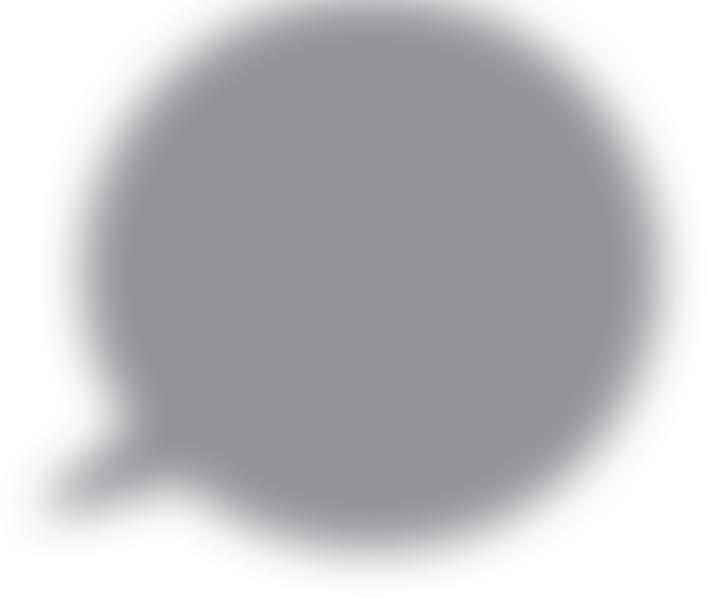
11 minute read
Design For Additive Manufacturing
An experiment in 3D printing in zero gravity
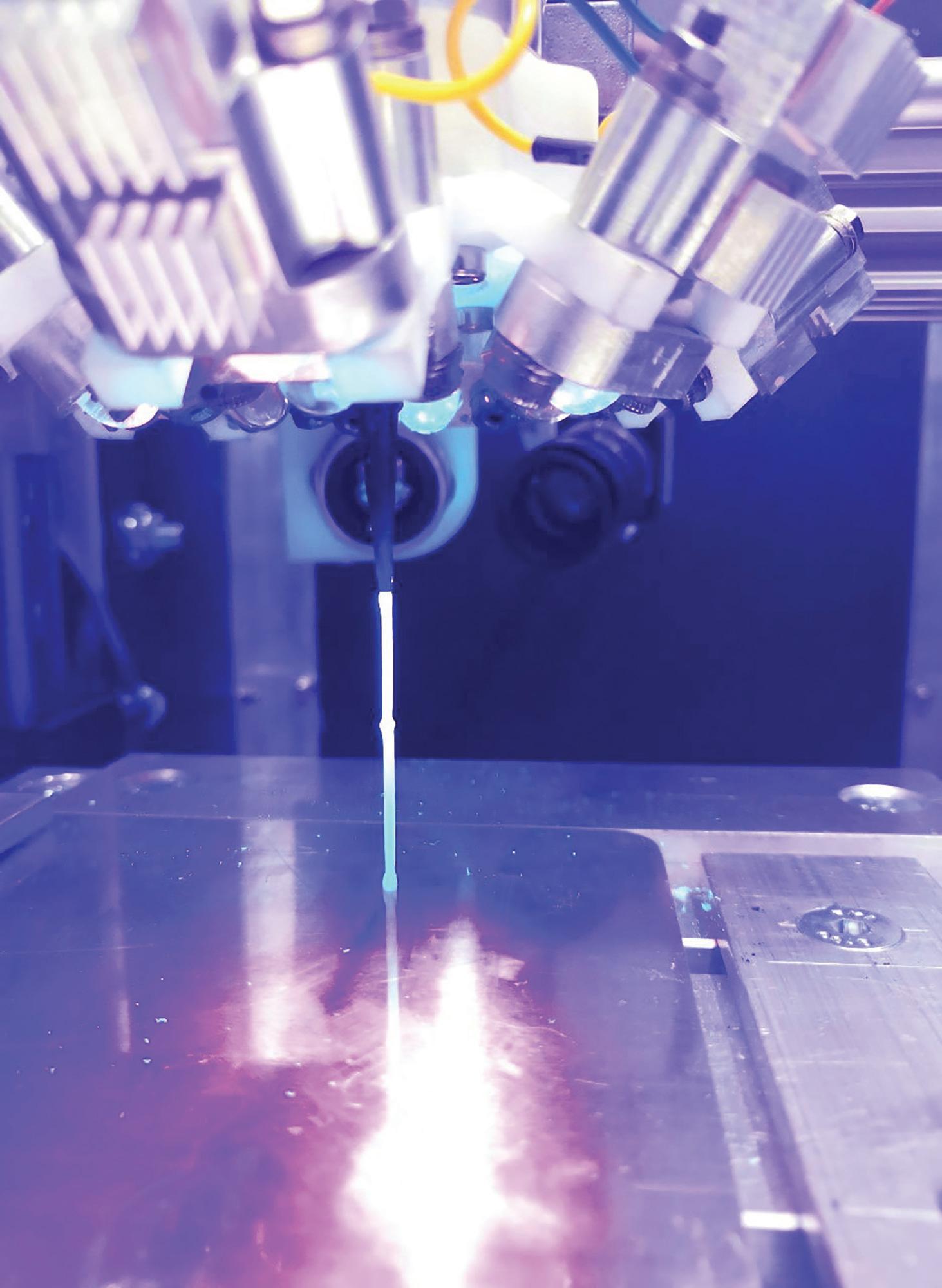
The resin is cured by UV radiation. USB 3 cameras, from IDS, keep an eye on the process. A number of researchers are
exploring the use of 3D printing/additive manufacturing in space applications. One experiment is testing the possibility of using 3D printing to make spacecra components directly in orbit. The Additive Manufacturing In Space (AIMIS-FYT) team at Munich University of Applied Sciences is developing and researching an additive manufacturing process in which the production of structures takes place in zero gravity. The benefi t here is that elements produced this way for space travel do not have to meet the high launch requirements. The process is being researched on parabolic fl ights in zero gravity - supported by a uEye CP industrial camera om IDS. For this additive manufacturing process the AIMIS-FYT team developed a 3D