WAREHOUSE AUTOMATION
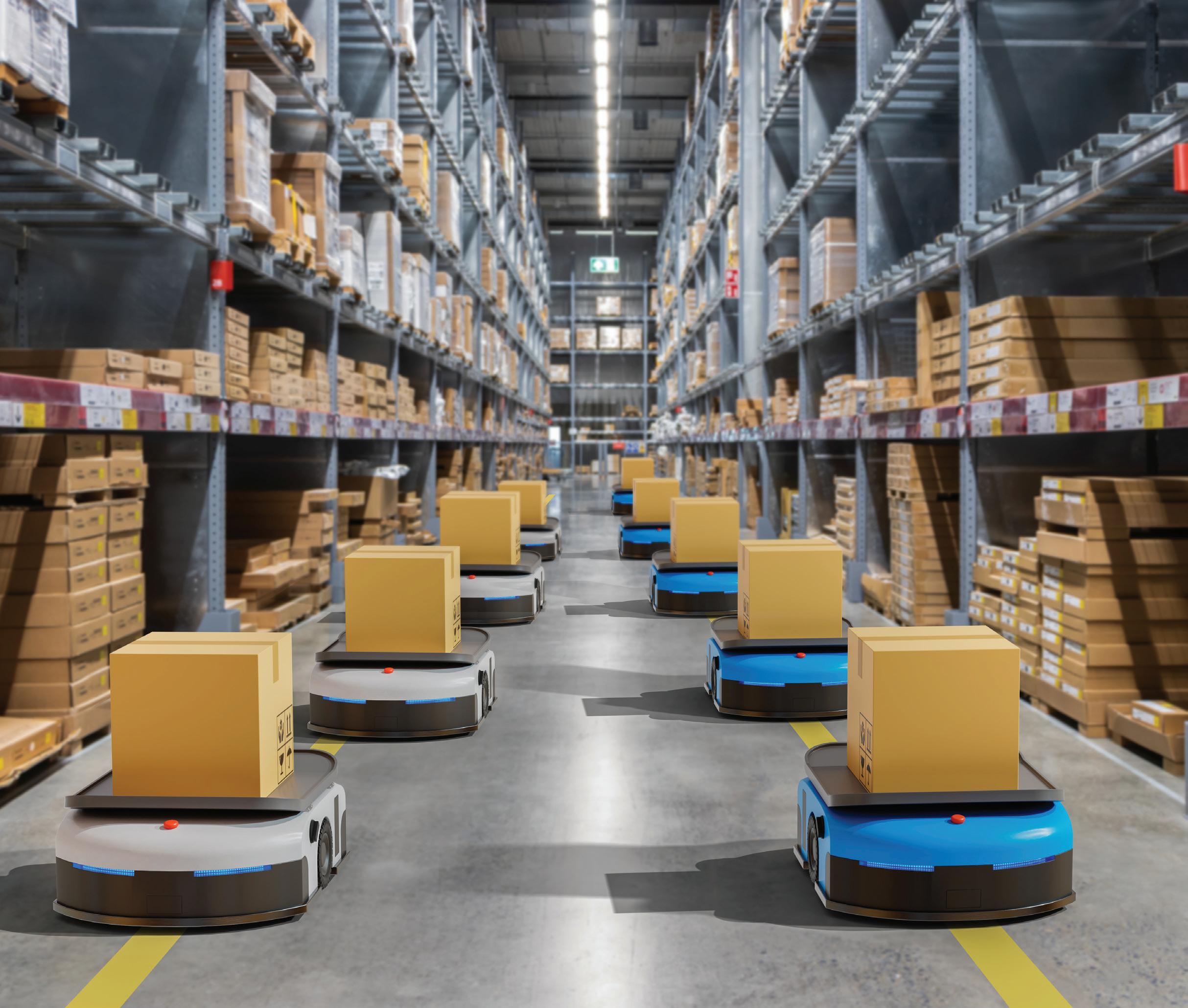
Low voltage compact motion: AMI812x integrated servo drive
www.beckhoff.com/ami8100
Perfect for AS/RS shuttles and AMRs: integrated servo drive for compact drive technology (up to 48 V DC) combines highly compact servomotor, output stage and fieldbus connection for all motion requirements in the power range up to 400 watts for single axes or with daisy-chain solutions in the machine supports cabinet-less concepts with compact footprints
IP65 protection degree possible with sealing ring option Safe torque off (STO) safety over FSoE (Safety over EtherCAT) reduces installation and integrates seamlessly into safety solutions
Beckhoff offers a complete, compact control solution for mobile equipment including a range of compact motion solutions for BLDC, MDR, servo technology and more.
