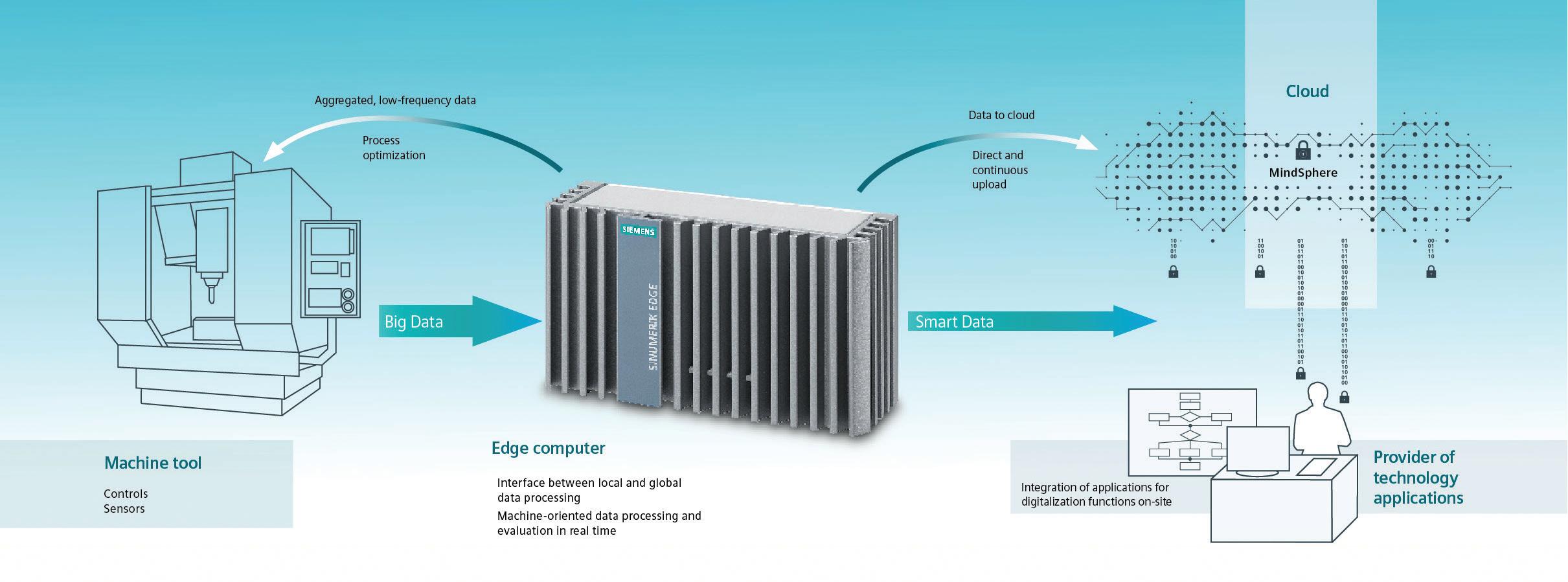
6 minute read
Internet of Things
A look at why edge computing is needed with CNC controls
The term “edge computing” simply means shi ing computing power to the edge of a network. With traditional local computing, the necessary devices are installed and set up once. Data transmission is mostly performed through local networks or external storage media. Updating devices always involves intervention in IT in astructure, which is why it is rarely done. Cloud computing is the exact opposite. Here, data are transferred to a central data center, processed, and the result re-imported. While the cloud’s data center is powerful, the potential volume of data is quickly restricted by the bandwidth of the connection, meaning that it is not possible to use all process data that is generated using the cloud. Edge computing technology is an interface between local and global data processing. An industrial computer is located at the machine, facilitating resource iendly processing of data streams. It also functions as an interface with the cloud, which will now be supplied with processed data – meaning less data tra c. Machine-oriented processing makes it possible to process and eff ectively use even high- equency data that permits only a short check-back indication time (latency).
