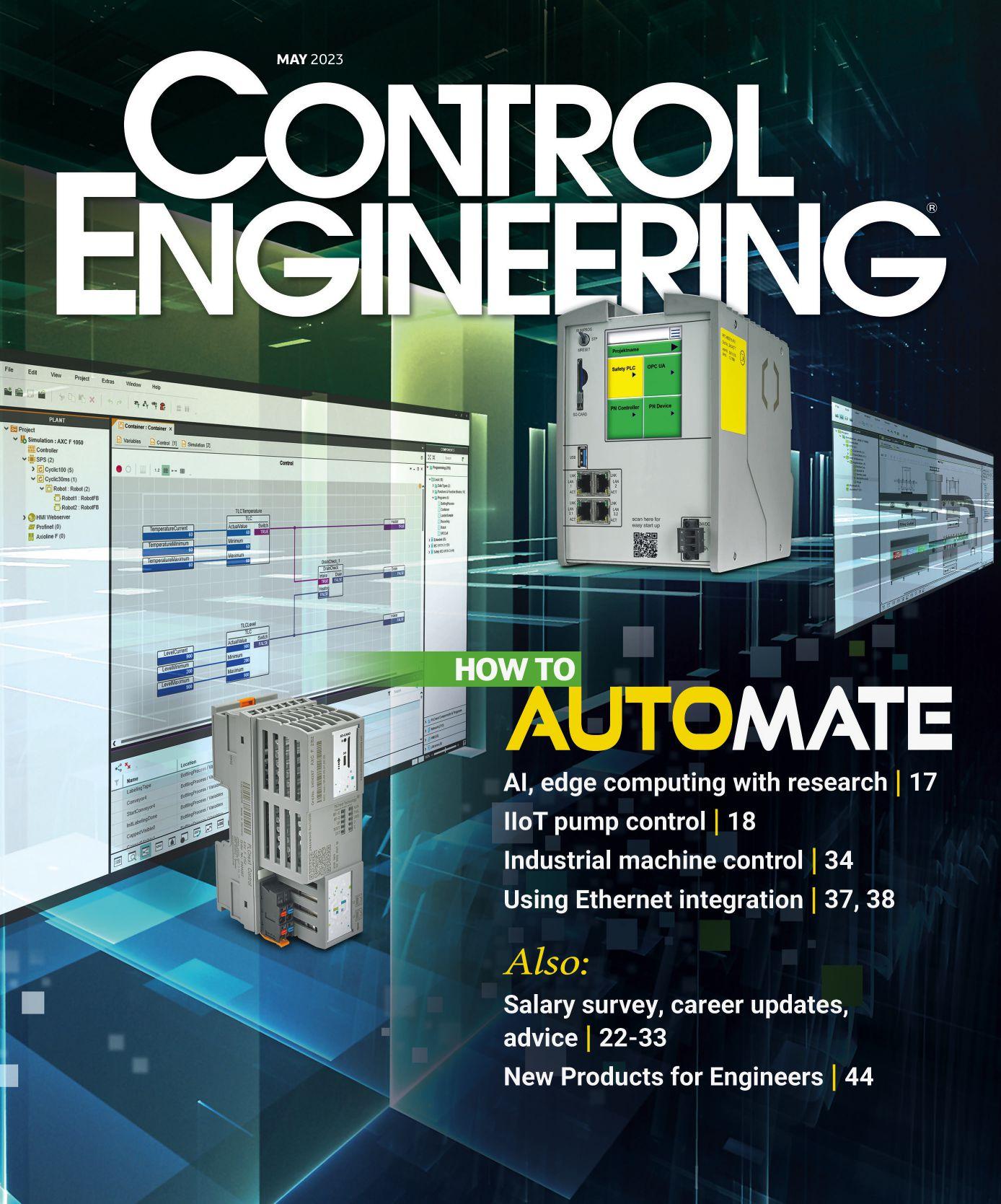


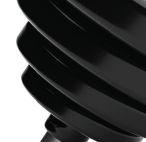
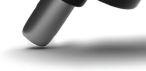
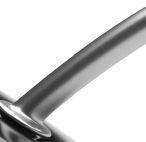
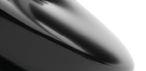

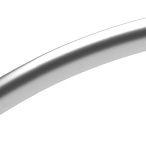




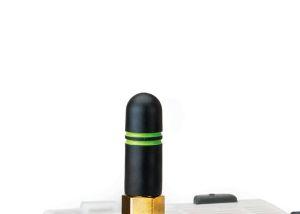
We’ve taken our most practical, most popular PLC family and supercharged it with features you wouldn’t expect from a simple low-cost controller. Data logging, Wi-Fi connectability, motion control, MQTT communication, and increased security measures are just a few of the impressive features o ered with the new CLICK PLUS PLC series. With a starting at price of only $97.00 and free easy-peasy programming software, CLICK PLUS PLCs are a “must have” for simple, a ordable control...with a kick!
Add up to 8 additional I/O modules for applications with larger I/O needs.
For custom stand-alone PLC I/O con gurations that exactly match your application (option module sold separately).
Schmalz End-of-Arm Tooling Kits
Features
• Starter kits are easily assembled
• Includes structural rail, connectors, cup mounts, vacuum tubing, vacuum cups, fittings, basic ejector, flange for Universal robot, and a blank robot flange
• Can be built to use internal or external vacuum
• Additional robot flanges are available to connect to Fanuc, Rethink, Universal, and Yaskawa robot arms
End-of-arm tooling starter kits include all the components needed to create a single-beam or dual-beam end-of-arm tool for a vacuum pick-and-place application. Kits are save time and money, but still allow a degree of customization.
First, cut the structural rail to the desired length, determine the location of the suction cups, and then assemble the Once assembled, add the robot interface flange brand of robot or drill your own using the included robot flange. That’s all it takes and your tooling is ready
• Single profile kit with minimum active 20 pound-force load (90 N), maximum active 78 pound-force load (350 N)
• Double profile kit with minimum active 56 pound-force load (250 N), maximum 140 active pound-force load (625 N)
• Vacuum suction cups in flat and bellowed styles made from Elastodur, silicone, or Nitrile in sizes up to 78mm
• Vacuum ejectors with a high suction rate of up to 860 I/min
• Spring plungers for vacuum cup mounting
• Couplers in G1/8 and G1/4
EtherCAT P integrates EtherCAT communication with system and peripheral voltage supply in one 4-wire standard Ethernet cable. The I/O system for EtherCAT P with IP67 protection takes full advantage of One Cable Automation: material and installation costs, as well as the required installation space in drag chains, cable trays and control cabinets are significantly reduced. The compact and robust I/O modules cover a wide signal range, from standard digital I/Os to complex analog signals and measurement technology. More than 100 additional EtherCAT P components are available. Find out more now!
When
44 | New Products for Engineers – See more products in every issue.
Ultrasonic prox sensors, rackmount network appliance, ultrasonic meter, flow converter, wireless access point, process analyzer, frequency signal conditioners, enclosure mounting options, rugged embedded computer, position sensors, edge gateway
See more products in every issue. www.controleng.com/NPE
47 | Back to Basics: Benefits of upgrading to Ethernet Ethernet is a robust and stable network framework that has more possibilities than other networking protocols.
The 2023 Control Engineering Product of the Year announcement is June 1. Don’t miss it!
Winners will be featured in the next version of the Product of the Year eBook on Thursday, June 1, 2023. https://www.controleng.com/events-and-awards/product-of-the-year/
NEWSLETTER: Digital Transformation
• How digital twin simulations advance digital transformation in manufacturing
• MQTT’s benefits for digital transformation
• Digital Transformation eBook
• Petrochemical company shifts attention to digitalization, optimization, sustainability
Keep up with emerging trends: subscribe. www.controleng.com/newsletters
Control Engineering eBook series: PLCs Spring Edition
As the cornerstone of many automation systems, PLCs are a tried-and-true industrial technology. However, as industry changes, so are the hardware and software considerations that come along with PLC selection, integration and programming. Featured articles include:
• A new future for process control systems
• Tips on how to choose industrial controller hardware, software
• PLC migration improves uptime for spice supplier
• Achieving on-stream control room relocation Learn more at www.controleng.com/ebooks
u Global System Integrator Report
Supplement to November/ December Control Engineering and Plant Engineering includes System Integrator of the Year, System Integrator Giants, application stories. www.controleng.com/ magazine
u Control Engineering digital edition
The tablet and digital editions provide links to additional article images and text online and links to other related, useful resources.
www.controleng.com/ magazine
The Unlimited Platform for Total System Integration
ALL YOUR DATA ALL YOUR DEVICES
ALL YOUR PEOPLE
ALL YOUR LOCATIONS
ALL YOUR OPERATIONS
ONE PLATFORM TO CONNECT ALL YOUR PROCESSES, PEOPLE & PROGRAMS Learn more about Ignition: ia.io/platform
u NOT TOO LONG AGO, factory floors were swamped with machines equipped with purpose-built software that used closed architecture unique to each device. These were isolated devices not connected to any cloud network and considered secure, safe, reliable and efficient for their intended designs.
‘ Cloud
resources
can
optimize
and
provide new
level of efficiencies that are difficult to replicate in
However, the proliferation of the Internet of Things (IoT) and cloud advances, the growing need for intelligent sensing and control solutions and the promised speed of emerging 5G wireless infrastructure are prompting manufacturers to rethink its industrial landscape. Manufacturers recognize the value analytics from the cloud brings in optimizing and introducing new levels of efficiencies that are difficult to replicate with traditional disconnected embedded devices.
traditional disconnected embedded devices
.’
Theoretically, these benefits from a connected embedded system are compelling enough for manufacturers to embrace this transformation, far outweighing the concerns of security and reliability that isolated embedded systems deliver. However, many underlying challenges could impact the health of the whole unit.
1. Governance and cybersecurity
2. Designing Hardware properly for embedded systems
3. Choose the right communication protocol ce
Sacheen Patil is vice president and global head of the IoT and embedded practice center of excellence at Yash Technologies.
4
u CONTROL ENGINEERING video explains 3 important things to know about PLC programming and adds another you may not have considered. Links to other PLC programming resources.
The 3-minute video covers use of appropriate PLC programming languages, PLC brand considerations, other tools common to all PLCs to help with tags and object-oriented architecture.
Frank Lamb is founder and owner of Automation Consulting LLC and member of the Control Engineering editorial advisory board.
Mark T. Hoske, Control
Engineering
u HOT TOPICS in Control Engineering, for March 2023, for stories posted in the last three months included PID tuning, digital twin, Hannover Messe 2023 and more. Link to each article below.
1. PID loop tuning parameters and control fundamentals
Understand proportional-integral-derivative (PID) control is and parameters for open- and closed-loop control.
2. Smart instrumentation helps with green hydrogen production, sustainability
Addition of green hydrogen energy processes needs smart instruments to help with goals for global sustainability and net-zero carbon emissions.
3. The impact of new technologies on automation and digitalization system architectures
Digital telecommunication evolution has been rapid over the past several years and is providing near realtime communication.
4. Logistics, robotics advances at the heart of improving automation
ProMat has a greater emphasis on robotics and how logistics improvements can make automation better in manufacturing facilities. See video.
5. How digital twin simulations advance digital transformation in manufacturing
By increasing visibility into a company’s manufacturing operations and testing an unlimited number of what-if possibilities in real-time, a digital twin can provide factories a reliable way to save time and money.
6. Hannover Messe 2023 Day Three: Connectivity and communication are critical to industrial transformation
Manufacturers and associations at Hannover Messe emphasized the need for better connectivity and communication with their products and each other.
7. Robots making farming more sustainable and flexible
Farmwise uses large autonomous machines and robots to eliminate the need for herbicides.
8. PID tuning advice
Control loop tuning information, advice.
9. Four things to look for in a robotic integration partner
Partner with an experienced robotic integrator that uses high-performance robots and peripherals.
10. How digital transformation powers the machine economy
Digital transformation technology is pushing digital twins closer to their real-world counterparts.
David Miller, CFE Media and Technology
Interact Analysis research shows the autonomous mobile robot (AMR) and automated guided vehicle (AGV) market is driving growth within the ultra-low voltage (LV) drives market. An ultra-LV drive is categorized as being <60 V.
In 2021, the global market for ultra-LV drives was valued at $753 million, and this is set to grow to $3.1 billion by 2027. The market for ultra-LV drives is at an inflection point in its growth cycle, with battery driven applications fueling growth. Many vendors historically not involved in this market have emerged due to demand from mobile robotics. The influence the AMR/AGV sector has on the ultra-LV drives market as a whole is expected to grow at a CAGR of 25.9%.
In 2022 alone, the AMR/AGV market accounted for 11% of ultra-LV drives market revenues. This share is predicted to grow to 56% by 2027. This is largely the result of fast-paced adoption of mobile robots, particularly those with integrated motor and drive. This saves cost and space, delivering greater drive efficiency. Integrated drives are more expensive than the alternatives.
Three main companies dominate the ultra-LV drives market, mainly with module type/decentralized drive types. Interroll, Insight Automation and Itoh Denki accounted for a combined ~30% of total ultra-LV drives 2021 market share. These companies manufacture motor rollers and the drive that is used to control the motor.
Read the Bundy article mentioned (upper right) at www.controleng.com to learn more about the April transactions. Online controleng.com u
With the rising importance of AMRs/AGVs in ultra-LV drives revenue, the top companies are unlikely to retain their position.
Blake Griffin, research manager at Interact Analysis said, “The Ultra-LV drives market is experiencing a period of exponential growth that is likely to continue for the next few years. The impact the AGV/AMR sector is having on the market is colossal and will change the supplier landscape dramatically in the coming years. Most vendors in the ultra-LV drives market registered double digit 2022 growth, with some reporting growth rates as high as 35%. Estimated revenue growth hit 24.2% in 2022, and unit shipments grew at 19.7%.” ce
– Interact Analysis is a CFE Media and Technology content partner.
THE BUNDY GROUP reported 15 automation transactions in the month of April. Thus far, the group has reported 46 transactions in the year of 2023. Bundy Group is a CFE Media and Technology content partner and reports on mergers and acquisitions for Control Engineering, Plant Engineering and Industrial Cybersecurity Pulse.
Bundy Group reported 15 automation transactions in April 2023. Courtesy: Bundy Group
MXD ANNOUNCED the launch of the Curriculum and Pathways Integrating Technology and Learning (CAPITAL) skill development program. The CAPITAL program, supported by $6.2 million in federal funding, is designed to address an expected 2-million worker shortage in the manufacturing workforce and provide resources aimed at meeting current and emerging workforce needs. MxD will develop certification-based manufacturing training courses and extend them to manufacturers, including those in the Defense Industrial Base (DIB). CAPITAL will help current students and workers and future members of the workforce develop the skills and training they need to ensure the DIB can effectively deploy advanced manufacturing technologies within U.S. factories, strengthening national security and increasing U.S. manufacturing’s global competitiveness. It will include courses and certifications that train workers for the most critical digital manufacturing roles, including artificial intelligence (AI) and cybersecurity for manufacturing.
“Manufacturers cannot effectively digitize without identifying the workforce of the future,” said Berardino Baratta, CEO of MxD in a press release. “Eighty percent of U.S. manufacturers ranked attracting and retaining a quality workforce as one of their greatest challenges. CAPITAL will both properly prepare the future workforce and bring current workers up to speed. The future of U.S. manufacturing hinges on our collective ability to close, or at least narrow, the impending skills gap.” ce
– Edited from an MxD press release by Control Engineering, CFE Media and Technology.
Industrial Internet of Things (IIoT) digitalization benefits include connectivity, consolidation, context, collaboration and cloud access.
