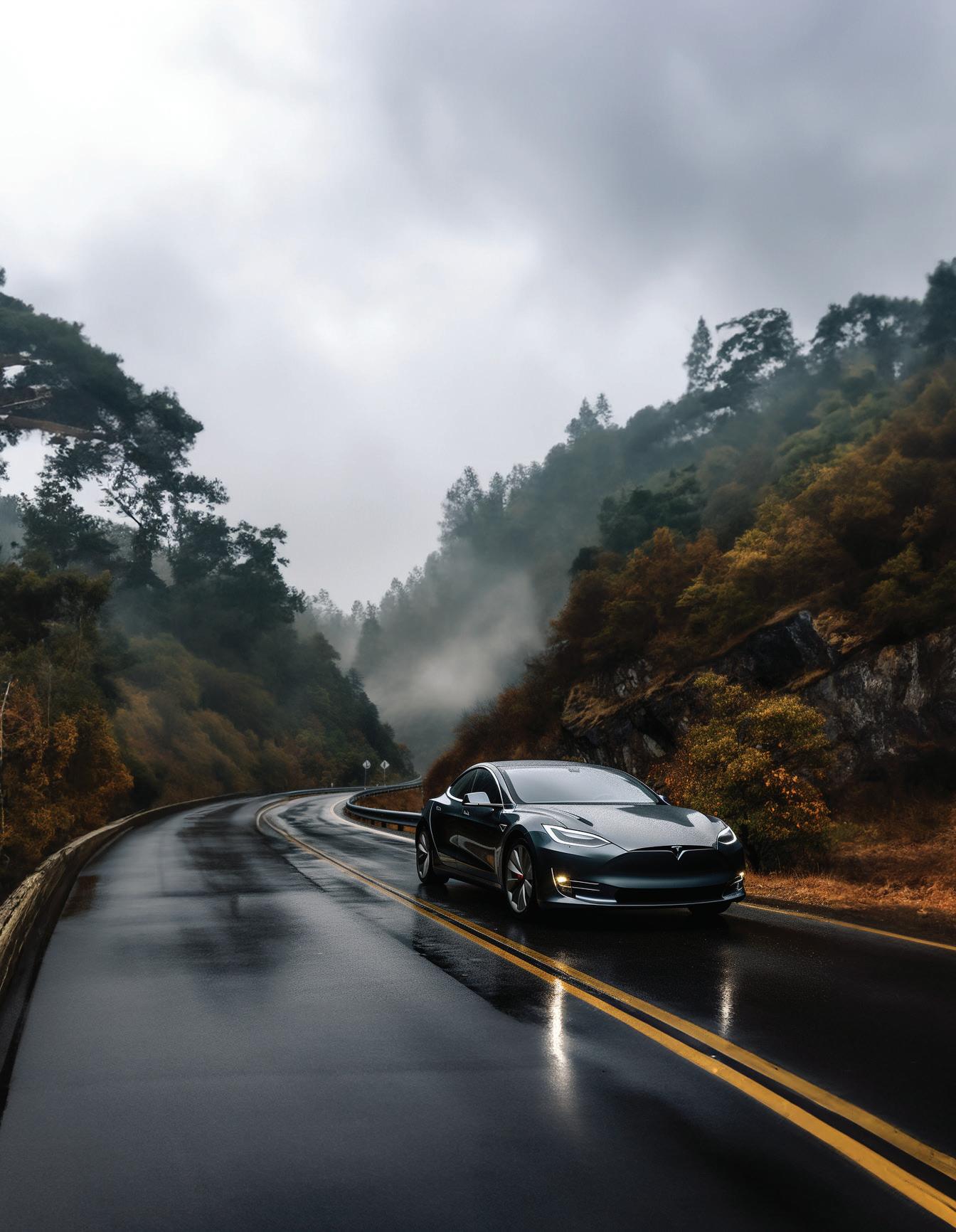
A Tesla navigates a winding mountain road, showcasing advanced EV drivetrain technology for optimal handling and performance in diverse driving conditions.
