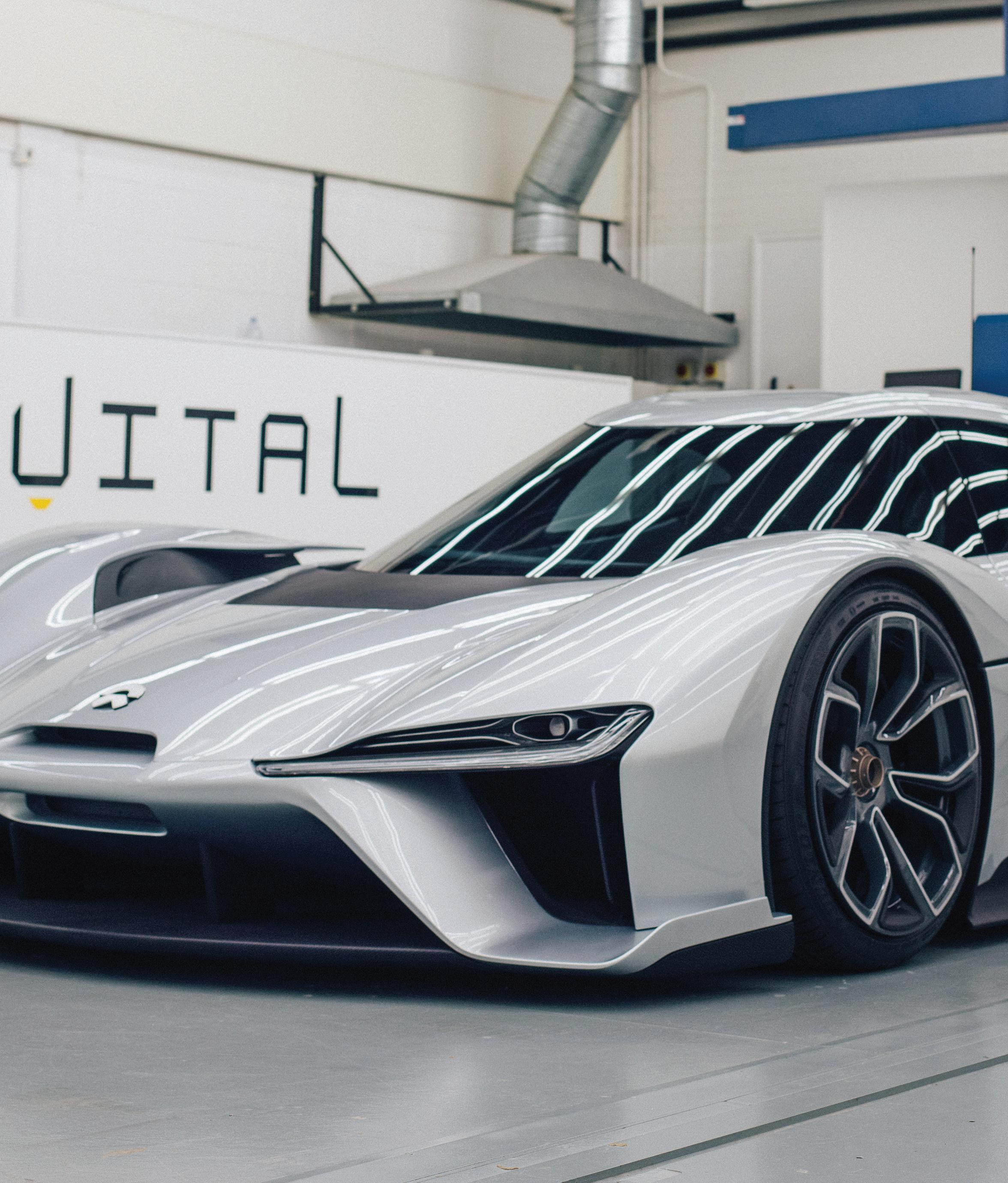
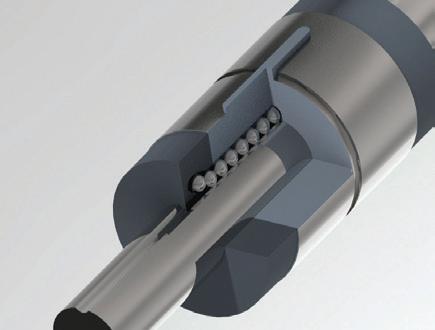
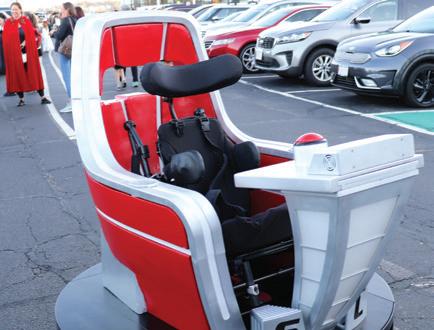
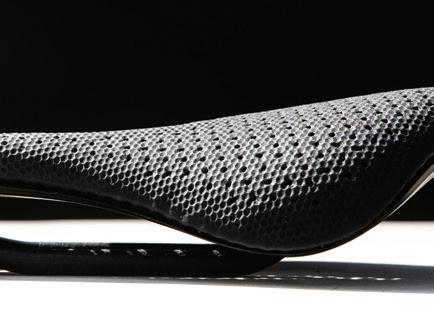

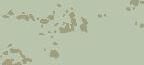


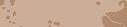
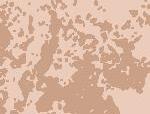

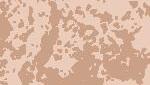
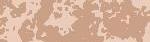
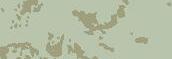
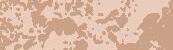

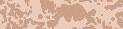


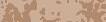
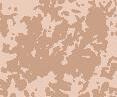
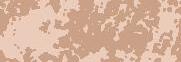





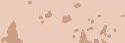

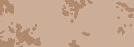

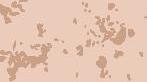

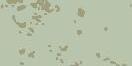







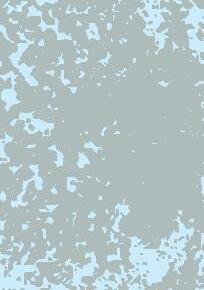




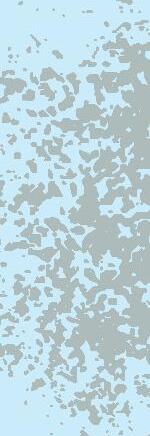

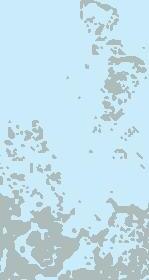






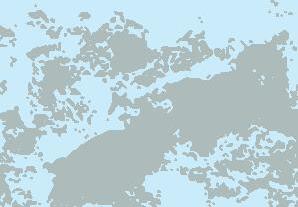


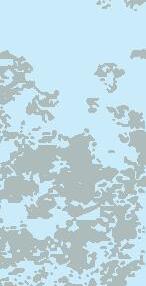

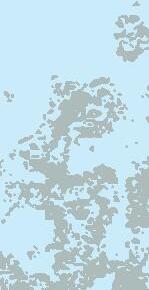
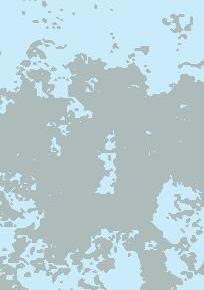

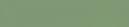
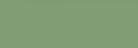

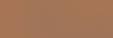












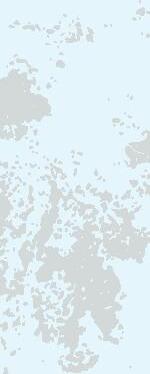

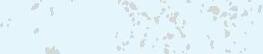


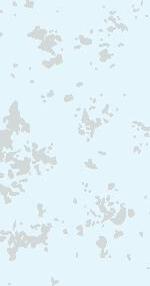









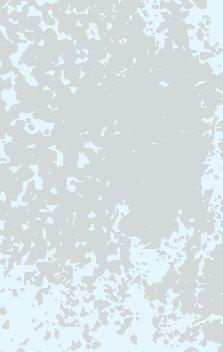
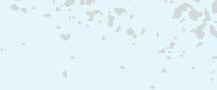






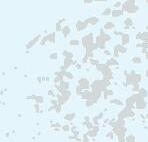




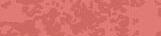
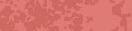









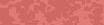


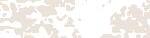

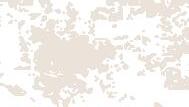








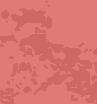





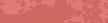







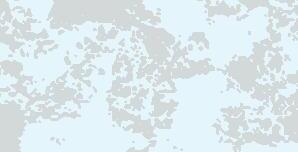
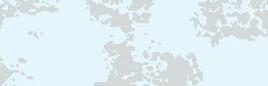