76
Automated storage and retrieval systems are a key enabler of the next-day delivery we’ve come to expect from online retailers. But like other types of automation, AS/RS equipment must meet the customer’s objectives for safety, footprint, and energy e ciency.
82
Amazon pushes the envelope on automation
Amazon continues to be a leader in automating warehouse operations, and that includes not only using existing technology but developing its own products and buying manufacturers of interest.
86
DHL’s Sally Miller on using robotic fleets
DHL is using robotics to support numerous warehousing and logistics tasks. The company innovates its logistics workflow and the tools and technologies deployed in DHL distribution centers around the world, as it continually improves e ciencies.
Say hello to the H-SERIES:
the only cobot with a 25kg payload and a 1700mm reach. It’s time to meet your new heavy-duty best friend.
Everything you buy online or in-store is stored in a warehouse at some point. The pandemic hastened the acceptance of e-commerce by causing consumers to stay at home and shop online. According to research firm Interact Analysis, 50,000 new warehouses will be built worldwide over the next six years.
Automated warehouse person-to-goods supplier Locus Robotics reported the billionth pick by a Locus robot this fall. This is just one example where warehouse automation is growing at an accelerating pace.
Because of these macroeconomic trends, warehouse automation remains a top priority, due in part to labor shortages and increasing demand om consumers. Logistics and warehousing are data-intensive processes that track inventory and material movement at every stage of the supply chain. The so ware and cloud-based services that track the logistics workflow om supplier to customer are increasingly being assisted by artificial intelligence-based algorithms that can “see” trends in the data — and make adjustments in real-time.
There is demand for all of the parts that go into warehouse automation, as well as for complete “turnkey” solutions. This special section looks at some of these areas as well as the technologies that make them possible.
In general, at the Mobile Robot Guide and The Robot Report, we follow most of these trends in the market and keep you up to date on the latest announcements — while our sister publication, Design World, focuses on the fascinating engineered components that make all of this automation possible.
Some of the areas where we see the greatest rates of innovation include:
• Autonomous mobile robots
• Data capture and the use of IOT devices in the warehouse
• Automated storage and retrieval systems
• Robotic sortation and piece picking
• Grocery order fulfillment solutions, and
• So ware and cloud-based services.
We hope that you find this first special section on Warehouse Automation a useful resource as you research, plan, and build new solutions for this exciting market.
Mike Oitzman EditorThe Mobile Robot Guide | The Robot Report
Automated storage and retrieval systems are a key enabler of the nextday delivery we’ve come to expect from online retailers. But like other types of automation, AS/RS equipment must meet the customer’s objectives for safety, footprint, and energy e ciency.
Years ago, as you drove through industrial suburbs in almost any midsized city in America, you would encounter huge warehouses and distribution centers, housing thousands of items for wholesale distribution or retail operations. And if you were a manufacturer of motion control components or systems, you passed right by these giant industrial buildings without a second thought, because you knew that virtually all of the stocking, picking, and transporting going on inside was being done manually.
Fast-forward to the present, and the explosion of e-commerce over the past 15 years has caused a fundamental shift in the way warehouses and distribution centers function. The “Amazon e ect” on consumer behavior has resulted in buyers — both B2C and B2B — who want their purchases delivered in shorter and shorter timeframes, putting pressure on warehousing and distribution providers to speed up and streamline their operations. The solution to achieve these goals, while maintaining profitability, is more automation — or, more specifically, automated storage and retrieval systems (AS/RS).
Storing and retrieving 40-ft long sections of carbon fiber required conveyors that could extend into and out of the storage area. Guide wheels and
tracks were used to create the necessary telescoping conveyor sections while keeping overall height to a minimum.
Warehouse operators, distribution centers, and manufacturing facilities implement AS/RS equipment for a variety of reasons. For warehouses, the primary concern may be to maximize storage density in the available space. Distribution centers often see increased customer satisfaction through shorter delivery times, and manufacturing operations use AS/RS to improve workflow and maintain better control over inventory.
Regardless of their customers’ reasons for automating storage and retrieval functions, when manufacturers of AS/RS equipment choose motion and motion control systems, three important criteria stand out: safety, footprint, and energy e ciency.
Putting safety first
When handling a load that’s located 40ft (or higher) above the floor — whether that load is a 10-lb bin or a 500-lb pallet — there’s a significant risk of injury to people and damage to the product or equipment if something goes wrong.
And in many cases, the transporting portion of an AS/RS is moving at very high speeds, increasing the possibility of injury or damage.
Automated storage and retrieval equipment is intended to operate with minimal human interaction until the final point of delivery. But because of the loads, speeds, and heights at which these systems operate, human safety is especially critical … not to mention the safety of the product being transported. A single bin or pallet of finished goods can be worth tens of thousands of dollars.
