
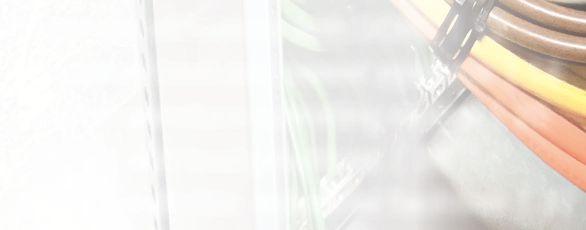
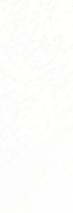


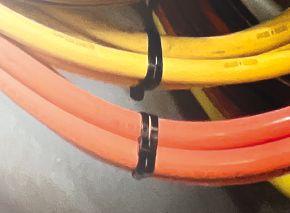
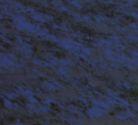


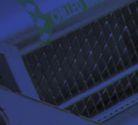
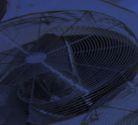
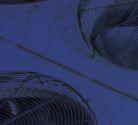
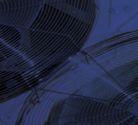
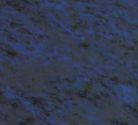
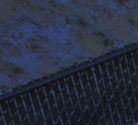
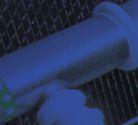
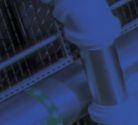
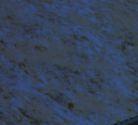
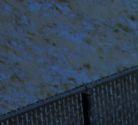
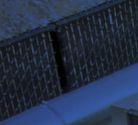
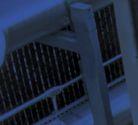
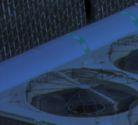
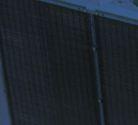
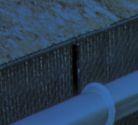
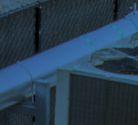

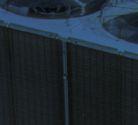
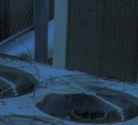
We’re
SyMAX
or visit us online at leeson.com today.
• Navien cascade system continuously matches operation to demand
• Meets temperature demands up to 185°F
• Redundancy allows servicing one unit, while others handle demand without interruption
• Cascade up to 32 units and common vent up to 12 units
• Navien EZNav™ multi-line intuitive control for easy set up and diagnostics
• Same day easy to install Navien Ready-Link® manifold system for wall or rack mounting
To learn more, visit Navieninc.com.
5 | Proceed with caution: Engineers are using AI more MEP/FP engineers can benefit from artificial intelligence when used with caution
6 | How to create a resilient, robust electrical distribution system
Switchgear, transformers and uninterruptible power supplies collectively form the backbone of electrical power systems
12 | Understand how to maximize efficiency and control with DOAS
Dedicated outdoor air systems enhance humidity control, reduce energy use, simplify ventilation design and improve efficiency
18 | Planning and design considerations for CHP systems
CHP systems provide solutions for lowering utility costs and increasing electrical and heat source reliability for continued facility operation
An example of an electrical switchgear and its construction. These enclosures come in various ratings, such as NEMA 3R. The enclosure rating depends on where the switchgear is located.
Courtesy: Certus
25 | How to use DOAS to design low-temperature operating rooms
Many health care facilities struggle to maintain temperature and humidity in operating rooms, especially as doctors are asking for lower temperature options
30 | Design of RTUs: Best practices
Specifying rooftop units (RTUs) involves much more than choosing unit types. RTU filtration and humidification requirements, energy efficiency, ease of maintenance and aesthetics are major considerations
37 | Automation and scalability shape industrial facility design
Current trends in industrial and manufacturing facilities include the rise of automation and AI, integration of IoT and addressing supply chain issues.
AMARA ROZGUS, Editor-in-Chief ARozgus@WTWHMedia.com
ANNA STEINGRUBER, Associate Editor ASteingruber@WTWHMedia.com
AMANDA PELLICCIONE, Marketing Research Manager APelliccione@WTWHMedia.com
MICHAEL SMITH, Art Director MSmith@WTWHMedia.com
DARREN BRUCE, PE, LEED AP BD+C, Director of Strategic Planning, Mid-Atlantic Region, NV5, Arlington, Va.
MICHAEL CHOW, PE, CEM, CXA, LEED AP BD+C, Principal, Metro CD Engineering LLC, Columbus, Ohio
TOM DIVINE, PE, Senior Electrical Engineer, Johnston, LLC, Houston
CORY DUGGIN, PE, LEED AP BD+C, BEMP, Energy Modeling Wizard, TLC Engineering Solutions, Brentwood, Tenn.
ROBERT J. GARRA JR., PE, CDT, Vice President, Electrical Engineer, CannonDesign, Grand Island, N.Y.
JASON GERKE, PE, LEED AP BD+C, CXA, Mechanical Engineer, GRAEF, Milwaukee
JOSHUA D. GREENE, PE, Associate Principal, Simpson Gumpertz & Heger, Waltham, Mass.
RAYMOND GRILL, PE, FSFPE, LEED AP, Principal, Ray Grill Consulting, PLLC, Clifton, Va.
DANNA JENSEN, PE, LEED AP BD+C, Principal, Certus, Carrollton, Texas
WILLIAM KOFFEL, PE, FSFPE, President, Koffel Associates Inc., Columbia, Md.
WILLIAM KOSIK, PE, CEM, LEGACY LEED AP BD+C, Lead Senior Mechanical Engineer, kW Mission Critical Engineering, Milwaukee
KENNETH KUTSMEDA, PE, LEED AP, Engineering Manager, Jacobs, Philadelphia
DAVID LOWREY, Chief Fire Marshal, Boulder (Colo.) Fire Rescue
JASON MAJERUS, PE, CEM, LEED AP, Principal, DLR Group, Cleveland
JUSTIN MILNE, PE, PMP, Senior Engineer, Southcentral Region, Jensen Hughes, Allen, Texas
GREGORY QUINN, PE, NCEES, LEED AP, Principal, Health Care Market Leader, Affiliated Engineers Inc., Madison, Wis.
BRIAN A. RENER, PE, LEED AP, Principal, Electrical Discipline Leader, SmithGroup, Chicago
CRAIG ROBERTS, CEM, Account Executive, National Technical Services, McKinstry, Powell, Tenn.
SUNONDO ROY, PE, LEED AP, Director, Design Group, Romeoville, Ill.
JONATHAN SAJDAK, PE, Senior Associate/Fire Protection Engineer, Page, Houston
RANDY SCHRECENGOST, PE, CEM, Austin Operations Group Manager/Senior Mechanical Engineer, Stanley Consultants, Austin, Texas
MATT SHORT, PE, Project Manager/Mechanical Engineer, Smith Seckman Reid, Houston
MARIO VECCHIARELLO, PE, CEM, GBE, Senior Vice President, CDM Smith Inc., Boston
RICHARD VEDVIK, PE, Senior Electrical Engineer and Acoustics Engineer, IMEG Corp., Rock Island, Ill.
TOBY WHITE, PE, LEED AP, Associate, Boston Fire & Life Safety Leader, Arup, Boston
APRIL WOODS, PE, LEED AP BD+C, Vice President, WSP USA, Orlando, Fla.
JOHN YOON, PE, LEED AP ID+C, Lead Electrical Engineer, McGuire Engineers Inc., Chicago
MEP/FP engineers can benefit from artificial intelligence when used with caution
While at the 2024 NFPA Conference & Expo, artificial intelligence (AI) was the keynote speaker’s topic of conversation. David Pogue, a multimedia presenter about science and technology, touched on the many ways that AI will change our lives. Some of his suggestions were terrific and will revolutionize building engineering. Other idea were startling and several audience members around me gasped or harumphed.
AI is revolutionizing engineering, offering unprecedented opportunities for mechanical, electrical, plumbing and fire protection (MEP/ FP) engineers. The integration of AI into engineering processes is not just a trend but a shift that enhances efficiency, accuracy and innovation.
Fire protection engineering, a primary topic of the conference, is another field where AI is making a significant impact. AI-powered fire simulation tools enable engineers to model and analyze fire scenarios with unprecedented detail and accuracy.
Amara Rozgus, Editor-in-Chief
The challenge, of course, is that not all of the details are accessible by AI systems, meaning it won’t necessarily have the latest codes or standards. And while AI can analyze and interpret vast amounts of information, it cannot predict what the authority having jurisdiction will say about occupancy classifications, or about why a particular product just won’t work in this application.
Like so many others, Pogue emphasized that AI was not going to take away anyone’s job. Instead, it would enhance many things.
Mechanical and plumbing engineers are leveraging AI to optimize design and — looking ahead to the building process — the construction phase. Through advanced simulations and fluid dynamics, AI can analyze vast datasets to find patterns and predict outcomes with precision.
In the realm of electrical engineering, AI is playing a role in the design and optimization of electrical systems. AI algorithms can analyze electrical networks to identify the best configurations that enhance efficiency and reliability.
The integration of AI into engineering is not without other challenges. Engineers must adapt to new tools and technologies. It is crucial for engineers to work closely with AI specialists, manufacturers and data scientists to address these challenges and ensure the responsible use of AI.
The benefits of AI for engineers across these disciplines are many. AI enhances decision-making by providing data-driven insights, reducing the reliance on intuition and guesswork. It enables more accurate and efficient designs, minimizing errors and rework. By automating routine tasks, AI frees up engineers to focus on more complex and creative aspects of their work, fostering innovation. cse
Eric Muth, formerly with Certus, Dallas
Switchgear, transformers and uninterruptible power supplies collectively form the backbone of electrical power systems, ensuring reliable electrical distribution and safeguarding critical equipment
In the field of electrical engineering and electrical infrastructure, the seamless operation of critical electrical systems relies heavily on the integration of robust components such as switchgear, transformers and uninterruptible power supplies (UPS). These indispensable elements play crucial roles in ensuring the reliability, efficiency and safety of electrical systems across various sectors, including mission critical, industrial, commercial and residential facilities.
• Learn about three pieces of electrical distribution systems equipment, including functions, key components and their importance in commercial buildings.
• Consider the codes and design requirements for switchgear, transformers and uninterruptible power supplies (UPS).
• Review an analysis of the different types and construction of each piece of electrical equipment.
Electrical switchgear performs as the foundation of electrical distribution, facilitating the control and protection of power flow, while transformers provide voltage transitions and distribution, bridging the gap between different voltage levels. Complementing these components, UPS provide vital backup power during outages or fluctuations, safeguarding against downtime and data loss.
Together, these vital pieces of electrical equipment form the backbone of modern electrical infrastructure, underpinning the functionality and resilience of critical operations in an ever-evolving technological landscape.
in electrical systems
Electrical switchgear is the foundation of electrical distribution within commercial facilities. Switchgear is composed of electrical devices, such
as circuit breakers, switches, fuses, relays and protective equipment, used to control, protect and isolate electrical equipment and circuits in power distribution and transmission systems. Switchgear plays a critical role in ensuring the safe, reliable and efficient operation of electrical networks by allowing operators to control the flow of electricity, protect against overloads and faults and isolate faulty equipment.
The construction of electrical switchgear involves several key components and processes to create a reliable and efficient system for controlling and protecting electrical power distribution. The main components of switchgear construction can give us a better understanding of their role in electrical distribution. Switchgear is typically housed in an enclosure or cabinet, which protects the internal components from environmental factors such as dust, moisture and physical damage.
Switchgear enclosure ratings include but are not limited to National Electrical Manufacturers Association (NEMA) 1, 3, 3R and 3Xall offering various types of protection including protection from rain, snow, dirt, dust water and so on. These enclosures may be made of metal, such as steel or aluminum or nonmetallic materials including but not limited to acrylonitrile butadiene styrene or polyvinyl chloride plastic or fiberglass.
Inside the switchgear are busbars: Busbars are conductive bars or strips made of copper or aluminum that carry electrical current within the switchgear assembly. These can be both horizontally mounted and vertically mounted within the board. Horizonal busbars connect the vertical sections of the switchgear together where vertical busbars distribute electricity to the branch circuits within a single vertical section. Depending on the number
FIGURE 1: An example of an electrical switchgear and its construction. These enclosures come in various ratings, such as NEMA 3R. The enclosure rating depends on where the switchgear is located. The left vertical shows the incoming power section with the main breaker to de-energize the downstream circuits for maintenance purposes. The right vertical illustrates the downstream branch circuits being served by the switch gear, which can include but is not limited to transformers, branch panels equipment, etc. Courtesy: Certus
of feeder breakers within the switchgear these may come in multiple vertical sections.
The busbars inside the gear will be bolted together for electrical continuity. They provide a low-resistance path for electricity to flow between the various components of the switchgear, such as circuit breakers or fused switches, otherwise referred to as the overcurrent protective devices (OCPD). OCPDs are automatic switches that are responsible for interrupting the flow of electrical current in a circuit when abnormal conditions occur, such as overloads or short circuits. They are a critical component of switchgear, providing protection for electrical equipment and wiring from damage caused by excessive currents.
Protective relays are devices that monitor electrical parameters, such as voltage, current and frequency and initiate protective functions in response to abnormal conditions. They can be used to trip circuit breakers, control the operation of switches or initiate alarm signals when predetermined thresholds are exceeded.
Control panels are integrated into switchgear assemblies to provide a centralized location for monitoring and controlling electrical systems. They may include instruments, meters and control devices for monitoring electrical parameters, as well as annunciators and alarms for indicating system status and alarms.
