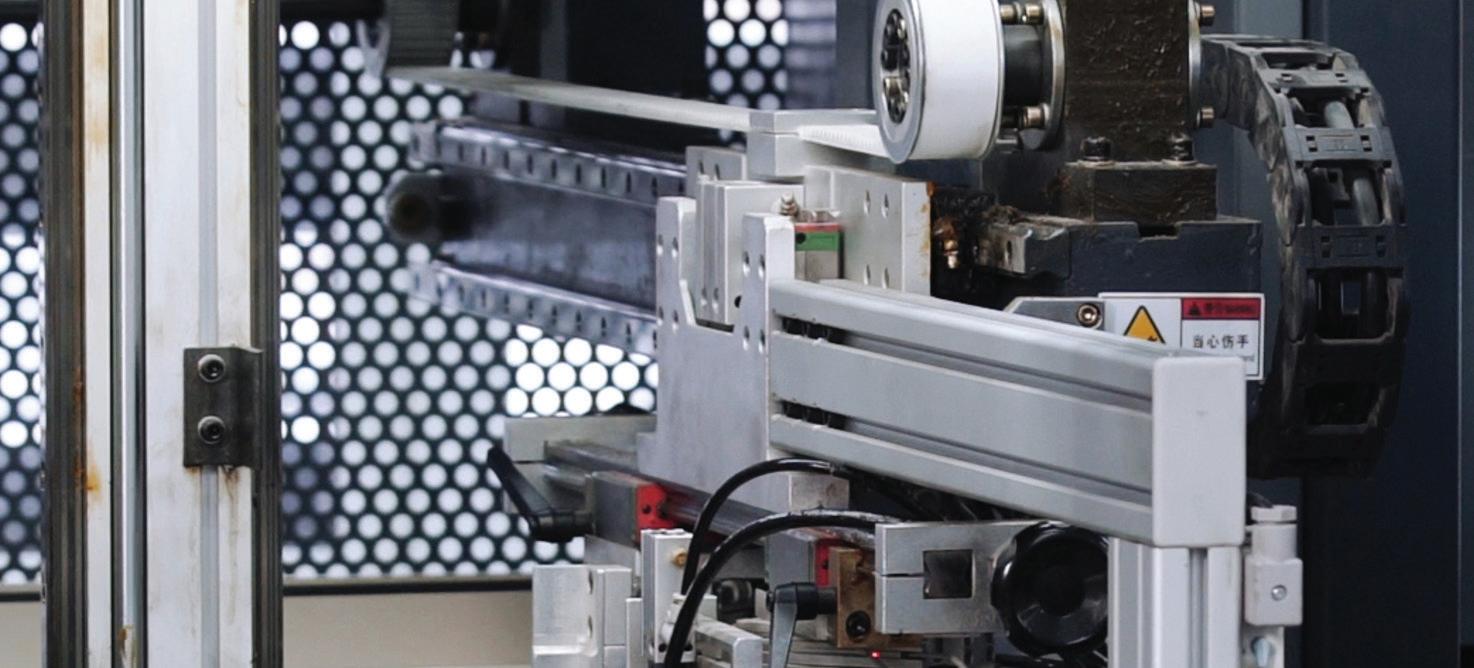
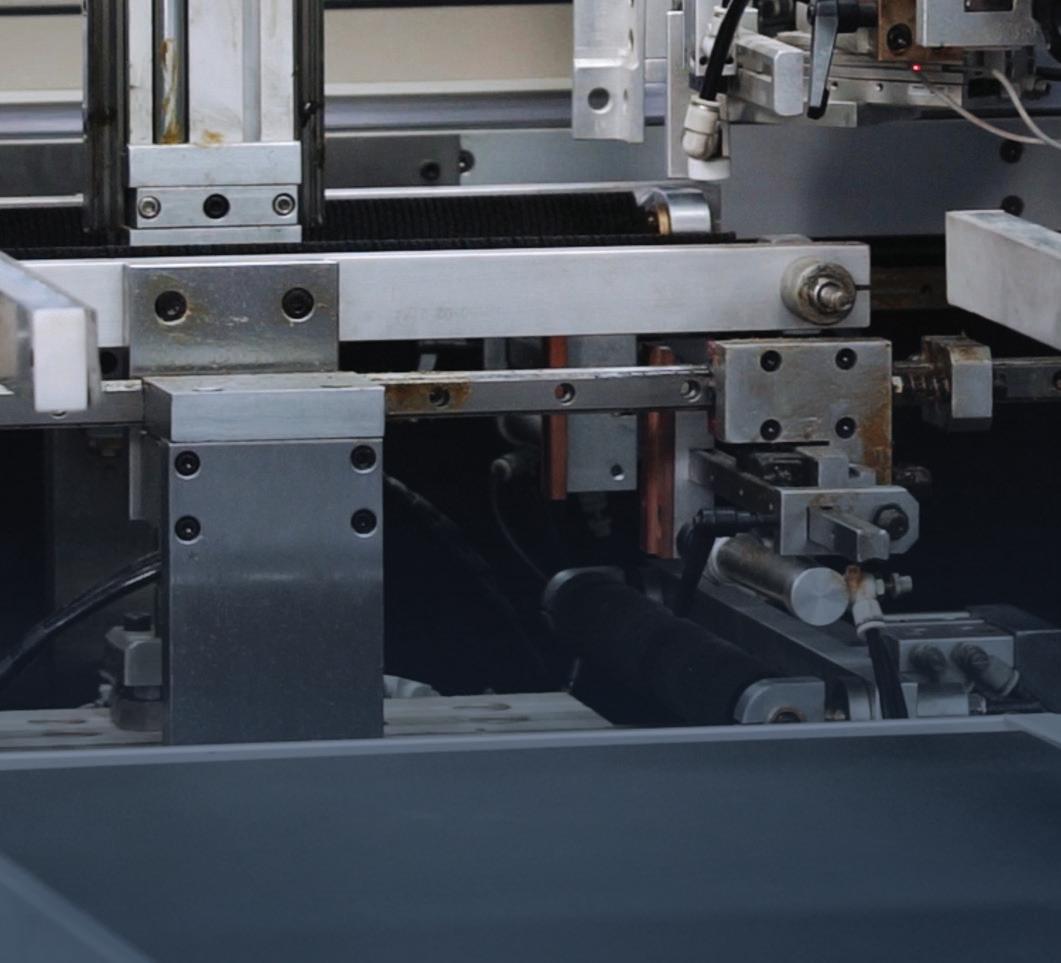
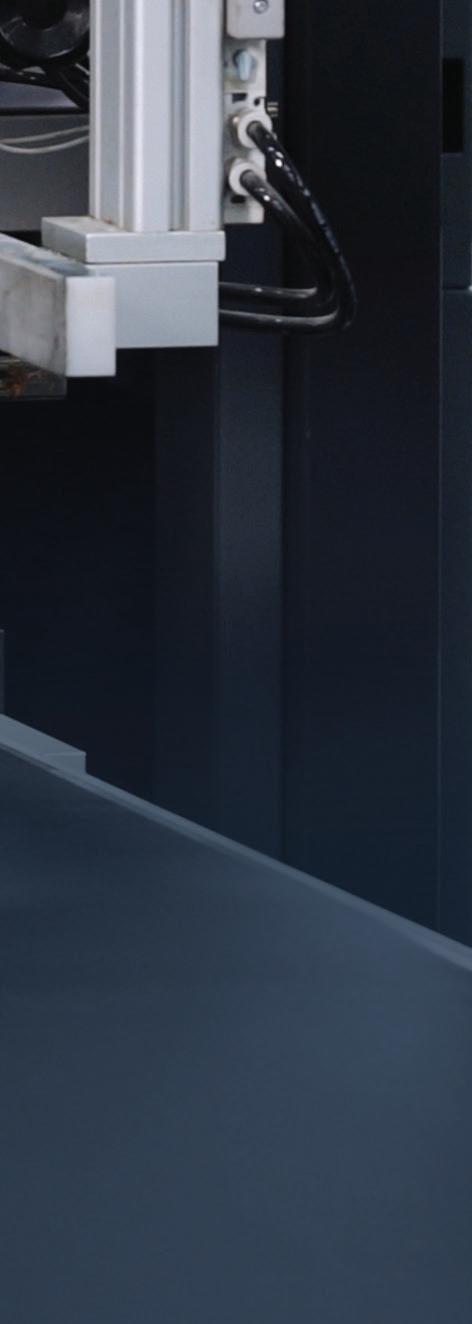
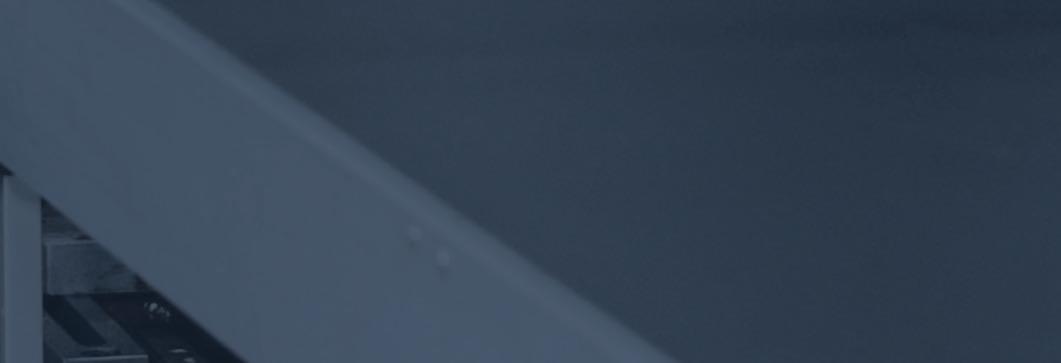

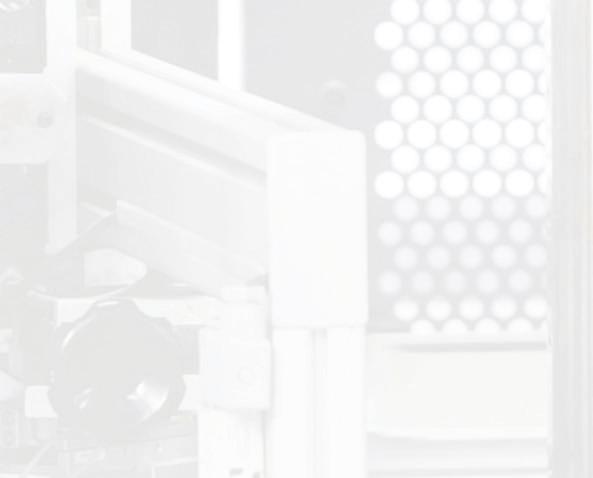
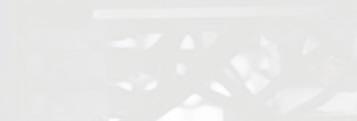
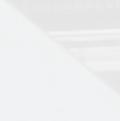
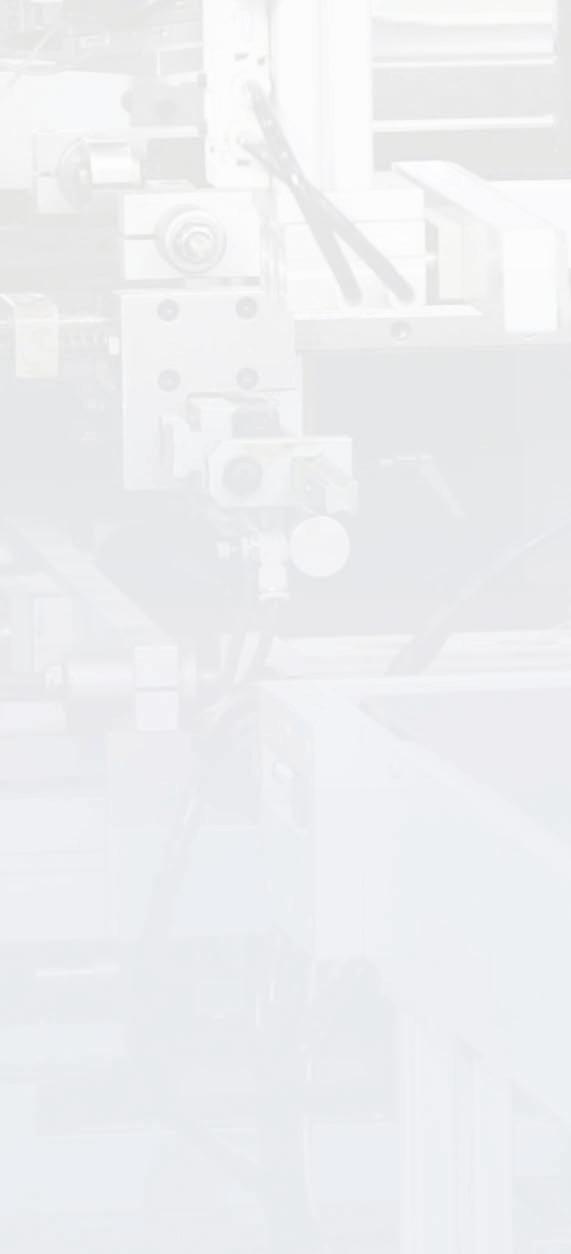
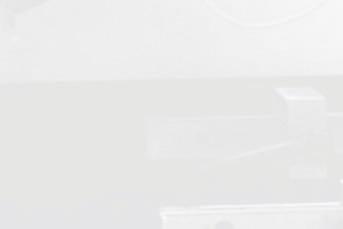
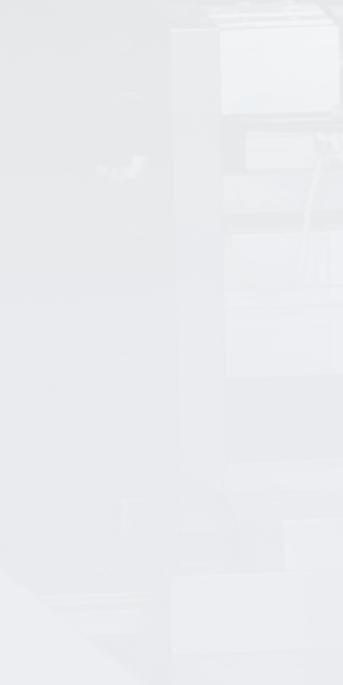
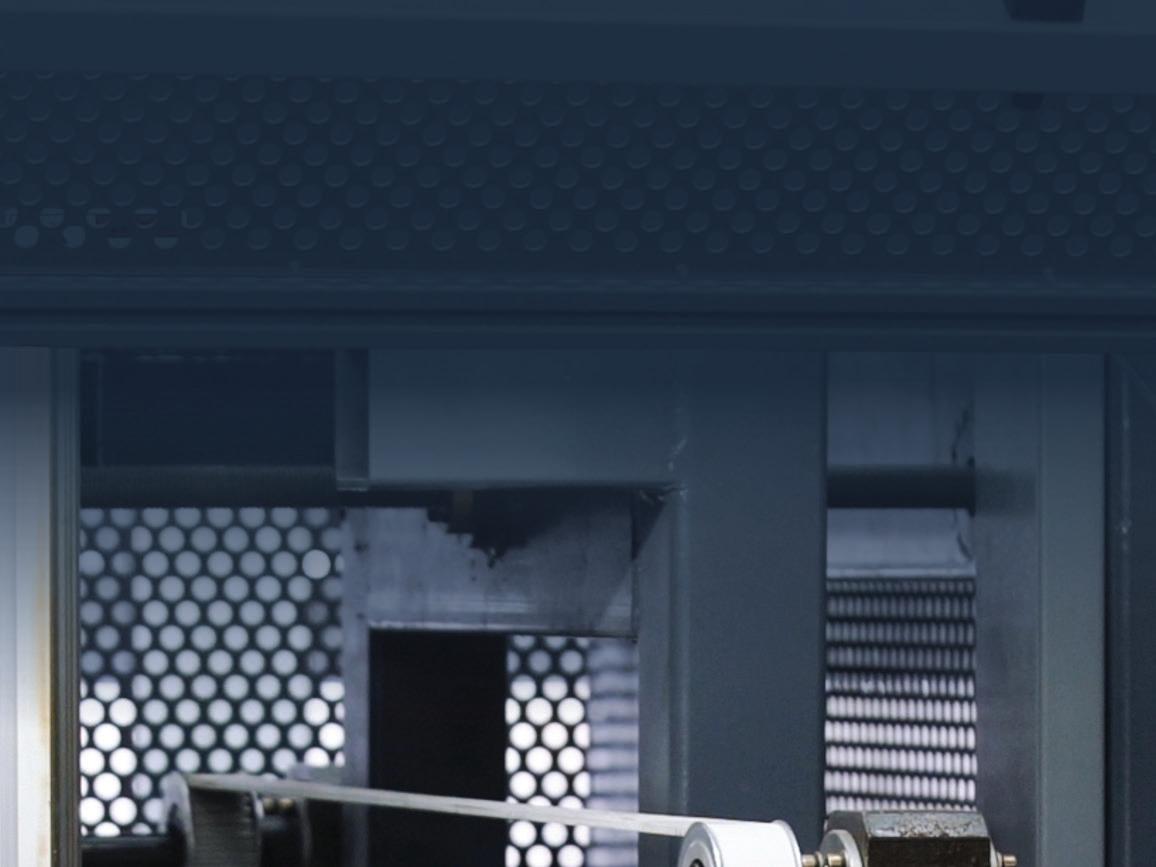

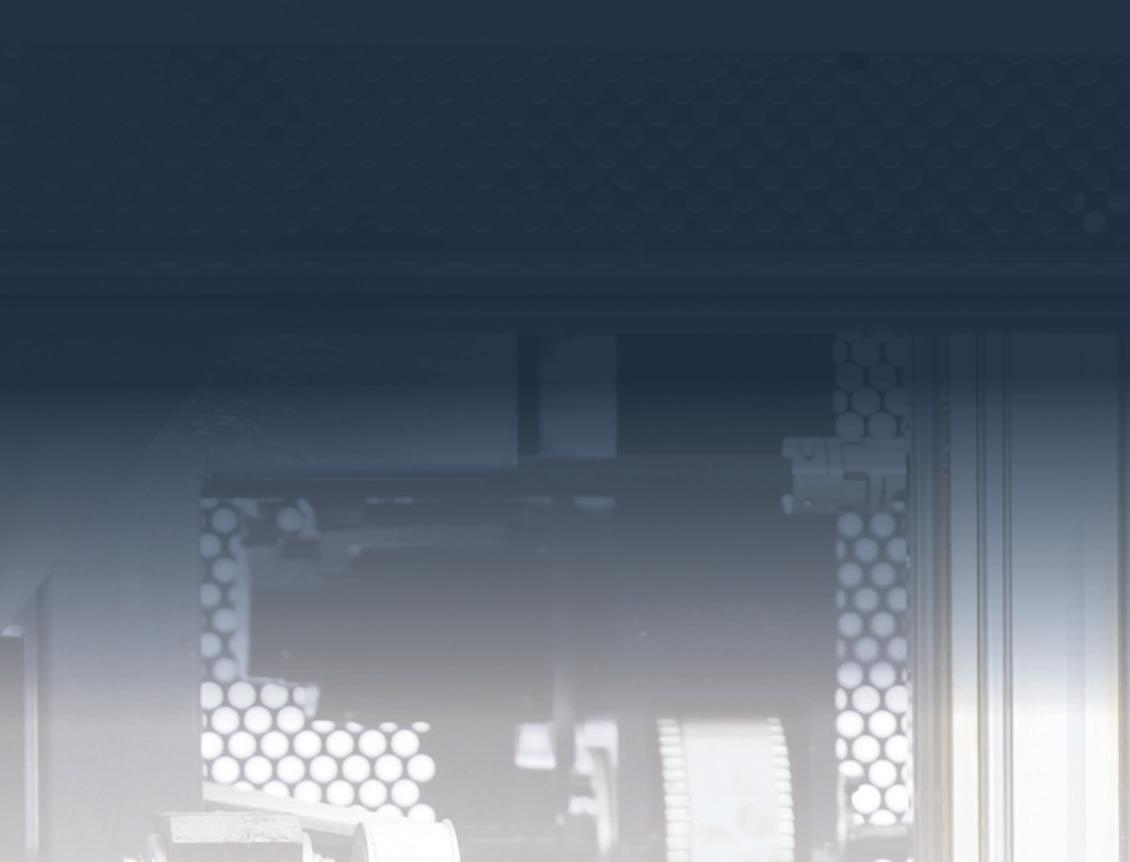
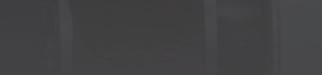

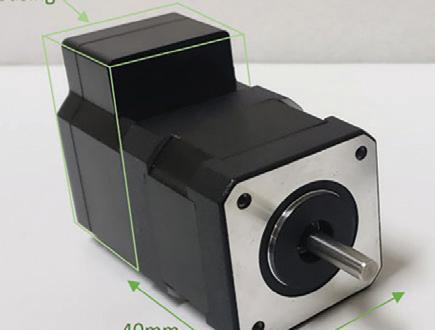
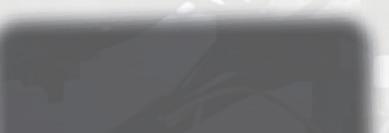
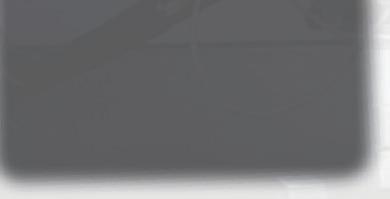
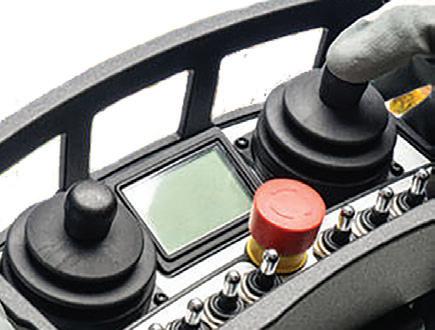
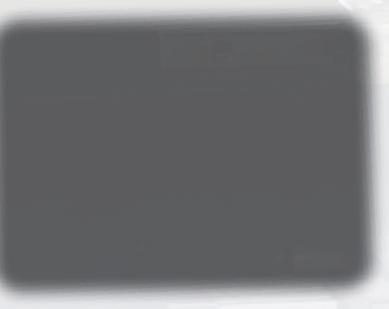
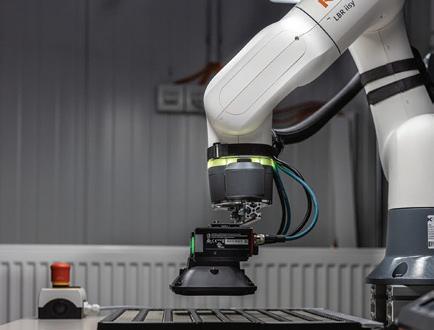



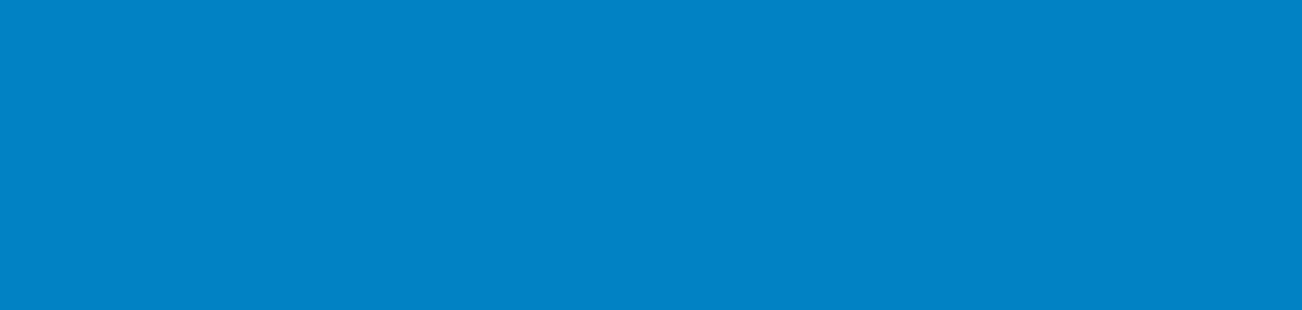
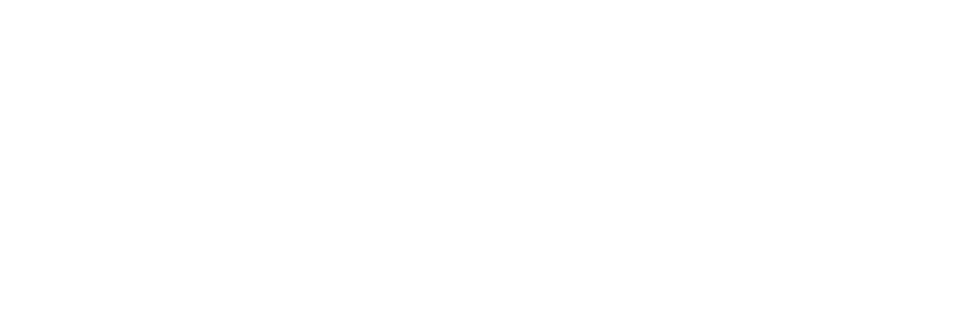



