
2 minute read
Fabco-Made NFPA
Versatile, rugged cylinders—when you need them A
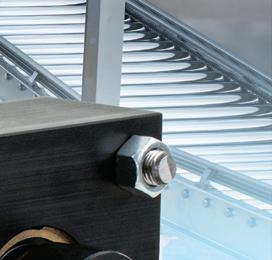
Our NFPA interchangeable pneumatic cylinders take the guesswork out of cylinder selection.
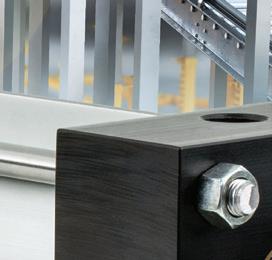

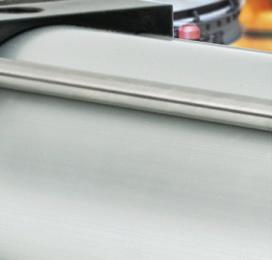
We design and manufacture our NFPA cylinders in Gainesville, Florida—so expect fast delivery, supply chain resilience and local support no matter your application. Built tough, our NFPA actuators feature anodized aluminum heads and barrels and stainless steel hardware for corrosion resistance. They also incorporate high-strength composite rod bearings and PTFE piston wear bands for superior load handling and long service life. Choose from 19 standard mounting options and hundreds of standard configurable options to meet the requirements of almost any application. Standard catalog not enough? Tell us about your application and let us design a custom solution optimized for your environment.
• Standard bore sizes: 1.5–6 inches
• Standard strokes to 99 inches
• Pressure rating: 250 PSI
• Temperature range: -10° to +165°F
• Conforms to NFPA dimensional specifications
• Lead time for standard configurations: 7–10 days
MADE IN GAINESVILLE, FLORIDA
Linear Motion
Iris actuators are rectangular voice coil motors designed for applications requiring short stroke motion with a low stiffness and high bandwidth.
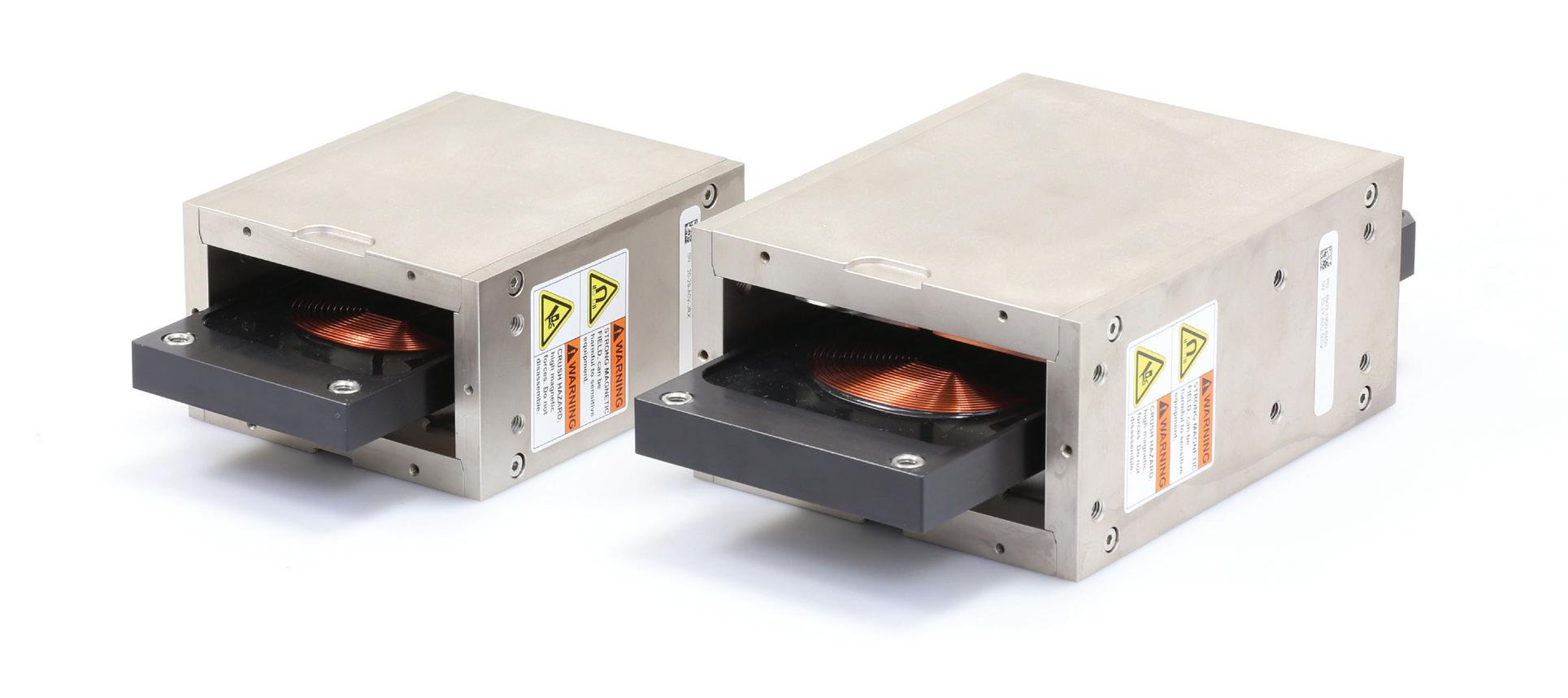
produced in-house, there is much more control over all of the variables involved. With a greater focus on components that reduce drift and deliver high linearity, the drive can enable high dynamic performance within a motion stage.