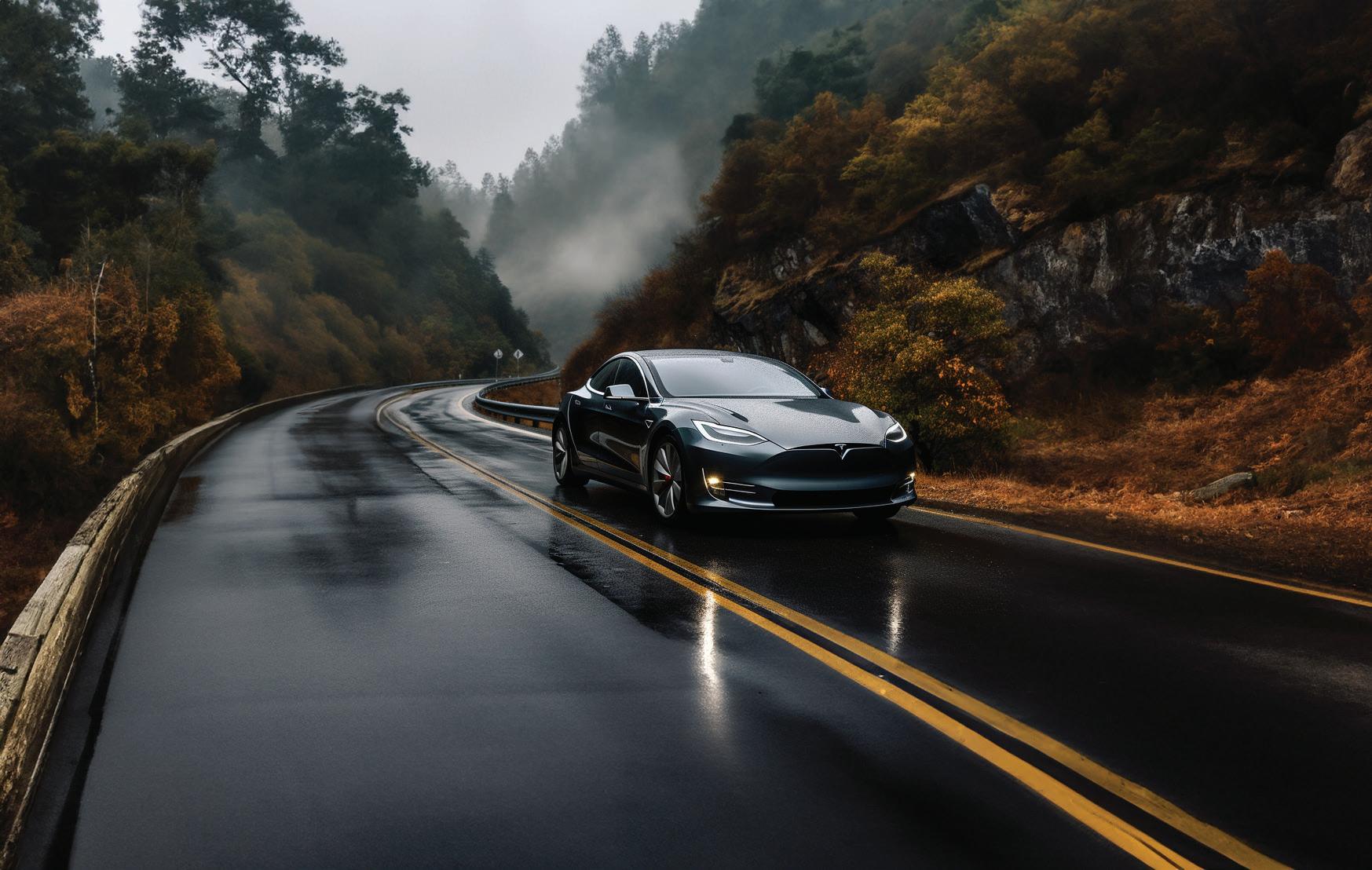
A Tesla navigates a winding mountain road, showcasing advanced EV drivetrain technology for optimal handling and performance in diverse driving conditions.
Aharon Etengoff • Contributor
Although the terms powertrain and drivetrain are often used interchangeably, both are distinct and support their own set of functions.
This article discusses the role of each in the context of electric vehicles (EVs), lists their key components, and explains how they work together. It also highlights primary design considerations and previews potential advancements.
