIRST, which included HDR, Foster + Partners, BR+A, L.F. Driscoll and Balfour Beatty.
The facility opened in October 2021 after six years of working through an IPD process. During the design — which involved the colocation of the team, including client, designers, engineers, construction managers, estimators and contractors lighting controls were at the center of multiple in-depth conversations focused on patient experience and comfort. Each area was discussed with the users, client and contractors to achieve the best design solution possible.
For the hospital, the patient room had to achieve maximum comfort: with zones for ambient illumination, patient reading, night light, charting, sink and visitor zones. The IPD team produced a solution that integrated all lighting controls via a bedside touchpad. The touchpad can do the following: control lighting and heating, ventilation and air conditioning (HVAC); achieve digital visual communication with the care team; enable patients to order food; control the TV; and enable communication with loved ones outside the facility.
The controls depended on a visual screen that was easy to read and understand, so patients have an intuitive interface without the need to learn
FIGURE 2: Patient room with lighting keypads on the headwall and in the family zone. Ambient, uplight, charting and family zone on. Shades are up for daylighting and views toward the city. Courtesy: HDR, Dan Schwalm PennFIRST
csemag.com
u When designing lighting control systems, it’s important for the electrical engineer or lighting designer to consider all aspects of use.
u Energy codes and standards challenge lighting designers to implement the most energy-efficient option for the health care project.
FIGURE 3: Caregiver station to override fixtures above patient rooms and linear corridor lighting separately. Charting station window control is on transparent mode to check on patient while the door is on opaque mode for privacy. Courtesy: HDR, Dan Schwalm PennFIRST
modern technologies. Most lighting zones mentioned above could be controlled and dimmed from the touchpad individually. Each zone is shown on the app, so the patient doesn’t have to guess the appropriate zone.
From the touchpad, the patient has control over their environment and they can dim the different zones as desired to achieve the best scenario possible for their comfort. They can also control the shades, lowering and raising them as desired. The scenarios are unlimited and flexible so different lighting settings can be achieved when the patients want to watch TV, read, order food, communicate with the care team or just relax.
For the less savvy patients, the traditional integration with the nurse call system was also introduced to control patient-oriented zones, such as the reading and ambient zones. An “all off” button on the nurse call was also introduced in case the nurse leaves the room with some lights on.
The caregivers also control a given set of keypads at localized areas around the room. At the charting station, two buttons control the tight beam chart task light, to not disturb the patient and the uplight in case more lighting is needed. In addition, the bedside station controls the exam lighting, reading light for the patient, ambient illumination and uplights.
At the main entrance, a keypad is divided into two clear sections: the upper section offering easy access for the patients/visitors to control the ambient illumination and uplights, while the lower section allows caregivers to control the charting lights
so they can see their way into the room without disturbing the patient with overhead lighting.
The visitor zone has its own keypad for local controls of the lighting in that zone, as well as control for the window shades. All buttons on the patient room keypads are properly labeled with a master raise and lower key to control the lights.
Patient corridors are critical spaces, where multiple functions coexist. Patient corridors are used by visitors as wayfinding, for the circulation of patients and as a potential work zone for caregivers in case of emergency. The control system must accommodate each function.
The lighting in the space consists of a series of linear lights on the core wall and a wall wash on top of each patient room for wayfinding. The lighting control system schedules the lighting to go on at 100% level in the morning, until 7 p.m. when the linear lights gradually dim down to 30% and the wall washers dim down to 50%. This creates a comfortable, human-centric environment for the patients where they can sleep at night and avoid spill lighting into the rooms.
For the remaining hours of visiting time, there is still ample illumination above the patient bedrooms for proper navigation. In the case of clinical emergency at nighttime, overrides are provided at each nurses’ station using an intuitive touchpad. The caregivers then can attend to a patient in need of care, in the corridor with ample illumination.
Charting stations are also part of the corridor and they are intended for the caregiver to process information and medication locally. One charting station can monitor two rooms at the same time. A linear fixture with regressed lens was used to reduce light spill into the rooms. Each charting station lighting is controlled separately for maximum control and to avoid patient discomfort during quiet times.
The doors and windows into the patient rooms include smart glass for patient comfort. The glass can be controlled by the caregiver at the charting station, to turn the window and door separately. This ensures that the patient can keep their privacy with the door on opaque setting, while the caregiver can monitor the patient through the window on
the transparent setting. The patient also has control of both the glass and window from inside the patient room unless the caregiver overrides that functionality.
Emergency life safety lighting in the corridors is controlled via a UL 924-rated device that ensures the lighting in the corridors are dimmed and controlled together with the regular lighting settings. The days of having dedicated noncontrolled emergency fixtures in a patient corridor are gone. The patient's experience is a primary goal in ensuring their comfort, therefore controlling the spill light into patient rooms at night is critical.
What are the challenges that designers face to achieve a more human-centric experience for a health care environment? Electrical engineers and lighting designers are faced with challenges due to updated, more stringent energy codes. Moreover, they are also challenged with an ever-changing environment of technologies and health care criteria.
