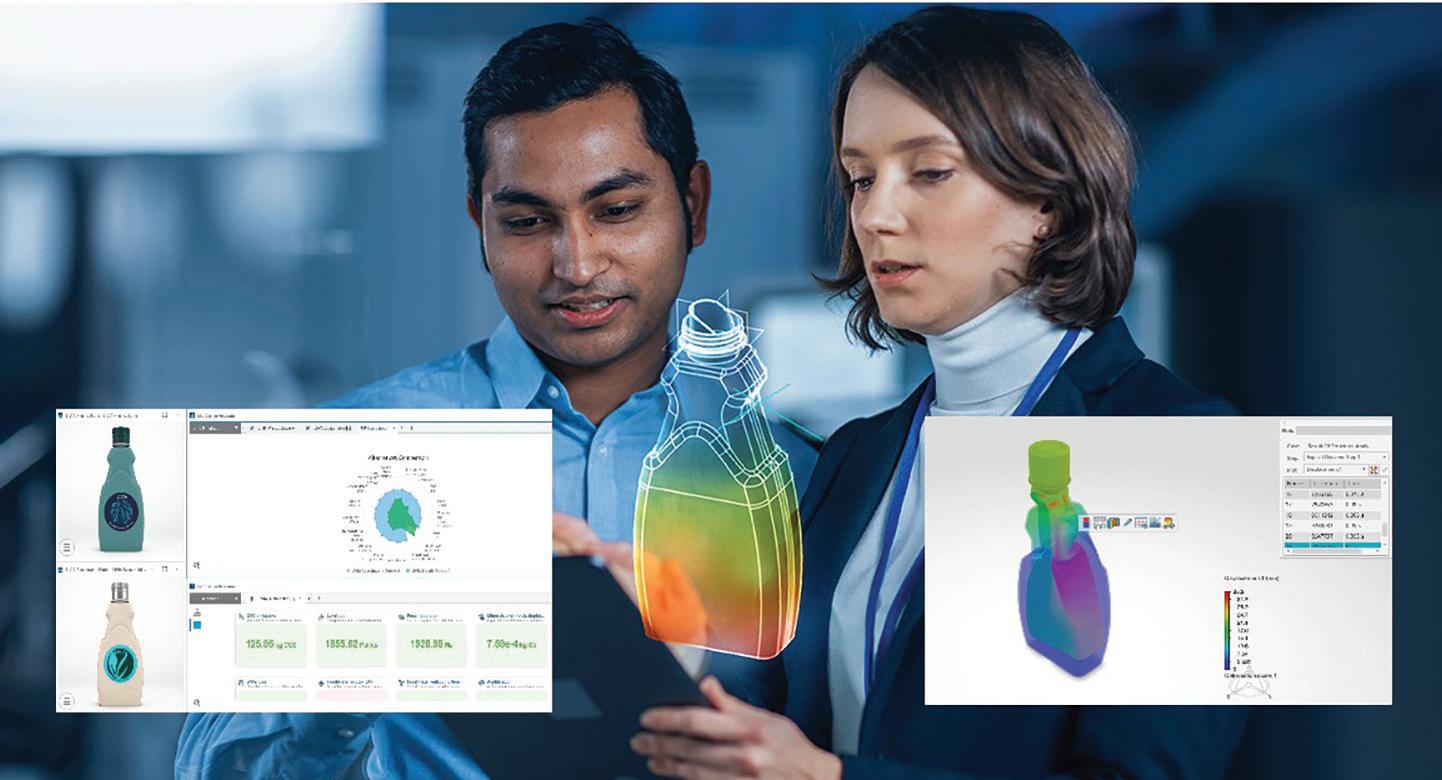
1 minute read
Design sustainable packaging with the virtual twin
Raymond Wodar • Global Business Consultant — CPG-Retail Industry • Dassault Systèmes
Most manufacturers know (or want to know) about the digital twin, which the Digital Twin Consortium defines as “a virtual representation of real-world entities and processes, synchronized at a specified frequency and fidelity.” The digital twin and its more comprehensive successor, the virtual twin, promise to make manufacturing more productive and less wasteful.
However, a virtual twin goes beyond digital continuity by representing a product or system as it exists in the present and the past. The past includes the traceability and history of the product or system’s design, testing, and manufacturing. The virtual twin also helps manufacturers simulate how a product will operate and must be maintained in the future.
Virtual twins help companies develop complex systems and products with hundreds or even thousands of parts. By applying virtual twin technology to the design process in the transportation and mobility industry, for example, planes, trains, and electric cars not only have more advanced features but are safer and more fuel-e cient. Similarly, healthcare companies can ensure better patient outcomes, and city planners can improve infrastructure and the quality of life for citizens.
Consumer packaged goods companies increasingly leverage virtual twin technology to design and manufacture more sustainable food and beverage packaging. This technology helps packaging manufacturers fully assess tradeo s between cost and eco-friendly designs, and it simulates decisions from materials to future recycling options before producing physical packaging.