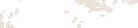














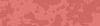
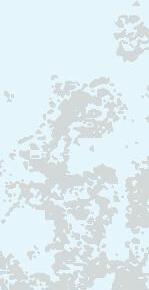
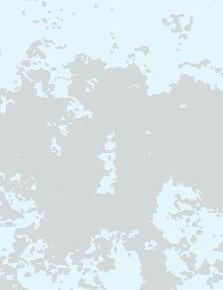
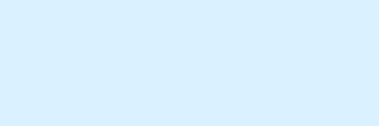
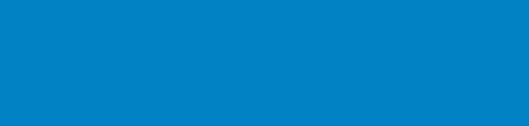
Order your cut-to-length and bulk cables today and save with AutomationDirect’s affordable pricing - No gimmicks. No hidden charges.
All AutomationDirect multi-conductor cable can be ordered cut to your speci ed lengths without the added cutting charges, hidden fees, and in ated shipping costs found with other suppliers.
With AutomationDirect you get:
• UL certified re-spooling facility - ensures that our cut-to-length cables maintain the UL certifications
• Low price per foot Starting at $0.23 (PLTC3-20-1S-1)
• Low minimum cut lengths
• Free, fast shipping (typically 2-day delivery)*
• Easy online, phone or email ordering
• 30-day money-back guarantee* (yes, even custom cut cable)
• NEW! Quabbin 150-, 300-, or 600-Volt low voltage control and signal cables are ideal for control and audio applications. Available in shielded or unshielded versions, twisted pair or twisted triad options, sizes of up to 16AWG, and with up to 25 conductors depending on cable size. These cables are UL and CSA approved, and proudly made in the USA.
Starting at $0.23/ft (Q7120-1)
• NEW! More LUTZE SILFLEX FBP food and beverage rated control cable sizes. This cable meets both UL and FDA requirements. It’s patent-pending design was evaluated by third party tester Ecolab for resistance to commonly used cleaning agents which reduces cabling as a contamination risk.
Starting at $0.75/ft (A6012003-1)
AutomationDirect has a large selection of quality MTW, THHN, and TFFN electrical wire in pre-spooled lengths that meets all NFPA and NEC requirements at great prices.
Starting at $24.50/500ft (MTW22BK)
Research, price, buy at: www.automationdirect.com/multi-conductor-cable www.automationdirect.com/wire
Ships Fast!
Advanced Materials
Digital Manufacturing
Electrical
Here in our seventeenth annual issue on Leadership in Engineering, we announce the winners in the Leadership Awards Program that we have been promoting throughout the year.
Fluid Power
Industrial Automation
Mechanical
Fastening & Joining Motion
The Design World User Community has cast votes and we are pleased to celebrate the winners in this special section of “Leadership in Engineering.” Networks
Mechatronics
Software
Switches & Sensors
Test & Measurement
CS Hyde Company is always changing and adapting to suit its customers. The engineering staff work on your project along with you, offering suggestions wherever it may be useful. With the benefit of an automated control system, a precision slitting machine can cut rolls of material to standard and custom sizes. Sizes range om 1-1/2, 3, and 6 in. cores. Width can be as much as 60 in., while maintaining tight tolerances throughout.
CS Hyde can also die-cut pieces of material using a variety of methods. Custom shapes are held to tight tolerances. The company also offers rapid prototyping capabilities, which allows for small runs, with no tooling charges, and ultra-fast turnaround times.
In addition, CS Hyde can cold laminate an adhesive of your choice to a variety of materials, and using 3M’s product line. Whether it’s Teflon Tape, Silicone Foam, Kevlar thread, or Mylar film, CS Hyde has what is needed.
Xometry is the US’s largest platform. Launched in 2014, the company has grown rapidly, driven by the ease of its instant quoting platform, manufacturing expertise, and devotion to helping customers with their project engineering needs. In 2018, Xometry acquired MakeTime, another leader in the manufacturing on-demand space to create the single largest manufacturing partner network in the industry. In 2019, Xometry acquired Shi , Europe’s largest CNC manufacturing network. Its partner network now spans the globe to support the needs of customers and to help drive the business of local machine shops and manufacturing facilities. Its algorithm sends jobs to a list of carefully vetted facilities with matched capabilities. Xometry’s Project Engineering team is always responsible for making sure the parts are done correctly and on time.
Xometry’s manufacturing capabilities include CNC Machining, Sheet Metal Fabrication, Direct Metal Laser Sintering (DMLS), Selective Laser Sintering (SLS), Fused Deposition Modeling (FDM), HP Multi Jet Fusion, PolyJet 3D, Die Casting, Binder Jetting, Urethane Casting, Finishing Services, and Injection Molding.
New automation technology almost 40 years in the cable business, Helukabel has designed products to provide an uninterrupted flow of power and data to today’s automated manufacturing systems.
The company continuously provides new cable solutions for customers, which allows them to maintain their position at the fore ont of the market.
HELUKABEL cables have long service lives, and have been tested to multi-million flexing cycles. This makes the automated manufacturing process leaner by reducing downtime and increasing productivity. The company also develops and manufactures complete cabling protection systems for robotics applications.
HELUKABEL combines a product portfolio of over 33,000+ line items with worldwide logistics operations to deliver the cable products you need, when you need them.
For more than 100 years, Boker’s has earned the reputation as a stamping leader. It delivers precision stampings in a complete range of sizes. Many inside diameters, thicknesses and more than 2,000 commonly specified and hard-to-find material options— including various types of steel, aluminum, brass, copper, nickel silver, plus non-metallic materials such as PTFE, polyester, fiber and nylon— are available.
Boker’s also delivers a wide selection of standard and non-standard washers, spacers and shims. With more than 32,000 stock tools, and outside diameters of .080” to 5.140” along with a variety of inside diameters, you have millions of flat washer possibilities. All stampings, washers, spacers and shims are available in short, medium and long runs with a 100-piece minimum. Boker’s also offers 3D printing for prototyping, complete Statistical Process Control (S.P.C.) capability, in-house tooling, and “Dock-to-Stock” and “Just-in-Time” programs.
Trelleborg Sealing Solutions offers a range of patented product designs and proprietary materials for static and dynamic sealing applications in the general industrial, automotive and aerospace markets. The company has nine R&D centers and more than 32 production facilities and 60 Customer Solution Centers worldwide. Trelleborg offers customers the strength of a global supplier combined with the service and support of a local partner, an unrivaled product range, and a portfolio of established brands and ServicePLUS value chain solutions.
The sealing solutions suit industrial applications in aerospace, automotive, chemical transportation, energy and renewables, fluid power, robotics, food, beverage and water, and other segments. Trelleborg experts collaborate with customers to design, engineer, and manufacture seals to meet specific application requirements. Whether starting with a customer specification, supporting with testing and qualification to get a product to market, or developing solutions to enhance manufacturing and supply chain processes, Trelleborg helps customers find the best solutions to their most challenging projects.
AutomationDirect offers exemplary service to its customers.
AutomationDirect provides customers with quick order and delivery through an online store and toll- ee number. Prices on most products are well below the industry average and a 30-day moneyback guarantee is offered on nearly all items.
Many of the products represent years of design and development by AutomationDirect’s own engineering team as well as their strategic partners. The company offers motors, sensors, pushbuttons, enclosures, circuit protection and more.
The state-of-the-art headquarters facility near Atlanta is designed throughout for maximum performance. Orders for in-stock items can be taken as late as 6 p.m. EST and be shipped for next-day delivery. The company provides online tutorial videos through their web store at www.automationdirect.com as well as their YouTube channel. A Customer Forum provides peer support on technical and application questions.
AutomationDirect’s customer support team has been rated topnotch by its customers. For 15 years straight, the Tech Support team was voted as best in service and support for various products. And, their own customer surveys consistently rank the company’s service as better than other suppliers.
igus has been manufacturing engineered plastics for more than 50 years and develops each of the plastic materials and all technology behind its products. A family developed and owned company, igus is committed to using its innovative materials to develop creative solutions and exceed customer expectations while delivering fast, accurate service.
Its business is centered around four main product lines that focus on the idea of “motion plastics:” energy chain systems, chainflex continuous-flex cables, iglide self-lubricating bearings, and drylin linear bearings and guides. The products are extensively tested under real world conditions. More than 28,000 products are available om stock within 24 hours.
Yaskawa is a leading global manufacturer of variable equency drives, servo systems, machine controllers and industrial robots. Yaskawa engineers invite you to wonder, “What if …?” And then they make it possible. Experience is o en the difference between solving a problem the right way and settling for “good enough.” The company has 100+ years of manufacturing excellence, and is in 30 countries with sales, service, and manufacturing locations.
Yaskawa AC Servo Systems come to a precise position with a speed and consistency. Rotary, linear, and direct drive motors can be connected to an advanced Yaskawa machine controller to achieve SINGULAR CONTROL: the ability to manage robots, servos and drives with a single controller and familiar IEC 61131-3 programming.
Yaskawa offers a variety of low and medium voltage AC drives that support every application in the industrial plant. The latest variable equency drives provide simple motor setup with flexible network communications, embedded functional safety, no-power programming, and easy-touse tools featuring mobile device connectivity with the DriveWizard® mobile app.
PBC Linear is a leader in the engineering, manufacturing, and assembly of a range of linear motion products. The company also offers custom engineering services. The core line of linear components includes bearings, sha ing, rail assemblies, and cam roller sliders. In addition, PBC Linear has created a sophisticated family of products that includes lead screws and motor lead screw assemblies, actuators, cartesian robotics, and mechatronics assemblies.
The story of PBC Linear begins with an innovative and patented solution in bearing design, the Frelon-lined plain bearing. That successful bearing design is now part of a larger family of products related to linear motion technologies, with many of them manufactured at our headquarters in Roscoe, Illinois USA.
Dedicated engineers at PBC Linear can work with industry professionals to produce prototypes, pilots, and small production runs, helping to bring customer ideas to market.
BAYCABLE is vertically integrated and can offer a range of manufacturing capabilities including custom cable constructions, full turnkey cable assembly and molding services, component customization, specialized testing, and in house mold tool manufacturing.
BAYCABLE delivers engineering expertise as an integrated solutions partner that can help create the optimal interconnect system for your application.
Early design collaboration with its Silicon Valley based engineering group takes a design om concept through pre-production into the initial production runs quickly. The company can provide medium to higher volume production by transferring production to its plant in Sonora, Mexico. Both manufacturing locations are ISO Registered.
BAYCABLE has a long legacy of delivering high performance reliable interconnect solutions to its customers.
COMSOL Multiphysics provides a platform that integrates multiphysics modeling capabilities with application design and simulation data management. With it, designers can drive innovation and expand their use of simulation in many technologies, such as vehicle electrification, renewable energy, medtech, electronics, power grids, and process engineering.
For example, the Application Builder allows for the creation of specialized applications (apps) built on top of multiphysics models. Apps simpli the running of simulations, while expanding upon the information provided by the underlying models. They are designed in ways that focus simulations toward specific engineering uses. Apps can be distributed to anyone the app designer chooses as compiled executable fi les, using COMSOL Compiler, or through an app management tool called COMSOL Server.
The latest version of COMSOL Multiphysics, Version 6.1, provides users with powerful multiphysics simulation tools in areas of highly competitive R&D, like audio technology and vehicle electrification.
Novotechnik is a manufacturer and global supplier of linear and rotary position sensors based on innovative potentiometric, Halleffect, magnetostrictive and inductive measurement principles. The company was founded in 1949 and is part of the Siedle Group.
The available application-proven sensors include premium position sensing solutions for applications requiring high precision and time-proven reliability under harsh conditions.
Novotechnik develops a wide spectrum of state-of-the-art position sensors with many standard options and custom enhancements. All sensors are rigorously tested to meet customers’ needs and application requirements while adhering to international standards. Novotechnik is certified to ISO 9001:2015 and IATF 16949:2016.
Dedicated local engineers provide technical support to assist with the seamless and cost-effective integration of position sensor systems into a wide variety of automation, agriculture, automotive, marine, robotics, medical and other applications.
AMETEK Programmable Power specializes in developing highly differentiated power and testing equipment for the world’s leading markets. What separates AMETEK Programmable Power om others is the ability to work closely with customers to develop specialized equipment to meet their specific requirements. With a customer focused mindset AMETEK Programmable Power also brings decades of experience to developing next-level power and testing equipment solutions. With that extensive experience and a proven track record in a variety of markets, AMETEK Programmable Power has the unique capability to help their customers succeed with the broadest range of systems in the market.
AMETEK Programmable Power’s products serve a wide range of stimulus (T&M) and process power needs in applications including semiconductor fabrication, commercial and defense ATE, oil exploration, solar array and battery string simulation, avionics, general R&D and EMC compliance testing.
72 LINEAR & ROTARY MOTION
Rediscovering ball splines for robust linear and rotary motion
As emerging opportunities for automation bring more axes of motion to machinery, more designers are finding that prepackaged solutions aren’t always flexible enough to meet application requirements.
78 TEST & MEASUREMENT
Applying PC-based test & measurementt instruments
For some features, PC-based scopes sport higher performance than simlar benchtop instruments.
82 MECHANICAL
A closer look at EMQ-rated bearings
The demand for a quiet electric motor — one that runs with very little noise and vibration — was the primary application that drove engineers to develop and market low-noise ball bearings.
88 3D CAD CAD helps put magic in wheelchair design
Cosplay goes to the next level when CAD and 3D printing are involved.
Follow the whole team on twitter @DesignWorld
EDITORIAL
VP, Editorial Director
Paul J. Heney pheney@wtwhmedia.com @wtwh_paulheney
Managing Editor Mike Santora msantora@wtwhmedia.com @dw_mikesantora
Executive Editor
Leland Teschler lteschler@wtwhmedia.com @dw_leeteschler
Executive Editor
Lisa Eitel leitel@wtwhmedia.com @dw_lisaeitel
Senior Editor Miles Budimir mbudimir@wtwhmedia.com @dw_motion
Senior Editor
Mary Gannon mgannon@wtwhmedia.com @dw_marygannon
Senior Editor
Rachael Pasini rpasini@wtwhmedia.com
Associate Editor Heather Hall hhall@wtwhmedia.com @wtwh_heathhall
Senior Contributing Editor
Leslie Langnau llangnau@wtwhmedia.com @dw_3dprinting
CREATIVE SERVICES
VP, Creative Services
Mark Rook mrook@wtwhmedia.com @wtwh_graphics
Senior Art Director
Matthew Claney mclaney@wtwhmedia.com @wtwh_designer
Senior Graphic Designer Allison Washko awashko@wtwhmedia.com
@wtwh_allison
Graphic Designer
Mariel Evans mevans@wtwhmedia.com @wtwh_mariel
Director, Audience Development
Bruce Sprague bsprague@wtwhmedia.com
WEB DEV / DIGITAL OPERATIONS
Web Development Manager
B. David Miyares dmiyares@wtwhmedia.com @wtwh_webdave
Senior Digital Media Manager Patrick Curran pcurran@wtwhmedia.com @wtwhseopatrick
Front End Developer Melissa Annand mannand@wtwhmedia.com
Software Engineer David Bozentka dbozentka@wtwhmedia.com
DIGITAL MARKETING
VP, Digital Marketing Virginia Goulding vgoulding@wtwhmedia.com @wtwh_virginia
Digital Marketing Manager
Taylor Meade tmeade@wtwhmedia.com @WTWH_Taylor
Digital Marketing Coordinator Jill Bresnahan jbresnahan@wtwhmedia.com @WTWH_Jill
Webinar Coordinator Halle Sibly hkirsh@wtwhmedia.com
Webinar Coordinator Kim Dorsey kdorsey@wtwhmedia.com
EVENTS
Events Manager Jen Osborne josborne@wtwhmedia.com @wtwh_jen
Events Manager Brittany Belko bbelko@wtwhmedia.com
Event Marketing Specialist
Olivia Zemanek ozemanek@wtwhmedia.com
VIDEO SERVICES
Video Manager
Bradley Voyten bvoyten@wtwhmedia.com @bv10wtwh
Videographer
Garrett McCafferty gmccafferty@wtwhmedia.com
PRODUCTION SERVICES
Customer Service Manager
Stephanie Hulett shulett@wtwhmedia.com
Customer Service
Representative Tracy Powers tpowers@wtwhmedia.com
Customer Service Representative JoAnn Martin jmartin@wtwhmedia.com
Customer Service Representative
Renee Massey-Linston renee@wtwhmedia.com
Customer Service Representative Trinidy Longgood tlonggood@wtwhmedia.com
Digital Production Manager Reggie Hall rhall@wtwhmedia.com
Digital Production Specialist Nicole Johnson njohnson@wtwhmedia.com
Digital Design Manager Samantha King sking@wtwhmedia.com
Marketing Graphic Designer Hannah Bragg hbragg@wtwhmedia.com
Digital Production Specialist
Elise Ondak eondak@wtwhmedia.com
FINANCE
Controller
Brian Korsberg bkorsberg@wtwhmedia.com
Accounts Receivable Specialist Jamila Milton jmilton@wtwhmedia.com
At the recent Danfoss Distributor Meeting in Orlando, I caught up with Eric Alström, the company’s President. The company is a year removed om the purchase of Eaton’s hydraulic business, and I asked him about some current issues facing manufacturers.
One area discussed at the meeting was the importance of diversity. Alström said that’s the first of their three main priorities — their people. And particularly, to further diversity, equity, and inclusion.
“We are doing a tremendous amount of activities now to shake up the organization … it starts with me and my leadership team. We have to walk the talk. So, no more excuses that, ‘Oh, we couldn’t find anything else but white males for these positions.’ Well, then start again — we’re just not going to approve those positions then. But we need to have a talent funnel that mirrors the areas where we do business, and it doesn’t today. We’re working really hard on changing that and step by step,” he said.
Alström pointed out that there’s empirical evidence that diverse teams produce better results — and have a much better innovation track record. One thing he said the company learned om Eaton is the idea of Employee Resource Groups. Alström himself is the executive sponsor for one called Multicultural and Nations, as he noted that this isn’t just a U.S. issue.
“Racism exists everywhere in the world and derogatory comments, those types of things, we take very seriously at Danfoss because it’s not really in our culture. Fairness is deeply rooted. So, we are really pushing this now. I’m happy to say that we actually are making great progress now, finally. Because we haven’t been great at it in the past, but now we’re really getting some traction.”
The company is encouraging STEM/STEAM careers for kids and hoping to get a more diverse cross-section of young adults into engineering. They’re working heavily with Iowa State University in Ames and have the Danfoss Innovation Accelerator in Cambridge, Mass., on the MIT campus.
But he said they also need to be stronger in other countries, such as Germany. “Europe today is very diverse, but sometimes I think we’re not watching that pipeline well enough,” Alström said. “We’re really onto that now. One of the cool things about hydraulics is that it’s not the first on university students’ list of companies that they look at. But we try to open what I call the Danfoss box and let them peek in. And then they see that we are really environmentally conscious, DE&I is high on our agenda, and we have great technology, so ware, autonomous machines, and all sorts of cool stuff … it’s actually pretty easy to attract diverse talent in engineering.” DW
Back in the 1980s, a buddy of mine who was a plant manager proudly showed me the computer network he’d set up. The primary task of the network was to let people in the ont o ces program the plant’s CNC machines with G code without having to visit the plant floor.
The network worked great, but this all happened long before the invention of the world-wide web. So there was no thought given to making the computer network or the CNC machines in the plant secure om outside mischief.
Unfortunately, it looks as though CNC security hasn’t progressed much past that in my iend’s 1980s network. At least that is the impression you might get om a recent report by researchers at cyber security so ware company Trend Micro and CNC integrator Celada. Researchers hailing om these firms studied security measures in widely used metal-working machine controls made by Haas Automation, Heidenhain, Fanuc, and Okuma as being representative of the field.
Overall, researchers concluded that security doesn’t seem to be a priority for controller makers. In that regard, they identified about 15 ways of attacking Haas, Heidenhain, and Okuma controllers, and 10 ways of messing up Fanuc controllers.
Generally, researchers found that common security mechanisms
deployed in ordinary computers and servers were absent on CNC installations. One basic problem they discovered was that many of the machines obeyed any command they were given without checking to see whether the command issuer was legitimate. (Interestingly, this shortcoming is also common in HVAC networks.) Fanuc controllers do have protocol authentication, but only as an option that end users must enable.
Machine controllers also typically lacked resource access controls which thwart the installation of malicious applications. Without such measures, there’s nothing to prevent CNC machines om being loaded with open-source code hiding harmful functions around legitimate ones.
Some CNC security problems are basic to the point of being humorous. For example, Heidenhain provides a default OEM password for all its controllers. The company leaves it up to the machine manufacturer to change the password. Moreover, the password is weak (six digits) and stored on a file system that an attacker can get to.
There were also troubling problems specific to different brands of controllers. For example, Haas controllers were susceptible to unauthorized modification of their firmware. The version of Linux running on Heidenhain machines was unpatched and affected by multiple
vulnerabilities. Ditto for the Okuma controller which ran an unpatched version of Windows.
The kind of potential havoc Trend Micro and Celada foresee arising om such security problems ranges om the machining of bad parts to endangerment of machine operators. They envision attackers potentially gaining control of parametric programs to modi the tool geometry so it introduces microdefects in the work piece or fooling operators into using a tool past it’s point of exhaustion. In one case, they found controllers could be hacked so nothing happened when the operator pressed the pause button.
It is clear that attackers would have to know their way around a CNC machine quite well to carry out some of the scenarios security researchers envision. That probably rules out pranks pulled by juvenile delinquents. More worrying is the possibility of sabotage by statesponsored hackers.
Before Stuxnet ruined almost one-fi h of Iran’s nuclear centrifuges in 2010, few people worried about malware in factories. Let’s hope it doesn’t take a similar event to get the attention of companies making CNC controllers.
lteschler@wtwhmedia.com
On Twitter @ DW_LeeTeschler
Control solenoid valves from The Lee Company offer superior quality, proven reliability, and long-lasting performance. For your most demanding medical and scientific applications, choose a valve that hits the mark every time.
Scan to explore our full collection of control solenoid valves.
German-based igus is expanding its “Chainge” recycling initiative, which was launched in 2019. The program will now allow for the recycling not only of e-chains and other technical plastic waste, but customers can also purchase processed material (ground material and regranulate) online, thus allowing for a single source.
A er the end of their service life, energy chain cable carriers (or e-chains) o en end up in industrial waste and thus incinerated. Their emissions pollute the environment, losing valuable resources forever. These are linear economic problems that the company has been trying to counter since 2019. Customers send worn-out e-chains, regardless of their manufacturer, to the corporate headquarters in Cologne, where igus re-granulates them for reuse. Customers receive a voucher in return for their old chains.
“What began as a small idea has rapidly picked up steam. Since the start of Chainge, we have collected and recycled [more than] 60 tons of high-performance plastics. Half of that was in 2022 alone,” said Michael Blass, CEO of e-chain systems. “This positive feedback has motivated us to think even bigger about recycling. To accelerate the transformation to a circular economy, we will therefore start including e-chains in the recycling program and other components made om technical plastics.”
To speed up the recycling process, the company launched a new online Chainge platform in October. There, owners of old plastic parts, such as bar stock and gears, can submit a recycling request, process returns, and manage credits for purchasing new products. As part of the expansion, additional locations will be added to the program, to further broaden the recycling network.
“Our recycling will no longer be limited to our headquarters in Cologne but can be performed worldwide. These additional capacities will allow us to make an even greater contribution to the circular economy,” said Blass.
The platform will also sell regranulate, which until now has only been used in in-house injection molding. Additionally, Chainge recently gave rise to the world’s first energy chain that was made entirely om recycled material.
“The special thing about igus is that you get everything om a single source. We are a plastics producer and supplier, an assembly service provider, a disposal company, and a producer and supplier of recycled material used to create new products. What we offer is unique in this form and enables us to work with our customers to turn plastic into a sustainable resource,” said Blass.
The new online platform is located at: https://chainge. igus.de. DW
Every month, the Innovation Spotlight section will showcase a featured product from one of our brands that sets it apart in the industry. Be sure to create an account on the Virtual Trade Show for full access, including the latest Innovation Spotlights! In addition to the monthly Innovation Spotlights, visit the Virtual Trade Show to get a comprehensive overview of the capabilities of each leading brand while viewing imagery, videos, downloads and literature.
The rapidly growing interest in various types of VTOL aircraft has created a highly competitive market environment for vehicle OEMs. Formsprag Clutch, a global leader in clutch and brake technologies, is uniquely positioned to support VTOL aircraft design engineers as they meet these application challenges.
Whether a modified standard product or a completely new custom solution is required, Formsprag provides complete engineering and sales support to customers around the world, from the very first concept to the detailed planning, design variation phase and commissioning. To help improve speed-tomarket, custom prototypes are often delivered in weeks, not months.
Formsprag clutches and brakes can be utilized on all types of VTOL vehicle designs, including aircraft that...
-are electric battery, electric hybrid, electric hydrogen or turbine engine powered
-utilize multirotor, tilt-rotor or decoupledpropulsive drive systems
-are driven by 3, 4, 6, 8, 10 or more vertical thrust tilt rotors/fans
-incorporate pusher/lateral rotors/fans
-are piloted or optionally piloted
-utilize tilt and/or foldable wings
-are designed to carry passengers, cargo or both
-feature redundant electric motors on all rotors/fans
For more information, download P-8971-FC from www.AltraLiterature.com
Introducing motionCONNECT, which offers a single-access IIoT solution connecting Altra’s heavy-duty couplings, clutches, and brakes across applications used in mining, steel mills, ports, and other key markets to one common cloud.
• Distinguish between failures that require immediate attention vs. planned maintenance
• Eradicate root causes for failure
• Reduce unscheduled maintenance and downtime
• Optimize maintenance planning and component lifetime
Altra motionCONNECT provides the right information to the right person at the right moment.
For more information, download P-8982-C from www.AltraLiterature.com
Amusement Park Water Ride: A popular Orlando, Florida theme park needed a replacement overrunning clutch for use on one of its rides. The problem was that the original competitor clutch was failing due to its age. Formsprag worked with a distribution partner as well as the ride maintenance engineers to ensure that the replacement clutch was suitably sized to meet the ride’s requirements. Ultimately, Formsprag provided a special replacement FSO-900 clutch that featured nickel plating to withstand the heavily treated water containing chlorine and other corrosive chemicals.
World’s Longest Wooden Roller Coaster: An overrunning clutch was needed for use on the world’s longest wooden roller coaster located at a major amusement park in Ohio. As part of the coaster refurbishment, an upgraded Formsprag FSO clutch, popular for use on roller coasters, was supplied to provide increased reliability and extended life. The new, replacement FSO-500 model features improved seals that allow for low-maintenance grease lubrication. The previous model had oil lubrication that could leak out and allow the clutch to become dry.
Water Plume Ride: A popular theme park located in Ohio needed a replacement overrunning clutch for use on one of its water plume rides. In response, Formsprag provided an upgraded replacement FSO-500 clutch. The new clutch featured nickel plating to fight corrosion due to chemicals in the water. Also, a food-grade grease was substituted to eliminate any oil lubrication from being introduced to the water that splashes onto the riders.
For more information, download P-8984-FC, P-8986-FC, & P-8991-FC from www.AltraLiterature.com
Boston Gear Original “Domed Crown™” Stainless Steel 700 Series
Utilizing the often imitated but never equaled 700 Series worm gearing combined with new exterior designs, the new stainless steel 700 Series performance has been optimized to withstand the harshest washdown conditions!
• NSF International Certified
• Rounded housing eliminates virtually all flat surfaces and prevents foreign matter accumulation or standing fluid
• Elimination of all exposed hardware promotes smooth surfaces to optimize washdown effectiveness
• Lubed for life with H1 rated food grade lubricant Klubersynth UH1 6-460
• IP69K-Rated when ordered with the high pressure washdown seal option
• Available in hollow and solid output shaft
For more information download P-1998-BG & P-7756-BG from www.AltraLiterature.com or visit www.BostonGear.com
Laser marked nameplate provides worry-free part identification while maintaining a smooth, unetched surface. Rounded housing prevents foreign matter adherence and fluid accumulation.
Ameridrives Universal Joint Rebuild & Repair Service for the North American Metal Shredder Market
Metal shredder facilities in North America, with an eye on increasing output while reducing costs and downtime, can send their damaged Ameridrives or competitor U-Joints directly to the Rebuild and Repair facility in Erie, Pennsylvania.
Every hour of shredder downtime can cost thousands of dollars. That’s why the Ameridrives facility is set up and staffed to provide fast turnaround of all customer U-Joint repairs and rebuilds.
Ameridrives offers emergency rebuild services for those instances when a U-Joint needs to be repaired within a matter of hours and returned. Their dedicated team of technicians work after hours and over the weekend, if necessary.
Comprehensive services include the inspection, remanufacturing and repair of all shafts, spline sections, yokes, flanges, knuckles and journal cross assemblies. We are also able to provide in-house Non-Destructive Testing (NDT) of cracks in the yoke, flange, journal cross and spline.
For more information, download P-8030-AC-NA from www.AltraLiterature.com
All internal components – sprags, energized springs, retainer, bearings, seal and hardware are refurbished or replaced to new performance standards.
The inner and outer races are ground to speci cations noted below so that no wear patterns remain.
• Sprag Surface is hardened to 58-62 Rc
• Sprag Surface nish is 15-25 microinches
• Sprag Surface taper limit is 0.0002 inch per inch
This feature is designed into the products with the manufacturing of oversized sprags, and will significantly reduce the user’s long term operating costs.
Consider These Advantages:
• Price A guaranteed savings of 30% (compared to list price for a new unit).
• Speed Clutches are received, inspected and rebuilt in the shortest possible time frame.
• Warranty The Model LLH has a 3 year warranty, all other models are 1 year on labor and materials, same as new clutches.
• Emergency Breakdown Program All products that are air freighted into the Formsprag Clutch plant are processed immediately and, in most cases, are able to be rebuilt within a 24-hour period.
A line of light curtain mirrors leverages the long scanning range of the company’s PROTECTOR Series Light Curtains to help control access near industrial machinery where there is the potential for injury. The mirrors enable safety professionals to guard multiple sides of a work cell using only one PROTECTOR emitter/receiver pair. By reflecting the sensing field om the emitter around the perimeter’s corners to the receiver, the mirrors eliminate the need to use more than one safety light curtain.
Simple to mount on a standard protective column, the mirrors are available in several sizes ranging om 18.7 in. to 74.8 in. to fit almost any safeguarding requirement om robotic work cells to factory automation. A large reflector surface maximizes the in ared beam for e cient multi-sided detection of persons or other larger objects when they intrude into a protected area. Compared to traditional mechanical barriers, sliding gates, and pull-back restraints, this solution offers greater flexibility in design, while simpli ing the machine’s setup, maintenance, and repair due to the light curtains providing unhindered access to it.
Because they are rated IP65/IP67, the new mirrors offer protection om low-pressure water jets and more substantial liquid ingress or immersion, making them ideal for industries subject to equent wash downs or water spray, such as food, beverage and pharmaceutical processing. DW
Rockford Systems, LLC | www.rockfordsystems.com
WHITTET-HIGGINS manufactures quality oriented, stocks abundantly and delivers quickly the best quality and largest array of adjustable, heavy thrust bearing, and torque load carrying retaining devices for bearing, power transmission and other industrial assemblies; and specialized tools for their careful assembly.
Visit our website–whittet-higgins.com–to peruse the many possibilities to improve your assemblies. Much technical detail delineated as well as 2D and 3D CAD models for engineering assistance. Call your local or a good distributor.
The powdered iglide i6-BLUE laser sintering material for 3D printers is easy to detect thanks to its blue coloring. It complies with FDA and EU 10/2011 regulations. The new material increases the safety of machines and systems in the food and beverage industry. iglide i6-BLUE is similar to iglide i6 in terms of strength and sliding properties and is particularly suitable for printing worm gears, toothed gears, and snap-on connections.
Manufacturers of machines and systems for the food and beverage industry have long used 3D printers as an alternative to conventional technologies, such as turning and milling. More and more design engineers want blue printing material. The color blue is easy to see and therefore increases food safety. If a 3D-printed component breaks, blue agments in the product are easy to see and can be quickly identified with detectors.
The problem is that there are still very few blue printing materials on the market that are robust and foodcompliant for the selective laser sintering manufacturing process. The material is resistant to temperatures between -40° and +80°C.
Tests have shown that 3D-printed gears made of iglide i6-BLUE have a longer service life than milled wheels made of polyoxymethylene (POM) and are at least nine times as abrasionresistant as PA12 material often used in selective laser sintering processes.
Due to the high elongation at break, the laser sintering printing material is also suitable for the additive manufacturing of snap-on connections. In addition, iglide i6-BLUE increases the hygiene of machines for the food and beverage industry. Microscopic solid lubricants are integrated into the laser sintering material and released automatically during movement, allowing low-friction dry operation. This eliminates the need for lubricants, which attract dust and dirt and can become a contamination risk.
Machine manufacturers who do not have their own 3D printer can use the igus 3D printing service — with no minimum order quantity. DW igus
www.igus.com
The i3 Control (“iCube” Control) debuted in the European market earlier this year and is now being introduced in North America. This open system platform consolidates various automation controls into one centralized controller, allowing for seamless and secure collaboration by teams across different locations. iCube Control, which combines powerful, modular hardware with a flexible so ware in astructure, is easily scalable and fully customizable to meet the individual needs of its users.
This machine control platform includes five elements:
• i³ MC, a machine controller for motion, logic, kinematics, safety, and more.
• i³ Engineer, which promotes multi-location collaboration by providing a single environment for motion, logic, and safety programming.
• i³ Data, a dedicated control module for real-time data acquisition, processing, communication, and feedback.
• i³ Web, a secure web-based management platform.
• i³ Kinematics, which delivers integrated control and safety for Delta, SCARA, 6-axis, Gantry, and customer-specific mechanisms. DW
Yaskawa America | www.icubecontrol.com
This area has long been one of the most read and sought after by our engineering audience! From screws to bolts and adhesives to springs, these critical but often overlooked components are the key to every successful design.
FastenerEngineering.com will serve readers in the mechanical design engineering space, providing news, product developments, application stories, technical how-to articles, and analysis of engineering trends. This site will focus on key issues facing the engineering markets around fastener technology, along with technical background on selected components.
ADDITIONAL RESOURCES:
• Special print section in select issues of Design World
• Fastener Engineering monthly newsletter
The TD 110 Tool Breakage Detector is specially designed for quickly sensing tool breakage during use within a machine tool. Providing contactee inspection of drill bits and end mills, it can determine whether a tool is broken off by more than 2 mm as it passes within a machine tool.
