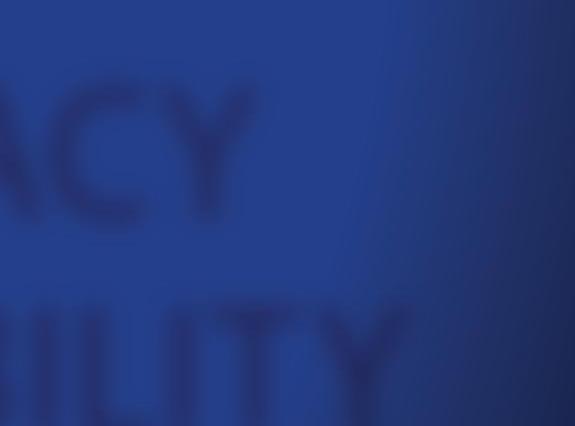
1 minute read
ACCURACY REPEATABILITY CUSTOMIZATION
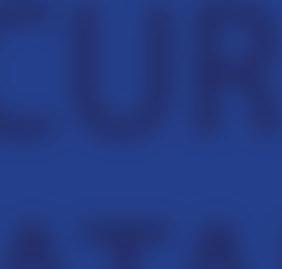
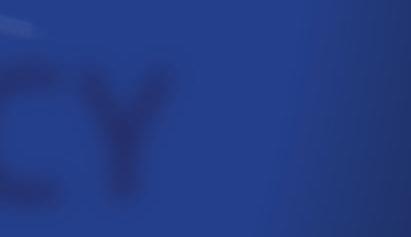


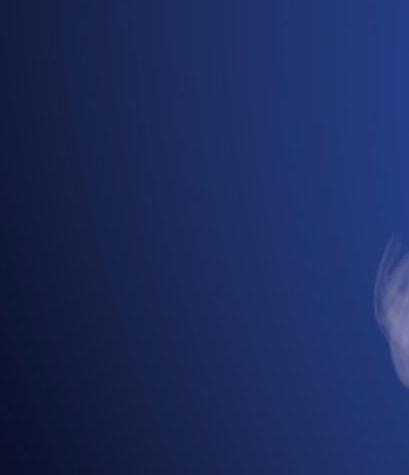
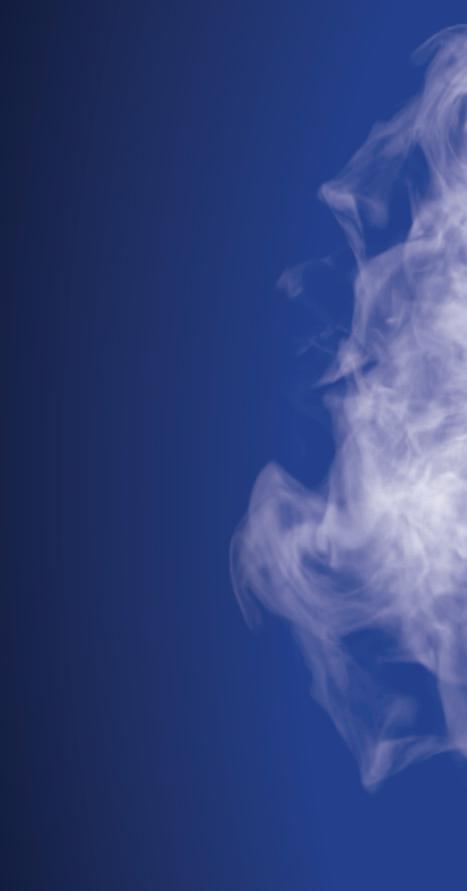

probably the most important is its contribution to friction. A higher (poorer) surface finish on rolling or sliding elements means more friction between those elements, and in turn, greater wear and reduced life. In fact, dynamic (or kinetic) friction between two moving components is directly related to the components’ surface finish.
