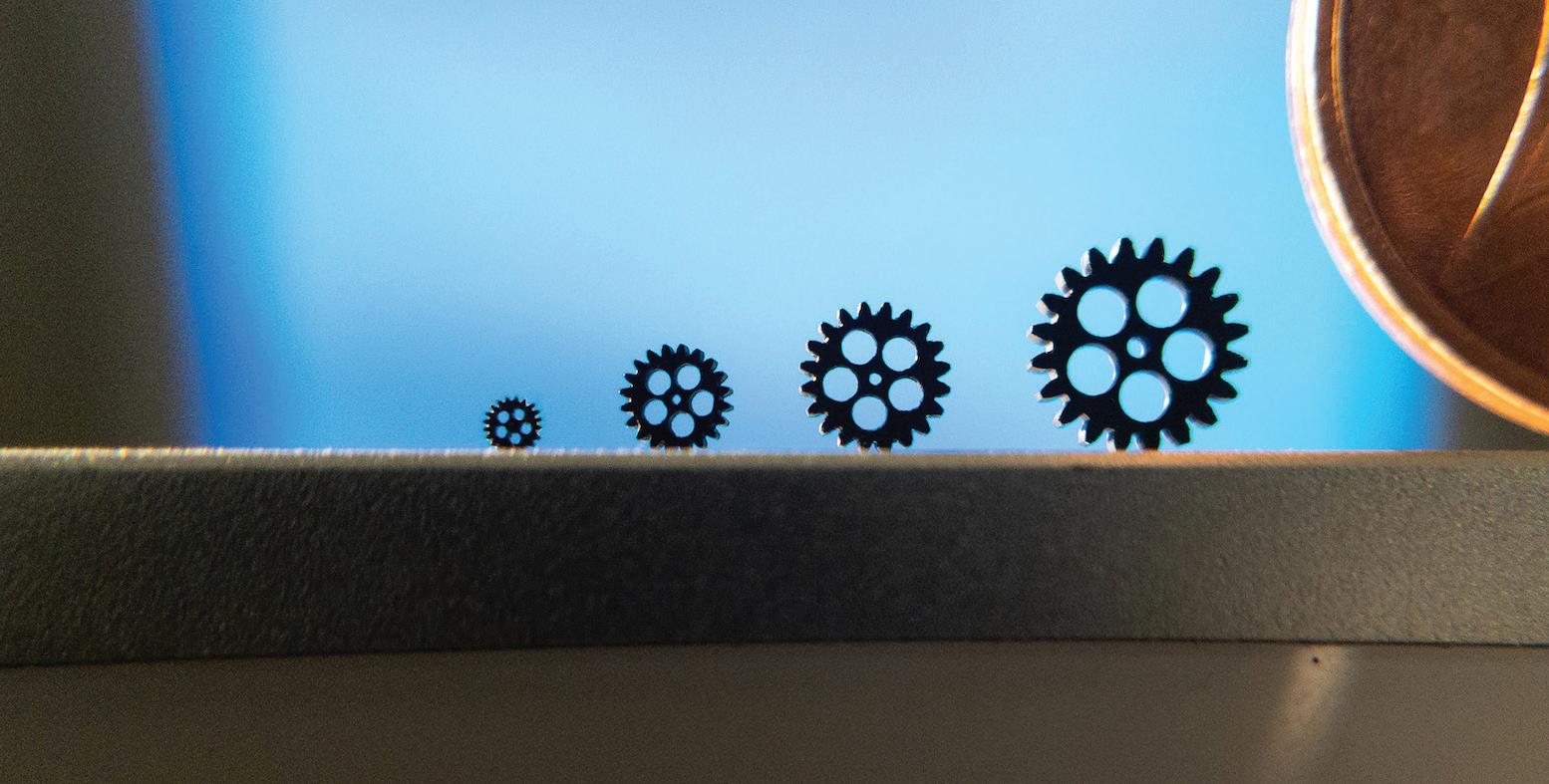
1 minute read
Micro AM is changing the economics of manufacturing
3D microprinting is a versatile technology appropriate for prototyping, small batches, and potentially mass manufacturing.
| courtesy of Accumold
Micro additive manufacturing (AM) appeals to an array of customers unable to fulfill design intent cost-e ectively or e ciently with traditional manufacturing processes. As micro AM is agnostic to part complexity, it allows for the manufacturing of hollow structures, holes, complicated interior details, and atypical shapes — and it’s promoting innovation as an enabling technology. Accumold, an Iowa-based company that specializes in micro molding, continues investing in its micro AM capability with the purchase of a second Fabrica 2.0 machine from Nano Dimension.
“The Fabrica 2.0 will make the prototype stage of the product development process more flexible and quicker for our customers. In time, it will move towards small- to medium-sized production runs and also promote creative geometric complexity and mass customization,” said Aaron Johnson, vice president of marketing and customer strategy at Accumold.