The tool breakage sensor can be placed in the work envelope so that it is fast and easy to reach during the tool change. The inductive sensor can detect tools as they pass by while they are spinning at their operational speed. Thanks to its rapid scanning technology, even very small tools made of HSS steel and carbide are detected.
The breakage sensor can then generate either a floating or an HTL switching signal and the machine control can evaluate it via standard instruction sets. These signals/outputs can be used to connect to a HEIDENHAIN TNC control or a PLC or to any other IOs of nearly every CNC control manufacturer. In addition, an LED signals whether a tool has been flagged.
Overall benefits include:
• Maintenance- ee sensor for reducing non-productive time for breakage inspection.
• Cooling lubricant and lightly contaminated tools are tolerated.
• Universally retrofittable thanks to standard interfaces for tool touch probes. DW
Eliminating electrical cabinets offers many advantages to machine builders, system integrators, and equipment end users alike, including space savings, simplified wiring, reduced installation effort, and lower costs. Beckhoff has been focused on making the cabinetless machine a reality for years with innovations such as One Cable Automation with EtherCAT P, the AMP8000 distributed servo system, and the C7015 ultra-compact Industrial PC, an IP65/67-rated machine controller. Now, the comprehensive, IP67-rated MX-System provides the next evolution in a complete machine-mountable control platform.
MX-System enables control cabinet- ee automation solutions in machine and system engineering. The MX-System provides a modular construction kit that combines all tasks and features of a machine’s control cabinet. These include energy supply, fuse protection and distribution, generation and monitoring of auxiliary voltages, sequence control with the inputs and outputs, control of motors and actuators as well as the connection level for field devices. With MX-System, fabrication, metalworking and additive applications can reduce control cabinet builds that previously took 24 hours to just one hour.
The space, cost and installation savings of MX-System make this cabinetless machine control solution suitable for countless fabrication, metalworking, and additive applications. DW
Beckhoff Automation
www.beckhoff.com
Medical device manufacturers are motivated to deliver groundbreaking drug delivery solutions driven by new pharmaceutical therapies and smart connected products that have the potential to transform the patient care paradigm om in-patient care to outpatient and selfadministered therapies. Innovators that provide a compelling and intuitive user experience have a competitive advantage. However, medical device makers face challenges in their quests to develop innovative devices that meet regulatory requirements, achieve sustainability goals, and improve patient experience and outcomes.
To address these challenges, medical device makers are leveraging computer-aided design (CAD), modeling, and simulation technologies unified on a collaborative and data-managed platform. This unified modeling and simulation (MODSIM) approach om Dassault Systèmes enables scientists, researchers, engineers, and designers to collaboratively develop and evaluate pharmaceutical therapies combined with mechanical and electronic devices for optimal patient care.
MODSIM delivers full associativity between CAD and computeraided engineering (CAE) models and connectivity with functional requirements, product designs, and simulation results to ensure decision traceability. Beginning with conceptual designs, designers and engineers can collaborate across work functions on developing a device and its components tailored to delivering a specific drug therapy.
They can analyze a range of physics that influence design performance, including structural analysis of components and assemblies, fluid dynamics, and fluid-structure interactions of the drug delivered through the device and electromagnetic analysis of the electronic components and antennas for wireless connectivity.
Combined with design exploration, optimization, and data management applications, MODSIM improves upon basic CAD and CAE integration. MODSIM enables workflow automation to eliminate laborious, repetitive, and error-prone tasks such as updating simulation models and re-meshing each design revision. Best practices for modeling and simulation are easily captured, templatized, and distributed to non-experts so they can reliably assess the implication of design
modifications. Data management apps and the cloud platform allow them to share their simulation results and share their thinking on performance-based decisions, regardless of their physical location.
Beyond the device function itself, developers need to evaluate the physical and physiological interaction of medical devices with the human body. For instance, when developing a drug delivery device, designers can use a virtual twin of the human body, which is a dynamic virtual 3D model, to analyze the sizing and ergonomics of their device, and the force required to insert a needle into the skin for various patient types ranging from adults to children. Similarly, cardiac implant makers can use a virtual twin of the heart to evaluate how an artificial heart valve will move during the cardiac cycle in a virtual environment
before physical prototyping or testing on humans. Significant technical advances are being made in the development of realistic, validated virtual models of human organs and musculoskeletal systems to enable the assessment of medical device safety and effectiveness.
Realistic modeling and simulation of medical devices interacting with virtual humans offers the promise of creating personalized virtual twins to evaluate the individual patient experience, device safety, and therapeutic outcomes. DW
Dassault Systèmes Life Sciences & Healthcare
www.3ds.com/industries/life-scienceshealthcare
Turn your design challenges into next-generation, marketleading medical devices with our extensive manufacturing capabilities and engineering expertise. We have facilities in Fremont, CA and Santa Ana Sonora Mexico.
The Type ABR Wi-Fi 11b/g/n+MCU module with PCB antenna is based on NXP Semiconductor’s 88MW320 wireless microcontroller. It supports Wi-Fi 802.11b/g/n up to 72.2Mbps PHY data rate with an integrated 200MHz Arm Cortex-M4F MCU for host-side applications. The module offers a complete network controller solution via a simple UART interface. The Wi-Fi, TCP/IP, security supplicant, and other network application features are hosted directly on the module. Its small form factor (22 x 19 x 2.4 mm) eases integration into size- and power-sensitive applications such as Industrial Internet of Things (IIoT), sensor networks, and gateways. With the rapid growth of IoT, the speed at which products and services go to market has become increasingly more critical. However, providing products with wireless communication functionality has historically required a level of Wi-Fi and other wireless communication technologies expertise. In response to this need, Murata developed the Type ABR as a solution to enable Wi-Fi functionality just by entering simple commands. It is compliant with the Radio Act, so there is no need to obtain separate certification. It also contains a built-in NXP MCU, allowing it to be used with so ware development tools (EZ-Connect, WMSDKA) that leverage the NXP amework for simpli ing application development. This reduces the amount of resources spent on design, allowing IoT devices to be developed and launched more e ciently. DW
In food and beverage manufacturing, clean-in-place (CIP) systems are a fundamental part of daily production that allow manufacturers to clean internal piping, tanks, and machines om one batch to the next to meet government regulations and ensure product quality and safety. For these manufacturers and others who use CIP systems, this cleaning process can represent up to 30% of a facility’s total utility costs.
These factors make the CIP operation a perfect candidate to be digitally transformed. By combining sensor-equipped devices like pressure regulators and valves and overlaying CIP so ware to capture and analyze critical process data, Emerson has designed a new CIP solution that combines sensors, hardware, and analytics that will soon offer manufacturers a esh set of options for optimizing utilities and enable automating reporting.
To understand the impact that this new digital solution can have on CIP processes in food and beverage manufacturing, consider a manual or sub-optimized CIP system in a brewery or dairy. A batch tank is connected to a water supply line and a series of cleaning supply tanks that contain media such as disinfectant, acid, and caustic and reused water. Each media tank pumps a process fluid into the batch tank in a sequence according to the cleaning protocol until the timed cycle is complete and the tank is considered clean.
Despite the simplicity of this configuration, many ine ciencies can exist. First, the operator overseeing the CIP system o en does not know how much media is consumed during each timed cleaning cycle. The operator monitors and fills the supply tanks and makes manual adjustments to flows, but the specific volume of media per wash cycle is o en unknown, creating an opportunity for untracked waste.
Second, the cleaning cycle may run for a preset amount of time deemed su cient for cleaning, but if no sensors or metrics are in place, then waste is likely occurring during the cycle.
Yet another common ine ciency and hidden cost within a CIP system is when an operator is manually logging process data like cycle times, pressures, and temperatures and completing routine system reporting on paper. This pencil-and-paper approach not only requires time for the operator to capture the data for reporting, but it also adds opportunities for human error during the recording process.
To achieve digital transformation of the CIP process, Emerson identified the valves, sensors, and instruments required to gather critical process data and combined them with newly developed
Inflation and broken supply chains shouldn’t dictate when you get your North American and international cords. Interpower is one of two remaining electrical cord manufacturers in America. And, if the cords you need are in stock, Interpower ships them the same day!
Whether North American 5-15, 5-20, 6-15, or 6-20 cords, or international country-specific cords bearing countryspecific plugs, IEC connectors are molded onto the other end to ensure cords are ready to use right out of the box! Amperage, gauge, length, and color—these preferences are up to you!
Manufacturers can access real-time process information via analytics software, equipping them with the tools to optimize e ciency and productivity.
so ware that collects and analyzes the data and presents it in report form. The system diagram shows how data collected on air, water, steam, chemicals, and energy is delivered to both the PLC that runs the machine or process and to an edge device where data is collected for local analysis and potentially forwarded to an enterprise-level system or the cloud.
With access to real-time process information via analytics so ware and available through automatic report generation, manufacturers can automate and optimize wash cycle settings, including cycle duration and media use, for optimal e ciency and maximum productivity. They also have the option to take the data and analytics further into enterprise-wide systems.
As part of its initial testing, Emerson developed an analytics package for beverage manufacturing with Lakeside Process Controls, a long-time Emerson
In
CIP systems, sensors like Emerson’s AVENTICS Series AF2 Flow Sensor monitor air consumption to provide real-time data.| courtesy of Emerson
channel partner who was tapped to bring customer knowledge and insight into the development process. The test skid used sample data to demonstrate how water, acid, detergent, and reclaim can be optimized during a CIP cycle, and it produced a 30% to 45% reduction in water consumption and a 20% reduction in operator time spent at the CIP station. This reduction in operator time alone represents a savings of $20K to $40K annually, and it can help to alleviate the all-too-common stress of a stretched workforce.
Digitalization of CIP systems also eliminates pencil-and-paper record keeping and replaces it with so ware capable of instantly converting process data into organized reports. Reports can be generated for satis ing government regulation and compliance requirements, planning system maintenance, scheduling downtime, and ordering media supplies.
Another unique feature of the CIP so ware is its ability to generate a “golden batch” score that represents the ideal benchmarks of a cycle running at optimal e ciency. Automated reports can then be set up to compare each wash cycle’s utilities consumption to the “golden batch” to track process improvements.
In addition to optimizing process e ciency, other productivity improvements were also demonstrated with the Lakeside skid. For instance, shorter cycle times resulted in up to 50% faster changeovers. Instead of using a timed cycle, sensors and so ware can tell the operator when the cleaning cycle is complete. This delivers a huge benefit for manufacturers in terms of conserving media usage and reducing overall energy consumption. Shorter cycle times also get batch tanks back online faster, increasing uptime and improving productivity.
While many suppliers offer CIP hardware and sensors, few have taken the steps to apply the available data to the deep analytics that can fully unlock the advantages of digitalization. And even fewer have done so in a way
that allows manufacturers to pick and choose how they access the process data and whose components they use to make that data available. This is where Emerson has taken a different approach by giving manufacturers the power to decide where and how they enter the digitalization process and by providing the so ware to capture significant benefits without requiring that the so ware be supported by Emerson brand components.
For instance, the Emerson CIP system built by Lakeside represents a complete end-to-end solution, but the so ware itself is agnostic and is designed to work with Emerson equipment and with competitor equipment to deliver the greatest amount of flexibility. This allows manufacturers at any stage of digital transformation to integrate any or all components, including the so ware, and to customize it for their needs. DW
Emerson | www.emerson.com
ABB is entering into a strategic partnership with US-based startup Scalable Robotics to enhance its portfolio of user- iendly robotic welding systems. Through 3D vision and embedded process understanding, the Scalable Robotics technology allows users to easily program welding robots without the need for coding. ABB Technology Ventures (ATV), the venture capital unit of ABB, will be the lead investor in Scalable’s seed funding investment round.
“Businesses are looking to robotics to help build resilience, flexibility, and e ciency in the face of global challenges, including labor shortages, disrupted
The Scalable platform allows a welder to teach a task to the robot by pointing to where the weld should be applied, with the robot learning the path on its own.
supply chains, and uncertainty,” said Marc Segura, President, Robotics Division at ABB.
“In the US alone, it is estimated there will be a shortage of 400,000 welders by 2024. To tackle this, we need to aid the adoption of robots by providing technology that is simple to use and easy to program, enabling manufacturers to easily introduce automated solutions that can weld more parts in less time while minimizing scrap and maximizing quality.”
Scalable’s technology enhances ABB’s existing portfolio of no-code programming applications that help to remove the need for specialized programming knowledge. The Scalable platform allows a welder to teach a task to the robot by pointing to where the weld should be applied, with the robot learning the path on its own. The platform features a 3-D camera in a protective box attached to the robot’s end-of-arm tooling and uses a touchscreen interface to guide the welder through the scan, teach, validate, and tuning steps.
The welder teaches the robot the positions of the welds by clicking a
The platform features a 3-D camera in a protective box attached to the robot’s end-of-arm tooling and uses a touchscreen interface to guide the welder through the scan, teach, validate, and tuning steps.
handheld stylus to indicate the desired approach, path, and departure points of the weld. The platform automatically generates a weld path validated within RobotStudio, ABB’s simulation and programming so ware. The operator makes any final modifications before the robot auto-tunes the program and sends it to the robot controller so the weld can be performed.
“We founded Scalable Robotics on the premise that industrial robots are tools that should be available to enterprises of all sizes and levels of technical sophistication,” said Tom Fuhlbrigge, Founder and CEO of Scalable Robotics. “Our novel human-robot interaction techniques enable people who know the arc welding process to intuitively show the robot what needs to be done with no robot experience required. We are very excited to join forces with ABB.” DW
Interpower® American-made North American and international cord sets provide correct amperages and voltages ensuring customers have country-specific plugs for their unique local mains power. Have your cords been waylaid and locked in a warehouse awaiting transport? Interpower in-stock cords, cord sets, and components ship the same day!
Interpower manufactures state-of-the-art electrical cord sets for global markets with no minimum order requirements. All Interpower cords and components are manufactured in accordance with Interpower’s product quality plan: hipot testing, continuity testing, and ground testing with multiple inspections. Interpower offers value-added options: lengths, colors, packaging and labeling!
® ®
Industrial automation so ware developer Copia Automation recently announced the release of DeviceLink, delivering automated backup and change detection for industrial control devices. Cloud-hosted and Git-based, Copia empowers controls engineers to unlock the advantages of DevOps workflows in driving greater team e ciency, code quality, and operational uptime.
“Once a machine is deployed to the factory floor, most manufacturers lose visibility into how control programs change. Teams are focused on keeping machines running and not documenting the code tweaks and edits that always occur over time,” explained Copia CEO Adam Gluck. “DeviceLink automatically backs up these control programs to one centralized location giving teams code security, up-to-date visibility and most important — change traceability.”
Copia’s DeviceLink works with Allen-Bradley, CODESYS, Beckhoff, and FANUC devices and can schedule code backups at any time or equency. FTP and Bash scripting are also supported, and Siemens device support is coming soon. Once the code is backed up, DeviceLink will compare it to the last known version. When changes are detected, it will create a new committed version. If desired, the new edits can be reviewed, approved, and merged into any ongoing development code.
Modern DevOps hits the factory floor, up-leveling data security and visibility, by detecting unauthorized code changes.
“Regardless of how much equipment we’re managing and how many sites that equipment is spread across, DeviceLink shows us all the live control code in one place,” said Kellen Murray, founder at Konductive. “We always have up-to-date restore points in case of failures and are proactively alerted to unauthorized changes.”
Device Link builds on the power of Copia Automations Git-based source control and its ability to render control programs in standard formats, including ladder logic (LD), function block diagram (FBD), and structured text. As changes occur, Copia can highlight the difference between versions.
“Not only do one gain knowledge of when PLC or robotic code changes, but one can also immediately see the exact edits,” stated Gluck. “This insight is crucial in determining whether the change was authorized and must be the restore point moving forward.”
DeviceLink helps bring modern DevOps practices to industrial automation, equipping control engineers with the same workflows used in traditional so ware development. The Git-based source controls allow engineers to work simultaneously on the same codebase, review code e ciently, and ensure that all changes are documented and accessible.
“By integrating Copia Automation’s platform into the daily workflow, we can better use engineering resources to handle more projects and ensure the highest quality code development,” Murray explained. “DeviceLink builds on these benefits by providing the same level of visibility into the control programs running on the factory floor.” DW Copia
We’ve added two new products to our broad line of cylinders and transducers: our new HB Series thrusters provide the high load capacity you need in a pneumatic thruster. And our new NTS series transducers give highly accurate temperature readings in a low-cost transducer.
Check out these new products, as well as our full range of cylinders, transducers and switches, at nasonptc.com/new
Volume elements: with the Voxelfill strategy, voxel cavities (component contour and inner walls) are printed and then selectively filled with material.
All image sources: AIM3D GmbH, Rostock (Germany)
Every 3D printing process competes with classic manufacturing strategies such as casting or milling in terms of mechanical properties, time factors and cost-effectiveness. It is also in competition with alternative 3D printing technologies. The present technological challenge: layerbased 3D build processes of polymers o en exhibit inhomogeneous structural properties. AIM3D hopes to solve that issue with its patentpending Voxelfill process. The company claims the process overcomes inhomogeneous strength issues by achieving defined, selective densities in the component.
In additive manufacturing of polymers, components have inhomogeneous strength properties due to the layer-based build process. This manifests itself primarily in the form of tensile and flexural strength shortcomings, as well as brittle behavior along the Z axis. In contrast, the strengths achieved along the X and Y axes with some processes are already close to the strengths possible with conventional injection moulding. AIM3D has demonstrated this with the processing of fibre-filled components based on PA6 GF30 material.
The phenomenon of inhomogeneous strength properties must be resolved in order to enable a wider applicability of 3D-printed components.
By using the 3D extrusion technology of AIM3D’s CEM process, it has developed a Voxelfill strategy that overcomes these limitations and increases the cost effectiveness of the CEM process. Voxelfill can also be used for multimaterial components and is suitable for constructing 3D components using plastics, metals and ceramics.
With the Voxelfill approach, components are no longer created exclusively in layers, but use cross-layer filling through voxels as volume areas. To do this, the component contour is first created as usual as the basic structure using one or more webs of the extruded material. A lattice pattern is
Selective filling of the volume elements: when the volume areas are filled, this does not include filling all voxels in one plane. This would again result in a Z direction weakness directly in the “seam” plane. By shifting the volume elements halfway up the voxel, a kind of “brick-like bond” is created in the component, resulting in the yield line being offset.
created inside the component, which defines the boundaries of the volume elements to be filled, similar to cavities. This structure of the voxels to be filled resembles the honeycomb in a beehive.
The Voxelfill strategy now comprises two process stages:
1. Generation of a lattice structure. The CEM system repeats a lattice structure up to a defined height of the volume elements, then at this point the previously created cavities (voxels) are filled by injecting thermoplastic material with the extruder.
2. Filling phase of the voxels. The second, even more important component of this 3D printing strategy is deployed. When the volume areas are filled, it does not include filling all voxels in one plane. This would again result in a Z direction weakness directly in the “seam” plane. By shifting the volume elements halfway up the voxel, a kind of “brick-like bond” is created in the component, resulting in the yield line being offset. This results in an increase in strength and also improves the elasticity of the components in the Z direction. In addition, the introduced volume elements greatly reduce the printing time for fully filled components and thus significantly increases the costeffectiveness of the CEM process.
Variations of the Voxelfill strategy with the CEM process enable the use of various materials: hybrid multimaterial solutions with different Voxelfill materials and different materials for
the contour/structure of the inner walls become possible. This way, the material properties can be “customised.” Defined component weight, damping properties, elasticity or changes to the centre of gravity can be tailored to the application. By selectively filling only certain volume chambers (selective densities), component properties could be influenced in a targeted manner on the basis of FE simulations.
With Voxelfill it is possible to only fill the areas of a component that are absolutely necessary for the flow of forces. As a result, from the outside these components purely look like conventional parts, and can also benefit from applying finishing processes. At the same time, however, the 3D printing process is carried out with reduced material and weight, right up to realizing lightweight components. Especially when deploying fibre-reinforced materials, the use of Voxelfill offers an additional option for specifically aligning the fibres in the component to enhance mechanical properties. In the flat plane, the CEM process offers good options for controlling the orientation of the fibres. With the Voxelfill strategy, this affects the contour and the inner walls of the component. By injecting the material into the volume chambers (filling the voxels), the 3D component also receives fibres that are aligned in the Z axis, thereby further improving mechanical properties.
Clemens Lieberwirth, CTO at AIM3D: “Of course, the Voxelfill process is particularly suitable for 3D printing of plastics and fibre-filled plastics, but it is also suitable for 3D printing of metal and ceramic components using the CEM process. In general, there are advantages due to the higher build speed and cross-layer filling.”
K 2022 and Formnext 2022 in the autumn of 2022 will mark the launch of AIM3D’s ExAM 510 granulate printer.
The ExAM 510 offers a greater build area, higher precision and accelerated build speeds. The ExAM 510 printer is a multimaterial printer for additive
Bond increase: by shifting the volume elements halfway up the voxel, a kind of “brick-like bond” is created in the component, resulting in the yield line being offset.
manufacturing that can consecutively print up to three materials. The increased build area of 510 x 510 x 400 mm³ opens up more applications. The build area can be heated up to 200 ºC in order to reduce the stresses in the component and to process high-performance materials. The significantly increased build rate or print speed depends on the material used and can be as high as 250 cm³/h (when using a 0.4 mm nozzle). This extruder class enables extrusion rates that are up to 10 times higher than commercially available filament extruders. AIM3D has equipped the system with a heatable process chamber for the use of high-temperature plastics. This makes it possible to also process high-temperature plastics such as PEEK, PEI, PSU, PPS, with or without fibre filling. DW
AIM3D | www.aim3d.de/
but
Hexagon and Raytheon Technologies have partnered to deliver a simulation tool that will enable evaluation and optimization of metal additive manufacturing (AM) processes through the prediction of thermal history and defects at the laser path and powder layer scale.
Combining technologies om Hexagon’s Manufacturing Intelligence division and Raytheon Technologies’ Pratt and Whitney business, the new so ware will predict defects before the expensive and time-consuming printing process begins. This analysis will help designers and engineers evaluate the print outcome and test combinations of materials, geometries, and print processes.
“We’ve partnered with Raytheon Technologies to deliver an intuitive and accessible tool that will help engineers quickly predict and mitigate risks,” said Jeff Robertson, Hexagon’s director of global business development. “The ability to evaluate full laser powder bed fusion (L-PBF) parts on the mesoscale will reduce the effort to achieve part certification and thereby support industrialization of metal 3D printing.”
The so ware will be made available to a range of companies engaged in additive manufacturing and will be complementary to Hexagon’s existing Simufact Additive tool. The similarity to the existing user interface will allow easy integration into existing manufacturing processes by users without the need for extensive training.
“By combining our additive manufacturing expertise with Hexagon’s we’re bringing a solution to market that helps manufacturers with all levels of experience make better products with greater e ciency,” said David Furrer, Pratt & Whitney senior fellow for materials and processes. DW
Manufacturing Intelligence Division hexagonmi.com
Structural analysis in version 6.1 using the new method for mechanical contact. The visualization shows the stress and deformation in the two metal tubes.
COMSOL Multiphysics version 6.1 is the latest version of the modeling and simulation so ware. Every aspect of the so ware’s simulation environment — om the ability to perform multiphysics analyses to the functionality for creating apps — delivers feature additions and workflow enhancements.
“This version provides our users with powerful multiphysics simulation tools in areas of highly competitive R&D, like audio technology and vehicle electrification,” said Bjorn Sjodin, VP of product management at COMSOL. “We have also strengthened the so ware’s foundation with new capabilities for optimization and the modeling of turbulent flow and mechanical contact.”
This release brings major upgrades to the fluid flow and mechanical simulation products. The CFD Module now includes high-fidelity turbulent flow with detached eddy simulation (DES). This yields the accuracy of large eddy simulation (LES) with substantially less computational effort. A new and fast method for mechanical contact is included in the Structural Mechanics Module and the MEMS Module. It introduces new functionality for solids, shells, and membranes with full support for self-contacting surfaces. There is a new method for assigning materials to thin structures that makes it easier to analyze gaskets, adhesive layers, and claddings.
Version 6.1 further expands the so ware’s capabilities for modeling speakers and microphones in consumer electronics with additional functionality for thermoviscous acoustics.
“We have a large and growing community of users among leading developers of audio technology. They use our so ware to analyze everything om smart phone speakers to earbuds and hearing aids. The functionality in this release completes the Acoustics Module simulation environment for analyzing electrovibroacoustics of microtransducers and microacoustic systems,” said Mads Herring Jensen, acoustics technology manager at COMSOL.
COMSOL continues its commitment to providing powerful simulation tools for engineers working on the electrification of vehicles. When assessing the operational reliability and safety of battery technology, users of the Battery Design Module will enjoy several important additions, including support for setting up thermal runaway propagation models.
“I am excited about our new user interface for battery packs,” said Henrik Ekstrom, electrochemistry technology director at COMSOL. “It will be very practical for battery developers interested in charge–discharge dynamics and thermal management simulations.” In the AC/DC Module, new functionality for rapid layout of motor windings and magnet arrays ensures a smooth workflow for electric motor design and analysis.
• Version control of reports and CAD assemblies in the Model Manager
• Automatic simplification of imported ECAD layouts for faster meshing and solving.
• Topology optimization with manufacturing constraints for milling.
• Multidimensional interpolation and inverse uncertainty quantification.
• Magnetohydrodynamics simulation with a library of liquid metals.
• Flowmeter analysis that includes coupled piezoelectric, structural, acoustics, and fluid flow effects.
• Simulation of acoustic streaming applications where ultrasound induces fluid motion.
• Analysis of fuel cell performance that includes effects of fuel impurities.
• Electrostatic discharge (ESD) simulation and prediction of lightning-induced damage to electronic components.
• Thermal analysis of satellites in orbit.
DW
COMSOL | www.comsol.com
Silicon Carbide (SiC) has made its mark in bringing faster, a smaller, and more reliable components than its fellow semiconductors to market. While SiC components have been around for a couple of decades, there is still a lot to learn and a lot to consider when choosing the most suitable WBG semiconductor for your device.
LET US HELP with tutorials, from looking at how WBG semis stack up in power conversion efficiency to an overview of SiC FETs and MOSFETs.
Check out our EE Classroom to learn more: www.eeworldonline.com/silicon-carbide-classroom
An electromagnetic simulation of an electric motor. The new functionality in version 6.1 makes the workflow for analyzing electric motors fast and accurate.
Oldham couplings are a good choice for food and beverage equipment due to their misalignment accommodation, zerobacklash properties, and balanced design. Ruland manufactures hubs in aluminum for general-purpose applications and 303 stainless steel for high corrosion and temperature applications, giving designers an off-the-shelf coupling suitable for various servo-driven applications such as connecting a motor to a ball screw, lead screw, or gearbox.
Oldham couplings are comprised of two hubs that mate to a center disk. This three-piece design allows food and beverage equipment designers to customize Oldham couplings with a clamp or set screw hub with inch, metric, keyed, and keyless bores. They have a balanced design for reduced vibration at speeds up to 6,000 rpm and operate with low bearing loads, protecting these sensitive components om premature failure. In addition, these couplings use a proprietary hub machining
process that leaves a smoother surface for interaction between the hub and disk, resulting in longer life and reduced downtime.
The Oldham disk is available in acetal for zero-backlash and high torque capacity, PEEK for high temperature and corrosion resistance, and nylon for dampening and noise reduction. In the event of failure or wear, the disk is replaceable, restoring the original performance characteristics of the coupling. Oldham couplings also act as a mechanical fuse during torque overload situations, with the disk breaking cleanly and stopping power transmission.
The use of 303 stainless steel combined with a PEEK disk allows designers to use standard Oldham couplings in various servo-driven applications. Stainless steel hubs have hardware of like material to maintain consistent corrosion resistance. Ruland adds a proprietary surface treatment to hardware to prevent galling.
These Oldham couplings are available in bore sizes om 1/8 to 1-1/4-in. and 3 to 32 mm. Disks can be manufactured with a center hole to allow further sha penetration or slots for retention hardware to attach the disk to a hub so it can stay in place during disassembly.
Oldham couplings are carefully manufactured in Ruland’s factory in Marlborough, Massachusetts under strict controls using proprietary processes DW
Ruland www.ruland.com
We make it easy to take your design further with a custom ring or spring.
• Economical Prototyping (No-Tooling-Charges™)
• Quick Lead Time
• Diameters from .118” to 120” in 40+ Materials
• Industry-Specialized Design Support
Oldham
ON QUALITY
Marking an anniversary with the trends, guidance, and products and services you’ll want to know about.
60_ Rob Bubencik Jr.
EAGLE STAINLESS TUBE & FABRICATION
40 years of quality success.
62_ STAINLESS STEEL: WHAT TO KNOW
And why you need to get it right for your application.
65_ 40 Years, Still Getting it Right
Eagle Stainless, still fabricating, cutting, and distributing quality tubing.
68_ What is the best advice for ordering tubing, you ask?
Eagle Stainless: Top 10 Guidlines
In 1982, Eagle Stainless Tube & Fabrication started in a small boiler room in Franklin, Mass. — with a bold commitment: To become a top supplier of the highest-quality stainless steel tubing and other metals worldwide. In 2022, as we mark our 40th anniversary, that commitment, our “eagle-eye” focus on quality across all facets of our family business, hasn’t changed.
The past four decades has seen Eagle Stainless go from a modest space started by my father, Eagle President and CEO Robert Bubencik Sr., and former partner Roy Elliot, to two 40,000-square-foot facilities for world-class manufacturing, warehousing, and distribution. Eagle has gone from a handful of employees to about 100 today who work in a family-run environment that promotes unity, communication, and enjoyment on the job.
Eagle supplies ultra-high precision, cut-to-length stainless steel tubing, components and parts, and off-the-shelf tubing sizes and grades for medical, aerospace, and industrial applications. Other Eagle inventory that helps our customers increase performance and profitability includes a focus on T300 series stainless steel –tubing, wire, and bar stock.
We at Eagle take great pride in serving all of our customers from small to large. Our customer base spans the world, from the United States to Australia, and Israel to Ireland and other European countries. My father’s dream has become Eagle’s reality, but there’s no time to rest on our accomplishments as we soar into the future!
Moving forward, we will continue to meet customers’ demand quality and precision, with zero room for error. From the outset of our small startup, the founders had the foresight to distinguish the company from the large metal service center chains by fo-
cusing on our core strength, the distribution and fabrication of stainless tubing. It is a challenging commodity to work because of its need to meet the most exacting of specifications.
One of our early successes was showing customers that we could meet — actually, exceed — their need for tubing absent of burrs. One of our specialties rapidly became deburred tubing of any diameter and quantity used in critical applications such as surgical instruments. We also instituted our Eagle Eye Quality Assurance program to ensure against digression from our customer pledge of zero defects. These early strategic decisions have worked well for us.
Our unparalleled expertise and uncompromising commitment to quality in raw stock, quality in machining, quality in fabricating and quality in finishing has contributed greatly to our success and longevity. This undaunting commitment from the top down continues to this day. It extends to our pledge of on-time delivery and fair pricing. And it extends to our culture of quality excellence in every department, where we check our products well beyond what the mills supply — well beyond what many competitors do.
ISO 9001 and ISO 13485 quality management certifications have been in place since 1998. ISO organizes processes, improves the efficiency of processes, and helps Eagle to continuously improve beyond most quality assurance (QA) programs. You’ll read more about quality and other topics in our Feature and Profile articles. The piece is endorsed by Blake Harrison, our sales manager, and highlights Eagle’s top 10 guidelines for ordering stainless tubing. Please give Blake a call to learn more.
The results from a customer survey we conducted in fall 2022 show an overwhelming majority of respondents reporting that they are likely to recommend our company. We are proud of this. Even more, we are proud of the fact that our customers keep coming back because of the quality reflected in our talented employees.
We have one particular project that my father started making back in 1982, and we have been producing it every year since then. We have orders lined up through 2023, thanks in large part to the dedication of our employees. Their critical role in our customers’ satisfaction cannot be emphasized enough.