printer with an extruder that dispenses a liquid photopolymer. “Our 3D printing process can directly print three-dimensional structures in space using a UV-curing adhesive or potting compound,” says Torben Schaefer, press o cer of the AIMIS-FYT team. Rather than create components layer by layer, the team created a 3D printer that builds parts directly using the three-dimensional movement of the print head. UV light cures the resin that is eely extruded into space in zero gravity, hardening the material in a short time. In combination with weightlessness, this process enables manufacturing without shape restrictions that normally exist due to gravity on Earth. Typical shape limitations are, for example, long overhangs that are not possible on
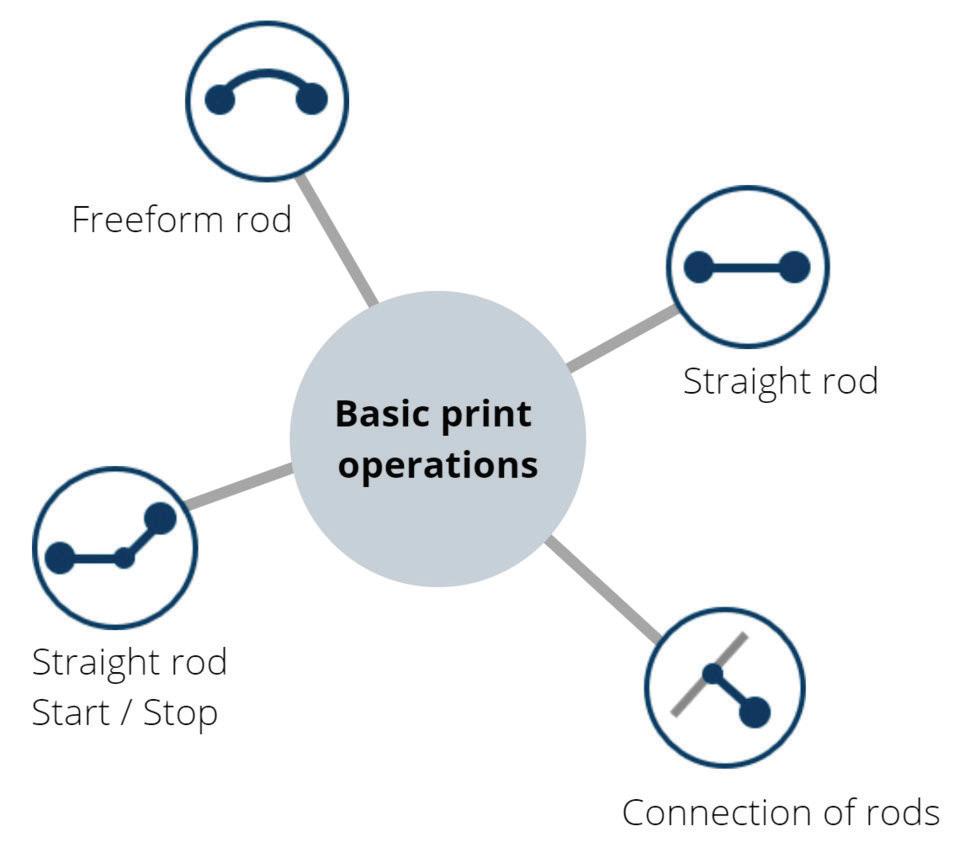
The four basic operations
of 3D printing.
earth or that can only be manufactured with elaborate support structures. In zero gravity, it is even possible to create components without a fixed anchor point, such as a pressure plate.