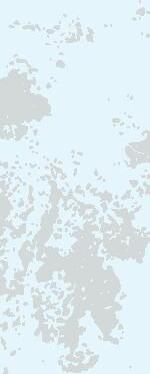
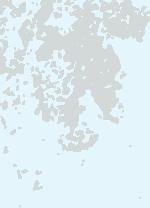



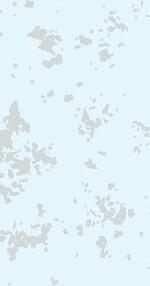
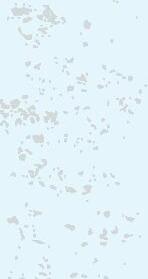







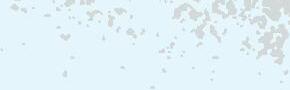



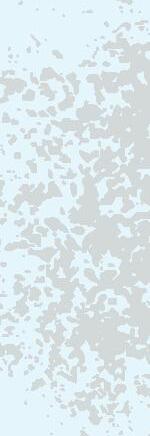




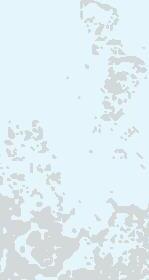



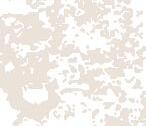
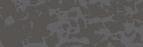

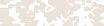
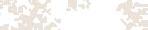


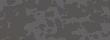



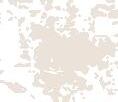











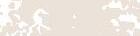
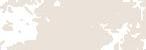



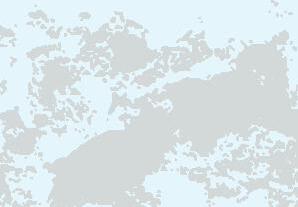
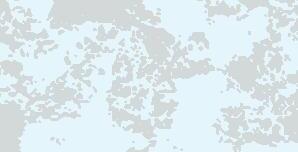


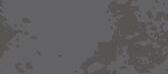



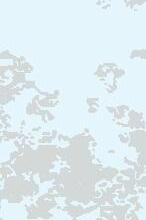

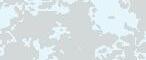
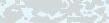






