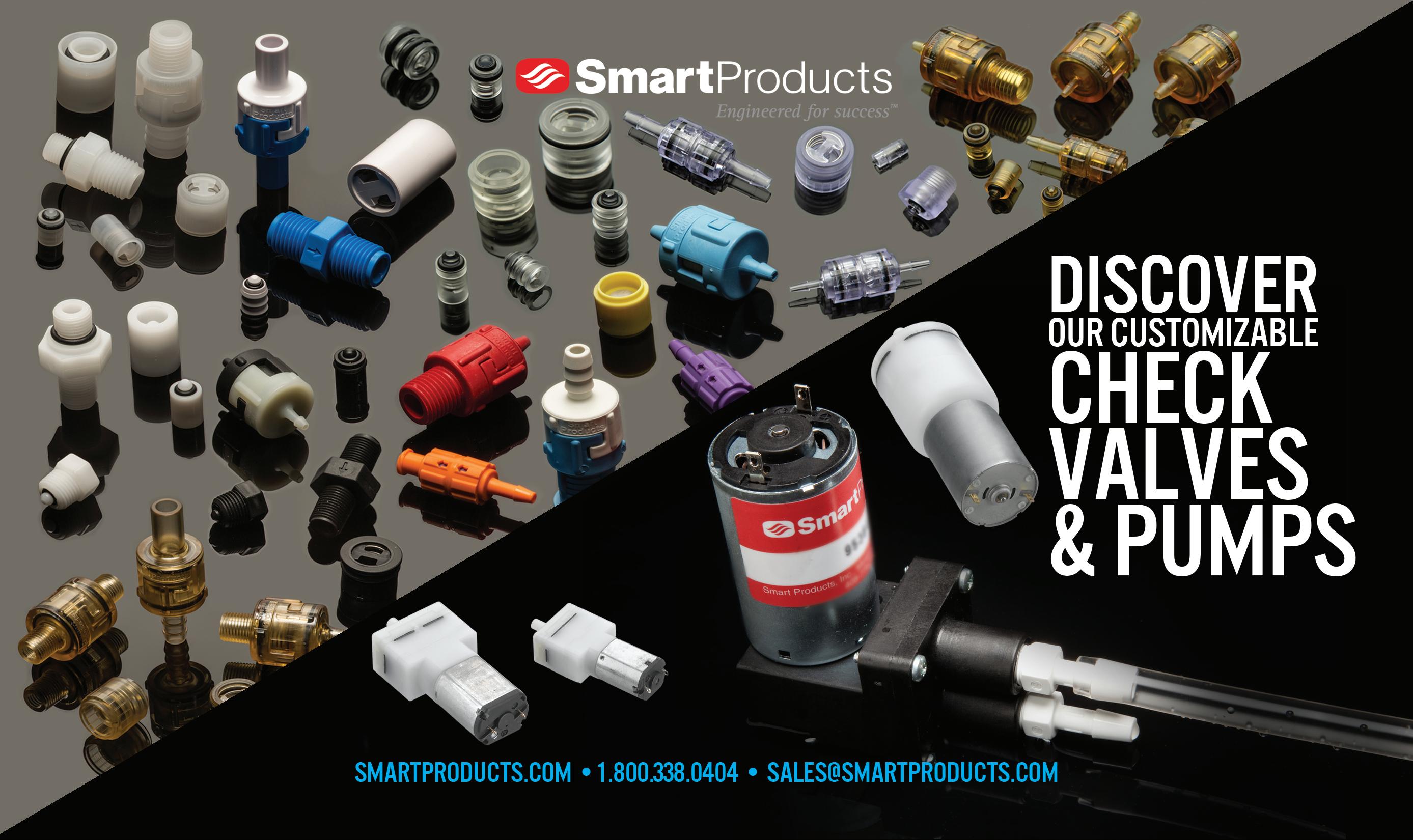
1 minute read
Design Notes Making transmission manufacturing automatic
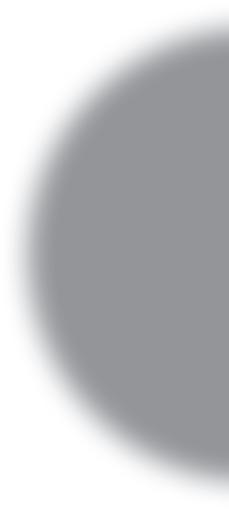

Edited by Mike Santora • Managing Editor
An automobile’s automatic transmission case is a complex casting with a sophisticated valve body with many channels and passages. These features must be precisely connected to perform the necessary control functions. However, it’s not always possible to cast all interconnections. Some case features necessitate drilling through the casting’s outer shell (and one or more internal channel walls) using cross drilling. Such drilling leaves a hole in the outer shell requiring sealing to prevent fluid loss.

