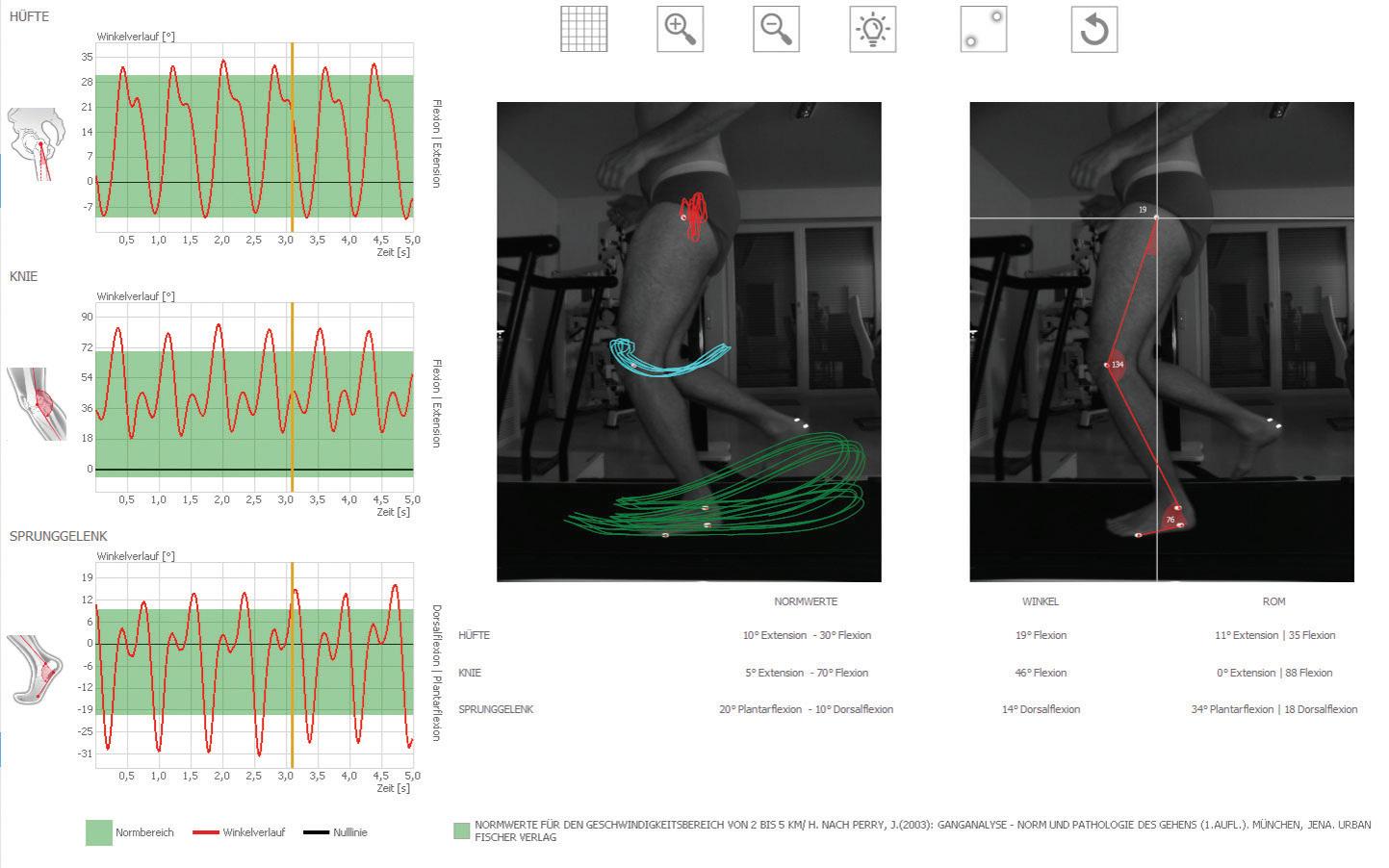
15 minute read
Design Notes
Straight up: industrial cameras help with spine and posture analysis
Edited by Mike Santora • Managing Editor

Video gait analysis and leg axis measurement.
Back pain is one of the leading causes of sick leave in Germany — o en caused by lack of exercise, work stress, and obesity. Other causes include osteoporosis, chronic infl ammatory diseases, or spinal deformities such as scoliosis. Innovative systems for 4D measurement of body statics can be used for precise diagnosis. DIERS International GmbH enables fast and high-resolution optical measurement of the back, spine, and pelvis with DIERS formetric 4D. A dynamic version and additional modules for determining the mobility of the cervical spine or gait analysis and leg axis measurement make the system a compact movement analysis laboratory. Up to 5 camera units are integrated and equipped with uEye industrial cameras om IDS Imaging Development Systems GmbH. Application DIERS formetric surveying technology is physically based on the principle of triangulation. A light projector casts a grid of lines onto the patient’s back, which is recorded by a camera unit. Computer so ware analyses the line curvatures and generates a three-dimensional image of the surface using photogrammetry (image measurement), similar to a virtual plaster cast. The examination is quick, radiation- ee, and contactless.
Additional components for a holistic movement analysis To carry out examinations in motion, the company also has a dynamic version of the DIERS formetric system in its range — DIERS 4D motion. The patient runs on a treadmill, using the latest projection and camera technology (60 images per second) and specially developed so ware; the complex interaction of the spine and pelvis are measured during walking and displayed in moving images. This enables an analysis of the vertebral body rotation and the creation of movement models of the spine. Additional modules increase the range of applications up to a compact motion analysis laboratory. With optional camera modules DIERS leg axis posterior and lateral for video-based analysis of the leg axis geometry, for example, asymmetries in stance and in the movement sequence can be determined and documented. The system so ware detects refl ective markers applied to the patient and calculates movement patterns (dynamic) and angles (static and dynamic). In the case of foot and posture corrections, the eff ects on the leg axes can thus be directly displayed and checked. With the additional module “Cervical Spine,” the mobility of the cervical spine can also be recorded three-dimensionally.

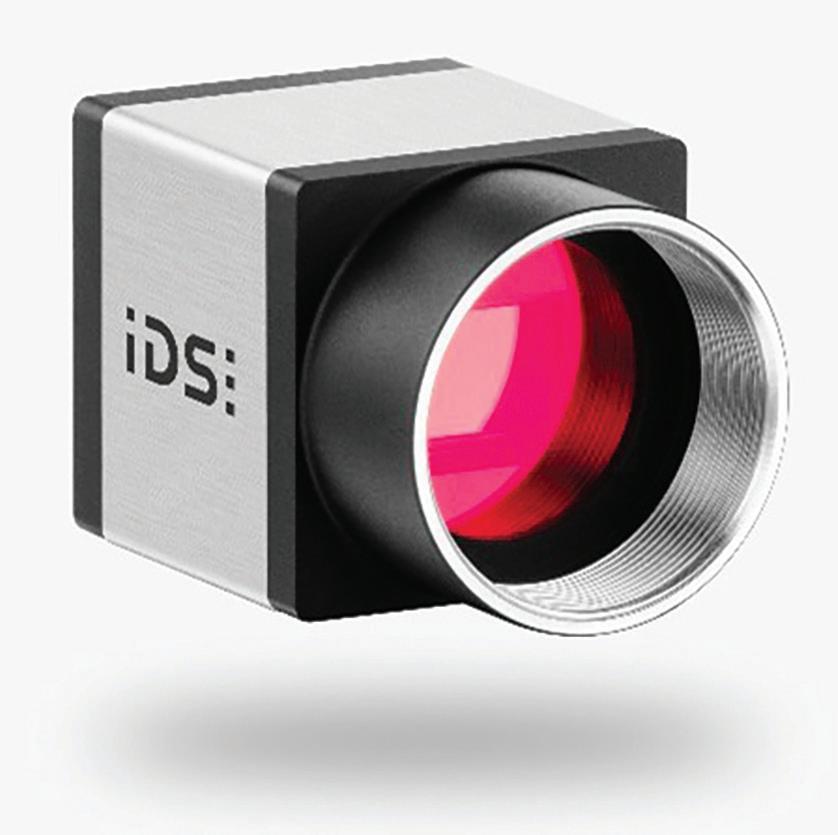
PLANETARY
BLDC and PMDC GEARMOTORS
RATED SPEED TORQUE GEAR RATIOS VOLTAGES 11 to 658 rpm 5 to 226 lb-in. 4:1 to 162:1 90/130, 24, 12 VDC High Torque. Compact Design. Long Life.