Digitalization projects can have a greater success rate when addressing five operational technology (OT) data essentials in the industrial Internet of Things (IIoT) era, according to Darek Kominek, senior consulting manager, Matrikon. This applies to modernize an existing OT data infrastructure or when building new infrastructure using the latest OT and information technology (IT) innovations as he explained in the March 28 Control Engineering webcast, “Five keys to successfully digitalizing your OT-data infrastructure.” Topics focus on:
• How data technology (DT) bridges the IT/OT gap and helps companies implement a unified OT data layer (UODL).
• A modern (OPC UA and MQTT-based) approach to data connectivity in new and existing systems.
• Making data meaningful: why it’s mandatory and how to do it with OT data security.
• Ensuring an edge-to-cloud connectivity architecture and making OT-data infrastructure scalable and extensible.
Explanations, examples and diagrams explain key issues associated with OT-data infrastructure modernization during the webcast. Attendees also will learn why and how using DT simplifies the undertaking and maximizes returns by creating a robust, coherent unified OT data layer, which is used across the shop floor, the enterprise and cloud, Kominek said. While there are many ways to overcome individual technical challenges, he said, the key to building cost-effective and sustainable solutions is to do so securely, systematically and sustainably, regardless of what infrastructure is in place now.
Five advantages of IIoT digitalization in the OT data layer are connectivity, consolidation, context, collaboration and cloud access. Enabling technologies
Five advantages of IIoT digitalization in the OT data layer are connectivity, consolidation, context, collaboration and cloud access. Enabling technologies include advanced software and some combination of on-premise and cloudbased applications, according to Darek Kominek, senior consulting manager, Matrikon, in a March 28 Control Engineering webcast. Courtesy: Matrikon, Control Engineering webcasts
include advanced software functionality with some combination of on-premise and cloud-based applications, Kominek said. This benefits all the traditional layers of operational technologies, including sensors and devices, control systems, operational technology applications and business-related applications. Elements include data-source connectivity and federation, data modeling and mapping, OT-side firewalls, de-militarized zones (DMZs) for cybersecurity, information-technology (IT) side firewalls and cloud communications, Kominek said. Open standards help avoid automation vendor lock-in strategies by using OPC UA in a unified OT data layer. The webcast is archived for a year. ce
Mark T. Hoske is content manager, Control Engineering, CFE Media and Technology, and webcast moderator, mhoske@cfemedia.com.
controleng.com
KEYWORDS: OT data infrastructure, unified OT data layer, digitalization
LEARNING OBJECTIVES
Explore how to digitalize an OT-data infrastructure.
Learn details about the five advantages of a unified OT data layer: Connectivity, consolidation, context, collaboration and cloud access.
CONSIDER THIS
How can OT infrastructure embrace digitalization and industrial Internet of Things (IIoT) advantages?
ONLINE https://www.controleng. com/webcasts/five-keys-tosuccessfully-digitalizing-yourot-data-infrastructure
In an April 19 webcast, Alec Grainger, senior product manager, GE Digital, explored considerations to be made to ensure scalability when installing and working with HMI/SCADA systems. Learn more and see a link to the archived webcast below.
LKEYWORDS: HMI, SCADA LEARNING OBJECTIVES
Learn about the evolution of modern SCADA
Explore the benefits of enterprise-wide, scalable HMI/SCADA systems
ONLINE
Top 10 modern SCADA system features https://www.controleng. com/articles/top-10modern-scada-systemfeatures/
CONSIDER THIS
Can HMI/SCADA systems help your applications scale?
earn about the evolution of modern supervisory control and data acquisition (SCADA) and human-machine interface (HMI) systems with advice on how to scale them across the enterprise in an April 19 webcast, “Can your HMI/SCADA system scale and serve as an enterprise-wide solution?” Results include 40% faster troubleshooting in less than a year, and a 70% increase in user-experience usability score. More information about and from the webcast follows. Webcast attendees qualify for a certificate of completion. The webcast is archived for a year,
"The benefits of an enterprise SCADA are centralized management, remote capabilities, and mobile operations," said Alec Grainger, senior product manager, GE Digital. Courtesy: Control Engineering webcasts, GE Digital
HMI/SCADA systems have been around for almost 40 years and are in widespread use today. However, users should rethink their existing architecture and deployment options with modern technologies in mind, according to Alec Grainger, senior product manager, GE Digital, and webcast instructor. Many organizations have multiple, disconnected SCADA systems, which increases costs and decreases the ability to optimize operations. Maintaining one, enterprise-wide SCADA system across multiple facilities helps increase efficiency and is more cost-effective. There are many reasons why some companies may not have adapted. For instance, the use legacy systems that have never been standardized into one SCADA system across multiple plants. Some companies even may have multiple systems acting as point
solutions in a facility. Still, because the technology is mature, not all SCADAs can deliver the required interoperability or scale to a cost-effective and easily implemented enterprise-wide solution.
According to Grainger, there are several selection criteria end-users should keep in mind to ensure an HMI/SCADA system is scalable:
• The system must be able to add more clients over time and must have the capacity for mobile access. Because an enterprise may not be focused in one geographical area, remote connectivity is essential.
• With expansion, more redundancy must be added. As applications become larger/more complex, outages potential becomes more threatening and redundancies must be added to mitigate system outage risk.
• End-users must be able to seamlessly integrate new components. Varying protocols used in different parts of an organization must be consolidated to enable interoperability and a consistent user experience.
Enterprise HMI and SCADA systems grant end-users several beneficial capabilities including centralized management, remote monitoring and operations, and large-scale visibility. Grainger's presentation highlighted outcomes from customers scaling HMI/ SCADA systems across an enterprise:
• Chemicals: 37% increase in abnormal situation handling effectiveness in less than one year.
• Water utility: 40% faster troubleshooting in less than one year.
• Power: 70% gain in user-experience usability.
• Building management: 25% reduction of energy bill within 18 months. ce
Edited by David Miller, content manager, Control Engineering, CFE Media and Technology, dmiller@cfemedia.com.
uHannover Messe returned in a more subdued form than in previous years as the show tries rebounding after the COVID-19 pandemic. Nevertheless, the show must go on and the theme of industrial transformation was very much prevalent for many companies. Automation remains a major priority for manufacturers looking to keep up with demand as labor woes continue to persist. So do supply chain challenges, though they aren’t as a big a problem as they were in 2022.
Because of COVID-19, many companies are turning their focus toward developing not just one product solution, but rather developing an entire suite. That can include everything from the motor or drive, parts inside the motor and drive and the cloud platform where the data goes after being transmitted.
“For us, it’s not just providing the product or hardware. We want to provide the whole solution,” said Ronai Ayhan, manager of global public relations, discrete automation, for Emerson. “We want to be able to give them anything they need in the portfolio.”
Amit Patel, director of digital transformation for Emerson, agreed. “We’re about connecting the factory floor and unlocking that trapped data. It’s about taking all these pieces to the cloud so something can be made out of it.”
Emerson’s theme “Floor to Cloud: The Future of Automation” encapsulates and serves as a model for what others are hoping to achieve in their efforts to transform on an industrial basis. Much of it is coming because companies need to stay
Hannover Messe (top) has 27 halls that can be used for exhibition and most were used in 2023. Left, Amazon Web Services emphasized data integration for better insights. Courtesy: Chris Vavra, CFE Media and Technology.
ahead of the curve and deliver products their customers want. The workers might not be there, but the demand remains strong.Lenze, a company known mostly for motors and drives, is tilting its focus toward automation. The company is leveraging their 75 years of history to help deliver a full portfolio that will give engineers what they need. The preferred method of delivery is less pen and paper and is more digital and automated.
“We started with improving drive technology because it’s what we’re known for, but we’re moving into automating our systems and platforms,” said Ines Oppermann, corporate communications for Lenze.
Making automation more open and smarter artificial intelligence (AI) and machine learning both play a role in enhancing automation by providing information to the user.
“You can train an AI model to learn
patterns,” said Werner Paulin, the product owner of Nupano, an open automation platform making its debut at Hannover Messe. “It can’t tell you what’s wrong or right, but it can tell you what is likely to happen.” Nupano is designed to let machine builders to bring innovations in at the machine level for themselves and let them leverage digitalization.
Companies looking to leverage digitalization are becoming more software-agnostic as the interoperability is more a concern.
“It’s about flexibility and control,” said Ramon Boncompte, a sales director and co-owner of Industrial Shields, whose company sold industrial programmable logic controllers based on open-source hardware. “We’re about saving resources and having the customer use our products to gather the data they need.” ce
Chris Vavra, web content manager, Control Engineering, CFE Media and Technology, cvavra@cfemedia.com.
uHannover Messe was much livelier Tuesday as more people came in after the Orthodox Easter holiday, and the activity reflected that overall. Many customers are looking for solutions for problems. In many booths, however, they are seeing how companies are working together with different vendors to make solutions that are better for everyone involved.
That might seem like a strange concept given how companies are often competing with one another. At the Amazon Web Services (AWS) booth, collaboration is the point.
"Floor to Cloud: The Future of Automation" was an Emerson demonstration at Hannover Messe 2023. Courtesy: Chris Vavra, CFE Media and Technology
“Here at the AWS booth, we are highlighting 30 different vendors sending all their data, and we’re feeding it into one center to help make better products,” said an Amazon spokesperson. “When it comes to data gathering and putting it all together, not a lot of manufacturers want to do this themselves.”
More to the point, they said they want to
bring operational technology (OT) and information technology (IT) together. Many of the services they provide are designed to help OT engineers and educate them in the tasks that, normally, should not require IT. Educating the OT engineer helps them understand what to look for and make better decisions based on the data they have.
“We’re interested in helping our customers get more value from their data,” the spokesperson said. “Companies often start out with a use case that’s successful and then they move on to the next thing and scale it up, but scaling is tough if the companies don’t have the proper context and understanding, which is what we try and provide for them.”
We want to put people in the best place to resolve the solution.”
Rockwell Automation is doing the same thing by using its partner program and those relationships to get the most value for its customers.
‘ We’re trying to be agnostic; we want to tie the digital thread together.’
Corey Jurek, a technology consultant for Rockwell Automation, described a pickand-place robot with the robot arm provided by Comau. Rather than have the robot arm and other pieces from other manufacturers causing a potential headache for users, Jurek said they simplified the process.
“What we’ve done is taken the robot controller aside, and we’ve installed our own encoder instead.”
Microsoft’s booth emphasized cloud and edge computing solutions throughout its booth. Vendors there were mostly focused on automating processes wherever possible and, when human intervention was needed, processes that didn’t require a lot of thought or action.
Tulip Interfaces’ focus was about augmenting frontline workers with connected applications and using apps to give engineers real-time information and alerting them to challenges or issues as they come up.
Lee Lewis, an enterprise account executive for Tulip, said, “We want the engineer to tweak it for their own preference. Very drag-and-drop. We made it so you can build your own app and tweak as needed.
Taking control of the base concept goes beyond the robot arm, though. They want to be able to provide users with all the information they need from the bottom on up and give engineers the best possible view of their data.
“We’re trying to be agnostic,” said Nina Tebbe, head of software sales for Central Europe for Rockwell Automation. “Regardless of whether it’s greenfield or brownfield, we want to tie the digital thread together. We want to take what’s there and weave it together.”
For a lot of these companies involved in collaboration and cooperation, that is what it comes down to: Finding a common point where all the data can reside, and the user can make their own decisions with the tools they have. ce
Chris Vavra, web content manager, Control Engineering, CFE Media and Technol-
uHannover Messe has revolved the 2023 show around the idea of industrial transformation. What that means is different depending on the company and their agenda. However, almost all companies can agree they are looking to get their information faster any way possible. Industrial networking advances are certainly at the heart of it, but so is relaying and communicating the data to the right people when they need it.
While this has gotten better in recent years, there’s still a long way to go.
Profibus and Profinet International (PI) is focused on developing and supplying fieldbus and Industrial Ethernet solutions for cost efficient and highly reliable automation. At their booth, they had many solutions designed for more than 20 manufacturers.
Xaver Schmidt, the chairman of PI, said, “Our goal is to collect developers, vendors and different communities and bring them together. We want to exchange ideas and different technologies and improve industrial communication.”
Ole Borgbjerg, senior director of sales at PTC, said, “Being industryagnostic is important to us. No matter if it’s process or discrete industries.”
cybersecurity. Operational technology (OT) and information technology (IT) are learning to work together and respond to each other’s language, but the process is a bumpy one.
“We want to bring OT and IT together,” said Nina Tebbe, head of software sales in Central Europe for Rockwell Automation. “Everyone should ask what the client wants to achieve. It’s important to look at it from their perspective.”
Patrick McCurdy described open-source programming as like the combs on a beehive. While perhaps a strange analogy at first glance, it does make sense upon further thought. Engineers, especially those are who just starting out, don’t want to be stuck using programmable logic controller (PLC) languages such as ladder logic when they’ve been working on Raspberry PI. They want the freedom and the flexibility to choose.
‘ Control systems need to be flexible, modular and able to take on many different forms.’
Improving communication in manufacturing has often been a challenge. In a large facility, it’s hard to tell what’s happening at any given moment. Even with the advances in digital technology, it still comes down to people responding and reacting. That isn’t always easy as the engineers are interacting more with the
Where the beehive analogy comes in is when the engineers are building their system, it needs to be flexible and modular and can take on many different forms. McCurdy said the PLCnext, which is where the honeycomb example started, called it an ecosystem.
“It’s an open ecosystem to do control and automation,” he said, adding later that this kind of flexibility for engineers brings “A world of openness.”
Beckhoff Automation’s Tuesday press conference described a trend that has been happening the last few years where manufacturers are going beyond their usual
Manufacturers emphasized providing customers with more total solutions to give their customers whatever help they need regardless of what it is.
niches and expanding their reach beyond their expertise.
“We are a system provider so we try to offer the complete automation system from I/O down to motion. We do this with a PC-based control system,” said Johannes Beckhoff, R&D department, Beckhoff Automation.
From there, he described the company as an industrial PC, an I/O, a motion, a system and an automation company. All of their expertise is folded together to give them more control over products and reduce reliance on other manufacturers and providers. There is a certain appeal to it from a control standpoint. In some cases, as was seen with SEW Eurodrive expanding from motors and drives to autonomous mobile robots (AMRs) and automated guided vehicles (AGVs), these expansions are leveraging the technology that already exists and finding new uses for them.
Through partnerships with associations and consortiums, they’re learning from their competition and other companies outside their market. It’s not just technology, but also philosophies and ideas and procedures. All of these help manufacturers willing to go down this road the tools they need to be successful in this endeavor. Customers also benefit because it can reduce the long-term price points if something needs to be fixed or repaired. ce
Chris Vavra, web content manager, Control Engineering, CFE Media and Technology, cvavra@cfemedia.com.
uWhile ProMat 2023 exhibits focused on technologies useful for distribution centers and warehouses, the industrial computing, automation and motion control products shown at the Beckhoff Automation booth could be used in many manufacturing and other industrial applications. ProMat 2023, March 20-23, in Chicago, was organized by MHI.
Beckhoff Automation enhanced its demonstration of the Beckhoff XPlanar advanced motion control platform by projecting videos onto the movers and tile base to show different applications and how floating movers could be applied for micro-fulfillment and other applications.
Described as a smaller-scale automated guided vehicle, the movers can operate individually, in pairs or in groups to handle larger loads. XPlanar has no mechanical parts, covers a small footprint, can be programmed with Beckhoff TwinCAT software and is being integrated by machine builders and others, in undisclosed applications. So far, custom
Beckhoff Automation projected application videos onto the movers and tile base (photos) to help show XPlanar motion control platform capabilities. Courtesy: Mark T. Hoske, Control Engineering
machine builder applications account for about 60%, and original equipment manufacturers (OEMs) account for about 40% of XPlanar use.
Each XPlanar mover can transport 400 g (about 9 lb). Mover routes and mover motions on the base can change on the fly (video clip). Movers also can precisely swirl and mix liquids they carry in a controlled manner.