Wiring and connections within switchgear assemblies must be carefully installed and maintained to ensure proper operation and reliability. Wiring methods and practices must comply with applicable NFPA 70: National Electrical Code (NEC) codes and standards to prevent electrical hazards and ensure safe operation. Safety features such as interlocks, barriers and warning labels are incorporated into switchgear assemblies to protect personnel and offer maximum maintenance safety. These features help prevent accidental contact with live parts and provide a clear indication of hazardous conditions.
‘ The construction of electrical switchgear involves several key components and processes to create a reliable and efficient system for controlling and protecting electrical power distribution.’
For commercial projects, switchgear is the backbone of a facility and designers must have a firm understanding of national and local codes to provide safe and effective designs. Designers must abide by NEC and any local code amendments and adhere to best design practices to produce a design that emphasizes safety and minimizes hazards. NEC Article 100 provides definitions for various terms used throughout the NEC, including definitions related to switchgear, but not limited to switchgear assembly and switchgear compartments.
FIGURE 2: Visual representation of busbars within electrical switchgear. The busbars run horizontally from each switchgear section and are bolted together to maintain continuity between each section. The alternating current is carried across the busbars, which supply current to the downstream branch circuits. Typically, these busbars are made from materials such as copper and aluminum. Courtesy: Certus
NEC Article 110 covers general requirements for electrical installations. This article addresses aspects such as installation and use of electrical equipment, working space requirements and access for maintenance.
NEC Article 240 provides requirements for overcurrent protection devices, such as fuses and circuit breakers, which are commonly used in switchgear assemblies to protect electrical circuits and equipment from overcurrents. NEC Article 250 covers requirements for grounding and bonding of electrical systems, including switchgear installations. This article addresses aspects such as grounding electrode systems, equipment bonding and grounding of metal enclosures to ensure electrical safety and system reliability.
NEC Article 408 provides requirements for switchboards and panelboards, which are types of switchgear assemblies used to control and distribute electrical power within buildings and facilities.
This article covers aspects such as construction, installation, wiring methods and access for maintenance. NEC section 517.17 covers provisions for additional ground fault protection on switchgear serving patient care areas, which include general care areas, critical care areas as well as wet procedure locations.
A transformer is an electrical device that is used to reduce or increase voltage through electromagnetic induction. It consists of two or more coils of insulated wire wound around a magnetic core, generally made of laminated iron or steel. Transformers play a crucial role in electrical power distribution and transmission systems by changing the voltage levels of alternating current electricity while maintaining the frequency. This allows designers to provide branch circuits for important electrical components such as receptacle branch circuits, lighting branch circuits, motor branch circuits, branch circuits for control circuits, as well as branch circuits serving pieces of equipment. Transformers are composed of various major components that make up their overall construction. Taking a deeper dive into the major components can help better understand their role in electrical distribution systems as well as a further in-depth conceptual understanding.
The first major component is the primary coil. The primary coil is also known as the input winding. The input winding is connected from the source of electrical energy such as a branch panel, distribution board, switchgear, etc. When the alternating current flows through the primary coil of the transformer it creates a change in magnetic flux within the transformer’s magnetic core. The magnetic core then provides a path for the magnetic flux generated by the current flowing through the primary coil. The transformer’s magnetic core is generally composed of laminated iron or steel to minimize energy losses due to eddy currents and hysteresis.
The next major component is the secondary coil. The changing magnetic flux created by the primary coil in the magnetic core generates a voltage in the secondary coil, also known as the output winding. The induced voltage in the secondary coil depends on the turn ratio between the primary and secondary windings. The turn ratio between the prima-
ry and secondary windings determines the voltage transformation ratio of the transformer.
A step-up transformer increases the voltage level from the primary to the secondary coil, while a step-down transformer decreases the voltage level. This voltage transformation enables efficient power transmission and distribution across different voltage levels.
During the design phase of a project, designers partake in multiple considerations for the an economical and code-compliant electrical room design. Particularly for transformers, designers may take the approach of suspending the equipment to the structure of the building, pad mounting or stacking them within the room while keeping NEC in mind for each instance. A better understanding of NEC that apply to transformers helps build a concrete understanding for proper and safe electrical design.
Taking code-compliant design into consideration is paramount for electrical safety and maintenance. NEC Article 240 discusses requirements for overcurrent protection devices, such as fuses and circuit breakers, which are used to protect electrical transformers and associated wiring from excessive currents. It specifies the sizing, location and installation of overcurrent protection devices for transformers.
NEC Article 110 includes requirements for equipment clearances which is key to proper room design.
NEC Article 450 provides detailed requirements for the installation, wiring and protection of transformers, including their location, ventilation and clearances. It covers various types of transformers, such as dry-type, liquid-filled and autotransformers and addresses specific installation considerations for transformer vaults and enclosures.
When dealing with the design of a health care facility, NEC Article 517 goes in-depth on the additional requirements needed to meet health care standards. For transformers installed in health care facilities, Article 517 provides provisions related to patient safety, electrical grounding and emergency power systems. It addresses the installation of transformers in patient care areas, critical care spaces and medical equipment rooms.
Article 700 delves into emergency systems. Article 700 can be applied to any mission critical facility such as health care facilities, data centers, commercial facilities, etc. Article 700 provides the foundation for emergency power systems, including generators, transfer switches and batteries, which may be connected to electrical transformers to provide backup power during outages. This article specifies the installation and operation of emer-
3: Completed electrophysiology lab in Dallas showing the final construction such as the light fixtures, lab equipment, light booms, monitor arms, etc.
Courtesy: Certus
‘
Article 110 addresses aspects such as wiring methods and equipment labeling to ensure the safety and reliability of electrical systems. ’
gency power systems to ensure their reliability and functionality during emergencies.
Next is Article 450, Section 450.9, which involves transformer ventilation. This section provides requirements for the ventilation of transformer vaults and enclosures to prevent the accumulation of heat and gases generated during transformer operation. It specifies minimum ventilation requirements based on the transformer's kilovolt-ampere rating and the type of cooling system used.
Lastly, NEC Article 110 lays the groundwork for general requirements for electrical installations. Article 110 addresses aspects such as wiring methods and equipment labeling to ensure the safety and reliability of electrical systems.
A UPS is a piece of electrical equipment that provides emergency backup power to connected equipment in the event of a power outage or disturbance. UPS systems are commonly used to protect electronic equipment, such as computers, servers, networking devices, telecommunications equipment and critical industrial processes, from power interruptions, voltage fluctuations and electrical disturbances.
maintenance or if the system incurs a failure, as well as a transfer switch to manage transitions between power sources.
A monitoring and control system oversees UPS operation, continuously monitoring parameters such as voltage input, voltage output and battery status, ensuring optimal performance. The components of a UPS are carefully engineered to guarantee uninterruptible power supply for various critical applications, including data centers, health care facilities and telecommunications infrastructure.
Each component of a UPS has a different role: Battery bank: The internal batteries store the electrical energy in the form of dc. Batteries are typically sized based on how long the UPS can provide backup power during a normal power outage. Battery technology can be several different types including valve-regulated lead-acid, lithium ion and nickel zinc. The size of the battery cabinet is largely dependent on how long the required run time is desired.
Inverter: The inverter converts the stored dc power to ac power.
Electrical system insights
u Switchgear, transformers and uninterruptible power supplies (UPS) are key components of electrical infrastructure, each fulfilling a distinct role to ensure reliable and safe power distribution across various sectors, from commercial and industrial to residential and health care.
u Switchgear controls and protects electrical flow, transformers manage voltage levels and UPS systems provide emergency backup power during outages, collectively forming the backbone of modern electrical systems.
A UPS works by converting incoming alternating current (ac) power from the main supply into direct current (dc) power, storing it in a battery and then converting it back to ac power when needed to power connected devices.
The construction of a UPS involves integrating several essential components to ensure a reliable backup power supply during normal power outages or disturbances. An UPS comprises a rectifier or charger responsible for converting alternating current from the main supply into direct current to charge a battery bank. This battery bank serves as the primary energy storage unit, storing electrical energy to be used during power interruptions.
An inverter then converts the stored dc power back into ac power to supply connected equipment. The system also includes a static bypass switch for seamless power transfer in case of UPS
Monitoring and control system: The monitoring system and control system oversees the entire operation of the UPS components. This constantly monitors input voltage, output voltage and the battery status. If a utility outage occurs, the transfer switch will switch from utility power to battery backup power.
Rectifier and charger: The rectifier and charger take incoming ac power and converts it into dc power.
Static bypass switch: This provides a path for normal power to bypass the UPS system and supply electricity directly to the equipment it is serving.
Transfer switch: The transfer switch switches power from normal power to UPS power.
Some practical uses of a UPS system in a facility include:
• Hospitals, clinics and health care facilities to provide backup power for medical equipment, patient care systems and critical life support systems. They help maintain patient safety and ensure continuity of care in the case of power disruptions.
• Telecommunications infrastructure relies on UPS systems to maintain uninterruptible power for communication equipment, including telecommunication rooms, switching centers and data transmission facilities. UPS systems help prevent service interruptions and downtime in telecommunications networks.
• Police stations, fire departments and emergency response centers rely on UPS systems to ensure continuous power supply for communication systems, dispatching equipment and emergency response coordination. UPS systems support critical operations during emergencies and natural disasters.
• Industrial facilities incorporate UPS systems to provide backup power for control systems, process automation equipment and manufacturing machinery. They help prevent production disruptions and equipment damage caused by power fluctuations or outages.
• Banks, stock exchanges and other financial institutions use UPS systems to safeguard critical electronic transactions, data processing systems and communication networks. UPS systems ensure continuous operation and data integrity in financial services environments.
• UPS systems are essential in data centers to provide backup power for servers, networking equipment and other critical information technology infrastructure. They ensure uninterrupted operation and prevent data loss or corruption during power outages.
UPSs play a crucial role in numerous applications, necessitating adherence to several NEC articles to ensure their safe and compliant installation. NEC Article 645 outlines the use of UPS systems in information technology equipment settings, while Article 517 provides guidelines for UPS installation in health care facilities, ensuring patient safety and system reliability.
Additionally, UPS systems integrated into emergency power systems fall under the guidelines of Article 700, ensuring their proper operation during power outages. Legally required standby power systems, which may include UPS components, are subject to regulations outlined in Article 701, ensuring the reliability of systems crucial for safety or security.
Moreover, Article 708 addresses the installation of critical operations power systems, including UPS systems, in facilities requiring continuous and reliable power supply. Compliance with these NEC articles ensures the safe and effective deployment of UPS systems across various industries and applications.
UPS, switchgear and transformers are indispensable components in modern electrical distribution systems, each playing a vital role in ensuring the reliability, safety and efficiency of power supply. UPS systems provide critical backup power, safeguarding against disruptions and protecting sensitive equipment in the event of outages or disturbances.
‘ UPS, switchgear and transformers are indispensable components in modern electrical distribution systems. ’
Switchgear acts as the heart of electrical distribution, enabling precise control, protection and isolation of electrical circuits, ensuring smooth and reliable power distribution. Transformers facilitate voltage transformation, optimizing power transmission and distribution while minimizing energy losses.
Together, these components form a robust infrastructure that underpins the functioning of various industries, critical facilities and infrastructure networks, ensuring uninterrupted power supply and supporting the seamless operation of modern society. cse
Eric Muth is an electrical designer with a wealth of experience in designing electrical distribution systems, particularly in the sector of health care facilities in the consulting engineering realm.
R. Daniel Rucker, PE, Smith Seckman Reid Inc., Nashville, Tenn.
Dedicated outdoor air systems enhance humidity control, reduce energy use, simplify ventilation design and improve efficiency in building ventilation systems.
Dedicated outdoor air systems (DOAS) have become common design considerations for the supply of ventilation, or outdoor air, to building spaces. As the name states, DOAS, provides dedicated outdoor ventilation air without real consideration of meeting the space cooling or heating loads. DOAS precondition the air, which relieves other space conditioning equipment of much of the latent load.
Why specify a DOAS?
The ASHRAE Design Guide for Dedicated Outdoor Air Systems states the following reasons for using DOAS:
• Improving humidity control.
• Reducing energy use.
• Desire to simplify ventilation design and control.
• Desire to use heating and cooling equipment that doesn’t provide ventilation and/or dehumidification.
• Reducing installation cost.
Consider the first point. DOAS dehumidification is not just a byproduct of the cooling coil process, it is the primary function. The second point is accomplished by only conditioning the desired amount of ventilation air and using reclaimed condenser heat, in this case with direct expansion (DX) cooling, in lieu of other heating means that have an associated cost. The third reason considers that the DOAS is a separate system from the space cooling and heating systems, which simplifies calculations for multizone systems that can be controlled separately from the space conditioning system equipment.
Therefore, the ventilation is “decoupled” from the heating and cooling systems, and operation of one does not affect operation of the other. The fourth point is that, typically, DOAS systems use low-pressure ductwork and are only sized for outdoor air requirements. This, along with other cost benefits, explains the fifth reason.
Ventilation air distribution in DOAS
An important consideration in DOAS design is
• Understand the best location of DOAS air distribution in a space.
• Learn how to use energy recovery for DOAS.
• Identify temperatures, controls and other key considerations for DOAS design.
how to distribute the ventilation air in the space. Two methods are commonly used. In the first method, the DOAS preconditioned air ventilation air can be mixed with return air from the zone-level heating, ventilation and air conditioning (HVAC) system. The supply air ductwork and diffusers are then utilized to distribute both the ventilation air and air for conditioning the spaces. This eliminates the need for extra diffusers and ductwork in the space, may be less costly and may make it easier to design on a drawing. Codes do require the ventilation air to be supplied continuously, so this method needs the supply fan(s) to operate continuously while the space is occupied. Zone air distribution effectiveness (Ez) must be accounted for when utilizing this method and is discussed in more detail below.
