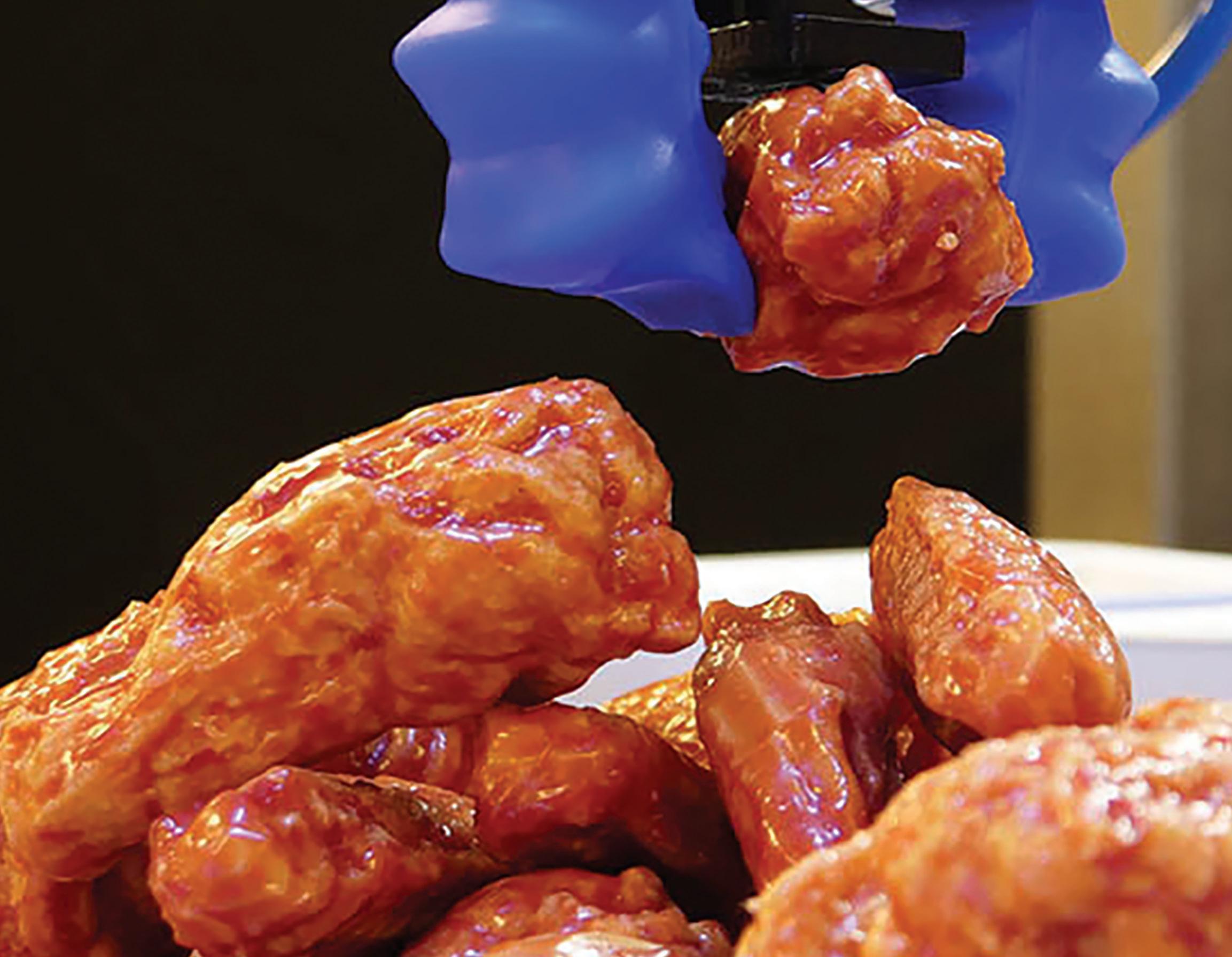
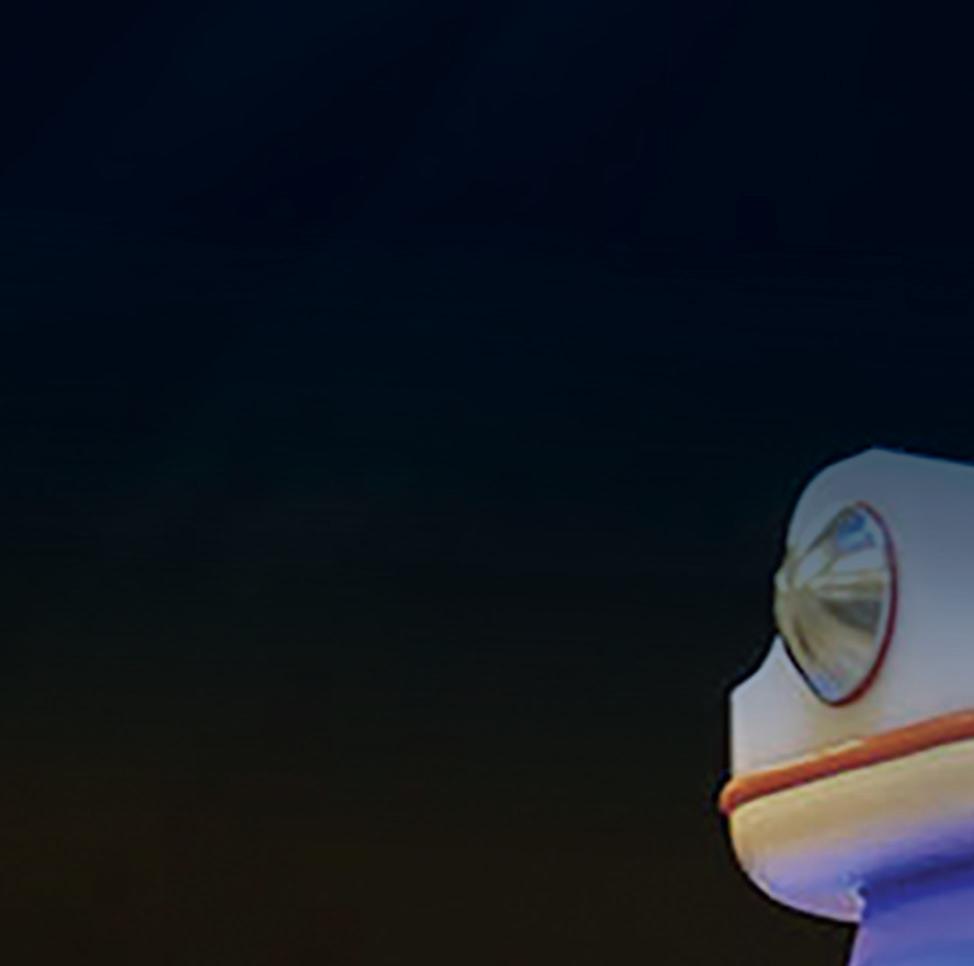
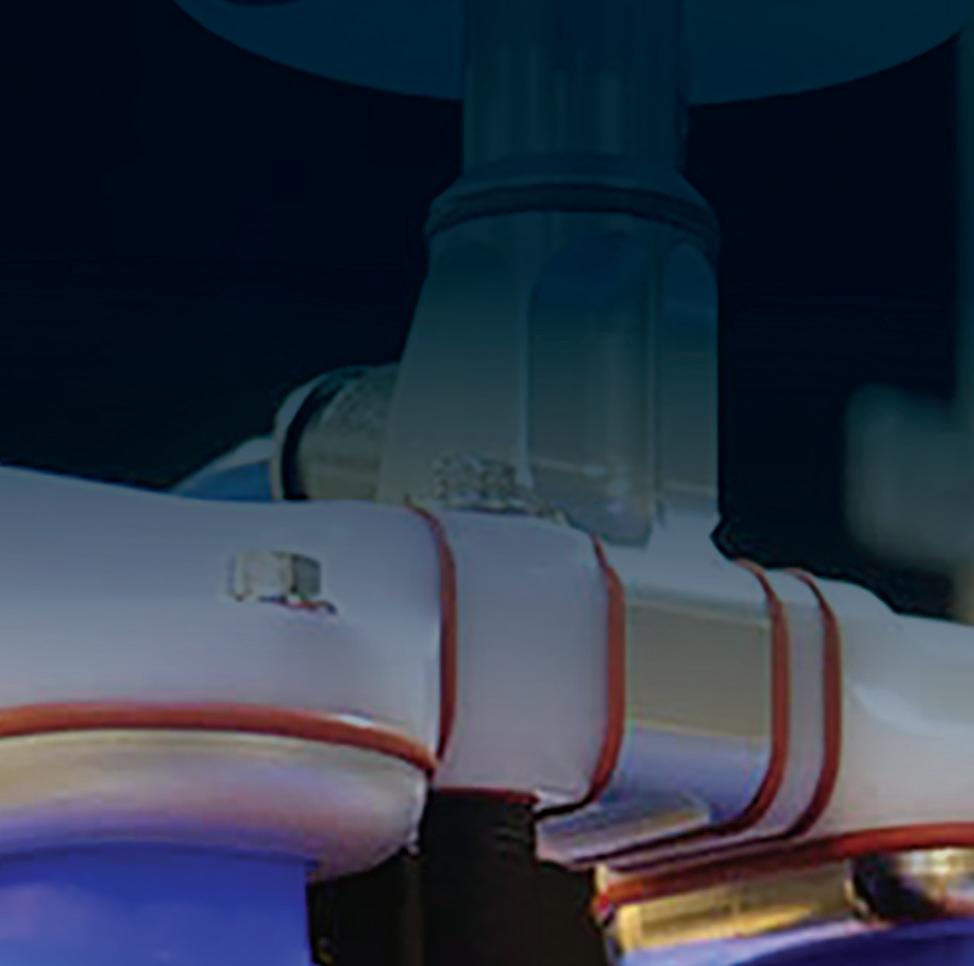
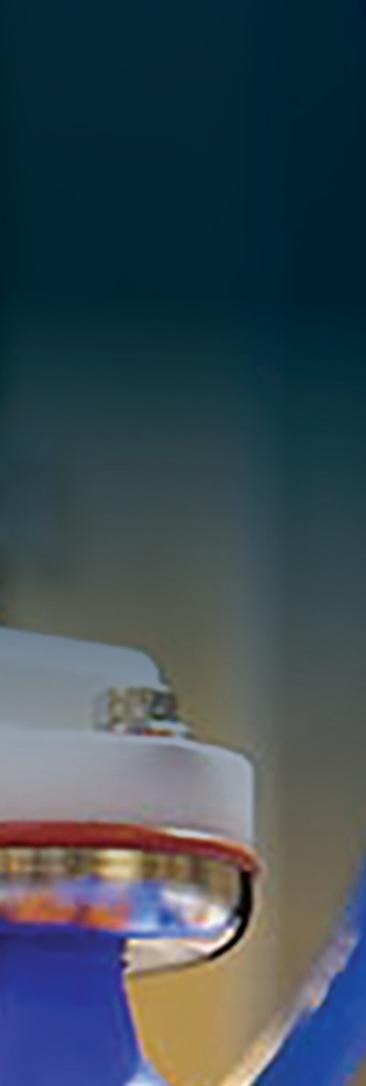
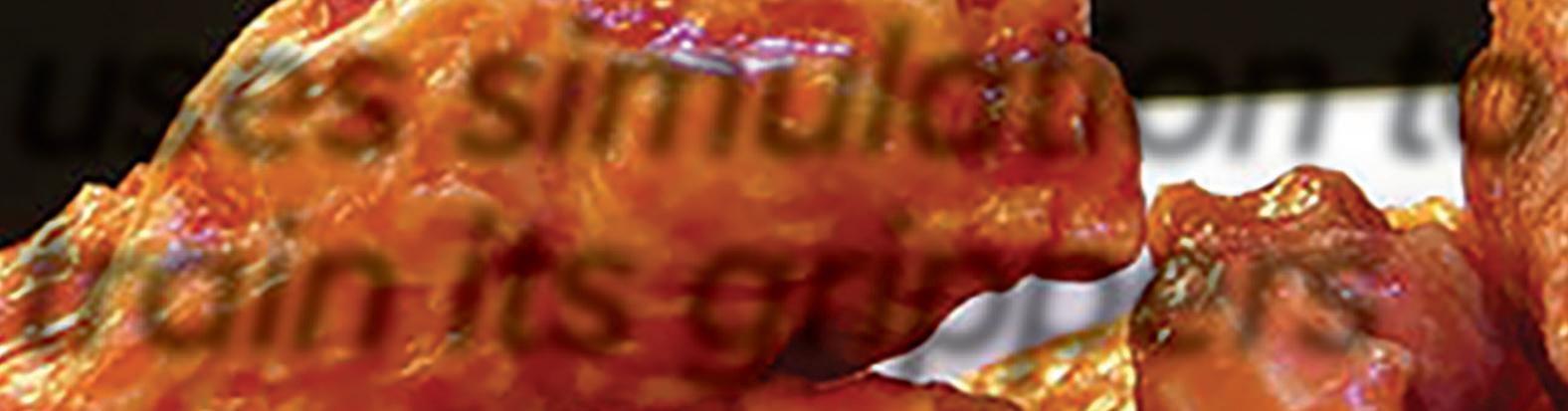

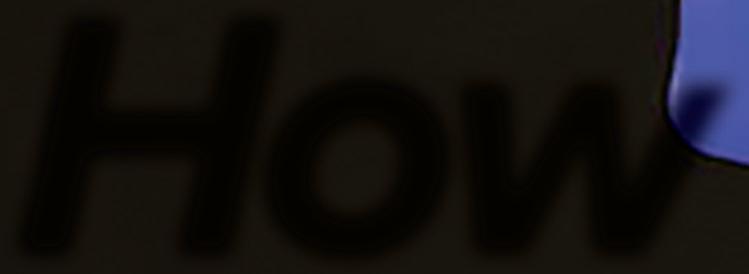
different lighting scenarios.
Soft Robotics applies NVIDIA Isaac Sim’s synthetic data to food processing automation to improve safety and increase production.
Developers have been striving to close the gap on robotic gripping for the past several years, pursuing applications for multibillion-dollar industries. Securely gripping and transferring fast-moving items on conveyor belts holds vast promise for businesses.
Soft Robotics, a Bedford, Mass. startup, is harnessing NVIDIA Isaac Sim to help close the sim-to-real gap for a handful of robotic gripping applications. One area is perfecting gripping for pick and placement of foods for packaging. Food packaging and processing companies are using the startup’s mGripAI system which combines soft grasping with 3D Vision and AI to grasp delicate foods such as proteins, produce, and bakery items without damage.
“We’re selling the hands, the eyes and the brains of the picking solution,” said David Weatherwax, senior director of software engineering at Soft Robotics.
Unlike other industries that have adopted robotics, the $8 trillion food market has been slow to develop robots to handle variable items in unstructured environments, says Soft Robotics.
The company, founded in 2013, recently landed $26 million in Series C funding from Tyson Ventures, Marel and Johnsonville Ventures.
Companies such as Tyson Foods and Johnsonville are betting on the adoption of robotic automation to help improve safety and increase production in their facilities. Both companies rely on Soft Robotics technologies.
Soft Robotics is a member of the NVIDIA Inception program, which provides companies with GPU support and AI platform guidance.