Powertrain: The core of EV propulsion
Responsible for managing and delivering electrical power, the EV powertrain comprises an integrated system of components that transform electrical energy into mechanical power. Specifically, electric motors create magnetic fields in stator windings to induce rotor rotation for propulsion. These motors also facilitate regenerative braking, reversing their function to convert kinetic energy back into electrical energy.
Battery traction packs are another essential powertrain component. These packs contain multiple lithiumion cells and embedded battery management systems (BMS) that regulate regenerative braking power
while ensuring optimal temperature, voltage, and capacity.
EV powertrains also include:
• Vehicle control unit (VCU): Often considered the “brain” of EV powertrains, the VCU oversees operations. It processes data from various sensors and systems, including the BMS and motor controllers, and regulates advanced driving features such as regenerative braking and energy optimization.
• Transmission: Many EVs employ a single-speed design with a fixed gear ratio, boosting energy efficiency by reducing mechanical complexity. In some EVs, electric motors drive the wheels directly, eliminating the need for traditional transmissions.
• Power electronics: These components manage the flow of electrical energy with inverters and converters — transforming dc from the battery into ac for the motor and vice versa during regenerative braking.
• Thermal management systems: Essential for maintaining optimal operating temperatures, these
systems employ liquid cooling circuits, heat exchangers, and advanced sensors to dissipate heat and prevent thermal runaway.
Drivetrain: Translating power into motion
The EV drivetrain efficiently transfers power from electric motors to the vehicle’s wheels. The transmission, a crucial component interfacing with the drivetrain and powertrain, optimally distributes torque. Specifically, differential gearsets within the drivetrain rotate each wheel at varying speeds — dynamically adjusting torque distribution to match wheel load and road conditions. EV drive shafts, connected directly to the differential gearsets, transmit optimized torque from the transmission to the wheels. This configuration ensures efficient power delivery and maximizes wheel performance on wet, slippery, or uneven roads.
EV axles, another important drivetrain component, bear the vehicle’s weight and facilitate wheel rotation. These axles maintain precise wheel alignment to improve traction and bolster responsive handling. In advanced EV models, axles might
include specialized components such as limited-slip differentials or torquevectoring systems.
Additionally, some EVs integrate specialized hub motors directly into each wheel, facilitating precise torque control and improved maneuverability.
Achieving optimal EV performance requires a comprehensive design approach that seamlessly integrates powertrain and drivetrain systems. Synchronization is essential, as powertrain motor control and energy management directly impact the drivetrain’s ability to efficiently manage handling, agility, and responsiveness.
Many EVs employ advanced control algorithms to match motor power output with torque requirements to ensure maximum efficiency and performance.
Effective thermal management systems are also essential for EV powertrains and drivetrains. These systems regulate operating temperatures and prevent component degradation with sophisticated cooling solutions, predictive algorithms, and innovative heat-shielding materials. Additionally, integrated thermal management helps maintain optimal performance, extend the lifespan of EV components, and ensure safety in high-temperature environments.
Future EV powertrains will likely offer more efficient energy generation and management capabilities. Emerging technologies such as solid-state batteries promise higher energy densities, faster charging options, and extended driving ranges. Power electronic advancements, including more sophisticated inverters and energy management systems, will further optimize the conversion and distribution of electrical power.
FEATURES AND BENEFITS
Controlled Self-Healing Property
Custom Designs (Mechanical/Electrical)
Alternative to Electrolytic, Mica, Film Foil & Ceramic
Total Safety, Reliability & Soft End of Lifetime Due to Controlled Self-Healing
Dry Solution, No Drying Out
Standard Solution
TYPICAL APPLICATIONS
DC-Link Capacitor in EV/HEV
Select Motor Drives
Renewable Energy (Wind, Solar, Power Grid)
Power Electronics That Need High Reliability
WBG Technology
Similarly, upcoming iterations of EV drivetrains will likely see substantial improvements in component design and operational efficiency. Advancements in materials science, for example, accelerate the development of lighter and more reliable drivetrain components, helping to reduce energy loss and bolster vehicle efficiency.
Innovations such as enhanced electric torque vectoring — precisely distributing power to each wheel — will improve control and handling, especially in all-wheel-drive systems. Moreover, new regenerative braking systems will capture and convert more kinetic energy.