The job of the designer is to assess those challenges and establish a set of priorities to meet client aspirations, project goals, budget and code.
Due to the advancement of tunable white technology, circadian rhythm entrainment became a reality. Tunable white technology is the ability of changing the color temperature of a source following the black body curve by mixing two or more different color sources. Entrainment is a fundamental property of circadian systems by which the period of the internal clock is synchronized to the period of the entraining stimuli.
Research cited in the health and wellness section of ANSI/IES RP-29-22 reinforces the effects of entraining patient’s circadian rhythm on increasing patient outcomes, accelerating healing and creating a human-centric environment for the patient to overcome the harsh clinical environment. Tunable white technology research cited by the health and wellness section of ANSI/IES RP-29-20 also suggests the amelioration of the caregiver’s health and work environment especially for the ones that work late and night shifts.
However, tunable white technology comes with a slew of challenges to the lighting control system.
There is currently little standardization of the technology which creates different comparative color temperature between different fixtures depending on binning. LED binning is a practice carried out to ensure high quality and consistency in the performance of LED light output and color. The technology is also still cost prohibitive in most health care projects and the cost is added to both the lighting fixtures and the lighting controls.
To overcome some of these challenges, it is recommended to put different fixture types on separate zones to avoid the difference in color temperature. This way each individual lighting type can be tuned separately to achieve the desired color temperature in the space. Another recommendation is to use the same manufacturer for the tunable white fixtures so the technology and the dimming rate, as well as color consistency, is the same.
Newer Digital Addressable Lighting Interface (DALI) protocols such as DALI DT8 and DALI-2 protocols also currently offer a solution for some manufacturers to provide a good standardization to follow the black body curve and provide another level of consistency.
As described in the case study, the future of health care lighting is through using controllable emergency lighting. To provide a human-centric comfortable solution, emergency lighting cannot be left on at night. This can be a burden to the budget, especially if every fixture is provided with a separate emergency module or if they need to be circuited to both the normal and the emergency circuits.
A suggested solution is to put long run fixtures on the same zone and circuit to use the same emergency module. Moreover, keeping the emergency lighting to the required minimum by code and by facility requirements can reduce cost and keep the project in budget. Some wireless lighting control systems can also be conducive since they reduce the amount of wiring.
However, one must keep in mind the requirements by NFPA 70: National Electrical Code, where some lighting control systems might not meet new emergency life safety requirements. It is also critical to consult with the client as some health care providers do not prefer wireless systems as they can cause electromagnetic interference with their sys-
‘ Patient corridors are critical spaces, where multiple functions coexist. ’
‘ It is also crucial to develop riser diagrams, schedules, details and sequence of operations that are reviewed by the client early in the process.’
tems and have batteries with short life spans which can also cause a maintenance issue.
Hospitals are a living structure of devices and equipment. With the advancement of newer wireless technologies, interference between different equipment in a hospital can create a serious challenge. Some occupancy sensors operate on the harmonics of newer real-time locating systems equipment and can interfere with them.
To use the advantages of wireless systems for a human-centric design, a careful investigation of the system frequency and its harmonics is crucial. If the project timeline permits, it is also encouraged to do a mock-up during the design phase with the various hospital and lighting equipment, which can lead to specifying the appropriate lighting control system early in the process.
A key element to achieving human-centric lighting controls is the capability to integrate multiple systems together. Because the building automation system (BAS) is often preferred by facility managers as an integration hub for a project’s major systems, it is crucial to integrate seamlessly with it.
Standard BAS protocol integration — such as BACnet, Modbus or others — is a feature in most lighting control systems. It is important to have a lighting control system that uses either no gateway with the BAS or minimal gateway. The former can be achieved using a lighting control system that uses the native BAS protocol.
Hence, control points between the two systems can be minimized and a direct two-way communication can be achieved. If the integration is successful, systems such as shades, smart glass, HVAC and others can be controlled from the lighting control system devices that already exist in the space. Reducing cost and consolidating keypads to lessen confusion in the space. In the case of a nurse call system, it can control lighting zones seamlessly as well.
A careful layout of the sequence of operations and how the system should operate makes the commissioning of the lighting system easier and less time consuming. This operational sequence should include the lighting zones and any integration between these different systems.
Because health care projects are projects that last for a long time and since a lot of upgrades can happen to the hospital, the lighting control system should be expandable and future proof. The ability for the systems to receive new products and upgrades is crucial. A distributed smart addressable system is a good approach.
Current lighting control systems are moving away from large, centralized lighting control panels toward more flexible plenum or fixture mounted lighting control modules. Each strategy comes with its own advantages and setbacks.
For instance, integrated controls in fixtures can cause a higher initial fixture cost but provides more flexibility in terms of future zoning. Fixture mounted controls and smart drivers are the way to the future so devices can be added to the lighting control grid seamlessly. A key approach to this is the standardization of both control modules and drivers.