This production process enables a variety of designs, such as printed structures for solar panels or antennas. For example, the production of mirrors for parabolic antennas or the manufacture of truss structures for the mounting of solar generators is possible. Those who develop small and micro satellites or even entire satellite constellations, can make them in orbit, rather than on Earth, reducing unit and launch costs for transporting their systems into orbit. Building satellites in space also enables developers to take more fuel on board, extending the use life.
“For satellites, the fuel is usually the limiting factor; at present, it usually lasts for around 15 years,” explains Torben Schaefer.
One of the first tests was the printing of straight rods, connections of rods and the creation of free-form rods. In one case, a conventional printing plate was used as the starting point for printing; in another case, the behavior of printing, free-floating rods was investigated.
The 3D printing process The main parameters of the printing process are the extrusion speed of the resin, the UV light intensity, the UV light time and the trajectory-- or the movement path of the printer.
“In our printing process, precise, pressure-stable and constant delivery of the medium is important. At the same time, the parameters should be kept constant during the entire process,” says Torben Schaefer. The USB 3 camera sponsored by IDS keeps a close eye on the process: It watches the nozzle of the printer in close-up and always moves relative to it. This way, the camera follows the nozzle with every movement. The image is cropped in such a way that the formation of the rods is captured around 4.5 cm below the nozzle.
“The IDS camera provides important results for the discharge of the resin and its curing. The UV LEDs produce a strong overexposure, which means that difficult lighting conditions exist. These are no problem for the U3-3260CP from the IDS portfolio: with the cost-effective 2.30 MPixel Sony sensor IMX249 (1920 x 1200 px). It makes the global shutter CMOS sensor with its 5.86 µm pixels predestined for applications like these, which are supposed to deliver a perfect result even in difficult lighting conditions - in this case, strong brightness due to overexposure.