Eagle’s philosophy has always been that quality can only be realized through the meticulous care of our employees and the consistency of commitment. That commitment includes our belief that quality in all we do requires employee empowerment. It is critical that we ensure our people feel a sense of ownership and personal pride when it comes to quality, from order entry to raw material, from purchasing to fabrication, and from QA to final testing and shipping.
The Eagle business model helps to empower employees in a number of ways. Our people experience important workplace stability that comes with consistency in leadership and operational processes that family-run businesses are well-positioned to provide. This allows us to work closely with employees in a setting where unity, respect, and open communication are prioritized.
We also support continued education in machining and other relevant
areas because well-trained employees are key to optimizing decision-making, productivity, and profitability. This leads to high employee morale, retention, and performance — and ultimately, world-class products and well-served customers.
I cannot think of anything more rewarding than knowing that even as our company has grown over the past four decades into the leader it is today, all of us at Eagle will continue our focus on meaningful and profitable partnerships with our customers. I foresee a bright future as we move into the next 40 years — and beyond.
Eagle Stainless Tube & Fabrication is a leading supplier of ultra-high precision, cut-to-length, stainless steel tubing and bar for medical, aerospace, and industrial applications. Custom and off-the-shelf sizes and grades are widely available. We offer cutting, precision machining, bending, CNC
Rob Bubencik Jr., Vice President of Operations at Eagle Stainless Tube & Fabrication, joined the family’s business in 1987 while attending Catholic University in Washington, D.C. After graduating with a degree in biomedical engineering in 1991, he began working at the company in sales and engineering. He received Six Sigma Green Belt from Greater Boston Manufacturing Partnership in 2005 and became VP of Operations in 2012.
machining, end forming, assemblies, and more. ISO 9001 and ISO 13485 quality management certifications have been in place since 1998. To learn more about Eagle or to discuss your application needs, visit us at https://eagletube.com, or call an Eagle expert at 800-528-8650.
Bob Sr. and Rob Jr. review a manufacturing process, 2005.
Eagle’s philosophy has always been that quality can only be realized through the meticulous care of our employees and the consistency of commitment.
Iron has been around for more than 1,000 years, but stainless steel is far newer, discovered in 1913. But when we talk about materials with nearly countless applications in the modern world what comes to mind?
Despite its relative infancy, it’s often stainless steel. What is stainless steel exactly — and why should designers, engineers, and specifiers consider it as an excellent candidate for a wide range of applications?
Stainless steel is the term used for the family of iron-based alloys that contains at least 10% chromium by weight. These alloys also include elements such as carbon, and other nonmetals and metals. Chromium is what gives steel its unique stainless corrosionresistant properties. With sufficient exposure to oxygen, chromium forms a tough and invisible protective film on the surface that allows steel to self-heal from mechanical or chemical damage. This is called the “passive layer.”
Increasing the chromium content and adding other alloying elements such as molybdenum, nickel and nitrogen further enhance a range of other useful properties, including plasticity, durability at high temperatures, ease of maintenance, and corrosion resistance. For these reasons, stainless is an ideal candidate in materials selection. Some may overlook stainless
because of its higher initial cost, but if correctly selected and maintained, it can provide the most value over the total life cycle cost (LCC) of a project. (See sidebar for more on initial cost and LCC.)
The global market certainly has been taking notice of stainless steel. Despite changes in the economy and other uncertainties, the value of stainless is on the rise, according to a study by Data Bridge Market Research. Valued at USD 104.23 billion in 2021, the market is expected to reach $166.13 billion by 2029, registering a CAGR of 6% during the forecast period of 2022-2029.
The vitality of the stainless steel market can be attributed to the versatility of stainless and its variety of applications, from medical to aerospace to industrial. There are so many grades of steel — more than 3,500 — that they are divided into a few main classes.
Professionals in the engineering and design space will want to know about these four typical classes and grades of stainless steel:
• 400 Series Martensitic — Grade 410. Straight chromium (12% - 18%); magnetic and can be hardened by heat treatment. Typical uses: Manufacturing, including fasteners, and plumb shafts.
• 300 Series Austenitic — Grade 304. Chromium (17% - 25%), nickel (8% - 25%); magnetic, not heattreatable. Can develop high strength by cold working. Additions of molybdenum (up to 7%) can increase the corrosion resistance. Typical uses: Food equipment, chemical equipment, and architectural applications.
• 300 Series Austenitic – Grade T316. Chromium (16% - 18%), nickel (10% - 14%), molybdenum (Mo) (2% - 3%) – the added Mo gives T316 better corrosion and pitting resistance over T304.
• Precipitation Hardening — Grade 17-7. Chromium (16% - 18%), nickel (6.5% - 7.75%), special highstrength alloy with good formability and fabricating characteristics. Develops strength by precipitation hardening reaction during heat treatment. Available in tube form.
• Precipitation Hardening — Grade 17-4. Chromium (12% - 18%), nickel (4% - 7%), martensitic or austenitic. Develops strength by preciptation hardening reaction during
And
you
heat treatment. Typical uses: Aerospace industry, and nuclear and chemical applications, including valves, gears, and petrochemical equipment. Available in wire and bar stock form.
Choose the right metal
Stainless steel is available in a variety of forms, including sheet, plate, wire, pipe, bar, and tubing. Tubing form — whether square, fractional, hypodermic, rectangular, or custom-shaped — depends on its application. There also are numerous grades of stainless steel, and not all are created equal.
Tubing is used in a variety of applications, including marine equipment, medical equipment, structural application, gas lines, heat exchangers, condensers, and any application requiring strength, corrosion resistance, or heat resistance. Operating environments significantly affect the performance of stainless steel.
For these reasons, temperatures and chemicals are among issues to consider when determining the right grade for an application or end product. For example, alloys such as 304 and 316
retain their strength, toughness, and corrosion-resistant properties in high temperatures. The primary difference between 304 and 316 is that 316 contains added molybdenum, allowing for superior resistance to chlorides. Tensile strength, ductility, and hardness are other important considerations.
It’s worth noting that T304L and T316L – L-grade options — are also available. L grade is defined by carbon content that is controlled to .03% - .04% depending upon the ASTM specification and size specified. L grade typically is specified when an application requires products that will be welded. The lower carbon provides enhanced protection against carbide precipitation during welding.
The ductility is the elongation during tensile strength. High ductility and high work hardening allows austenitic grades to be formed. While hardness of carbon steels can be increased by heat treatment, austenitic stainless is only hardened by cold working operations. All 300 series have a certain degree of work hardening, and 316 grades are easier to harden.
Factoring in form and process is critical when selecting the right stainless steel. Austenitic stainless is widely available in most forms. Most products require additional forming or machining before they can precisely match their application. In stainless tubing, an Eagle Stainless specialty, formed components are ideal for use in aerospace components, heat exchangers, medical devices and more. (See Products and Services for more on medical device other applications.)
Stainless tubing can be bent, coiled, redrawn, machined, welded, or formed into a variety of shapes. For stainless used in machining processes such as computer numerical control, machining, drilling, and bevel-cutting, the optimal machining rate typically is one that can mitigate the risk of workhardening.
Just as not all stainless grades are created equal, neither are stainless steel suppliers. Choosing the right supplier starts with trust — from the outset. Suppliers that can show a track record of consistently high levels of product and service quality are fundamental to trust. The ISO series of certifications, for example, are recognized internationally. These standards make industries more efficient and break down barriers to international trade.
Working with a supplier that is certified to a quality system recognized by your customers is critical. It is not unusual for companies to carry multiple certifications such as ISO 9001, and ISO 13485 for medical devices. Your customers require quality systems recognized by their industry.
Choose a stainless steel supplier that can match or exceed your strong commitment to quality products and systems. An experienced supplier also can provide additional recommendations on standard and custom options. These experts will be the partners you can count on to help prioritize your material requirements and serve as a guide for selecting the ideal stainless steel for your application.
Resources
• Eagle Stainless Tube & Fabrication Inc. (https://eagletube.com)
• American Iron and Steel Institute (AISI) (www.steel.org)
• British Stainless Steel Association (BSSA) (https://bssa.org.uk)
• Data Bridge Market Research (www.databridgemarketresearch. com/reports/global-stainless-steelmarket#)
• Southern Africa Stainless Steel Development Association (SASSDA) (https://sassda.co.za)
• Specialty Steel Industry of North America (SSNA) (www.ssina.com)
• Steel Tube Institute (STI) (https:// steeltubeinstitute.org)
• Corrosion resistance — Chromium is the alloying element that imparts to stainless steel their corrosion-resistant qualities. Low-alloyed grades resist corrosion in atmospheric and pure water environments. High-alloyed grades can resist corrosion in most acids, alkaline solutions, and chlorinebearing environments, thus making their properties useful in applications such as processing plants.
• Fire and heat resistance — Special high-chromium and nickel-alloyed grades resist scaling and retain high strength at high temperatures. Stain less steel is used extensively in heat exchangers, super-heaters, boilers, feedwater heaters, valves, and mainstream lines as well as aircraft and aerospace applications.
• Hygiene — Cleanliness is a matter of high importance. Stainless steel is relatively easy to clean, making it the first choice for strict hygiene conditions such as in hospitals, kitchens, and food processing plants.
• Aesthetic appearance — The bright and easily maintained surface of stainless steel provides a modern and attractive appearance.
• Strength-to-weight advantage — The work-hardening property of austenitic grades of stainless steel results in a significant strengthening of the material from cold-working alone, and the high strength duplex grades allow for reduced material thickness over conventional grades. This yields considerable cost savings.
• Ease of fabrication — Modern steel-making techniques mean that stainless steel can be cut welded, bent, formed, machined, assembled, and fabricated as readily as traditional steel.
• Impact resistance — The austenitic microstructure of the 300 stainless steel series provides high toughness at elevated temperatures. Their range starts at far below freezing, making these steels particularly suited to cryogenic applications.
• Long-term value — In considering total cost of stainless steel, it is important to consider not only material and production costs, but life cycle cost (LCC), the method for quantifying all costs, initial and ongoing, associated with the duration of a project. Stainless may not always be the least expensive material when considering upfront costs. However, experts agree: Stainless is often the least expensive material compared to others when calculating its LCC. The higher acquisition cost of stainless components is also offset by improvements in operating and maintenance costs, long life expectancy, and higher resale value.
• Recyclability — Stainless steel is 100% recyclable into the same product without degradation. More than 50% of new stainless comes from old remelted stainless scrap, thereby completing the full life cycle. According to the Specialty Steel Industry of North America, the metal’s high scrap value and successful recapture ensures its diversion from landfills. The content of the 300 series stainless grades used in the architecture, building, and construction market is 75% to 85%. On average the recycled content of stainless steel is 60%. In North America and other parts of the world recycled contents can be higher.
Using both semi-automated and automated optical measuring equipment allows Eagle to keep its quality at the highest levels.
Since 1982, Eagle Stainless Tube & Fabrication has been providing companies in medical, aerospace, industrial, and other industries worldwide with millions of feet of stainless tubing per year. The company’s focus is on serving customers with an extensive selection of high-quality precision-made stainless tubing, as well as off-the-shelf sizes and grades. In four decades that focus hasn’t changed.
Eagle Stainless stands out from the competition through its commitment to quality. The company meets international standards for quality management systems through its ISO 9001 and ISO 13485 certifications. The core of Eagle’s products and services are comprised of: Distribution of small-diameter stainless steel tubing; cut-to-length tubing; and fabricated components:
• Distribution. Eagle ships products, including tubing, bar stock, hollow bar, and both seamless and welded tubing, from an extensive inventory.
• Cut-to-length. Eagle’s manufacturing facilities enable the cutting and deburring of up to two inches in diameter and quantities of one piece to a million pieces of fractional, metric, pipe, and hypodermic tubing.
• Custom-fabricated. Working to customer specifications and specializing in bending, CNC and EDM/ECG machining and laser-machining, Eagle can produce close-tolerance parts for medical and other industries.
These value-added operations allow the company to help customers with the high-precision design and fabrication of products that fit their project.
Stainless steel tubing can be cut to length, bent, coiled, re-drawn, end formed, machined, welded, or formed into a variety of shapes. Whether it’s cutting, bending, coiling, or end-forming, Eagle’s two 40,000-square-foot facilities for manufacturing, warehousing, and distribution are where customers consistently turn to for worldclass products and services.
Eagle’s value-added offerings across all company operations include assisting customers with both custom design and fabrication of high-precision products that fit their project. Eagle’s standard and custom stainless steel tubes are used in nearly countless products — from heat exchangers and condensers to instrumentation and medical devices.
One example of Eagle’s many popular products is hypodermic tubing, used in medical device applications. (See sidebar for information on hypodermic tubes and Eagle’s lab kit for evaluation and testing.)
Regardless of your application, you can count on Eagle’s 40 years of expertise when designing and fabricating your metal project. Let Eagle know of your requirements. Unsure what they are? One of our specialists will be happy to assist you: https:// eagletube.com or 800-528-8650.
Stainless steel hypodermic tubes, also known as “hypotubes,” are medical-grade needle tubes that are used in the medical industry for test, evaluation, and prototyping by designers and laboratory personnel. This tubing comprises much of the backbone of medical components used in various medical and scientific applications.
Hypodermic tubing is generally made from stainless steel because it provides the uniformity, strength, and corrosion resistance that is required in most medical applications. Tubing grades generally are T (type) 316 and T304, though many are made from 304 stainless because of its availability and relative cost-effectiveness. Eagle Stainless stocks both T316 and T304 in a variety of gauge sizes, from 3 STD (standard tube) to 33 STD. (For more, see sizing guide chart.)
The tube is typically welded and purchased to outside diameter (OD) and inside diameter (ID) requirements, and is in full-hard temper condition. T304 material is stocked to ASTM-A908 specifications.
Design assistance
Eagle offers a helpful lab kit featuring a large assortment of T304 series stainless steel hypodermic tubing that is well suited for evaluation, prototyping, and testing. Customers that find it helpful are those wanting to experiment with a variety of sizes before placing production orders.
The lab kit includes 90 pieces of 40-inch-long hypodermic tubing in a full range of sizes from 3 gauge to 33 gauge, as well as some custom sizes — all with a variety of wall thicknesses. The kit also contains a helpful reorder form for production quantities of required sizes.
Hypotubing comes in standard 10-foot lengths. Eagle cuts orders to shorter lengths as required.
When considering your design needs for stainless steel tubing, you call a manufacturer. You talk with an expert who’s knowledgeable. At the same time, you feel overwhelmed by all of the questions. No worries. Eagle’s top 10 guidelines will give you the knowledge and confidence you need before requesting a quote for stainless products.
1. WHICH ALLOY? A series of alloys you’ll want to know about fall under the broad designation of “stainless steel.” These include 300 series austenitic, 400 series martensitic, 400 series ferritic, precipitation hardening, and duplex grades. The higher alloys in 300s and precipitation hardening series resist chemical corrosion and are the most popular and available alloys. The most common are T304, T304L, T316, and T316L. These are stocked in most standard fractional and hypodermic sizes.
2. WHAT TEMPER OR HARDNESS? You will need to specify the temper of your stainless steel. Hardness often is used as a surrogate measure for strength because it is easier to measure. Temper is specified by description, annealed to full hard, or mechanical properties such as hardness, tensile strength, yield strength, or elongation. For example, full hard #3 temper is common for hypodermic-grade tubing made from T304 and T316 stainless.
I’m Blake Harrison, Sales Manager at Eagle Stainless Tube & Fabrication, and I recommend these top 10 guidelines for ordering stainless tubing. My experience spans more than 30 years in the medical and technical industries. I joined Eagle in 2014, bringing my expertise in tubing and wire fabrication, including 15 years in insert molding. I am committed to ensuring that your designs are cost-effectively manufactured to meet your requirements. Regardless of your application, you can count on Eagle’s expertise when designing and fabricating your metal project.
Looking for more detail or unsure about your requirements? I’d be happy to assist you: info@eagletube.com or 800-528-8650.
3. WELDED OR SEAMLESS? Welded tubes start as long coils of cold-rolled stainless steel strip that are rolled into tube form and drawn down to the desired diameter. Material also can be drawn over a mandrel to smooth out the weld seam in the inside of the tube. This also allows for tighter inside diameter (ID) tolerances and better concentricity. Other advantages of welded tubing are thinner wall thickness, a higher ratio between the outer diameter (OD) and wall thickness, and lower costs. Seamless tubing is made from tube hollows that are then drawn down to desired diameters. Heavy walls are more easily achieved with a seamless tubing process. Advantages of seamless tubing are higher pressure rating, superior corrosion resistance, and cleanliness. (See sidebar for more guidelines on OD and wall thickness.)
4. WHAT SPECIFICATIONS? Tubing can be made to a variety of specifications. ASTM, AMS, ASME, and ISO designations are the most popular. ASTM standards fit a series of specifications that depend on its chemical composition: Heat treatment, temperature, and physical or mechanical attributes. For example, Eagle-welded tubes with outer diameters of up to 5 inches are certified to ASTM A-249/A-269. Seamless tubes are typically made to ASTM-A213. ISO specifications are used to consistently ensure that materials, products, and processes follow specific guidelines.
5. WHAT CROSS-SECTIONAL DIMENSIONS? Most standard tubing is produced to meet exact outside diameter and wall thickness dimensions. If your application is more sensitive to inside diameter, you can special-order tubing using that dimension plus wall thickness. Some applications need tight tolerances on both inside and outside diameters, in which case the wall thickness is taken as theoretical.
6. HOW LONG? Stainless steel tubing is typically made in either 10-foot or 20-foot random lengths. However, tubing might be cut to shorter lengths for delivery purposes. Eagle Stainless also can cut and deburr tubing to 0.008 in. and longer. Depending on the tube OD and length, tolerances such as +/-0.010 in. or +/-0.005 inches can be held on small-diameter tubing applications.
7. WHAT SURFACE FINISH? Stainless steel often is chosen for its aesthetic appearance, so make sure to specify the surface finish you need. The most common is the shiny, silvery finish that manufacturers refer to as “bright.” Or you can request a “pickled” or dull finish. Polishing and centerless grinding operations can be performed as secondary processes to produce desired RMS finishes as needed. Finishes also can be added to improve functionality or for purposes of appearance. Finishes can stop corrosion, prevent decay, and improve hygiene.
8. HOW STRAIGHT? Stainless steel is typically produced in “reasonable” straight conditions. However, where straightness is critical, additional straightening operations can be performed to ensure desired requirements.
9. WHICH ONE, OVALITY, CONCENTRICIY OR ECCENTRICITY? Depending on your need, you will generally be considering these three measures. Ovality is the roundness or the difference between the maximum and minimum OD, obtained by measurement of high and low points at any one cross-section of a tube. Also, the concentricity or eccentricity is the difference between the center of the OD of the tube when compared to the center of the ID.
10. HOW CLEAN? Commercially cleaned tubes are defined as tubes that are free from drawing oils, dirt, grease, and other compounds. They are visually inspected with an unaided eye. Precision-cleaned parts can be specified to have parts visually inspected under magnification, or have a lint-free cloth or tissue passed through the ID. A light gray discoloration is not cause for rejection.
Stainless steel tubing is generally ordered to outside diameter (OD) and wall thickness, and is inventoried as Eagle Service Center Stock. Tubing has three dimensions: OD, inside diameter (ID), and wall thickness. Only two can be specified with tolerances. The third is theoretical.
If ID is the more important dimension for your project, tubing can be specially produced by our mill to ID and wall thickness, or to OD and ID dimensions. Tolerances in any tube are applicable only to two cross-sectional dimensions.
Thus, if OD and wall thickness are specified, the ID might not conform to stated tolerances. Conversely, if the ID and wall thickness are specified, the OD might not be within tolerance.
5G Technology World is EEWorldOnline’s newest site covering 5G technology, systems, infrastructure, and wireless design and development.
Get caught up on critical 5G information, check out the following articles on 5GTechnologyWorld.com:
Massive MIMO performance testing: Emulate the channel
Performing MIMO testing using real-world conditions is critical for successful 5G deployments.
www.5gtechnologyworld.com/massive-mimoperformance-testing-emulate-the-channel
5G moves into production, causes test issues
5G Technology World talks with Teradyne’s Jeorge Hurtarte, who explains components and over-the-air production test of 5G components.
www.5gtechnologyworld.com/5g-moves-intoproduction-causes-test-issues
5G is hot, keep your components and systems cool 5G’s antennas and the devices that drive them generate more heat than their LTE predecessors. That creates new cooling problems for wireless devices and systems.
www.5gtechnologyworld.com/5g-is-hot-keep-yourcomponents-and-systems-cool
IEEE 1588 adds timing performance while reducing cost and risk
GPS and GNSS have been the standards for network timing, but they have security issues. A Master clock and IEEE 1588 reduces the risk and lowers installation costs.
www.5gtechnologyworld.com/ieee-1588-adds-timingperformance-while-reducing-cost-and-risk
For additional content, go to: www.5gtechnologyworld.com
Ball splines have one or more grooves that guide balls to enable nearly friction-free linear or rotary motion.
bring more axes of motion to machinery, more designers are finding that prepackaged solutions aren’t always flexible enough to meet application requirements. This shift has caused many designers to reconsider ball splines, mostly because of their unique ability to integrate rotary and linear motion on a single shaft. This capability provides motion performance and stability advantage — giving designers more ways to compress an assembly, extend a stroke, or distribute a load … as well as new flexibility to meet modern automation demands.
Ball splines can be used in applications such as pick-andplace machines that twist and move back and forth.
Like ballscrews, ball splines provide nearly friction-free motion by restricting physical contact to tangential points of rolling balls, which are guided by ballscrew threads and the raceways within a nut. Ball splines then augment this rotary guidance by adding one or more linear grooves (also called splines) along the shaft to facilitate front-to-back movements. These grooves provide a low-friction linear path while enabling transmission torsional loads.
The result is a highly e cient mechanical drive device suitable for various axial-load transfer
and torque-transmission applications. Ball splines resist the radial displacements caused by torque loads and need small forces to achieve axial displacement of the spline member while transmitting torque. This makes them capable of high-speed operation under high torsional loads.
Integrating linear and rotational motion without a ball spline typically requires mounting separate shafts in a dual-stacked, four-bearing architecture built around Cartesian coordinates. This setup takes time to build and test, consumes a lot of space, and can require higher
High-precision ball splines are available in various sizes, nut types and finished ends. Online resources such as the Thomson Ball Spline Selector Tool can help users quickly narrow their choices for the optimal component for their application.
maintenance interaction. Ball splines enable a single-shaft solution that provides greater design flexibility and requires much less space.
Stability: Besides reducing the number of shafts needed, the spline structure adds stability. The solidness of a ball spline provides a cost-e ective way to extend a vertical stroke beyond the scope of what a robot might provide. It also enables cantilevered architectures and can add antirotational guidance.
Enhancing performance: To those compressed stable assemblies, ball splines bring the characteristic performance advantages of other
ballscrew components. The reduced friction enables higher-speed operations, less wear, longer and more predictable life expectancy, less backlash and seizure, and no stick-slip.
Twists and turns: Ball splines are especially appropriate for automation applications that humans might traditionally perform with the twist of a wrist, such as moving a test tube or opening the lid of a sample jar for a laboratory scale. High-speed pick-andplace applications are another common ball-spline use.
Robots can certainly perform many of the same tasks as ball splines and with greater freedom of movement. Still, if that freedom is not critical to the application, ball splines can o er numerous other benefi ts and eliminate the high expense of a robot.
Ball splines can provide comparable precision in a smaller footprint and move higher loads faster, with more robust mechanics and often at a lower development cost.Specification and customization
Initially, integrating rotary and linear motion resulted from mechanical and electrical engineers collaborating on a solution using two or more shafts. Today, there are various o -
Ball splines are especially appropriate for automation applications that humans might traditionally perform with the twist of a wrist, such as moving a test tube or opening a sample jar for a laboratory scale.
Realize your vision with Festo‘s approach to smart automation for electronics manufacturing. Partner with Festo today.
Industry Leadership
Superior Quality Products
Global Training & Support
• Travels range from .5” (12.5 mm) to 2” (50 mm).
• Positioning accuracies range from 0.0001” to 0.00004” per inch of travel straight line accuracy.
• Actuator mounting brackets are available in both center line and side drive configurations.
• Choose from four methods of actuation.
• Available in both Inch and Metric versions.
• Solid Models Available for all Del-Tron Models.
the-shelf ball spline options with lengths to 3,000 mm and diameters of 6 to 50 mm.
Ball splines are also quite amenable to customization. Depending on the specification, manufacturers can often tap holes, add reductions for radial bearings or coaxial holes, or make other modifications needed to integrate the ball spline unit into the machine.
When designing a solution, the ability to extend a stroke or compress a system may be the key to success. Ball splines provide this game-changing flexibility that designers may not find in a prepackaged multi-shaft assembly. More actions that once required a technician or assembler can now be automated, making those movements safer and more e cient, with better control. These automated solutions are especially relevant amidst today’s rising labor costs, labor shortages, and high absenteeism.
Machine designers should consider ball splines for any application requiring both rotary and linear motion, especially if space is at a premium and stroke, load, high speed, reliability, or durability are critical.
For those already familiar with ball splines, it may be time to revisit their use in new designs. The advances in digital technology make them easier to incorporate into integrated axes of modern systems. For engineers unfamiliar with ball splines, it’s a good idea to review design projects and see if integrating rotary and linear motion on a single shaft could provide space savings, improved cycle time, or better machine reliability. DW
The editors of Design World produce key technology content compiled in individual PDFs available for download.
Motion control systems can vary from simple, straightforward single-axis direct-drive systems with little wiring to large and complex multi-axis robotic systems with a hornet’s nest of cables. This is usually where cabling, which was an afterthought, now takes center stage. This Design Guide details cable carrier subtypes as well as the different designs into which cable carriers integrate.
DC motors are motion components that take electrical power in the form of direct current and convert it into mechanical rotation. In this Design Guide, the editors of Design World detail the most common dc motor types as well common ways to quantify their output during the design-engineering process.
Linear motors are one of the latest motion components to go mainstream for OEMs building moving machinery requiring high precision. This exclusive Design Guide reviews the functions and variations of linear motors for precision automation as well as their connectivity and configuration requirements.
Find these and additional guides in our DESIGN GUIDE LIBRARY, bookmark this site as guides are added on an ongoing basis!
designworldonline.com/design-guide-library
For some features, PCbased scopes sport higher performance than similar benchtop instruments.
An example of a high-performance PC-based scope is the PicoScope 6000E series. It sports -3 dB bandwidths of up to 1 GHz and a capture memory (shared between active channels) of up to 2 GS. Some models also handle a maximum single capture duration of up to 1.6 sec at the max sampling rate.
It used to be the case that only a few kinds of relatively simple instruments were based on PCs. Now, several categories of lab-grade instrumentation take the PC approach, including oscilloscopes. PCbased instruments o er a number of benefits including lower cost, portability, and flexibility, in terms of being able to perform a number of di erent functions.
As an example, consider the debugging and validation of electronic systems. Such tasks call for versatile instruments with wide-ranging functions and easy programmability. An engineer working on high-speed logic signals one day might be called upon to run a long-duration soak test the following day and check for immunity to power harmonics the next.
PC-based test instruments can address such needs. Instrument acquisition hardware sits in a compact external enclosure that connects to the host computer, typically with a USB 2.0 or 3.0 connection. The enclosure hosts connectors for the input and output signals to and from the deviceunder-test (DUT) and a separate power connection, where required.
This sort of economical PC-based instrumentation is possible thanks to advanced FPGA technology that controls the channel settings, signal conditioning, triggering, on-board memory management and communication with the host PC. The FPGA does the heavy-duty processing of test data acquisition and/or signal generation. Data flowing on the USB interface is limited to commands, responses and composite information required for
processing and display of graphical or numerical test data.
Separation of the acquisition hardware from the analysis and display platform allows products such as those from Pico Technology to benefit from improvements to PC and display technology as it becomes available. For instance, Pico instrument software works with any Windows 10 or 11 machine and other industry standard platforms. Most Pico software packages can take advantage of high-definition and UHD displays for presentation of waveforms, measurements and analysis results.
It might be useful to review features of widely available PC-based test instruments. For example, PicoScope oscilloscopes feature real-time bandwidths from 10 MHz to 1 GHz and a choice of two, four or eight analog channels, and up to 16 digital channels on the MSO models. There are flexible and high-resolution models too, with up to 16 bits for precision analog measurements. Most models have an integrated function generator/
Serial decoding is a standard feature of PicoScope instruments. The decoded data can be displayed in graph mode as depicted here, in tabular format, or in both formats simultaneously. Graph format shows decoded data in a bus format, aligned with the analog waveform, on a common time axis, with error frames marked in red. Frames can be zoomed and correlated with acquired analog channels to investigate timing errors or other signal integrity issues that are a root cause of data errors.
arbitrary waveform generator (AWG). The next generation PicoScope 7 user interface, with versions for Windows, Linux & Mac operating systems, delivers six instrument functions: oscilloscope, spectrum analyzer, serial protocol analyzer (30 serial decoder/analyzers included, with more in development), logic analyzer (on MSO models), and a function/sweep generator.
Most PicoScope models include a signal generator that can deliver sine, square, triangle, ramp, sin(x)/x, Gaussian, half sine, white noise and PRBS waveforms. This is complemented with a sweep function that enables device testing over a predefined frequency range. This sweeping can be helpful in testing filters and operational amplifiers over their specified operating range. More complex devices need testing with real-world waveforms, which is where an AWG comes in handy. Many PicoScopes include an AWG, which can now be fully controlled from within the PicoScope 7 user interface.
Real-world waveforms captured with a PicoScope can be loaded into the AWG memory and replayed as needed for device testing and performance verification. For an example of where
this capability can be useful, consider a staged car crash with sensors set to record the impact characteristics. It’s an expensive test, and something that you would only want to do once. But the ability to save the waveforms allows them to be subsequently replayed as often as needed with the PicoScope AWG for development of safety-related systems. Furthermore, the original waveform can be modified with the AWG editor to stress the DUT and see how it behaves at the extremes of its specification, and with ‘known good’ and ‘known bad’ signals for go/no-go testing.
Also of note is that the decoding of serial protocols is included in PicoScope as standard. The decoded data can be displayed in graphs or tables or in both of these ways simultaneously. Serial protocols have become particularly important in vehicles because the growing number of vehicle convenience and comfort features have led to the demand for lower-cost wiring alternatives.
LIN (Local Interconnect Network) was developed to provide a common sensor/actuator bus standard. Initially introduced in 2000 as an inexpensive
Economical PC-based instrumentation is possible thanks to advanced FPGA technology that controls the channel settings, signal conditioning, triggering, on-board memory management and communication with the host PC.
serial communication bus, the latest version (2.2A) is now standardized as ISO 17987. LIN uses a simple and low-cost single wire physical layer implementation based on ISO 9141 (as used by the K-line onboard diagnostic standard). This single-wire implementation does make LIN more susceptible to EMC than two-wire buses, which in turn limits the data rate to 20 kb/sec and the recommended number of nodes to 16.
Although serial buses like LIN offer several advantages, they also present difficulties during troubleshooting and debugging because data transmits in packets or frames that must be decoded before the designer can make sense of the information flow. Manually decoding (or “bit counting”) streams of binary data is error prone and time-consuming.
PicoScope includes decoding and analysis of widely used serial standards to help engineers see what is happening in their design to identify programming and timing errors and check for other signal integrity issues. Timing analysis tools help to show performance of each design element, enabling the engineer to identify those parts of the design that need to be improved to optimize overall system performance. Frames can be zoomed and correlated with acquired analog channels to investigate timing errors or other signal integrity issues that are root cause of data errors.
The PicoScope can decode a number of serial protocols including common ones such as CAN, Ethernet 10Base-T and 100Base-TX, and SPI and UART (RS-232/RS-422/RS-485), and USB protocol data as standard.
Data can be displayed in hex, binary, ASCII or decimal formats. To help make decoded data even easier to read PicoScope enables use of a link file so that, for example, address hex 03DF can be displayed as “Oil Temperature,” or whatever the parameter means. A filter function displays only those packets that match userdefined conditions. Statistics displays detail timing and voltage information on each packet, which helps to determine safe margins, noise immunity, and design reliability over extended operating periods. DW
The demand for a quiet electric motor — one that runs with very little noise and vibration — was the primary application that drove engineers to develop and market low-noise ball bearings. Accordingly, the manufacturing equipment industry coined the term electric motor quality (EMQ) to identify this special class of low-noise bearings. Today, a wide range of applications require the use of EMQ bearings.