TwinCAT/BSD, a UNIX-based version of Beckhoff Automation programming and control platform, extends TwinCAT software beyond Microsoft Windows. Hypervisor virtualization software can run on TwinCAT UNIX or Microsoft Windows in virtual machine architectures. Such configurations make it easier for IT to run updates of Microsoft Windows software applications while avoiding disturbance to run-time applications for operations. Multiple controllers and higher-level applications could run in one piece of computing hardware. Many configurations and silicon combinations, speed and computing cores provide a wide range of computing power, all programmable with Beckhoff TwinCAT software.
Top 5 Control Engineering content: April 17-23, 2023
The top 5 articles from the week include Hannover Messe 2023, AI and robotics integration.
How to organize, protect and apply big data in automation
Big data in automation and manufacturing can transform operations, but great care needs to be applied when inserting it into a company.
How to simplify PLC, control device management with Git version control, auto-backup Webcast on PLC and control device programming explains Git version control and automated-backup capabilities help simplifying programmable logic controller (PLC) and control device management. Benefits include reduction in onboarding costs and better code.
SHOWS, CONFERENCES
May 15-19, CSIA Executive Conference, https://www.controlsys.org/events/conference2023
May 22-25, Automate by A3, https://www.automateshow.com
June 18-24, 2023 Honeywell Users Group (HUG), https://pmt.honeywell.com/us/en/about-pmt/honeywell-users-group
June 24-27, EASA 2023 Convention and Solutions Expo, https://easa.com/convention
Sept. 9-11, Pack Expo Las Vegas 2023, PMMI, https://packexpolasvegas.com
Sept. 26-28, Ignition Community Conference, Inductive Automation, https://inductiveautomation.com/resources/icc#
Under development for release in mid-2024, the Beckhoff MX System, a rugged, industrial cabinet-less machine control platform, provides modular, integrated, hot-swappable control system components: Controllers, I/O modules, communications and power supplies. The MX System, also programmable with Beckhoff TwinCAT software, is designed to operate outside of control cabinets in stand-alone configurations and/or could extend control capabilities inside existing control enclosures.
Other coverage from ProMat includes Control Engineering articles on intralogistics, warehouse robotics advancements, mobile robot software management. ce
Mark T. Hoske is content manager, Control Engineering, CFE Media and Technology, mhoske@cfemedia.com.
DIGITAL TRANSFORMATION and best practices related to the growing digitalization ecosystem of connected, data-driven and automated technologies were among topics of presentations, discussions and thought leaders at the 2023 Manufacturing in America Summit, April 12 and 13 in Detroit, by Siemens and Electro-Matic (a SunSource Co. and value-added distributor of products, including Siemens).
Benefits of digital transformation can include increased energy efficiency and sustainability, process visibility, quality, speed to market, lower costs, easier workflow and supply chain integration, improved safety and other advantages. To begin the event, Siemens assembled speakers to talk about applying advanced digital, automated technologies for greater efficiency in a variety of implementations.
• Raj Batra, president of Siemens Digital Industries USA and of the Siemens Foundation, an organization designed to help fill skills gap
• Garlin Gilchrist, lieutenant governor of Michigan and two-time technology startup entrepreneur
• Tom Kelly, executive director, CEO, Automation Alley, an automation advocacy and assistance organization for Southeast Michigan
• Christopher Alan, owner, president, Dasher Lawless and AutoParkit, an automated parking business
• Tisha Livingston, CEO/co-founder, Infinite Acres, a vertical, automated, sustainable farming company, FarmTech Society vice president.
Manufacturing in America fits what is happening in this country, which includes technological advancement and the global ecosystem of talent to make manufacturing work. Digitalization and automation help get products to market faster, waste less and be more sustainable in that effort, and 100 technology breakout sessions at Manufacturing in America are designed to help, Batra explained.
“We are bringing manufacturing back to the U.S.,” Batra explained with the number of manufacturing locations increasing and $108 billion, a new manufacturing construction spending record in 2022, he explained.
Gilchrist said manufacturing has accomplished a lot and has a bold, exciting future ahead, where government plays a role, in connected, useful and creative opportunities through government-private cooperation to collaborate to unlock innovation. Michigan has a rich history of strong manufacturing careers and continues with growth in 3D printing, robotics and other areas to help manufacturers grow.
Kelly said Automation Alley formed in 2019 to rebrand Southeast Michigan as high-technology hub. The organization works with governments, educational organizations and companies to reshape how the world perceives eight Detroit-area counties, building communities to re-dominate in manufacturing to apply what’s possible by using advanced technologies. Automation Alley takes care to ensure technologies are applied correctly. An analogy is to not to put smartwatches on horses, Kelly suggested, but build smarter automobiles.
Continued on page 16
Continued from page 15
Christopher Alan, owner, president, CEO, Dasher Lawless and AutoParkit, an automated parking technology company, uses industrial automation in applications people can use. With AutoParkit, users can use a phone app to have the car delivered to a secure room. Self-parking and retrieval technology increases parking density, avoids car damage and creates a more secure environment for users, Alan said. In an old Detroit Free Press building, an AutoParkit application for apartments uses a 30-foot-tall basement that only would fit 32 cars with a conventional parking design and makes room for 110 cars. Applying the AutoParkit automated concepts to other areas, Dasher Lawless has created AutoChargit, advanced electric vehicle charging solutions; AutoStorit, an automated smart storage application to more efficiently store and retrieve goods; and AutoDockit, an automated boat retrieval system.
Infinite Acres, which began in 2015, has five production farms operating and two under construction, is among a handful of automated vertical farm companies. It is the only one, Livingston said, that is profitable. Vertical farms, treated as automated manufacturing stack the produce, optimize lighting and moisture and use 95% less water than traditional farming. In a Hamilton, Ohio, facility, 10 acres of lettuce is grown in 1 acre, with 17-20 more growing cycles possible indoors with optimization using computers, machine vision, artificial intelligence, economical LED lighting, motion control and other automation compared to outdoor lettuce farming. Rather than have robots go to where the crops like humans harvest, Infinite Acres adds efficiency by moving the to the robots. With optimization, lettuce harvest is in 20 days. Vertical
Vertical farm productivity benefit from scalable and repeatable processes that use digital twins to help optimization, as explained by Tisha Livingston, CEO and co-founder, Infinite Acres, speaking at the 2023 Manufacturing in America Summit. Courtesy: Mark T. Hoske, Control Engineering
farms grow 300 times as much food per square foot than outdoor traditional farming. Vertical farms also save energy by removing steps in the supply chain (photo). Automated systems are underway for tomatoes (dwarf tomatoes can use the same platform as lettuce), cucumbers and a variety of berries and other crops, she said. It’s not only lettuce.
See more photos and more comments from each speaker with this article online.
Engineering, CFE Media,
3010 Highland Parkway, Suite 310, Downers Grove, IL 60515. 630-571-4070, Fax 630-214-4504
Content Specialists/Editorial
Mark T. Hoske, Content Manager 630-571-4070, x2227, MHoske@CFEMedia.com
David Miller, Content Manager, 312-481-5068, DMiller@CFEMedia.com
Emily Guenther, Director of Interactive Media 630-571-4070, x2229, eguenther@CFEMedia.com
Amanda Pelliccione, Director of Research 978-302-3463, APelliccione@CFEMedia.com
Gary Cohen, Senior Editor GCohen@CFEMedia.com
Chris Vavra, Web Content Manager CVavra@CFEMedia.com
Contributing Content Specialists
Suzanne Gill, Control Engineering Europe suzanne.gill@imlgroup.co.uk
Agata Abramczyk, Control Engineering Poland agata.abramczyk@trademedia.pl
Lukáš Smelík, Control Engineering Czech Republic lukas.smelik@trademedia.cz
Aileen Jin, Control Engineering China aileenjin@cechina.cn
Editorial Advisory Board www.controleng.com/EAB
Doug Bell, president, InterConnecting Automation, www.interconnectingautomation.com
David Bishop, chairman and a founder Matrix Technologies, www.matrixti.com
Daniel E. Capano, senior project manager, Gannett Fleming Engineers and Architects, www.gannettfleming.com
Frank Lamb founder and owner Automation Consulting LLC, www.automationllc.com
Joe Martin, president and founder Martin Control Systems, www.martincsi.com
Rick Pierro, president and co-founder Superior Controls, www.superiorcontrols.com Mark Voigtmann, partner, automation practice lead Faegre Baker Daniels, www.FaegreBD.com
CFE Media and Technology Contributor Guidelines Overview
Content For Engineers. That’s what CFE Media stands for, and what CFE Media is all about – engineers sharing with their peers. We welcome content submissions for all interested parties in engineering. We will use those materials online, on our website, in print and in newsletters to keep engineers informed about the products, solutions and industry trends.
www.controleng.com/contribute explains how to submit press releases, products, images, feature articles, case studies, white papers, and other media.
* Content should focus on helping engineers solve problems. Articles that are commercial or are critical of other products or organizations will be rejected. (Technology discussions and comparative tables may be accepted if non-promotional and if contributor corroborates information with sources cited.)
* If the content meets criteria noted in guidelines, expect to see it first on our Websites. Content for our e-newsletters comes from content already available on our Websites. All content for print also will be online. All content that appears in our print magazines will appear as space permits, and we will indicate in print if more content from that article is available online.
* Deadlines for feature articles for the print magazines are at least two months in advance of the publication date. It is best to discuss all feature articles with the appropriate content manager prior to submission.
Learn more at: www.controleng.com/contribute
Control processes, SCADA and HMI are leading applications for edge computing; AI enhances control capabilities.
Control Engineering subscriber research on “Edge computing and artificial intelligence technology” was conducted in February and March 2023 to learn how those technologies are being used for automation, controls and instrumentation. About half of respondents agree edge computing is a better target for artificial intelligence (AI) software/algorithms than programmable logic controllers. Computing power, networking capabilities and reliability are the leading reasons respondents are using AI with edge computing. The top reasons respondents use AI/ machine learning (ML) include access to capabilities previously unavailable in other software (61%) and to enhance traditional control methods (58%). Summary results follow.
Among survey respondents, 98% are using edge computing in some way. Edge computing is most commonly used in control processes (51%) and supervisory control and data acquisition (SCADA) software (50%) for automation, controls and instrumentation applications and with human-machine interface software (46): This is a three-way tie, all within the margin of error.
Controls, automation or instrumentation technical support is used, or expected to be in use, for edge computing by 28% of respondents. Another 21% cited operational technology (OT) or engineering department support.
Half of respondents said edge computing is used because it enables a more agile and responsive monitoring and control system over other compute or logic devices, as well as providing next-generation control solutions like AI/ML. About the same number said it supports better decision making by faster processing of real-time data. Among respondents, 88% use cloud resources with edge computing; analytics (55%) and memory/storage (50%) are the top cloud resources.
AI/ML was acquired by 53% of respondents through an application that an automation, controls or instrumentation vendor or distributor provided to them. Among respondents, 73% are using AI/ML for controls, automation or instrumentation technical support; 47% for OT or engineering department support. The top reasons respondents use AI/ML include access to capabilities previously unavailable in other software (61%) and to enhance traditional control methods (58%). After initial startup and regular operation, 22% of respondents cite they update the data model that helps guide the AI/ML application in real time; 16% weekly; 12% twice a year and 11% daily.
About half (51%) of respondents agree edge computing is a better target for AI software/algorithms than programmable logic controllers (PLCs). Computing power (38%), networking capabilities (37%) and reliability (32%) are the top three reasons why respondents are using AI with edge computing.
To do the research, subscribers were sent an email from Control Engineering asking them to participate. Information was collected from Feb. 8 through March 23, 2023. With 121 respondents, the margin of error for the results was +/-8.9% at a 95% confidence level.
Think again about how edge computing and AI can be applied to automation, controls and instrumentation applications. ce
Mark T. Hoske is Control Engineering content manager, mhoske@cfemedia.com. Amanda Pelliccione, director of research and awards programs for CFE Media and Technology, did the research and assembled the report and much of the information above.
Don Dickinson, Phoenix Contact USA
While Industry 4.0 can potentially allow for the intelligent optimization of multi-pump systems, without an open control platform, operators may struggle to properly coordinate their devices.
Industry 4.0 holds the promise of optimal performance, improved reliability and cost savings in the operation of automated systems, including multipump systems used in municipal water and wastewater systems. Those benefits cannot be fully realized using proprietary legacy control platforms.
Open platforms enable Industry 4.0 by facilitating the integration and interoperability of diverse systems
and devices and providing a foundation for collaboration and innovation. (Figure 1) The future of pump control, and all automation, is open, and it’s now.
Pump systems vary greatly, as do the devices that control them. Generally, there are two ends to the pump controller spectrum. On one end is the dedicated-purpose controller. On the other are general-purpose devices, such as programmable logic controllers (PLCs), which are programmed to control multi-pump systems along with peripheral functions, or even entire pump stations.
Dedicated controllers are optimized for pumping applications, have a defined feature/function set, are easy to specify and are supported by the manufacturer. By contrast, PLCs can be programmed to provide any required function and offer a wide range of choices for hardware platforms and communications for integration into plant networks.
Both approaches have been employed for decades, and each has advantages for specific use-cases. However, they both have disadvantages as well. Dedicated-purpose controllers typically are fixed designs without options for upgrades or migration to newer technology. PLCs require specific knowledge of proprietary platforms for programming and support, and the feature/function set programmed by a third party is custom and difficult to support over the lifecycle of the system. Although PLCs have more options for migration to newer platforms than
FIGURE 2: Open platform PLCs, such as Phoenix Contact’s PLCnext Control, allow the implementation of automation projects without the limitations of proprietary systems.
dedicated-purpose controllers, transitioning from a legacy PLC system to a current platform can be time-consuming and costly, even if using the same manufacturer. Other drawbacks of each include limited options for process visualization and the need for special hardware that may require added programming and configuration.
The ideal pump controller would combine the best features of a dedicated-purpose controller and PLCbased controller with none of the disadvantages. It would be built on an open platform that supports application development in a variety of programming environments from different sources. Most importantly, the ideal controller would be easily integrated with other systems and devices, enabling sharing of real-time data and analytics to make better decisions for an operating a pump system. (Figure 2)
Why are open platforms so beneficial in automation? Open platforms enable use of advanced technologies and applications such as the Industrial Internet of Things (IIoT), machine learning and cloud communications to provide greater connectivity, interoperability and flexibility. Open platforms enable:
• Interoperability: Open platforms allow different systems and devices to communicate, work together and seamlessly integrate diverse technologies and data sources, leading to increased efficiencies.
• Data sharing: Open platforms enable data sharing across different systems and applications essential for process optimization and greater efficiencies.
• Collaboration: Open platforms provide a foundation for collaboration between manufacturers, programmers, suppliers, system integrators and customers leading to more innovative products and services.
FIGURE 3: Open PLCs make it easy to get real-time data, while also connecting to common cloud platforms such as AWS from Amazon and Azure from Microsoft.
‘ A controller should be easily integrated with other systems and devices, enabling sharing of real-time data and analytics to make better decisions.’
• Flexibility: Open platforms allow manufacturers to adopt new technologies and processes quickly and easily, allowing a nimble response to changing market conditions and needs.
Linux is a popular open-source platform due to its open-source nature, flexibility, stability, security and affordability. A pump control application running on industrial hardware with a Linux operating system can offer advanced capabilities that go well beyond basic functions of starting and stopping pumps. Application enhancements could include:
• Predictive maintenance: Leveraging data analytics and machine learning algorithms to predict when maintenance is required for a multi-pump system enables proactive maintenance, reduces downtime and increases system reliability and resilience.
• Real-time monitoring: Real-time monitoring of pump systems provides valuable insights into the performance of individual pumps and the system, allowing for quick and effective intervention in the event of a problem. (Figure 3)
• Improved efficiency: Data analytics can help to optimize pump systems by identifying areas for improvement. For example, data can be used to determine the most energy-efficient operating conditions for individual pumps, reducing energy consumption and operating costs.
