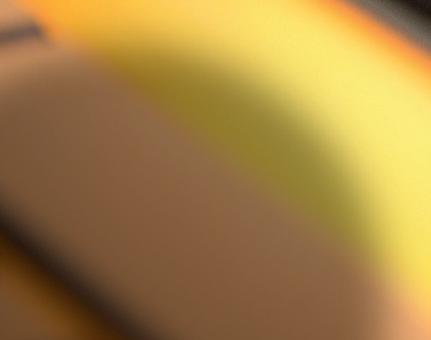
1 minute read
Design for manufacturability analysis prevents 3DP disasters
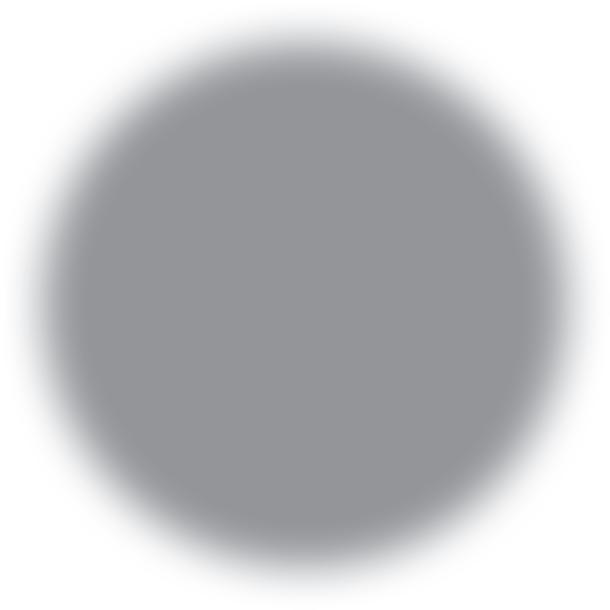
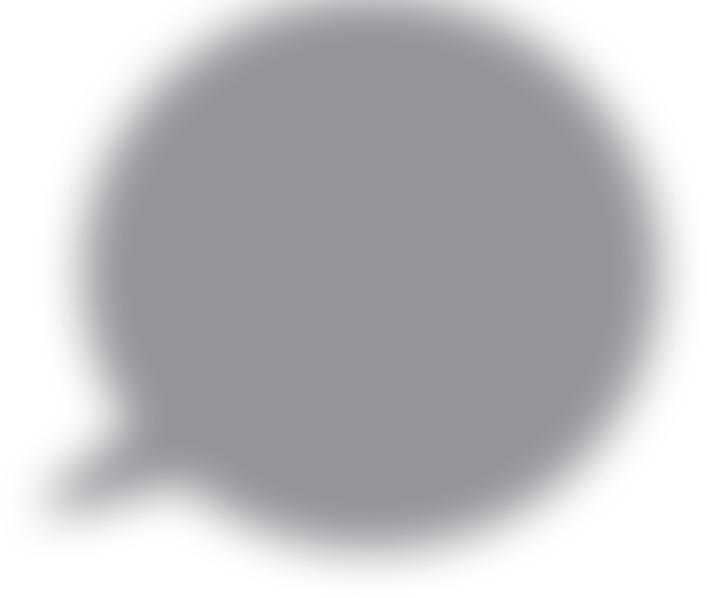
| courtesy Protolabs
Additive manufacturing is a brilliant technology, but there are a few limitations that engineers must consider. A design for manufacturability analysis provides guidance and highlights critical issues, such as parts that are too large to be produced, or non-critical issues, such as dimensions that are close to thresholds and may not form completely.

Protolabs o ers manufacturers peace of mind with its online design for manufacturability (DFM) analysis for 3D-printed parts. In a matter of seconds, the service assures that parts are suitable for manufacturing before committing to production.
The automated feedback enables product developers and engineers to optimize additive designs before parts are printed, which helps accelerate product development and avoid unnecessary production costs by making design adjustments early.
“We understand the importance of speed, but ensuring that parts are correct, high quality, and delivered rapidly is critical. Instant analysis means you can have all the advantages of additive manufacturing with even more
The automated DFM analysis warns users of any issues before order submission.