“Computing at the edge” But what exactly is Industrial Edge? This digitalization platform is much more than just a hardware item. With the help of analytics, it expands existing automation procedures to include machine-oriented data processing — directly within manufacturing companies. Applications are managed and installed via the cloud. This means that Industrial Edge has an advantage over local networks in that applications can be updated at any time without having to intervene in the production process. Direct connection to the cloud also allows Industrial Edge to upload processed data directly and continuously. Machine tools generate up to 2 MB of process data per second. Uploading this data to the cloud om several machines is not possible. Therefore, intelligent algorithms must be used to reduce the volume of data. Big data are turned into smart data, and the Industrial Edge combines local, e cient data processing in automation with the advantages of the cloud.
Why Industrial Edge? The Siemens concept combines hardware and so ware to bring production and manufacturing data together with globally
quality assured edge computers tailored to the relevant digitalization task. You might think that machine tools equipped with Sinumerik CNC already have a powerful processing unit that will cover these tasks. The Siemens CNC controller does feature processing units, but the core competence of a numerical control unit (NCU) is path and speed control, which is ensured by the machine builder. The architecture of the CNC machine is tailored precisely to this core competence. Although computing power for additional data analysis algorithms may exist, su cient capacity cannot be guaranteed. With this in mind, Industrial Edge facilitates the integration of applications om various sides. In addition, Industrial Edge