• Increased automation: More data allows more decisions to be automated, reducing the need for manual intervention and increasing efficiency. For
controleng.com
KEYWORDS: Pump Control, OPA
LEARNING OBJECTIVES
Learn how Industry 4.0 can allow for the intelligent optimization of multi-pump systems by more effecitvely coordinating many devices.
See how open platforms can enable interoperability, collaboration and flexibility.
ONLINE
For more on Open Process Automation, also visit www. opengroup.org.
CONSIDER THIS
Does your control system currently face integration challenges?
FIGURE 4: A central marketplace like the PLCnext Store from Phoenix Contact can connect software developers with users to implement advanced pump control functions.
FIGURE 5: PLCnext Control from Phoenix Contact allows the parallel programming and combination of familiar IEC 61131-3 programming languages, with high-level languages such as C/C++, C#, or MATLAB Simulink.
example, automatically controlling the speed of individual pumps in response to changes in demand ensures the system operates at peak efficiency.
this approach is that it is a closed, proprietary system, is expensive to install and requires a subscription service to maintain access to data. The ideal pump controller handles control and advanced functions on one platform to minimize cost and support requirements. The ideal controller is built on an open platform such as Linux, allows integration of best-in-class components, offers cloud connectivity and supports applications in different programming languages from different sources. (Figure 5) The concept of open process automation is gaining traction in the process-rich industries, where upgrades or replacement of large-scale plant systems is immensely costly and requires protracted downtime to accomplish.
New open standards are on the way
Open Process Automation (OPA) is developing a new standard for process automation systems. The goal of OPA is to create an open, interoperable and secure standard for process automation systems that allows users to mix and match hardware and software components from multiple vendors, enabling greater flexibility and innovation.
between
Enhanced collaboration: Greater integration allows more collaboration between different parts of the pump system and the pump system and peripheral systems. This enables data to be shared in real-time, allowing quick and effective decision-making.
Pump manufacturers do offer products that use data to improve efficiency and reduce downtime and platforms that allow customers to monitor and manage pumps remotely, with data analytics and machine learning algorithms to optimize performance.
The ideal pump controller would support any pump or pump system and would easily integrate into other systems to achieve plant-wide goals for improved efficiencies and cost reduction.
Some suppliers offer advanced platforms that can be used on any pump system. Use real-time monitoring to optimize pump performance and reduce lifecycle costs by providing detailed information on when to repair or replace a pump. A drawback to
OPA is being developed by the Open Process Automation Forum (OPAF), a group of more than 200 companies from a wide range of industries. The forum is developing a set of standards and specifications for OPA, which will enable the interoperability of hardware and software components from different vendors. OPA benefits include the ability to customize and optimize process automation systems to meet specific needs; reduce costs and increase efficiency using standard, off-theshelf components; and improve cybersecurity using secure, interoperable components.
OPA shifts the process automation industry from closed, proprietary systems to open, interoperable systems that offer greater flexibility and innovation. The OPA approach, an open platform for industrial systems, is available now. So too are pump control applications running on a Linux platform that represent the future of pump control. ce
- Don Dickinson, senior business development manager — water/wastewater, Phoenix Contact USA. Edited by David Miller, content manager, Control Engineering, CFE Media and Technology, dmiller@cfemedia.com.
If you’re a system integrator with demonstrable industry success, Control Engineering and Plant Engineering urge you to enter the 2024 System Integrator of the Year competition. Past System Integrator of the Year winners—Class of 2023, Class of 2022, and Class of 2021—are not eligible to enter the 2024 System Integrator of the Year program.
The chosen System Integrator of the Year winners will receive worldwide recognition from Control Engineering and Plant Engineering The winners also will be featured as the cover story of the Global System Integrator Report, distributed in December 2023.
Control Engineering and Plant Engineering’s panel of judges will conscientiously evaluate all entries. Three general criteria will be considered for the selection of the System Integrator of the Year:
• Business skills
• Technical competence
• Customer satisfaction
Leading-edge automation technologies are helping solve workforce shortages and economic challenges; salaries increased.
Continuing manufacturing workforce shortages and the economy were cited as the biggest threats to manufacturing; threat of worker shortages was cited by 48% of respondents, down from 57% in 2022, but still up significantly from 37% in 2021. Leading automation technologies are helping resolve those issues. Salaries increased 7% from last year to $111,345. These were among the key findings in the 2023 Control Engineering Career and Salary Survey and Report.
This year, the economy, cited among biggest threats by 43%, was within the 6-percentage-point margin of error for the research, making it a statistical tie with workforce shortages as the biggest perceived threat to manufacturing. Economy was third in 2022 at 31%. Supply chain concerns eased: “Lack of necessary materials,” backed off to 30%, down from 42%, which was sec-
ond in 2022 and about even with 27% in 2021. Energy concerns also fell.
More engineers expect to receive a salary increase in the coming year: 71%, up from 67% in 2022 and 62% in 2021; while 29% expect benefits to increase, compared to 26% in 2022 and 23% in 2021.
While Control Engineering subscribers answering the survey differs from year to year, salary and benefits increased with the strong demand for automation, controls and instrumentation talent to help fill the labor market skills gap. Average annual salary for survey respondents was $111,345, up 7% from $104,071 last year. Average salary increased more than bonuses decreased, however. Non-salary compensation decreased to $15,929, for those receiving bonus or profit-sharing, down 16.9% from $19,162. Leading criteria for bonuses were 55% company profitability and 43% personal performance, similar to last year.
In results reflecting Control Engineering ’s diversity of controls, automation and instrumentation coverage, subscribers placed double-digit value on all 23 technologies listed in the new question: “What technologies are most likely to help you in the coming year? Check all that apply,” with four replies in a statistical dead heat for the top spot: 32% Process optimization; 31% Automation applications/upgrades; 28% Automation: Robotics, collaborative robotics, mobile robotics; and 27% Analytics: Data analytics. Interestingly, no technology on the list of 23 was separated from any other by more than 3 percentage points, except “other” at 2%, at the bottom, well below the lowest 11%, representing a
FIGURE 3: In 2023, the average salary of respondents is $111,345, up from $104,071 in 2022. In 2023, average bonuses among those receiving them was $15,929, down from $19,162 in 2022.
nine-way statistical tie for last, but still in the double digits. (See “What technologies” table.)
Three factors with greatest impact on job satisfaction were technical challenge and financial compensation tied at 30% and feeling of accomplishment at 25%.
Top three skills to get ahead were 72% engineering and communication/presentation and project management virtually tied at 62% and 61%.
Hours worked increased among respondents, with an 8-percentage point increase of those working 50 or more hours in 2023 compared to 2022.
9% worked fewer than 40 (11% in 2022)
42% worked 40 to 44 hours (43% in 2022)
24% worked 45 to 49 hours (29% in 2022)
14% worked 50 to 54 hours (9% in 2022)
3% worked 55 to 59 hours (same)
8% worked 60 or more (up from 5%).
A new question asked the best ways to advance skills in automation, controls and instrumentation: 84% said hands-on experience, 68% said continuing education and, in a three-way virtual tie for third:
• Being mentored
• Reading industry publications, sites, email newsletters, digital guides, vendor, research and association sites and materials
• Networking at conferences, memberships in industry organizations, participation in standards bodies and other industry groups.
Subsequent articles in this section provide advice on engineering employee hiring and retention and related engineering career topics. Articles in Control Engineering discuss how automation, controls and
Company profitability
Personal performance
New business, sales increase, commission
Product profitability
Plant or line productivity
Quality metrics
Safety metrics
Company stock performance
Uptime/downtime
Reducing plant costs
Customer feedback
Energy efficiencies or other sustainability metrics**
Application of industry standards*
Better system integration, information flow*
Increased line flexibility*
IT/OT collaboration*
Other
Not applicable (no bonus received)
FIGURE 4: In 2023, company profits remained ahead of personal performance as the leading criteria for non-salary compensation, after being tied in 2021. Four* criteria were added and one** was modified.
instrumentation bring greater efficiencies to manufacturing, often to optimize and help with manufacturing workforce shortages.
Survey methods, ChatGPT input
Research for the 2023 Control Engineering Career and Salary Report resulted from an emailed survey to subscribers, producing 266 qualified responses from March 10 to April 4, 2023, for a margin of error
technologies are most likely to help you in the coming year? Check all that apply.
Analytics: Data analytics 25%
Industrial internet of things (IoT), such as more interconnected sensors, monitoring, data collection
25%
Process design, measurements, optimization
25% Remote controls, monitoring
24% Artificial intelligence (AI) and machine learning (ML) 22%
Automation: Motion control optimization with advanced actuators, drives 22% Better HMI and SCADA designs
Industrial communications: faster and easier among devices and systems
Analytics for predictive or prescriptive maintenance
Cybersecurity technologies
Industrial communications: Wireless networking
Cloud computing
Digital twins and simulation
Power quality and reliability
Sustainability metrics, measurements and related optimization
Edge computing 13%
Advanced integrated industrial safety, fail-safe technologies 12% Vision system optimization
All graphics courtesy: Control Engineering research, CFE Media and CFE Technology
of +/-6% at a 95% confidence level. Survey respondents were invited to anonymously provide their annual compensation information and opinions on the current state of their facilities and industries. To help update survey questions this year, on Feb. 17, ChatGPT artificial intelligence (AI) software was asked to provide “20 questions to help careers of control engineers and electrical engineers and mechanical engineers with automation, controls and instrumentation.” Two ChatGPT responses were among existing questions, and elements of three replies were edited and integrated into questions about skills, technologies and advice needed to get ahead.
As Figure 1 shows, 45% expect a salary increase of up to 3% in 2023 equal to 2022 (51% in 2021; 52% in 2020; 63% in 2019; 56% in 2018); 19% expect an increase of 4%
to 6% or more (up from 12% in 2022; 14% in 2021; 18% in 2020; 11% in 2019; 19% in 2018); 7% expect more than 6% increase (down from 10% in 2022); 28% expect the same (32% in 2022 and 2021; 30% in 2020; 25% in 2019; 23% in 2018); and 1% expect a salary decrease (1% in 2022; 3% in 2021; 1% in 2020 and 2019; 2% in 2018).
For base salary compensation, the minimum was $22,000 ($20,000 in 2022; $28,000 in 2021), and the maximum was $300,000, (up from $266,700 in 2022 and $250,000 in 2021), for 266 survey respondents providing this information in 2023.
For non-salary compensation (Figure 2), 29% expect and increase (26% in 2022; 23% in 2021); 14% expect an increase of 4% or more (same as 2022, up from 12% in 2021); 57% expect about the same (62% in 2022 and 2021); and 14% expect less (12% in 2022 and 15% in 2021).
For those receiving non-salary com-
Technical
Financial
Physical
Advancement
pensation (Figure 3), average received was $15,929, down about 17% from $19,162 from last year’s respondents. The 2023 average across all respondents was $11,518, compared to $12,838 in 2021 and $11,937 in 2020. In 2023, 21% received no bonus.
Two leading criteria for non-salary compensation were company profitability at 55%, about the same as last year; and personal performance at 43%, down from 49% in 2022 (Figure 4). Much farther down the scale were new business/sales at 23%, up from 17% last year; product profits at 19%, about the same as last year; plant or line productivity 17% about the same last year; quality metrics also 17%, safety metrics 13%, company stock also 13%; uptime/ downtime 11%; reducing plant costs 10% and customer feedback 10%, rounding out the double-digit replies.
Leading factors influencing job satisfaction for engineers were technical challenge, financial compensation, feeling of accomplishment, relationship with colleagues, flexible work hours, benefits, job security, feeling of recognition, workload, relationship with boss, ability to work from home, location, advancement opportunities and company financial health, filling out the double-digit replies. (Respondents were asked to rank the top three.) Figure 5 shows six more factors for job satisfaction.
For skills needed to get ahead, respondents were asked to check as many as apply. Engineering skills remained with a solid lead at 72%, down just a bit from 77% last year, followed by 62% project management skills, 61% communications/ presentation skills in a statistical tie. Computer skills dropped to 47% from 58% in 2022. Tying at 41% were team building and (new to the list of choices) system integration. Filling out double-digit replies were 21% marketing/sales, 18%
Lack
Lack
Inadequate management Competition
Regulations, codes, standards, etc.
Government/political interference
Energy costs
Lack of investments for equipment
Outsourcing, offshoring Downsizing
Lack of investments for workflow, manufacturing design
Don't know
language and 12% for finance/accounting. See related graphics in the next article, which highlights career advice from survey respondents, covering skills needed to get ahead and technologies likely to help. Materials and energy are less of a concern among respondents this year and economy and competition are more of a concern. The top three perceived threats to manufacturing, as mentioned, are 48% lack of available skills, 42% economy (31% last year), 30% lack of necessary materials (down from 42% in 2022), 23% competition (up from 14% in 2022), 18% inadequate management, 14% for energy costs (down from 20% last year) as well as government/political interference, regulation codes standards and taxes and tariffs, and 13% lack of investments for equipment and software upgrades (8% last year). (Figure 6)
Demographics help provide context for the numbers, and extra figures online provide more context.
Younger workers benefit from easier to use and optimize automation, controls and instrumentation as more experienced workers retire.
Among those taking the survey, 45% are 60 and older (up from 42% last year); 29% are 50 to 59 years of age (down from 32%), 15% 40 to 49 years of age (16% in 2022), 9% 30 to 39 years of age (up from 7%), 2% under 30 years of age (up from 1%), and 1% would prefer not to say.
Years working for current employer, 36% 9 years or less (down from 43%), 29% 10 to 19 years (up from 26%), 29% 20 to 29 years (up from 18%) and 15% were 30 or more years (up from 13%).
For more information, see this article online and download the Control Engineering 2023 Career and Salary Report.
CONSIDER THIS
On the next pages, see related articles offering advice on:
Advancement skills and advice
Workforce training
Women in engineering
How digitalization helps the workforce
Workforce skills
KEYWORDS: 2023 salary survey, career advice
Learn about key threats to manufacturing from the 2023 Control Engineering Career and Salary Survey.
Examine skills needed to advance in engineering.
Compare and benchmark your career progress with peers.
ONLINE
Benchmarking and link to the 2023 Control Engineering Career and Salary Survey and Report: If reading from the digital edition, click on the headline for benchmarking tables for more information.
www.controleng.com/magazine
www.controleng.com/research
https://www.controleng.com/system-integration/ workforce-development/#pillar-article-header
Highest level of education completed increased in master’s degree and decreased in bachelor’s degree respondents: 3% high school diploma, 4% trade/ technical school diploma, 8% associate degree, 10% college attendance, 39% had a bachelor’s degree (down from 48%), 30% had a master’s degree (up from 23), 2% dual bachelor’s degrees and 4% a doctoral degree.
Years in current industry: 9% 9 or fewer years; 14% 10 to 19 years; 24% 20 to 29 years; 30% 30-39 years and 23% 40 years or more. ce
Mark T. Hoske is content manager, Control Engineering, CFE Media and Technology, mhoske@cfemedia.com. Amanda Pelliccione, director of research and awards programs for CFE Media and Technology, conducted the research and assembled the related report.
Advice from the 2023 Control Engineering Career and Salary Survey included answers to artificial intelligent questions suggested by ChatGPT.
Advice about skills and technologies needed to get ahead in automation, control and instrumentation were among the advice 2023 Control Engineering Career and Salary Survey and Report. Two write-in questions asked survey respondents for advice. Among survey respondents, 89 offered advice on skills; 74 provided technology-related advice.
To help update survey questions this year, on Feb. 17, ChatGPT artificial intelligence (AI) software was asked to provide “20 questions to help careers of control engineers and electrical engineers and mechanical engineers with automation, controls and instrumentation.”