| courtesy Protolabs certainty without sacrificing speed,” said Andrea Landoni, 3D printing product manager at Protolabs EMEA.
The DFM analysis is available globally on parts uploaded to Protolabs’ website for any of the company’s plastic and metal 3D printing technologies. When users receive their quotes, the analysis immediately highlights potential manufacturability advisories concerning thin walls, small gaps, and parts that exceed maximum size restrictions. This eliminates lost-time incidents for most common issues, preventing engineers from proceeding with orders only to discover issues hours later. While most problems are solved, there are circumstances where the user may still require further support.
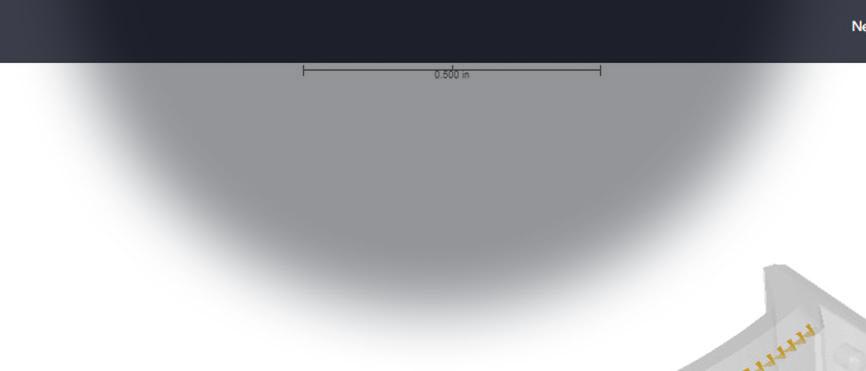
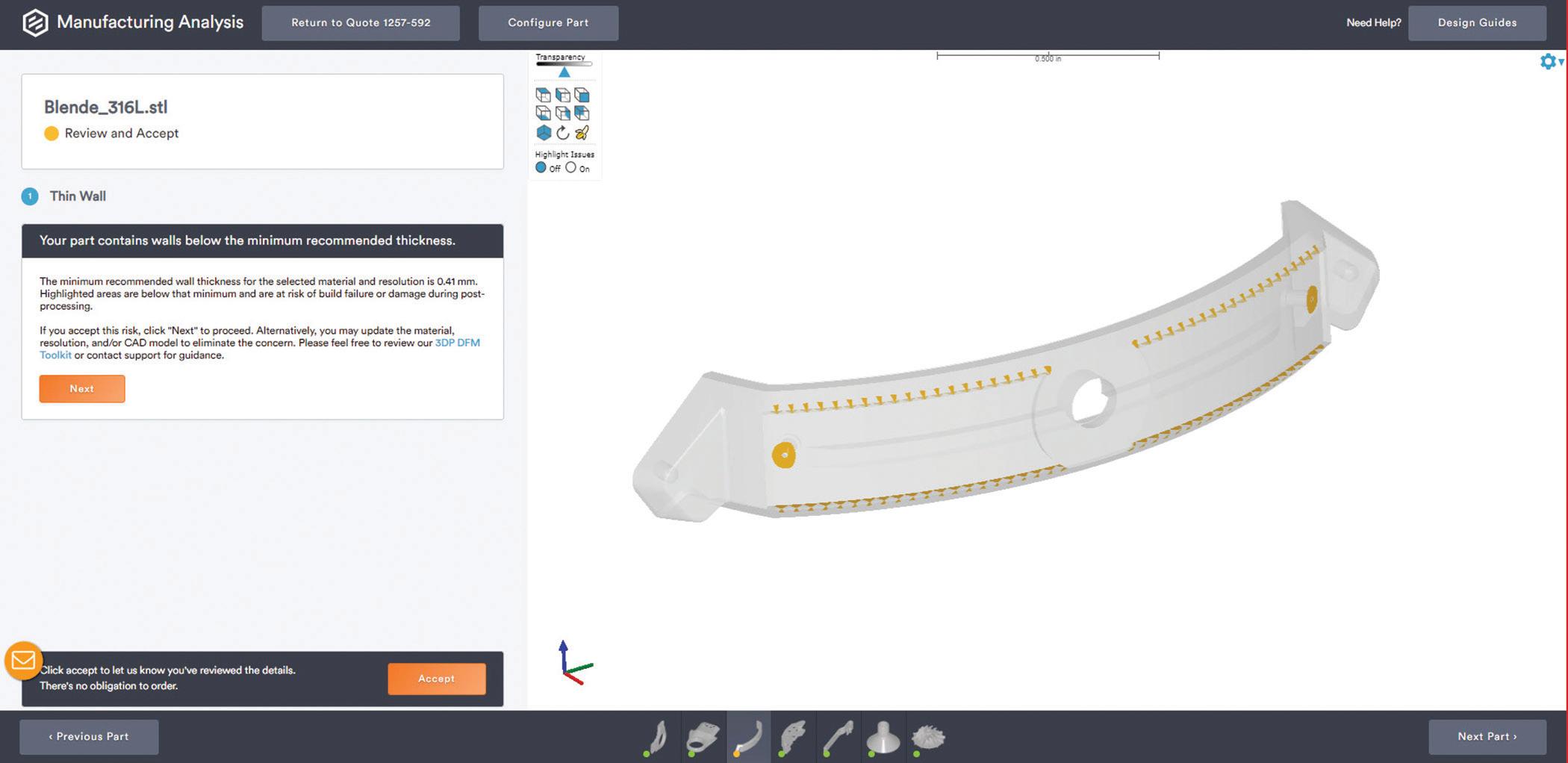