Concurrently, EV engineers are adopting an increasingly comprehensive design approach to powertrain and drivetrain integration. With the advent of sophisticated
An overview of EV powertrain architecture, detailing components such as the traction motor, inverter, BMS, and power converters.
AI-driven sensors and machine learning algorithms, EV transmissions can dynamically and precisely adjust power distribution for various driving conditions. More seamless powertrain-drivetrain integration will extend battery life and bolster performance while paving the way for fully autonomous driving capabilities.
Summary
Although operationally integrated, EV powertrains and drivetrains are separate systems supporting distinct functions. The powertrain is responsible for managing and delivering electrical power, and it’s comprised of an integrated system of components that transform electrical energy into mechanical power. At the same time, the drivetrain transfers power from electric motors to the vehicle’s wheels.
References:
• Understanding the Powertrain of an Electric Vehicle, Power Electronics News
• An Overview of the Electric Vehicle (EV) Drivetrain System, Datamyte
• The Vital Roles of EV Powertrain Components, Exro
• Getting to the Heart of EVs: A close-up look at the electric drivetrain, Innovative Automation
Simon Baggott • CMO | Q5D
Vehicles are becoming increasingly reliant on electronics. Electric vehicles (EVs), in particular, are packed with sensors and actuators that regulate and protect every aspect of the drivetrain.
A vehicle’s wiring harness — which connects all these electrical and electronic circuits — is one of the largest and heaviest components purchased by EV makers. It’s also the last barrier to fully automated manufacturing and the benefits that it could bring.
Wire harnesses are safety-critical vehicle components, particularly in
ALL-ELECTRIC VEHICLE
AFDC.ENERGY.GOV
EVs with advanced driver-assistance systems (ADAS) and autonomous driving technologies. They also feed signals and power for driver convenience functions, such as heated seats, navigation, and infotainment and communications systems. However, there are problems arising from manual wire harness production, as follows:
• Manual processing: Typically produced by hand, harnesses are increasingly complex and costly to manufacture.
• Supply-chain complexities: Production is labor intensive, so
most harnesses are produced in countries with lower labor costs. Final assembly, however, typically occurs thousands of miles away from production, adding significant transportation costs, complexity, and risk to the supply chain. For example, many wire harnesses for the European market were made in Ukraine, which is suffering a devastated supply chain, throttling overall vehicle sales.
• Quality testing: Every circuit must be tested in every manually produced wire harness because the process is so prone to errors.
EV drivetrain parts contain hundreds of temperature, pressure, position, speed, current, voltage, gas concentration, level, humidity, and speed sensors — all of which require electrical connectivity.
Automated wiring would likely only require sample testing because it achieves more consistent quality.
• Over-ordering: Quality issues are so common that some vehicle maker executives have stated they need to “over-order” to ensure sufficient inventory of acceptable quality. Each harness costs approximately $1,000 to $2,000 for a typical mid-range EV, so every order has a significant loss (and waste).
• Over-specifying: Every conventional harness wire must use insulated wires to prevent short circuits, adding insulation weight and cost. Also, wires must be heavier than the electrical requirement demands to withstand the physical pressures encountered during assembly and vehicle use. Adding unnecessary weight to an EV compromises its range, and a shorter range means consumers expect to pay less for vehicles.
• Assembly rework: Quality issues often occur when harnesses are manually bent and twisted during the final assembly.
• Repairs and recalls: Warranty claims are costly, and vehicle recalls are even more expensive. In 2022, CNET reported that Nissan had recalled nearly 700,000 of its 2014-2016 Rogue SUVs over fire risk. A poorly sealed wiring connector caused the issue. That same year, the US National Highway Traffic Safety Administration (NHTSA) cited that electrical system faults and failures accounted for 20% of all vehicle recalls.
• Reputation: The cost to a vehicle’s brand reputation when a recall occurs is incalculable but can run into the tens of millions of dollars.
KOA Speer is your ideal passive component partner. We offer a diverse and expanding family of surface mount and leaded resistors, as well as our Quality 1st mandate to deliver unmatched service and product quality… demonstrated by our 99%+ on-time performance despite shipping billions of resistors every month! Don’t Roll the Dice on your passives, count on KOA Speer!
