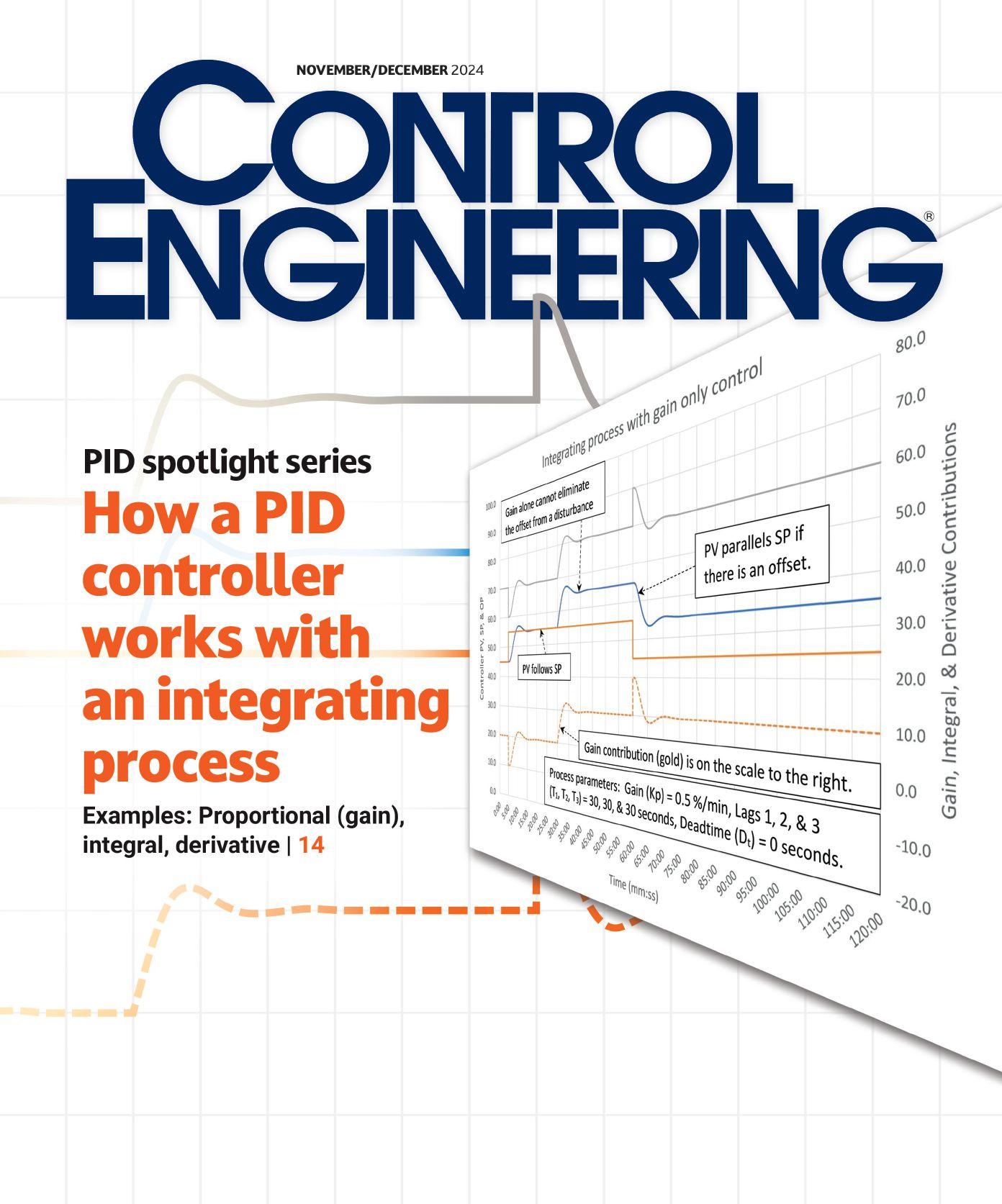

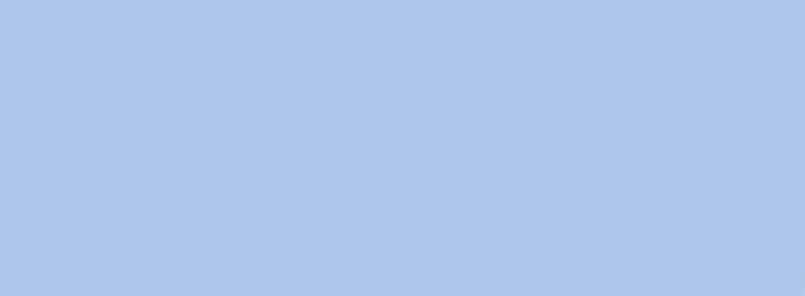
Starting at only $199.00
The BRX PLC has advanced features that allow it to easily take on the role of an edge computing device - gathering, re ning, and delivering control system data to upstream IT collection and BIG DATA analysis programs.
With BRX’s embedded Web server, you can instantly access system status, diagnostic information, and monitor memory usage from any Internet-ready device.
The integrated Rest API and secure HTTPS protocol allow BRX to work with ow control tools like Node-RED® in order to supply high-level IT systems with the plant- oor data they need.
With the growing number of IIoT platforms and cloud computing services, BRX controllers utilize the industry-standard MQTT(S) and FTP protocols to seamlessly integrate with asset management/IIoT platforms including:
• Microsoft Azure®
• IBM Watson®
devicecatalog.azure.com
With robust task management and a variety of interrupt styles for task prioritization.
Discrete, process, and multi-axis motion control instructions to support even complex applications, executed with familiar ladder logic programming.
Enabling scripted math and algebra, to support rich data pre-processing right at the edge.
Order your cut-to-length and bulk cables today and save with AutomationDirect’s affordable pricing - No gimmicks. No hidden charges.
Over 35 types of cable available in bulk or cut-to-length sizes and shipped fast!
All our multi-conductor cables can be ordered cut to your specified lengths without added cutting charges, hidden fees, or inflated shipping costs found with other suppliers.
With AutomationDirect you get: Cut-to-Length Cables with NO Hidden Fees
• UL certified re-spooling facilityensures that our cut-to-length cables maintain their UL certifications
• Low price per foot starting at $0.18/ft.
• Free, fast shipping (typically 2-day delivery)*
• Easy online, phone or email ordering
• Low minimum cut lengths
• 45-day money-back guarantee* (yes, even custom cut cable)
Starting at $0.74 /ft. (20 ft. min)
LUTZE ELECTRONIC® 300V shielded/unshielded industrial grade multi-conductor flexible cables are ideal for most control and signal applications. cables are ideal for most control and applications.
• Available in 22 AWG to 16 AWG sizes
• Power Limited Tray Cable (UL) Type PLTC rated for cable tray use
• AWM rated for use in appliance wiring
• Ideal for use in machines/machine tools, plant cabling, HVAC technology, assembly/production lines, process instrumentation, and for industrial controls
• Thoroughly tested and certified by ECOLAB for use with cleaning and disinfecting agents used in Food and Beverage applications
• Made in the USA
AutomationDirect has a large selection of quality electrical MTW, THHN, DLO, TFFN, AWM, and HAR wire in pre-spooled lengths that meets all NFPA and NEC requirements at great prices.
| New facility: Six net zero benefits, seven smart manufacturing methods; Four benefits: Automation ecosystem adds new features, applications, partners, integration; New AI-powered closed-loop tools can revolutionize manufacturing in 9 ways
| Think Again: New metrics, ground-breaking stories, 2025 topics using research, share knowledge
| COVER: PID spotlight, part 11: How a PID controller works with an integrating process
| Why it's critical to integrate distributed control systems
| How to use AI, neural networks in feedback closed-loop control
| Iron foundry integrates SCADA, ERP
| Transforming the robotics industry: A sustainable communication protocol
| The cost of inaction: Securing manufacturing and critical infrastructure
| Five technologies for a future-proof edge control platform, flexible stack deployment
| Automated Warehouse supplement
• Over 500 modules to choose from
• Works with a wide variety of well-known fieldbuses
• Specialty modules for 3-phase power measurement, IO-Link master, CANopen and more
• High-density 12mm wide modules
• 1, 2, 4, 8 or 16 channel options
Control Engineering eBook series, now available: Winter Edition
78 | New Products for Engineers, www.controleng.com/products
Water-cooled servomotor series; Mini AC-operated position sensors; Controllers for a distributed I/O system; Precision limit switches; Servo drive with functional safety measures; Wireless transmitter for field asset monitoring.
Product of the Year nominations are underway at https://www.controleng.com/events-and-awards/product-of-the-year
79 | Back to Basics: NAMUR module type package (MTP)
Times to market can be reduced by up to 50%, engineering effort can be reduced by up to 70% and flexibility can be increased by 80%.
IIoT for Engineers Newsletter
• Digital twins, digitalization, AI analytics, Ethernet connections
Mechatronics and Motion Control
• AMR integration, more uptime, modular robotics
CE Motors & Drives Newsletter
• Robotic motion, VFDs, PWM, AI in motion
Stay ahead. Subscribe! www.controleng.com/newsletters
u Global System Integrator Report
ENCLOSED: November/December 2024 edition with 2025 System Integrator of the Year, System Integrator Giants, case studies, trends and tutorials and more! www.controleng.com/GSIR
u Applied Automation eBook
Featured articles in this eBook include what’s driving the IT/ OT divide for manufacturers, how to build resilient industrial networks and reduce downtime, is your change management initiative up to par among more than 45 pages of content. Learn more at: www.controleng.com/ebooks
u System Integration eBook
Featured articles include: Gain critical advice on automation, SCADA from system integrators; How to mitigate labor challenges with the right automation investments; PLCs, PACs and edge controllers in an era of high availability. More topics at: www.controleng.com/ebooks
u Control Engineering digital edition
Five digital edition advantages: 1. Useful links throughout. 2. Click on headlines to see online version with more text and often more images and graphics. 3. Download a PDF version. 4. Cover page faces a wide selection of topical eBooks. 5. Sustainability. www.controleng.com/ magazine
u Latest automation mergers, October 2024 involve AI, analytics, motionClint Bundy is managing director, Bundy Group.
u PID spotlight part 10: Heuristic tuning, deadtime-dominant self-limiting processEd Bullerdiek, process control engineer, retired (A)
https://www.controleng.com/articles/pid-controller-tuning-insights
u How to incorporate digital transformation into SCADA master planningFrancisco Alcala, senior automation engineer, and Srisylesh Balaji, junior automation engineer, CDM Smith
https://www.controleng.com/articles/how-to-incorporate-digital-transformation-into-scada-master-planning
u How to unlock design efficiency, standards for P&ID developmentA. Prabhakaran, automation engineer and Eric J. Silverman, PE, PMP, CDT, is vice president and automation regional team leader, CDM Smith (B)
https://www.controleng.com/articles/how-to-unlock-design-efficiency-standards-for-pid-development
u More answers now: Back to basics: What you need to know about today’s PLCsFrank Lamb, founder and owner, Automation Consulting LLC, and Braden Hadwiger, mechanical engineer, Huffman Engineering Inc. (C)
https://www.controleng.com/articles/more-answers-now-back-to-basics-what-you-need-to-know-about-todays-plcs
u Are manufacturing plants prepared for the benefits eSCADA systems offer?Wes Sutton, market development lead for horizontal solutions at Rockwell Automation (D)
https://www.controleng.com/articles/are-manufacturing-plants-prepared-for-the-benefits-escada-systems-offer
u The ultimate guide to configuring multidimensional arrays in SCADA systemsVinoth Upendra Janardhanan, mid-level automation engineer, CDM Smith
u How one mining company dug up control loop optimization's benefitsBrad Malik, senior process controls engineer, Rio Tinto Kennecott, and Maxym Lachance, project manager of optimization, advanced control, and alarm management at BBA (E)
https://www.controleng.com/articles/how-one-mining-company-dug-up-control-loop-optimizations-benefits
u Understanding EPA Requirements for CEMS Design - Keith N. Linsley, senior global product manager for CEMS and process analyzer systems, Emerson
u Industry 4.0 is enhancing quality and efficiency - Brandon Teachman, owner of Automation Coffee Break
u Proven applications benefits using piezoelectric controlled pneumatics and why
uCustomers can see how ABB technologies are saving energy in a new $100 million advanced manufacturing facility, customer experience center and innovation lab that combines and expands two
‘ The highly automated, advanced manufacturing facility is expected to attract engineering and other skilled workforce talent.’
other Wisconsin sites and adds adjacent warehousing space. At the ribbon-cutting event Oct. 29, company executives explained how ABB motors, drives, and other products can show customers how to effectively and efficiently apply
Tim Skell, ABB global HVACR application engineering manager (HVACR stands for heating, ventilation, air conditioning, refrigeration), explains how ABB variable frequency drives (VFDs) are configured with redundancy or bypass for various design risk scenarios to fit different applications and facilities, part of the ABB New Berlin, Wisconsin, mechanical room tour. Courtesy: Mark T. Hoske, Control Engineering, WTWH Media
advanced technologies to meet 2030 sustainability and decarbonization goals. The facility (see videos, photos) will employ more than 700 workers with an additional 100 jobs within three years in a phased opening and expansion.
At the event, ABB explained six key benefits to employees, elected officials, education leaders and media that the site:
• Supports future growth in ABB’s largest market with production of electric drive technologies used in a variety of industries. The highly automated, advanced manufacturing facility is expected to attract engineering and other skilled workforce talent.
• Creates a new manufacturing and customer experience facility with digital technologies that help ABB meeting sustainability goals for 2030 and beyond.
• Applies geothermal heating and modern HVAC system designed to recycle waste heat, eliminate natural gas use and reduce energy use more than 45%.
• Saves transportation costs and associated emissions by locating a warehouse distribution center on the campus.
• Meets requirements of the Build America Buy America Act (BABAA).
• Is important for industrial, power, transportation and building sectors.
About ABB’s New Berlin drive manufacturing (no photos were allowed) Daniel Beaudet, director quality – advanced manufacturing, continuous improvement, U.S. motion business, said ABB worked with Porche Consulting on seven attributes of this smart factory of the future:
1. Adaptable and scalable to handle demand variability and meet customer lead times.
2. Attractive, creating operator engagement and demonstrating net zero carbon emission sustainability goals.
3. Lean material and information flow, improving connections to suppliers and customers.
4. External customer focus with on-time delivery and improved communication and feedback with greater information transparency.
5. Lean and robust processes to mitigate issues earlier and lessen impact to assembly lines with quality, standards, early abnormality detection and error proofing.
6. Smart and data driven systems with interoperable systems, modeling, simulation, intelligent automation, strong cybersecurity and networked sensors.
7. Top quality enabled by integrated systems throughout the value system. See more text, photos and videos with this article online. ce
Mark T. Hoske is editor-in-chief, Control Engineering, WTWH Media, mhoske@wtwhmedia.com.
Four benefits:
uNew automation ecosystem features, applications, partners and capabilities for operational technology and information technology (IT/OT) convergence were among highlights at the Bosch Rexroth “ctrlX Automation Media Day 2024.” Control Engineering covered the event and received an exclusive in-person tour of the technology demonstration room and other areas at the Rexroth Hoffman Estates, Illinois, headquarters. The automation ecosystem expansion helps in four areas:
• The Linux-based operating system, Rexroth ctrlX OS, works with more and different types of automation, providing new features and application areas.
• The extended ecosystem of Bosch Rexroth ctrlX has more than 100 partner companies, with increased focus on IT/OT convergence.
• Developers are adding a variety of ctrlX apps, more than 80 (more than half from third parties) as of Novem-
ber with many more under development and in approval stages, extending applications. More than 2,500 customers use ctrlX; five OEMs use the operating system, including Congatec for its multicore hypervisor, Dell on servers, Nokia for 5G cloud services and Wago for building automation. New offerings include a new ctrlX OS, ctrlX Works engineering toolbox software, ctrlX PLC, ctrlX Motion, ctrlX World, ctrlX I/O, ctrlX Safety, ctrlX drive products and ctrlX motors. Engineering savings can total 30%, Rexroth said.
• System integration with Rexroth hardware and software was demonstrated after the formal media presentation.
See more text, photos and videos with this article online. ce
Mark T. Hoske is editor-in-chief, Control Engineering, mhoske@wtwhmedia.com.
Bosch Rexroth’s ctrlX is shifting toward IT/OT convergence capabilities, in the ctrlX OS Ecosystem, initiated by Bosch Rexroth. Recent additions to the partner network ctrlX World are Pepperl+Fuchs, ServiceNow and SMC. Courtesy: Mark T. Hoske, Control Engineering
controleng.com
Coverage on Automation Fair, Pack Expo Advanced Automation Forum, April 30 May 1, 2025, Boston Convention and Exhibition Center https://www.advancedautomationforum.com
Artificial intelligence (AI) helps manufacturers empower workers, improve performance and enhance productivity with a closed-loop machine-vision-based application for real-time worker training and quality control, according to Rapta, an applied AI software company based in Portland, Oregon. The company said its collaborative AI cameras and sensors can improve manufacturing yield with 90% lower rework costs; 98% faster inspection; 5-times faster training time; 6-month return on investment (ROI) and 1-day setup and use.
The Rapta AI Supercoach and AI Supervisor systems are self-contained
AI solutions that “set a new standard in real-time worker training and quality control, helping manufacturers solve today’s toughest challenges — without the need for a cloud connection,” the company said in an Oct. 17 statement.
AI-enabled machine-vision systems can resolve some of the most pressing manufacturing problems, Rapta said, such as production training, real-time quality control and automated work instructions. To exceed capabilities of traditional vision systems, Rapta said an AI-based machine vision system should excel in nine key areas.