Bodine planetary gearmotors deliver high continuous and peak torques. These 60 mm gearmotors are available from stock and with many custom options. PMDC models rated up to IP-66. Low-voltage 12 & 24 VDC models are ideal for solar or battery powered applications.
Visit our website at: bodine-electric.com
Design Notes
The measurement data and Holistic movement asymmetries are displayed analysis at a graphically and can be analyzed. The measurement process takes place using a running speed of up to 30 km/h. special head hood. The DIERS formetric 4D system requires an additional camera system for the Cervical Spine Module. With the integration of these and other measurement systems, it is possible for the fi rst time to view the fps. This makes the camera suitable for complex biomechanical interaction in classic industrial applications like surface the human musculoskeletal system inspection but also for detailed image holistically. The spectrum of uses ranges evaluation in medical technology. om medical diagnosis to training The UI-3240CP-M-GL Rev.2 is a therapy and sports science. It detects powerful industrial camera with the scoliosis, pelvic obliquity, and rotation, e2v 1.3 megapixel CMOS sensor. This progress controls in osteoporosis and sensor is one of the most sensitive arthrosis, and neurological examinations sensors in the IDS portfolio. Besides its (e.g,. Romberg test), posture tests, outstanding light sensitivity, the camera (Matthiass test, Flamingo test) and much is distinguished by several additional more. Up to 5 uEye CP industrial cameras functions — for example, the sensor om IDS are used per unit. off ers two global and rolling shutter variants that can be switched during Up to 5 uEye cameras per unit in use operation, thus providing maximum The uEye CP stands for “Compact fl exibility for changing requirements and Power” and is suitable for all kinds of environmental conditions. industrial applications with its high level of functionality with comprehensive Outlook pixel pre-processing and its size of The medical technology market is only 29 x 29 x 29 mm. The internal 120 highly regulated, so changes and new MB image memory for buff ering image developments of products must be sequences also qualifi es it for multi- well-considered through elaborate camera systems. The USB 3.0 cameras certifi cation and approval procedures. enable a data rate of 420 MByte/s, low At the same time, price pressure is CPU load, and easy integration. Users increasing. Nevertheless, DIERS is can choose om many modern CMOS currently working on various new sensors om Sony, CMOSIS, e2v, and developments — om insole production ON Semiconductor, with a range of to research projects in the rehabilitation resolutions. and care sector. In addition to classic 2D The model UI-3040CP-M-GL Rev. industrial cameras, 3D models are also 2 enables strong image quality even in conceivable, which inherently introduce low light or when shooting fast-moving the spatial component. DW subjects. The integrated IMX273 global shutter CMOS sensor om Sony’s IDS Pregius range scores particularly well for www.ids-imaging.us its image quality, high sensitivity, and wide dynamic range. With a resolution of 1.57 MPixel (1448 x 1086 px) at 3.45 µm pixels, it achieves an impressive 243
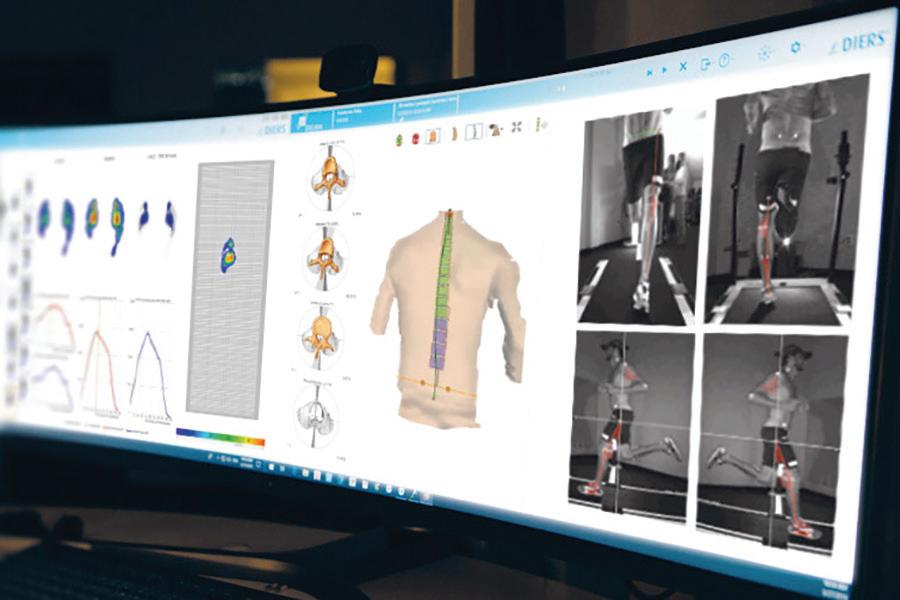
Design Notes
Thirty-fi ve non-Sulzer OH2 process pumps were upgraded using the OHX retrofi t kit.
Retrofi t solution improves pump reliability for refinery
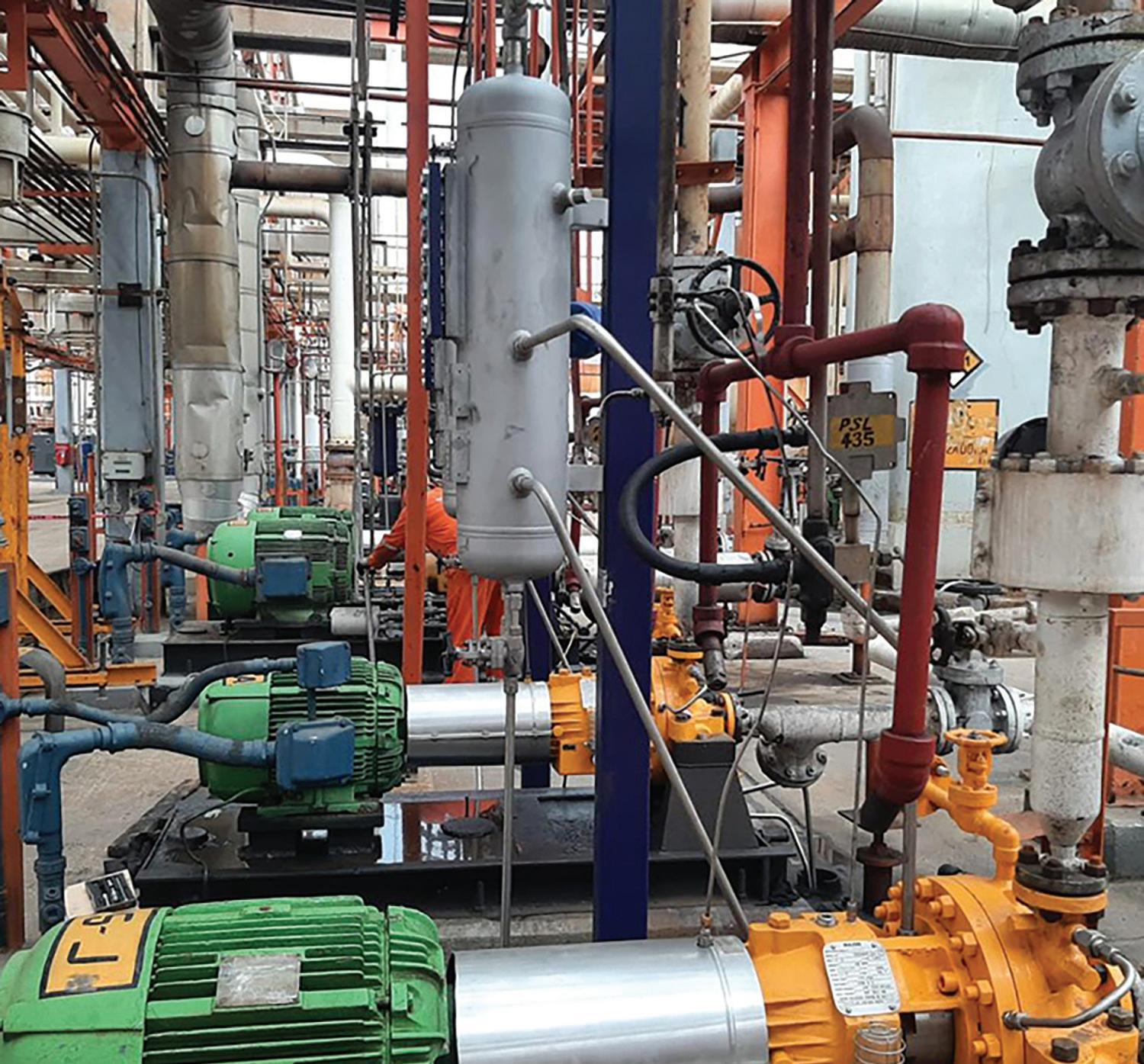
Edited by Mike Santora • Managing Editor
of process pumps, usually om myriad manufacturers, that may have been in operation for decades. Over the years, API 610 specifi cations, which govern their design, have evolved to improve both safety and reliability. Today, modern materials and design concepts om Sulzer can be used to improve the performance of existing pumps, as exemplifi ed by a case in Mexico, where 35 process pumps were upgraded. For time-served assets in refi neries and petrochemical plants, extending service life can be a challenge and a replacement may appear to be the simplest option. However, in some cases, this may require extended lead times and changes in the existing pipework or pump foundations. A much quicker solution is to upgrade key components of the pump, bringing it in line with current specifi cations while simpli ing the parts inventory at the same time.
