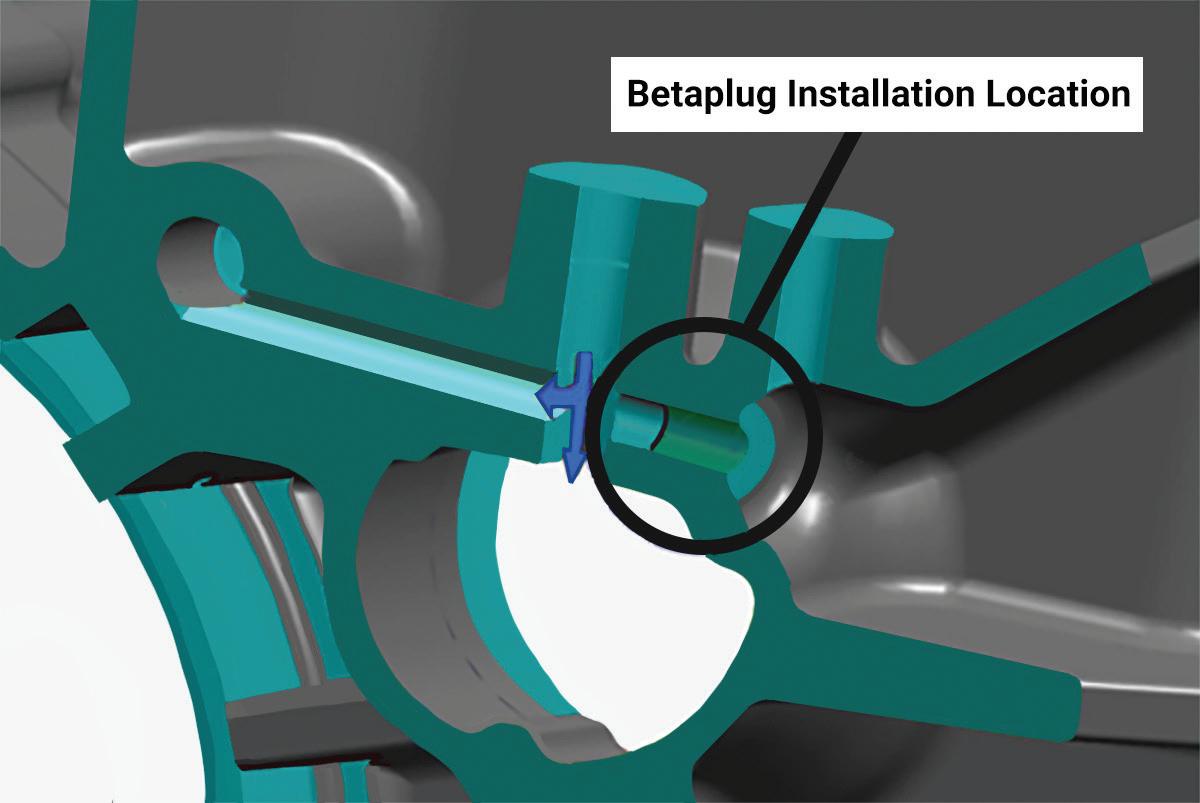
2 minute read
Design Notes
Fine-tuning the case-plugging process that bite into the housing during installation. More specifically, the Betaplug product is designed to install in a matching tapered bore that creates a suitable fit. It reduces unnecessary expansion and has a predictable boss stress suitable for brittle materials or thin wall conditions.
Using the Betaplug expansion plug eliminated the cracked housing and production yield issues. However, the manufacturer carried over an improper installation specification that created new manufacturing issues — namely, an unacceptable scrap rate, yield issues, and fixturing damage.
With proper installation, the pin is installed 0.5 to 0.8 mm below flush of the plug body, and all stake marks are present. With overinstallation, the pin is over-driven so far that it contacts the plug body. This overpressing causes the plug body to extrude up the installation hole wall — resulting in a pin that’s greater than 0.8 mm below flush of the plug body.