• Closed-loop work recognition
• Full traceability with photographic evidence
• Rapid AI vision model training
• No-code assembly builder
• Full integration with digital tools
• Human-like AI vision
• Comprehensive revision control
• Mechanical scene memorization
• Real-time continuous quality control
Edited from information provided by Rapta by Mark T. Hoske, editor-in-chief, Control Engineering, WTWH Media, mhoske@wtwhmedia.com.
uBUNDY GROUP, an investment bank and advisory firm that specializes in the automation segment, provides an update
on 12 mergers and acquisitions and capital placement activities for this industry in November, including Ametek, SCIO
Automation and Siemens, among others. Three follow. See more with this article online.
Ametek acquired Virtek Vision International, Oct. 31
Ametek Inc. acquired Virtek Vision International, a provider of advanced laserbased projection and inspection systems. Virtek specializes in 3D laser projectors, smart cameras and AI-powered quality control systems, offering machine vision solutions that automate assembly processes and improve manufacturing efficiencies in aerospace, defense and industrial applications.
Siemens agreed to acquire Altair Engineering, Oct. 30
Siemens has agreed to acquire Altair Engineering Inc., a provider of software in the industrial simulation and analysis market, for $113 per share, valuing the deal at approximately $10 billion. The offer represents a 19% premium to Altair’s closing price on Oct. 21, 2024. This acquisition strengthens Siemens' position in industrial software.
SCIO Automation acquired CEC Controls Co., Aug. 15
CEC Controls Company Inc., a Warren, Michigan-based subsidiary of UK-based John Wood Group, has been acquired by SCIO Automation GmbH. As a leading controls system integrator in the automotive sector, CEC Controls also expanded into markets like water and wastewater, industrial manufacturing, pharmaceuticals and food and beverage. The acquisition enhances SCIO’s North American presence and strengthens its discrete automation segment. ce
Clint Bundy is managing director, Bundy Group, which helps with mergers, acquisitions and raising capital. Edited by Mark T. Hoske, editor-in-chief, Control Engineering, WTWH Media, mhoske@wtwhmedia.com.
Control Engineering 2024 Motors and Drives research provides insights on purchasing, implementation challenges, future features and advice.
The Control Engineering 2024
Motors and Drives Audience Research Report reveals key trends about motor and drives purchasing behaviors, challenges with motor and drive selection, integration and use and subscribers’ desires for future features in motors and drives. Some results are summarized below with more advice and two more graphics online; a 22-page downloadable report is available free with this article at www.controleng.com, WTWH Media.
“When selecting motors and drives, respondents are most influenced by technical and customer support, product quality, previous experience with the brand, and alignment of the brand’s product/service with their project’s requirements,” said Amanda Pelliccione, marketing research manager, WTWH Media and Control Engineering, in the report. Those were the top four answers on top factors influencing brand preference, providing statistically differentiation among other answers. With 160 respondents, the margin of error for the report is plus or minus 7.7%. These four factors, ranging from 60% to 53%, were significantly higher than initial product cost in the next tier of responses statistically tied with seven other factors (38% to 31%) including company specifications, easier integration with existing network capabilities and lifetime product value (which would include energy efficiency considerations).
That data point supports another finding
Energy savings and durability are the top two anticipated improvements in future motors and drives, according to the Control Engineering 2024 Motors and Drives Audience Research Report. Courtesy: Control Engineering
in the research: “Programming or configuration tops the list of significant challenges respondents face when working with motors and drives in control systems. Other challenges include system integration with existing automation and/or networks and control complexity,” Pelliccione said. Desired features in motors and drives include sustainability, durability and better controls. “Respondents are looking forward to energy-saving motor and drive technologies in the next few years,” Pelliccione said, “along with enhanced durability features and advanced control algorithms, among other innovations.”
More than 20 respondents answered an open-ended question seeking “advice on motor and drive topics for automation and
controls.” Advice follows, lightly edited. Consider initial cost, efficiency, harmonics mitigation and friendly programming. Automation and controls are no longer optional. Energy efficiency and process optimization are significant factors in the food processing industry because margins are very tight. Optimized processes are often the difference between failure and success.
Return on investment (ROI) is critical. Ease of programming helps. ce
Mark T. Hoske is editor-in-chief, Control Engineering, mhoske@wtwhmedia.com.
Remote wireless devices connected to the Industrial Internet of Things (IIoT) run on Tadiran bobbin-type LiSOCl2 batteries.
Our batteries offer a winning combination: a patented hybrid layer capacitor (HLC) that delivers the high pulses required for two-way wireless communications; the widest temperature range of all; and the lowest self-discharge rate (0.7% per year), enabling our cells to last up to 4 times longer than the competition.
Looking to have your remote wireless device complete a 40-year marathon? Then team up with Tadiran batteries that last a lifetime.
1111 Superior Avenue, 26th Floor, Cleveland, OH 44114
Mark T. Hoske, editor-in-chief 847-830-3215, MHoske@WTWHMedia.com
Sheri Kasprzak, managing editor, engineering, automation and control, SKasprzak@WTWHMedia.com
Stephanie Neil, vice president, editorial director engineering, automation and control, 508-344-0620 SNeil@WTWHMedia.com
Emily Guenther, webinar coordinator EGuenther@WTWHMedia.com
Amanda Pelliccione, marketing research manager 978-302-3463, APelliccione@WTWHMedia.com
Gary Cohen, senior editor GCohen@WTWHMedia.com
Anna Steingruber, associate editor ASteingruber@WTWHMedia.com
Chris Vavra, senior editor
Suzanne Gill, Control Engineering Europe suzanne.gill@imlgroup.co.uk
Agata Abramczyk, Control Engineering Poland agata.abramczyk@trademedia.pl Lukáš Smelík, Control Engineering Czech Republic lukas.smelik@trademedia.cz
Aileen Jin, Control Engineering China aileenjin@cechina.cn
Editorial Advisory Board www.controleng.com/EAB
Doug Bell, president, InterConnecting Automation, www.interconnectingautomation.com
David Bishop, chairman and a founder Matrix Technologies, www.matrixti.com
Daniel E. Capano, senior project manager, Gannett Fleming Engineers and Architects, www.gannettfleming.com
Frank Lamb, founder and owner Automation Consulting LLC, www.automationllc.com
Joe Martin, president and founder Martin Control Systems, www.martincsi.com Rick Pierro, president and co-founder Superior Controls, www.superiorcontrols.com
Eric J. Silverman, PE, PMP, CDT, vice president, senior automation engineer, CDM Smith, www.cdmsmith.com Mark Voigtmann, partner, automation practice lead Faegre Baker Daniels, www.FaegreBD.com
WTWH Media Contributor Guidelines Overview
Content For Engineers. WTWH Media focuses on engineers sharing with their peers. We welcome content submissions for all interested parties in engineering. We will use those materials online, on our Website, in print and in newsletters to keep engineers informed about the products, solutions and industry trends.
* Control Engineering Submissions instructions at https://www.controleng.com/connect/how-to-contribute gives an overview of how to submit press releases, products, images and graphics, bylined feature articles, case studies, white papers and other media.
* Content should focus on helping engineers solve problems. Articles that are commercial in nature or that are critical of other products or organizations will be rejected. (Technology discussions and comparative tables may be accepted if nonpromotional and if contributor corroborates information with sources cited.)
* If the content meets criteria noted in guidelines, expect to see it first on the website. Content for enewsletters comes from content already available on the website. All content for print also will be online. All content that appears in the print magazine will appear as space permits, and we will indicate in print if more content from that article is available online.
* Deadlines for feature articles vary based on where it appears. Print-related content is due at least three months in advance of the publication date. Again, it is best to discuss all feature articles with the content manager prior to submission. Learn more at: https://www.controleng.com/connect/how-to-contribute
Control Engineering provides new metrics software; reflect on ground-breaking stories; research on 2025; share knowledge.
Control Engineering focuses on the control loop (measure, decide, actuate), and we share information to help others measure, make decisions and improve. Below see a new measurement tool, my opinion of some of the best coverage as we wrap up our 70th year and prepare for 2025.
Control Engineering, and other WTWH Media publication customers can look at various metrics using the new WTWH Media measurement tool, CLARA. The data-driven, technology enabled performance platform aggregates audiences to enable marketers to identify and drive return on investment (ROI)-based programs.
Ethernet everywhere, a 1999 article predicting Ethernet’s use with throughout automation.
Artificial intelligence, within, a 2003 article explaining AI applications in control engineering.
Engagement (page views) for the period was 577,265 in 2024 through Nov. 28. Audience company size (employees) are: 23% under 200; 30% 201 to 1000; 22% 1001 to 9,999; and 25% 10,000 and more.
Audience job functions are: 35% operations; 33% engineering; 24% IT and 8% sales. Among top 10 audience domains are Chevron, Shell and Intel. The top 5 general on-site topics are: Variable frequency drive (VFDs); Programmable logic controller (PLCs); Process control; Automation control systems and Automation standardization. Learn more at www.wtwhmedia.com
I recently was asked about the most-significant Control Engineering articles among many thousands during my 30 years. Consider these forward-looking topics with links to each with this column online. https://www.controleng. com/magazine Let me know your favorites.
7 things noncontrol people should know about control engineers, 2014
5 enduring developments in electronic motion control, 2019 Control loops benefit more than control systems, a 2021 summary of an MIT professor’s wider look at the value of control theory. New cost analysis: Open process automation saves 52% versus DCS, showing the power of standardization for cost savings and for control effectiveness, March/April 2024.
The Global System Integrator Report (GSIR), a collection of articles, research and recognition, with this issue, tops off each year’s coverage of system integration topics.
To determine 2025 coverage, Control Engineering asked subcribers what they need to do their jobs better. Research results create the annual editorial calendar, located at www.controleng.com/research. Find real-time measures of what’s useful on Control Engineering annual, monthly and weekly articles about the mostread articles at www.controleng.com. Think again about sharing your knowledge in 2025 with a Control Engineering article or as a webcast instructor. https://www.controleng.com/ connect/how-to-contribute ce
Mark T. Hoske is editor-in-chief, Control Engineering, WTWH Media, mhoske@wtwhmedia.com.
Ed Bullerdiek, process control engineer, retired
Control of an integrating process with a proportional-integral-derivative (PID) controller begins with learning the role of controller gain, integral and derivative in controlling the integrating process. PID control of an integrating process has certain similarities to self-limiting processes, but is very different in some important ways.
In PID spotlight part 3 [https://www.controleng. com/articles/pid-spotlight-part-3-how-to-select-one-of-four-process-responses/] on process types I stated that “how we tune a PID controller depends on the type of process response.” In other words, once you mate a PID controller to a process the mated pair behave in a way that is unique to that (type of) process. Furthermore, a PID/integrating process behaves, and is therefore tuned, differently than a PID/self-regulating process. There are different things to look for and a different set of rules.
COVER: FIGURE 1: The response of an integrating process to gain only (P) control (controller gain K = 1.0) Images courtesy: Ed Bullerdiek, retired control engineer
As we did for self-regulating processes let’s explore how controller gain, integral, and derivative individually affect the process, beginning with controller gain. As with self-limiting processes we will use this information to figure out how to blend them together to get a functioning controller.
Figure 1 shows how controller gain alone interacts with an integrating process.
There are several things to discuss here beginning with the definition of process gain (Kp) for an integrating process. Self-limiting process gain (Kp) is defined as the change in process variable (PV) relative to the change in controller output (OP) expressed as ΔPV/ΔOP (%/%). If you change the controller output connected to an integrating process the PV will eventually go to infinity (or negative infinity) if left long enough. The self-limiting process definition of process gain is useless for an integrating process because the answer will always be “infinity.”
What we really need to know is when we change the controller output how much will the direction of the PV change? This is defined as Kp = (ΔPV/
minute)/ΔOP {(%/min)/%}. For simplicity we usually express process gain for integrators as %/minute with the understanding that this is per a one percent change in the controller output (note that disturbances are also expressed in percent change in controller output equivalent).
When we look at the change in controller setpoint (SP) at the 5 minute mark the one thing that should really jump out at us is the PV gets to the SP without the need for integral action. This is radically different from a self-limiting process where integral is required to drive the PV to SP. What’s going on here?
A material (or energy) balance process like a level holds an inventory that does not change as long as the input and output flow rates match. A SP change does not change the uncontrolled flow (input or output), it is merely a request to change the inventory. The controller does this by (in this case) reducing the output flow until the inventory (PV) matches the SP, at which point when the error drops to zero the gain contribution drops to zero and the OP is back where it started. The material balance has been restored.
I am emphasizing this seemingly trivial point because it significantly affects how we think about tuning an integrating process (more importantly you must forget how controller gain works with a self-limiting process). One thing to realize is that when you make a SP change to an integrating process integral action is actually counterproductive (are you surprised?)
At the 30 minute mark the inlet flow increases 10% (OP equivalent). To match the change in inlet flow the OP must increase 10%. This can only happen when the error between the PV and the SP multiplied by the controller gain equals the change in inlet flow {ΔOP = ΔInlet Flow = (PV – SP) * K}. Just like a self-limiting process a disturbance to an integrating process will result in a permanent offset from SP unless integral action is used. Finally at the 60 minute mark the SP is changed again. The PV parallels the change in SP, maintaining the constant offset that was caused by the change in inlet flow at the 30 minute mark.
What we have learned about gain only control of an integrating process is:
• The PV will follow SP changes without the need for integral action. In fact integral action will likely be counterproductive.
• A disturbance will result in a persistent offset between the PV and SP. Integral action will be required to eliminate the offset.
This presents us with a couple of problems that we didn’t have with self-limiting processes. One is that if we have to balance tuning for SP changes versus disturbance rejection we have a balancing problem; how much integral can we include to remove disturbances without impacting the response to SP changes? Fortunately we almost never change SP’s on integrating processes (at least in refineries), so this is generally not an issue. The second problem is we cannot use a SP change to test controller tuning for disturbance rejection.
Figures 2 and 3 show how raising controller gain affects controller performance.
As in figure 1 the input flow changes 10% at the 30-minute mark. The controller output (OP) changes 10% after some initial oscillation to match the change in input. The higher controller gain reduces the PV offset from SP, however it does not and cannot eliminate it. This behavior is identical to how a self-limiting process behaves; raising controller gain reduces PV offset from SP, but at the
controleng.com
KEYWORDS: Proportionalintegral-derivative, PID tutorial
LEARNING OBJECTIVES
Know the definition of process gain for an integrating process.
Understand how integrating processes under PID control behave similarly to selflimiting processes.
Examine differences of how integrating processes under PID control behave relative to self-limiting processes.
CONSIDER THIS Integrating processes when controlled by a PID controller do not behave like selflimiting processes. What are the similarities, and what are the differences? How will this affect how we think about tuning PID controllers mated to integrating processes?
risk of increased controller oscillation.
Figure 3 shows that, similar to self-limiting processes if the controller gain is raised too high the controller goes unstable. Furthermore, the PV and OP peaks line up, which is a key visual cue to use during heuristic controller tuning efforts.
Figure 4 shows how integral alone interacts with an integrating process.
Figure 4 shows us that integral only control of an integrating process doesn’t work. One quirk of integrating processes is integral only control is always unstable no matter how slow the integral tuning constant (Ti) is set. One common tuning problem of integrating processes is inadequate controller gain relative to the integral tuning constant, which will result in a continuous slow roll of the process. (Figure 4 was made using a parallel PID to show how integral action doesn’t work without controller gain.)
Similar to a self-limiting process when there is too much integral action (relative to controller gain) the PV and OP peaks do not line up.
Figure 5 shows what happens when a little controller gain is added to complement integral control of an integrating process (PI control).
4: The response of an integrating process to integral only (I) control (integral Ti = 0.05 repeats/minute – parallel PID algorithm)
In Figure 5 we see that adding a little bit of controller gain to the controller stabilizes the controller while retaining an integral constant of 0.05 repeats/ minute (parallel PID algorithm). The response to the SP change at the 5-minute mark still swings a little bit; raising controller gain further will stop this. Note that the integral contribution slows the return of the OP to 70% between 5 and 12 minutes. This results in the PV overshooting the SP (PV will always overshoot the SP after a SP change when integral is present); the PV doesn’t return to SP for another 20 minutes as the integral contribution returns to zero. In short, the presence of integral hinders the response of the controller to a SP change.
The response to the disturbance at the 60-minute mark is identical to the response of a self-limiting process. The controller gain responds first (as expected) followed by the integral action trying to eliminate the offset. After some swinging the controller gain contribution drops to zero as the PV settles on SP (the error has returned to zero) and the integral contribution (and change in OP)
‘ Integral is required for eliminating process variable offset caused by a process disturbance, but it hinders response to a setpoint change. ’
matches the size of the disturbance (10%).
This illustrates an issue with tuning an integrating process; integral is required for eliminating PV offset caused by a process disturbance, but it hinders response to a SP change. Fortunately, the SP of most integrating processes are rarely changed.
Figure 6 shows how derivative alone interacts with an integrating process.
Figure 6 shows how derivative penalizes PV movement. The 4% disturbance to inlet flow that starts at the 30-minute mark causes the PV to ramp upward 2%/minute. A derivative constant of 4 minutes moves the OP enough to reduce the ramp rate to 0.67%/minute. (The 60 second derivative filter was used to slow the derivative response enough for you to see the impact of adding derivative. Note that very few control systems allow adding a filter to derivative.)
Derivative action on changes in PV (the recommended option for derivative control) does not respond to the SP change at the 5-minute mark.
Figure 7 shows how raising derivative affects controller performance.
