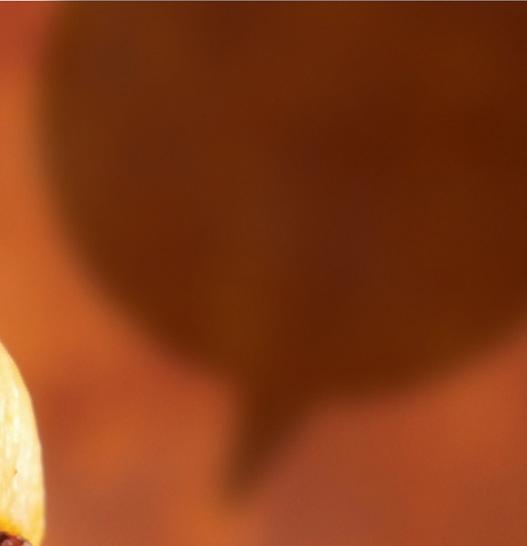
13 minute read
Design Notes
Interceptor metal detectors save pork producer’s bacon
Edited by Mike Santora • Associate Editor
The North American pork producer installed four Interceptor machines to meet the exacting inspection demands of a new fastfood customer.
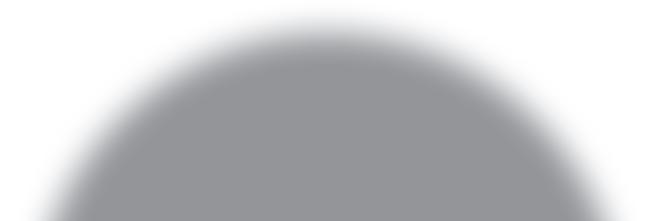
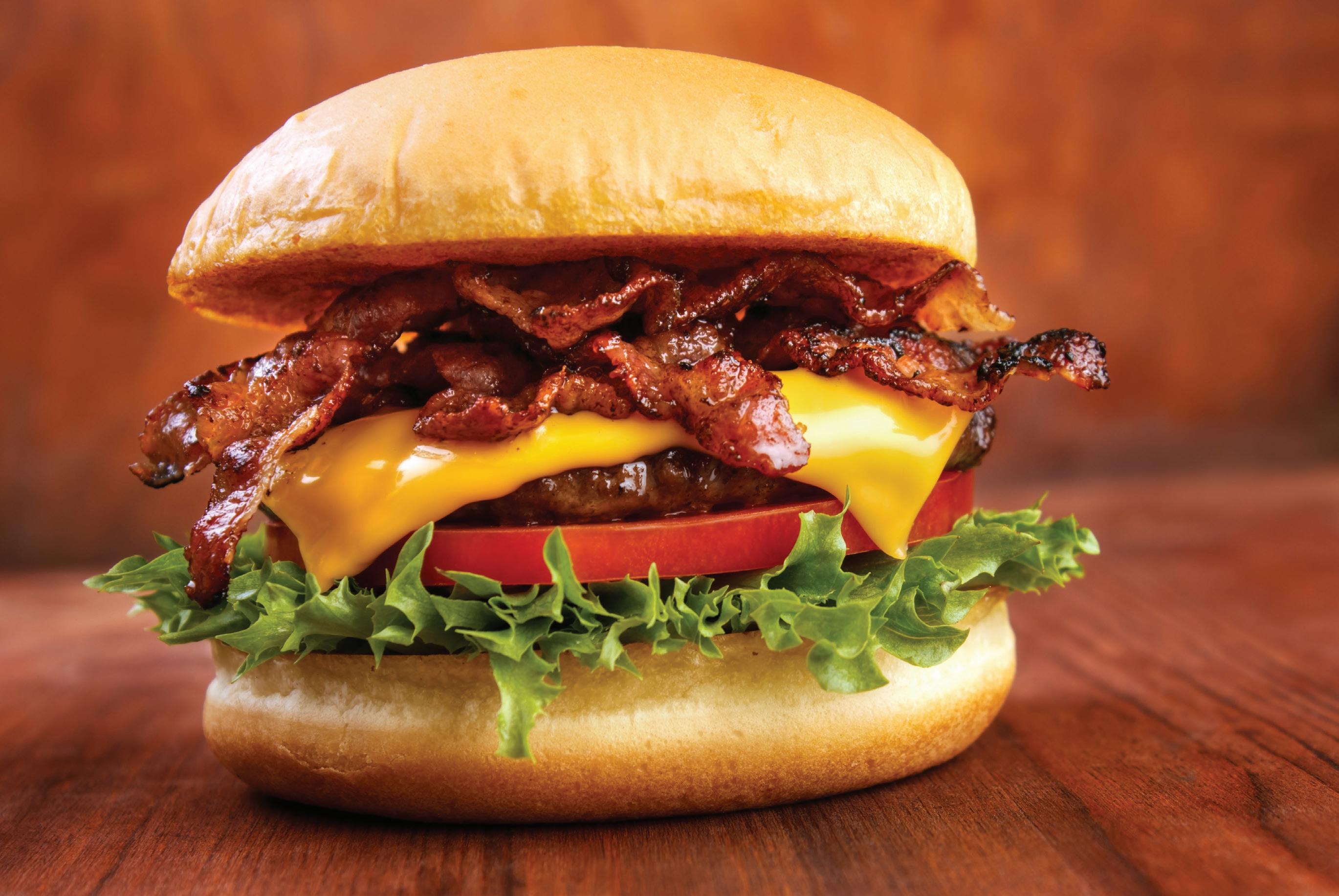
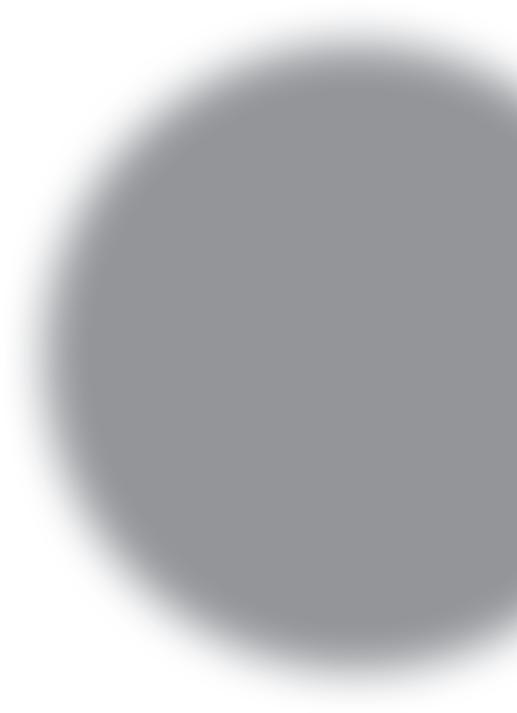
Single pass product learning and automatic calibration stop operatives from constantly resetting and recalibrating the metal detector for di erent pack sizes.