To further analyze the exit behavior from the nozzle in zero gravity, the process is carried out at a slower speed. The contour of the rod must be precisely captured.
“For this, the high frame rate and resolution of the camera are crucial for a high-quality evaluation,” says Torben Schaefer from the AIMIS team. With a frame rate of 47.0 fps, the IDS camera ensures good image quality with minimal noise - perfect conditions for its task in space.
A finished truss structure
in zero gravity - detail shot from the IDS camera.
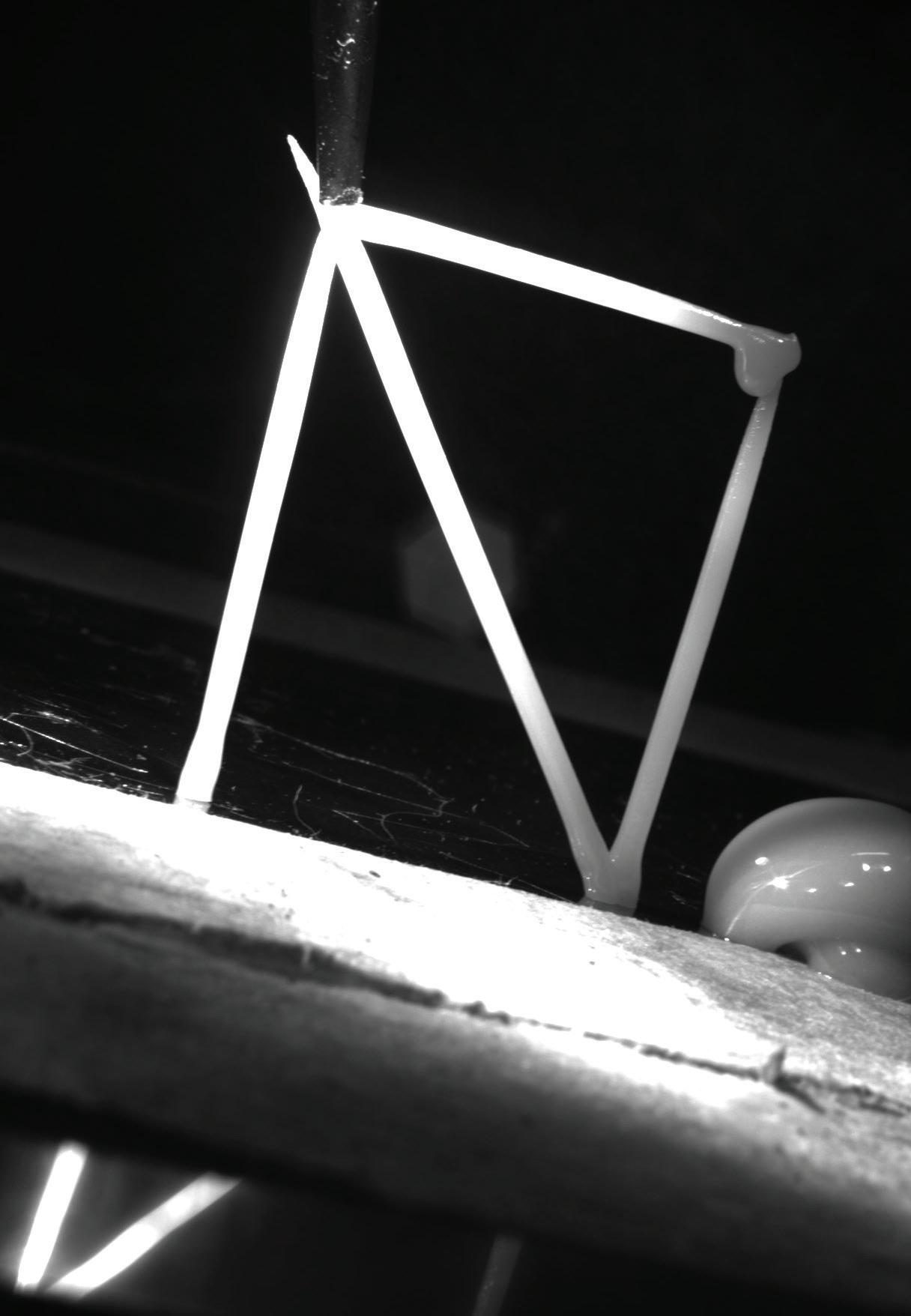
Design for Additive Manufacturing
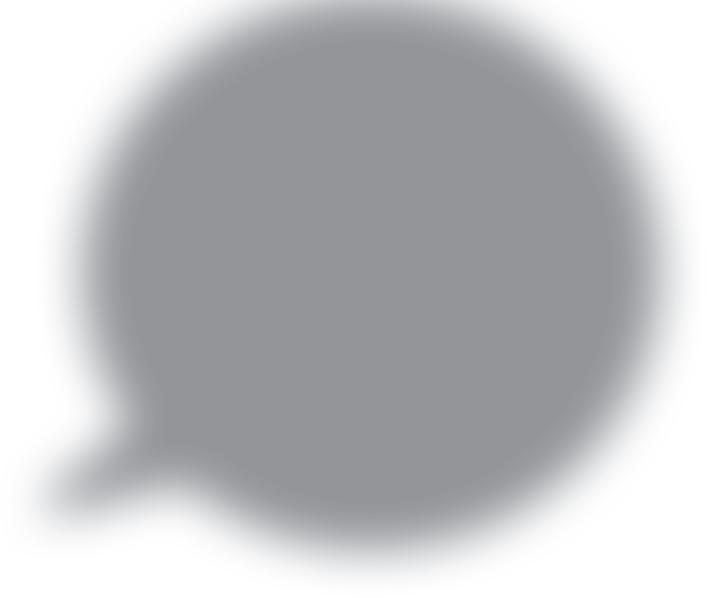
In addition, the camera was easy to install. “We were able to seamlessly integrate the camera into our C++-based monitoring system with the help of the IDS SDK,” says Torben Schäfer. According to him, this is where all the data om the sensors converge and provide a comprehensive overview of the current status of the printer and the individual print parameters. “We can start and stop the recording of the IDS camera and all other measurements with one click. Since there are only twenty seconds of zero gravity on a parabolic fl ight and there is a break of around one and a half minutes between two parabolas, we only save the most important information by starting and stopping measurements and recordings in a targeted manner.” In addition, a live image of the printing process is displayed on the monitor with the help of the IDS so ware. “This live feed makes it easier for us to set up and quickly analyze the printhead.”
Outlook The fi ndings om the experiments will be used to further optimize the printing process of the four basic 3D printing operations (straight bar, straight bar with start / stop points, ee-form bar as well as connections between bars) and to prove the primary function of additive manufacturing in zero gravity. The aim is to test the technology in space, as it off ers the chance to drastically reduce the cost of components in space technology. “With the AIMIS-FYT project, we have the opportunity to actively shape the future of space travel,” says Michael Kringer, project manager of the AIMISFYT team. The powerful little IDS camera has successfully recommended itself for future missions - on Earth and in space.