Figure 7 shows that too much derivative will result in controller oscillation. Further increases to derivative will result in controller instability. Similar to self-limiting processes the visual cue for too much derivative is rapid swings of the OP caused by high derivative chasing small changes in the rate of change of the PV.
Note that increasing derivative did further reduce the rate of change of the process variable (PV).
As a general rule derivative is never used for level control. Derivative causes small changes in inlet flow to become large changes in outlet flow, which will upset downstream processes. Levels are typically tuned to avoid rapid changes to outlet
PI control of an integrating process (K = 0.35, Ti = 0.05 repeats/ minute – parallel PID algorithm)
6: The response of an integrating process to derivative only (D) control (derivative Td = 4 minutes, derivative filter = 60 seconds – parallel PID algorithm)
flow regardless of what the inlet flow is doing, thus dampening any upsets. This surge flow management requires special attention to controller tuning to avoid overflowing or emptying the vessel while still minimizing changes in flow to the downstream process. There are, of course, exceptions to this
FIGURE 7: The response of an integrating process to derivative only (D) control (derivative Td = 12 minutes, derivative filter = 0 seconds – parallel PID algorithm)
rule, but these depend on the process. We will look at tuning to minimize the impact of disturbances and tuning to minimize controller output movement (surge management).
‘ Good control loop tuning means blending controller gain, integral, and (rarely) derivative together to get the best controller response. ’
• Too much derivative will cause swinging.
The differences are:
• Controller gain alone is adequate for SP changes. The PV will settle back on SP without the use of integral. In fact, integral will result in the PV overshooting the SP and delay the eventual return of the PV to SP.
• Integral alone is always unstable on an integrating process. Controller gain is required to maintain stable control. What may appear to be too much integral may in fact be too little controller gain (heuristic tuning will not be as simple as just slowing down the integral action).
Online controleng.com
ONLINE
Link to PID spotlights, parts 1-10 and with this article online, starting with “Three reasons to tune control loops: Safety, profit, energy efficiency.”
https://www.controleng.com/ articles/three-reasons-totune-control-loops-safetyprofit-energy-efficiency
Aug. 1 RCEP webcast is available for one year: How to automate series: The mechanics of loop tuning
https://www.controleng.com/ webcasts/how-to-automatethe-mechanics-of-loop-tuning
Summary: Blending gain, integral and derivative? 4 similarities, 3 differences We have learned that integrating processes respond to PID control in some ways similar to self-limiting processes, and in other ways quite differently. The similarities include:
• Controller gain cannot eliminate the error between the process variable (PV) and setpoint (SP) that is caused by a process disturbance. Integral action is required to eliminate the error.
• Too much controller gain will cause swinging. The visual cue that the controller gain is too high is the process variable (PV) and controller output (OP) peaks will line up.
• Too much integral will cause swinging. The visual cue that integral is too high is the PV and OP peaks do not line up.
• Derivative, by penalizing PV movement, will slow down the ramp rate caused by a disturbance.
As with self-limiting processes, good control loop tuning means blending controller gain, integral, and (rarely) derivative together to get the ‘best’ controller response. One challenge will be determining what ‘best’ is as part of the goal will be to avoid unnecessarily disturbing downstream processes. We will see that our thought process for tuning an integrating process will in some ways be similar to, and in other very different from, how we tune a self-limiting process. ce
Ed Bullerdiek is a retired control engineer with 37 years of process control experience in petroleum refining and oil production. Edited by Mark T. Hoske, editor-in-chief, Control Engineering, WTWH Media, mhoske@wtwhmedia.com.
Claudio Fayad, Emerson
The distributed control system (DCS) is still the heart of modern automation, driving the most-optimized plants, and preparing for future data-centric operations.
Since its inception, the distributed control system (DCS) has been one of the most critical components of any automation strategy, integrating what used to be independent applications. No other automation technology can bring the same level of out-of-the-box integration of automation components, along with powerful data contextualization. Plants around the globe rely on their DCS to make it easier to implement the complex process control strategies that provide critical business differentiators.
The world has changed dramatically in the last few years. Organizations worldwide are facing new calls for increased efficiency of production to meet changing and expanding global needs, while they simultaneously heed the call from government and the public to operate more sustainably. These shifts, requiring a never-ending wave of digital transformation, have increased the complexity of plant operations, requiring far more optimization and connectivity. Real-time control is still critical, but it is not everything.
KEYWORDS: DCS, datacentric control system
Understand how integrating distributed control systems improve data-collection and analysis efforts for automated organizations.
Establishing how modern DCS should take center stage in an automation platform.
It would be easy to assume that as the process control world becomes more data-centric, the proportional-integral-derivative (PID) loop- and interlock-focused control system would grind away in the corner, siloed, performing its tasks while engineers and IT teams build new networks of independent systems to connect sensors needed for monitoring and optimization. Hypothetically, this strategy would allow organizations to bring data to key applica-
tions without having to deal with the complexity and expense of moving it through DCS controllers.
As teams have begun that journey over the last decade, they have learned a valuable lesson: process optimization requires data contextualization. Leaving out the DCS and its ability to contextualize data results in a decreased ability to effectively use the collected data. This forces teams to find new ways to integrate systems and gather context, which increases complexity, making it extremely difficult to maintain the resulting systems of systems, while reducing flexibility to drive future business.
Forward-thinking automation suppliers have taken note of this conundrum and are evolving the modern DCS. Instead of an architecture based on everything passing through controllers, the DCS is evolving into a comprehensive, software-based automation platform that is data centric, secure, extensible and easy to use, while maintaining its out-of-the-box capability to integrate different applications.
As a result, the best strategy to improve optimization is not to build complex rings of new solutions around a controller-centric DCS, but rather to engineer with a modernized DCS at the center of the automation strategy. Doing so empowers organizations to take advantage of new capabilities and prepare for the coming paradigm shift, where operational excellence will be driven by a data-centric DCS at the heart of a comprehensive automation platform.
When people think of control systems, they typically imagine field devices communicating with input/output (I/O) cards, which then transmit that communication to a controller and display the result on a human machine interface (HMI) in the control room. Yet today’s modern DCS solutions are already so much more than that (Figure 1). Technologies like advanced process control, alarm management, device management, advanced ana-
‘ DCS is becoming data-centric and secure, while efficiently moving data and providing real-time control. ’
lytics, historians, simulation, advanced HMIs, opensource cross-platform unified architecture (OPC UA) and other applications are critical to managing complex processes with tighter control and lower variability. They are a part of the DCS. Breaking applications into disparate solutions to isolate control quickly creates complex custom-engineered connections that require significant overhead to manage and maintain.
A better approach is putting a modern DCS at the center of an automation platform, providing organizations with the ability to build solutions that provide all those capabilities but without the required complex engineering effort.
New technologies at the edge continue to increase the data flow from the DCS to external systems. Edge environment solutions provide secure data mobility via a data diode, unidirectionally moving data from the control system to a wide array of third-party applications, simplifying and making it more cost-effective to distribute contextualized DCS data to optimization applications running anywhere.
In coming years, new technologies like Ethernet Advanced Physical Layer (APL) will reshape the face of control, bringing more data from more devices connected via much faster networks. Not only will plants need a way to bring that data into their automation architecture — a task best accomplished with a modern control system that is Ethernet-APL ready — they will need ways to keep it moving efficiently through the control system to other applications. Doing so efficiently and affordably will require avoiding the need to perform complex engineering.
Modernizing to a new DCS designed to operate at the heart of a comprehensive automation platform is the solution. Automation suppliers are piloting new technologies, such as enhancing DCS flexibility with software-defined controllers. This decouples the controller software from hardware and creates new data paths to move data through the DCS more efficiently
and effectively. This makes it easier to apply context, without adding complexity or reducing flexibility.
Innovators are designing new data fabrics, leveraging open protocols like OPC UA and MQTT, to move the control system from its primary focus on PIDs and interlocks. This evolution will create a platform for data-centric, secure, and efficient movement of data — while still providing real-time control. This new platform will allow a wide variety of applications to be fully integrated, benefiting from the contextualized data from intelligent field devices, without relying on controllers as the single data pathway for field data.
Boundless automation is the end goal where automation systems come together, without silos, to deliver operational excellence. As sustainability, reliability and efficiency goals continue to put pressure on teams to accomplish more with the automation they have, the boundless automation-driven integrated architecture for seamless data mobility from field to edge to cloud will help them accomplish those goals.
Legacy DCSs have an overdependency on controllers, which makes handling field data and interacting with other systems significantly more complex. Isolating the DCS by creating new architectures (and, by proxy, new silos) for every necessary functionality is not the answer — the data contextualization from the control system is too valuable. The right step is to modernize the DCS and position it at the center of the modern automation platform, leveraging available advanced functionality that is available, as well as preparing for new technologies and capabilities. ce
Claudio Fayad is vice president of technology of Emerson's process systems and solutions business.
FIGURE: Modern control systems incorporate advanced process control, alarm management, device management, advanced analytics, historians, simulation, advanced HMIs, OPC UA, and more to create a cohesive, connected solution that eliminates data silos.
Courtesy: Emerson
u A distributed control system is critical to effectively analyze the data collected by automated organizations.
uDistributing contextualized DCS data provides a simpler and more cost-effective way to optimize applications.
Gilles April, PE, GICSP, CDM Smith
Artificial intelligence (AI) and neural networks (NNs), as empirical model-based tools, can be used in a feedback closed-loop control implementation. A described project created provided the basis for the explanation.
Aproject used a neural network (NN) solution after consideration and testing to provide complex closed-loop control of a nonlinear multivariable application. The goal was to develop an NN solution that would be used to control the viscosity of the resin produced by a chemical reactor unit. It had been a trial-and-error process until the project team applied the NN-based control system, which determined the relationship between input chemical materials mass, other variables, and the resin viscosity. Once the NN model was developed and applied to the chemical reactor, which functioned as a black box, operators could determine the targeted resin viscosity and know, using the NN model, which input chemical material mass to vary and by how much to achieve the target. Developing this NN model was not easy; the team
involved learned a great deal about key success factors, described below.
Using AI, NN for control
AI and NNs, as empirical model-based tools, can be used in a feedback closed-loop control implementation. Feedback closed-loop control is a control strategy that aims to control a process variable at a setpoint value by modulating an output element affecting the measured process variable and measuring the resulting change in the process variable, which provides feedback to the controller until the difference between this measurement and the setpoint value (error) is zero. In feedback closed-loop implementation, the NN model can be used to predict the measured process value instead of measuring it from an instrument. The NN engine in this kind of application is often called a soft sensor.
NNs are the backbone of deep-learning algorithms, which are a subset of machine learning, and which is a subset of AI. There are other AI algorithms similar in function to NNs, but in feedback closed-loop control implementation, they function similarly. For this example, NN is used as a base prediction algorithm. Other AI algorithms would be used in the same manner.
It’s necessary to understand the concept behind these algorithms, particularly the NN algorithm. The NN algorithm uses a dataset to determine the relationship between input data variables and output variables, creating a model. This method can work with variables that are simple in relationship, or work in very complex, nonlinear multivariable applications, such as that developed for the resin reactor project, to use the mass of different chemicals (input) in determining the viscosity of a compound (output) when a chemical reaction is present.
FIGURE 2: Neural Network diagram
An NN is much more complex in nature and more difficult to implement than simply using a first-principle formula like speed=distance/time. NN is not necessarily the best tool for a simple linear application but is a powerful and useful tool for complex applications where other methods, such as first principle, fuzzy logic control, advanced regulatory control or model-prediction control, cannot provide the required reliable functionality. Figure 2 shows how a simple NN works.
An NN approximates relationships between input and output values by training (modifying the weights of an NN’s hidden layers) and then, using this knowledge, predicting output values if different input values are fed into the algorithm. This prediction is an approximation in which the precision can be adjusted.
Figure 3: Simple NN model applied to predict the measured value speed in feedback closed-loop control implementation Courtesy: CDM Smith
As an example, we analyze the following simple NN algorithm in Table 1. The NN algorithm analyzes the two input variables, distance, and time, in relation to the output, which is the speed. While in training, it adjusts values (weights) in the NN hidden layers until the overall model reflects the dataset variables’ relationships.
When the algorithm determines it has almost 100% confidence in its determined relationship, it can end its training phase, and it is ready to be fed with other numeric input values to calculate (predict) the corresponding output in Table 2.
The reliability and precision of the forecast value for speed is relative to the validity and exactitude of the base dataset and the defined precision of the NN implementation. In our example, all predicted values are estimated. As we can see in this example, the forecast value by the NN algorithm is less precise than using the first-principle formula speed=distance/time.
Now, in the real world, each measuring instrument has an error margin, even if the instrument
Table 2: Prediction phase based on static values and training from the previous set
Table 3: Training phase using more realistic instrumentation-based values and associated errors
Table 4: Prediction phase based on instrumentationbased values and associate errors
has just been calibrated. This means that repetitive measurements of the same variable would be either similar to or within the margin of error associated with the instrument. Instruments can also become mis-calibrated with time. A more realistic version of the above dataset, with measurements and errors, could look like Table 3.
After being trained with the previous table to determine the relationship between the inputs, dis-
3: Simple NN model applied to predict the measured value speed in feedback closed-loop control implementation
tance and time and the output speed, the NN could provide the following results in Table 4.
Online controleng.com
KEYWORDS: AI for feedback closed loop applications
LEARNING OBJECTIVES
Understand the neural network (NN) basic function.
Learn the importance of data quality used in NN or other artificial intelligence (AI) applications.
Explore the basic principles of using AI, particularly NNs, in a feedback closed-loop application.
CONSIDER THIS
Are you using AI and NN to improve your feedback closed loop control applications?
ONLINE
https://www.controleng.com/ ai-machine-learning
Instrument error and miscalibration affect the precision of the NN prediction. Instrument calibration, which drifts in time, could have a bigger effect than inherent instrument error, or vice versa. The NN prediction is as good as the quality of the match between the values used to train the algorithm and the values used as inputs to get a forecast output value. This could lead to high variability in the quality and accuracy of the NN forecast value, which, in a feedback closed-loop control scheme, could have a very erratic and unwanted effect. Another factor influencing the precision of the NN forecast values is the coupling between the input variables. The input variables should be as independent as possible because the coupling between inputs will affect the precision and reliability of the forecast values. Selecting the right independent variables to be part of the NN could be challenging but is critical. This is often a trial-and-error process.
To have better precision and reliability in the NN forecast values, tight control of the quality of the data fed into the NN algorithm is required. At a minimum, gross error detection should be performed on the data, and ideally some data validation should be used to increase the quality of the dataset. This part is often skipped in an NN control application, leading to poor
control loop performance. Another factor is that the model should be trained with enough data to cover the entire spectrum of operational data. The better the quality of the dataset, the better the chance of obtaining a good and reliable prediction. Clamping the prediction values helps ensure the values are within expected boundaries.
Some applications are challenging for NN or other AI algorithms implementation. Applications related to a stable measurement with minor change over time in the plant process or equipment characteristics are the most suitable to successfully implement in an NN or AI environment, while applications in which the equipment or plant process is changing because of wear, aging, or other factors are less suitable. In this case, the NN must be trained more often to keep its model up to date. Between training sessions, the NN prediction quality is affected because the dataset used to train it originally does not reflect reality anymore. And while in training, no prediction is produced.
Once the NN algorithm is developed with a high-quality reliable, validated, non-degrading, finite-input dataset with operational boundaries and with independent variables, it can be successfully implemented in different control schemes. Simple feedback closed loop using some arrangement of controllers (such as proportional-integral-derivative or PID control), can be successfully implemented. More complex controller design approaches are also feasible.
Another challenge for both NN- and AI-based controls implementation is having trained personnel to maintain it in a fully acceptable functional state. Personnel resourcing is critical to implementation success and can be hard to fulfill.
Overall, NN- and AI-based feedback closed-loop or other controls methodologies should be applied to specific complex, nonlinear, multivariable applications. These algorithms are too complex and not the most cost-effective or easiest-to-maintain reliable approach for simple applications. ce
Gilles April, PE, GICSP, senior automation engineer, CDM Smith; Edited by Mark T. Hoske, editor-inchief, Control Engineering, WTWH Media, mhoske@wtwhmedia.com.
Aaron Block, Inductive Automation
Most American foundries are family-owned and privately held small- to mid-sized companies that have minimal capital to invest in digital transformation initiatives. In an increasingly competitive market, organizations like Ferroloy, Inc., a 50,000 squarefoot cast iron foundry and machine shop in Wichita, Kansas, understand new approaches and innovative technologies vital to success.
Ferroloy needed to find an alternative to its highly manual data collection processes, which were riddled with inaccurate and unused data. The company wanted a solution to improve throughput and quality, reduce equipment downtime, and integrate with its existing software and specialized machinery. This was top-of-mind for Mark Soucie, Ferroloy’s president and owner, when he attended a presentation from Folsom, California-based system integrator Artek Integrated Solutions about the ben-
efits and return on investment of a connected, integrated factory. Ferroloy chose Artek to implement an industrial automation platform for SCADA, HMI, IIoT and more into its foundry (Figure 1).
SCADA implementation as a team effort
SCADA systems are not as common in foundries as Excel spreadsheets or scratch paper (see Figure 2).
“The truth is that a lot of other foundries are looking for something like what we've implemented for Ferroloy, and they just don't know where to start,” said Jerry Eppler, co-founder and chief executive officer of Artek. “Mark [Soucie] was in the exact same position and thankfully found us at the right time and right when he was beginning his journey, and we helped guide him through this process to really take the ideas that he had and the opportunities that he knew were there and really bring them to fruition.”