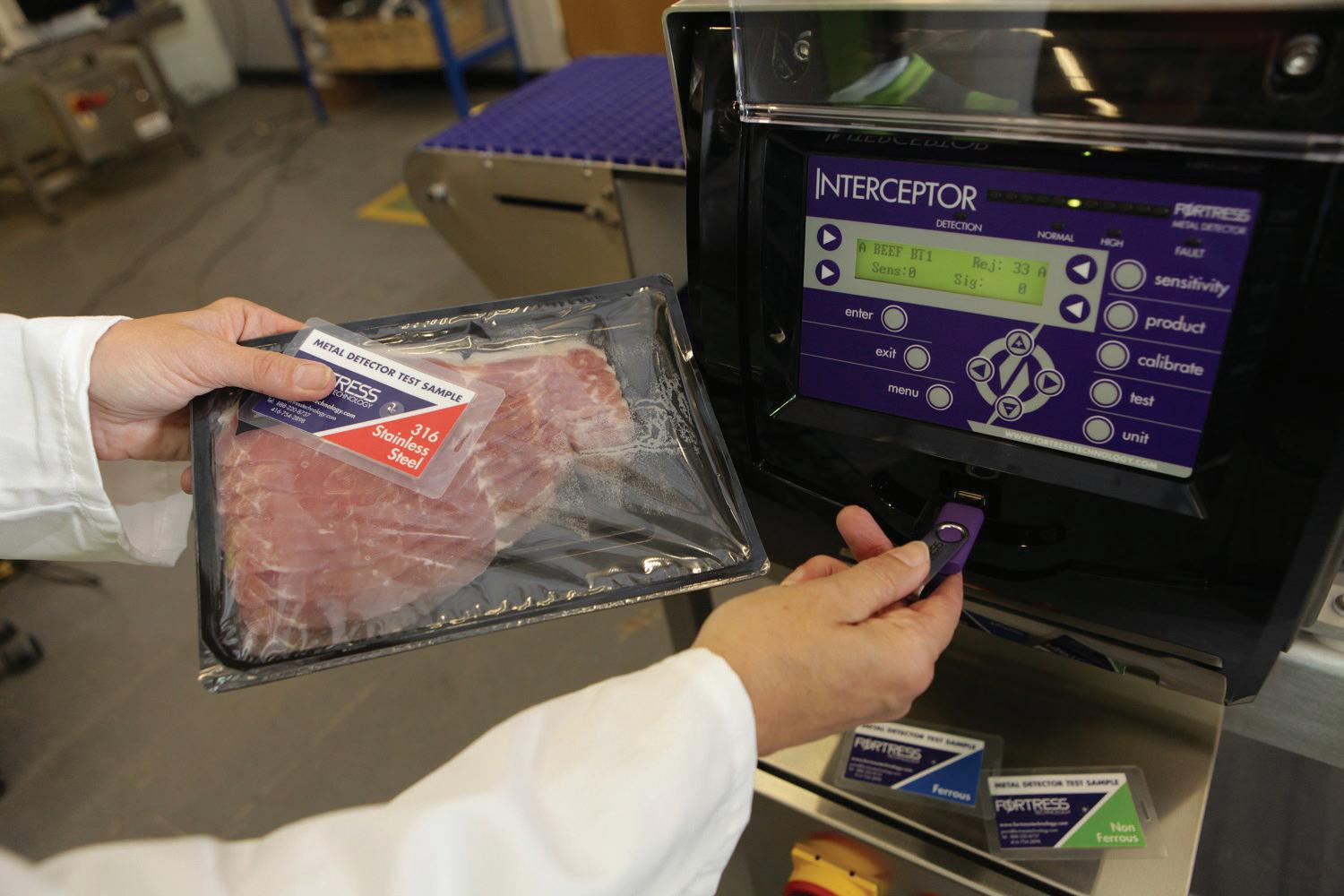
Four Interceptor metal detectors om Fortress
Technology have enabled a North American pork producer to meet its new fast-food customer’s requirements for inspecting high volumes of bacon. The Interceptor’s increased sensitivity and simultaneous multi equency innovation has helped the producer satis its client’s food safety specifi cations. The Interceptor has also eliminated false rejects by isolating product eff ect. When a leading pork producer won a new contract with a major fast-food chain, investment in a higher-quality metal detection system was crucial to meeting its client’s standards. The company’s existing inspection equipment struggled to cope with the notorious product eff ect common with challenging meat products that are wet and highly conductive. Salty products such as bacon can be especially challenging to inspect as it increases the conductivity of the wet product. This impacts a metal detector’s ability to distinguish between any metal contaminants, including stainless steel, that may have been introduced during processing and the false signal given by the combination of product attributes. These diff erent factors can lead to false readings and consequently higher product waste. Regional Sales Manager at Fortress Technology Eric Garr said: “Product eff ect can make it di cult for standard detectors to tell the diff erence between the signal generated by the bacon itself and any signal given off by a metal contaminant. As well as resulting in a high volume of false rejects, there’s greater potential for real contamination to be missed.” With the fast-food chain demanding more stringent sensitivity specifi cations, the bacon producer sought a solution to conquer product eff ect once and for all. User- iendly features that support quick setup are always highly valued by this busy production plant, said Eric. Inspecting retail and bulk packages of bacon ranging om between 