Soft Robotics develops unique models for every one of its gripping applications, each requiring specific data sets. And picking from piles of wet, slippery chicken and other foods can be a tricky challenge.
Using Omniverse and Isaac Sim, the company can create 3D renderings of chicken parts with different backgrounds, like on conveyor belts or in bins and with different lighting scenarios.
The company taps into Isaac Replicator to develop synthetic data, generating hundreds of thousands of images per model and distributing that among an array of instances in the cloud. Isaac Replicator is a set of tools, APIs, and workflows for generating synthetic data using Isaac Sim.
It also runs pose estimation models to help its gripping system see the angle of the item to pick.
NVIDIA A100 GPUs onsite enable Soft Robotics to run split-second inference with the unique models for each application in these food-processing facilities. Meanwhile, simulation and training in Isaac Sim offer access to NVIDIA A100s for scaling up workloads.
“Our current setup is fully synthetic, which allows us to rapidly deploy new applications. We’re all in on Omniverse and Isaac Sim, and that’s been working great for us,” said Weatherwax.
A big challenge at Soft Robotics is solving issues with occlusion for an understanding of how different pieces of chicken stack up and overlap one
another when dumped into a pile. “How those form can be pretty complex,” Weatherwax said.
Glares on wet chicken can potentially throw off detection models. “A key thing for us is the lighting, so the NVIDIA RTXdriven ray tracing is really important,” he said.
But where it really gets interesting is modeling it all in 3D and figuring out in a split second which item is the least obstructed in a pile and most accessible for a robot gripper to pick and place. Building synthetic data sets with physics-based accuracy, Omniverse enables Soft Robotics to create such environments. “One of the big challenges we have is how all these amorphous objects form into a pile,” Weatherwax said.
Production lines in food processing plants can move fast. But robots deployed with application-specific models promise to handle as many as 100 picks per minute.
Still a work in progress, success in such tasks hinges on accurate representations of piles of items, supported by training data sets that consider every possible way items can fall into a pile.
The objective is to provide the robot with the best available pick from a complex and dynamic environment. If
Meat-packing companies rely on lines of people for processing chicken, but like so many other industries they have faced employee shortages.
food items fall off the conveyor belt or otherwise become damaged then it is considered waste, which directly impacts yield.
Meat-packing companies rely on lines of people for processing chicken, but like so many other industries they have faced employee shortages. Some that are building new plants for food processing can’t even attract enough workers at launch, said Weatherwax.
“They are having a lot of staffing challenges, so there’s a push to automate,” he said.
The Omniverse-driven work for food processing companies has delivered a more than 10X increase in its simulation capacity, accelerating deployment times for AI picking systems from months to days.
And that’s enabling Soft Robotics customers to get a grip on more than just deploying automated chickenpicking lines — it’s ensuring that they are covered for an employment challenge that has hit many industries, especially those with increased injury and health risks.
“Handling raw chicken is a job better suited for a robot,” he said. RR
The SHA-IDT Series is a family of compact actuators that deliver high torque with exceptional accuracy and repeatability. These hollow shaft servo actuators feature Harmonic Drive® precision strain wave gears combined with a brushless servomotor, a brake, two magnetic absolute encoders and an integrated servo drive with CANopen® communication. This revolutionary product eliminates the need for an external drive and greatly simplifies wiring yet delivers high-positional accuracy and torsional stiffness in a compact housing.
• Actuator + Integrated Servo Drive utilizing CANopen® communication
• 48 VDC nominal supply voltage
• A single cable with only 4 conductors is needed: CANH, CANL, +48VDC, 0VDC
• Zero Backlash
• Panel Mount Connectors with radial and axial options
• Dual Absolute Encoders
• Output Encoder: 16bit (65,536 cpr) resolution
• Input Encoder: 17bit (131,072 cpr) resolution
• Control Modes include: Torque, Velocity, and Position Control, CSP, CSV, CST
Like many companies that turn to automation, FMO Surface had difficulty attracting human employees for monotonous yet demanding tasks.
FMO Surface, a family-owned company that specializes in finishing plastics, was founded in 1999 in Lemgo, Germany and employs 75 people. The company’s customers come from a variety of industries, including automotive, electronics, aerospace and mechanical engineering. Manufacturers that produce bicycles and household appliances also make use of FMO Surface’s services.
Because approximately seven million plastic bus connectors are laser-marked with eight-digit data matrix codes (DMC) here every year before being installed in controllers, FMO Surface began to automate various related processes several years ago. Companies such as FMO Surface find it increasingly difficult to attract human employees for monotonous yet demanding tasks such as checking DMCs.
It found a job for its new LBR iisy, a collaborative robot arm from KUKA, in bus connector quality control. Because multiple components are marked with a
DMC and are dependent on one another, reliability is of decisive importance for the traceability of an entire module. For this reason, the readability and completeness of the Data Matrix codes require special quality control attention, previously carried out manually with a scanner by human employees at FMO Surface.
“We save an enormous amount of time using the LBR iisy because we no longer have to scan each part individually,” said Tim Hertz, laser department foreman, FMO Surface. “And if the cobot reports a fault, we don’t have to open a cage or stop an entire system; we simply remove the defective part and replace it.” This type of quality inspection helps keep the price of production and finishing down.