ChatGPT responses were integrated into the survey questions about skills, technologies and advice needed to get ahead. A sampling of each set of human respondent advice follows, lightly edited for style.
The question asked: Please provide advice about skills needed to get ahead in your areas of responsibility today (Figure 1), including how and why.
Stay aware of technologies and technology innovation. Keep up with certifications and skills training. Cybersecurity and artificial intelligence (AI) expertise are absolute.
Initiate goal-setting techniques. Encourage all employees to function as a production team. Freely support all employees who acknowledge performance-related operational techniques.
Learn the basics first. A good programmable logic controller (PLC) programmer should have strong knowledge of controls wiring and devices along with a basic understanding of tooling and design.
Troubleshooting is something that is constantly overlooked and needs to be addressed in this industry. That is why someone with experience should mentor people just coming into the industry.
Being able to communication ideas well to those above and below your position. Getting people to understand your ideas is one of the hardest tasks in industry today.
There seems to be an implied assumption an IT graduate can step into automation. Being able to work with software is only 30% of the job. Hands-on skills and familiarity with the actual automation components matters much more. Trade schools provide people who are better able to hit the ground running. They will learn the software as a part of doing the job.
Be able to travel. You will learn four times more in the field under production than in possible in the office.
First, AI and machine learning (ML)
All graphics courtesy: Control Engineering research, CFE Media and CFE Technology
‘
Continue improve your skills on how to do more with less. Automate to run more tests and make more improvements to processes with fewer personnel, less resources and less time.
’
have to be learned because they will lead technology transformation. Secondly, team building and soft skills must be mastered.
My current job is mostly project management, plus providing technical support for other teams. Team building and informal mentoring are the skills most used. Good relationships and effective communication are essential for big projects.
Training in problem solving and systems thinking. It is important to have mastery of your specialty, but also develop an awareness of other aspects of the project and product and how the fit together, even at the business level.
System simulation is critical to being able to design complex circuits and minimizing time required on bench prototyping and development.
Learn the applicability of AI and cloud computing in process automation. Many applications are going to the cloud and using AI. Getting familiar with how those technologies affect and/or are used in the industry will help those in automation and controls to stay up to date.
Develop leadership ability to keep the team motivated and optimize resources and productivity.
Keeping up with market knowledge and new trends help to offer products and services adapted to the client´s needs. Technical capacities enable abilities to offer innovative and creative solutions, maximizing the return on investment.
Hands-on experiences
Continuing education
Being mentored
Reading industry publications, sites, email newsletters, digital guides, vendor, research and association sites and materials
Networking at conferences, memberships in industry organizations, participation in standards bodies and other industry groups
Mentoring others
Search engines and online AI
Other
When asked to provide advice about technologies most likely to help in the next year (See table, p. 23), including how and why, answers included the following.
AI offers the greatest door-opening opportunities by being able to analyze and combine various datapoints and datasets to see opportunities, trends and areas to address.
Develop less complex and extensive data collection and reporting systems. Highly flexible systems can create an undesirable complexity that needs to be understood and is less helpful for most users.
Internet of Things (IoT) will help me to live and work smarter. IoT also enables the concept of a smart home to become a reality and to assist with a smart-city infrastructure.
Wireless communications is everywhere and is beginning to be introduced into older established technologies. The more you can understand, the more you can accomplish by moving existing products forward.
The need for Linux-based control systems will continue to grow for easier network convergence, data manipulation and reporting, integrated human-machine
interface (HMI), programmable safety and servo system control.
Digital controls for processes, advanced operating sequences and a high-level of feedback provides accuracy to the process being controlled. ce
Mark T. Hoske is content manager, Control Engineering, CFE Media and Technology, mhoske@cfemedia.com. Amanda Pelliccione, director of research and awards programs for CFE Media and Technology, conducted the research and assembled the related report.
controleng.com
LEARNING OBJECTIVES
Learn from automation skills advice provided by peers taking the 2023 Control Engineering Career and Salary Survey.
Discern applicable advice from peers about technologies needed to advance in engineering.
CONSIDER THIS
What automation, controls and instrumentation skills and technologies are you cultivating to advance competitiveness?
ONLINE
See 2022 salary survey advice. https://www.controleng.com/articles/ career-salary-survey-2022-engineering-advice/
A
controls engineer for a system integrator said he enjoys frequent learning while developing and commissioning PLCs, HMI and SCADA systems.
As controls engineer for a systems integrator, I develop programmable logic controllers (PLCs), human-machine interfaces (HMI) programs and commission for new sites or additions, develop supervisory control and data acquisition (SCADA) systems, develop network architectures, troubleshoot existing controllers, and commission on customer sites.
Industries typically include food and beverage facilities, especially pistachio processing, however, I’m currently working at an oil and gas extraction and processing facility. Deliverables are diverse and can be industrial control panel fabrication, electrical control and power distribution design, and electrical conduit and cable installations. Modifications or troubleshooting of a control system beyond our technicians’ abilities is what I’ll work on, as well as on new site commissioning for controls and automation.
Control panel fabrication
I started out in my company’s panel fabrication shop after graduating with my bachelors in electrical engineering. I wanted to get an understanding about how to actually build a control system so I could understand the equipment I’m working with and work on them in the field, if necessary. After a year in the shop and becoming the foreman for a short time I moved into controls engineering, which I have been doing for three years.
The best part of my job is the ability to learn something new almost all the time. I’m fairly new to the career, but in that time, I’ve
CONTROL PANEL:
Ian Ives, control engineer at JTI
Electrical & Instrumentation LLC, began in the JTI panel fabrication shop, then advanced into controls engineering. Courtesy: JTI Electrical & Instrumentation LLC
learned how to be effective with hand and power tools, how to design, develop, and commission technologies that have a large impact on my community. Each time I learn something new, I find more details to delve into, such as how types of wired networks like copper, coaxial, and fiber can coexist and the constraints of each network type.
The most challenging part of the job is the travel. I’m a homebody and enjoy being with my family, but you travel where the jobs need you to be. I love seeing new places and people, but after a month or two I need to be home to breathe easy.
Work includes upgrading controllers from Rockwell Automation, Allen-Bradley PLC-5s, SLCs, and end of life CompactLogix controllers, and in-service controllers, along with creating or modifying SCADA systems. Supply chain issues has created some constraints on some projects. The supply chain has been rough on everyone worldwide. Everyone wants systems that increase production or gather more data for analytics or replace parts more quickly. It
doesn’t appear to be easing up soon. Useful tools include a Linux virtual machine for troubleshooting networking issues when commissioning new sites, to help see network traffic when commissioning or testing intrusion detection systems.
In my first job, I worked with a lead controls engineer and did some programming for edge-ofnetwork actuators, like remote pumps, and that taught me quite a bit. Learning by doing and working with the lead engineer (letting me make mistakes without damaging anything) really helped. Areas of interest include industry trends and case studies, especially industrial Internet of Things (IIoT), cybersecurity and networks; because I’m interested in how they will change future work. ce
Ian Ives is control engineer at JTI Electrical & Instrumentation LLC; Edited by Mark T. Hoske, content manager, Control Engineering , CFE Media and Technology, mhoske@cfemedia.com.
controleng.com
KEYWORDS: System integrator, PLC, HMI, SCADA
Work includes developing and commissioning PLCs, HMI and SCADA systems
Advice: Involve younger people throughout. CONSIDER THIS
How are you mentoring younger engineers? ONLINE
With this article, see more on working with young people.
Also see: https://www.JTIelecttric.com
Companies that make, design or package something likely have engineers on the payroll. The same goes for those companies traditionally thought of as being highly technical, mechanical or automated. Industrial automation and the factory floor has implementers, integrators and process designers; often the behind-the-scenes teams need to know and learn much of the same information that engineers and technicians understand.
Onboarding is more than filling out forms (the average new hire is assigned 41 administrative tasks to complete). It’s about processes, responsibilities, cultural fit and training. Training is one of the most successful elements of any onboarding program, for productivity and employee retention. A report by LinkedIn, a Microsoft Corp. company, said 94% of employees would potentially stay longer with a company that invests in learning and development. Despite corporate training being regarded as an important tool for employee retention, companies need to overcome challenges associated with facilitation and completion. Employees do not have much
time to spend on learning and development. One report said the average employee only has 24 minutes a week to spend on learning. This might explain why 60% of workers embarked upon their own skills training, highlighting an unmet appetite in the workforce for greater knowledge. Online learning raises retention rates by 25% to 60%.
Cost is another training challenge. Organizations spent $1,296 per employee on learning. The argument could be made that the cost of not training your employees is even higher. Every penny spent on online training leads to a $30 increase in output. In a survey of 2,500 companies, those with “comprehensive training programs” have a 218% higher revenue per employee and a 24% higher profit margin. Untrained employees take up to six times longer to perform the same task as trained employees.
“There is a direct correlation between effective onboarding and employee retention and engagement,” said Susan Vitale, chief marketing officer for iCIMS, manufacturer of talent acquisition software. "Ninety-one percent of [first-year] employees are retained in companies that have a formal onboarding program, but of those who don’t, just half are retained.” Courtesy: Real Time Automation
With this article online, see 2 more pages of content, and 22 sources for materials cited in this article.
Three ways to improve engineering retention https://www.controleng.com/articles/ three-ways-to-improve-engineer-retention Online controleng.com
Training should be an important part of an employee’s first few months, especially for non-engineering positions in highly technical industries. All the statistics mentioned previously are compounded by the shallow learning curve these positions tend to experience, making it even more imperative for those companies to provide comprehensive, longer-term training as part of their employee development process.
“We have asked ourselves: How could it be better,” said Katie Schaaf Klinzing, director of support at Braintree. “We turn this question on our new hires because we’ve learned that our best source of insights into how to set them up for success is to ask.”
For employees taking on non-engineering positions in highly technical industries, ensuring reasonable, mutually understood expectations are in place prior to starting, and having access to extensive training after starting should be part of the decision-making process to ensure success today, tomorrow and beyond. ce
Pat Lafferty, marketing copywriter, Real Time Automation. Edited by David Miller, content manager, Control Engineering, CFE Media and Technology, dmiller@cfemedia.com.
Digital telecommunication evolution has been rapid over the past several years and is providing near real-time communication.
Digital technologies have evolved in the past 20 years, and things that were unconceivable a couple of decades ago, right now are being adopted and taken as common standards. Telecommunications, computing hardware, integrated circuits miniaturization, cloud computing, machine learning, advanced analytics, cryptography and other related technologies are evolving, providing more functionality at affordable costs.
Digital telecommunication evolution has been rapid. 5G wireless communication provides super-high speeds and huge bandwidths on mobile or static devices. Multifrequency fiber-optic cables installed everywhere provide ultrahigh-speed data highways globally, which provides near-realtime video communications across nations including the ability to stream high-definition movies. The expansion of the telecommunications system will continue.
Hardware miniaturization and new chip manufacturing techniques are bringing us cheaper, faster, smaller and power-efficient computing devices that we may deploy pretty much everywhere, in appliances, in the field, or clustered in high-performance cloud computing arrangements. Along with the telecommunication explosion, computing capabilities are elastic and ubiquitous and becoming almost limitless.
Machine learning (ML), deep learning, cryptography and other advanced algorithms can be implemented in computing systems and also into small intelligent devices, providing immense insights
and value. All of this is possible due to the evolution of telecommunications networks and computing hardware.
While digital technology has exploded, major new challenges are arising. People are more connected and demand more information to be delivered in real time. Industries run analytics, markets are very fluid and split-second business decisions must be taken. There is a very close relationship between technological evolution and upcoming challenges.
‘New system architectures for automation can help new industry operational and business challenges.’
Automation has taken advantage of these technological bursts. We see more sophisticated devices, intelligent wireless instruments, powerful programmable logic controllers (PLCs), edge computing devices, supervisory control and data acquisition (SCADA) and distributed control systems (DCS) and historians, running in huge servers or in cloud computing environments, serving users on workstations, tablets and other portable devices. Even with the advances in telecom and computing technologies, automation architectures have not changed much. While many components have advanced, underlying architec-
tures have largely remained the same.
The oil and gas industry has traditionally been conservative in terms of technology adoption, due also to the fact that it faces specific challenges that are different from other industries. Nevertheless, as technology evolved, operations have become more complex, markets are more volatile, competition is fierce, and environment and sustainability plans and issues must be addressed.
This industry is fully realizing the value of technology in the current operating environment. Hydrocarbons are getting harder to produce, operating margins are shrinking, more restrictive environmental regulations are in place, and safety policies demand less exposure of personnel to field conditions. All these developments are pushing this business not only to broadly implementing more automation and digitalization solutions, but also to adopt new advanced system architectures that best solve the actual and upcoming operational and business challenges in this industry.
Classic automation architectures are failing to keep up with the new challenges that the industry is facing. New system architectures for automation should be adopted that better fit with new industry operational and business challenges.
Identified below are system architectural paradigms that have been successful in other computational architectures but overlooked by automation.
1. Flatter architecture: Even when
new automation systems are currently using updated technology, their architectures are too vertical. Field devices, connected through a telecom infrastructure to SCADA/DCS, then tied to a historian, then connected to applications and business intelligence systems, in a sort of a totem fashion, raise problems by having diverse user interfaces, many interfaces among layers and the use of multiple databases (Figure 1). New architectures must be flatter, with fewer database layers and less interfaces among levels. The entire system should be based on a unified digital platform that includes most of the functionality in fewer levels (Figure 2). This digital platform must also be flexible enough to leverage on existing instruments, automation devices, and systems as much as possible.
2. High availability and fault tolerance: Some automation systems still adopt the classic warm-standby configuration. The user buys two systems just to use one, in case the system that is running fails. Automation architectures can improve by incorporating new fault-tolerant schemes, which automatically adapt in case of failure of one of the hardware components, with minimal or no failover time.
3. Elastic: In a corporation, business and operations scenarios may suddenly change and automation architectures
must quickly adapt to those changes. Traditional architectures are rigid, resistant to changes. New architecture must quickly expand as business expands or shrink if business requires. It must be elastic to quickly expand or contract within minutes and without losing operativity.
4. Secure from the ground up: Cybersecurity must not be a layer installed on top of a classic automation system architecture. An automation architecture must incorporate cybersecurity mechanisms from its conception, adopting cybersecurity strategies like the zero-trust architectures (ZTA) approach from its early design stages. Potential cyberattacks over automation systems that are controlling critical assets (in either industry) represent a clear danger that must be properly addressed by the new architectures.
5. Single point of configuration: In current practice, as shown in Figure 1, adding a new field device or making a configuration change must be done on each one of the layers to maintain system integrity. New architectures must adopt a “configure-once” design. By installing a new device or changing its configuration, changes must be automatically made through the system.
6. Push intelligence as low in the architecture as possible: “Dumb” remote terminal units (RTUs) or limited-function PLCs are part of the past. Data sponging, ana-
lytics, smart processing, machine learning (ML) and artificial intelligence (AI) must be done as closely as possible to the process. Edge devices can take on a good portion of the processing on new architectures. Automation system design paradigms have changed. New technology is available, but new business and challenges have emerged. Design, develop, implement and deploy automation systems based on these new paradigms to help solve industry operational challenges with a faster and better return on investment (ROI). ce
Mario Torre is digital architect at Sensia (a JV of Rockwell Automation and SLB). Edited by Chris Vavra, web content manager, Control Engineering, CFE Media and Technology, cvavra@cfemedia.com.
KEYWORDS: digitalization, digital architectures
LEARNING OBJECTIVES
Learn about the challenges that have come with the rise of digital technologies.
Understand six architectural paradigms and how they affect operations, provide benefits.
CONSIDER THIS
What role are digital technologies playing in the evolution of your business?
ONLINE
https://www.controleng.com/digital-transformation
A “Women in Manufacturing” event is one way Jane Addams Resource Corp. helps increase the number of women in industrial careers; JARC offers free training.