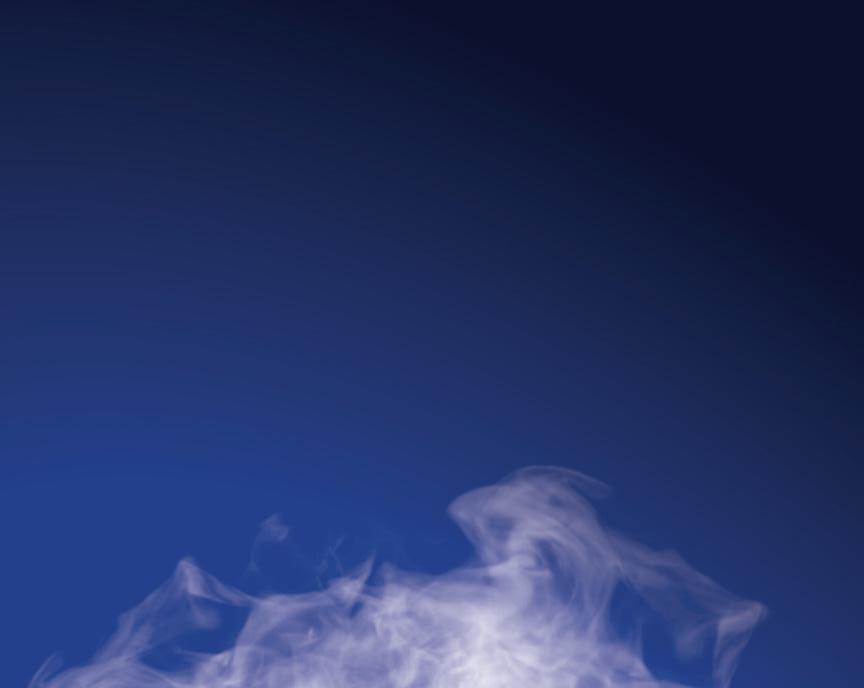
A poor surface roughness can also damage plastic or rubber parts that ride on metal shafts or guides. For example, both the rubber seals used on ball nuts and the plastic nuts often used on lead screws can be damaged if the surface roughness of the ball or lead screw shaft is too high.
In recirculating linear bearings, the surface roughness of the recirculation guides can create pulsations that show up as planar errors during travel. And a maximum