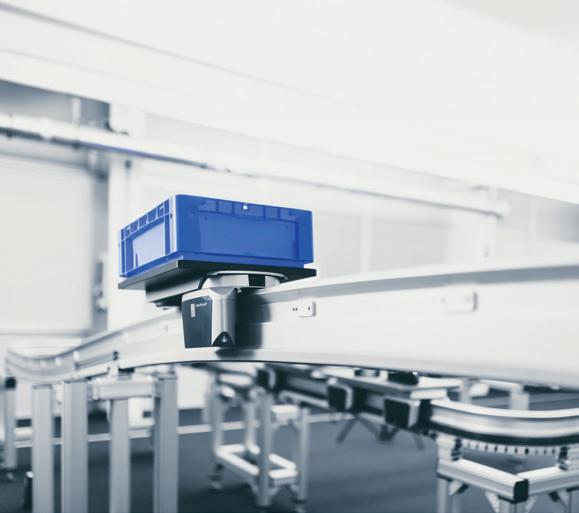
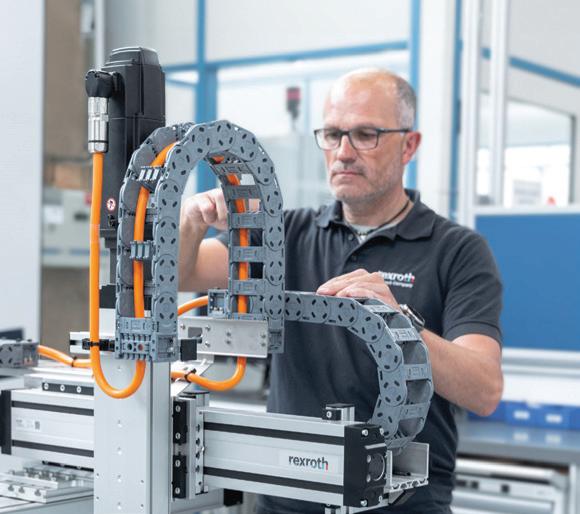
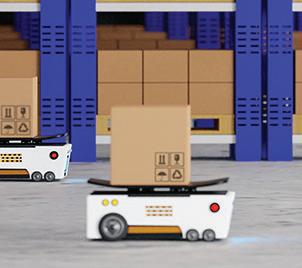
MOTION CONTROL
Pallet conveying — for pacing small electronics and more
PAGE 22
LINEAR MOTION
How linear motion technology is meeting the challenges of tomorrow
PAGE 26
THE ROBOT REPORT
What do customers expect from mobile robots?
PAGE 58
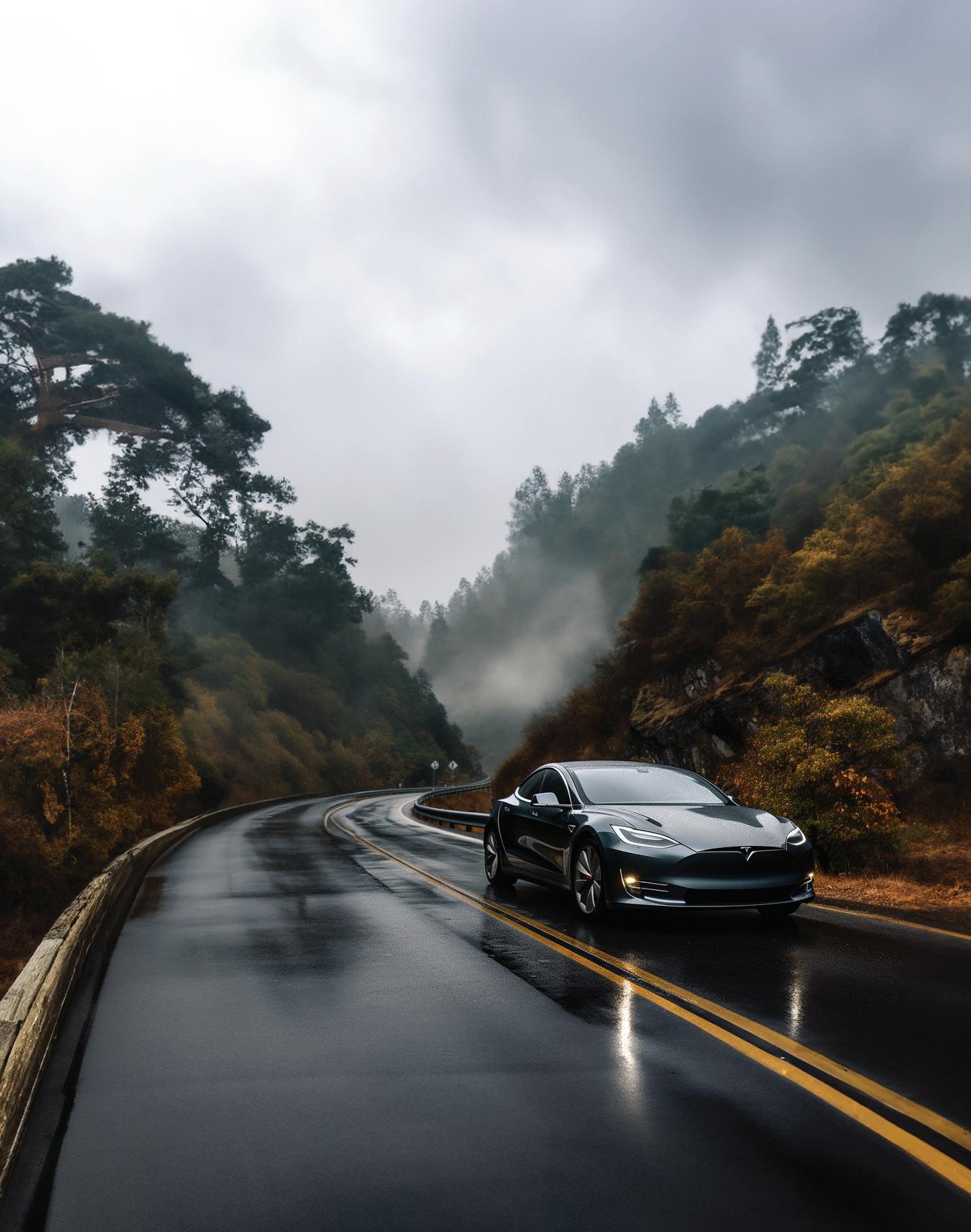
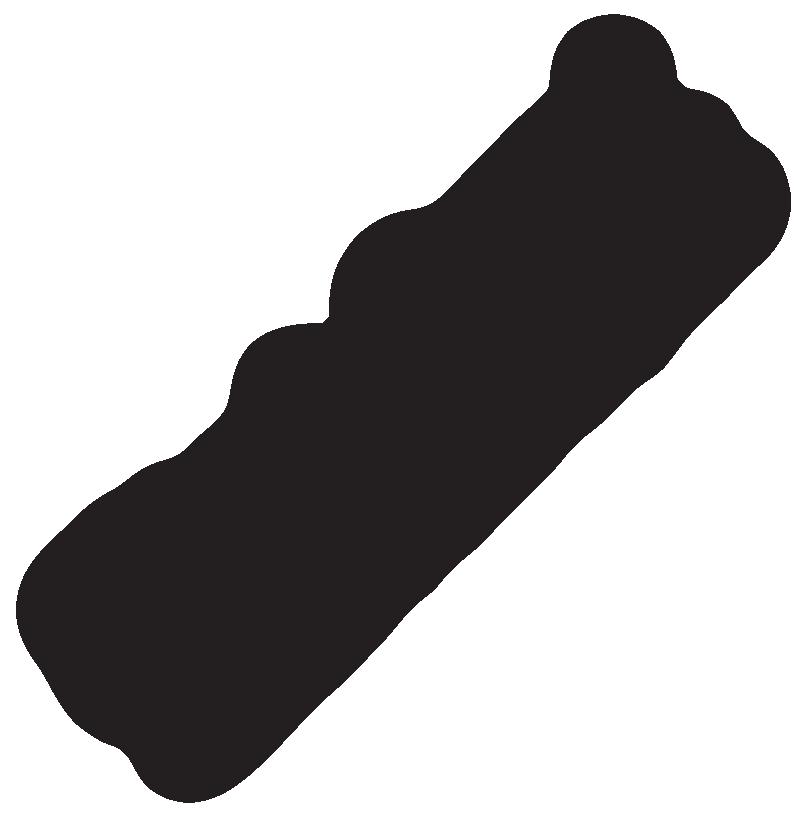
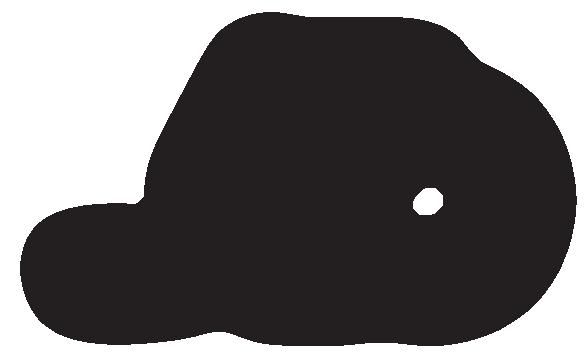
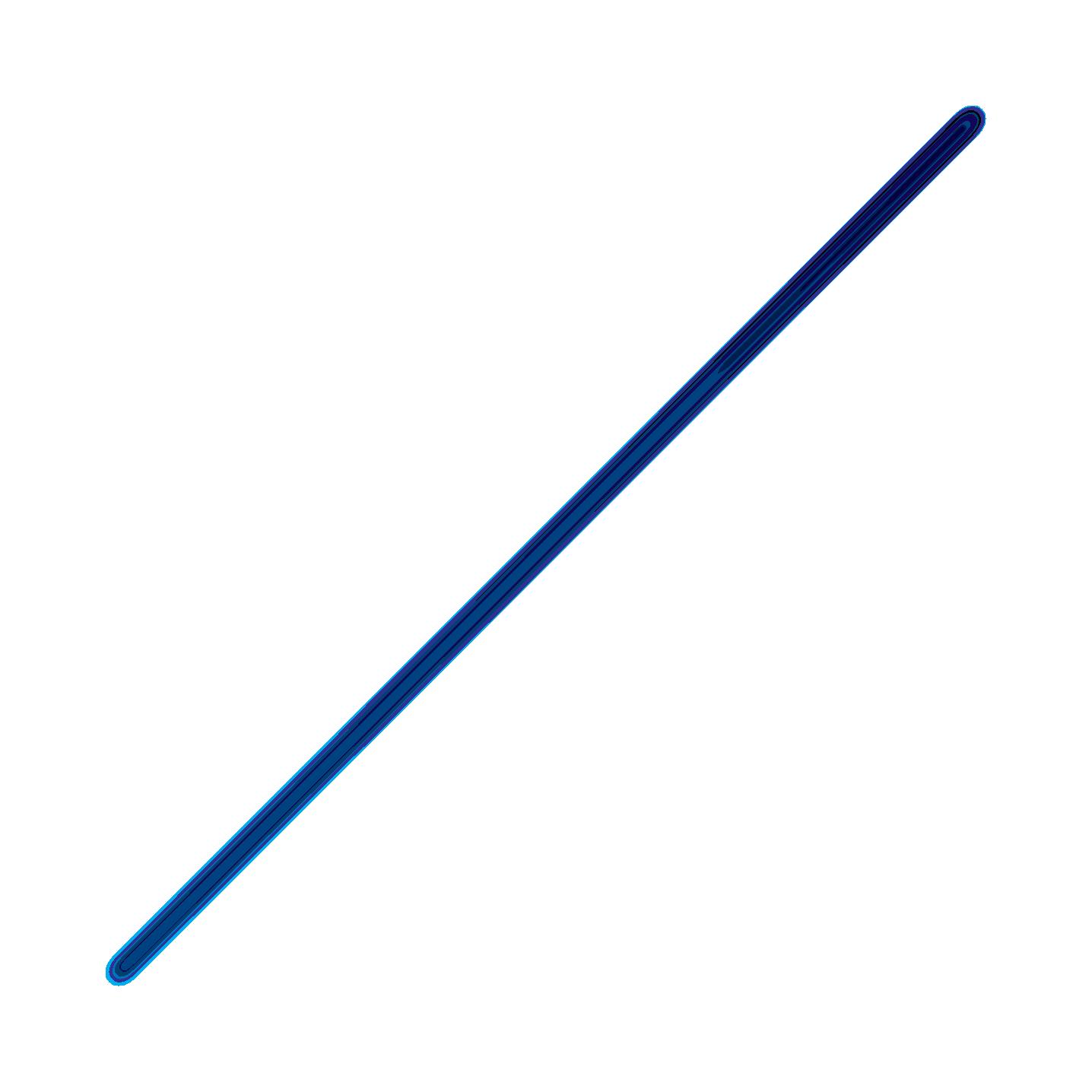
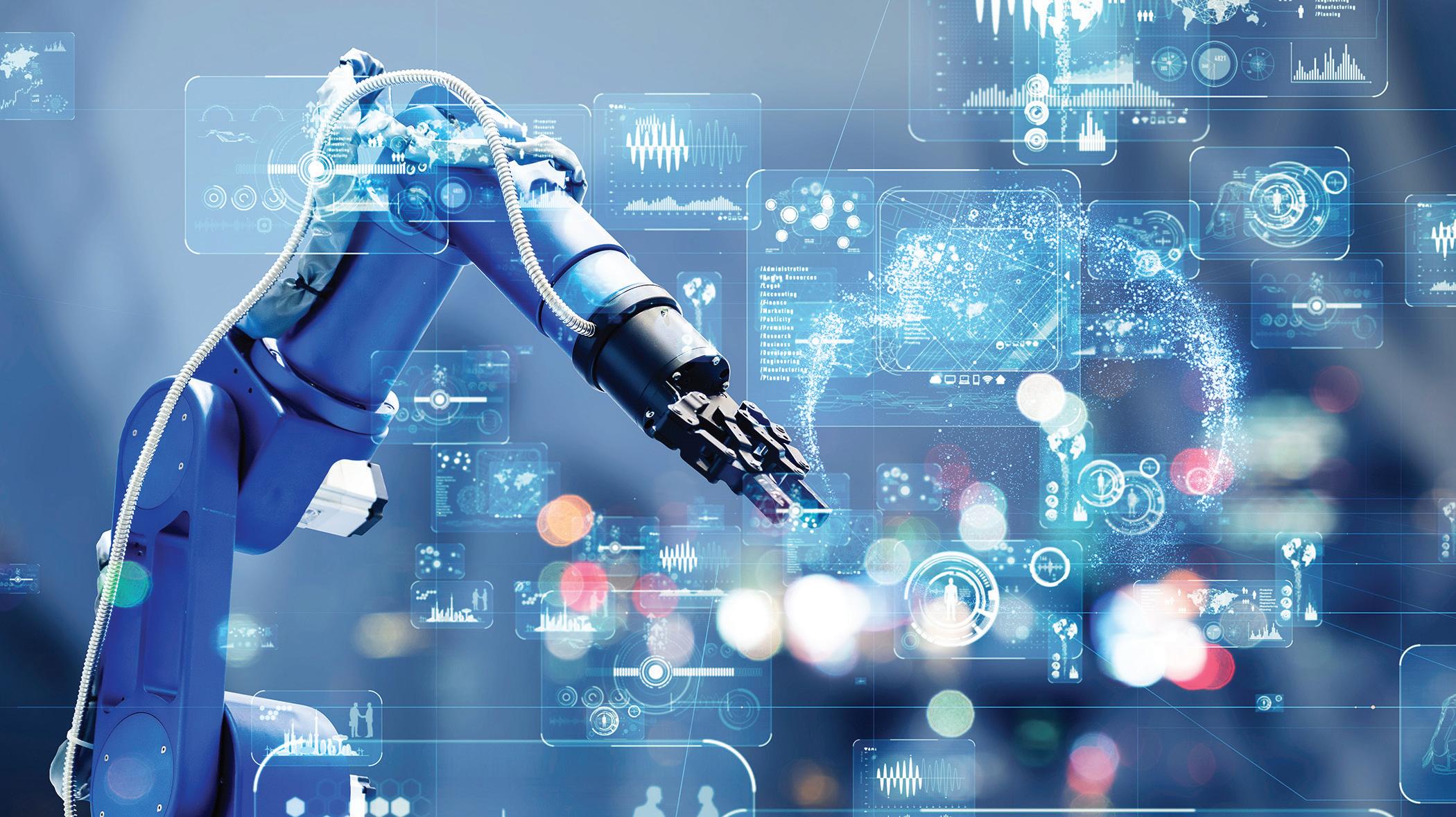
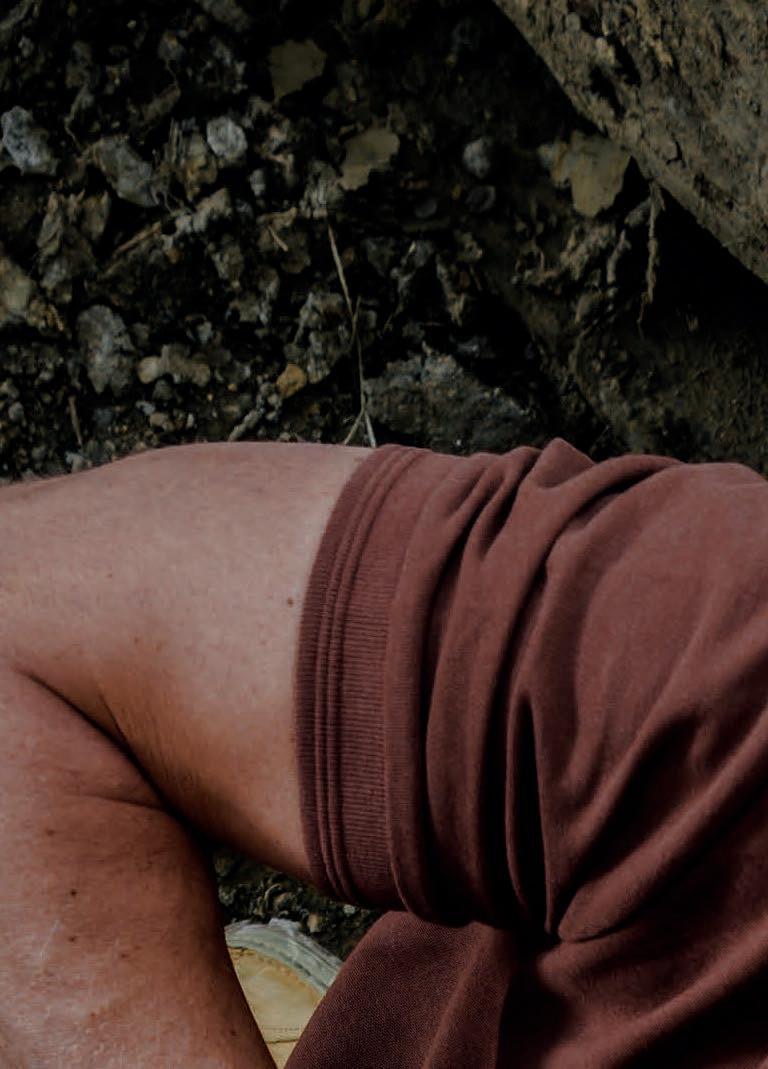
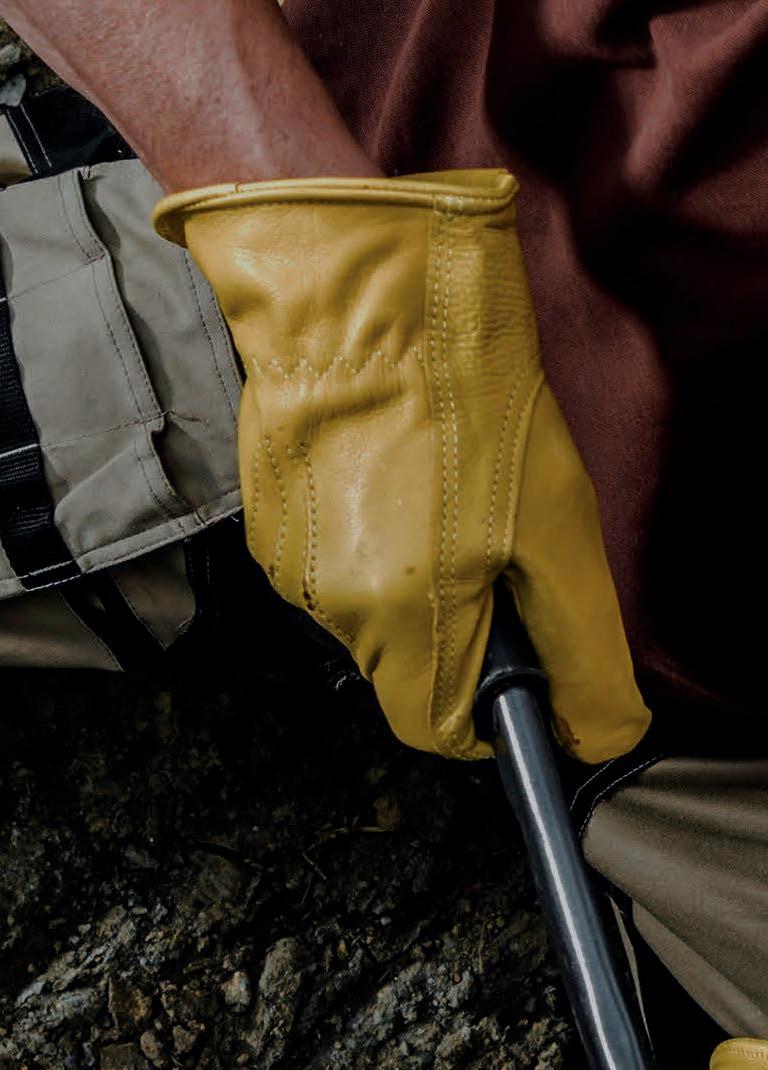
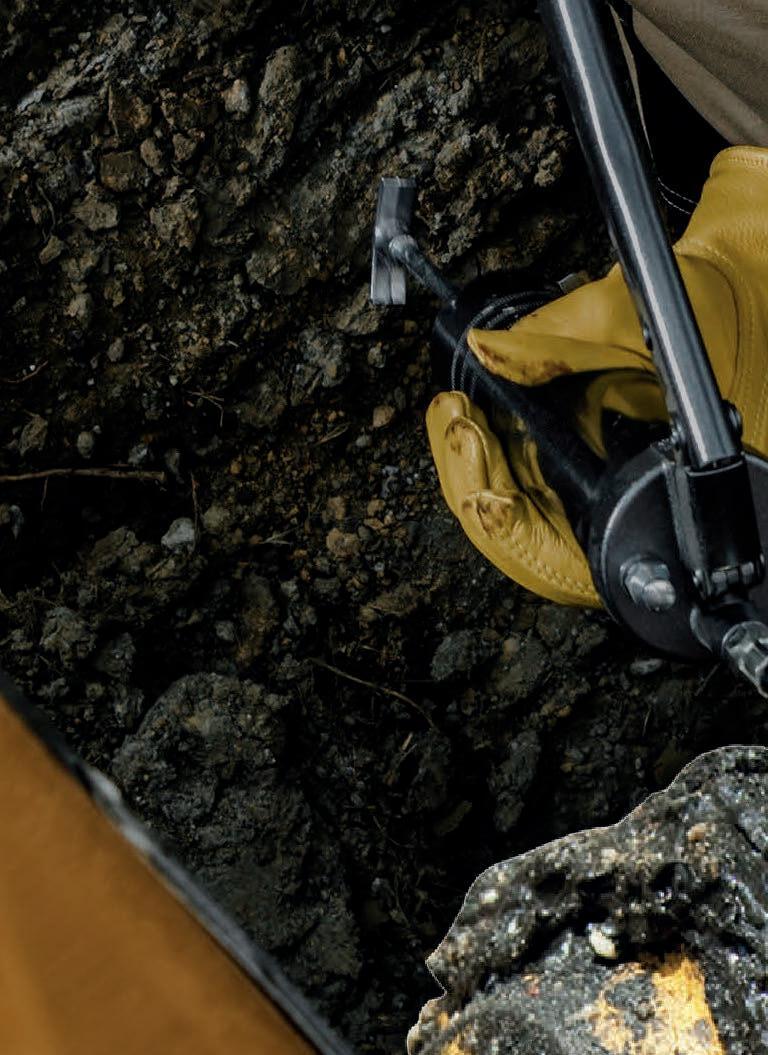

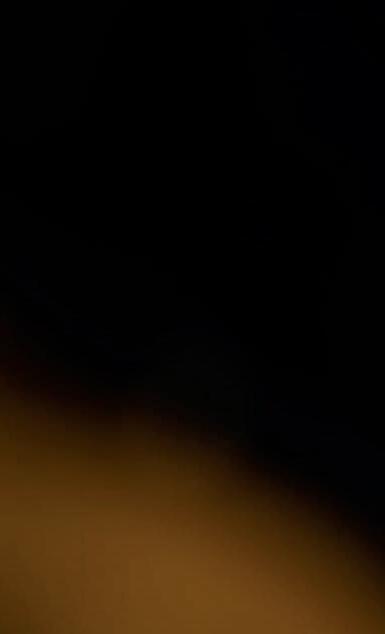


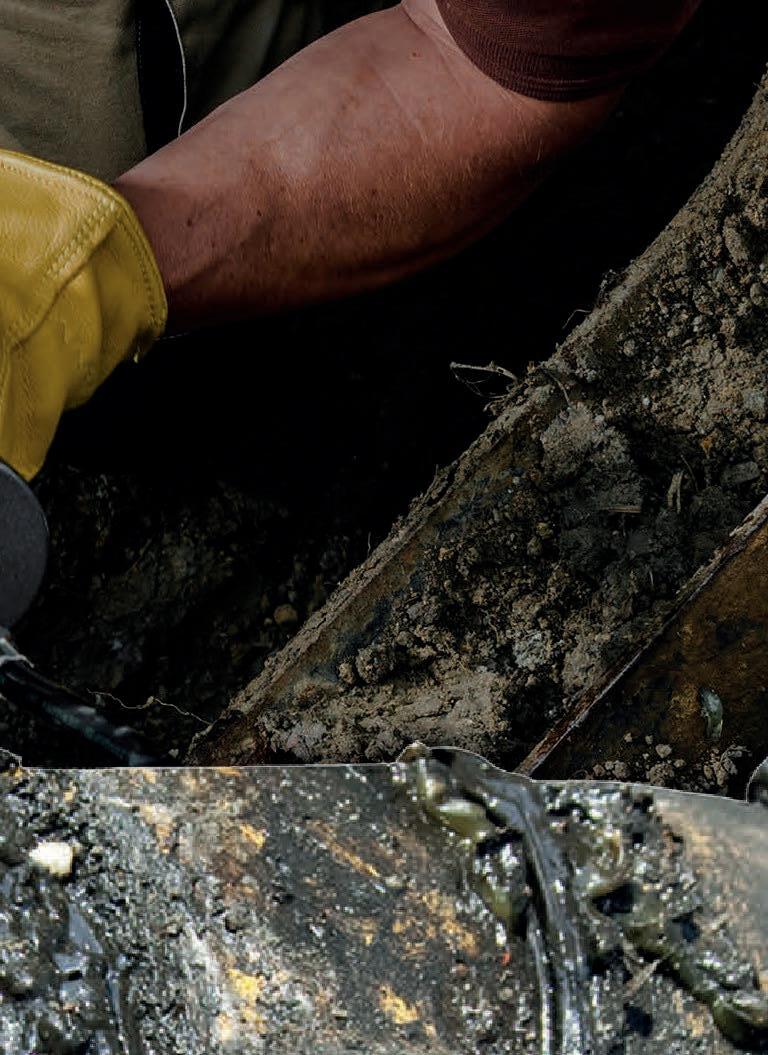
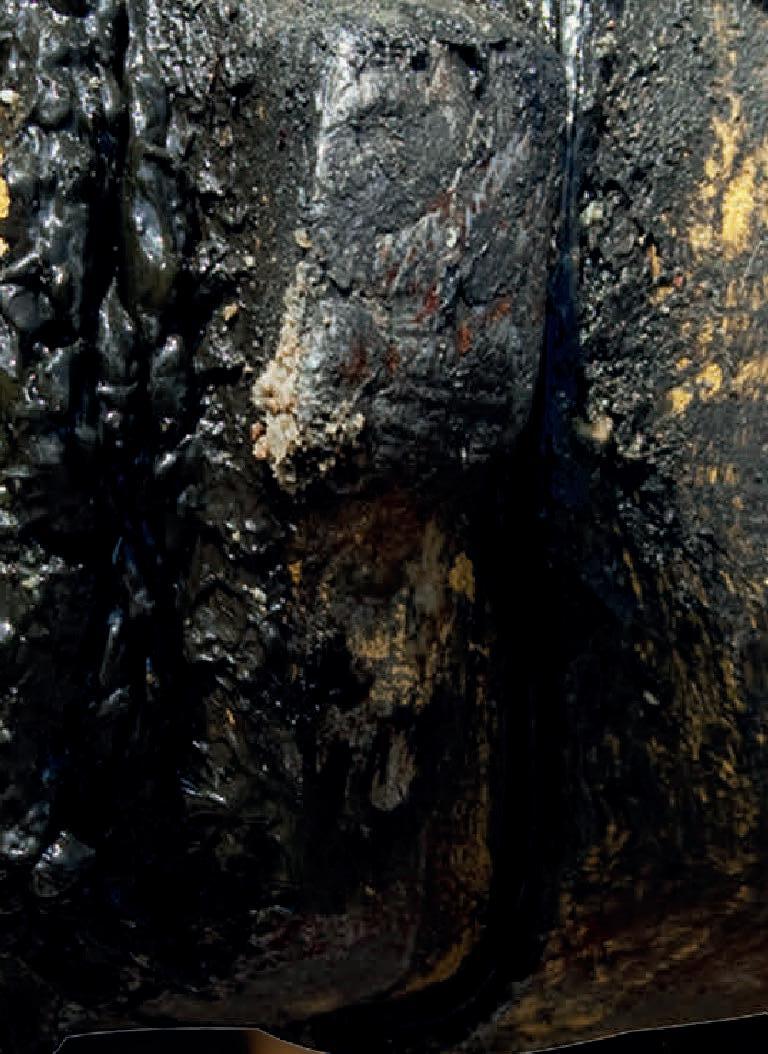
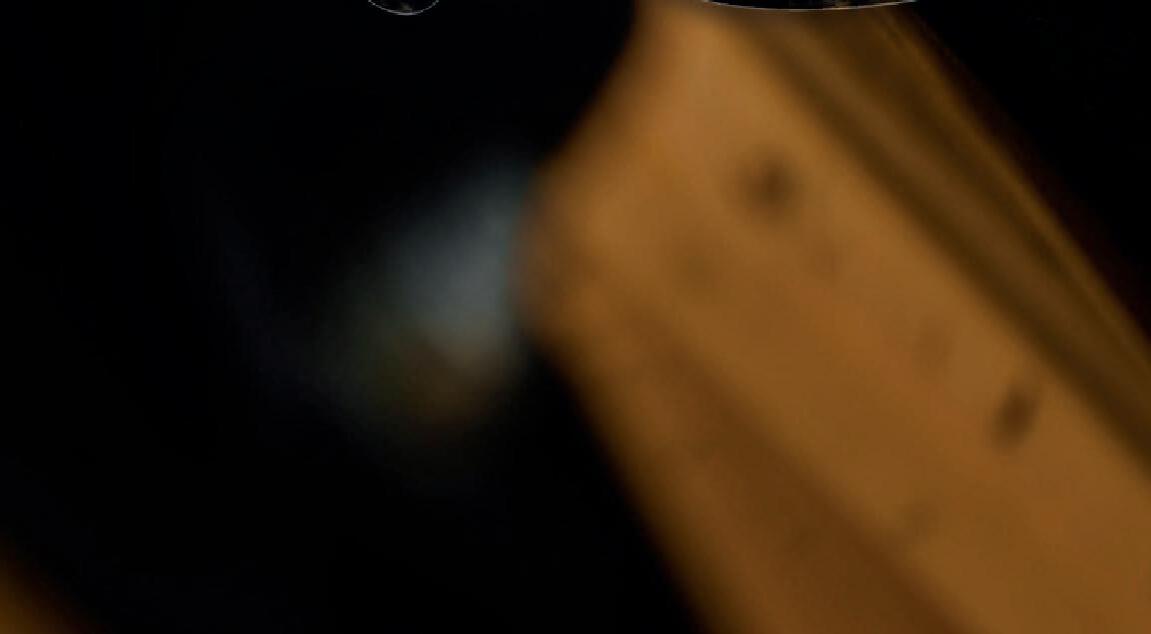
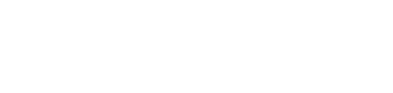
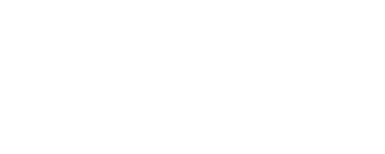
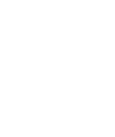



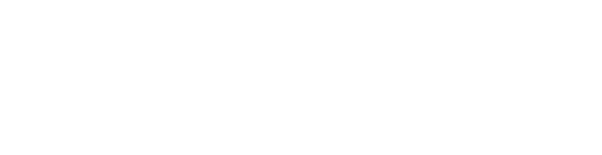

Pallet conveying — for pacing small electronics and more
PAGE 22
How linear motion technology is meeting the challenges of tomorrow
PAGE 26
THE ROBOT REPORT
What do customers expect from mobile robots?
PAGE 58
Lubricants and lubrication-related downtime account for a combined $990 billion per year in lost revenue worldwide. Eliminate grease and other lubricants from your equipment, and go zero with igus. Join us at a trade show this fall and go zero!
THK is a leading manufacturer of high quality and ultra precise miniature linear guides, ball screws, cross roller rings and actuators for a wide range of industries, including industrial automation, medical, aerospace, semiconductor, machine tool and robotics.
LM Guides - SRS Series - Featuring patented THK Caged Technology, the SRS Miniature LM guides perform with smooth and quiet motion, long-term maintenance free operation, increased speed and accuracy, low dust generation and a long life.
Cross Roller Rings - RAU Series - THK Micro Cross Roller Ring Series RAU are compact and lightweight and even more rigid than a double row angular contact ball bearing type. Spacer retainers enable smooth movement and high rotation accuracy.
Ball Screws - BNK and MTF Series - BNK with finished shaft ends and MTF Roll-Formed screw shaft are known for their high accuracy, low noise, smooth movement and long-term maintenance free operation.
Actuators - KR Series - KR Actuators consist of LM guide units on the ends and ball screw unit in the center making them highly rigid and highly accurate in a minimal space.
To learn more, call us at 847-310-1111 or visit www.thk.com.
starting at $3.75/5 pk. (PLUG532)
NITRA pneumatic push-to-connect fittings are easily installed and work well with flexible tubing to make sealed connections.
• Threaded connections available with NPT, G-thread, and BSPT R-thread types
• Union-style fittings
• Available in thermoplastic, nickel-plated brass, or stainless steel bodies
• Configuration options include male straight (hex and round body), bulkhead female, long male elbow, tee reducers, and much more
• High working pressure and temperature
• Threaded elbow and tee fitting bodies can be rotated after installation
starting at $23.00 (7001000100U)