will create a relatively open environment in which various technology providers and tool and work-holding manufacturers can develop their applications. Direct implementation into the CNC would not be possible because these have already been customized by the machine builders and do not off er a uniform platform. This customization is necessary because machine tool builders have to guarantee the productivity and quality of the machining process. Industrial Edge is separate om this system and off ers a foundation for other technology providers. The aim is to create a new business segment around Industrial Edge that various providers can use. With crossindustry infl uences and global developers of applications, Industrial Edge should become a platform for digital transformation. To this end, Industrial Edge has its own development platform for easy and fault- ee programming of applications. Runtime so ware ensures connectivity with connected automation devices and with the Edge Management system. This connection is an interface to the IIoT cloud. It facilitates further processing of data in higher-level IT systems as well as administration and updating of the applications themselves. Industrial Edge is not only used for analyzing and processing CNC machine process data, it also off ers a platform where data om another sensor technology installed in the machine will be processed. For example, camera images can be constantly evaluated to mechanically monitor component clamping. Results of the data processing by Edge applications will be imported directly back into the machine, therefore optimizing the current process and minimizing wear and improving quality. Edge computing is going to be a core aspect of machine tool use in the future. Only by using applications with a specifi c technological background can further increases in productivity be achieved. Industrial Edge creates an environment that facilitates real-time data evaluation — thus laying the foundation for use of future-oriented technologies. DW
