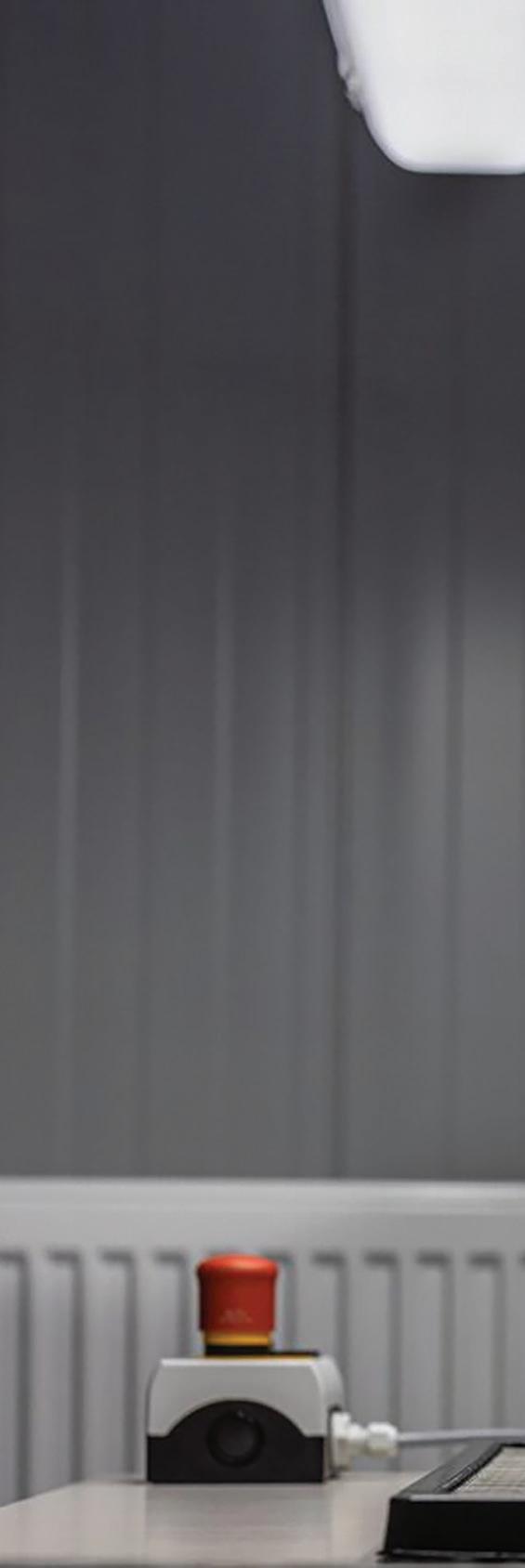
1 minute read
The Robot Report Cobot assists plastic finishers with quality inspection
Like many companies that turn to automation, FMO Surface had difficulty attracting human employees for monotonous yet demanding tasks.
| KUKA
FMO Surface, a family-owned company that specializes in finishing plastics, was founded in 1999 in Lemgo, Germany and employs 75 people. The company’s customers come from a variety of industries, including automotive, electronics, aerospace and mechanical engineering. Manufacturers that produce bicycles and household appliances also make use of FMO Surface’s services.
Challenge
Because approximately seven million plastic bus connectors are laser-marked with eight-digit data matrix codes (DMC) here every year before being installed in controllers, FMO Surface began to automate various related processes several years ago. Companies such as FMO Surface find it increasingly difficult to attract human employees for monotonous yet demanding tasks such as checking DMCs.
It found a job for its new LBR iisy, a collaborative robot arm from KUKA, in bus connector quality control. Because multiple components are marked with a
DMC and are dependent on one another, reliability is of decisive importance for the traceability of an entire module. For this reason, the readability and completeness of the Data Matrix codes require special quality control attention, previously carried out manually with a scanner by human employees at FMO Surface.
“We save an enormous amount of time using the LBR iisy because we no longer have to scan each part individually,” said Tim Hertz, laser department foreman, FMO Surface. “And if the cobot reports a fault, we don’t have to open a cage or stop an entire system; we simply remove the defective part and replace it.” This type of quality inspection helps keep the price of production and finishing down.