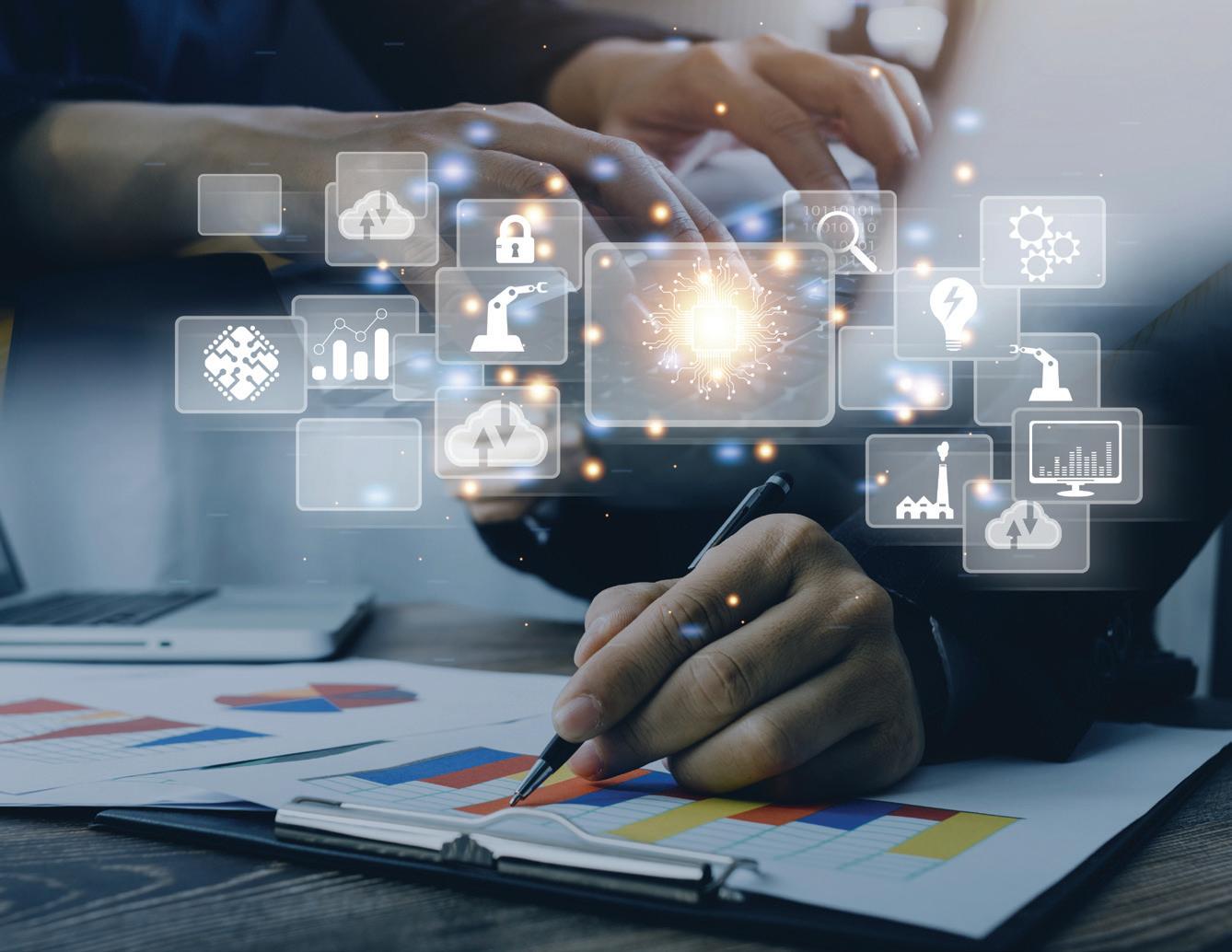
2 minute read
Sustainable Engineering
Correlating process functions to energy use, raw material consumption, and emissions generation via sensors can yield information about specific operations that can be standardized on one data set. Filters on this locally processed data then remove all irrelevant or invalid data to output actionable information. Edge computing in such arrangements also helps industrial operations keep massive amounts of raw data (the production of which has only grown exponentially over recent decades) o remote servers that globally consume more than 200 trillion Watt-hours every year.
through a facility to profile and target areas of potential improvement.
Key is the reduction of waste heat and emissions from electric utility power plants and transmission systems (purchased power) as well as the power distribution elements, motors, drives, engines, compressors, lights, mechanical components, and other elements under an operator’s control in the plant itself.
The EMIS solution
In many cases, DX software for the improvement of energy e ciency takes the form of energy management information systems or EMISs. EMIS software is complemented by sensors (wired and wireless), data systems, and employee as well as organization programs to review and apply EMIS data collected from energyperformance tracking. Comprehensive deployments can even aggregate the data across a whole plant (or multiple company locations) to optimize energy use. In contrast with legacy approaches (in which operations may have only reviewed energy consumption trends every month or year over year) today’s EMIS-based systems often use sensor- generated data collected every day, hour, or minute (or in realtime) to detect or profile even slight issues rather quickly.
EMIS digital twins can also inform future designs without impacting immediate facility operations. These designs often include component and subsystem purchases such as the procurement of automation subassemblies right-sized for a given application; smart controls to optimize machine routines; regenerative drives; electric motors with NEMA-certified e ciencies; actuators in place of fluidpower technologies; LED lighting; and predictive-maintenance peripherals to identify irregular or degraded system performance before resulting ine ciencies linger or compound energy and production losses.
Edge devices key to reducing waste Sustainability-related programs leveraging edge computing are seeing increased adoption for two main reasons. First of all, edge computing supports green-engineering e orts through its processing of vast data streams to improve monitored operations’ sustainability profile.