A combination of mechanical and electrical/electronic means are used to ensure safety in storage and retrieval systems. Vertical axes typically incorporate a friction break, providing a mechanical means of protection in case the vertical driving belt breaks. It’s also typical for AS/RS manufacturers to require an electromagnetic brake on the vertical motor for protection in case of an electrical failure.
Safety is also addressed in the higher-level control system. For many manufacturers, the use of safety PLCs
is standard on our AS/RS equipment. It can be especially important during maintenance and troubleshooting, when human interaction is required.
Similarly, drive-based safety — with integrated STO (safe torque o ), SS1 (safe stop 1), or other safe stop functions — is becoming pervasive in the industry. Some AS/RS equipment manufacturers are moving one step further, by using motion controllers with safety functions that run on the fieldbus, replacing hardwired safety logic. This makes the system more cost-e ective and more e cient.
One of the principal reasons for implementing automated storage and retrieval is to put warehouse and inventory space to better use. For a lot of customers, expanding storage capacity is one of the key objectives when setting up an AS/RS. Thus, it’s no surprise that manufacturers of AS/RS equipment strive to use the smallest components and most compact systems possible.
For example, in AS/RS applications, you typically want a motor with a high torque-to-size ratio. However, a designer needs to carefully define the motion profile to ensure you’re not oversizing the motor. A motor with a continuous torque rating that meets the application’s peak torque requirements would be clearly oversized.
Similarly, when choosing linear guides and systems, compactness is one of the key criteria for AS/RS manufacturers. In shuttle systems, this typically means using telescoping guides on the horizontal axes, which retrieve and replace bins or trays from the storage rack. The application’s bin density strategy — that is, the number of bins that are stacked one behind the other in the storage rack, or the number of “bins deep” — dictates the reach needed by the guide rails, which can be as much as 3 ft for a single bin. ● WH
A typical fixed-aisle AS/RS configuration. Goods are stored on fixed racks in totes or cartons. Operators can either pick the goods based on lights indicating the desired tote or carton, or the goods can be retrieved by lift and shuttle systems and delivered to the operator (referred to as “goods-to-operator”) by means of a roller conveyor.
Automated storage and retrieval systems use sophisticated controls to store, retrieve, and deliver materials to specified locations. The Material Handling Industry identifies six main types of AS/RS equipment, which can be grouped into three categories:
1. Fixed-aisle (F/A) storage and retrieval systems are constructed with one or more aisles of storage racking, which are served by a moving structure — often a crane or shuttle — that can reach each storage location and place or retrieve loads with a telescoping arm.
• Unit-load AS/RS: These are generally the largest AS/RS systems, typically used for handling pallets or pallet-sized materials weighing 1000 lb or more.
• Mini-load AS/RS: Rather than handling pallets, mini-load systems handle totes, cartons, or trays weighing less than 1000 lb.
• Micro-load AS/RS: Micro-load systems deal with loads that are typically less than 100 lb, stored in small totes or trays.
2. Vertical lift modules (VLMs) have vertical columns of trays or storage bins in both the back and the front of the module, with a mechanism in the center to automatically insert or extract materials.
3. Carousels are characterized by a series of bins that rotate horizontally or vertically.
• Horizontal carousels: These systems rotate horizontally around a track to position the bin in the picking position.
• Vertical carousels: These rotate vertically and are typically enclosed on all sides to secure the materials being transported. The requested bin or shelf is presented to a window, and products are picked though this window.
Energy e ciency starts with the selection of individual components and sub-systems. For example, when a product is being retrieved, the vertical axis is held in position for a certain period of time. To maximize energy e ciency, you should choose a motor that is able to hold the vertical load with minimal power. Another way to improve e ciency is to capture regenerative energy — especially from vertical axes — and feed it back to the power source or store it in battery packs.
Mechanical components typically contribute to energy e ciency by way of lowering the moved mass, and therefore, the inertia of the system. Vertical lifts that were once driven by chains have migrated to steel-reinforced timing belts and pulleys. As AS/RS equipment has evolved, the required speeds and accelerations of the horizontal and vertical axes have increased greatly.
Other examples of mechanical components that can contribute to lowering energy consumption are E-chains constructed from lightweight plastic and guide rails with an optimized, weight-reduced profile.
Energy e ciency is important to AS/RS manufacturers because it helps them deliver a better value proposition to their customers. Maximizing energy e ciency requires not only using components and sub-systems that are themselves energy e cient, but also using those components and systems intelligently. This is best accomplished by monitoring the actual system requirements and comparing those with the expected performance.
• Adjustable handles and knobs replace standard hardware and can be used to torque components without tools.
• Levers can be used with Ruland shaft collars for quick installation and adjustment.
Adjustable
• Slit couplings are available in short and long styles giving designers a variety of body sizes to choose from to t application envelope and performance requirements.