Improvements for aging assets For example, a refi nery in Mexico, which was commissioned in 1976, processed several thousands of barrels per day. But since the refi nery was built, API standards have moved on considerably, now in its 11th edition. Within the plant, process pumps are used
for transporting propane, liquefi ed petroleum gas (LPG), sour water, and gasoline. Maintenance engineers had identifi ed several pumps that were manufactured to 6th edition standards and would benefi t om improved reliability. For example, one of the signifi cant factors aff ecting seal performance is pump vibration, and since the 8th edition, the API 610 specifi cation for stiff ness of the impeller sha has increased, reducing vibration, and extending the mean time between failures (MTBF). In addition, the design of the mechanical seals has also been enhanced, and, in this case, a double seal as per API 682 was implemented to further increase reliability and reduce fugitive emissions to comply with new environmental regulations. Thirty-fi ve non-Sulzer OH2 process pumps had been identifi ed for upgrade and Sulzer was selected to handle the issue.
Cost-eff ective retrofi t solution Sulzer engineers developed the OHX pump retrofi t kit to off er the latest API specifi cations to any brand of OH2 pump while delivering overall performance improvements without replacing the casing or making any changes to the connecting pipework. Only the aff ected parts can be upgraded, which is more cost-eff ective than replacing the whole pump. A new case cover with API 682 seal chamber meets latest API 610 standards, including the double mechanical seal. In addition, the bearings are upgraded to a longer life component, extending the expected service life om 25’000 hours to 50’000 hours. This improvement also includes upgraded oil guards, which off er much better oil sealing compared to the components of the 1970s. The retrofi t kit also introduces a cooling fan and an improved coupling and guard. The former helps to reduce bearing temperatures, extending their service life, while the latter meets the latest occupational safety and health administration (OSHA) requirements.
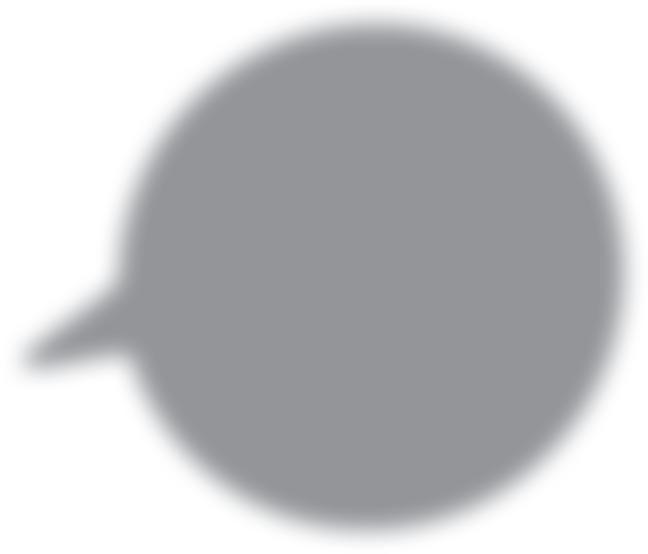
Improved performance Isabel Najera, Project Manager for Sulzer, explained, “The objective of this retrofi t solution was to optimize long-term performance and reliability without impacting the existing in astructure. Pump upgrade projects such as the one for the refi nery begin with essential information being gathered, including impeller diameter and volute measurements, which enable the case cover and other components to be manufactured without aff ecting the process pumps’ operation.” Once all the parts are complete, they can be either installed on-site or at the local Sulzer service center, keeping downtime to an absolute minimum. In most cases, these process pumps are paired with a standby unit, enabling the application to continue while one is upgraded. Following on om the retrofi t program, the updated equipment at the refi nery now has common parts with pumps on-site that have been installed more recently, allowing the spare parts inventory to be optimized. DW
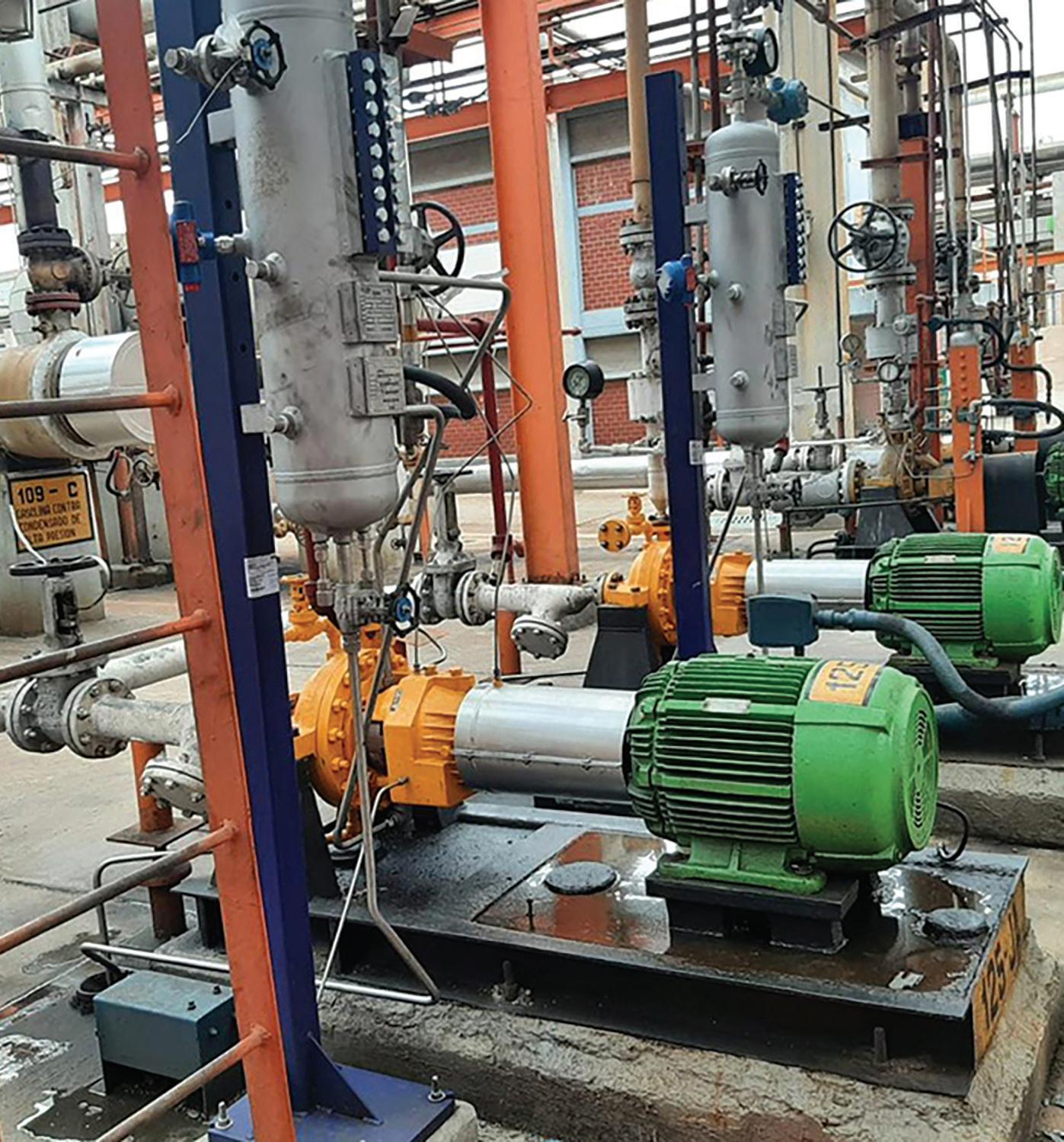
Sulzer’s onsite support was provided by the local service center.
