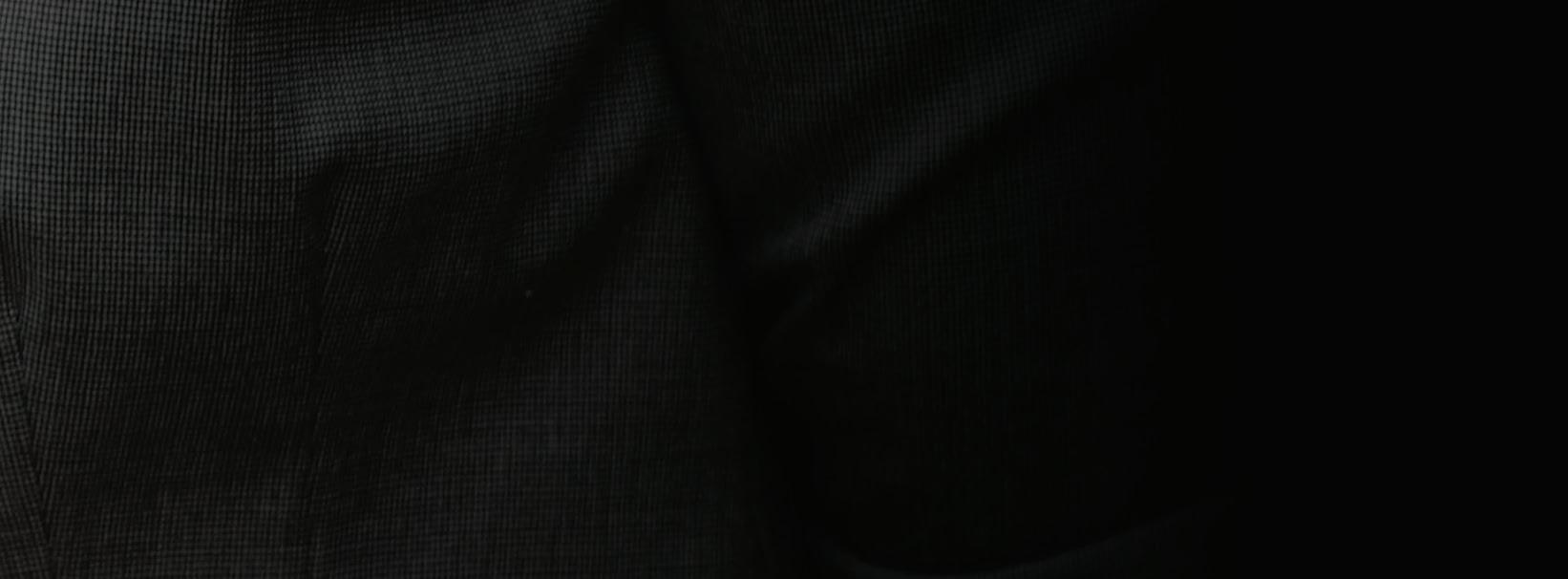
7 minute read
Maureen Lincoln
From math to engineering,
with love
Mary Gannon • Senior Editor
Maureen Lincoln, PE, has founded and served as CEO of companies throughout her career but engineering is where her heart lies. As the founder of Kerelaw Engineering, P.C., a Bronx-based product design and engineering agency, she is responsible for steering the company’s engineering team. She has been the Director of Engineering for the company since 2019, and previously served as the company’s Principal Engineer during its first years of business operation, beginning in 2016.
An MIT graduate, Lincoln has always been drawn to math and mechanisms. “I’ve always been fascinated by mechanical things, even at a young age,” she said. “My mother tells me I made paper dolls with moving parts, and my brother often reminds me I took apart all his toys. Once I was old enough to ride a bicycle, I was really hooked by mechanism designs and how to use them.”
Lincoln found her way to engineering through a deep love for math, which her parents encouraged. She was enrolled in a gifted student program from 4th to 8th grade, where she studied math on an independent basis. “I took all the math coursed available until I exhausted the system. While still in high school, I took undergraduate math classes at a local university. Math was the inroad to my engineering career and success.”