Siemens Industry, Inc. usa.siemens.com/cnc-edge
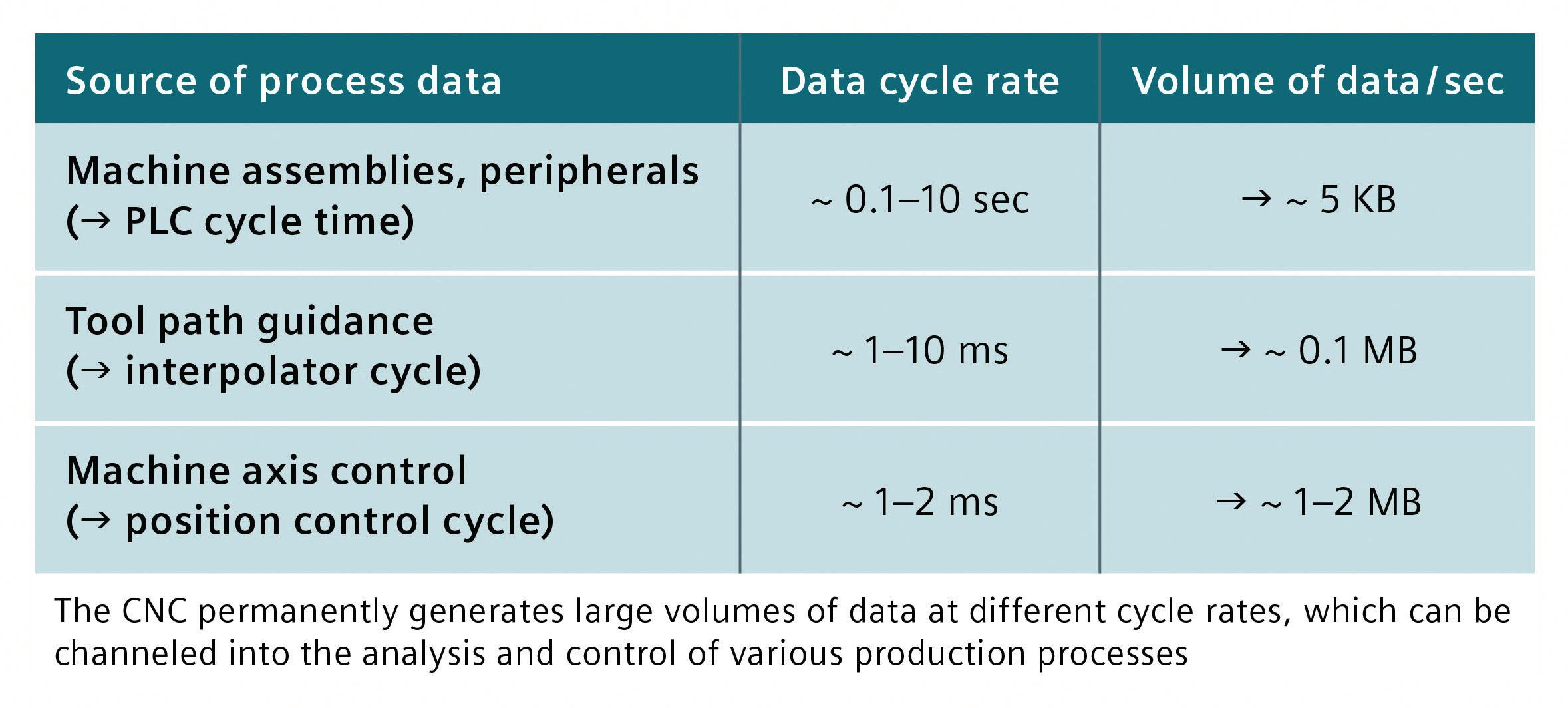
Internet of Things
Drive technology with certifi ed PROFINET PROFIdrive in servo motor
Profi bus o cially certifi ed the fully integrated
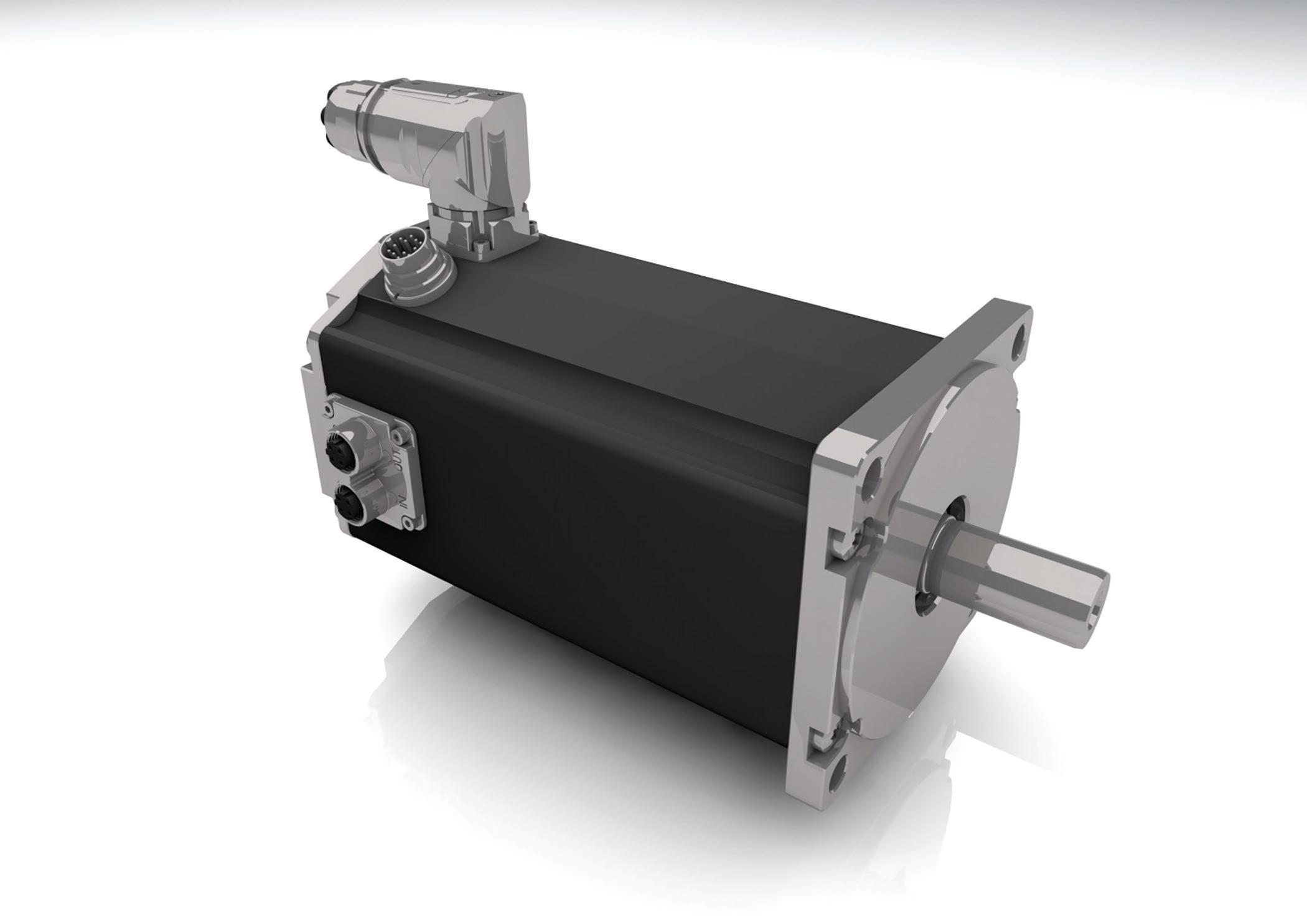
Profi net network in this servo motor. The motor, which the manufacturer claims is a milestone in terms of cabling, commissioning and IIoT capability, is the fi rst drive technology manufacturer to fully integrate its certifi ed PROFINET solution with PROFIdrive into a motor. The certifi cation assures the servo motor meets the high standards of stability, even under extreme bus conditions, are always maintained. Currently the products BG 95 dPro, BG 75 dPro, BG 66 dPro and the BGE 5510 dPro are available with PROFINET interface, covering the output power om 1 to 4000 W. DW
Dunkermotoren USA Inc. www.dunkermotoren.com/en/
WHAT DO YOU THINK?
Connect and discuss this and other engineering design issues with thousands of professionals online
Internet of Things
FPGA-based solution stack accelerates the development of industrial automation systems

Lattice Automate is a low power FPGA-based solution stack. It includes so ware tools, industrial IP cores, modular hardware development boards, and so ware-programmable reference designs and demos that simpli and accelerate implementation of applications like robotics, scalable multi-channel motor control with predictive maintenance, and real-time industrial networking. Intelligent industrial systems made possible by Automate will help in automating future smart factories, warehouses, and commercial buildings.