Plenum-rated panels can be challenging in health care environments for maintenance above ceilings. This is why they are typically located in the corridors to avoid patient room shutdown. Plenum-rated panels are great to reduce cost and to zone multiple fixtures together in large areas such as corridors and lobbies. DALI and addressable systems represent about 70% of connected lighting systems according to the EU Joint Research Centre (JRC) and most European manufacturers have it as a standard offering. The technology is slowly making its way into the United States. If those are widely available, a system can be expandable.
The key to standardization is contacting manufacturers early in the process and communicating to them the importance of integrating specific drivers into their lighting fixtures. If the quantity is available, manufacturers will certainly be open to use such products.
Given the above-mentioned challenges, the best way to achieve a great design is to tailor it to the user’s needs. A strong understanding of what the client requirements are is crucial. Clear communication between the users and the design team is imperative. This communication can be visual, where different control scenarios can be shown or be in the format of a schedule or a diagram to indicate how zones are controlled and what type of devices are used.
Depending on the project timeline and delivery method, at least one meeting per phase for lighting controls is encouraged so the client can see the progress and comment on the changes. On larger immersive projects, the frequency of that review can increase to a weekly basis to ensure proper understanding of lighting controls by the client.
It is encouraged to show the different control scenarios to the client visually in the space. Renderings can be used to simulate them and to define how the space will look when built. This accelerates the sign-off process and eliminates future questions and requests for information.
It is also crucial to develop riser diagrams, schedules, details and sequence of operations that are reviewed by the client early in the process. The details and diagrams should be generic in nature to allow showing the intent without locking to a specific manufacturer and to make bidding easier. Documenting this information should be clear and consistent. It should also indicate which zones are dimmed, on emergency and the devices that control each zone.
Finally, a good lighting control system that provides a human-centric environment is critical for patient healing and eventually a better patient outcome. Specifying touchless controls, providing the patient with more controllability and circadian entrainment can promote faster healing, which can increase patient outcomes and reduce infection. This helps having a better return on investment as patient satisfaction and TPS scores increase. It also offers a viable solution for expanding in the future and adding the most current version of the lighting control system. cse
Paul Daniel, LC, LEED AP, is a senior lighting designer and senior professional associate at HDR.
Richard Vedvik, PE, IMEG Corp., Rock Island, Illinois
Centralized, remote and distributed standby generator designs are all options for power systems. Which one is best?
When designing or assessing campus-style distribution systems, the topic of centralized versus decentralized standby power systems is a necessary focus. This article will explain the various attributes associated with a variety of standby generator systems. It is intentionally written in a format that starts by making a case for each arrangement by addressing the positive and beneficial aspects then finishes with the negative compromises and limitations.
It is very common for a campus to grow in a manner that results in multiple distributed standby generator systems spread across the campus both electrically and geographically. The typical arrangement is an essential electrical system (EES) consisting of one or more generator sets, serving a defined “building.” Other buildings, usually separated by age, have a separate EES.
The primary reason for distributed systems is due to the cost and complexity of centralized systems and the lack of capacity in the older generator systems to accommodate new building additions. Many projects lack the budget to overhaul and upgrade the existing EES. The primary benefit of decentralized arrangements, other than initial cost to each building, is both electrical and geographic diversity to prevent single points of failure.
If a natural disaster damages the east side of a building or campus, the utility and standby power systems may be damaged beyond immediate repair. While the portions of the building or campus served will be without power, the other areas of the building may still sustain power, allowing for continued operation. This approach is popular in mission critical and health care campuses where evacuation and shutdowns are not acceptable.
For campuses that experience frequent growth
FIGURE 1: Two 600 kW 4,160 V standby generators were relocated to a remodeled space that was sized for a third generator and larger generators. This system is planned for expansion to operate as a centralized location in a remote utility plant. Courtesy: IMEG Corp.
• Learn pros and cons for centralized and decentralized generator systems.
• Acquire strategies for centralized campus power backup.
• Review and example on centralized generators for both utility backup and emergency electrical system duties.
and renovation, the distributed configuration can be less expensive due to localized and right-sized electrical distribution providing a lower cost to feeders and electrical gear. Because the needs of each building on a campus may vary, additional savings may be had for systems that do not need to meet more stringent requirements of Level 1 systems, as defined in NFPA 110: Standard for Emergency and Standby Power Systems.
For example, a health care campus will likely have Level 1 EES to serve the areas that are within the International Building Code (IBC) occupancy classification of I-2 (institutional), and may also have IBC occupancy classifications of B (business), A (assembly), S (storage), etc.
The other occupancy types may be able to have a Level 2 EES as defined by NFPA 110 or may only require emergency loads as defined by NFPA 70: National Electrical Code (NEC) Article 700 and would not fall under Article 517 or NFPA 99: Health Care Facilities Code, which both govern health care designs. Providing different levels for EES serving different buildings on a campus may also allow for different fuel types and storage amounts. In this example, the Level 1 EES would likely consist of diesel standby generator sets with on-site storage sufficient for 96 hours of operation (with or without refueling during the 96 hours).
the most glaring one is the lack of shared capacity. For example, if a campus has 4 megawatts (MW) of total standby power through four 1-MW generator sets and if none of those sets can be connected in parallel, the available capacity at any point in the system is limited to 1 MW. This can have the effect of increasing costs for future projects, additions or renovations if the closest and most convenient generator system lacks capacity.