10lbs and 15lbs, single pass product learning, and automatic calibration means that operatives are not having to constantly reset and recalibrate the metal detector for the diff erent pack sizes. “These automated technology features make the manufacturing process much simpler for production staff and signifi cantly reduces the time spent introducing and checking operating protocols,” said Eric. The Interceptor works by carrying out a real-time analysis of a low- equency and a high- equency output signal simultaneously. Although the size of metallic contaminant that’s detectable depends on the product size and temperature, as well as the aperture size, typically, the Interceptor can improve detection levels for stainless steel by as much as 100% in contrast to standard metal detectors. The result is a more reliable and accurate reading regardless of the size, shape, and orientation of metal particles. Additionally, a built-in Noise Immunity structure minimizes external electrical disturbances, further lowering the occurrence of false rejects. The enhanced sensitivity, accuracy, and cost e ciencies have helped the producer’s new clients meet demand. Having invested in four new Interceptors, the pork plant continues to retain its reputation for quality and food safety. “The combination of 100% increased metal detection sensitivity, elimination of false product rejects, and easy-to-use automated features has reassured our client, their customer, and consequently millions of fast-food consumers,” said Eric. DW
Fortress Technology fortresstechnology.com
WHAT DO YOU THINK?
Connect and discuss this and other engineering design issues with thousands of professionals online
Design Notes
Precision motors help make history on the Red Planet
Edited by Mike Santora • Associate Editor

The helicopter’s camera photographed the ground with the shadow during the fl ight (left). Next to it is a picture taken by the rover of the hovering Mars helicopter.