Metal Work is a trusted name in pneumatic components, and we now carry several valve types, including toggle and axial lever manual valves, push-pull manual valves, mechanically operated air valves (mechanical limit switch valves), pushbutton air valves, air pilot valves, and solenoid valves. Configuration and port sizes include 3-port, 3-way, 2-position, and 5-port, 4-way, 2- or 3-position valves.
• Coils sold separately for solenoid valves in voltages from 12 VDC to 220 VAC
• Solenoid valves are available in internally and externally piloted versions
• Externally piloted valves allow a comprehensive pressure range and control pressures down to a full vacuum
starting at $15.50
Cylinder Position Switches
NITRA cylinder position switches are compact purpose-built switches designed to detect the position of a cylinder.
• Electronic solid state switch output
• GMR sensing technology
• LED switch status indication
• Integral 0.15m cable with M8 snap-fit connector or 3-meter wire leads
• Come with either 45 or 90 degree cable
• 5-28 VDC operating voltage
• NEMA 6 / IP67 rating
• CE, RoHS, REACH approvals
- brushed or bldc motors - 5 amps per axis - 16 analog inputs - 16 on/off drivers - home and limit in - live tech support - made in the USA
Startups have it made. With a single match, they can ignite engineers’ creativity and fuel collaboration and quality naturally within their emerging cultures. Light the same match in a long-standing company, and many people flee and protest, clinging to the way things have always been.
In chapter one of “Quality Management for Dummies” by Anthony Murphy, VP and head of product management at Plex, Rockwell Automation’s smart manufacturing platform, the opening line states, “It seems silly to say that a quality management program starts with developing quality as a mindset, but it’s absolutely true.” Quality is imperative to any organization that aims to persevere and grow. Murphy urges teams to value it and leverage digital tools to develop “a living system designed to proactively support, manage, and control all aspects of an organization’s operations that impact product quality.”
But documenting controls and telling employees how to think through emails and mandatory training isn’t enough. Quality takes action, and it starts with leadership.
“Quality is all about people, and it's all about leadership setting the tone, standard, and culture. Leadership's job is to foster a culture of quality, think about it holistically, and define and measure it,” Murphy said during an interview. “But defining quality is not only product quality. It's also how you engage with your people and
your team, how you communicate, how you think about the community in which you operate, and being a good steward there.”
Though I went into that interview seeking insight into digital tools for modern quality management systems, I left with an understanding that developing a culture of quality is almost synonymous with workforce development strategies.
“People and culture are the hardest parts to solve for. They’re the most variable,” said Murphy. “If you don’t have a strong culture and direction from the top, and if it isn’t a fundamental priority, then it’s not going to be successful.”