Redundancy in the processes enabled one pump to be repaired without a ecting production.
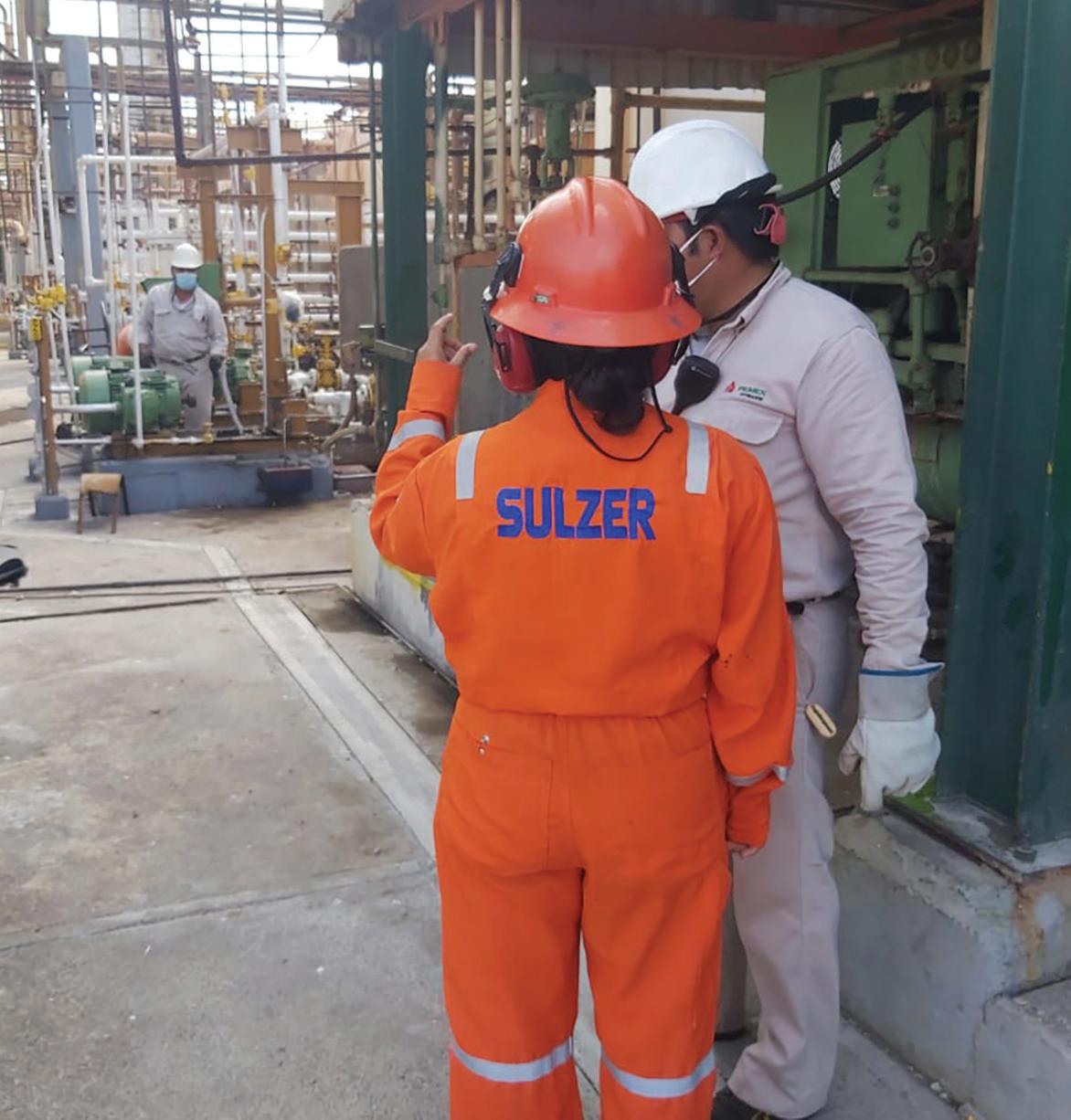
Design Notes
Pharma 4.0 with intelligent size changeover
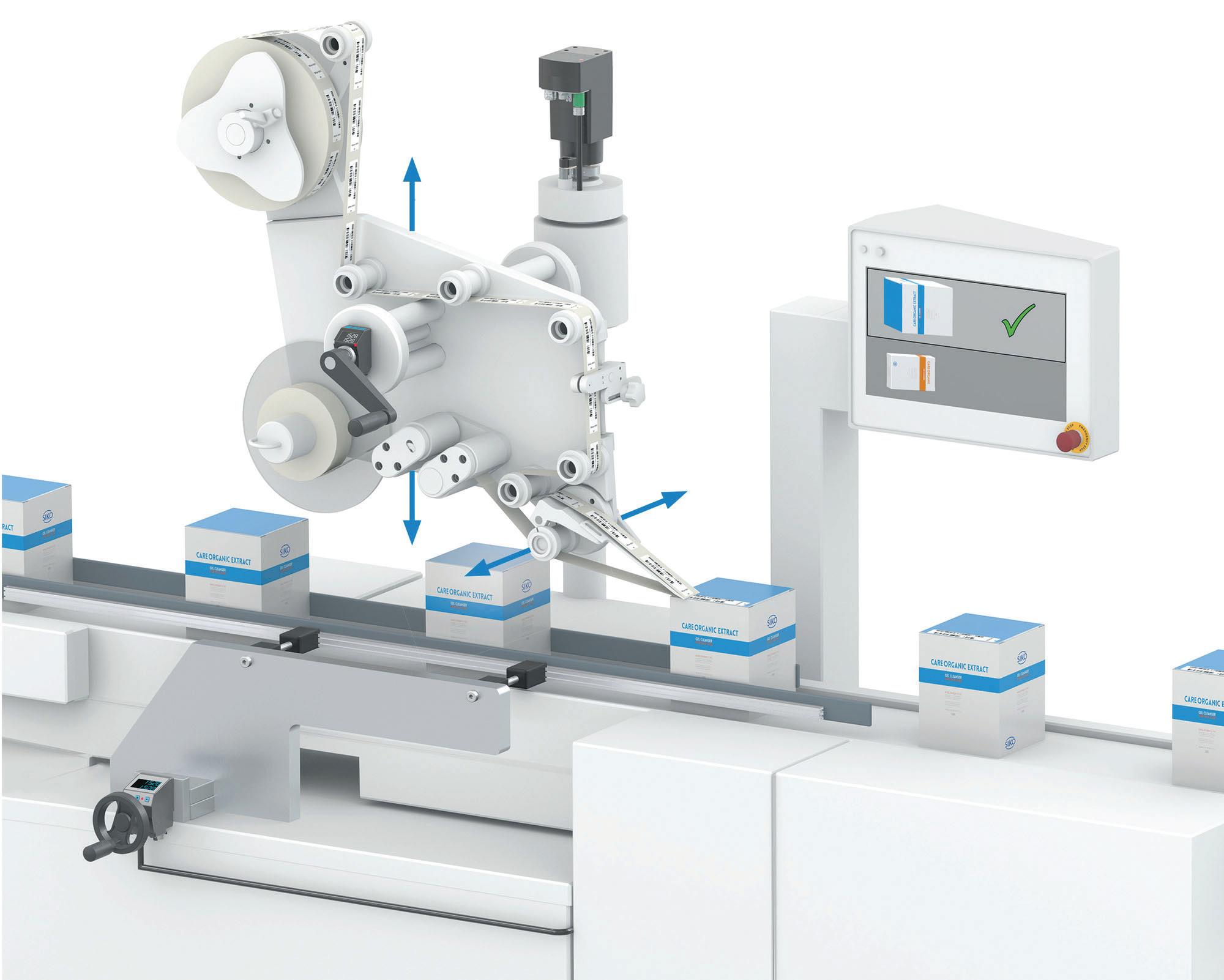
Juergen Schuh — Head of the Changeover Solutions business unit at SIKO
“Size changeover” is not a term that immediately makes people stop and pay attention in the pharmaceutical industry. However, considering the challenges in pharmaceutical manufacturing, which are characterized by cost, competitive pressure, and strict regulations, intelligent size changeover means competitive advantages in terms of e ciency, product quality, and process reliability. With automated, networked solutions, pharmaceutical companies can take a decisive step towards Pharma 4.0. In the pharmaceutical industry, “centerlining” is relevant, which means optimum machine settings must always be selected to prevent unnecessary deviations in the process. The aim is to network manufacturing, technology, maintenance, and electronic data acquisition in the best possible way. In addition, the growing variety of products and ever smaller batch sizes in pharmaceutical manufacturing demand a high degree of fl exibility om the systems. This is where size changeover comes into play, which can be a decisive factor for system availability. With optimized size changeover, reconfi guration times for product changes can be signifi cantly reduced and process reliability increased. SIKO GmbH,

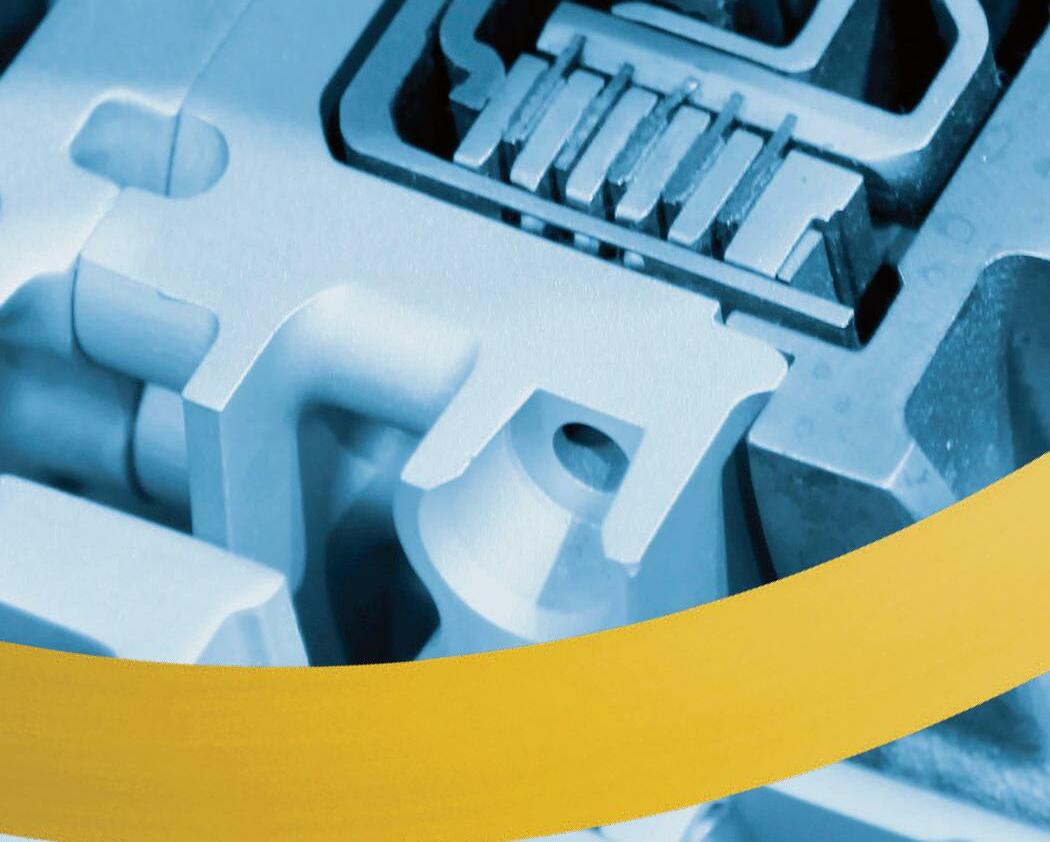