A second method to distribute the ventilation air is to deliver the DOAS air directly to the space utilizing traditional diffusers and grilles. Both methods are common, but this method is used especially with ductless system types, such as variable refrigerant flow (VRF) cassettes and chilled beams. An advantage of the second method is that if there is an operational problem with either the DOAS or space conditioning system, it can be identified without being masked or compensated for by the other system. Another benefit comes from the possible reduced amount of required air to a space.
Most ventilation codes include an Ez for the required outside air calculations. In many traditional systems, which are responsible for providing both ventilation and space conditioning, the outside air is mixed with the return air and conditioned before being supplied to the space. When this air is designed to be supplied from a ceiling diffuser that is 15 F warmer than the space temperature, and the return air is via the ceiling, the Ez value is 0.8. This results in a 20% increase in the required outdoor airflow provided to the space. This must also be applied to DOAS if the air from the DOAS is mixed with return air from the space and then conditioned (heated) to satisfy the heat-
ing load in the space. When ducted in this manner, the required ventilation air from the DOAS to the return air stream is effectively increased 20%.
However, if the DOAS air is supplied directly to the space at the ceiling at a temperature just cooler than space temperature, the Ez effectiveness is 1.0 and no increase in required ventilation air is needed. The extra 20% can add up across a building, and can lead to increased DOAS equipment and energy costs. Usually, the DOAS air that ducts to grilles in the spaces are easier to balance. An additional benefit of DOAS ducted directly to spaces is that the supply fans used for space conditioning do not have to operate continuously to maintain code required ventilation. They can cycle off in a deadband condition when not required for
ventilation airflow should provide overall positive building pressure and meet the code-required minimum energy recovery enthalpy recovery ratio.
4: Delivering dedicated outdoor air directly to a space using traditional diffusers and grilles is common in chilled beam applications. Courtesy: Smith Seckman Reid Inc.
space cooling or heating. On the other hand, supplying DOAS air directly to the space does require the costs of grilles, their installation and any additional ductwork.
Note the nominal capacity of a DX cooling coil, such as what you’d find in a zone-level packaged or split system, is listed in product catalogs at Air Conditioning Heating and Refrigeration Institute (AHRI) Standard Rating Conditions. The engineer is advised to account for different entering air conditions when DOAS are used in conjunction with the space cooling and heating equipment. Capacities of the space conditioning equipment and other parameters differ from the nominal AHRI published conditions for the space equipment based on entering air condition. Nominal capacity values, or capacities listed at AHRI conditions, do not apply and a manufacturer’s selection is recommended to ensure space loads are met. The HVAC engineer should consider these strategies and determine which is best for the project before detailed design begins.
Exhaust air energy recovery is often considered when designing a DOAS to potentially reduce equipment sizing and energy usage. Energy codes require energy recovery for systems with high percentages of outside air. The percentage where energy recovery is required has steadily decreased with new code updates. The applicability of this require-
ment varies based on climate zone, supply fan airflow rate, percentage of outside air and ventilation system operating hours per year. When required by codes, energy recovery devices, such as enthalpy wheels and fixed membrane heat exchangers, must have a minimum enthalpy recovery ratio of 50%.
Additionally, a bypass damper or some other control must be included to disable the device when outside air conditions are not conducive for energy recovery, such as when air economizers would normally be active.
There are exceptions to the energy recovery requirements, so verify specific code requirements enforced for each project. It is considered best practice to utilize energy recovery where possible, even if there is an exception that applies. At times, the exhaust flow from the spaces may need to be increased from minimum requirements to meet the efficiency standard for the energy recovery device. The engineer should design the DOAS ventilation airflow and the exhaust airflow to provide overall positive building pressure and meet the code required minimum energy recovery enthalpy recovery ratio.
When including energy recovery in a DOAS, engineers must decide whether to account for the capacity of the energy recovery device when sizing cooling and heating coils. If cooling and heating capacities are reduced, energy recovery can appear more cost-effective, but risk increases. However, if capacities are not reduced, the ventilation load is met even if the energy recovery device fails or is later removed. Either way, maintenance of the energy recovery device is just as critical as any other portion of the DOAS.
To dehumidify the raw outdoor air in summer, the DOAS cools the supply air down below saturation or dewpoint, and moisture is removed from the air as condensate. Many engineers will use the ASHRAE dehumidification design condition and heat recovery temperatures to assure they have accounted for the full dehumidification load. A leaving coil temperature of 52 F or lower is typically used for the design. In cooling season, the air can be sent to the spaces at this temperature, but there is a risk of overcooling some spaces. At times, the saturated air is reheated to avoid over cooling.
However, energy codes limit the reheat in cooling season to no more than 60 F if the majority of zone-level HVAC systems served by the DOAS require cooling. In this way, not only is no ventilation load added for the space conditioning systems, but the DOAS helps to reduce the load on the space cooling system.
Additionally, engineers need to be mindful of the supply location of the DOAS airflow in the space, and that the air needs to be cooler than the space temperature to utilize the zone effectiveness ratio of one for the required airflow calculations mentioned above. Therefore, many engineers specify duct insulation on the DOAS air even when the duct is exposed in a conditioned space.
Demand control ventilation (DCV) can be accomplished with a DOAS design. Typically, variable air volume (VAV) cooling only terminals are used to provide DOAS supply air to a space requiring DCV. In this scenario, the DOAS maintains a duct static pressure setpoint in the supply duct and the supply fan speed varies to maintain the static pressure. The VAV terminal can be set to a minimum unoccupied flow. As carbon dioxide (CO2) levels rise when spaces become occupied, the VAV terminal opens and supplies more ventilation airrequiring the DOAS supply fan to increase until the CO2setpoint level is obtained.
Constant volume VAV terminals are also needed to maintain the proper ventilation air for other spaces that do not need DCV. Without constant volume VAV control, the required ventilation airflow can fluctuate and become too little or too much. Likewise, there needs to be control for the exhaust amounts and supply, while maintaining overall building pressure. Energy codes are less likely to require DCV if energy recovery requirements are met. The requirement depends on which code or standard is used, and which year version is enforced. To minimize complications, the engineer is advised to check the DCV code section that applies to the project early in the design process.
Packaged equipment manufacturers provide almost all components necessary for the operation
of a DOAS, but there are a few others the engineer may want to consider.
Outside air measuring stations: DOAS units do not necessarily include an outdoor air measuring station. Information from the station can be valuable in trouble shooting, and can be used to vary the supply speed based on filter loading so that the airflow rate through the unit remains constant. The outside air measurement provides one of the most crucial pieces of information available for why a DOAS was chosen in the first place. You can’t control what you don’t measure, so the outside air measurement should be considered for each DOAS. There are multiple ways to accomplish reading the airflow values, including piezo rings and thermal dispersion instruments. For similar reasons, exhaust airflow measurement is desired and the engineer can choose what might be the best method for their project.
Condensate overflow sensors: While these are not required for most applications, many DOAS units are roof mounted and ducted through to the spaces below. Eventually, condensate drains get clogged and need to be cleaned out. Even though the condensate is at the roof level and may not pose an immediate nuisance threat to occupants below, chances are high that the overflow will get into the duct and leak into the ceiling space. An overflow alarm sensor prevents this from becoming a problem. It can de-activate the unit and keep it from becoming a larger issue. The building automation system (BAS) or local alarm should be signaled. The DOAS is the main way ventilation air is sup-
FIGURE 5: Measuring the temperature, humidity and other status points allows engineers to see the benefits and required maintenance on dedicated outdoor air systems.
csemag.com
DOAS insights
uDOAS improve humidity control and reduce energy consumption by decoupling ventilation from other heating and cooling systems.
uDistributing ventilation air directly to spaces with DOAS can enhance efficiency and reduce required airflow.
FIGURE 6: This 11-ton, roof-mounted, packaged dedicated outdoor air system is a heat pump that uses a separate variable refrigerant flow system to heat and cool individual spaces. Courtesy: Smith Seckman Reid Inc.
plied, so its continued operation is crucial to the indoor air quality.
Filter gauges: These should be provided, and control alarms signaled, when the filter pressure drop indicates it requires changing. It is not uncommon for the filters to need changing more often than most facility operators may be expecting. DOAS, with 100% outside air, have the capability of introducing much more air particulates than other air systems, making monthly filter changes common. The particulate quantity depends on the local environment and what might be circulating in the air at the project site. There are many variables, so a good filter alarm is crucial. It is also best practice to filter the exhaust before it flows through the enthalpy wheel, and place a filter gauge and alarm there as well.
With packaged DOAS equipment, most temperature and humidity sensor status indicators are included. The usual monitoring points include:
• Temperature points: exhaust, outside air, mixed air (outside air downstream of enthalpy wheel), cooling coil leaving air, hot gas reheat leaving, hot gas reheat leaving air and supply air to spaces.
• Humidity points: exhaust before the enthapy wheel (or space humidity), outside air and supply air to spaces.
• Other status points: supply fan on/off status and speed, exhaust fan on/off status and speed,
‘ The DOAS is the main way ventilation air is supplied, so its continued operation is crucial to the indoor air quality.’
enthalpy wheel on/off status, filter differential pressures, supply and exhaust airflows and heating percentage.
• Any sensors not provided by the DOAS manufacturer can be added to the BAS as separate control points.
Package units usually come programmed for five modes of operation.
• Cooling: In cooling mode, supply air temperature set point can be 60 F and the compressors modulate to maintain the supply air setpoint.
• Heating: In heating mode, the supply air setpoint can be 68 F, or 2 degrees lower than the space temperature, and the heat input is modulated to maintain the supply air setpoint.
• Vent: Vent mode is when neither cooling nor heating is required. The enthalpy wheel can be turned off or bypassed.
• Dehumidification: Dehumidification is a special case of the cooling mode, and is initiated when the exhaust or space humidity level reaches a setpoint of 60% relative humidity. The compressors only modulate to maintain a low suction temperature and the hot gas reheat is modulated to maintain the supply air temperature.
• Off: Off is for when no ventilation air is required or unoccupied periods.
It is best practice to use the packaged unit manufacturer’s programmed algorithms for these functions and only monitor the sensors and devices mentioned above. Actual control points for user input are usually unit start/stop, supply air temperature setpoint, cooling season setpoint and heating season setpoint. This keeps the controls simple for operating personnel. cse
R. Daniel Rucker, PE, is a Senior mechanical engineer at Smith Seckman Reid Inc.
Jason Gerke, PE, CxA, LEED AP BD+C, GRAEF, Milwaukee; and Anthony Chmielewski, PEC – A Zero 6 Energy Company. Brookfield, Wisconsin
Combined heat and power systems provide solutions for lowering utility costs, increasing electrical and heat source reliability and providing resilience for continued facility operation.
Combined heat and power (CHP), or cogeneration, is a process where electricity and usable heat are produced coincidentally. The benefit of CHP is increased energy use efficiency compared to traditional utility power generation from the grid and heat from a local source - such as a facility steam boiler. Limiting factors preventing widespread expansion in the early development days included the physical separation of power-generating facilities from industrial hosts and utility control of the sale of generated electricity to customers.
However, CHP has always been popular in heavy industrial or campus facilities, where substantial amounts of electricity and thermal energy are used continuously.
CHP plants offer upward of 80% increased overall efficiency, which reduces energy cost, lowers emissions, lessens the greenhouse gas footprint through less fuel consumption and improves reliability by locating a backup source of electrical generation at the host site to protect against grid outages.
The U.S. Department of Energy, Office of Energy Efficiency and Renewable Energy, defines the CHP process as “the concurrent production of electricity or mechanical power and useful thermal energy (heating and/or cooling) from a single source of energy.” While this basic definition allows for several different input fuels to have a variety of outputs, this article is based on natural gas as the input fuel and electricity with a heat supply as the output.
Because natural gas is the most common fuel for CHP facilities, recent trends are driven by low natural gas prices, the desire to lower greenhouse gas footprint and financial incentives from the government’s green energy initiatives. Proponents of CHP have stipulated that distributed generation, meaning noncentralized electrical power generation, helps avoid the need for new electrical transmission and distribution infrastructure and eases power grid congestion. With the rapid advancement of electric vehicles and renewable energy generation, the country’s electrical transmission and distribution infrastructure will be pushed to the limit and CHP can assist in this transition.
CHP projects may be implemented for a variety of facility types and for a variety of sizes depending on parameters. There are drivers for each system type and size that are based on the specific site needs, including financial restrictions, owner needs and process requirements.
In most cases, large CHP projects are the most viable and successful because of economies of scale. Large-scale energy cost savings in fuel and electricity provide enhanced payback when compared to overall capital expenditures and the level of effort required to execute a successfully CHP project. Additionally, large CHP hosts or owners are often familiar with the integration and operation of these types of complex facilities.
Small CHP projects have been more successful recently due to the fully integrated packaged designs developed by equipment integrators. These small CHPs are marketed as either containerized or “plug-and-play,” where a host can simply purchase a fully integrated package and install the CHP within their existing system infrastructure. Examples of these types of systems are microturbines with heat recovery, reciprocating engine generators with hot water heat recovery systems and waste heat packages that produce usable energy from heat that would normally be exhausted to the atmosphere.
Numerous factors contribute to the successful implementation of a CHP project, but the following are generally most prevalent:
• The project is in an area where the electrical utility is a proponent of CHP or open market electrical interconnection conditions exist. Many projects fail because the interconnection of a distributed generation asset is blocked by the utility, even if the host’s desire is only to serve internal, “behind the meter” electrical demand. Islanding or disconnecting from the utility completely often derails projects because of the high cost of redundant generation assets and reliability risk factors.