DW
IDS Imaging Development Systems GmbH en.ids-imaging.com
WHAT DO YOU THINK?
Connect and discuss this and other engineering design issues with thousands of professionals online
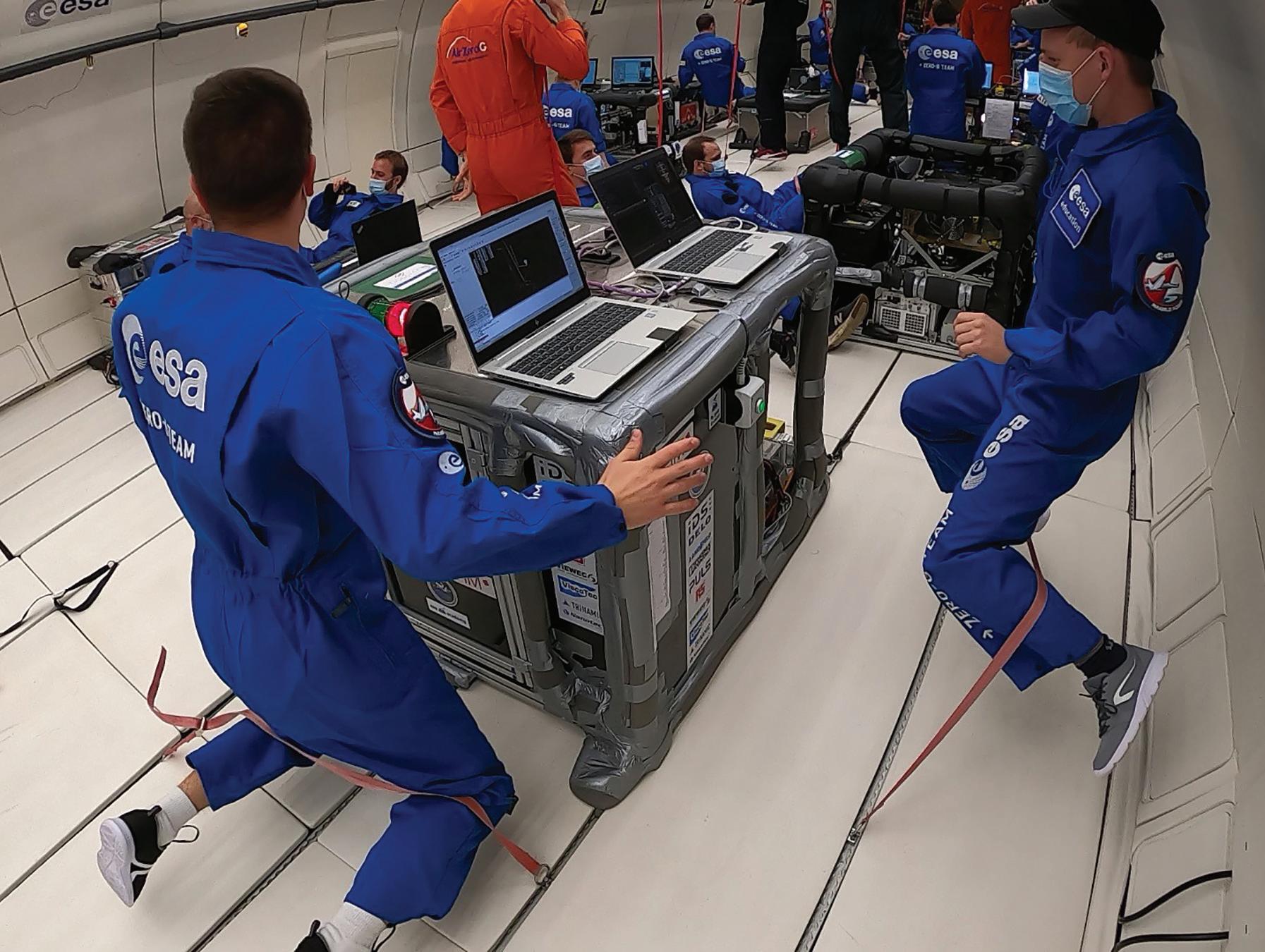
During the parabolic fl ight of the esa programme FYT, zero gravity prevails for 20 seconds.
Design software automates the creation and production of lattices
Subscribers to Carbon3D’s 3D
printing technology now have access to the Carbon Design Engine software, which automates the process of creating performance-oriented lattices. The lattice generating technology has been proven in production with the design of critical lattice products like the Resolution Medical Lattice Swabs developed for COVID-19 testing, Specialized S-Works Power Saddle with Mirror technology, and CCM Super Tacks X helmets.