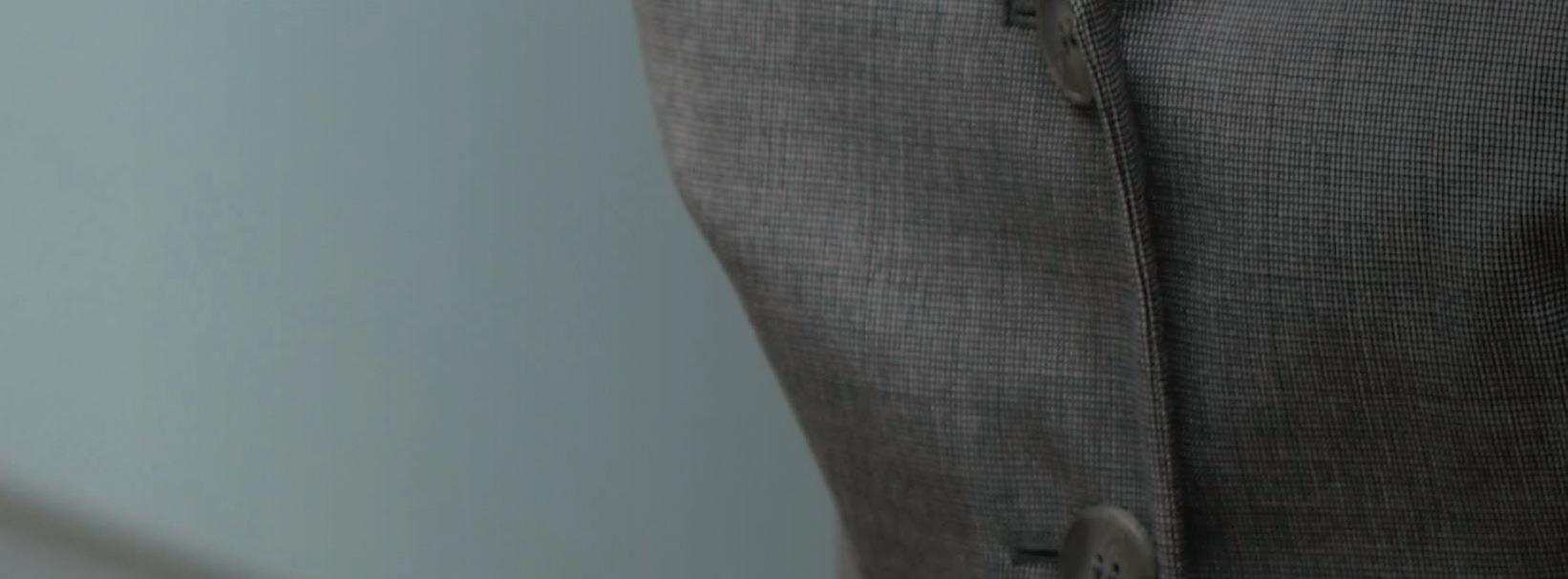
Maureen Lincoln, PE


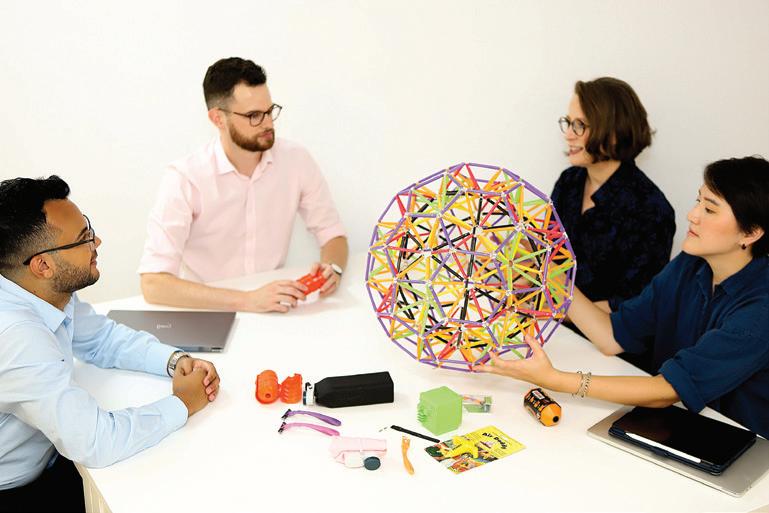

Maureen Lincoln is founder and director of engineering at Kerelaw Engineering, where she works with a small and talented team to provide engineered solutions to clients that look great, function as required and meet market expectations. Top,Joseph Tatis, engineering intern works on a product design; bottom right, the entire team from left to right,Zoe Ho (Industrial Designer), Joseph Tatis (Engineering Intern), herself, Chris Findlay (Program Manager) and Phyllis Isola (Office Manager), and Lassie Lou; and bottom left,the engineering team collaborates on design projects.