‘When consulting with a campus, one simple question to ask the client is if the building can be evacuated at any time, without hesitation.’
A Level 2 EES for a smaller medical office building may be a single natural gas standby generator with a local temporary connection cabinet. Buildings that do not need an EES at all could get by with battery backup of emergency and egress lighting and fire alarm systems.
When consulting with a campus, one simple question to ask the client is if the building can be evacuated at any time, without hesitation. If the answer is yes, then it’s likely the backup power requirements can be less stringent when compared to areas that cannot be evacuated.
There are, however, negative aspects of a distributed or decentralized standby power system and
Additionally, if one generator is taken out of operation for maintenance, the other generator sets on campus are not able to back feed, requiring temporary connections. NEC Article 700.3(F) recognizes the vulnerability of a single generator and requires installed, temporary connection capability that can be avoided with paralleled generators of adequate size.
Decentralized generator systems also spread out the equipment causing additional maintenance hassles and increased footprints. Fuel storage is required for each, fuel treatment is required for each, battery systems are multiplied and testing is multiplied. Each generator location needs to be coordinated with outside air intakes for the heating, ventilation and air conditioning (HVAC) system and noise concerns within the campus and adjacent properties.
A central utility plant, or CUP, can be located adjacent to the buildings served or can be remote from the buildings served. The CUP can contain chilled water systems, heating water or steam systems and electrical distribution systems for both normal (utility) and standby (emergency) sources.
Centralized electrical distribution can be independent of mechanical systems and locating them inside of a CUP is just one option. It is common for normal utility sources to be centralized, typically at the 15 kilovolt (kV) distribution voltage class. This may or may not be equipment owned by the cli-
ent, though it is common for the facility to own and operate the medium-voltage distribution for the normal service. Likewise, standby generator sets can be centralized and distributed at the same voltage as the normal service.
Large buildings or campus arrangements are subject to voltage drop concerns when distributed across the space, therefore, one of the first decisions the team should consider is the distribution voltage for both the normal and standby systems. In the U.S., typical building service voltages are 208/120 V for smaller buildings and 480/277 V for larger buildings (with stepdown transformers for 208/120
A CENTRALIZED standby generator arrangement will be explored further in the following case study
An existing hospital campus is undergoing a master planning effort to determine strategies for growth and infrastructure improvements. The campus is currently fed from two utility sources, Circuit A and Circuit B at 13.8 kilovolts (kV). The two sources serve 15-kV switchgear that distributes power throughout the campus through underground duct banks with taps made in maintenance holes.
The health care buildings have double-ended unit substations that include 15-kV switchgear to allow for selection of either Circuit A or Circuit B. Each building has dedicated standby diesel generator sets serving transfer switches in each building. The generator sets and associated distribution is at 480/277 V, which matches the secondary side of the unit substation transformers in each building.
The master planning effort identified campus growth that would necessitate relocation of the existing utility service and the future building layout will require replacement of the existing 13.8 kV underground distribution. A new electrical service yard is planned for the center of the campus and new 13.8 kV underground distribution will serve both existing and future buildings. The route for the new duct banks is coordinated with the 20-year campus plan to avoid future disruptions and con-
flicts. Once the team solidified the utility plans, it moved the focus to campus backup and the existing standby generator sets.
The campus has a newer, 3-megawatt (MW) standby diesel generator set that is connected to utility Circuit A to provide campus backup of that circuit in the event of an outage. Circuit B is not connected to the campus backup generator. As a result, most of the buildings on campus are connected to Circuit A which has an average load of 1.9 MW while Circuit B has an average load of 0.5 MW.
The campus has a central utility plant (CUP) for heating systems, but the CUP is only fed from Circuit B. The master plan effort included a study to provide campus backup of Circuit B. A second 3-MW standby diesel generator set is planned, to be connected to Circuit B in new switchgear.
An understanding of phasing is required in order to mitigate long outages of campus power. The proposed project phasing is as follows:
• Route new utility feeds from Circuit A and Circuit B to the new service location. Provide switchgear suitable for the full camps buildout.
• Provide a new 13,8-kV, 3-MW standby diesel generator for backup of Circuit B. Provide necessary controls and switchgear to allow for campus backup.
• Provide new 13.8-kV underground distribution across the campus, with new maintenance holes and duct banks. Pro-
vide new maintenance holes near each building feed.
• Starting with buildings that already have two campus feeds, refeed the Circuit B side, then refeed the Circuit A side. These buildings will not experience an outage.
• Refeed the remaining buildings, with coordinated outage plans as utility cables are switched over.
• Once the campus is operating on the new 13.8 kV distribution, relocate the existing 13.8-kV, 3-MW generator to the new service yard and connect to Circuit A.
• The existing distribution can now be demolished to make room for campus expansion.
The master plan effort includes two options for essential branch power for each building: centralized or decentralized. The first option is to maintain the current decentralized generator sets across campus and upgrade each as needed. New buildings would get local standby generator sets. For additional redundancy, tie breakers and tie feeders can connect essential branch distribution in adjacent/connected buildings. However, this method of providing redundancy is costly given the distances involved being between 1,000-1,500 feet and the necessary size of the tie feeders being 2,000-3,000 A.
