Hybridsolutions


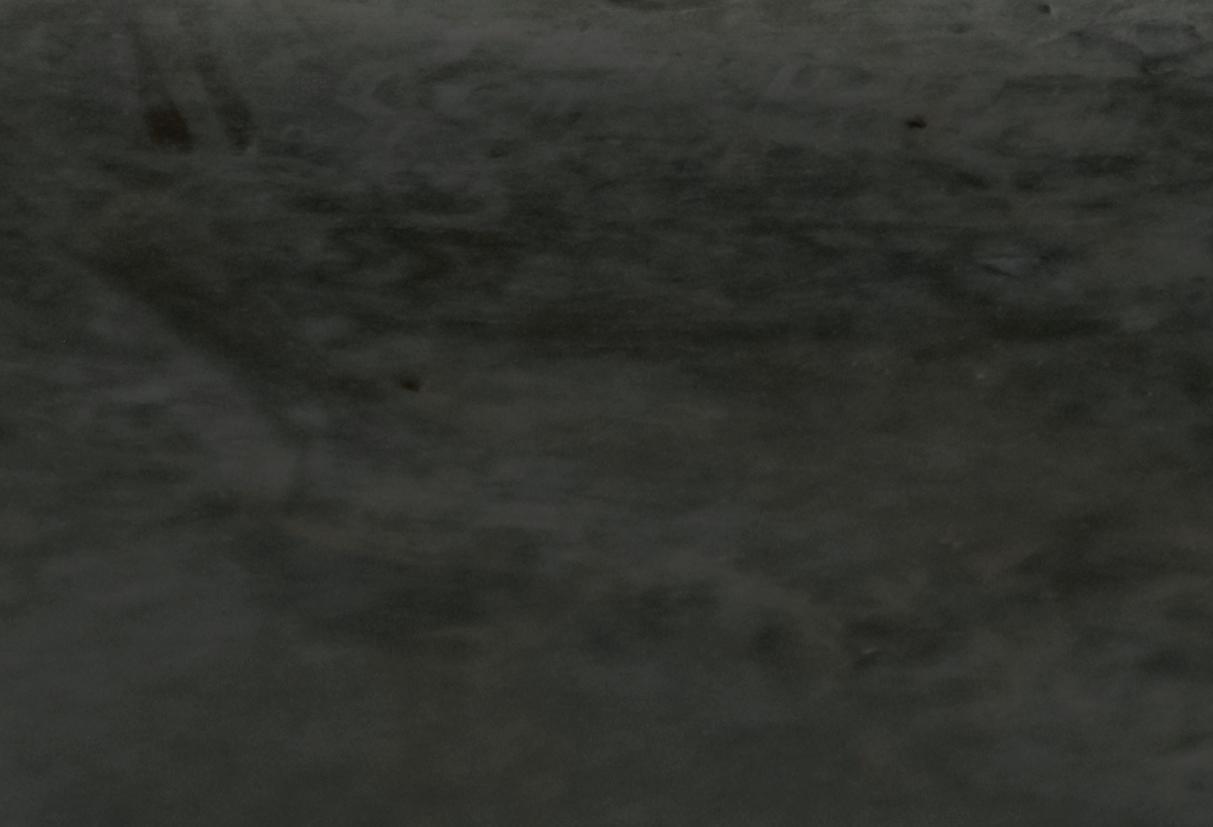
When mechanical anchors meet adhesives

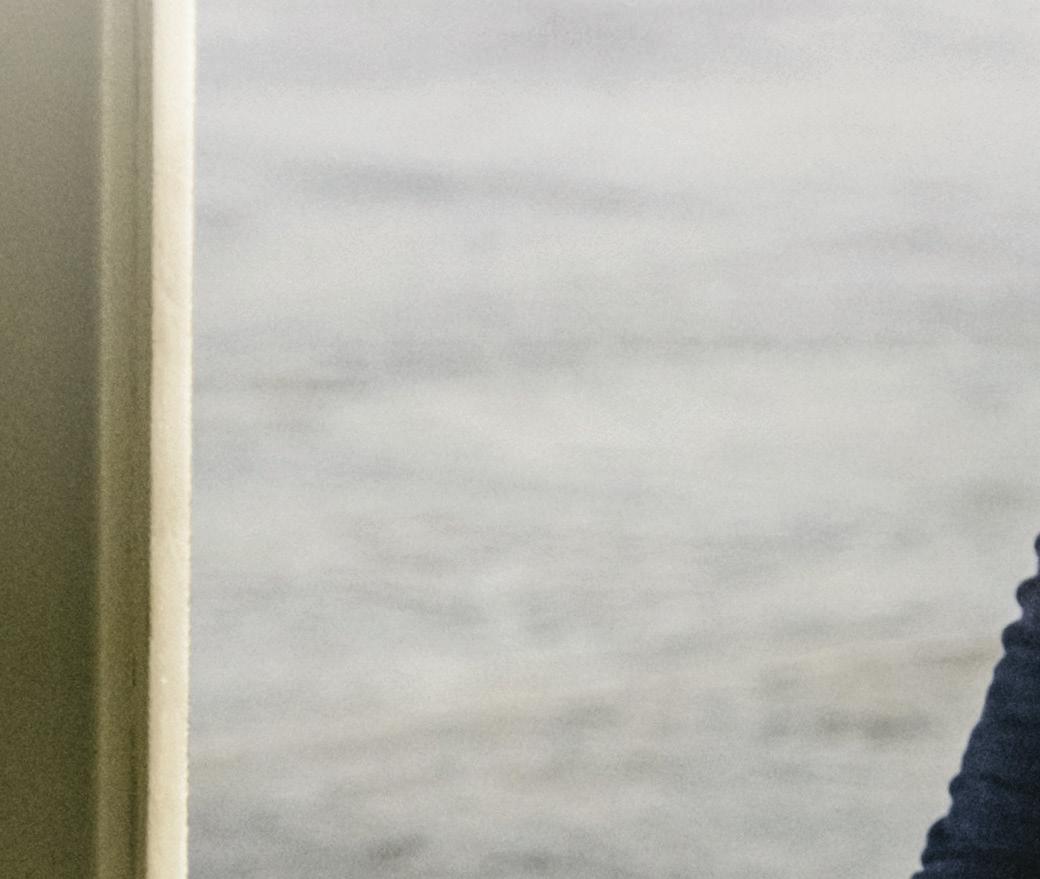
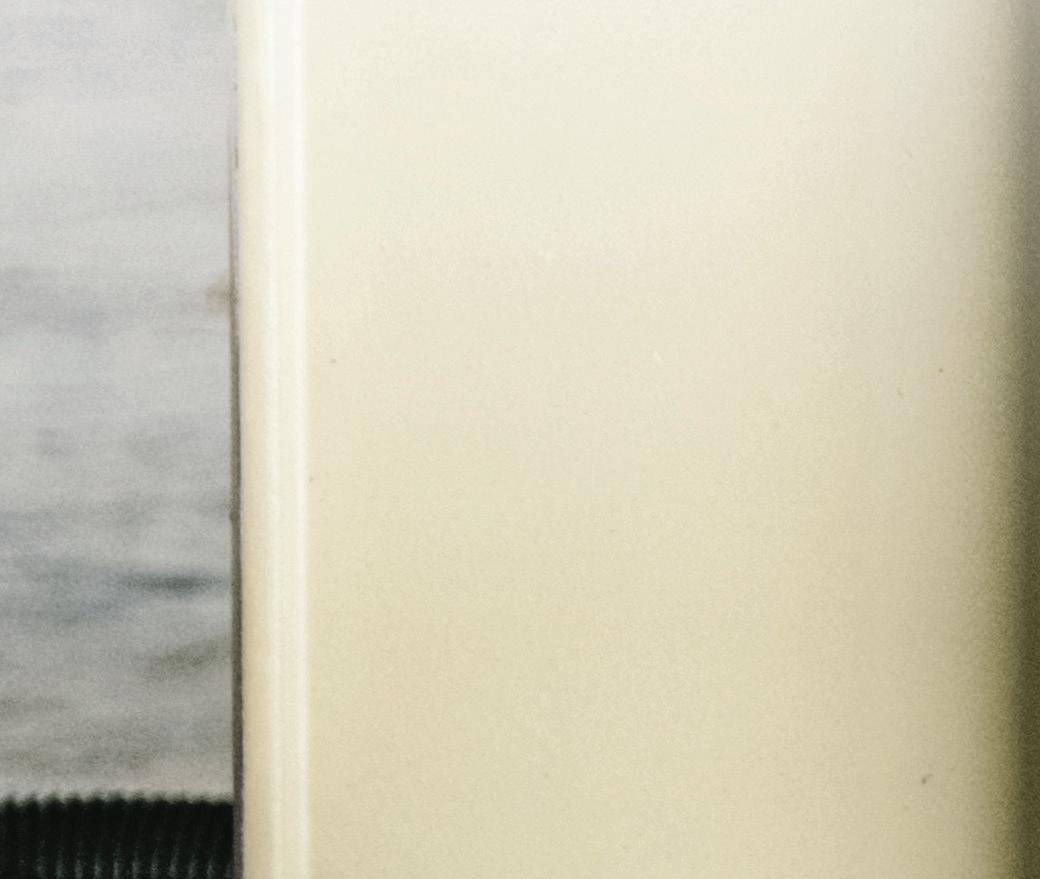

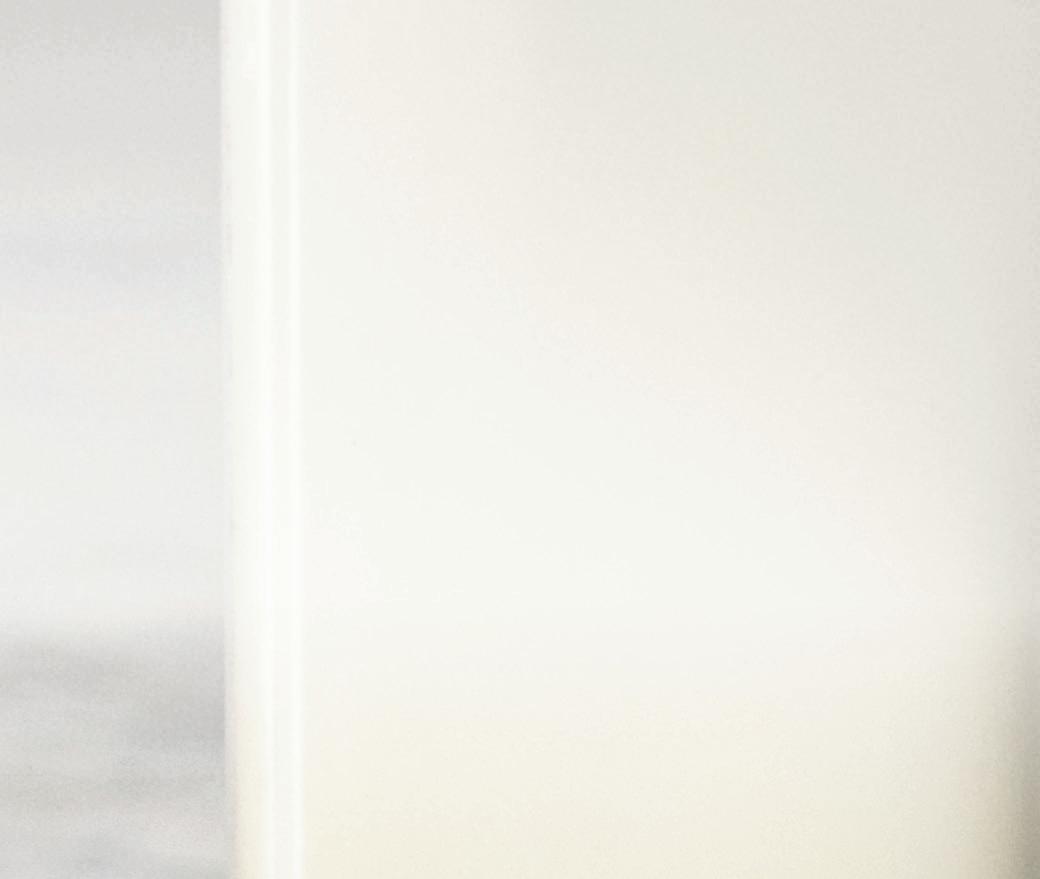


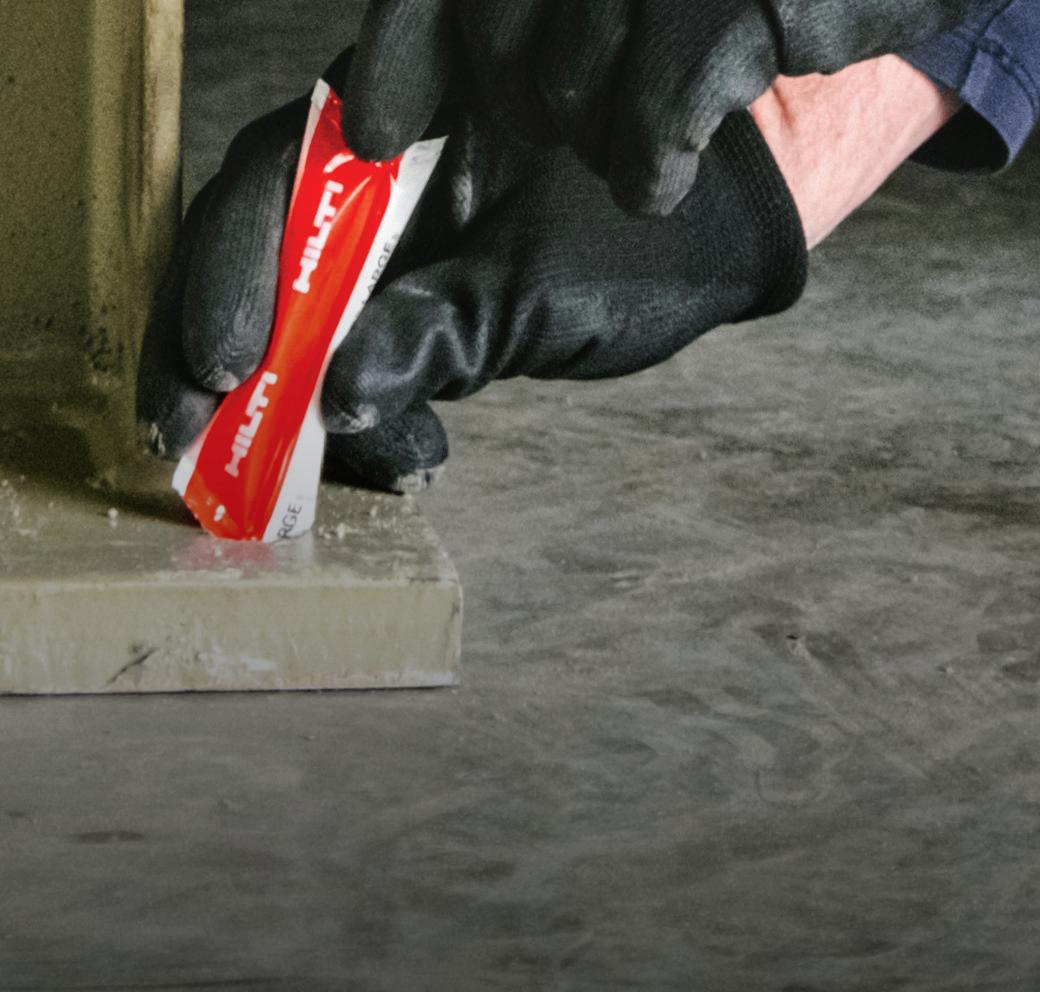

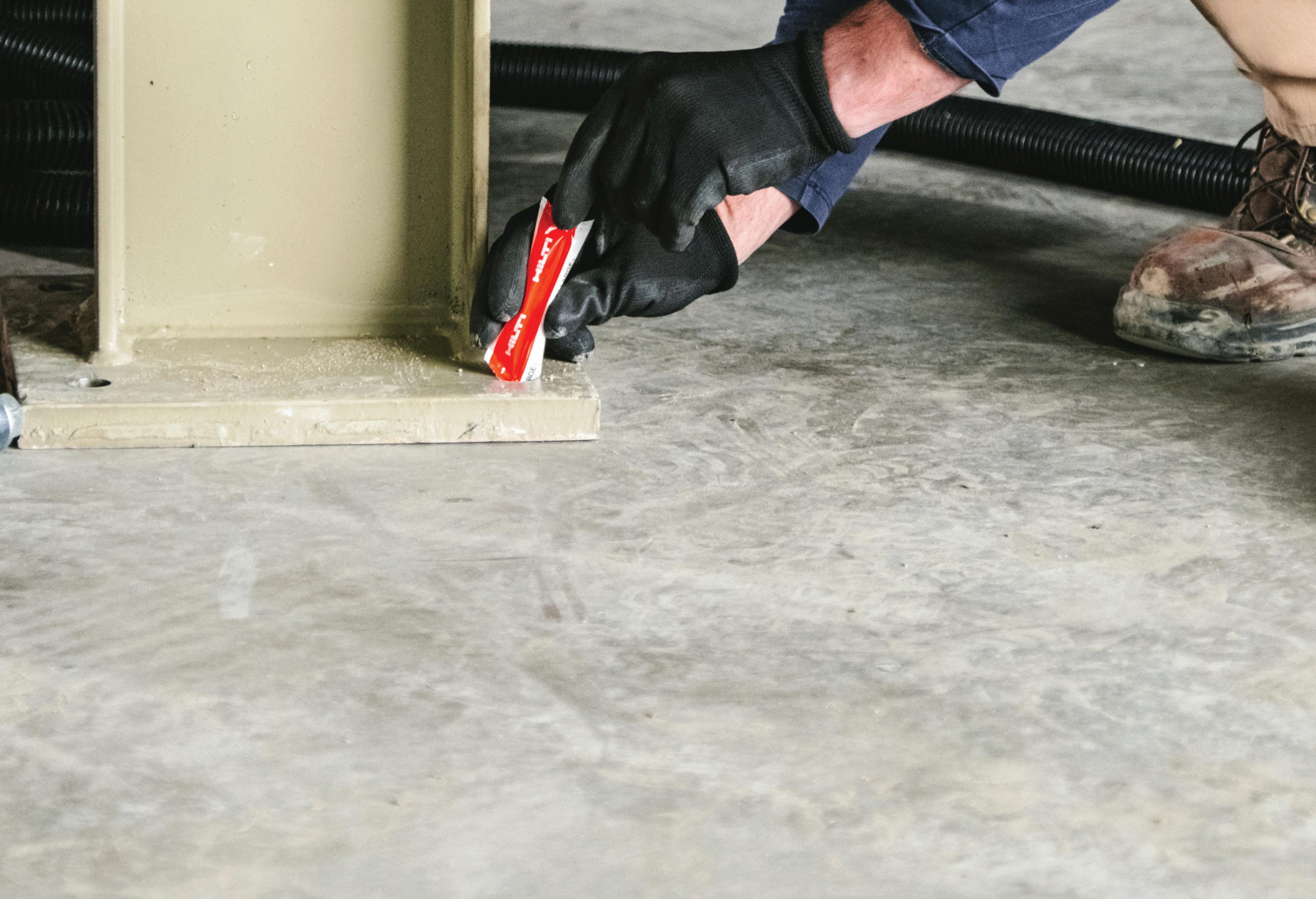
When mechanical anchors meet adhesives
Sift through a few headlines, and you’ll likely come across news about labor shortages in several sectors. The trades are not immune.
“Construction Workforce Shortage Tops Half a Million in 2023,” states the Associated Builders and Contractors. “Labor Shortages Forecast to Persist for Years,” predicts The Society for Human Resource Management.