Edited by Mike Santora • Managing EditorNoise in a rotating bearing is the audible component of vibration and a function of rotational speed. The greater the vibration, the shorter the bearing’s lifespan — plus, excessive vibration can damage the motor or machinery.
Vibration is caused by several factors, including rough or damaged raceway and ball surfaces, poor geometric tolerances (roundness, concentricity, runout, or parallelism), contamination, improper lubrication, incorrect radial play, and improper shaft and housing fits.
An EMQ bearing is manufactured by superfinishing the rolling contact surfaces to a mirror-like finish, which provides smooth rotation. Equally important is maintaining tight control of the geometric tolerances of the bearing components.
Particle contamination in a bearing adds to the noise level — engineers can prevent this, however, by using seals to prevent the ingress of contaminants and taking care to use only “clean” lubricants that have been filtered to remove large solid particles. Specifying the proper radial clearance is also vital; it should be as close to zero as possible without causing the bearing to bind up during rotation. If the radial clearance is too loose, it results in excessive noise-causing vibration.
As with any type of bearing, the lifespan of EMQ bearings also depends on external factors. Great care should be taken during handling and mounting because impact forces from dropping a bearing or hitting it during installation can create small dents in the raceways, called brinelling. Brinelling creates excessive vibration during rotation, eventually leading to bearing failure.
Shaft and housing roundness can also contribute to noise, especially in smaller and thin-section bearings. Poor roundness can distort the bearing rings upon installation, which prevents smooth rotation and leads to the generation of noise.
Manufacturers of EMQ bearings typically perform 100% noise inspection on the bearings using a special piece of equipment called the Anderon meter (or a similar instrument). This device measures the vibration velocity (displacement x
frequency) of a rotating bearing in Anderon units (equivalent to 7.5 microns per second) across three frequency bands: low, medium, and high. The higher the vibration velocity, the noisier the bearing.
Lastly, it’s important to stress that EMQ standards are not uniform between bearing manufacturers — except those located in China, where there is a national standard. Despite this lack of uniformity, rest assured that an EMQ rating from a manufacturer (based on su cient empirical evidence) indicates the bearing is suitable for use in electric motors. DW
AST
Bearingswww.astbearings.com
As with any type of bearing, the lifespan of EMQ bearings also depends on external factors. Great care should be taken during handling and mounting.
Check out the DESIGN WORLD WEBINAR SERIES where manufacturers share atheir experiences and expertise to help design engineers better understand technology, product related issues and challenges.
WEBINAR
FOR UPCOMING AND ON-DEMAND WEBINARS, GO TO: www.designworldonline.com/design-world-online-events-and-webinars
When Savannah Smith rolled along the Halloween parade route in Salem, Mass., this year, many stopped to admire her costume. She sat in a perfect replica of the chair used in The Voice, the television show where four coaches eliminate or embrace auditioning singers. Savannah’s chair included the big red button, which she pressed frequently.
Few knew the story behind the rolling chair was a result of a months-long collaboration between Dassault Systèmes and Magic Wheelchair, a nonprofit that builds costumes for kids who use wheelchairs.
Savannah has Ogden Syndrome, a rare neurodevelopment disorder that a ects fewer than 100 people in the world. She’s used a wheelchair for many years. At Halloween, she wore a costume she and her wheelchair could accommodate. It certainly was never the other way around; her costume accommodating her wheelchair. Until this year.
This year’s costume was a challenge to build, says Chinloo Lama, user experience design director at Dassault Systèmes.
“It’s not a traditional vehicle or a fantastical thing. It’s more like a movie prop with very specific style requirements; lights on it and everything” Lama says. “It’s not something more of our mechanical engineers knew how to do.”
Sixteen people at SolidWorks worked nights at weekends at the company’s Waltham, Mass., 3-D Experience Lab on various costume builds. In years past, they constructed a monster truck, a motorcycle, and—to diversify their projects and to test their computer-aided design software on nonvehicle projects, a large castle pulled by two large cats.
But they did it, 16 people with various roles at SolidWorks working nights at weekends at home and at the company’s Waltham, Mass., 3-D Experience Lab on their fourth costume build. They’d taken a year o during COVID but were back strong. Every year brought new and unforeseen challenges, but crew members knew their stu ; they’d already constructed a monster truck, a motorcycle, and—to diversify their projects and to test their computer-aided design software on nonvehicle projects, a large castle pulled by two large cats.
For 2022, Savannah’s family chose The Voice chair because she and her family watch the show together. The chair is particularly important in the show because coaches sit with their back to auditioning singers. If they like what they’re hearing, they rotate their chairs to mark their approval. Some singers get the coveted “four rotations;” others get none.
To rotate their chair, the coaches press a red button that spins the chair around to face the stage.
The project collaboration began five years ago, when Lama met Dan Vogel, Magic Wheelchair’s regional director, at a Maker Faire in Queens, N.Y. Vogel was there to “find people with special equipment to help make our costumes,” he says. Lama told him SolidWorks would likely grant his organization a free CAD license.
After a short time, they sought each other out again, both with the same idea.
“I learned about Magic Wheelchair and what they did, and I thought a 3D CAD project like ours might be useful,” Lama says.
“As I was about to leave, I thought, well maybe I should ask SolidWorks if they would make a magic wheelchair. They’re the perfect company,” Vogel says.
Lama rounded up the first team of volunteers. Many of them have enrolled again on subsequent builds.
Team members do the 3D modeling in SolidWorks CAD and prints and machines parts in the lab, which houses 3D printers and CNC mills. Though engineers make up the bulk of team members, volunteers from other departments—like marketing and administration— join in. One particular member, who had cosplay experience brought a wealth of knowledge about costume design and creation.
This year, they needed people with electronics knowhow to create the lighted button. This year’s team began meeting in July.
“I would say all the digital and hand sketches took a month or so because we wanted to get it right before we cut any foam or made anything physically,” Lama said. “We had a month of discussion and design and backand-forth about what we wanted to do.”
Once they had the basic design in hand, engineers spent a few weeks creating a 3D CAD model. Then the cutting and the printing began in earnest.
Though they worked on separate parts at different times, designers needed to work together because the chair’s base, frame, chair, and the pedestal in front needed to fit together, Lama says.
The process definitely wasn’t linear, says Lama, who helped work on the chair’s base.
“It was like ‘well, the base is done, let’s start fabricating,’” she says. “Others were finishing up their digital models while we were cutting the wood and foam. There was a cascade of tasks.”
Almost half the chair parts were 3D printed. A track that runs around the arms and the top of the chair was printed in segments and magnetically connected. So was section along the edge of the chair that housed lights. The team also printed parts of two cup holders attached to the chair. The cup holders don’t sit in the same place as on The Voice chair, but placement was more convenient for Savannah, Lama said.
The red button on the wheelchair costume acted as a very special communication tool that played snippets of music when pressed. In school, Savannah is learning to communicate by pressing large buttons that play prerecorded messages when pressed. It said “I choose you,” Happy Halloween,” and “Team Savannah.”
The SolidWorks team incorporated that tool into her costume. Lights change color and play a musical tune and plays a short message, giving Savannah more control over what she expresses.
“We can be contestants and she can judge us harshly,” Lama says.
“Savannah has limited vision, so to be able to locate the button was a task we had to address with the lights,” she adds. “Also, because her mobility is limited, we had to address reach. We wanted to ensure nothing around her arm would impede her movement.
“We designed quite a few things to accommodate what she’s learning in school,” Lama says.
The team designed a light cylinder that held the button so Savannah could see it from every angle. The cylinder also put the button in her arm’s reach without being in the way.
The big reveal
Long associated with witches, Salem, Mass., hosts a monthlong celebration of Halloween, Salem Haunted Happening. The event had been shuttered for two years due to COVID, so—in addition to being the 40th anniversary of the event—2022 was a big deal. The parade on October 25 helped cap the event. Its theme this year was “who’s your hero?” which fit nicely with The Voice chair.
The Smith family saw the costume for the first time the morning before the parade. The “reveal” took place in a nearby park. They were overjoyed.
“They really knocked this one out of the park. I don’t know how they do all this,” Mark Curran, Savannah’s dad, told Boston television station WCVB.
Toward the end of the costumemaking, the volunteers realized the caster wheels on the platform to which the wheelchair was secured were small enough to get caught in the cobblestones on the parade route.
“They’re great for ambiance, terrible for the costume,” Lama says.
The team had done a dry run two weeks before the parade, using only the wheeled base with the wheelchair secured to the top to avoid Savannah’s
family seeing the costume.
The team switched to larger wheels—“almost like on a wheelbarrow”—that would still have a low profile, to absorb the impact of the bumps. Here again, it helped to have engineers on the team who knew exactly what to it, Lama says.
“They knew what we needed and banged it out and got it done,” she adds.
The parade made the four months of work all worthwhile, Lama says.
“There was definitely tears and excitement, and the best part was seeing Savannah so happy and pushing that button constantly,” Lama says.
She felt that people who would otherwise feel awkward approaching a wheelchair because they might not know what to say, came up freely with words of congratulations and praise. Savannah herself seemed comfortable gesturing where she wanted to go and what she approved of, Lama says.
Students on a local high school cross country team pulled the costume along the parade route.
Savannah received oohhs and aahhs from everyone watching.
“I was in tears because it was that kind of moment for me,” Lacey Smith, Savannah’s mom, says.
So, will the SolidWorks Magic Wheelchair team gather again next year? Very likely, Lama says.
“It’s hard to think about next year when you’re exhausted in the moment,” she says. “But then a few days later you remember how magical and how worth it the build is.” DW
Modern manufacturing relies on critical connections made via strong electroplating, as more and more devices are connected to provide instant access to information and data. However, any electrical device’s e ectiveness and reliability depends highly upon the quality of the connections and specifically the plating used on the connector or contacts. Proper electrodeposition is key to ensuring a device performs reliably whereas improper plating can negatively a ect performance, utility, and durability of the electrical device.
Gold and silver are two common electroplating processes that produce highly reliable and conductive connections for contacts and connectors. However, they both have their own unique advantages and disadvantages. Both gold and silver are highly conductive and corrosion resistant; however, silver will form a sulfide compound (tarnish) and gold can be a costly option.
Benefits of gold-plated connectors
Gold is a highly noble (unreactive) metal that can enhance the performance of connectors in a variety of electrical applications. The benefits of using gold-plating include:
• Superior corrosion resistance — In comparison with other metals, gold’s resistance to oxidation or corrosion is extremely high. In situations where the contacts of a connector are likely to be exposed to corrosive substances or conditions, gold plating can serve as an e ective barrier from oxidation and corrosion. As a result, gold-plated connectors are an excellent choice for more corrosive applications where the connector or contact may
Learn the proper electrodeposition for contacts and connectors to ensure reliability in your electrical devices.
be exposed. Applications include high humidity environments or applications with frequent thermal cycling as well as exposure to corrosive salts or acids. In the latter application, a heavier gold deposit or even duplex gold deposit may be required to ensure there is su cient gold to eliminate any porosity in the deposit thereby forming an e ective barrier to corrosion.
• High electrical conductivity — Besides copper and silver, gold is the third most conductive metal in the world. However, gold does not produce any oxides or other compounds, so it maintains its high conductivity even at elevated temperatures or when exposed to corrosive environments. Its high/ consistent conductivity ensures stable current flow even at very low voltages making gold an excellent choice for micro-electronic applications where milli-volts transmit milli-amps.
• Enhanced durability — Electroplated gold can be alloyed with small amounts of nickel or cobalt to increase the hardness from that of pure gold (< 90 Knoop) to as high as 200 Knoop. This hardened gold deposit is commonly
referred to as hard gold. When plated to a su cient thickness (> 50 uin.) over an electrolytic or electroless nickel base, hard gold can provide a durable coating for repeated connection cycles. Hard gold is not prone to fretting or galling due to its natural lubricity.
• Ductility — Because gold is such a malleable metal, it’s suitable for flexible connections and springs. Gold’s ductility makes it more likely that plating will hold up to multiple cycles of contact. However, goldplated electrical connectors or springs require a suitable underplate material to guarantee the finish meets the design requirements. It is generally recommended that an engineered nickel such as a sulfamate nickel be used as an underplate to gold when plating a flexible contact or spring.
• Solderable deposit — Gold plating is an excellent finish for forming reliable solder joints and will consistently and evenly wet with using just a mild rosin flux without acid activation. Gold can be plated on nearly any substrate including stainless steel terminals or connectors to allow for subsequent
joining through soldering. Generally, only a thin deposit of soft gold of 0.00001 in. per side is required to form a reliable solderable gold contact but heavier gold deposits can be soldered as well. When soldering to a gold electrodeposit, the gold plating di uses into the solder joint through a mechanism called solid-state di usion. Because of this phenomenon, care should be taken to not exceed more than 3% by weight gold in the solder joint as this can cause embrittlement within the joint itself. As a general rule, deposits of < 0.00005 in. per side will result in less than 3% by weight gold in the solder joint.
• Non-magnetic — As a final point, gold is not magnetic. This is advantageous in scenarios where electromagnetic fields can create interference. For instance, gold plating may be suitable for connectors used in medical equipment like Magnetic Resonance Imaging (MRI) scanners.
Like gold, silver is a precious metal that provides a very conductive surface while forming an e ective barrier to corrosion. Its primary advantage is cost — it is about
1/100 the cost of gold which allows for a wider range of use and plating at higher thicknesses than gold. The primary disadvantage of silver is that it is a semi-precious metal and forms sulfur compounds such as silver sulfide or tarnish which can a ect the conductivity of the silver electrodeposit over time. Its advantages include:
• Highest electrical and thermal conductivity — Because of its high conductivity and lower cost, silver is perhaps the ideal precious metal for applications where high power transfer of electricity is a design requirement. Examples include plating of current exchange bodies, fuse cutouts, stabs, terminals bus bars or other high-power connectors. Because of the lower cost, plating of larger copper or aluminum conductors with silver is not cost prohibitive and provides a very reliable precious metal coating that resists oxidation and produces low contact resistance. Aside from electricity, silver is also an excellent conductor of heat, which allows connections that transfer large amounts of power to naturally regulate thermal hot spots preventing oxidation of the substrate materials.
• Protection against corrosion — Like gold, silver is a precious metal that can form an e ective barrier to corrosion. Because of its lower cost, silver can commonly be plated to thicknesses exceeding 0.001 in. per side forming a very pore-free precious metal barrier to corrosion. Silver is commonly plated over an electrolytic or electroless nickel barrier further increasing the overall corrosion protection. When plated over copper or aluminum conductors, silver forms an e ective barrier to prevent the substrate materials from forming compounds or oxides. This eliminates increase in contact resistance or thermal hot spots in a conductor over time.
• Superior lubricity — Silver is a natural metallic lubricant which provides outstanding lubricity even at extreme temperatures. It is an excellent choice for applications such as high temperature threaded or sliding contacts
Harwin’s connector products are proven to perform in extreme conditions, with shock, vibration and temperature range rigorously tested.
n ‘Inside the box’ connectivity
n High-Rel connectors
n Industrial board-to-board
n EMC shielding solutions
where galling may be a design concern. Silver is commonly used for plating of stainless steel and other high temperature alloys to preventing seizing of moving or threaded parts within turbine engines or turbo chargers where temperatures can exceed 1250°F.
Silver provides outstanding sliding lubricity on high contact pressure switches or contacts including fuse pad or stab connectors or high pressure socket connectors. The use of a lubricous nickel underplate such as electroless nickel can further enhance the lubricity and wear properties of silver electroplating on a connector or contact.
Gold versus silver: what are the di erences?
Gold and silver are among the two most frequently used precious metals for connectors and contacts in various sectors. Here are a few major di erences between gold and silver electroplating.
• Cost: gold plating disadvantage
Global industrial demand, political and economic uncertainty, and currency devaluation all play a role in driving up the price of gold. Many countries and people turn to gold in periods of economic instability because of its globally accepted value as a currency alternative. However, with the IoT, gold is now sought for more industrial reasons than merely as an investment or as decorative jewelry: gold is truly an essential metal in the production of modern electrical and electronic devices.
Increasing gold prices can significantly a ect the manufacture of gold-plated components, especially for applications which use heavy gold deposits. Even though no other material can match all the properties of gold, silver has many similar properties at a fraction of the cost. Silver can be plated more heavily and at a lower cost with deposit that yields many similar properties. However, the formation of
sulfide compounds or silver tarnish, is one of the limiting factors for silver in applications very sensitive to increases in contact resistance.
• Silver tarnish: silver plating disadvantage — Silver does not form oxides or compounds with oxygen under normal conditions; however, silver plating does form various sulfur compounds such as silver sulfide. Although silver sulfide compounds are relatively conductive, they do increase the contact resistance of the silver plating over that of pure silver alone. In many switching applications, any silver tarnish is e ectively wiped from the surface within the sliding contact zone. However, in static applications, silver sulfide or tarnish can increase the contact resistance enough to change the signal path for very low voltage applications. Various antitarnish inhibitors such as Enthone’s Evabrite products or Technic’s Tarniban products are available; however, all of these anti-tarnish compounds do add an organic or metallic film on the surface that alters the properties of the silver electrodeposit away from that of pure silver.
In contrast to silver, gold does not form sulfide compounds or tarnish under any normal condition. That makes gold a more viable option for
lower voltage signal transmission applications where minor changes in contact resistance can impact product performance. Critical applications such as life-safety sensors or applications for autonomous vehicles require extremely reliable real-time signal transmission that only gold plating can provide.
Selecting the appropriate metal plating for connectors and contacts is a key part of manufacturing a reliable product. The type of electrodeposit used can impact the product’s quality, performance, longevity, and cost. Gold and silver are both high-quality precious metal deposits, but they have di erent unique benefits and drawbacks that should be considered prior to specifying a specific finish. DW
This article is condensed from a larger article, which can be found at advancedplatingtech.com/blog/.
Advanced Plating Technologies advancedplatingtech.com
Important decisions loom for manufacturers
making
more eco-friendly.
Energy chains from igus are reliably used in many applications across the world, from beverage vending machines to steel mills.
Nowadays, sustainability permeates nearly every manufacturing decision. It’s not enough to just make a product anymore. Businesses are tasked with ensuring they comply with green energy initiatives, and phrases such as “circular economy” and “eco-friendly” dominate the industry lexicon. To adapt a phrase, the message seems clear: Go Green or Go Home.
While commonplace now, it’s important to realize that this focus on sustainability as a worldwide goal is still very much in its infancy. The first “Earth Summit” hosted by the United Nations occurred in 1992, with the objective to produce a “broad agenda and a new blueprint for international action on environment and development issues,” according to the UN. While not the first international conference to address environmental issues, the 1992 Earth Summit is considered by many to be the turning point in sustainability progress. A follow-up meeting was held in 2012.
Sustainability objectives have crystallized during modern manufacturing leaders’ rise through the labor ranks, and now they are embracing the worldwide trend to meet the challenges ahead.
Progress is being made and examples abound. Earlier this year, igus, a German manufacturer of high-performance motion plastics, unveiled the world’s first urban bike made from recycled plastic. The company, which runs its North American operations out of Providence, R.I., also unveiled the first energy chain made entirely of recycled material in June.
Cables have proven much harder to recycle. There are ways, however, in which manufacturers can improve their sustainability objectives by evaluating their cable selection.
Cables perform many different functions: uses include power, data, control, movement and motor feedback. They are used in robots, cleanrooms, energy chains, and manufacturing equipment. Statistics indicate the wire and cable market will reach $15.1 billion in the United States in 2022, a year-overyear increase of 6%.
The best way to enhance sustainability is to have a clear objective on how the cable supports the process. Cables start at less than $1 per foot, but a more expensive cable with added functionality might be a better choice. When it comes to cables for moving applications, such as on industrial machinery and equipment, this is certainly the case.
“We have had customers realize this and put a heavy emphasis on proper planning as well as installation,” said Tim Marran, igus’ Product Manager for chainflex cables. “This had led us to even offering a service where we will have certified technicians on site to do the cable and e-chain (cable carrier) installation work. That gives the customer peace of mind knowing that cable installation techniques, like cable placement in the neutral axis of an e-chain
igus also o ers readychains, which are pre-assembled and eliminate assembly time and reduce costs.
and strain relief, can be done properly.”
A range of mistakes are frequently made with cable installation for moving applications, including lack of interior separation in energy chains, uneven weight distribution, improper strain relief and not installing cables along the neutral axis.
“Simple considerations in the beginning of the process can prevent issues such as loss of continuity, insulation damage, mechanical deformation or electromagnetic interference,’’ Marran said.
E ciency begins by selecting the right cables and installing them properly. Replacing cables every six months or year is highly ine cient. Manufacturers who design products and know precisely what they want the cable to achieve are in the best position to improve sustainability.
“It’s important to be transparent about the best way to reach a long lifetime of the cable selected,’’ said Marran, whose company o ers a 36-month guarantee on its cables. “We have the testing and data to back it up. Every year we do research and development, and our testing process backs up our guarantee.”
igus has been one of the leaders in adopting sustainable objectives. Besides designing a bike from recycled plastic and recycling energy chains, the company has stated its intentions to have all of its buildings and production be CO2 neutral by
2025. It reduced its CO2 emissions by 31% in 2021.
For cable design, the company has been seeking to make cables that are used in energy chain systems smaller. “This will help save space and weight inside the cable carrier system,’’ Marran said. “That will help with machine e ciency.”
Marran emphasized, however, that in some applications, larger cables might be more e cient. “This is where certain approvals or electrical characteristics would be beneficial to cut down on the number of parts and the amount of cable produced,’’ Marran said. “For instance, if insulation material increase would help gain the proper approval for 1,000 V instead of 600 V, the overall cable outside diameter might be a bit larger. But that part number could be used in many more applications, considering it would be electrically applicable in more areas.”
He cited the example of an automated guided vehicle application that improved e ciency by simply swapping cables. “We were able to increase the lifetime of their cable by 10x, simply by selecting the cable for the specific motion they were seeing,’’ Marran said.
One method in which manufacturers can improve e ciency — both with cable performance and plant operation — is through recently developed predictive maintenance systems. “Smart Plastics,” as igus calls it, allows customers to predict the lifetime of a product. The benefit is that manufacturers can see when equipment is reaching the end of its
igus o ≠ers more than 950 cable types and have a guaranteed service life of 36 months.
AEROSPACE
AUTOMOTIVE COMMUNICATION INDUSTRIAL & ROBOTICS DEFENSE TEST & MEASUREMENTS
LEMO High-Speed Connectors
Scan to learn more about LEMO® Connectors
• Absolute signal integrity
• SPE speed up to 1 Gb/s
• USB 3.1 speed up to 10 Gb/s
• 360° screening for Full EMC shielding
• Push-Pull latching mechanism
• Robust, secure, compact integrations
• IP50, IP66, and IP68
• Up to 5000 mating cycles
• Temperature range -55 °C to 250 °C
• Up to 12 alignment keyways
useful life. By replacing the component before it breaks, predictive maintenance also eliminates unplanned downtime.
“Smart Plastics isn’t just for our cables, but it also extends to e-chain parts, e-chain assemblies and other aspects as well,’’ Marran said. “I think it will be something more and more manufacturers focus on in the next 10 years.”
The company also provides a lifetime calculator and suggests other cables that might last even longer. “It might save the customer money if they aren’t looking for millions and millions of flex cycles,’’ Marran said.
For sustainability goals, it’s essential that manufacturers maximize e ciency because cables can be hard to recycle. There are many di erent cable layers — copper conductors, insulation, inner jacketing, shielding, outer jacketing and center strain relieving elements — that complicate the recycling process.
“Cable recycling is more complicated than with energy chains,’’ Marran said. “It doesn’t mean it’s impossible. We have been recycling cuts of cable for many years now.”
The company o ers a 36-month guarantee and customers can order customized lengths. Whether it’s 1, 100, 10,000 ft or anything in between, customers can get the right cable with proper mechanical benefits.
“We already optimize the design of the cable, and with seven di erent jacket materials we can customize the cable part number solution to the specific application,’’ Marran said. “Customers aren’t wasting money on a cable they don’t need the mechanical benefits from but aren’t paying the smallest amount of money for a cable that won’t work and will require frequent replacement.”
The company did take one of the first steps this year in recycling initiatives with its first e-chain made from entirely recycled material.
Igus has been collecting used energy chains from customers since 2019, so
HELUKABEL is a global cable system solutions provider specializing in the production of cables, wires, cable assemblies, robotic dress packs, and drag chains. Our electrical solutions consistently and reliably provide power and transmit data for our customer’s applications across a vast array of automation-focused industries.
With a comprehensive product portfolio of more than 33,000 stock items, and the capabilities to design and build custom solutions, HELUKABEL is your one-stop source for electrical connection technology.
they do not end up in industrial waste. More than 32 tons of material have been collected across 13 countries since the program began.
“The focus should not be only on first use of products, but also the reuse of raw materials,’’ said Jörg Ottersbach, head of igus’ e-chains business unit. “We see a lot of ‘cradle-to-cradle’ potential and strive to reprocess as many raw materials and discarded products as possible so that precious resources are not wasted but used wisely for as long as possible.”
The challenge to develop sustainably friendly cables will become even more critical in the years ahead. Marran said increasing automation and a focus on reducing downtime will drive growth in the cable industry.
“With the pandemic we have faced in the last few years, more and more manufacturers are starting to look at di erent processes that can be automated,’’ Marran said. “We’ve also seen an increased focus on downtime costs. With the world getting more automated, it is also looking at becoming more and more e cient.”
With its written guarantee, lifetime calculator and wide range of cables, igus is poised to embrace the challenges of improving sustainability. The company started developing its cable products at nearly the same time as the 1992 UN meeting in Brazil. That has put them ahead of other companies that are now racing to catch up.
Smart plastics for energy chains and chainflex cables include sensor systems that detect breakage, monitor push/pull forces, cable tension and the electrical resistance of conductors. It also o ers monitoring to check for unexpected operational states, such as a broken cable carrier link, that can dramatically reduce unplanned downtime.
“We’re continually testing and adding new cables to the automation market,’’ Marran said. “Not many suppliers pour as much time, e ort and energy into research, developing and testing of the cables to ensure they are the best cables for moving applications.”
Thomas Renner writes on architecture, building, engineering and other trade industry topics for publications throughout the United States. DW Igus Inc. | igus.com
In June, igus announced the world’s first cable carrier system made from recycled material.
In 2019, we were operating at a world-record revenue pace. And for seven years, we had the luxury of orchestrating a plan to educate and train our people without compromising production. Of course, COVID disrupted all that, and we didn’t want to fall backward. We still wanted to educate our people, but we didn’t want to put them at risk.
As we iterated our COVID protocols and best practices, we researched the question: What industry has the most to lose if it can’t open or operate? NFL football was a big one. The NFL can withstand a season without fans in the seats because of its television revenue. But what happens when it can’t field a team? How do managers keep the team safe in close quarters and have enough players to maintain revenue?
We watched the NFL intently and drilled in further by analyzing casinos. We discovered that the Hard Rock Casino hired a consulting group called the Global Biorisk Advisory Council (GBAC). This group provided detailed training on how to prevent and reduce spread, protect people, assess airflow, and how many times a day surfaces must be wiped down — all the factors for operating during COVID. So, I sent five of my young operators
to become GBAC warriors, as they’re called. We trained them in transmission, prevention, and identification, wiped down lights, knobs — any surface that would be touched — at least four times a day, and sprayed and disinfected all buildings at least twice a week.
Meanwhile, we learned that Case Western Reserve University was using robots we’ve been experimenting with in our virtual reality (VR) program. We sat down with them and helped underwrite the cost of putting telepresence robots into the Weatherhead School of
Management so that we could train our people remotely and safely. But at the end of the day, we identified an opportunity for advanced education for people who may not be able to travel to a class, regardless of COVID.
We had such big plans for 2020, coming off a record year, a record pace, with new clients and products and on a trajectory we had been executing for years. As we look to 2023, we hope we see a little return to normalcy in the marketplace — a market reawakening.
We’re excited to see our friends at IFPE 2023. We’re a family business, as are many of our clients. And if they’re not a family business, they now understand a family business dynamic by working with us. I’ve known many of these people for more than 40 years, and some worked with my grandparents. It’s always neat when a random person walks up to the booth and tells me a story about my grandfather driving an RV through Arizona for a visit in 1971.
IFPE is an opportunity to bring everybody together and loosen up a bit. We’ve all been so tightly wound that I’m looking forward to a gigantic cocktail party with new and familiar faces.
Permco will be a 110-year-old family business at IFPE 2023. We’ve been doing this for a while and have had much time for introspection on what we want to be when we grow up. As we move forward, we take the fundamental strength of our product design and add some new gadgets
that work quieter and at higher pressures and speeds. We also have new electrical controls that people will get to see.
But we’re not only in the blood and guts of the hydraulic world — hardcore dump trucks, construction equipment, and garbage trucks. We’re also working on some sexy applications, such as windmills. People don’t necessarily equate an old hydraulic system used on dump trucks and mining machinery to a windmill, but that windmill is a gigantic gearbox that needs lubrication. And our big pumps provide lubrication circuits on those windmills. Also, commercial solar panels use hydraulics to move with the sun and position themselves at the best angles. So, we’re looking at energy and where the market’s going. We want to be part of the blood and guts. We want to be part of the sexy side. And we’re really excited to showcase all that at IFPE 2023.
Permco permco.com
coming
We had such big plans for 2020,
o a record year, a record pace, with new clients and products and on a trajectory we had been executing for years. As we look to 2023, we hope we see a little return to normalcy in the marketplace — a market reawakening.
Fluid power manufacturers got creative during COVID to embrace the “new normal,” and many brave companies saw opportunities within the uncertainty.
Permco is one such company that partitioned its attention to innovation and people development while filling backorders and managing employee safety. In 2021, Permco partnered with Case Western Reserve University in Cleveland to implement a new virtual learning program with telepresence robots. The robots serve as proxy students so employees can attend class from home and feel immersed in the experience.
But why would a hydraulic pump manufacturer branch out into the virtual reality (VR) and robotics business in the middle of a pandemic?
Like every manufacturer, Permco faced COVID-related hurdles and needed to adapt quickly to new safety standards while keeping production afloat. Management filled in for absent staff by taking calls, running machines, and doing engineering work over the phone. Everyone needed to cross-train quickly while working remotely and caring for their families. Several employees suffered COVID health complications, including a lead trainer eager to teach the next generation and secure the company’s future.
How proxy robots and haptic gloves arrived in fl uid power technician training.
Permco has trained 2,500 technicians over the past 25 years at its in-person hydraulic school. The team also developed an “under 30” plan about eight years ago to develop younger talent and place them in strategic training programs. During COVID, the company shut down inperson instruction for employees and customers and felt pressured to accelerate its talent development plan. But without their lead trainer, they needed alternatives.
“Most people don’t have the discipline to divert labor from production to a project that will provide future efficiency,” said Robby Shell, Permco’s Chief Operating Officer. “But we must lay the seeds and the groundwork for the next generation.”
During COVID, Permco wanted to send a few employees to Case’s Weatherhead School of Management to receive their Master of Business Administration (MBA) degrees. However, no one could abandon their daily responsibilities during a pandemic, and they couldn’t take classes in person.
Permco learned that Weatherhead was using alternative methods for remote instruction. Unlike signing into virtual conferencing software and using webinar-style learning, Case students could experience a live classroom with proxy robots.
The robots were positioned in classrooms where instructors moved about in front of a hybrid human-robot audience. Proxy students were immersed in the classroom and could rotate their “heads” 360° to look at other human or proxy students and participate in discussions. They could also break out into groups and physically move to different rooms without changing screens or instructor intervention.
Permco saw such robots as an opportunity to experiment with proxy learning and propel its next-generation training plans forward despite the pandemic.
As a result, the fluid power system manufacturer supplied Weatherhead with eight telepresence robots at no cost so that Permco employees and other Case students could receive immersed education remotely.
But why would a hydraulic pump manufacturer branch out into the virtual reality (VR) and robotics business in the middle of a pandemic?
“It was a huge benefit for our young people who have families and were working extremely difficult hours,” said Shell. “One Case student was pregnant and couldn’t attend classes or afford a robot, so we lent the student one of ours. We are proud to help Weatherhead accelerate their program and provide education for people all over the world without being physically present.”