Murphy’s advice is to make it easy to do the right thing by blending people, processes, and technology to maximize value from each. The job of leadership is to align workers’ goals with the company’s goals so that everyone benefits. Tough decisionmaking is part of the gig, and frequent communication creates trust and transparency. Overall, leadership needs to reinforce quality as a priority not just because it sounds good but because the company is actually doing something about it. DW
Force that can hardly be restrained.
The new DiaForce diagonal compact fans.
The revolutionary fan concept combines the advantages of axial and centrifugal fans:
– Up to 50% more air performance
– Up to 6 dB(A) lower sound levels
–Ideal for cooling-intensive IT applications
–Optionally with integrated FanCheck diagnostic tool for calculating the specific remaining service life
More information for your application: ebmpapst.com/diaforce
Pallet conveying for pacing small electronics and more Pallet conveyors are hardly a new development, but the increasing speed and precision of these systems have made them the go-to conveyance option for a growing number of industries that are trying to boost throughput to keep up with demand.
How linear motion technology is meeting the challenges of tomorrow
To meet the complex factory automation challenges of tomorrow, linear motion systems are evolving to become quicker, more economical, and more sustainable.
How many ways are there to measure temperature? Temperature is the most commonly measured physical quantity. Thermometry, the measurement of temperature, involves a wide range of technologies.
Help us honor the companies that have provided the most leadership in engineering
It has been a fascinating decade for all businesses, including manufacturers. We’ve seen the difficult supply chain issues brought on by the worldwide pandemic, along with a shortage of qualified workers and the strong reshoring trends in many industries. If nothing else, this helps to show how resilient manufacturers can be.
These companies represent the best and brightest, and they reflect the continued vision, integrity, and creativity of their design (and manufacturing) engineers.
We think they deserve recognition from you, too. Vote online for one or more of the companies listed through October.
FOLLOW THE WHOLE TEAM @DESIGNWORLD
EDITORIAL
VP, Editorial Director
Paul J. Heney pheney@wtwhmedia.com @wtwh_paulheney
Managing Editor Mike Santora msantora@wtwhmedia.com @dw_mikesantora
Executive Editor Lisa Eitel leitel@wtwhmedia.com @dw_lisaeitel
Senior Editor Miles Budimir mbudimir@wtwhmedia.com @dw_motion
Senior Editor Mary Gannon mgannon@wtwhmedia.com @dw_marygannon
Senior Editor Rachael Pasini rpasini@wtwhmedia.com @WTWH_Rachael
Associate Editor Heather Hall hhall@wtwhmedia.com @wtwh_heathhall
CREATIVE SERVICES
VP, Creative Director Matthew Claney mclaney@wtwhmedia.com @wtwh_designer
Art Director Allison Washko awashko@wtwhmedia.com
LLC 1111 Superior Ave. 26th Floor Cleveland, OH 44114
Ph: 888.543.2447
Director, Audience Development Bruce Sprague bsprague@wtwhmedia.com
WEB DEV / DIGITAL OPERATIONS
Web Development Manager B. David Miyares dmiyares@wtwhmedia.com @wtwh_webdave
Senior Digital Media Manager
Patrick Curran pcurran@wtwhmedia.com @wtwhseopatrick
Front End Developer Melissa Annand mannand@wtwhmedia.com
Software Engineer David Bozentka dbozentka@wtwhmedia.com
DIGITAL MARKETING
VP, Digital Marketing Virginia Goulding vgoulding@wtwhmedia.com @wtwh_virginia
Digital Marketing Manager Taylor Meade tmeade@wtwhmedia.com @WTWH_Taylor
Digital Marketing Coordinator Meagan Konvalin mkonvalin@wtwhmedia.com
Webinar Coordinator Emira Wininger ewininger@wtwhmedia.com
Webinar Coordinator Dan Santarelli dsantarelli@wtwhmedia.com
EVENTS
Events Manager Jen Osborne josborne@wtwhmedia.com @wtwh_jen
Events Manager Brittany Belko bbelko@wtwhmedia.com
Event Coordinator Alexis Ferenczy aferenczy@wtwhmedia.com
FINANCE
Controller Brian Korsberg bkorsberg@wtwhmedia.com
Accounts Receivable Specialist Jamila Milton jmilton@wtwhmedia.com
VIDEO SERVICES
Videographer Cole Kistler cole@wtwhmedia.com
PRODUCTION SERVICES
Customer Service Manager Stephanie Hulett shulett@wtwhmedia.com
Customer Service Representative Tracy Powers tpowers@wtwhmedia.com
Customer Service Representative JoAnn Martin jmartin@wtwhmedia.com
Customer Service Representative Renee Massey-Linston renee@wtwhmedia.com
Customer Service Representative Trinidy Longgood tlonggood@wtwhmedia.com
Digital Production Manager Reggie Hall rhall@wtwhmedia.com
Digital Production Specialist Nicole Johnson njohnson@wtwhmedia.com
Digital Design Manager Samantha King sking@wtwhmedia.com
Marketing Graphic Designer Hannah Bragg hbragg@wtwhmedia.com
Digital Production Specialist Elise Ondak eondak@wtwhmedia.com
HUMAN RESOURCES
Vice President of Human Resources Edith Tarter etarter@wtwhmedia.com
Image processing is developing rapidly, and smart solutions combining camera technology with artificial intelligence are on the rise. They hold great potential for tackling demanding tasks and the skilled worker shortage.
Global robotic integrator AWL developed an intelligent robotic depalletizer solution to efficiently process packages randomly arranged on a pallet. RODE, an acronym for RObotic DEpalletizer, has two Ensenso 3D cameras from IDS Imaging Development Systems to provide the required image data.
At DHL eCommerce in Rotterdam, RODE automatically destacks up to 800 parcels per hour and places
them on a corresponding sorting belt. The challenge is to pick parcels of different sizes and weights, with a maximum weight of 31.5 kg. RODE must independently recognize the position of the objects and decide which package to pick next. It then must determine the best gripping position and avoid collision with other parcels or the machine.
The two Ensenso X36 3D cameras provide 2D and 3D information on products on a pallet measuring 1,200 x 1,200 mm and a maximum height of 2,400 mm. The integrated image processing system processes this further and enables the depalletizer to identify each individual package and
determine the corresponding gripping position.
Each camera system consists of a projector unit and two GigE cameras with either 1.6 MP or 5 MP CMOS sensors. AWL opted for the 5 MP variant for its solution. Mounting and adjustment brackets, three lenses, and sync and patch cables for connecting the cameras to the projector unit are also included. The integrated FlexView2 technology ensures better spatial resolution and high robustness with dark or reflective surfaces. The 3D systems come assembled and precalibrated. However, an integrated setup wizard guides users through focusing and calibration setup. DW
AEROSPACE & MILITARY
Titanium alloys are a staple for aerospace components due to their high strength, light weight, high-temperature performance, and corrosion resistance. Bright Laser Technologies (BLT) has created a new titanium powder, Ti₂AlNb, which it believes has promise for large-scale manufacturing. Though the alloy’s poor room-temperature plasticity and thermal deformability create challenges in traditional manufacturing methods, additive manufacturing (AM) offers a new pathway.
BLT uses inert gas atomization technology and processing techniques to consistently mass produce the material while reducing satellite particles. The nominal chemical composition of BLT-Ti₂AlNb powder is Ti-22Al-25Nb, and the product specification is 15 to 53 μm. The new alloy exhibits low density and oxidation resistance at room and high temperatures and sustains extended use up to 900° C. After heat treatment, parts produced from the powder achieve a tensile strength of 250 to 270 MPa, yield strength of 140 to 160 MPa, and elongation of 38.8 to 42.8% at 900° C.
In recent years, Ti₂AlNb development has garnered significant global attention, yet successful production of Ti₂AlNb parts using AM technology and related research is still in its early stages. BLT believes its achievement in massproducing the high-quality powder will advance research into AM processes, microstructures, and the alloy’s properties and promote the large-scale engineering application of Ti₂AlNb parts. DW BLT www.xa-blt.com
STEELS
Materials of: ALLUMINUM and CORROSION RESISTANT STEEL
WHITTET-HIGGINS manufactures quality oriented, stocks abundantly and delivers quickly the best quality and largest array of adjustable, heavy thrust bearing, and torque load carrying retaining devices for bearing, power transmission and other industrial assemblies; and specialized tools for their careful assembly.
Visit our website–whittet-higgins.com–to peruse the many possibilities to improve your assemblies. Much technical detail delineated as well as 2D and 3D CAD models for engineering assistance. Call your local or a good distributor.
BXR Brakes
· Up to 480 in-lbs static
· Up to a 1.125'' bore
· 19 watts or less
· Produced for over 10 years
Our Innovative design features a very thin profile, reducing weight & saving space.
For more information:
Call: 800.533.1731
www.mikipulley-us.com
Energy recovery projects are widely adopted in Asia and Europe and are gaining traction in Latin America, where landfill space is scarce. WEG is participating in Brazil’s first power generation project using solid waste from the Barueri, Carapicuíba, and Santana de Parnaíba municipalities, part of the São Paulo Metropolitan Region. The project will help reduce environmental impact and convert waste into clean energy that can supply power to approximately 320,000 people.
WEG will supply a 20-MW turbogenerator set featuring a condensing steam turbine with reaction technology, turbo gearbox, and synchronous generator ST 41 line. The supply set also includes a hydraulic unit, control and protection panels, and services, such as installation,
commissioning, assisted startup and operation, operation training, and performance testing.
Led by the Orizon Group, construction of the Barueri Energy Recovery Power Plant is scheduled to take 30 months and start operations in January 2027. The solution provides a viable alternative for densely populated areas with limited landfill space. Besides being a sustainable solution, this project turns an environmental liability into clean energy, generating jobs and promoting regional development. DW
Manufacturers in every industry seek high-performance technology that allows them to respond strategically to the everchanging market. Emerson’s new Aventics XV pneumatic valves aim to equip those looking for an interoperable, flexible, and cost-effective valve platform. The new series is suitable for machine builders who operate globally, with universal threads and other features supporting regional standards and global availability.
The Series XV valves feature multiple interoperable valve sizes and higher flow rates in a compact design. The XV03 provides flow volumes of up to 350 liters per minute in normal conditions (NL/min), and the XV05, scheduled for release in October 2024, provides up to 880 NL/min.
All valves in this series use Aventics’ core technology and include metal threads, parallel wiring, aluminum base plates, and compact dimensions for easier production system integration. The valves use consistent interfaces and have wide connectivity from single wiring over parallel connections, such as D-Sub connectors. They also support leading fieldbus protocols, including Profinet, Ethernet/IP, EtherCAT, Powerlink, Modbus TCP, IO-Link, and AS-I, to simplify integration into machine control networks.
Series XV valves are also designed for easy commissioning. The Aventics online configurator supports the system layout and provides useful information, while system documentation in the design phase helps accelerate machine development. The aim is to help manufacturers boost productivity and allow them to offer products customized for specific markets and customer preferences. DW
Emerson www.emerson.com
EDITED BY MIKE SANTORA
Olympia Express has adopted software from the Siemens Xcelerator portfolio to help create innovations such as the newly launched Mina portable coffee press. Olympia Express
When Olympia Express needed to digitally transform the design and production of its world-renowned espresso machines, it reached out to Siemens Digital Industries Software. The company felt that its Xcelerator portfolio might be the right solution.
For more than 95 years, Olympia Express has designed and manufactured espresso machines with Swiss precision that have gained a reputation for robustness and longevity and have been called the best in the world. Schätti AG acquired the brand in 2011 and has since been designing and manufacturing Olympia Express products in Glarus, Switzerland, using Siemens’ Solid Edge software to build on the company’s legacy and find new avenues for innovation and market development.
Thomas Schätti, CEO of Olympia Express, explained, “When we took over the company, the previous owners had designed in 2D, so the data was very useful to us. The decision to switch to the Siemens Xcelerator software portfolio was driven by our need for precision and efficiency. Solid Edge allows us to create highly accurate 3D models that streamline our production process from design to manufacturing, saving time and resources to be on the top of our game. We remodeled all the parts of the machine in Solid Edge and made new models and spare parts. We started afresh and built a complete data engineering set. And since then, we have made various design iterations and improvements to the machines.”
The primary benefit of the 3D modeling is that it speeds up the design
process and reduces the number of physical prototypes — reducing development efforts by 50%. It also frees up resources for new innovation projects. Olympia Express’ engineering team can easily model and quickly 3D print a prototype to get a better feel of the components in various materials.
The engineering team also uses visualization capabilities for internal communications. Considering that they often need to service Cremina machines that are 50 years old, the exploded view capabilities are fundamental. These allow the engineering team to provide documentation for assembly and service, making it easier to see which spare parts are needed and how to replace them.
Olympia Express manages design and engineering data in Teamcenter
software for product lifecycle management, which enables secure control of engineering data revision and efficient and managed design review. The company also uses NX CAM software on the shop floor to prepare its high-accuracy components for manufacture. As Schätti said, “To be on the top of our game, on the shop floor we use NX CAM to guarantee the highest standards of production, allowing us to produce the components of the coffee machine in excellent quality. We rely on Teamcenter to manage our product data and enhance collaboration across our teams, keeping all design data in one place, including data of our vintage Olympia Express.”
While the Olympia Express brand and its Cremina espresso machines have achieved legendary status within the coffee-loving community, the company is not content to rest on its name and reputation alone. It has used Solid Edge to help develop Mina, a new portable espresso machine that only needs access to boiling water and
fresh grounds to achieve the highquality beverage wherever they need it. Solid Edge’s 3D modeling tools have enabled the team to efficiently reuse its knowledge and 3D data and create a brand-new product category for the company, launching at World of Coffee this month.
Despite its name, Olympia Express places itself in the “slow foods” revolution. As Schätti said, “Our products make coffee to the quality of an Italian coffee bar with a machine that is just a fraction of the size and cost of a professional machine — the key is that they are built like a professional machine, with the same care, quality materials, and careful design. We build our machines for a small eternity — they are designed and built to last multiple lifetimes and their use should be a celebration of making an outstanding coffee.” DW
Siemens
sw.siemens.com
With Interpower® you don’t have to stress about power cords. Interpower North American and international cords and cord sets provide the correct AC power for country-specific customers to safely connect to the mains power. Interpower manufactures state-of-the-art electrical cord sets for global markets with 1-week U.S. lead-times.
Interpower cords and components are manufactured in accordance with Interpower’s product quality plan: hipot testing, continuity testing, and ground testing with inspections after each stage of the manufacturing process. And we don’t cut corners when it comes to raw materials.
®
Toll-Free Phone: (800) 662-2290
E-mail: info@interpower.com
Business Hours: 7 a.m.–5 p.m. CST
EDITED BY MIKE SANTORA
Here’s the scene: a large oil and gas exploration and production company operates its own secure network with long-range communication towers spread over hundreds of square miles throughout Texas. The company had been using commercial-grade managed switches for over a decade to manage traffic between local area networks (LANs) and backhaul (highcapacity) network connections. For a time, it wasn’t a problem. But this was Texas.
Summer temperatures frequently reached well over 100° F, and the company experienced frequent failures with its existing switches. The company needed a more robust solution that could withstand extreme environmental conditions. It also needed a solution that its technicians could swap out quickly and easily, to avoid production delays and stoppages that could harm profitability.
Red Lion and Automated Dynamics, Corp (ADC) believed its N-Tron Series NT5000 Gigabit Managed Switches could be the solution. They are designed for ease of use, security, and reliability. Its features simplify installation and setup via a configuration wizard, while an industry-ready, rugged design ensures smooth operation in harsh environments.
The company engaged Red Lion to demonstrate the N-Tron Series NT5000 Gigabit Managed Switch features and interface. The company ordered two NT5000 Gigabit Managed Layer 2 Ethernet Switches immediately. After a few weeks of testing, they ordered an additional 150 switches.
The N-Tron Series NT5000 Gigabit Managed Switches are designed for ease of use, security, and reliability. Its features make installation and setup easy via a configuration wizard, while an industryready, rugged design ensures smooth operation in harsh environments.
Interpower North American and international cords and cord sets provide the correct AC power to allow country-specific customers to safely connect to their mains power without reconfiguration. Interpower manufactures state-of-the-art electrical cord sets for global markets with 1-week U.S. lead-times.
Interpower cords and components are manufactured in accordance with Interpower’s product quality plan: hipot testing, continuity testing, and ground testing with inspections after each stage of the manufacturing process. Cords are also rigorously tested at Interpower’s testing facility in Ames, Iowa.
Toll-Free Phone: (800) 662-2290
E-mail: info@interpower.com
Business Hours: 7 a.m.–5 p.m. CST Order Online! www.interpower.com
«
«
«
«
The NT5000 is easy for end users to set up, requires little training, and has a simple learning curve. The configuration wizard takes technicians through basic steps to establish basic settings and get switches
In the event of any communication loss, the NT5000 enables the company to reset switches themselves, remotely, and establish new credentials in-house. This contrasts with other switches which need to be retrieved from the field and returned to the factory for reflashing, draining resources and interrupting production as a
Lead time was also a deciding factor. Red Lion built and shipped the products within just four weeks to meet company’s demand.
Since installing N-Tron Series NT5000 managed switches, the company has experienced no communication interruptions or failures, with no associated loss of production or profitability. The NT5000 is now the company’s specification for all managed switches in its network. The company plans to order more NT5000 switches.
Clay Cearley of ADC spoke with company leaders about the NT5000 implementation. “They’ve fully standardized on this product from Red Lion,” said Cearley. “This is the switch they’re going to use from now on.” DW
Registration is open! Whether you're interested in the latest developments in clean energy, automobile technology, or power electronics, ECCE 2024 has something for everyone With engaging technical sessions, insightful keynote speakers, and unparalleled networking opportunities, this is an event that you won't want to miss
Showcase your company/ university to conference attendees (2400+ people expected to attend)
Participate in the Career Fair:
Hire the best and newest students in the engineering field (300+ expected to attend)
$500 off for new exhibitors Booths starting at $2700
These accomplished leaders will share their wealth of knowledge and experience in topics like wide power systems, electric aircraft, electrification technoglogies and power semi-conductors.
Prof Dushan Boroyevich, Virginia
Tech – CPES
Ms Bezos-O’Connor, NASA
Mr Matthew Potter, John Deere
Intelligent Solutions Group
Dr Olga Spahn, ARPA-E
Motion Control
Pallet conveyors are hardly a new development, but the increasing speed and precision of these systems have made them the go-to conveyance option for a growing number of industries that are trying to boost throughput to keep up with demand.
Small electronics is one market that has shown rising demand for pallet conveyors as their technology continues to improve, with both well-established and recently developed features that benefit assembly lines.
Unitized transportation of discrete product
A key draw of pallet conveyors in the small electronics industry comes from
the fundamentals of their design. Unlike a standard belted conveyor, which runs all items on a line at the same speed, pallet conveyors position each piece on its own platform, which can stop or start with precision. The belt or rollers underneath each platform continue moving, allowing individual pieces to stay at a workstation without disrupting the entire line.
This model is particularly desirable for small electronic assembly, which requires intricate steps and attention to detail. Moving each piece at its own pace ensures that no employees must rush through assembly or
inspection at their stations, preventing mistakes common in a more highstress environment.