• Control ex is a highly exible encoder coupling designed for applications with high speed, low torque, and wide differences in shaft sizes (up to a 4:1 small to large ratio).
• Slit couplings are available in bore sizes from 1.5mm to 12mm (1/8” to 1/2”) and control ex couplings are available in sizes from 6mm to 40mm (1/4” to 1-1/2”).
Slit Coupling
• Available with OD ats and holes for direct mounting of the collar to other components.
Control ex Coupling
• Assortment of components that allow users to build small assemblies for mounting sensors, conveyor rails, machine guards, and more.
• Optional pre-designed kits make it easier to select the right system for your application.
• Proprietary manufacturing processes ensure superior t, nish, and holding power.
• Manufactured in a variety of sizes, styles, and materials.
• Widest selection in the industry: over 3000 standard single and double universal joints to start your next design with.
• Available from Ruland in 2 weeks or less for the shortest lead times in the industry.
• Yokes, pins, and blocks are precision machined, ground, and selectively heat treated for smooth operation at high operating angles.
www.ruland.com | sales@ruland.com
• Hand operated: no tools required to install, remove, & adjust.
• Best suited for systems that require frequent adjustments.application.
Amazon continues to be a leader in automating warehouse operations, and that includes not only using existing technology but developing its own products and buying manufacturers of interest. In September, the company announced it was acquiring Cloostermans, a Belgium-based company that specializes in mechatronics. Cloostermans has been selling products to Amazon since at least 2019, including technology Amazon uses in its operation to move and stack heavy pallets and totes and robots to package products for customer orders.
Amazon said this acquisition will ramp up its R&D and deployment in those areas.
“We’re thrilled to be joining the Amazon family and extending the impact we can have at a global scale,” said Frederik Berckmoes-Joos, CEO of Cloostermans. “Amazon has raised the bar for how supply chain technologies can benefit employees and customers, and we’re looking forward to be part of the next chapter of this innovation.”
The financial terms of the deal were not disclosed. Founded in 1884, Cloostermans has been privately held for the last six generations. Cloostermans has about 200 employees that will join Amazon Global Robotics’ growing presence in Europe.
Amazon said it has deployed more than 520,000 robots in its facilities worldwide. Of course, that all started in 2012 when Amazon acquired Kiva Systems and its automated guided vehicle (AGV) technology for $775 million. Amazon recently introduced its first autonomous mobile robot (AMR), Proteus. It does similar tasks as the Kiva robots, but can work freely around Amazon workers instead of caged o areas.
Since the acquisition of Kiva Systems, Amazon has built out an impressive robotics portfolio. And it’s not limited to just warehouse robotics systems. Amazon has a pending deal to acquire iRobot for $1.7 billion that is being reviewed by the Federal Trade Commission. It also acquired Canvas Technology, Dispatch and Zoox, and invested in companies such as Agility Robotics, which will be demoing and talking about its bipedal robot, Digit, at RoboBusiness 2022.
“Amazon’s investments in robotics and technology are supporting how we build a better and safer workplace for our employees and deliver for our customers,” said Ian Simpson, vice president of global robotics at Amazon, in a statement. “As we continue to broaden and accelerate the robotics and technology we design, engineer and
deploy across our operations, we look forward to welcoming Cloostermans to Amazon and are excited to see what we can build together.”
Teaching robots to do more Robots picking items in Amazon’s warehouses need to be able to handle millions of different items of various shapes, sizes, and weights. Right now, the company primarily uses suction grippers, which use air and a tight seal to lift items, but Amazon’s robotics team is developing a more flexible gripper to reliably pick up items suction grippers struggle to pick.
Amazon is teaching robots how to understand cluttered environments in three dimensions, locate specific items and pick them using a pinch grasp, or a thumb and finger hold. The company’s current vacuum-like grippers use elastic
suction cups that form to the surface of an item. This creates a tight seal that allows the robot to pick objects.
Amazon said this method works great for flat items that only require one point of contact for picking, like rulers or cards. It’s less effective, Amazon said, for items that require more than one point of contact to pick up, for example, a book will fly open if you pick it from just the front or back cover.
Suction grippers also struggle to get a tight seal on bags filled with granular items, like marbles, according to Amazon. And even on items these grippers can pick up well, if the angle of attachment changes because of the momentum of the robot arm swinging it from one place to another, then the seal will break too early and the robot drops the item.
These cases are why Amazon is interested in the pinch-grasp method.
robots, which currently operate in caged-off spaces away from Amazon employees, Proteus is able to work freely among them.
This change means that Proteus needs to be prepared to adapt quickly to unexpected changes in its environment. John Enright, principal engineer at Amazon Robotics, recently gave some insight into how the company developed the technology behind Proteus. He explained the approach to the AMR’s navigation in the video above.