In addition, edge computing supports green-engineering e orts by minimizing scrap and defective output products. Because solid industrial waste is nearly twentyfold that generated by municipalities worldwide, all conservation e orts here are worthwhile. Sensor arrays used in this way prevent overproduction of a given ingredient or subcomponent while concurrently preventing the output of defective items destined for scrapping. Continuous machine monitoring quickly identifies value anomalies and malfunctions; these can then trigger warnings, a temporary halt to operation if possible, and [ideally predefined] troubleshooting and corrective measures. Upon completion of machine rebooting or repairs, operations are resumed — and all the collected, filtered, and standardized machine data of the downtime event can be used to yield deeper insights into a given machine’s profile and prevent similar issues in the future … or optimize upgraded or next-generation versions of the equipment. DW
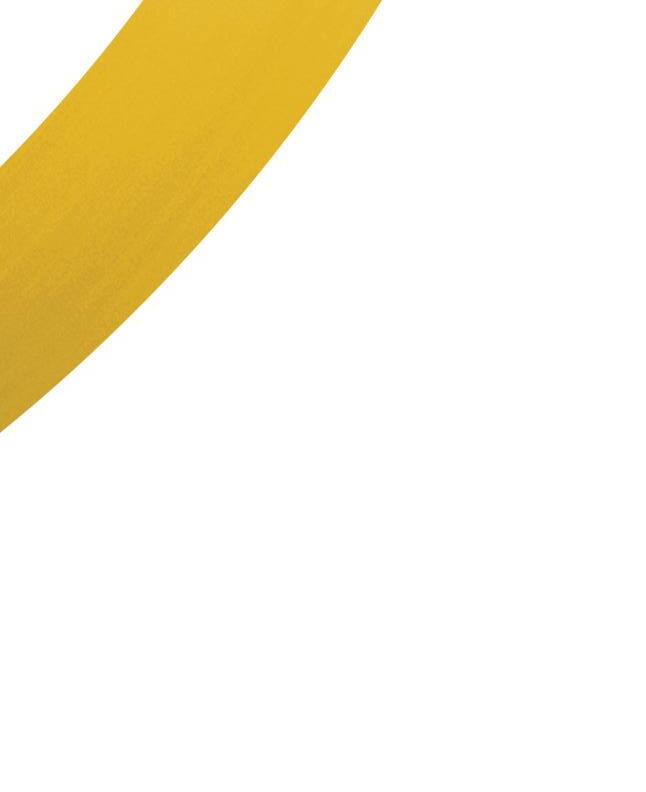
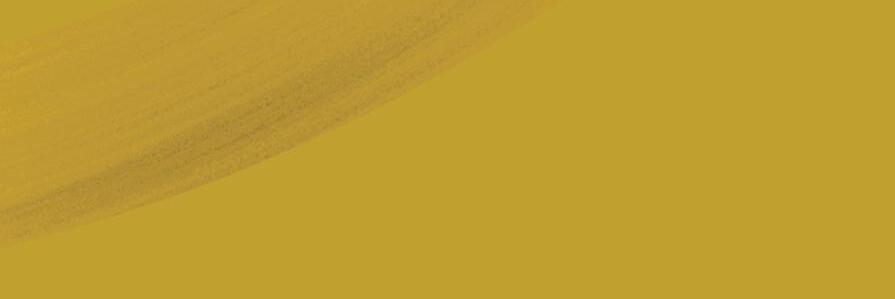
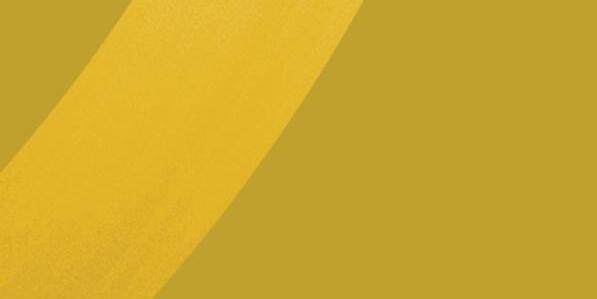

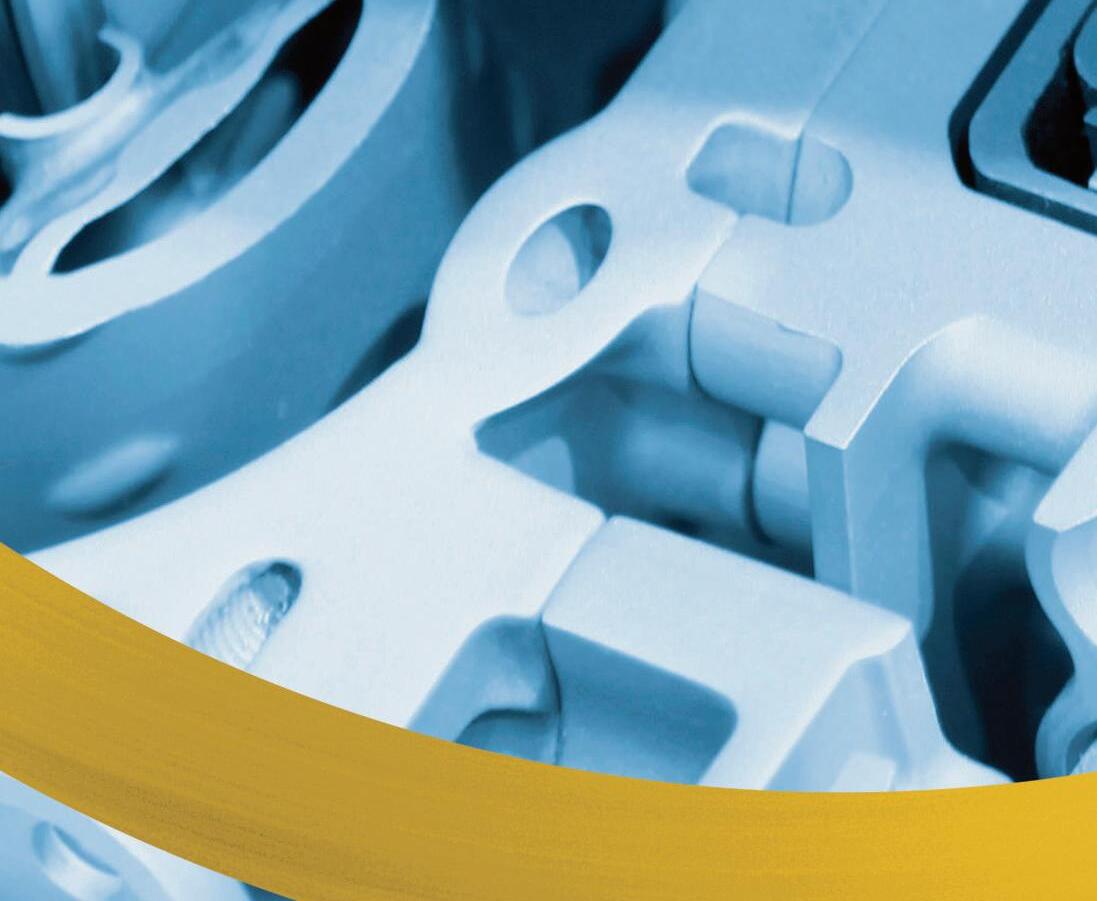
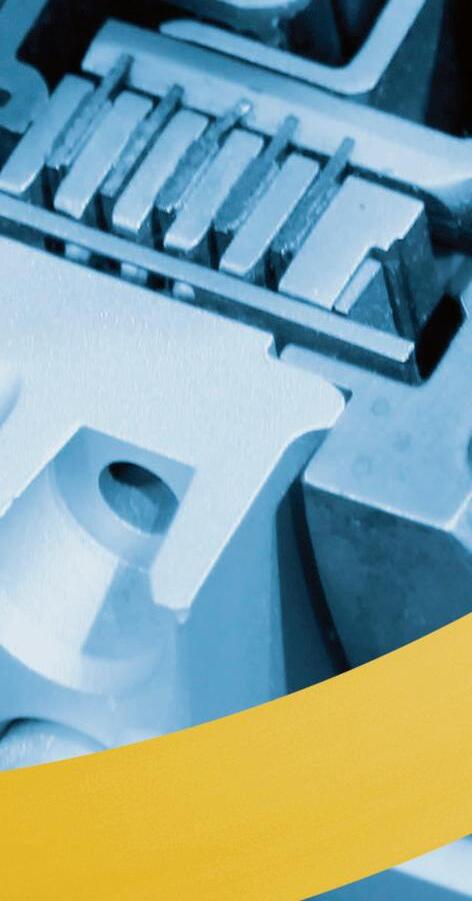
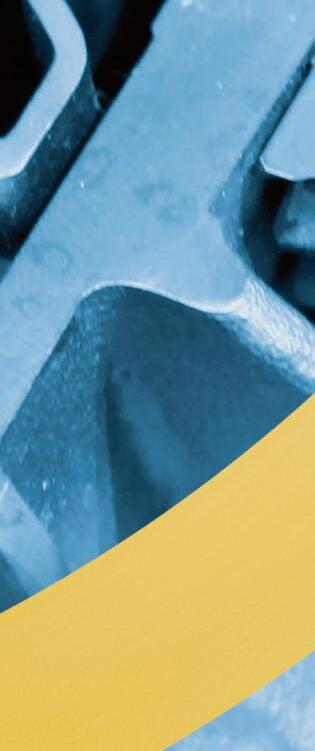