Arecent “Women in Manufacturing” event organized by Jane Addams Resource Corp. (JARC) is among ways the organization highlights and encourages women (and other under-represented groups) to train for and excel in skilled manufacturing jobs, including workplace safety, print reading, metrology, statistical process control, geometric dimensioning and tolerances, 3D printing, G-code programming for computer numerical controls (CNC) and welding processes. JARC specializes in urban workforce development and supports healthy communities and economies by teaching low-income adults and workers the skills to earn a living wage.
At the event, Regan Brewer Johnson, JARC president, provided an on-screen welcome to speakers and guests. She said working people should not live in poverty; JARC and its supporters provide training, especially in struggling communities, so workers can get better-paying jobs with benefits.
Chicago Alderman Emma Mitts said women no longer have to take the back seat because of help from JARC free training and life-skill programs that provide pathways to higher-paying manufacturing jobs with benefits.
“The world is open. Get up and get
uJane Addams Resource Corp. (JARC) provided statistics on 873 program participants between Sept. 1, 2017, and Aug. 31, 2022:
u73% from the black, Indigenous and people of color (BIPOC) community
u 32% women
u 27% Latinx
u87% of those who began JARC’s Bridges to Careers Opportunities attained one or more industry-recognized credential (such as welding, CNC, safety)
u 9 of 10 clients reported at least one positive financial outcome.
courage together. We have to tell young people to get skills and training.” Many opportunities are available with appropriate training and skills, she added; traditional barriers have been removed.
Tammy Phillips, president and CEO of Howe Corp. and chair of the JARC board of directors, said the opportunities have never been greater to improve manufacturing employment diversity, equity and inclusion. She said great pay and benefits are available in rewarding careers with paths for advancement.
The event also included tours of the Freedman Seating Co. factory and the JARC Training Center on-site, which is one of two JARC training facilities in Chicago. JARC recently expanded reach from locations in Chicago and Baltimore to Providence, Rhode Island. ce
Two award-winning graduates (left) of Jane Addams Resource Corp. training discussed how their lives significantly changed with higher paying manufacturing careers with benefits, part of a recent JARC Women in Manufacturing event. On the right, Danielle Hoske, JARC director of development, data and communications, helped organize event and served as moderator. Courtesy: Mark T. Hoske, Control Engineering, CFE Media and Technology
Mark T. Hoske is content manager, Control Engineering, CFE Media and Technology, mhoske@cfemedia.com.
controleng.com
With this article, see more details about these programs and more photos.
https://www.controleng.com/system-integration/ workforce-development https://www.jane-addams.org
Although engineers are renowned and valued for technical skills and industry expertise, people skills are essential to excel in the profession.
I began my career as a mechanical engineer writing custom inspection routines for coordinate measurement machines. And as I transitioned from a working engineer into project management, sales, and now leading a product marketing team, I learned emotional intelligence is as important as logicalmathematical intelligence in the workplace — mostly because the workplace is filled with a lot of other people.
Experience has taught me engineers skilled in communication and collaboration are more successful in their careers and can better promote growth and innovation in their organizations.
Developing people skills can seem challenging, but anyone can do it, and it is
critical for professional development and long-term success. Here are some key areas to focus on to improve people skills.
Why this is important: Engineering professionals often work on teams comprised of people from diverse backgrounds with different technical capabilities. It’s essential to be able to communicate technical information effectively to both experts and those without any technical knowledge — and it is easy for engineers to appear arrogant if they do not adapt their communication style to fit their audience.
Tips for effective communication: Whether you’re an engineering student or an experienced engineer, practice is the key to improvement. Joining a club or attending after-hours social activities with colleagues are great opportunities to practice your communication skills.
RILEY HALL is the director of product marketing for Fictiv, explains five ways engineers can improve their people skills. Courtesy: Fictiv
Why this is important: Creating strong working relationships with co-workers not only helps you become a happier human, but also benefits teamwork and builds trust. Forging good relationships helps you grow in your career and provide a more positive working experience.
Tips for building relationships: Mostly, building relationships is about paying attention to the people around you and showing you genuinely care about them. Ask your co-workers about their interests. Be respectful. Learn about the important people/ dog(s)/cat(s)/other animal(s) in their life, if they’re willing to share. Listen first, talk second. Practice active listening. Be honest.
KEYWORDS: Engineering people skills
LEARNING OBJECTIVES
Understand that engineers do better when they improve their people skills.
Review five ways to improve people skills if you are in engineering.
CONSIDER THIS
Relating the value of what you have engineered adds value to the engineering.
ONLINE
https://www.controleng.com/system-integration/ workforce-development/ Online controleng.com
Listen to others and learn about them. How do they communicate? What are they into? See if you can explain a concept or theory to someone new, someone not familiar with the idea, but interested in it — teaching others cannot only solidify and broaden your knowledge, but also spark a good conversation.
If they ask questions or say they don’t understand, consider their point of view. Is there a different way to articulate your point that’ll make more sense to them? Ask if they’re familiar with the topic, then try to tailor what you say based on their level of interest and previous experience.
Why being a team player is important: With remote work becoming more commonplace, building strong communication and collaboration habits are more important than ever to creating a high-functioning virtual or hybrid office. People from all different departments, backgrounds, and locations appreciate a positive attitude, and teams that treat each other with respect do the best work. Remember, your ideas aren’t always the best ideas, and maintaining humility and listening to others are critical components of highly effective teams.
Tips for being a team player: Positive attitudes and kindness are contagious. Be supportive, honest, and respectful to your team members. When a co-worker is (Continued on P2, prior to p. 44)
Paul Avery, Yaskawa America
For machine control and other applications, controlling motor speed with variable frequency drives (VFDs) can save energy, but it’s not as easy as just adding a VFD. What else needs to be considered for motor control system efficiency?
Besides the many other features on a modern variable frequency drive (VFD), the simple ability to run an AC induction motor at speeds other than 60 Hz is a very wonderful thing.
By slowing the motor down to meet the demand of the application, a VFD reduces the power required to keep the load moving. Power usage over time equals energy, so the bottom line is that a VFD saves energy by not running at full load.
Most people are already familiar with all the information in the previous paragraph, so maybe using a
VFD isn’t up for debate. Assume instead that the VFD purchase has been made already. But is that all there is to properly using a VFD to save money? Like most things in life, it’s slightly more complex than that. How can a VFD be optimized for energy savings?
A brief discussion of a proper VFD installation is needed, first. No one saves money through energy cost reduction if a VFD blows up or melts down after improper installation. Many VFD manufacturers are happy to offer extended warranties on products if they are installed and wired by people that they have vetted or factory trained. (As a factory trainer myself, I emphatically endorse using installers that have been sent to the factory to practice and learn all the ins and outs of proper VFD installation. Training includes many different scenarios to provide the experience needed to avoid pitfalls.)
FIGURE 1: Proper torquing of power wiring done by a certified installer is one of the steps that help the drive’s lifespan and increase VFD return on investment. Images courtesy: Yaskawa America
Proper installation can avoid problems and short VFD lifespans. A good installation technician will notice environmental issues that can lead to premature VFD failures like high ambient temperatures, long motor lead lengths and power factor correction capacitors. If an early demise can be avoided, some VFDs can last a very long time, making the return on investment (ROI) very high indeed.
By itself, the VFD can be integral to energy savings but the drive is only one part of the whole installation. The two other parts that matter the most are the motor driving the load and the cable connecting the VFD and the motor.
The motor is probably the more important of the two items. First, make sure that the motor is up to the job of handling the pulse-width-modulation
2: An output reactor is sometimes necessary for a VFD installation.
(PWM) voltage that the VFD will be sending it. Some older motors, besides being inefficient, were manufactured with inferior insulation systems that may not be able to handle the voltage created by a VFD and exacerbated by a long motor lead. Generally, any application that has motor leads over 100m should consider an output reactor between the motor and VFD to help protect that first turn in the stator (where the insulation is thinnest) from failing. Like many things, there is a tradeoff to be considered. Any kind of output filtering, like that load reactor, will come with its own losses. However, the slight decrease in efficiency is worth the extended life of the motor.
Another motor consideration is the size. Applications need a motor capable of continuously delivering the torque that the load requires. A properly sized motor is preferable to an oversized motor. An under-loaded motor can suffer from a poor power factor which greatly decreases the efficiency of the whole system. Address this tradeoff. An oversized motor might provide peace of mind that the system will not fail any time soon since heat losses in all of the components are well below their thresholds, but the properly sized motor will be more efficient. If correctly selected and installed, the properly sized motor also will live a long life, so the tradeoff is heavily weighted towards the properly sized motor. For new installations, the motor selected will most likely be very efficient due to government regulations regarding motor efficiencies. Generally, the closer the rated speed of the motor is to the synchronous speed, the more efficient the motor is. To optimally run a motor, a VFD needs an accurate value for the motor’s rated slip. A good auto-tune done by the VFD while attached to just the motor can yield a very good value for motor slip. See more on auto-tuning later and how it applies to VFD control methods.
Motor cable considerations generally relate to the cable length and gauge. The proper cable gauge should be found by consulting the VFD manufacturer’s installation documents. As mentioned earli-
FIGURE 3: A dv/dt filter will sometimes be necessary in VFD applications with very long motor lead lengths.
er, long lead lengths can actually lead to premature motor failure unless precautions are observed. Large changes in impedance can cause a point of reflection for the PWM pulses (with their corresponding high dv/dt values) coming from the VFD. It is not an all or nothing thing. The greater the difference in impedance, the more of the pulse is reflected. Sometimes the only fix is to dampen the steep dv/dt of the pulses through filtering. Again, the filtering components come with their own set of energy losses and additional installation costs.
To get the best torque per amp performance out of a new VFD, a proper auto-tune is needed. An effective auto-tuning routine for a VFD will help the drive build a good motor model in the VFD. From the factory, the drive is most likely set up for a typical motor that matches the VFD size. That means that the rated motor amps value in the VFD will be based on NPPA 70: National Electrical Code (NEC) values for a motor of that voltage and horsepower. On top of that, the motor model will require values for expected losses in windings and magnetic fields. Values like losses are rarely specified on the motor nameplate. These loss values are named things like “Line to Line Resistance (Ω)” and “Leakage Inductance (%).” It is probably best left to the VFD to run its own tests on the motor after some of the typical nameplate values are input to the drive. The end result will most definitely show a reduction in output current while running the same speed and load as the pre-tuned motor. It is highly recommended that the auto-tuning function be run on a motor without any load attached. An
FIGURE 4: An auto-tune operation for a new drive installation is simple and will lead to more efficient control of the motor.
controleng.com
KEYWORDS: VFD, energy efficiency
LEARNING OBJECTIVES
Learn how using proper VFD installation techniques can maximize energy savings. Understand how pairing the proper motor and cabling with a VFD can optimize performance.
Hear how training your VFD on fluctuating loads can help increase efficiency.
ONLINE https://www.controleng. com/articles/ vfds-from-the-inside-out CONSIDER THIS What techniques can you apply to maximize the performance and efficiency of your VFD?
FIGURE 5: Having the VFD stop during times of low demand can help with energy savings.
‘ Improve VFD efficiency by training it howto deal with application situations where the load fluctuates.’
attached load will skew the current and slip measurements. It is also preferable that the auto-tuned motor’s internal temperature is close to its normal running temperature due to resistance changing with temperature.
u
VFD performance
uUsing installation technicians that have been vetted or factory trained can substantially increase the lifespan of a VFD.
uWhen installing a VFD, paying proper attention to the motor that drives the load and the cable connecting the VFD and the motor are integral to ensuring optimal performance.
uGetting the best torque per amp performance out of a VFD also requires that end-users perform a proper auto-tune.
Another way to help a VFD get the best efficiency out of the application is to train it on how to deal with situations where the load fluctuates. During operation at low loads, decreasing the output voltage to an optimal point can help minimize power consumption and maximize efficiency. An energy savings mode in a VFD can help maximize the efficiency, especially for V/Hz applications seen in fans and pumps. It can be helpful to think of energy savings as the inverse of torque boost. One increases the voltage from the normal levels to increase the output torque, and the other decreases the voltage to minimize power usage, resulting in a more efficient use of energy.
Sometimes it may be necessary for the VFD stop running if the load becomes too low. This is referred to as sleep. It is called sleep because despite the drive output turning off, the VFD remains in a run state and monitors to see if the conditions of the applications warrant waking up to start driving the load again. This type of operation is common on pumping applications where the demand on the
pump can change based on usage or time of day. The VFD will need to be programmed with what states (such as running at a minimum speed or outputting too low of a pressure) will need to occur to cause the drive to go to sleep or wake back up.
A final energy savings possibility relates to what is colloquially called “vampire power.” It refers to the power that devices draw even when they are not turned on. Consider an LCD flat-panel TV. Even when it’s not “on,” a certain residual power is drawn. Maybe it is not enough power by itself to warrant concern, but consider how many devices in are also drawing power while they are off. Then, multiply that by all the houses and businesses in the world, and concern accumulates. The same principle applies to VFDs. Even when the VFD is not running, it is drawing some current in through its rectifier and bus capacitors. Some manufacturers have created a function that uses a small DC power supply to keep the VFD “brain” alive while opening up an input breaker when it has not been running for a long enough time. Because the brain still has power, it can close the input breaker whenever a new run command is received. Maybe a single drive’s non-running power draw does not warrant the extra equipment, but what if you have 50 or 100 VFDs? The power waste could be significant.
A VFD by itself can be a big win for energy savings due to its ability to match motor speed to load demands. However, there are other factors such as motor sizing, cable selection, auto-tuning and energy saving functions that should also be considered to maximize those energy savings. ce
Paul Avery, senior product training engineer, Yaskawa America. Edited by David Miller, content manager, Control Engineering, CFE Media and Technology, dmiller@cfemedia.com.
Thomas Burke, CC-Link Partner Association (CLPA)
time-sensitive networking (TSN) gives users a secure and accurate way to communicate within industrial control systems (ICS) with interoperability.
Ethernet time-sensitive networking (TSN) is a set of IEEE standards that provides deterministic real-time communication over Ethernet networks. It provides a reliable and low-latency network infrastructure for industrial control and automation systems, enabling real-time communication among devices in a network. Ethernet TSN offers several benefits for manufacturers, such as improved network performance, increased network flexibility and extended benefits for industrial communications.
Ethernet TSN provides deterministic communication, which means network traffic is delivered with a guaranteed latency and jitter. This is achieved by time-scheduling network traffic and reserving bandwidth for critical traffic. In traditional Ethernet networks, traffic is delivered on a best-effort basis, which can lead to unpredictable latency and jitter. This unpredictability can be problematic for real-time communication applications, such as control and automation systems, where timely data delivery is critical.
Ethernet TSN provides several mechanisms to achieve deterministic communication. One is timeaware shaper (TAS), which enables the prioritization of traffic based on the time-criticality of the application. TAS uses a time-based scheduling algorithm to ensure critical traffic is delivered with the required latency and jitter. This mechanism enables Ethernet TSN to provide low-latency communication, which is essential for real-time applications.
Ethernet TSN provides increased flexibility through use of time-scheduling and reservation mechanisms. These enable different types of traffic to be prioritized and allocated bandwidth according to their requirements. This flexibility enables Ethernet TSN to support a wide range of applica-
tions with varying communication requirements.
Ethernet TSN provides support for multiple traffic classes, which enables different types of traffic to be treated differently. Voice traffic can be given higher priority than data traffic, ensuring voice communication is not affected by network congestion. This flexibility is essential for applications where different types of traffic have different requirements.
Ethernet TSN provides support for quality of service (QoS) mechanisms, which enables traffic to be allocated different levels of service. QoS mechanisms enable traffic to be prioritized based on parameters such as bandwidth, latency and jitter, ensuring traffic is delivered with the required level of performance. This flexibility enables Ethernet TSN to support a wide range of applications with different performance requirements.