The Fabrica 2.0 can cater to volume applications — multiple thousands of small parts and components fitting easily in the machine’s 50 x 50 x 100 mm build envelope — so OEMs can reduce reliance on economies of scale. Micro AM technology makes possible low- to medium-volume production runs that were previously uneconomical due to high tooling and setup costs associated with traditional manufacturing alternatives.
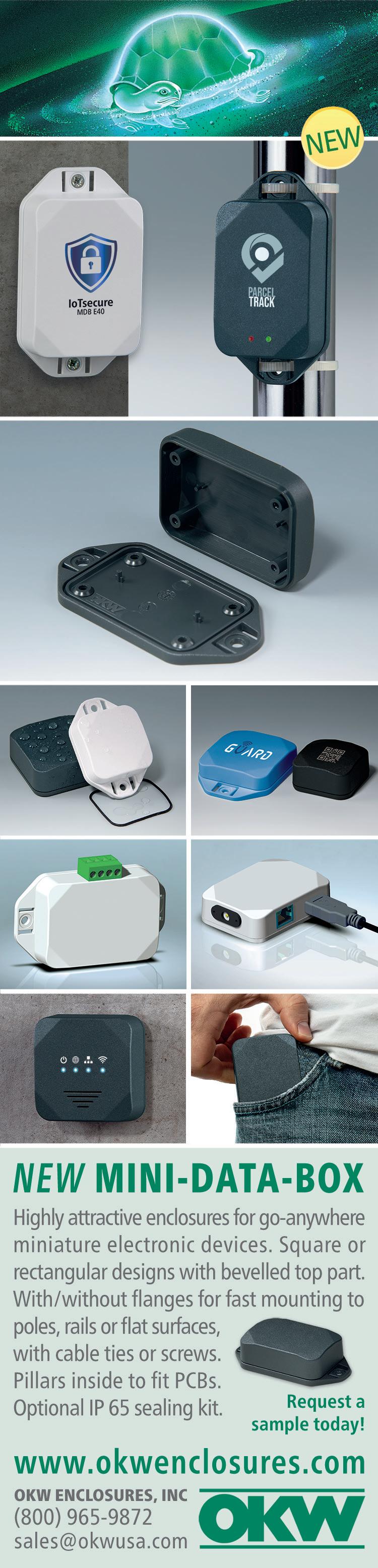
“In general terms, success through the use of the Fabrica 2.0 is measured in microns and hours. Micron-level detail can be achieved without the need to fabricate tools, and this means that you can have intricate and geometrically complex prototypes in a matter of hours,” said Johnson.
With traditional micro tooling, increased complexity means increased cost, so part complexity is limited. However, with micro AM technology, the absence of physical tools enables design engineers to think outside the box and attain design goals previously unimaginable. This design freedom, coupled with AM’s inherent manufacturing agility, a ords reassessments of all aspects of the product development process.
“Through the use of Fabrica 2.0, you can also optimize workflow, the technology producing less scrap and fewer tools than conventional manufacturing processes,” said Johnson. “It also promotes the reduction of iterative process, assembly, and inventory. This means that significant operational cost benefits are now attainable at the micro manufacturing level for our customers.”

The Fabrica 2.0 system 3D prints micron-level resolution parts for aerospace, electronics, automotive, medical, optics, and R&D applications.
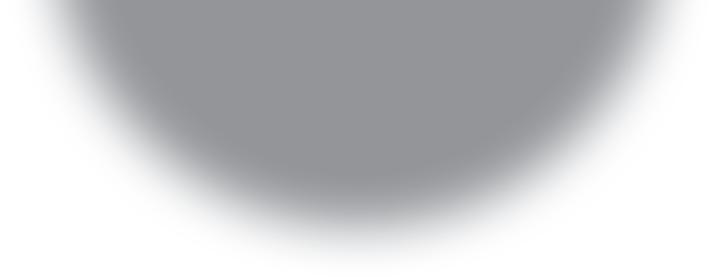
The Fabrica 2.0 system enables the drive toward miniaturization for high precision for high-performance applications. This includes micronlevel resolution of medical devices, micro-optics, semiconductors, microelectronics, micro-electro-mechanical systems (MEMS), and microfluidics. The Digital Light Processing (DLP) based system enables the critical advantages of additive manufacturing, including rapid prototyping, high-mix-low-volume production, IP security, and a minimal environmental footprint. DW
Accumold | www.accu-mold.com
Nano Dimension www.nano-di.com
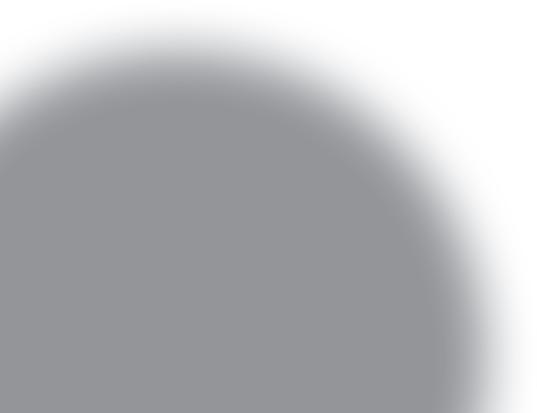