As this technology improves, these systems become even more individualized by product. One system available for small electronics applications operates similarly to a monorail system with pallets that can stop independently instead of requiring designated stopping spots. Sensors in the front of each platform detect any obstacles, whether a hand, tool, or other shuttle, in its way and wait until the item is moved before continuing. These smarter platforms eliminate the need for designated stop and start spaces between each workstation to hold oncoming pallets,
condensing the machine’s physical and energy footprint.
Palletized conveyors with robotic compatibility
In addition to working well with products, palletized conveyor systems integrate seamlessly with larger automation systems, including robotic cells. The shift to automation for assembly lines has grown substantially over the past few years, with lingering staffing shortages impacting worker availability. This demand is even higher for small electronics applications due to the increased finesse and speed that robots can reach for fine-detail work compared to their human counterparts. The one drawback of automated assembly workers is the increased need for consistency. Unlike human employees who can see when a piece
a set task without any external input. Many robotic cells are now being equipped with sophisticated vision systems to accommodate imperfections in product placement. However, this technology is relatively new, and is expensive to implement.
While flat belts need suitable placement of the objects and exact stop times to line them up for robotic workers without advanced vision systems, pallet conveyance can be engineered to hold each item in place with programmed stop points at suitable positions. The security of a pallet system also stops the items from shifting due to any sudden stops and starts in the line to more improve accuracy.
Low total cost of ownership with palletized conveyors
Not only does the single-product format of a pallet conveyor lock in product alignment, but it also protects the products themselves. Stops and starts on a conveyor belt can cause unsecured products to slide around and present a risk of damage.
Pallet conveyors
reduce the number of stops and starts and hold the product more firmly in place to prevent the shifts in momentum from impacting. These two elements work together reduce product losses and drive ROI for the line.
The cost savings over time are even higher with the monorailstyle system. Instead of needing a separate pallet for each component to be released one at a time into the station, the monorail style system can bring multiple components at one time, increasing throughput and profitability. This unit also has fewer pneumatic components and controls, reducing the cost of operation and maintenance. Commonality of parts and modules makes future expansions and modifications easier by reducing the number of system components needed for any additions to the line.
Other conveyor considerations
Specific pallet conveyor systems offer some additional benefits that apply to unique situations. Small electronics manufacturers often need equipment and conveyors that are compatible with electrostatic discharge (ESD) requirements. Some applications also need pallets that can handle clean room environments.
Finding the right solution for each application requires thorough consideration of these and other features that may dictate the conveyor’s requirements. Line operators should also consider the additional components to the line, such as robotics, feeders, and other machines that can impact the complete system. Integrating these important components into the machine design ensures that a pallet conveyor’s benefits can be fully realized for small electronics applications. DW
To meet the complex factory automation challenges of tomorrow, linear motion systems are evolving to become quicker, more economical, and more sustainable.
LINEAR motion components are central to the functioning of a host of machines and mechatronic systems. They enable reliable guidance, precise positioning, and advanced handling capabilities. Such features are key for a number of applications including machine tools, semiconductor manufacturing, and battery production and consumer goods, among others.
The pre-installed operating software for the Smart Function Kit for Handling mechatronic subsystem guides users quickly and intuitively through the commissioning process.
Bosch Rexroth AG
Applications such as these rely increasingly on factory automation, which is developing faster than ever before, and linear motion technology must keep pace if it is to meet future challenges in the best way possible. But what does this actually mean? The experts at Bosch Rexroth have identified three key areas of development for future-proof linear motion technology: Firstly, mechanical engineering and production companies should be able to implement a wide range of applications more quickly. Secondly, they should focus on efficient, low-maintenance products with a long service life. Finally, the organization should be focused on a high level of flexibility as the requirements for the Factory of the Future are consistently changing.
Digital transformation is a new and far-reaching development saving designers and manufacturers both time and money. In engineering, digital processes fundamentally simplify the design of linear motion technology products, reducing the time to market. For example, the digital design and
configuration of linear robots in a seamlessly connected tool chain streamlines the process and prevents input errors through plausibility checks. By using a tool that guides users to products and configurations that best fit their design needs, they can be sure the products have the correct size and speed, and can be used in the intended environment. Bosch Rexroth has made this possible with the LinSelect sizing tool. The user simply enters a few parameters, including load size, orientation, speed, travel, accuracy requirement, the environment and duty cycle, and the tool displays a list of results with clear product recommendations according to specified criteria.
After selection, the project can be visualized in 3D with the online configurator and all associated products can be purchased through the seamlessly connected online shop.
Quality online support for complex industrial goods saves a great deal of time during day-to-day business. The selector for electromechanical cylinders demonstrates how application-specific solutions can be easily selected using a digital process. When dealing with small electronics, the solutions are drastically
different compared to larger items, like automobiles, for assembly line testing. Narrowing the possible EMCs required for an application reduces the ancillary component choices and the overall solution complexity. The web-based tool covers the entire process, from selection and configuration to ordering. Direct dynamic feedback, plausibility checks, and intuitive graphical user guidance make the system easier to operate and significantly increase transparency, time savings, and userfriendliness in engineering.
The development work also focuses on software solutions that allow mechanical engineering companies and users to optimize commissioning and programming, two processes that are both time consuming and costly. An example is the Smart Function Kits, modular subsystems for pressing and joining, handling, or dispensing. They feature a commissioning wizard which reduces the work involved by up to 80% by automatically matching the drive, module, and motor parameters, thus eliminating input errors. Process creation is also carried out using the pre-installed operating software. Prepared function blocks are simply sequenced and parameterized visually
via drag-and-drop — without the need for programming knowledge. Connecting to a higher-level control system can also be done quickly with the help of ready-made programming modules.
Linear motion technology components and smart mechatronic solutions boost production when manufacturers concentrate on developing a high level of performance in a small space.
For instance, long relubrication intervals can reduce operating costs and increase efficiency. Through continuous material research and product improvements, for example, Bosch Rexroth has been able to increase the service life of ball rail systems without relubrication up to 20,000 km. Ball-screw assemblies manage up to 200 million revolutions with factory lubrication, which in many cases equates to lifelong lubrication. Given the numerous linear motion technology components that can be found in virtually every machine in a factory, such components offer great potential for decreasing costs and maintenance time over the long term.
What’s more, in modern factory automation, a product is considered future-proof when it demonstrates flexibility and sustainability. Longer lubrication intervals not only reduce operating costs — they conserve resources too. Pneumatic actuators can be replaced by electromechanical cylinders which consume significantly
less energy. Bosch Rexroth's linear guides are designed so that the runner block and rail can be replaced independently of each other, saving money and materials. Linear motion holds the potential to drastically expand automation possibilities. By combining compact integrated measuring systems with linear motors for direct position detection, linear motion technology gives manufacturing lines the sensitivity of the human hand with the precision of robotics.
Linear motion technology has by no means reached the end of its development. There are opportunities for application in a host of different industries including battery, assembly, machine tools, warehouse automation, medical, and aerospace. After all, the current challenges in factory automation are driving innovation and continuous improvements. Solutions which are geared to market requirements and implement new ideas in a way that is durable and easy to use are a real win for mechanical engineering, users, and climate protection. DW
Bosch Rexroth www.boschrexroth.com
The Smart Flex Effector tactile compensation module gives industrial robots almost human sensitivity, redefining the boundaries of factory automation.
Bosch Rexroth AG
Elevate your Industry 4.0 projects with OKW’s IIoT enclosures! Our versatile range, designed for sensors and smart devices, ensures robust protection and seamless communication. Discover mobile, wearable, and wall-mounted options that are waterproof, dustproof, and ready for any environment. Upgrade to OKW – where innovation meets reliability.
Request a sample today!
Temperatureisthemostcommonlymeasuredphysical quantity.Thermometry,themeasurementoftemperature, involvesawiderangeoftechnologies.
JEFF SHEPARD
ge from maintaining a comfortable and safe environment for people to industrial processes operating at over 3,000 °C and quantum computing operating at near absolute zero.
This FAQ reviews some of the more common ways to measure temperature.
Mercury thermometers were once the most common thermometry instrument. However, except for some specialized applications, organic materials like industrial alcohols have displaced mercury. Industrial fluid-expansion thermometers consist of a measurement probe connected by a stem to a pressure bulb and display (Figure 1). The display contains a bourdon tube measuring system that’s inexpensive and provides good repeatability. These thermometers don’t require a power source, simplifying installation.
Thermocouples use two dissimilar metals to form a junction where an induced voltage occurs in response to changes in temperature because of the Seebeck effect. Thermocouples don’t usually have a linear response to temperature changes and require active circuitry to translate
the voltage changes into a temperature reading. Like a fluid-expansion thermometer, thermocouples don’t need an external power source and are relatively simple to install but have limited accuracy. Thermocouples can measure wider temperature ranges than liquid-expansion devices. They can be packaged for use in high-temperature applications like kilns and for challenging environments like immersion in acids and other aggressive chemicals.
Two technologies are used to make resistance temperature devices (RTDs), metals, and thermistors. Metallic RTDs consist of fine wires made using platinum (Pt), nickel (Ni), or copper (Cu) that have a known resistance/temperature (r/t) relationship. Platinum RTDs are most common in industrial electronics since they have the most stable r/t relationship over the largest temperature range (from 0 to 500 °C) and they are the most environmentally rugged. Thermocouples and Pt RTDs have been developed to monitor cryogenic temperatures in quantum computers, high-energy physics labs, and similar applications.
Thermistors are semiconductor devices whose resistance changes with temperature. There are two basic types of thermistors, negative temperature
• Available Sizes Flange and Cylindrical Nuts
• Accuracy Class 5, 7, & 10
• Machined Journals
• State of the Art Metrology and Inspection
• Integrated Ball Screw Motors
- NEMA 08, 11, 14, 17, & 23
• Applications
- Medical Lab Automation
- Optical Sensor Adjustments
- Pick and Place
- Packing Line Push Systems
- Measurement Systems
- Mechanical Automation
• Customization Available
coefficient (NTC) and positive temperature coefficient (PTC) devices. For NTCs, an increase in temperature results in a resistance decrease, and for PTCs, when the temperature increases, so does the resistance. NTCs and PTCs are used as temperature sensors in various applications and for temperature regulation in industrial consumer, medical, and other equipment. NTCs are also used to provide inrush current limiting in power conversion applications, while PTCs are used to provide resettable overcurrent protection in electronic systems.
Infrared (IR) temperature sensors are non-contact devices. They detect IR radiation coming from the item being monitored. IR detectors can provide spot measurements of a precise location or can be used in a matrix to provide a snapshot of the temperatures over a larger area. As a non-contact technology, IR temperature sensors can be used remotely from the item being monitored and can also be used to
1: Fluid-expansion thermometers are used in some industrial applications.
monitor high temperatures over 3,000 °C (Figure 2).
As the name implies, bimetallic temperature sensors use two metals. The metals have different thermal coefficients of expansion, and when strips of the two metals are bonded together, the structure bends in response to temperature changes. Bimetallic temperature sensors are robust, low-cost, and don’t require a power source. However, they usually have a limited operating temperature range and are not suited for measuring
very low temperatures. They can also require frequent recalibration, especially in high shock and vibration applications.
Change-of-state temperature sensors are based on materials like certain lacquers and other marker materials, pellets, and liquid crystals that experience a change in appearance at a predetermined temperature. Sensors based on lacquers, markers, and pellets experience an irreversible change, so the operator does not need to continually monitor the equipment. They are used for monitoring spot temperatures on industrial equipment or monitoring the temperature of materials in transit and they alert operators if a trigger temperature has been reached. Liquid-crystal-based temperature measuring strips can be designed to monitor a specific temperature range of interest and consist of a series of bars that enable the temperature to be estimated, not precisely measured (Figure 3).
2. IR temperature sensors can remotely monitor temperatures into the thousands of degrees C.
Instruments
Figure 3: These liquid-crystal monitoring strips provide reliable and low-cost temperature estimates.
Lotus Transfer Press Solutions
Summary
As shown, many technologies have been developed for measuring and monitoring temperature. They are used across various applications from consumer devices to industrial systems and quantum computers. Some passive devices have been developed to monitor the temperature of materials like foods and medicines in transit to ensure they don’t exceed safe storage temperatures. DW
References
• 7 Basic Types of Temperature Measuring Sensors, Wastewater Digest
• Component temperature measurement, XP Power
• Introduction to Temperature Measurement, Omega Engineering
• Liquid expansion – what does this mean & why is it used? Brannan
• Measuring Temperatures Precisely, HBK
• Resistance Temperature Sensors for High Energy Physics Applications, Lake Shore Cryotronics
A Tesla navigates a winding mountain road, showcasing advanced EV drivetrain technology for optimal handling and performance in diverse driving conditions.
Aharon Etengoff • Contributor
Although the terms powertrain and drivetrain are often used interchangeably, both are distinct and support their own set of functions.
This article discusses the role of each in the context of electric vehicles (EVs), lists their key components, and explains how they work together. It also highlights primary design considerations and previews potential advancements.
Powertrain: The core of EV propulsion
Responsible for managing and delivering electrical power, the EV powertrain comprises an integrated system of components that transform electrical energy into mechanical power. Specifically, electric motors create magnetic fields in stator windings to induce rotor rotation for propulsion. These motors also facilitate regenerative braking, reversing their function to convert kinetic energy back into electrical energy.
Battery traction packs are another essential powertrain component. These packs contain multiple lithiumion cells and embedded battery management systems (BMS) that regulate regenerative braking power
while ensuring optimal temperature, voltage, and capacity.
EV powertrains also include:
• Vehicle control unit (VCU): Often considered the “brain” of EV powertrains, the VCU oversees operations. It processes data from various sensors and systems, including the BMS and motor controllers, and regulates advanced driving features such as regenerative braking and energy optimization.
• Transmission: Many EVs employ a single-speed design with a fixed gear ratio, boosting energy efficiency by reducing mechanical complexity. In some EVs, electric motors drive the wheels directly, eliminating the need for traditional transmissions.
• Power electronics: These components manage the flow of electrical energy with inverters and converters — transforming dc from the battery into ac for the motor and vice versa during regenerative braking.
• Thermal management systems: Essential for maintaining optimal operating temperatures, these
systems employ liquid cooling circuits, heat exchangers, and advanced sensors to dissipate heat and prevent thermal runaway.
Drivetrain: Translating power into motion
The EV drivetrain efficiently transfers power from electric motors to the vehicle’s wheels. The transmission, a crucial component interfacing with the drivetrain and powertrain, optimally distributes torque. Specifically, differential gearsets within the drivetrain rotate each wheel at varying speeds — dynamically adjusting torque distribution to match wheel load and road conditions. EV drive shafts, connected directly to the differential gearsets, transmit optimized torque from the transmission to the wheels. This configuration ensures efficient power delivery and maximizes wheel performance on wet, slippery, or uneven roads.
EV axles, another important drivetrain component, bear the vehicle’s weight and facilitate wheel rotation. These axles maintain precise wheel alignment to improve traction and bolster responsive handling. In advanced EV models, axles might
include specialized components such as limited-slip differentials or torquevectoring systems.
Additionally, some EVs integrate specialized hub motors directly into each wheel, facilitating precise torque control and improved maneuverability.
Achieving optimal EV performance requires a comprehensive design approach that seamlessly integrates powertrain and drivetrain systems. Synchronization is essential, as powertrain motor control and energy management directly impact the drivetrain’s ability to efficiently manage handling, agility, and responsiveness.
Many EVs employ advanced control algorithms to match motor power output with torque requirements to ensure maximum efficiency and performance.
Effective thermal management systems are also essential for EV powertrains and drivetrains. These systems regulate operating temperatures and prevent component degradation with sophisticated cooling solutions, predictive algorithms, and innovative heat-shielding materials. Additionally, integrated thermal management helps maintain optimal performance, extend the lifespan of EV components, and ensure safety in high-temperature environments.
Future EV powertrains will likely offer more efficient energy generation and management capabilities. Emerging technologies such as solid-state batteries promise higher energy densities, faster charging options, and extended driving ranges. Power electronic advancements, including more sophisticated inverters and energy management systems, will further optimize the conversion and distribution of electrical power.
FEATURES AND BENEFITS
Controlled Self-Healing Property
Custom Designs (Mechanical/Electrical)
Alternative to Electrolytic, Mica, Film Foil & Ceramic
Total Safety, Reliability & Soft End of Lifetime Due to Controlled Self-Healing
Dry Solution, No Drying Out
Standard Solution
TYPICAL APPLICATIONS
DC-Link Capacitor in EV/HEV
Select Motor Drives
Renewable Energy (Wind, Solar, Power Grid)
Power Electronics That Need High Reliability
WBG Technology
Similarly, upcoming iterations of EV drivetrains will likely see substantial improvements in component design and operational efficiency. Advancements in materials science, for example, accelerate the development of lighter and more reliable drivetrain components, helping to reduce energy loss and bolster vehicle efficiency.
Innovations such as enhanced electric torque vectoring — precisely distributing power to each wheel — will improve control and handling, especially in all-wheel-drive systems. Moreover, new regenerative braking systems will capture and convert more kinetic energy.
Concurrently, EV engineers are adopting an increasingly comprehensive design approach to powertrain and drivetrain integration. With the advent of sophisticated
An overview of EV powertrain architecture, detailing components such as the traction motor, inverter, BMS, and power converters.
AI-driven sensors and machine learning algorithms, EV transmissions can dynamically and precisely adjust power distribution for various driving conditions. More seamless powertrain-drivetrain integration will extend battery life and bolster performance while paving the way for fully autonomous driving capabilities.
Summary
Although operationally integrated, EV powertrains and drivetrains are separate systems supporting distinct functions. The powertrain is responsible for managing and delivering electrical power, and it’s comprised of an integrated system of components that transform electrical energy into mechanical power. At the same time, the drivetrain transfers power from electric motors to the vehicle’s wheels.
References:
• Understanding the Powertrain of an Electric Vehicle, Power Electronics News
• An Overview of the Electric Vehicle (EV) Drivetrain System, Datamyte
• The Vital Roles of EV Powertrain Components, Exro
• Getting to the Heart of EVs: A close-up look at the electric drivetrain, Innovative Automation
Simon Baggott • CMO | Q5D
Vehicles are becoming increasingly reliant on electronics. Electric vehicles (EVs), in particular, are packed with sensors and actuators that regulate and protect every aspect of the drivetrain.
A vehicle’s wiring harness — which connects all these electrical and electronic circuits — is one of the largest and heaviest components purchased by EV makers. It’s also the last barrier to fully automated manufacturing and the benefits that it could bring.
Wire harnesses are safety-critical vehicle components, particularly in
ALL-ELECTRIC VEHICLE
AFDC.ENERGY.GOV
EVs with advanced driver-assistance systems (ADAS) and autonomous driving technologies. They also feed signals and power for driver convenience functions, such as heated seats, navigation, and infotainment and communications systems. However, there are problems arising from manual wire harness production, as follows:
• Manual processing: Typically produced by hand, harnesses are increasingly complex and costly to manufacture.
• Supply-chain complexities: Production is labor intensive, so
most harnesses are produced in countries with lower labor costs. Final assembly, however, typically occurs thousands of miles away from production, adding significant transportation costs, complexity, and risk to the supply chain. For example, many wire harnesses for the European market were made in Ukraine, which is suffering a devastated supply chain, throttling overall vehicle sales.