Ethernet with TSN is extending the benefits of already-popular standard Ethernet with standardization, scalability, high-performance capabilities and interoperability.
Leading vendors have created a consortium called the TSN Industrial Automation Conformance Collaboration (TIACC). Avnu, CC-Link Partner Association, ODVA, OPC Foundation and Profibus International (PI) have collaborated to develop one conformance test plan for the IEC/IEEE 60802 profile of TSN for Industrial Automation. The organizations seek to provide end users with confidence IEC/IEEE 60802-compliant devices will coexist at the TSN level on shared networks regardless of differences in manufacturers or automation protocols. ce
Thomas Burke is Global Strategic Advisor at CC-Link Partner Association, a CFE Media and Technology content partner. Edited by Chris Vavra, web content manager, Control Engineering, CFE Media and Technology, cvavra@cfemedia.com.
controleng.com
KEYWORDS: Ethernet, timesensitive networking, TSN LEARNING OBJECTIVES
Understand the benefits of Ethernet TSN for manufacturers.
Learn about TSN network flexibility and the ways it can help companies be more agile.
Learn how organizations are collaborating to make Ethernet TSN more useful. ONLINE
See more benefits with this article online.
https://www.controleng. com/industrial-networking/ ethernet/
CONSIDER THIS
What benefits can Ethernet TSN provide your facility?
David Miller, Control Engineering
Al Beydoun, president and executive director of ODVA, in a video discussed how SPE and APL will change industrial networking.
“SPE minimizes hardware requirements by allowing for usage of smaller physical interfaces, which makes it cost effective to connect to simple devices. Additional device connectivity opens up possibilities for diagnostics along with development of prognostics,” said Al Beydoun, president and executive director of ODVA.
Many used to doubt that industrial Ethernet could ever take the place of legacy fieldbus on the plant floor. Prior to the rise of deterministic Ethernet communication protocols such as EtherCAT (EtherCAT Technology Group), EtherNet/IP (ODVA), and Profinet (PI North America), Ethernet simply wasn’t capable of accommodating the extremely rapid cycle times mandated by complex motion control applications, which often require control-loop updates take place within milliseconds to function properly. However, with these issues solved, Ethernet has increasingly become the preferred industrial network, particularly in discrete manufacturing.
Still, despite the rise in preference for industrial Ethernet networks, many fieldbus installations remain in place, particularly in the process industries where the shift to Ethernet has been more challenging. One of the reasons for this is that longer cable runs are often needed in large, outdoor environments common to some process industries. With typical industrial Ethernet being limited to a maximum length of 100 meters to prevent signal decay, this can present an issue.
Moreover, with many process industry applications taking place in areas classified as hazardous zones and divisions by the National Electric Code, costly safety measures that require specific expertise must be undertaken to ensure Ethernet cabling and connectors will not ignite a flame.
Enabling longer Ethernet cable lengths, hazardous-area installations
Single-Pair Ethernet (SPE) and Ethernet
Advanced Physical Layer (APL) are recent innovations in Ethernet’s physical layer — the first tier of the Open Systems Interconnection (OSI) model — may help to surmount these obstacles.
In a recent Control Engineering video interview, Al Beydoun, president and executive director of ODVA, shared more information about the benefits SPE and Ethernet APL can offer endusers. View the video via the link in the online box below. ce
David Miller is content manager, Control Engineering, CFE Media and Technology, dmiller@cfemedia.com.
KEYWORDS: Online Text online text
Understand the key technical benefits and trends driving the move to SPE and Ethernet APL technology.
Learn the specific application areas where SPE and Ethernet APL will be most beneficial.
Understand how SPE and Ethernet APL will help automation and control engineers.
CONSIDER THIS
Could SPE and APL facilitate IT/OT convergence in your operation?
ONLINE
See the related video here: https://www.controleng.com/articles/video-interview-benefitsand-applications-for-spe-and-ethernet-apl
Daniel E. Capano, Gannett Fleming Engineers and Architects
Do you debate risks vs. cost of cybersecurity technologies, processes and training? Maersk estimated NotPetya costs at $250-300 million.
In 2017, one of the most widespread and devastating cyberattacks was perpetrated against worldwide shipping giant Maersk. It started on a quiet afternoon in June, when staffers began seeing messages advising them that their file systems were being repaired, while others received the message that their important files had been encrypted. A payment of $300 in bitcoin was demanded for the encryption key.
This set off a panic in Maersk headquarters; entry systems and phone networks had been rendered useless by the apparent malware spreading rapidly throughout the company’s network and beyond. By the end of the day, their networks had been so deeply corrupted that the company simply shut down. This was no small feat, however; Maersk is a global shipping titan, responsible for 76 ports around the globe, more than 800 vessels carrying all manner of goods and about one-fifth of global trade. This entire enterprise was brought to its knees by a mystery malware that had spread to every Maersk location across the globe, and Maersk wasn’t even the target.
Since 2012, Ukraine and Russia had been slugging it out in an undeclared war that served as a proving ground for Russia’s cyberwarfare tactics. A group of Russian hackers called Sandworm had thoroughly compromised the Ukrainian government and dozens of Ukrainian companies. The attackers were firmly entrenched in the networks and systems of the most vital and critical infra-
structure in the country. Among the atrocities perpetrated at the behest of the Russian government, Sandworm installed malware in the power grid, which was periodically activated to do the most damage and demoralize the populace. A perfect example of this was shutting down the grid in the middle of the winter. Massive amounts of data were destroyed outright in a series of malicious attacks on Ukrainian businesses, particularly banks.
One way the Russians were able to apply such a broad and sweeping campaign of destruction was through the compromise of the Linkos Group, a small software firm that markets an accounting software package called M.E.Doc. This software was used by nearly everyone who did business in the Ukraine and gave Sandworm a vast attack surface to work with. Sandworm ad hijacked the firm’s update servers early in 2017, and this gave them back-door access to the thousands of computers running M.E.Doc.
That June, Sandworm released a particularly vicious cyberweapon called NotPetya, which spread rapidly and automatically. The code was indiscriminate in whom it attacked; it was designed to do the largest amount of damage as quickly as possible and with the widest swath of destruction. The ransomware spread so quickly and effectively that once the message popped up on a screen, the damage was already extensively complete.
NotPetya was comprised of two major elements: a penetration tool called EternalBlue, created by the National Security Agency (NSA) and leaked in early 2017, and Mimikatz, a software application that had the ability to pull user passwords out
KEYWORDS: Industrial cybersecurity
LEARNING OBJECTIVES
Understand malware’s rapid, indiscriminate spread.
Weigh the costs versus benefits: This attack’s cost estimates for Maersk was $250 to $300 million; costs for all companies were estimated at $10 billion total. Review preparedness and recovery efforts.
CONSIDER THIS
When justifying cybersecurity investments, does your company use specific costs?
ONLINE
https://www.gannettfleming. com/
Published by Industrial Cybersecurity Pulse, Sept. 30, 2021.
https://www. industrialcybersecuritypulse. com/threats-vulnerabilities/ throwback-attack-hownotpetya-accidentally-tookdown-global-shipping-giantmaersk/
of RAM and reuse them to compromise targeted machines. While Microsoft had issued a patch for EternalBlue, Mimikatz allowed for the retrieval of passwords, which, in turn, allowed those passwords to infect unpatched machines anywhere in the world.
‘ The code was indiscriminate in whom it attacked; it was designed to do the largest amount of damage as quickly as possible and with the widest swath of destruction.’
The origin of the name — called NotPetya by Kaspersky to differentiate it from the Petya strain is also an indicator of the intent of its designers. Petya is a ransomware package that was used to extort money from compromised users in exchange for a decryption key. NotPetya was not “legitimate” ransomware; its intent was purely destructive. Any ransom payment was wasted. There was no decryption key for the destroyed data. Sandworm had targeted only Ukraine with NotPetya, but the effects achieved affected the entire world.
Within hours of NotPetya’s release, the malware had raced around the world and infected countless computers. Victims included FedEx’s European subsidiary, TNT Express; several French companies; a hospital in Pennsylvania; the pharmaceutical company Merck; and, of course, Maersk. The radiation monitoring system at the Chernobyl Nuclear Plant went offline. The infection even spread back
uMaersk estimated that NotPetya had cost the company between $250 and $300 million.
uTrucking companies lost tens of millions of dollars.
uTNT Express lost about $400 million.
uMerck lost $870 million.
uGlobal costs were estimated at $10 billion.
to Russia, corrupting state oil company Rosneft. The attack resulted in damages of about $10 billion.
“It was the equivalent of using a nuclear bomb to achieve a small tactical victory,” said Tom Bossert, White House homeland security advisor at the time. It was completely reckless to a degree that should not be tolerated by the community of nations. This was cyberwarfare at its worst, where a nation-state exploits the lack of national borders on the internet and has a callous disregard for human life. What amounted to a political attack on a rival state became an attack on the rest of the world. The strike was aimed at Ukraine, but also hit Maersk, which, in turn, affected the rest of the world.
The back door Sandworm exploited had existed for several weeks in Linkos’ servers prior to activation of the attack. Linkos denied they were the perpetrators of the attack, complaining that they were also victims. In July 2017, Ukraine’s cybercrime unit seized servers from Intellect Services, the company that produces the M.E.Doc software.
Analysis of the servers showed that they had not been updated for at least four years, and security patches were nonexistent. There was evidence of Russian presence in the servers, and several employees’ accounts had been compromised. Intellect Services subsequently closed the back doors into the software, and state prosecutors promised the company would be held to account for the vast damage caused by their lax security procedures.
It turns out one infection was responsible for the Maersk compromise. M.E.Doc had been installed on a company computer in Odessa, a Ukrainian port city on the Black Sea. This was all NotPetya needed to infect the entire system. Across the globe, port facilities shut down, and tens of thousands of truckloads of goods were turned away. Maersk’s entire booking system went down, as well as the complex loading systems used to systematically load container ships to avoid capsizing them. Maersk was dead in the water.
An incident response team was assembled, and an emergency recovery center was put together in Great Britain to mitigate and recover from the NotPetya attack. This was a global effort and required hundreds of staffers working 24/7 to rebuild the
network. All computer equipment was confiscated, and new computers were obtained and then distributed to recovery personnel. Staff began rebuilding servers from the ground up. However, this effort came to a grinding halt when it was realized that there was no clean backup of the company’s domain controllers.
A domain controller is a server that responds to requests for user authentication and verification. Domain controllers check usernames and passwords, or other access credentials, to allow or deny user access to network resources. Without a working domain controller, the network is a collection of disparate servers and data that can only be accessed locally. Maersk had about 150 domain controllers throughout its global system that would have ordinarily been able to sync with one another and, thereby, become a backup for a compromised or damaged server. This is an effective and decentralized backup strategy that would have allowed for quick recovery from a localized event; however, no one had visualized a scenario where all the company’s domain controllers were wiped out in a massive attack. If the domain controllers couldn’t be recovered, it was unlikely anything could.
Maersk staffers finally found one pristine backup in their Ghana office. By a stroke of luck, a blackout had knocked the server offline prior to the NotPetya attack, disconnecting it from the network. It contained a single clean copy of the company’s domain controller data, and its discovery was a source of great relief to the recovery team.
Getting the data to the recovery center was a story in itself. The public network infrastructure in Ghana left much to be desired, and the available bandwidth was very low. The backup was several hundred gigabytes of data, and it would take days to transmit it to the recovery center. The next option was to put a staffer on a plane from Ghana to London, but none of the staffers had a British visa. The next scheme was to fly the staffer to Nigeria to meet a Maersk employee and hand over the hard drive personally. That Maersk employee then got back on a plane for the six-and-a-half-hour flight back to Heathrow.
The recovery team began bringing up Maersk’s
core services, concentrating on port services. Key to this was the ability to read a ship’s inventory each ship has 18,000 containers — and determine what was where and where it was bound for. The booking system came back online sometime later, but it would be at least two weeks before port facilities began operating normally again. After that, the recovery team began issuing clean laptops and computers to staff members. Everything the employees had loaded on their machines was gone; the hard drives were wiped, and new, clean copies of Microsoft Windows were installed.
‘ Everything the employees had loaded on their machines was gone; the hard drives were wiped, and new, clean copies of Microsoft Windows were installed.’
When it was over, Maersk estimated that NotPetya had cost the company between $250 million and $300 million, though many believe this number was on the low side. Costs down the line were also significant; trucking companies lost tens of millions of dollars, TNT Express lost about $400 million and Merck lost a staggering $870 million. The disruption to the global supply chain, of which Maersk is a major component, was extensive, and losses accumulated into the billions.
The Maersk incident was an expensive and significant wake-up call. It pointed to the need for education and diligence in promoting and practicing cyber hygiene and instituting robust cyber defenses. NotPetya was a glimpse into what cyberwarfare could be. Without preparedness on every level, no one is safe from the sort of damage this malware caused. ce
Daniel E. Capano is senior project manager, Gannett Fleming Engineers and Architects, and on the Control Engineering Editorial Advisory Board. Gannett Fleming is a content partner. Edited by Industrial Cybersecurity Pulse, a CFE Media and Technology publication.
Santiago Murguia, Rotork
Digitalization for valve and actuator automation can help improve facility management and reduce downtime across the board.
The industrial Internet of Things (IIoT) technology, which relies on devices equipped with sensors, electronics and software to enable them to gather and share data, is the foundation of an approach that enables a site to run as efficiently and safely as possible.
When it comes to valves and actuators, modern technological innovations are not just about the products themselves; it is also about the data they are able to generate and retain, which enables engineers to make faster and better-informed decisions.
To meet these requirements, engineers incorporate field communication networks that enable plant equipment to be controlled and monitored by their distributed control systems (DCSs). For a DCS to function effectively, it requires a master station. This provides an essential link between field devices and the central DCS.
KEYWORDS: process valves, distributed control system (DCS)
LEARNING OBJECTIVES
Understand how industrial Internet of Things (IIoT) technology helps enables a site run as efficiently and safely as possible.
Learn what role a distributed control system (DCS) plays in connecting the IIoT with process valves and actuators.
ONLINE
See additional sensor and actuator stories at https://www.controleng. com/processinstrumentation-sensors/
CONSIDER THIS
What role do actuators and valves play in your facility? Online controleng.com
The value of data provided by the digitization of systems cannot be overstated. However, to receive data, a site first needs to be fitted with the appropriate equipment that can retrieve useful information. When operating hundreds of valves on a site, having an intelligent actuator that can provide advanced data logging capabilities is vital to a functional digital asset management network. Intelligent actuators should give the operator access to the data both in the field and in the control room, via an integrated network.
Comprehensive data communication is an essential element in modern actuation. A network control system for valve actuators will allow the site operator to control the operation at all times, 365 days a year, while monitoring up to 240 actuators on a single fault tolerant field network, and up to 20km long without repeaters.
A master station is usually available in either single, dual or hot standby configurations. The single option provides redundant host connections and redundant field network loops while the dual configuration sees two fully isolated independent units installed side by side. The hot standby variant offers full redundancy, and every interface is replicated. In the event of a fault occurring, the changeover to the standby is seamless without loss of data and control.
The maintenance and management of assets digitally through a cloud-based system can also offer benefits. An intelligent asset management cloud-based system will be able to analyze information from the data loggers within the intelligent actuators.
For decades, intelligent actuators have been able to capture useful data — torque, operations, temperature initially, and later vibration with the latest product range — and keep this data stored in the actuator. The challenge then was this data was not really used for the benefit of the plant operation. Today, with the technology available it is possible
to process and make sense of the data to analyze not only actuator performance, but also valve performance.