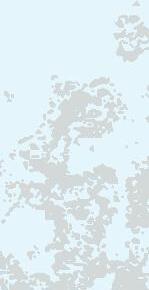





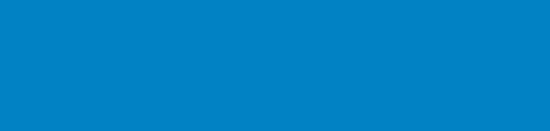

Starting at $659.00 (100W system with cables and I/O breakout)
LS Electric servo systems provide the most requested features — setup wizards, auto tuning, built-in indexers and more — in an extremely cost-effective package:
• 17 standard servo systems from 100W to 7.5kW
• 230 VAC & 460 VAC three-phase input power (230 VAC single-phase up to 2.2kW)
• Low and medium inertia models
• 19-bit absolute encoders available on certain models
• Control via high-speed pulse train, analog speed or torque signal, or internal indexing
• Use with AutomationDirect CLICK, Do-more BRX, or Productivity Series PLCs; or any other host controller
• FREE setup software with Auto-Tuning (AND built-in o-scope functionality)
• Fully digital with up to 1kHz velocity loop response
• 30-day money-back guarantee
• Two-year warranty
LS Electric® MSS Series
Inline Planetary Gearboxes
Starting at $288.00 (96200004)
Perfectly matched LS Electric gearboxes offer easy mounting to the servo motor. Use these gearboxes to increase the available torque or to solve inertia mismatch problems.
• 5:1, 10:1 and 20:1* gearbox models exactly matched to each motor size
• Increase the available output torque by 5x, 10x or 20x*
• Full motor output torque allowed for all pairings
• Reflected inertia of the load is reduced by the square of the reduction ratio!
• Mounting hardware included *15:1 max ratio for 7.5kW system
Engineering leaders are not immune to that constant management mantra of motivate, motivate, motivate. In fact, some managers I’ve known seem to do little more than try to motivate others, with flowery speeches and too-long-toread emails ending in statements like “This is going to be THE YEAR!!!”
But in his book, What to say when you talk to yourself, Shad Helmstetter, Ph.D., goes against the grain in many ways and doesn’t really believe that this kind of motivation works at all. He posits that this sort of encouragement, whether coming from a boss or a coach or a fitness instructor, is always very short-lived, as the energy depends on the person trying to motivate. Thus, it has to be repeated often (and endlessly) — which sure sounds like a recipe for tediousness and boredom.
According to Helmstetter, the real key is encouraging people to motivate themselves. Employees want to believe that they can do more individually and achieve more as a team. But the negative self-talk that we all tend to participate in weighs us down and reprograms our subconscious to truly believe those things. Think of all the things we say to ourselves in our heads (and sometimes to others). “I can’t get the hang of this new system,” “I won’t ever get anything out of these conferences,” “I don’t get along with anyone in that department” ... all of these harmful and negative types of self-talk really do become self-fulfilling prophecies — and they serve to hold back individuals.
Many of us short-change ourselves with the negative way we speak to ourselves. Think about the things you tell yourself, especially concerning tasks that you wrestle with at work. It’s not about having a Pollyanna attitude that isn’t realistic, but it’s more about refocusing and reframing how you see challenging tasks.
If you have coworkers who seem to struggle with their outlook on things, perhaps a casual chat about self-talk (and how you’ve successfully incorporated it into your life), might be a good topic for a one-on-one lunch with them sometime soon. And maybe a copy of Helmstetter’s excellent book, after you’ve read it yourself, might be the thing that really helps that coworker to motivate themself — for years to come. DW
If you’ve driven on U.S. roads in the last few years or so, chances are pretty good that at one time or another you’ve experienced the scourge of blinding headlights.
For the longest time I suspected it was only me that was bothered, that I was simply getting older and my eyes more sensitive to light at night time. But as it turns out, I’m not alone in thinking the lights are too damn bright, as the steady stream of news articles over the past few years and adjacent commentary make clear.
The fact is that headlights have gotten progressively better over the last century. The earliest headlights in the late 19th century when the first automobiles were introduced were lanterns powered by oil or gas. These earliest headlights illuminated the road better than nothing, but they were not that powerful.
Shortly thereafter came electric headlights, which were a marginal improvement. What really revolutionized lighting was the invention of the sealedbeam headlight shortly before WWII. This produced a more focused beam of light that helped illuminate the road better
than anything that had come before. Improvements continued with halogen lighting in the later part of the 20th century, followed by the introduction of xenon-based high intensity discharge (HID) technology and most recently LED headlights. However, that’s just part of the story. The other key factor involves vehicle design itself. As the U.S. automobile market has become saturated with ever bigger vehicle sizes, the roads are now filled with larger SUVs and trucks, all of which have front ends that sit higher o the ground. Consequently, the headlight placement in these vehicles is also higher up, and thus more of the intensity of the light is at eye-level of other drivers on the road, leading to the blinding headlight phenomenon.
But wait, there’s still more! Perhaps the most important factor involves an old federal law on automobile headlights in the U.S. The law states that all vehicles in the U.S. must have both a low-beam and a high-beam headlight. The problem is that the solution to excessively bright headlights lies in so-called adaptive headlight technology,
which uses a single beam that’s software controlled to respond to the surroundings, making the beam stronger and more intense when it needs to be and dialing it back in other instances.
Thus, while adaptive headlight technology has been standard on newer vehicles across the world, it has not been legal to build it into vehicles in the U.S. because of the law requiring two separate beams. The good news is that thanks to the Infrastructure Bill passed last year, there is a provision that rescinds the two-beam requirement and opens the door for adaptive headlight technology to be incorporated in vehicles in the U.S.
The lesson here may be how many di erent factors play a role in solving a problem. From the design of the headlights (including the software used in the new adaptive technology) to the vehicle design itself, to the role of government regulations and the need to revisit them as our technology continues to evolve; it takes a great amount of coordination to get it all right in the end. And save our collective eyeballs. DW
Dim
Follow the whole team on twitter @DesignWorld
EDITORIAL
VP, Editorial Director
Paul J. Heney pheney@wtwhmedia.com @wtwh_paulheney
Managing Editor
Mike Santora msantora@wtwhmedia.com @dw_mikesantora
Executive Editor
Lisa Eitel leitel@wtwhmedia.com @dw_lisaeitel
Senior Editor
Miles Budimir mbudimir@wtwhmedia.com @dw_motion
Senior Editor
Mary Gannon mgannon@wtwhmedia.com @dw_marygannon
Senior Editor
Rachael Pasini rpasini@wtwhmedia.com @WTWH_Rachael
Associate Editor
Heather Hall hhall@wtwhmedia.com @wtwh_heathhall
CREATIVE SERVICES
VP, Creative Services
Mark Rook mrook@wtwhmedia.com @wtwh_graphics
Senior Art Director
Matthew Claney mclaney@wtwhmedia.com @wtwh_designer
Senior Graphic Designer
Allison Washko awashko@wtwhmedia.com @wtwh_allison
Graphic Designer
Mariel Evans mevans@wtwhmedia.com @wtwh_mariel
Director,
Bruce Sprague bsprague@wtwhmedia.com
WEB DEV / DIGITAL OPERATIONS
Web Development Manager
B. David Miyares dmiyares@wtwhmedia.com @wtwh_webdave
Senior Digital Media Manager
Patrick Curran pcurran@wtwhmedia.com @wtwhseopatrick
Front End Developer
Melissa Annand mannand@wtwhmedia.com
Software Engineer David Bozentka dbozentka@wtwhmedia.com
DIGITAL MARKETING
VP, Digital Marketing Virginia Goulding vgoulding@wtwhmedia.com @wtwh_virginia
Digital Marketing Manager Taylor Meade tmeade@wtwhmedia.com @WTWH_Taylor
Webinar Coordinator Halle Sibly hkirsh@wtwhmedia.com
Webinar Coordinator Kim Dorsey kdorsey@wtwhmedia.com
EVENTS
Events Manager Jen Osborne josborne@wtwhmedia.com @wtwh_jen
Events Manager Brittany Belko bbelko@wtwhmedia.com
Event Marketing Specialist Olivia Zemanek ozemanek@wtwhmedia.com
VIDEO SERVICES
Videographer
Garrett McCafferty gmccafferty@wtwhmedia.com
Videographer
Kara Singleton ksingleton@wtwhmedia.com
PRODUCTION SERVICES
Customer Service Manager
Stephanie Hulett shulett@wtwhmedia.com
Customer Service Representative
Tracy Powers tpowers@wtwhmedia.com
Customer Service Representative
JoAnn Martin jmartin@wtwhmedia.com
Customer Service Representative
Renee Massey-Linston renee@wtwhmedia.com
Customer Service Representative Trinidy Longgood tlonggood@wtwhmedia.com
Digital Production Manager
Reggie Hall rhall@wtwhmedia.com
Digital Production Specialist
Nicole Johnson njohnson@wtwhmedia.com
Digital Design Manager
Samantha King sking@wtwhmedia.com
Marketing Graphic Designer Hannah Bragg hbragg@wtwhmedia.com
Digital Production Specialist
Elise Ondak eondak@wtwhmedia.com
FINANCE
Controller
Brian Korsberg bkorsberg@wtwhmedia.com
Accounts Receivable Specialist Jamila Milton jmilton@wtwhmedia.com
Interpower® accessory power strips (APS) incorporate one AC power inlet with multiple AC power outlets allowing multiple device integration. Customizable options include push button, rocker, or guarded circuit breakers, connector locks, and fuses. Voltages range from 10A-15A/100240VAC. Common APS configurations are 10 or 12 Sheet F outlets or an 8 Sheet F and 4 Sheet J outlet combination. In-stock accessory power strips ship the same day!
• World-class customer service 7 a.m. to 6 p.m.
• Value-added services including lengths, colors, & packaging
• No minimum order or dollar requirements
®
Toll-Free Phone: (800) 662-2290
E-mail: info@interpower.com
Business Hours: 7 a.m.–6 p.m. CST
Order Online! www.interpower.com
®
Machine Vision is becoming much more critical in automation applications, especially where robotics is involved. GigE Vision is a global standard communication protocol that has been adopted by machine vision camera manufacturers. Illustration courtesy of Antaira
As robots are increasingly used in various material handling processes, more users are finding that the addition of vision to these robots is enhancing and expanding their capabilities. Vision Guided Robot (VGR) technology has advanced beyond the early days of programmable transfer machines thanks to advances in 2D and 3D cameras, visual servo control, embedded Ethernet networks, and increasingly more sophisticated software including AI.
Advances in RGBD cameras — composed of a standard RGB camera and a depth sensor — have received considerable attention lately because of their ability to quickly acquire 3D models of the environment and to estimate the camera pose in a low-cost way.
Empowering a robot to “see” allows it to precisely and consistently differentiate, pick, sort, move, weld or assemble
various parts no matter their complexity. For instance, a multiple-step manual welding task on an automobile assembly line might take ten “blind” robots to perform since each part must be mounted in place before every weld. However, this same multi-step welding process can be done with a single VGR, since its camera can precisely align the different parts in place without human assistance.
Flexibility is another huge benefit of VGRs. As with a machine vision system on an assembly line, a VGR uses intelligent processing to give it instructions. A slight alteration to the code allows the same robot to perform entirely different tasks, i.e., switching between products and batch runs, with no mechanical adjustments.
And then there is safety. With VGRs, factories can significantly reduce the risk of on-site accidents. A vision-
guided forklift inside a warehouse, for example, will sense obstructions along its pre-programmed paths and avoid contact with people or objects while precisely selecting items o pallets to meet customer orders. At Amazon, for instance, robotic material handling “cobots” (collaborative robots) safely work directly alongside humans. The Amazon Sparrow robot uses vision and a robotic arm and is able to pick up a new item and deposit it on a metal chute every three seconds, handling more than 1,000 items per hour.
To add vision to a robot, one or more cameras are needed. One is mounted on the robotic arm, serving as the machine’s eye. Other cameras are installed in strategic locations in the working cell to capture more visual data. Adding these static cameras will compensate for the limitations of the arm-mounted camera. Careful attention must be given to ensure the camera and lens has the proper resolution, frame rate, and depth-of-
field required for the application at an acceptable cost. Low-cost GigE Vision cameras are preferred since they use standardized, o -the-shelf Ethernet cables and components, while eliminating the need for frame grabbers.
A major trend today is to purchase VGRs already equipped with a vision system supplied by the robot manufacturer. This translates into faster adaptation into a production line, lower costs, and more responsive technical support from a single manufacturer.
Whether the vision system is installed by the end-user or the OEM, it will require an industrial Ethernet switch to create an embedded Ethernet network within the robot. Ethernet allows the individual robot parts to communicate with each other and is suitable for VGRs because Ethernet can handle image data. High port-count Industrial Gigabit Ethernet switches for robots can make the networking of Ethernet nodes uncomplicated.
Space inside a robot is always a limiting factor. A compact DIN-rail design
Interpower® accessory power strips (APS) incorporate one AC power inlet with multiple AC power outlets allowing multiple device integration. Customizable options include push button, rocker, or guarded circuit breakers, connector locks, and fuses. Voltages range from 10A-15A/100240VAC. Common APS configurations are 10 or 12 Sheet F outlets or an 8 Sheet F and 4 Sheet J outlet combination. In-stock accessory power strips ship the same day!
• World-class customer service 7 a.m. to 6 p.m.
• Value-added services including lengths, colors, & packaging
• No minimum order or dollar requirements
Antaira
fiber Ethernet switches are IP67 rated for harsh industrial environments including resistance to moisture, dust, vibration, and shock.
| courtesy of Antaira
Toll-Free Phone: (800) 662-2290
E-mail: info@interpower.com
Business Hours: 7 a.m.–6 p.m. CST
Ethernet switch can easily fit next to a power supply, contactor, or relay. Power over Ethernet (PoE, PoE+, PoE++) is available on most to uncomplicate the connection of cameras and other components. In addition to multiple Gigabit Ethernet ports, industrial switches also o er SFP slots for fiber optic connections. Fiber is impervious to electronic noise, so the SFP slots may be useful in running long-distance communications between the robot and a remote higher-level controller. While the industrial switch’s remaining Ethernet ports are able to collect data from various components in the robotic cell.
These Ethernet switches are built industrial-grade to withstand harsh manufacturing environments. They
are housed in sturdy IP30-rated metal cases and can be trusted to handle high levels of vibration, electronic interference, and wide temperature swings. DW
Antaira Technologies
www.antaira.com
(Source: Hanry Martel, Field Application Engineer, Antaira Technologies)
Fortress Technology’s supermarket-spec metal detector is sensitive enough to adapt to the fine oil and sugar tolerances on the honey roast nut line.
Most snack producers opt for gravity metal detectors. With 15 Fortress Vertex snack inspection systems integrated with multi-head weighers in its Liverpool factory, global nut supplier Trigon Snacks is no exception. Yet, for its latest coated honey roast nut production line, the sustainable nut specialist selected a custom linear Stealth metal detector with an innovative retractable conveyor reject system.
Processing 7,000 tons of nuts annually from its British Retail Consortium A-grade and RSPO certified facility, Trigon Snacks supplies a wide range of nuts and snacks to the licensed trade, retailers, and food service operators. Marketed under its own brands, and retailer own-labels, for its new honey roasted nuts line the company commissioned a highly sensitive conveyorstyle metal detection concept to ensure compliance with global retailer and regulatory standards.
Stringent retailer COPs specified that as “naked nuts” the new honeycoated range must be inspected for metal contaminants prior to own-label packaging. Additionally, Trigon required a supermarket spec metal detector that was sensitive enough to adapt to the fine oil and sugar tolerances and meet the regulatory requirements of every geographical market they are sold in.
For logistical reasons, a small-footprint, wide-head Fortress Stealth metal detector engineered to inspect the fried, dried, and seasoned nuts on a
conveyor before entering the chute and falling into the one-ton sacks, was the most viable and accessible option.
Screening 32 tons of honey roasted nuts daily, space limitations were a key driver to the design, said the company’s lead engineer Mark Grieve. “Being located on a mezzanine floor, we commissioned a wide head yet highly sensitive metal detector with a specially adapted linear conveyor system measuring just 40 cm wide.”
Factoring in the conveying and reject system was critical to guarantee reliable operation and avoid false readings. Given the tight footprint, a custom solution was the best way to ensure that metal detector performance was not compromised.
The low-profile nuts combined with the inspection speed meant that a kicker would be incompatible. It is also virtually impossible to isolate and divert contaminated products with
naked products. With insufficient space to accommodate a flap style reject, Fortress instead engineered a clever and efficient retracting band conveyor and reject mechanism.
The metal detector which sits at the front of the conveyor calculates precisely how long any contaminated nuts will take to reach the end of the conveyor band, communicating via the metal detector control system. The belt then smoothly retracts back on a sliding rail rolling the rejected nuts into the dedicated bin located beneath the conveyor, resuming its inspection position in just seconds.
To-date, Trigon reports zero false rejects on its new honey roasted nut line, upholding the company’s longstanding sustainable, ethical, and traceable principles. Despite admitting he was slightly apprehensive by the compact dimensions of the entire system, Mark corroborates that it has already proved itself to be a reliable and easy to use machine.
Hourly manual tests are the only reported source of daily waste. The lead engineer estimates this to be less than 0.05% of the total production, well below the food manufacturing average which on some lines can reach double figures.
From a sensitivity perspective, the metal detector is exceeding expectations identifying ferrous and non-ferrous particles smaller than 1.0 mm and stainless-steel particles under 1.5 mm. This level of sensitivity can be attributed to the low-profile metal detector head.
Affirming the importance of customizing the aperture, Eric Garr, North America Regional Sales Manager commented: “Aperture size is critical to optimal operation. Customizing the aperture around the product being inspected is one way to ensure the metal detector will perform to optimal levels. Additionally, integrating a conveyor system, fully assembled and checked, is another failsafe way of making sure a producers’ stringent sensitivity requirements are not compromised.” DW
Fortress Technology | www.fortresstechnology.com
WHITTET-HIGGINS manufactures quality oriented, stocks abundantly and delivers quickly the best quality and largest array of adjustable, heavy thrust bearing, and torque load carrying retaining devices for bearing, power transmission and other industrial assemblies; and specialized tools for their careful assembly.
Visit our website–whittet-higgins.com–to peruse the many possibilities to improve your assemblies. Much technical detail delineated as well as 2D and 3D CAD models for engineering assistance. Call your local or a good distributor.
Until now, many users have shied away from the e ort required to introduce autonomous guided vehicles (AGVs) and autonomous mobile robots (AMRs) into their processes. Project durations are often several months, and the areas of application in the facility must be equipped with marking strips, reflectors or mirrors. Afterwards, specialists must manually train the mobile units to e ectively navigate their environment.
With the ROKIT Locator software, mobile robots can independently determine their position. Users no longer need expert knowledge or additional infrastructure to commission a mobile robot. Locator allows mobile robots to determine their position and orientation in any environment, simplifying the automation of intralogistics tasks in industry and trade. Locator is compatible with various industrial controllers and laser sensors on the market and is suitable for mobile units of all sizes and drive types.
Locator enables the robots to evaluate the signals from a laser sensor in the vehicle and convert them into coordinates in space.
No permanently installed aids, such as markers or reflectors, are required for orientation and position determination. Users only need one click to start up the system and familiarize the unit with its surroundings in a onetime orientation trip. An intuitive user interface based on 3D technology is provided for this purpose. The software maps an initially unknown environment and automatically creates a map.
Locator stores this map on the vehicle itself, or optionally on an on-site server component. If several mobile units are used, they all access this map. Afterwards, immediate localization is possible without initial knowledge.
If a vehicle detects a change in the environment, such as when setting up a new storage location, it sends this information to the server,
which automatically updates the map accordingly and sends it to all the mobile units in the fleet. Mobile units purchased subsequently with the Locator take over the server data when they are put into operation and can drive off immediately.
The Locator can be used in various vehicle types, industries, and applications. The software is independent of the hardware used by a vehicle manufacturer. As an encapsulated function block, it fits into numerous control systems and supports a wide range of laser sensors, including safety lasers. DW
Bosch Rexroth
www.boschrexroth.com/en/ us/products/product-groups/ assembly-technology/topics/amr/
Turn your design challenges into next-generation, marketleading medical devices with our extensive manufacturing capabilities and engineering expertise. We have facilities in Fremont, CA and Santa Ana Sonora Mexico.
HydraForce, Tan Delta Systems, and Elevāt have developed a way to eliminate the most common causes of o -highway machine downtime. The solution is composed of di erent parts, a mobile machine telematics solution from Elevāt that seamlessly incorporates with manifold assemblies using HydraForce cartridge valves and Tan Delta oil conditioning sensors.
The integrated solution provides a centralized portal along with email and text alerts providing fleet operators with remote monitoring, control, and optimization capabilities for field-deployed assets.
The solution supports remote diagnostics, predictive maintenance, live updates, and proactive telematics reports. The interface is easy-to-use with fast access to data. It reports in a clear format so issues can be addressed before they impact machine operation.
The Tan Delta oil conditioning sensors provide operators with machine operational data and deliver custom alerts to inform the operator or owner when hydraulic fluids require maintenance. The combination of an electronic controller architecture with telematics provides multiple benefits to users, including real-time data and ongoing alerts of oil conditions. The reported information will prevent excessive wear of hydraulic components and catastrophic failures that can occur
when machines are in operation, thus, leading to increased productivity and reductions in machine downtimes and maintenance costs.
Through accurate monitoring of oil health, maintenance scheduling can also be optimized as equipment is serviced only when required, and operators can rest assured that any unexpected changes in the oil condition will be immediately detected and reported. This can also extend the operational life of equipment and overall machine health, as optimal oil conditions prevent unnecessary wear and tear. DW
Elevāt | elevat-iot.com
Four new high resolution, high repeatability XY Alignment Stages, the AU200120x120 Alignment Stages, feature 120 mm (4.724 in.) of travel in both the X and Y axes. These low profile 87 mm (3.425 in.) high XY stages, have a 188 mm x 188 mm (7.401 in. x 7.401 in.) open aperture. Easy integration of tooling and fixtures is facilitated through a precision series of threaded mounting holes.
The AU200-120x120-01 XY Stage is stepper motor driven, featuring a resolution of two microns when using a 10 micro-steps-per-step micro-stepper motor driver and one micron repeatability. The AU200-120x120-02 Stage is supplied with threephase brushless servo motors and quadrature incremental encoders, and AU200120x120-03 has DC servo motors with quadrature incremental encoders. The two closed loop servo motor options o er greater resolution, repeatability, positional accuracy, higher travel speeds, and greater throughput. The AU200-120x120-04 has the knobs on the stepper motors replaced with quadrature incremental encoders for position verification.
Typical applications include: alignment, inspection, testing, scanning, laser drilling, machining, semiconductor handling, sampling, assembly, and optical applications in industrial, medical and research applications. The AU200-120x120 alignment stages can be ordered as a complete plug-and-play system with compatible motion controllers with PC interface, joystick and keypad. DW OES
This series of waveguide frequency multipliers addresses 5G, test-and-measurement, mobile and satellite communications, radar systems, research and development, and weather and earth observation applications.
The series of in-stock, waveguide frequency multipliers covers 26.5 GHz to 110 GHz, including popular mmWave waveguide bands: Ka, U, V, E and W.
The waveguide frequency multipliers are engineered with GaAs and GaN MMIC semiconductor technology for lower conversion loss. They provide output power from +10 dBm to +20 dBm. They feature DC voltages from +6 Vdc to +15 Vdc and allow input frequency multiplication ranges from two times to six times the output.
The frequency multipliers also feature female SMA connectors and offer efficient performance in a small package.
The new line ensures reliable, all-weather performance. They operate at temperatures from -40 to 176 degrees Fahrenheit, under exposure to 95% relative humidity, and up to an altitude of 10,000 feet. They are tough and compact with military-grade, gold-plated aluminum waveguide package designs. DW
Fairview
The food industry is booming — especially the fresh food business on the Internet. More and more fresh and processed foods, as well as ready-to-eat meals and convenience products, are being ordered online and must be produced and packaged with speed, e ciency, and tight control of hygienic conditions to maintain food quality.
This calls for ensuring that food and packaging technology is as agile and responsive as the front-end digital Internet technology driving growth. Automation and robot technology are, therefore, increasingly being used in logistics and warehousing for food and packaging companies. However, adding this technology only makes sense if the degree of automation can be adapted to the specific requirements of the company, enables a strong return on investment (ROI), and supports growth strategies.
The newest generation of smart, open automation platforms, like Bosch Rexroth’s ctrlX AUTOMATION, combine machine control, the IT world, and the Internet of Things (IoT), using fundamentally new, open software architecture. The ctrlX AUTOMATION platform includes advanced controller and drive hardware components, stateof-the-art software technologies for implementing IoT, artificial intelligence, security, and connectivity solutions for all PLC and motion tasks.
The platform’s foundation is its Linux realtime operating system, which is considered the most stable and secure of its kind. Thanks to the container technology of the operating system, all functions and applications can be mapped with separate apps and combined as desired.
The ctrlX CORE controller system used in CIMCORP’s robot solutions combines compact size and lighter weight with Linuxbased multicore technology that breaks down the boundaries between embedded system platforms and drive-based technology.
Platforms like ctrlX AUTOMATION are taking a new, smartphone-inspired approach to programming automation functions. Just as society now uses apps to individually adapt smartphones to a user’s needs, automation OEMs and end-users can now do the same.
O ering both versatility and scalability, the ctrlX DRIVE system covers both simple single-axis applications and complex multi-axis machine systems, enabling faster implementation of coste ective individual solutions that grow as requirements evolve.
Machine builders can choose apps from the automation platform provider and use apps from third-party suppliers or even apps created by OEMs or end-users in the food processing and packaging industry, thereby expanding the range of options supported to meet specific and unique operational needs. Existing code can also be integrated as an app for real-time and non-real-time applications. There is a free choice of programming language; C++, Python, Java, and many more are supported.
How fresh food automatically has a longer shelf life
A leading supplier of e-commerce intralogistics technologies has upgraded its robotic technology to leverage multiple ctrlX AUTOMATION capabilities. CIMCOROP
MCORP’s robotic material handling systems for food processing and logistics operations, like this gantry robot, use the advanced capabilities of the ctrlX AUTOMATION platform to accelerate processes in order processing and shipping.
GROUP has developed robotic solutions for order processing and warehousing in the food and beverage, retail, e-commerce, fast-moving consumer goods (FMCG), and postal services sectors. With CIMCORP’s robot solutions, companies from the food industry and other segments can specify and accelerate processes in order processing and shipping. For fresh food, this means that perishable products reach the market faster and have a longer shelf life, leading to less food waste.
The company was an early partner and adopter of the ctrlX AUTOMATION platform and helped actively shape a specific solution for intralogistics. The core component here is the gantry robot used in various applications in their operations.
According to Jani Tuomola, Head of Machine Development at CIMCORP, the company already had a close business relationship with Bosch Rexroth, so they were well prepared to transition to ctrlX AUTOMATION.
“Bosch Rexroth had previously supplied control systems to CIMCORP, and we were always very happy with the quality of the products and the service and support o ered,” he said.
CIMCORP realized multiple benefits from using the new platform as the automation controller for its gantry robot. The control cabinet space was reduced by 30%, and the arrangement of the control cabinet components was optimized to save space compared to the previous system.
The open control system for integrating IoT and security enabled CIMCORP to implement easy connections to logistics software. CIMCORP also uses the ctrlX CORE control platform, which is integrated into the drive in a space-saving manner, and the ctrlX MOTION software for Cartesian robots DW
Bosch Rexroth
www.boschrexroth.com
Whether you need a variable-speed AC, a high starting-torque PMDC, or a zero-maintenance brushless DC gearmotor, we’ll help you find the right solution for your application.
.
If you’ve got questions, we’ll find the right solution.
Cryogenic measurements of the multi-channel RF cable Cri/oFlex-3. Flexible cables are terminated with SMA connectors. The measurements were performed at frigid liquid nitrogen temperatures.
The Background Imaging of Cosmic Extragalactic Polarization Project (BICEP) has been ongoing for several years and is now seeking solutions for a hardware upgrade to its telescope’s sensitivity as the project digs deeper into the cosmos to learn more about the origins of the universe. That’s why Delft Circuits, a maker of cryogenic cabling solutions, will join the BICEP project in Antarctica, supporting NASA’s Jet Propulsion Laboratory (JPL) at CalTech and other project partners.
A team at JPL is pioneering a new way to scale the number of detectors on the high optical frequency receivers
The multi-channel Cri/ oFlex-3 cables with vacuum feedthrough. The connector blocks and the flexible part of the cables are shown. Similar cables are being used in the BICEP project.
of the telescope array. The team at the Jet Propulsion Lab has determined that advanced cables made by Delft Circuits will be installed in the telescope’s cryostat as part of its new camera. The team will also replace the telescope’s sensors with new thermal kinetic inductance detectors (TKIDs), which are superconductive detectors leveraging the properties of quantum mechanics. The infrastructure requirements of TKIDs, and the techniques used to measure them, are extremely similar to what is required in a quantum system. Once the new equipment is installed, the experiment will determine if the
frequency multiplexing enabled by this new technology will allow for the necessary scaling of the telescope’s detectors to greater sensitivities.
“I was very happy to find Delft Circuits, which was able to meet our stringent requirements for transmitting microwave frequencies, flexibility, and cryogenic performance in a single cable. This makes my work considerably easier,” said Lorenzo Minutolo of Caltech and NASA’s Jet Propulsion Laboratory a liate. “The cables perform well and remain flexible at any temperature. This is beneficial for us because they make it much simpler to
A team at JPL is pioneering a new way to scale the number of detectors on the high optical frequency receivers of the telescope array.
assemble the hardware we need for this Antarctica upgrade. We can therefore devote more time and resources to other aspects of the experiment, which helps us reach our objectives faster and at a reduced expense.”
The Cri/oFlex multi-channel and RF cryogenic I/O cables, which will be used inside the BICEP Array telescope, are durable and flexible rather than rigid like the alternative. This provides users the opportunity to design and test multiple prototypes in their process while reusing the cables over and over for each di erent iteration. This had not been possible before, thus providing significant value for users in terms of cost and setup time.
“Our product is the only cable capable of providing microwave
transmission capability in a flexible cable that performs in cryogenic conditions. We are very pleased that scientists of this caliber see value in this 3-in-1 combination we’ve developed,” said Kiefer Vermeulen, Research and Development Engineer at Delft Circuits. “Users can now accomplish what used to be weeks of setup work in only a couple of hours. We consider it an important milestone in our development to be trusted by the famous BICEP project, in conjunction with so many distinguished scientists and research partners. This is a proud day for our team.”