a manufacturer of sensors and positioning systems, has introduced various options for size changeover, om purely mechanical position indicators to fully automated positioning drives. In pharmaceutical manufacturing, size changeover occurs everywhere, especially in packaging processes, labeling, and product inspections. Whenever the dimensions on the machine must be changed for a new product, this involves size changeovers — whether manually via a crank or automatically via an actuator. Always exercise caution when changing the machine settings, as errors can creep in and harm the product result. Monitored or even automated size changeover minimizes the risk of incorrect settings and can make processes more fl exible. A distinction is made between manual, monitored, and automated size changeovers. Which type of format change is most suitable depends on the requirements: the more sizes need to be changed over, and the more demanding manufacturing is om a quality perspective — which is usually the case in the pharmaceutical sector — the more sensible it is to use monitored or automated positioning systems. For manual size changeover, both mechanical and electronic position indicators are used, which indicate the actual value of the current position. They are suitable for basic machines with rather in equent adjustments. The common mechanical-digital SIKO position indicators are precise, easy to read, and confi gured for each application. Electronic position indicators have an advantage over mechanical ones in that they are eely programmable and can therefore be used with greater fl exibility. Parameters such as
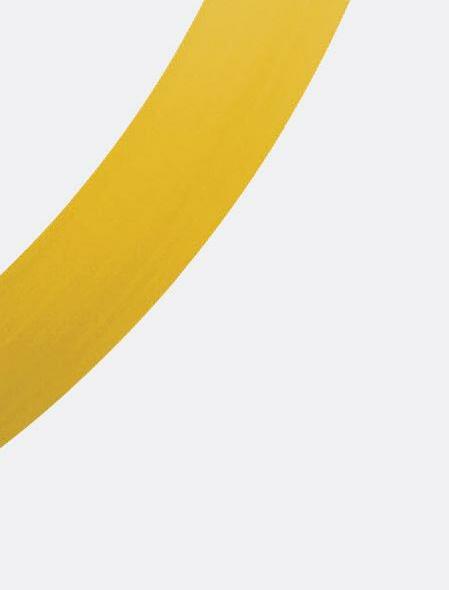
Comparison of optimization potential through intelligent positioning solutions.