The focus now is on how to retrieve this data in the most efficient way. To process it and present it in a streamlined and simple way that allows the operator to have a holistic view of what is exactly occurring on site, allowing for faster and informed decisions when it comes to maintenance and minimizing downtime.
uModern technological innovations for valves and actuators are about the data they are able to generate and retain, which enables engineers to make faster and betterinformed decisions.
uThe industrial Internet of Things (IIoT) and asset management can help streamline many of these concepts and make it easier for engineers to get the data they need from valves and actuators.
All the elements of modern intelligent electric actuation — from cloudbased intelligent asset management to DCS and master stations — provide simplified, secure, and economical solutions to support longterm efficiency and asset management. ce
Santiago Murguia is global portfolio manager at Rotork. This originally appeared on Control Engineering Europe’s website. Edited by Chris Vavra, web content manager, CFE Media and Technology, cvavra@cfemedia.com.
provide simplified, secure, and economical solutions to support long-term efficiency and asset management.
New Products for Engineers Database
(continued from p. 33)
...struggling, offer to listen or to help. Even if they don’t take you up on your offer, the gesture won’t go unnoticed. Letting them know you’re willing to help not only is the kind, but also is how you strengthen your relationship and build team solidarity.
Why it is important: Experienced engineers are often looked to in times of crisis, and it is important to lead by example. Providing a considered, confident and logical point of view is always useful in times of stress, and so is a willingness to listen to others’ input. Good leadership is servant leadership. Sometimes, it means providing a solution. It often means helping the team find the solution, not persuading others that your way is the right way.
Tips: Do not be afraid to take on leadership roles at work or with volunteer organizations. Research successful leaders you’d want to work with and learn about how they operate. Take a professional course on leadership. Find a leader in your company (or elsewhere) you admire and ask if you may pick their brain. Many professionals are happy to share what got them to where they are in
their careers, and enjoy sharing knowledge and experience.
Why it is important: Networking allows engineers to meet new people, learn about new opportunities and stay up-to-date with the latest developments in their field. You never know when you may need to tap into your network to source a part, get help with a unique problem, or look for a new job.
Tips: Research networking events and webinars in your community and attend the ones interesting to you. Join professional groups like ASME, SAE or ASQ — those organizations often host trade shows and in-person networking events throughout the year.
Like most things in life, developing people skills is a continuous learning process, but improving them will make you a better human and a more successful engineer. ce
Riley Hall is the director of product marketing for Fictiv. Edited by Mark T. Hoske, content manager, Control Engineering, CFE Media and Technology, mhoske@cfemedia.com.
The Control Engineering Product of the Year program highlights some of the best new control, instrumentation, and automation products as chosen by Control Engineering’s print and online subscribers. Winners are announced on June 1 at: https://www.controleng.com/events-and-awards/product-of-the-year
AutomationDirect added Wenglor OPT series cylindrical and rectangular ultrasonic sensors. These sensors, in diffuse and through-beam sensing styles, offer sensing distances up to 2000mm, rugged stainless steel and plastic housings, and protection ratings up to IP68 for use in challenging industrial environments. The sensors are IO-Link v1.1 compatible, offering advanced configuration options such as through-beam, synchronous, and mute operating modes, window teach-in, and external temperature compensation. AutomationDirect, www.automationdirect.com
The Model 205 PermaStream H2S in Liquids Process Analyzer from Analytical Systems Keco offers an accurate quantification of hydrogen sulfide (H 2S) in sample streams of crude oil as part of environmental compliance, safety and quality control practices. The inline analyzer measures H 2S in light/medium/heavy crude oil, dirty/clean water, diesel, fuel oil and drilling fluid in real time. By providing accurate and continuous monitoring of H2S levels in liquid streams, the analyzer helps companies demonstrate compliance with air permits promoting the reduction of environmental impacts. Naturally found in crude oil, H 2S can pose a threat when inhaled due. Its corrosive properties can cause damage. Analytical Systems Keco, www.liquidgasanalyzers.com
network appliance has
The new ANR-ICEDA1 1U rackmount network appliance product from Acrosser Technology is Powered by an Intel Xeon D-1713NT processor (Intel code name “Ice Lake-D”), which is Intel's newest System on a chip (SoC) with integrated Ethernet in high-density ball-grid Array packages. It delivers server-class computing, hardware-based security and high-bandwidth I/Os for networking applications at the edge. It supports dual-channel DDR4 SO-DIMM and has max memory capacity of 64GB with error-correcting code (ECC). Acrosser Technology, www.acrosser.com
Antaira Technologies’ ARS-7235-5E-AC-T is an industrial dual radio IEEE 802.11a/b/g/n/ac wireless LAN access point with added router capabilities. Embedded with the Qualcomm IPQ4029 SoC chipset, it is said to have network robustness, stability and a wide network coverage with a very low voltage input of 9V. It supports highspeed data transmission of up to 867Mbps. Features include industrial 2x2 MIMO; supports 5*10/100/1000Base-TX WAN/LAN Ports; and 2.4GHz and 5G. Antaira, www.antaira.com
The Teqwave H ensures the accurate and reliable measurement of sugar content in fruit juices and distilled beverages or the concentration of cleaning agents. In its hygienic design, the meter fulfills the highest quality standards with state-of-the-art algorithms and a flexible application concept for optimal process control, even for changing batches. Liquid analysis allows users to reduce costs because it measures different concentrations simultaneously using only one sensor. In addition, preinstalled concentration data sets make using the same sensor without reprogramming possible. It also allows reading additional parameters, such as acid content. Continuous inline measurement also means no sampling is required. The full-bore design is easy to clean and guarantees the highest hygienic standards are fulfilled. Endress+Hauser, www.us.endress.com
The IFC 400 from Krohne helps detect external influences such as excessive vibration, temperature extremes and magnetic field effects, and also detects process influences like chemicals and excessive sedimentation in the liquid. It has a self-diagnostic function covering three aspects: process conditions, device functioning and out-of-spec testing. The process measurement check detects leaks, contamination, liner deformation and air entrainment in the process liquid. The device function selfcheck continuously monitors electronics and sensor hardware. Out-ofspec testing detects sudden unexplained flow changes, linearity issues and uncertain measurements. It has two versions: a compact version (IFC 400 C) and field-mounted version (IFC 400 F). Both have aluminum housings. Krohne, www.us.krohne.com
The SCU-2200 universal analog-to-frequency converters from ProSense accept milliamp, voltage, RTD, thermocouple or potentiometer inputs and provide a scalable single-frequency output (up to 25kHz). They are helpful when a controller does not have any analog input points available but does have a frequency input. The SCU-2500 series frequency (input) conditioners are useful for converting frequency signals from encoders, magnetic pick-ups, variable speed drives and flow meters to an analog signal for a PLC, recorder or digital display. They accept frequency signals up to 100kHz.
ProSense, www.prosense.net
See more New Products for Engineers www.controleng.com/NPE
Stahlin Enclosures has announced the availability of mounting flanges for its polycarbonate enclosures. The flanges provide a durable alternative to mounting feet and will meet customer requirements and preferences for a full flange. They can be used in a variety of applications and surface types, or in combination with user-added mounting materials and hardware, such as Stahlin pole mount kits or channel. Available with the enclosure or as an accessory kit, the new mounting flange is an ideal solution for most installations and offers numerous competitive advantages. A built-in water-shedding design features a radius that prevents accumulation of water and provides a mounting “cross,” which allows for multiple screw positions and adds flexibility during installation.
Stahlin Enclosures, www.stahlin.com
The DV-1000 embedded computer is designed to combine high-performance computing and flexible expansion capabilities into a compact footprint for edge computing in manufacturing, smart city and industrial applications. It incorporates technologies including: High performance 9/8th Gen Intel Core processors and support for up to 32GB of DDR4 2666 MHz memory; built-in I/O and modular expansion to provide connectivity with various pieces of equipment, including 2x GbE LAN, 2x COM, and 6x USB, to connect to different types of sensors and other devices. LAN, USB, COM and IGN; and a rugged design with industrial certification. The DV-1000 can withstand wide temperatures (-40 to 70°C) and implements wide voltage protection (9-48VDC). Cincoze Co., LTD., www.cincoze.com
NewTek Sensor Solutions offers its hermetically sealed position sensors with a 4 to 20 mA current loop output that has become the data transmission standard in the process control industry. Offering rugged operations and high performance with low power consumption, Newtek’s HI Series of Hermetically Sealed 4 to 20 mA LVDTs ensure highly reliable and consistent data output for factory automation, materials testing and packaging equipment applications, the company says. Requiring less power than similar DC-operated LVDTs and signal conditioners, these 4 to 20 mA sensors also satisfy low power budgets. Sustaining accuracy with no errors over long-distance transmissions, the 4 to 20 mA current does not degrade over long connections and is less sensitive to background electrical noise. Simple to connect and configure, the 4 to 20 mA output position sensors offer plug and play compatibility with most PLCs and controllers. Units require less wiring and fewer connections to reduce startup costs.
Newtek Sensor Solutions, www.newteksensors.com
PLCnext Edge Gateway software from Phoenix Contact is designed to collect data in demanding IIoT and edge computing environments. The downloadable app has an advanced industrial design and no code/low code programming to collect data from any device or sensor and send it directly to a cloud service of the end-user's choice It is scalable for nearly any control system, from a single small machine to an entire manufacturing floor. The gateway requires no programming experience. The simple, webbased configuration uses checkboxes and simple prompts to configure connections. It is compatible with hardware in the PLCnext ecosystem, including the Phoenix Contact AXC F 1152/2152 controllers and Axioline I/O. The PLCnext Edge Gateway currently has drivers to connect with Axiobus (local Axioline I/O connection), Modbus, EtherNet/IP (Rockwell controllers only) and the PLCnext API (local control data and variables within PLCnext Engineer.) Cloud connections are available for Amazon Web Services, Microsoft Azure and DSA Brokers. Phoenix Contact, www.phoenixcontact.com
Ethernet is a robust and stable network framework that has more possibilities than other networking protocols.
Ethernet has been a popular networking protocol for over four decades and is widely used in local area networks (LANs) and wide area networks (WANs). Ethernet provides a fast and reliable way to transfer data and is the most commonly used protocol for connecting devices in industrial automation and control systems.
One of the key benefits of Ethernet integration is the ability to connect multiple devices and systems, allowing for the transfer of data and information between them. This enables the integration of different devices and systems, such as sensors, actuators and controllers, into one network, making it easier to monitor, control and automate processes.
When integrating devices and systems over Ethernet, consider the communication protocols and data formats used by each device. Different devices may use different communication protocols and data formats, making information exchange difficult.
To overcome this challenge, it is best to translate the different communication protocols inside the controller, which acts as a bridge between the different devices and systems and can act as a normalizing point. The controller can translate the data between different protocols and formats, making it possible to exchange information between devices and systems that would otherwise be incompatible.
It provides a centralized location for support and maintenance personnel to see the data and troubleshoot should issues arise. There are options for translation devices, but it is recommended to try to use in rack communication modules. These modules reduce complexity in many ways, including wiring, “black box” data mapping, panel space and sometimes costs while maintaining centralized control.
In the perfect plant floor scenario, all devices and equipment would be aligned on one protocol. It is difficult to achieve due to attempts to leverage the value of various solutions from around the globe. The best path is aligning communication protocols when looking to upgrade or bring new equipment into a facility. It is often worth the upfront costs to upgrade equipment to a standard before integrating it into the network. A clean slate provides a better return on investment (ROI).
Since Ethernet technology supports high data transfers, (10 mbps to 100 gbps), users can control and collect data in real time, an ideal scenario for manufactures and industrial facilities. Furthermore, the increased bandwidth can generate faster, more efficient data transfers between devices forgoing a quicker response time. Since bandwidth is high and more data can be transferred, one can integrate a significant number of devices and systems into the automation process. These devices can include programmable logic controllers (PLCs), distributed control systems (DCS), supervisory control and data acquisition (SCADA), Internet of Things (IoT) devices, wireless systems and more. PLC and DCS are considered advanced control systems. By integrating them into the process via Ethernet, users can expect an increased performance and response in the overall automation process compared to legacy protocols. Ethernet is robust and stable and has more possibilities than other networking protocols such as serial communications and fieldbuses. Ethernet provides fault tolerance and failover capabilities, so the network functions even in the event of a failure. Ethernet is a commonly accepted universal protocol understood by resources in the operational technology (OT) and information technology (IT) layers. More people can design, develop, install and support an Ethernet system than all who understand alternate protocols combined. That understanding helps provide IT/OT collaboration and convergence. ce
Bryan Little is operations director for Avanceon, a CFE Media and Technology content partner. Avanceon is a CSIA certified member. Edited by Chris Vavra, web content manager, Control Engineering , CFE Media and Technology, cvavra@cfemedia.com.
Onlineu controleng.com
KEYWORDS: Ethernet, Ethernet integration
LEARNING OBJECTIVES
Learn the importance of aligning communication protocols in manufacturing. Understand Ethernet’s benefits and advantages as a communication protocol. Learn how it can help bridge the IT/OT gap.
ONLINE
https://www.controleng. com/industrial-networking/ ethernet/
CONSIDER THIS
How has Ethernet helped your facility?
ContentStream
Patrick Lynch, Director of Content Marketing Solutions 630-571-4070 x2210
PLynch@CFEMedia.com
AR, IL, IN, IA, KS, KY, LA, MN, MO, MS, NE, ND, OK, OH, SD, TX, WI, Central Canada
Robert Levinger 630-571-4070 x2218
RLevinger@cfetechnology.com
AK, AZ, CA, CO, HI, ID, MT, NV, NM, OR, UT, WA, WY, Western Canada
Aaron Maassen 816-797-9969 AMaassen@CFEMedia.com
Jim Langhenry, Co-Founder/Publisher, CFE Media JLanghenry@CFEMedia.com
Steve Rourke, Co-Founder, CFE Media SRourke@CFEMedia.com
Courtney Murphy, Marketing Services Manager 630-229-3057 CMurphy@cfemedia.com
McKenzie Burns, Marketing and Events Manager mburns@cfemedia.com
Brian Gross, Marketing Consultant, Global SI Database 630-571-4070, x2217, BGross@CFEMedia.com
Michael Smith, Creative Director 630-779-8910, MSmith@CFEMedia.com
Paul Brouch, Director of Operations PBrouch@CFEMedia.com
Michael Rotz, Print Production Manager 717-422-3622 mike.rotz@frycomm.com
Maria Bartell, Account Director, Infogroup Targeting Solutions 847-378-2275, maria.bartell@infogroup.com
Rick Ellis, Audience Management Director 303-246-1250, REllis@CFEMedia.com
Letters to the editor: Please e-mail us your opinions to MHoske@CFEMedia.com or fax 630-214-4504. Letters should include name, company, and address, and may be edited.
Information: For a Media Kit or Editorial Calendar, go to www.controleng.com/mediainfo.
Marketing consultants: See ad index.
Custom reprints, electronic: Paul Brouch, PBrouch@CFEMedia.com
For 3 to 600 HP fan and pump applications, the FP605 AC drive saves time and resources on installation and programming, while maximizing efficiency for peak energy savings and the return on your investment.
• Enclosure options: IP20/UL Type 1 or IP55/UL Type 12
• Narrow footprint for side-by-side mounting
• Induction, PM and synchronous reluctance motor control
• Supports all major industrial network communications
• Pump control features that maximize drive and pump life
• Mobile-friendly setup (USB ON-THE-GO or Bluetooth)
• Programmable without main power supply connected
Need a simple solution for your industrial fan or pump? Contact Yaskawa for help today.
Servo motors and gear units offer a high degree of dynamics and performance with a compact design, making them excellent for confined spaces. Multiple frame sizes and torque ratings makes them the perfect fit in material handling, hoist and gantry
applications, and a wide variety of machine automation applications. Their modular design allows for direct gear unit mounting without adapters or couplings. Pair that with the option of single-cable technology and you’ve got a flexible, precise servo drive solution.