An installation tool is designed to install the inner pin below flush while staking over the plug body’s back edge.
So, the manufacturer contacted Promess and The Lee Company. Both companies were asked to examine the complete installation and assembly process and suggest a solution to the high scrap rate.
The Lee Company engineers determined that the Betaplug products were being overpressed; this produced excessive radial force when the pin moved to expand the plug body and extrude the plug in the installation bore. The manufacturer was reluctant to change the distance-based programming because successfully installed plugs weren’t failing in the field.
New sealing component requires new sealing approach
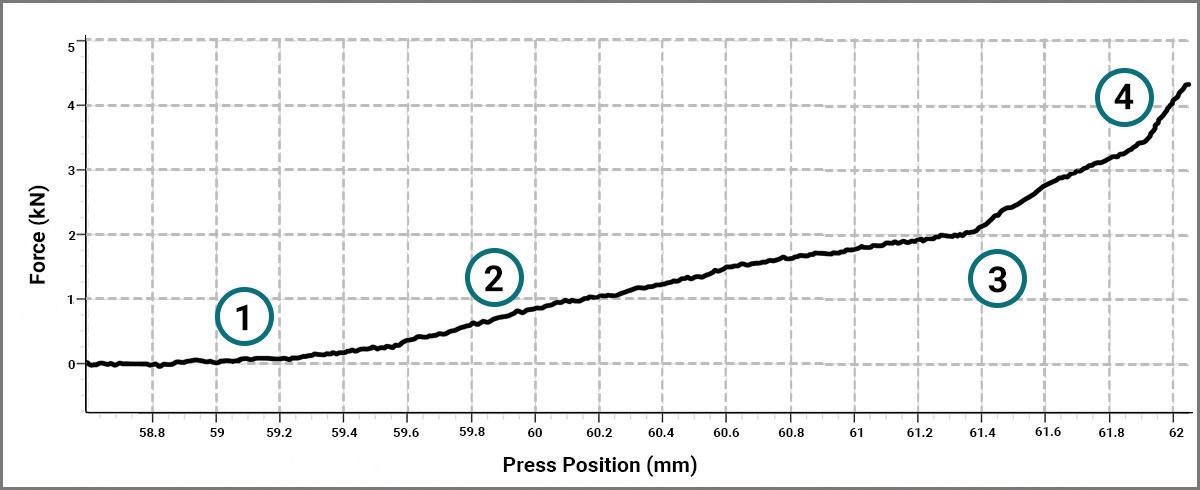
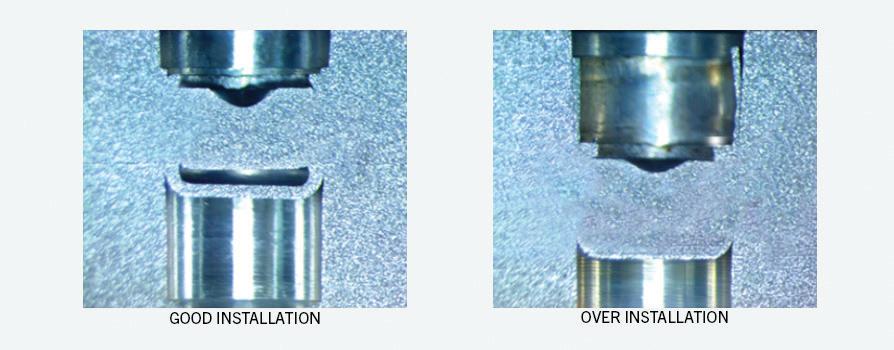
Force starts to increase here when the cup moves through the bore. 2) The cup stops, and the pin begins moving into the cup. 3) The inflection point is when the system begins staking the part. 4) Final inflection is when staking has been finished and the rate of change completes.