background using transition edge sensors. TKIDs will replace those sensors, and their performance will be validated by comparing their results with existing maps produced using the old technology. If successful, the experiment will validate TKIDs as a viable technology for future missions.
Del Circuits del -circuits.com
Trenton is a manufacturing facility focusing mainly on manufacturing parts for machines and tractors used for agriculture.
Trenton is a manufacturing facility focusing mainly on manufacturing parts for machines and tractors used for agriculture. Trenton’s Giordano Cecchini explained the benefit of having VICIVISION measuring machine involved in the process of producing parts at their facility.
“A company like Trenton, with its good reputation, is a real landmark in this area. Most of the manufacturing is done in-house, and we take care of many di erent client requests,” said Cecchini.
Using VICIVISON Measuring Machines enables them to be one step ahead in a competitive market. Cecchini said. “In terms of production and quality, we always try to have the best equipment available, and this machine can be used to carry out inspection on an entire line.”
The accuracy and simplicity of the VICIVISION Measuring Machine allows Trenton to better prioritize its time to more important tasks for its operational needs. Trenton uses an M2018 Techno with a Touchprobe to measure the many di erent parts they make in their manufacturing line.
“We can produce parts up to 1500 mm in length and inspect them on the Vici machine using the Touchprobe to measure keyway slots and planes. This machine measures parts 2000mm in length, and 180mm in width, giving Trenton the versatility they need in measuring the mechanical components they create,” Cecchini said.
Investing in a VICIVISION machine comes from the company’s decision to combine quantity and quality within production. That’s the focus that makes Trenton a cutting-edge company, capable of manufacturing many parts, from facing and centering to grinding.
Catching inaccuracies early can reduce the amount of waste, therefore saving a significant amount of time and money. Trenton’s Quality Control team said that it helps to know that they are starting production o on the right foot, especially with such a short setup time.”
They also explained that users can measure a part in 93 seconds, and the results indicate the validity of the part being measured. The tolerances for each measurement are defined by either a green or red line indicating the accuracy of the measurements for the product produced. Catching inaccuracies early can reduce the amount of waste, therefore saving a significant amount of time and money.
Trenton has had the Measuring Machine for a year, and over time they have created many new programs giving them the ability to increase the number of parts that are inspected. This intuitive machine allows for innovation in the process of the entire production, and with new technologies, it means that Trenton is better able to anticipate
its customer’s needs.
As Trenton continues to manufacture the many di erent parts in their production line, they know the decision to have this Measuring Machine involved in the process is a great investment that ensures e ciency and accuracy in making quality products. DW VICIVISION
www.vicivision.com
As Trenton continues to manufacture the many di erent parts in their production line, they know the decision to have this Measuring Machine involved in the process is a great investment that ensures e ciency and accuracy in making quality products.
The Automation Ecosystem from Formlabs enables new levels of 3D printing productivity with Form Auto for back-to-back throughput, Fleet Control for advanced fleet management, and High-Volume Resin System for high-capacity printing. The Automation Ecosystem reduces the amount of operator labor and minimizes idle printer time with 24/7 printing so users can e ciently produce enduse parts, prototypes, and customizable products at a lower cost-per-part.
The Automation Ecosystem enables users to expand from one Form 3+ or Form 3B+ 3D printer to a scalable fleet of 3D printers easily.
As users scale their 3D printing production from one to multiple printers, the Automation Ecosystem makes the transition easy without adding management
complexity. With the ability to manage multi-user, multimaterial printer fleets, the system enables continuous production so users can send multiple prints to run overnight and into the weekend. Together with Formlabs 3D printers, the Ecosystem provides a three-time increase in productivity while saving up to 80% on labor, lowering cost per part by 30%, and reducing packaging waste up to 90%.
The system includes:
• Form Auto: Form Auto enables automated 24/7 printing with automatic part removal so users can level up production and reduce labor. When parts are complete, Form Auto seamlessly removes finished parts from the Build Platform 2 using the patented Quick Release Technology, and starts the next print in the queue as soon as possible. The hardware extension works with Form 3 or Form 3+ 3D printers.
• Fleet Control: Fleet Control simplifies advanced 3D printer fleet management, optimizing workflows to maximize fleet productivity. It’s a suite of new features within Formlabs’ Dashboard and PreForm software that includes centralized queue management and automatic printer assignment to optimize production, performance, and printer e ciency with Form 3+, Form 3B+, Form 3L, and Form 3BL printer fleets.
• High Volume Resin System: The High Volume Resin System increases resin capacity to five liters, five times the standard cartridge size, enabling users to create more parts with fewer interruptions for cartridge replacements. This system streamlines workflows, with consistent resin dispensing with a Resin Pump while reducing downtime and user intervention to change cartridges, as well as packaging waste. This is compatible with the Form 3+, Form 3B+. Form 3L and Form 3BL. DW
Meltio is making it easier for customers to integrate its Meltio Engine CNC with its Engine Robot Integration systems. Meltio is a multinational wire-laser metal 3D printing manufacturer. Its engineering team developed 14 evaluation points, 9 focused on toolpath strategy, to ensure a comprehensive software ecosystem to meet a variety of customer needs.
The Meltio Engine Software Partners ecosystem includes key software players in the additive manufacturing market, and enables it to complement the Meltio Horizon to deliver end-to-end additive manufacturing software.
The key players that have joined Meltio Engine’s Software Partner ecosystem for hybrid and robotic platforms include SKM DCAM by SKM Informatik; AdaOne by Adaxis; AiSync by AiBuild; Esprit by Hexagon; Fusion 360 by Autodesk; Aplus+Mastercam by Camufacturing and Mastercam; Hypermill by OpenMind; SiemensNX by Siemens; Hy5CAM by 1ATechnologies; RobotStudio 3D Printing PowerPack by ABB; and SprutCAM X by SprutCam.
Meltio provides an open platform for hardware (any robot or CNC) and for software that allows the use of any software to manufacture metal parts and
meet the growing demand of industrial applications in the market with hybrid and robotic additive manufacturing processes.
Meltio has created a process for validating technically each solution, avoiding extra work between the final customer and every software provider, for example as defining post-processors or ensuring the specific software can get the most out of the Meltio Engine as the possibility to use two materials in the same part (Dual-Wire). Meltio’s engineers have studied the technical requirements for developing the slicing strategies for the majority of the parts that the industry requires. They have defined 9 levels of complexity, including example geometries that represent help customers as well as developers understand the diversity of parts.
This software ecosystem o ers to the market tools to address several parts and industries through advanced slicing features such as: fixed tool orientation, revolved surfaces, features on non-planar surfaces, simple surface coating, radial cladding, 360 features, variable layer deposition, controlled area repair, and non-controlled area repair. DW
Meltio Meltio3d.com
CoreTechnologie (CT) is cooperating with Meteor Inkjet Ltd. of the UK, a supplier of electronics, software, tools, and services for industrial 3D inkjet printing. The two partners will ensure integration of their software environments and develop innovative tools specifically designed for binder and material jet applications. The precision and multi-material capability of inkjet printing and new possibilities for automating additive manufacturing are the focus of the collaboration.
CoreTechnologie is the developer of 4D_Additive, a software suite for a seamless additive manufacturing process o ering functions for model repair, geometry analysis and optimization, support, lattice and surface texture generation, and nesting and slicing. Combined with Meteor’s world-leading printhead drive electronics and Met3D Digital Front End, it provides printer manufacturers with a straightforward path from design to production of inkjet printing systems for additive manufacturing.
The implementation of inkjet technology for the application of binders or materials requires a close integration of the hardware and software of industrial printing systems and innovative tools for additive manufacturing, as well as the reading capabilities for all common CAD formats and the provision of optimized 3D data in a special format for inkjet printers. DW
CoreTechnologie
www.coretechnologie.com/products/4d-additive
Jabil Inc. offers a forecast of five additive manufacturing trends that will continue to accelerate innovations this year.
According to a recent report from Grand View Research, the additive manufacturing market is projected to reach $76B by 2030, growing at a CAGR of 20.8% over the forecasted period. Aggressive market expansion is attributed in part to increased adoption of additive manufacturing in industrial applications and sustained momentum in incumbent industry segments, including automotive, healthcare, and aerospace and defense.
Here are five additive manufacturing predictions that Jesse Sumstad, senior product manager, Jabil Additive, sees as the additive manufacturing continues to mature.
1. Sustainable materials are having a moment. Increased demand for environmentally friendly materials is growing rapidly as companies seek more sustainable solutions to reduce raw materials, waste and carbon footprints. Moreover, regulatory pressures to recycle and repurpose plastic waste for 3D printing applications continues to gather momentum, especially in Europe where plastic waste pollution is being tackled on multiple levels. Equally important, the trend for bio-based and bio-compatible materials used in packaging and other traditional manufacturing applications is transitioning to the additive market. Examples include Jabil’s low-carbon PK 5000 and formaldehyde-free PA 0600.
2. Additive manufacturing processes need to be ecofriendly. While a lot of focus is on the development of sustainable, recyclable materials, expect to see this broaden to encompass demands for more eco-friendly processes and 3D printing platforms. Technical feasibility and research into more sustainable processes and machine platforms need to be addressed over the next 12-to-18 months as part of all-encompassing circular economy initiatives.
3. The industrialization of AM continues. Over the past year, additive manufacturing has seen an uptick in volume serial production of final parts. While prototyping and tooling still rank high on the list of AM applications, it’s clear that the production of end-use parts is growing, along with the availability of rigorous manufacturing processes and Quality Management Systems
(QMS) to ensure the highest levels of part reliability, resiliency and robustness. Future expansion is forecasted, especially for applications where Design for Additive Manufacturing (DfAM) is being used to design parts. Additionally, as the costs of additive manufacturing continue to come down, the ability to compete with injection molding increases, resulting in more viable uses for AM to manufacture end-use parts.
4. Applications are propelling pellet printers forward. Interest in pellet printers is growing alongside the availability of pellet-based materials for making large parts based on the favorable economics of this type of 3D printing. Continued expansion in this area is on the horizon, particularly for applications involving large-scale castings and patterns.
5. Custom materials nearing a heyday:
The push is on for custom materials as companies recognize opportunities to achieve extra ductility, flexibility, and agility with materials tailored for specific applications. In particular, growing interest in polyketone-based materials is being driven by the need for high degrees of impact strength while being resistant to most fuels and fuel additives. As a result, this type of engineered material is ideally suited for fuel-tank applications.
An additive manufacturing pioneer and manufacturing powerhouse, Jabil has supported market growth through its materials, processes and machines.
“As serial production becomes more viable and mainstream, we need to take a holistic view of the end-to-end part production ecosystem,” said Sumstad. “All the factors that impact success — from design for additive and the use of engineered materials to post-processing methods and cost of labor — must be part of the overall decision-making process.” DW
Jabil | www.jabil.com
For engineers and designers working on modern-day motion and other industrial applications, it’s vital to understand the advantages and disadvantages of stepper and brushless dc (BLDC) motors. Here we’ll look at a widely used hybrid stepper motor and a 3-phase BLDC motor and compare both devices. We’ll consider the working principles of these motors (physical size and power density) and make observations about the acceleration and noise aspects of each motor. Experiments performed under various load conditions reveal changes in power, e ciency, and temperature.
A comparative study of stepper vs. brushless dc motors reveals the pros and cons of both motor types.
The key dimensions of the EZmotion MMS742038-24-R1-1 BLDC motor and a general-purpose stepper motor used in the test setup are shown here.
Stepper motors
Most widely used stepper motors are hybrid stepper motors, which consist of permanent magnet rotors and electromagnet stators. Rotors have two cups with permanent magnets; one with north poles, and a second with south poles.
A simplified stepper motor has a rotor made of two cups of permanent magnets. Each cup has three teeth with a respective magnet pole. In this case, these cups are assembled such that they are out of phase by a half-pitch (60°). The stator consists of four poles with two phase windings.
Steppers are electronically commutated. According to step input pulses, the bipolar stepper driver uses a dual H-bridge circuit to energize the stator poles in a sequence that allows the rotor to rotate by a step angle. The step angle can be calculated with the following equation:
Step Angle (in °) = 360/(2 x (n_ROTORTEETH) (n_PHASE))
For each step pulse, the rotor rotates 30° — this stepper is known as a 12 full-step stepper motor. During full-step operation, the commutation sequence and rotor position follow a particular sequence. Most stepper motors on the market have 50 or 100 pole pairs, with 200 or 400 full steps for one full rotor revolution. This makes the step angle as small as 1.8° or 0.9°.
With an advanced stepper motor driver, this small step angle can be further divided into even smaller angles by implementing microstepping operation. The step angle can be reduced by a half-step, quarter-step, and
The graphics show the simplified working principles of hybrid bipolar stepper motors.
Here, the working principles of a BLDC motor and a simplified single pole pair 3-phase BLDC motor (denoted as (a) and (b) in the figure respectively) are shown.
up to a 1/256 step. Stepper motors o er superior positional accuracy because they can step by such small angles.
Brushless dc motors have a permanent magnet rotor and electromagnet stator and require electronic commutation. To commutate brushless dc motors, the instantaneous position of the rotor is required. To meet this requirement, Hall-e ect sensors are used to realize the rotor’s angular position. This information is fed to a microcontroller (MCU) that switches the phase winding current using the 3-phase inverter circuit. Essentially, the dc input voltage is converted to 3-phase ac voltage to sequentially energize the stator poles using an inverter circuit.
The rotor magnetic field always chases the stator magnetic field, which results in the motor spinning. Because the simplified motor is a single pole pair BLDC, each commutation step is 60 electrical and mechanical degrees. BLDC trapezoidal commutation and the rotor position can be obtained. However, typical trapezoidal commutation makes the motor susceptible to torque ripple. As a result, an advanced commutation technique called field-oriented control (FOC) is used on the motor for testing. FOC provides minimal torque ripple and smooth motor operation.
To set up the stepper motor test, a NEMA 23 bipolar stepper motor is used along with a magnetic particle brake for load simulation. The motor test requires five main components described below:
• An encoder (mounted on the particle brake’s other end) monitors the shaft’s rotational speed.
• A bipolar stepper motor driver — featuring parallel inputs, internal current sensing, and regulation — controls the stepper motor.
• A 24V dc bench supply placed in series with a current meter measures the dc current draw of the stepper motor under di erent load conditions. In addition, the 24V dc bench supply powers the stepper motor driver.
• The motor driver’s MotionLAB, which is compatible with the serial peripheral interface (SPI), configures the stepper motor driver’s parameters, such as the step mode, rated current, and additional motor settings.
• A function generator sends square pulses to the driver, which drives the motor forward.
Similar to the stepper motor test, the brushless dc motor test set-up includes a magnetic particle brake for load simulation, as well as a NEMA 17 BLDC motor with an integrated controller.
To power the controller, a 24V dc bench supply is used in series with a current meter to measure the dc current draw of the brushless dc motor under di erent load conditions. Then the MotionLAB GUI can drive the BLDC in speed control mode for this test.
Steppers typically operate under constant current, otherwise known as constant torque. This forces steppers to always draw the maximum current, regardless of the load on the motor shaft. As a result, steppers can provide maximum torque across the low-speed range. However, this also leads to large amounts of wasted energy in the windings in the form of heat.
In this experiment, the stepper motor was tested in three microstepping resolutions: half-step, fourth-step, and eighth-step. The dc
The dc current draw at various motor speeds under di erent load conditions are
current draw was recorded at various motors speeds under three di erent load conditions (no load, 8.2 N-cm, and 11.5 N-cm). The experimental results demonstrate the stepper motor’s less e cient measured dc current draw compared to a BLDC motor.
The no-load current draw was also measured for the brushless dc motor, half-step stepper motor, fourth-step stepper motor, and eighth-step stepper motor. The stepper motor draws a significantly higher zero-speed current than the BLDC, even when there is no mechanical operation. Furthermore, the stepper motor current draw remains high across the low-speed range. As the motor speed increases to the high-speed range, the stepper motor’s current draw begins to decrease due to the inductance of the motor windings and back EMF.
Next, the current draw was measured for the BLDC motor, half-step stepper motor, fourth-step stepper motor, and eighth-step stepper motor when there was some load added on the shaft. The stepper motors stall at high speeds because they have less current in the windings. Although microstepping increases the motor’s positional resolution, it also decreases the output torque. The eight-step and fourth-step stepper motors stalled at the midrange speed as well. Meanwhile, the BLDC motor only draws what it needs depending on the shaft’s load.
Under no-load conditions, the BLDC draws a small current to rotate the rotor. At the same time, the current draw increases if load is added to the shaft, allowing the BLDC motor to continue spinning at a higher speed than the stepper motor. Therefore, BLDC motors
are more power-e cient compared to stepper motors due to their ability to draw current based on the load.
Power density is a measure of motor output power per unit volume. Brushless dc motors typically have higher power density compared to stepper motors.
Using these dimensions, the volume can be estimated as 73 cm3 for the BLDC motor and 131 cm3 for the stepper motor. A motor’s output power is equal to the output speed multiplied by the output torque. The BLDC motor continues to spin at a higher speed compared to the stepper motor under the same load conditions, which means that the BLDC motor provides a higher power density, because it has a higher power output with a smaller volume.
This area has long been one of the most read and sought after by our engineering audience! From screws to bolts and adhesives to springs, these critical but often overlooked components are the key to every successful design.
FastenerEngineering.com will serve readers in the mechanical design engineering space, providing news, product developments, application stories, technical how-to articles, and analysis of engineering trends. This site will focus on key issues facing the engineering markets around fastener technology, along with technical background on selected components.
ADDITIONAL RESOURCES:
• Special print section in select issues of Design World
• Fastener Engineering monthly newsletter
Power density plays an important role in applications with limited available space and a high power requirement, such as drones and quadcopters.
As mentioned previously, constant current operation for the stepper motor leads to major energy losses in the windings, mainly in the form of heat. During the experiment, the motors’ body temperature was measured in an ambient temperature of 22°C.
The stepper motor’s temperature rises steadily regardless of the load on the shaft. In comparison, the brushless dc motor’s ability to not draw excessive current means the body
temperature only increases minimally. Unlike stepper motors, BLDCs convert a high percentage of input power into mechanical power instead of heat.
The high pole count of steppers is directly responsible for their superior positional accuracy over BLDCs. However, the high pole count also results in limited acceleration and more audible noise during operation. Accelerating a stepper motor can be difficult because it requires a gradual ramping of motor speed to sustain the shaft’s angular positional accuracy. If a stepper accelerates quickly, then it faces the risk of missing steps, which
can cause issues in many applications. In addition, if there is low input current combined with high acceleration demand, then the stepper may stall.
In terms of noise, brushless dc and stepper motors can detect a particular torque, otherwise known as cogging torque, which causes vibrations and ringing at every step of the stepper motor rotation. Because the BLDC current draw is proportional to the load on the shaft, BLDCs can draw the additional current required to accelerate the load within the motor’s rated speed range. BLDCs are much quieter during normal operation than steppers. Therefore, BLDC motors are reliable and efficient solutions that offer high speed, high acceleration, and less audible noise.
While the positional accuracy of BLDC motors is proportional to the angle sensor accuracy, integrated BLDC motors with a high-resolution angle sensor can offer exceptional positional accuracy. With microstepping, stepper motors offer superior positional accuracy over brushless dc motors. This comes with the disadvantage of offering less torque beginning from mid-range speeds, which lead to missing steps or stalling. Steppers lack the ability to quickly accelerate, and they produce more noise than BLDCs. Overall, stepper motors are a less expensive solution, but they are limited to lowspeed applications. BLDC motors are dependable, quieter solutions that offer higher efficiency and accuracy across a wide speed range. DW
(two shows, one price)
The International Fluid Power Exposition (IFPE) is the place where engineers meet to:
Spark new ideas with in-depth technical conversations with other engineers.
Discover solutions current suppliers can offer to your unique challenges.
Find new partners among suppliers pushing the envelope on what fluid power can do.
Including Bosch Rexroth , Danfoss Power Solutions , Parker Hannifin , Poclain , IFM Efector , Hawe Hydraulik , Husco , and 375+ more!
Join your peers from these OEMs:
∙ Caterpillar Inc
∙ Volvo Construction Equipment
∙ Liebherr
∙ CASE Construction Equipment
∙ Komatsu
∙ John Deere Construction
∙ Doosan Bobcat
∙
KOBELCO Construction Machinery USA
∙ LBX Company
“ There’s no other show in the world I think that brings the OEM machine manufacturers and the suppliers as close together as this show. It’s a good place to meet and learn about what’s going on. In the Americas, in the Western Hemisphere, this is the show for fluid power.”
KEN ROSENBECKER SALES MANAGER NORTH AMERICA | WIPRO INFRASTRUCTURE ENGINEERING
See why IFPE is the can’t-miss fluid power event of 2023! Learn more at IFPE.com
INTERNATIONAL FLUID POWER EXPO
MARCH 14-18, 2023
LAS VEGAS, NV, USA
Industrial belt drives in motion designs consist of rubber, engineered plastic, metal, or (most common) multimaterial belts that wrap around drive pulleys — grooved or otherwise profiled wheels mounted on a shaft — in turn driven by electric motors. Powered by various motor types, belt drives run axes transmitting fractional horsepower to 7,000 hp or more. Most belt drives in motion designs also wrap the belt around one or more idler pulleys that keep the belt taut and on track. While industrial belts are generally non-serviceable and can exhibit wear and vulnerability to oil as well as debris contamination, their benefits abound. The main reasons that engineers pick belt drives over other options is that modern varieties require little if no maintenance; they’re less expensive than chain drives; and they’re quiet and e cient, even up to 95% or more. In addition, the tensile members of today’s belts — cords embedded into the belt rubber that carry most of the belt load — are stronger than ever.
Belt drives have continued to evolve with new applications.
Belt drives are indispensable in cartoning (cardboard-box folding) applications.
Made of steel, polyester, aramid, fiberglass, or carbon fiber, these tensile cords render today’s belt drives thoroughly modern power-transmission devices.
Note: Terminology for belt drives is more consistent than that for other motion components. That said, in some contexts the term sheave is used instead of pulley. The terms sheave and pulley are interchangeable, with few regions and industries di erentiating sheave to mean any drive pulley — distinct from idler pulleys that have flat (or simply profiled) outer diameters. Otherwise, sheave can imply a rugged steel or cast-iron drive wheel that’s less precisely cast or machined than the pulleys found in motion designs — which are our primary focus in this article.
Flat belts are the original design for automated machinery — first applied in such designs during the first Industrial Revolution and before. In fact, flat belts were and remain especially important in pump and sawmill operations — and once reigned supreme in driving many axes o common steam-powered line drives through factories. Versions made of leather quickly gave way to rubber and neoprene — hastened by the innovations of the burgeoning automotive industry and new forms of independent pieces of machinery run o electric motors. Today, highly engineered flat belts still find myriad uses in conveying and materialhandling applications.
However, the faster axis speeds associated with many motor-powered
Recent years have seen convergence of specialty belt drive systems in mass-produced consumer and light industrial tools with standard belt drives integrated into various machine designs.Machine designs often employ gear, chain, and belt drives for power transmission. The latter come in V belt and synchronous-belt variations (as the ones shown here) to serve different applications. | Gennady Danilkin
designs necessitated belts with new geometry — so next came V belts having trapezoidal cross sections. Their easier tracking on pulleys and higher friction (which we’ll explain more on a moment) also allow high force transmission even at tension values lower than typical.
Reinforced cords embedded in belt backing — the tension-carrying zone — was another innovation still core to modern belt variations.
Combining flat and V-belt design elements are ribbed or poly-groove V belts — those with a cord-reinforced tension-bearing face and multiple trapezoidal profiles running the inner belt circumference. Drives based on ribbed V belts are exceptionally compact and necessitate lower tensions than flat belts.
Other belt-related innovations came to include the introduction of toothed belts for synchronous chain-like operation; heat-resistant belt insulation layers; elasticized and other highly engineered working belt surfaces; and pre-stretched tensile cords of various materials.
Recent years have seen convergence of specialty belt drive systems in mass-produced consumer
and light industrial tools with the standard belt drives integrated into various machine designs. That’s because options have proliferated for belts with flat and round profiles as well as those with various V-shaped profiles and toothed belts for synchronous operation.
The Association for Rubber Products Manufacturers (ARPM) originating from the Rubber
Manufacturers Association (RMA) and the National Industrial Belting Association (NIBA) along with component suppliers dictate the details of how the geometries and performance of these industrial belt drives are standardized and quantified.
Many manufacturers describe belts and pulleys with fi ve main geometries. Pitch diameter is the drive pulley’s diameter. Center distance is the distance between the two pulleys’ centers. Minimum wrap angle is a measure of how much the belt wraps around the smallest pulley. Belt length is how long the belt would be if cut and laid flat. Finally, in the case of toothed belts (also called synchronous belts) the pitch is the number of teeth per some length — so a 3-mm pitch means that the belt has one tooth every 3 mm, for example.
Power ratings based on belt and pulley size (along with motor output) are adjusted for the belt-drive length and wrap diameters. Traditionally, charts of belt geometries and counts, horsepower ratings, and speed and force capabilities assist design engineers in the specification process. Today, sizing and selection software tools abound to match required values to a machine axis’ geometry and torque (output force) and speed requirements. These also provide service-factor adjustments informed by the belt or other component supplier’s own historical experience with given industry and application type. DW
Linear Motion Tips | linearmotiontips.com
Silicon Carbide (SiC) has made its mark in bringing faster, a smaller, and more reliable components than its fellow semiconductors to market. While SiC components have been around for a couple of decades, there is still a lot to learn and a lot to consider when choosing the most suitable WBG semiconductor for your device.
LET US HELP with tutorials, from looking at how WBG semis stack up in power conversion efficiency to an overview of SiC FETs and MOSFETs.
Check out our EE Classroom to learn more: www.eeworldonline.com/silicon-carbide-classroom
As more industrial and commercial applications are requiring greater functionality, there is a need for low-profile input devices that enable users to achieve fine control, even in the harshest field environments.
Antonin Deschamps • APEMMany heavy-duty industrial and commercial applications, despite the large scope and scale of driven equipment, still need delicate operator-initiated control for various aspects of their operation. For instance, a massive gantry crane may require precise positioning of the pickup apparatus, or a construction equipment operator may need to set the position of a blade or other attachment. Incorporating these types of fine control, along with other types of operator input, can be challenging in an industrial setting (Figure 1).
Furthermore, as digital automation methods have become the norm, along with an increasing availability of electronic sensors, machines are gaining much more functionality than traditional and basic systems. Whether the application is a fixed installation, a portable piece of equipment, or a vehicle, these additional technologies are prompting a greater need for industrial-rated operator control devices able to provide a responsive and accurate interface to digital controls while surviving the rigors of the environment.
Putting precise control into the hands and fingers of operators takes many forms. For some modern systems, touchscreen displays are incorporated into the design. Touchscreens work fine for personal electronics, but their relative fragility and lack of tactile feedback make them less than ideal for heavy-duty equipment applications.
Proportional joysticks address these and other issues. True proportional joysticks — which are different than simple on/off control at each compass point — are a classic form of operator input for relatively delicate actions. These types of joysticks are commonly seen in certain aircraft controls or video games, providing an excellent way for operators to command two (X-Y) or more axes of motion in a smooth and positional manner.
However, using the whole hand and arm may not provide the finest control
because an operator’s thumb and index finger are much more agile. Using a full-size joystick is less practical when there are many pairs of axes to be controlled. Another consideration is that the relatively large size of a traditional proportional joystick makes it more susceptible to damage or unintended operation.
In many cases, the best solution to address these issues and provide refined control in a robust form factor is to use a low-profile joystick, sometimes
called a thumbstick, which can be used by the thumb or fingers.
Many of the most challenging industrial, commercial, and marine applications require extensive operator interface. Sometimes an operator input device can be mounted in a relatively protected fixed location, like a control panel. But more commonly, operators need to be close to the work. This means that wired or wireless consoles, vehicle armrests, pendants, and belly boxes must be populated with several operator interface devices. Each of these locations is space-constrained and subject to considerable abuse. Belly boxes can be dropped, where an extended joystick can absorb a significant impact. Controls on board a pitching ship or vehicle may serve as an ill-advised handhold. These actions can damage flimsy devices and create undesirable and potentially dangerous equipment operation.
For these reasons, thumbsticks should be compact and extend no more than about 2-in. above a panel face. This minimized height makes them less vulnerable to impact, and it also means that any guarding provisions can be low enough to avoid interfering with operator use. A low-profile thumbstick also makes it
suitable for multiple devices to be installed on dense control arrays while providing easy operator access.