• Quality testing: Every circuit must be tested in every manually produced wire harness because the process is so prone to errors.
EV drivetrain parts contain hundreds of temperature, pressure, position, speed, current, voltage, gas concentration, level, humidity, and speed sensors — all of which require electrical connectivity.
Automated wiring would likely only require sample testing because it achieves more consistent quality.
• Over-ordering: Quality issues are so common that some vehicle maker executives have stated they need to “over-order” to ensure sufficient inventory of acceptable quality. Each harness costs approximately $1,000 to $2,000 for a typical mid-range EV, so every order has a significant loss (and waste).
• Over-specifying: Every conventional harness wire must use insulated wires to prevent short circuits, adding insulation weight and cost. Also, wires must be heavier than the electrical requirement demands to withstand the physical pressures encountered during assembly and vehicle use. Adding unnecessary weight to an EV compromises its range, and a shorter range means consumers expect to pay less for vehicles.
• Assembly rework: Quality issues often occur when harnesses are manually bent and twisted during the final assembly.
• Repairs and recalls: Warranty claims are costly, and vehicle recalls are even more expensive. In 2022, CNET reported that Nissan had recalled nearly 700,000 of its 2014-2016 Rogue SUVs over fire risk. A poorly sealed wiring connector caused the issue. That same year, the US National Highway Traffic Safety Administration (NHTSA) cited that electrical system faults and failures accounted for 20% of all vehicle recalls.
• Reputation: The cost to a vehicle’s brand reputation when a recall occurs is incalculable but can run into the tens of millions of dollars.
KOA Speer is your ideal passive component partner. We offer a diverse and expanding family of surface mount and leaded resistors, as well as our Quality 1st mandate to deliver unmatched service and product quality… demonstrated by our 99%+ on-time performance despite shipping billions of resistors every month! Don’t Roll the Dice on your passives, count on KOA Speer!
Use fewer resistors for high voltage pplications - working voltage up to 3000 VDC
Heat shock resistance & anti-sulfur available
Given the above concerns, research financed by the European Regional Development Fund and published in March 2023 concluded that “automation in the wiring harness industry still constitutes the biggest deficiency. Despite research findings and patents, to our knowledge, none of these solutions have been implemented in the field, and the state-of-the-art manufacturing process is still highly labor-intensive.”
Overcoming production challenges
There have been many attempts to address wire harness challenges. Some manufacturers have attempted to automate wire harness production, but with limitations. Most automation
This five-axis additive manufacturing cell can automatically and securely add bare or insulated conductors into components with simple or complex 3D shapes.
SENSORS: Inductive and Capacitive Proximity Sensors • Photoelectric Sensors • Level Sensors • Ultrasonic Sensors • Magnetic Sensors • Limit Switches • Interlocks
SWITCHES: Solid State Relays & Contactors • Soft Starters • IEC Contactors & Overloads • Switching Power Supplies • Miniature Circuit Breakers • Electromechanical Relays
CARLO GAVAZZI has the solution for your application needs, whether it’s our industry leading solid state relays & contactors, energy meters, monitoring relays, soft starters or sensors, available with or without IO-Link.
CONTROLS: AC and DC Energy Meters and Transducers • Universal Web Platform • CurrentVoltage- and 3-Phase Monitoring Relays • Current Transformers • Timers • Panel Meters
Contact us today, and one of our field sales representatives will show you why we are one of the fastest growing automation companies worldwide. We’ll even provide a free evaluation sample to qualified OEMs.
machines simply bundle wires together and, in some instances, affix connectors to the ends of the wires. Inevitably, there’s still manual work involved, such as visually checking the terminations, fixing the bundles together to make the complete harness, and ensuring that wires do not become entangled or otherwise damaged in the process.
Additionally, conventional automation has yet to solve concerns about weight, fragility, or supply chain logistics. However, a new hybrid additive manufacturing and automation process offers a higher degree of automation and reliability. It uses an “electrical function automation” robot cell, which enables the full or partial replacement of traditional wire harnesses. It’s eliminating, or at least mitigating, the need for manual processes — adding electrical conductors to EV battery packs, infotainment systems, and more.
A precision five-axis robot with interchangeable tools can add 3D polymeric features to metal, ceramic, or polymer surfaces. It can handle complex shapes, add bare or insulated wires, and attach electrical connectors to make the components functional. The robot can also route wires with conductors up to 3mm in diameter, approximately 13 AWG. This means each conductor can carry over 20 amps, sufficient for low-level signals and functions that include powering relays or fans.
Anchoring each wire to a substrate is fast, cost-effective, and flexible. The substrate can also be the component. For example, it can be a battery pack or a part designed to carry the wiring for attachment to the component. It can be rigid or flexible. Because each wire is individually secured, it might not require insulation,
Bare or insulated wires with conductors up to 3mm in diameter can be automatically secured onto complex 3D components.
saving cost and weight. Because it’s securely positioned, it’s also less prone to environmental and mechanical damage.
The finished products or components with integrated wiring also lend themselves to robotic final assembly. It reduces labor and supply chain risks by co-locating the integration of electrical conductors and components with the vehicles’ final assembly.
Automating wire harness production in EV manufacturing can reduce the size and weight of sub-assemblies and their parts, enabling onshore manufacturing. It can also increase vehicle reliability, cut after-sales warranty and recall costs, and protect the value of the brands in which automakers invest so much to build.
The five-axis robotic cells described here are expected to be integrated into EV manufacturing lines within the next 12 to 18 months. Who will take pole position, we wonder? EV
Ross Feng • General Manager • Viasion Technology Co. Ltd.
As technology progresses, vehicles are gradually transitioning from fuel to electric power, requiring the integration of advanced electrical systems to ensure full functionality. However, these advancements bring new challenges in maintaining electric vehicle (EV) reliability on the roads and over long distances.
This article will examine the obstacles that high-frequency printed circuit boards (PCBs) encounter in EV applications and the strategies to overcome them.
The role of PCBs PCBs play a vital role in EVs because they serve as the backbone for various electronic components and modules, including:
• Powering up the powertrain – An EV’s motor, controller, and battery rely on complex highfrequency PCBs whose durability and reliability directly impact the vehicle’s longevity and efficacy.
• Overseeing the battery management systems – A dedicated high-frequency PCB powers an EV’s battery pack. The PCB monitors the battery’s health and state of charge and can control the temperature.
• Ensuring reliable infotainment and internet connectivity –EVs are more than a means of transportation; they’re also mobile tech hubs. A high-density interconnect PCB is integrated into an EV to facilitate high-speed data transfer and enable entertainment modules inside the vehicle.
• Managing the recharging infrastructure – High-frequency PCBs manage a vehicle’s charging
infrastructure. They’re integral to the onboard chargers that take electricity from the power grid to recharge the car. The reliability and functionality of the onboard chargers are highly dependent on the quality of PCBs.
Every challenge has a solution
Integrating high-frequency PCBs in EVs presents challenges that may include the following:
Mechanical stress. Road surfaces are rarely consistent. Drivers may experience bumps or different vibrations due to uneven pavement. This may present an issue for EVs, as repeated mechanical stress and vibration can damage critical components. The ideal solution is to strengthen the PCBs using durable but suitable materials and vibration fatigue analysis.
Vibration fatigue analysis studies movements and vibrations and, in this case, how they can affect the PCB. This analysis includes identifying key points where a PCB can fail or crack, allowing designers and engineers to apply modifications or materials that ensure this component is more durable and shock-proof.
Heat dissipation and management. EVs generate a lot of heat, which can reduce their reliability and lifespan. So, they require a sufficient thermal management system to prevent overheating.
To attain optimal temperatures, PCB designers must add thermal management mechanisms, such as thermal vias, heat sinks, and heat pipes. By adding these components, an EV’s high-frequency PCB can maintain safe temperature levels, prolonging the operational lifespan and reliability of the vehicle.
Exposure to electromagnetic waves. One challenge that high-frequency PCBs face in EV applications is electromagnetic interference caused by high-powered or sensitive electronic parts being close to each other. One consequence is that electromagnetic waves can disrupt an EV’s operations, which can be detrimental to the safety of the passengers.
The solution to this issue is to add sufficient shielding, ground plane separation, and filtering to a PCB to weaken the effects of electromagnetic waves that can interfere with the vehicle’s functionality.
Spacing concerns. PCB designers are often challenged to find adequate space to safely fit components in EVs. Fortunately, there’s a simple solution: employ miniaturization techniques on the PCB design and add multiple functions on the circuit boards.
Miniaturization and multi-functionalization of the PCBs allow them to become more compact and lightweight, making it easier to fit into an EV’s electrical system.
Handling powerful electric currents. High-frequency PCBs must properly handle strong electric currents during vehicle operation, which carry a lot of heat that can build up inside the electrical systems. If left unchecked, the accumulated heat from the flowing currents can negatively alter EV performance and lifespan.
To address this concern, heavy copper and other advanced materials that can withstand strong currents are used on the printed circuit board — making it better at safely carrying electrical currents. Designers must also apply optimal layouts and heat dissipation mechanisms to ensure flowing electric currents are manageable.
High-frequency PCBs present challenges when used in EV applications. It’s imperative to address issues, such as thermal management, electromagnetic interference, space limitations, and electric currents. Fortunately, reliable solutions can effectively mitigate risks like overheating and reduced lifespan. EV
Viking Tech America Corporation is a manufacturer of passive components, including resistors, inductors, capacitors, and supercapacitors. As a global leader in thin film production, we support many ODM and OEM customers with high-reliability components that meet the highest standards such as AR..A Series
AR..A Series Benefits
• Available in sizes from 0201 to 2512.
• Tight tolerances of 0.01% to 0.1% for precision in critical designs.
• Low TCRs from 5ppm to 50ppm.
• Resistance range of 10 to 1MO.
• Suitable for applications in automotive applications, medical devices, testing equipment, and communication devices.
Viking Tech America Corporation
4 Executive Circle Ste 140 Irvine, CA 92614
+949-398-5228
sales@vikingamerica.com www.vikingamerica.com
FROM repetitive stress injuries and extreme temperatures to forklift collisions, warehouses have always been hazardous environments for human workers. Robots and advanced software can benefit warehouse safety, according to Locus Robotics.
Spikes in retail and e-commerce activity, such as Amazon Prime Day, are a “major cause” of employee injuries, according to a U.S. Senate interim report.
Labor union and regulatory scrutiny join other challenges for warehouse operators, including insurance claims, recruitment and retention, damaged goods, and global competition.
“Some say that robots are replacing people, but what we’re actually doing is adding co-workers,” said Kait Peterson, vice president of product marketing at Locus Robotics. “We did a study in France because the European market is very, very conscientious about worker health and safety. We wanted to see how our robots complied with European labor and ergonomics regulations, and they came out with flying colors.”
“Our customer Boots in the U.K. has seen about a 77% reduction in workplace injuries since launching LocusBots,” said Kary Zate, senior director of marketing communications at Locus Robotics.
Introducing a new series of ultra-lightweight gear units featuring a newly engineered lightweight structure with an ultra-compact shape. Ideal for use on end of arm axes for small industrial and collaborative robots, the CSF-ULW is also well suited for general industrial machinery where weight is a critical factor. The two smallest sizes, 8 and 11, are available today. Other sizes coming soon!
• Zero Backlash
• High Accuracy
• Ultra Lightweight
• Ultra Compact
• Reduction Ratios 30:1~100:1
• Super Flat Configuration, 19mm (size 8); 21.5mm (size 11)
• Outer Diameter: φ 42.5mm (size 8);
φ 50.5mm (size 11)
• Weight: 90g (size 8), 150g (size 11)
Boots also reported that the amount of people calling in sick declined once they were no longer moving heavy steel carts, he said.
“They actually nicknamed the carts ‘widowmakers,'” Zate recalled. “Folks were turning the corner and bumping into them. And so the workers themselves were absolutely thrilled that robots changed their situation.”
“We also change the ergonomics, because walking is reduced, and there’s no lifting,” he said. “A worker at one of our customer sites said that her biggest thrill is that she’s no longer fatigued at the end of the day and that ‘I can go home and be the mother I’ve always wanted to be.'”
Not only are warehouse associates more aware of their surroundings when they’re not behind carts, but they can also focus more on picking, he said.
Locus provides native-language support for multiple languages so that when an associate wearing a lowfrequency Bluetooth tag approaches, the robot’s display automatically changes. “That also helps with their comfort and stress levels,” said Peterson.
Robots extend productivity for older, younger workers
Another benefit of automation is that it can extend the careers of warehouse workers who might otherwise be worn out physically and be unlikely to be replaced by younger generations, noted Zate.
“Only 14% of Gen Z would even consider working in a warehouse; they’re looking for something different in the long term,” he said. “Anecdotally, we’ve heard of workers inviting their family members and
friends to come work at automated warehouses. They say, “You’ve got to come to this place because first, the work is easier, comparatively. Second, we’re working with technology.’ There’s a coolness factor.”
Peterson added: “About a year ago, UPS Healthcare added robots to its fleet and had a naming contest. Some people named them after their kids, and some let their kids suggest names for the robots. We’re actually retraining people to live in the next generation of work, because the Gen Z
Position, angle and speed measurement
Contactless, no wear and maintenance-free
High positioning accuracy and mounting tolerances
At maxon, we develop and build high precision electric drive systems combining brushed and brushless DC motors, gearheads, sensors, and controllers into complete mechatronic drive systems. With our products, complex challenges like highly dynamic multi-axis positioning, synchronization or compactnesscan be solved cost-effectively and efficiently.
Engineered for peak performance, our advanced drive technology ensures unparalleled efficiency, agility, and reliability. For more go to: www.maxongroup.us
and Gen Alpha people that are coming are already familiar with multiple technologies.”
Systems must learn to mind their surroundings, says Locus Peterson also cited case studies involving cold storage, time-sensitive packaging, and multi-level mezzanines with forklifts, all of which can stress workers and affect warehouse safety.
“The key is not just scale — we have sites running almost 1,000 robots across four mezzanine levels,” she said. “It’s important to design for safety across applications and environments.”
“Somebody doesn’t put a pallet all the way into the rack, or somebody goes up high without double-checking what’s below. Somebody drops shrink wrap on the floor — all kinds of stuff happens in logistics,” said Peterson. “Our ability to design not only the robot, but also the software to be responsive and proactive to changes in supply chain environments, is a key differentiator from a safety perspective.”
While interoperability among mobile robots is a subject of standards-making efforts, Locus is working to make sure that safety is consistent among its models, said Zate. Communications with forklifts, which are sometimes manual and in different or overlapping zones, is another goal.
“Our robots can now see forklifts and have ‘no-go’ zones so they don’t go under them,” he said. “We’ve launched PIT or powered industrial truck-to-robot visibility. Not only is it robot to human; it’s robot to robot and robot to PIT that’s human-controlled.”
Locus is also working on warehouse safety with other automation providers such as Berkshire Grey around packaging, sortation, and conveyance.
“As the market matures, there’s no tolerance for someone’s science experiment anymore,” said Zate. “Buyers want a solution that’s tested, that’s reliable, and that’s secure and safe.”
Peterson noted that humanoid robots will have to prove that they
to blocked paths
Locus claimed at MODEX 2024 that its AI and LocusHub support warehouse safety. Gina Chung, Locus Robotics
provide more value than other form factors and that they don’t reduce warehouse safety.
“What does it solve, and is it doing it better than a human?” she asked. “Can we solve these problems in a different way? Mobile manipulation is a small subset.”
Operational visibility can also improve warehouse safety
Even before it deploys autonomous mobile robots (AMRs) at a customer site, Locus Robotics conducts a “concept of operations” or COO process, explained Peterson. “We take a snapshot of their operations, design out what the robots would do, and simulate that out,” she said.
“We also launched LocusHub at MODEX. It’s our data intelligence platform for customers to look at trends over time,” Peterson said. “Companies were desperate for a solution and recognized that they had fewer injuries. As we get bigger, we’ll have even more anonymized data, as we recently surpassed 3 billion picks.”
Wilmington, Mass.-based Locus won a 2024 RBR50 Robotics Innovation Award for passing 2 billion picks last year.
“Most of the operators are asking, ‘How do we meet these SLAs [service-level agreements] and keep our productivity up? How do we get the most out of our workforce that’s dwindling?'” said Zate. “They look at warehouse safety as a soft benefit. Connecting that information with their HR [human resources] teams will help them to see the benefits across the board.”
One of the benefits of Locus’ robotics-as-a-service (RaaS) model is that it handles all of the maintenance, upgrades, and repairs, said Peterson. So when a warehouse safety update is pushed out through LocusHub, customers can automatically get them, she said.
“Within our LocusHub platform, we’re making predictive recommendations, but there’s still human interaction, and the human still has to make a decision about the data that the AI is presenting,” Peterson said. “Just because people could see their supply chain from end to end, if the data was crappy, it didn’t do anything for them. That’s why AI will be big for things beyond using ChatGPT to slot inventory orders.” RR
• Inline planetary gearbox with very short overall length
• Conforms to industry standard wheel sizes
• Rotating hub with dual wheel bearings eliminates overhung load and supports very high payloads
• Fully sealed, maintenance free
• Customized design with modified GAM gearbox
• Meets the demanding shock and reversing loads, as well as overhung load, of an automated parking robot wheel drive.
• Standard GSL Strain Wave (harmonic) robotic gearbox
• Custom housing and mounting flange provides mounting surface and pilot to directly mount wheel
• Developed by GAM in collaboration with Customer
• Custom planetary gearbox developed by GAM for motor manufacturer
• Custom motor rotor shaft with an integral sun gear (gearbox input) reduces the overall length.
• Wheel mounts directly to spline output shaft
• Planetary gearing with offset input shaft
• Stub shaft opposite the output simplifies adding encoder or brake
• Well-suited to narrow track gauge where a coaxial drive would not work
The Robot Report Staff
Mobile robots have become an essential part of the automation landscape in recent years. For end users, they offer flexibility, scalability, and efficiency for various industries and applications. But what do customers actually want from mobile robots, and how do they evaluate and select different technologies and vendors?
Interact Analysis, a market research firm, recently revealed the results of its 2024 Mobile Robots Buyer Survey. The global survey covered the preferences, expectations, and challenges of end users of mobile automation. The company talked to 300 buyers and users of mobile robots, covering different company sizes, sectors, and regions.
With the survey, Interact Analysis hoped to shed light on the current and future adoption of mobile robots,
the factors that influence purchasing decisions, and the pain points and benefits of using mobile automation.
The survey showed that mobile robot adoption is growing across different industries, but not at the same pace in each sector. Ninety-five percent of respondents said they already use some form of mobile automation in their facilities, such as automated forklifts, platforms, conveyors, and autonomous mobile robots (AMRs). This proportion, however, varied greatly by company size and sector.
Larger companies, with revenues over $1 billion, were more likely to use mobile robots than smaller ones. Manufacturers, especially those in the automotive, electrical, and semiconductor sectors, were also
more likely to use mobile robots than retailers, third-party logistics (3PLs), or other industries.
71% of respondents said they only partially automated their workflows with mobile robots, indicating there is still room for improvement and expansion of mobile automation.