The centralized option can be broken down into two sub-options, one of which uses the pair of 3 MW generators as both the essential branch power and utility
V loads). The centralized generator system can distribute at the building service voltage or at higher voltages to reduce wire size, which will aid with costing and voltage drop.
Alternatively, centralized systems can take advantage of 5- or 15-kV voltage ranges to greatly reduce the cost to distribute over longer distances, even several miles away. When using mediumvoltage distribution, the buildings served will need to plan for large transformers to step-down to the building service voltage. Step-down transformers can be part of single-ended or double-ended unit substations. The type and location is based on bud-
get, space and desired redundancy. Additionally, 15 kV fused switches are provided at the transformer primary and can include radial or loop outputs for future expansion capability.
A centralized and remote location can improve the exterior aesthetics of the various buildings served by removing exterior enclosures from the areas around each building. Freeing up space around buildings allows for more flexibility for future expansions and alleviates concerns with noise and exhaust emissions near buildings.
The ability to parallel standby generator sets together is the strongest argument for centralized
backup power source. Providing separate standby diesel generators for centralized essential branch power is the typical approach. The operating voltage of the centralized generators can be 4,160 V or 13.8 kV, with associated distribution across campus in dedicated duct banks and maintenance holes at each building.
As is typical with centralized medium-voltage systems, new unit substations will be needed at each building to replace the existing decentralized generators. Because the existing generators are nearing end of useful life, this option is not cost-prohibitive because replacing the existing generators is necessary anyway.
The other centralized option, which uses the pair of 13.8-kV, 3-MW campus utility backup generators, saves both cost and space but has its own challenges. In a utility outage, the centralized generators need to prioritize the essential electrical branch first.
For example, when a Type 10, Level X is required by NFPA 110: Standard for Emergency and Standby Power Systems for a hospital, the transfer switches in each building need to transfer within 10 seconds for the life safety and critical branch transfer switches. After a predetermined amount of time has passed (usually 60 seconds) the various equipment branch transfer switches can transfer.
At this time, the centralized generator paralleling gear will evaluate the current
vide both utility backup to several buildings while also providing emergency electrical system backup for a free-standing surgical center. The utility backup uses a service-entrance transfer switch with delayed transfer and load shed controls while the surgical center has separate transfer switches for life safety, critical and equipment branches. Courtesy: IMEG Corp.
load on the generators and, if the load is within predetermined values, the Circuit A transfer sequence will start. This will bring Circuit A online, powered from the centralized standby generators and will return “normal” power to the transfer switches fed by that circuit on the normal side.
Transfer inhibit signals are required in these transfer switches to prevent them from returning to “normal.” This inhibit signal is important because the Circuit A transfer sequence includes a “load shed” command which will remove the Circuit A load from the generators if they become
overloaded (usually an under-frequency alarm). The same sequence and controls will follow for Circuit B, with the same load shed commands.
At this point, the entire campus will have power restored to the normal Circuits A and B, with all campus transfer switches in the “emergency” position. When utility power is restored, the first loads to transfer will be Circuits A and B. Then the typical retransfer to normal sequence will occur within the various transfer switches within each of the buildings.
generator systems. The size and quantity of standby generator sets required to achieve N+1 sizing can be less than decentralized. Let’s work through an example:
• Building A has 550 kilowatts (kW) of emergency load.
• Building B has 375 kW of emergency load.
• Building C has 900 kW of emergency load.
Total emergency load is 1,825 kW. Assume the generator sizing calculations (for voltage dip and frequency dip) require a generator sized for 2,400 kW, minimum. A centralized system can achieve N+1 with two 2,500-kW or three 1,250-kW standby generators. For a decentralized generator system to achieve N+1, each building would need a pair of generators, bringing the campus total to at least six.
When determining the number of generators to parallel to serve the total campus load, the designer then needs to evaluate several factors, such as type of building, loads served, how they interact with the generator that creates voltage dip and how long they can sustain being without power before the EES is online.
For instance, in a Level 1 system that feeds a health care occupancy, the engineer must determine the loads required to connect within 10 seconds or the sum of the critical and life safety branches. This load is what drives the smallest engine size allowed. Let’s revisit the example, this time with the load broken out by essential branches, as defined by NFPA 99 Article 517.
• Building A has 20 kW of life safety branch load, 175 kW of critical branch load and 355 kW of equipment branch load.
• Building B has 10 kW of life safety branch load, 75 kW of critical branch load and 290 kW of equipment branch load.
• Building C has 35 kW of life safety branch load, 350 kW of critical branch load and 515 kW of equipment branch load.
Now we can see that we have 665 kW of load that needs to be online within 10 seconds and after running generator sizing calculations, we may find that the minimum generator size needed is 900 kW, making 1,000 kW (or 1,250 kW in our example) the preferred choice for each generator. Next, the designer needs to determine the available growth that this minimum size allows. If the campus is expected to double in size over the next 20 years, then the recommended minimum generator size needs to increase accordingly.