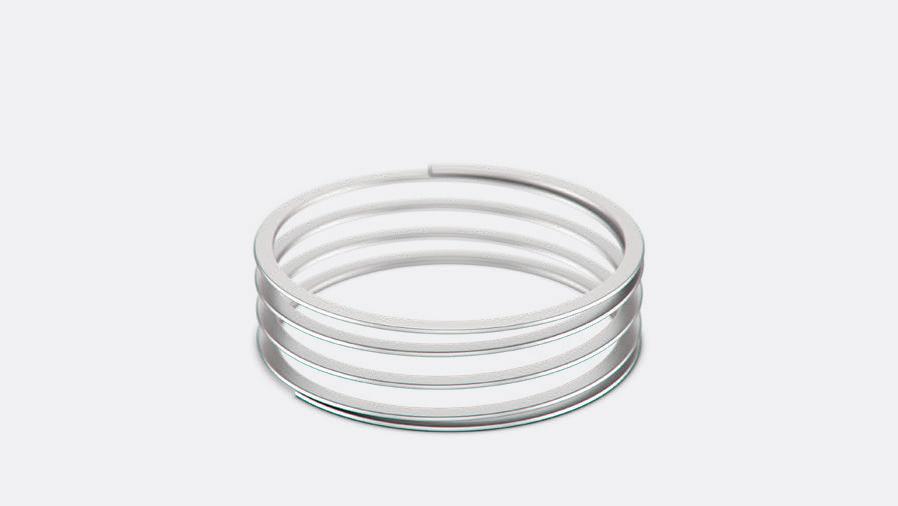
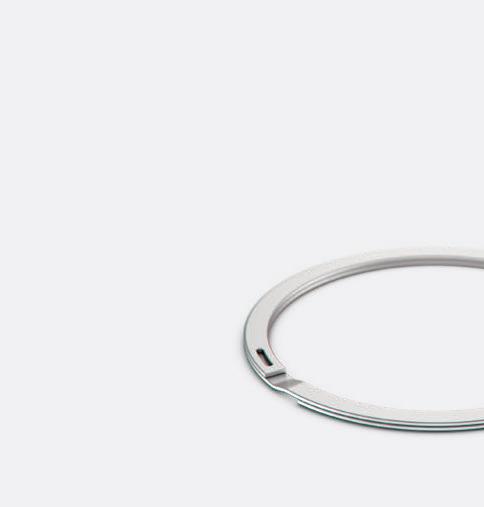
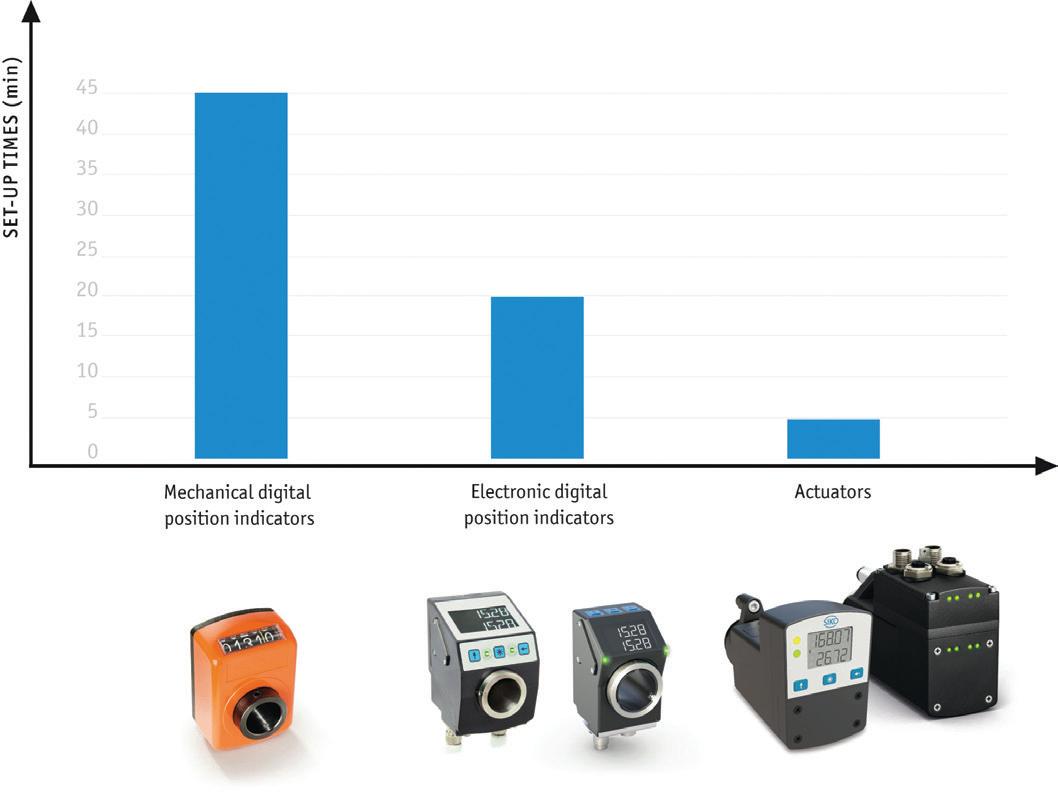
OPTIMIZE YOUR DESIGN
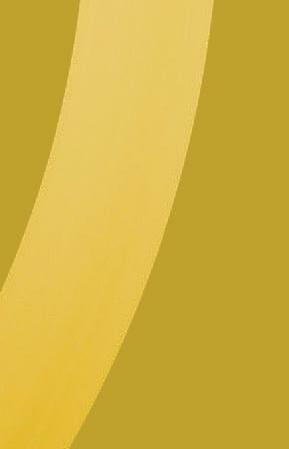
We make it easy to take your design further with a custom ring or spring.
• Economical Prototyping (No-Tooling-Charges™) • Quick Lead Time • Diameters from .118” to 120” in 40+ Materials • Industry-Specialized Design Support Industry-Specialized Design Support
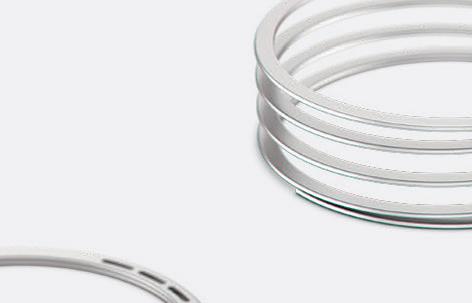
Custom Retaining Rings and Wave Springs
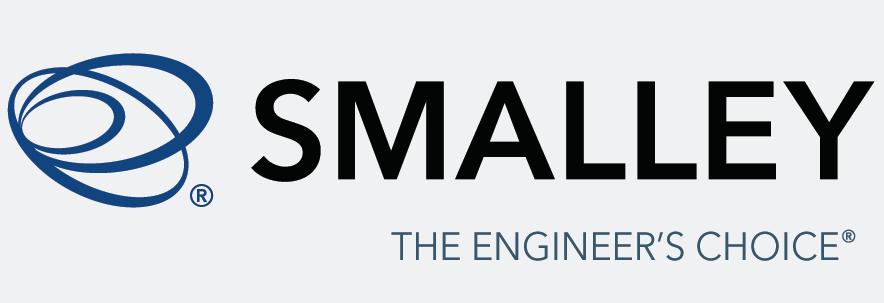
Design Notes

spindle pitch, decimal places, direction of rotation, mounting position, or use in angle mode can be conveniently confi gured. Monitored size changeover is made possible by bus-compatible electronic position indicators with setpoint value specifi cations which are integrated into the machine control system. Actual and target values are exchanged and compared between the individual position indicators and the higher-level control unit with a formula management system in which all product variants are stored with their setpoint values as formulas. This enables increased process reliability, as the system is only restarted when all setpoint and actual values on the indicators match. Rejects or damage to system parts are thus avoided. The changeover of the axes is still carried out manually with this variant, whereas the monitoring of the correct settings is carried out electronically. The special feature of the electronic position indicators is the LED lights which clearly display the position status to the operator: Green lights for “position correct,” red lights signal “position not correct.” Monitored size changeover can be helpful in pharmaceutical manufacturing, for example, in the case of systems for cartoning machines requiring equent adjustment. A relatively new development are “Track & Trace” systems, which require prescription drugs to be provided with a clear, traceable label. This involves several processes such as printing, reading, labeling, and weighing. The process reliability of these systems is increased with monitored size changeover. If axes are changed over without any manual intervention, this is called automatic size changeover via compact positioning drives. The actuator, networked with the machine control system, moves directly to the required position. With automation, a further signifi cant reduction in reconfi guration times is achieved. An actuator is characterized by its highly integrated design, which combines all components in one device: the brushless DC motor (which is wear- ee), a low-backlash and powerful gearbox, a position encoder, and power and control electronics. The integration of the actuator into the machine controls and the communication with the controls is easily achievable.