To ensure the success of the project, Soucie brought on an in-house engineer, Clint VenJohn, as process engineer at Ferroloy. VenJohn, with Jim LaPratt, design service engineer at Artek, were instrumental in designing and implementing Ferroloy’s industrial automation platform, even though each came differed in software experience levels. LaPratt had 25 years in the foundry industry, combined with extensive knowledge of the platform. VenJohn had no prior experience. Far from a setback, between VenJohn’s OT background as a plant operations manager and strong knack for IT, and free learning resources from the vendor, he was quickly contributing “some marvelous ideas” to the project, LaPratt said.
With this Ignition system, Ferroloy wanted to implement lean manufacturing practices to drive overall behavioral change and to rely more on systems versus individual skill.
“What we're trying to accomplish is to digitize an aged process and gain better visibility to unlock the latent potential within the process,” said VenJohn.
Previously, data was mostly used to solve individual problems rather than to bolster companywide initiatives. To create a SCADA system that was beneficial to operators as well as upper management, Artek built and configured a MySQL database on Ferroloy’s servers, which was then connected to industrial automation platform, specifically a tag historian module, as a centralized repository for maximizing data collection and analytics. This combination created a single source of truth anyone could reference (see Figure 3).
“The goal with the Ferroloy project was to digitally transform their disconnected foundry that relied heavily on manual paper data collection through efficient data collection and analysis,” said Eppler.
Ferroloy’s target is to increase capacity by 25 to 30% while reducing scrap by 30 to 35%. The industrial automation system allows Ferroloy to identify methods for improving efficiency, backed by quantitative data. With the new software, “we're able to see more or less up-to-the-minute production data, whereas before we would lag behind by a week or so,” said VenJohn, to identify trends and shift reports. "Those have been huge improvements and have allowed us to identify and more quickly react to problems.”
The industrial automation platform was a cost-effective solution for achieving this new level of data collection, which is critical for a foundry the size of Ferroloy. The low initial cost isn’t what gives Soucie confidence; it’s the flexibility to adapt and make changes quickly based on real-time data. With the
3: Ignition’s Tag Historian Module created a single source of truth.
‘ We could see up-to-date production data, compared to a week or more lag previously. ’
data analytics facilitated through the new software, Soucie said the opportunities could be endless.
The digitization process proved more complicated than a simple transition from paper to human machine interface (HMI). There was also a human element. The last thing Ferroloy or Artek wanted was to distract operators in a fast-paced environment while they were pouring 2,700ºF molten iron (see Figure 4).
While the initial impulse was to adhere to a high-performance grayscale philosophy, LaPratt and VenJohn adapted their approach to better suit the workforce, keeping the screens straightforward, focusing on ease of use and legibility.
“We have a lot of employees out there that are not very tech-savvy, some older and some that there's a language barrier with. The simplicity of [the HMI] just makes it easy for them to interact with and be able to do what they need to do easily and properly,” said VenJohn.
All visualization for the system was designed using the software, and each screen features a minimal set of buttons, reducing interaction to the essentials of a given process. With so few visual components, the HMIs needed to retain color to make key information “pop” so that operators could quickly ascertain the status of the process in progress.
controleng.com
KEYWORDS: Industrial automation platform, SCADA
Understand how Ferroloy, a foundry headquartered in Wichita, Kansas, automated its data collection processes to establish a connected, integrated factory.
Grasp steps needed to automate in ways that help connect systems and processes.
‘ The new software brought previously siloed data into screens to verify that products are good at the point of use.’
u
SCADA and ERP insights
uInvesting in digital transformation initiatives can help industrial plants remain competitive.
uIncorporating industrial automation platform for SCADA, HMI, IIoT and more can help industrial plants gather data seamlessly and make processes safer and faster.
“Due to the extreme heat needed to melt iron, safety is a high priority in a foundry. We wanted to make sure our screens were extremely intuitive and simple as to not distract operators from the potential hazards around them,” said Eppler.
Ferroloy, like many foundries, has a heterogeneous mix of programmable logic controllers (PLCs) from a variety of manufacturers across a range of vintages, plus other types of equipment that do not communicate via PLC at all.
The industrial automation platform has a suite of device drivers that allowed Ferroloy to connect to all their hardware. This freedom also sparked ideas for additional creative solutions; the foundry environment is inherently dusty, making it particularly harsh on electronics, so Ferroloy needed a software that could run on equipment that was inexpensive to replace. Ferroloy is using smart televisions to display key performance indicator (KPI) dashboards above each of the six production lines for quick reference.
“Ferroloy’s main problems were that the data that they were gathering on the floor was siloed from their equipment through that software. If you needed that information, you had to walk there to get it,” said LaPratt. The new software “brought the siloed data from their Hitachi and Heraeus equipment directly into screens that could be used on the floor for verification that the product was good at the point it was being used.”
Connecting the new software to Ferroloy’s Sinto molding machines allowed molding production data to be fed back to the ERP system through an API. This eliminated the need for the operator to input the data on the floor and reduced the risk of data entry errors (Figure 5). Originally, Artek planned on using a third-party solution to connect the industrial automation platform to the PLCs collecting data from the molding machines, but thanks to some fortuitous timing, the software vendor released a needed PLC driver during the project’s development phase. The driver, which supports the industrial communications used in the PLC, allowed for a direct connection, eliminating the need for any additional software and lowering the overall cost of the project in the process.
Artek needed to integrate the industrial automation platform with an off-premises ERP software-asa-service (SaaS) Ferroloy implemented over a decade prior. Pulling data from Ferroloy’s ERP system was a cornerstone of the project, eliminating data reentry and its corresponding human error. Artek created sync routines that run through an API interface to monitor Odyssey and look for changes in real time. The integration of the industrial automation platform and the ERP is vital because certain steps in the iron casting process have rigorous time limits. The HMI displays what is currently on all six pour lines, each of which have molds coming down them, along with data synced from the ERP system. This allows operators to know what is being poured when they tap the furnace and put the molten iron into the ladle, because once a new ladle is started, the iron is only usable for 10 minutes. ce
Aaron Block is a case study program manager with Inductive Automation.
Steven Palma, Robotics Software Engineer, ZettaScale, Paris, France
Zenoh’s adoption by ROS 2 not only sets the stage for next-gen robotics but also slashes energy use.
Open-Source Robotics Foundation (OSRF) announced September 2023 a non-DDS robotic middleware (RMW) alternative to be adopted by the Robot Operating System 2 open-source project (ROS 2). The main motivations for this change are to overcome communication technical limitations, improve the out-of-the-box experience for new users and create a more robust RMW abstraction layer. Zenoh, the communication protocol was chosen as the new RMW, contributes to this energy transition and helps the robotics space.
When examining the energy efficiency of communication protocols, three key elements are important. The first, known as processing efficiency, measures the amount of work required to create and process a packet during user-data transmission and reception. The second, referred to as wire efficiency, quantifies the additional bytes a protocol adds on top of user data. The third, routing efficiency, considers the distance — or network hops — data must travel. Traditional protocols like the data distribution service (DDS), which have been the backbone of ROS 2 since its creation, come with significant wire overhead. DDS adds 56 bytes on top of every data message to ensure participant discovery, reliable delivery, message order, Quality of Service (QoS) policies, and more. While necessary for its proper functionality, excessive overhead slows down communications and reduces wire efficiency. Intuitively, moving large amounts of overhead bytes across the network leads to an increase in energy con-
sumption, which makes operating a robotic system more costly.
Protocols like message queuing telemetry transport (MQTT) require all data exchanged by the applications to go through a cloud-based broker, which might be located far away from the devices, even for local communication. A high-routing efficient protocol would enable direct communication between devices on the same network, moving data through the shortest path available and reducing network hops. The topology constraint of MQTT results in the data having to be relayed and traveling longer distances, enlarging energy expenditure.
The wide industry adoption of protocols like DDS and MQTT has made the communication stack of robots a power-hungry endeavor. Many autonomous mobile robots (AMRs) can use up to 50% of their operational energy without even moving, spending their battery only on data communication and processing. For a modern AMR, this is about 3kW. Reducing protocol overhead and improving data routing are crucial steps toward minimizing energy waste and enhancing the overall robotic performance.
Zenoh is a novel pub/sub/query protocol designed to unify data in motion, data at rest and computations across the cloud to micro-controller
FIGURE 1: Zenoh is an Open-Source Software (OSS) project under the Eclipse Foundation. Images courtesy: ZettaScale
Open-source robotics
u A high-routing efficient protocol enables direct communication between devices on the same network, moving data through the shortest path available.
uZenoh was engineered to tackle the energy inefficiencies inherent in traditional communication technologies.
continuum. It offers a set of unified abstractions and supports different network topologies like peer-to-peer, routed, mesh and brokered communication. Zenoh runs efficiently on server-grade hardware and constrained microcontrollers and networks (see Figure 1), featuring a minimal wire overhead of 5 bytes, low latency and high throughput performance. Zenoh has been engineered from the ground up to tackle the energy inefficiencies inherent in traditional communication technologies. Unlike DDS, Zenoh reduces the energy required for discovery data transfer in robotics applications by up to 90% (see Figure 2). This reduction is achieved through a combination of minimal overhead and an innovative discovery approach. While DDS adds 56 bytes per message, Zenoh lowers this overhead to as little as 5 bytes. While DDS’s dynamic discovery information provides precise and extensive details about participants’ availability in the system — quickly leading to scalability issues — Zenoh employs sets and set-theory operations to generalize information distributed across the network, reducing discovery traffic and enhancing wire efficiency.
Unlike MQTT, Zenoh can facilitate local communication by not imposing any constraint on the network topology of the system, allowing devices to communicate directly or through minimal interme-
diary steps without needing a broker. This locality allows Zenoh to minimize network hops, achieving not only faster but also far less energy-intensive communication. Zenoh's wire and routing efficiency enables it to perform exceptionally well on both constrained hardware and low-power networks.
What about the processing efficiency? According to a study by National Taiwan University (NTU) researchers, Zenoh’s throughput is largely higher than other protocols — 10 times greater than MQTT’s and approximately five times higher than DDS’s. In a single-machine scenario, and similarly for a multi-machine one, Zenoh in peer-to-peer mode outperforms DDS by roughly 2x, MQTT by 130x, and Kafka by 65x at an 8-byte payload size. This means Zenoh requires significantly less central processing unit (CPU) power to handle the same amount of data.
Zenoh's flexibility in supporting various communication topologies, combined with its ability to manage high throughput with low latency and minimal overhead, made it the preferred RMW alternative for ROS 2. Zenoh also addresses many other long-standing challenges in robotic system deployments, particularly those critical for robot-to-anything (R2X) applications. Zenoh facilitates easy integration by supporting a broad range of network technologies, including transmission control protocol/internet protocol (TCP/IP), user datagram protocol/IP, quick UDP internet connections (QUIC), Serial, Bluetooth and more. Its extensive plug-in ecosystem allows for interoperability with other existing protocols in the risk management framework (RMF) system without significant modifications. Zenoh’s capability to scale is particularly beneficial for deployments requiring robust communication across large robot fleets. With a unified application programming internface (API), it enables developers to focus on creating a more responsive RMF and fleet of robots more simply, rather than dealing with network complexities (see Figure 3).
Zenoh's proper use of resources aligns with the growing emphasis on sustainability in technology. Reduced energy consumption translates into lower operational costs and a smaller carbon footprint. ce
Steven Palma is a robotics software engineer with ZettaScale.
Dino Busalachi, Barry-Wehmiller Design Group (Formerly Velta Technology
In the modern digital landscape, the C-suite and board of directors play a pivotal role in securing operational technology (OT) systems.
In today’s increasingly connected industrial landscape, cybersecurity for manufacturing environments and critical infrastructure has become a critical concern that demands attention from the highest levels of corporate leadership. The C-suite and board of directors play a pivotal role in addressing the unique challenges of securing operational technology (OT) systems.
The potential costs of inadequate OT security for adverse cyber events are staggering. Every business knows their “number” when it comes to the cost of plant downtime, whether it’s half a million dollars a day, a hundred thousand dollars per line or whatever your metric is. Cybersecurity incidents can lead to production disruptions, safety risks and significant financial losses. Moreover, regulatory pressures are increasing. The SEC is now mandating reporting requirements for cybersecurity incidents, and organizations are facing growing liability concerns
Executives and the board of directors are being held liable and responsible, personally in some cases, for failing to provide due diligence in securing manufacturing or critical infrastructure environments.
To address these challenges and minimize cybersecurity risks, the C-suite and board must take an active role in OT security. The following steps can help them get up to speed:
1. Recognize the unique nature of OT security: Understand that IT security practices alone are insufficient for protecting manufacturing environments.
2. Allocate resources: Invest in OT-specific security tools, training and personnel.
3. Foster collaboration: Encourage cooperation between IT and OT teams, breaking down silos that hinder effective security measures. A tabletop exercise involving both teams is a good first step.
4. Engage with OT vendors: Build relationships with reputable automation technology vendors and experienced system integrators to understand and address security concerns.
5. Implement continuous monitoring: Deploy tools for ongoing asset inventory and vulnerability management in OT environments. A one-time snapshot of plant floor vulnerability is not sufficient in today’s heightened state of cyber risk.
6. Develop incident response plans: Create and regularly practice OT-specific incident response procedures. Involve both the OT and IT teams in this effort to share knowledge.
7. Address supply chain security: Work with suppliers and OEMs to ensure they meet the highest-level cybersecurity standards.
8. Lead by example: Make OT security a priority, and communicate its importance throughout the organization. Simply passing the baton to IT is guaranteed to leave the organization vulnerable.
By taking proactive steps to address these issues, C-suite executives can protect their organizations from potential disasters and position themselves as leaders in an increasingly security-conscious industrial landscape. ce
Dino Busalachi is director Barry-Wehmiller Design Group (formerly Velta Technology). Edited by Gary Cohen, senior editor, Control Engineering, gcohen@wtwhmedia.com.
Cybersecurity insights
uCybersecurity incidents in manufacturing and critical infrastructure lead to severe production disruptions, safety risks, financial losses and increased regulatory pressures.
uTraditional IT security practices are often insufficient for protecting industrial environments.
uExecutives must prioritize OT security.
DoShik Wood, Stratus Technologies, an SGH brand
Digital transformation is an ongoing journey for manufacturers, driven by the need to enhance efficiency, insight and safety without disrupting operations. Modernizing control platforms offers a strategic opportunity.
Digital transformation has aptly been described as a journey, and it’s a journey that nearly every manufacturer has been on since the introduction of Industry 4.0 a decade ago. Each organization goes at its own pace, with different stops along the way toward the goal of new efficiency, insight and safety. While each path is different, the commonality is the need to change without disrupting the business.
Day to day, digital transformation manifests itself most practically at the ground level. For most organizations, there are limited windows to make a technology change, and any change must be weighed against potential risk, impact or disruption to operations.
Modernization of control platforms provides a key opportunity to leverage new technologies to improve current operations as well as lay a foundation for long-term growth and digital innovation. These projects are often catalyzed by a few common drivers where the business must adapt:
• External triggers: Upgrading processes and data capture to meet compliance with new regulations, reporting requirements and/or industry mandates that are often environmental or security related.
• Reliability: Organizations looking to the break-fix cycle or that have faced too many disruptions under the umbrella of data loss and downtime
(planned or unplanned). Each can introduce risk into the business as well as divert teams from higher-value work, particularly innovation and transformation.
• Supportability: Underlying computer hardware is no longer supportable due to parts, application support or OS support. Applications may be versions behind and out of vendors’ support windows.
• More computing power: Modern software that conveys new capability and security requires new levels of compute and memory capacity. Additionally, older infrastructure is not equipped to support interaction with cloud applications, having been deployed years ago for traditional on-premises operations. Organizations can take advantage of these opportunities to build and deploy modern control architectures that are future proof and provide the reliability and computing power to support evolving requirements of the business. Deploying a resilient and flexible edge compute infrastructure provides the foundation for increased automation and digitalization through software deployment and data acquisition. It opens the door to invite other functions to the table for cross-functional alignment of current and future needs.
Digital transformation outcomes are predicated on the ability to translate the abundance of data generated into actionable insights. Automation and control generate most of this data at edge locations. Automation and control platforms today are increasingly software driven, requiring greater processing power and a level of reliability far beyond the traditional off-the-shelf computing platforms or traditional industrial PCs (IPCs) the industry has relied on for years as good enough.
Organizations now want it all. They’re looking
for one “box” they can deploy in any environment whether on a remote asset, the factory floor or in an operations center — with the power to run any software stack they choose. They want to use open, vendor-agnostic tools, re-task equipment, deploy new software without disruption and run the box remotely without downtime or human touch.
By converging operational technology (OT) and information technology (IT) tools and techniques, teams can deploy a single hardware box that supports all those needs. They can have production applications in one computing platform that is accessible remotely, with open, non-proprietary standards. This enables organizations to deploy their own stack wherever they need it and run it with maximum reliability, with little if any touch. Using a core set of technologies — fault tolerance, virtualization, containerization, remote management and cybersecurity — organizations are building a futureproof control platform for current and future needs.
Some of the most fundamental aspects of digitalization are the availability of computing resources and the reliability of those resources to run without unplanned downtime. More than ever, OT and IT teams must jointly select purpose-built compute hardware capable of meeting current and future needs. As control architectures become more complex and run higher-level production software, it is essential for computing resources to run continuously with minimal on-site IT support.
There are now fault-tolerant servers available that combine redundant internal CPU, storage, I/O and power sources with monitoring software to predict failure and proactively resolve issues to deliver 99.99999% availability. This hardware-based fault tolerance in one computing platform reduces the failover latency to seconds (vs. the failover of a cluster) and requires a fraction of the complexity and cost of standing up and managing a cluster, not to mention the recovery time if it fails.