The team needs to determine how the centralized generators and associated equipment will be protected. Keeping the paralleling controls and distribution switchgear inside conditioned (and access controlled) buildings is preferred. While generators may be in exterior enclosures and generators can feature onboard paralleling controls to reduce the footprint of the distribution, electronics always prefer a conditioned environment with low dust, humidity and a moderate temperature range.
Remote buildings, such as a CUP that house the generator sets, fuel polishing systems, day tanks, engine controllers and associated electrical distribution should take future expansion into consideration. The layout of the generators, for example, should allow for additional units or accommodate replacement with larger units as the campus grows. This requires a larger footprint or at least the planning for building expansion, which drives up the costs associated with centralized systems.
Centralized systems are not without their challenges. Initial costs can be higher when a greenfield campus is initially constructed because the central system needs to be sized (or scalable) for all projected campus growth. It is also common for centralized systems to be a retrofit solution for an existing campus looking to expand further.
In addition, feeder routes must be carefully coordinated with other utilities and future expansion plans. The routing could be underground duct banks, routing through utility tunnels or a combination thereof, but the pathway should be separated from normal utility pathway to prevent a single excavator or event from damaging both normal utility and emergency services.
Underground duct banks are also subject to ground water ingress and the need for periodic maintenance holes (due to wire spool length limitations) means that designers should consider methods of providing adequate drainage of conduit and maintenance holes. Drainage systems may include connection to stormwater drainage or pumping solutions.
Some campuses want a full backup of the normal utility through standby generators that operate at the service entrance voltage, which is usually 5- or 15-kV class. Solutions that offer this level of backup are often subject to more rigorous requirements, such as U.S. Environmental Protection Agency (EPA) Tier emission levels.
An advantage to having a lower emission EPA Tier standard allows for load curtailment, which can provide financial savings through agreements with the local utility. These generators are typically independent of emergency standby generators; however, we can consider an arrangement in which large, standby generators operating at the utility service voltage can provide both essential standby and utility backup power.
When using campus backup generators for emergency backup, there are several aspects to be aware of when doing this. There are several reasons why it is not acceptable to simply rely on the campus backup generator to provide the essential electrical branch for each building.
• Division of branches is not possible with utility backup.
• Two sources of power within a patient care area, where required by NFPA 99, is not possible.
• Transfer switches are still required in each building, for each required branch.
• Branch segregation required within NEC Article 700, 701 and 702 (or NEC 517) are still required at the branch circuit level.
• Each building will need transformers if the generator voltage is different from the building voltage. These transformers are separate from the incoming service transformers. This is commonly
accomplished using unit substations when the generator voltage is 5 or 15 kV, but can occur with traditional exterior or interior step-down transformers.
• The building transfer switches need additional programming to inhibit retransfer to normal when the campus backup is online. cse
Richard Vedvik, PE, is a senior electrical engineer and acoustics engineer at IMEG Corp. He is a member of the Consulting-Specifying Engineer editorial advisory board.
csemag.com
u When designing or assessing campus-style distribution systems, it is important to focus on centralized versus decentralized standby power systems.
u Decentralized standby generators offer electrical and geographic diversity to prevent single points of failure and can be less expensive due to localized and right-sized electrical distribution.
u Centralized standby generators offer shared capacity and N+1 redundancy, but can be more expensive and require larger equipment.
Learn about the trends here
CSE: What are some current trends in data centers?
Bill Kosik: According to the Jones Lang LaSalle study H1 2022 Global Data Center Outlook, starting in 2017, hyperscale data centers nearly doubled electricity consumption to 87 terawatt-hours, while traditional data centers halved electricity consumption to 33 terawatt-hours. Because hyperscale data centers have a much higher information technology power densi-
ty (watts per square foot) than traditional enterprise data centers, a single data center can be designed with an IT load of dozens of megawatts in the same footprint.
In 2010, the global energy demand for hyperscale and cloud data centers was 13% and for traditional data centers 87%. By 2022, global energy demand for traditional data centers was projected to be 23% with cloud and hyperscale data centers making up 77%.
Brian Rener: We are seeing increased requirements for higher density rack loads (30 kW or greater) and various forms of water cooling mixed with air cooling for high-performance or artificial intelligence computing. It may only be future provisions for now, but there is expressed need to have future flexibility
Ameya Soparkar: Apart from more capacity being added in cloud and colocation sectors and new developers entering the data center facility market, there are three trends that I find are noteworthy. The first is the enterprise data center market which continues to see a gradual increase.
FIGURE 1: The University of Utah Downtown Data Center in the high desert of Salt Lake City uses a combination of outside air-free cooling economizer, direct evaporative cooling and fluid coolers for an up to 10 megawatt predominantly air-cooled system (with a limited amount of liquid-cooled high-performance cooling). Courtesy: SmithGroup
The second is edge computing, which has grown in companies that don’t have IT as their core business function, manufacturing, pharmaceuticals, retail, etc. with server loads of less than 2 MW.