A low profile is important but may not be enough to protect a generic thumbstick when exposed to damaging force. Therefore, thumbsticks made for industry should have a stainless-steel shaft, along with similarly tough metal gimble and base mechanicals and limiters. Because bare metal is not an ideal contact surface for operators, the stick and cap should be covered by a material such as nylon, which provides a durable yet easily gripped surface (Figure 2).
Thumbstick applications are often exposed to falling or directed water, so these devices must be rated at least IP66. This is best accomplished with a convoluted gaiter to protect the moving location where the stick enters the device, in combination with a robust panel mounting design that permits dropin or rear-mount installation for the best design flexibility. Users should also look for devices rated for an ultra-wide temperature range to guarantee performance under harsh conditions.
Older joystick designs may have used relatively fragile and short-lived potentiometers, but today’s designers should instead insist on proven Hall e ect sensor technology. Non-contact Hall e ect sensors, operating at standard 3.3 or 5VDC and implemented in conjunction with robust mechanicals, result in a device that can endure an expected lifetime of 10 million cycles.
Older joystick designs may have used relatively fragile and short-lived potentiometers, but today’s designers should instead insist on proven Hall effect sensor technology.
For compatibility with the widest range of applications with X or X-Y axes, the Hall e ect sensors should be capable of operating as single- or dual-axis, with dual and dual-inverse outputs available in analog or PWM formats. The availability of center-detect functionality, and center-tap signaling (Z-axis pushbutton), provides even more options for designers to fine-tune the device selection to meet their needs.
In fact, designers should look for a device meeting not only the criteria described above, but also providing su cient configuration flexibility in terms of:
• Signaling options
• Gain levels
• Movement limiters
• Handle shapes
• Spring force levels
• Colors
Industrial-grade thumbsticks should be able to survive a 1m free fall and be rated for vibration, EMC, and ESD resistance in accordance with applicable IEC standards. Designers should ensure the products they select come with a comprehensive validation plan, ensuring adherence to all standards and performance requirements.
Providing practical operator controls for space-constrained belly boxes is a prime use case for thumbsticks. Some belly boxes are wired but are still relatively heavy and require a neck strap, while wireless versions can be even more weighty due to batteries. One drop as the box is picked up or removed can be catastrophic for the input devices unless they are built to withstand this type of rough treatment. Add to these considerations the fact that belly boxes are often used in highEMI environments due to welding, and the need for rugged and properly rated operator input devices becomes clear (Figure 3).
The control console of a ship is another prime application for functions, such as thrusters, requiring precise operator control. Obviously, any shipboard device or instrument can be subject to water spray, but some users may think of a marine control panel as relatively protected from a mechanical standpoint. However, aboard a constantly moving ship, it can be quite common for users to grab anything handy to keep their balance. Thumbsticks are less susceptible to this problem than a larger joystick, and well-built thumbsticks will easily survive such abuse.
In addition to the above industrial and marine applications, there are also many commercial applications for thumbsticks. As electric vehicles and other transport equipment, such as wheelchairs, become more advanced, they need user input devices sized for convenient use but tough enough to handle mistreatment.
For industries as varied as construction, material handling, industrial robotics, marine controls, and more, the increasing use of automation and sensors is driving a need for refined control options that can survive in harsh environments. Low-profile Hall e ect sensor joysticks/thumbsticks provide designers and users with a high-performance solution for fine control in the most challenging applications. DW
prime use case requiring a range of compact but accurate control options in a space-limited location, able to withstand abuse in the field.
Key technology content produced by the editors of Design World compiled in individual PDFs. Download your free design guide today!
The editors of Design World detail the construction, control, and networking of servomotors — and approaches to tuning and inertia matching for top performance ... even in highly dynamic applications.
DESIGN
Motion systems for industrial automation command electric motors to drive mechanical linkages for precise speed, force, and position outputs. This Design Guide details motion systems with various electric, electronic, and mechanical components.
Find
Stepper motors in traditional arrangements run openloop without the need for tuning as in servo setups — but stepper motors are making inroads even in designs with feedback. In this exclusive Design Guide, the editors of Design World detail application variations and the vast array of steppermotor designs.
Covering the latest motion and control components, equipment and systems in ASRS design
Digital transformation done right:
Complete digitization and edge computing on the PLC
Broad horizontal communication via all modern and legacy fieldbus protocols
Vertical communication via open protocols such as MQTT and OPC UA as well as PRP (Parallel Redundant Protocol)
Redundant controllers without specialized hardware, with EtherCAT cable redundancy
Highest performance control systems without limitations
Flexible architecture with backwards compatible firmware
Longest system life cycle in the industry with system obsolescence protection
The complete Beckhoff control platform covers all your hardware and software needs for complete fulfillment center automation.
© Al Ferreira Photography76
62
From trend to trade: how automation evolves out of necessity
What was unthinkable in the past has become commonplace in modern warehouses. Robots and scalable automation are now must-haves for thriving during market fluctuations.
70
Designing the “last mile” in automation
To increase e ciency and boost productivity, Tier 1 automotive supplier Denso accelerated AMR deployment from warehouse to line-side production.
76
Drones take the night shift for improved inventory tracking
Gone are the days when inventory inaccuracy is just part of doing business. As new technology is increasingly a ordable and pervasive, more thirdparty logistics (3PL) companies embrace innovation to improve their competitive advantage.
82
Vet supply distributor improves productivity and safety with AMRs
Long-standing partnerships make scaling warehouse automation systems easier. With Körber’s insight and Locus Robotics’ fleet of LocusBots, Lambert Vet Supply grew operations and improved employee well-being.
88 Product News
Warehouse automation has been around a lot longer in the U.S. than people may assume. Though today we think of autonomous robots and software-driven machines operating continuously in human-free environments, automation looked di erent (and meant something di erent) in past decades. Its modernday roots grew during the Technological Revolution, also known as the Second Industrial Revolution, which ushered in the 20th century. The birth of mass production called for new technologies and systems to make manufacturing and distribution scalable and more e cient. However, space and labor were key factors that kept the U.S. in manual mode much longer than other countries.
“Warehouse automation in Europe and Japan was probably 10 years ahead of the U.S. in terms of pick up because labor was more expensive in those countries and space was more restricted. Here in the U.S., companies had a lot of land and a ordable labor,” said Markus Schmidt, president of Swisslog Americas, a global warehouse automation provider. “But that equation has, of course, turned over the years.”
COVID certainly changed the nature of warehouse operations since market demand shifted rapidly and e-commerce skyrocketed. Plus, after COVID, getting
What was unthinkable in the past has become commonplace in modern warehouses. Robots and scalable automation are now must-haves for thriving during market fluctuations.
people to work in distribution centers was hard, so there was a drastic labor shortage amidst increasing consumer demand.
Before COVID, warehouse automation focused on conveyance and sortation for goods-to-person applications. Over the past five years, especially during COVID, interest in autonomous mobile robots (AMRs) increased to reduce labor dependencies, increase efficiency, and afford rapid scaling in the event of sudden market changes.
Take online grocery shopping, for instance. The dawn of mobile apps and real-time information exchange made it easy for consumers to order groceries online and have them delivered or ready for pickup at the store. While demand was manageable, personal shoppers walked the aisles and pulled items from shelves to fulfill individual orders. However, during the pandemic, online grocery sales increased suddenly, and safety protocols restrained manual fulfillment.
In response, new technology and small distribution centers emerged and picked grocery items efficiently
and accurately with less labor. Such automation was unthinkable years ago because there was no need for it. Now, most advanced distribution centers have goods-to-person robotic solutions for item storage and picking.
“There are a lot of new companies with innovation entering the space, and there are a lot of established players. The industry overall grows about 20% year over year,” said Schmidt.
Back in the day, when labor was plentiful, the buzzword wasn’t “automation” — it was “throughput.” In the early 20th century, transportation advancements made it possible to deliver goods faster to a broader customer base. The focus was on making more products quicker and getting them into customers’ hands.
But mass production came to a screeching halt during the Great Depression, which some claim was partially due to the overproduction of goods. As the economy started looking up, the Digital Revolution, or the Third Industrial Revolution, spawned around
1947 and paved the way for computers, advanced networking technology, and eventually automated storage and retrieval systems (AS/RS).
Yet as markets fluctuated, warehouses still felt the pangs of storing too much inventory that didn’t move. So, throughput became a balancing act, and companies started valuing efficiency, flexibility, and scalability — both up and down.
Until recently, if a warehouse needed more throughout, it would add more storage capacity and labor. In today’s automated systems, throughput and storage aren’t strictly proportional.
For example, Swisslog’s CarryPick storage and order picking system includes robots that carry mobile racks of goods, and warehouses can scale robots and racks independently.
“You can add more robots to get more throughput. Or you can add more racks to get more inventory,” said Schmidt. “That flexibility is especially valuable for online businesses and all warehouses during peak retail seasons.”
Once an automation system is in place, it’s relatively simple to scale it to meet demand. However, how does a warehouse justify expanding or adding new automation, especially for goods with special storage or handling requirements?
Continuing with the grocery example, in an e-grocery warehouse, there are typically three major product categories that can be differentiated by temperature
Modern automated warehouses are flexible and can scale inventory or throughput independently.
| Courtesy of Swisslog
Product data drives AutoStore system design to ensure the solution meets all inventory, throughput, and operational requirements.
zone: ambient for dry goods, chilled for fresh produce, and freezing for frozen foods. Before COVID, frozen foods had relatively lower volumes than chilled and dry groceries. So, the first attempts to automate grocery order fulfillment focused on chilled and dry foods. However, as frozen food demand has increased, there’s an opportunity to expand automation for this product category.
But in the case of frozen food, the automation technology must withstand freezing temperatures to operate properly. Plus, the frozen food section of the warehouse and all environments where frozen goods are stocked, stored, picked, and transported must maintain strict temperature requirements — not to mention any pickup holding areas or delivery vehicles.
With all the extra considerations, warehouses need to be sure that they have enough volume to justify automating new product lines with
AutoStore robots use 0.1 kW of energy per hour, providing an energyefficient goods-to-person solution.
| Courtesy of Swisslog
AutoStore saves space and time with compact robots and vertically stacked bins organized on an aluminum grid.
| Courtesy of Swisslog
different, strict requirements. Or they need to consider an adaptable and scalable solution that can adjust throughput seasonally or in response to market changes.
One solution is to set up one or more micro fulfillment centers to address varying demand and product requirements. Micro fulfillment centers are small, automated distribution centers located close to the consumer with limited inventory and throughput to serve a geographical area.
The big challenge with micro fulfillment centers is sizing. If they are too small, the return on investment may be disappointing. But if they are too big, there may be too much distance between the distribution center and the consumer. Warehouses need to find that sweet spot that balances size and distance. For instance, a superstore that sells many different goods constantly may need one large distribution center with different temperature zones to fulfill orders for 3-5 nearby stores. Other companies may find it practical to set up multiple micro fulfillment centers, each tailored for specific product requirements.
Micro fulfillment centers can also benefit online-only retailers. Companies that want to expand to a different geographical area can build a small center to serve online customers only with no investment in a physical store. Brick-and-mortar companies are already experimenting with this concept by diverting online orders to online-only micro fulfillment centers and dodging store fulfillment completely.
Systems such as Swisslog’s AutoStore take the guesswork out of warehouse automation. AutoStore is a standardized product with robots, specifically shaped plastic bins, and an aluminum grid on which the robots drive. Warehouses can select the size of the grid; how many
bins, robots, and pick stations to include; where to locate the pick stations; and then Swisslog does the heavy lifting.
“We look at a specific client application, figure out how much inventory they need, how much throughput they need, and then we design a solution specifically for that requirement using the AutoStore technology,” said Schmidt.
Automation companies such as Swisslog rely on customer data to analyze and understand the customer’s specific requirements and capabilities to tailor solutions. That means warehouses must provide lots of detailed product and operational data, especially when turning over manual processes, such as picking, to robots.
In highly automated distribution centers, the trend is to have robots automate the picking process. However, not everything is pickable by automation.
“I would say in today’s world, probably 70% is pickable, and 30% is not,” said Schmidt. “You need to make sure you get that percentage correct, and then you also need to design a way of dealing with products that are not automatically pickable because those you still need to pick conventionally.”
Though robots take the limelight when building a fully automated or hybrid system, advanced software is the glue that connects and runs the warehouse. Integrating technology to operate as one cohesive system is complicated and gets interesting when robots, automated processes, and humans need to interact. Software needs to guide both technology and people to do the right things at the right times while monitoring equipment, inventory, and locations and communicating with other software, such as customer-facing apps that send notifications on order status.
Software orchestrates all the moving parts, synchronizes data, and helps make decisions. If a robot on the floor
sees an obstruction in its path, whether nearby or far away, it will either need to stop, go around the obstruction, or navigate a different pathway. Plus, software is needed to instruct the robot to make local decisions or communicate with a human operator who can tell the robot what to do. Some decisions must be made locally in milliseconds, while others can be programmed more strategically in advance.
Today, the buzzword is “Industry 4.0,” which translates “Fourth Industrial Revolution” into modern-day digital speak. With advanced technology and the adoption of cloud computing, the world is more intricately connected, which can make it quite brittle, as COVID revealed. Though history may repeat itself, the current trajectory is an upswing for automation.
As warehouse automation seeks to decrease dependence on manual labor, there’s still plenty of room for engineers to build lucrative careers. Remember, what was unthinkable a few decades ago is now commonplace. More than ever, companies value innovation and creativity and want to stock bright minds to stay behind the economic cue ball. No one really knows what the future holds, but scalability, flexibility, and robots have already shifted from trend to trade.
“In schools and universities, there’s a lot of teaching around automation and manufacturing. But I think we as a society have squeezed out the last little bit,” said Schmidt. “In warehouse automation, where everything was conventional, we are just now entering the phase where real interesting automation takes place, and it’s going to continue for a while.” l WH Swisslog |
FFor many large manufacturers, material conveyance has been the “last mile” for automation. That’s been the case for Denso, a Tier 1 automotive supplier that manufactures products ranging from spark plugs to fuel injectors in its 800,000-square-foot powertrain component production facility in Athens, Tenn. A renewed emphasis on improving manufacturing e ciencies and profitability, combined with a tight labor market, brought automated conveyance to the forefront.
Denso turned to Mobile Industrial Robots (MiR) to automate material conveyance and is now running six MiR250 robots through two production areas, including transport to and from the warehouse, to support line-side manufacturing, and including facilities and spare parts transport. The company also has five MiR500s for anticipated new business.
Like most manufacturers, Denso is always looking for opportunities to boost productivity and e ciency. “We knew we had a lot of people that were getting paid to move parts all day long, walking carts from one place to the other,” said Travis Olinger, logistics and automation engineer in Denso’s Total Industrial Engineering (TIE) group. “But if we have people that are only conveying parts, then that’s a non-value-added activity, and we had plenty of open jobs for value-added activities within the production environment. We wanted to pay people to make parts for us that make us money, and not pay them to move parts that cost us money.”
Research showed that Denso associates were walking up to 12 miles per day, moving material between production and the warehouse, and spending
To increase e ciency and boost productivity, Tier 1 automotive supplier Denso accelerated AMR deployment from warehouse to line-side production.
about 60% of their time just pushing carts. As the team explored options for automated conveyance, it quickly became clear that automated guided vehicles (AGVs) and their infrastructure requirements and costs couldn’t meet Denso’s needs.
“We’re an extremely dynamic environment,” said Olinger. “We didn’t want to have to go through that entire infrastructure change every time we moved something. The autonomous mobile robot was key to us: to be able to navigate on its own, with quick mapping, quick changes.”
The team brought MiR and other AMR options in house for testing, using the spark plug production lines as a pilot area. The processes included moving
empty totes to production and full finished kit totes back to the warehouse.
“We set up a test course and we ran [the robot] through the wringer,” said Robert Blackburn, project leader. “We were able to throw different things at it, different challenges, and get user feedback.”
The MiR250 had recently been introduced, and the team was attracted to its 2-mps speed, the payload of 250 kg to handle heavy metal parts, and the ability to navigate narrow spaces.
“Honestly, my initial concern was safety,” said Danny Thompson, logistics associate. “A lot of people were worried about them running into stuff or hitting something. I was very surprised at how well they responded to anything stopped — traffic or things that have blocked their pathway. The robot’s able to communicate and move out of the way
With the MiR250 robots, associates no longer walk 12 miles per day and have grown quite fond of working alongside their autonomous colleagues.
or make adjustments — or even come to a complete stop and allow the other foot traffic to continue on.”
MiR partner Advanced Control Solutions (ACS) helped develop the third-party integration necessary to work with the REST API calls along with Denso’s internal software to integrate with production.
“We use Fleet for our maps for all of our mission creation and our locations,” said Olinger. “But we also wanted to be efficient with some proximity cueing and to allow the associates themselves to call for the robots and prioritize in FIFO [firstin, first-out] order. Also, the REST APIs enabled us to manage charging.”
Denso can prioritize robots based on charging status and use a decision tree when a mission is finished. The system
looks for other missions available, checks for adequate charge percentage, and sends robots to missions or to charge as appropriate.
Denso has also been able to integrate the robot to automatically open the door in and out of a clean-room area, using the MiR I/O modules to send wireless signals to Wise Modules in the roll-up door controller. Fleet zones automatically send the appropriate signals via the I/O module when the robot approaches the door.
To prepare for the MiR robot implementation, the TIE team studied the workers in the area to understand exactly what the job entailed, what aspects of the job could be carried out by a robot (conveyance), and what parts of the job would need to remain with the associate. From there, work elements were transferred until all conveyance could be handled by one associate. That person acted as the robot during the research period.
“The associate level was very much involved throughout the implementation of the MiR robots,” said Blackburn. “Once we knew that they could handle all the robot elements, we knew that the robot could then take its place and become that associate. That’s how the transition took place.”
The MiR250 robots boosted productivity and led to unexpected benefits, such as increased associate accountability during the parts ordering process.
During that time, associates provided invaluable input and feedback to optimize the approach for better efficiencies. Associates are also very involved in the design of top modules for the robots.
“As we have designed those cart tops for different areas and different applications, the associates have been instrumental in those design processes because they’re handling those carts every day,” said Olinger. “From an ergonomic standpoint, we don’t just want to replace the conveyance and then shift that work onto someone else. They’re the experts. They’re the people handling the carts, they’re the people handling the parts. They are extremely helpful in those cart designs and making it a more efficient process.”
Standardizing on the MiR250 shelflifter and ROEQ carts allows Denso to expand quickly into other areas using the same cart base and customizing it for each use. As associates approach the engineering team with requests for automated conveyance, they can easily design racks around the carts, helping to free up space, increase flexibility, and gain the advantages of automated conveyance more quickly.
Those efficiencies now extend to other areas as well. The facilities maintenance crew purchased carts and now gets supplies delivered automatically from receiving.
After the initial success of the warehouse and spark plug area, Olinger and Blackburn turned to work-inprocess (WIP) conveyance and quickly expanded into the gasoline plant. An unexpected benefit was the alleviation of tensions around whether workers had delivered parts correctly, on time, and to the right place.
“Now, on both sides, everyone has accountability,” said Olinger. “We know what time parts were ordered, how many were ordered. We know what time it was completed, and when the robot picked it up. It took a lot of that tension away, and allowed departments to work together better, because all the information’s available.”
Denso’s ROI plans for projects are typically less than two years, but the indirect cost reduction specific to the MiR robots replacing conveyance achieved an ROI in a year or less. Within six months of the project launch, Denso was able to cover all finished kit lines in the ignition plant with AMR conveyance and achieve a six-head-count reduction in workers manually moving parts. Those workers have moved to inspection processes or other roles that allow them to challenge themselves professionally and add greater value to the company.
Overall, employee morale has also improved, with employees recognizing Denso as an innovative company that
■ Four scan planes in a single sensor enable environment perception for cliff detection, collision avoidance, and bay occupancy checks
■ 100° horizontal field of view and 0.1° angular resolution facilitate object tracking and follow me
■ Precise light spot and high sampling rate offer enhanced perception and small object detection
For more information, visit pepperl-fuchs.com
wants to make employees’ jobs easier and that the company cares about the ergonomic aspect of the job.
“The thing I would say for anyone else that’s looking at potentially rolling out AMRs for conveyance is that the benefits you’re not thinking of now are almost going to outweigh what you are considering,” said Olinger. “As you start to see the efficiency gains, and how it improves your overall culture, and then how departments will come up with their own ways to use them to save money, there is a broader benefit to be attained than just that initial indirect cost reduction. It’s well worth that initial investment, and well worth that initial period of change.”
Denso received extensive support from both MiR and ACS to ensure a smooth rollout and ongoing success. ACS delivered the robots and walked the Denso team through the initial setup and mission-creation and mapping process. From there, the robots’ ease of use allowed the TIE team to move into new areas very quickly.
“Probably a day of setting everything up, and then another week of testing and working out all the little wrinkles,” said Blackburn. “After we learned that first area, we were able to do it independently.”
MiR provided a week of onsite MiR Academy training, including for Denso employees who could be groomed into super-user roles to support the project longterm. MiR has also assigned a Denso North America-specific contact, has created a group for Denso on the MiR community site, and conducts monthly meetings with Denso.
Denso has also purchased five MiR500s for anticipated new business. With automated conveyance and logistics now at the forefront of production decisions, the TIE team can better plan for things such as aisle widths, streamlined processes, and where to focus headcount with MiR conveyance systems in place out of the gate.
“Technology and innovation are very much a part of what we need to focus on going forward,” said Blackburn. “Basically, if you’re not going to focus on that, then you’re doing your company or your plant a disservice by not coming out with the best ways to improve on existing manufacturing environments.” l WH
Denso | denso.com
During in-house testing, Denso was impressed by how responsive the robots were to obstructions and how they could quickly communicate and adjust based on objects around them.
• Adjustable handles and knobs replace standard hardware and can be used to torque components without tools.
• Levers can be used with Ruland shaft collars for quick installation and adjustment.
• Slit couplings are available in short and long styles giving designers a variety of body sizes to choose from to t application envelope and performance requirements.
• Control ex is a highly exible encoder coupling designed for applications with high speed, low torque, and wide differences in shaft sizes (up to a 4:1 small to large ratio).
• Slit couplings are available in bore sizes from 1.5mm to 12mm (1/8” to 1/2”) and control ex couplings are available in sizes from 6mm to 40mm (1/4” to 1-1/2”).
Ruland Manufacturing is proud to support the FIRST Robotics Competition as a Gold Supplier of precision shaft collars & couplings.
• Available with OD ats and holes for direct mounting of the collar to other components.
• Proprietary manufacturing processes ensure superior t, nish, and holding power.
• Manufactured in a variety of sizes, styles, and materials.
• Widest selection in the industry: over 3000 standard single and double universal joints to start your next design with.
• Available from Ruland in 2 weeks or less for the shortest lead times in the industry.
• Yokes, pins, and blocks are precision machined, ground, and selectively heat treated for smooth operation at high operating angles.
• Assortment of components that allow users to build small assemblies for mounting sensors, conveyor rails, machine guards, and more.
• Optional pre-designed kits make it easier to select the right system for your application.
• Hand operated: no tools required to install, remove, & adjust.
• Best suited for systems that require frequent adjustments.application.
All products available directly on RULAND.COM www.ruland.com |
IInventory accuracy is one of the most important KPIs for any 3PL or warehouse. The higher the accuracy, the faster orders can be processed, leading to e ciencies that reduce overhead costs and increase the capacity to support more business. To achieve acceptable inventory accuracy rates, warehouses typically require extensive labor to manually audit stored goods (also known as cycle counting). Plus, many warehouses keep inventory more than 30-ft o the ground, posing safety hazards and slowing operations. However, as more 3PLs embrace automation, alternative solutions are taking flight.
For instance, PFS, an eCommerce fulfillment provider and business unit of PFSweb, has integrated Vimaan’s StorTRACK Air self-flying warehouse drones to automate inventory tracking activities within its fulfillment operation that stores and picks, packs, and ships inventory for premier brands. Scanning inventory from the ground to the ceiling, the robots capture up to 1,500 locations per hour and deliver highly accurate inventory status details to the PFS Warehouse Management System (WMS). Implementation improves the accuracy and traceability of client product inventory across PFS fulfillment centers.
Manual inventory tracking is a laborintensive, time-consuming, and costly process. Plus, today’s labor market makes finding and retaining warehouse sta di cult.
Gone are the days when inventory inaccuracy is just part of doing business. As new technology is increasingly a ordable and pervasive, more third-party logistics (3PL) companies embrace innovation to improve their competitive advantage.
Without drones, PFS personnel use ladders, lifts, and mechanical order pickers to manually count inventory with handheld RF technology. Team members can scan approximately 400 labels per hour, while the drones can do 1,500 labels per hour.
“A significant portion of the brands we support at PFS fall under high-value verticals and require 99.9% inventory accuracy, according to our service agreements,” said Jon Gardner, SVP of fulfillment operations at PFS. “Drone automation offers a more efficient and accurate inventory management solution that enables us to better support our clients.”
Especially with the rise in demand for multi-node fulfillment operations, tracking inventory more efficiently across facilities is more critical than ever. PFS plans to use approximately 12 drones per facility, where some operate while others charge, to cover the entire facility.
Many warehouse drones are flying barcode scanners, but efficient cycle counting requires much more than barcodes to improve inventory accuracies. A complete view of inventory includes accurate counts,
barcode capture, label reading, damage detection, and even reporting on items located in the wrong place. Finding a solution that can do all of this and support efficient WMS reconciliation delivers the most value across the entire warehouse.
Vimaan StorTRACK AIR drones capture images of inventory, while intelligent software uses optical character recognition (OCR) to expand the label types and configurations, such as a pallet or box. For example, premier brands with small-piece products typically come in cases with multiple items of the same SKU located within a larger box or bin. With image capture,
efficient use of vertical space, reduce safety hazards for associates, and speed up inventory tracking.| Courtesy of PFS
Say hello to the
The safest cobot on the marketplace, delivered in 4 weeks or less.
Six-axis articulation
Force torque sensors on each axis
PLe CAT 4 Safety Rating
1700mm Reach 25kg Payload
drones can efficiently scan case labels, and OCR can translate the information.
After scanning the designated inventory locations, the drones return to a data exchange location that downloads the data captured in flight. PFS compares what the drones saw to its WMS inventory and generates a discrepancy report if the drones’ scans differ from the WMS data. This enables near real-time investigation against any discrepancy.
Warehouse staff typically schedule flight times outside operational hours to ensure no associates are in the aisles while drones scan inventory. The drones run overnight when fulfillment activities are either done for the day or slower, but they can operate during break hours if a discrepancy occurs and an area needs to be checked. Staff can also place caution lighting in an aisle to prevent employees or machines such as lifts from entering an aisle while drone counting is taking place if a count is required during operating hours.
“Drones reduce the amount of machinery required to perform audits and, therefore, we find that they create a safer warehouse environment,” said Gardner. “Since employees and drones do not operate in a particular area at the same time, there is little interaction.”
Because they fly in closed environments and around people, warehouse drones require highly robust collision and obstacle avoidance capabilities. Also, because the drones are operated indoors, they do not need to comply with strict FAA regulations or rely on GPS signals.
Vimaan took care of all software integration, and PFS can use either an API or flat file to exchange inventory information. If the warehouse layout
changes, such as a rack height or beam height, Vimaan reprograms the system so that the drones navigate accurately. But the true advantage of the Vimaan inventory tracking and management solution is the proprietary AI-enabled computer vision, which extends beyond drone flight. The image capture technology allows for dimensioning in addition to OCR, and PFS is exploring other uses. For example, an image capture device can be set up at pack stations to capture a photo of orders as they are packed. The images can then be referenced for damage checks, shipping validation, dispute resolutions, and more.