A proper installation for a Betaplug product should be terminated when the staking is complete, regardless of where the unit is located within the bore. The manufacturer’s engineers wanted to install the plug at a fixed point within the bore regardless of the optimum staking location; that was where the steel ball plug had performed best. However, in a tight bore, it generated the excessive installation force that extruded the Betaplug expansion plug.
Promess engineers recommended that the manufacturer change the programming to measure more than a simple force level or distance. The engineers highlighted the benefit of combining EMAP instrumentation with the sophisticated data-processing capabilities of the Promess Motion Controller. The result is the ability to measure and control absolute force, distance, and more complex relationships, such as the rate- of-change between those measurements. During installation, the Betaplug product initially moves as a unit until it lands on the outer plug body and begins to dig into the bore. When adequate resistance is achieved, the plug body stops moving, but the inner pin continues moving, generating the expansion force that creates leaktight seals and ensures retention. When the pin is 0.5 to 0.8 mm below flush, the installation tool stakes over the top edge of the plug body.
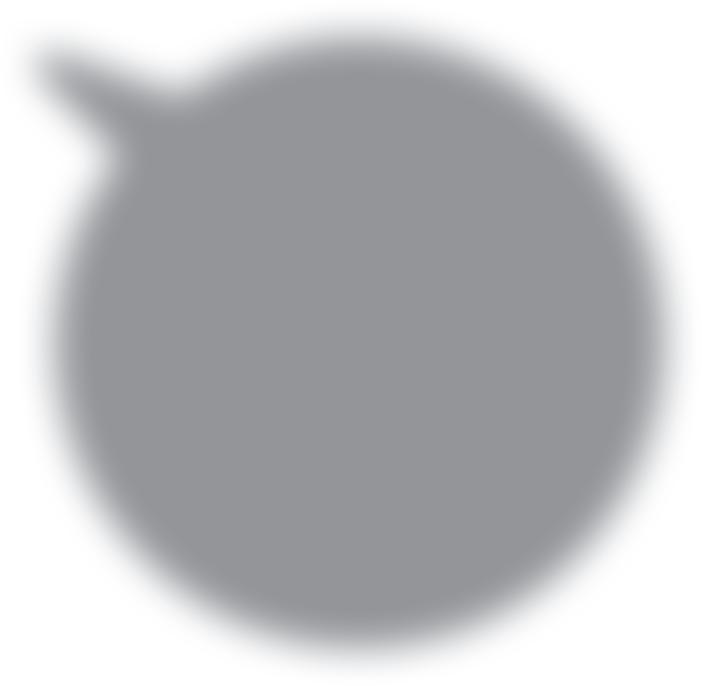
Shown here is Promess’ Electric Servo Press used to install the Betaplug product.

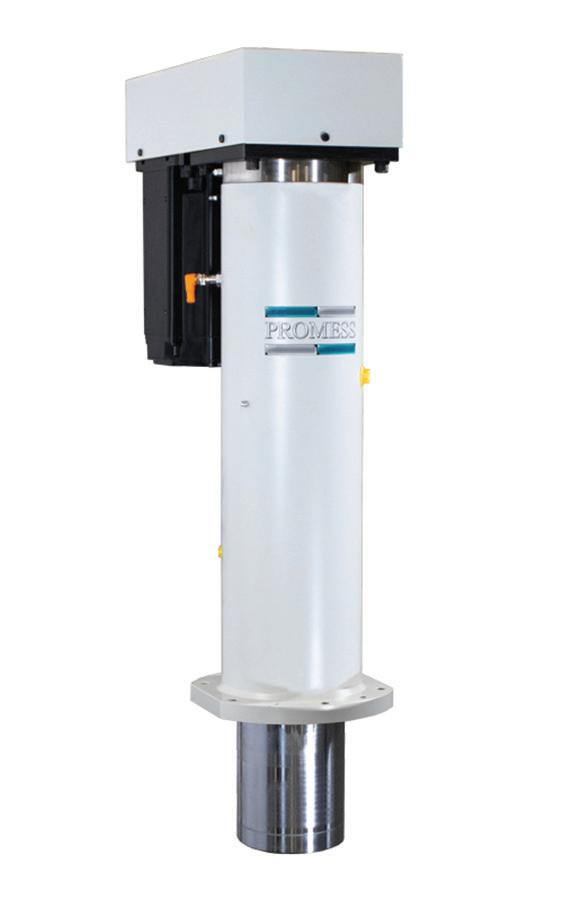

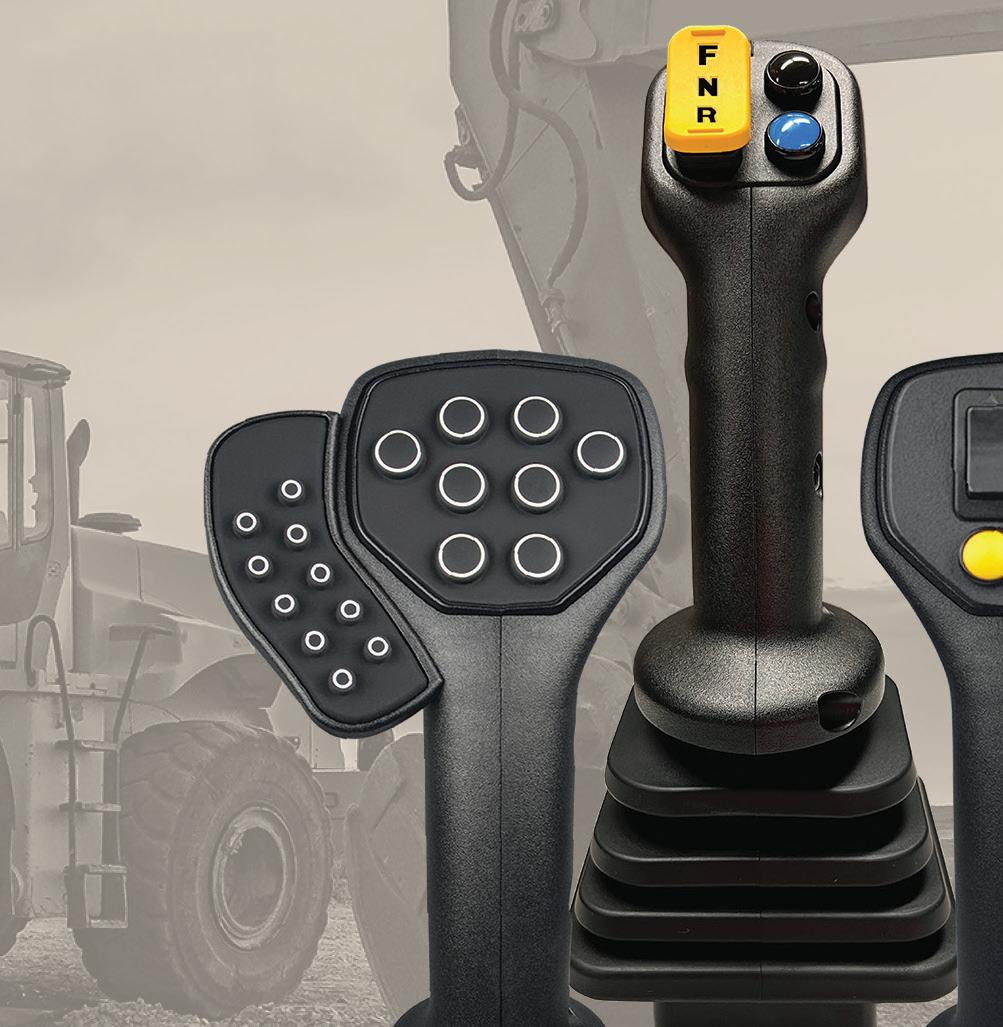
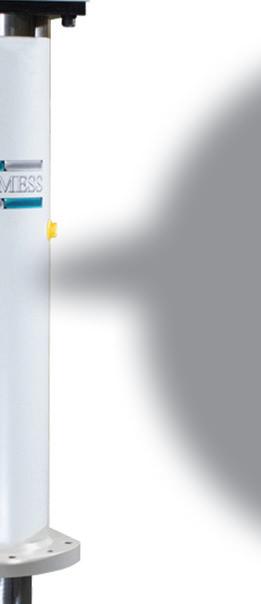
This transition produces a readily detectable inflection point in the rate of change relationship between press force and distance. After it’s detected, it’s a simple matter to stop the press when the pin is appropriately inserted into the plug body. The result is a properly staked installation that avoids harmful pin over-insertion. As an added benefit, the programming can also detect parts that are upside down, sideways, or missing a pin/component.