The cloud-based application provides the computational power to generate complex shapes quickly and efficiently without requiring local resources. Design Engine software has a fully interactive user interface and offers product teams the ability to produce five different types of conformal lattices. The software creates conformal lattices that robustly populate even the most challenging design surfaces, eliminating the tedious design revisions post-generation.
“Traditional CAD tools have not kept pace with the innovation of 3D printers and materials. This lack of progression limits the ‘idea to design’ stage of the product development lifecycle. With the release of Design Engine to all Carbon subscribers, we are helping designers iterate through their design thinking, faster,” said Phil DeSimone, Chief Product and Business Development Officer. “On average it can take 18 - 24 months to bring a consumer product to market. But when we put the best design tools, 3D printers and materials in the hands of designers and manufacturers, we’ve seen our customers accelerate the development of innovative new products - going from idea to finished designs to production in less time.”
3D printing enables the production of latticed parts that can deliver considerable mechanical performance advantages beyond those that can be produced via traditional production methods. However, traditional design tools are limited in their additive manufacturing support, particularly for complex geometries like lattices, which makes designing functional parts difficult. To simplify lattice design generation, Carbon developed the Carbon Design Engine to collaborate on design projects with customers, and has now made it available for all subscribers to access directly.
“Working with Carbon allowed CCM to leverage its pipeline to launch something the industry had never seen before in the Super Tacks X helmet,” said Jeff Dalzell, Vice President of Product Creation at CCM Hockey. “Within days of prototyping with the Design Engine, we gained creative insights into even more applications for performanceoriented lattices in our future product lines.”
Due to its deep integration with Carbon’s platform and materials, Design Engine can predict lattice performance prior to lattice generation, streamlining design optimization. Similarly, Design Engine offers builtin guidance to help engineers develop successful parts. DW