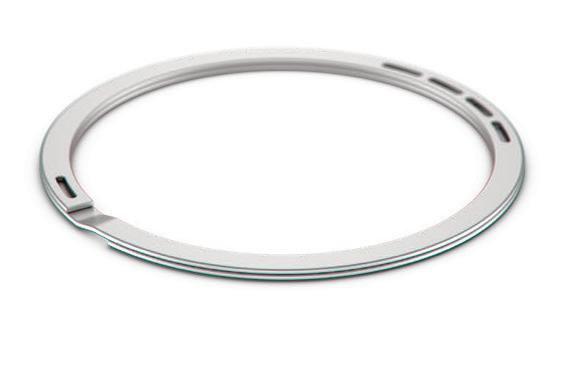

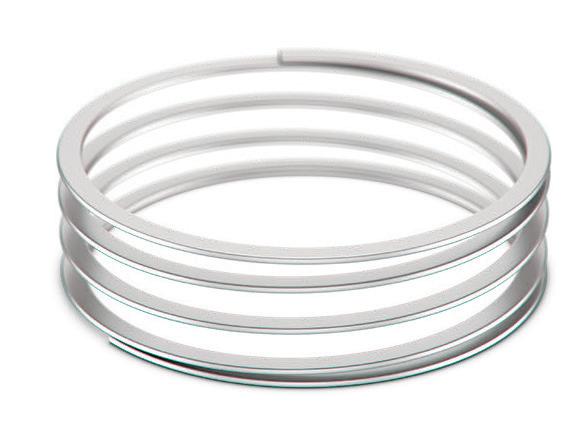
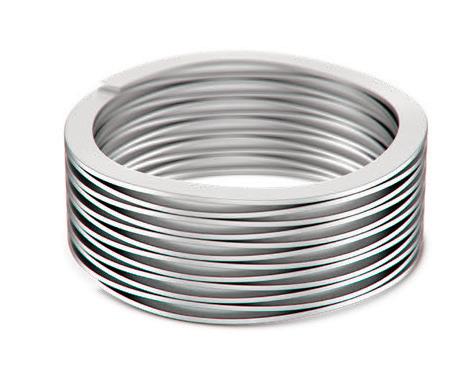

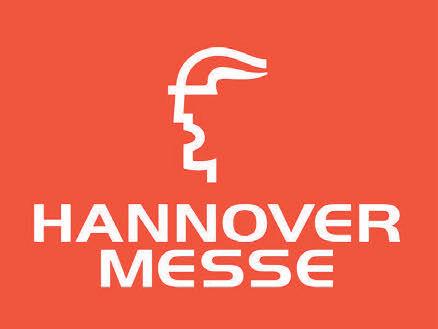


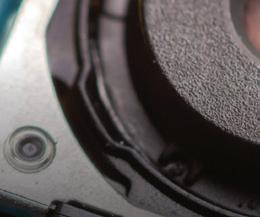
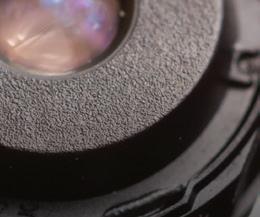

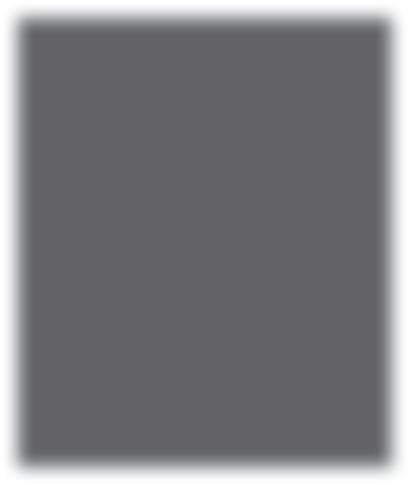
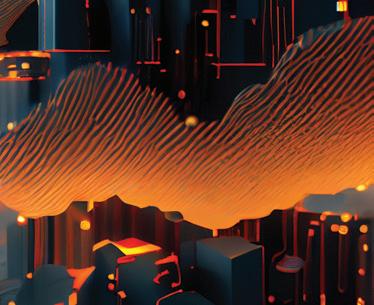
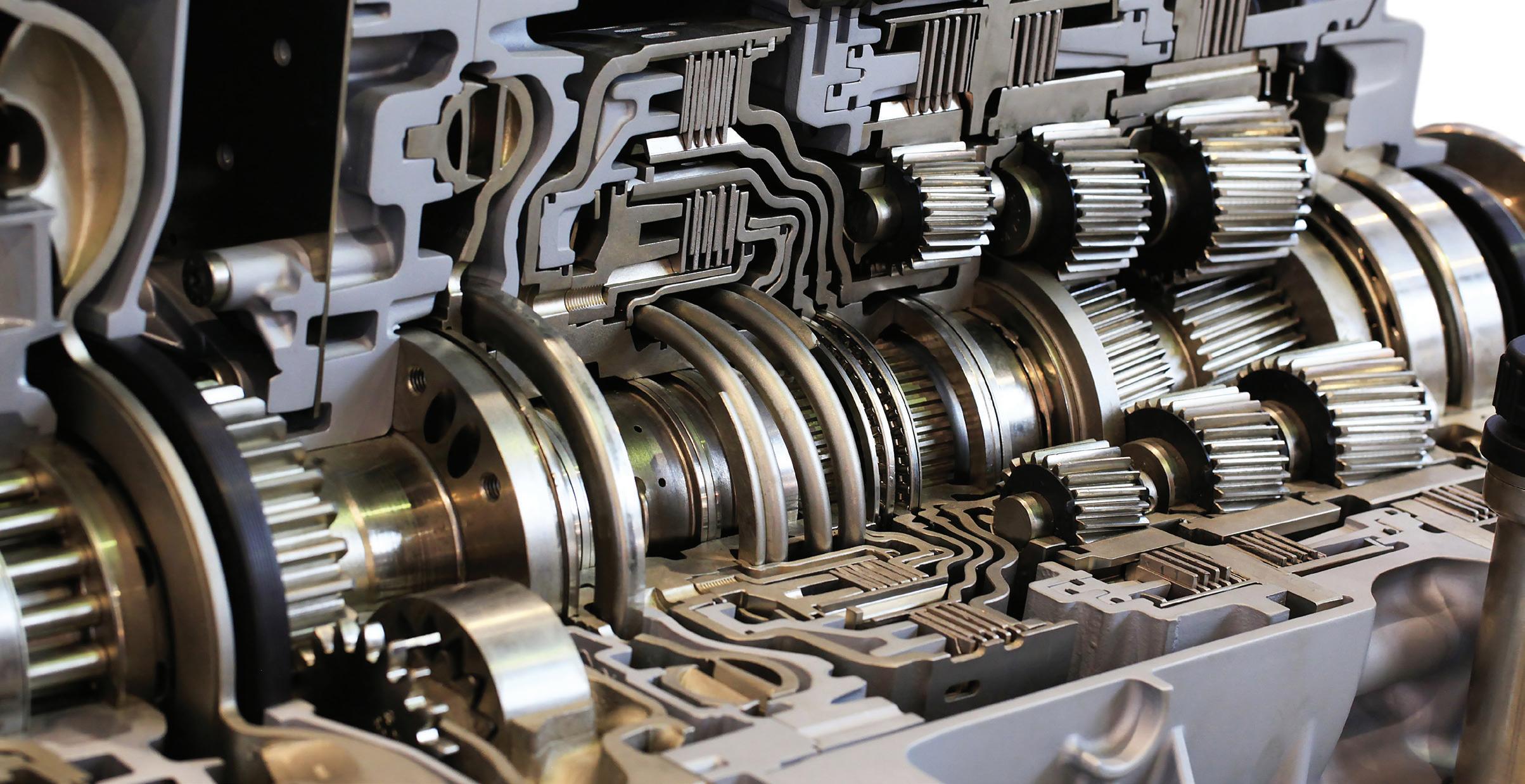