Promess engineers and their Lee counterparts performed extensive laboratory testing to validate the new programming. This was done prior to installing the upgraded application in the manufacturer’s plant, where more trials were performed. The new rate of change-based application was put into production after all the needed tests were completed. DW
Lee Company |
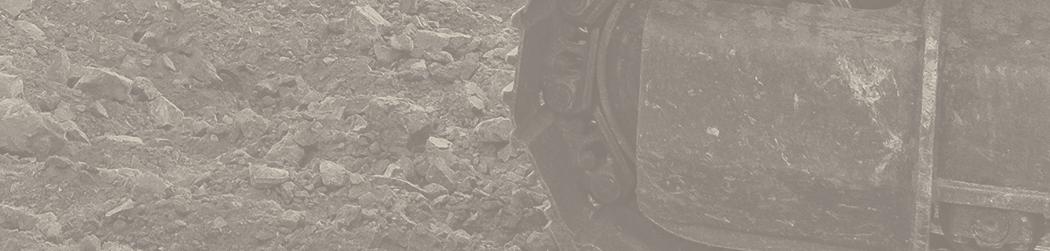
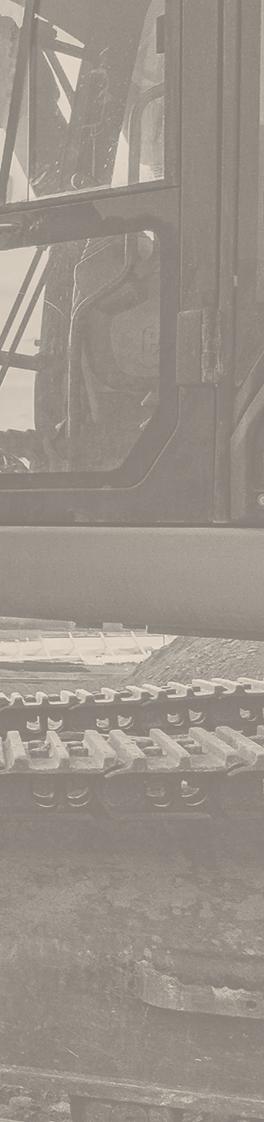

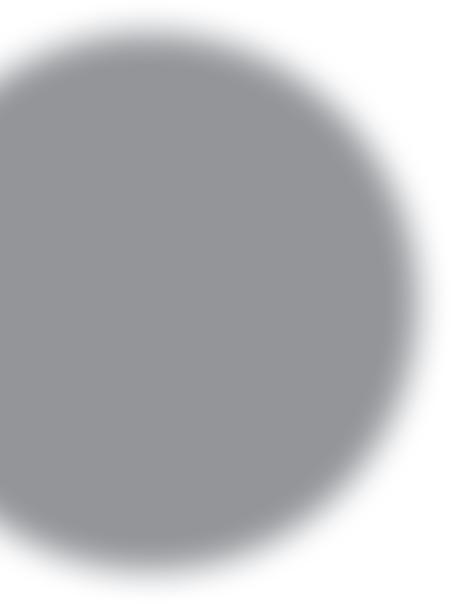