Permco is a family-owned business with roots in the mining industry. It started out designing and manufacturing replacement parts and continues developing hydraulic systems and components for various applications. It consistently hires and retains bright minds and hard workers who share a passion for precision and dedication to the industry.
With the overwhelming increase in orders during COVID, Permco desperately needed technicians, but the learning curve was so steep that they couldn’t train people fast enough. Technicians need three to seven years to learn Permco’s assembly procedures, equivalent to the time doctors or Ph.D. students need to develop expertise in their fields.
Previously, standard Permco training consisted of shadowing assembly experts and learning little pieces of the process over a long period. However, during COVID, there was strict social distancing, transparent plastic sheets hanging from each workstation, and locked facilities
requiring vaccination for access. So, when the team discovered virtual training opportunities, they immediately saw the value in developing expertise in less time without a physical presence.
“The virtual program allowed us to train people by building a pump a hundred times virtually before they ever touch the physical part, which shortens the learning curve immensely,” said Shell. “With the virtual training environment, technicians already know what the gears look like, what they’re supposed to do with them, and how they fit. The VR program builds competency faster and really came into fruition as we moved to continuous improvement.”
The system Permco developed to make their pumps virtual can be used for almost any object in a specific engineering format.
For example, if a company needs to build pens, they can run the pen and parts through Permco’s software and present identical parts lying virtually on an assembly table. The VR program then guides a technician through the entire pen assembly process.
While developing the VR program, one major challenge they faced was capturing the physical feel that technicians rely on during real-life assembly. For instance, the feeling of tightness or resistance in moving parts is lost in a virtual environment.
In response, they turned to haptic technology that Kent State University’s mechatronics engineers developed. Haptic technology provides kinesthetic communication to users in a virtual environment to simulate a sense of touch. This technology is widely explored
Permco saw such robots as an opportunity to experiment with proxy learning and propel its next-generation training plans forward despite the pandemic.
for medical applications, such as inserting needles, performing surgery, and limb rehabilitating, and it’s shown to reduce time to competency. With the close tolerances in manufactured parts, Permco saw a parallel need for sensory feedback in assembly precision to shorten the learning curve. As a result, the fluid power system manufacturer decided to incorporate Kent State’s haptic glove technology into its VR training program.
The haptic glove allows a technician to open a virtual cabinet and grab a steel gear off a shelf. Before inserting the gear into a pump, the technician can physically inspect the gear’s quality by running an index finger across the surface. During real-life assembly, if the steel gear has a burr on its surface and is mated to a bronze plate, the burr will create a groove in the plate, which will cause leaks and decrease pump efficiency. The technician must feel for burrs, smooth them out, then feel again to ensure they’re removed. During VR assembly, the haptic
glove can create a burr-like sensation that the technician-in-training can detect and remove, giving employees a virtual hands-on approach to learning.
With the new VR program, Permco can offer remote training for employees and help educate young talent before they start their careers. The team currently works with junior high and high school STEM and vo-tech programs to make VR learning more available.
“When we go to job fairs or career day events at these vo-tech schools, there’s a long line in front of the Permco booth because everybody wants to put that headset on,” said Shell. “Since we’re addressing a younger demographic accustomed to gaming, we want to take virtual training further. For instance, we want to create competitions and tournaments to see who’s the best pump builder. We
even want to give our clients some friendly competition and test their knowledge by leaving out parts to see if they catch mistakes. We’re going have all kinds of fun with this technology as we go forward.”
Permco also plans to use the VR program in other business areas, such as customer service and training, maintenance, and troubleshooting. It also welcomes new opportunities to develop virtual training programs for any external organization.
“It was a big challenge for us to divert labor from production, but the VR and robotics programs spawned because of it,” said Shell. “Now, we believe that we can take individual training actions on any product that exists in digital engineering software, run it through our program, and develop training on any assembly, inspection, or process.”
Technicians rely on their sense of touch during production, so the VR program will introduce haptic gloves to simulate sensations that technicians experience in real life.
It’s no secret that hydraulic systems are the workhorses of dirty environments and gear pumps are at the back of the herd. Fluid power manufacturers know they’re not in production for the glamor, yet they’re passionate about the industry and providing the best quality for their customers.
While some industries want to reinvent the wheel just to get noticed, hydraulic pumps haven’t changed much over the years. The fundamental concepts and machines have persisted, and customers don’t seem to desire cutting-edge components just because they’re new. They’re looking for reliable products and custom solutions to specific problems.
For instance, Permco’s American Champ series is one of the most widely used dump pumps on dump trucks in the U.S. The series is hand-crafted and hand-tested in Streetsboro, Ohio, and includes different configurations
Though Permco refines its products to meet changing customer needs, it continues to produce legacy pumps that remain favorable for certain applications.
While some organizations chase industry trends in fear of obsolescence, others look intrinsically for innovation opportunities that bring the best to their customers.
for light-, medium-, and heavy-duty trucks and trailers. The tried-and-true design concept has been around for more than 50 years, and Permco continues evolving its series to meet customer needs and application requirements.
One notable development is the Gemini DG-20/RG-20, designed for dual use, such as switching a tractor from a truck to a trailer with a walking floor. With dual-purpose valves, operators can easily adjust pressure settings depending on the application.
Another product with a dual-pressure option is the MVP, which is designed for hard-to-fit class 8 automatic transmissions. With these transmissions,
Permco found that there wasn’t enough space for their existing pumps, and the pumps even interfered. In response, engineers incorporated a remotely mounted tipping valve block rotated on its side so that customers could install a smaller pump and all the parts fit better.
“We don’t expect anything to come out that makes people stop and think they’ve been doing it wrong all these years,” said Ryan Crosby, Warranty Manager at Permco. “Our designs are working, but we’re always thinking of the future and constantly brainstorming and innovating.”
Many experienced technicians start out as customers or in the field with boots on the ground. Their first-hand experience allows
Many experienced technicians start out as customers or in the field with boots on the ground. Their first-hand experience allows them to see how innovations can help or hinder applications, whether a process, procedure, or design enhancement.
them to see how innovations can help or hinder applications, whether a process, procedure, or design enhancement.
For example, roller bearings dominated pump designs thirty years ago. Mining and similar environments still use roller bearings because they can tolerate contamination. However, roller bearings have a finite life, which is unfavorable in many applications. Therefore, like many manufacturers, Permco created new pumps with bushings as an alternative solution for customers.
“With each rotation, a little bit of life is taken from the roller bearings, whereas the bushings ride on a hydrodynamic film of oil, so you don’t have that metal-to-metal contact,” said Joel Auckerman, Permco’s Engineering Manager. “You can run higher pressures with the bushings, and they provide a more durable product as long as you keep the oil clean.”
Permco builds a range of bushing pumps for small-sized applications, such as fan motors and bed hoists, and large applications, such as cranes and mobile crushers. And as solution designs increasingly require compact footprints, customers are asking for smaller components with more power. Permco’s smallest bushing pump is the 124 series, with displacements from 0.62 through 2.48 in. 3 and working pressure up to 3,500 psi.
Though the market shifted toward bushings, Permco still produces roller-bearing designs for customers with high-contamination environments. So long as customers request legacy designs, Permco will manufacture them by hand to fulfill each customer’s need.
“We’re always striving and exploring alternatives that help cut costs for our customers without compromising the quality or integrity of our products,” said Crosby. “And we’re always available for onsite evaluations to test equipment and help fine-tune solutions.”
As manufacturers such as Permco demonstrate, innovation isn’t always about reinventing the wheel but reconfiguring existing products to fit specific customer requirements. It’s about improving service, product training, and support so that customers can maintain their investments effectively and reap long-lasting benefits. It’s also about looking inward at production processes, suppliers, employee development, and management to ensure that customers receive the highest quality, cost-effective products to build their machines and systems.
However, make no mistake. The great minds of each organization are constantly tinkering with something substantial in the background. Of course, they can’t tell us what they’re working on, but their brainstorming board is always full of ideas and strategies.
“Permco is very unique to have so many bright employees with multiple years of combined experience and to be located in northeast Ohio in an area where everyone wants to work hard and love life,” said Crosby. Permco
Though the market shifted toward bushings, Permco still produces roller-bearing designs for customers with high-contamination environments. So long as customers request legacy designs, Permco will manufacture them by hand to fulfi ll each customer’s need.
Permco’s no stranger to thinking outside of the box — nor outside of the country. It started doing business in China in the 1980s with intentions that differed from other manufacturers at the time. Today, its partner facilities in the Sichuan province embody the heart and soul of Permco’s dedication to quality products for its customers and quality of life for its employees.
“My grandfather, who started this company, was a Georgia Tech mechanical engineer,” said Robby Shell, Permco’s Chief Operating Officer. “When he joined the military, he was stationed in the Pacific for part of his tour and spent time in Chengdu, the capital of China’s Sichuan province, from 1943 to 1945. When he returned to the U.S., he brought home something inside of him that created a spiritual connection between the Shell family and Chengdu’s people.”
This special connection was passed down to Shell’s father, who became an avid stamp collector specializing in stamps from China. In 1980, Shell’s father visited China for the first time to learn more about the people and economy in hopes of establishing business overseas. Over the next eight years, Permco managers traveled to various provinces and met with government leaders until they found the right province to work with.
But instead of setting up a new hydraulic pump facility, they got into the hotel business.
“When my father traveled over there in the eighties, he noticed that most of the reputable hotels didn’t have Western-style commodes, showers, bathtubs, sinks, and things like that,” said Shell. “He felt like China was a sleeping giant and that there’d be an explosion in tourism once the country opened up.”
Like all manufacturers, Permco was forced to think outside of the box during COVID to ensure consistent quality despite supply chain issues.
Shell’s father predicted that China would quickly feel pressured to upgrade its hospitality to accommodate Westernstyle preferences. And he was right.
As new hotels sprung up in the mid1980s, cultured marble was favored for bathroom surfaces, such as sinks, counters, and even wainscotted walls. Shell’s father responded by opening a plant in Huntington, West Virginia, to create cultured marble products and sell them to China’s hotels. Once the business gained competency, Shell’s father moved the plant to China so that local workers could learn the trade and start making products for their own market. He then started a bigger system with more capacity, established the business, and moved that one to China as well.
Building businesses unrelated to fluid power gave Permco time to understand the opportunities available for hydraulics. Looking back, Permco is the leading cast iron roller bearing gear manufacturer in China.
“Our philosophy is that we want to be part of that domestic economy,” said Shell. “We didn’t go there to find cheap parts and bootleg them back to the U.S. We wanted to develop the business for China’s domestic market, and if we could do some trading back and forth as well, that’d be a bonus.”
In 2008, the Sichuan province had a horrible earthquake that killed more than 87,000 people. The earthquake was so strong, it changed landscapes, created
new lakes, and swallowed old lakes into the earth. Shell’s family was a large U.S. donor to Chengdu’s relief and recovery efforts. “Some companies say they fuel your technology. Some say they drive your innovation. At Permco, we say ‘it’s personal.’ And that thread gets woven through the fabric of everything we do and makes us different,” said Shell.
Like other businesses, Permco’s challenges come from areas not under their direct control. The hydraulic pump manufacturer relies on foundries to pour cast iron, make steel, and provide parts such as bearings, nuts, bolts, gaskets, and seals. Tariffs also create hurdles and force management to think differently about supply chains and productivity. And of course, COVID revealed vulnerabilities and reinforced the importance of trusted relationships.
“In the U.S., we’re set up to build larger products for larger applications,” said Ryan Crosby, Warranty Manager at Permco. “But in conjunction with our China facilities, we can also provide compact solutions for customers who need smaller pumps. Permco’s global footprint and product availability is really a game-changer for its customers.” Permco
Partnering with 3D printing helps prosthetics developer create better products, gain workflow efficiencies, meet increasing demand, and shift to titanium 3D printing, all within in 6 months.
Point Designs is an innovator in the field of partial hand prosthetic design and provides artificial digit solutions through a combination of additive manufacturing (AM), mechanical design, and clinical care. Founded by researchers out of the Biomechatronics Development Laboratory at the University of Colorado, Point Designs needed manufacturing support when demand for its products outpaced in-house capacity.
With early access to lab resources at the University of Colorado, the company’s developers created its Point Digit solution with 3D printing in mind from the beginning.
The development team took advantage of the benefits of design for additive manufacturing (DfAM) by creating organic shapes, semi-hollow structures, and assemblies in situ. These types of features are uniquely enabled by AM and are a compelling reason for many to use the technology, enabling parts to be designed specifically for their intended function, at reduced weight, and with reduced assembly. However, achieving a successful 3D print can be tricky, especially when the final product entails detailed mechanisms that require strict tolerances. According to Point Designs CEO Levin Sliker, working with 3D Systems helped his team improve its designs to be optimized for the printing process.
The company’s team selected 3D Systems as its production partner to help solve its supply issue and advance its product development process. Through close collaboration with 3D Systems’ experts, the company changed from steel to titanium material in just six months, gaining workflow efficiencies and valuable knowledge to advance its portfolio.
3D printing offers the ability to develop custom partial hand prosthetics.
One key AM-enabled feature that Point Designs uses is a live hinge, which is printed as an assembly in situ and allows rotation for more natural movement. Sliker says the ability to print this assembly in place is an incredible benefit because the hinge components are not only small, but they are internal components. “To assemble them any other way would be difficult, if not impossible,” says Sliker. “Not only would it be time-consuming, but you’d have to keep track of some really tiny parts. Printing everything in place with a live hinge really simplifies our assembly and manufacturing.”
Despite the short timeline to product launch, the development team had some design-related challenges to overcome when it started its work with 3D Systems, in particular when it came to part orientation. They had selected a build orientation to accommodate the critical dimensions and tight tolerances of its final parts. However, this orientation was not optimized for scaled production. Together, the 3D Systems team and the development team worked together to devise a new print strategy that would enable substantially more parts to be printed in a single build while taking downstream processes into account. To avoid support scarring on critical surfaces, the two companies worked together to come up with support structures that would be easy to remove, as well as post-processing techniques to deliver the desired finish on those surfaces.
When the development team was searching for a manufacturing partner, its primary concern was capacity. By selecting 3D Systems, Sliker says it gained titanium as a
bonus. But Point Designs is not the only one benefitting. Jeff Soelberg is an end-user of the Point Digit solution and has worn both the steel and titanium versions. With a 30% reduction in weight enabled by the new material, the difference was instantly noticeable. When wearing the steel device, Soelberg said it felt as if he was carrying around a small weight: “The switch to titanium feels so much lighter and much more natural,” he shared.
Beyond weight reduction, the material and design of these devices have earned a plethora of positive feedback from end-users because they offer strength, durability, and easy washing. Recipients can take them into any environment they would take their regular fingers. Soelberg said that with practice, he
Since working with 3D Systems we have really honed our design protocol in-house. 3D Systems has brought new perspective and knowledge about optimizing our designs for high volume 3D printing, improving postprocessing methods, and increasing the yield of high precision components from each build plate.
- Levin Sliker, Co-Founder & CEO, Point
is back to doing 95% of the activities he pursued prior to his accident.
In switching materials, 3D Systems helped the development team navigate titanium-specific challenges, sharing know-how that will translate to future projects. Primary among these was assistance in designing to accommodate titanium’s shrink factor.
“By working with the 3D Systems team we’ve definitely improved our design process for existing and future products, so that the next product will be easier to implement and quicker to achieve a frozen design file ready for mass production,” said Sliker.
The titanium Point Digit 2.0 solution is printed using 3D Systems’ direct metal printing (DMP) technology and LaserForm Ti Gr23 (A) material, which features best-inclass oxygen levels (<25 ppm) and an inert printing atmosphere, ensuring exceptionally strong and accurate parts with high chemical purity and repeatability. By using the same digital data package per part, the printing machines enable scalability of production by delivering the same outcome across all DMP machines with no global off-sets.
The two companies collaborated on four products, each comprised of multiple 3D printed components
and available in multiple sizes for a total of 17 SKUs and 107 unique components. Once the development team receives the printed parts from 3D Systems, they are assembled using a combination of off-the-shelf and custom components. Following assembly, the development team delivers its products to a prosthetist, who creates a custom prosthetic socket for each recipient.
“The fact that 3D Systems’ Application Innovation Group could support us through printing using its own technology was really enabling for us,” says Sliker. “The familiarity they have with the capabilities of their machines proved allowed this partnership to flourish.”
In terms of solving its supply issue, Griffin Drye, business development specialist at Point Designs, says that since working with 3D Systems, the companies have established a reliable production cadence and Point Designs hasn’t experienced any back-ordered products since, which is a meaningful and welcomed achievement. This has been possible through the close and open communication between the two companies,
allowing each to have visibility into the other’s timelines for accurate forecasting and planning. Following the successful launch of Point Digit 2.0, a Class I medical device, Point Designs is now pursuing numerous other prosthetic offerings which will leverage 3D Systems’ expertise.
The use of 3D printing has resulted in:
• 30% weight reduction for a better end-user experience
• greater DfAM know-how based on the guidance of AM experts
• product lauch in six months due to 3D printing
• elimination of back-orders thanks to an effective production schedule.
3D Systems
www.3dsystems.com
The scale of sizes that 3D printing machines can handle is impressive, from huge wind turbine blades to parts that are small, such as two microns. John Kawola, CEO of Boston Micro Fabrication discusses the microscale side of 3D printing.
Microscale 3D printing is the concept of making parts at millimeter scale or even sub millimeter scale. It’s a technology that has been available for five, maybe even 10 years. What’s new is that this technology is being commercialized for industrial use.
Boston Micro Fabrication (BMF) uses a microscale technology that is a variant of stereolithography. It is called projection micro stereolithography, or PµSL. A Boston MIT professor, Nick Fang, developed the idea. Fang had been working on micro fabrication techniques over the years.
A lot of those micro fabrication techniques are not 3D printing. These techniques include embossing, and etching and photolithography. But for 3D printed micro parts, applications include the semiconductor and the MIM space.
Fang’s idea was to try to move into the 3D printing/additive manufacturing space. The concept was to use the PµSL approach, which is similar to other DLP 3D printers in the market. The approach consists of a resin bath, with light to cure the resin. In BMF systems, the light source is focused down to a very fine resolution and the movement is controlled to ensure precision. Microscale 3D printing fits a market segment of high-value
industries that do product development, manufacturing, and production, but with resolution and dimensional accuracy requirements in the millimeter, and perhaps micron area in tolerances, such as electronic connectors.
Other small size production technologies exist, including photon lithography. One criticism of photon lithography is that it takes a long time to make a very small part. For example, a 20-millimeter size part might take a week to build.
The connector market, worldwide, is valued at $100 billion dollars. And connectors are getting smaller all the time. New markets, such as AR/VR for glasses are emerging that suit this technology. Design efforts continue to try to miniaturize in the optics and photonics market. In the medical device market, things are getting smaller, whether they’re sensors or drug delivery devices, or implantable devices. There’s a trend around industries wanting to get smaller.
Design challenges with microscale parts are not much different than those for macro parts. If it’s a connector, it needs to have certain features to be a connector, same with chip packaging. It needs to have certain characteristics to hold a chip, or a lens holder, but there are always considerations about how are you going to make it, including how to mold, machine, and/or stamp the part. One of the realities is the manufacturing processes for these smaller parts are more difficult and much more expensive.
For example, if you’re molding something like a computer mouse, that’s not that hard to do. The injection mold for that mouse is maybe tens of thousands of dollars, maybe $25,000. But if you’re making something really small, that
Microscale 3D printing is the concept of making parts at millimeter scale or even sub millimeter scale. It’s a technology that has been available for five, maybe even 10 years. What’s new is that this technology is being commercialized for industrial use.
injection mold may no longer be $25,000. It might be $250,000 because you need to machine that mold to get all the tolerances that you need, and you need to be able to build in the ports and all the dynamics that go into an injection mold, but at a very small scale.
Most users of these micro 3D printing machines are using them for prototyping. Until about two years ago, affordable micro 3D printers were not available for this application. Users could not get the resolution and detail they wanted one for one.
Today, about a third of users are doing some production. Users are testing materials, their design and then looking into production quantities. Some are finding out it’s less expensive to let the 3D printer handle the mold than to machine or stamp them. The mold materials are predominantly resin-based, with some ceramic materials.
What goes into the development of a macro 3D printer
BMF’s chief technology officer, Chunguang Xia, came from the semiconductor industry. One of the challenges was ensuring high tolerance, to create a platform when people are looking to get tolerances in the plus or minus five-micron area. At this level, measurements are done using technologies similar to a CT scanner.
“We needed to have a platform that could image onto the resin and create the part,” says Kawola. “If you’re making a larger part, our platform actually moves to be able to image in certain sections. All of that had to stack up. You’re also dealing with material shrinkage, so you’ve got all these variables that you’re trying to get to a place where you’re plus or minus whatever that tolerance is. I think it’s just a lot of good engineering by our team here to recognize that’s the target.”
For the DLP system, high precision optics were needed. “We’re really focusing down to a certain pixel size,” Kawola continued. “When we talk about,
let’s say 10-micron optical resolution, that’s actually the size of the pixel that’s being imaged onto the liquid. Most DLP systems in the market are upside down, so they’re coming out of the liquid. That has a lot of advantages. We are top down. We do that for a couple reasons. One is we need to control layer thickness. The thicknesses of our layers are in the 10-to-20-micron range, so we need to be able to highly control that. Two, all DLP systems, all resin-based systems, when that light comes down and polymerizes the resin, that’s a reaction and there’s heat. Most 3D printing systems, there’s heat being generated and that’s one of the challenges, actually, for a lot of DLP platforms.
“A company in Chicago, Azul, has some new breakthroughs in how to control that heat and try to cool that process as it goes, but it’s a challenge and heat is bad for trying to maintain dimensional accuracy. That’s another reason why we are top down because when you’re bottom up, you only have a thin layer of resin. There’s heat there and that can build up. When the system is top down and you have a vat, it acts as a heat sink, so you don’t really have that buildup of heat that affects most other technologies.”
An ecosystem for materials has been evolving for about five years. BMF is an open platform. “For prototyping, arguably the materials don’t matter that much. They need to be close enough and most people can be pretty happy, but when you get into manufacturing, they need to be really close or exact. I think the collective wisdom of more companies coming into the 3D printing material space, in my opinion, has significantly moved the industry forward over the last five years, at least.
“Now, it’s not just the 3D printing companies with their material science departments within each company. Now you’ve got Henkel, and Covestro, and BASF and Evonik and all these big companies coming in and developing materials to help push that along. We’ve tried to take advantage of that. We’ve tried to shop around and see what’s available and partner with as many people as we can. I think what’s attractive also in that open business model is if resins work on some other DLP printer, and have proven to be successful and attractive to customers, they will probably work on our platform too. We can take things that have been developed. We need to modify them a little bit, primarily because our layers are thinner. We have to tune them essentially, but then we can offer that wider range of materials for the customers.
“The other important thing that we believe in for the open materials model is if big customers are really going to go into production, they’re going to want to have more control over the material supply chain. That’s our opinion. They’re going to want to be involved. I mean, we even see it when we work with some of them. We’re still a small company and when we go to a big chemical company and ask them to do something for us, they’re polite, but they don’t jump, but if we go there with a customer that is already one of their customers on the thermoplastic side, who already buy tons of plastic pellets, they are more willing, I think, to think about working together to develop 3D printing materials for that customer.”
There’s been a significant improvement in materials over the last ten years for nearly all 3D printing platforms.
A key trend now is to make sure that all the systems, the materials, and the software are designed with manufacturing in mind so that the systems can be put into a factory and put in series or parallel with other manufacturing technologies, and can work with the quality management system that the company may have. Users are realizing that for most 3D printing technologies, the very large majority of the cost is not the labor. It’s the amortization of the machine, it’s the materials and the labor’s a relatively small component.
The automation piece is important when it adds real value, but it should be balanced with the cost and flexibility that comes with a person. “A person’s pretty flexible. If he drops something on the floor, he picks it up. If the robot drops something on the floor and it didn’t mean to, it doesn’t know how to pick it up. There’s that balance there. I’ve been in injection molding houses and I’ve been in 3D printing service bureaus where there’s 20 machines running and there’s one or two people. I think the automation will help, but I think there’s still lots of room to go in terms of getting the machines to the point where they may need more automation.”
Kawola thinks that for all of 3D printing, whether it’s resin-based, or filament-based or powder-based, the key is to get those additive manufactured materials, those 3D printing materials to be sufficiently the same as molding materials or machine materials.
“Our challenge and the industry’s challenge is to try to get that part to be close enough to the thermoplastic to be suitable for the application.”
Boston Micro Fabrication
www.bmf3d.com
Additive hardware continues to improve in productivity, accuracy, and in ease of use. Now, the focus is on software to improve additive functions and capabilities, and to take additive to the next level. Hardik Kabaria, the director of Software Engineer focused on R&D at Carbon, offers insights.
Kabaria notes that more engineers are involved in some way with 3D printing/ additive manufacturing. Reports from ASME, for example, estimate that about 88% of the engineers use 3D printing, whether it’s for prototyping, bridge manufacturing, or actual manufacturing of the
parts. More engineers view 3D printing as a toolkit, so more design tools are emerging to support them.
These tools support engineers to make amazing parts and to take advantage of 3D printing’s design and manufacturing capabilities.
With its manufacturing capabilities, each process is different, for example between plastic and metal materials, and every process underneath that.
Software is making it easier to place different mechanical functions in specific areas of a part. A bike saddle, for example, can be made aesthetically pleasing, as well as comfortable. If you create many different types of foam, layered into a bike saddle, it’s possible to reduce pressure for greater riding comfort. But then it will create a nightmare in terms of manufacturing cost and assembly. Shifting to a lattice design achieves the same comfort, but with less assembly and less cost.
Software programs are also working on robustness. An issue that often occurs is that the data for a 3D printable part will have gaps in the data. The triangle measure is not clean, for example. Thus, software developers are looking to create tools that are more robust in handling these issues, as well as being easier to use.
“So, there is a lot of opportunity to create amazing software in the CAD and CAE world to help these engineers create products,” says Kabaria. “I think as the processes mature more parts are going out as production parts (rather than prototypes) through these processes.”
“Additive manufacturing is, in my mind, still in a very early stage because amazing innovations continue to develop on the software side allowing users to create amazing designs. Lattices are one particular innovation. We had to innovate. But we just didn’t innovate on how to draw lattices on all the different type of lattices available. We innovated on the
software that underlies this type of software.
“Once it gets to a mature state, the next stage is making these tools easier in terms of accessibility. That means any engineer who may not have a lot of background on 3D printing can at least use these tools easily. They should be able to make some parts, and then come the ideas of all the things one would have to do to optimize those designs for any particular
manufacturing process. That in my mind is sort of the middle stage, continues Kabaria.
“And then the final stage is when everything is workflow optimized. That means the users are not going through three different tools. Everything is connected, often with plugins. But I still think we are far from that. We are in the place where we are innovating on the core technology about what lattices are, how to generate lattices and
how to help users pick the right lattices with the minimum design iterations. Can the simulation software handle performing mechanical simulations on these lattices? I would say we are in that stage. And it’s exciting because there are a lot of unsolved problems and it can lead to amazing parts using this new way to manufacture things. So, that’s where we are all trying to create impact.”
A design that uses lattices can have 10 to 40,000 different primitives. This factor is significantly higher than the number of primitives typically seen in designs made for traditional manufacturing. Some developers of lattice software are innovating how to represent the primitives more efficiently—not just by representing them as triangles, for example.
Software programs are also working on robustness. One area this affects is custom manufacturing. When you have custom manufacturing, data are captured in some way, whether it’s from an iPhone scan or dental labs scanner. An issue that often occurs is that the data will have holes. The triangle measure is not clean. Thus, software developers are looking to create tools that are more robust in handling these issues, as well as being easier to use.
“At Carbon, we are able to deal with the parts that have holes. That means we have a way to create a meaningful out of a non-meaningful input. I think there is active innovation here, algorithms being developed. I would say the state of the art is changing every month.
A challenge, however, involves handling all of that data.
“Can we use GPU (graphics processing units) to make the processing faster? I think that’s a great question,” says Kabaria. “We at Carbon are working on that idea. That type of innovation is what is going to take us to the middle age, where it is easy to use these tools for any engineer who may not have background in innovating.”
Tools integrate with CAD software
Improvements in working with established CAD programs are on the way. For most, though, it’s not an optimized flow, yet.
Notes Kabaria, there are several reasons for this situation. One is because the tools are still emerging. It’s difficult to create a full ecosystem today, but it will improve. Plugins are one solution for now.
“Everybody’s thinking about this,” says Kabaria. Our philosophy at Carbon has been that before we create workflow optimization, we make sure that the parts being designed on Design Engine are good enough in terms of business or performance logic. So, it’s going to be painful in the
short term, but you still get benefit out of it. That means at the end our customers are putting a kick ass product in the market that they feel proud of, and know they cannot make any other way. And hence maybe that pain is worth it because we did enable to create a superior product. And the examples are countless from helmets to saddles.
“Let’s say we wanted to achieve a particular energy absorption performance. For a helmet, you want to do that by keeping the helmet volume the same. You don’t want to make a heavier helmet, but you want to achieve better energy absorption. Then you could use lattices, especially alongside elastomers because lattices and elastomers could create a competing metamaterial together that would outperform foam.
“Imagine you want to achieve a sort of cushioning response. That means you have a bike saddle and you don’t want to just create a bike saddle with 3D printing so it looks aesthetically cool. But you also want to reduce the peak pressure at the SIT bones. Academia has explored this quite a bit to understand that if you create many different types of foam, layered into a bike saddle, it’s possible to reduce that pressure. But then it will create a nightmare in terms of manufacturing cost and assembly. Shifting to a lattice design achieves the same comfort, but with less assembly and less cost.
“The business logic aspect comes in two ways because you are designing on the means of manufacturing. That means you are designing parts, let’s say using lattice structures and elastomer materials for Carbon, and you’re printing on a Carbon machine during the prototyping phase. So, you create this design, you test it
Increasingly, software for additive manufacturing is developing an ecosystem for engineers, helping them find more applications that they can put in production.
out, you can do this fast because you are not needing to create a mold to test three or four different foam molded designs. Over the course of 18 months, you can do 70 integrations in three months. So the product development cycle is shorter and it is shorter for two reasons.