• There is continuous electrical and thermal energy demand of reasonable size. Electrical and thermal demand needs to “match” in a certain
• Understand how combined heat and power systems
• Identify the steps that lead to successful implementation of combined heat and power systems.
• Learn planning and design considerations for combined heat and power systems.
There are numerous design considerations when planning for a CHP facility. The considerations are typical for most large and small CHP systems and are driven by equipment options, local building codes and owner needs. The design team for a CHP system needs experienced project partners to successfully implement a system, whether a standalone structure or an integrated system.
Combined heat and power systems include many different systems, each individually addressed in building codes. These systems include boilers, turbines and electrical distribution gear. These systems are supported by other building utilities including natural gas distribution, ventilation systems, lighting, fire alarm, security/surveillance and general plumbing systems. There are numerous sub-sets of these main systems to support the overall process system of CHP.
CHP insights
u Combined heat and power systems enhance energy efficiency and reduce both operational costs and greenhouse gas emissions.
u The success of CHP projects often hinges on factors like continuous demand for electrical and thermal energy, favorable utility policies and attractive payback on energy cost savings.
range. Projects are generally not successful if one or the other is abnormally small. A CHP design configuration can be selected as more “electrical power dense” or “thermal concentrated,” but generally a continuous demand of some minimum size is required for a CHP to make sense.
• Payback on CHP energy cost savings are attractive enough from a capital expenditure standpoint. A CHP host can either deploy available capital or enter a contract to buy energy from a third-party-owned CHP on the host site. In many cases, the host’s core business is completely unrelated to the CHP and the savings payback potential is not worth that capital commitment. Many hosts prefer to deploy available capital to their core business interests. Additionally, signing long-term agreements, generally 15-20 years, with a third party is often challenging from a business commitment and financing perspective. However, if energy cost is a substantial component of the host’s operating cost structure and the savings payback is significant, a CHP project can be successful.
• The host is motivated by outside factors. This may include emissions reductions, desire to lower their greenhouse gas footprint, necessary replacement of existing energy infrastructure or expansion of energy users such as electrical and thermal as part of a facility expansion.
Available CHP equipment, including specialized boilers, turbines and electrical gear, will primarily drive the building layout. This equipment is typically specialized for the specific installation and requires close coordination with the equipment manufacturers to ensure the systems can provide the required capacity and capability. Building size will further be driven by the available space on a site. Often a single-story structure will be the most cost-effective, but site constraints require a multistory building to house the equipment.
A CHP facility needs to house the primary process equipment and allow for the utility connections to serve this equipment. As mentioned, there are several sub-systems required to support a CHP process that require space in and around the building in addition to the space requirements for the direct process equipment.
Sub-system space considerations include:
• Input fuel source: An example of this is natural gas that requires space for a large meter assembly on the building exterior and close coordination with the supplier to ensure adequate supply during normal operation and through any unexpected events that may affect the distribution system.
• The transformation, metering and distribution of electrical power: This electrical distribution needs to comply with utility requirements for metering, isolation and other standards. Commonly, electricity is generated through a turbine uti-
lizing boiler steam or hot water from a generator or engine jacket. This hot temperature medium is then fed through a turbine generator to produce electricity. The electricity from the turbine may be medium voltage that requires transformers and other gear in a separate electrical room to convert it into a usable type for the building or campus.
• Support space for CHP operators: While the CHP process may be set up to be automated, operators are still required to perform maintenance, oversee the process and be available to address operational issues as they occur.
An important part of the design for a CHP process is compliance with local building codes. Different areas in the U.S. utilize different versions of codes, some current, some a few years old. Generally, in the U.S. compliance with International Code Council (ICC), such as the International Building Code, International Mechanical Code and the International Energy Conservation Code, are the minimum requirement, though some areas of the country utilize uniform codes or other standards. The design team must identify early on which codes are in effect for the project location, especially if the design team includes project partners from different areas of the country.
Commonly, utilizing the ICC codes for the specific years adopted by the local authority having jurisdiction (AHJ) will provide 70% of the project’s code requirements. The AHJ may provide other information that is focused directly on CHP systems, such as New York City’s Building Code and Energy Code, which provides specific separation and efficiency requirements that must be met for code compliance. Another source of information for planning and design of CHP systems is located in the National Fire Protection Codes (NFPA), including NFPA 13: Standard for the Installation of Sprinkler Systems, NFPA 70: National Electrical Code and NFPA 110: Standard for Emergency and Standby Power Systems. It is important that the design team carefully considers other NFPA standards that may apply to the project and ensure that the design meets a standard of care by using the best resources available.
of power dense combined heat and power design
The DTE Dearborn Central Energy Plant (CEP) is a 34-megawatt (MW) gas-fired combined heat and power (CHP) plant that is co-located with a chilled water plant and equipped with a thermal energy storage tank. The facility is designed to deliver 34 MW of power to DTE Electric’s power grid, generate up to 225,000 pounds per hour of steam for heating and process use, produce hot and chilled water for campus buildings and store chilled water to help minimize on-peak electrical demand.
DTE reports that the CEP is a highly efficient and flexible central plant that includes: a 50% reduction in carbon footprint, as compared to an older steam powerhouse that the CEP replaced; a 50% reduction in water use, a 60% improvement in chilled water production efficiency, as compared to multiple existing in-building chillers; and a significant amount of space heating provided from recovered waste heat.
The success of the project is rooted in the fact that it was a collaborative effort between DTE Electric, a regulated utility and and DTE Energy Services, a nonregulated third-party developer or operator. When necessary, power from the CHP generators can be pushed to the power grid or utilized within the boundaries of the Ford campus — providing a high degree of design flexibility. The campus included yearround large continuous thermal users (steam, hot water and chilled water).
The CHP itself consisted of two 14.5 MW gas turbines and two heat recovery steam generators, which can be supplementally fired when necessary, to produce additional steam beyond that produced from gas turbine exhaust heat. The CHP design includes a 5 MW condensing steam turbine generator, which can utilize steam produced from exhaust heat during the summer months when heating steam demand is low and electrical demand is high. Use of gas turbines indicates a “power dense” CHP design, where a reasonably substantial amount of electric generation is normally deployed. In this kind of design, heat recovery can be operated in a very wide range, from nonfired (heat recovery only mode in the summer) to supplementally fired, when substantially more steam for process and heating use is required in the winter. The chilled water plant includes electric-driven mechanical chillers, utilizing the electric power generated by gas turbines.
All CHP project success factors were evident in the CEP. The electrical utility involvement was crucial to interconnection approvals, design and execution. The Ford campus provided a large thermal and electrical demand host. The highly efficient design in all aspects of the CEP provided substantial energy cost savings from previous operations. The company's overall carbon dioxide footprint was substantially reduced at their primary research and engineering campus, which was not only required from a regulatory perspective but also from an overall company desire.
‘ It is imperative that the project team include an early review of allowable discharge limits, site approval and general conformance with land use requirements before starting a CHP project.’
Miura is dedicated to producing reliable, efficient, and safe steam generation systems for pet food processing companies. Our complete solutions approach ensures your facility operates at peak efficiency, addressing all aspects of your boiler room. We invite you to experience unparalleled efficiency and savings with Miura during our limited-time Summertime Savings event.
Owner requirements may be considered the most important part of the design process, because without these requirements the project may not exist. The project owner could be a system developer, process company or other organization providing project funding. There are a few common goals of a CHP project including: to increase electrical reliability on a site with the benefit of an additional heat source, to provide the facility with the ability to go off-grid and be standalone from the local electrical utility or to increase project resilience for the facility in the aftermath of a natural disaster by quickly reengaging the process and systems at a facility.
There are many resources beyond building codes to consider when designing CHP systems. The Environmental Protection Agency provides basic resources for planning and designing CHP systems focused on increasing reliability and resilience in buildings, particularly for protecting buildings during and after natural disasters.
Environmental compliance is an integral part of establishing a CHP system for a facility. Compliance standards vary throughout the country and each location may have specific requirements beyond those of federal or state codes. It is imperative that the project team include an early review of allowable discharge limits, site approval and general conformance with land use requirements before starting a CHP project. These requirements may greatly affect the size and location of a CHP project as well as the construction and operation of the facility. cse
Jason Gerke, PE, CxA, LEED AP BD+C, is Practice Area Leader – MEP | Principal, at GRAEF,
Anthony Chmielewski is a Principal at PEC - A Zero6 Energy Company.
Addison solutions o er significant benefits for data centers. These include:
OUTDOOR Packaged DX
• Available in both Air-Source and Water-Source Heat Pump Configurations
• Adaptable for every application requiring dedicated outdoor air, mixed air, and dehumidification
• Supplies conditioned make-up air to replace exhaust air as well as outside air needed for occupants
Modular Indoor Air Handler (CRAH)
• Modular Design
• Adaptable for every application requiring dedicated outdoor air, mixed air, or recirculation
• Available in both Air-Source and Water-Source heat pump applications
• Available with HybridAir Technology
Indoor Vertical Water-Cooled DX (CRAC)
• Dedicated Outdoor Air or Recirculating Cooling/Dehumidification Operation
• Optional Water-Source Heat Pump Operation
• Compact Design
• Compatible with every application requiring indoor units for ventilation, cooling and/or dehumidification
Split System DX or Chilled Water (CRAC/CRAH)
• Dedicated Outdoor Air or Recirculating Cooling/ Dehumidification Operation
• Optional Heat Pump Operation
• Modular Design - allows installation in tight spaces
• Ideal for every application requiring split systems for ventilation, cooling and/or dehumidification
• Downflow Air Tower available as a DX split system or a chilled-water AHU
Addison products excel in data centers for our unmatched reliability, e iciency and redundancy features. Engineered to maintain precise environmental conditions, Addison products ensure uninterrupted operation of sensitive equipment. Our customizable options make them the ideal choice for safeguarding critical infrastructure. Addison solutions also boast unbeatable 12-week lead times for standard products ensuring prompt deployment and minimal downtime for data center operations. www.addison-hvac.com
Caleb Marvin, PE, Certus Consulting Engineers, Dallas
In the realm of surgical precision and patient care, every detail within the operating room environment plays a pivotal role in ensuring successful outcomes. Temperature and humidity within the operating room stand as critical determinants of both patient safety and surgical efficacy. Surgeons and medical professionals alike understand that the delicate balance between surgical team comfort, patient safety and optimal surgical conditions hinges upon careful control of environmental variables, of which temperature is no exception.
ASHRAE Standard 170: Ventilation of Health Care Facilities dictates that the temperature range in an operating room should fall between 68 F and 75 F, but also allows for temperatures to be outside of this range for surgeon preference or surgical procedure requirements. More and more surgeons are requesting temperatures as low as 62 F in operating rooms for personal comfort reasons. This becomes difficult for existing facilities that don’t have additional measures beyond a typical heating, ventilation and air conditioning (HVAC) system required to achieve these lower temperatures.
With the volume of air that operating rooms are normally provided, it seems simple enough to achieve temperatures lower than 68 F. However,
Many hospitals and health care facilities struggle to maintain temperature and humidity in operating rooms, especially as doctors are asking for lower temperature options. Three kinds of dedicated outdoor air systems can solve this challenge.
issues often arise from the second environmental condition — relative humidity.
Space relative humidity affects multiple functions that are crucial to successful procedures in an operating room. Low relative humidity (below 20% as required by ASHRAE 170, or 30% in some jurisdictions) can lead to static electricity or desiccation of tissues, causing them to become brittle and more prone to damage during surgical manipulation. Humidifiers are required in most climates to maintain the minimum relative humidity with the high quantity of outside air provided in operating rooms. Various strategies can be used to maintain a relative humidity below the maximum of 60% allowed by ASHRAE 170.
Controlling humidity helps mitigate the risk of microbial growth and transmission within the operating room. High humidity levels can create conditions conducive to the proliferation of bacteria, viruses and fungi, which pose a significant risk of surgical site infections. By keeping humidity within recommended ranges, health care facilities can reduce the likelihood of airborne and surface-borne pathogens spreading during surgical procedures. Many medical devices and equipment used in surgical procedures are sensitive to environmental conditions, including humidity levels. Excessive humidity can damage electronic components and lead to equipment malfunction, compromising patient safety and surgical efficiency. High
• Identify the concerns with existing systems and low temperature operating rooms.
• Learn the different types of dedicated outdoor air system units.
• Understand how an engineer implements dedicated outdoor air systems unit in an existing system
1, ABOVE: A diagram of the components in a direct expansion refrigeration cycle system. Courtesy: Certus Consulting Engineers
air to the operating room must be at or below 49 F dewpoint.
Keeping the same dewpoint with a 62 F space, what happens to the relative humidity? At those conditions, the operating room would have a relative humidity of 62%, above the maximum allowed conditions by AHRAE 170 and most applicable codes. This is that supplemental or special systems are required to provide low-temperature operating rooms for surgeons. To achieve a 62 F temperature setpoint and 50% relative humidity, the dewpoint of the supply air to the space must be a maximum of 43° F. Typical HVAC systems deliver supply air from 49 to 52 F dewpoint and are therefore unable to meet the demand.
humidity levels may compromise the sterility of surgical instruments and supplies, increasing the risk of contamination and surgical complications.
AHRAE 170 indicates relative humidity for operating rooms must remain between 20% to 60%. These humidity requirements mean that the dewpoint of the discharge air supplied to the operating rooms must be evaluated to maintain both the room temperature setpoint and the room relative humidity setpoint.