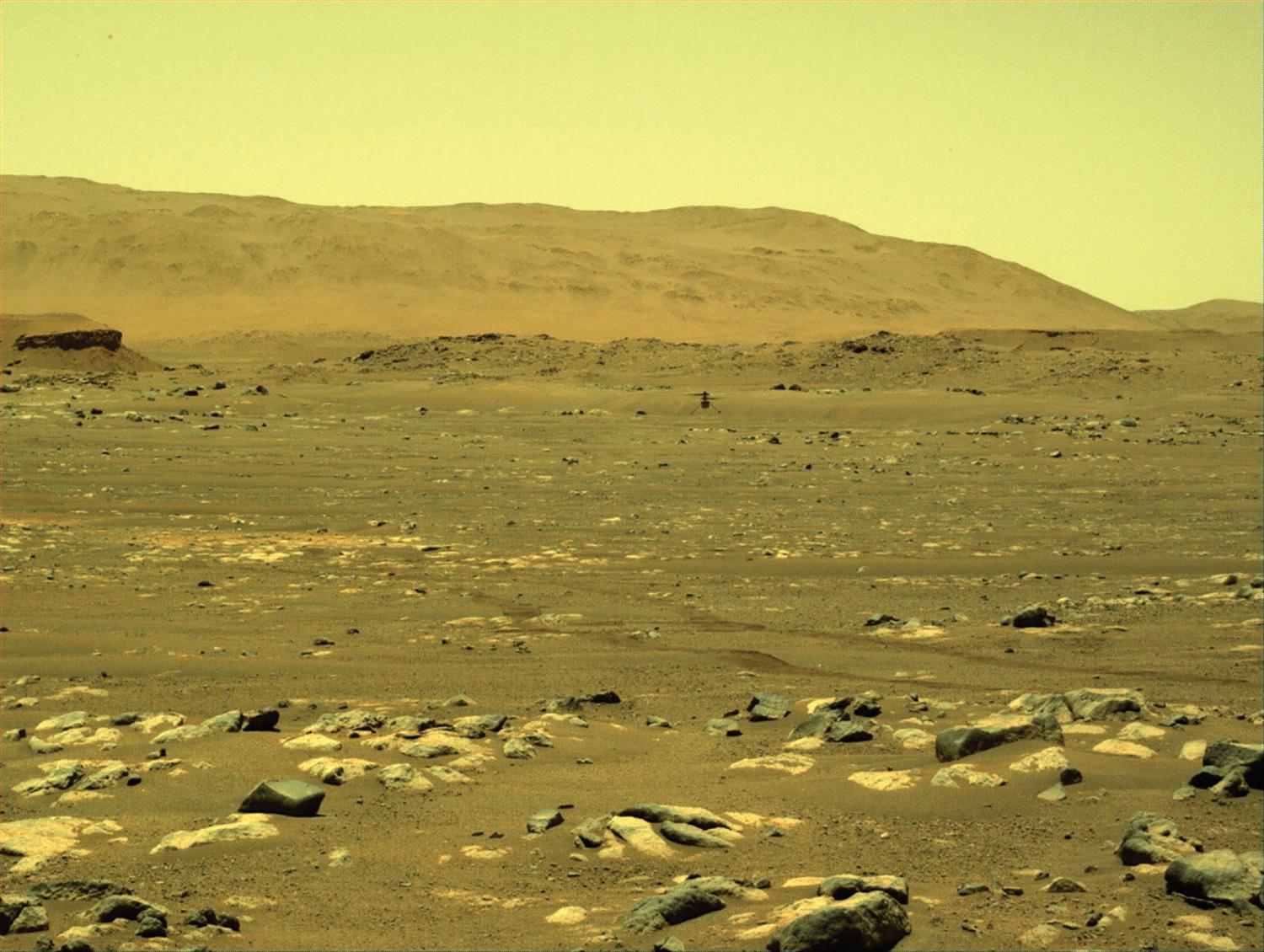

NASA’s Ingenuity helicopter has successfully completed its pioneering fl ight on Mars. This is the fi rst time in the history of powered, uncrewed spacefl ight that a device has fl own in a controlled manner on another planet. A short fl ight for “Ingenuity,” but a big success for uncrewed space fl ight. NASA’s Mars helicopter fl ew over the surface of the Red Planet for about 40 seconds on Monday, April 19th, and landed back on four legs. From NASA’s perspective, this is a historic event similar to the Wright brothers’ fi rst controlled fl ight in 1903. With the Mars helicopter, the concept of powered, uncrewed, and autonomous fl ights on foreign planets is being tested. This is comparable to the fi rst Mars rover, “Sojourner,” which paved the way for scientifi c follow-up missions such as “Curiosity” and currently “Perseverance. “ “Ingenuity” is about to complete several fl ights over a period of 30 days, each lasting up to 90 seconds and reaching a maximum altitude of fi ve meters. Six micromotors control the helicopter’s fl ight direction. The helicopter is equipped with six maxon brushed DC motors specifi cally modifi ed for this challenge. The DCX series of drives, with diameters of 10 millimeters, control the pitch of the rotor blades and the direction of fl ight for the helicopter, which weighs only 1.8 kilograms and is solar-powered. The lightweight design is a prerequisite for a successful fl ight on the Red Planet, where there is hardly any atmosphere, comparable to conditions at an altitude of 30 kilometers on Earth. “The biggest challenge in developing the motors was the extreme weight requirement,”
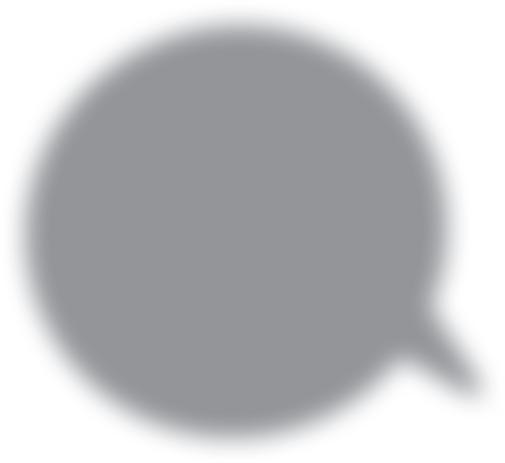