Despite how natural it is for humans, it’s not a simple one to develop in a robot. To teach a robot to pick items out of piles of other items using this method, researchers first needed to teach it to be able to estimate the shape of items that could be partially obscured by other items.
As humans, we do this without even thinking about it, but robots have a much harder time understanding the whole shape of an item if they can’t see all of it. Amazon’s robots gauge what they’re picking by using multiple camera angles and machine learning models trained to recognize and estimate the shape of individual items. The robot uses this to decide how to best grasp the item on two surfaces.
Once the robot makes those observations, it uses a set of motion algorithms to combine the information it gathered about the scene and the item with the known dynamics of the robot to calculate how to move the item from one place to another.
The robot also continues to use its multiple-angle view of the situation throughout the pick. This is another deviation from typical picking methods, where a robot won’t usually continue to look at the scene as it carries out a pick. So far, Amazon’s team has seen encouraging success with its pinchgrasping robots. A prototype robot
achieved a 10-fold reduction in damage on certain items, like books, without slowing down operations, Amazon said. Despite this, Amazon still sees room for improvement. The team is currently using an off-the-shelf gripper that can only pick items that weigh less than 2 lbs. This makes the gripper capable of handling only half of the items that Amazon has available for purchase. Going forward, the team plans to design its own gripper for the job.
In the future, Amazon hopes that it can implement its pinch-grasping robot alongside its current suction ones so that it can decide which robot would be best suited to picking each individual item. The company is using a similar strategy with its Proteus autonomous mobile robot (AMR).
Earlier this year, Amazon unveiled its first-ever autonomous mobile robot (AMR) Proteus. The company first entered the mobile robot space in 2012, when it acquired Kiva Systems for $775 million. Kiva Systems offered automated guided vehicles (AGVs) that have been at work in Amazon’s warehouses since.
Proteus has a similar design to the Kiva robots. It slides under Amazon’s GoCarts, lifts them up and moves them across warehouses to employees or other robotic cells. Unlike the Kiva
“Our design focuses on safety, efficiency and cost-effectiveness,” Enright said. “We employ a wide range of diverse and redundant sensing modalities that allow us to provide certain guarantees on vehicle behavior.” Proteus’ job is to store, move and sort Amazon’s blue GoCarts, a central part of the company’s logistics operations. The AMR travels to where the carts are and slides underneath them to move them. It uses general navigation abilities to travel to the general location of the GoCarts, and then uses its high precision LiDAR to find the carts.
To slide under the cart, Proteus uses a two-step detection and motion process. First, the robot will perform a small “S” curve to remove any lateral error in its positioning under the GoCart. Next, it performs a straight motion to tunnel under the cart and lift it.
Proteus carries the cart to its desired storage location, which it identifies with Amazon’s fiducial plus. Fiducial plus is a custom-made ground target that aids Proteus in its alignment capabilities and in finding storage cells. These fiducials help the robot to perform millimeterlevel corrections on its positioning. The AMR has been deployed in Amazon’s outbound GoCart handling areas in its fulfillment and sorting centers. A source told The Robot Report Amazon will use both the Proteus AMRs and the Kiva-like AGVs moving forward. l WH
IKO’s C-Lube linear guides have run maintenance-free for 20,000 km and beyond—thanks to our unique C-Lube technology. They also feature a compact size, high load capacity and flexible design options to achieve precise linear motion across a diverse range of industries.
To learn more, visit ikont.com/linearguides
The new Boston Dynamics Stretch robot is being tested by DHL for autonomous trailer unloading.
| Boston Dynamics
DDHL is using robotics to support numerous warehousing and logistics tasks. The company innovates its logistics workflow and the tools and technologies deployed in DHL distribution centers around the world, as it continually improves e ciencies. Sally Miller, DHL Supply Chain’s CIO for North America, recently spoke to The Robot Report about the types of robots the company uses — as well as the innovation cycle it employs to find the most e ective solutions.
TRR: Boston Dynamics and DHL have been working closely together for the last couple of years to test the Stretch robot. The robot will be tasked with several box-moving tasks inside DHL warehouses Can you update us on that partnership?
Miller: So we’re in the final testing phase, and this is the final iteration. The unit is on-site at one of our facilities. And we’re doing the final tweaks before the unit returns to Boston and they finalize any changes before we’re live in January. Following that, the rollout of subsequent sites will start. But this is just a final test period, then we’re ready to go.
TRR: Truck unloading is vital to your operations. Other robotics companies are also attacking this application. Why did you choose Boston Dynamics Stretch over the others? Did you try other solutions?