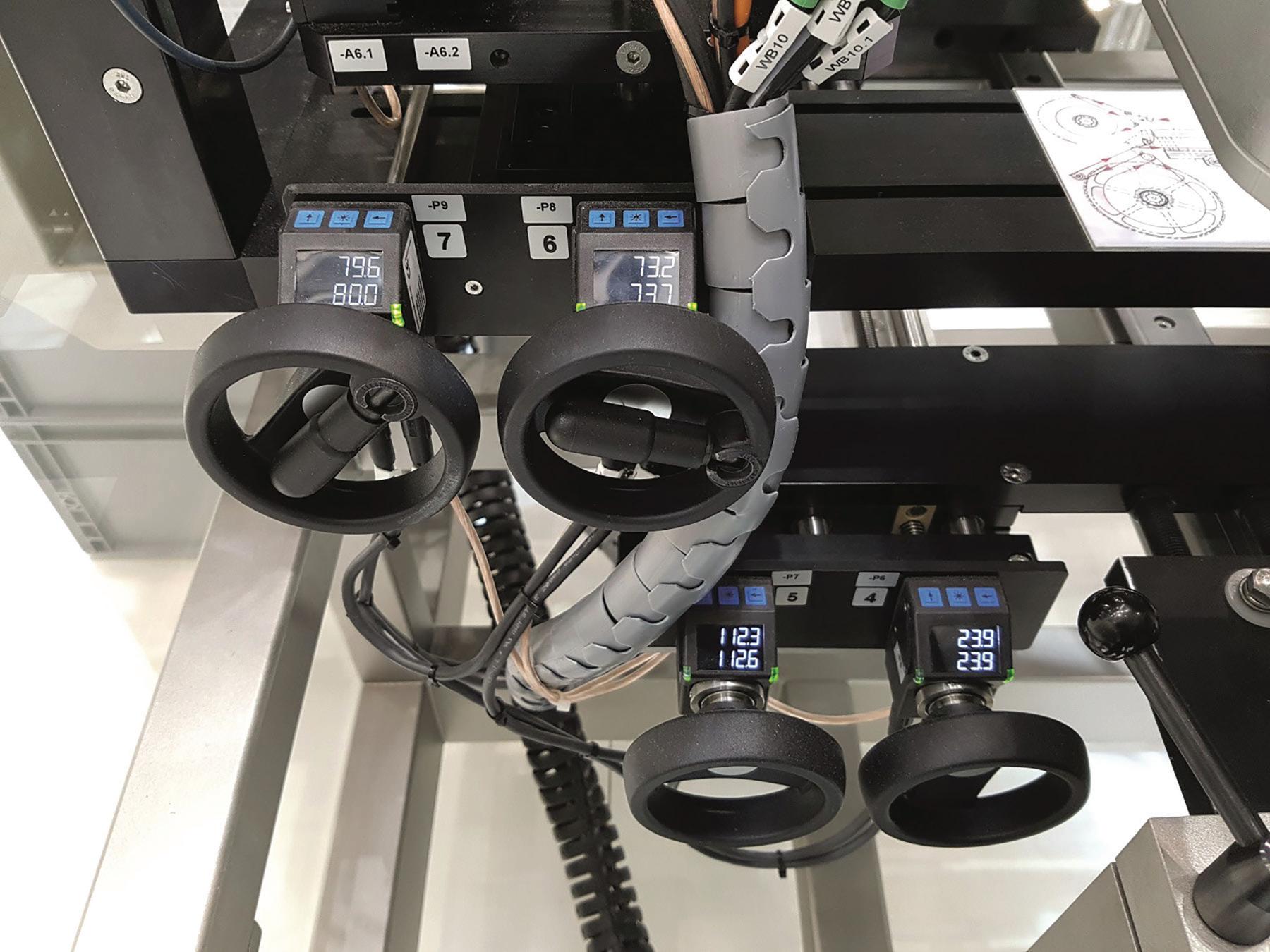
Size changeover using SIKO position indicators on a Track & Trace system in pharmaceutical manufacturing.

Depending on the application’s requirements, diff erent power classes of actuators are required: om small actuators with low power requirements for fi ne adjustment in a folding box magazine to feeding systems for large cardboard boxes where entire machine aggregates must be moved with actuators with relatively high torques. With this variant of size changeover, the controls only initiate a system restart when the process data exchange between the drive and the control has resulted in a match between the actual and setpoint values. Another functionality of the compact actuator makes it possible to conclude operating status: the diagnostic capability. By collecting and monitoring various drive parameters like current consumption in the motor, temperature, or voltage values at the control and load circuit, irregularities can be detected at an early stage. In pharmaceutical manufacturing, smart size changeover involves several dimensions: there are the directly measurable eff ects such as reduction of set-up times, increased plant availability, increased e ciency, and increased process reliability. Also, intelligent solutions help carry out secondary processes within manufacturing as unobtrusively as possible. DW

SIKO www.siko-global.com
Automated machine reconfi guration with SIKO actuator.
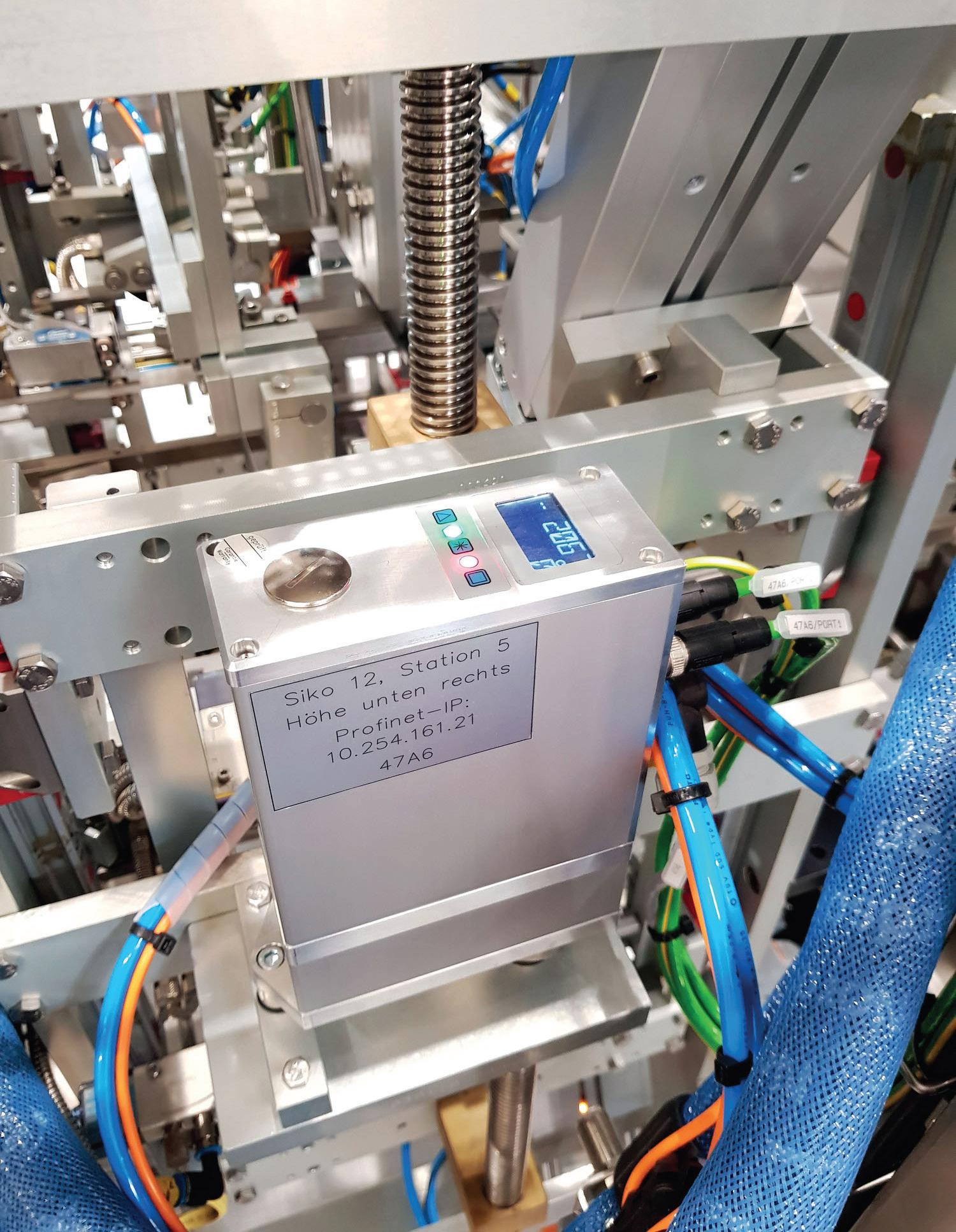

American Made North American & International Power Cords
Interpower North American and international cords and cord sets arrive with the correct country-specific amperages and voltages to connect to the local mains power. Interpower standards-ready cords are used worldwide—and ready to use right out of the box!