surface roughness is sometimes recommended for the mounting and reference surfaces used for profiled linear guides in order to avoid plastic deformation of these surfaces caused by stresses from the guide mounting screws.
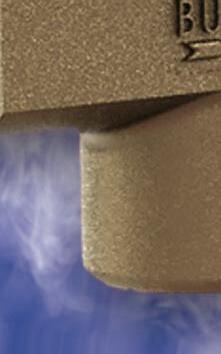
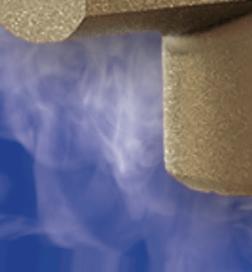

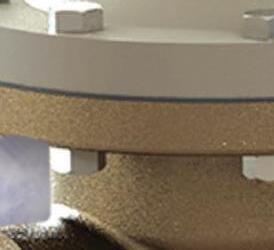

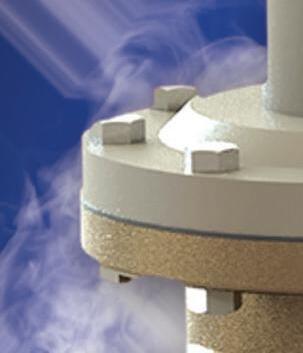
For plain bearings that are lubricated through the transfer of material from the bearing to the shaft (or