says Aiko Stenzel, design engineer at maxon. “Every tenth of a gram had to be saved to make the helicopter fl y. What’s great is that despite the weight savings, we found a drive solution that has enough power to adjust the rotor blades. And this, in the face of high vibrations and temperature fl uctuations.” The standard variants of the DCX motors are available for everyone and can be confi gured online according to the individual customer specifi cations. Eugen Elmiger, CEO of the maxon Group, watched the NASA transmission of the fi rst fl ight data live. He said, “It is a fantastic feeling to know that our precision drives worked as planned and that we were able to make our contribution to this historic event. I am proud of our employees and look forward to the next milestones on Mars.” maxon’s drives are also used in the Perseverance rover. There are ten BLDC motors and a special gearbox that will be used, among other things, to handle the soil samples inside the rover. The fi rst of these motors has already completed its task: It placed the Mars helicopter safely on the ground. DW
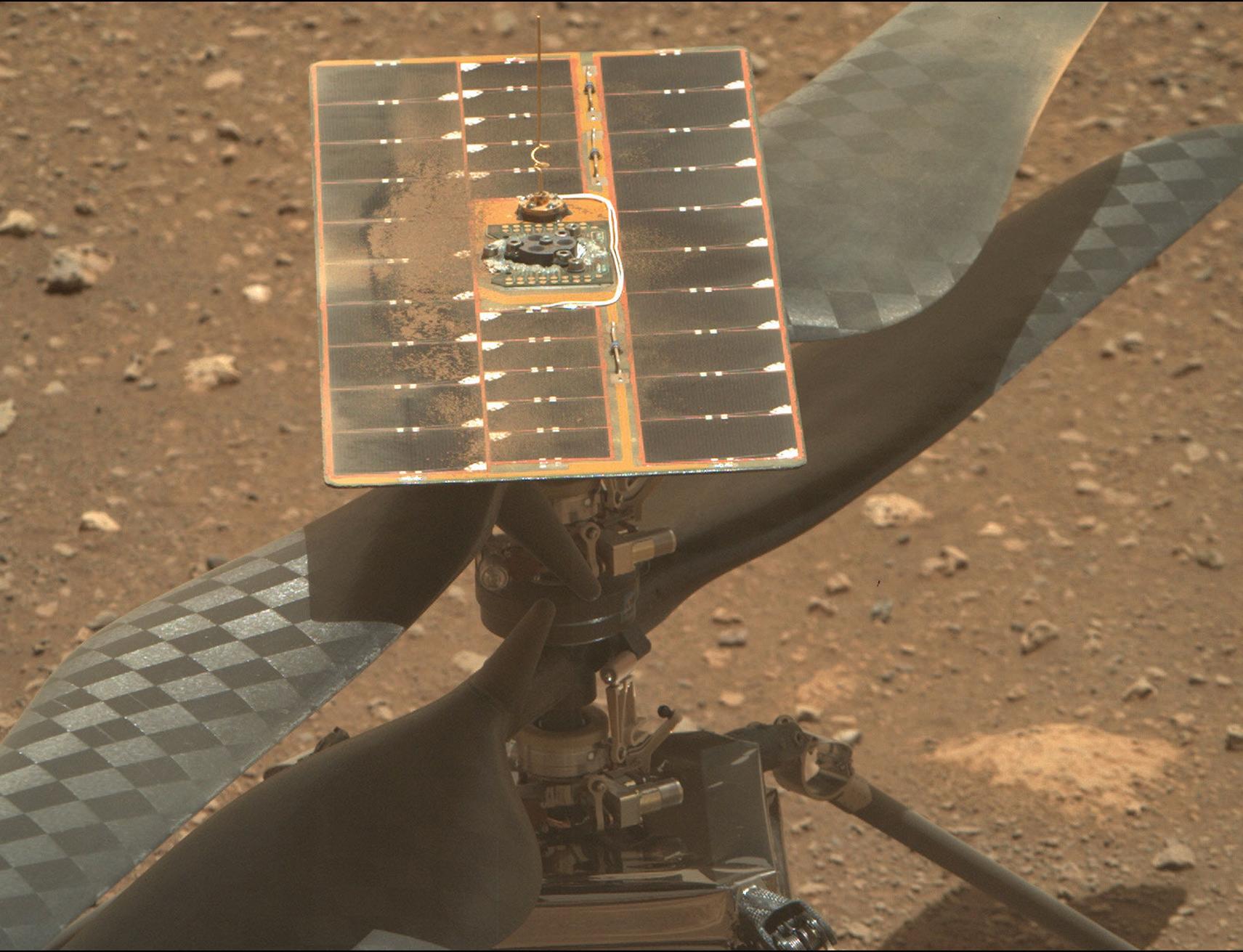
maxon | mars.maxonworld.com Close-up view of the maxon DCX motors.
WHAT DO YOU THINK?
Connect and discuss this and other engineering design issues with thousands of professionals online
MAGNETIC ENCODERS FOR POSITION FEEDBACK
Contactless, no wear and maintenance-free High positioning accuracy and resolution Economical, small, compact designs and custom solutions Flexible ring diameters and measuring lengths
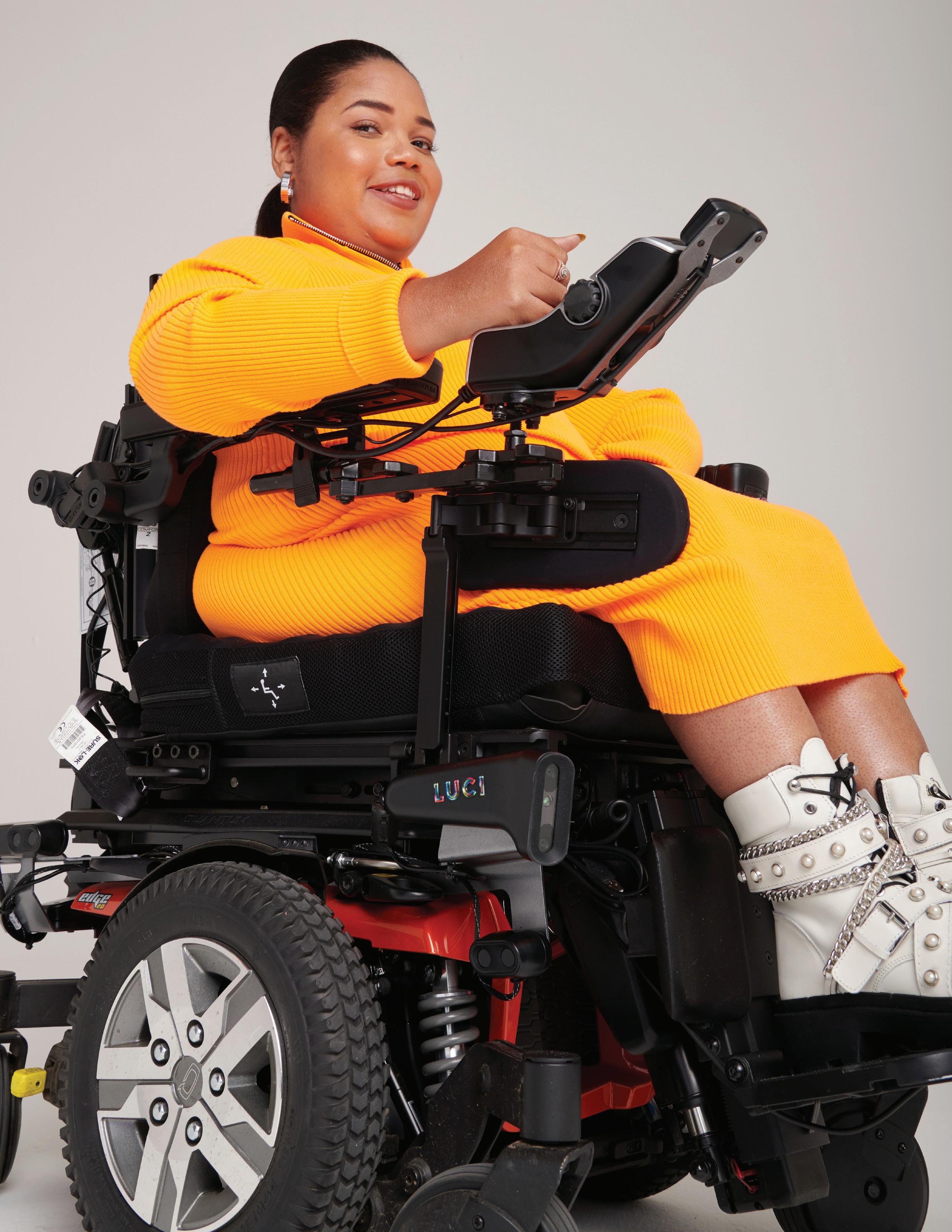
Design Notes
How injection molding can help power wheelchair applications
Edited by Mike Santora • Associate Editor

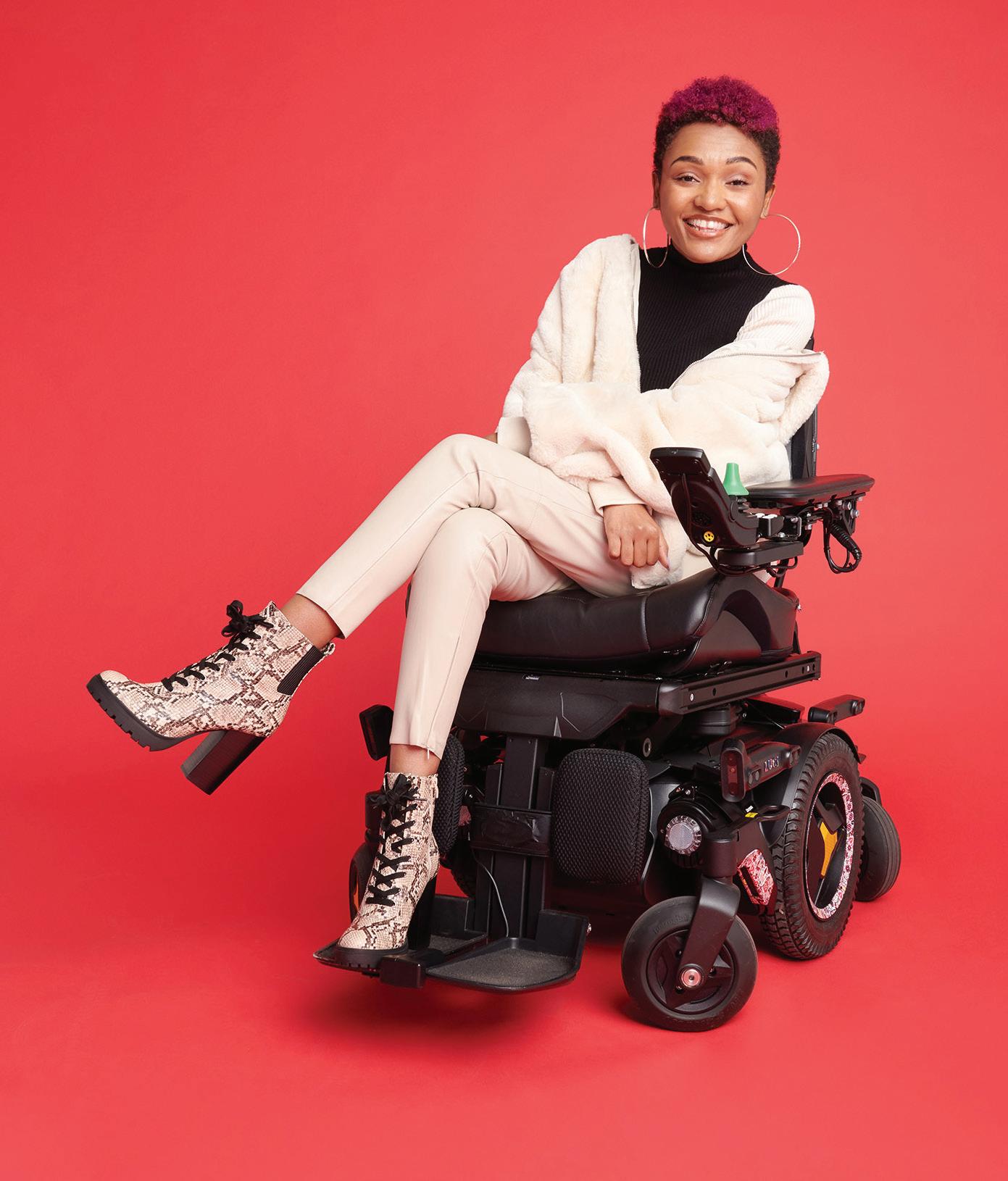
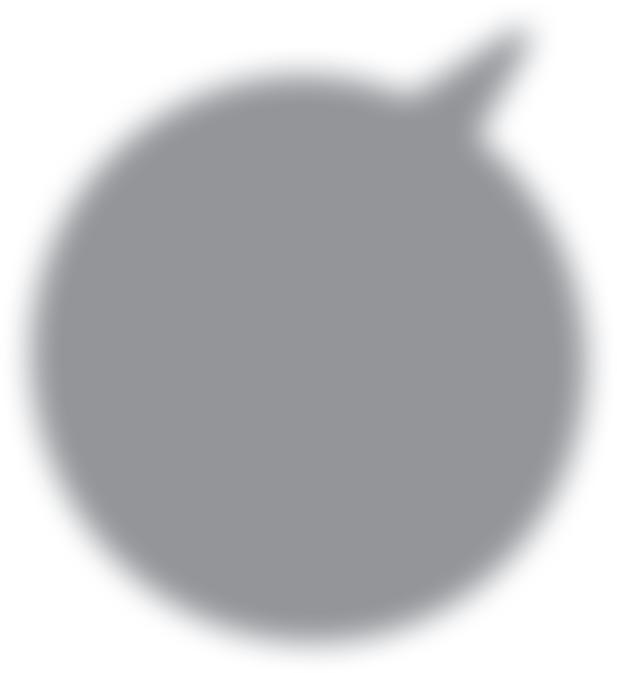
Brothers Barry and Jered Dean didn’t set out to start a company. But nothing on the market solved their problem: Keeping Barry’s daughter, Katherine, safe in her power wheelchair. Users can get hurt if the devices, which weigh hundreds of pounds, tip over or run into objects. That happened to Katherine, who was born with cerebral palsy, when her power wheelchair tipped over, resulting in