Use fewer resistors for high voltage pplications - working voltage up to 3000 VDC
Heat shock resistance & anti-sulfur available
Given the above concerns, research financed by the European Regional Development Fund and published in March 2023 concluded that “automation in the wiring harness industry still constitutes the biggest deficiency. Despite research findings and patents, to our knowledge, none of these solutions have been implemented in the field, and the state-of-the-art manufacturing process is still highly labor-intensive.”
Overcoming production challenges
There have been many attempts to address wire harness challenges. Some manufacturers have attempted to automate wire harness production, but with limitations. Most automation
This five-axis additive manufacturing cell can automatically and securely add bare or insulated conductors into components with simple or complex 3D shapes.
SENSORS: Inductive and Capacitive Proximity Sensors • Photoelectric Sensors • Level Sensors • Ultrasonic Sensors • Magnetic Sensors • Limit Switches • Interlocks
SWITCHES: Solid State Relays & Contactors • Soft Starters • IEC Contactors & Overloads • Switching Power Supplies • Miniature Circuit Breakers • Electromechanical Relays
CARLO GAVAZZI has the solution for your application needs, whether it’s our industry leading solid state relays & contactors, energy meters, monitoring relays, soft starters or sensors, available with or without IO-Link.
CONTROLS: AC and DC Energy Meters and Transducers • Universal Web Platform • CurrentVoltage- and 3-Phase Monitoring Relays • Current Transformers • Timers • Panel Meters
Contact us today, and one of our field sales representatives will show you why we are one of the fastest growing automation companies worldwide. We’ll even provide a free evaluation sample to qualified OEMs.
machines simply bundle wires together and, in some instances, affix connectors to the ends of the wires. Inevitably, there’s still manual work involved, such as visually checking the terminations, fixing the bundles together to make the complete harness, and ensuring that wires do not become entangled or otherwise damaged in the process.
Additionally, conventional automation has yet to solve concerns about weight, fragility, or supply chain logistics. However, a new hybrid additive manufacturing and automation process offers a higher degree of automation and reliability. It uses an “electrical function automation” robot cell, which enables the full or partial replacement of traditional wire harnesses. It’s eliminating, or at least mitigating, the need for manual processes — adding electrical conductors to EV battery packs, infotainment systems, and more.
A precision five-axis robot with interchangeable tools can add 3D polymeric features to metal, ceramic, or polymer surfaces. It can handle complex shapes, add bare or insulated wires, and attach electrical connectors to make the components functional. The robot can also route wires with conductors up to 3mm in diameter, approximately 13 AWG. This means each conductor can carry over 20 amps, sufficient for low-level signals and functions that include powering relays or fans.
Anchoring each wire to a substrate is fast, cost-effective, and flexible. The substrate can also be the component. For example, it can be a battery pack or a part designed to carry the wiring for attachment to the component. It can be rigid or flexible. Because each wire is individually secured, it might not require insulation,
Bare or insulated wires with conductors up to 3mm in diameter can be automatically secured onto complex 3D components.
saving cost and weight. Because it’s securely positioned, it’s also less prone to environmental and mechanical damage.
The finished products or components with integrated wiring also lend themselves to robotic final assembly. It reduces labor and supply chain risks by co-locating the integration of electrical conductors and components with the vehicles’ final assembly.
Automating wire harness production in EV manufacturing can reduce the size and weight of sub-assemblies and their parts, enabling onshore manufacturing. It can also increase vehicle reliability, cut after-sales warranty and recall costs, and protect the value of the brands in which automakers invest so much to build.
The five-axis robotic cells described here are expected to be integrated into EV manufacturing lines within the next 12 to 18 months. Who will take pole position, we wonder? EV
Ross Feng • General Manager • Viasion Technology Co. Ltd.
As technology progresses, vehicles are gradually transitioning from fuel to electric power, requiring the integration of advanced electrical systems to ensure full functionality. However, these advancements bring new challenges in maintaining electric vehicle (EV) reliability on the roads and over long distances.
This article will examine the obstacles that high-frequency printed circuit boards (PCBs) encounter in EV applications and the strategies to overcome them.