Solution
Equipped with dual Keyence cameras, the LBR iisy cobot checks DMCs. Each tray that slides under the LBR iisy contains 200 plastic parts. One camera carries out the quality inspection with associated software, while the second camera assesses codes for completeness.
“The first step spot checks the quality of the codes on the basis of 20 parts,” explained Hertz. “If everything is OK, the cobot moves over the tray again to check whether all 200 parts are present and all codes are readable.”
If the robot finds an issue with a code, it stops and points out the affected bus connector. A human colleague then replaces the faulty part; the robot checks the tray again and ideally releases it. This human-robot collaboration ensures maximum safety and efficiency.
With the aid of the KUKA smartPAD pro and the KR C5 microrobot controller, even employees with virtually no experience in robot programming can operate and train the cobot.
“The LBR iisy runs on the basis of the new iiQKA.OS operating system, which makes it easy to install, configure and program,” said KUKA’s Robert Korte. The cobot not only is up and running in just a few minutes but can adapt to new challenges equally quickly. That’s an enormous advantage for Fest: “We don’t have engineers here, so ease of integration is all the more important.”
Bastian Fest, managing director of FMO Surface, met Korte at a trade show and learned about the advantages of the LBR iisy collaborative robot. Fest then took a closer look at the LBR iisy at KUKA’s branch office in Siegen and decided to purchase it.
“The LBR iisy combines several factors that we require: flexibility, ease of programming and suitability for collaborative operation. That is why we purchased it, even without actually knowing where exactly we wanted to use it,” said Fest of this seemingly unusual approach.
Say hello to the
The safest cobot on the marketplace, delivered in 4 weeks or less.
Six-axis articulation
Force torque sensors on each axis
PLe CAT 4 Safety Rating
1700mm Reach 25kg Payload
The employees at FMO Surface were enthusiastic about the new colleague right away.
“Thanks to the safety features, collaboration with people in a single workspace is possible,” said KUKA sales engineer Robert Korte.
In the past, this type of quality control for DMCs was much more time-consuming. “When checking for completeness, we had to scan each part individually,” said Hertz. For this, an employee had to take the components out of the tray and subsequently put them back again. Today, with the LBR iisy, this task is performed much faster and more precisely.
FMO said the LBR iisy cobot could also provide valuable services in pad printing in the near future. Furthermore, the company hopes to make use of the larger versions of the LBR iisy with their payload
capacities of 11 and 15 kilograms.
FMO Surface has also collaborated with KUKA on using a KR CYBERTECH nano (KR 10 R1420) robot arm for palletizing and to tend a laser system. Two years later, FMO Surface added another industrial robot om the KR CYBERTECH series to turn over, measure and laser plastic parts to be finished.
“Particularly in view of the shortage of skilled workers, automation plays an important role for a medium-sized company like ours,” said FMO Surface. RR
Turnkey or custom automation solutions for less Gantry Robots Delta Robots
7th Axis for Robots
Gearboxes & Motors Control & Software
X Low-cost automation solutions
X • ROI after 3 to 18 months
X • Free training courses
X • No minimum order quantity
X • Free software packages
X • RBTX online robotic marketplace
Co-development projects where
The past few years have seen many organizations implement techdriven changes at a rapid pace. As society becomes more digital, embracing technology and effectively managing new processes is key to the success of almost every business.
With rapid workplace transformation evident across industries, whether that’s moving to hybrid working or adopting new technologies, what can we expect from 2023? Here are five predictions for the coming year.
In recent years, we have witnessed the development of many different types of sophisticated technologies. Advances in robotics, machine learning and other technologies have increased the pace of this change tenfold. While these promise to change or revolutionize the business world, all technology companies suffer from the same problem – they can’t be good at everything.
In the world of robotics, this is no different. Creating a robotic system requires hardware development, software development, application
development, sensors, and interfaces to name a few. That’s why 2023 will be the year of turnkey solutions.
Original equipment manufacturers (OEMs) – companies creating new applications and products around existing technologies – will lie at the heart of this. They are able to drive innovation by combining technologies to deliver complete solutions for the most common applications, such as welding and palletizing. The result? Automation will become more sophisticated yet more straightforward to use than ever before.
Enabled Robotics, an OEM based in Denmark, is a great example of how this works. Since 2016, the company has been working to combine two types of cutting-edge technology by mounting
collaborative robot arms (cobots) onto autonomous mobile robots (AMRs). This hybrid technology is now operating in industry, warehouse management and production and bringing robotics to service applications and hospital intralogistics.
Ultimately, these out-of-the-box solutions make it easier for companies to integrate crucial technologies and there is no limit to the imaginative ways companies will find to bring robots alongside humans in the world of work.
Traditional industrial robots remain important in manufacturing, but we are seeing a trend towards deploying more flexible models of production. This is largely due to the fact that traditional industrial robots are typically large and fixed and entail complex deployment.
In contrast, cobots can perform a similar range of activities to traditional industrial robots but are smaller, lighter and easier to deploy. They are designed to work alongside humans and are better suited to environments that require flexibility and adaptability. On top of this, they are most cost-effective for businesses looking to deploy automation – a key consideration as we move into 2023.