And lastly, liquid cooling. With Microsoft clearing the way by running a production data center on two-phase immersion cooling, the adoption rate of the technology as well as direct to chip liquid cooling is on the rise.
Robert Sty: Over the past few years, many colocation providers have moved to a standardized model for several reasons. Recently, the ability to procure equipment early on within the design process to secure a position at the start of the supply chain has taken on a new importance. Every year we see higher density deployments and the discussion around when to move to a liquid cooled solution. For years, the discussion in almost every forum was decreasing a data center, power usage effectiveness value, yet the prolonged drought in the western United States has changed the conversation to finding a balance between reduced energy use in conjunction with reducing waterbased heat rejection strategies.
CSE: What future trends (one to three years) should an engineer or designer expect for such projects?
Robert Sty: As municipalities push back against using water-based heat rejection technologies (cooling towers, direct/ indirect evaporative cooling), our teams
will be challenged with finding new ways to effectively cool data centers. More attention will be given to developing solutions that can manage extreme temperatures — for example when the temperature reached 115˚F in Oregon and the deep freeze Texas suffered in 2021. The industry has seen a large interest in the investigation of on-site power generation strategies to address markets where the utility is constrained.
Bill Kosik: According to the latest City of Chicago Energy Benchmarking Study (2019), of the commercial buildings included in the study, data centers represent only 1% of the floor space but are responsible for 26% of the indirect greenhouse gas emissions. As municipalities expand their decarbonization programs, commercial buildings (in particular, data centers) are a significant part of the reduction potential.
Ameya Soparkar: Designing for mission critical IT in facility infrastructure that was not initially designed to be mission critical will be the challenge. With the growth in enterprise and edge data centers, IT hardware is being placed in areas that were considered nontraditional spaces and in buildings that were not designed for data center operation. Ensuring uninterruptible power, continuous cooling and seamless maintainability will require the engineers/designers to look at the infrastructure from the basic elements and come with creative ways to make modifications/additions to fulfill the mission critical requirement of the business.
CSE: What types of challenges do you encounter for these types of projects that you might not face on other types of structures?
Ameya Soparkar: In typical data center projects, probable failures are factored in the design and the system is designed for continuous operation. You will have large cooling plants, redundant generators capable to supporting 100% of the building load, fuel storage to last days. The infrastructure runs 24x7x365, which
in many commercial buildings is not the case, hence having an on-site team and response strategy for any time during the day and year for failures is common in data centers.
Bill Kosik: Fast-paced, multiple client, site challenges (power, water), rapid technology advancements, certain organizations use standardized (but often customized) equipment configurations. Due to the aggressive design and construction schedules, vendors and equipment manufacturers sometimes have difficulty in meeting delivery dates. Finding the balance between efficiency, reliability, maintainability and cost can be difficult unless the customer has clear standards in place.
Robert Sty: There can be significant pushback from municipalities against large scale data center development versus other types of projects, such as high-tech manufacturing. Although the systems and platforms, are critical to the operation of every business, the facilities themselves do not always support many primary jobs (direct employees).
CSE: What are professionals doing to ensure such projects meet challenges associated with emerging technologies?
Robert Sty: Retrofitting existing data centers can be a significant challenge when considering new and emerging technologies. The facility may not have the power or cooling infrastructure in place to support higher density deployments. Strategies, such as rear door heat exchangers, could be appropriate in this type of scenario. We have also proposed adding supplemental structural framing to support new equipment on the roofs of data centers. While new greenfield designs can be easier to adapt to potential new technologies, there are still limitations to space, power and cooling infrastructure given the allotted footprint of the facility.
Brian Rener: Higher density rack power demands means increased future demands for water to rack or water to
Bill Kosik, PE, CEM, BEMP
Senior Energy Engineer
DNV
Oak Park, Illinois
Brian Rener, PE, LEED AP
Principal, Mission Critical Leader
SmithGroup
Chicago
Ameya Soparkar Market Leader, Mission Critical
Affiliated Engineers Inc.
Rockville, Maryland
Robert Sty, PE, LEED AP
Vice President
HDR Inc.
Phoenix
chip. In some cases, liquid immersion tanks are being considered. The presence or water in a data center brings special challenges which as increase structural capacity on the data center floor and careful consultation of fluid spill management.
CSE: What types of cloud, edge or fog computing requests are you getting and how do you help the owner achieve these goals?
Ameya Soparkar: The cloud companies have extremely capable people on staff and if new builds are kept aside, gen-
Continued on page 63
csemag.com
Data center insights
uThe demand for energy and water will directly impact how data centers are designed and operated.
uCost constraints, location and energy use will dictate the location of data centers.
Greenheck’s line of energy recovery products and innovative energy efficiency technology helps turn down energy usage drastically with configure-to-order and cutting-edge applied science. Engineered, tested, and certified to exceed expectations for operating efficiency and product performance, add Greenheck to your data center project. It’s elevated energy efficiency that delivers.
Specify with confidence. Specify Greenheck.