When it comes to emerging technologies, artificial intelligence was the most commonly mentioned emerging trend that customers were interested in, specifically when it came to mobile automation.
On the other hand, customers weren’t very familiar with the VDA 5050 standard for communication and interoperability. Only 20% of respondents said they were fully aware of it, and only 8% said it was or would soon be a mandatory requirement in their purchasing decision-making between mobile robots and fleet
managers developed by the German Association of the Automotive Industry (VDA).
Customers more concerned with cost than loyalty, says Interact Analysis Interact Analysis’ survey revealed that cost and integration difficulties are the main barriers and drivers of mobile robot adoption, and that these were two major factors for both technology and vendor selection. The most common reason for not using mobile robots was the high price or perceived lack of return on investment (ROI), followed by environmental factors such as floor suitability, space constraints, or climate.
Customers are not loyal to one mobile robot brand or type, according to the survey. Instead, they would rather use multiple brands and types for different workflows and facilities.
On average, respondents used
Interact Analysis’ survey gave insights into what end users expect from autonomous mobile robots.
3.4 different mobile robot brands, and 123 brands were mentioned in total, reflecting the fragmentation and diversity of the market.
ABB was the most mentioned brand, followed by OMRON, KUKA, and Locus Robotics. However, when survey takers were asked which brand they consider based in class, the answers varied by industry and applications Interact Analysis plans to share those results at a later date.
Customers did indicate they prefer to use the same mobile robot brands across different workflows in the same building, but not necessarily across different buildings or facilities in their network. This suggests customers care little about robot interoperability within a facility.
When selecting a vendor, the most important factors were the vendor’s track record, integration expertise, and local/on-site support, followed by the
stability and size of the vendor. Price and product range were less important than the vendor’s reputation and service, the survey found.
Chinese vendors were not very popular among customers, with only 20% of respondents saying they had used or would consider using them in the future. The most common reasons for not considering Chinese vendors were security concerns, performance issues, safety issues, and legal reasons.
The survey found the most common reason for needing to automate was the desire to reduce operating costs, followed by the need to improve reliability and accuracy. Surprisingly, a lack of labor was not one of the biggest reasons for automation.
When selecting technology for an automation project, the lowest lifetime cost and the ease/speed of integration were the most important factors, followed by system flexibility and performance.
When automating, customers expect a quick return on investment (ROI) and smooth implementation from mobile robots. Eighty percent of respondents
Position sensors for stroke measurement in hydraulic cylinders
Compact safety rotary encoders for position and speed measurement
Dynamically compensated inclination sensors for precise angle measurement
expected an ROI within three years, with most of those expecting it between 18 months and three years. 3PLs typically expected a quicker ROI than other sectors.
Customers typically measure the success of robot implementation by a variety of different metrics. The most common metrics used to measure the success of mobile robot implementation were ROI, productivity, throughput, accuracy, and cost reduction.
Before making a final purchase, customers also expected to see the automation system in action, either through an in-house demo, a reference site visit, or a visit to the supplier’s demo center.
During the purchasing and implementation process, the most common pain points were operation slowdowns, routing and tasking difficulties, and problems with integrating with internal software.
© Interact Analysis 2024
Once a robot was operational, the most common pain points were lack of maintenance prediction, costly downtime, and too much manual intervention required.
Major barriers to adopting mobile robots are lack of available budget and other competing priorities. Interact Analysis
“The survey provides valuable insights for mobile robot suppliers and integrators who want to better understand and serve their customers,” said Ash Sharma, chief commercial officer and vice president of research for robotics and warehouse automation at Interact Analysis. RR
The GML is a planetary gearbox designed specifically for Wheel Drive applications. The rotating hub design, along with dual wheel bearings, eliminates overhung loads, allowing the gearbox to accommodate very high loads — ideal for pulleys or wheel drives.
• Directly mount a wheel to the output flange and pilot on the rotating gearbox housing
• Motor mount customized to your motor, no coupling needed
• Fully sealed and maintenance free
• Compact inline design with very short overall length
• Available in 3 sizes with optional wheel
GAM Enterprises, Inc.
801 E. Business Center Dr. Mount Prospect, IL 60056
888-GAM-7117 | 847-649-2500
www.gamweb.com
info@gamweb.com
The new FBS Series gear unit features an extra large hollow shaft with a compact outer diameter that is ideal for robots and machines requiring complex cabling to pass through the axis of rotation. It includes large cross-roller bearings, enabling the load to be mounted directly to the output and is available in two sizes (25, 32) and three reduction ratios (30:1, 50:1, 100:1).
Scan the QR code for more information on the FBS Series Hollow-Shaft Gear Unit.
Today’s AGVs must be compact and functional robots which are able to move vertically and carry heavy loads. These AGVs cannot fail, and so the choice of their motorization is crucial. There are 5 key points to consider when motorizing an AGV.
1. Choose compact motorization where possible - Drives must fit into restricted spaces, as they are sometimes integrated into existing trucks. A small footprint is critical for applications in logistics.
2. Focus on ease of use – select a plug-and-play solution.
3. Opt for fast delivery of your motor solution
4. Base the design on modularity - Not all AGVs do the same job and therefore having the flexibility to select a solution to match needed specifications is essential.
5. Prioritize safety – select motor options with integrated sensors.
maxon’s IDX motor has a diameter of only 56 mm, its performance is equivalent to that of a motor with a footprint 25% larger. The IDX motorization thus combines performance in a compact size and ideal for AGVs.
Go to Drive.tech for more details.
Visit www.maxongroup.us for more maxon solutions.
Phone: 508.677.0520
www.maxongroup.us info.us@maxongroup.com
From material research to responsible recycling, Dassault Systèmes’ 3D modeling software streamlines the packaging lifecycle.
packaged goods (CPG) companies are under pressure to create more sustainable packaging. Now, faced with the inevitable move to environmentally friendly products, manufacturers are reassessing the materials, the packaging machines, and the recycling responsibility. All of which starts with the packaging design.
Dassault Systèmes provides software that can optimize the design process. Design World asked Raymond Wodar, the company’s global director business consulting for the CPG and retail industry, how the initial design impacts the entire product lifecycle — and how to start the process.
Who in a CPG organization is responsible for sustainable design?
Wodar: In a consumer packaged goods organization, sustainable design is typically a cross-functional effort that involves several departments and roles. The brand marketing function will likely define the parameters for the project and the packaging design and development teams are responsible for incorporating sustainable materials into the design. The teams need to work with internal sustainability or environmental affairs groups that will provide the goals
Stephanie Neil Executive Editor
and standards needed to achieve sustainability targets. Supply chain and procurement teams will also be involved for sourcing sustainable materials and managing the logistics packaging requirements. Other functions may involve advanced R&D topics like materials research and help from outside agencies to determine latest trends and consumer requirements.
Beyond materials, what needs to be considered when creating a sustainable package design?
Wodar: When creating a sustainable package design, several factors beyond just the choice of materials need to be considered to minimize environmental impact and enhance overall sustainability. The design should be optimized to minimize the size and weight of the package to decrease material usage and excess packaging while still effectively protecting the product. A lighter product will also reduce transportation emissions in the supply chain. A thorough evaluation of the entire supply chain will help us understand the environmental impact from production through transportation and distribution. This includes considering how far materials and finished products need to travel and the associated carbon footprint of that journey.
Considerations for end-of-product-life are critical as well. This involves designing for disassembly (if applicable), providing clear recycling or disposal instructions, and considering the lifecycle impact of the packaging once it has been discarded. Using materials that are widely accepted by recycling systems or that can biodegrade in industrial composting facilities is critical.
For a brand manufacturer, the cost profile of the package will be very important so that tradeoffs between material cost, weight, and quality can be properly balanced to provide the consumer a great value while managing internal product margins.
Wodar: Regulatory pressures related to sustainable packaging are increasingly influencing how companies design, produce, and manage packaging. These pressures come from various levels of government and regulatory bodies and can vary by region. Many regions are implementing extended producer responsibility (EPR) programs that require producers to take responsibility for the
entire lifecycle of their packaging, including end-of-life disposal and recycling. Companies may need to manage or contribute to the costs of collection, recycling, or disposal. Several countries and states have introduced bans or restrictions on single-use plastics and certain types of packaging. Regulations might limit or prohibit the use of plastic bags, straws, or other singleuse plastic items, pushing companies to seek alternative materials or packaging solutions. Governments are starting to set targets for waste reduction, recycling rates, or the reduction of packaging waste. Companies are often required to meet these targets or face penalties. For companies operating globally, international regulations and agreements, such as the European Union’s Packaging and Packaging Waste Directive, can affect packaging design and sustainability practices.
How can 3D modeling software help?
Wodar: 3D modeling software enhances the design process by providing a detailed, interactive platform to explore and optimize sustainable packaging solutions, leading to more effective and efficient design outcomes. 3D modeling software allows designers to create detailed visual representations of packaging designs. This helps in visualizing how sustainable materials and design choices will look and function in the real world before physical prototypes are made. Before creating physical prototypes, 3D models can be used to simulate how the packaging will behave under various conditions. This includes testing durability, functionality, and fit, which helps in optimizing the design for better performance with sustainable materials. More advanced 3D modeling tools can also integrate with lifecycle assessment (LCA) software to evaluate the environmental impact of packaging designs. This helps in understanding the potential environmental footprint of different design choices and materials.
PBC Linear is here to provide innovative solutions through the development and manufacturing of linear motion components, mechanical subassemblies, and customized systems to meet customers’ specific application needs. Our diverse staff of engineers with in-depth industry knowledge and decades of experience collaborate with you to solve your linear motion needs.
Headquartered in a 200,000 square-foot facility in Roscoe, Illinois, USA, where production is streamlined and maximized to produce unmatched quality and designed specifically for the most complex and meticulous applications, resulting in ready to install linear solutions.
PBC Linear has the ability to provide smooth and reliable linear motion solutions for a wide array of applications ranging from very small pick-and-place assemblies and scanners used in lab automation to heavy-duty lift systems in industrial manufacturing. Other applications utilizing our components and/or systems are kiosks, unattended retail systems, scanners, printers, and etchers.
What does a virtual twin do?
Wodar: A virtual twin is not only a digital replica of a physical object, system, or process, but it integrates real time data, simulations, and analytics to provide a comprehensive and dynamic model that mirrors the real-world counterpart. The most powerful part of virtual twins is the ability to perform ‘what-if’ scenario analysis. This allows for simulation of various scenarios and testing of different conditions without impacting the physical entity. Imagine testing how a package will behave when dropped, or when stacked in a pallet, or when going through temperature extremes, without needing to use a physical prototype. This is useful for assessing the impact of design changes, operational adjustments, or environmental factors. More advanced virtual twins can predict future performance or potential issues based on historical data and simulation results.
Can creating a virtual twin using 3D modeling software accelerate the time-to-market for a sustainable package design?
Wodar: Yes, using a virtual twin created with 3D modeling software streamlines and accelerates the entire process of sustainable package design. By enabling rapid design iterations, accurate simulations, and efficient collaboration, it reduces the time required to bring a new sustainable packaging solution to market. Designers can simulate how different design changes impact the packaging functionality, sustainability, and consumer appeal without the need for physical prototypes. This includes testing how the packaging performs in various conditions. This highly compresses the time needed to validate the design. Virtual twins also enable the testing of different sustainable materials to evaluate their performance, recyclability, and environmental impact, leading to
better material selection and design optimization.
What are the other benefits of using a virtual twin in sustainable design?
Wodar: Virtual twins offer a wide range of benefits in sustainable design, from cost savings and quality improvements to enhanced collaboration and environmental impact reduction. By leveraging these advantages, organizations can drive innovation, optimize design processes, and achieve their sustainability objectives more effectively. Using virtual twins minimizes the need for physical prototypes, saving costs associated with materials, manufacturing, and testing. By optimizing designs and processes virtually, companies can reduce material waste and energy consumption, leading to lower production costs and a smaller environmental footprint. Virtual twins enable designers to fine-tune every aspect of the design for optimal
Intelligently
Reduction of variants through constant torque over a wide speed range
performance, durability, and sustainability. This leads to higher-quality products that meet or exceed performance expectations.
What is the Dassault Systèmes product that CPGs would use to accomplish this?
Wodar: It is called the Perfect Package industry solution experience. The comprehensive solution helps CPG companies design and optimize packaging in record time. Capabilities include structural design, modeling and simulation (MODSIM), project management, specifications management, lifecycle analysis, and more.
Is understanding the production of the sustainable package part of the process?
Wodar: Yes, understanding the production of a sustainable package is integral to ensuring that the packaging is truly sustainable. It helps in making informed decisions about materials, manufacturing processes, and cost implications, ultimately leading to a more effective and environmentally responsible packaging solution. Different materials may require specific manufacturing processes. Understanding these processes helps ensure that the packaging can be produced efficiently and sustainably. For instance, some materials may need specialized machinery or processes that could impact production costs and the environmental profile. Also, assessing the energy consumption, water use, and waste generated during production is vital for understanding the overall environmental impact. Sustainable production practices aim to minimize these factors.
What is the responsibility of the machine builder in this sustainability journey?
Wodar: The machine builder's role is integral to the sustainable packaging journey. Their involvement in designing, producing, and supporting efficient and adaptable machinery helps ensure that packaging manufacturers can meet
their sustainability goals effectively. By collaborating with other stakeholders and focusing on energy efficiency, material compatibility, and innovation, machine builders contribute significantly to the advance of sustainable packaging solutions. Builders must ensure that their machinery can handle and process sustainable materials, such as biodegradable films, recycled paper, or alternative substrates, without compromising performance or quality.
In a circular economy, does recycling of the package come into the design process?
Wodar: Yes, in a circular economy, the design process is significantly influenced by how the package will be recycled. The principles of a circular economy aim to minimize waste and make the most of resources. This requires considering the entire lifecycle of a product, including its end-of-life stage. Key considerations in the design process for packaging in a circular economy include choosing materials that are recyclable and can be separated easily from other components. Biodegradable or compostable materials might also be considered. OEM
Find more packaging news, trends, and research on WTWH Media’s Packaging OEM by visiting packagingoem.com or scanning the QR code
• Dual AC/DC rated; see below specifications
• Integrated door or side panel mounting
• Rear facing terminals for easy installation
• Loadsafe RT Series
• Switch make/break operation is semi- independent from operator’s actuation speed
• Silver contacts ensures safe and durable operation
• UL 60947-4-1
scan the qr code to learn more
908-806-9400 908-806-9490 (FAX) info@altechcorp.com
www.altechcorp.com/HTML/MDS-A.html
KHK USA offers the broadest selection of stock metric gearing in North America. Designed for use in industrial automation applications, conveyor systems, packaging equipment, robotics, and general machinery applications, KHK’s selection of spur gears, helical gears, internal ring gears, gear racks, bevel gears, screw gears, worms & wormwheels, ratchets & pawls, gear couplings, right-angle gearboxes, and gear lubrication systems are available in various materials and sizes. KHK’s website offers free 3D CAD models for all gear products, complete product specifications, and 24/7 shopping. With KHK USA, stock gears are delivered from stock, with no minimum order or credit card surcharges.
khk usa inc.
259 Elm Place, Mineola NY 11501 516-248-3850
www.khkgears.us
PBC Linear is here to provide innovative solutions through the development and manufacturing of linear motion components, mechanical subassemblies, and customized systems to meet customers’ specific application needs.
Headquartered in a 200,000 square-foot facility in Roscoe, Illinois, USA, where production is streamlined and maximized to produce unmatched quality and designed specifically for the most complex and meticulous applications, resulting in ready to install linear solutions.
PBC Linear has the ability to provide smooth and reliable linear motion solutions for a wide array of applications ranging from very small pick-and-place assemblies and scanners used in lab automation to heavy-duty lift systems in industrial manufacturing.
Other applications utilizing our components and/or systems are kiosks, unattended retail systems, scanners, printers, and etchers.
From mobile robots and automated storage to picking, palletizing, and sortation systems, warehouse operators have a wide range of options to choose from. To get started or scale up with automation, end users need to evaluate their own processes and environments, find the best fit for their applications, and deploy and manage multiple systems.
6402 E. Rockton Road Roscoe, Illinois 61073 USA
+1.815.389.5600
Pbclinear.com pbc linear
Automated Warehouse Week will provide guidance, with expert insights into the evolving technologies, use cases, and business best practices.
REGISTER TODAY roboweeks.com
Robotics Engineering Week features keynotes and panels, delivered by the leading minds in robotics and automation, addressing the most critical issues facing the commercial robotics developers of today.
In the ever-evolving packaging landscape, OEMs constantly seek ways to enhance efficiency, flexibility, and reliability in their packaging lines. At the forefront of this technological evolution is Dorner Conveyors, a leading innovator in conveyor solutions. With a commitment to integrating cutting-edge technologies and adapting to the latest industry trends, Dorner is well-prepared to continue as the preferred choice for OEMs looking to build or upgrade their packaging lines.
One of the most significant advancements in packaging technology is the integration of robotics. Dorner Conveyors excels in facilitating seamless interactions between conveyor systems and robotic components. Dorner's conveyor solutions are meticulously engineered to interface with a wide range of robotic arms and automation systems, enabling precise and efficient product handling, sorting, and packaging.
This compatibility ensures smooth operation across various stages of the packaging process, minimizing manual intervention and optimizing workflow efficiency. Dorner's conveyors are designed with built-in features that support automation, such as smooth transfer points, adjustable speeds, and the ability for real-time data communication.
Dorner's precision is the catalyst for this integration. Dorner's fabric belted conveyors utilize a v-guided underside of the belt, which tracks in the conveyor's frame to ensure that the belt is centered, ensuring that the product is as precise as possible to interact with the robot on the packaging line.
This integration allows for enhanced precision in packaging applications, contributing to higher productivity and reduced operational costs. Whether for a high-speed production line or intricate packaging tasks, Dorner's conveyors ensure that robotic systems perform at their best, providing OEMs with a robust solution for modern packaging demands.
As technology advances, the packaging industry faces increasing demands for flexibility and adaptability. Dorner's
conveyor systems are built with these evolving needs in mind. The modular design of our entire breadth of conveyors allows for easy customization and reconfiguration, accommodating emerging technologies such as IoT-enabled systems, advanced sensors, and machine learning applications.
This adaptability ensures that Dorner's conveyors can integrate with the latest technological innovations, making them a future-proof choice for OEMs. By leveraging Dorner's adaptable solutions, OEMs can stay ahead of technological trends and incorporate new features into their packaging lines without overhauling existing infrastructure. This forward-thinking approach enhances operational efficiency and supports long-term growth and scalability.
When it comes to performance and reliability, Dorner Conveyors sets the benchmark. Their extensive range of conveyor systems includes low-profile, sanitary, and heavy-duty models, each designed to meet specific operational requirements. With a focus on high-quality materials and robust construction, Dorner's conveyors are engineered to withstand the demands of high-speed and heavy-duty applications. Dorner's advanced controls and monitoring systems also provide realtime performance data, enabling proactive maintenance and minimizing downtime. This ensures that packaging lines operate smoothly and efficiently, contributing to consistent product quality and overall operational success.