The cobot industry is projected to grow to USD 2.2 billion by 2026 (The Collaborative Robot Market 2022 Report, Interact Analysis). As cobots continue to change the way work is done in applications such as packing, palletizing, welding and assembly, in 2023 we will see even larger companies turning to lightweight cobots to increase modularity in their production. Robot weight and versatility will be key specifications for those looking for new automation solutions and we will see more reconfigurable robotic work cells than ever before.
As more companies move towards cobot automation, many will still want to handle heavy payloads. The good news is that we have recently seen the introduction of several higher payload, longer-reach cobots. In 2023, these will continue to transform parts of the manufacturing industry, improving the working lives of many employees. Universal Robots introduced in 2022 a new cobot, the UR20, which is built for higher payloads, faster speeds, and superior motion control all within a lightweight, small-footprint system. The 20 kg payload capacity will transform
industries such as palletizing while its 1750 mm reach is eagerly anticipated for use in welding. Manufacturers looking for that extra flexibility will find the robot light enough to be unbolted and relocated or attached to a heavy base with wheels. This will create new possibilities for applications and will drive innovation across the board. The UR20 will be delivered to customers in 2023.
The recent IFR World Robotics Report showed industrial robot installations reached an all-time high in 2021, increasing by 31% over the previous year. Overall, worldwide annual robot installations between 2015 and 2021 have more than doubled. Although growth in 2022 seems to be slower across the sector, this is largely down to global uncertainties triggered by the pandemic and scarcity of electronic components.
We expect the upward trend of cobot automation to resume in 2023. Why? Because businesses across the world are facing labor and skills shortages and, despite the day-to-day challenges facing industry right now, we are in the midst of a transition towards industry
5.0 where working alongside robots will create more human-centric, sustainable and resilient businesses.
5. Customers will be found at the heart of product development
Although we talk extensively about robot collaboration in the workplace, human collaboration is what drives innovation.
Customers understand their own needs better than anyone else and, as the automation market has matured, are better placed than ever before to offer valuable input on their requirements. This means robotics companies will involve customers much more in product development. It is why Universal Robots has reorganized its product creation teams and is focusing heavily on understanding the problems customers are facing before designing solutions.
Co-development projects where robotics companies and customers work together in developing specific solutions
are also bound to increase in 2023 and beyond. Ultimately these allow customers to directly influence the product they are buying, while at the same time delivering valuable feedback for the robotic companies – meaning they will be able to launch a product to the benefit of the whole market.
Now more than ever, businesses need to innovate constantly and remain adaptable in order to survive and expand. As we head into 2023, they will rely ever more on technology and innovation to break new ground with turnkey solutions at the heart – all of which make the year ahead an exciting time for automation. RR
Anders Billesø Beck leads the development of cobot technologies to keep global businesses agile, productive and innovative. Anders is vice president for strategy and innovation at Universal Robots, the global leader in flexible automation, and holds a Ph.D. in robotics om DTU, the Technical University of Denmark.
He is a former elite swimmer and member of the Danish national team, and he has also held leading positions at the Danish Technological Institute. Anders combines his scientific background with contributions to the global collaborative automation industry to change the way the world works.
So much happens between issues of R&D World that even another issue would not be enough to keep up. That’s why it makes sense to visit rdworldonline.com and stay on Twitter, Facebook and Linkedin. It’s updated regularly with relevant technical information and other significant news for the design engineering community.
According to researchers at Carnegie Mellon University (CMU), even simple robotic grippers can solve some complex manipulation tasks. Sometimes they just need a little help om their environment by pushing an object against a table or a wall.
This is known as “Extrinsic Dexterity.” The CMU team said previous work in extrinsic dexterity used careful assumptions about contacts that impose restrictions on robot design, robot motions, and the variations of the physical parameters. They tried to improve upon these limitations by developing a system based on reinforcement learning (RL).
They studied the task of “Occluded Grasping,” which aims to grasp an object in configurations that are initially occluded; the robot needs to move the object into a configuration om which these grasps can be achieved. The policy learns emergent behaviors of pushing the object against the wall to rotate and then grasp it without additional reward terms on extrinsic dexterity.
“This research may open up new possibilities in manipulation with a simple gripper,” said study Wenxuan Zhou at Carnegie Mellon University. “Potential applications include warehouse robots or housekeeping robots that help people to organize their home.”
The team used reinforcement learning to train a neural network and tested the system in the MuJoCo physics simulator. The simulated robot attempted to grasp objects and was rewarded when successful.
The researchers then zero-shot transferred the technology to a physical robotics system, which consisted of a Frank Emika robotic arm and a parallel gripper. The robot grasped items confined within an open bin that were initially oriented in ways the robot couldn’t handle. It then needed to figure out how to use its environment to create success picks, for example, by pushing an item against the wall of the bin to reorient said object.
Here’s an example of how the gripper could use its environment to help grasp an object. The gripper first moves close to the object and makes contact on the side of the object with the top finger. It then pushes the object against the wall to rotate it. During this stage, the gripper
With the exploitation of external resources such as contact surfaces or gravity, even simple grippers can perform skillful maneuvers that are typically studied with a multifingered dexterous hand.
| Carnegie Mellon Universityusually maintains a fixed or rolling contact with the object, but sliding also occurs. The object might have sliding or sticking contacts with the wall and the ground. After the gripper has rotated a bit further and the bottom fingertip is below the object, the gripper will let the object drop on the bottom finger. After that, the gripper will try to match the desired pose more precisely. At this point, the policy has executed the grasp successfully and it is ready to close the gripper.