arm and leg injuries. A er some debate, Barry, a Grammy-nominated Nashville songwriter, and Jered, a Denver-based design engineer, were sketching ideas out at a restaurant on a paper tablecloth — and in business. “We chose to go ahead and go for it because it didn’t seem anybody was going to do this anytime soon,” Jered. “We couldn’t aff ord for our family to wait for somebody else to do it.”
Design Notes
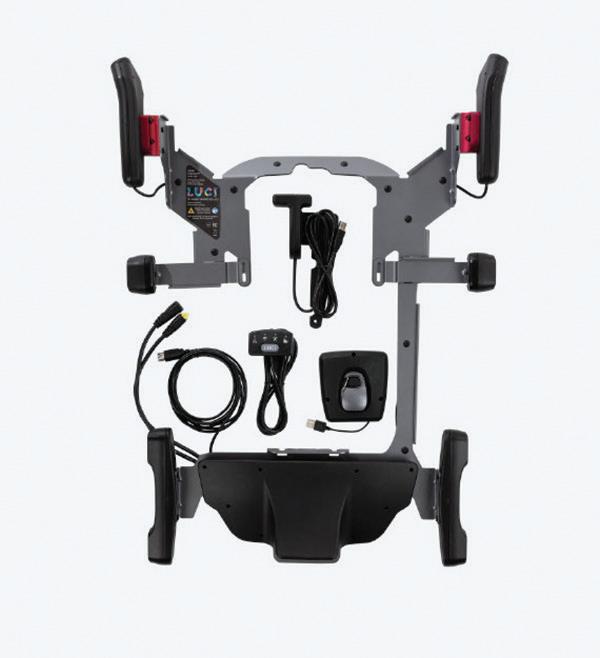

Finalizing the design for the housings holding the millimeterwave radar sensors further involved several calls with Protolabs engineers to tweak the plans. ABS plastic was recommended because it was durable, cost-e ective, and compatible with the radar sensors.

What they came up with, along with a little manufacturing help om Protolabs, is LUCI, an attachable accessory system that brings smart technology to power wheelchairs for stability, security, and connectivity. LUCI’s hardware and so ware combine to give power wheelchairs a 360° view of the world to avoid collisions and drop-off s and warn of tipping dangers. Cloud-based communications can alert loved ones of an accident and securely send user data to family and medical team members. LUCI incorporates stereo-vision cameras and in ared, ultrasonic, and radar sensors in a patented, fi rst-of-its-kind system that gets mounted between the seat and wheels of a power wheelchair. The Dean brothers, with Barry as CEO and Jered as chief technology o cer, founded the LUCI company in 2017. A er years of development, they began selling the LUCI system in early 2021. The product already has earned widespread recognition, named Time magazine’s Best Inventions of 2020, Popular Science’s Best of What’s New, a CES 2021 Health & Wellness Innovation Award, and Mobility Management’s “Smart Technology” Product Award.