The standard setpoint for an operating room at code recommended minimum is 68 F at 50% relative humidity. The dewpoint of this room condition is 49 F at sea level, which means that the supply
To aid existing systems in achieving lower space temperatures, dedicated outside air systems (DOAS) can be installed to condition and dehumidify outside air. By pretreating the outside air to below the required dewpoint, the existing mixed air system only needs to handle the sensible space load.
Three DOAS system types are generally used to pre-treat the outside air before being introduced into an existing system:
• Direct expansion (DX).
• Glycol chilled water.
• Desiccant.
All three options have the capability to be placed in series in the outside air path to dehumidify outside air before being supplied to an existing HVAC unit.
DX DOAS units: These units cool outside air through the refrigeration cycle and can come as packaged units with all components integral or with the evaporator coil located in the DOAS with a separate condensing unit. It is worth mentioning here that care must be taken in selecting DX systems to achieve low leaving air temperatures. DX desiccant systems utilizing hot gas for regeneration were popular for a time, but hot gas required for regeneration may not be available in low sensible load conditions.
Glycol chilled water: Standard chilled water plants provide 42 F chilled water to air handling
water DOAS gave a rural hospital’s operating rooms precise temperature and humidity control.
Certus was asked to help a rural hospital attain low-temperature operating rooms with their existing air handling systems. The operating rooms were having difficulty maintaining the required 68 F room setpoint at 50% relative humidity, and a new doctor requested the spaces to get to 62 F at 50% relative humidity. With these initial requirements, the first task was to determine what kind of dedicated outdoor air system (DOAS) to provide.
Maintenance response time was a key factor in system and equipment selection. The facility wasn’t comfortable with desiccant technology, as there were no other desiccant systems at the hospital or in the region. The hospital had both DX and chilled water systems with qualified service technicians in the area who could respond quickly.
The final decision between DX and glycol chilled water came down to controllability with the system. The facility preferred precise control with glycol-chilled water.
The DOAS unit was designed to deliver a constant discharge air temperature of 40 F to both existing AHUs. A first filter was provided in the unit to protect coils from dirt, but final filters were provided only in the existing AHUs. The DOAS came with two cooling coils to maximize the energy efficiency. A normal chilled water coil off the existing plant provided the first stage of cooling for the outside air down to 49 F.
An existing water-cooled plant allowed for a more efficient cooling mode, rather than increasing the size of the air-cooled glycol chiller to handle the entire outside air load. The pipe size for the mains did not need to be increased either, as the chilled water load was moved from the existing AHUs to the DOAS unit. A sub-cooling coil then followed the primary cooling coil. This setup required a heating water preheat coil before the cooling coils to protect the chilled water coil from freezing.
‘ An existing water-cooled plant allowed for a more efficient cooling mode, rather than increasing the size of the air-cooled glycol chiller to handle the entire outside air load.’
The operating rooms were served by one air handling unit (AHU) on the roof and another in an interior mechanical room, with outside air connection on the same roof. A glycol-chilled water DOAS could be placed on the roof, ducted to the outside air inlet on the rooftop unit and into the outside air duct outside. An air-cooled chiller with integral pumps kept the equipment consolidated to one area. The glycol chilled water temperature was because of the desire to achieve a 40 F discharge temperature off the sub-cooling coil. Because the chiller was placed near the DOAS unit, the system volume was too little with the piping for the air-cooled chiller. A buffer tank was added to allow for the minimum system volume required for constant temperature back to the chiller.
unit (AHU) cooling coils. This delivery temperature creates problems when attempting to cool air down to lower dewpoint temperatures. The heat transfer through the coil is unable to cool the air down to lower temperatures with standard chilled water plant supply temperatures.
Glycol can be provided with chilled water then to create a mixture that reduces the freezing point of the water to supply lower temperatures as low as 28 F. Lower temperatures achieve better efficiency for the coil, but engineers must pay attention to manufacturers’ recommendations that water temperatures below freezing can cause ice to form from condensate on the cooling coil. For this reason, 34
A unique challenge in this project came when ducting to both existing AHUs. One AHU was a constant volume system with no economizer, while the other was a variable volume system with economizer cycle. How do you control different systems when one is calling for a constant quantity of outside air and the other calling for a varying amount? The DOAS was sized for the minimum amount of outside air required for the two units. Motorized dampers in the taps to each AHU and separate outside air intakes in the ducts with motorized dampers were provided to close off the DOAS unit and bring outside air in normally by the existing AHU supply fans.
The economizer cycle for the existing AHU was enabled when the dry bulb was less than 65 F, and the dew point was less than 40 F. Once the economizer was enabled, the DOAS was called to disable, and the motorized dampers switched their respective positions to allow outside air into each unit. This allowed the two separate systems to receive outside air at the necessary dewpoint for the desired condition.
F is a common glycol-chilled water supply temperature with 20%-30% propylene glycol. Glycol chilled water systems require the same equipment and components as a standard chilled water system to provide glycol chilled water to AHU cooling coils. Typically, an air-cooled chiller is provided and then pumped through a closed circuit. Based on loop length, a buffer tank may be required to maintain the manufacturer’s recommended time lag so that the glycol chilled water can provide constant water temperature back to the chiller. Glycol makeup units can also be provided to monitor and release glycol into the system to maintain a constant mixture.
FIGURE 3: An example of a desiccant dedicated outdoor air system. Courtesy: Certus Engineers
csemag.com
Operating room insights
u The three system options when retrofitting low-temperature operating rooms are direct expansion, glycol chilled water and desiccant.
u Precise control of environmental conditions, such as maintaining a specific dewpoint, is crucial in retrofitting operating rooms.
Desiccant: This technology utilizes a wheel impregnated with a chemical media, typically silica, to drive moisture from one airstream to another. A desiccant wheel uses the difference in relative humidity between two airstreams to absorb moisture from a saturated airstream and move the moisture to a dry air stream. This process allows the saturated airstream to be dehumidified below the required dewpoint.
Type 2 active desiccant systems heat the incoming reactivation air to dry it out before entering the wheel, which allows the maximum absorption of moisture from the saturated air stream. This is the most common type of desiccant for retrofit applications, as it is typically a packaged unit using heating water, electric, steam or natural gas to heat the process airstream for regeneration of the media.
Type 3 desiccant systems can dehumidify the using return air, but the process may be difficult to implement in existing systems. This type is excellent when used for greenfield and expansions where return ductwork can be planned with a new unit.
With these three options, how does one make the decision of which to use to help an existing system? Each option has benefits and drawbacks that need to be evaluated by the engineer and facility staff to make the best decision for the facility.
DX: This system type is generally the lowest upfront cost option and simplest from a maintenance standpoint. Most facilities have staff trained in these types of units, and fewer total components
need to be serviced and maintained by facility staff. While DX is typically the lowest first cost, it is also the least efficient option, with higher operating costs for the cooling provided. Attention to the existing electrical infrastructure is required to see the impact of adding the large electrical load to existing switchgear. The designer must balance the lower first cost from a mechanical side to the potential increase in electrical equipment.
There are also a few limitations with DX when cooling outside air down to the required dewpoint for lower-temperature operating rooms. Suction temperature becomes a concern when the cooling down to lower temperatures, and DX systems may not be able to achieve dewpoints around 42 F for colder rooms. As it gets cold, the coil can become frosted and iced over. Minimal loads are difficult on the compressor where the turn down of the variable speed drive is unable to maintain the low load. Hot gas bypass can be provided to help impose load on the compressor in these moments.
Glycol chilled water: This system comes in at a higher first cost than DX solutions, but has better controllability. Electronically actuated control valves modulate to maintain a specific discharge air temperature off the coil and deliver within a +/-0.5 F deadband. This type of system can easily maintain the necessary discharge air temperature for the space setpoints as low as necessary. Maintenance can become a burden as there are more components needed for glycol chilled water systems. Glycol chilled water systems with air-cooled chillers can run into similar problems at low loads. Variable speed drives on the compressors and hot gas bypass can be provided on the chiller keep load on the compressor in low load situations.
Desiccant: These systems can be very energy efficient, but may have a higher upfront cost than other DOAS options, and come with a complexity that requires special training for operators. Desiccant DOAS units can use either a variable frequency drive to modulate the desiccant wheel or maintain a constant wheel speed with bypass dampers to modulate and maintain a specific design dewpoint delivered by the unit. A desiccant DOAS unit’s energy efficiency will be dictated by the heat source used for the reactivation air. Heating water, natural gas, steam or electric can all be used to heat the air. The heating water tempera-
ture may not be high enough for reactivation temperatures if low temperature heating water is used for condensing appliances at the facility. Natural gas may not be available at the site, and pipe routing can be difficult if it must be run through occupied spaces. Central steam systems are less common in hospitals, so steam may not be readily available. Electric heat is always an option, but the amount needs to be coordinated at the electrical distribution level to see if it is feasible.
Now that the engineer has looked through the options and worked with the facility to decide which one is best for the facility based on upfront cost, maintainability and energy efficiency, how do they implement the DOAS into the existing system? Install the DOAS in the outside air path before it is introduced to the existing air handling unit to pretreat the outside air. The minimum outside air must flow through the DOAS system to achieve the desired dewpoint and then be supplied to the existing AHU. Pre-treated outside air can be ducted to an existing outside air duct routed to an indoor AHU or directly to the outside air louver on an exterior unit. In both situations, care should be taken if economizer cycles are provided for existing AHUs. Normal
economizer operation begins at 65 F dry bulb, which will introduce humid outside air to the unit and be unable to maintain the required dewpoint mixed with the pre-treated outside air. Economizer cycles either need to be disabled, or additional programming for the economizer cycle should to be enabled once the dry bulb is below 65 F and the dewpoint is below the required for the space setpoint.
As health care engineers, the health and safety of patients must guide our recommendations and decisions. At the same time, we need to be good financial stewards for our clients.
In evaluating requested low space temperature operating rooms, especially in retrofit applications, multiple options must be evaluated based on existing utilities available, maintenance staff availability and total cost of ownership versus simplicity and upfront cost.
There is not a “one size fits all” solution to this challenge. The key is for the engineer to understand all factors and to lead the discussion with key stakeholders to help develop the right solution to what is actually a very complex engineering problem. cse
Caleb Marvin is a senior associate at Certus Consulting Engineers, working predominantly on health care projects.
Tony Gonzalez, PE, Syska Hennessy, Hamilton, New Jersey
Rooftop units (RTUs) are popular choices for heating, ventilation and air conditioning (HVAC) systems because they optimize space, provide efficient climate control and feature modular designs. They save valuable floor space compared to air handling units (AHUs), which are situated inside a build-
ing. Design teams clearly recognize these advantages: Today RTUs cool approximately 60% of floor space in commercial buildings within the U.S., according to the U.S. Department of Energy.
The technology, in short, is proven. But design teams face challenges in terms of choice: With so many options now available, how do you specify the right RTU for a particular project? Following are several considerations to guide these decisions. When it comes to HVAC equipment on rooftops, there are specific code requirements to ensure safety, accessibility and proper installation. The International Mechanical Code Section 306.5 mandates that if equipment requiring access (such as HVAC units) is located on a roof with a slope of three units vertical in 12 units horizontal (25% slope) or greater, a level platform must be provided on each side of the appliance or equipment. This platform ensures safe access for service, repair or maintenance of rooftop equipment. Equipment must also be installed at least 10 feet from the edge of the roof or proper fall protection must be provided along the perimeter of the roof.
Furthermore, equipment must also be positioned so that water, snow or ice from the roof or eaves cannot fall directly on the unit or be ingested into the outside-air intake. Maintaining sufficient distance between fresh air intakes and exhaust fans is also important to prevent contamination of the fresh air being delivered to the unit.
When installing HVAC equipment on new or existing roofs, careful consideration of weight-related factors is essential to ensure safety and prevent damage to the building. Smaller packaged HVAC units typically weigh around 600 pounds, while larger semi-custom or fully custom units can reach up to 65,000 pounds. Understanding the weight of the specific unit you’re installing is crucial for proper structural support. Additional structural reinforcement is often necessary to accommodate the weight of large HVAC units. Therefore, HVAC engineers should coordinate carefully with structural engineers to assess the new or existing roof structure and determine if modifications are needed. They should also consider factors such as snow load, wind load and dead load (permanent weight) when calculating the total load on the roof.
The first step for a design team is to select among four overarching categories, which include dedicated outside air systems (DOAS), packaged units, semi-custom units and custom units. Below is an overview of each:
DOAS are used to provide fresh air for ventilation; there is no recirculation. Therefore, they are typically used in conjunction with another type of system that handles heating and cooling loads. Common choices for these supplemental systems are fan coil units, chilled beams terminals and variable refrigerant flow/volume systems, which offer energy efficiency and individual temperature control for each zone.
FIGURE 3: Design of individual components for the semi-custom unit used on the Hackensack Meridian hybrid operating room project. The unit was designed with a service corridor to protect the maintenance staff from the weather and houses the piping, electrical components and the steam generator serving the unit. Courtesy: Syska Hennessy
Energy efficiency is yet another consideration. ASHRAE Standard 90.1: Energy Standard for Buildings Except Low-Rise Residential Buildings serves as a benchmark for energy-efficient building design. It has been updated regularly since its inception in 1975 and remains the energy efficiency guide for most commercial buildings.
The entire HVAC system, including RTUs, variable air volume boxes, building automation systems, ductwork configurations and fans, must meet the requirements outlined in ASHRAE 90.1. Section 6.8 of Standard 90.1 provides specific guidelines related to the minimum efficiency requirements of electrically operated unitary air conditioners and condensing units. These minimum efficiencies must be met for all new equipment installations.