According to the researchers, one of the key decisions in this strategy is to use the top finger to rotate the object instead of the bottom finger. One might suppose an alternative approach which is to use the bottom finger to scoop the object against the wall and then directly roll the finger underneath the object to reach the grasp. However, this strategy is not physically feasible on the parallel gripper due to the limited degree of freedom of the finger.
Another successful strategy is to flip the object to stand on its side and then move to the grasp. This strategy relies on the fact that the object remains stable after the rotation.
The researchers tested the system on items that varied in weight, shape and slickness, including cardboard boxes, plastic bottles and a container
According to researchers at Carnegie Mellon University (CMU), even simple robotic grippers can solve some complex manipulation tasks. Sometimes they just need a little help from their environment by pushing an object against a table or a wall.
CGI Motion standard products are designed with customization in mind. Our team of experts will work with you on selecting the optimal base product and craft a unique solution to help di erentiate your product or application. So when you think customization, think standard CGI assemblies.
Connect with us today to explore what CGI Motion can do for you.
of whipped cream. According to the researchers, the simple grippers successfully grasped items 78% of the time.
The researchers also employed a lowlevel controller due to the fact that they expected the agent to use extrinsic dexterity which involves rich contacts among the gripper, the object and the bin. They choose operation spacecontrol (OSC) as the lower-level controller to execute the policy output which operates at a higher frequency than the RL policy. Given a desired pose of the end-effector, OSC first calculates the corresponding force and torque at the end-effector to minimize the pose error.
Then, the desired force and torque of the end-effector will be converted into desired joint torques according to the model of the robot. We choose relatively low gains so that the controller becomes compliant in the end-effector space. There are two benefits of a compliant OSC in such a contact-rich manipulation task with extrinsic dexterity:
“First, being compliant in end-effector space allows safe execution of the motions without smashing the gripper on the objects or the bin. Limiting the delta pose and selecting proper gains will limit the final force and torque output of the end-effector. If we use a controller that is compliant in the joint configuration space instead, we will not have direct control over the maximum force the end-effector might have on the object and the bin. Second … using OSC as the low-level controller might speed up RL training and improve sim2real transfer for contact-rich manipulation.”
Next steps
One limitation of this work, the researchers admitted, is that the policy was trained with box-shaped objects. Although it may generalize to other shapes to some extent as shown in the experiments, the policy might be improved by including other shapes during training.
In addition, the pose of the object alone may not be sufficient to generalize to novel objects. The CMU team said that using a better representation of the shape, such as a point cloud or keypoints, could improve generalization across shapes. However, these changes would also increase the training complexity.
Another limitation is that we assume a reasonably accurate robot and gripper model, in terms of geometries, kinematic and dynamic parameters. It would be interesting to explore how to extend the method to transfer across robots and grippers.
Despite the simplicity of the proposed method, the researchers stress the following two key takeaways.
“First, we provide a concrete example that a simple gripper can do much more than pick-and-place while being cheaper and easier to maintain than a dexterous hand, following previous work in extrinsic dexterity,” the team said. “We envision more future work in this direction in manipulation. Second, RL can be a good option to generate policies with emergent extrinsic dexterity, and sim2real transfer works reasonably well with our proposed system. Our work takes a step towards deploying contactrich policies with a simple gripper in the real world.” RR
At CGI we serve a wide array of industries including medical, robotics, aerospace, defense, semiconductor, industrial automation, motion control, and many others. Our core business is manufacturing precision motion control solutions.
CGI’s diverse customer base and wide range of applications have earned us a reputation for quality, reliability, and flexibility. One of the distinct competitive advantages we are able to provide our customers is an engineering team that is knowledgeable and easy to work with. CGI is certified to ISO9001 and ISO13485 quality management systems. In addition, we are FDA and AS9100 compliant. Our unique quality control environment is weaved into the fabric of our manufacturing facility. We work daily with customers who demand both precision and rapid turnarounds.
CS Hyde Company
FEP Film: The transparent film on the bottom of the resin tank
FEP Film has become an ideal solution for SLA and DLP printers as a surface film for the bottom of the resin tank. Coupled with clarity and release properties, FEP is an ideal barrier film that allows light transmission while extending stability and strength for resin 3D printing.
CS Hyde is a stock supplier and converter of FEP & PFA film available in a variety of thicknesses. We also o er specialty adhesive lamination to FEP film, as well as custom width slitting, sheeting, and tight tolerance die cutting. Other polymer films available include ULTEM® PEI, TPX®, Kapton®, Mylar®, and many other engineering and high-performance plastics.