“Protolabs understands that specific projects require technical consultancy to solve complex issues. In these circumstances, our Application Engineers are still on hand to overcome these challenges and accelerate the process,” said Landoni.
The company has also recently broadened its additive material and finishing options. Product developers and engineers can now choose 3D-printed silicone in multiple levels of shore-A hardness. The material is 100% pure silicone, which is biocompatible and functional at various temperatures. Earlier this year, vapor smoothing was launched for select materials, providing enhanced finishes that eliminate rough surfaces and leave a glossy, aesthetic appearance on 3D-printed parts. DW
Protolabs www.protolabs.com

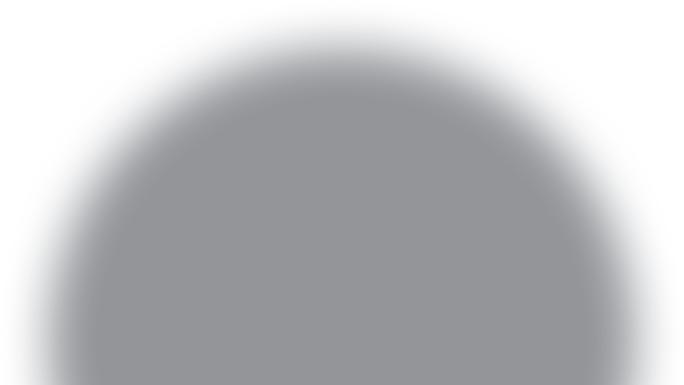
The online manufacturability analysis provides design guidance so that engineers can correct and reevaluate parts quickly.
| courtesy Protolabs
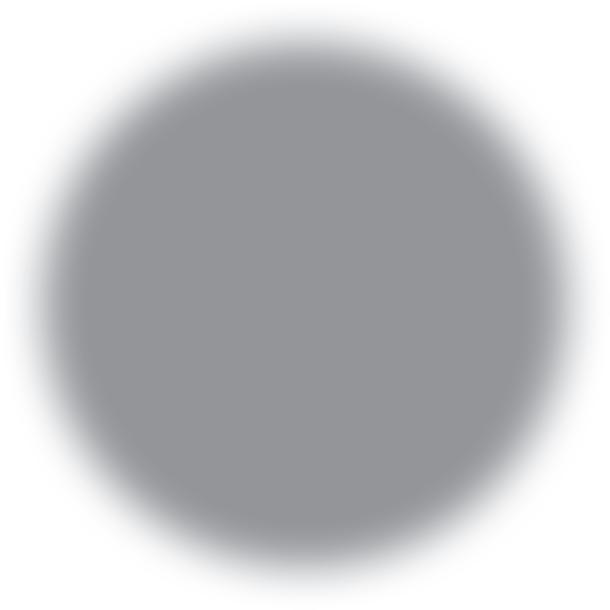