DOAS are especially advantageous in places like airports, classrooms and conference rooms, where there are higher requirements for outside air used for ventilation. The downside, however, is that they are usually more costly because there is extra piping and equipment involved.
Packaged units are simple, self-contained units used for light commercial buildings where precision temperature control is not required. They typically range in size from 2 to 150 tons and each unit comprises direct expansion cooling, an electrical or gas heating coil and a single air filter. Additional components and features are available as options, but these units lack the customization available in semi-custom and custom units.
The plus of packaged units is cost-efficiency; they’re off-the-shelf. The minus is a dearth of customization options, for the same reason. Furthermore, packaged units are not the most energy-efficient choice. They meet the basic criteria but
• Gain an overview of advantages and disadvantages of four types of rooftop units (RTUs).
• Assess the relationship between RTUs and energy efficiency.
• Learn about the integration of emerging technologies into the design of RTUs.
4: This is one of the operating suites on the Hackensack Meridian hybrid operating room project. Ductwork was routed below the roof from the semi-custom rooftop unit to the two operating rooms. An array of laminar high-efficiency particulate air diffusers were used at the ceiling to supply air to the room, while lower return grilles were used to return air back to the rooftop unit. Courtesy: Syska Hennessy
are unlikely to exceed more ambitious targets for decarbonization.
Semi-custom units are good fits for projects with strict guidelines for filtration and humidification, although they are more expensive than packaged units and DOAS. These units are more robust and provide up to 250 tons of cooling. Because there are more options associated with semi-custom units, they are often used in health care and pharmaceutical environments. In these cases, facility owners and managers understand that the precision associated with the equipment leads to higher costs.
Custom units are, not surprisingly, more costly than semi-custom units. These units are the most versatile and have the capability to incorporate their own heating and cooling equipment, like a small mechanical equipment room within the unit. Expense is one downside; another is lead time. It takes longer to procure the units because they are fully customizable.
But they offer many benefits: Custom units can meet stringent criteria for footprints and filtration, they can be built to withstand higher static pressures and lower supply-air temperatures and they
can be painted with custom exterior finishes or cladding for aesthetic coordination.
With simpler projects, such as an office or retail space, cost is usually the key consideration and packaged units suffice. These units comply with minimum code requirements across most jurisdictions.
But if a project has higher filtration or humidification requirements, the solution is often a semi-custom or custom unit. Below is a case study that exemplifies the decision-making process:
Syska Hennessy, which served as the mechanical engineer for the fit-out of two hybrid operating rooms at Hackensack Meridian Hospital in Hackensack, New Jersey, chose a semi-custom unit for the project.
That was the logical choice in this instance. The hospital intended these operating rooms (ORs) to be used for both imaging and cardiac catheterization. Since the ORs were relatively large, had a high airchange-rate requirement and required high-efficiency particulate air filtration, they needed fans capable
Greenheck's comprehensive line of Dedicated Outdoor Air Systems, available in models RV, RVE, and RVC, deliver up to 100% fresh outdoor air and industry-leading features that are pre-engineered and factory-tested to meet the demands of your projects. Offering airflow up to 18,000 cfm, cooling, heating, and energy recovery options , Greenheck’s DOAS products elevate ventilation performance.
Specify with Confidence. Specify Greenheck.
FIGURE 5: Shown is an example of a semi-custom unit used for a health care facility. The unit comprises supply and return fans, a direct expansion refrigerant cooling coil, gas heating, pre- and final air filters and an air-side economizer. Courtesy: Syska Hennessy
csemag.com
RTU insights
u Rooftop unit (RTU) filtration and humidification requirements, energy efficiency, ease of maintenance and aesthetics are major considerations.
u RTUs are popular for their space efficiency and modular designs, cooling around 60% of commercial floor space in the U.S.
u Design teams must select from four categories of RTUs based on project needs and energy efficiency considerations.
of delivering high airflow and static pressure.
A fan array comprising multiple fans was chosen to increase energy efficiency as well as redundancy in the fan system. The team needed an RTU, therefore that could provide higher static pressure and proper humidification and be equipped with pre-filters and final filters. The unit was constructed with a large maintenance vestibule to house the humidifier system, piping and provide the maintenance staff with protection from the weather while maintaining the unit.
Similar criteria influence choices for other health care projects. But regardless of the unit type, design teams must also consider access for future maintenance and efficiency. Engineers should work closely with vendors to select the correct fans. Otherwise, they face the risk of oversizing, which leads to an excess power draw.
It is difficult to compare custom and semi-custom units with packaged units and DOAS in the realm of energy efficiency because the former two are used with chiller plants, which means that the cooling process happens elsewhere. That said, engineers can choose fans for the semi-custom and custom units that offer higher efficiency — assuming that a client is willing to pay extra.
Once a unit is installed, proper maintenance is required. For example, facility staff should replace filters at proper intervals, because as debris accumulates on the filters, it adds resistance to the air stream, which translates into more energy usage. The manufacturer typically suggests replacement intervals. But with semi-custom and custom units, designers can install a gauge to monitor pressure drops across the filters. Once the gauge measures a
certain setpoint, the filters should be changed. It’s a more scientific approach toward maintenance. Energy efficiency also extends outside the design of the AHU. Ductwork systems must also be rightsized to minimize the amount of static pressure required by the RTU to deliver the proper airflow to the building.
Design teams should also think about future needs and strategies to integrate emerging technologies into their RTUs.
For instance, it is possible to equip semi-custom and custom units with energy recovery features. Energy recovery systems use air that is exhausted from a building to pre-treat the air coming into the building, which decreases demand for extra cooling and heating. Energy recovery wheels are becoming more efficient, allowing for better energy transfer. New refrigerants are being developed every few years that are slowly but surely replacing chlorofluorocarbon-type refrigerants, which are detrimental to the environment. Current regulatory requirements are now phasing in the use of mildly flammable A2L refrigerants with lower global warming potential, such as R-400 and R-500 series blends. And the new refrigerants can be included in packaged and semi-custom units.
Additional methods of promoting energy efficiency include upgrading the control systems on basic packaged RTUs with features such as multispeed or variable speed supply fans, modulating outdoor air control dampers, modulating heating coils and employing demand-controlled ventilation.
When it comes to designing RTUs, engineers must consider filtration and humidification requirements, energy-efficiency, the ease of maintenance, the potential for integration with emerging technologies and even aesthetics, while ensuring that solutions do not exceed budgets. Decisions require input from several trades; they cannot be made in a vacuum. The process may be time-consuming, but the end-result is an RTU that satisfies specific facility needs efficiently and lasts for a long time. cse
Tony Gonzalez, PE, is an associate partner at Syska Hennessy. He has more than 25 years of experience in mechanical engineering.
Eaton’s Experiential Learning (ExL) series is designed to further professionals understanding and knowledge of power systems at any stage of their career.
The courses provide hands-on training on power system design, system protection and coordination and power quality.
Trainings are hosted at local manufacturing facilities around the United States and at Eaton Experience Centers or enterprise datacenters. All attendees are given the opportunity to get a first-hand look at equipment construction and products.
To learn more go to: Eaton.com/ExL
Hailing from Ashland, Ohio, Dee Molisher, the Pentair® Next-Gen Submersible Solids Handling Pump, excels against the toughest clogging culprits. Your next top pick, equipped with a powerful one-two punch of a semi-open stainless steel impeller and a robust cutter plate, is ready to make an immediate impact. POWERFUL.
Current trends in industrial and manufacturing facilities include the rise of automation and AI, integration of IoT and addressing supply chain issues.
CSE: What are current trends in industrial and manufacturing facilities that engineers should be aware of?
Jarron Gass: The rise of automation has led to more autonomous warehouses equipped with additional conveyors and other obstructions, presenting new challenges for traditional fire protection methods. These challenges require new designs and drive further research and development within the discipline. The goal is to find ways to provide protection that meets or exceeds current standards, while avoiding obtrusiveness or disruption to automated processes. Some of these methods are driving more integration between systems to create an over-arching system that works together for more robust protection.
Michael Whalen: Generative artificial intelligence (AI) is the hottest trend right now, in almost all industries, not just manufacturing. AI and the introduction of smart factories has the possibility to increase efficiency, reduce cost and increase safety by analyzing an immense amount of data with respect to the manufacturing processes.
CSE: What are professionals doing to ensure such projects (both new and existing structures) meet challenges associated with emerging technologies?
Justin Milne: In industries that rely on developing technologies, management of change issues are crucial. Specific management of change references in the International Fire Code (IFC) and NFPA 1: Fire Code apply to hazardous materials, where the consequences may be severe. Management of change is a mutually agreed-upon procedure in which owners agree to implement changes to processes, materials, staffing, technology, equipment, procedures and facilities. This process is often formalized through methods outlined in process and nuclear safety management programs.
When emerging technology presents hazards to the built environment, it’s important to consider management of change as an operational engineering control. However, if new technology does not pose unique challenges, additional scrutiny may not be warranted.
Jonathan Sajdak: One key to success for industrial and manufacturing projects is designing for future capacity and changing tools, equipment and processes. Manufacturing efficiencies are always improving, so it’s critical that the engineering system infrastructure meets the required capacity to serve the facility’s needs. A common example in fire protection is accounting for an adequate water supply on a project. It is not sufficient to only plan for the present needs
Jarron Gass, PE, CFPS, Fire Protection Discipline Leader
CDM Smith
Pittsburgh
Justin Milne, PE, PMP, Senior Engineer
Jensen Hughes Allen, Texas
Jonathan Sajdak, PE, Associate Principal / Fire Protection engineering director
Page
Houston
Michael Whalen, PE, LEED AP BD&C, Project Manager
HDR Engineering New York, NY
in a facility, as new materials and hazards can be introduced at any time. Safety factors should be incorporated into hydraulic calculations and pipes should be sized conservatively to allow for future changes.
Michael Whalen: Emerging technologies are responsible for a number of trends the built environment. As an industry, we can be proactive in future
• Understand the impact of automation on the design of industrial and manufacturing facilities.
• Identify strategies to address scalability and future-proofing for plants.
• Learn how plants and industrial facilities are adapting to supply chain challenges.
FIGURE 1: This structural plastics manufacturing facility and office demonstrates some of the unique considerations engineers face when designing industrial buildings. Courtesy: Page
proofing projects to the greatest extent possible by considering how buildings will be adaptable, agile and responsive to emerging technologies. Retrofit and adaptation is a key trend that we are currently experiencing. Network architecture needs to be scalable. Cloud-based solutions should be considered, and control platforms should be as modular as possible to allow the acceptance of technology advancements with minimal change to existing infrastructure.
‘The amount of data and monitoring generated from equipment is growing exponentially, and futureproofing the network capacity should be a key consideration in designs.’
CSE: What are plant owners and managers requesting from consulting engineers to make the facility more prepared for the future?
Jarron Gass: As rapidly developing and advancing technologies become more available, the front-end due diligence process is also expanding significantly. This requires more thought, discussion, and preparation for future expansions and implementations of emerging technologies. Coordination and input from the design team, owners, operators and other key stakeholders are essential to develop a strategic and comprehensive plan that should address the current process, potential future upgrades or expansions, optimization initiatives and sustainability goals.
Justin Milne: Water supply is a significant fire and life safety issue that more owners and managers are paying attention to. Because firefighting activities rely on large amounts of water, it is possible for a fire to compromise municipal or industrial base water supplies. The impact of industrial and manufacturing facilities on overall water supplies is not typically considered in base codes and standards. However, this oversight can have dire consequences depending on the application.
Jonathan Sajdak: One of the most common requests from owners is to design for spare capacity and plan for future expansion of building systems. Due to changes in manufacturing technologies and the likelihood of future production increases, owners want flexible systems that can adapt with the ever-changing processes occurring within these facilities. Additionally, for fire alarm systems, it has become more common for owners to request connections to building management systems and/or provide digital workstations. This allows for constant monitoring of devices and system status across facilities, while also permitting the control of certain system features.
Michael Whalen: Plant owners like modularity, so they can easily add to their plant equipment and infrastructure when required, with little to no interference to existing production. The amount of data and monitoring generated from equipment is growing exponentially, and futureproofing the network capacity should be a key consideration in designs. Full building information models, including maintenance records, energy usage and part identification, are being delivered to help owners maintain their facilities more efficiently. cse
Whether it’s hospitals, data centers or pharmaceutical companies, seamless, energy-efficient and cost-optimized heating and cooling systems are crucial for operations. Belimo‘s new butterfly valves feature NFC for fast commissioning, programing and diagnostics, plus accurate control to ensure efficient operation. Available in nominal sizes of 4“, 5“ and 6“.
With Belimo products, you can unlock the full potential of your HVAC systems, and ensure optimal performance at all times.
Discover the advantages www.belimo.com
Engineering innovation plays a vital role in the vitality of industrial manufacturing. You’re invited to explore the profiles on the following pages and celebrate the success stories of our participating manufacturing innovators:
• ABB Motors and Mechanical
• Addison HVAC
• Belimo
• Berner International
• Champion Fiberglass
cse202407_innovIND_LEADHalf.indd 1
• Cummins
• DriSteem
• Greenheck
• Inaba Denko America
• LEESON Motors
• Noritz
• Pentair
• RenewAire
• Rheem
• Trane
• Viking Group, Inc.
Utility projects can be complex with challenging underground installation. In our Utility Solutions Guide, learn more about how fiberglass conduit, elbows, utility risers and interference gasket conduit can help provide solutions to common utility challenges.
Discover the advantages, engineering benefits and material and installation savings that have led to successful outcomes in thousands of projects.
Learn how BABA-Compliant Champion Fiberglass® mitigates utility project challenges.