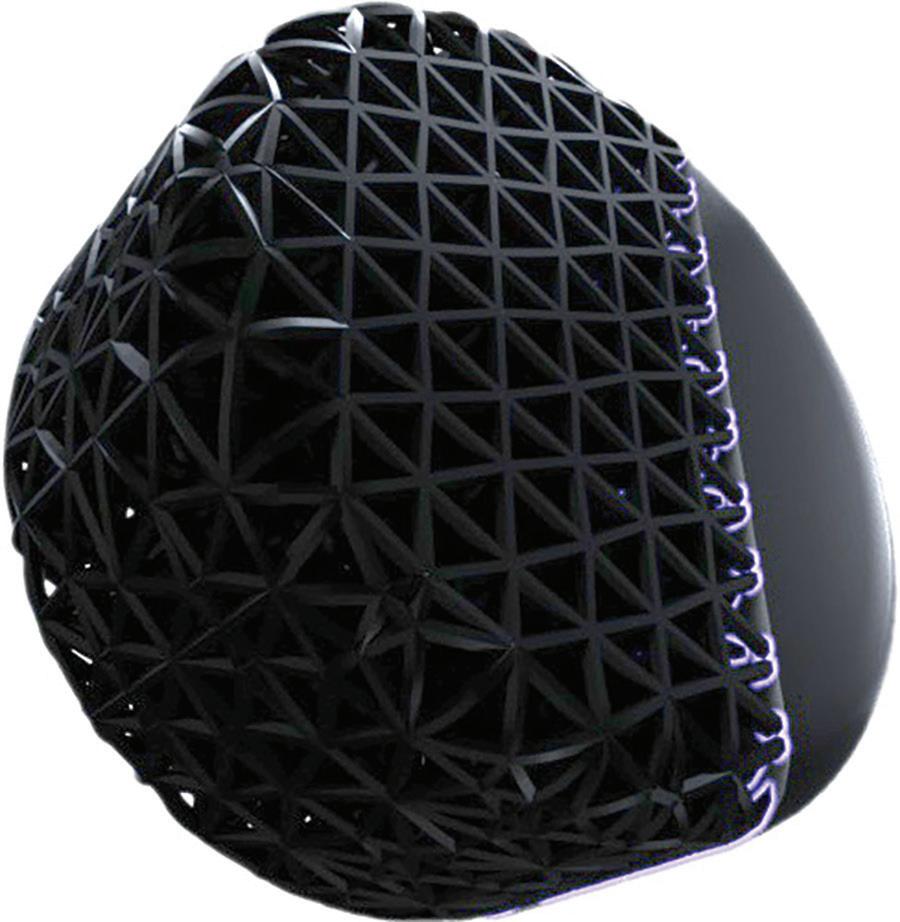
Carbon www.carbon3d.com
Design for Additive Manufacturing
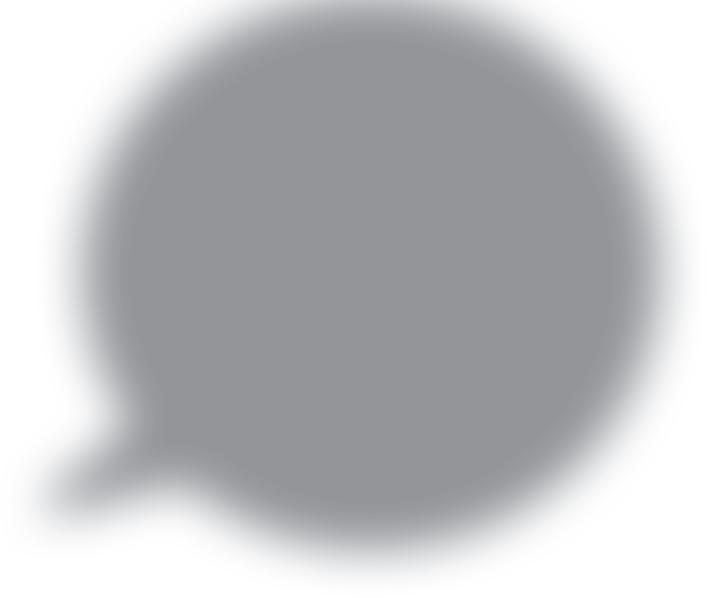
Desktop Metal announces a fully dense, sinterable 6061 aluminum powder
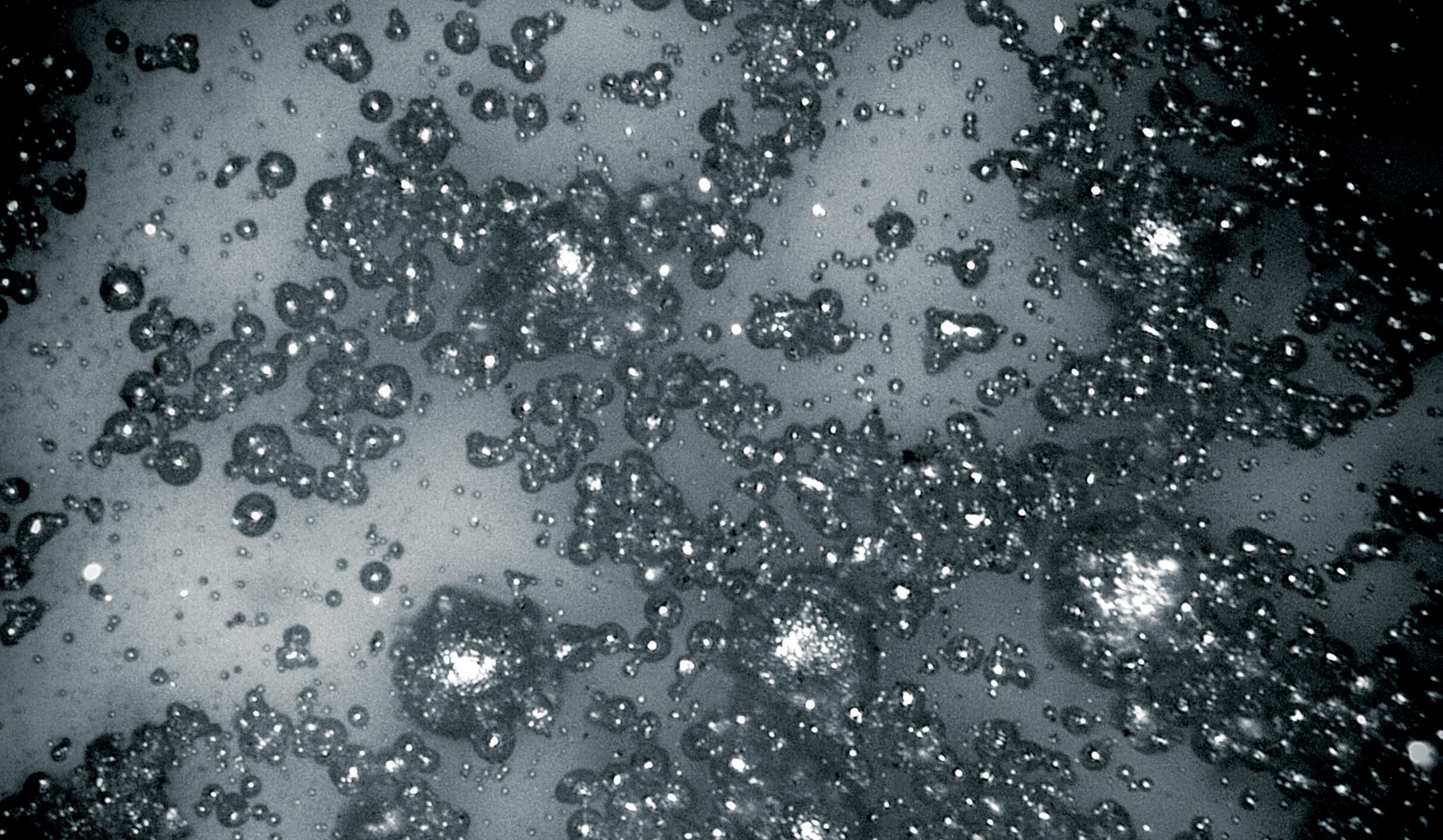
Desktop Metal, Inc., and Uniformity Labs, a leading additive
manufacturing company of industrial 3D printing materials and processes, announced a breakthrough powder that enables aluminum sintering for binder jetting AM technology. This new powder is the result of a multi-year collaboration between the companies to develop a low-cost, raw material yielding fully dense, sinterable 6061 aluminum with greater than ten percent (10%) elongation and improved yield strength (YS) and ultimate tensile strength (UTS) versus wrought 6061 aluminum with comparable heat treatment. Said Ric Fulop, CEO and co-founder of Desktop Metal, “The global aluminum castings market is more than $50 billion per year, and it is ripe for disruption with binder jetting AM solutions. These are the best reported properties we are aware of for a sintered 6061 aluminum powder.” “The introduction of lightweight metals to binder jetting opens the door to a variety of thermal and structural applications across industries,” said Adam Hopkins, founder and CEO of Uniformity Labs. “This development is a step towards the adoption of mass-produced printed aluminum parts.” Prior techniques used to sinter aluminum included coating powder particles, mixing sintering aids into the powder, using binders containing nanoparticles, or adding metals such as lead, tin, and magnesium. The new powder also enables compatibility with water-based binders and has a higher minimum ignition energy (MIE) relative to other commercially available 6061 aluminum powders, for a better safety profi le. Desktop Metal and Uniformity Labs plan to continue to work together over the coming year to quali the powder and scale production for commercial release. Once fully qualifi ed, Uniformity 6061 aluminum will be available for use with the Desktop Metal Production System platform, which off ers an inert, chemically inactive processing environment and auxiliary powder processing equipment. DW
Desktop Metal www.desktopmetal.com