guide), some amount of surface roughness is necessary, since the “peaks” on the surface of the guide serve to scrape o small amounts of material from the inside of the bearing. These small bits of material settle in the “valleys” on the surface of the shaft (or guide) and provide lubrication as the bearing travels back and forth. Similarly, when external lubrication is applied to plain bronze bearings, the valleys in the surface of the shaft capture and hold the lubrication to reduce friction and wear. DW
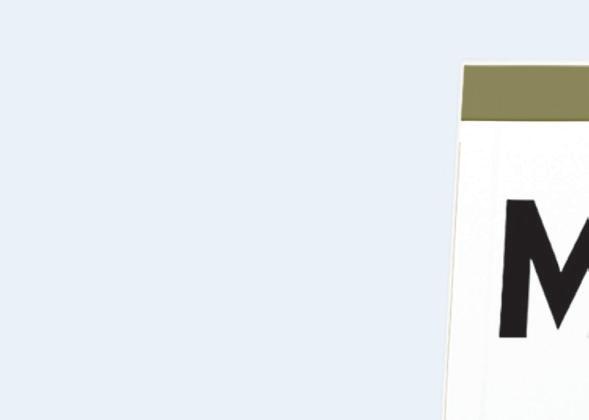
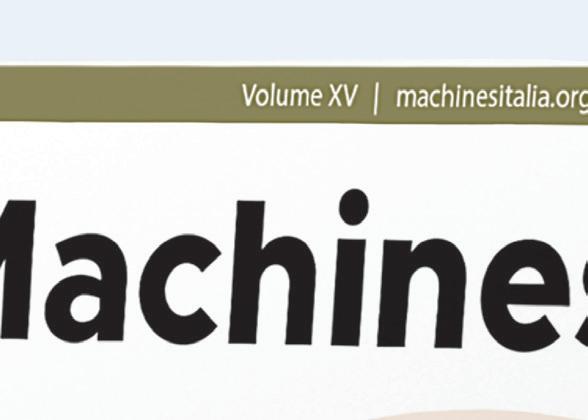
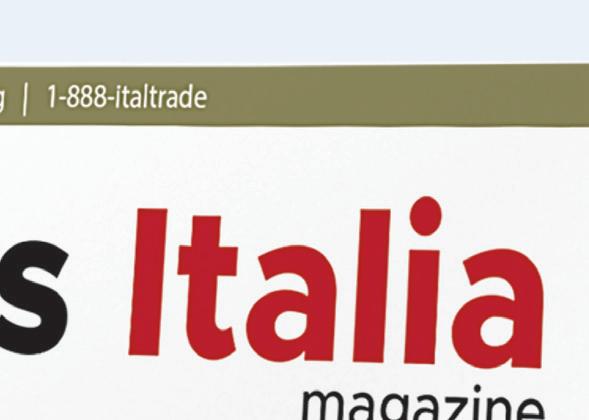
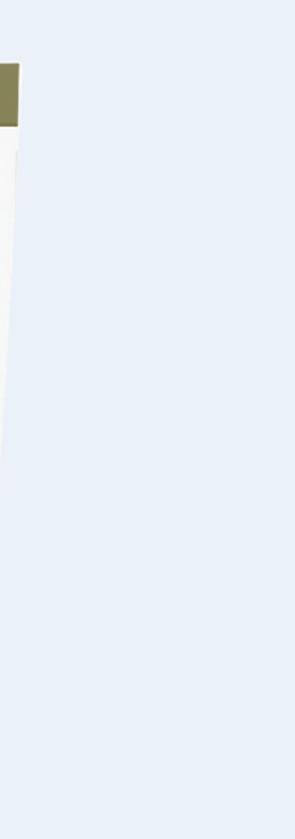
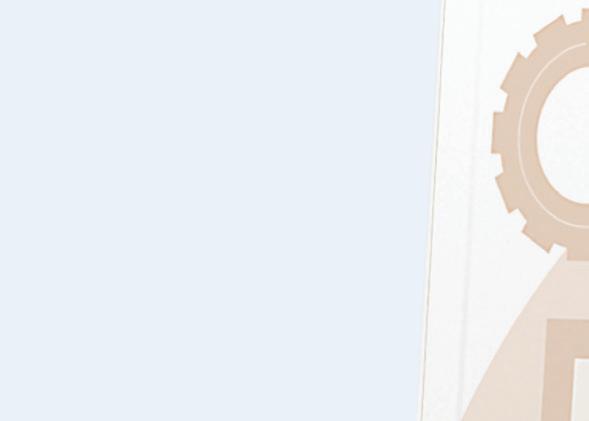
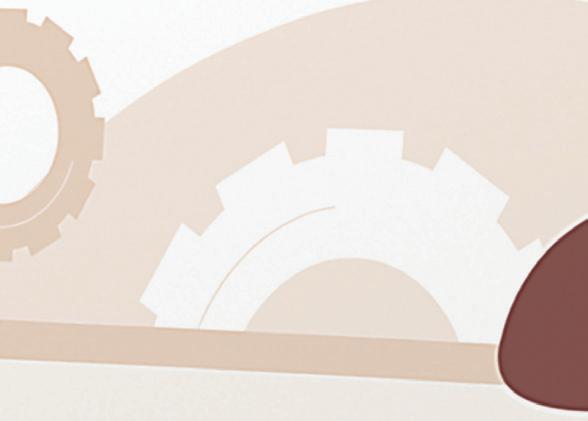
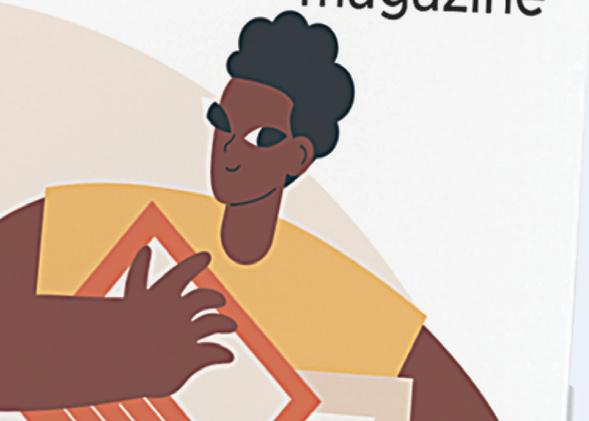
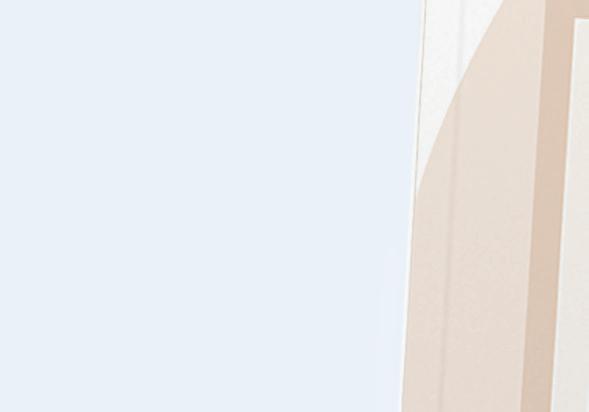
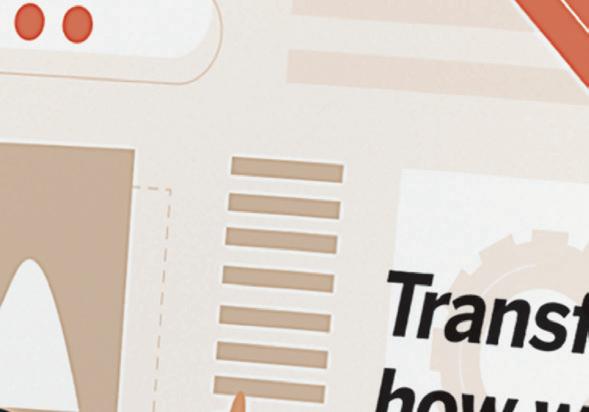
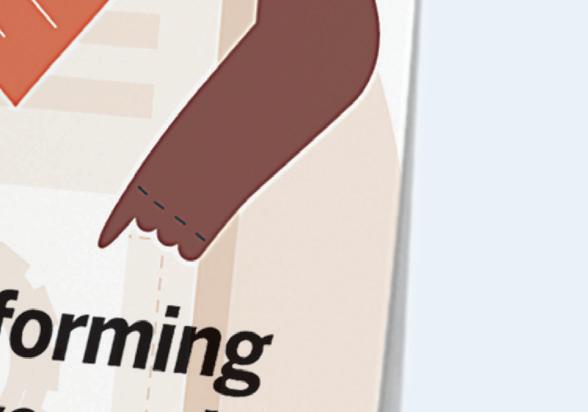
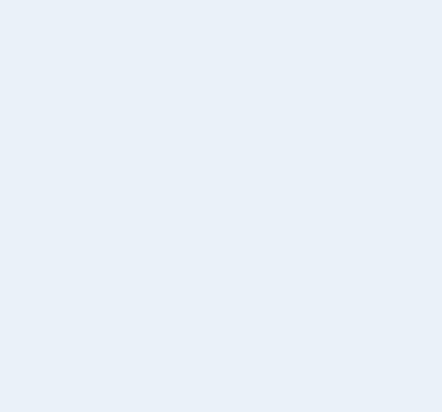

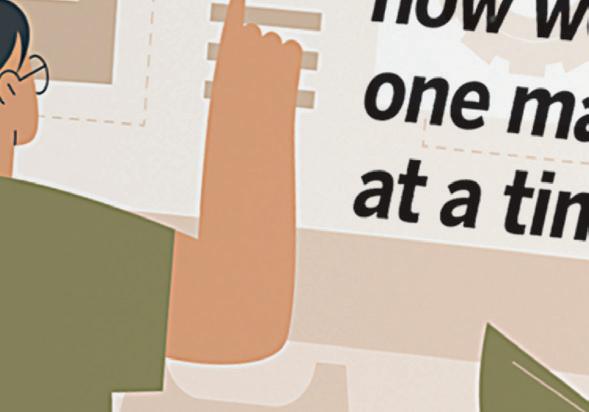