More controllable cross-drill sealing method
One automotive manufacturer — a longtime customer of monitoringsystems supplier Promess — employed a Promess Electro-Mechanical Assembly Press (EMAP) to press steel ball bearings into cross-drilled holes to seal the holes. While this sealing method worked in previous applications, it failed for a new thin-walled transmission case, causing housing cracks, unacceptable leakage rates, and warranty issues.
The EMAP is an electric servo press instrumented to monitor and precisely control peak force and final position. However, the user had programmed the ball-pressing application to stop at a specific distance, so only distance was controlled. Neither the dimensions of the ball nor the diameter and surface finish of the hole were held to tight tolerances. As a result, the same level of force could leave the ball in a broad range of positions within the hole. This variability was the root cause of the leaks and cracks.
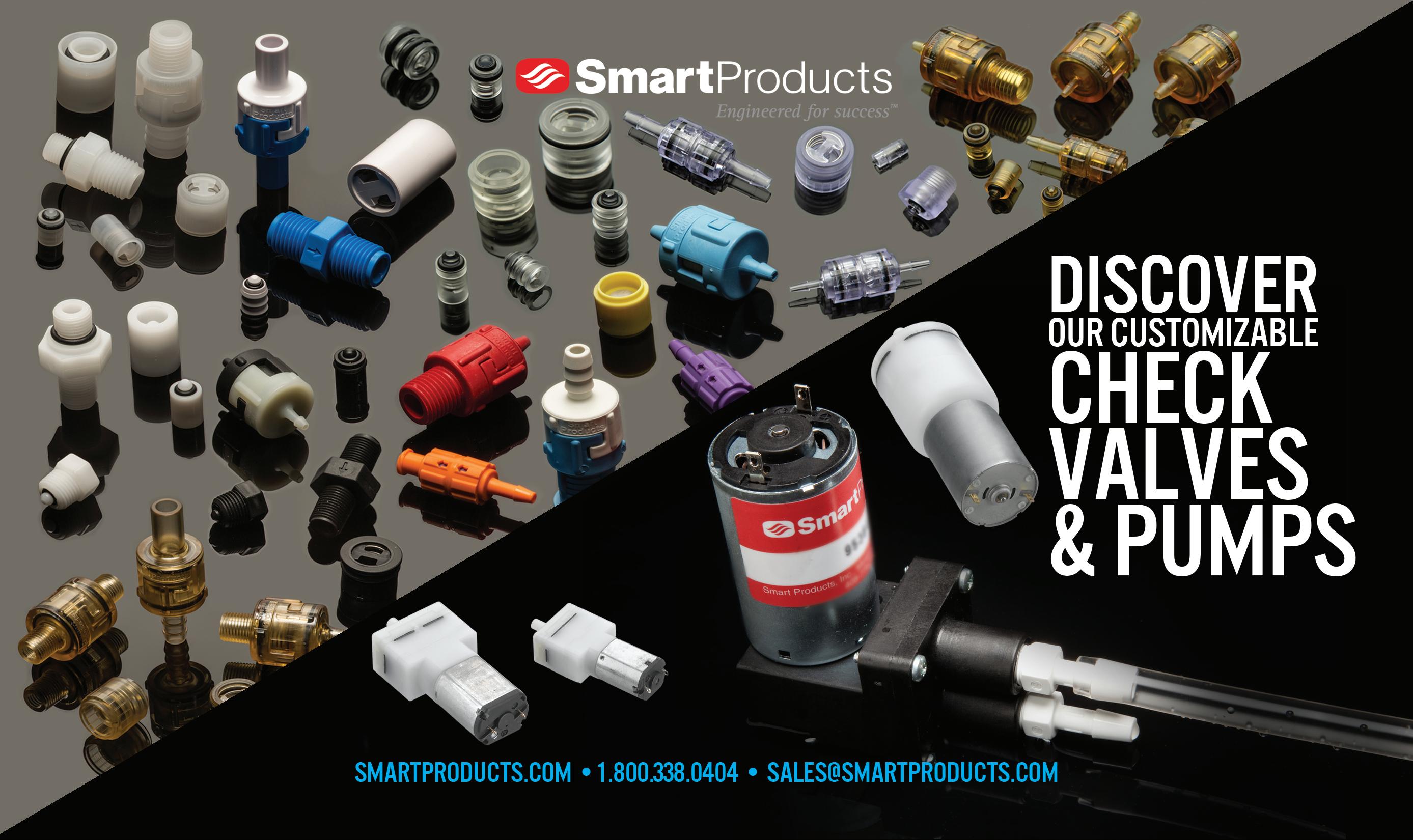
To address these unacceptable yield issues, the manufacturer replaced the steel ball with a Betaplug expansion plug produced by The Lee Company. This preassembled, two-piece tapered expansion plug has an inner pin and an outer plug body with lands and grooves
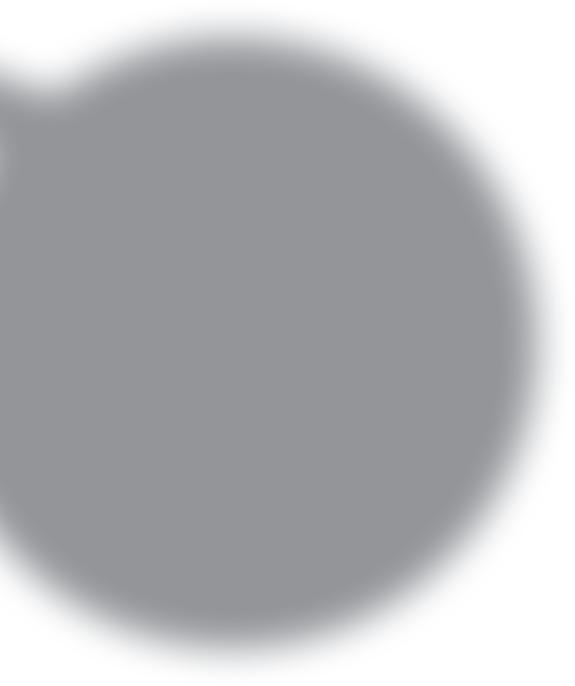
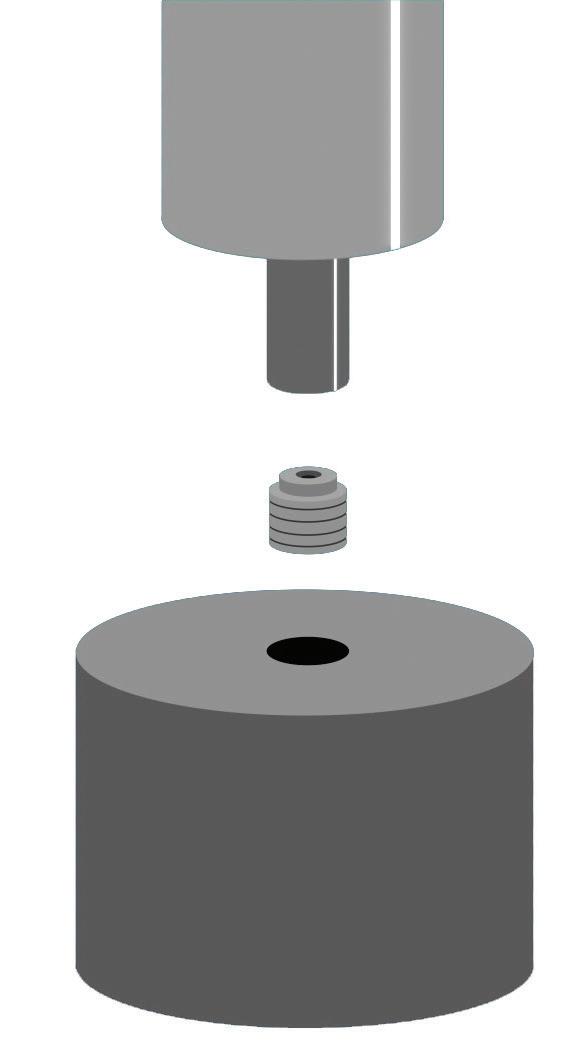