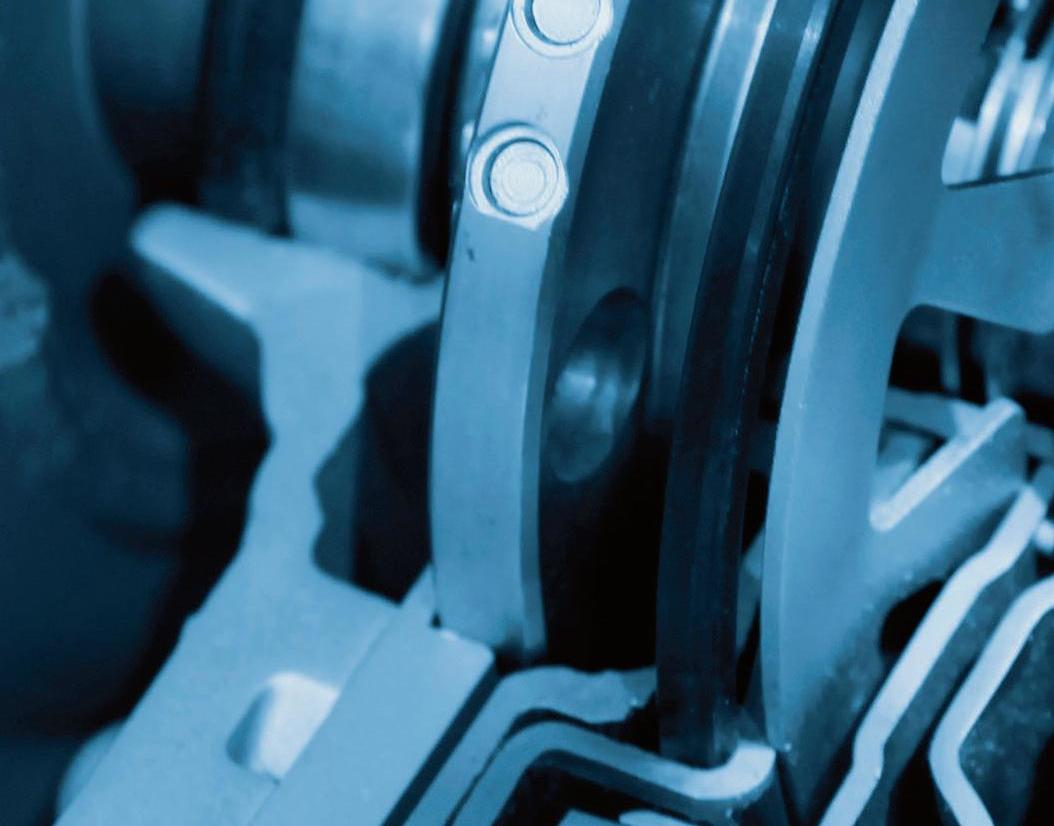
Technology trends like the IoT and Edge computing are driving development of intelligent automation systems to improve e ciency and worker safety. According to Fortune Business Insights, the global industrial automation market is projected to reach USD $326.14 billion by 2027.
The Automate stack off ers reference designs and so ware tools for the rapid development of popular industrial applications, including: • Scalable motor control – accelerates development of fl exible motor control systems, including a GUI-based user interface for system monitoring and control. • Predictive maintenance – minimizes machine downtime by monitoring multiple motors in a system. • Embedded real-time networking – implements an extensible sense and control system for a large number of devices using a Lattice Nexus FPGA as the central controller. • Cyber resiliency – enables a hardware Root-of-Trust that can detect, protect, and recover om a fi rmware-based attack in real time. • Easy-to-use So ware Design Methodology – the stack supports Lattice Propel for simpli ing development of industrial automation systems with so ware/hardware co-processing using an embedded RISC-V processor. DW
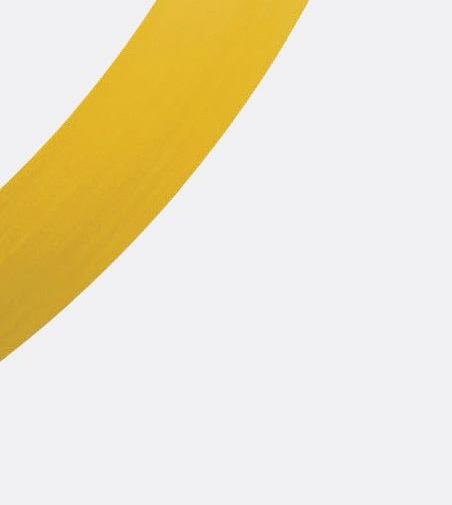
Lattice Semiconductor www.latticesemi.com
WHAT DO YOU THINK?
Connect and discuss this and other engineering design issues with thousands of professionals online
SICK OF COIL SPRINGS?