This level of computing reliability opens doors to new flexibility and the ability to comfortably consolidate the existing computing infrastructure and deploy more complex software stacks. A control engineer, for example, gains the option to move control into a fault-tolerant platform and can now decide whether to continue to use traditional programmable logic controllers (PLCs) or move the logic to a control platform — or even embrace use of software-based PLCs.
By using such platforms, organizations are able to go years without unplanned downtime or the need to refresh computing infrastructure. This reliability matches the long lifespan of OT assets that teams are accustomed to, rather than the three-year tech refresh cycle of typical IT equipment.
‘ Modernization of control platforms provides a key opportunity to leverage new technologies to improve current operations as well as lay a foundation for long-term growth and digital innovation.’
Operations teams need to deploy a range of production applications. Building on the fault tolerance of a computing platform, teams can consolidate software workloads. Virtualization provides the means to deploy multiple applications as partitioned individual virtual machines (VMs).
Using virtualization, the core human machine interface supervisory control and data acquisition (HMI SCADA), distributed control systems (DCS) and historians continue to run on the platform, but as virtual machines. They may easily be supplemented with batch capability or complemented with engineering workstations. Running multiple VMs enables a team to run applications from multiple vendors simultaneously. A single compute platform with virtualization may run Rockwell Automation PlantPAx alongside AVEVA System Platform and Inductive Automation Ignition. Virtualization provides an efficient way for teams to deploy all required software.
Importantly, manufacturers can connect to cloud implementations, particularly for manufacturing execution systems (MES) integrated into enterprise resource planning (ERP) and order operations at the enterprise level. This integration is essential for multisite deployment and standardization. Depending on the compute platform sizing, organizations are running anywhere from three or four VMs up to a few dozen on one platform. The virtualized software stack running on a fault-tolerant computing platform provides full reliability and prevents any computing downtime for the applications. Virtualization
controleng.com
KEYWORDS: Digital transformation, digitalization, Industry 4.0
LEARNING OBJECTIVES
Understand the critical role of fault-tolerant computing platforms in ensuring continuous operation and minimizing downtime.
Explore how virtualization and containerization technologies optimize software deployment, flexibly with scalability.
Evaluate the integration of edge orchestration and remote management techniques.
CONSIDER THIS
In the modern, highly connected industrial environment, how can manufacturers modernize control platforms to ensure reliability, scalability and future-proofing while supporting digital transformation?
‘ [Organizations are] looking for one “box” they can deploy in any environment — whether on a remote asset, the factory floor or in an operations center — with the power to run any software stack they choose.’
is a key tool for OT teams to deploy layered software, re-task equipment and support software deployment.
Applications are deployed as containers, a software package that contains all codes and dependencies. This allows the application to run consistently across computing environments. For operations teams managing heterogenous environments, containers provide an approach to deploy with consistency. These applications are then managed through orchestration. Common applications include Docker and Kubernetes.
Digital transformation insights
uFault tolerance, virtualization, containerization, remote management and cybersecurity enable reliable, flexible and scalable control systems.
u A vendor-agnostic "one-box" edge solution simplifies operations, supports multiple applications and enables seamless remote management and upgrades.
uUpgrading control platforms enhances operations, meets compliance and lays the groundwork for longterm innovation while minimizing disruptions.
Containers provide a useful complement to VMs for a few reasons. First, they provide the ability to deploy software or potentially test in a lighter-weight package that offers continuous updating and deployment. Second, use of containers and orchestration (discussed in the next section) is well understood by IT teams. They provide IT teams with segmented space on an OT compute platform, and IT applications can easily run alongside OT applications. From an OT standpoint, running containers within a segmented VM provides a landing spot for IT to deploy applications without risk of disrupting OT applications running in parallel VMs. Continuous deployment with containers meets OT and IT requirements to evolve software and deploy new software in an ongoing fashion without disrupting operations.
Remote management has always been a key requirement in automation and control, particularly related to stranded assets or remote sites with limited IT staff. Many options exist today to build remote management into the control platform, and they are a key element in the control platforms of the future.
Teams can deploy thin managers and remote desk-
top to monitor asset performance remotely. Many organizations strive for the single-pane-of-glass functionality and visibility of operations. Connectivity via OPC UA is another simple means of connecting the control platform into the operations center. The platform also offers store forward of data in the event of intermittent connectivity due to network disruption or low bandwidth WAN connectivity.
Perhaps of greatest emerging interest is the technique of edge orchestration, which is a method of deploying software one-to-many from a centralized location. This method of easily deploying and updating software is well established in the IT world and is now more common in OT applications. It allows continuous integration and continuous deployment (CI/CD) for rapid updates. Using this approach, teams can remotely deploy new software and incorporate DevOps approaches into the OT world.
Cybersecurity concerns and considerations are perhaps the most consistent requirement and often the top issue for OT and IT teams. Any modernization project or software deployment catalyzes the discussion of cybersecurity, a topic that often brings OT and IT teams together to find a joint solution.
Cybersecurity teams often reference the NIST Cybersecurity Framework (CSF), which outlines specific capabilities for an organization to consider. It encompasses a range of software applications and myriad vendor choices. This full range of cybersecurity solutions can be deployed using virtualization to run alongside other OT applications. Vendors such as Fortinet, Palo Alto, Xage, Claroty, Dragos and others are well recognized in industrial automation and provide a comprehensive range of cybersecurity capabilities. Each also provides applications available as VMs. The fault-tolerant computing platform is crucial not just for enhancing cybersecurity applications, but also for delivering the essential reliability OT applications demand. This reliability enables IT applications to run on the same platform, allowing teams to streamline operations by managing one platform instead of maintaining two separate systems. ce
DoShik Wood, senior director, product marketing, Stratus Technologies, an SGH brand, Maynard, Massachusetts. Edited by Gary Cohen, senior editor, Control Engineering, gcohen@wtwhmedia.com.
ASTEPHANIE NEIL • EXECUTIVE EDITOR
rtificial intelligence, together with the adaptive data cloud, has profoundly changed operations in the warehouse and on the factory floor.
The ability to analyze data across the entire value chain is improving productivity, aiding maintenance operations, and creating new serviceoriented business opportunities. That was the message Microsoft’s Kathleen Mitford delivered in her opening keynote at the International Manufacturing
Technology Show (IMTS) 2024 in Chicago this past September.
From combing through CAD libraries to applying natural language models to maintenance records for delivering stepby-step instructions on how to fix a robot or even a jet engine, manufacturers have undergone an AI transformation. Everyone — from the CIO to the engineer to the operators — can access programs like Microsoft’s Copilot to act as a generative AI assistant.
The democratization of AI is an inevitable part of the factory floor going forward. “Basically, if [manufacturers] have not started on their AI journey, they’re late,” said Mitford, Microsoft’s corporate vice president of global industry marketing, in an interview with Automated Warehouse.
And if organizations are late with AI, they will miss out on the next evolution of AI, which is the democratization of automation.
During IMTS, there were examples of new products and services that unite AI and automation via programming, remote diagnostics, workcell workflows, and even self-service marketplaces to design and buy a machine online.
Here are just a few examples on display at IMTS that showcase these emerging areas of innovation:
Osaro: The Osaro Robotic Bagging System is an e-commerce robotic setup that can accurately scan and identify disparate items in a tote, effortlessly handle new SKUs, and quickly adapt to changing inventory. This allows the robot to pick and place multiple items into the auto-bagging machine and then to the conveyor to go out for delivery.
What’s different here is the company’s AutoModel. It allows AI to learn on the fly versus having to be trained, which is time-consuming, according to Brent Barcey, Osaro’s senior vice president of corporate development. Its rapid AI system allows for dynamic changes in the inbound and outbound flow of goods and the
integration of new peripherals, enabling the order-fulfillment line to adapt and evolve in real-time, ensuring continuous efficiency and productivity.
Olis Robotics: The company’s videobased remote diagnostic system watches a robot 24/7 on the packaging line or warehouse. Power over Ethernet cameras are set up around a cell, and when the visual system detects an issue, it saves the video files to allow an engineer to see what happened and even remotely take action.
Working with Universal Robots (UR), FANUC, and Kawasaki robots, the diagnostic system can connect to multiple robots through the robot controller. It also connects to the PLC that provides stats on what’s been going on for the past minute or past 24 hours.
“This is a pretty comprehensive diagnostic suite for automation,” said Olis CEO Fredrik Rydén, noting that the data allows for predictive maintenance as well. “When you have facilities that have a lot of volume of products going out the door, you want to keep them
running. This is a tool to ensure you can do that.”
In addition, by partnering with collaborative robot providers like UR, the goal is to make the robot experts more efficient, especially in the face of a labor shortage.
“What UR has been spearheading is the ability for anyone to adopt automation by making it easy to program the robots. Now it is easy to keep them running as well,” Rydén said.
Tulip Interfaces: This no-code system offers an almost effortless way to build applications, which could be workflows, traceability, dashboards, or machine monitoring, for example. The common data model includes templates for different applications that are available for download and includes application program interfaces (APIs) to connect other applications.
As part of the system, the operator is provided instructions, as well as
continuous feedback to show errors that may have occurred during a repeatable process. In addition, the Tulip starter kit provides pre-built applications that can be implemented in multiple ways. This allows small and large manufacturers alike to adapt the system to their processes.
“The goal is to democratize this so you don’t need to be an engineer to do it,” said Natalia Gutierrez, product marketing manager at Tulip.
Vention: When it comes to designing a machine, Vention is incorporating AI into the process to make suggestions on the next component – which is added automatically to expedite the design process.
On the automation side, Vention released a machine motion AI controller with NVIDIA Jetson. The low-power system is designed for accelerating machine learning applications and enables robots to learn in the cloud.
“We’ll have a robotics model in the cloud that will learn from the operation that is running to give you a better program for your robot for more efficient operation.” said Carl Hajal, Vention’s senior software and robotics segment manager.
He noted that Vention differentiated its AI offering by applying it both on the controller and in the cloud. When programming a robot, Vention has also added a co-pilot that can write a program for the engineer and push it into an existing script to update it.
Hajal claimed that this should accelerate programming by about 50% for engineers.
Vention is known for its self-serve platform, which allows OEMs to design automated equipment, robot cells, and tooling online, while providing real-time bill of materials and pricing information before the equipment is shipped out for assembly on site.
Now, with the proliferation of tools and cloud-based services that make automation accessible and easy to use,
self-serve marketplaces are popping up from different technology providers. igus: The motion plastics company makes flexible cables, chains, linear bearings, slides, actuators, motors, and more. The differentiator for igus products is its self-lubricating material, a proprietary blend, said Felix Brockmeyer, igus CEO.
Over the years, customers have asked igus to assemble its parts into entire systems. Now, the company has an internal startup, called RBTX by igus, which is an online marketplace that connects users with suppliers of compatible, cost-effective robotic components using simple tools.
“It started with small and midsized manufacturers and OEMs in mind, but now everybody is our customer base,” Brockmeyer told Automated Warehouse. “There is a need in the market to offer simple automation instead of what normally is overkill.”
To that end, pricing for specialized robot applications such as pick and place, material handling, machine loading and unloading can be offered at lower price than a traditional feature-rich system.
“There wasn’t an offering in the market to address people that just want to do simple automation tasks,” said Brockmeyer.
The igus robot control includes the company’s own open-source software, which can be downloaded for free to start writing programs before buying a robot. There are also application-specific overviews including videos showing how it works.
“It’s automation for anybody,” Brockmeyer said.
Universal Robots: The UR Marketplace was also a talking point at IMTS. It is a one-stop shop to choose and purchase cobots, components, and services. The platform offers a range of equipment from the UR ecosystem and a quoting and ordering management process and 24/7 call support. AW
For more news on AI and digital transformation in the warehouse, visit Design World’s sibling site Automated Warehouse at: automatedwarehouseonline.com
STEPHANIE NEIL • EXECUTIVE EDITOR
The addition of robots, motion control, and digital twin tools leads to a 90% improvement in overall logistics efficiency.
ABB’s Measurements & Analytics factory in the Italian village of Ossuccio — situated on the shores of Lake Como — produces pressure transmitters that enable industrial companies around the world to measure, monitor, and control applied force. This technology is key for both safety and efficiency and is a fundamental component in industrial digital transformation.
Today, the Ossuccio factory exports the majority of its components to other ABB factories around the world through its logistics center. It’s a midsize operation that has relied on warehouse workers to prepare products for shipment.
But ABB, like its industrial customers, continues to strive for efficiency through innovation — regardless of the size of the operation. So, the company used its own in-house automation, robotics technology and simulation capabilities to modernize the historic facility, which has been on Lake Como since World War II.
The modernization effort included the addition of ABB’s OmniVance FlexBuffer robot system, an advanced automated storage and retrieval system (ASRS) that manages all of the warehouse loading and offloading activities. According to the company, the robot not only transformed the warehouse into a fully
Autonomously transport materials up to 4,200 lb with the industry’s most comprehensive autonomous mobile robots and fleet management software.
Adoption of the AS/RS has alleviated the physical strain associated with manually handling heavy boxes.
automated operation, but it has also led to 90% improvement in overall logistics efficiency.
“We wanted to improve logistics at the Ossuccio site while also enhancing the entire manufacturing process,” said Mariafrancesca Madrigrano, general manager of the ABB Measurement & Analytics factory. “Upgrading the existing warehouse was an important project that we did together with our colleagues in robotics in order to align with the current state-of-the-art automation.”
ABB configures its own robots
The solution consists of two FlexBuffer systems connected by a conveyor, each one equipped with ABB robots. The control architecture includes ABB Group’s B&R Industrial Automation PLCs and HMIs to drive the conveyor system and robot control from ABB’s OmniCore control platform.
“These are palletizing/depalletizing robots handling a combination of either boxes or totes within a combined
The
application,” said Craig McDonnell, business-line managing director of ABB Robotics. “In this application, the FlexBuffer system is managing the inbound or outbound location of the totes, balancing of the tote or boxes between two separate buffering systems, and the complete software architecture to manage that.”
To that end, FlexBuffer allows for easy transitions between buffering,
storing, and sequencing tasks. It combines temporary storage and sequencing functions to provide additional functionality over traditional ASRS.
The mixed-item variant of the FlexBuffer enables the user to store a wide variety of box sizes, all being handled with the same robot gripper. And the dynamic racking positions all boxes with minimal loss of space.
The application at the ABB warehouse is an example of the scalability of the system, as ABB robotics are typically found in larger e-commerce sites, McDonnell said.
“Over recent years, we've found there's a big need for manufacturing processes to drive greater efficiency,” he explained. “Like in this plant, they were using a lot of robots in the end processes, be it welding or whatever it might be that you need for that specific process.”
“But the intralogistics feeding typically was the last part to be automated in many of these smaller factories. And the trouble was, it just ends up being too custom,” added McDonnell. “So, we've spent quite a bit of time coming up with a standardized modular system that you can use in small to medium-size facilities.”
The system was designed in ABB’s RobotStudio, a simulation tool for robot applications, which created a complete digital twin architecture. This reduces commissioning time as well as enables remote access after the installation.
“In the digital twin, we build a complete duplicate all the way down to the deep robot motion in the actual runtime engines. Then you have much quicker commissioning times and troubleshooting assistance,” McDonnell explained.
While the decision to deploy the ASRS in the warehouse was driven by customer needs, the digital transformation aspect was an extra benefit.
“The reason digital transformation is important is because the goal of ABB
is to serve the customer better,” said Madrigrano. “The big advantages have been that we’ve reduced the possibility of human error, and we’ve reduced throughput time.”
And the entire workforce benefits. Adoption of the system has enhanced working conditions for operators, alleviating the physical strain associated with manually handling heavy boxes.
In addition, many people were reallocated to other manufacturing areas that required additional manpower, giving the factory a greater flexibility during peak production times. AW
Scan the QR code to see ABB’s newly automated Ossuccio site
www.youtube.com/watch?v=gxc8-o8-WAA
Why accept a standard product for your custom application?
NEWT is committed to being the premier manufacturer of choice for customers requiring specialty wire, cable and extruded tubing to meet existing and emerging worldwide markets. Our custom products and solutions are not only engineered to the exacting specifications of our customers, but designed to perform under the harsh conditions of today’s advanced manufacturing processes. Cables we specialize in are LITZ, multi-conductor cables, hybrid configurations, coaxial, twin axial, miniature and micro-miniature coaxial cables, ultra flexible, high flex life, low/high temperature cables, braids, and a variety of proprietary cable designs. Contact us today and let us help you dream beyond today’s technology and achieve the impossible.
Emerging technologies are revolutionizing supply planning, enhancing supply chain efficiency, agility, and resiliency. Real-time data and advanced analytics driven by connected assets and systems help identify potential disruptions, mitigate risks and make informed decisions. We will discuss key insights into today's supply chain challenges.
What are today’s supply chain challenges?
The constantly evolving global supply chain landscape poses a range of challenges for businesses today that can impact their operational efficiency and effectiveness. Here are the biggest challenges:
• Business disruptions and market volatility: Over the past five years, supply chain operations in various industries faced unexpected events, which resulted in reactive responses. This can impede the ability to meet demand, leading to lost revenue, increased costs, and a decline in overall profit margins.
• Demand predictability: Social media, COVID driven direct-to-consumer (DTC) models, market volatility, and now inflation have made traditional demand forecasting insufficient. Operations are leaning on outdated forecast approaches that also lag and fail to respond adequately to current market dynamics.