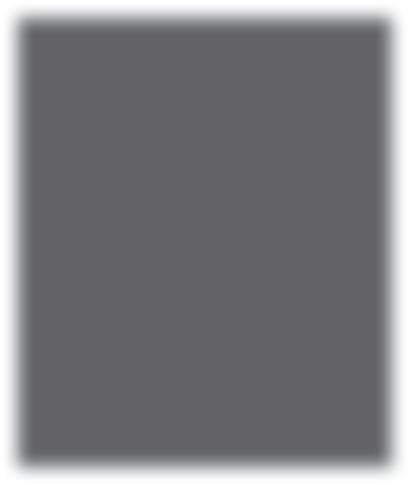
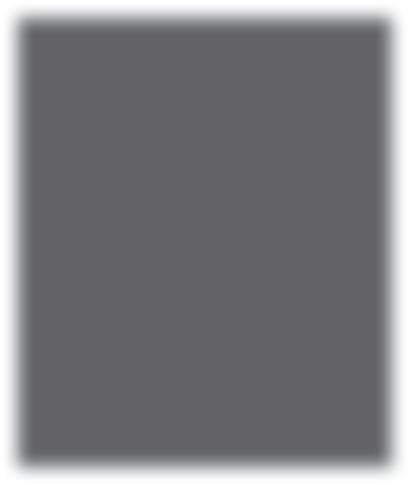
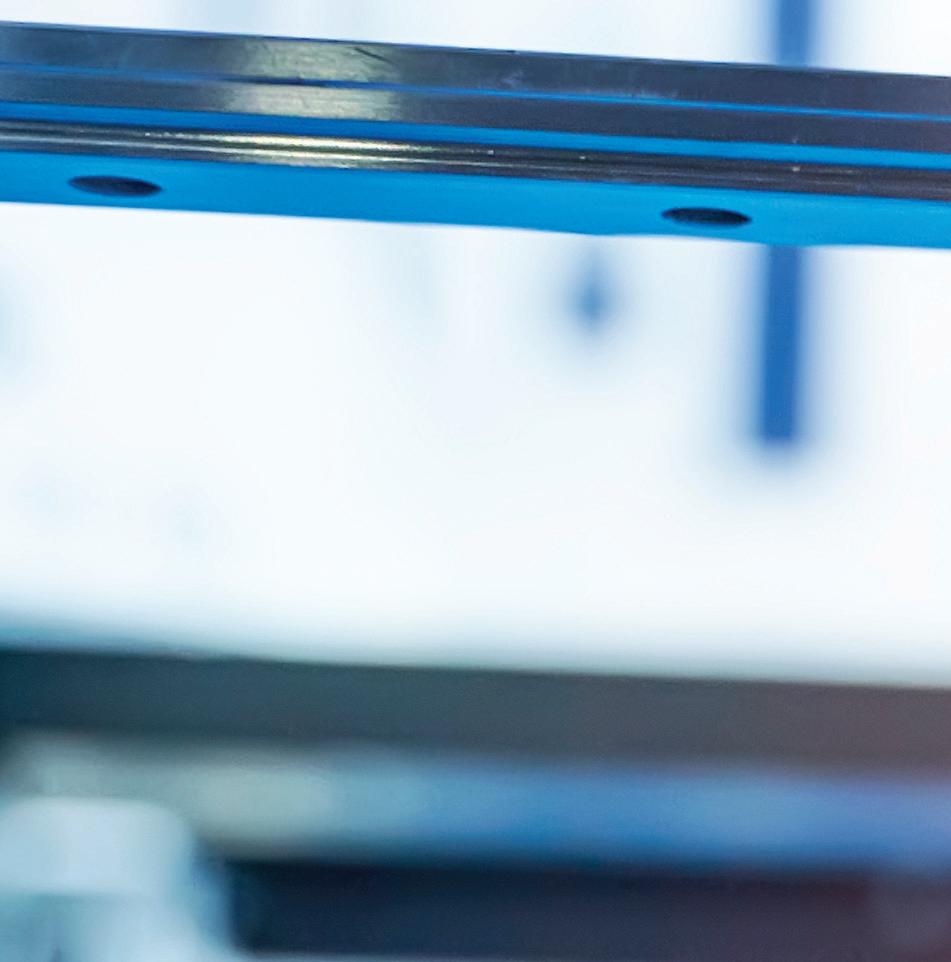
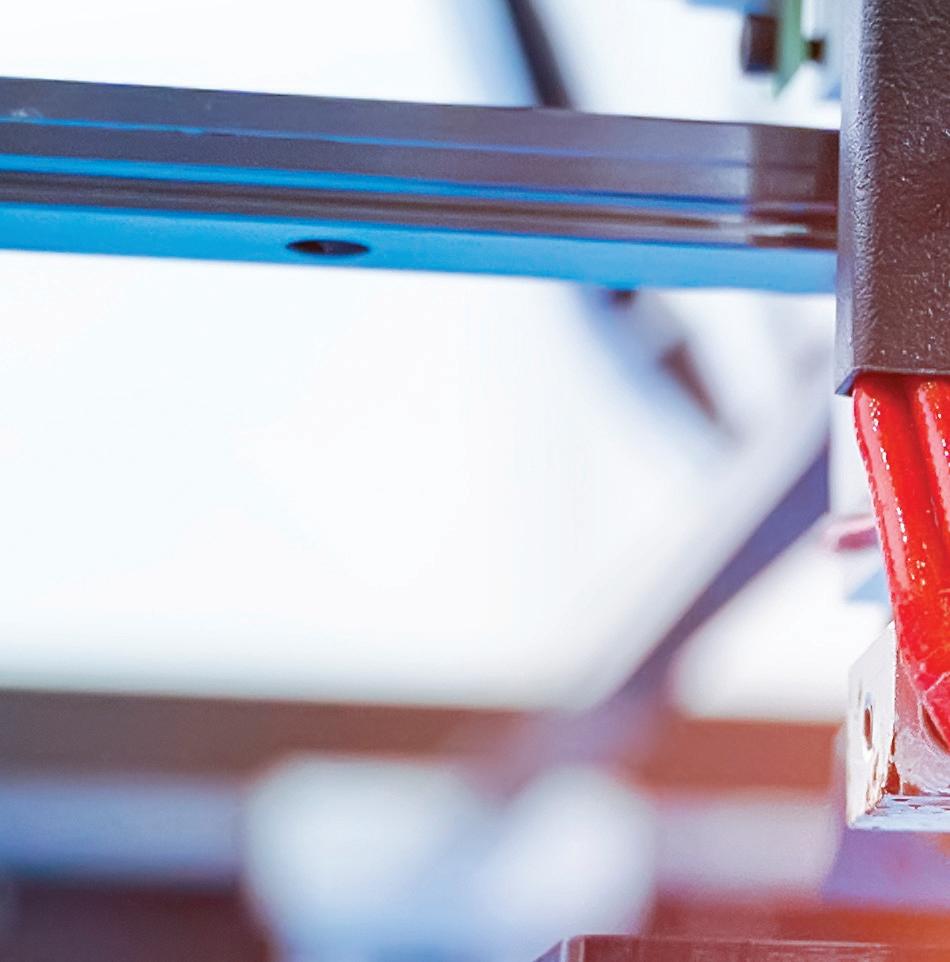
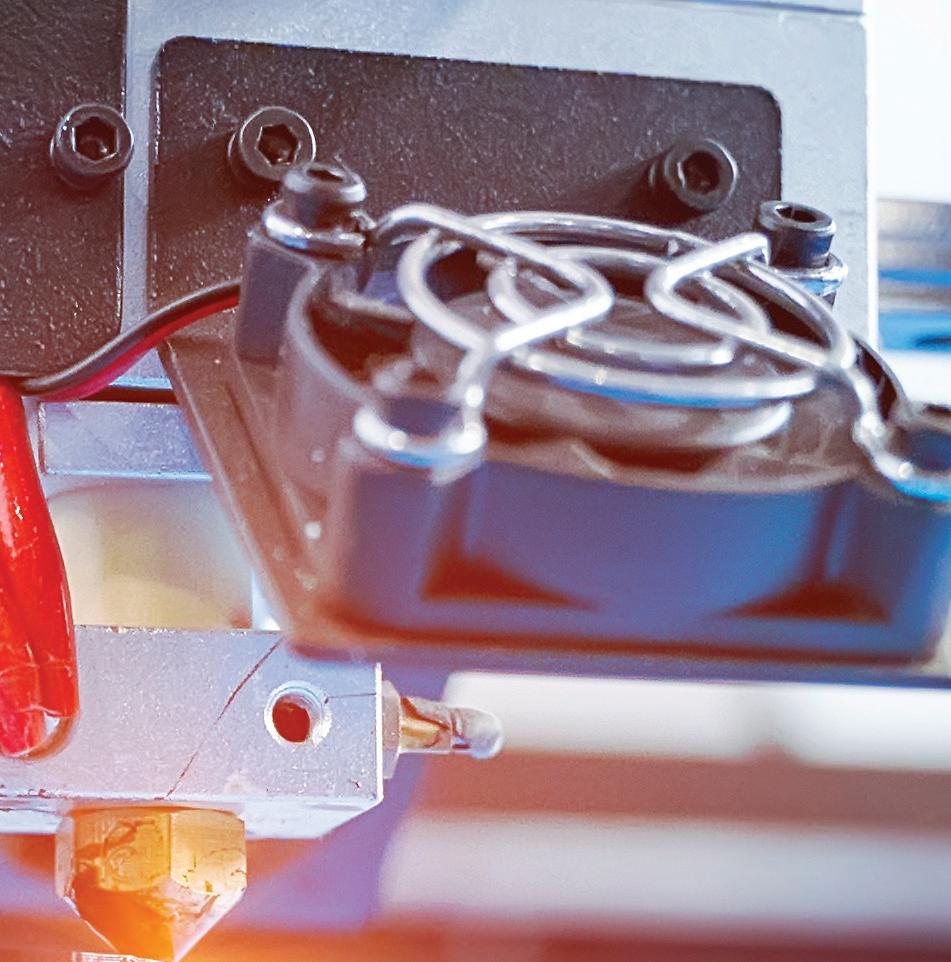

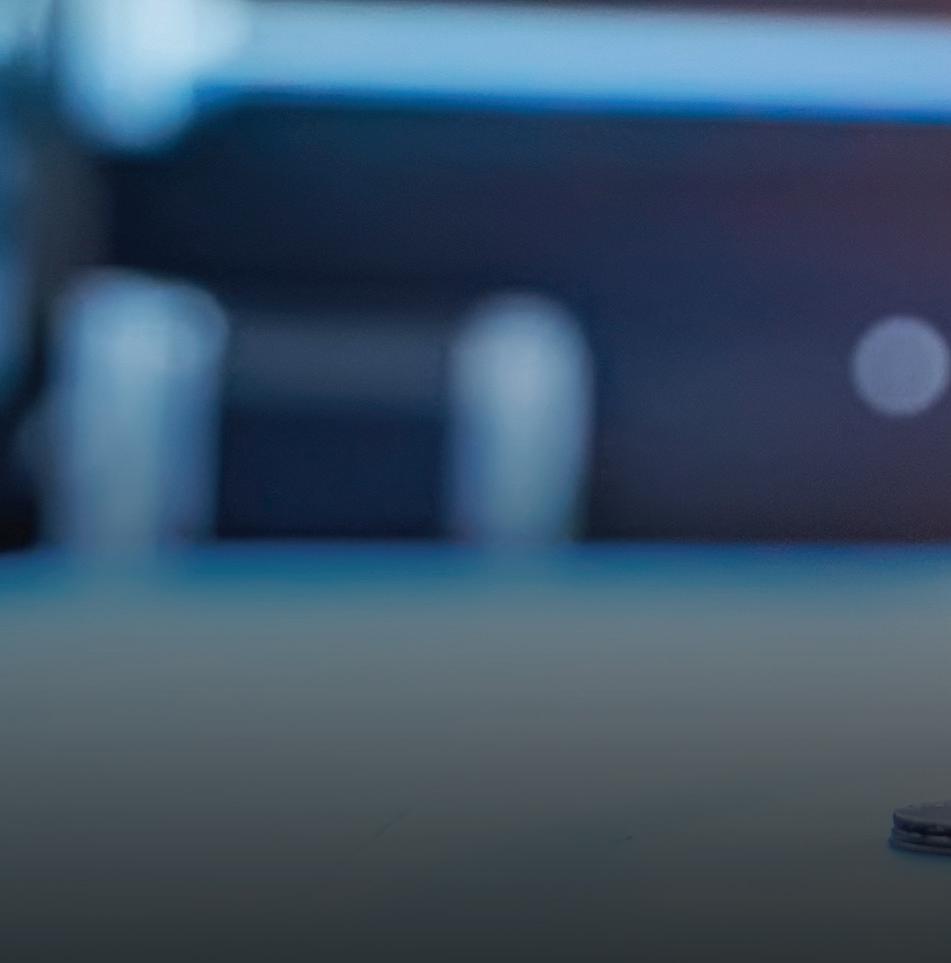
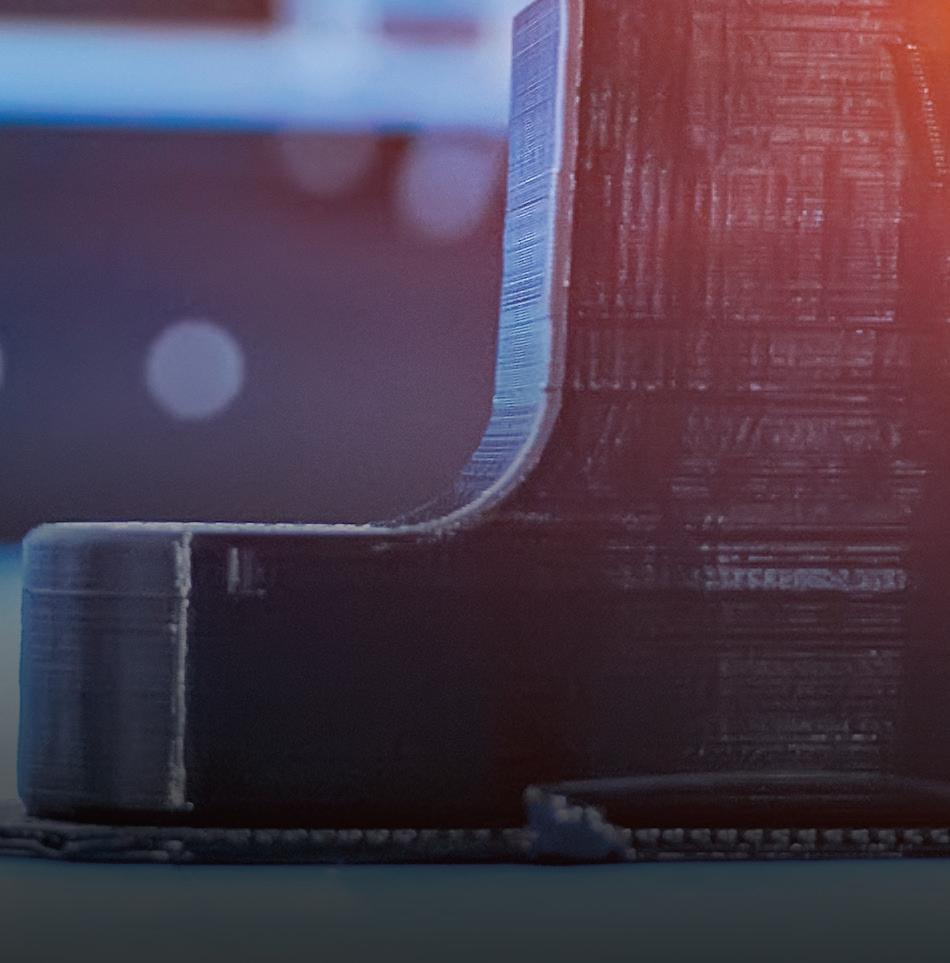
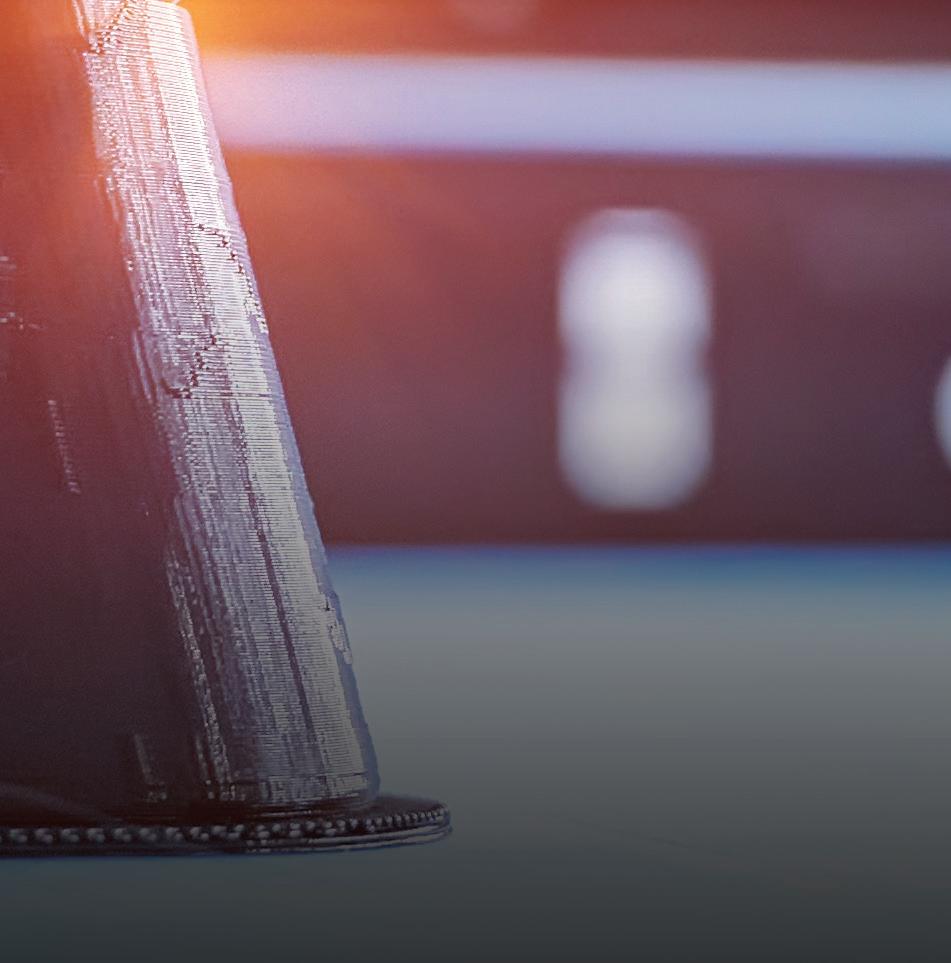

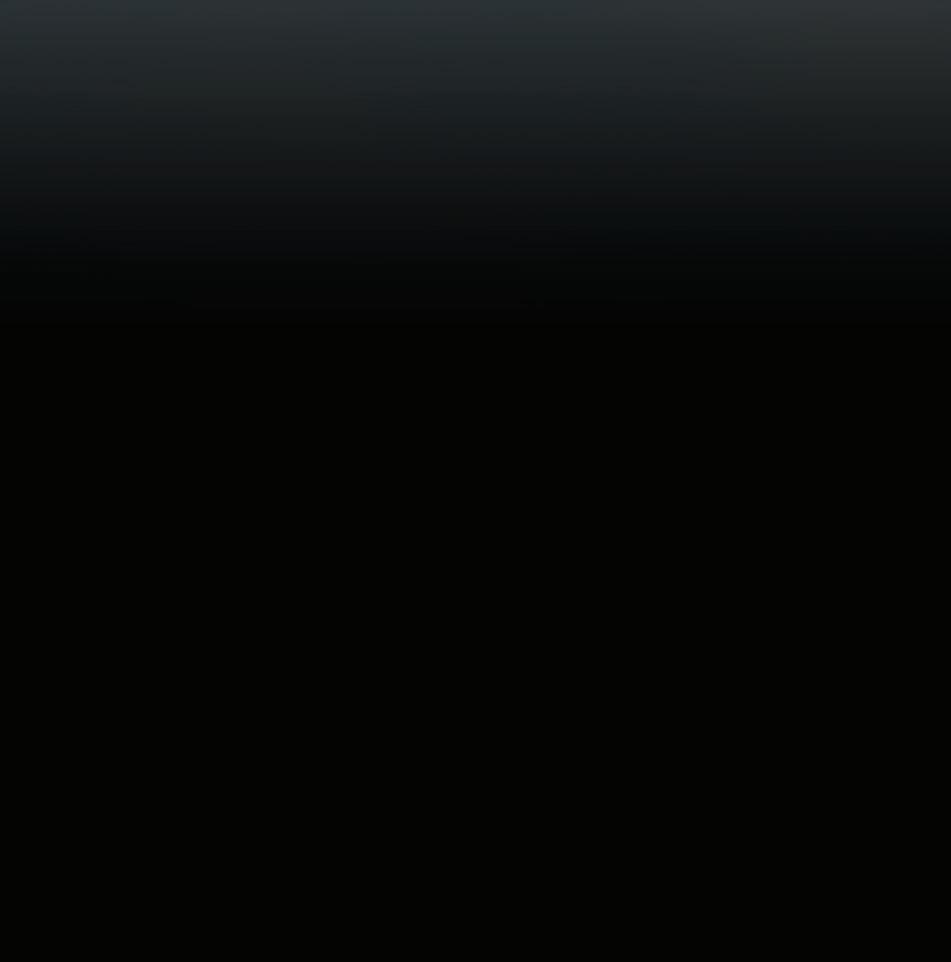

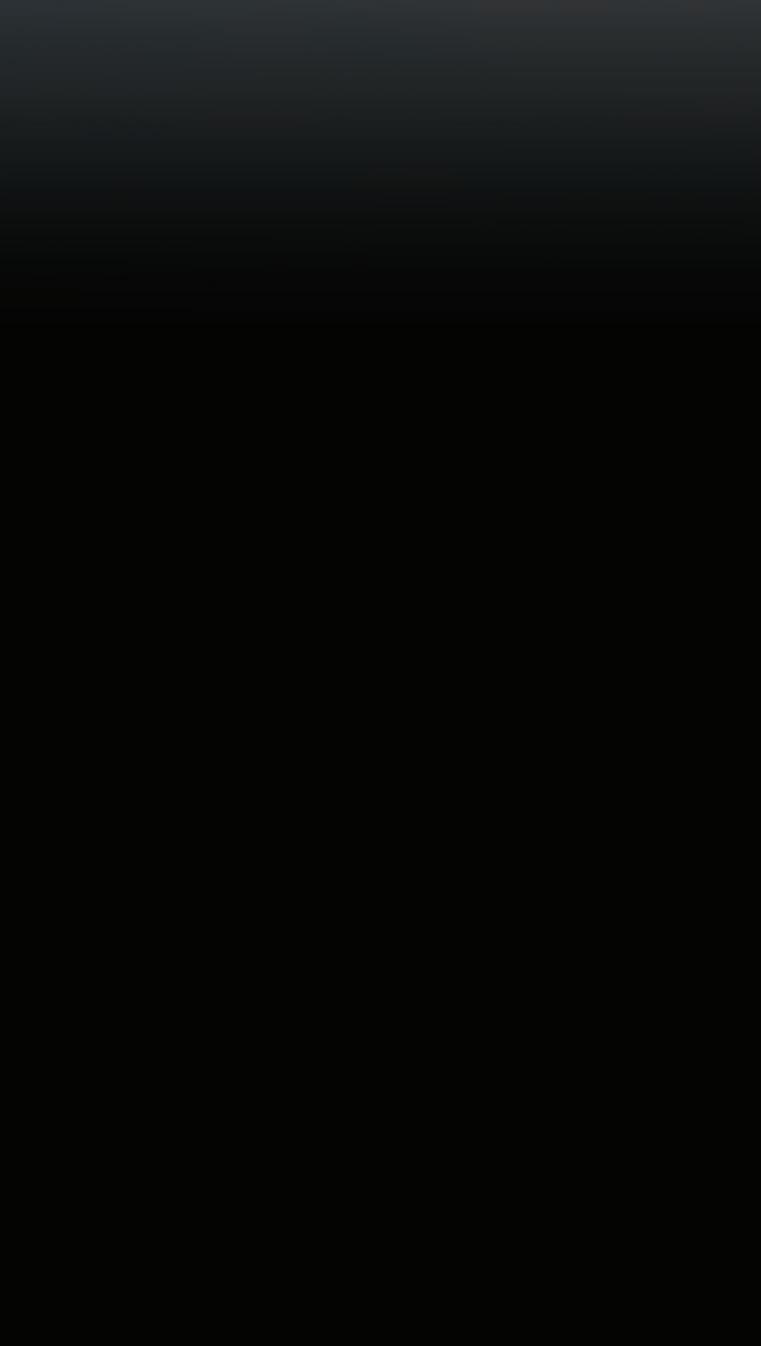
