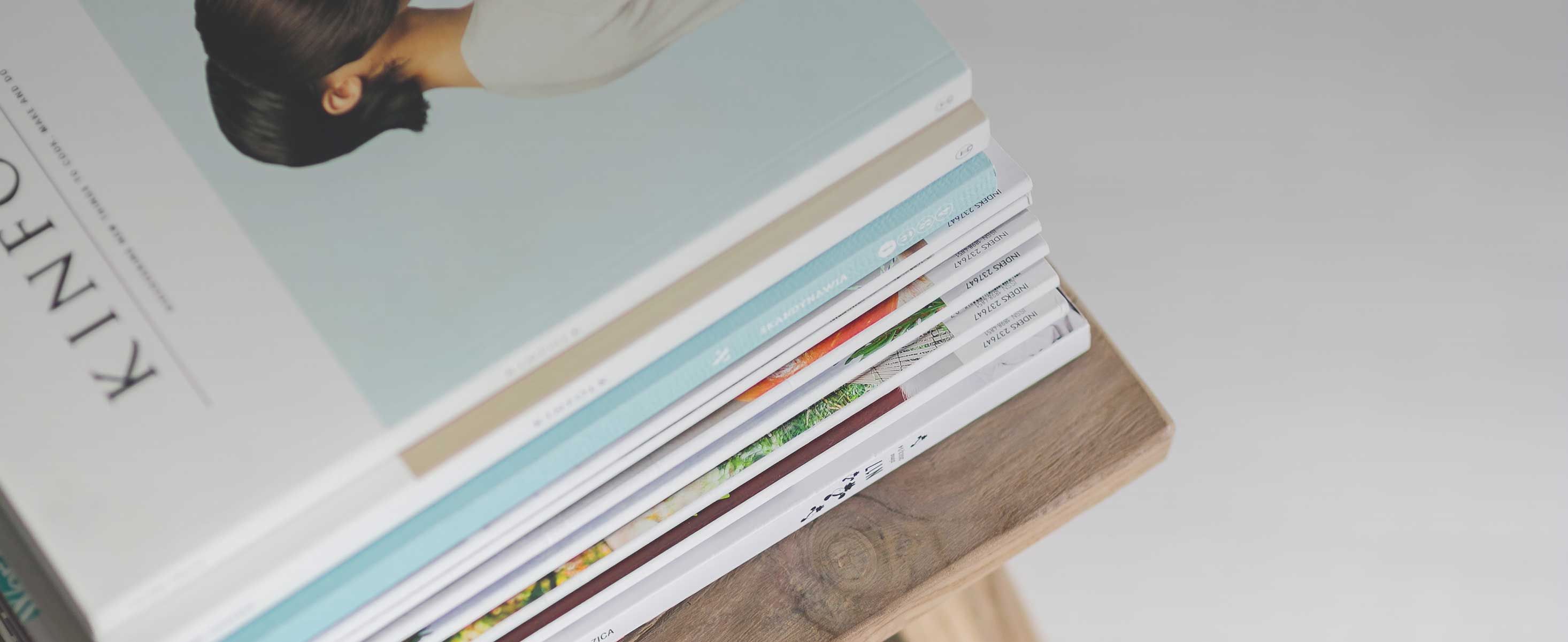
1 minute read
Compact linear motion system for small spaces
When you need to implement complex applications in small spaces, this family of compact linear systems can make design easier. Designers needing thrust and bearing support in a single, compact unit now have the flexibility to build such applications with these versatile components.
As demand for smaller-scale applications grows, so does the challenge of packing high functionality into a smaller footprint. In building a compact linear system, a designer can configure a unit or combination of units from a variety of components based on their specific application details. Components include, but are not limited to:
• Integrated stepper motors
• Lead screws
• Profile rail linear guides
• 60 Case LinearRace shafting
• Linear Ball Bushing bearings
• End blocks
Many features can be customized, including screw diameters and leads, mounting holes and mounting configurations.
To take maximum advantage of such flexibility, engineers can refer to an innovative 3D modeling tool that optimizes their solution by revealing design tradeo s in real time. The tool guides the designer in tailoring motor size, stroke length, and other variables to function most e ectively within given load and space parameters.
The resulting design information is used to produce a prototype, which is sent back to the engineer for testing. Because of such close user involvement during the design process, the number of design iterations is reduced, which, in turn, decreases the likelihood of mistakes being made.
These compact linear systems are appropriate for applications requiring high-accuracy linear axes in confined spaces, such as 3D printers, microscope stage managers, medical pipetting systems, and semiconductor manufacturing. They are available with NEMA motor sizes between 14 and 23; stroke lengths of up to 40-in. (1000 mm); and load capacities up to 2091 ls (9300 N). DW Thomson