• Holistic inventory visibility and optimization: Inventory management is complex and dynamic. The end of 2022-2023 saw excess inventory across many organizations due to COVIDrelated supply chain constraints. This led to higher costs, lower margins, and waste. The long term impact will lead to lost sales, and loss of differentiation, loyalty, and market positioning. Adopting an integrated approach and leveraging advanced technology and best practices, businesses can overcome these challenges - improving supply chain efficiency and resilience.
What is lacking in today’s supply chain strategies?
Supply planning today involves technology, data analysis and stakeholder collaboration. While technical and data analytic advancements have been made, there are still several areas that need improvements in the industry:
• Accurate transparency of data
• Dynamic supply planning and execution based on integrated intelligence and automated decision-making
• Convergence of network modeling, scenario and traditional planning and planning
Businesses want to improve supply chain visibility, predict, and mitigate risks, and optimize performance. Incorporating advanced concepts can enhance agility and resilience, meet customers’ evolving needs, and optimize performance. Below are a few advanced technologies and characteristics that must be included in an organization’s growth plans for supply chain optimization.
• Artificial intelligence and machine learning: Artificial Intelligence (AI) and Machine Learning (ML) can help businesses analyze data, find patterns, and make proactive decisions to mitigate risk. Many planning solutions have already integrated AI/ML into their core plans, but further integration of this can enhance algorithms. This could include detecting shifts and anomalies -- optimizing execution, automating operations such as key planning processes and real time decisions, and more.
• Digital twins and advanced simulation: Digital twins and simulation create virtual versions of physical assets, processes, and systems. These outputs can be used to evaluate scenarios and risk, identify key constraints, optimize, and evaluate alternative configurations.
With data and AI/ML, digital twins can continuously evaluate supply chains and networks, informing businesses in an unprecedented way.
• Automation and autonomous systems: The targeted deployment of automated storage retrieval systems (ASRS), autonomous mobile robots (AMR) and other assets with IoT connectivity, RFID asset tracking and machine vision can mitigate risks ranging from labor shortages to inventory loss. Working in tandem with digital twin and AI/ML, these assets comprise self-optimizing systems that drive higher output and efficiency by learning from both physical and simulated scenarios in the connected warehouse.
The future of supply chain planning requires digitization, automation, connectivity, and data-driven decision-making. Organizations that embrace these technologies create agile, transparent and efficient supply chains that are resilient to market changes and disruptions. AW
You can read more in our recent whitepaper, Synchronizing Supply & Demand in 2023 and Beyond.
Sustainability Report: Hormel Foods reduced packaging by nearly 1.7 million pounds in 2023
Many food and beverage manufacturers have committed to environmental, social, and governance (ESG) programs, stating specific goals around lowering emissions, addressing sustainability across the supply chain, reducing product and packaging waste, and providing a more inclusive workplace.
Hormel Foods is one of those companies focused on ESG and making a positive impact on the world. With over 20,000 employees and over 40 manufacturing facilities providing products to 80 or so countries, the company has a real responsibility that must be tracked — which it does. Known for its many brands, including Planters, Skippy, SPAM, Hormel Square Table, Justin's, Jennie-O, and more than 30 others, the company recently released its 18th Global Impact Report, highlighting areas of the organization where continuous improvement and responsible business practices made a difference in 2023.
To measure its accomplishments, Hormel set 20 qualitative and quantitative goals it expects to achieve by the end of 2030, tracked by a program it calls the "20 by 30 Challenge." While it covers many ESG angles, from a sustainability perspective, there's an effort to cut back on nonrenewable energy use, greenhouse gas (GHG) emissions, water use, and solid waste sent to landfills.
Another top priority in the sustainability category: Reduce packaging.
A key highlight of the company's 2023 progress includes reducing product packaging by nearly 1.7 million pounds. According to company officials, this was accomplished by optimizing packaging design and improving shipping efficiencies.
Stephanie Neil Executive Editor
The redesign of the Planters brand plastic bottle resulted in a projected annual savings of 440,000 pounds of plastic.
An example is the redesign of the Planters brand plastic bottle with a projected annual savings of 440,000 pounds of plastic, along with tweaks to avoid any issues with the recycling cleaning process. This follows work in 2022 when the Hormel engineering team redesigned Justin's peanut butter jars to use 30% less plastic, which will amount to over 165,000 pounds of materials saved annually, the company said. The packaging for Hormel Square Table entrees was also redesigned to include 25% of material from postconsumer recycling, saving over 382,000 pounds of material annually, and the thickness of the board for Jennie-O ground turkey boxes was reduced, generating over 1 million pounds of material savings annually, according to the company website.
When redesigning packaging where "less is more," the idea for the change may come from Hormel's R&D packaging team, a supplier, marketing, or even a customer request, but implementing the change is a collaborative effort, which includes machine builders.
"They are integral to the success of many of these projects," said Oliver Ballinger, senior scientist, packaging R&D at Hormel Foods, in an interview with Packaging OEM. Working with packaging engineers and the production team, new designs are tested on the packaging line and OEM feedback is provided on how changes perform on the equipment.
The design engineers utilize CAD and different 3D and simulation software for strength comparison of sustainable materials, Ballinger explained, noting examples of weak points on a bottle or digital top load strength. But much of the change comes from the creative solutions — the "what if" questions asked by engineers that lead to the ultimate solution.
The "what if" simulations can be done to determine where material distribution needs to be to maximize the strength of a bottle and accurately portray what the strength will be once bottles are physically produced, Ballinger said. "Without that technology, or with inaccuracies in that technology, it adds time, complexity, and cost to need to physically produce trial molds for bottles to be manufactured and tested just to find out they didn't meet the strength requirements or had quality defects."
After successful completion of those evaluations, the material goes through a series of pre-commercialization tests before full approval. If new equipment is utilized, a parallel path of factory acceptance testing (FAT) occurs with the equipment.
New sustainable designs are not only focused on reducing packaging waste but also food waste.
"We don't want to make a sustainable packaging change and have that change drastically reduce the shelf life of the product and therefore result in more food waste," said Ballinger. "The same goes for proper package and product sizing. If we find out that consumers struggle to eat through a one-pound package of lunch meat and product consistently gets thrown away, then we need to look at making that package smaller to fit the need of the consumer."
When new materials are used, they go through evaluations, including barrier, abuse, machine runnability, shelf-life, etc., before they become viable.
New equipment can be brought in pending the kind of product changes and equipment capabilities. "But in general, we try to make changes that work on current equipment," said Ballinger.
As a result, OEMs always factor into the sustainability equation to make the necessary changes required on existing — or new — equipment. OEM
• Available Sizes Flange and Cylindrical Nuts
• Accuracy Class 5, 7, & 10
• Machined Journals
• State of the Art Metrology and Inspection
• Integrated Ball Screw Motors
- NEMA 08, 11, 14, 17, & 23
• Applications
- Medical Lab Automation
- Optical Sensor Adjustments
- Pick and Place
- Packing Line Push Systems
- Measurement Systems
- Mechanical Automation
• Customization Available
Stephanie Neil • Executive Editor
Using natural-language technology, batteryfree smart tags, and a smartphone, Wiliot’s data platform can provide supply chain analysis and report on the state of the product inside the package.
What if your package could talk? Imagine the story it would tell about its supply chain journey, including handling and transport conditions, carbon footprint, and even the state of the product inside the package. Today, technology is available to make "talking packages" a retail reality, and Wiliot, an ambient IoT data carrier, is a company that is making it happen.
Unlike an RFID system that requires dedicated readers, ambient IoT harvests energy from the radio waves generated by everyday devices like smartphones and tablets. It then uses this energy to communicate with other devices or applications.
According to research and advisory group Gartner, ambient IoT is one of the technologies that will play a significant role in the future of digital organizations by enabling new ecosystems, new business models based on knowing the location or behavior of objects, smarter products with new behaviors, and a much lower cost of tracking and monitoring.
Understanding its potential, Wiliot is taking its ambient IoT platform a step further by integrating natural-language technology with its IoT Pixels which are stamp-sized, battery-free smart tags that can be affixed to products, packaging, containers, crates, pallets, and more. Communicating via Bluetooth, these IoT Pixels provide information such as location, temperature, humidity, and carbon footprint to the Wiliot cloud where the data is analyzed.
Recently, Wiliot expanded the breadth of this offering by announcing the launch of WiliBot, a generative AI (GenAI) chatbot that enables naturallanguage conversations with any ambient IoT-connected product. When GenAI is combined with this source of real-time ambient physical world data, manufacturers, warehouses, retailers, and eventually consumers, can have important conversations with the products they make, source, distribute, and ultimately purchase.
According to the company, with WiliBot, individuals can converse with products and supply chains using a smartphone to ask specific questions such as: What's the shelf life of this product? How did it get to the store? Which product should I stock next, and why? Is this product safe to stock, and why? What is the carbon footprint of this product, and why is it so low or so high?
"Ambient IoT and generative AI are increasingly symbiotic technologies," explained Wiliot CEO Tal Tamir. "Ambient IoT generates vast amounts of data about trillions of everyday things, and GenAI can uniquely make sense
of all that data. On the flip side, GenAI learns by analyzing vast amounts of data. To a real extent, that data has so far been finite, but ambient IoT presents massive new physical world datasets that a GenAI platform like WiliBot — and others — can use to describe products, materials, supply chains, and everything connected to the internet."
For example, the Wiliot-developed AI and machine-learning algorithms can identify supply chain events — such as sensing that shipments of produce or pharmaceuticals have been handled at unsafe temperatures — and automatically generate alerts or AI responses that allow businesses to course-correct or optimize operations.
According to Wiliot, the importance of the linkage between ambient IoT and AI was demonstrated during recent projects with leading food retailers. In the projects, the Wiliot Ambient Data
Platform revealed that food shrink (food that is lost, damaged, or spoiled before it reaches store shelves) accounts for roughly 5% of goods in the food chain.
The Wiliot platform can solve twothirds of these food shrink issues, the company said, ensuring a safer food supply, higher customer satisfaction, and lower costs. And WiliBot will now democratize access to these insights across the organization.
"Although Wiliot's work in generative AI is relatively recent, the company has long been a pioneer in artificial intelligence and machine learning for deriving insights into ambient IoT data," Tamir said. "As more companies have begun rolling out Wiliot's Ambient Data Platform, we've been asked how GenAI capabilities might make the transformation even easier. Our answer is WiliBot, the real-world combination of ambient IoT and AI."
Timeline for testing the technology Wiliot is currently piloting WiliBot with its key enterprise customers with a broader rollout scheduled for 2025.
In the future, this convergence of ambient IoT and generative AI will be made available to consumers in-store and at home through an ecosystem of mobile apps enabling consumers to converse with their products. The ability for the package or product to "talk" will provide more insight and understanding of the overall carbon footprint, materials composition, ethical sourcing compliance, quality and safety, and more, the company said. OEM
• 16-40 A / 600 V AC / 60 V DC
• Silver contacts ensures safe and durable operation
• UL 60947-4-1
LSF Series
• Extended/direct handle
• Integrated Base and DIN-Rail Mounting
RT Series
• Door mounted
• Integrated door or side panel mounting
• Well designed door mounting version
• No extra parts needed
908-806-9400
908-806-9490 (FAX) info@altechcorp.com www.altechcorp.com/HTML/MDS-A.html
KHK USA offers the broadest selection of stock metric gearing in North America. Designed for use in industrial automation applications, conveyor systems, packaging equipment, robotics, and general machinery applications, KHK’s selection of spur gears, helical gears, internal ring gears, gear racks, bevel gears, screw gears, worms & wormwheels, ratchets & pawls, gear couplings, right-angle gearboxes, and gear lubrication systems are available in various materials and sizes. KHK’s website offers free 3D CAD models for all gear products, complete product specifications, and 24/7 shopping. With KHK USA, stock gears are delivered from stock, with no minimum order or credit card surcharges.
khk usa inc.
259 Elm Place, Mineola NY 11501 516-248-3850
www.khkgears.us
Stop waiting and get rolling with American-made miniature ball screw assemblies from PBC Linear. Our ball screw production process offers a substantial reduction in lead times and costs compared to other available options, avoiding costly downtimes! PBC Linear is recognized for their high-quality standards for screw-driven technology. When ordering lead screws or ball screws, customers should expect to receive a complete screw and nut set that’s out-of-the-box ready to be incorporated into your next project application.
Choose between 5, 7, and 10 grade accuracy for either 6 mm, 8 mm, or 10 mm ball screw sizes with various available leads. Contact PBC Linear for a quote at +1.815.389.5600 or visit pbclinear.com to learn more.
ADVERTISEMENT
Case studies provide valuable discovery of challenge situations, recommended solutions, and implementation actions to solve specific real-life issues.
Control Engineering magazine invites you to explore the pages to follow while you learn and benefit from the case study success stories and project details shared by the following companies:
Actemium
Beckhoff Automation LLC
Motion
Pacific Blue Engineering
DigiKey Electronics
Endress + Hauser Inc.
E Tech Group
Patti Engineering
Quantum Design Inc.
Trihedral Engineering
Hargrove Controls + Automation LLC
Lafert North America
Matrix Technologies, Inc.
Velta Technology
Vertech Industrial Systems, LLC
Wunderlich-Malec Engineering
challenge: Develop a new swim spa delivering the best swim quality and strongest swim resistance current in the market.
solution: A complete redesign of the traditional swim current system to eliminate mechanical flow control and implement true variable-speed capability with Lafert HPS Series permanent magnet motors and Invertek Optidrive E3 drives.
Result: The Hydropool Executive Trainers are the only jetted swim spa in the market with a true variable-speed swim current system. Lafert permanent magnet motors power the adjustable current and support an unparalleled swim experience which delivers the strongest swim resistance and lowest operating costs of any Hydropool swim spa.
summaRy: Hydropool Hot Tubs, industry-leading Canadian manufacturer of hot tubs and swim spas and Jacuzzi company, was seeking a partner to support their development of next-generation technologies for a top-of-range swim spa. Lafert Group, long-standing manufacturer of permanent magnet motors for air and water movement equipment, started working with Hydropool to develop and integrate a proof-of-concept variable-speed swim current system.
The proof-of-concept eliminated swim current turbulence introduced by mechanical flow controls used in most swim spas, and the adjustable output could challenge worldclass triathletes or deliver a gentle current for young children at play. The value of the motor technology at the core of the proof-of-concept was apparent from the first test swim, and Hydropool engaged Lafert to support development of their new swim spa, the Executive Trainer.
The Executive Trainer swim current system is powered by two customized Lafert HPS Series permanent magnet motors, which are highly efficient at all speeds and exceed the IE5 “Ultra-Premium” standard for efficiency. The motors are about half the weight and volume of an equivalent-power induction motor and were engineered for reliable operation in the high-temperature, high-humidity environment of the swim spa enclosure. HPS Series motors are available to be customized for a broad range of machine applications up to fifty horsepower.
+1-800-661-6413
+1-800-661-6413 • lna.info@shi-g.com lafertna.com
Challenge: Schluchseewerk AG wanted to record and optimize the efficiency of its turbines at the pumped storage plant in Wehr, Germany, despite difficult flow conditions. For this purpose, it was looking for a reliable flowmeter.
Solution: Endress+Hauser’s Proline Prosonic Flow W 400 ultrasonic flowmeter, is installed from the outside on pipes. It measures independently of the pressure and is easy to install, saves space and does not interrupt the process.
ReSult: Schluchseewerk AG has precise measurement despite short inlet runs and disturbed flow profiles, precise determination of turbine efficiency, and optimum process control and monitoring.
SummaRy: At the Schluchseewerk AG Wehr pumped storage plant, water is pumped from the Wehra basin to the higher Hornberg basin. When the water flows back, it generates electricity using a turbine and generator.
Previously, water volumes were estimated based on basin size and turbine output, but precise measurement is crucial for optimizing turbine efficiency. Schluchseewerk AG needed accurate flow measurements to verify performance improvements after changing the turbine impeller geometry. However, finding a suitable flowmeter was challenging due to large pipe diameters (up to 2 meters), high pressures (over 60 bar), difficult access, and short inlet runs.
Endress+Hauser’s Proline Prosonic Flow W 400 with FlowDC function provided the solution. This noninvasive ultrasonic flowmeter installs externally on pipes up to 4 meters in diameter, measures independently of pressure, and is easy to install without interrupting the process. It maintains high accuracy even with short inlet runs and disturbed flow profiles, ensuring reliable measurements under challenging conditions.
you want to learn more?
challenge: Houston, TX is nearing completion of a 1.8-billion-dollar expansion of their Northeast Water Purification Plant allowing them to meet projected demand while pivoting their supply from ground water to more sustainable surface water.
solution: The scope of this project required software capable of managing a vast distributed array of infrastructure that includes over 200 PLCs. The city and its engineering partners ultimately chose VTScada as the soul SCADA provider.
Result: VTScada’s powerful software engine, unique integrated design, and commitment to security provide the city with an unmatched performance, resiliency, and scalability.
summaRy: The City of Houston, Texas serves a rapidly growing population of 2.3 million people. To manage this unprecedented growth, they have expanded the capacity of their Northeast Water Purification Plant from 80 million gallons a day to almost 400 MGD, making it one of the largest progressive design builds of its kind in the US.
After an extended evaluation of features, performance, ROI, and security, the city chose VTScada as the sole SCADA software platform. The completed application distributes its services across 12 servers including two historian servers, four I/O servers, four engineering servers, and two for remote access. Each server group employs automatic failover and synchronization according to a simple set of server lists eliminating downtime and data loss.
In addition to a suite of out-of-the-box SCADA features, intuitive design tools allowed developers to create custom High-Performance displays for processes such as Flocculation & Sedimentation, Ozone Generation, Intake Pump Stations, and Chlorine Dioxide Generators. Operators can access these screens from 40 workstations including dual, quad, and six-monitor displays in the control room. This project is scheduled for completion this year.