What’s more, these drives also feature low noise, ensuring no additional disturbances are introduced into the system. This eliminates jitter, which could cause inaccuracy, and enables applications to move at specific velocities without being impacted by noise and disturbances. This is essential in scanning applications, for instance.
The drives also feature a high switching frequency which provides high bandwidth and good attenuation for external disturbances. Internal filtering also limits disturbances to other systems like external sensors which can be extremely sensitive to noise in high-precision applications.
Real-world motion control
Another integral part of the Proton Motion Stage is the motion controller. The Poseidon motion controller works with the Prodrive Motion Platform (PMP) to collect sensor data and then communicate seamlessly with the servo drives to determine new position setpoints.
The motion controller features multiple EtherCAT buses which help to reduce the delay between the motion controller and the servo drives. Combined with the controller’s multicore x86 processor, this shortens the amount of time needed to collect sensor values, calculate new setpoints, and communicate these back to the drives. The faster this process, the more it can help improve the overall performance of the motion stage.
The PMP motion control software, with real-time performance and tooling, runs the algorithms required for motion control. However, it also provides extensive simulation capabilities. The PMP integration in Simulink lets engineers generate ready-to-load binaries, which can be loaded into the system easily, without requiring a specialist software engineer.
The big benefi t of simulation is that the stage’s processes can be tested even without the hardware in place to verify that it’s working. Optimization of the hardware or control of the system, and the impact of any changes to them, can then be captured at this early stage, making it quicker when the time comes to complete testing with the hardware.
However, this approach is also beneficial for saving businesses
PMP motion software provides real-time performance and tooling. The Matlab and Simulink interfaces allow the combination of simulation code with an existing motion system, providing more opportunities for control loop optimization and tuning.
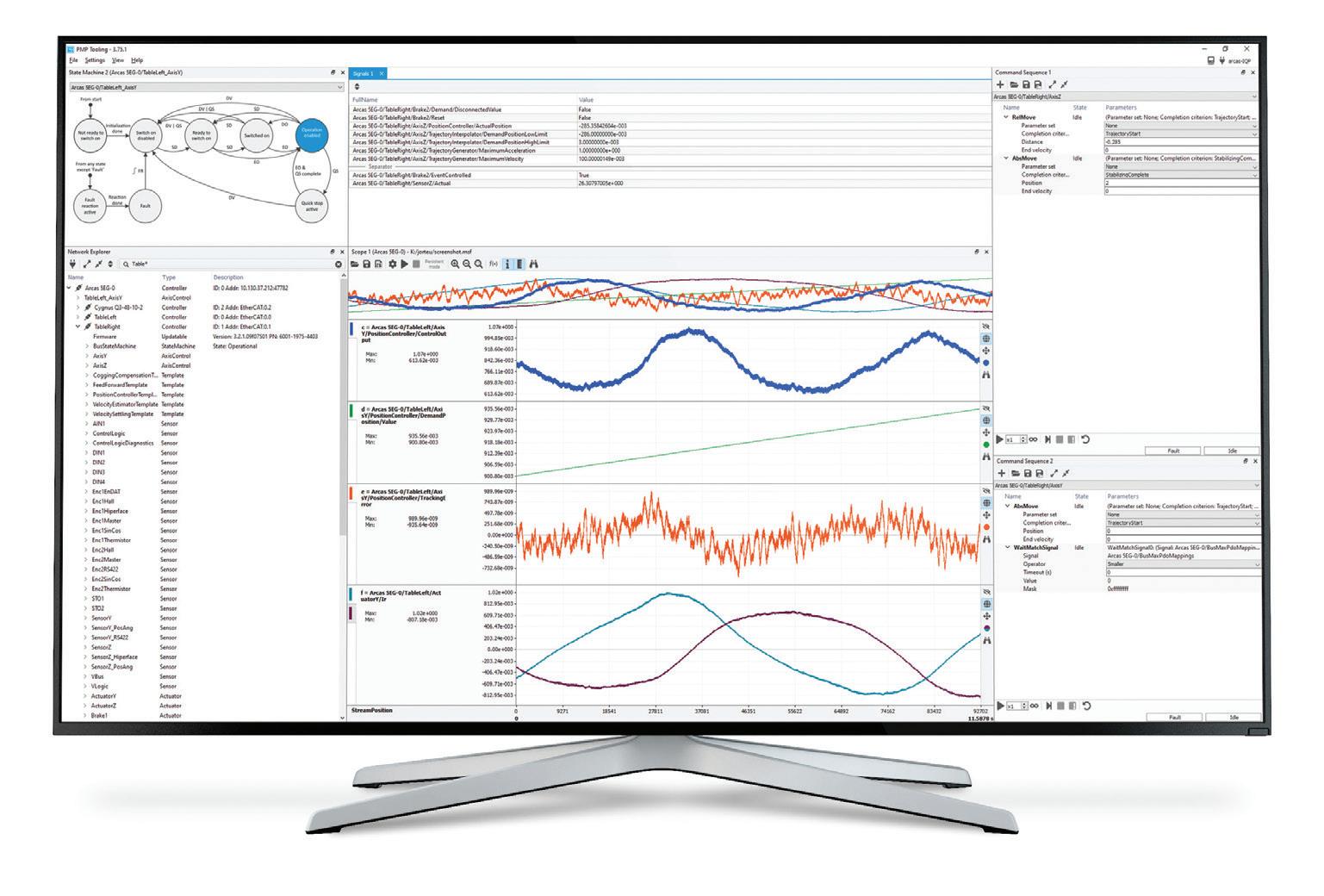