Miller: Truck unloading is one of the key activities in any warehouse. Not all of the trucks that we unload have carton products — a lot of the items are palletized. Only a certain percent of our facilities have floor-loaded products.
What we enjoy about working with Boston Dynamics is they are looking at use cases beyond just carton unloading. There are several other areas where we’re doing activities with cases that the Stretch unit could theoretically be used for. The real value in the Stretch robot comes in multiple activities beyond just case unloading. We’ve focused significantly on Boston Dynamics, there are other solutions that
Digit v2 carrying a box. Digit v2 is the preproduction version of Digit. | Agility Robotics
DHL
are coming to market, but right now we are focused on Stretch.
TRR: Can you take us inside the trailer unloading process? I know it’s a grueling process for humans. Agility Robotics is making a two-legged robot that has been tested for trailer unloading. There’s a nice video showing the Digit robot working collaboratively with humans, carrying things into and out of a trailer. Are you considering removing humans from the trailer unloading process?
Miller: Attracting and retaining hourly labor is a challenge for everyone, especially with today’s scarcity of resources. Trailer unloading
Murrelektronik has developed efficient and economical system solutions for integrating industrial image processing systems. The advantages include minimal installation effort as a result of decentralized, pluggable modules that can be mounted directly on the machine.
This achieves the goal of maximum performance with minimum wiring effort. The compact, powerful module is located right where it is needed. All in all, this saves installation time and reduces installation efforts while offering maximum availability enhanced by LED diagnostics each module. As a result, control cabinet components for connecting camera systems are replaced by a decentralized installation systems.
Autonomous mobile robots from Locus Robotics.
| Locus Robotics
retail, e-commerce, automotive, and a catch-all bucket. DHL facilities aren’t all the same. They’re customized for the unique requirements of the customer.
is one of the least liked jobs in the facility. I feel that Stretch will be able to unload faster autonomously than a two-legged robot. And the fact that it doesn’t work with humans is OK for now. Based on the speed that it can work, it’s a win that we don’t need people there.
TRR: DHL has a large fleet of Locus robots running around its facilities. Can you tell us a little bit about how DHL deployed the Locus solution and what it’s doing every day in the facilities?
Miller: We have deployed LocusBots in probably 15 facilities and are close to 2,000 bots deployed. This solution works extremely well. Locus is a very innovative company that keeps coming up with use cases to do more of the work in the facility. Our associates love working with the bots. They are cobots designed to work alongside associates. The associates travel less during the day and like going home and telling their families they’re working with robots.
We’re seeing that sites that have the solution deployed have lower turnover and a higher applicant rate. People want to work in environments where there’s more technology deployed. So Locus is a very effective solution that we have deployed where we’re doing highvolume each pick to totes.
TRR: Locus Robotics is a pioneer of the Robots-as-a-Service (RaaS) concept. What is your perspective of RaaS? Does RaaS simplify the sales process? What sold you on this business model? Were you initially doubtful this would be a reasonable solution for DHL?
Miller: We have a global agreement with Locus and their commercial model that they were able to work with us on works well with our commercial contracts. So it was beneficial to us. Obviously, we reassess if we should do the capital outlay versus the RaaS fee. But right now, it is more favorable to us.
TRR: Can you walk us through the process DHL uses to evaluate a new solution and ultimately decide which robots are beneficial? What key performance indicators do you measure?
Miller: For assessment, we look at things that people bring to us, whether they be a startup company, an existing vendor with us, a customer, or a venture capital company. We have a lot of connections with VC firms because they want to bounce how viable some of these ideas are off of us. So we have a lot of inputs from various sources that we investigate.
The first thing we look at is whether the solution fits into a significant number of our facilities. We support several market verticals ranging from CPG, tech, life sciences, and healthcare,
If you walk into an apparel e-commerce facility, you’re going to see a lot of automation. If you walk into a tire distribution center, it’s going to be quite manual. Not everything fits. We have a database of all of our site profile information, so we’re able to quickly see if this is something we should dedicate resources to. If it makes it past that, we do a proof-of-concept where we take the solution to one of our sites that we believe it’s a fit for, and we test it out.
Based on how well it performs and how many sites we think it can be deployed at, it then moves to the product stage where it’s available for any of our 500 sites to deploy. But, usually, the proof-of-concept tends to be an iterative process with the vendor to make tweaks based on what we learned to make the return on the investment and the value to us better. So that’s a value that we bring to the vendor and why a lot of companies want to work with us; they will get that feedback if it moves to proof-of-concept. And if we think there’s a potential for the solution to become a product, we really provide the resourcing to get as much value out of the solution as we can. l WH
You can’t talk about intralogistics without mentioning digital transformation. It has been revolutionizing modern distribution and fulfillment centers, and it’s the basis for emerging technologies that are crucial for staying competitive. Robotics, machine learning, artificial intelligence, predictive maintenance, intelligent motion control, and voice-activated solutions support digitization in general and fuel exciting advances in a core technology for which Beckhoff is a market leader: PC-based automation.