VTScada is award-winning software designed to run the largest critical systems in the world. While it was built with massive applications in mind, its unique design make mission critical capabilities practical for the smallest systems. Find out how: www.vtscada.com.
Challenge: A Leading Biopharma company needed reliable backup power to ensure continued operations during extended electric utility interruptions immediately for the next California fire season. The need to support essential GMP systems would provide for the safe storage of products and critical work processes.
Solution: Wunderlich – Malec in collaboration with the customer determined the best generation and distribution systems to provide a sustainable energy supply to facilities.
ReSult: Backup diesel generation with additional fuel storage provided for essential loads and electrical systems. Redesign of distribution systems to support essential loads from onsite generation and islanding controls made best use of client generation resources without extensive capital investment.
SummaRy: Wunderlich – Malec (WM) used its electrical engineering and control system skills with its software modeling systems to optimize solutions for each customer facility to achieve five days of local, islanding power while optimizing sustainability goals.
WM’s subject matter experts skilled in medium voltage, islanding, load management, utility interconnect, electrical design and control system integration, provided system changes and additions to campus facility generation and distribution systems. The initial Phase of the project was completed at an accelerated schedule to ensure backup power generation system during the fire season. Electrical distribution and control system changes were compatible with subsequent backup power generation solutions. Subsequent phases increased fuel storage and improved reliability of the system.
An Energy Gap Analysis and Risk assessment utilized a PEER dynamic scorecard for each customer’s campus facility to evaluate its energy sustainability and estimate baseline costs. The project costs and schedules were reduced with maximum reuse of equipment, control systems and prior installations.
WM’s mGrid® technology optimized operational sustainability, energy cost savings, better efficiency, carbon reduction and increased renewable content meeting the clients’ objectives. The customer receives support assurance of long-term service from WM’s local office. Phone 952-933-3222 or
Challenge: Lehnen Industrial Services needed to create a mid-range, compact lip balm filling machine that could overcome the limitations of legacy PLC controls, which included high costs, limited memory, and space constraints.
Solution: By integrating Beckhoff’s PC-based control technology, including C6015 ultra-compact IPCs, TwinCAT 3 automation software, and ELM series ultra-compact servo drives, Lehnen optimized the ProFill SF machine for future-proof performance and space savings.
ReSult: Lehnen’s ProFill SF machine improved functionality while reducing control costs by 40%. The new system offers the required compact footprint and high-precision filling, meeting industry demands and ensuring future scalability.
SummaRy: Lehnen Industrial Services faced the challenge of creating a mid-range lip balm filling machine that balanced cost, performance, and compact design. Initially hampered by the limitations of legacy PLC controls, including costly contracts, limited controller memory, and excessive hardware space requirements, Lehnen sought a more modern solution. The company turned to Beckhoff for its PC-based control technology, integrating C6015 ultra-compact IPCs, TwinCAT 3 software, and ELM series servo drives.
This transition allowed Lehnen to overcome previous technology challenges and future-proof their ProFill SF machine. The new system maintained a small footprint and high-precision filling capabilities, crucial for avoiding product waste and ensuring efficiency. With Beckhoff’s innovative approach, Lehnen reduced control costs by 40% and simplified machine commissioning, all while enhancing overall performance. The ProFill SF now processes 60 tubes per minute, filling, capping, labeling, and coding up to 30,000 lip balm sticks per day, ensuring Lehnen remains competitive in the market.
Challenge: When a major steel company’s network of nine legacy A-series Mitsubishi PLCs failed to report product masses to their database, they sought Patti Engineering’s legacy upgrade expertise to solve the problem.
Solution: Patti Engineering took a phased approach, upgrading each PLC to the modern Q-series counterpart. They added a Mitsubishi Ethernet communication module to restore communication between the product masstracking PLC and the client’s database.
ReSult: The upgrades improved system reliability while providing easy access to spare parts. Product traceability improved by reporting the current location of every coil. The Ethernet communication module improved troubleshooting flexibility.
SummaRy: When a ring network of nine legacy PLCs failed to report product masses to their database, a major steel company trusted Patti Engineering’s legacy upgrade expertise to seamlessly replace the older A-series Mitsubishi PLCs with their modern Q-series counterparts.
Patti Engineering knows to expect the unexpected during any legacy upgrade project. While relying on the redundant pathway within the ring network seemed like a great plan, engineers studied it further before proceeding. They discovered several compromised MELSECNET fiber optic cables disrupting PLC communication. After replacing the cables to restore network integrity, the team was able to upgrade each PLC without disruption.
As if one surprise wasn’t enough, with the first PLC in place, a network architecture change occurred inhibiting the original data collection application from retrieving data from the mass-tracking PLC. Patti Engineering resolved this problem by adding a Mitsubishi Ethernet communication module that communicated directly with the customer’s PostgreSQL database.
With the upgrade completed, the manufacturer enjoyed reliable system operation with easy access to spare parts. The Ethernet communication module resolved the data collection issue and provided engineers greater troubleshooting flexibility by eliminating the need to interface directly with the machines. Product traceability was also improved.
Challenge: MillerKnoll needed an order execution system that could handle their entire production process, including product sequencing, schedule management, inventory management and more. And it had to work with their existing software ecosystem.
Solution: Vertech created a system that bridges multiple data and ERP systems and accurately records and replicates data into a large-scale Azure Cloud instance. It integrates with Vertech’s previous SPC work in Ignition as well as MillerKnoll’s entire LiveFactory ecosystem.
ReSult: The new MES not only streamlined MillerKnoll’s manufacturing operations but also improved efficiency, data tracking, and coordination.
SummaRy: By using Ignition, Vertech created an MES system that unifies multiple data sources and simplifies manufacturing operations from an operator and manager perspective. It incorporates the following features:
Operator Interface - This front-end interface contains all the info an operator needs at a glance. This includes bills of materials, manufacturing holds, part defects, inspections and work instructions.
Automated Order Schedules - Automated order schedules were created for each manufacturing site and for individual lines within the site. Schedulers and line supervisors can create their own dynamic sequencing rules based on the characteristics of the order.
or scan QR to read the full Case Study.
Contextualized Production Data - We split and optimized production into time-based slices to ensure each work order would satisfy the required total number of shipped products for the day.
Rework Tracking - The system tracks the performance and rework percentage across multiple part and line configurations, then reports which lines are having the most difficulty reaching performance metrics such as Takt time.
ERP Sync - Lastly, the system executes transactions against various ERP systems that validate customer and order shipment data. Staff can stay up to date with order fulfillment and see how specific production issues might impact delivery timelines.
See more at www.vertech.com/case-studies/millerknoll
Challenge: A conveyor motor company needed to add EtherNet/IP to an existing motor product design. However, they didn’t have compacity on the software for in house integration.
Solution: The RTConnect™ module allows the manufacturer to add communication protocols while limiting the burden on the manufacturers engineering team. They simply modified their PCB to expose a serial line, 5.5 VDC and a few lines of GPIO for LEDs.
ReSult: Within weeks they had working prototypes and within months they had a device through certification. By leveraging RTA as a protocol partner, the devices launched quickly, and the
SummaRy: Devices today require an ever-growing list of communication protocols to serve the market’s needs. Designing and deploying all this technology is placing a large burden on manufacturers. This manufacturer estimated the effort to deploy a home grown EtherNet/IP deployment on a home spun Ethernet physical layer would take over a year of effort and carry significant risk. This effort and these features were also not deemed core competency.
The manufacturer was able to offset the risk of doing the project in-house by leveraging a protocol partner. RTA can not only solve their current communication needs, but also maintain the communication stacks as they evolve. Additionally, they can offer additional communication solutions for future projects.
You know bringing your products to market is challenging. After investing so much in your devices, what you need is a protocol partner to help reduce deployment risk and speed your development to market. The RTConnect module maximizes your potential by easily integrating Ethernet-based communication protocols into your serial devices.
Now you can support EtherNet/IP, PROFINET, BACnet/IP, Modbus TCP, MQTT and OPC UA in a compact module with a proven Ethernet PHY, ensuring the reliable performance you need.
Challenge: When E Tech Group conducted a comprehensive IT/OT network assessment for a food and beverage manufacturer, significant cybersecurity vulnerabilities were uncovered.
Solution: E Tech Group designed and implemented essential network security improvements including: separation of IT and OT domains; firewalls to create a DMZ between them; a jump box to minimize OT network access points, and a network threat detection engine for comprehensive traffic monitoring.
ReSult: When a recent ransomware cyberattack took place, it was quickly identified by the threat detection engine, minimizing its impact. All critical OT assets remained protected, and the facility continued production without disruption.
SummaRy: A forward-looking manufacturer invested in an IT/OT network assessment with E Tech Group in 2018. The assessment uncovered critical vulnerabilities in the facility’s network architecture. This manufacturer made the critically important decision to move forward with E Tech Group’s recommendations - a decision that ultimately safeguarded their OT assets when they later faced the challenge of a ransomware attack.
Within the assessment results, E Tech Group recommended network improvements to strengthen the facility’s cybersecurity posture. These included implementing a demilitarized zone (DMZ) architecture to separate the IT and OT networks. Firewalls and jump boxes would serve this purpose, restricting OT network access and facilitating secure connections. A further recommendation was made to connect a network threat detection engine so that any suspect traffic would be quickly identified.
Click or scan QR to read the full Case Study online.
Years later, a threat actor successfully breached the enterprise network through an incorrectly configured cloud-based server. However, the threat detection engine identified and flagged the anomalous network traffic patterns that ensued. Because of the proactive measures taken, the OT network remained out of reach of the attacker and therefore no production disruption occurred.
E Tech Group can identify your facility’s vulnerabilities and then complete the remediations required to protect it from the next cyberattack.
1-855-202-1444 www.etechgroup.com
Challenge: The rapid onset of the COVID-19 pandemic presented unprecedented challenges for the global healthcare sector. Among the most critical was the urgent need to develop and deploy a high-capacity COVID-19 vaccine. This project was undertaken by Matrix Technologies to retrofit an existing Fill Line to fill and package a COVID-19 vaccine.
Solution: Seamless collaboration and excellent work by Matrix Technologies, Inc. deployed new Rockwell FactoryTalk servers, new ControlLogix PLC program and HMI application with FT Batch Recipes for the new Buffer and Formulation operations.
ReSult: The project was successfully completed within the accelerated timeline to contribute to an estimated 6.3 million lives saved.
SummaRy: Matrix Technologies, Inc. embarked on a project to retrofit an existing Fill Line at the client’s site for filling and packaging a COVID-19 vaccine. This initiative involved developing and configuring a new process, migrating existing process control areas to a new HMI server, and setting up a new Batch server to segregate the new vaccine areas from the existing ones. The project began with a design phase that included reviewing and updating P&IDs, equipment lists, instrument lists, I/O lists, and process descriptions. During the development and configuration phase, a new Rockwell FactoryTalk (FT) server stack was deployed, featuring redundant FT View Site Edition (SE) HMI servers and an FT Batch server. A new ControlLogix PLC program was created to manage the Vaccine Line Buffer and Formulation operations. Additionally, a new redundant HMI application was developed using FT View SE to visually represent the vaccine line operations.
To control the new Buffer and Formulation operations, a new FT Batch Area Model was created, and FT Batch Recipes were developed. To ensure the system met the design criteria, a fully simulated factory acceptance test was performed with participation from the client. A risk-based approach following GAMP 5 guidance was used to generate Installation and Operational Qualifications test scripts and reports. Onsite support was provided for protocol execution, discrepancy resolution, and close-out activities.
Challenge: Replace a deprecated supervisory system. Deploy a modern system in a singular platform providing seamless integration between the plant floor and business operations team without rewriting existing code for 34 different existing systems.
Solution: Deploy a PlantPAx solution with a “wrapper” for each existing system.
ReSult: With a singular platform, the company has reduced troubleshooting efforts, created a consistent image by utilizing high-performance graphics, and eliminated data gaps in their historian due to outdated and unsupported software. Additionally, they have automated backups of their PLCs and enhanced reporting capabilities that help them analyze data to make better operational decisions.
SummaRy: AA pharmaceutical company installed a control system infrastructure around 2012, which included supervisory system and roughly 30 PLCs on two different control system platforms. The system was not properly maintained over time, resulting in poor performance and data integrity issues. The facility was routinely audited, and often required deviation explanations to produce satisfactory results. This introduced risk to the business, so a project was created to address it.
The objective of this project was to deploy a PlantPAx 5.2 solution that upgraded hardware and software for 34 PLCs and provided a modern and robust supervisory system all on one control system platform. This was accomplished by wrapping new logic around existing code without modifying how the existing systems currently operate.
The primary benefit of the project was the modernization of the control system by removing obsolescence from the critical systems the plant used to run daily operations. In addition, the project simplified troubleshooting, improved data integrity, streamlined access to data, and reduced the amount of training required to maintain multiple control system platforms.
Challenge: A meat plant’s end-of-line palletizing was a persistent bottleneck. Manual work was labor-intensive and error-prone, limiting output. To achieve growth goals, they needed a faster, more reliable solution.
Solution: The collaborative palletizing demo showcased its flexibility and efficiency, convincing the plant to invest in a tailored solution. The Motion Automation Intelligence team analyzed the production line, box sizes (9–30 pounds) and existing PLC system.
ReSult: The collaborative palletizing system led to record-breaking production outputs, exceeding their initial goals. It also improved labor allocation, freeing up two to three employees for more engaging and value-added roles in the plant.
SummaRy: When a major meat manufacturing company sought to supercharge their end-of-line production, they turned to Motion Automation Intelligence for a collaborative palletizing solution. The current production line was too slow and labor-intensive.
Impressed by Motion Automation
Intelligence’s collaborative palletizing technology, the company requested a demo, which proved to be a game-changer. It showcased the flexibility and efficiency of collaborative robots, convincing the plant to move forward with a customized solution. The turnkey collaborative palletizing system was designed for seamless integration:
• PLC integration: The system interfaced directly with their existing PLC, enabling real-time monitoring of cycle rates, cartons produced, and overall system performance.
• User-friendly interface: The intuitive interface made it easy for operators to manage and monitor the palletizing process.
The results? Record-breaking output and a happier, more engaged workforce. The project’s success solidified Motion Automation Intelligence’s reputation as a trusted partner, leading to further collaborations. This case study demonstrates how collaborative palletizing can revolutionize meat processing—boosting efficiency, freeing up valuable human capital,
Challenge: A food and beverage company acquired 12 new plants, needing to align technologies and secure network integration. This involved auditing Operational Technology (OT) devices, Main Distribution Frame (MDF), and Intermediate Distribution Frame (IDF) cabinets to identify cybersecurity gaps.
Solution: Actemium used advanced tools to catalog all OT devices and assess network security. They reviewed MDF/IDF cabinets and existing OT software (MES, HMI, SCADA) to identify vulnerabilities, ensuring compliance with cybersecurity standards.
ReSult: Actemium provided a detailed report with gap analysis, recommendations, and budget estimates, ensuring secure integration of new facilities without disruption, strengthening the company’s overall cybersecurity posture.
SummaRy: A leading food and beverage company recently acquired a new division, facing significant challenges in integrating its operations with existing infrastructure while ensuring cybersecurity. To address these complexities, the company partnered with Actemium to conduct a thorough assessment of 12 newly acquired manufacturing plants. The primary focus was to evaluate the existing Operational Technology (OT) landscape, assess cybersecurity standards, and identify potential risks.
Actemium employed advanced scanning tools to catalog all networked OT devices and performed detailed evaluations of Main Distribution Frame (MDF) and Intermediate Distribution Frame (IDF) cabinets, checking for compliance with cybersecurity standards. Additionally, the team analyzed existing OT software, including MES, HMI, and SCADA systems, to map out the technological landscape and identify vulnerabilities.
The comprehensive assessment led to the creation of a detailed Facility Status Report, a Technology Gap Analysis, and actionable recommendations with budgetary insights. These findings provided a clear roadmap for closing security gaps, prioritizing risks, and aligning technological standards across the company’s expanded operations. Actemium’s expertise ensured a smooth integration of the new facilities, reinforcing cybersecurity and operational resilience. This case study highlights the importance of proactive technological assessments in securing and optimizing corporate acquisitions.
Contact: Wilfred.misener@actemium.com
Challenge: DigiKey wanted to increase efficiency and productivity and reduce delivery cycle time.
Solution: The largest component of the newly automated system is the KNAPP Order Storage and Retrieval (OSR).
ReSult: The automation systems in DigiKey’s Product Distribution Center Expansion (PDCe) allow the company to pick, pack and ship an average of 25,000 orders a day to customers in more than 180 countries around the world.
SummaRy: DigiKey’s PDCe is almost fully automated. The company has developed many proprietary systems to ensure customers get the right part in the right quantity every time. The KNAPP OSR system provides the right parts to the picker, eliminating walk time and providing an ergonomically appropriate environment for the picker.
This high level of automation improves picking efficiency by up to 35% and improves packaging quality and efficiency.
CliCK or scan
QR to learn more
The PDCe features two primary sorting systems to provide redundancy in the case of a breakdown and to enable future growth. Creating a teamfriendly work environment while also planning for scalability and growth was top of mind in the plans and design of the building. There are over 27 miles of automated conveyor belts in the facility, and an average order will travel more than 3,200 feet inside the building.
Sustainability was also an integral part of the planning and construction of the facility. DigiKey specially designed a conveying system that maximizes energy usage and efficiency.