Drones are just one of many automation solutions that 3PLs and warehouses can leverage to increase efficiency and reduce costs. They help optimize vertical space without associated safety hazards or operational challenges. They also work with existing processes and environments so facilities can omit layout changes and focus on making existing processes more effective. However, warehouses shouldn’t deploy drones for the sake of using drones. It’s about the value being delivered to the inventory management processes.
“With drones, warehouse design focuses heavily on clear product labeling,” said Gardner. “Racking depth and labeling requirements are keys to designing a warehouse optimized for drone use. The layout allows the drone to move faster and see the label better and also optimizes space by allowing for more pick locations per square foot within the warehouse.” l WH
PFS | pfscommerce.com
Vimaan | vimaan.ai
Long-standing partnerships make scaling warehouse automation systems easier. With Körber’s insight and Locus Robotics’
Business growth creates new problems — good problems, of course, but problems nonetheless. And warehouses and fulfillment centers in every industry face similar problems whenever they expand or open new locations.
For instance, Lambert Vet Supply (LVS), a distributor of veterinary supplies, has experienced growth and continuously seeks solutions to new problems. Established in 1994, LVS aims to provide pet owners with quality pet supplies, pet medications, and veterinary supplies. The company is headquartered in Fairbury, Nebraska, and has grown over the years to include locations in Belleville, Kansas, and Neosho, Missouri. Most recently, it’s partnered with a warehouse network in Dothan, Alabama.
LVS had an existing partnership with Körber, an international technology group, and it was looking for a robotic product that could make its new warehouses more e cient and easily integrate into its existing K.Motion Warehouse Management System (WMS).
LVS decided to expand its relationship with Körber by deploying 24 autonomous mobile robots (AMRs) created by Locus Robotics.
In early 2022, Locus expanded its line of warehouse AMRs with the introduction of Locus Vector and Locus Max. These new form factors joined the Locus Origin robot to form a comprehensive family of AMRs for a broad range of warehouse use cases. The new line addresses use cases from e-commerce, case-picking, and pallet-picking to scenarios requiring larger, heavier payloads to support the full range of product movement needs in today’s fulfillment and distribution warehouses. The LocusBot family includes:
Locus Origin: The company’s flagship AMR that can operate for 14 hours on a single charge and has a payload capacity of 80 lb. Engineered for maximum warehouse e ciency, Locus Origin couples fulfillment productivity with agile maneuverability, incorporating navigation and vision system technologies. It works collaboratively with associates in dynamic warehouse environments.
fleet of LocusBots, Lambert Vet Supply grew operations and improved employee well-being.
Locus Vector: The industrial-strength AMR with a 600-lb payload capacity and flexibility for a wide range of roles from fulfillment to transport to put-away. Locus Vector features omnidirectional mobility and compact design.
Locus Max: The heavyweight AMR with a 3,000-lb payload limit and unparalleled flexibility to easily transport a wide variety of heavy materials, cartons, or pallets across a facility. Locus Max is ideal for industrial and material handling applications.
LocusBots are fully integrated within LocusOne, a multi-bot warehouse orchestration platform that delivers predictable, efficient, and scalable productivity and cost optimization for all product movement within the four walls of the warehouse. The platform centralizes and coordinates a dynamic, multi-bot fleet while also providing detailed, forwardlooking, and actionable business intelligence and reporting for effective management and planning.
The company offers its LocusBots through a Robotics as a Service (RaaS) model. RaaS is subscription-based and helps reduce cost and operational barriers often associated with deploying new automation solutions.
For example, a company that owns its equipment depreciates it as a capital asset over its working life and is responsible for the maintenance and repair of the equipment over its lifetime. At the end of the product’s life, the company is responsible for disposing of obsolete equipment. RaaS changes all of that. In a RaaS contract, the company only pays for what it consumes, and all of the deployment, integration, support, and equipment maintenance costs are included in the service level contract. This model not only allows the company to deploy quickly but also gives the company the ability to step in if a robot isn’t operating correctly.
“Being a long-standing Körber partner and understanding our capability in delivering complete end-to-end software, robotics, and
Körber turns challenges into opportunities with a depth and breadth of technologies and expertise to conquer supply chain complexity, spanning warehouse management, warehouse control, robotics, voice, and simulation to address labor challenges through productivity gains and improve employee satisfaction and retention.Locus Robotics line of LocusBots includes the Origin, Vector, and Max and have different payload capacities for a broad range of warehouse use cases.
operational solutions, Lambert looked to us when it was time to take the next step in their warehouse digitization journey,” said John Santagate, vice president of robotics software, Körber Business Area Supply Chain. “The subscription-based model is ideal for Lambert as it provides a fast, cost-effective, flexible, and scalable robotic solution that will drive operational efficiency — next to making great strides to take account of their associates’ health, safety and wellbeing.”
Employee well-being is essential for maintaining an adequate workforce, and employee involvement in deploying AMR solutions is critical. The Körber Supply Chain Benchmarking Report 2022 showed that hiring and retaining labor remains among the top challenges for today’s supply chains. The report shows that only 37% of supply chain professionals have an adequate number of employees, and more than one in three turn over at least 50% of their warehouse associates each year.
“In an increasingly tight labor market, employee engagement is key to attracting and retaining employees. Equipping warehouse associates with the right tools and technology, such as gamification, artificial intelligence, and voice picking systems, will enable them to work as efficiently as possible while directly addressing labor challenges such as lower unemployment rates and high employee turnover,” said Sean Elliott, chief technology officer of software, Körber Business Area Supply Chain.
Körber turns challenges into opportunities with a depth and breadth of technologies and expertise to conquer supply chain complexity, spanning warehouse management, warehouse control, robotics, voice, and simulation to address labor challenges through productivity gains and improve employee satisfaction and retention.
Since implementing the AMRs, LVS has seen improvements in efficiency, productivity, and employee health and safety.
With the new system, warehouse associates’ training needs have been significantly reduced, as has the amount of walking distance those employees have to cover. According to LVS, it’s seen an up to 50% decrease in walking distance for its employees.
“We are experiencing record growth in both our consumer and professional pet-care e-commerce segments while navigating unprecedented and unpredictable labor challenges,” said Tammy Schmidt, VP/COO, Lambert Veterinary Supply. “Being able to seamlessly integrate and ramp up and down, the Robots as a Service provides us with the needed flexibility and scalability to meet our growing e-commerce customer demand while maintaining a smaller dependable team of warehouse associates and reducing onboarding of new warehouse associates to minutes from weeks.”
Altogether, implementing Locus’ AMRs from Körber resulted in minimized exhaustion, stress, and risk of injury from activities, such as loading and pushing carts for warehouse associates, and increased productivity.
Körber | korber.com
Locus Robotics | locusrobotics.com
So many exciting things are happening in warehouse automation with more innovative and e cient options than ever before. Here’s a look at a few warehouse automation technologies that sprung up or were recently enhanced with new features.
Opex is expanding the capabilities of its leading-edge Sure Sort warehouse automation technology to incorporate radio frequency identification (RFID) scanning to increase operational speed and e ciency. Sure Sort is a warehouse automation solution for distribution centers, retail stores, and third-party logistics companies that look for cost-e ective and accurate order handling, cross-docking, and reverse logistics. Opex has added the option of RFID scanning capabilities to meet evolving customer needs, especially for apparel manufacturers and retailers.
Bar codes sometimes get hidden in garments and require additional operator handling, which slows operations. Because RFID employs radio waves, scanning does not require a visual connection. In addition to the apparel industry, RFID scanning is popular for cell phone and pharmaceutical processing.
With increasing labor costs and supply chain challenges, the demand for more responsive warehouse automation technology has never been more crucial. Sure Sort robotic delivery vehicles, iBOTs, quickly and accurately process up to 2,400 items each hour with as little as three operators and can recharge as they travel through the system.
Opex introduced Sure Sort in 2017 to direct a wide range of items, including cylindrical, clear, plastic bagged, and blister pack items up to 5 lb. It can handle products as large as 15-in. long, 12-in. wide, and 6-in. high.
Features include:
Opex’s Sure Sort is a warehouse automation solution that now includes RFID scanning to increase operational speed and e ciency.
• iBOT technology powering robotic vehicles that are multi-directional, intelligent, wireless, and highly energy e cient
• Configurable sort bins, totes, and boxes
• OPEX scan tunnels that scan items on six sides and read up to eight barcodes on a given SKU
• Warehouse Management System (WMS) integration using a simplistic API
• Configurable LED pack-to-light system that notifies workers when orders are complete or additional actions are required
• An optional dimensioner that captures product attributes in real-time as items pass through the scan tunnel and provides up-to-date information to the WMS
Popular uses of Sure Sort include:
• Order fulfillment applications for e-commerce
• Retail store distribution (brick and mortar)
• Parcel sortation/presort by zip code or mail zone to reduce shipping charges
• Kitting for assembly of item-of-the-month clubs or meal delivery kits, for example
• Reverse logistics and replenishment
• Warehouse cross-docking, retail cross-docking, and sort-to-aisle where space is limited
Opex | opex.com
Murrelektronik has developed efficient and economical system solutions for integrating industrial image processing systems. The advantages include minimal installation effort as a result of decentralized, pluggable modules that can be mounted directly on the machine.
This achieves the goal of maximum performance with minimum wiring effort. The compact, powerful module is located right where it is needed. All in all, this saves installation time and reduces installation efforts while offering maximum availability enhanced by LED diagnostics each module. As a result, control cabinet components for connecting camera systems are replaced by a decentralized installation systems.
The Numina Group recently launched Pakt, a fully productized pack and ship automation solution built for fulfillment operations. Pakt breaks down the financial and operational barriers for end-of-line automation by reducing pack and ship labor and increasing throughput capacity. In addition, Pakt connects with any robotic fulfillment technology, unlocking full throughput capacity potential in the modern, e-commerce-driven warehouse environment.
Pakt is designed for distribution centers (DCs) with eight or more employees in their packing and shipping departments. The system’s modular design allows it to scale from 800 to 20,000 cartons and full case parcels per day.
Numina Group views fulfillment like a triathlon in that it has three events — picking, packing, and shipping — and warehouses are only as fast as their slowest event. After automating the picking process, the bottleneck often merely shifts to packing and shipping. Pakt eliminates the bottlenecks and labor that exist after picking, ensuring operations can fulfill orders faster and meet customer delivery expectations.
Pakt’s components are powered by RDS, Numina Group’s warehouse execution and control software, and include:
• Scan, Weigh, Vision Audit: Ensures that the right products have been picked into the right shipping container based on weight while capturing an image of the carton content.
• Print, Fold, Insertion (PFI): Automatically inserts any packing slips, marketing materials, or compliance documentation into shipping containers using a robotic arm.
• Void and Auto-Taping: Rules-based, system-directed void insertion and automatic shipping container taping.
• Print and Apply: Automatically manifests, prints, and applies labels for shipping, ASN, UCC, packing slips, packing sheets, and more.
• Shipping Sortation: Automatically sorts shipping containers based on parcel carriers, LTL, FTL, and exception designations.
Numina Group | numinagroup.com
Numina Group’s Pakt is a fully productized pack and ship automation solution that breaks down barriers for endof-line automation and increases throughput capacity.
IKO’s C-Lube linear guides have run maintenance-free for 20,000 km and beyond—thanks to our unique C-Lube technology. They also feature a compact size, high load capacity and flexible design options to achieve precise linear motion across a diverse range of industries.
To learn more, visit ikont.com/linear-guides
Exotec recently introduced three new solutions that integrate with its Skypod system: Skypath (a new conveyor system), Skypicker (an improved picking solution), and Deepsky (new proprietary warehouse software). Each of these new solutions leverages Exotec’s signature modular design allowing customers to meet their dynamic business needs by easily adding new solutions to their existing systems. The latest products bring Exotec closer to its vision of warehouses where people work smarter, not harder, through robotics.
Skypath is a modular conveyor system that can reach a maximum throughput of 2,500 totes per hour. The modular design consists of straight, curved, and inclined building blocks that fit most logistic needs and layouts and can easily adapt to customer needs.
Skypicker is an intelligent picking solution for modern warehouses. It features machine learning vision that automatically detects each item’s dimensions to intelligently place items in preparation containers in a way that optimizes the available space and smooth package handling. Improvements to the system allow the Skypicker to reach outputs of up to 600 items per hour reliably.
Deepsky is an end-to-end warehouse software that integrates Exotec technology with most warehouse management and control systems and third-party automation equipment. It automatically collects data, feeds it into pre-configured dashboards for immediate visibility, and optimizes for consistent performance.
As inflation, economic headwinds, and labor shortages continue to place mounting pressure on supply chains, businesses worldwide are looking for ways to address their immediate needs while positioning themselves for an unpredictable future. Increasingly, this means doing more with less.
Exotec | exotec.com
Exotec’s Skypicker picking automation solution uses machine learning vision to detect item dimensions, place them intelligently, and optimize available space.
Pio’s product in-out warehouse automation solution enables more e ective space usage and faster picking and packing operations.
AutoStore has launched Pio, its product in/out warehouse automation system, in North America for the first time. The plug-and-play version of AutoStore’s automated storage and retrieval system (ASRS) is tailored for small and medium-sized businesses.
Pio is a modular and scalable ASRS product that runs on standard plug-and-play software that can connect to the most common online retail and shipping platforms. The system is based on a pay-per-pick model. Similar to a robotics-as-a-service model, users will only purchase product bins and the frames that robots run on, while AutoStore owns and manages the robots, ports, and software.
Users pay a fee for each item picked, which can lower the initial investment for deployment, allowing retailers with smaller margins to access the system. Pio is aimed at small to mediumsized retailers that sell anything from apparel to sporting goods, crafts, and cosmetics. It doesn’t require any added labor or floor space to be implemented.
AutoStore | autostoresystem.com
Brain Corp announced its BrainOS Inventory Insights, a new and proprietary solution able to deliver next-generation in-store inventory analytics to retailers. The solution is in partnership with Google Cloud.
Brain Corp, which already powers the largest global fleet of autonomous robots in public spaces and the world’s largest fleet of robotic inventory scanners, will now o er retail customers a true end-to-end solution for analyzing the inventory data collected by its BrainOS-powered inventory scanning robots.
Using BrainOS Inventory Insights, retailers will be able to identify out-of-stock and low-stock events quickly, assess product details such as where an item is (product location), if it’s in the correct place (planogram compliance), and ensure it’s priced correctly (price tag compliance). By providing these highly accurate, actionable, and localized insights, retailers can intelligently manage their inventory, improve operational e ciencies, improve productivity, and elevate their customer shopping experiences across all channels to increase revenue, margins, and customer loyalty.
BrainOS Inventory Insights utilizes Google Cloud’s Vertex AI Vision models, including the product recognizer and tag recognizer models, combined with Google Cloud’s BigQuery, enabling Brain Corp to deliver this solution across retail segments at scale.
Brain Corp | braincorp.com
BrainOS helps retailers quickly identify out-ofstock and lowstock events and assess product details, such as location and price.
Today’s e-commerce market demands that Automated Storage and Retrieval Systems offer real competitive advantages
By Doug Schuchart, Global Material Handling and Intralogistics Manager, Beckhoff AutomationThe Automated Storage and Retrieval System (AS/RS) has become a fundamental piece of automated equipment in modern fulfillment centers. Once only attainable by largerscale operations, new advances now make a wide range of smaller systems available at significantly lower cost. Micro-fulfillment has also driven smaller and more flexible AS/RS options to the market. Now, scalable AS/RS solutions are available for most any size fulfillment operation, making the AS/RS a central investment in modern operations of all sizes.
AS/RS systems maximize warehouse and distribution center efficiency by tightly integrating all areas of intralogistics and saturating facilities with highly automated equipment. Common elements found in an AS/RS can include:
• Shuttle systems
• Vertical and horizontal carousels
• Cube-based storage
• Unit and mini load systems
• Vertical lift modules (VLM) and indexing conveyors (VIC)
• Goods to operator and goods to robot (G2O/G2R) pick stations
As a leading supplier of control technology in material handling and intralogistics, Beckhoff offers a broad range of technologies to help automated equipment suppliers gain a competitive advantage.
Optimized industrial networking for AS/RS applications
EtherCAT, an open, real-time and deterministic Ethernet fieldbus communication protocol developed by Beckhoff, is the backbone of Beckhoff control systems. The EtherCAT Technology Group (ETG), an independent organization that manages the EtherCAT technology with all member companies, is the largest Ethernet and fieldbus organization in the world. Adoption in material handling and intralogistics is particularly high in part due to its almost unlimited capability to control numerous devices. One EtherCAT network can accommodate more than 65,000 devices on a single linear network, such as long conveying and sortation systems. It also offers the
G2O/G2R pick stations are common elements in AS/RS solutions, as in this Honeywell Intelligrated system.
Beckhoff’s feature-rich EP7402 MDR controller benefits AS/RS applications.
ability to add many branches with zero impact on the network performance. You can go big and go long without any worry about system communication limitations.
Being the fastest fieldbus in the world, EtherCAT also has considerable benefits for AS/RS motion control requirements, network security, digitization (IoT) and machine safety. Its openness enables unrestricted communication with all other open protocols to support any brownfield or greenfield installation such as EtherNet/IP, PROFINET, DeviceNet and PROFIBUS.
Beckhoff offers a large portfolio of control technology including a wide range of compact controllers, compact plugand-play I/O solutions for any signal type, and a collection of compact, low-voltage drive technology ideal for mobile applications. Specifically for the motion control requirements of unit load and mini-load shuttles, customers can choose from compact drives that co-mingle with standard I/O signals on a traditional local or remote rack in IP20, and IP65/67-rated machine-mounted drives, as well as integrated motor drives. Drive technology is offered for servo, stepper, BLDC, as well as AC and DC motors. Beckhoff’s powerful TwinCAT automation software platform supports simple configuration of motion axes as well as CNC functions required for gantry-style unit load storage systems.
Beckhoff machine controllers with motherboards developed and produced in-house extend hardware lifecycle and offer on-board removable storage media. Local databases running alongside the PLC on the same device support local analytics of historical and real-time data with the help of the TwinCAT real-time integrated scope tools and analytics functions. This, along with the extensive diagnostics capabilities of EtherCAT, enables monitoring of equipment for predictive maintenance, ensuring the highest uptime in production and improved asset reliability.
Beckhoff combines functions integral to an AS/RS into one powerful machine controller, including vision, robotics, speech, HMI and machine learning. And for related material handling systems, such as G2O/G2R technologies, we offer innovative solutions, including Flying Motion with XPlanar and a motor-driven roller (MDR) controller that’s manufacturer agnostic.
For more information: www.beckhoff.com/intralogistics
To move fast this year, logistics companies will be looking for solutions that automate processes and increase throughput while decreasing costs. End users and OEMs need solutions that don’t require custom design and installation, but rather are standardized, easy to install, operate, and maintain, and solve multiple applications, rather than discrete devices that only satisfy a single need. And leading companies will also be looking for their solutions that include advanced data and analytics capabilities to enable better decision-making and troubleshooting.
But historically, machine vision technologies have been complex, powerful solutions that brought warehouses to a new level of automation. However, these solutions were not as pervasive because they still required a skilled engineer to operate and maintain and were challenged by the high level of variation and variability within logistics. But the recent acceleration of logistics operations caused by the pandemic and unprecedented growth in e-commerce has flipped the typical machine vision technology model on its head.
While the ultimate goal of logistics companies is to have ‘dark warehouses’ that require few workers and rely on automation and robotics, the reality is that many companies are simply trying to evolve into a more automated, connected facility. This is why technology providers have shifted their focus to the development of standard, easy-to-use vision solutions for logistics, enabled in large part by advanced technologies such as AI.
At Cognex Corporation, a machine vision leader for over 40 years, we’ve committed to creating products and solutions that will help logistics firms increase throughput, improve productivity, ensure traceability, and keep costs down. Our portfolio helps customers optimize all areas of the warehouse – from inbound and order fulfillment to sortation and outbound – with standard solutions that bypass the need for custom installation and are easier to maintain and lead to quicker ROI.
Most recently, we’ve released our new Modular Vision Tunnels, which represent the next iteration of logistics technology innovation. These standard solutions, which accurately read codes on packages at high speeds with short gaps, are helping leading logistics companies progress on their journey toward the next generation facility.
These 5- and 6-sided tunnels are quick and easy to install and address multiple challenging applications such as inbound receiving, outbound truck loading, and high-speed ship sorting. They don’t require a high-level engineer to configure and only need minimal human intervention to operate, relieving challenges related to the labor shortage. Edge Intelligence data analytics software is built within these tunnels, allowing customers to easily set up and maintain the tunnels with real-time insights into performance and maintenance.
Across other areas of the facility, Cognex is helping logistics providers be more accurate and efficient. The new In-Sight 2800 Detector, built upon AI-based edge learning technology, solves multiple sortation applications (item detection, item classification, and process issue detection) with a single device. Edge learning technology simplifies these applications for users of any skill level and represents an easy way for warehouses to automate, without a major learning curve.
Sortation integrator, SDI, is already using the In-Sight 2800 Detector at several leading retailers to accelerate item detection and classification. “The biggest feature of the In-Sight 2800 Detector as far as we’re concerned is the edge learning technology,” says Dave Bodenheimer, VP, Research and Product Development at SDI. “The ability to ignore noise on trays and detect a wide variety of products, the ease of training of the system, are all things that brought us to the new Detector.”
Cognex’s hands-free barcode reading solutions, which are mounted overhead, allow workers to use one fluid motion to scan boxes in any orientation. These solutions are simple to learn and install and free up workers from the repetitive ‘pick up, put down’ motion that handheld scanners require. Handsfree solutions offer a quick ROI and support revenue recovery, which can be instrumental in gaining more support for automation projects.
Come see us at ProMat at North Hall (N6301) to experience these solutions in action. Visit www.cognex.com/ logistics and view our Logistics Solutions Guide and ROI Calculator to learn more.
Conveyors are an integral part of many warehouses and factories, especially in material handling and packaging applications. They are found in a variety of settings, from small businesses to large distribution centers.
Conveyors can make a facility much more efficient and productive, but if they are not used correctly, they can pose a danger to staff.
By knowing how important it is to follow safety rules and make sure they are adhered to, businesses can create an environment that shows employees their health and safety are a top priority.
One of the best ways to promote safety is to make sure there are set operational procedures.
Some operational basics should require that employees know how to safely start, stop, and operate conveyors, as well as what to do in case of an emergency. More detailed instructions could show the right way to clear jams or do regular preventive maintenance.
Once the procedures have been established, ensure that all appropriate employees are properly trained. Any employee who works with or around conveyors on the warehouse floor must understand their proper operation so they can safeguard themselves and the equipment.
This education shouldn’t only occur for new hires. Rather, it should be a part of ongoing training and education, giving companies the ability to refresh procedures to ensure worker and equipment safety. It’s important that this critical information be readily available to employees and, most importantly, be enforced.
The U.S. Department of Labor’s Occupational Safety and Health Administration (OSHA) has published several safety standards for conveyor systems. Companies can mitigate injury, reduce downtime, and prevent equipment damage by adhering to these standards and establishing well-defined safety protocols.
The OSHA safety guidelines cover everything from guards and moving parts to emergency stop devices and lockout/ tagout. For a company to adhere to these safety standards, it must determine how its organization will define safety and the methods to enforce them.
These safety standards are part of daily operations, so a facility must be organized and systematic about how each standard will be presented and implemented. Details matter.
Regular safety checks on the conveyor system are an important part of making sure that employees are safe and that the equipment works.
This inspection should be conducted by a qualified technician and include a thorough examination of all components, including the belt, pulleys, motors, and other moving parts. Any damaged parts should be repaired or replaced as soon as possible.
In addition to routine inspections, it is also important to regularly clean conveyors, removing debris that could cause problems or impact performance. In general, a clean workplace is important for running a business well and keeping workers safe.
Using a conveyor eliminates the need for employees to lift heavy objects or walk long distances, reducing the risk of injuries in the workplace. It’s important, however, to understand the best type of conveyor for your facility.
When choosing a conveyor system, it is important to select one that best matches your application. You should never have to settle for a conveyor that’s good enough. Conveyors today are engineered for specific applications to best meet you production and safety goals.
For example, if you are conveying heavy or abrasive materials, a more heavy-duty conveyor rated for that load is required. Operating in an area with limited space? Consider a lift-gate conveyor or a system designed with tight turns. For operations that heavily involve e-commerce, logistics, packaging, palletizing, a conveyor with a painted frame adds much needed durability for those types of demanding, 24/7 environments.
Equally as important as selecting the right conveyor is choosing the company behind it. Dorner, a leader in industrial and commercial conveyors, has the equipment and experts to create a safe and effective working environment. As an ISOcertified manufacturer, their conveyors perform to standards that maximize production and output.
Dorner conveyors help increase productivity while promoting safety in your facility.
Original equipment manufacturers (OEMs), integrators, and end users require dynamic and reliable ways to move goods. Festo, a leading automation supplier, offers worldclass electric and pneumatic automation solutions for Intralogistics – the art of optimizing, integrating, automating, and managing the logistical flow of information and material goods within the walls of a fulfillment or distribution center.
Festo also offers productivity tools, global support, and custom solutions that ensure component interoperability and bring OEMs and integrator solutions to the market faster with less engineering overhead.
Festo offers the world’s most complete interoperable electric automation product range that provides design symmetry, streamlines design and acquisition, lowers inventory, and ensures global technical support. Key Intralogistics components include EMMT series servo motors for controllability and path accuracy in positioning applications and a space-saving single-cable solution that reduces installation effort.
EGC series axes are ideal for linear gantries and cantilevered axes. Linear actuators in the ELGA family deliver speed, acceleration, and accuracy in the most demanding applications. CMMT, a compact servo drive series, offers precise force and speed. Auto-tuning supports easy commissioning and automatically optimizes control behavior of rotary and linear motion.
The Festo Simplified Motion Series (SMS) axes offer an alternative to more expensive and complex traditional servo motion. SMS takes proven ball screw axes, toothed belt axes, mini slides, electric cylinders, piston rod, and rotary actuators and integrates them with an onboard servo drive. Users commission two-position functionality via onboard push buttons with no additional software. When controlled with IO-Link, positioning along the axis length is infinitely variable.
The company offers innovative and high-quality pneumatic solutions from servo pneumatics to the world’s first intelligent valve terminal, the VTEM, to the industry leading DFSP stopper cylinder. Festo’s core range of components meets most application needs and is readily available for quick shipping, which lowers supply chain risk. Plus, the new Festo Pneumatic Essentials program — a one-stop-shop for the 16 most applied pneumatic components — feature innovative compact design for today’s smaller footprint machines and competitive prices.
The Festo Automation Experience (AX) is a new artificial intelligence platform for predictive maintenance, predictive quality, and energy optimization. Using advanced analytics, Festo AX maps data to learn a component, machine, product, or energy system’s healthy state. It provides early-warning actionable information to correct anomalies when data trends out of normal.
Festo servo drives, integrated drives, remote I/O systems, and valve terminals are integrated into electric and pneumatic automation systems. OEMs and integrators combined Festo electrics and pneumatics into larger environments using Ethernet-based protocols, and function blocks simplify integration with Rockwell, Beckhoff, Siemens, Omron, and others.
Festo emphasizes connectivity to Ethernet-based protocols through IO-Link. Its most advanced remote I/O solutions, including CPX-E and CPX-AP-I, enable fast connection to host PLCs and the widest possible range of automation components from Festo and third-party suppliers.
CPX-AP-I, a new generation decentralized I/O, connects valve terminals and digital and analog I/O to the integrated system. CPX-AP-I can accommodate over 80 digital and analog input blocks, valve manifolds, and IO-Link master modules per system, with cable lengths up to 50 meters (164 feet), making it ideal for Intralogistics systems.
Using Festo online engineering productivity tools, such as Handling Guide Online, engineers can quickly and easily define mechatronic 1D, 2D or 3D kinematics. They can also select the matching motor and servo drive or valve terminals plus the remote I/O system, reduce design time from hours to minutes, and ensure interoperability of components.
Festo Didactic takes lifelong learning and mechatronic technical training to a new level. It provides lab-based equipment that replicates real world automation to two-year educational institutions and trains at customer sites. The Festo Learning Experience (Festo LX) is a new online portal to make it easier to create individual learning experiences.