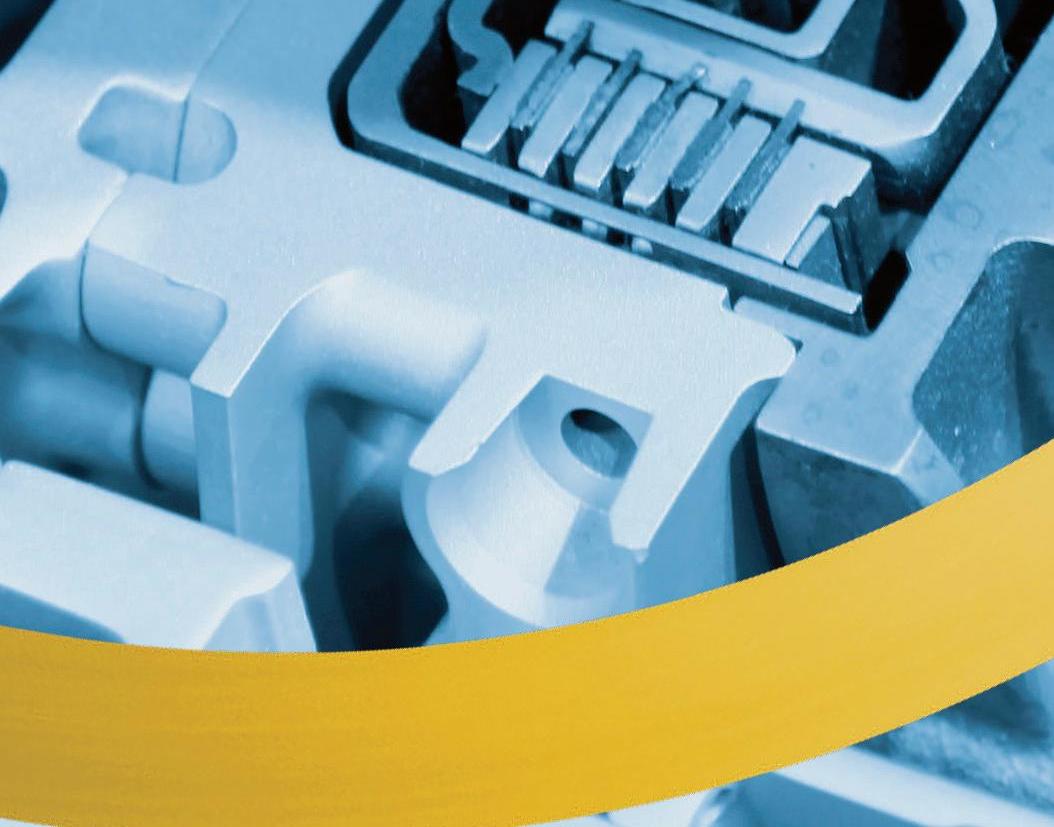


We were too. That’s why we invented the wave spring.
• Optimize Application Space & Weight • Industry-Specialized Design Support • Large Selection from Stock • Easy to Customize
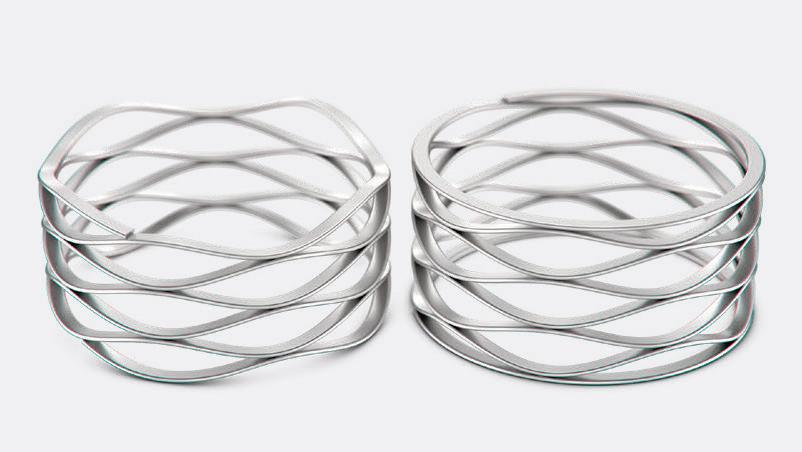
Crest-to-Crest® Wave Springs