Season 4 of DigiKey’s Factory Tomorrow video series takes viewers inside the company’s distribution center to see firsthand how automation fills gaps across the warehouse. To view the video series and learn more about DigiKey’s automation offerings, visit www.digikey.com/automation
sales@digikey.com • 1-800-344-4539
www.digikey.com
Challenge: A new Microsoft security patch made it extremely difficult to configure and enable DCOM. Each recovery from OPC disruptions was causing multi-hour production delays.
Solution: They avoided DCOM completely by tunnelling OPC DA, using Skkynet’s Cogent DataHub software.
ReSult: The application runs faster. There are no intermittent dropouts between clients and servers, and no machine down time.
SummaRy: A large pharmaceutical manufacturer in the European Union recently faced a serious problem. Changes to security enforcement in Microsoft Windows meant that minor disruptions in the control system were shutting down whole production lines for up to five hours.
“It was a lot of cost,” said Stephen Doody, plant automation team leader. “Not only were we losing the manufacturing time, but the knock-on effect meant that half of our control staff was then tied up as long as five hours to get the line back running.”
Security for four vision system PCs and a main controller PC was configured on the plant LAN. That approach was only possible with minimal DCOM security. However, the Windows security patch required raising DCOM authorization levels, causing serious problems.
To avoid the problems they stopped using DCOM. Instead, they used Cogent DataHub software from Skkynet to tunnel between their PCs. All networking is now done by tunnelling, which makes only local connections to the OPC DA servers. Users log in locally to any OPC DA server, as needed.
CliCk or scan QR to read the full Case Study online.
“The whole solution was pretty much a no-brainer for management because it was saving a heap of money,” said Doody.
Challenge: PLC5 controls and HMI are discontinued making it risky to continue running lines using those controls. Replacement parts are not available and often customers resort to Ebay. Some parts may never be available and many companies can’t afford lengthy downtimes.
Solution: Quantum replaced the PLCs with a Rockwell Compactlogix PLC, and the HMI with a Rockwell PanelView Plus 6 HMI. Communications from the PLC to the HMI were changed from DH+ to Ethernet and the existing VFD’s were converted to Powerflex VFD’s with Ethernet communications.
ReSult: These upgrades have made the system more operable and reliable and has reduced the overall risk of downtime.
SummaRy: A food manufacturing facility in Rockford, Illinois needed to upgrade a Pellet Pan Coating line containing four separate pellet pans. 25% of their business relied on each of the 4 pans making this a significant project. If one pan goes down, 25% of their business would be lost until the needed parts are found.
Quantum started by creating new electrical schematics with the Contrologix hardware, Powerflex 753 series VFD’s and Powerflex 523 series VFD’s. The old PLC 5 processor, I/O modules, power supply and rack were removed from the machines leaving only the existing PLC 5 wiring arms intact. To allow the conversion to happen without having to rewire all the inputs and outputs, the new ControlLogix rack, processor, power supply, I/O modules, and PLC 5 to ControlLogix conversion cables were installed. Next, the old VFD’s were removed and the new Powerflex VFD’s were installed.
The PLC 5 logic was converted to a ControlLogix format using the Rockwell conversion software. Logic was then added to communicate with and control the Powerflex VFD’s. In the final stages, Quantum recreated the PanelView 1000e screens for the PanelView Plus 6 using the Rockwell FactoryTalk View ME software. Tags were changed to match the ControlLogix PLC, Alarm controls and messages were reworked and Ethernet communications were added.
815-885-1300 • qdisales@quantumdi.com
Challenge: A food and beverage company faced safety risks in warehouse operations after initial AGV integration led to injuries and operational halts.
Solution: Pacific Blue Engineering (PBE) optimized AGV safety settings, enhanced operational modes, and provided comprehensive training for safer automation.
ReSult: Improved workplace safety and a projected multi-million-dollar margin increase over five years.
SummaRy: A major food and beverage company aimed to boost margins by integrating Autonomous Guided Vehicles (AGVs) and Autonomous Intelligent Vehicles (AIVs) into its operations. However, past attempts led to safety incidents, halting progress. Determined to proceed safely, the client engaged Pacific Blue Engineering (PBE), renowned machine safety specialists, to assess and mitigate risks.
PBE’s team identified necessary safety setting adjustments in the AGVs to ensure that operations stopped if objects or personnel were detected in their path. Additionally, PBE collaborated with Original Equipment Manufacturers (OEMs) to address potential risks across all operation modes. To further support safety, PBE provided the client’s teams with essential training resources.
As a result, the company achieved a safer work environment and significant cost savings. With improved margins projected to reach tens of millions over five years, the client successfully leveraged the latest in AI and autonomous vehicle technology to maintain a competitive edge.
Challenge: Third-party audit revealed critical gaps in manufactured homes facility’s OT security, including poor asset visibility, inadequate endpoint protection, and weak vulnerability management controls.
Solution: Implemented Zero Trust defense strategy, enhancing cybersecurity without disrupting existing network infrastructure.
ReSult: Successfully deployed TXOne EdgeIPS solution, established network segmentation and virtual patching, while maintaining operational efficiency across multi-shift manufacturing operations.
SummaRy: A leading manufactured homes producer faced significant cybersecurity vulnerabilities in their off-site building operations, as identified through an external audit. The company’s multi-level automation process, critical for designing, cutting, assembling, and packaging housing components, required robust protection without compromising operational efficiency.
Partnering with TXOne Networks and Velta Technology (now part of BW Design Group), the company implemented a comprehensive defense-in-depth strategy. The solution focused on protecting individual manufacturing cells through advanced network segmentation, virtual patching, and automated OT protocol monitoring.
This approach was particularly crucial given the facility’s emphasis on employee safety, component precision, and operational resilience.
The implemented solutions have strengthened the plant’s cybersecurity framework while maintaining operational flexibility. By preventing costly shutdowns and enabling secure asset management, the new system safeguards not only the manufacturing process but also the company’s quality standards, inventory management, and market reputation.
Scan QR code to learn more about Velta’s capabilities. Craig.duckworth@bwdesigngroup.com
www.veltatech.com
Challenge: A conveyor motor company needed to add EtherNet/IP to an existing motor product design. However, they didn’t have compacity on the software for in house integration.
Solution: The RTConnect™ module allows the manufacturer to add communication protocols while limiting the burden on the manufacturers engineering team. They simply modified their PCB to expose a serial line, 5.5 VDC and a few lines of GPIO for LEDs.
ReSult: Within weeks they had working prototypes and within months they had a device through certification. By leveraging RTA as a protocol partner, the devices launched quickly, and the
SummaRy: Devices today require an ever-growing list of communication protocols to serve the market’s needs. Designing and deploying all this technology is placing a large burden on manufacturers. This manufacturer estimated the effort to deploy a home grown EtherNet/IP deployment on a home spun Ethernet physical layer would take over a year of effort and carry significant risk. This effort and these features were also not deemed core competency.
The manufacturer was able to offset the risk of doing the project in-house by leveraging a protocol partner. RTA can not only solve their current communication needs, but also maintain the communication stacks as they evolve. Additionally, they can offer additional communication solutions for future projects.
You know bringing your products to market is challenging. After investing so much in your devices, what you need is a protocol partner to help reduce deployment risk and speed your development to market. The RTConnect module maximizes your potential by easily integrating Ethernet-based communication protocols into your serial devices.
Now you can support EtherNet/IP, PROFINET, BACnet/IP, Modbus TCP, MQTT and OPC UA in a compact module with a proven Ethernet PHY, ensuring the reliable performance you need.
Rittal North America
The adoption of busbar power distribution systems on a global scale has accelerated in the last few years. Research estimates that the market for copper busbar power panels in North America alone will grow by nearly 7.5% annually through 2032, an increase that’s driven by several key factors.
One such factor is a global shift in safety regulations to help prevent instances of arc flash. A recent study found that there are roughly 30,000 arc flash incidents in the United States each year, many of which are powerful enough to cause significant injury to workers and costly damage to equipment.
This is pushing regulatory agencies to revise compliance guidelines. The short-circuit current ratings (SCCR) index outlines the appropriate level of short-circuit current electrical equipment can carry to help avoid electrical fault or arc flash, and recent changes to the SCCR have made it challenging for manufacturers to safely install and operate traditional block-and-cable power distribution.
While compliance and safety are major players in the move to busbar power, the need to optimize the use of space inside an industrial enclosure and the demand for faster, more efficient configuration and installation are also leading the charge toward busbar power.
Rittal’s new Busbar 101 guide provides an introduction to busbar power distribution, the benefits of busbar compared to blockand-cable, ways that busbar can help reduce costs, and the ideal applications for busbar.
CLICK here and download the guide to get started now.
See more New Products for Engineers www.controleng.com/NPE
With the AM8300 servomotor series, Beckhoff expands its drive technology portfolio to include modular motors with integrated water cooling. Compared to conventional convection-cooled motors, these devices support higher speed requirements and boost standstill torque by a factor of three. The efficient and effective cooling technology enables extreme power density, accommodating a rated power of up to 40 kW in the smallest installation spaces. Numerous options are available. The new The IP65-rated servomotors offer maximum dynamics with dependable performance: the increased speed and torque do not affect the rotor moment of inertia.
Beckhoff Automation, http://www.beckhoff.com/am8300
NewTek offers a vented design for its miniaturized series of AC-operated position sensors with greater endurance to pressure, temperature, shock and vibration. Sensors have greater accuracy and the ability to fit into restrictive spaces when measuring the deformation of samples in test chambers for hydraulics and material testing applications. In geologic testing, the sensors help determine properties of the ground, rock and soil. They are used in asphalt testing to evaluate deformation resistance and in oil field exploration and extraction.
NewTek, https://www.newteksensors.com/lvdt-sensors/m-375-series/
The Siemens ET 200SP CPU 1514SP-2 PN and CPU 1514SP F-2 PN are the latest enhancements to the ET 200SP Distributed I/O System. These CPUs, driven by the Simatic S7-1500 controllers’ firmware version V3.0, have the functionality of the CPU 1515(F)-2 PN, and dual integrated Profinet IO interfaces. Interface X1 has a 2-port switch (requires a suitable BusAdapter) supporting Profinet IO RT and IRT. The X2 offers one port for Profinet IO RT. Siemens, https://www.usa.siemens.com
AutomationDirect added a variety of new Metrol limit switches to its lineup of precision limit switches. These ultra-precise mechanical limit switches have a repeatability down to 0.5 microns (µm) and are some of the smallest switches/sensors available. Tiny size allows mounting in tight locations. Precision touch limit switches have a 1-micron repeat accuracy, 90-degree straight touch limit switches have a 6mm smooth barrel, mini stopper precision limit switches are in 8, 10 and 13mm flat head styles, and high precision tool setter limit switches have threaded M4 mounting holes or downward installation options. Models without an LED cost less.
AutomationDirect, www.automationdirect.com/limit-switch
Trio Motion Technology updated its DX3 EtherCAT servo drive with functional safety safe torque off (STO), meeting safety levels SIL3 and PLe. The motion specialist has increased voltage to 480V for the DX3 EtherCAT model and DX3 Conventional model that supports pulse-and-direction, analog and CANopen control. The DX3 single-axis servo drive range increases design flexibility for machine builders in a cost-optimal package.
Trio Motion Technology, www.triomotion.com/public/products/dx3/DX3-FSO.php
The Emerson Rosemount 802 Wireless Multi-Discrete Input or Output Transmitter has eight discrete input/output (I/O) channels, each configurable as an input or an output. WirelessHART capability allows the transmitter to connect to a wireless gateway, which can link to a host (such as a control system or asset management system) via a wired connection. This allows the host to monitor and control assets remotely over a WirelessHART network. The wireless capabilities reduce costs of monitoring and controlling field-installed assets, such as motors, valves and pumps. Emerson, http://emerson.com/Rosemount802
NAMUR Module Type Package cuts times to market up to 50% and engineering efforts by up to 70%; flexibility can be increased by 80%.
The NAMUR Module Type Package (MTP) interface can make process lines more flexible and meet fast changing demands. Product lifecycles are getting shorter. Previously production or process lines were built and remained unchanged for decades, modern production lines need to be more flexible to meet fast-changing demands. Automation technology vendors have traditionally used custom-made control systems and interfaces, which often require extensive rewriting of the control system and commissioning every time a change in the line is needed. MTP enables production lines to become more flexible and respond rapidly to changing market requirements.
‘ Turck
Production lines can be built or expanded with any available modules, ensuring that production is matched to demand in the most cost-effective way. Times to market can be reduced by up to 50%, engineering effort can be reduced by up to 70% and flexibility can be increased by 80%.
Banner offers a variety of MTP solutions for end-to-end modularization in production.
’ Tony Coghlan
The MTP standard began in 2014 by the NAMUR association of process industry end-user companies. The goal was to create a standard for intelligent equipment modules to improve flexibility and efficiency of process lines.
MTP is a manufacturer-independent interface which describes the functions of a module. The modules internal control system implements the functions in the same way that a mana0ger delegates a task to a colleague. The higher-level control system doesn’t need to know how the module implements the function, just that it is being done.
Instead of programming to control individual actuators in the modules, a new Process Orchestration Layer (POL), based on supervisory control and data acquisition (SCADA), manufacturing execution systems (MES) or industrial internet of things (IIoT), sends commands to the services of the module. The status and process values of the services are received by the POL to continue the process control. Because the commands are standardized across all manufacturers, a similar module from any manufacturer can be controlled without changing the POL. This benefits the end customer and frees up skid builders to use different equipment manufacturers, helping to shorten production times and alleviate component shortages.
The first practical application of MTP standards in an industrial environment took place in 2020 at Evonik’s amino-acid plant in Singapore, integrating a chiller package unit into a conventional production facility. Since then, vendors have worked to bring products to market. At the ACHEMA exhibition earlier this year, 12 manufacturers exhibited solutions and products for automation in Process Equipment Assemblies (PEAs); seven demonstrated POL solutions.
Codesys system platform enables different fieldbus/Ethernet protocols to be used in one automation system. The edge controller generates the MTP file based on Codesys. It is then stored and installed in the POL. The instructions are communicated via OPC UA. The MTP can help quickly integrate PEAs into modular plants, providing a prerequisite for end-to-end modularization in production, allowing rapid commissioning and enabling plug and produce. The interface provides diagnostics and predictive maintenance. MTP defines services to configure, visualize and operate. ce
Tony Coghlan is managing director at Turck Banner. This content originally appeared on Control Engineering Europe, Nov. 6. Edited by Mark T. Hoske, editor-in-chief, Control Engineering, WTWH Media, mhoske@wtwhmedia.com.
https://www.controleng.com/articles/ making-process-control-more-flexible https://www.controleng.com/magazine/international-editions Control Engineering Europe https://www.controlengeurope.com NAMUR https://www.namur.net/en/index.html PI North America https://us.profinet.com
Sales
Automation Direct...........................C2.................www.automationdirect.com
Automation Direct...........................1 .................www.automationdirect.com
Altech Corporation .....................38, 39, 49, 55 ............www.altechcorp.com
Beckhoff...................................6 .................www.beckhoff.com
Dataforth Corporation........................80.................www.dataforth.com
Digi-Key Electronics..........................C4.................www.digikey.com/automation
Graybar Electric Co. .........................C3.................www.graybar.com
Kalypso ...................................46.................www.kalypso.com
KHK-USA................................53, 56 ...............www.khkgears.us
Lafert .....................................10.................www.lafertna.com
Migatron ..................................57.................www.migatron.com
Motion....................................19.................www.motion.com
New England Wire ........................41, 45 ...............www.newenglandwire.com
Parvalux...................................37.................www.parvalux.com
PBC Linear...............................51, 56 ...............www.pbclinear.com
Rockwell Automation ........................43.................www.rockwellautomation.com
Skkynet ...................................25.................www.CogentDataHub.com
Tadiran....................................12.................www.tadiranbat.com
Trihedral Engineering. .......................2 .................www.VTScada.com/redundancy
Trihedral Engineering. ....................Bellyband .............www.VTScada.com/redundancy
Valmet ....................................57.................www.valmet.com
Wago .....................................4 .................www.wago.com/us/
312-961-6840
Sales Account Manager Brian Gross BGross@WTWHMedia.com 847-946-3668
Sales Account Manager Richard Groth RGroth@WTWHMedia.com 774-277-7266
Sales Account Manager Robert Levinger RLevinger@WTWHTMedia.com 516-209-8587
Sales Account Manager
Dean Morris DMorris@WTWHmedia.com 513-205-9975
Sales Account Manager Judy Pinsel
847-624-8418 JPinsel@WTWHmedia.com
Patrick Lynch, Senior Vice President, Sales & Strategy 847-452-1191, PLynch@WTWHMedia.com
McKenzie Burns, Marketing Manager MBurns@WTWHmedia.com
Courtney New, Program Manager, Content Studio CNew@WTWHMedia.com
Paul Brouch, Operations Manager 708-743-5278, PBrouch@WTWHMedia.com
Rick Ellis, Director, Audience Growth 303-246-1250, REllis@WTWHMedia.com
Michael Rotz, Print Production Manager 717-422-3622, mike.rotz@frycomm.com
Custom reprints, print/electronic: Matt Claney, 216-860-5253, mclaney@wtwhmedia.com
Information: For a Media Kit or Editorial Calendar, go to https://www.controleng.com/advertise-with-us.
Letters to the editor: Please e-mail us your opinions to MHoske@WTWHMedia.com. Letters should include name, company, and address, and may be edited.
Make the move to smarter manufacturing in the era of Industry 4.0 with Graybar Industrial Solutions. Whether you’re looking to improve operational efficiency, harness the power of your data, or scale your operations for future growth, Graybar has the logistical expertise and access to top manufacturers to help you keep everything moving and working like it should.