Understanding that every packaging line has unique requirements, Dorner offers customized solutions to meet specific needs. Our Engineered Solutions team collaborates closely with OEMs to design conveyor systems that seamlessly integrate with existing equipment and workflows. Whether you need conveyors for complex packaging tasks or highvolume production, Dorner provides tailored solutions that enhance operational efficiency and can help achieve your goals. Working with Dorner gives OEMs access
to expertise and a wide range of options for optimizing their packaging lines. This personalized approach ensures that each conveyor system is designed to address the unique challenges and objectives of the application, delivering optimal performance and value.
Dorner's commitment to innovation drives its continuous development of advanced conveyor technologies. Their investment in research and development ensures that their products incorporate the latest advancements, positioning them as a leading choice for OEMs seeking to stay ahead in the packaging industry. By partnering with Dorner, OEMs benefit from a conveyor solutions provider dedicated to pushing the boundaries of technology and performance. This commitment to innovation enables OEMs to build packaging lines that are not only efficient and reliable but also equipped to handle future challenges and opportunities.
In summary, Dorner Conveyors is a leader in providing advanced, adaptable, high-performance conveyor solutions for packaging lines. With their expertise in integrating robotics and new technologies and their focus on reliability and customization, Dorner is the ideal partner for OEMs looking to enhance their packaging operations and achieve long-term success. Trust Dorner to deliver innovative solutions that drive efficiency, flexibility, and excellence in your packaging line projects. OEM
on Dorner’s Packaging Conveyors visit our website dornerconveyors.com or visit booth N-5623 at Pack Expo International in Chicago. For more information
LogiDrive® is a complete decentralized drive package that greatly reduces engineering and commissioning efforts. With this modular system, the number of variants can be minimized, making maintenance easier and reducing Total Cost of Ownership (TCO) for the operator. The LogiDrive interface is intuitive and allows for easy control and monitoring of all units within the system. When paired with the NORDCON APP with NORDAC ACCESS BT Bluetooth stick, LogiDrive systems can provide real or nearreal time drive status to proactively predict maintenance issues and keep systems running smoothly. LogiDrive systems can be configured with IE3, IE4, and latest IE5+ permanent magnet synchronous motors that maintain extremely high efficiency, even at partial loads.
Energy Efficient
• Compliance with the most stringent efficiency regulations
• Considerable reduction of Total Cost of Ownership (TCO)
• High efficiency, even in partial load ranges and at low speeds
• Permanent Magnet Synchronous Motor (PMSM) technology
Variant Reduction
• Standardization of gear motor versions designed for intralogistics and airport technology
• Simplified engineering and selection
• Constant torque over a wide speed range through variable frequency drive technology
Service and Maintenance Friendly
• Considerable reduction of spare parts inventory
• Plug-and-Play technology
• Compact, space-saving design
• 25% weight reduction with lightweight aluminum housing
• Replacement of individual components possible
NORD offers unmatched product versatility, fast, reliable sales and support, and direct access to our engineering team. We also offer online tools for easy configuration and ordering of gear motors and spare parts, as well as 24/7/365 emergency breakdown service. OEM
The main advantages of a quickaccess fastener over a traditional screw are the reduced time and effort required to operate it.
The main advantages of a quick-access fastener over a traditional screw are the reduced time and effort required to operate it.
fasteners typically require only a quarter-turn or other single motion to release, allowing for quick and easy access to the component being secured. This can be particularly beneficial in applications where frequent access is required, such as in maintenance or repair scenarios.
Another important advantage of quick access fasteners over screws is vibration resistance. This ensures panels remain secure, while traditional screws and lock washers may loosen over time due to vibration.
Quick access fasteners also provide a secure and reliable clamping force with minimal risk of over-tightening or undertightening. This can be a common issue when manually tightening a traditional screw.
An exploded view of a quick access fastener versus a traditional screw.
In addition, quick access fasteners are available in a wide range of materials and sizes to meet various environmental and strength requirements. Flush-mounted and other low-profile designs provide a sleek and unobtrusive appearance while still maintaining a secure connection.
Life expectancy, or cycle life, is another crucial benefit. Is the part going to stand the test of time? Applications requiring quick and frequent access need a part that can perform consistently over a long period of time. With the easy-quarter turn motion, quick access fasteners can outperform a traditional screw’s cycle life.
The enhanced performance and benefits of quick access fasteners do have a price premium and may be a bit much for applications where only very occasional access is required. However, for applications requiring frequent access, quick access fasteners facilitate fast and easy operation while remaining secured to the panel, preventing fastener loss.
Ultimately, the choice between a quick access fastener and a traditional screw will depend on the specific requirements and constraints of the application. Factors to consider include the frequency of access required, vibration, the level of security needed, the space available for installation, and the budget for the project. In some cases, a combination of both quick access fasteners and traditional screws may be the best option to balance the benefits of each type of fastener.
Southco www.southco.com
This article is not another article about Torque, Tension, Hydrogen Embrittlement, Flexural Modulus, and numerous other common subjects covered about fasteners and fastening applications. It is simply about what is going on in the fastener industry today that will influence your work.
The number one problem today for the domestic fastener manufacturer is they have a shortage of skilled workers to run the machinery to produce the fasteners. The United States government is aware of this problem, but aid is moving slower than a snail.
More than 200 billion screws are used every year in the United States. There are more standard sizes of fasteners than all the other component industries combined and then you add in all the “Special” fasteners.
85-90% of the standard commercial industrial mechanical fasteners are imported from China and Taiwan. The problems multiply here, no one in the U.S. has any plans if a typhoon, or worse, a tsunami hits Taiwan or the Eastern shore of China. Production would be shut down in a matter of a few weeks or a month because of a shortage of fasteners. Second thought, it is not if China takes over Taiwan, but when and how our government reacts, China could stop shipments of fasteners to the States and again in a matter of a few weeks production of all types of products would shut down.
Ever wonder how a mechanical engineer, civil engineer, or a design
engineer knew how to put together a product with the effects of vibration, wind load, temperature changes, moisture, corrosion, and improper installation among other potential problems? There is not one engineering school in the United States that has any coursework in fasteners or fastening application engineering. Ask your engineering friends how many hours of fastener education they received in college. The answer you will get is “None.” Most fastener engineers learn from the College of Hard Knocks. Fasteners are only about 2% of the total cost of the components in a product but cost 4-5 times as much to install. This Total Cost of Ownership in Fastening is the 15% – 85% Rule. The 85% is made up of Sourcing, Application Design, Ordering, Logistics & Handling, Quality Inspection, Stocking, PreAssembly and Final Assembly. Fastener engineers can cut down on these expenses by evaluating their application design early in the process to ensure the best performance.
The Industrial Fastener Market is estimated at $86 billion and projected to be $121 billion by 2030. The Automobile industry is the largest consumer of fasteners, followed by Aerospace and Construction in third place. However, the EV automobile market uses fewer fasteners and nylon fasteners are replacing the typical steel fasteners in many applications. Your car in 2030 may be “Snaped Together” instead of screwed together. Adhesives
are also playing a significant role in replacing metal fasteners.
Fastener innovation is led by the United States. Every week there seems to be one or more applications for a patent or tradename with the USPTO. The website www.usfastenersources. com annually recognizes new innovative fasteners that will be available “off the shelf” for fastener distributors and endusers.
Fasteners are classified as a Type “C” Component because they are a low-cost, high-volume component. I think the “C” should stand for a “Critical Component.” 80% of automotive recalls are fastener related. 43% of the weight of the weight of the airframe on commercial airplanes is fasteners. On a Boeing 747-400 there are three million fasteners, which includes 850,000 rivets. Fasteners and Fastener Application Engineers do not get the respect they earn, but they are especially important to the design and production of successful products. Re-read the subtitle noted above. Keep up the excellent work, read all the articles, catalogs, and brochures about fasteners and fastening applications you can get firsthand. Have the suppliers of your fasteners join in and give you help, when and where it is needed. Your suppliers will be very willing to help. Finally, test and evaluate all the design stages to always improve the application and performance of the fasteners. Africa Studio | Adobe Stock
Flat: Generally used for load disbursement
Tab/Lock: Designed to effectively lock an assembly into place
Finishing: Often found on consumer products
Wave: For obtaining loads when the load is static or the working range is small
Belleville: Delivers the highest load capacity of all the spring washers
Fender: Distributes a load evenly across a large surface area
Shim Stacks: Ideal for simple AND complex applications
Boker’s Inc.
3104 Snelling Avenue
Minneapolis, MN 55406-1937
Phone: 612-729-9365
TOLL-FREE: 800-927-4377 (in the US & Canada) bokers.com
NBK is a manufacturer of Specialty Screws including Plastic Fasteners. In this April, NBK acquired Solid Spot LLC’s plastic fastener business and then, more various product lineup are available such as PEEK, RENY, PC, PVDF, PTFE, POM, etc.
NBK manufactures not only plastic screws but also low profile (low head), miniature size(less than M3), vacuum application, anti-galling, chemical resistance, non-magnetic, and more.
Flexible customization is available.
NBK America LLC
307 East Church Road, Suite 7
King of Prussia, PA 19406
Phone: 484-685-7500 https://www.nbk1560.com/en-US/
Ian Wright • Senior Editor • engineering.com
From prototyping to materials science, sports equipment has more in common with the aerospace and automotive industries than you might think.
Wherever you look, the story of 3D printing adoption tends to follow a similar arc across industries. It begins with prototyping, followed by a small set of niche use cases, eventually culminating in end-use parts and, sometimes, mass production. Examples of this pattern of development can be found in aerospace, automotive, and even sports equipment.
That last one may not get as much attention as the other two — probably because the industry is only a fraction of their size — but that doesn’t mean it’s not worth talking about. Sure, we hear a
lot about 3D printing for the Olympics, or when there’s some new innovation in bicycle manufacturing, but there are plenty of more mundane examples in sports equipment that highlight the challenges and opportunities for additive manufacturing (AM).
The Past — 3D printed prototypes and customization
“Most of these companies, depending on what they make, have a one- or two-
year product release cycle,” said Jon Walker, key account manager at EOS. “Given that the development cycle is every 12 months, the ability to iterate very quickly in the prototyping phase is invaluable.”
Perhaps the best recent example of this is Wilson’s airless basketball, introduced in 2023. According to Walker, the project went from concept to prototype to reality in just a few
Creating Wilson’s airless basketballs, shown here in three different colors, involved a delicate balance between CAD model revisions and material selection. EOS
Traditional desktop 3D printers are fine for prototyping parts, but can be costly in terms of volume production and time-to-market. With the 1000 x 1000 x 700 mm build area, industrial manufacturers can produce near-net shape parts and have greater ability to customize. The result is decreased costs and reduced time-to-market.
3dplatform.com
SIMO processed UG series actuators are qualified to tolerances of 6x less bow, 2x less twist, and 2x better flatness. Built with quality CNC roll threaded lead screws with an innovative constant force anti-backlash nut. The CFT nut is self-lubricating and maintenance free.
months. “The feedback loop between General Lattice and Wilson was intense,” he said. “Parts were built in Texas, sent to Ohio for testing, and the results were used to re-optimize the CAD file. The speed and the amount of work we accomplished really showed how digitalization and rapid prototyping can drastically shorten development cycles.”
Sports equipment also offers plenty of examples of another major benefit of AM: customization. Walker cited the 2012 Summer Olympics and a project involving EOS and athletic shoemaker New Balance. The companies measured the US running team’s gaits using highspeed cameras and other sensors to design bespoke outsole patterns for each athlete’s cleats. “A quarter-second advantage, gained by optimizing your track spike to the way your foot rolls
across the track could be the difference between first and last place,” he said, “especially in events like the 100 meters.”
In many respects, the sports equipment industry is similar to automotive and aerospace: highly competitive, highly regulated, and constantly striving for advantages through cutting-edge innovation. However, unlike these other industries, its relatively small size means that it needs to take a different approach to research and development. By taking advantage of the technological leadership in aerospace and automotive, the sports industry can essentially “draft” behind them, like cyclists or speedskaters exploiting a leader’s slipstream.
“This isn’t new,” said Walker, citing the late hockey equipment designer
Brian Heaton as an example. “He lived in Windsor, Ontario and was familiar with the automotive industry. That’s how he knew about synthetic leathers with hydrophobic properties, which was revolutionary at the time. Before the early 1980s, goalie pads were literally cowhide stuffed with horse hair because the hockey industry alone just wasn’t big enough to convince a company like DuPont to design these materials from scratch.”
Present
As is often the case with 3D printing in other industries, engineers designing sports equipment for additive manufacturing need to strike a balance between revising CAD models and adjusting material properties.
EOS and New Balance
partnered to design custom footwear for the 2012 US Olympic running team by capturing each athlete’s unique gait using sensors and high-speed cameras. EOS
However, because sports equipment manufacturing is considerably smaller than other AM users — such as aerospace, medical, or automotive — the industry’s ability to drive innovation in materials science and software development is proportionally diminished.
Nevertheless, there have still been significant advances in both these areas when it comes to sports equipment. “We recently added PEBA to our portfolio of polymer materials,” said Walker. Polyether block amide, known under the trade names of PEBAX and VESTAMID E, is a thermoplastic elastomer that’s about as well known and widely used in sports equipment as Kevlar is in defense.
“It’s been used in the sports industry for years, but no one was able to powderize it and 3D print it,” Walker added. “So, for us, PEBA is really exciting. The fact that it’s a family of materials means it can hit different niches. For example, a really soft PEBA could replace certain foams, while a really stiff PEBA might be able to replace certain hard plastics.”
When it comes to engineering software for additive manufacturing, the story in sports equipment is a familiar one: “You design something, you think you know what material to make it in, but you don’t actually know how the material will act in a specific shape or what the performance will be,” said Walker. “A lot of software companies, like General
Lattice for example, are doing real-world physical testing and then incorporating that data back into their software. So now, if you pick a gyroid lattice and a certain material, the software will give you a rough estimation of the performance.”
Eliminating (or at least reducing) the need to 3D print different versions of the same part in different materials for physical testing saves on development time as well as cost. Fortunately for engineers working in sports equipment, this is another improvement that’s being driven by the much larger aerospace and automotive industries.
The Future – AM sports equipment for amateurs
We’ve covered two of the three major steps in 3D printing adoption: prototyping and niche use cases. What about mass production, the third and most difficult hurdle to clear? How close is the average consumer to ordering customized footwear based on their natural gait? On the one hand, mass customization is something AM excels at and it’s especially sought after in sports equipment as opposed to aircraft or automobiles, where the demand for bespoke products is limited to the rare few who can afford them.
As Walker pointed out, “No two body parts are the same, and I think everyone has had a pair of shoes, a hat, a helmet, or a glove that just didn’t fit right and made the product uncomfortable
Engineers and shoe designers at New Balance used 3D printing to make customized shoes for elite runners in hopes of improving their performance. EOS
to wear.” Interestingly, the challenge here is the same one facing 3D printing adoption in the automotive, aerospace, and medical industries: regulation.
“Almost every piece of sports equipment in a store is regulated somehow,” he said. “It could be size, like a maximum size for a baseball glove, or safety standards like the NOCSAE standard for batting helmets, the CSA and HECC standards for hockey helmets, or the NFL’s own rigorous testing standard for football helmets. Traditionally, you’d test small, medium, and large sizes, or in footwear, sizes 10, 11, and 12, and validate that they work. But with 3D printing, where each iteration can be different, how do you test all those variations?”
The current approach involves validating some subset of sizes from across the available range, but it’s still novel and likely oversimplified. Walker noted that there are only a handful of products that have been validated this way. “The real issue is defining the boundaries because there are still limits,”
he said. “You’re not going to make a golf club that’s 10-ft wide because no one could swing it. But moving a few millimeters in either direction can make a big difference, and no one wants to deal with the USGA’s approval process for 300 different permutations.”
Regulatory challenges aside, Walker remains optimistic about the future of AM in sports equipment, in part because of its connections to other industries. “If
someone could unlock a high-strength 3D printed nylon that meets automotive requirements, it could close the gap in sports equipment,” he said. “I’ve heard aerospace companies say the golf shaft industry gets all the cool composites, and I’ve heard golf shaft companies say aerospace is where all the development is. There’s a lot of symbiosis in sports equipment and other industries, even if they don’t realize it.” DW
3D Platform is the trusted source for industrial-strength, largeformat 3D printers. Based in Roscoe, Illinois, USA, the 3D Platform team is focused on driving advancements in technology to innovate, design, and build next-generation equipment for additive manufacturing. Our approach to 3D printing focuses on four clear industry demands:
Scalability and increased throughput from high-flow extruders allows smart manufacturers to shed legacy product development cycles and small-scale models for full-size prototypes and production.
Open market-enabled solutions allow users to go bigger with 16 times the speed of competitors’ extruders for faster printing and exceptionally strong parts.
• Quick-Swap dual extruder heads deliver high quality 3D prints.
• Modular design accommodates variable nozzle and filament sizes
• Nozzle flexibility for fine layer resolutions or faster printing and strength.
Affordability of equipment and materials allows SMB’s and Fortune 100 companies to tailor 3D printing to their needs, and quickly develop new products and bring them to the market.
Robust industrial technology stands up to harsh environments and the excessive demands of rapid manufacturing using the world’s leading linear motion mechatronics, reliable motors, and sophisticated control systems.
To learn more about 3D Platform, visit www.3dplatform.com.
3D Platform 6402 E. Rockton Road Roscoe, Illinois 61073 USA +1.779.771.0000 3dplatform.com marketing@3dplatform.com sales@3dplatform.com
CS Hyde Company is your source for high performance adhesive tapes, polymer films, fabrics, and silicone. Our product line is comprised of various types of materials with performance properties required for additive manufacturing, including low friction, nonstick release, and high temperature resistance. Common release surfaces include ULTEM® PEI, TPX®, or Optically Clear FEP/PFA. FDM/FFF printers equipped with PEI sheets benefit from surface durability and a surface that will hold filament in place and remove cleanly when cooled. Aside from printing surfaces, we have helped design engineers with material solutions for LCD screen bonding, silicone gasket designs, and linear rail or carriage friction reduction.
Finding solutions to industry related problems is a huge part of what makes CS Hyde a trusted vendor in the additive industry. Working with hobbyists to 3D machine manufactures has given us insight to the ongoing issues within the additive manufacturing industry regarding printing surfaces, as well as machine component manufacturing. Our polymer knowledge allows us to recommend compatible polymers for property specific applications like UV transparency or material outgassing. With converting machinery expertise, we have been able to produce custom products utilizing adhesive lamination, slitting, sheeting, die cutting, and rapid prototyping.
HOW VIRTUAL INCISION DESIGNED THE SMALL BUT MIGHTY MIRA SURGICAL ROBOT — AND THEN SHRANK IT AGAIN FOR SPACE
TANDEM DIABETES CARE TAPS MINIATURIZATION AND AUTOMATION FOR ITS LATEST SYSTEMS
How Virtual Incision designed the small but mighty MIRA surgical robot — and then shrank it again for S pace
THE VIRTUAL INCISION MIRA SURGICAL SYSTEM’S DESIGN WAS SMALL TO START WITH — AND THEN CAME AN OPPORTUNITY TO TEST ABOARD THE INTERNATIONAL SPACE STATION.