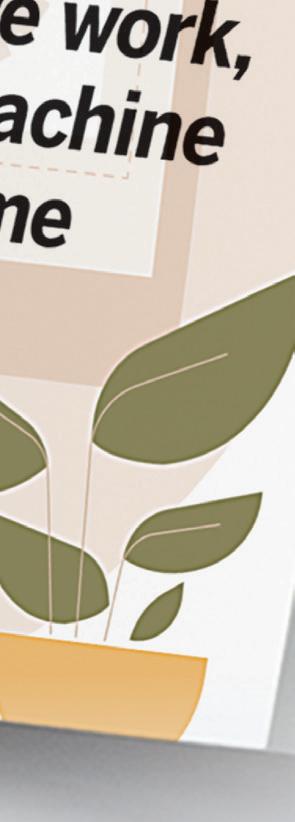
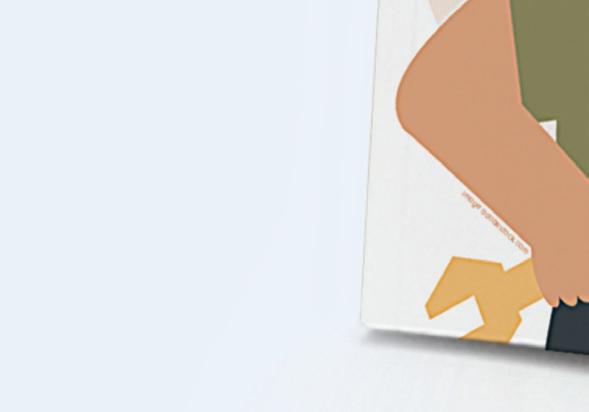
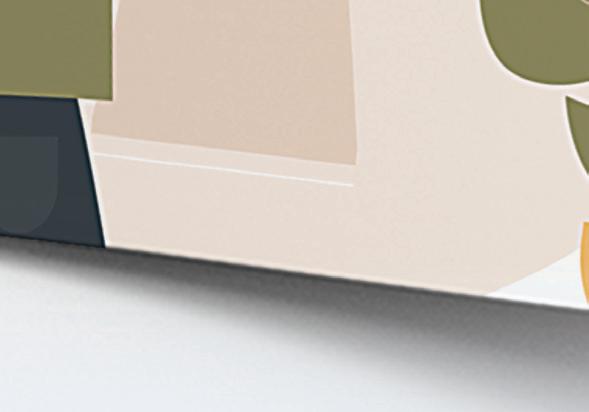
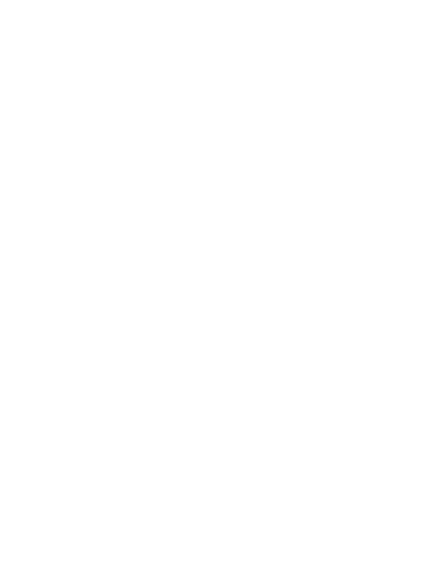
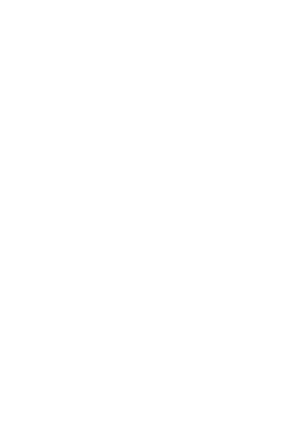
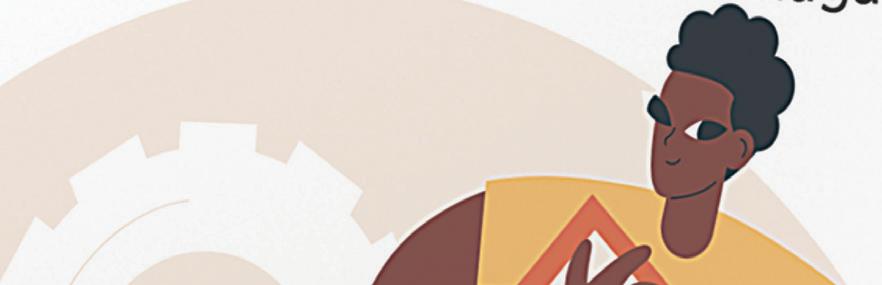
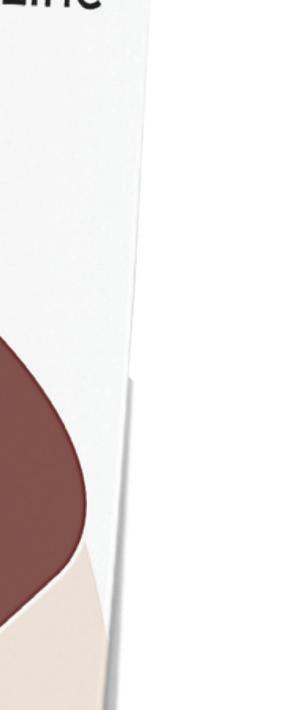
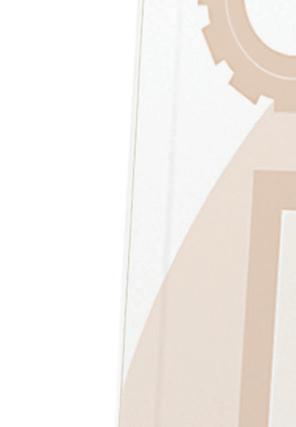
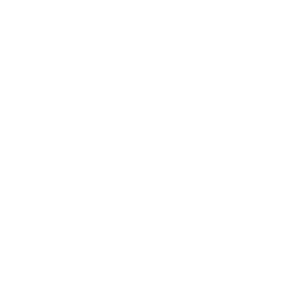
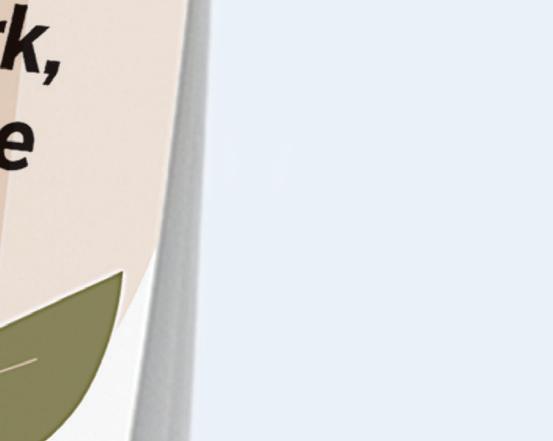

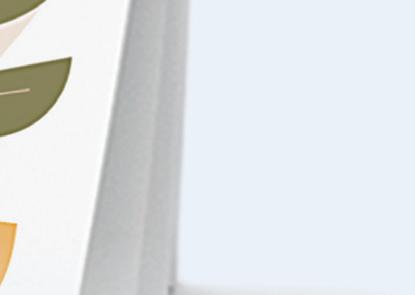
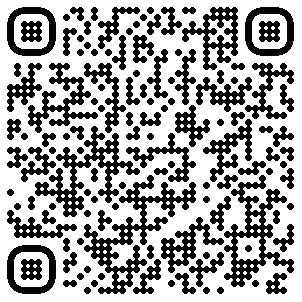