A gantry robot (sometimes referred to as a cartesian robot) uses XYZ coordinates to move multiple axes—typically three—to a specific location within its workspace. gantry robots can be extremely beneficial for engineers that are looking to automate their warehouses, improve their current systems, or solve unique design challenges. In this blog post, we will explore a few applications where gantry robots have an advantage in comparison to other automated systems, along with the types of motor controllers and drivers needed—we will even offer a tool that will help you design your own custom gantry robot at the end.
Believe it or not, gantry robots are actually used often in everyday life. Whether it is a two-axis gantry robot, such as a crane, which can move large parts of a multiple story-high building, or even a 3D printer within a much smaller area of operation, both still rely on the same mechanics to complete the process. The benefits of a gantry robot are endless since they cater to most applications that require automated assistance—pick and place, labeling, measuring, and other processes that require both speed and precision with an outstanding return on investment. The ability to automate these procedures with a gantry robot system will allow you to turn an operation that would normally take an assembly line of three to four people into a process that requires just one, or possibly even no one, depending on how intricate the system is, i.e. peripheral AI.
A key benefit offered by a gantry robot over other automated solutions, such as an articulated robot arm or a SCARA robot system, is that they provide a more flexible workspace while enabling a much faster pick rate. The cube-shaped workspace of a gantry robot allows for easier calculation of coordinates without the constraint of a SCARA or other robotic arms’ reach. Since robotic arms and SCARA robots require a round or multi-axis workspace, the circumference will always need to be factored in when planning out coordinates. However, a gantry robot system has definitive corners to its workspace which allows for much simpler calculation.
Another aspect to consider is that most robotic arms will be defined to certain sizes which will limit its workspace, whereas a gantry can be multiple meters long! The igus® XXL Gantry, which is a large DIY, 3-axis linear gantry robot that has an action radius of 2,000 x 2,000 x 1,500 millimeters and is particularly suitable for palletizing applications of up to 10 kilograms, is a perfect example of this.
When it comes to motor controllers, you will typically need something that can control the power running through the motor, and depending on the application, you may need a controller that can also read data from the motor.
There are generally two types of controllers:
• Motor cards, also known as motor driver, motor amplifier, power amplifier, output stage, etc.
• PLC or master controller, which is a device that would do most of the reading and processing data such as controlling the speed, reading the encoder, processing other signals like limit switches.
Again, both of these depend on exactly what you need your linear actuator and/or motor to do.
These motor controllers may also come in many different variations. Although some controllers may only have switches and buttons that you can interact with, others may contain software interfaces that are capable of making precise adjustments to the motors’ capabilities. These controllers have the ability of working in tandem with a master controller to create a top-level control system. A common and popular example of this would be a CNC machine and its control system. These machines are equipped with motor drivers and other elements that are all regulated and controlled by the master system, combining it into a user-friendly digital interface.
An igus® gantry robot can be controlled directly by our own Robot Control system, which offers many advantages— smooth motion with 1/256 microstepping, Trinamics Stallguard2 and CoolStep Technologies for energy saving, an intuitive programming environment with 3D interface, and more. It is also possible to use your own control system with an igus® gantry robot, or alternatively, you may operate each axis individually with its own control system—for example, with our D1 or D3 dryve motor control system. With this configuration, you will need an additional master control system to control the coordination of the movement. Please note that a control system is not included in the box with an igus® gantry robot, but can be optionally obtained from us.
Automated systems and machines are revolutionizing storage and retrieval systems to support the demand for faster processes and efficiency gains. Sophisticated conveyors, sorters, palletizers and robotic systems can move product more quickly and reliably than traditional warehouse machinery, but they require exceptional motion products to provide accuracy and longevity. Here is an overview of some of the advanced, high-performance motion devices available and the features that make them well-suited for use in modern, automated warehouses.
• Linear Roller Guides, such as the Super MX Series from IKO International, are desirable whenever a mechanism must handle heavy loads in any direction or large moment loads. Using cylindrical rollers that make a larger contact area with the raceway than guides that use steel balls, they offer higher load ratings. The large contact area also provides exceptional rigidity with less elastic deformation under load for stable performance.IKO Super MX also has built-in C-Lube technology which provides long-term maintenance-free operation. Since lubrication maintenance is reduced, these guides are particularly beneficial for robotics in warehouses where tight spaces make lubrication difficult. And, their interchangeability allows them to be matched, replaced or freely added without replacing an entire bearing and rail assembly, giving engineers greater design freedom.
• Crossed Roller Bearings. For applications with complex rotary motion requirements, crossed roller bearings can provide high rotational accuracy and are engineered to handle radial, thrust and moment loads at the same time. Different types of crossed roller bearings can be chosen depending on the intended task and can provide extra-high rigidity or satisfy restrictive space and weight requirements for robotic devices that perform light-duty wrist and arm motion.IKO International’s lineup of crossed roller bearings provide rigidity, smooth motion and accuracy in a wide variety of sizes and types to fit various rotating and positioning mechanisms. IKO offers standard, high rigidity and mounting hole type and slim and
extra slim versions to meet a range of size and application requirements. Bearings are also available with rubber seals to protect against dust, dirt and grease.
• Linear Ball Spline Guides. Available in standard and C-Lube models, these guides have an external cylinder that enables smooth linear motion along a spline shaft, making four-point contact with the raceway. This construction allows the cylinder to move with high accuracy and rigidity, even during fluctuating and complex loads common in material handling applications such as pick and place machines. Flanged and long type cylinders are also available.
Motion products are proving essential to the automated machines and systems that are transforming storage and retrieval operations. IKO International’s lineup of linear roller guides, crossed roller bearings and linear ball splines gives machine designers the rigidity, accuracy and smooth motion these systems require along with design freedom and protection from harsh industrial conditions. That means goods can move quickly, efficiently and reliably, and machines can run longer, providing a better return on investment for automated warehousing systems.
For more information about IKO International’s motion products for automated warehouses, contact us.
Where there is e-commerce, there is inevitably logistics management. After all, what could be more efficient than a network-connected fleet of AGVs to travel around huge warehouses and find the required product in record time? These automated guided vehicles have enabled the automation of all these internal transport tasks. They are able to retrieve goods at height in vertical warehouses before transporting them to the conveying chain. In order to meet the high productivity requirements of order preparation, these AGVs must:
• Be compact and offer high power density. The robots must occupy as little space as possible in order to adapt to the confined spaces. Therefore, they need compact motors without compromising on power.
• Implement SS1 safety regulations to avoid obstacles and collisions with human operators. In terms of the drive, this involves using integrated temperature sensors in the motor as well as electronics to prevent the risk of overheating.
• Be connected to the other AGVs in the fleet, in order to be maneuvered simultaneously within the same space. This connectivity is enabled by EtherCAT, CANopen or I/O bus communication.
• With or without electronics, the IDX 56M motors meet all the criteria, whether used for a traction, lifting or steering system.
Whether rollers or belts, conveyors take care of transporting goods to the operations area, where they are scanned, for instance. During this stage, maintenance challenges are decisive, as the slightest breakdown would result in huge losses. Choosing a reliable, connected drive system to minimize maintenance operations is therefore key. This way, motors with integrated electronics can be controlled remotely and perform diagnostics or an update without having to be near the machine.
• With its communication buses, the range of IDX 56L motors can be controlled remotely, simplifying all your maintenance operations.
To arrive safely at their destination, goods need to be correctly packaged and labeled. Depending on the size and shape of the product, the packaging machines take care of this stage using multi-axis systems. Generally equipped with several independent motors, these machines require a master controller to synchronize all the operations in the chain. There are also major challenges here in terms of compact size, maintenance, and connectivity.
The ZUB master controller from maxon allows IDX 56M or 70 motors to operate in complete harmony: while one retrieves a box, the other is already preparing the tape to seal the parcel.
For more info:
Growth in automation in e-commerce - drive.tech
When both servo motors and stepper motors satisfy the basic requirements of a positioning application, it’s important to have a deeper understanding of the two technologies.
A stepper motor design uses an axially magnetized rare earth permanent magnet that is sandwiched between two toothed rotor cups. A rotor cup can have either 50 or 100 teeth, and the two rotor cups are skewed at half a tooth pitch. For a stepper motor, every tooth on both rotor cups becomes a pole.
A servo motor design uses a radially magnetized rotor instead of teeth, which is the main reason servo motors have significantly fewer poles. The low number of poles also requires the use of encoder feedback to minimize error, which increases the motor body length.
The stop accuracy of a stepper motor is dependent on its winding characteristics, rotor construction accuracy, and number of teeth/poles in its rotor. The stop accuracy of a servo motor depends on assembly accuracy, encoder resolution, and operating algorithm.
For both, friction torque or gravitational load can alter the actual stop position, so there’s a small error (+/-0.05° at most) as you move from position to position. While a stepper motor offers better repeatability at 7.2° increments or almost perfect repeatability at 360° increments, a servo motor’s stop accuracy can be improved by increasing the encoder resolution.
The high pole count of stepper motors allows them to generate high starting torque and run smoothly at low speeds. However, the torque decreases in the high-speed region due to high winding inductance, pole count, and L/R constants. The low pole count and winding inductance of servo motors allow them to maintain their torque better throughout their entire speed range.
The performance differences between a stepper motor and a servo motor can be best shown by their speed-torque curves. Stepper motors generally work better for short distances at low speeds while servo motors work better for long distances at high speeds.
A servo motor system has to operate with closed-loop control, and a stepper motor typically operates with open-loop control. A servo motor uses feedback in order to control the motor’s position, speed, or torque. A stepper motor is commanded to move to a specific location without the need for feedback but could lose synchronism due to overload.
The addition of closed-loop feedback does complicate the driver design and increases the number of components. In addition to a pulse generator, phase sequencer, and FET from a typical stepper motor system, a servo motor system also contains a rotor position counter, F/V converter, current amp, speed amp, position amp, and deviation counter. All of these components are required to run the motor in a PID loop where the driver constantly computes errors and adjusts the proportional/integral/derivative gains for correction on the fly. This is why servo motor systems are more expensive and requires more processing time.
Most stepper motors use a current chopper driver technology, which provides a constant current supply regardless of load. Current is proportional to temperature, so a stepper motor’s duty cycle needs to be limited to about 50%. Servo motors offer more efficient current control because it only draws the current it needs. However, they use more power to generate holding torque than stepper motors.
Closed-loop feedback allows more efficient current control, which affects motor temperature, duty cycle, and performance. Efficient current control also lowers noise, vibration, and energy consumption. Stepper motors tend to vibrate more when not properly sized, while servo motors tend to “hunt” more if not properly sized or tuned.
For users who are looking for a middle ground, closed-loop stepper motors are another alternative.
In the world of autonomous mobile robots (AMRs), navigation is the greatest challenge facing material handling design engineering teams. Most commonly, this is accomplished using 2-D LiDAR scanners to identify structures in an environment and map the surrounding area. Data from the scanner, and possibly other sensing technologies, is input into usercreated software to determine the robot’s location on a virtual map. This navigation technique, which does not require additional hardware such as tapes, wires, or reflectors, is called “natural feature navigation” or “free navigation.” The 2-D LiDAR scanners used to accomplish this task provide highly accurate angular position data up to a full 360° rotation, as well as distance feedback per angular step. 2-D LiDAR has undoubtedly been the optimal solution for this type of free navigation in the market for many years.
As self-driving robots continue to evolve, new technological advances are solving increasingly complex applications and behaviors. The goal is to improve warehouse efficiency, accuracy, productivity, and throughput. One example of a growing trend in the AMR market is the introduction of mobile collaborative robots or “Cobots.” A cobot is a robot designed to interact directly with a human in a shared space. This means that humans and robots must coexist in close proximity. Collaborative robots are designed for the purpose of performing specific tasks, allowing the human worker to focus on more important priorities. This interaction between robots and humans creates new challenges for AMR navigation, where advanced sensor technologies become even more critical to the design and implementation of the machine.
Traditional 2-D LiDAR solutions offer many benefits, but for this challenging application, there is one key drawback: they can only detect a target in a single plane. Imagine a scenario where a robot is following
a human target with a single-plane scanner. If the target bends down to pick up a dropped object, it will no longer be detected by the scanner. For this reason, these applications would need to use a system or scanner that can monitor objects at various height levels. This is where 3-D LiDAR or multilayer LiDAR sensors have become the ideal solution for these types of support task robots. They offer the same advantages as conventional LiDAR solutions by providing a high sampling rate and measurement density while enabling object perception in a 3-D space.
In general, the 3-D LiDAR or multilayer LiDAR sensors provide information that is critical to the navigation and maneuverability of the robot. Another important aspect of these cobots is safety. The self-driving robots must be able to safely navigate the facility and perform tasks such as following a human target without putting the robot itself or others in the facility at risk. As a result, it is common practice to incorporate additional safety-related sensor technologies to perform specific tasks such as collision avoidance. These products carry safety approval to ensure that personnel working in close proximity are protected from harm by providing the necessary redundancy and self-monitoring features. One example technology for this purpose is safe ultrasonic sensor systems. Safety ultrasonic sensors deliver reliable protection results in any environment due to their natural resistance to dirt and debris. Combining 3-D LiDAR with enhanced safety solutions changes the game for collaborative robots and makes material handling easier than ever.
In true WAGO fashion, the manufacturer is continually innovating and improving its product offering. WAGO’s 221 Series Lever Nuts are an excellent example of this, representing the company’s answer to the twist-type splicing wire connector. This termination device quickly and easily connects different wire sizes and types, using 2, 3, and 5-wire connectors.
“A few years ago, WAGO developed the original 222 Series LEVER-NUTS®, which has been effective and successful,” shares Evan Syens, Product Manager, Electrical Splicing Connectors with WAGO Corporation. “However, innovation doesn’t stop for us just because a product has hit the market. We never settle for ‘good enough’ and are always striving for better. WAGO is all about ongoing advancements.”
To this end, WAGO created their newest version wire-connector solution, the 221 Series LEVER-NUTS®— and they’ve quickly become one of the company’s top-grossing products.
“The biggest difference between the original 222 and the latest 221 Series is the size, as the newest version is smaller,” says Syens. “But, perhaps, the most notable feature of our 221 Series LEVERNUTS® products is their transparent housing, which is significant.”
This is because with a typical twist-type connector, it’s impossible to know how secure the wire connections are for each terminal, which is a maintenance and safety concern.
“The clear housing completely takes the guesswork out of the installation process,” Syens explains. “Without it, how would you know how many twists are ideal for a secure connection? There’s room for error. In fact, installers will often secure wires with electrical tape to maintain the twist-type connection. But that’s unnecessary, thanks to WAGO’s innovation. Simply pull the orange lever up, insert a stripped conductor (according to the strip-length gauge on the side of the 221) and push the lever back down. That’s it. You’re done.”
Since every 221 Series LEVER-NUTS® also includes CAGE CLAMP® technology (the spring-pressured connection technology that WAGO pioneered back in the ’50s), installers can also ensure a secure a reliable connection. The CAGE CLAMP® is starting to become the industry standard for electrical interconnection technologies.
What’s more, is WAGO has incorporated test slots in the LEVERNUTS® Series for additional safety — one in the direction of wire insertion and one on the opposite side. This allows an installer to insert a test probe into the slots to determine if a wire is live.
“Another unique feature about these products is that they’re reusable, without any added steps. For example, there’s no need to re-strip the wires. Simply lift the lever and connect the new wires,” he says. “Again, it’s that simple.”
WAGO offers two different versions of the 221 Series:
• The original variant: 24-12 AWG
• The 10 AWG variant: 20-10 AWG
“The 20 to 10-gauge version also has three variants — a 2, 3, and 5-conductor, which goes up to 600 volts and 30 amps. And, as for the operating temperature, each variant is approved to 105° C,” says Syens.
Along with these innovative connectors, WAGO also offers a line of mounting carriers that can be mounted onto a DIN Rail or chassis, easily cleaning up your cabinet, panel, or junction box.
“It’s really about peace of mind because with CAGE CLAMP® technology, you can be confident in a secure connection for your application,” says Syens.
Whether for an electrical contractor, DIY home projects, lighting applications or use in hazardous locations, WAGO’s 221 LEVER-NUTS® Series offers fast, safe, and dependable connection technology.
“Now when people see the orange lever, they associate it with WAGO and know the product can be trusted.”
• Terminate conductors from 24–10 AWG (with two models: 24-12 AWG and 20-10 AWG)
• Connect solid, stranded, and fine-stranded conductors
• Combine different wire sizes and types
• Install devices with higher levels of power consumption
• Save time connecting wires without the use of tools
Known for their dexterity and safety, Doosan Robotics
H-SERIES cobots are the most powerful in the marketplace, providing unrivaled and precise performance in palletizing. Featuring a maximum reach of 1700mm and 25kg payload, Doosan’s H-SERIES not only has a higher payload and longer reach than competitors, but it can also safely perform highly complex tasks using precise force and compliance control based on the 6-axis force torque sensors. With the highest collision sensitivity in the industry our cobots can also be trusted to share space with personnel, all while enhancing production output and maximizing labor. Doosan Robotics also delivers in a fraction of the time of industry competitors, with an average delivery time of four weeks.
Murrelektronik’s modular plug & play solutions allow you to get your vision system up and running quickly thanks to our IP67 rated modules that can be mounted on the machine. This decentralized installation concept significantly cuts planning and installation e orts. Control cabinets can be smaller and cable runs shortened when the modules are put where they are needed. In use, the detailed LED diagnostics in our solutions reduce your equipment downtime if a fault occurs in the system.
Why accept a standard product for your custom application?
NEWT is committed to being the premier manufacturer of choice for customers requiring specialty wire, cable and extruded tubing to meet existing and emerging worldwide markets. Our custom products and solutions are not only engineered to the exacting specifications of our customers, but designed to perform under the harsh conditions of today’s advanced manufacturing processes. Cables we specialize in are LITZ, multi-conductor cables, hybrid configurations, coaxial, twin axial, miniature and micro-miniature coaxial cables, ultra flexible, high flex life, low/high temperature cables, braids, and a variety of proprietary cable designs. Contact us today and let us help you dream beyond today’s technology and achieve the impossible.
Any automated system is only as good as its reliability. An automated guided vehicle (AGV) needs to do the job it is programmed to do, without error, quickly and e ciently. Therefore, the role AGVs play in materials handling is essential and their reliability is dependent on the component parts used to manufacture including robust motors. Motors for AGVs must be reliable and low maintenance and they need to be capable of being in operation 24/7 without loss of functionality.
The type of motor needed for your AGV depends on the type and size of the automated guided vehicle you have, and how much weight it will be expected to transfer at any one time. A motor that is too small won’t be able to function long and one that is too big and powerful could cause functionality issues.
The recommended motors for AGVs are brushless DC motors. Brushless motors are more powerful, quieter and lower maintenance solutions that su er less wear and tear than standard DC motors. By using the appropriate motor for the equipment it can reduce maintenance costs and diminish lost revenues from downtime.
Parvalux o ers an expanded selection of brushless motors that are highly e cient with a high starting torque. If you need something more specific, our expert team can design and build custom brushless DC motors for AGVs used in industries all over the world.
Check out the DESIGN WORLD WEBINAR SERIES where manufacturers share atheir experiences and expertise to help design engineers better understand technology, product related issues and challenges.
WEBINAR
FOR UPCOMING AND ON-DEMAND WEBINARS, GO TO: www.designworldonline.com/design-world-online-events-and-webinars
different lighting scenarios.
Soft Robotics applies NVIDIA Isaac Sim’s synthetic data to food processing automation to improve safety and increase production.
Developers have been striving to close the gap on robotic gripping for the past several years, pursuing applications for multibillion-dollar industries. Securely gripping and transferring fast-moving items on conveyor belts holds vast promise for businesses.
Soft Robotics, a Bedford, Mass. startup, is harnessing NVIDIA Isaac Sim to help close the sim-to-real gap for a handful of robotic gripping applications. One area is perfecting gripping for pick and placement of foods for packaging. Food packaging and processing companies are using the startup’s mGripAI system which combines soft grasping with 3D Vision and AI to grasp delicate foods such as proteins, produce, and bakery items without damage.
“We’re selling the hands, the eyes and the brains of the picking solution,” said David Weatherwax, senior director of software engineering at Soft Robotics.
Unlike other industries that have adopted robotics, the $8 trillion food market has been slow to develop robots to handle variable items in unstructured environments, says Soft Robotics.
The company, founded in 2013, recently landed $26 million in Series C funding from Tyson Ventures, Marel and Johnsonville Ventures.
Companies such as Tyson Foods and Johnsonville are betting on the adoption of robotic automation to help improve safety and increase production in their facilities. Both companies rely on Soft Robotics technologies.
Soft Robotics is a member of the NVIDIA Inception program, which provides companies with GPU support and AI platform guidance.
Soft Robotics develops unique models for every one of its gripping applications, each requiring specific data sets. And picking from piles of wet, slippery chicken and other foods can be a tricky challenge.
Using Omniverse and Isaac Sim, the company can create 3D renderings of chicken parts with different backgrounds, like on conveyor belts or in bins and with different lighting scenarios.
The company taps into Isaac Replicator to develop synthetic data, generating hundreds of thousands of images per model and distributing that among an array of instances in the cloud. Isaac Replicator is a set of tools, APIs, and workflows for generating synthetic data using Isaac Sim.
It also runs pose estimation models to help its gripping system see the angle of the item to pick.
NVIDIA A100 GPUs onsite enable Soft Robotics to run split-second inference with the unique models for each application in these food-processing facilities. Meanwhile, simulation and training in Isaac Sim offer access to NVIDIA A100s for scaling up workloads.
“Our current setup is fully synthetic, which allows us to rapidly deploy new applications. We’re all in on Omniverse and Isaac Sim, and that’s been working great for us,” said Weatherwax.
A big challenge at Soft Robotics is solving issues with occlusion for an understanding of how different pieces of chicken stack up and overlap one
another when dumped into a pile. “How those form can be pretty complex,” Weatherwax said.
Glares on wet chicken can potentially throw off detection models. “A key thing for us is the lighting, so the NVIDIA RTXdriven ray tracing is really important,” he said.
But where it really gets interesting is modeling it all in 3D and figuring out in a split second which item is the least obstructed in a pile and most accessible for a robot gripper to pick and place. Building synthetic data sets with physics-based accuracy, Omniverse enables Soft Robotics to create such environments. “One of the big challenges we have is how all these amorphous objects form into a pile,” Weatherwax said.
Production lines in food processing plants can move fast. But robots deployed with application-specific models promise to handle as many as 100 picks per minute.
Still a work in progress, success in such tasks hinges on accurate representations of piles of items, supported by training data sets that consider every possible way items can fall into a pile.
The objective is to provide the robot with the best available pick from a complex and dynamic environment. If
Meat-packing companies rely on lines of people for processing chicken, but like so many other industries they have faced employee shortages.
food items fall off the conveyor belt or otherwise become damaged then it is considered waste, which directly impacts yield.
Meat-packing companies rely on lines of people for processing chicken, but like so many other industries they have faced employee shortages. Some that are building new plants for food processing can’t even attract enough workers at launch, said Weatherwax.
“They are having a lot of staffing challenges, so there’s a push to automate,” he said.
The Omniverse-driven work for food processing companies has delivered a more than 10X increase in its simulation capacity, accelerating deployment times for AI picking systems from months to days.
And that’s enabling Soft Robotics customers to get a grip on more than just deploying automated chickenpicking lines — it’s ensuring that they are covered for an employment challenge that has hit many industries, especially those with increased injury and health risks.
“Handling raw chicken is a job better suited for a robot,” he said. RR
The SHA-IDT Series is a family of compact actuators that deliver high torque with exceptional accuracy and repeatability. These hollow shaft servo actuators feature Harmonic Drive® precision strain wave gears combined with a brushless servomotor, a brake, two magnetic absolute encoders and an integrated servo drive with CANopen® communication. This revolutionary product eliminates the need for an external drive and greatly simplifies wiring yet delivers high-positional accuracy and torsional stiffness in a compact housing.
• Actuator + Integrated Servo Drive utilizing CANopen® communication
• 48 VDC nominal supply voltage
• A single cable with only 4 conductors is needed: CANH, CANL, +48VDC, 0VDC
• Zero Backlash
• Panel Mount Connectors with radial and axial options
• Dual Absolute Encoders
• Output Encoder: 16bit (65,536 cpr) resolution
• Input Encoder: 17bit (131,072 cpr) resolution
• Control Modes include: Torque, Velocity, and Position Control, CSP, CSV, CST
Like many companies that turn to automation, FMO Surface had difficulty attracting human employees for monotonous yet demanding tasks.
FMO Surface, a family-owned company that specializes in finishing plastics, was founded in 1999 in Lemgo, Germany and employs 75 people. The company’s customers come from a variety of industries, including automotive, electronics, aerospace and mechanical engineering. Manufacturers that produce bicycles and household appliances also make use of FMO Surface’s services.
Because approximately seven million plastic bus connectors are laser-marked with eight-digit data matrix codes (DMC) here every year before being installed in controllers, FMO Surface began to automate various related processes several years ago. Companies such as FMO Surface find it increasingly difficult to attract human employees for monotonous yet demanding tasks such as checking DMCs.
It found a job for its new LBR iisy, a collaborative robot arm from KUKA, in bus connector quality control. Because multiple components are marked with a
DMC and are dependent on one another, reliability is of decisive importance for the traceability of an entire module. For this reason, the readability and completeness of the Data Matrix codes require special quality control attention, previously carried out manually with a scanner by human employees at FMO Surface.
“We save an enormous amount of time using the LBR iisy because we no longer have to scan each part individually,” said Tim Hertz, laser department foreman, FMO Surface. “And if the cobot reports a fault, we don’t have to open a cage or stop an entire system; we simply remove the defective part and replace it.” This type of quality inspection helps keep the price of production and finishing down.
Solution
Equipped with dual Keyence cameras, the LBR iisy cobot checks DMCs. Each tray that slides under the LBR iisy contains 200 plastic parts. One camera carries out the quality inspection with associated software, while the second camera assesses codes for completeness.
“The first step spot checks the quality of the codes on the basis of 20 parts,” explained Hertz. “If everything is OK, the cobot moves over the tray again to check whether all 200 parts are present and all codes are readable.”
If the robot finds an issue with a code, it stops and points out the affected bus connector. A human colleague then replaces the faulty part; the robot checks the tray again and ideally releases it. This human-robot collaboration ensures maximum safety and efficiency.
With the aid of the KUKA smartPAD pro and the KR C5 microrobot controller, even employees with virtually no experience in robot programming can operate and train the cobot.
“The LBR iisy runs on the basis of the new iiQKA.OS operating system, which makes it easy to install, configure and program,” said KUKA’s Robert Korte. The cobot not only is up and running in just a few minutes but can adapt to new challenges equally quickly. That’s an enormous advantage for Fest: “We don’t have engineers here, so ease of integration is all the more important.”
Bastian Fest, managing director of FMO Surface, met Korte at a trade show and learned about the advantages of the LBR iisy collaborative robot. Fest then took a closer look at the LBR iisy at KUKA’s branch office in Siegen and decided to purchase it.
“The LBR iisy combines several factors that we require: flexibility, ease of programming and suitability for collaborative operation. That is why we purchased it, even without actually knowing where exactly we wanted to use it,” said Fest of this seemingly unusual approach.
Say hello to the
The safest cobot on the marketplace, delivered in 4 weeks or less.
Six-axis articulation
Force torque sensors on each axis
PLe CAT 4 Safety Rating
1700mm Reach 25kg Payload
The employees at FMO Surface were enthusiastic about the new colleague right away.
“Thanks to the safety features, collaboration with people in a single workspace is possible,” said KUKA sales engineer Robert Korte.
In the past, this type of quality control for DMCs was much more time-consuming. “When checking for completeness, we had to scan each part individually,” said Hertz. For this, an employee had to take the components out of the tray and subsequently put them back again. Today, with the LBR iisy, this task is performed much faster and more precisely.