Download the guide: https://hubs.ly/Q02BCK-w0
Industrial operations are staying ahead of tightening energy regulations while reducing environmental impact with abb ’s baldor- reliance SP4 motors. SP4 motors meet nema Super Premium efficiency levels in a standard aC induction design operating independently of a variable speed drive.*
t he idea is simple: take a proven aC induction motor design and make it better by reducing motor losses by an average of 20 percent while maintaining the simplicity and reliability of motors currently in operation.
most industrial electric motors run direct on line (Dol – without the use of a variable speed drive), and SP4 allows users to improve total system efficiency without the need for investments in additional equipment. a s a standalone unit, SP4 achieves nema Super Premium efficiency; however, when paired with a drive, even higher efficiency levels are attainable.
SP4 motors run cooler, reducing heat-based energy losses and extending bearing life, which also leads to lower electrical energy consumption, operating costs and total cost of ownership.
SP4 motors meet current u.S. Department of energy efficiency standards as well as anticipated medium electric motor ( mem ) regulations, which take effect on June 1, 2027, in the united States. t hese regulations mandate that motors up to 100 horsepower maintain nema Premium efficiency, while motors between 100 and 250 horsepower must achieve nema Super Premium efficiency.
Forty-five percent of the world’s electricity is converted by electric motors into motion, and there are more than 300 million industrial electric-driven systems in operations worldwide. a s costs and demand for electricity continues to grow, abb will remain at the forefront of energy efficiency and sustainability by embedding circularity in products and solutions, offering lifetime services and investing in new business models to reduce waste, increase recycling and foster reusability.
* nema Super Premium efficiency is generally comparable to Ie 4 efficiency for a C induction motors operated direct on line (Dol ) as defined by the International e lectrotechnical Commission (Ie C).
Click to learn more.
HybridAir, a groundbreaking new technology from Addison, seamlessly merges air, water and refrigeration into an exclusive air handling solution. Aligned with a broader goal of transitioning to cleaner and more sustainable energy sources, this innovation effectively tackles the toughest hurdles of electrification and decarbonization.
HybridAir has multiple configurations that can be used for treating outdoor air, to provide supplemental comfort cooling and heating. For more information about HybridAir, visit www.hybridairsystem.com
FrostShield is a revolutionary new mechanical and unit control technology for dedicated outdoor air systems brought to you by Addison. FrostShield not only extends the operating range of air-source heat pumps, but also removes the need for the unit to enter defrost mode during heating operation.
FrostShield brings steady comfort and energy savings, without relying on strip heaters or fossil fuels. To learn more about this technology, visit www.frostshieldHP.com.
Addison HVAC is a pioneering force in the HVAC industry, renowned for innovation and excellence. With a strong commitment to technological advancement and sustainability, we lead the way in shaping dedicated outdoor air systems.
www.addison-hvac.com
Belimo stands as the global leader in the development, production, and sale of damper actuators, control valves, sensors, and meters. A consistent focus on market and customer needs
underscores our dedication to delivering superior value, surpassing customer expectations, and outpacing competitors. A testament to this commitment is the allocation of approximately 7% of sales toward research and development, ensuring Belimo’s solutions consistently set new industry benchmarks.
From the creation of the first direct coupled actuator in 1976 to our next generation butterfly valves with enhanced computing power, Belimo continues to demonstrate its pioneering spirit, providing significant added value for the HVAC market.
The Belimo advanced butterfly valve is designed specifically for HVAC applications. It offers an intelligent, energy efficient, and reliable high flow solution, with a focus on ease of installation, application flexibility, and longevity.
The Belimo Energy Valve ® is an IoT, cloud-connected pressure independent valve that monitors coil performance and energy consumption while maintaining Delta T. It features patented glycol monitoring and compensation, ensuring precise flow measurement and compliance with design requirements. Integration with our Thermal Energy Meter facilitates energy control and efficient billing.
Belimo Room Sensors enhance comfort with maintenancefree devices accurately measuring temperature, humidity, and CO 2 . The streamlined design, optionally equipped with an ePaper touch display, integrates NFC for quick setup and adjustments through the Belimo Assistant App. This app provides easy data access, field adjustability, commissioning, and troubleshooting, even without power.
For more information, or to speak to a Belimo representative, visit belimo.com .
Sleek, beautiful air curtains for main entrances
• Air curtains for when aesthetics matter
• AMCA Certified - Meets the ASHRAE 90.1 Vestibule Exception
• Smart control and BACnet compatibility available
• Simple to install, operate and maintain
• Made in U.S.A.
ASHRAE 90.1: Research leads to Vestibule Exception
In addition to product innovation, Berner has been instrumental in the drive to achieve greater recognition of the air curtain, a.k.a. air door, as an important part of any building’s design. Part of that drive has been to research and promote third-party studies on the efficacy and benefits of air curtains. This research has led to air curtains being included as an exception to vestibules in ASHRAE Standard 90.1-2019, ASHRAE Standard 189.1, the IECC (International Energy Conservation Code) and the IgCC (International Green Construction Code) building codes.
To make it easier for an architect and their client to say yes to using an air curtain over customer doorways, Berner developed the Berner Architectural Collection. The Collection features a range of air curtain designs that are quiet, technologically advanced, beautiful for entrances
where aesthetics and comfort matter. Built on Berner’s strong engineering foundation, these sleek and elegant air curtains are AMCA certified, meeting the vestibule exception in ASHRAE 90.1 and other energy codes.
Known for engineering and innovation, in 2002, Berner was the first to introduce a built-in digital controller to program and control air curtains. The Berner Intelliswitch includes the time delay, speed control, a scheduling function, preset operating programs, and more. As smart phones became more common, Berner developed the Berner AIR app for programming, operating and monitoring the air curtain from one’s device, simplifying setting up and monitoring air curtains.
Berner continues to improve and update both the Intelliswitch and the Berner AIR app. The most recent improvement is the ability to truly integrate a Berner Architectural or Industrial air curtain using BACnet or Modbus with the building management system (BMS).
• Save energy
• Protect thermal comfort
• Provide chemical-free insect control
• Keep out fumes and vehicle exhaust Phone: 800.245.4455 | www.Berner.com
When the door is open, Berner Air Curtains: Saving energy and creating healthy, comfortable environments.
Cummins Fridley campus is home to one of the world’s largest microgrid testing labs in the world, the Power Integration Center (PIC). Since its opening in 2022, the PIC’s mission has been to innovate for a greener future. Regardless of your power needs or your wildest imaginations, the PIC is built to test these possibilities in a zero-risk environment. This highly configurable facility spans over 20,000 sq ft. and was designed by our team of leading engineers and microgrid advisors.
Outdoor Testing Pads - The largest part of the lab, this space is dedicated to testing any source or load that can be integrated into a microgrid (ex. Gensets, Battery Energy Storage, Hydrogen Fuel Cells and Electrolyzers, EV Chargers, and more). The outdoor testing pads are comprised of:
• Five 500 kW Testing Pads
• Two 2000 kW Testing Pads
• Two 500 kW RLC Load Banks
Electrical Mezzanine Unique Features:
• Utility Distribution Substation
• Step-Down transformer – 13.8 kV to 480 V
• Two 1 MW utility feeds
• Distribution switchgear Solar Inverter Testing (Photovoltaic/PV)
• 400 kW rooftop solar array
• 105 kW DC simulation power supply
• Programmable weather scenarios Bi-Directional Inverter Testing (Battery Energy Storage/BESS)
• 120 kW battery simulator
Main Switchgear Room - This room houses a 2 MW switchgear lineup that’s the primary working switchgear utilized for customer simulations within the lab. The switchgear is separated into three buses with tiebreakers in-between and a ring bus around the back allowing for the creation of multiple different power system topologies including:
• Isolated Bus
• Common Bus
• Single Transfer Pair
• Dual Transfer Pair
• Main-Tie-Main
• Dual Transfer Pair with Tie
Engineering Control Room - The control room acts as the central nervous system for the whole facility. Signals from the sources, loads and connections are brought together for our team of engineers to conduct and visualize the extensive testing needed to evaluate solutions.
Click here to discover the microgrid configurations made possible at PIC.
Humidity control is an essential component of any HVAC system design. Fluctuations in relative humidity (RH) levels can spell disaster in facilities that depend on maintaining consistent material quality or keeping static electricity at bay.
Investing in humidity control systems also aligns with broader sustainability goals. By optimizing indoor humidity levels, facilities can reduce the risk of mold growth and moisture-related damage to building materials and furnishings, prolonging the lifespan of structures and reducing the need for costly repairs. Additionally, by minimizing energy consumption associated with HVAC heating and cooling systems, facilities can lower their carbon footprint and contribute to environmental conservation efforts.
It’s important to understand that investing in technologies to regulate indoor humidity levels is not just a short-term solution. It’s a long-term strategy with far-reaching implications for building preservation, energy efficiency, and occupant health. By creating safer, more comfortable, and more sustainable environments, we can reap the benefits of reduced health risks, conservation of building materials, and lower energy consumption for years to come, providing a solid return on investment.
DriSteem’s existing lineup of world-class humidification, evaporative cooling, and water treatment systems has now been extended with the addition of the new Evair™ dehumidifier. Our complete line of humidity control systems helps you construct comprehensive humidity control solutions like never before.
DriSteem representatives offer a depth of experience and expertise in specifying humidification, dehumidification, adiabatic, and water treatment systems in all types of facilities.
Ensure the success of your next project with DriSteem’s complete range of humidity control systems.
• Prevent damage to sensitive instruments in processing environments
• Minimize the risk of equipment failure in manufacturing facilities
• Preserve important materials and artifacts in storage spaces and museums
• Safeguard against the spread of viruses and bacteria in offices
CLICK here or scan the QR code to contact your local humidity control expert and discuss your project’s humidity control needs.
Greenheck has various tools to assist you in product selection, including our CAPS ® and eCAPS ® product selection software programs that guide you from initial design through detailed submittals. The eCAPS ® online product selection tool provides access to the most complete catalog of HVAC Level of Development (LOD) 200 and 300 product content where you can quickly select and specify the best value HVAC products for your project.
Our latest tool, the eCAPS ® Bridge for Revit ® software plug-in, directly links our eCAPS capabilities and BIM content library into Revit ® saving time and streamlining the product selection process. With the eCAPS Bridge for Revit, you can make performance-based selections and insert LOD 200 and 300 content without leaving Revit. Multiple Greenheck product schedules can then be configured and created in a single click.
Other functions of the eCAPS Bridge for Revit include:
• Rapid reselection of placed LOD 300 content for easy performance, model, and schedule updates within your Revit project.
• Your shared parameters can be added and mapped to Greenheck parameters in one click for easy data transfer.
• Users can rename schedule headers and save these changes to their schedule layout setting for future use.
• Global clearance on/off buttons allow users to easily adjust service clearances on all Greenheck content placed in the Revit ® project.
Many product types including fans, louvers, dedicated outdoor air units, preconditioners, and hundreds of Revit families are available with more being added with each release. This add-in is free to download and use. Download the eCAPS Bridge for Revit at greenheck.com/revit
For more information on all of Greenheck’s product selection tools, visit https://www.greenheck.com/resources/software
info@greenheck.com | 715-359-6171 www.greenheck.com
Introducing the Linebrace Vertical Pipe Support – a cutting-edge solution specifically designed to prevent expansion-induced buckling in vertical lineset and copper pipe installation.
Vertical lineset installations are always subject to severe stress due to a combination of thermal expansion and gravity, usually resulting in buckling or kinking the elbow fitting at the lower end of each pipe run.
The LineBrace clamp supports the weight of vertical lineset risers in VRF and VRV AC systems and reduces the thermal expansion load on the lowest copper elbow by 50%.
Featuring a state-of-the-art clamping mechanism that securely grips the pipe, minimizing movement and maintaining alignment. Plus, with no brazing needed, installation is quicker and more straightforward, saving time and reducing labor costs.
LineBrace Benefits:
• No “hot work” (brazing) required.
• Reduces weight load on vertical riser.
• Reduces thermal expansion by 50%.
• Easy to retrofit onto existing linesets.
• Molded insulation sleeve preserves thermal integrity.
• Available from 3⁄8” to 1¾”, in 1⁄8” increments.
“When running refrigerant piping vertically up 150’ in a shaftway, we were very concerned about pipe expansion. It was even more difficult, because the shaftway will not have future access, so any refrigerant leaks in that area could be catastrophic. We were happy to find LineBrace, a product that didn’t require any additional brazing and was able to help us separate the vertical riser piping into 75’ up and 75’ down, so the expansion can be dispersed on the horizontal sections of piping directly connected above and below the vertical riser.”
Steven Palone – VP and Service Manager at Palone Bros.
Explore the legacy of LEESON ® Motors, recognized for decades for premium motor craftsmanship. As an integral part of the Regal Rexnord ® family, LEESON Motors leads the charge in electric motor excellence, providing a comprehensive array of products meticulously crafted to power your applications with reliability and performance.
From gearmotors to permanent magnet EC motors, fan and blower motors, Regal Rexnord’s motor portfolio caters to the diverse needs of various industries. Engineered to endure the most rigorous conditions, their LEESON branded general purpose motors and Farm/Ag motors deliver steadfast operation, even in the harshest environments.
Among the motor offerings stands the legendary Extreme Duck ® Ultra, an emblem of durability and ingenuity. With its IP69 certification and patented fully-encapsulated stainless motor body design, the Extreme Duck Ultra motor excels in the most demanding spray-down environments, while its Q-Car rotor design ensures effortless bearing and seal replacement, simplifying maintenance tasks.