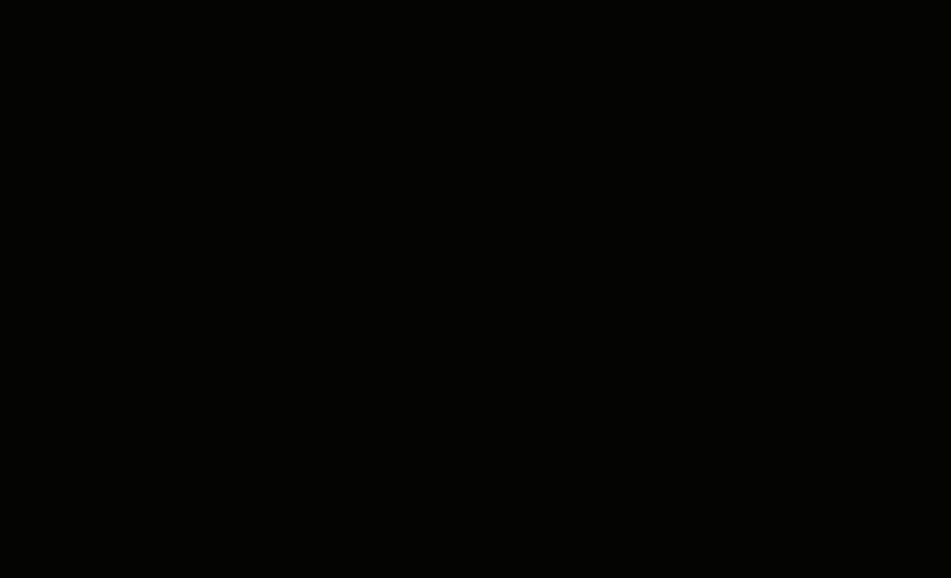
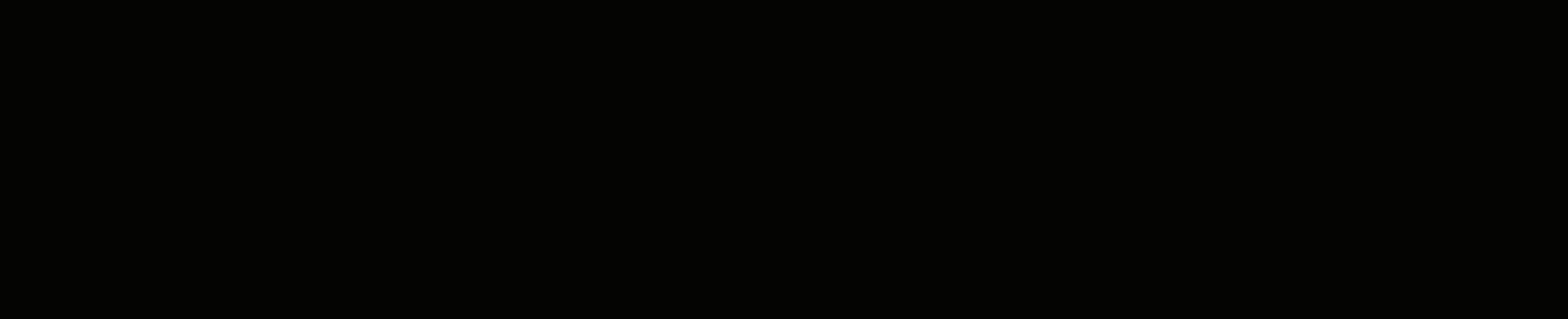
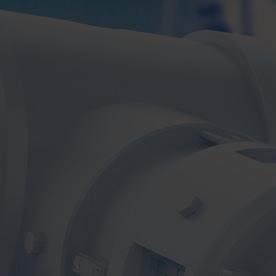
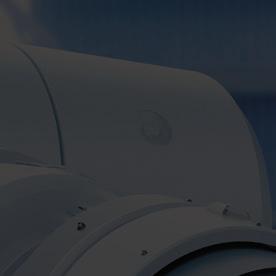
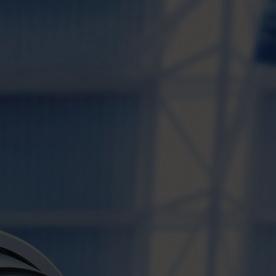
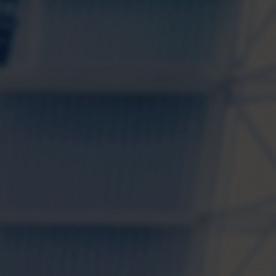
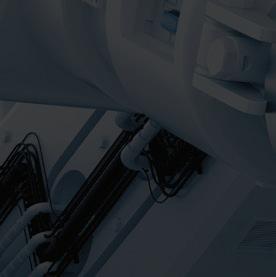
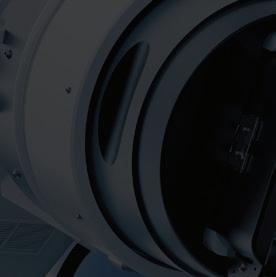

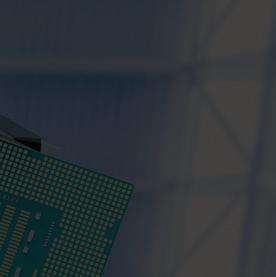

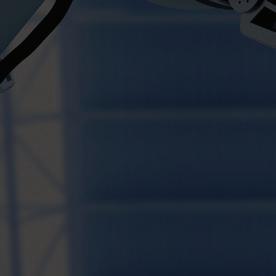