She then enrolled at MIT, where she earned her BS in Mechanical Engineering. “While at MIT, I took the design competition class 2.70 (now 2.007) with Professor Woodie Flowers. His hands-on approach to teaching further opened my eyes to the wonders and powers of engineering,” Lincoln said. “His teaching team further reinforced my decision to be and stay in engineering, including anecdotes of consulting gigs and practical design feedback. Sadly, Professor Flowers is no longer with us, but I still remember and use my learnings from his class.”
A career in design
Upon graduation, she began her career in product design and development, always with a strong focus on innovation, manufacturing and job creation. As her corporate career progressed, Lincoln used her technical training, mentoring skills and team building abilities to develop strong engineering teams and product development programs.
Over her career, she has worked in new product design and development in the automotive, industrial, consumer and medical industries, especially now working with her team at Kerelaw for nimble and innovative designs.
“We recently worked with a client to quickly repackage their proven technology and leverage their industrial brand recognition to provide air purifier technology solutions for institutional and business settings,” she said. “We jumped in as part of the core team to translate their vision to tangible features and benefits while offering a design optimized for manufacturing. Together we worked to launch a beautiful, quiet, and efficient machine that supports post-Covid reopening plans. It’s already been adopted by Fortune 100 companies and well-known universities to improve air quality in shared spaces.”
Her engineering career has run the gamut from quality engineer to senior design engineer, director of product engineering to CEO. Through each of those career types, she has learned the importance of troubleshooting and teamwork.
“Early in my career, I worked on an automotive sensor with intermittent functionality. Like many of us engineers have experienced, the issue did not fully present itself until the parts were run at production volumes and used in the field,” Lincoln explained. “Though the issue would not create a safety issue, it was a production disruption that could potentially cost my former employer thousands of dollars in late delivery charges. With this potential liability and client dissatisfaction, fixing this problem became a priority.
“A team of us at the factory analyzed the issues, found the root
cause and brainstormed solutions. I discovered a way to predict the failure by looking at the specific circuit characteristics and developed a handheld, battery powered tester that could be used to sort inventory,” she continued. “We sorted the inventory at our site and shipped verified replacements. I then flew to several international sites to sort the inventory there, missing Thanksgiving with my family!
“We did find and implement a solid design change to prevent reoccurrence, added this new test to the line, and managed to provide inventory to the customer without creating a ‘line down’
situation, avoiding any financial penalties,” she concluded. “In fact, the customer was so pleased with our commitment and so grateful with the result they sent a letter to the VP of our site specifically calling out my team and me. It felt great to have my effort recognized, but it felt even better that this letter was used by our marketing group to procure future business.”
Shaping great engineers
Lincoln noted that although there has been a great focus on STEM and STEAM and mentoring over the years, the number of young women engineers entering the workforce has not increased the way one would expect. She said retention must play a part in this.
“I think the best way to increase the participation is to keep women in engineering. Not to focus on the hurdles that once were — we are beyond that — but the opportunities that there are now,” she said. “Today’s business is more flexible and more collaborative. At my company, we work as an agile team with hybrid work schedules that help to promote better work/ life balance. It’s a culture of enthusiasm and respect that comes right from the top. Most important, it’s a learning environment for us all. We learn from each other based on our diverse perspectives and experiences, and from the challenges our clients hire us to solve. It’s an environment I can share
with young engineers to move and inspire them to continue a role in engineering.”
She added that while family responsibilities are certainly part of the reason women leave engineering careers, the general structure of engineering groups is also a factor. “The women I know with engineering degrees that no longer work in engineering (my daughter included!) opted to move from an individual contributor position to a more team-based role,” she said. “These include positions in marketing and/or program management.”
Lincoln said it’s better for the industry as a whole to engage more women in engineering careers because the women engineers she knows bring a unique understanding of clients’ unspoken requirements and unconsidered consumer use scenarios. “I’ve worked with women with excellent team building skills, especially keen on bringing out new ideas from team members who perhaps were hesitant about sharing in a group setting or had not yet looked at a challenge from a new perspective,” she said. “Diverse perspectives and experiences certainly help identify the best of the many possible engineering solutions one can use to solve a design challenge and having women as part of the engineering team makes this possible.”
Finally, Lincoln imparted some advice to those studying to become engineers, noting the importance of internship programs. “It’s a great way to learn real-life, professional skills and gain confidence in a safe environment, especially if you can find the right mentor.