FMO said the LBR iisy cobot could also provide valuable services in pad printing in the near future. Furthermore, the company hopes to make use of the larger versions of the LBR iisy with their payload
capacities of 11 and 15 kilograms.
FMO Surface has also collaborated with KUKA on using a KR CYBERTECH nano (KR 10 R1420) robot arm for palletizing and to tend a laser system. Two years later, FMO Surface added another industrial robot om the KR CYBERTECH series to turn over, measure and laser plastic parts to be finished.
“Particularly in view of the shortage of skilled workers, automation plays an important role for a medium-sized company like ours,” said FMO Surface. RR
Turnkey or custom automation solutions for less Gantry Robots Delta Robots
7th Axis for Robots
Gearboxes & Motors Control & Software
X Low-cost automation solutions
X • ROI after 3 to 18 months
X • Free training courses
X • No minimum order quantity
X • Free software packages
X • RBTX online robotic marketplace
Co-development projects where
The past few years have seen many organizations implement techdriven changes at a rapid pace. As society becomes more digital, embracing technology and effectively managing new processes is key to the success of almost every business.
With rapid workplace transformation evident across industries, whether that’s moving to hybrid working or adopting new technologies, what can we expect from 2023? Here are five predictions for the coming year.
In recent years, we have witnessed the development of many different types of sophisticated technologies. Advances in robotics, machine learning and other technologies have increased the pace of this change tenfold. While these promise to change or revolutionize the business world, all technology companies suffer from the same problem – they can’t be good at everything.
In the world of robotics, this is no different. Creating a robotic system requires hardware development, software development, application
development, sensors, and interfaces to name a few. That’s why 2023 will be the year of turnkey solutions.
Original equipment manufacturers (OEMs) – companies creating new applications and products around existing technologies – will lie at the heart of this. They are able to drive innovation by combining technologies to deliver complete solutions for the most common applications, such as welding and palletizing. The result? Automation will become more sophisticated yet more straightforward to use than ever before.
Enabled Robotics, an OEM based in Denmark, is a great example of how this works. Since 2016, the company has been working to combine two types of cutting-edge technology by mounting
collaborative robot arms (cobots) onto autonomous mobile robots (AMRs). This hybrid technology is now operating in industry, warehouse management and production and bringing robotics to service applications and hospital intralogistics.
Ultimately, these out-of-the-box solutions make it easier for companies to integrate crucial technologies and there is no limit to the imaginative ways companies will find to bring robots alongside humans in the world of work.
Traditional industrial robots remain important in manufacturing, but we are seeing a trend towards deploying more flexible models of production. This is largely due to the fact that traditional industrial robots are typically large and fixed and entail complex deployment.
In contrast, cobots can perform a similar range of activities to traditional industrial robots but are smaller, lighter and easier to deploy. They are designed to work alongside humans and are better suited to environments that require flexibility and adaptability. On top of this, they are most cost-effective for businesses looking to deploy automation – a key consideration as we move into 2023.
The cobot industry is projected to grow to USD 2.2 billion by 2026 (The Collaborative Robot Market 2022 Report, Interact Analysis). As cobots continue to change the way work is done in applications such as packing, palletizing, welding and assembly, in 2023 we will see even larger companies turning to lightweight cobots to increase modularity in their production. Robot weight and versatility will be key specifications for those looking for new automation solutions and we will see more reconfigurable robotic work cells than ever before.
As more companies move towards cobot automation, many will still want to handle heavy payloads. The good news is that we have recently seen the introduction of several higher payload, longer-reach cobots. In 2023, these will continue to transform parts of the manufacturing industry, improving the working lives of many employees. Universal Robots introduced in 2022 a new cobot, the UR20, which is built for higher payloads, faster speeds, and superior motion control all within a lightweight, small-footprint system. The 20 kg payload capacity will transform
industries such as palletizing while its 1750 mm reach is eagerly anticipated for use in welding. Manufacturers looking for that extra flexibility will find the robot light enough to be unbolted and relocated or attached to a heavy base with wheels. This will create new possibilities for applications and will drive innovation across the board. The UR20 will be delivered to customers in 2023.
The recent IFR World Robotics Report showed industrial robot installations reached an all-time high in 2021, increasing by 31% over the previous year. Overall, worldwide annual robot installations between 2015 and 2021 have more than doubled. Although growth in 2022 seems to be slower across the sector, this is largely down to global uncertainties triggered by the pandemic and scarcity of electronic components.
We expect the upward trend of cobot automation to resume in 2023. Why? Because businesses across the world are facing labor and skills shortages and, despite the day-to-day challenges facing industry right now, we are in the midst of a transition towards industry
5.0 where working alongside robots will create more human-centric, sustainable and resilient businesses.
5. Customers will be found at the heart of product development
Although we talk extensively about robot collaboration in the workplace, human collaboration is what drives innovation.
Customers understand their own needs better than anyone else and, as the automation market has matured, are better placed than ever before to offer valuable input on their requirements. This means robotics companies will involve customers much more in product development. It is why Universal Robots has reorganized its product creation teams and is focusing heavily on understanding the problems customers are facing before designing solutions.
Co-development projects where robotics companies and customers work together in developing specific solutions
are also bound to increase in 2023 and beyond. Ultimately these allow customers to directly influence the product they are buying, while at the same time delivering valuable feedback for the robotic companies – meaning they will be able to launch a product to the benefit of the whole market.
Now more than ever, businesses need to innovate constantly and remain adaptable in order to survive and expand. As we head into 2023, they will rely ever more on technology and innovation to break new ground with turnkey solutions at the heart – all of which make the year ahead an exciting time for automation. RR
Anders Billesø Beck leads the development of cobot technologies to keep global businesses agile, productive and innovative. Anders is vice president for strategy and innovation at Universal Robots, the global leader in flexible automation, and holds a Ph.D. in robotics om DTU, the Technical University of Denmark.
He is a former elite swimmer and member of the Danish national team, and he has also held leading positions at the Danish Technological Institute. Anders combines his scientific background with contributions to the global collaborative automation industry to change the way the world works.
So much happens between issues of R&D World that even another issue would not be enough to keep up. That’s why it makes sense to visit rdworldonline.com and stay on Twitter, Facebook and Linkedin. It’s updated regularly with relevant technical information and other significant news for the design engineering community.
According to researchers at Carnegie Mellon University (CMU), even simple robotic grippers can solve some complex manipulation tasks. Sometimes they just need a little help om their environment by pushing an object against a table or a wall.
This is known as “Extrinsic Dexterity.” The CMU team said previous work in extrinsic dexterity used careful assumptions about contacts that impose restrictions on robot design, robot motions, and the variations of the physical parameters. They tried to improve upon these limitations by developing a system based on reinforcement learning (RL).
They studied the task of “Occluded Grasping,” which aims to grasp an object in configurations that are initially occluded; the robot needs to move the object into a configuration om which these grasps can be achieved. The policy learns emergent behaviors of pushing the object against the wall to rotate and then grasp it without additional reward terms on extrinsic dexterity.
“This research may open up new possibilities in manipulation with a simple gripper,” said study Wenxuan Zhou at Carnegie Mellon University. “Potential applications include warehouse robots or housekeeping robots that help people to organize their home.”
The team used reinforcement learning to train a neural network and tested the system in the MuJoCo physics simulator. The simulated robot attempted to grasp objects and was rewarded when successful.
The researchers then zero-shot transferred the technology to a physical robotics system, which consisted of a Frank Emika robotic arm and a parallel gripper. The robot grasped items confined within an open bin that were initially oriented in ways the robot couldn’t handle. It then needed to figure out how to use its environment to create success picks, for example, by pushing an item against the wall of the bin to reorient said object.
Here’s an example of how the gripper could use its environment to help grasp an object. The gripper first moves close to the object and makes contact on the side of the object with the top finger. It then pushes the object against the wall to rotate it. During this stage, the gripper
With the exploitation of external resources such as contact surfaces or gravity, even simple grippers can perform skillful maneuvers that are typically studied with a multifingered dexterous hand.
| Carnegie Mellon Universityusually maintains a fixed or rolling contact with the object, but sliding also occurs. The object might have sliding or sticking contacts with the wall and the ground. After the gripper has rotated a bit further and the bottom fingertip is below the object, the gripper will let the object drop on the bottom finger. After that, the gripper will try to match the desired pose more precisely. At this point, the policy has executed the grasp successfully and it is ready to close the gripper.
According to the researchers, one of the key decisions in this strategy is to use the top finger to rotate the object instead of the bottom finger. One might suppose an alternative approach which is to use the bottom finger to scoop the object against the wall and then directly roll the finger underneath the object to reach the grasp. However, this strategy is not physically feasible on the parallel gripper due to the limited degree of freedom of the finger.
Another successful strategy is to flip the object to stand on its side and then move to the grasp. This strategy relies on the fact that the object remains stable after the rotation.
The researchers tested the system on items that varied in weight, shape and slickness, including cardboard boxes, plastic bottles and a container
According to researchers at Carnegie Mellon University (CMU), even simple robotic grippers can solve some complex manipulation tasks. Sometimes they just need a little help from their environment by pushing an object against a table or a wall.
CGI Motion standard products are designed with customization in mind. Our team of experts will work with you on selecting the optimal base product and craft a unique solution to help di erentiate your product or application. So when you think customization, think standard CGI assemblies.
Connect with us today to explore what CGI Motion can do for you.
of whipped cream. According to the researchers, the simple grippers successfully grasped items 78% of the time.
The researchers also employed a lowlevel controller due to the fact that they expected the agent to use extrinsic dexterity which involves rich contacts among the gripper, the object and the bin. They choose operation spacecontrol (OSC) as the lower-level controller to execute the policy output which operates at a higher frequency than the RL policy. Given a desired pose of the end-effector, OSC first calculates the corresponding force and torque at the end-effector to minimize the pose error.
Then, the desired force and torque of the end-effector will be converted into desired joint torques according to the model of the robot. We choose relatively low gains so that the controller becomes compliant in the end-effector space. There are two benefits of a compliant OSC in such a contact-rich manipulation task with extrinsic dexterity:
“First, being compliant in end-effector space allows safe execution of the motions without smashing the gripper on the objects or the bin. Limiting the delta pose and selecting proper gains will limit the final force and torque output of the end-effector. If we use a controller that is compliant in the joint configuration space instead, we will not have direct control over the maximum force the end-effector might have on the object and the bin. Second … using OSC as the low-level controller might speed up RL training and improve sim2real transfer for contact-rich manipulation.”
Next steps
One limitation of this work, the researchers admitted, is that the policy was trained with box-shaped objects. Although it may generalize to other shapes to some extent as shown in the experiments, the policy might be improved by including other shapes during training.
In addition, the pose of the object alone may not be sufficient to generalize to novel objects. The CMU team said that using a better representation of the shape, such as a point cloud or keypoints, could improve generalization across shapes. However, these changes would also increase the training complexity.
Another limitation is that we assume a reasonably accurate robot and gripper model, in terms of geometries, kinematic and dynamic parameters. It would be interesting to explore how to extend the method to transfer across robots and grippers.
Despite the simplicity of the proposed method, the researchers stress the following two key takeaways.
“First, we provide a concrete example that a simple gripper can do much more than pick-and-place while being cheaper and easier to maintain than a dexterous hand, following previous work in extrinsic dexterity,” the team said. “We envision more future work in this direction in manipulation. Second, RL can be a good option to generate policies with emergent extrinsic dexterity, and sim2real transfer works reasonably well with our proposed system. Our work takes a step towards deploying contactrich policies with a simple gripper in the real world.” RR
At CGI we serve a wide array of industries including medical, robotics, aerospace, defense, semiconductor, industrial automation, motion control, and many others. Our core business is manufacturing precision motion control solutions.
CGI’s diverse customer base and wide range of applications have earned us a reputation for quality, reliability, and flexibility. One of the distinct competitive advantages we are able to provide our customers is an engineering team that is knowledgeable and easy to work with. CGI is certified to ISO9001 and ISO13485 quality management systems. In addition, we are FDA and AS9100 compliant. Our unique quality control environment is weaved into the fabric of our manufacturing facility. We work daily with customers who demand both precision and rapid turnarounds.
CS Hyde Company
FEP Film: The transparent film on the bottom of the resin tank
FEP Film has become an ideal solution for SLA and DLP printers as a surface film for the bottom of the resin tank. Coupled with clarity and release properties, FEP is an ideal barrier film that allows light transmission while extending stability and strength for resin 3D printing.
CS Hyde is a stock supplier and converter of FEP & PFA film available in a variety of thicknesses. We also o er specialty adhesive lamination to FEP film, as well as custom width slitting, sheeting, and tight tolerance die cutting. Other polymer films available include ULTEM® PEI, TPX®, Kapton®, Mylar®, and many other engineering and high-performance plastics.
CGI Inc. 3400 Arrowhead Drive Carson City, NV 89706
Toll Free: 1.800.568.4327
Ph: 1.775.882.3422
Fx: 1.775.882.9599
WWW.CGIMOTION.COM
Contact
www.cshyde.com
1.800.461.4161
Known for their dexterity and safety, Doosan Robotics H-SERIES cobots are the most powerful in the marketplace, providing unrivaled and precise performance in palletizing. Featuring a maximum reach of 1700mm and 25kg payload, Doosan’s H-SERIES not only has a higher payload and longer reach than competitors, but it can also safely perform highly complex tasks using precise force and compliance control based on the 6-axis force torque sensors. With the highest collision sensitivity in the industry our cobots can also be trusted to share space with personnel, all while enhancing production output and maximizing labor. Doosan Robotics also delivers in a fraction of the time of industry competitors, with an average delivery time of four weeks.
Doosan Robotics
doosanrobotics.com
The drive wheels on Autonomous Mobile Robot platforms benefit from the inherent characteristics of harmonic planetary technology; primarily, smoothness of travel, backdrivability, and an e ciency curve that does not degrade over time. The integral cross roller bearing construction contributes to an excellent balance of torque density, sti ness, and radial load support in a compact and reliable package. Available in dozens of standard reduction ratios, these low backlash drive trains include motor adaptation as required.
3D printed robotic grippers from igus® utilize wearresistant iglide® 3D printing materials, with wear rates comparable to similar injection-molded components. iglide® 3D printing materials contain embedded lubricants, eliminating the need for routine maintenance and making them resistant to dirt and dust. 3D printing allows for complex geometries not normally possible with injection molding, ensuring you can find the exact solution required for your application. Choosing 3D printed grippers can also save up to 85% in costs and reduce manufacturing time by about 70%. Whether you need a single prototype, or plan to outfit an entire line of robots, igus® can provide a solution — no minimum order quantity required!
Here at Lin Engineering, we find solutions to your problems by focusing on three basic elements: Find, Optimize, and Integrate. There are such a vast number of products on the market that just narrowing the options can be di cult. Our engineers will help you find the motor you need. The motor may then be optimized for your application by changing the winding, magnets, bearings, and more. We work with your team throughout this process to configure the motor to your application so it can be seamlessly integrated within your product or assembly.
Contact Info: Sarah Phann sphann@igus.net
Contact info: Lin Engineering 16245 Vineyard Blvd. Morgan Hill, CA 95037 https://www.linengineering.com/ 1.408.919.0200
Today’s AGVs must be compact and functional robots which are able to move vertically and carry heavy loads. These AGVs cannot fail, and so the choice of their motorization is crucial. There are 5 key points to consider when motorizing an AGV.
1. Choose compact motorization where possible - Drives must fit into restricted spaces, as they are sometimes integrated into existing trucks. A small footprint is critical for applications in logistics.
2. Focus on ease of use – select a plug-and-play solution.
3. Opt for fast delivery of your motor solution
4. Base the design on modularity - Not all AGVs do the same job and therefore having the flexibility to select a solution to match needed specifications is essential.
5. Prioritize safety – select motor options with integrated sensors.
maxon’s IDX motor has a diameter of only 56 mm, its performance is equivalent to that of a motor with a footprint 25% larger. The IDX motorization thus combines performance in a compact size and ideal for AGVs.
Go to Drive.tech for more details. Visit www.maxongroup.us for more maxon solutions.
Motus Labs Introduces Orbital Flex Design™: Motus Lab’s patent-pending Orbital Flex Design™ (OFD) is a new gear design which focuses on delivering zero backlash and high torque density gear solutions. The solid rigid cup enables OFD to remain consistent for the life of the gear without the common performance degradation found in most gear solutions.
The Motus Labs Orbital Flex Design™ (OFD) delivers:
• Superior performance
• Lower cost of ownership for robotic and motion control solutions
• Improved ROI for customers
Why accept a standard product for your custom application?
NEWT is committed to being the premier manufacturer of choice for customers requiring specialty wire, cable and extruded tubing to meet existing and emerging worldwide markets. Our custom products and solutions are not only engineered to the exacting specifications of our customers, but designed to perform under the harsh conditions of today’s advanced manufacturing processes. Cables we specialize in are LITZ, multi-conductor cables, hybrid configurations, coaxial, twin axial, miniature and micro-miniature coaxial cables, ultra flexible, high flex life, low/high temperature cables, braids, and a variety of proprietary cable designs. Contact us today and let us help you dream beyond today’s technology and achieve the impossible.
Advancing innovation for over 100 years Contact info: New England Wire Technologies www.newenglandwire.com 603.838.6624
Robots are flexible and adaptable. Quickly re-tasking robots for job variety can be challenging.
Some common solutions: Changing workpieces – Quick-change gripper fingers and gripper changeouts are easily automated for workpiece variety or changing workpiece characteristics during manufacturing.
Flexible machine table fixtures – Robots are widely identified for their ability to handle workpieces. They also excel at automatically replacing fixtures and other peripheral tooling.
Automating multiple tasks – Use the robot to accomplish a secondary task. Instead of remaining idle during machining, the robot can automatically deburr workpieces.
Adjustable custom tooling – Use dove tails and adjustable mountings in EOATs to expand tools for changing conditions or reach requirements.
Many standard solutions are available - make the most of your investment with automation expert support today!
SCHUNK: 211 Kitty Hawk Drive, Morrisville, NC 27560 919-572-2705 info@us.schunk.com
Zero-Max, Inc.
zero-max.com
The recently released Zero-Max IP65-rated Crown Gear Drives are used in the OpenAire Vertical Opening Glass Wall System for a swimming pool enclosure on a Cruise Ship. This retractable Wall System provides a naturally ventilated, healthy, safe, and energy-e cient environment made possible with a mechanical drive system using the drives.
The IP65-Rated Crown Gear Drive features nickelplated aluminum housing, stainless-steel shafts, and includes purpose-built shaft seals. It provides an added level of protection to withstand conditions such as frequent washdowns, corrosive elements, and outdoor installations that can include temperature extremes, sunlight, rain, humidity, and condensation. This fully enclosed design prevents contamination from water, chemicals, and debris, allowing it to hold up to harsher operating environments.
Another important feature is the drives are pre-lubricated, making them a “Lubed-for-Life” design o ering maintenance-free operation for the life of the product. Most important, these Zero-Max Crown Gear Drives have been tested by an independent laboratory to obtain the IP65 Certification for ingress protection against dirt and water.
Heilind Electronics
heilind.com
Heilind Electronics, a distributor of electronic components and authorized distributor for Molex, is stocking and shipping Molex’s OneBlade 1.00 mm Wire-to-Board Connector System.
OneBlade connector’s single housing can be used interchangeably as a vertical or right-angle header consisting of only three components, which mitigates the risk of material shortages. This also means less production tooling is required; the innovative design allows Molex to invest in additional capacity when needed to support customers’ demands in a timely manner.
The connectors also feature a housing designed for vacuum pick and place, removing the need for cover tape, and increasing production e ciency.
OneBlade Wire-to-Board Connector System’s dual-contact design o ers secure electrical contact and reliability for disruption-free operations. These products are suitable in consumer, home appliance, and data center applications.
A World-Class brand.
Miki Pulley established its business roots by providing variable speed belt drives to the burgeoning Asian machine industry several decades ago. Over time, our product line has evolved to serve many more facets of motion control. With offices, production facilities, and partner companies spanning the globe, our Customer Service and Engineering expertise are positioned at the forefront of our industry.
We collaborate with Design Engineers to identify the most efficient, cost effective solutions for their rotary motion control and mechatronic applications.
We offer electromagnetic clutches and brakes for a variety of motion control applications. Additionally, we offer high performance servo couplings, jaw & spider style couplings, and high-speed metal disc couplings. Keyless shaft locking devices also bring a very simple, but important element to our product offering. We also offer downloadable 3D CAD models on our user-friendly website.
Miki Pulley US
13200 Sixth Ave. N Plymouth, MN 55441-5509 800.533.1731
www.mikipulley-us.com
www.designworldonline.com/leadership
Nominate engineering leadership for a person or inventor, engineering leadership by a specific department, or an overall company accomplishment.
PRODUCT LINE INCLUDES:
• Electro-Magnetic Brakes
• Electro-Magnetic Clutches
• High Performance Shaft Couplings
• Keyless Shaft Locking Devices
BXW BRAKE:
This unique, low profile design is 2/3 the thickness of other brakes that Miki offers.
BXR-LE BRAKE: Provides highly responsive braking and holding power while minimizing battery usage for AGV applications.
ALS MACHINED COUPLING:
Offering high torque and response with a shore hardness of 97 these couplings are available with clamping hubs or set-screw hubs for a wide variety of applications.
Rollvis SA was founded in Geneva in 1970 and our production facility is located in Plan-Le Ouates, known as the cradle of high precision engineering in Geneva.
While benefiting from more than half a century of experience and growth, we have dedicated ourselves to the design and production of the highest quality planetary Roller Screws.
Contact us:
Rollvis USA
Tel: 832-302-0951
lee@rollvis.com
www.Rollvis.com
www.designworldonline.com/leadership
Nominate engineering leadership for a person or inventor, engineering leadership by a specific department, or an overall company accomplishment.
The aerospace segment is key for Rollvis, with a long history of serving customers in this area. We have robust processes and maintain an EN9100 certification in addition to our regular ISO9001. As a key supplier we work with customers from early in the concept stage to develop and produce the highest quality parts.
Planetary roller screws are a proven technology for the most demanding applications where high load and high reliability are required. The original planetary roller screw patent dates back to 1942. The orbiting rollers have a carefully ground profile and the design includes synchronizing gears that assure the optimal kinematics are maintained. These design features make roller screws ideal for many specialty applications, including replacing hydraulic pistons where a high load density is required.
Roller Screws are not catalog items. The vast majority of parts produced by Rollvis are not made per catalog dimensions. This includes customized dimensions and features on the nut which allow the screws to be more easily integrated to customer assemblies. Customization does not need to cost more to your project. Have a discussion with your local Rollvis support person to see how customizations could be a part of your design.
SALES
Ryan Ashdown rashdown@wtwhmedia.com 216.316.6691
Jami Brownlee jbrownlee@wtwhmedia.com 224.760.1055
Mary Ann Cooke mcooke@wtwhmedia.com 781.710.4659
Jim Dempsey jdempsey@wtwhmedia.com 216.387.1916
Mike Francesconi mfrancesconi@wtwhmedia.com 630.488.9029
Jim Powers jpowers@wtwhmedia.com 312.925.7793 @jpowers_media
Courtney Nagle cseel@wtwhmedia.com 440.523.1685
@wtwh_CSeel
LEADERSHIP TEAM
Publisher
Mike Emich memich@wtwhmedia.com
508.446.1823
@wtwh_memich
CEO
Scott McCafferty smccafferty@wtwhmedia.com
310.279.3844
@SMMcCafferty
EVP
Marshall Matheson mmatheson@wtwhmedia.com
805.895.3609
@mmatheson
DESIGN WORLD does not pass judgment on subjects of controversy nor enter into dispute with or between any individuals or organizations. DESIGN WORLD is also an independent forum for the expression of opinions relevant to industry issues. Letters to the editor and by-lined articles express the views of the author and not necessarily of the publisher or the publication. Every effort is made to provide accurate information; however, publisher assumes no responsibility for accuracy of submitted advertising and editorial information. Non-commissioned articles and news releases cannot be acknowledged. Unsolicited materials cannot be returned nor will this organization assume responsibility for their care.
DESIGN WORLD does not endorse any products, programs or services of advertisers or editorial contributors. Copyright© 2023 by WTWH Media, LLC. No part of this publication may be reproduced in any form or by any means, electronic or mechanical, or by recording, or by any information storage or retrieval system, without written permission from the publisher.
Subscription Rates: Free and controlled circulation to qualified subscribers. Nonqualified persons may subscribe at the following rates: U.S. and possessions: 1 year: $125; 2 years: $200; 3 years: $275; Canadian and foreign, 1 year: $195; only US funds are accepted. Single copies $15 each. Subscriptions are prepaid, and check or money orders only.
Subscriber Services: To order a subscription or change your address, please email: designworld@omeda.com or visit our web site at www.designworldonline.com
DESIGN WORLD (ISSN 1941-7217) is published monthly by: WTWH Media, LLC; 1111 Superior Ave., Suite 2600, Cleveland, OH 44114. Periodicals postage paid at Cleveland, OH & additional mailing offices.
POSTMASTER: Send address changes to: Design World, 1111 Superior Ave., Suite 2600, Cleveland, OH 44114
“Dumber than a box of rocks” is a colorful idiom. Suppose it is wrong. Suppose a box of rocks is actually smart.
I will admit I checked the cover of Power magazine when I first read about thermal energy storage using a box of rocks. I checked to make sure it wasn’t the April Fool’s Day edition. The article indicated a box of rocks was an intelligent solution to the vexing problem of storage of renewable energy.
Renewable energy immediately conjures images of windmills and photovoltaic panels and disproportionately means renewable electricity. Windmills and photovoltaics share one shortcoming, intermittency. Power grid operators love dispatchable power sources, plants they can summon when needed. Grid operators can’t summon solar energy at night or wind energy when the wind isn’t blowing — so storage is the obvious answer.
Electricity storage conjures images of batteries, large banks of batteries collecting electrical energy and making it dispatchable. That image is o target. Electricity is being stored today, but not very much by batteries. Pump hydro provides most of the electricity storage, by some accounts, 96% of the 4.67 TWh of total storage capacity. The world currently uses around 28 PWh of electricity. We don’t currently store much electricity, relying on dispatchable fossil generation to keep the lights on.
Battery storage capacity is estimated to be ~56 GWh, needing to grow by 15-17x to yield stable electricity supply by 2030 due to decarbonization. Most battery storages use lithium-ion batteries and, while other chemistries are being deployed, most estimates are for lithium-ion to be the dominant battery chemistry for stationary, transportation, and portable applications. Costs have dropped significantly, but lithium-ion batteries are still the most
expensive commonly used batteries. Lithiumion batteries seem to be the smart solution for energy storage, but there are drawbacks, their performance degrades both with number of cycles and calendar age. Plus, they don’t last forever, and overheating and fires can occur. A plain old box of rocks, dumb as it may sound, may prove to be a smarter solution. Siemens Gamesa Renewable Energy is one of the companies developing electric thermal energy storage (ETES), currently in operation in a large pilot. 1,000 tonnes of volcanic rock are the storage medium. Resistance heaters make hot air, heating the rock to 650° C when electricity is in surplus. When electricity is needed, steam is made to power a turbine. This is a new spin on simply storing and using the heat. It allows the use of existing power generation capacity as fossil plants are decommissioned. The technology has been under development since 2014 and piloted starting in 2019.
There are disadvantages, for sure. Battery systems are more e cient, with roundtrip e ciency around 80%. It is only about 50% for ETES, over 95% to heat. The advantages are cost and longevity: rocks are cheap and don’t age. The estimates are that the initial capital will be well less than half of a battery system. Rocks also don’t catch fire. There is no concern about there being su cient rocks, while there are concerns about supplies of battery materials. Recycling, a concern in batteries, is not with rock. It is quite possible a box of rocks is an intelligent solution. DW
As a leading manufacturer of precision-engineered fluid power products, Permco designs and builds the best-value solutions that uniquely fit their customers’ needs. With a decades-long tradition of exceptional customer service, Permco offers the highest quality product available to a wide customer base of OEM’s and distributors. Permco understands that the only success that matters is the success of their customers and are committed to reducing costs while continuing to make the process of doing business easy. With Permco, it’s personal.
• Resolution ≤5 mV
• Accuracy ±0.25% of full scale
• Real-time adjustable PID control
• Integrated 0 to 10 VDC, 4-20 mA signal, or 3.3 VDC serial communication
• 0 to 10 VDC feedback pressure monitor
• Virtually silent
• No integral bleed required
• Multiple pressure ranges from vacuum to 150 psig
• 2.7 to 65 l/min flow control
The future of proportional control has arrived— and it’s digital. The Clippard Cordis is a revolutionary microcontroller primed for escape velocity from a proportional control market that has grown stagnant.
With unparalleled performance and flexibility not possible with current analog proportional controllers, the Cordis makes everything from calibration, to sensor variety, to future development opportunities more accessible and less complicated.
Contact your distributor today to learn more about how the Cordis can provide precise, real-time control for your application, or visit clippard.com to request more information.
877-245-6247