“One is, of course, you are using printed prototypes. And the same printer at Carbon is available to do manufacturing. And the second is the design is digital. That means you change your lattice parameters by a click of a button and you get a slightly different design. Yet, the workflow between designing the primitive and the CAD on Solidworks and generating lattice is going to be painful, but it’s still faster. And we have showcased that with our customers, that you can reduce the product conceptualization of the prototype and manufacturing time significantly. So that means you are able to put more product in the market faster if you utilize these technology platforms and that is your business logic. Second, you can add more skews, you are not restricted to offering just three sizes, you can offer five. There’s a whole scale between one or three t-shirt sizes to 50 skews.
“In my mind that is the business logic; let the product company be in the decision and driving seat to figure out what’s right for its customer segment. And this certainly helps in the medical device segment as well as consumer products. So, you don’t necessarily have to generalize too much and have sort of one size fits all approach.”
Based on customer demand, more companies are developing opensource software.
According to Kabaria, Carbon will offer general availability of its lattice software at some point. “That means you can design a lattice structure in the Design Engine Pro and download the STL file and you can choose to put it on any printing process of your liking. We are becoming more agnostic and we are certainly proud of that because we believe not every material, not every process needs to be tied up to a particular machine. But at the same time, we are being cautious. If a user wanted to use the Design Engine Pro and extended capability for a metal AM part, we are happy to jump on call and help you figure out all the areas where you may run into problems, because we certainly want to enable you to do that.
For Kabaria, applications are a motivating force. “I think the software is a tool to accelerate the product design needs to manufacturing. And I’ll give an example that has still to date astonished me because I’ve been working for Carbon since 2015. I didn’t have an additive manufacturing background before, but since then I have been sort of living, breathing lattice structures in one form or another. But that means I’m also always on the lookout for places where you could apply lattice structures. During COVID we all ran into the shortage of COVID 19 swabs. Swabs were something I would have never in my dreams imagined being made with 3D printing. Yet, the shortage and breaking of the supply chain sort of demanded that need.
We played a role in it. We were able to design the swab. And within 20 days we did a clinical trial at Beth Israel Deaconess Medical Center at Harvard, at Stanford. We proved that the swab is as good
as the gold standard swab. And it was in use at hundreds of clinical institutions and it was produced using the same printer using the same design engine and the same materials that are already validating. So, in my mind, at least for me, the moral of the story is there are more applications out there than any one human or one organization can ever think of. Everybody has realized that the faster you do the product development, the more applications you can reach.
So, what excites me the most is as these tools go out the door, I think they will enable an ecosystem of engineers to find more applications that they can put in production, whether it’s once in a year or it’s a recurring product for tens of years, it doesn’t matter. We just want to enable engineers to put more products in manufacturing on any additive manufacturing platform.
Many AM vendors are developing additive ecosystems that offer more complete approaches to the use of additive technology for manufacturing. Here’s a look at what one company is doing.
Desktop Metal has been busy creating a portfolio of “Team DM” brands to make 3D printing accessible to companies of all sizes, helping them produce products more sustainably and closer to the point of end use. This portfolio offers a range of production capable 3D printers from binder jetting to digital light processing.
“The COVID pandemic exposed the weaknesses of our current manufacturing infrastructure,” said Ric Fulop, Co-Founder and CEO of Desktop Metal. “With today’s AM technologies, every country can have its own self-sustaining manufacturing industry with parts that can be shipped digitally and printed quickly.”
For Binder jetting, the S-Max Flex prints standard silica sand with furan binders and delivers final parts with dimensional accuracy of +/- 0.5 mm. The system comes with several accessories and safety features that are configurable to fit a variety of spaces.
A highlight of the portfolio is the Production System P-1, which was launched during the height of the COVID pandemic. A high-speed 3D printing system for end-use metal parts, the P-1 was designed as a gateway to the top-of-the-line Production System P-50 – one of the fastest systems to 3D print metal parts at scale. The P-1 shares the same patentpending Single Pass Jetting (SPJ) technology as the P-50, as well as common software and electronics for easy scalability.
The Production System is one of several Desktop Metal printing platforms that relies on binder jetting technology, which is widely regarded as one of the 3D printing methods likely to deliver mass production additive manufacturing at high speeds and competitive prices.
Nearly a dozen metals are now qualified for printing on the Production System P-1 and P-50 –delivering good part quality and surface finish, with sintered part mechanical properties that meet or
exceed applicable industry standards, and final part densities up to or exceeding 99%. A partial list of qualified materials includes:
• Stainless steels, including 17-4 PH, 316L, 420, 440C, and DM HH SS
• Tool steels, including D2 and S7
• Low-alloy steels, including 4140
• Copper alloys
• Nickel superalloys, including IN625
• Precious metals, including silver and gold
• Ti64 and 6061 in development
Binder jetting
After years of contraction, the U.S. metal casting industry is experiencing growth as a result of supply chain changes related to the COVID-19 pandemic. This growth was one of the reasons
Desktop Metal bought ExOne and launched the ExOne S-Max Flex, a scalable, large-format binder jetting system that 3D prints sand tooling. Applications include sand casting complex metal designs for the aerospace, automotive, and energy industries.
The S-Max Flex combines ExOne’s sand printing expertise in process and materials with the SPJ technology to deliver a build rate
up to 115 l/h. The goal is to make good sand 3D printing accessible to every foundry.
It pairs an affordable industrial robot with an end effector printhead design that deposits binder into a 1900 x 1000 x 1000 mm (74 x 39 x 39 in.) telescoping build box that grows as the parts are built layer by layer. Additional build box sizes are available up to 4700 x 1000 x 1000 mm (185 x 39 x 39 in.), with taller versions available up to 1000 x 2500 x 2400 mm (39 x 98 x 94 in.).
The S-Max Flex prints standard silica sand with furan binders and delivers final parts with dimensional accuracy of +/- 0.5 mm. The system comes with several accessories and safety features that are configurable to fit a variety of spaces.
Industries beyond metal casting are also set to take advantage of the S-Max Flex’s large form factor and ability to binder jet a variety of powders. Infiltrated sand tooling for plastic thermoforming, composite layup, and sacrificial tooling applications are printed on S-Max machines, along with infiltrated sand consumer products, such as those offered by Sandhelden and Deeptime. Desktop Metal’s Forust brand, which upcycles byproducts of the wood waste stream into consumer designs, will also leverage the new system to print large form factor wood parts
at scale cost-effectively. Additional projects are underway printing reclaimed concrete and other materials.
Another binder jet 3D printing system is the X-Series line for metal and ceramic powders in a range of particle sizes. Like the S-Max Flex, this line of printers is derived from the acquisition of ExOne.
The X-Series line offers a differentiated approach to binder jetting enabled by patented Triple ACT — an advanced compaction technology for dispensing, spreading, and compacting powders during the binder jet printing process. This flexible, open material platform architecture can bind together a range of powders with a D50 of 3 to 100 microns.
Three X-Series models are available:
• InnoventX, an affordable, entry-level binder jet system for academic, R&D, and low-volume production applications.
• X25Pro, a mid-sized system for volume production with a build box of 400 x 250 x 250 mm (15.75 x 9.84 x 9.84 in)
• X160Pro, as large metal binder jet
P-1 is a high-speed 3D printing system for enduse metal parts. It uses the same Single Pass Jetting (SPJ) technology as the P-50, as well as common software and electronics for easy scalability.
system with a build box of 800 x 500 x 400 mm (31.5 x 19.7 x 15.8 in).
The X-Series printers repeatably deliver tight dimensional tolerances and densities of 97-99% or greater — in line with or surpassing metal injection molding or gravity castings. Surface roughness values as low as 4 µm (Ra) can be achieved directly out of the furnace.
When Desktop Metal bought EnvisionTEC, it rebranded the 3D printing line as ETEC. This line uses digital light processing (DLP)
Stainless Steel (DM HHSS) is a custom stainless-steel alloy that combines high strength and hardness with corrosion resistance. A key application is its use to make offset sockets.
technology, and the goal is to bring high-speed, photopolymer 3D printing to volume manufacturers of consumer and industrial products.
These 3D printers offer extreme levels of accuracy and surface finish and have been used in the healthcare, dental, medical and jewelry industries since 2002. Another result of the EnvisionTEC acquisition was the launch of Desktop Health to focus on healthcare and dental customers.
Through a partnership with Adaptive3D, another subsidiary of Desktop Metal, ETEC offers a broad portfolio of photopolymer 3D printing materials, including Elastic Tough Rubber 90 (ETR 90), which is one of the highest tear strength elastomers on the market. ETR can be found in products on store shelves, including power tool adapters and recoil pads.
When it comes to materials, Desktop Metal has released several, including DM HH Stainless Steel (DM HH-SS), a custom stainlesssteel alloy that combines high strength and hardness with corrosion resistance, for use on the Production System platform.
DM HH-SS is a custom, heat treatable-alloy that combines the tensile strength, ductility, and corrosion resistance of 13-8 PH stainless steel with hardness comparable to low-alloy steels, such as 4140. These attributes may help companies eliminate the use of low-alloy steels, which also require a subsequent plating step for applications needing corrosion protection. DM HH-SS is also suitable for conformally cooled injection tool core and cavity applications, where millions of injection strokes per year are required.
An example of a key DM HHSS application is the offset socket,
often used for manufacturing tooling in scenarios where space is limited and a traditional tool would not be able to access a bolt. Instead of maintaining an inventory of a variety of tools to accommodate multiple socket sizes for each bolt size, users can maintain a digital warehouse of each socket size and print quantities of different sizes together in a single build.
Another material finding greater use in 3D printing is copper. Desktop Metal announced it has qualified commercially pure copper (> 99.95% purity) for use on the Production System platform.
With its thermal and electrical conductivity, commercially pure copper suits applications that require heat or electricity transfer, such as cold plates, pucks and manifolds, heat sinks, heat exchangers, and bus bars used in power-intensive electrical applications. It is the third-mostconsumed industrial metal in the world.
Desktop Metal’s materials science team has qualified and fully characterized commercially pure copper (C10300) printed on Production System technology. Liquid cooling plates, which are used to regulate temperature on microprocessors, are an example. Coolant flows through the fins, which provide a large surface area to transfer heat from the passing fluid to the heat sink to cool the chip attached to the outer body. These cooling geometries typically require capital-intensive, long lead time, and skilled laborintensive production processes, such as skiving and machining, given the challenges associated with achieving precision and repeatability in such a small form factor. In addition, these commonly used conventional manufacturing processes are subtractive and
produce excess scrap material, greatly increasing the associated part costs. Binder jetting on the Production System can produce a liquid cooling plate as a single component.
D2 tool steel is a versatile highcarbon, high-chromium air-hardening tool steel characterized by its hardness and compressive strength after heat treatment. This tool steel is wear resistant, dimensionally stable, and resists corrosion in the hardened condition, a key benefit for conformal cooling applications. D2 is used for a variety of cold work tools that require a combination of wear resistance and moderate toughness, such as coining and sizing tool members, blanking and forming dies, shear cutting tools, gauges, burnishing tools, and other wear parts. An example application is rotating cams.
Cams are used in oil and gas or chemical processing applications to convert rotary motion into reciprocating linear motion in a machine. Typically, these parts require multiple manufacturing steps, beginning with CNC machining, followed by broaching of the spline on a separate machine. Binder jetting enables the production of cams in a single printing step, reducing both the cost and lead time of the part, while also supporting the production of different cam sizes in one build.
D2 tool steel suits this application because of its hardness and corrosion resistance, which ensures a longer lifetime as the cam mechanically interacts with a sliding pin. In addition, because these components are often integrated into machines operating in harsh environments, the corrosion resistance provided by D2 ensures that the parts will perform as intended and not deteriorate.
Vital Auto was founded by three friends who got together, quit their jobs, and decided to set up a shop in a garage. One of the first contracts the company took on was for the NIO EP9 supercar concept, which set the team on a course to produce extremely realistic vehicular prototypes.
Located in the heart of the UK’s auto industry, Vital Auto is an industrial design studio with expertise in automotive design. The company’s clientele includes many of the major automotive manufacturers, such as Volvo, Nissan, Lotus, McLaren, Geely, TATA, and more.
“Clients typically come to us to try and push the boundaries of what’s possible with the technology available,” said Shay Moradi, Vital’s VP of Innovation & Experiential Technology. When manufacturers don’t have time for experimentation themselves, they rely on Vital Auto with any kind of challenge to turn ideas, initial sketches, drawings, or technical specifications into a fully realized physical form.
Vital Auto was founded in 2015 when three friends got together, quit their jobs, and decided to set up a shop—fittingly—in a garage. One of the first contracts the company took on was for the NIO EP9 supercar concept, which instantly set the team on a course to produce
extremely realistic vehicular prototypes.
Today, depending on the client request, the team will start anywhere from simply a sketch on a piece of paper to an already designed vehicle. They develop cars from a blank sheet, design all the mainframes, all the exterior and interior elements, open/closings, and interactive elements. With five to 30 people working on a single concept, a typical project could take anywhere from three to 12 months.
In this time, a typical show car goes through up to a dozen core design iterations, and within those, there can be further iterations of smaller components until the design meets the expectations of their customer.
“It’s all well in our industry to look at virtual properties as a means of evaluating a product before it goes to market. However, I think there’s always going to be a place for physical manufactured objects as well. There’s nothing that beats the sensation and feeling of holding an object in your hands with the correct weight, with the correct proportions, and the dynamics of how the physical environment changes your perception of that physical object,” said Moradi.
“Most of our customers will come to us with an innovative idea, something that’s never been done before. So, the challenges for us are new every single day and they’re endless,” said Anthony Barnicott, Design Engineer in charge of additive manufacturing. “These challenges can range from, how can we produce this number of parts in this amount of time to, how can we make a sustainable product or how can we make a part that achieves a particular weight while still achieving a particular performance.”
While traditional show cars are normally made from milling clay, the team also uses three- and five-axis CNC milling, hand forming, hand clay
modeling, and GRP composites. These traditional processes are, however, often not ideal for producing the custom parts required for one-off concepts.
“We’ve used 3D printing from day one. We wanted to introduce it to our manufacturing processes, not only to reduce costs, but to give the customer more diversity with their designs and their ideas,” said Barnicott.
Today, Barnicott runs a whole 3D printing department, including 14 largeformat FDM printers, three Formlabs 3L large-format SLA printers, and five Fuse 1 SLS printers.
“In terms of capacity, all those printers have run 100%, 24/7, pretty much since day one. We use these printers for all areas of our concepts and designs. Typically, we would use the Fuse 1s for our production-based parts and we
The team mainly uses the Fuse 1s for mechanical parts, such as door hinges, door handle inners, door internals, and structural applications. They can use these parts straight off the printer, with minimal finishing.
we moved to the White material to produce a production-ready part.”
This air vent was based on a proprietary design. 3D scanning technology was used to create a digital file of the vent. Then, software was used to create a custom external skin for customer approval. Once done, the designers went on to product a production ready part.
would use our Form 3Ls for our conceptbased parts,” said Barnicott.
“We use the Form 3L machines for anything that is an A-class finished surface. So typically, in an automotive interior where you have parts that are not being trimmed with leather or Alcantara or some sort of cloth material. Formlabs materials give us a nice, smooth finish for our painters to work with; we can use these parts straight out the printer, straight onto a vehicle,” said Barnicott.
“What interests me most about the Form 3L machines is their versatility, the ability to do a material change in less than five minutes and the variability of those materials going from a soft, flexible material to a hard and rigid material for us is priceless,” said Barnicott.
The team uses the Form 3L’s with multiple materials for a wide array of applications from air vents to door seals.
Customers will often approach a highend auto manufacturer with a proprietary product that they want to encase in their own design.
“One customer, for example, approached us with a proprietary air vent from another vehicle that they wished to have inside their own interior. We used 3D scanning technology to reproduce this part digitally and then created an external skin. We first produced this in the Draft material to test out the design and allow the customer to verify it. From there,
“When working with incredibly intricate designs, such as small switch packs, what we’re able to do is use multiple materials to achieve a mechanical product that not only functions correctly, but can be used in a real-world environment. [For these switch packs], we combined harder materials, such as the Tough 2000 for the top surface, with the lighter, more cost effective materials for the internals.”
“Typically, door seals for automotive applications can be incredibly costly to produce. there’s simply no other way other than extrusion molding to produce them. This comes at, not only a very large tooling cost, but also a long lead time as well. We were able to experiment with one of Formlabs’ newest materials, the Flexible 80A. The Form 3L enabled us to produce sections of this door seal overnight to test various geometries and was printed within 50 microns of the actual design.”
Having the Form 3L empowers the team to produce multiple iterations of parts in most cases within 24 hours. They ended up buying three different machines so they could produce up to three different iterations of a part at the same time, even using three different materials. They can then pass on the cost savings to the customer or offer more value by showcasing multiple design options for the same price.
“One of the beauties of using additive manufacturing is the compression of a timeframe. So what do you do in that span of time that you have freed up? We sort of see it as extending the possibility space into imagining alternatives, into adding more iteration loops in the process,“ said Moradi.
“There are many products we
Small switch packs are incredibly intricate parts. Designers and Vital Auto used multiple materials to achieve a mechanical product that functions correctly and can be used in a realworld environment. The engineers combined harder materials, such as the Tough 2000 for the top surface, with the lighter, more cost-effective materials for the internals.
produce that we simply wouldn’t be able to without our Form 3Ls. With some of the most advanced manufacturing techniques, such as seven-axis CNC machining, we’d be able to produce these parts, but it would come at a huge compromising cost,” said Barnicott.
“The Fuse 1 one was our first venture into SLS technology. As a small business, this is a technology we thought we would never be able to have on site. With the Fuse 1, not only do we have one of the machines, but we actually have five of the machines on the site. What these machines enable us to do is produce structural mechanical parts quickly, not only for testing but for physical applications in most of our concepts. This process would have typically been done by CNC machining, either on our site or off site, depending on the geometry, and we would have to wait two to four days to get the parts in our hands. The Fuse 1 enables us to cover all of this on site and have parts in our hand in most instances, less than 24 hours,” said Barnicott.
The team mainly uses the Fuse 1s for mechanical parts, such as door hinges, door handle inners, door internals, and structural applications. They can use these parts straight off the printer, with minimal finishing. Some of the applications where the team used the Fuse 1s include an air duct.
“A lot of automotive interior parts can be incredibly tricky to produce without going down the
traditional injection molded route. Items such as internal air ducts and vents, items that are never seen, but yet require a large cost to produce. We use the Fuse 1 to produce these parts. It allows us to be much more versatile with the designs we put in the vehicle without incurring the large costs that they would typically have.”
“3D printing has allowed us to combine both the SLA and SLS materials to work our way through design iterations on a specific project. This allows us to quickly produce multiple iterations, combining both processes, using them for their specific properties, to achieve a final design. This can be anything from mechanical parts to clear parts to check their optical quality and output.”
While it’s often said that additive manufacturing is here to replace subtractive manufacturing, the Vital Auto team sees benefits in combining different technologies to leverage their best qualities.
“We use the two processes together to help support each other. We have many parts
where we would use subtractive manufacturing and then use additive manufacturing to produce all the finer details. This allows us to have a much more cost-effective way of producing a lot of our concept models,” said Barnicott.
“The progression in technology and 3D printing over the last 10 years is phenomenal. When I first started, producing low volume, niche vehicles, some of the products that we produce today would simply have been inaccessible. And not only am I able to produce these parts today, but I’m also able to produce them cost-effectively, quickly,” said Barnicott.
3D printing not only helps the team create better products faster, but also to attract new business. They found that many of their customers turn to them because they want to have access to the latest technologies and they want to have their components made using the latest cutting edge materials.
“There are certain things that you just can’t class as emerging technologies anymore. 3D printing is one of those things. It’s advanced to a point where everything that we produce is good enough for use in the final presentation stage with all the layers of making that we apply on top of that. 3D printing has gone from almost a novelty to becoming an absolutely inseparable part of what we do,“ said Moradi.
Formlabs | www.formlabs.com
Many automotive interior parts can be tricky to produce without using traditional injection molding. Internal air ducts and vents may never be seen, yet they are costly to produce. Formlabs Fuse 1 was used to produce these parts, enabling more versatility with the designs without incurring large costs.
Additive manufacturing continues to evolve. Here’s a look at how Wayne Davey, Global Head of Sales and Goto-Market for 3D Printing Solutions, HP Inc., sees the latest developments in this industry.
Q: Over the last few years, various commentators have discussed the need for designers to think differently when designing for additive manufacturing versus machining and injection molding. Where do you see the design thinking now, and where does it need to get to in order to take full advantage of AM?
Davey: The manufacturing industry is seeing the benefits of reframing the design process to better suit additive manufacturing. With a fresh perspective to product structure and design, manufacturers are able to create unique, cost-effective and, most importantly, commercially useful products. Engineers developing products which cannot be manufactured today is one element of 3D printing realizing its full potential. To take 3D printing to the next level, however, means looking towards mass scale production. For that, we need to pair 3D printing with other innovative technologies like AI and machine learning. Using data-driven insights, manufacturers can push the boundaries even further and create complex, high quality parts that are also sustainable.
A great example of this is HP’s partnership with Cobra Golf and Parmatech where a first of its kind, limited edition, 3D printed putter is being manufactured commercially using HP Metal Jet. The KING Supersport-35 putter features a thin exoskeleton braced by lattice beams—entirely different from traditional putters made with solid chunks of metal. Cobra Golf is also leveraging HP’s Multi Jet Fusion platform for three oversized models in the King 3D Printed Series – the GrandSport-35, the SuperNova and the Agera – producing a nylon lattice cartridge to optimize weight distribution for high moments of inertia and stability. And just last month, Cobra Golf announced that it is expanding its collection of KING Putters with new options for personalization, like different shapes and colors.
Cobra Golf and so many others are showing the world what can be achieved when 3D printing platforms and design tools are seamless. As the industry continues to leverage breakthroughs in automation, software, and data, customers will be better equipped to understand the entire end-to-end lifecycle, from supply chain to the useful life of a part, so that better parts can be printed with improved design.
Q: Are there new applications emerging as a result of additive’s capabilities? What are they?
Davey: The ability for increased customization has broken down the barriers of what is possible for new and emerging applications. Take healthcare for example. Through the evolving capabilities of AM, the health and wellness industry is poised to greatly benefit from the advanced design and manufacturing. According to HP’s Digital Manufacturing report, 55% of those surveyed predict the medical industry will see the most innovation. AM has the capabilities to deliver
personalized and customized care of specific aliments. Consider as an example, a blend of advanced 3D printing and cloud-based software that allows podiatrists and orthotists to capture 3D renderings of a patient’s foot, fine-tune and prescribe personalized orthoses for their patients in less than five minutes.
The automotive industry is also investing heavily in AM. They are taking parts and redesigning them using metal binder jetting for structural components for the first time. While the pieces or functionalities might not be an emerging application, the way in which they are designed and created are a first for a heavily regulated industry.
A strong example of this is HP’s collaboration with GM and GKN Forecast3D. GM recently turned to HP’s Multi Jet Fusion printing technology to produce a spoiler closeout seal, which typically goes through a standard finishing process. In three weeks, together with GM and GKN Forecast3D, we were able to design, create, and implement a viable value stream
for the rear spoiler seal, with speed and flexibility that would have not been possible with traditional manufacturing models. The result was an accelerated production schedule, creating and polishing the required 60,000 parts over the span of five weeks for use on approximately 30,000 parts for fullsized SUVs.
Q: Scaling additive technology is becoming a more frequent subject. What do users of AM need to understand to convince management to invest in AM now, and what does management need to understand about AM scale to have more confidence in this technology?
Davey: The value proposition for AM investment today is threepronged:
Manufacturers are seeking greater supply diversification with an emphasis on localized, ondemand production to build more resilient supply chains
Consumers want the goods they purchase to be tailored specifically to them—hyper personalized—
an expectation filtering in from their experiences interacting and consuming in the digital world.
Sustainability mindset, consumers are actively making calculated purchasing decisions that are also better for the planet. These market moving trends are all intertwined by one common factor – traditional manufacturing methods are inefficient and costly at addressing all three, especially at once. The opportunity cost of not evolving with the new manufacturing paradigms facing us today is a risk that can no longer be overlooked. And it’s not just one industry being impacted. Across the board, automakers, health and wellness brands, sports equipment manufacturers and so many more are looking for new processes and technologies like 3D printing that help them meet these demands quickly, economically, and at a mass scale.
3D printing’s capabilities are unmatched. It offers economic viability removing cost implications of part inventories, expedites iteration and speed to market, and is less resource intensive. These
COBRA Golf, a leader in golf club innovation, used 3D Printing technology on its KING Supersport-35 putter. This putter has been in collaboration with COBRA engineers and the teams at HP and Parmatech. It features a fully 3D printed metal body with an intricate lattice structure to optimize weight distribution and deliver the highestpossible MOI in a blade shape. In addition to the 3D printed design, the putter features a face insert designed in partnership with SIK Golf, which uses their patented Descending Loft Technology (DLT) to create the most consistent and accurate roll on every putt.
The COBRA’s LE 3D-printed Supersport-35 Putter represents a revolutionary advancement in the way golf clubs are designed and manufactured. Born out of a forward-thinking philosophy, COBRA selected HP as its partner to pioneer 3D printing in golf due because of HP’s Metal Jet Technology. With its quick processing time and design adaptability, COBRA engineers were able to design, prototype, and test multiple iterations and bring the product to market faster than using
COBRA and HP began working together in early 2019 and, by early 2020, the team had created thirty-five different design iterations over the course of eight months using the HP Metal Jet.
The Supersport putter, which comes in an oversized blade shape, features SIK Golf’s Patented Descending Loft technology reengineered into an aluminum face insert. This insert design strategically saves weight from the front of the putter to be repositioned heel-toe and tunes the feel to a slightly softer feel than a traditional all-steel SIK putter face. Their signature face design uses four descending lofts (4°, 3°, 2°, 1°) to ensure the
are all factors that can improve a company’s bottom line. As the ability to scale increases, so does that reality of mass-personalization through additive manufacturing.
Q: There’s a lot of discussion about the supply chain. What are some of the better applications for additive in a supply chain system today? What could they be in the next few years? What will it take to get there?
Davey: Companies are actively looking for ways that 3D printing can strengthen their supply chains,
enabling them to become more agile, creating more innovative product development and manufacturing strategies. We saw firsthand during the pandemic that 3D printing can be a solution to a distributed supply chain, helping manufacturers develop, iterate and manufacture goods at a challenging time. Through 3D printing, manufacturers can create parts needed for goods that may have been backlogged due to the supply chain – enabling a quicker time to customer journey.
But it’s not just in times of crisis that additive will bring benefits to the supply chain system. 3D printing enables both short and long-term solutions capable of near-instant
responses to market changes. What once worked in traditional manufacturing models are not conducive to today’s environment. For example, older models were not built for shorter runs or minimized inventory. Localized production will continue to be prioritized. This is an unparalleled competitive advantage for companies, but customers and the world around us see benefits as well.
most consistent launch conditions for every putting stroke.
HP Metal Jet 3D printing delivers excellent part quality and requires minimal post-process finishing. The entire putter body is printed using 316 stainless steel, and then sintered at a high temperature to bind the metal and form the final head part. Due to the capabilities of Metal Jet printing, engineers printed an intricate lattice structure within the body – a manufacturing feat that wouldn’t be possible using traditional casting or forging methods. The lattice fine-tunes feel and optimizes the distribution of weight within the putter head to create the highest MOI without the need for additional fixed weights. During the final step of the manufacturing process, the surfaces of the putter are precision milled using a
Computer Numeric Controlled (CNC) machine to ensure precise shaping and detail while adding the finishing touches to the cosmetic. The Supersport features a high MOI heel-toe weighted design for maximum stability, and a plumber neck hosel with a 35-degree toe hang suitable for slight arc putting strokes.
The lattice structure removes weight from the center of the putterhead and pushes significant amounts of weight to the perimeter. The result is superior MOI levels and massively increased stability and forgiveness.
The final product is a celebration of a major revolution in golf club manufacturing in the form of a high-performance putter that will appeal to golf purists seeking a clean look and feel but is packed with advanced technology to improve the quality of a golfer’s short game.
Among the many benefits of using 3D printing is how it effects sustainable efforts in design and production. Here are highlights from an interview with Nadav Goshen, president and CEO at MakerBot on 3D printing developments in this area.
The subject of sustainability and 3D printing covers a range of issues. Goshen and MakerBot are focused on changing the way we make things, specifically around overall production. Changes to the production process can be enormous, covering initial design phases through manufacturing.
“In each part of the journey from a design to a part, 3D printing brings a lot of value into sustainability,” he says. For example, there’s a cost to maintaining a number of parts somewhere for future use. One aspect of storing the parts is they must be stored properly and then transported back and forth, all of which has a cost associated with it.
3D printing/additive manufacturing can eliminate those costs by producing the part where it is needed, when it’s needed.
“Because of the way industry typically fabricates things, we are constrained by the need to have parts ready, not necessarily when they’re needed. But 3D printing can change that. The digital element of additive manufacturing and 3D printing can really take all of this waste out of the system and make sure that we are more considerate about the resources we use when we build things.”
On the design side, there’s more opportunities to really, for example, cut cost and waste from the manufacturing process. When you design with sustainability in mind, or when you get to the production side of things, you have much more efficiency on that side.”
The quality of desktop professional grade 3D printers continues to improve. “Once more designers and engineers have more access to such 3D printers, they can really experiment with the technology. And that brings new design thoughts into a process of engineering product. So, we see that trend coming.
“In some industries, we see that subtractive design is eliminating possibilities, because you need to do multiple parts. Thus, you have multiples of tools, fasteners, etc. to produce and assemble the multiple parts. You also have double the waste. Once you think in additive, though, then you can combine two parts into one. And then you cut almost in half the overall environmental cost to produce a part. So, we see that trend coming.
Once you think in additive, then you can combine two parts into one. And then you cut almost in half the overall environmental cost to produce a part.
The way industry typically fabricates things requires that parts be available before they are needed. 3D printing can change that. The digital element of additive manufacturing and 3D printing can take wait and waste out of the system and ensure greater consideration about the resources used when building things.
“We see a number of economical drivers, but sustainability by itself needs to be fueled by the industry to make it more, I would say, embedded within companies’ P and L statements and the way they think about process.
“We see that for example in aviation and aerospace, where that kind of additive thinking really translates into less complicated and also lighter parts. When you have that, then it translates immediately into less or better fuel economy.
“So, all of this process is making a full circle from the possibilities we have to
the economic value and then to the process of manufacturing.”
For the C-Suite, working with innovation imposes a risk. Engineers are more comfortable with innovation because they are closer to the technology and can get hands-on experience with it. The C-level is a bit further away from innovative technology. Thus, executives can have a gap of knowledge and experience where they potentially view that
technology, such as 3D printing, as a higher risk than what it should be. Such an approach was common sense during the early days of a technology, but after a decade, it’s time for a new perspective. Part of changing the habitual perspective involves how to communicate to the C-level executive that the technology has matured and is less risky, and that there are use cases across the world. Hopefully, we won’t rely on events such as pandemics to bring greater awareness to the C suites about how useful 3D printing can be, especially with supply chains.
Another part of the issue is the cost of insurance. You don’t understand the cost of not having something unless you have “insurance” for it. This insurance covers situations we are not really prepared for. And again, the pandemic proved that if we are not putting some type of thought, action and policies in place, i.e., insurance, when the time comes, then there is a big cost to not being prepared.