CGI Inc. 3400 Arrowhead Drive Carson City, NV 89706
Toll Free: 1.800.568.4327
Ph: 1.775.882.3422
Fx: 1.775.882.9599
WWW.CGIMOTION.COM
Contact
www.cshyde.com
1.800.461.4161
Known for their dexterity and safety, Doosan Robotics H-SERIES cobots are the most powerful in the marketplace, providing unrivaled and precise performance in palletizing. Featuring a maximum reach of 1700mm and 25kg payload, Doosan’s H-SERIES not only has a higher payload and longer reach than competitors, but it can also safely perform highly complex tasks using precise force and compliance control based on the 6-axis force torque sensors. With the highest collision sensitivity in the industry our cobots can also be trusted to share space with personnel, all while enhancing production output and maximizing labor. Doosan Robotics also delivers in a fraction of the time of industry competitors, with an average delivery time of four weeks.
Doosan Robotics
doosanrobotics.com
The drive wheels on Autonomous Mobile Robot platforms benefit from the inherent characteristics of harmonic planetary technology; primarily, smoothness of travel, backdrivability, and an e ciency curve that does not degrade over time. The integral cross roller bearing construction contributes to an excellent balance of torque density, sti ness, and radial load support in a compact and reliable package. Available in dozens of standard reduction ratios, these low backlash drive trains include motor adaptation as required.
3D printed robotic grippers from igus® utilize wearresistant iglide® 3D printing materials, with wear rates comparable to similar injection-molded components. iglide® 3D printing materials contain embedded lubricants, eliminating the need for routine maintenance and making them resistant to dirt and dust. 3D printing allows for complex geometries not normally possible with injection molding, ensuring you can find the exact solution required for your application. Choosing 3D printed grippers can also save up to 85% in costs and reduce manufacturing time by about 70%. Whether you need a single prototype, or plan to outfit an entire line of robots, igus® can provide a solution — no minimum order quantity required!
Here at Lin Engineering, we find solutions to your problems by focusing on three basic elements: Find, Optimize, and Integrate. There are such a vast number of products on the market that just narrowing the options can be di cult. Our engineers will help you find the motor you need. The motor may then be optimized for your application by changing the winding, magnets, bearings, and more. We work with your team throughout this process to configure the motor to your application so it can be seamlessly integrated within your product or assembly.
Contact Info: Sarah Phann sphann@igus.net
Contact info: Lin Engineering 16245 Vineyard Blvd. Morgan Hill, CA 95037 https://www.linengineering.com/ 1.408.919.0200
Today’s AGVs must be compact and functional robots which are able to move vertically and carry heavy loads. These AGVs cannot fail, and so the choice of their motorization is crucial. There are 5 key points to consider when motorizing an AGV.
1. Choose compact motorization where possible - Drives must fit into restricted spaces, as they are sometimes integrated into existing trucks. A small footprint is critical for applications in logistics.
2. Focus on ease of use – select a plug-and-play solution.
3. Opt for fast delivery of your motor solution
4. Base the design on modularity - Not all AGVs do the same job and therefore having the flexibility to select a solution to match needed specifications is essential.
5. Prioritize safety – select motor options with integrated sensors.
maxon’s IDX motor has a diameter of only 56 mm, its performance is equivalent to that of a motor with a footprint 25% larger. The IDX motorization thus combines performance in a compact size and ideal for AGVs.
Go to Drive.tech for more details. Visit www.maxongroup.us for more maxon solutions.
Motus Labs Introduces Orbital Flex Design™: Motus Lab’s patent-pending Orbital Flex Design™ (OFD) is a new gear design which focuses on delivering zero backlash and high torque density gear solutions. The solid rigid cup enables OFD to remain consistent for the life of the gear without the common performance degradation found in most gear solutions.
The Motus Labs Orbital Flex Design™ (OFD) delivers:
• Superior performance
• Lower cost of ownership for robotic and motion control solutions
• Improved ROI for customers
Why accept a standard product for your custom application?
NEWT is committed to being the premier manufacturer of choice for customers requiring specialty wire, cable and extruded tubing to meet existing and emerging worldwide markets. Our custom products and solutions are not only engineered to the exacting specifications of our customers, but designed to perform under the harsh conditions of today’s advanced manufacturing processes. Cables we specialize in are LITZ, multi-conductor cables, hybrid configurations, coaxial, twin axial, miniature and micro-miniature coaxial cables, ultra flexible, high flex life, low/high temperature cables, braids, and a variety of proprietary cable designs. Contact us today and let us help you dream beyond today’s technology and achieve the impossible.
Advancing innovation for over 100 years Contact info: New England Wire Technologies www.newenglandwire.com 603.838.6624
Robots are flexible and adaptable. Quickly re-tasking robots for job variety can be challenging.
Some common solutions: Changing workpieces – Quick-change gripper fingers and gripper changeouts are easily automated for workpiece variety or changing workpiece characteristics during manufacturing.
Flexible machine table fixtures – Robots are widely identified for their ability to handle workpieces. They also excel at automatically replacing fixtures and other peripheral tooling.
Automating multiple tasks – Use the robot to accomplish a secondary task. Instead of remaining idle during machining, the robot can automatically deburr workpieces.
Adjustable custom tooling – Use dove tails and adjustable mountings in EOATs to expand tools for changing conditions or reach requirements.
Many standard solutions are available - make the most of your investment with automation expert support today!
SCHUNK: 211 Kitty Hawk Drive, Morrisville, NC 27560 919-572-2705 info@us.schunk.com