Every Interpower cord and component is subjected to Interpower’s strict quality control procedures: hipot testing, continuity testing, ground testing, and multiple inspections after each process. Interpower hospital-grade cords are made in the U.S.A.!
Interpower offers value-added options such as custom lengths, colors, packaging and labeling with no minimum order requirements, and expert customer service from 7 a.m. to 6 p.m. CST.
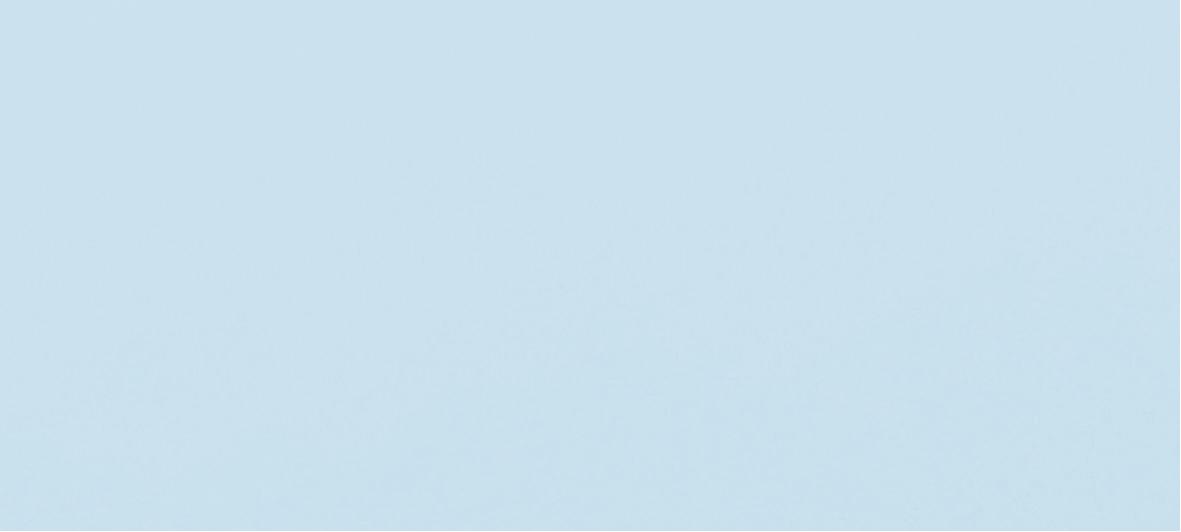
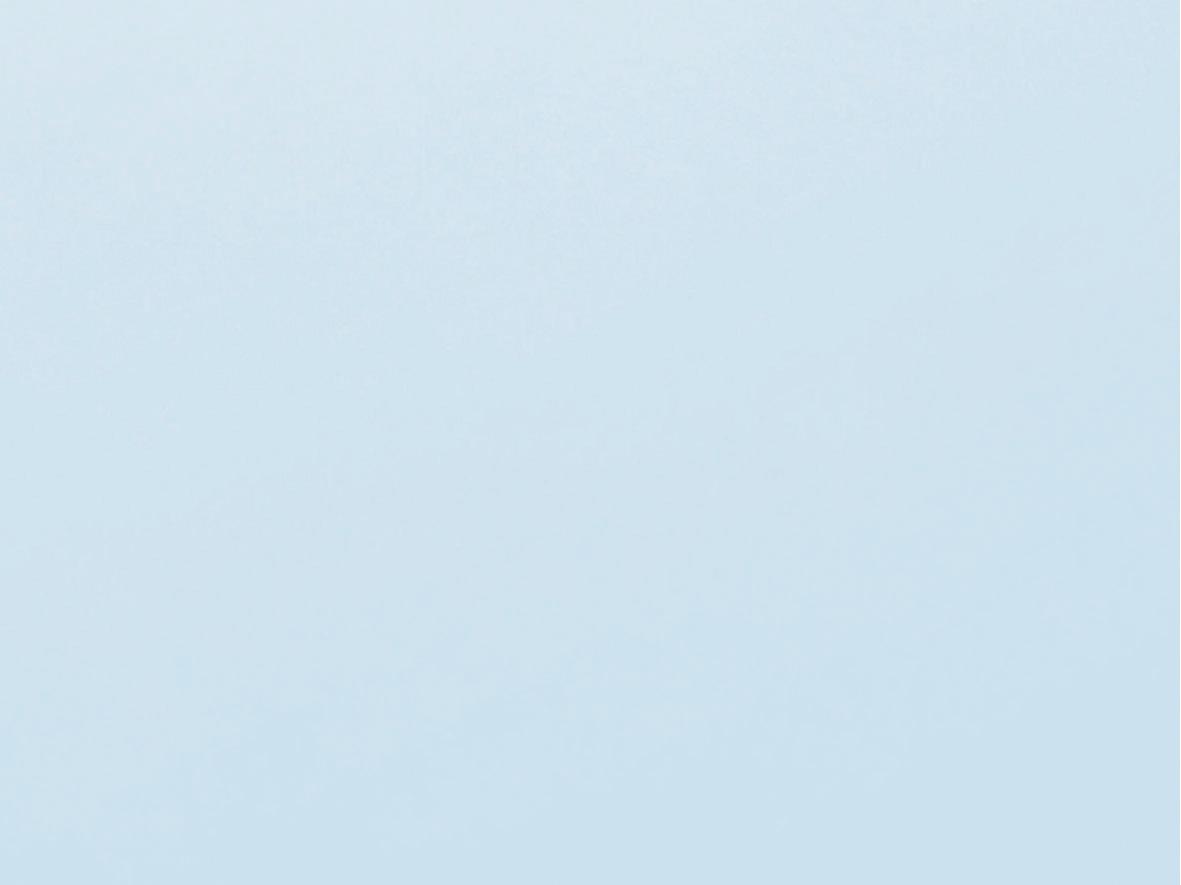
Toll-Free Phone: (800) 662-2290 E-mail: info@interpower.com
Business Hours:
7 a.m.–6 p.m. CST