Digitization, however, is only beneficial through easy data access throughout the enterprise. Beckhoff successfully uses the automation controller for local data capture, edge processing and sharing across the enterprise and the cloud. The ease, flexibility, speed, and security of how data are gathered, structured, and transmitted sets the Beckhoff solution apart from PLCs and PACs. Traditional PLCs do not support local databases for storing important system and operational data, restrict how data can be structured, and lack modern communication options and cloud connectivity. The TwinCAT automation platform supports a wide range of open and modern communication options to the warehouse control system or warehouse management system, and across the enterprise. It comprehensively supports legacy communication required in brownfield installations, allowing custom protocols. Beckhoff leads in open communication, being the first supplier to integrate OPC UA as both a server and a client for another open, secure communication protocol option. Beckhoff offers a complete suite of automation software products and cloud-based solutions — and offers IoT hardware solutions for brownfield sites and supports connectivity through product certification from leading cloud services, including Amazon Web Services and Microsoft Azure. Beckhoff automation controllers can also create localized private cloud implementations.
By Doug Schuchart Global Material Handling and Intralogistics Manager Beckhoff AutomationDigitization begins with the ability to use one common fieldbus for communication to all devices across the fulfillment center. EtherCAT offers the capability to use gateways for all open Ethernet protocols such as EtherNet/IP and PROFINET and legacy protocols like DeviceNet, PROFIBUS, and CANopen. As a result, EtherCAT is the only protocol that can support a single-network architecture for the entire intralogistics enterprise.
EtherCAT boasts flexible communication via any topology to as many as 65,535 devices on a single network segment — typically in microseconds. EtherCAT is the ideal protocol for the highway of conveyors connecting thousands of sensor devices, I/O modules and motor drives across a fulfillment center. This results in far fewer CPUs (or PLCs) and no switches that increase digital traffic delays, cost and reengineering requirements due to lifecycle obsolescence.
While EtherCAT creates a flexible, real-time communication highway to send data from sensors, motors, and other field devices, the Beckhoff IoT toolbox extends it to the enterprise level and/or cloud. TwinCAT Analytics, Condition Monitoring, Power Monitoring, and the built-in, real-time TwinCAT Scope all enable predictive maintenance, improved diagnostics, and extensive remote support capabilities to increase uptime. This is crucial in modern intralogistics environments influenced by e-commerce demands,. For the autonomous optimization of equipment, systems and robots via pre-trained neural networks, Beckhoff announced TwinCAT Machine Learning. Integrated into our real-time automation platform, these tools ensure retailers and intralogistics equipment suppliers can meet growing consumer demands for shorter delivery times with higher accuracy.
With TwinCAT and EtherCAT, Beckhoff is already a proven leader in the automation of intralogistics systems. We look forward to helping all intralogistics professionals achieve their automation goals to outperform rivals and not just survive, but thrive through the digital transformation.
Automated systems and machines are revolutionizing storage and retrieval systems to support the demand for faster processes and efficiency gains. Sophisticated conveyors, sorters, palletizers and robotic systems can move product more quickly and reliably than traditional warehouse machinery, but they require exceptional motion products to provide accuracy and longevity. Here is an overview of some of the advanced, high-performance motion devices available and the features that make them well-suited for use in modern, automated warehouses.
• Linear Roller Guides, such as the Super MX Series from IKO International, are desirable whenever a mechanism must handle heavy loads in any direction or large moment loads. Using cylindrical rollers that make a larger contact area with the raceway than guides that use steel balls, they offer higher load ratings. The large contact area also provides exceptional rigidity with less elastic deformation under load for stable performance.IKO Super MX also has built-in C-Lube technology which provides long-term maintenance-free operation. Since lubrication maintenance is reduced, these guides are particularly beneficial for robotics in warehouses where tight spaces make lubrication difficult. And, their interchangeability allows them to be matched, replaced or freely added without replacing an entire bearing and rail assembly, giving engineers greater design freedom.
• Crossed Roller Bearings. For applications with complex rotary motion requirements, crossed roller bearings can provide high rotational accuracy and are engineered to handle radial, thrust and moment loads at the same time. Different types of crossed roller bearings can be chosen depending on the intended task and can provide extra-high rigidity or satisfy
restrictive space and weight requirements for robotic devices that perform light-duty wrist and arm motion. IKO International’s lineup of crossed roller bearings provide rigidity, smooth motion and accuracy in a wide variety of sizes and types to fit various rotating and positioning mechanisms. IKO offers standard, high rigidity and mounting hole type and slim and extra slim versions to meet a range of size and application requirements. Bearings are also available with rubber seals to protect against dust, dirt and grease.