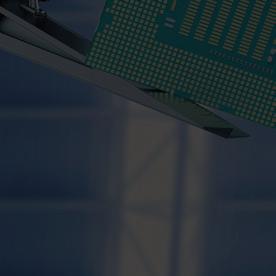
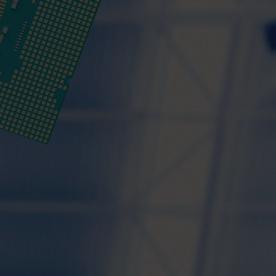

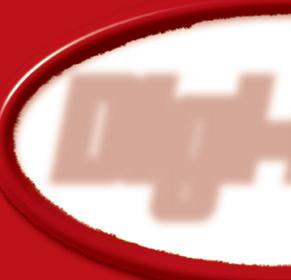
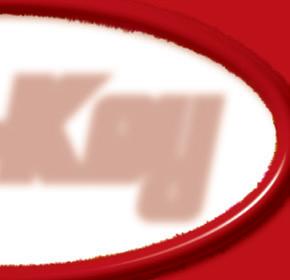
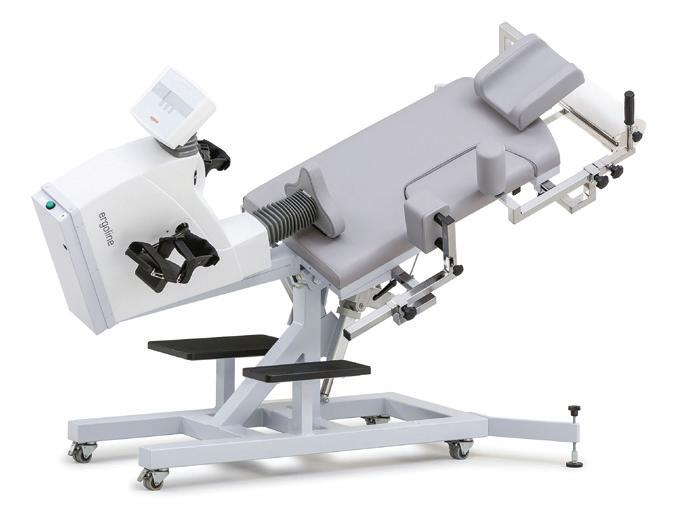
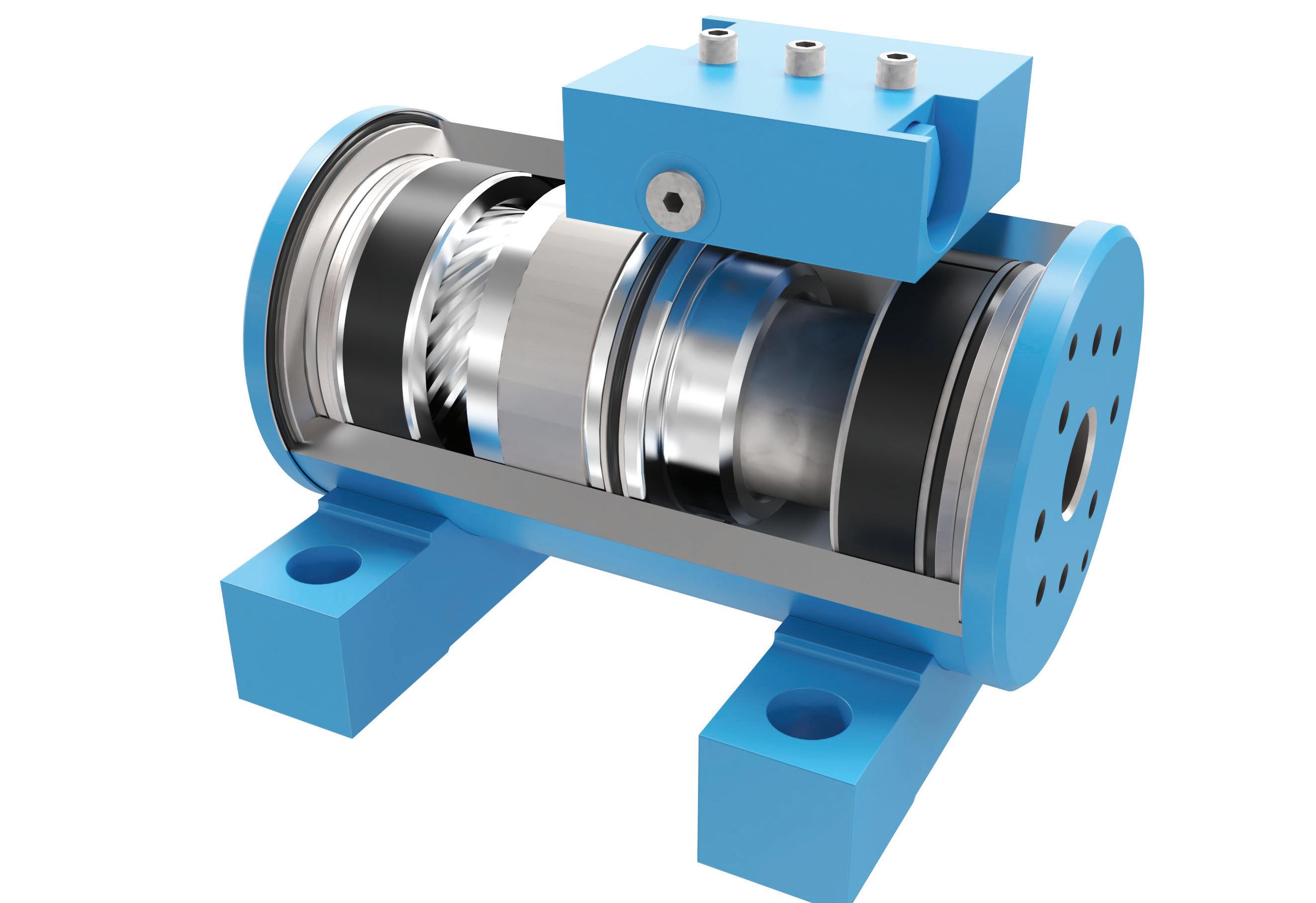

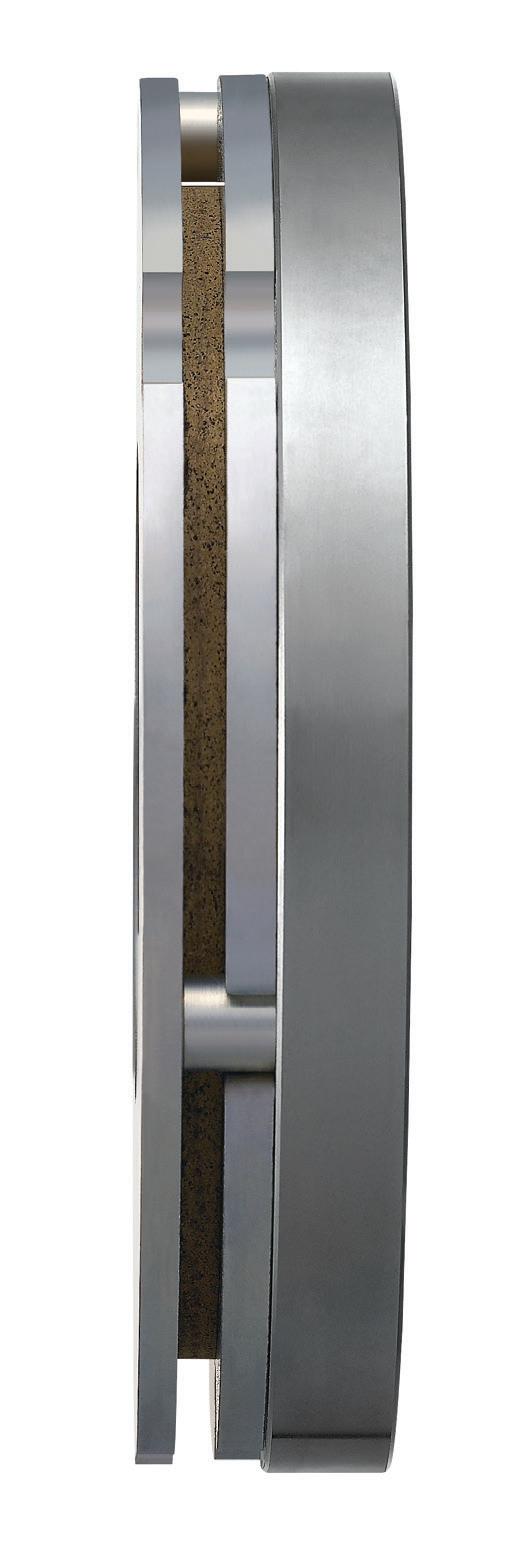
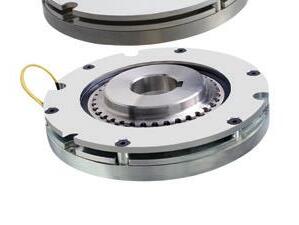
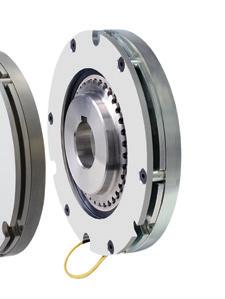
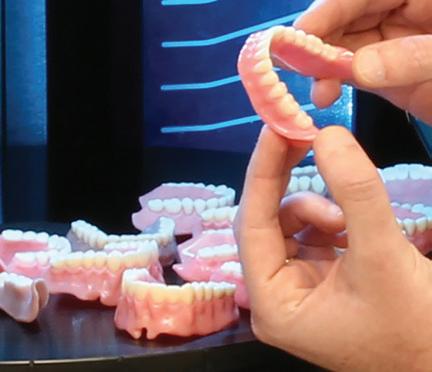