The role of PCBs PCBs play a vital role in EVs because they serve as the backbone for various electronic components and modules, including:
• Powering up the powertrain – An EV’s motor, controller, and battery rely on complex highfrequency PCBs whose durability and reliability directly impact the vehicle’s longevity and efficacy.
• Overseeing the battery management systems – A dedicated high-frequency PCB powers an EV’s battery pack. The PCB monitors the battery’s health and state of charge and can control the temperature.
• Ensuring reliable infotainment and internet connectivity –EVs are more than a means of transportation; they’re also mobile tech hubs. A high-density interconnect PCB is integrated into an EV to facilitate high-speed data transfer and enable entertainment modules inside the vehicle.
• Managing the recharging infrastructure – High-frequency PCBs manage a vehicle’s charging
infrastructure. They’re integral to the onboard chargers that take electricity from the power grid to recharge the car. The reliability and functionality of the onboard chargers are highly dependent on the quality of PCBs.
Every challenge has a solution
Integrating high-frequency PCBs in EVs presents challenges that may include the following:
Mechanical stress. Road surfaces are rarely consistent. Drivers may experience bumps or different vibrations due to uneven pavement. This may present an issue for EVs, as repeated mechanical stress and vibration can damage critical components. The ideal solution is to strengthen the PCBs using durable but suitable materials and vibration fatigue analysis.
Vibration fatigue analysis studies movements and vibrations and, in this case, how they can affect the PCB. This analysis includes identifying key points where a PCB can fail or crack, allowing designers and engineers to apply modifications or materials that ensure this component is more durable and shock-proof.
Heat dissipation and management. EVs generate a lot of heat, which can reduce their reliability and lifespan. So, they require a sufficient thermal management system to prevent overheating.
To attain optimal temperatures, PCB designers must add thermal management mechanisms, such as thermal vias, heat sinks, and heat pipes. By adding these components, an EV’s high-frequency PCB can maintain safe temperature levels, prolonging the operational lifespan and reliability of the vehicle.
Exposure to electromagnetic waves. One challenge that high-frequency PCBs face in EV applications is electromagnetic interference caused by high-powered or sensitive electronic parts being close to each other. One consequence is that electromagnetic waves can disrupt an EV’s operations, which can be detrimental to the safety of the passengers.
The solution to this issue is to add sufficient shielding, ground plane separation, and filtering to a PCB to weaken the effects of electromagnetic waves that can interfere with the vehicle’s functionality.
Spacing concerns. PCB designers are often challenged to find adequate space to safely fit components in EVs. Fortunately, there’s a simple solution: employ miniaturization techniques on the PCB design and add multiple functions on the circuit boards.
Miniaturization and multi-functionalization of the PCBs allow them to become more compact and lightweight, making it easier to fit into an EV’s electrical system.
Handling powerful electric currents. High-frequency PCBs must properly handle strong electric currents during vehicle operation, which carry a lot of heat that can build up inside the electrical systems. If left unchecked, the accumulated heat from the flowing currents can negatively alter EV performance and lifespan.
To address this concern, heavy copper and other advanced materials that can withstand strong currents are used on the printed circuit board — making it better at safely carrying electrical currents. Designers must also apply optimal layouts and heat dissipation mechanisms to ensure flowing electric currents are manageable.
High-frequency PCBs present challenges when used in EV applications. It’s imperative to address issues, such as thermal management, electromagnetic interference, space limitations, and electric currents. Fortunately, reliable solutions can effectively mitigate risks like overheating and reduced lifespan. EV
Viking Tech America Corporation is a manufacturer of passive components, including resistors, inductors, capacitors, and supercapacitors. As a global leader in thin film production, we support many ODM and OEM customers with high-reliability components that meet the highest standards such as AR..A Series
AR..A Series Benefits
• Available in sizes from 0201 to 2512.
• Tight tolerances of 0.01% to 0.1% for precision in critical designs.
• Low TCRs from 5ppm to 50ppm.
• Resistance range of 10 to 1MO.
• Suitable for applications in automotive applications, medical devices, testing equipment, and communication devices.
Viking Tech America Corporation
4 Executive Circle Ste 140 Irvine, CA 92614
+949-398-5228
sales@vikingamerica.com www.vikingamerica.com