• Linear Ball Spline Guides. Available in standard and C-Lube models, these guides have an external cylinder that enables smooth linear motion along a spline shaft, making four-point contact with the raceway. This construction allows the cylinder to move with high accuracy and rigidity, even during fluctuating and complex loads common in material handling applications such as pick and place machines. Flanged and long type cylinders are also available.
Motion products are proving essential to the automated machines and systems that are transforming storage and retrieval operations. IKO International’s lineup of linear roller guides, crossed roller bearings and linear ball splines gives machine designers the rigidity, accuracy and smooth motion these systems require along with design freedom and protection from harsh industrial conditions. That means goods can move quickly, efficiently and reliably, and machines can run longer, providing a better return on investment for automated warehousing systems.
For more information about IKO International’s motion products for automated warehouses, visit www.ikont.com.
Any automated system is only as good as its reliability. An automated guided vehicle (AGV) for example, needs to do the job it is programmed to do; without error, quickly and efficiently.
Since 2020 in the world of e-commerce, consumer expectations have grown exponentially with same day or next day delivery considered the norm. Introducing computer-controlled load-carriers (AGVs) will speed up product distribution and therefore ensure customers’ growing expectations are met. If the AGVs picking stock are not accurate or efficient, the customer may get the wrong item, or receive the item late meaning they are unlikely to return.
Therefore, the role AGVs play in material handling is paramount and their reliability is dependent on the component parts used to manufacture them which includes robust motors. Motors for AGVs must be reliable, low maintenance and they need to be capable of being in operation 24/7 without loss of functionality. If the AGVs aren’t running, then the warehouse and production lines can’t continue working meaning revenue is lost for every hour they are down. However, if the AGVs are set up correctly with the most appropriate motors then they can help businesses to reduce labor costs, increase productivity and improve scalability of the business.
Although there are numerous tasks an AGV can carry out within the manufacturing and logistics industries they are more commonly used to transport products around a warehouse, production line assembly, or order picking.
Like any automated system, AGVs are reliant on systems in place to ensure they can carry out their tasks such as:
• Guiding tapes, wires or sensors around the warehouse.
• Ability to react instantly and flexibly to system control instructions.
Unlike human counterparts, AGVs can run for 24/7 and need to be equipped with reliable motors which can withstand constant use as well as quick changes in speed and direction.
So, what type of motor do you need for your AGV?
That depends on the type and size of the automated guided vehicle you have, and how much weight it will be expected to transfer at any one time. A motor that is too small won’t be able to function – or at least not for long – and one that is too big and powerful could cause functionality issues.
The recommended motors for AGVs are brushless DC motors (BLDC motors) because they are powerful, quieter, require lower maintenance and therefore extremely durable and efficient. Ensuring the most appropriate motor for the equipment is installed can reduce expensive maintenance costs as well as lost revenue through downtime.
However, with Parvalux’s brushless motors, they rarely need maintenance, and are highly efficient with a high starting torque, which means they are consistent in speed. This enables the timings of build on production lines and delivery times to be assessed more accurately. This makes reporting and assessing capacity for the warehouse easier.
Parvalux can provide you with the reliable AGV electric motors that you need in order to have your warehouse and production lines running as effectively and efficiently as possible. The main benefit of AGV electric motors is that when chosen correctly, there is minimum maintenance and less fluctuation in labor.
To find out more about the AGV motors stocked by Parvalux, visit: www.parvalux.com.
Known for their dexterity and safety, Doosan Robotics H-SERIES cobots are the most powerful in the marketplace, providing unrivaled and precise performance in palletizing. Featuring a maximum reach of 1700mm and 25kg payload, Doosan’s H-SERIES not only has a higher payload and longer reach than competitors, but it can also safely perform highly complex tasks using precise force and compliance control based on the 6-axis force torque sensors. With the highest collision sensitivity in the industry our cobots can also be trusted to share space with personnel, all while enhancing production output and maximizing labor. Doosan Robotics also delivers in a fraction of the time of industry competitors, with an average delivery time of four weeks.
Murrelektronik’s modular plug & play solutions allow you to get your vision system up and running quickly thanks to our IP67 rated modules that can be mounted on the machine. This decentralized installation concept significantly cuts planning and installation e orts. Control cabinets can be smaller and cable runs shortened when the modules are put where they are needed. In use, the detailed LED diagnostics in our solutions reduce your equipment downtime if a fault occurs in the system.
Doosan Robotics doosanrobotics.com
Murrelektronik, Inc.
1327 Northbrook Parkway, Suite 460 Suwanee, GA 30024 770.497.9292 murrinc.com 2info@murrinc.com