Uniformity Labs www.uniformitylabs.com
Stratasys multi-material J5 DentaJet 3D printer enables mixed trays of dental parts
The J5 DentaJet 3D
printer is a multi-material dental 3D printer that enables technicians to load mixed trays of dental parts. The 3D printer can produce at least five times more dental parts on a single mixed tray than competitive 3D printers, yet its compact footprint consumes only 4.6 sq. ft (0.43m2) of floor space.
Dental labs must produce several parts in multiple materials for either removable partial denture (RPD) applications or dental implant cases. For example, each implant case comprises a top and bottom rigid opaque model, a soft gingiva mask, and a biocompatible surgical guide. This requires three different materials, forcing technicians to either use multiple 3D printers or do separate 3D prints using different materials. The J5 DentaJet easily handles up to five materials, including support material.
The multicolor, multi-material J5 DentaJet also produces 3D-printed case presentations with realism previously possible using time-consuming wax models. Now, designs can be produced digitally in a few hours. The high resolution of PolyJet materials means dentists can seat crowns and bridges in minutes due to the accuracy of the models – to 18.75 microns, or less than half the width of a human hair.
According to Stratasys estimates, the total addressable segment for dental 3D printing is about $1 billion. With a growing array of 3D printing technologies, from polymerization to stereolithography, Stratasys can be a complete 3D printing provider for its customers, matching the right technology to the right application. The J5 DentaJet is now ideal for customers needing to produce high volumes of realistic, highly accurate models.
The J5 DentaJet is launching with a full range of resins tailored to meet the needs of the dental industry. Available biocompatible resins include a clear resin, VeroGlaze opaque white for temporary in-mouth placement, and a clear and flexible resin. In addition, Separator digital material automatically coats models to make it much easier to separate the acrylic device from the model and remove wax and residue. Other available resins include VeroDent PureWhite, and CMY resins for color.

The J5 DentaJet 3D printer is available now. DW
Stratasys www.stratasys.com