Design Challenge: Developing fast and creating ‘invisible’ housings In addition to their urgency to create a safer alternative for Katherine and other power wheelchair riders, the Deans’ announcement of their intent to develop such a product generated intense interest om wheelchair manufacturers. For the speed and fl exibility required in the design, the Deans’ turned to Protolabs for the injection-molding of plastic prototypes and production parts. They also used Protolabs to prototype the sheet metal components and even handle services they hadn’t initially anticipated. As a power wheelchair steers LUCI with a joystick or other means, onboard sensors map the surroundings to recognize anything in the way, om curbs and vehicles, to pets and people. The mapping technology includes a pair of millimeter-wave radar sensors that detect the range, velocity, and angle of objects in the environment. The plastic housings that contain the radar sensors posed a design challenge, Jered said, because those housings need to be “invisible” to the business card-sized radar sensors. The housings have to be of a certain shape, material, and thinness to enable the radar devices to do their job of identi ing potential hazards. Another concern was fi nding a way of securely attaching all of the plastic housings holding LUCI’s various sensors and electronics to the system’s “smart ame,” Jered said. The ame is a sheet metal platform with several brackets that get mounted between the seat and wheels of a new or existing power wheelchair to install the LUCI system. Off ering a user experience that merges rider intent and independence with the protection and assistance that LUCI’s technology provides was also a priority. One expression of that, Jered said, needed to be through LUCI’s dashboard, its user interface. The dashboard, located on the wheelchair’s control panel, has four indicator lights to track Wi-Fi and cellular connection and sensor obstruction. He wanted each light to have a corresponding symbol that would identi its function while also being attractive and durable.