Under the LEESON brand, the SyMAX® motor line continues to set new benchmarks for excellence. Formerly under the Marathon Motors family, SyMAX now proudly bears the LEESON legacy, delivering unmatched performance and energy optimization to meet the evolving demands of modern industries such as variable speed efficiency and precise airflow control.
Look to LEESON motors when you need to drive your operations forward with cutting-edge technology and an unwavering commitment to quality. Whether you need robust motors for unique challenges, the people behind LEESON motors possess the expertise and products to enhance your performance.
Experience the enduring legacy of LEESON motors today and discover why our brand epitomizes reliability, durability, and innovation. Reach out to unlock the potential of LEESON motors and propel your success to new heights.
Noritz has launched the innovative Hybrid Hot Series, a solution that combines the benefits of hot-water storage with the efficiency of tankless water heating, specifically designed to meet the demands of high-volume commercial applications. This groundbreaking technology is ideal for establishments like restaurants and hotels, where large quantities of hot water are required in short bursts, followed by extended periods of zero demand.
The Hybrid Hot Series storage tanks feature a specially designed heat trap that enhances the stratification of hot water within the tanks. This heat trap, resembling an elephant nose, enables maximum hot-water efficiency and achieves optimal stratification. As hot water tends to rise to the top due to its lower density, the trap facilitates the central withdrawal of hot water from the tankless water heater, while preventing unwanted convection flow during standby periods. Additionally, the tank’s concrete lining and polyurethane insulation minimize heat loss, resulting in reduced energy consumption.
Noritz’s Hybrid Hot tank boasts a half-inch-thick cement lining, offering superior corrosion protection compared to traditional glass linings, eliminating the need for frequent anode rod maintenance. Furthermore, the tank’s two inches of polyurethane foam insulation ensure excellent heat retention, leading to significant energy and cost savings.
The Hybrid Hot Series storage tanks feature a specially designed heat trap that enhances the stratification of hot water within the tanks.
The Hybrid Hot Series incorporates a dedicated ¾-inch MNPT recirculation return port, strategically placed on the side of the tank. This feature simplifies installation by allowing plumbers to connect the recirculation return line to the incoming cold-water line without requiring complex plumbing configurations.
With an industry-leading 10-year warranty for both the tank and tankless components, the Hybrid Hot Series ensures long-term reliability and customer satisfaction. The tankless water heater achieves a remarkable thermal efficiency rating of 98%, accompanied by a 0.96 uniform energy factor (UEF).
Noritz’s Hybrid Hot Series is revolutionizing water heating in commercial settings by providing a seamless combination of hot-water storage and tankless technology. This innovative solution guarantees an abundant supply of hot water, eliminating the need to heat the entire tank, thereby reducing energy consumption and costs.
Going one-on-one with clogging culprits calls for an all-star pump. Pentair has recently launched Dee Molisher, the Pentair ® Next-Gen Submersible Solids Handling Pump, to help wastewater operators win the battle against modern flushables.
Engineered to combat the most challenging clogging culprits, including flushable wipes, diapers, hygiene products, and more that infiltrate the wastewater stream, these Next-Gen Pumps are equipped with a semi-open stainless steel impeller and a robust cutter plate that annihilates unwanted materials before they cause an issue. This clever combination keeps Dee in the game at peak performance when other teams pull from their bench.
Built with service in mind, the Next-Gen Pumps feature permanently lubricated bearings that require no regular maintenance and an oilfilled motor to provide superior heat transfer and lower running temperatures. Any leaks are detected in the outer chamber before they reach the motor housing, helping protect against unwanted downtime.
With the addition of a super high-head curve and premium efficient motors on most models, the Next-Gen Series aims to help lower the cost of ownership.
Hailing from Ashland, Ohio, Dee Molisher is ready to positively impact your organization and help you win in the trenches while keeping operating costs at bay.
Your scouts can watch Dee Molisher in action at pentair.com/allstar
RenewAire has launched two new additions, the HE07 and HE10, to its popular HE Series configurable line of commercial energy recovery ventilators (ERVs). These self-contained packaged ERVs can be used as a stand-alone unit or in concert with other HVAC equipment, and they have a wide CFM range. The HE07 boasts a CFM range of 166–694, while its counterpart, the HE10 has a CFM range of 250–1,100.
The new HE07 and HE10 ERVs have new features and designations like backward curved impellers and EC motors, as they replace the EV450 and HE1X, respectively. The HE07 offers greater balancing capabilities, due to independent exhaust and supply air blower motors, versus the former EV450’s single blower motor. The dual motors enable fieldadjustable exhaust/supply air balance ratios for precise efficiency and effectiveness.
For both the HE07 and HE10 ERVs, the factory-installed isolation dampers will reduce jobsite and contractor installation time. The redesign also includes a factory reorganization to accelerate production and reduce lead times on USA-assembled units. Factory-installation, integration and testing production time have been significantly reduced for units with standard and optional controls.
Other features on the ERVs include:
• Latest generation of UL-listed G5 static-plate core; tested and passed under AHRI 1060;
• Differential pressure control accommodates both 2-inch MERV 8 standard filters or higher static with 2-inch MERV 13 option;
• New motor, impeller and AC/DC power supply improves output and reduces operational dB level;
• Adds specification flexibility with indoor/outdoor and horizontal/vertical configuration options;
• An industry-leading 10-year structural and performance warranty for the static-plate core, two-year warranty for commercial products.
The HE Series ERVs promises to help engineers increase ventilation while also helping to mitigate infectious pathogens and other airborne microbes such as allergens, mold and mildew. In addition, this line of ERVs is known for its optimizing energy efficiency and cost savings—up to 65% on ventilation energy costs.
For more information contact: marketing@renewaire.com | 800-627-4499 www.renewaire.com
Set up your next commercial project for success with Rheem ® commercial packaged units that come with patented innovations in our PlusOne ® ServiceSmart package—engineered to service faster, smarter and easier.
Thoughtfully designed with direct input from HVAC professionals, the ServiceSmart package includes features like:
• Qwik-slide Blower Assembly & Heat Exchanger – by removing a few screws, the entire blower assembly or gas heat exchanger assembly slides out on a guided track, making service and maintenance easier and safer
• Single-point Wiring – provides quick, plug and play installation, saving time and money, and simplifying the wiring process
• Qwik-clean Drain Pan – remove four exterior screws to easily slide out the drain pan with built-in overflow switch for quick cleaning
• Qwik-change Flex-fit Rack – takes only a few seconds to easily switch from 2” to 4” filters
• Easier Access Features – quarter-turn, tool-less entry, hinged panels and panel prop rods are all included because of field-input from HVAC pros
With ServiceSmart, contractors and building owners can realize tangible benefits. Regular, recommended maintenance of HVAC units can help extend equipment life and ensure peak performance.
Our accessible drain pan and filter rack design simplify routine maintenance while easy-access features make it simple for contractors to service unit components. This helps reduce damage risk to the unit and roof membrane while making it safer to complete repairs efficiently.
A blind time study found ServiceSmart features can help contractors reduce time spent on service calls by up to 100 minutes, on average.1 This can lead to significant cost and time savings for building owners and contractors.
A system optimization service that pays back.
Your building portfolio is a universe of its own— a hard-working, complex, and multidimensional universe that must meet the daily demands of your operation. And yet, you need to identify ways to do this while utilizing less: less burden of human intervention, less energy use, and less carbon impact on our world. This is what Trane Autonomous Control Powered by Brainbox AI ® is all about: self-directed optimization and performance, driven by AI technology that never sleeps. Trane Autonomous Control works tirelessly to identify improvement opportunities and carry out tasks that will help cost-effectively reduce your HVAC energy consumption and your carbon footprint.
What if we took everything you know about running your building, and everything Trane knows about system optimization, and created a bigger universe of information all brought together using artificial intelligence? That is Trane Autonomous Control. It’s about using the equipment you already have in your building, better. It’s the next level of system control, Autonomous Control.
How does it work? Trane Autonomous Control is powered by intelligence that analyzes live data 24/7, then uses that information to predict occupancy, zone temperature, and energy load up to two hours in advance, with unprecedented accuracy. It works within your systems to constantly identify inconsistencies and inefficiencies. Once these are identified, it works to help improve and correct these issues automatically, without the need for human intervention, or upfront costs.
By implementing Trane Autonomous Control with well-maintained and serviced equipment, you can also expedite your sustainability goals.
Maximizing energy reduction through the analysis of energy usage patterns, forecasted weather, and projected occupancy across all of your buildings, it enhances the efficiency and performance of your existing system, and can help reduce energy consumption, costs, and your carbon footprint by up to 40 percent.1
Click here to learn more about Trane Autonomous Control today.
www.trane.com
1 https://brainboxai.com/en/articles/introducing-ai-to-hvac-the-future-of-building-automation
Familiar with Viking Tools for Revit ®, Hydraulic Assistant and Clean Agent Assistant? These tools have a fresh new identity! Viking recently rebranded the tools to reflect the “Design to Delivery” concept. This new name reflects a strategic shift, emphasizing the tools’ enhanced capability to enable users to design systems with Viking products, request quotes and facilitate the ordering and delivery processes directly to the job site. The digital tools within the Design to Delivery framework will showcase existing products which feature new names.
“Hydraulic Assistant” has been reintroduced as “vCalc”. With vCalc, users can effortlessly perform Hazen-Williams or Darcy calculations and plan robust piping systems through a user-friendly interface, now enhanced with minor fixes and improvements for an optimized experience.
“Viking Tools for Revit ® ” will also join the Design to Delivery portfolio under the new name “vDesign”. This comprehensive suite of design tools caters specifically to fire protection designers, featuring a library of Revit families integrated with the Viking product line for the design of fire suppression
systems. Notably, the vDesign toolbar now incorporates added icons for each tool, replacing the drop-down menu for increased convenience, accompanied by various minor fixes and improvements.
The latest addition to the Design to Delivery portfolio is “vInert,” taking the place of “Clean Agent Assistant”, which streamlines the process of calculating and designing an Oxeo Extinguishing System. Start by selecting an agent (argon or nitrogen), configure your system, and determine the design concentration. Enter the room’s volume or dimensions, then start designing your pipe network. As you proceed, vInert generates a 3D model to help you visualize and plot key points. When you’re done, you’ll receive a submittal list and a bill of materials you can submit.
From designing custom products to getting an order delivered, the Design to Delivery portfolio is equipped with the tools you need to make your job easier.
ABB Motors US .2 .www .abb .com/motors-generators
ADDISON .23 .www .addison-hvac .com
BELIMO .39 .www .belimo .com
BERNER AIR CURTAINS .24 .www .Berner .com
Cummins .C-4 www .cummins .tech/csejulyaug24
Eaton .35 .www .Eaton .com/ExL
Greenheck .33 .www .greenheck .com
LEESON Motors .C-2 www .leeson .com
Lennox Industries .29 .https://www .lennoxcommercial .com
Miura North America, Inc .22 .www .miuraboiler .com
Navien, Inc .1 .www .Navien .com
Pentair Flow Technologies .36 .www .pentair .com
Pritchard Brown .38 .WWW .PRITCHARDBROWN .COM
RenewAire LLC .17 .www .RenewAire .com
Ruud Commercial Air .4 .www .RuudCommercial .com
Tjernlund Products .56 .www .tjernlund .com
ULINE . . . .11 .www .uline .com
Yaskawa America, Inc .C-3 www .yaskawa .com
VP, Sales
Matt Waddell MWaddell@WTWHMedia.com 312-961-6840
Sales Account Manager
Brian Gross BGross@WTWHMedia.com 847-946-3668
Sales Account Manager
Richard Groth RGroth@WTWHMedia.com 774-277-7266
Sales Account Manager
Robert Levinger RLevinger@WTWHMedia.com 516-209-8587
Sales Account Manager
Judy Pinsel 847-624-8418 JPinsel@WTWHMedia.com
Patrick Lynch, Senior Vice President, Sales & Strategy 847-452-1191, PLynch@WTWHMedia.com
McKenzie Burns, Marketing Manager MBurns@WTWHmedia.com
Courtney New, Program Manager, Content Studio CNew@WTWHMedia.com
Paul Brouch, Operations Manager 708-743-5278, PBrouch@WTWHMedia.com
Rick Ellis, Director, Audience Growth 303-246-1250, REllis@WTWHMedia.com
Custom reprints, print/electronic: Paul Brouch, PBrouch@WTWHMedia.com
Information: For a Media Kit or Editorial Calendar, go to https://www.csemag.com/advertise-with-us.
Letters to the editor: Please email us your opinions to ARozgus@WTWHMedia.com. Letters should include name, company and contact details, and may be edited.
a
range of
to choose from. Automated Warehouse Week will provide guidance, with expert insights into the evolving technologies, use cases, and business best practices.
Keep your finger on the pulse of top industry news
FAN-tastic experience, performance, and reliability using the Yaskawa HV600 Variable Frequency Drive in your building operations.
Maximize uptime, minimize downtime, and experience Yaskawa’s world renowned quality yourself with the HV600 Drive. The HV600 helps minimize energy costs and maximize occupant comfort because it is specifically designed for building automation applications.
• Program without power
• Fast and easy installation, commissioning
• HVAC programming and function terminology
• UL Type 1 and 12 drives; UL Type 1, 12, and 3R drive packages
Become a big fan of the Yaskawa HV600 Variable Frequency Drive. Call Yaskawa at 1-800-927-5292.
We understand the challenges that data center and mission critical operators face.
Get industry-leading power technology built with sustainability in mind with the approved use of alternative fuels such as HVO. Get up to 90% reduction in GHG without compromising performance with the award-winning Centum™ Series, powered by the fail-safe QSK78 engine. For your most critical applications - switch on sustainability. And keep it on