Additive manufacturing and 3D printing is insurance for supply chain
Additive manufacturing and 3D printing is insurance for supply chain shortages and to everything that might happen. In many cases, these economic factors were not really put into the overall calculation of reasons to use 3D printing.
shortages and to everything that might happen. In many cases, these economic factors were not really put into the overall calculation of reasons to use 3D printing.
“I think both perspectives are changing now. The risk averse nature is changing and the need to understand or the understanding that the need to invest in a different way to manufacture and to have a supply chain strategy is also something that companies are investing in. The actual hidden costs in the supply chain have made the C-executive really consider their strategy around supply chain, manufacturing, and overall engineering.”
Another factor that will help the C-Suite re-evaluate 3D printing is the price of this technology. The investment that is needed to get 3D printing technology into your organization is lower. Systems that are capable, that are engineering grade, are being sold for a few thousand dollars, which is
potentially affordable on a designer’s discretionary budget. Then if you want to move up to more advanced additive manufacturing technology based on a proven use case, your company can invest to get a manufacturing grade machine.
“I think this is what we need to do because if your sales pitch is too theoretical, then it becomes less tangible for the C-executive,” continues Goshen.
A highly innovative technology, like 3D printing, brings enormous possibilities for addressing design and manufacturing challenges. But it comes with an inherent “trap” that what it can deliver is real. It’s easy for C-suite executives to lose confidence in the practical engineering that this technology can bring to their own day to day challenges.
“I’m C-suite. I know my challenges. They’re not in the conceptual world. They’re in the
practical world. And what I need to get a decision about investing in something new is, how does that translate into pragmatics? Let’s see more executive P and L contribution to my business,” says Goshen.
Desktop 3D printers can play a key role in demonstrating pragmatic benefits. With a very low investment, engineers can eventually change the way products are made and change the way their company handles the supply chain. A desktop 3D printer can help engineers make their ideas, their concepts tangible in the minds of their bosses.
As Goshen notes, technology needs to shift from being inspiring to being practical for executives to buy into it.
“We need that transition from an inspiring technology into practical technology, aside from innovation to engineering. And I think what is really happening is what happened in the computing industry maybe 20 years ago, for example, where it
A product needs to serve a specific purpose. We are now in the stage where we can take this technology into different applications.
became more accessible.”
Goshen compares the adoption of 3D printing to that of the early adoption of personal computers. Computing, to Goshen, is a crosstechnology product. A 3D printer, on the other hand, is a combination of chemistry and embedded computing, and all of it has to work together.
“3D printing is a much more complex process to control versus electric circuits on boards. So, I think this is what is affecting how this technology’s been spread. While it’s easy to get a part, it’s less easy to tune the printer. And that’s a challenge.
“I think there are many desktop machines, but they are not practical because they get to the point where they print the part, but it’s not repeatable. It’s not dimensionally accurate. And it’s really not easy to use and it’s not reliable. And when you have this, and this we had in the last few years, then it contributes to the confusion and also to the frustration of users.
So, we need to get the technology into the stage where it’s reliable and repeatable and it’s really engineering grade. This is the journey. It’s different between desktop and engineering grade machines. We need to make sure that we have engineering grade machines in the hand of anyone that has a practical use to it. I think that’s what is happening right now.”
The additive technology is still quite fragmented with people grouping brands and systems together. One example is what MakerBot calls engineering grade desktop versions. Desktop 3D printers and engineering grade desktop 3D printers are similar in size. Maybe the cost is double the desktop one, but it offers features such as in-process tuning that is required to get these engineering
grade machines accepted.
“In computing, I think that inprocess tuning was built in because its electronics. In 3D printing, it’s a combination of... I wouldn’t get into the details, but every engineer knows that taking a solid, liquefying it, and then getting it back to solid involves a micro-level accuracy and involves a complex system to make sure that you can control it and you can maintain the same results.
Three general categories
The range of 3D printing features and functions is wide. That fact is also contributing to the reluctance of some to invest in this technology. One category is the hobbyist market, or the maker market. This market was the origin of the desktop movement. “It’s a great market. I’m a user. But it’s a market where users have the skills in trying to get something to work and the willingness to participate in the result process. It means that I’m involved in the process of making, because I’m a maker. I enjoy that process of making it successful. But it’s not a professional use case,” notes Goshen.
The second category is education, which has different needs because of the use of technology for learning purposes. They use 3D printing to make learning more immersive. It ties into STEM education in many ways.
“The third category is what I call entry level engineering, which we are operating in, which is an accessible and affordable engineering grade machine. But it is still aimed at the individual engineer. It brings to the table a well-tuned, reliable engineering grade device that can be used for professional purposes to design and engineer parts.
“A subset of this category is the shared office 3D printer, which is a larger than an individual printer,
often a floor model. That is a natural expansion of that individual printer,” says Goshen.
And then, on top of this, comes various levels of scalability in terms of materials and manufacturing focused printers. And then it becomes more specific. Then you move from the prototyping and small plastic production part to manufacturing. And this is another world by itself.
“All of this is using the same technology. But they’re not the same products. All of them use the same underlying technology, but classifying them together is probably not accurate and could contribute to the confusion that we already have in this fragmented industry,” notes Goshen.
Goshen sees the industry shifting since it’s early days when people expected we’ll have a 3D printer at each house without thinking about the basics of what products are.
“A product needs to serve a specific purpose. There has been confusion between the technology and the applications and the product translation of that technology. Which is something common with hype cycles. We are now in the stage where we can take this technology into different applications.
“I think that’s the cost that you’re paying today. We can reduce the cost today if we just change the way we think about manufacturing in general,” he says.
One of the changes engineers can expect is to have greater control and empowerment at the point of need with 3D printers.
As AM becomes more accepted as part of a manufacturing supply chain, it is altering the way engineers work and develop products. We recently had a conversation with Daniel Lazier, product marketing manager at Markforged. Here are highlights from the interview.
One of the changes engineers can expect is to have greater control and empowerment at the point of need with 3D printers.
“Back in the day when I was a design engineer, the nature of my job was to create a design and then rely on
We now see engineers, technicians and point managers alike, all converging on the point of the manufacturing line that needs that critical part and locating a printer as close to that, pushing that printer as far forward into that manufacturing challenge as possible.
on great manufacturing platforms. Now it’s sort of reverted back to this reality where I am directly in control of creating that part, pulling it right off the printer and getting that hands-on feedback as to how my design worked out.
a completely different and distinct set of resources, often outside of my business entirely, to make the part. And that might take weeks or months, depending on what the part was and what processes it was beholden to. I recall how frustrating that could be when the reality of your job, your timetable, and even your cost structure is dictated by someone completely outside of your business and outside of your control.
“The very nature of that job and that role changes when you’re empowered with equipment right on your desk,” continues Lazier. “In addition, the kind of components and parts that you rely on now can be produced right where you need them. And as an engineer, you are actually specifically involved with the creation of that part.
With 3D printing, designers can qualify a part all the way from prototype to production at a design lab or geographically distinct office, and then push that design to production where it may be pulled down by production resources somewhere completely different across the planet. This process is happening for a specific and growing band of use cases and applications, especially with printers
like the Markforged Digital Forge, and other cloud manufacturing capabilities.
With 3D printing, you have more choice about how hands on you want to be with a design, depending on the organization, the individuals involved with manufacturing, and the roles and responsibilities of those individuals.
“What I thought engineering would be before I went to college, I assumed I would be involved in the process of actually creating my object. But the reality was, at least in 2015, when I started my career as an engineer, it was really hands off. I could go walk through the factory, and go see how the parts were being created. But when I was actually doing my job, it was all behind a computer screen.
“And the beauty of 3D printing today is I’m sitting in a room that’s like 10 by 12, and I have three 3D printers sitting behind me. Even as I’ve transitioned to a role that has less to do with engineering, the process of actually creating physical parts, and every little detail that goes into that, are completely under my control. And by extension, the people who make great designs and made those great designs, create it
Engineers can be involved in the manufacturing process. If you’re a concept development engineer that’s making prototypes, you are interacting with the folks that are involved with mass production use cases in that you need to reflect manufacturability in the design of your final part. If you are, by contrast, directly involved with the creation of those manufacturing processes, then the nature of your very job is on that manufacturing line.
“And the trend we’re seeing is this emergence of humongous, gargantuan manufacturing plants of 9, 10 million square feet, where it could take almost an hour to walk from one end to the other. It doesn’t just matter that you have a 3D printer at the factory itself, it actually matters where in that factory you are, because it could take a while to walk that part from one place to another.
“We now see engineers, technicians and point managers alike, all converging on the point of the manufacturing line that needs that critical part and locating a printer as close to that, pushing that printer as far forward into that manufacturing challenge as possible.
“The biggest difference we see is in the role and the response. I talked a lot about the transition of the role and responsibilities of the individual engineer. The reality of the technician’s role and responsibilities change as well, where there’s less time doing the manual processes of clamping, fixturing, programming, doing all the things that it takes to get a successful part out of the CNC mill, and spending more time actually making parts, managing
things from the digital level where those individuals are now empowered to make more parts for more people, solve more problems, which is a great transition to see as well.”
“One of the challenges we’re all facing right now is coordination of distinct supply chains. There’s a small but growing wedge of production parts that can be produced on a 3D printer today, at least in economic and logistically feasible means. The challenge becomes, how do I get the rest of this part or this assembly or this add product produced at the point of need? And the really exciting part and trend we’re seeing emerging out of the pandemic is, manufacturers are by nature parallelizing their supply chains so that more parts are available in distinct, shorter supply chains.
“And while that may be potentially more expensive in the short run, it ends up being far more beneficial for manufacturers in the long run when they have the ability to more flexibly balance load, demand on specific discrete components of their supply chain, and then rely on the flexible components of the supply chain like 3D printing, additive manufacturing to fill in the gaps.
The supply chain, after the pandemic
Will the changes experienced with the supply chain over the last two years continue, or it return to how it operated pre-pandemic?
“I think over the next few years, as we transition from pandemic to endemic, we right size the really critical links of global supply chains, like shipping, trucking, warehousing, and we get to a new point of equilibrium where we’ve got the right resources to solve the right problems in manufacturing. I think we’ll see a sort of asymptotic releveling to something that looked a lot more like what it looked like in 2019.
“I think that said, manufacturers are going to clamp down on the specific use cases where we all mutually have found it’s more beneficial, both from a cost and lead time, to parallelize and have this flexibility. And something that might cost a little more in the short term to spool up, and in fact, things that people are investing in now that you can’t just throw in the garbage can, like in a new factory, we’re going to find new and more powerful ways to use these things and produce products with more flexibility, more customization, and ultimately more acceptance at the end-customer level. And I think those advantages are going to be here to stay and they’re going to be enduring.
Additive manufacturing is influencing the supply chain. At the extreme level, look at the U.S. military and how its supply chains have evolved.
“Even before the pandemic, they had some of the most austere supply chain challenges that you could imagine, needing to get a specific part or bracket somewhere in some desert in the middle of Kuwait where there are no roads, how do you get a part there? And we saw the
military really treat 3D printing almost like, their terminology, not mine, 3D duct tape. I’m making something that’s sort of going to take the form of the object I need.
“In the case of Markforged, they were making really strong parts that conventionally could only be made of metal, but sort of coming in as this, I love that metaphor of this duct tape. The thing that solves the problem cheaply, quickly and efficiently that I can make at any time, at any point where it’s needed with the portability of the printers.”
3D printers can be rugged and work in hostile environments, as the military example shows.
“I did a little science experiment a while back. I actually wanted to see if I could 3D print while driving to a customer location. I was running a little under the gun and I needed to show them a demonstration part. At the time I was living in Los Angeles and I was driving down to Orange County, about a two hour drive down a pretty, I’ll say bumpy Interstate 5 freeway. I hooked the printer up to my car battery. The printers are just so robust, reliable, and it bears mentioning, power efficient, that throwing the thing in the back of my Honda Accord and getting a successful printout was really a no muss or fuss experience. Mileage may vary on the 3D printing on the road, I should probably disclaim.”
Markforged
Recently, the World Economic Forum, in collaboration with ETH Zurich and Fraunhofer IGCV, IPT and IAPT, released a report on the current state of additive manufacturing (AM) and its future. Their goal was to provide a realistic understanding of what AM can deliver today and why some are achieving that potential while others are not, as well as define the most probable near-term future production scenarios and what needs to happen to make those scenarios a reality. Pat Carey, Senior Vice President of Strategic Growth for Stratasys addresses this subject.
Q: What are some of the roadblocks along the value chain that AM can address?
A: According to Carey, additive technology helps in several areas of the value chain including local production, the iterative process, and bureaucracy.
“The ability to produce a part locally is a big deal, especially when we’re all dealing with parts on boats coming from China,” notes Carey.
Also, companies are shifting to a more personal, mass production model that favors additive manufacturing over other manufacturing technologies.
The Stratasys F770 3D printer will build large parts. It features the longest fully heated build chamber on the market and a generous build volume of over 13 cubic feet (372 liters). The system, priced under $100,000, is designed for prototyping, jigs and fixtures, and tooling applications requiring standard thermoplastics.
“I’ve been working with a number of product design firms that were following a traditional process of product design,” notes Carey. “Prototypes were a challenge …. with all the supply chain issues. …. Many of them have switched to using additive manufacturing. They wanted to change their processes, but changing processes in big companies is difficult. …. So, we’re seeing a number of large companies entertain new design processes which include faster iteration or skipping whole steps of iteration. One of the fun complaints I’ve heard from some customers is that the additive product process is faster than their bureaucracy can keep up with. So, it’s interesting to hear that from customers, ‘Pat, your technology is really helpful, but it’s so fast that the paperwork can’t keep up.’”
The recent acquisition of Origin One enables Stratasys to take advantage of its new approach to the additive manufacturing of end-use parts.
Origin One uses Programmable PhotoPolymerization to precisely control light, heat, and force, among other variables, to produce parts with exceptional accuracy and consistency.
The design process has always aligned with the manufacturing process. Designers know in advance whether a part will need to be manufactured through injection molding or machining. And they know the limitations of each process. Now, as designers turn to additive processes, they are beginning to question why they make certain design decisions because additive enables different decisions and approaches.
“The design process is very different and it has to do with both the customization, iteration, design, those three needs are really not separated for a lot of companies right now,” adds Carey. “They’re saying, ‘I can actually do this. I can have an idea and have a part or a product that looks and feels just like it in the customer’s hands in a week,’ which for them is nearly unbelievable.”
Additive manufacturing allows you to skip some or many of the typical steps of iteration.
Traditional manufacturing technologies often require the use
of defined steps for prototyping, depending on the part or object. Prototypes range from the initial stage where it’s a white or gray prototype, to the how-does-it-feel prototype, to the how-does-it-look, how-does-it-fit-into-a-package prototype.
“Some customers were going through all these processes and some of those processes were decades old and they’d always done it that way. Well, the supply chain challenges, COVID challenges, Trump trade wars, all this stuff blew that up.”
The realization that companies could not do what they used to do set in. They had to deliver products to the marketplace. They were forced to change.
“I tell people from a 3D printer perspective COVID’s been great. A lot of choices have been eliminated.”
To get product to market, companies had to do something. “So, we saw people adopt stuff and like, “Wow, this is really interesting. This really works. Why are we doing it the old way?”
Q: What kind of industrialization steps are needed for AM to reach its full potential?
A: Part of the issue is that prototyping has been done on the side. Early versions of 3D printers were standalone systems. To move into manufacturing, they now need to be inline—meaning they need to be part of the manufacturing line.
“And we know the manufacturing line is a complex software and data driven process nowadays. Millions and probably billions of dollars have been spent making these manufacturing lines that way, because we need to know what’s going in and what’s going out.”
For a number of industries, including aerospace and automotive, collecting data on the part and storing that data for warranty or
other issues is a big deal.
Thus, the next steps for the additive industry are the connectivity part--to continue to give the 3D printer data, get data in return, and store that data in a standard format.
“Those are big processes that need to be adapted and a lot of the 3D companies are just starting that.
“Another issue is what I call serviceability. If I go on a factory floor with a printer, I need to match its serviceability with that of all the other products on that floor. And that means either train company operators to fix it or have a response time to fix it, especially if it’s key to a product. If it’s key, the downtime of the printer is a big deal. This is a big challenge for 3D printing.
“Users can go online, depending on the printing company, and find the answer on a blog. Well, that’s not going to work on a factory. So those types of challenges around serviceability, reliability, and then repeatability are some of the challenges around industrialization that we’re seeing the industry take on, … get together and have discussions on.”
The questions to discuss and answer revolve around: Will it make the same part over and over exactly the same like injection molding or machining does?
“I don’t think we need to pave any new ground because we can watch what everybody else in the factory’s done. And to be honest, the customers tell us what we need to do. They say, “If you want to be here, you need to do this, this, this, this, this.” It’s just, how do we adapt to it? And then how do we, as an industry start to agree that this is what we’re going to do.”
Q: Is 3D printing additive manufacturing too disruptive to manufacturing right now?
A: “I don’t think so. A lot of it’s going to be driven by the materials. So, if we’re bringing a material to manufacturing that they already know, nylon is the easiest one to talk about. Also, Polycarbonate. So, no, I don’t think so. We’re seeing this, to be honest, we’re seeing the advantages outweigh the effort, the gap.”
Q: Can additive manufacturing be advanced or developed to the point where it fits in with traditional manufacturing processes, the way the manufacturing people want it to do so?
A: “Yes, but one of the common discussions I have with executives revolves around how it’s not a replacement for traditional manufacturing. You can’t take one out and put AM in its place.
Designing for additive at the very beginning of the process has been a key part of making this technology economically viable. Mass production brings in new challenges. Simply taking an older part and trying to duplicate it on an additive system
Jigs and fixtures are common tools when manufacturing a part. They are also used when a part undergoes secondary processes, such as finishing, and may be known better as masking fixtures. The FDM Fixture Generator lets users 3D print these fixtures. The module came about as a result of a collaboration between Stratasys and nTopology. Users can generate and 3D print custom fixtures with a few clicks.
usually doesn’t work economically. And it doesn’t take advantage of additive.
“That’s a caution I always tell people. But if we start up front, back to the earlier discussion on COVID and how additive helped because we had a time problem, that became a key element. Especially for large companies that introduce products on a monthly basis. When you’re not introducing new products to consumers, they get bored. During the pandemic lockdown, consumers had a lot of time on their hands. So, there was a lot of pressure to introduce new products and companies couldn’t do it with traditional methods.
“That changed the world a little bit and made it an advantage for additive. And I think we’ll see that on the manufacturing floor as well. When we think about automotive, going from making millions of the same car to tens of thousands of the same car. Personalization.
Customization. As a company processes change, it makes additive more favorable, more appealing than in the past. If a company needs to make two million of a part identically, well, we’re not going to compete with an old process for that. But the markets are changing I think, to our (additive) advantage.
Q: What efforts are underway to address the current criticisms of post-production with AM to make that process more efficient and more cost effective?
A: “I think it is a fair criticism. We’ve spent a lot of decades actually, we’re over 30 years old as Stratasys, getting reliable parts out of the printer. And when it was just prototypes, we mostly did sanding and some painting. There was not a lot of thought put into post processing. But now that we’re going into production environments, there’s an expectation of durability and quality. So if I’m a manufacturer, I’m making a consumer device that somebody’s going to have in front of them, in their hand, the quality of the device is part of the brand. And a 3D printed part needs to carry that level of quality.
The expectation’s going way up, and so there’s more focus on postproduction, as well as with some of the newer technologies like powder effusion, DLP as those parts ramp up in production. Post-processing is a big factor because postprocessing can really slow down the additive process and it can either add a lot of value or detract a lot of value. We are, as Stratasys, experiencing a big focus on post processing. It is a fair criticism and it’s a big opportunity in my view.”
Q: What’s your prediction for the future of post processing?
A: “I think there will be many new processes in additive postprocessing. The big trend will be integration with the printer, though. Can I pass information from the printer about the parts to the postprocessing and then customize this?
“Post-processing can be customized. In a lot of cases really, in the old world, it’s just a tank of something, water, glycol, or alcohol to clean the parts. It’s basically a dumb tank. Now we’re starting to see the post-processing process actually gather information and develop information around those parts and be able to pass that information along with the part. So a part goes on an airplane or in a car, it’s possible today to trace back where was that made. Where was it post-processed? What was happening in post-processing?
“And we’re in the polymer space. So heat has a lot to do with polymerization. So what happened heat wise or what happened to the surface? And did that surface make it more or less biocompatible, more or less food grade? All as additive goes into new industries, there’s new sets of requirements, FDA requirements, and so on. Post processing can help or hinder a lot of that.
“I also see a lot more tracking of and storing of the data. I’m seeing control systems put in post processing machines. So rather than being a tank, literally with a drain, it’s actually a smart box that knows what’s going on. We’re starting to see that.”
Q: Could you say that additive is driving digital manufacturing or is additive adapting to digital manufacturing?
A: Carey sees both options. Traditional manufacturing technology is being altered to become more digital, that’s a lot of what efforts such as IoT are about. But additive is inherently digital, so it’s ahead of traditional manufacturing technology.
For Carey, materials are key. “Either metal or polymer, the materials are the most important thing. We’re going to start to see an area where the materials are developed to fit the product. Customers come to us, ‘Can you make a material that looks and feels like this?’ That’s going to start to happen where the end product will drive the chemistry, not here’s ABS now figure out what you can make with it. Before, the material drove the product. Now the product will drive the material and we’ll be able to make materials on the fly or change the materials or affect the materials on the fly. That’s what’s going to start happening. And that will be true digitization.
“And we’ve done some experiments. We’ve had some of these demonstrator systems out there over the last three or four years. We’re able to mix the materials at the point of jetting. And we’re talking to customers who have requirements about putting different materials at different places in a part. Because this place undergoes a different stress and needs more something here or less something there.” And medical is making similar requests.
“We talk to a lot of universities and in the bio space. We get questions such as ‘Can I put down a material that looks like bone, or looks like skin, or looks like cardiac or nerve material?’ We’re starting to see that around jetting.
“Many limitations are being removed. And then the smart customers start to do stuff with it. I tell people, we make a tool. It’s amazing what humans can do with the tool. We don’t make a product, we make a tool that we give to humans and then see what they do with it. That’s what’s going to be cool about 3D printing.
“And we’re starting to see bio materials come in. I’m seeing more and more focus on materials that are sustainably made from current plant-based fibers.”
Q: What do you think is going to be the next phase for AM? Are we going to go back to more technological developments or are we going to continue in more of a business development phase?
A: Carey sees a key trend being ecosystems. “I think a lot of the players are established as we look at the industry. I spent a lot of time in Silicon Valley over the last decade. Many of innovative startups had one or two innovations; they tend to get grouped into multiple innovation companies. And then those multiple innovation companies start to form ecosystems because they can’t innovate any faster and can’t do everything. When I mentioned connectivity, that’s really networking. So, when a printer goes onto a factory floor, it’s networking.
Well, if I need to network my device to somebody else’s, I better have a common language. I better have a common data format that requires an agreement, which is an ecosystem.
We’re starting to see ecosystems. 3D printing is a relatively tiny industry. And to be honest, we’re mostly friendly with each other. And we’re seeing a lot of ecosystems and partnerships develop. It’s kind of exciting to see at this time of a
35-year-old industry, but it’s very small and everybody wants to be successful. And we’ve watched how technologies progressed over these years. I think we can follow that building ecosystems, building standards, agreeing how to do stuff.
“It’s an exciting time right now in additive, we went through the hype period of 2013, 2014. We went through the financial hype period of 2021. And now it’s all out there. We can all see how each other is doing, growing, shrinking. It’s not just about press releases anymore. We can look at each other’s numbers. And I think there will be a period of rationalization in the next six months to a year that will really help to market go ahead.”
Stratasys
www.stratasys.com
3D Platform is the trusted source for industrial-strength, large-format 3D printers. Based in Roscoe, Illinois, USA, the 3D Platform team is focused on driving advancements in technology to innovate, design, and build next-generation equipment for additive manufacturing. Our approach to 3D printing focuses on four clear industry demands:
Scalability and increased throughput from high-flow extruders allows smart manufacturers to shed legacy product development cycles and small-scale models for full-size prototypes and production.
Open market-enabled solutions allow users to go bigger with 16 times the speed of competitors’ extruders for faster printing and exceptionally strong parts.
• Quick-Swap dual extruder heads deliver high quality 3D prints.
Affordability of equipment and materials allows SMB’s and Fortune 100 companies to tailor 3D printing to their needs, and quickly develop new products and bring them to the market.
Robust industrial technology stands up to harsh environments and the excessive demands of rapid manufacturing using the world’s leading linear motion mechatronics, reliable motors, and sophisticated control systems.
•
• Modular design accommodates variable nozzle and filament sizes Nozzle flexibility for fine layer resolutions or faster printing and strength.
To learn more about 3D Platform, visit www.3dplatform.com.
3D Platform 6402 E. Rockton Road Roscoe, Illinois 61073 USA +1.779.771.0000 3dplatform.com
marketing@3dplatform.com
sales@3dplatform.com
CS Hyde Company is your source high performance tapes, polymer films, fabrics, and silicone. For over 20 years we have been supplying almost every industry with performance materials for all types of applications. Our product line is composed of a variety of materials with properties associated with additive manufacturing/3D printing including low friction, nonstick release, and high temperature resistance. As a polymer film supplier of engineering grade thermoplastics and PTFE Fluoropolymers, we have grown to be a premiere source for custom printing surfaces. Common materials include ULTEM® PEI, and Optically Clear FEP tape or film. FDM printers using PEI benefit from a surface with durability and a surface that will hold filament in place and remove cleanly when cooled. Our PEI sheets are also pre-laminated with high temperature 3M™ adhesive that adhere to spring steel or glass build plates. FEP film is a great release material for resin vats found on DLP, Laser, LCD or as a release layer for tensioned “drum” style resin vats. Our custom cutting capabilities allow us to cut these materials to exact dimensions of any build plate or resin tray. Common sizes are available on our online catalog for click and ship availability.
Bring new precision and performance to every stage in your additive machine development with Yaskawa motion control
Rise above the desktop: Shaky, imprecise desktop machines become robust industrial performers with motion control that overcomes vibration, boosts speed and gets you ready for tomorrow's hybrid technologies.
Advance the industry standard: Industrial quality printers benefit from Yaskawa's smooth and precise motion, plus worldwide support that distinguishes your machine in a crowded marketplace.
Restate the state of the art: Top tier manufacturers need new ideas, plus the engineering support to make them work. Yaskawa supplies both, using the latest linear and robotic motion systems and Singular Control to create a seamless, supportable development environment.
Our motion control technology also prepares you for new frontiers in additive manufacturing:
• Robotic systems that produce curvilinear motion for true 3D deposition
• Additive/Subtractive technology which combines the benefits of 3D printing and traditional routing/machining
Yaskawa servos provide smooth, precise motion for additive manufacturing, while the G-code compatible MP3300iec controller can operate any motion device to implement the latest advances in hybrid manufacturing. Couple these with Yaskawa Compass™, our customizable user interface software package, to bring new precision, performance, and creativity to your additive machines.
Zero-Max
zero-max.com
These new Extra-Duty Overhung Load Adaptor (OHLA) models are based on decades of experience solving overhung load issues in the most demanding applications. The new designs have several carefully chosen upgrades, including spherical bearings, enhanced sealing technology, stronger shafts, and a longer profile delivering increased operating life, heavy load capacities, and higher speed ratings.
While the standard OHLA product line is designed to handle high loads at high operating speeds, these new Extra-Duty models maximize performance in the most demanding applications. They provide a solid, permanent mounting surface eliminating premature motor or pump failure due to axial and radial overhung loads on a motor or pump shaft.
They feature these important design enhancements:
• Extended Housing Length for improved load distribution on the bearings, increasing load capacity and operating lifetime.
• Spherical Roller Bearings as standard for the best combination of high load and high-speed capacity.
• Dual Grease Zerks with one grease fitting located above each spherical bearing to apply grease directly into both bearing assemblies.
These new BusWorks NT series remote I/O modules are now UL Listed for Class 1 Division 2 Groups A, B, C, D hazardous locations with volatile substances in the United States and Canada. This certification permits the use of the BusWorks NT series remote I/O modules in environments with flammable liquids, gases, or vapors. The Class I Div 2 certification is often required for electronics deployed in chemical, oil, gas, mining, and other manufacturing facilities. With the higher safety rating, the Ethernet modules can be installed closer to sensors and actuators to reduce installation costs for monitoring and controlling automated machinery. The Ethernet modules have also passed testing for the European ATEX and IECEx Zone 2 safety certification that is widely accepted in many countries globally for explosive atmospheres.
Ryan Ashdown rashdown@wtwhmedia.com 216.316.6691
Jami Brownlee jbrownlee@wtwhmedia.com 224.760.1055
Mary Ann Cooke mcooke@wtwhmedia.com 781.710.4659
Jim Dempsey jdempsey@wtwhmedia.com 216.387.1916
Mike Francesconi mfrancesconi@wtwhmedia.com 630.488.9029
Jim Powers jpowers@wtwhmedia.com 312.925.7793 @jpowers_media
Courtney Nagle cseel@wtwhmedia.com 440.523.1685 @wtwh_CSeel
Publisher Mike Emich memich@wtwhmedia.com 508.446.1823 @wtwh_memich
Managing Director Scott McCafferty smccafferty@wtwhmedia.com 310.279.3844 @SMMcCafferty
EVP Marshall Matheson mmatheson@wtwhmedia.com 805.895.3609 @mmatheson
Follow the whole team on twitter @DesignWorld
DESIGN WORLD does not pass judgment on subjects of controversy nor enter into dispute with or between any individuals or organizations. DESIGN WORLD is also an independent forum for the expression of opinions relevant to industry issues. Letters to the editor and by-lined articles express the views of the author and not necessarily of the publisher or the publication. Every effort is made to provide accurate information; however, publisher assumes no responsibility for accuracy of submitted advertising and editorial information. Non-commissioned articles and news releases cannot be acknowledged. Unsolicited materials cannot be returned nor will this organization assume responsibility for their care.
DESIGN WORLD does not endorse any products, programs or services of advertisers or editorial contributors. Copyright© 2022 by WTWH Media, LLC. No part of this publication may be reproduced in any form or by any means, electronic or mechanical, or by recording, or by any information storage or retrieval system, without written permission from the publisher.
Subscription Rates: Free and controlled circulation to qualified subscribers. Nonqualified persons may subscribe at the following rates: U.S. and possessions: 1 year: $125; 2 years: $200; 3 years: $275; Canadian and foreign, 1 year: $195; only US funds are accepted. Single copies $15 each. Subscriptions are prepaid, and check or money orders only.
Subscriber Services: To order a subscription or change your address, please email: designworld@omeda.com or visit our web site at www.designworldonline.com
DESIGN WORLD (ISSN 1941-7217) is published monthly by: WTWH Media, LLC; 1111 Superior Ave., Suite 2600, Cleveland, OH 44114. Periodicals postage paid at Cleveland, OH & additional mailing offices.
POSTMASTER: Send address changes to: Design World, 1111 Superior Ave., Suite 2600, Cleveland, OH 44114