Continued from page 61
eral requests that are received are more on the tasks that we as consulting engineers are more streamlined to do, calculations, studies, computational fluid dynamics, energy analysis, etc. The edge projects is where we do quite a bit of feasibility studies, evaluation of different technologies, total cost of ownership analysis for our clients so that they can decide which option serves them best for the short and long term. We see ourselves as trusted advisers to our clients and try to develop designs and engineering solutions that would fulfill the requirements of their business.
Robert Sty: The purpose of edge computing is to bring the cloud closer to the device for faster processing of data and reduction in latency. Every company defines their edge a little differently depending on the business function. One approach is the deployment of smaller facilities that do not have regular on-site facilities staff, driving solutions that are a little more robust from a reliability viewpoint. Additional options include diesel fuel capacity, N+2 versus N+1 platforms and overall facility envelope enclosures that are hardened and secure. In 2020, ASHRAE TC9.9 put forth a technical bulletin addressing some of these concerns for edge facilities. cse
ABB Motors US................. . 2......... www.new abb.com/motors-generators/nema-low-voltage-ac-motors/hvac-motors/critical-cooling-motors
AGF Manufacturing, Inc.......... 29 www agfmfg com
CFE Media GSI Database......... 63 https://gspplatform cfemedia com/si/home
CFE Media LLC 41 www cfemedia com
CFE Media NPE Database 63 https://gspplatform cfemedia com/pe/home
CHAMPION FIBERGLASS......... 29 www championfiberglass com
Cummins..................... C-4 www cummins com
Eaton 6, 20 www Eaton com/microgrid
Fujitsu General America, Inc 1......... www fujitsugeneral com
Greenheck 62 www greenheck com
Hammond Power Solutions....... 63 www hammondpowersolutions com
Industrial Cybersecutiy Pulse 21 www industrialcybersecuritypulse com
Lennox Industries............... 28 https://www lennoxcommercial com
Miura North America, Inc 47 www miuraboiler com
Pritchard Brown ................ 59 ........ WWW.PRITCHARDBROWN.COM
Reliable Controls............... C-2 www reliablecontrols com
Rheem 4......... www RheemCommercial com
RUSKIN 41 www ruskin com
Tjernlund Products.............. 64 www tjernlund com
Yaskawa America, Inc........... C-3 www yaskawa com
Publisher/Midwest
Matt Waddell MWaddell@CFEMedia.com
3010 Highland Parkway, Suite #310 312-961-6840 Downers Grove, IL 60515
Account Manager
Robert Levinger RLevinger@cfetechnology.com 630-571-4070 x2218
West, TX, OK
Aaron Maassen AMaassen@CFEMedia.com Integrated Media Manager 816-797-9969
Northeast
Richard A. Groth Jr. RGroth@CFEMedia.com 12 Pine Street 774-277-7266 Franklin, MA 02038
Director of Content Marketing Solutions
Patrick Lynch PLynch@CFEMedia.com 3010 Highland Parkway, Suite #310 847-452-1191 Downers Grove, IL 60515
Marketing Consultant
Brian Gross BGross@CFEMedia.com 3010 Highland Parkway, 630-571-4070 x2217 Suite #310 Downers Grove, IL 60515
Jim Langhenry, Co-Founder and Publisher, CFE Media JLanghenry@CFEMedia.com
Steve Rourke, Co-Founder, CFE Media SRourke@CFEMedia.com
McKenzie Burns, Marketing-Events Manager MBurns@cfemedia.com
Courtney Murphy, Marketing and Events Manager CMurphy@cfemedia.com
Paul Brouch, Director of Operations 630-571-4070 x2208, PBrouch@CFEMedia.com
Rick Ellis, Audience Management Director 303-246-1250, REllis@CFEMedia.com
Michael Smith, Creative Director 630-779-8910, MSmith@CFEMedia.com
Michael Rotz, Print Production Manager 717-422-3622, mike.rotz@frycomm.com
Maria Bartell, List Rental Account Director Infogroup Targeting Solutions 847-378-2275, maria.bartell@infogroup.com
Claude Marada, List Rental Manager 402-836-6274, claude.marada@infogroup.com
Letters to the Editor: Please e-mail your letters to ARozgus@CFEMedia.com
Letters should include name, company, and address, and may be edited for space and clarity.
Information: For a Media Kit or Editorial Calendar, go to https://www.csemag.com/advertise-with-us/ Marketing consultants: See ad index.
Custom reprints, electronic: Paul Brouch, PBrouch@CFEMedia.com
TM
External events influencing power quality can interrupt equipment and cause failure of electrical components. A lack of redundancy potentially puts mission critical data at risk. A lightning strike or even a planned generator test could interrupt the critical cooling of a data center. If data center colocation is not on line, redundancy at the primary location is a sound investment.
Our HV600 Redundant VFD Solutions help to insure that these external events are one less thing to worry about. They provide seamless automatic switchover during the primary failure of any fan, pump, chiller, or cooling tower application.
Yaskawa has over 35 years experience in delivering quality HVAC VFD solutions and our products are built in U.S.A.
The data doesn’t lie. Yaskawa drives outperform the rest. Call about our HV600 Redundant Drive Solutions today