“To safeguard against mistakes, always check your work,” she added. “It’s the best professional advice I ever received, and many times has saved me from publishing mistakes. Another way to minimize mistakes is to look at the problem from different perspectives. If you can look at the problem from different perspectives and still converge on the same solution, then the solution is robust.
“I’ve learned it’s important to recognize and communicate mistakes right away,” Lincoln concluded. “To make a bad mistake better, offer some initial analysis and solutions as well.”
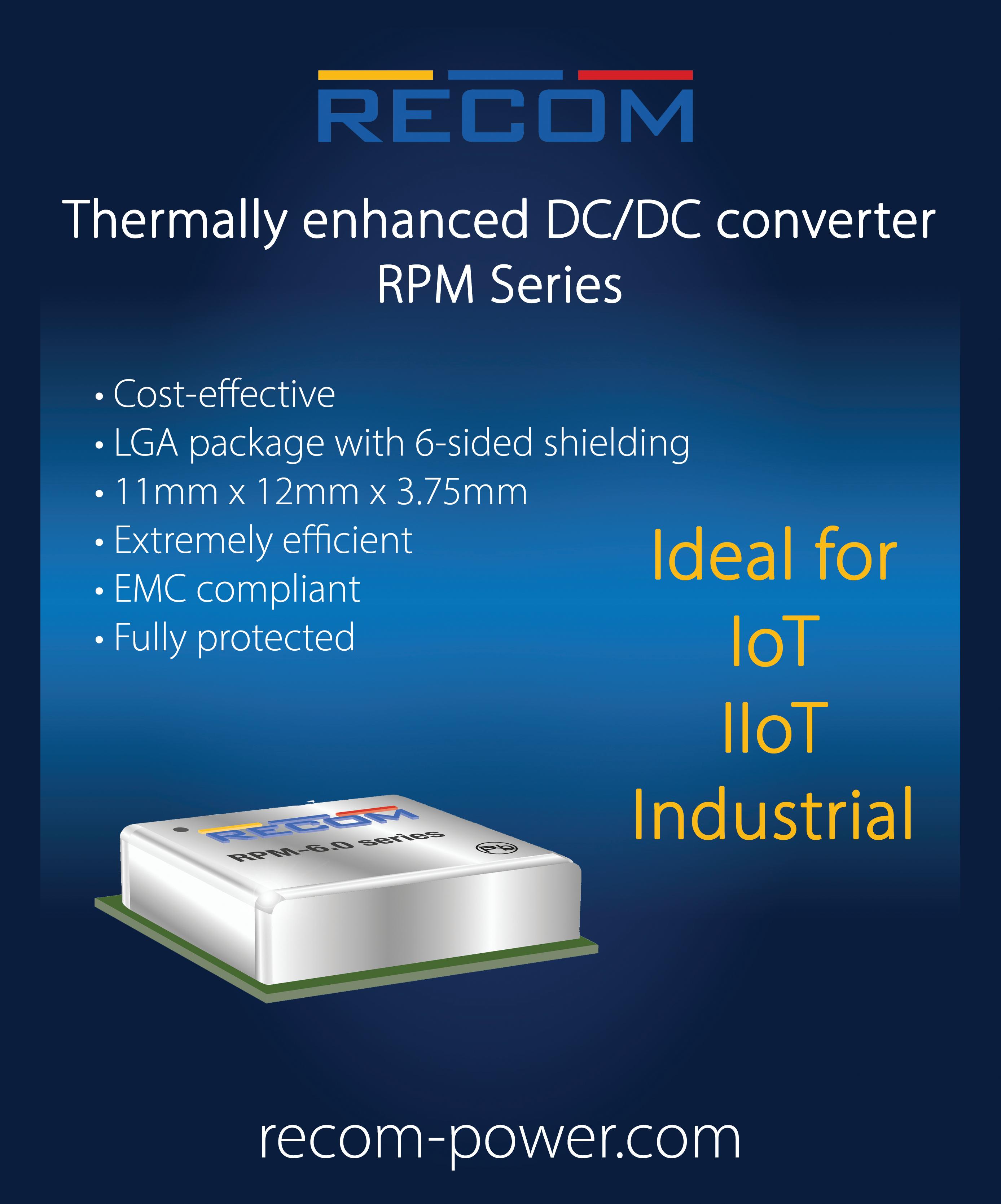