Solution: Iterative design, insert molding, pad printing Jered used tech-enabled manufacturing’s online quoting system and automated manufacturing analysis to design plastic housings for LUCI’s sensors and electronics. Getting the design just right for the housings holding the millimeterwave radar sensors further involved several calls with Protolabs engineers to tweak those plans. ABS plastic was recommended because it was durable, cost-eff ective, and compatible with the radar sensors. Crucially, the material was injection molded in a shape and at a thinness necessary for the radar devices to work properly. Jered iterated rapidly on the housings, cutting test tools, having prototypes made, and working with Protolabs on revisions before making new tools for another round of prototyping. The process was more cost-eff ective. When Jered mentioned his concern about securing the plastic housings to LUCI’S ame, insert molding was suggested. Insert molding, in this case, incorporates threaded metal inserts into LUCI’s molded plastic housings to improve their strength when they’re attached to the ame. Insert molding is working so well that Jered now uses it any time possible for attaching plastic parts securely to metal. Jered also used sheet metal fabrication to prototype dozens of parts
for the smart ame and brackets that hold LUCI’s sensors. For LUCI’s dashboard, Jered had considered using stickers, labels, or engraving for the symbols that identi the purpose of each indicator light. He found a better solution in Protolabs’ pad printing process, which transfers a two-dimensional image, like a company logo, to a three-dimensional object. The pad-printed symbols are more attractive and durable.
Outcome Jered and Barry Dean felt a “super sense of urgency” to deliver LUCI to the market, given their personal stake and the high level of interest om potential users and the wheelchair industry. “That urgency trickled through to everything, how we’re doing our manufacturing, how we’re doing our product development, our sales,” Jered said. “All those things go to how can we get LUCI to the broadest number of users possible. It’s the diff erence between someone being able to independently drive themselves and somebody being pushed or not having that eedom in all locations. That’s a lot of pressure on getting it out, getting it right, and getting it done.” That speed and lower tooling costs make digital manufacturing providers like Protolabs a cost-eff ective choice, Jered said. While piece-part prices are a little higher initially, they become more favorable with on-demand manufacturing. DW

Protolabs protolabs.com
Fabco-Made NFPA
Versatile, rugged cylinders—when you need them
FABCO-AIR
A member of Festo Group

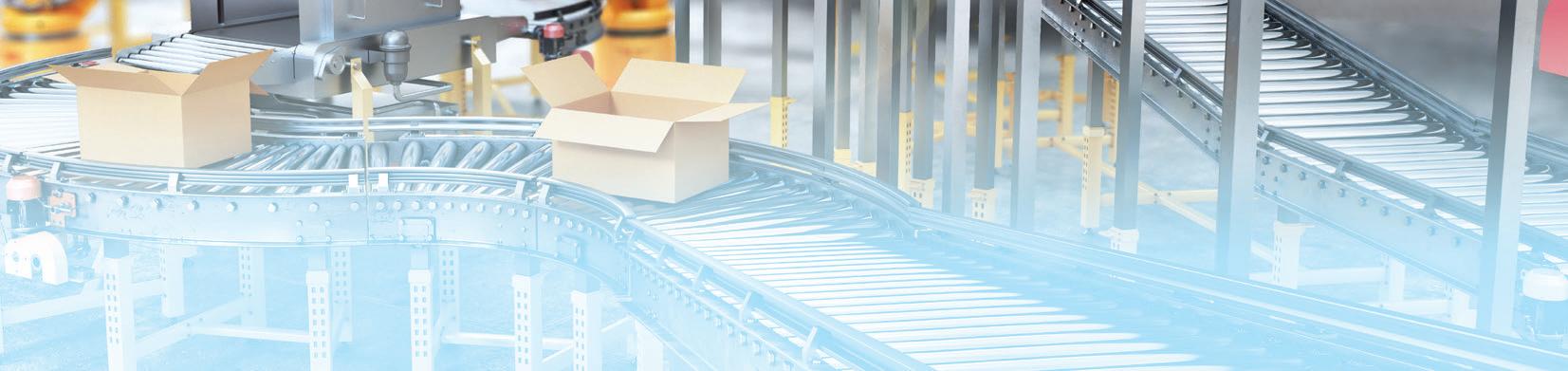

Our NFPA interchangeable pneumatic cylinders take the guesswork out of cylinder selection.
We design and manufacture our NFPA cylinders in Gainesville, Florida—so expect fast delivery, supply chain resilience and local support no matter your application. Built tough, our NFPA actuators feature anodized aluminum heads and barrels and stainless steel hardware for corrosion resistance. They also incorporate highstrength composite rod bears and PTFE piston wear bands for superior load handling and long service life. Choose from 19 standard mounting options and hundreds of standard configurable options to meet the requirements of almost any application. Standard catalog not enough? Tell us about your application and let us design a custom solution optimized for your environment. • Standard bore sizes: 1.5–6 inches • Standard strokes to 99 inches • Pressure rating: 250 PSI • Temperature range: -10° to +165°F • Conforms to NFPA dimensional specifications • Lead time for standard configurations: 7–10 days