In conversations with Medical Design & Outsourcing, surgical robotics developers often say they try to use as many off-the-shelf components as possible.
That wasn’t possible for the MIRA (Miniaturized In Vivo Robotic Assistant) Surgical System, Virtual Incision co-founder and Chief Technology Officer Shane Farritor said.
“Everything in our device is quite custom … from scratch, bespoke,” he said in an interview. “… Our robot’s different than everyone else because it’s miniature, and we think miniature is big.”
Virtual Incision’s MIRA won FDA de novo classification in February 2024 as a table-mounted miniaturized electromechanical surgical system. At the same time, a modified version called spaceMIRA was in orbit aboard the International Space Station for a mission to test how well surgeons on Earth could control the robot.
“The story starts with the University of Nebraska Medical Center,” Farritor said. “I was on faculty at the engineering college, but the medical center acquired the eighth da Vinci ever sold. They were very early adopters of robotic surgery and they hired my co-founder, Dr. Dmitry Oleynikov, to start a robotic surgery program. And this is 2002, 2003 — really, really early. He and I both thought that there’d be another way to do surgery, that it should be small robots that go inside the body rather than big robots reaching in from the outside. Da Vinci is an incredible machine, maybe the best medical device ever made. But we think there’s also an advantage to small devices. So we started making little robots.”
In the beginning, those robots looked like miniature versions of the rovers NASA sent to Mars. Before joining the University of Nebraska, Farritor worked on the Mars Rover project through Massachusetts Institute of Technology’s Field and Space Robotics Laboratory and the C.S. Draper Laboratories Unmanned Vehicle Lab.
Virtual Incision’s research won funding from the U.S. government “because NASA and the Army want to do surgery in crazy places, and miniature devices lend
themselves to crazy places,” Farritor said.
Virtual Incision is designing more devices for soft-tissue, abdominal procedures.
“We think every surgical procedure can be addressed with a miniature robot,” Farritor said.
Designing a miniature surgical robot “Most of the other devices are big robots on the outside,” Farritor said. “That means you put big motors on the outside, and then you have usually cable transmission into the body to actuate the tips of the instruments. That has a lot of advantages, but you have a bigger motor and then you have to have a bigger motor to hold that motor and it snowballs into a big device.”
So Virtual incision designed MIRA with local actuators, placing miniaturized Maxon motors closer to where the robot’s instruments would actually be working.
“Mechanically, our robots are pretty tightly packed and that can cause all kinds of other problems, but we think it has all sorts of advantages to the challenges we think we’ve overcome,” he said. “You can’t have big motors, you have to use little motors efficiently. Efficiency is a big issue, heat dissipation, all these sorts of things start to come into play. But we think MIRA is a fantastic device and shows the feasibility of this approach.”
One advantage is the ability to quickly move from quadrant to quadrant within a patient.
“To go from the rectum all the way up to the spleen, over to the liver, and then down to your cecum happens in seconds with our device,” he said. “There’s no docking, there’s no undocking, there’s no instrument change required. Multiquadrant access is one of the powerful aspects of miniature.”
Another advantage of miniaturization is constant triangulation. Instead of a multiport system that inserts instruments from several incisions and comes together inside the patient, the MIRA system is internally triangulated when it drops in.
“It’s really inherent with the design of the device and it’s, again, part of being miniature. The surgeon always gets the
same first-person view, like we’ve shrunk them down and put them inside the body,” he said.
For simplicity and ease of use, Virtual Incision designed the MIRA system with a single cable and to use only four disposables — and no drapes. The system can be set up in six to eight minutes.
“Our focus has always been on simplicity in the operating room, and that’s been the driving ethos in the work that we do. We want to make our system easy to use so that you don’t need special teams to be trained and you can do surgery in forward environments, you can do surgery at night. All these things that make it simpler, we think also makes it more useful. One of the effects of simplicity can be low cost.”
MIRA is also designed for up to 15 cycles of reuse with vaporized hydrogen peroxide (VHP) sterilization. Ethylene oxide is difficult to work with and the surgical robot can’t be sterilized with an autoclave, so VHP is “the next-simplest” method of sterilization, Farritor said.
“It made sense for us,” he said. “It’s another step toward simplicity and sustainability.”
Making MIRA even smaller for space Virtual Incision modified MIRA into an even more compact spaceMIRA to fit inside a NASA-provided locker aboard the International Space Station. Those microwave-size lockers fit in EXPRESS Racks, short for “expedite the processing of experiments to space station.” Those racks have connections for power, data and video, plus cooling, water, nitrogen supply and vacuum exhaust.
To fit into one of those lockers, SpaceMIRA is about three inches shorter than its Earth-bound predecessor.
“MIRA has a long straight section that will accommodate different abdominal wall thicknesses and different surgical targets inside the body so you can extend to different targets. We didn’t need to do all that in our experiment, so we were able to shorten it and fit it in the diagonal of that EXPRESS Rack locker,” Farritor said. “NASA does a lot of these lockers and they know
how to handle them, so that really simplified our in-flight operations.”
Virtual Incision conducted two experiments aboard the ISS. The first was a pre-programmed run for semiautonomous surgery, testing how well the surgical robot could cut rubber bands on its own as a simulation of
The second experiment was to test and demonstrate telesurgery, giving surgeons on the ground control of the robot as it orbited 250 miles above Earth. They performed simple and advanced tasks despite 600-800 ms of latency.
“They learn to deal with the delay. This was only simulated surgery, but I was really encouraged that they were all able to do the task,” Farritor said. “It’s preliminary, but they all moved very deliberately, so the total distance traveled was actually less than when they would do these procedures on Earth. … It really just confirms and encourages a lot of the things that we’re already doing.”
The Virtual Incision team will review data from spaceMIRA after it returns to Earth to learn more.
“Don’t measure — cut twice.” Asked for advice he would offer to designers and engineers at other device developers, Farritor said Virtual Incision has a “building ethos.”
“We make things and try them quickly, over and over and over again,” he said. “It’s very easy in the medical device industry to forget that and to try to get everything perfect before you try something. You have to look for ways to make little bets, to try small versions or test different aspects of what you’re trying to do in a physical way. and as clinically relevant as you can. So we really encourage that quick iteration and quick design process.”
“The saying is measure twice and cut once,” he continued. “Don’t measure. Just start cutting. Boards are cheap. If you’re measuring twice, you’re probably following a plan and following a plan means you’re probably not being as innovative as you could. So don’t measure — cut twice.”
Go to wtwh.me/virtualincision
ORDER A TEST PUMP: knf.com/shop
KNF further expands its Smooth Flow series, with the introduction of FP 7 and FP 25. These new liquid pumps deliver adjustable flow rates from 15 – 70 ml/min and 50 – 250 ml/min, respectively. Both pumps produce up to 1 bar (14.5 psi). High pressure versions achieve up to 6 bar (87 psi). All versions feature:
• Very low pulsation for efficient flow, reduced noise/vibration, and reduced system stress
• Self-priming, even at low motor speeds
• Options including materials, connections, mounts, motors, and boxer configurations. Ideal applications include medical equipment, inkjet printing, 3D printing, fuel cells, and solvent handling.
Learn more at knf.com/en/us/stories-events/news/article/fp7-fp25
Tandem Diabetes Care EVP and Chief Strategy Officer Elizabeth Gasser didn’t exactly plan for the whirlwind past year or so.
Over about two months, Tandem announced continuous glucose monitor (CGM) integration with the latestgeneration technology from Dexcom and Abbott, launched its Tandem Source diabetes management platform and began the rollout of its new Mobi miniature insulin pump.
Those milestones added to the January 2023 acquisition of AMF Medical, adding a differentiated patch pump to the Tandem portfolio.
“We certainly didn’t plan that from the outset, [to] do four back-to-back releases,” Gasser said in an interview.
“Sometimes that’s how technology comes out along the way. It’s made for a busy, intense year.”
Tandem’s t:slim X2 has used Control IQ automated insulin delivery (AID) software for years. But the company’s newest offering highlights another diabetes care trend: miniaturization.
Those trends of automation and miniaturization help reduce the cognitive burden for patients; Gasser said:
“We can make it more wearable and more convenient.”
Tandem’s origins
Dick Allen, one of Tandem’s founding board members, encountered pumps when he had to help manage his granddaughter’s diabetes. He discovered that the insulin pump at the time was “a very funky medical device,” Gasser said, and Allen believed there had to be a better way for patients to manage diabetes
“It’s fundamental in our space and it’s been a core tenet for Tandem since inception,” Gasser said. “From day one, the company set itself the goal of thinking about how to make this feel less like a medical device and make it easier to use and more appealing from a consumer perspective.”
That mindset led to the development of Tandem’s first t:slim pump and the following iterations. It developed into the company’s pursuit of varied CGM integration, providing more options to more patients. Mobi is yet another example of a smaller, durable device created to give patients yet another option.
“These devices are on you 24/7,” Gasser said. “They’re as intimate as devices get, other than phones, which are very personal devices. Honing in on that idea of how do we make it feel more consumer and less medical is important.”
Leading the way in automation Automation, AI, algorithms and the like have long been a hot topic in medtech.
“The arc of technology points toward miniaturization and automation,” Gasser said.
Tandem Senior Director of Medical Affairs Laurel Messer sees AID moving toward systems that require less user interaction and burden.
“This is a partnership between better algorithms and exceptional wearability,” she said. “The future will include reduced user input, potentially getting to a point of a fully closed loop that does not require user interaction for meals. We need to relentlessly drive AID toward this goal to limit the impact and burden of diabetes on people living life.”
Tandem’s Control IQ automatically monitors and regulates blood glucose. The advanced hybrid closed-loop automated insulin delivery feature predicts and helps prevent high and low blood sugar. It leads to improved time in range throughout the day and night.
Gasser said she often invokes the Nest example when talking automation — the advent of cruise control and the capacity to implement machine learning so more and more can be done with automation. She calls it “the Nest–ification of tech,” referring to Google’s line of smart home devices.
Tandem approached this concept with Control IQ as an adaptive algorithm that can be iterated upon to continuously reduce the need for user engagement.
With diabetes, as Gasser explains it, treatment requires the administration of something physical and constant engagement. The aim is to take the physical burden out of the equation.
“Automation requires that we think about what wraps around it in terms of
the user experience, that the interaction is intuitive, usable and builds trust,” Gasser said. “There’s the information that the patient makes visible through the applications themselves to help people understand their relationship with the automation. We spend a lot of time on it. It’s a significant investment.”
Diabetes devices are getting smaller all the time. The Dexcom G7 is 60% smaller than the G6. Abbott’s FreeStyle Libre 3 is about the size of two stacked pennies, compared to Libre 2, which is about the size of two stacked quarters.
Tandem is following suit with Mobi and eventually the Sigi patch pump from AMF Medical. Mobi is half the size of the t:slim X2 pump.
“There’s a consistent theme across CGM and pumps rolling into miniaturization,” Gasser said.
The Mobi automated insulin pump with the accompanying mobile app Image courtesy of Tandem Diabetes Care
There remain limitations, though, such as capacity on the pump side. With Mobi’s 200-unit cartridge and Sigi’s eventual 160-unit cartridge, the company continues to create smaller devices that can still provide the necessary levels of therapy to different patients with different needs.
Gasser said that while they can “pack quite a lot in a small place,” developers will eventually reach the boundaries of what’s possible — at least in a durable way. However, the company believes that its options and their shrinking sizes will enable more choice among patients.
“We’re allowing people to customize form factor, capacity and wearability to how they want to engage with their insulin therapy,” Gasser said.
As a global technology leader with over 300 patents, KNF delivers custom-engineered diaphragm, solenoid, and swing piston pump solutions driven by precision and innovation. Drawing on our broad engineering and applications experience, KNF collaborates closely with customers throughout the entire development process to create the best solution while balancing required performance, product lifetime, and cost.
KNF engineers strive to optimize not only our pump, but to also assist customers in optimizing their overall system. We align our inspection and testing procedures with application requirements, delivering any batch size—from thousands to single pumps. KNF Neuberger liquid and vacuum/compressor pumps handle many clinical diagnostic instrument tasks including washing, waste handling, metering/dosing, aspiration, degassing/debubbling, direct liquid transfer and recirculation, vacuum-over-liquid transfer, vacuum evacuation, and pneumatics.
KNF Neuberger, Inc.
2 Black Forest Rd Trenton, NJ 08691, USA www.knf.com 609-890-8600 knfusa@knf.com
Nitto Kohki’s DC motor-driven air compressors and vacuum pumps are ideal for applications requiring exceptionally reliable air flow, pressure or vacuum performance. Featuring oil-free operation, a single moving part, low noise, and low vibration, this line of linear air compressors comes in 12V and 24V models. Other benefits include:
• Very low power consumption
• Self-cooling design
• Exceptional service life (rated at 10,000 hours)
• Easy maintenance
Ideal for demanding applications in the medical device and laboratory equipment industry, including dialysis machines, blood separators, blood analyzers, incubators, heart assist devices and more.
NITTO KOHKI U.S.A., INC.
46 Chancellor Drive Roselle, IL 60172
Toll Free: (800) 843 6336
Phone: (630) 924 8811
Fax: (630) 924 0808
E-mail: info-pumps@nittokohki.com www.nittokohki.com
SDP/SI creates precision gears, superior mechanical components, and customized motion control solutions for medical device OEMs. With over 70 years of experience and proven performance SDP/SI provides the reliability that the medical industry requires. Partnering with companies that include Abbott Laboratories, Intuitive Surgical, Siemens Healthcare, Medtronic, and many more, we provide support from the early design stage through delivery.
• Precision CNC Manufacturing
• Engineering Development – with years of experience we know how to make systems smaller, lighter, and faster.
• ISO 7 Class 1000 Cleanroom for Assembly
• Gear Cutting / Bevel Gear Cutting
• Custom Drive Systems / Gearboxes
Send an RFQ online, discuss your project with our engineers, visit our facility. We look forward to working with you!
Stock Drive Products/Sterling Instrument (SDP/SI) 250 Duffy Avenue, Hicksville, NY 11801
https://www.sdp-si.com sdp-sisupport@sdp-si.com (516) 328-3300
Ryan Ashdown rashdown@wtwhmedia.com
216.316.6691
Jami Brownlee jbrownlee@wtwhmedia.com
224.760.1055
Mary Ann Cooke
mcooke@wtwhmedia.com
781.710.4659
Jim Dempsey jdempsey@wtwhmedia.com 216.387.1916
Mike Francesconi
mfrancesconi@wtwhmedia.com
630.488.9029
Jim Powers jpowers@wtwhmedia.com 312.925.7793
Publisher Courtney Nagle cseel@wtwhmedia.com 440.523.1685
CEO
Scott McCafferty smccafferty@wtwhmedia.com 310.279.3844
EVP
Marshall Matheson mmatheson@wtwhmedia.com 805.895.3609
CFO
Ken Gradman kgradman@wtwhmedia.com 773-680-5955
DESIGN WORLD does not pass judgment on subjects of controversy nor enter into dispute with or between any individuals or organizations. DESIGN WORLD is also an independent forum for the expression of opinions relevant to industry issues. Letters to the editor and by-lined articles express the views of the author and not necessarily of the publisher or the publication. Every effort is made to provide accurate information; however, publisher assumes no responsibility for accuracy of submitted advertising and editorial information. Non-commissioned articles and news releases cannot be acknowledged. Unsolicited materials cannot be returned nor will this organization assume responsibility for their care.
DESIGN WORLD does not endorse any products, programs or services of advertisers or editorial contributors. Copyright© 2024 by WTWH Media, LLC. No part of this publication may be reproduced in any form or by any means, electronic or mechanical, or by recording, or by any information storage or retrieval system, without written permission from the publisher.
Subscription Rates: Free and controlled circulation to qualified subscribers. Non-qualified persons may subscribe at the following rates: U.S. and possessions: 1 year: $125; 2 years: $200; 3 years: $275; Canadian and foreign, 1 year: $195; only US funds are accepted. Single copies $15 each. Subscriptions are prepaid, and check or money orders only.
Subscriber Services: To order a subscription or change an address visit our website at: www.designworldonline.com
DESIGN WORLD (ISSN 1941-7217) is published monthly by: WTWH Media, LLC; 1111 Superior Ave., Suite 2600, Cleveland, OH 44114. Periodicals postage paid at Cleveland, OH & additional mailing offices.
POSTMASTER: Send address changes to: Design World, 1111 Superior Ave., Suite 2600, Cleveland, OH 44114
By Mark Jones
My wife, Erin, is now the proud owner of a plug-in hybrid vehicle. It is a purchase intended to make us more sustainable. Like previous purchases intended to reduce our environmental impact, it does not make economic sense.
It is not our first hybrid. It is our first lithium-ion battery vehicle, fitting since both of us spent part of our careers developing better lithium-ion batteries. We both spent large chunks of time focused on sustainability. We actually try to live more sustainably and consider sustainability when making decisions.
Erin wrestled with going full electric but found the plug-in hybrid a more compelling choice. The car has a 40-mile range on full EV. That more than suffices most days. Her average is fewer than 10 miles per day. The 18-kWh battery is more than sufficient for typical use. Visiting our daughter is a common road trip and could not be done on a single EV charge. Going full EV would require a significant change in driving habits. Additionally, my studies during my working career pointed toward limitations around battery supply. At the macro level, having more vehicles with 40 miles of full EV are a better allocation of limited batteries than fewer vehicles with longer range. On both counts, the plugin option, backstopped by gasoline, is the best compromise for our household and the planet. Most days, driving uses only electric power. On those days, it is as good as an EV for the planet. On longer trips, we’re still far more efficient than the internal combustion version of the same car.
The plug-in hybrid provides continuous feedback on efficiency. It makes driving a game where trying to
maximize efficiency is the goal. Driving more efficiently is directionally correct for sustainability but doesn’t tell the full story. It doesn’t tell me whether my GHG emissions are less, whether money is being saved, or even whether time is saved. Instantaneous efficiency makes for a fun game, but emissions, money, and time are what I ultimately care about.
The plug-in hybrid joining our household was noticeable. Our electricity use increased by 1.5 times. That was about what I was expecting. For many, per-person car and home energy use are about equal. Crunching the numbers showed that the delivered cost of the electricity per mile was slightly higher than operation on gasoline at current prices.
Emissions are reduced when using only electricity, but only by about 20%. I was certainly hoping for more. Buying even more renewable energy
will make it better, but at an additional cost. Based on actual usage, that 20% equates to about 800 pounds of GHG emissions avoided every year. The difference in sticker price between the PHEV and HEV was about $10,000, or about $2500/ton CO2 avoided over a 10-year life. That is about 10-100X the normally quoted abatement costs. The PHEV is reducing GHG emissions, but at a high cost.
Time is saved. Plugging takes seconds and avoids the gas station. Erin will save about 12 hours a year, 120 hours over an assumed 10-year life. That works out to $80/hour. So time is saved, but likely at a high cost.
We considered sustainability when making a car purchase. It wasn’t a decision made purely on economics. Had cost-saving been our goal, our more sustainable choice would have missed the mark. DW
K- and L-Coding
Voltage & Power supply
Compact design
Currents up to 16 A
Fully integrated drive components, control electronics and automation software – all from a single source – and all designed to work together perfectly.