Blame what you will: the pandemic, inflation, supply-chain constraints, an aging workforce, or something else. Ultimately, demands for production are not going anywhere and, in fact, are increasing in most sectors. The resilient industries will be those that innovate and rethink the status quo.
“Skilled labor is one of the biggest cost drivers of any construction or building site,” shares Josh Beasley, a product manager with Hilti North America and past field engineer.
“Unfortunately, it’s becoming increasingly harder to find, which is further driving costs. Add this to strict project deadlines and budget limitations, and it leaves contractors seriously looking for ways to speed and maximize the labor output they do have.”
One way to do so is to ensure a high level of training and experience — challenging, given the skilled labor shortage. Another way is to choose tools and methodologies that simplify and speed operations.
“We’re always focused on developing technology that’s faster, safer, and easier to use, and this is especially important in the current economy,” says Beasley. “Contractors might be limited by the available workforce, but we can support them with solutions that ease some of the burden.”
According to customer feedback, one area of project construction that has drained time and costs — and typically required skilled labor — was adhesive anchoring. So, the team at Hilti decided to do something about it. The company is a global provider and manufacturer of tools, technology, and services to the commercial construction industry.
“It’s been an iterative process that involved identifying the needs of engineers and installers,” he says. “Then, once we had a prototype of the initial product, we took it into the field to seek additional feedback until we narrowed down a technology that best suited both users’ needs.”
The result: a dual-action anchor that combines the high performance of adhesive anchors with the simplicity of screw anchors.
An anchor is a fastener designed to attach one or more fixtures to a concrete surface. Anchors are commonly used in the building and construction industries.
“Given a choice, an installer will almost always prefer a mechanical anchor because they’re quicker to install and cost-effective. An engineer, on the other hand, is likely to specify an adhesive anchor for heavier-duty applications because of the anchor’s high performance,” says Beasley. “So, sometimes there’s a bit of a tug-of-war between contractors and engineers about the ideal product to use, depending on the project.”
An adhesive anchor is a postinstalled fastener that’s inserted into
a drilled hole in hardened concrete, masonry, or stone. Loads are transferred to the base material by the bond between the anchor and the adhesive, and the adhesive and the base material.
“Adhesive anchors are the preferred choice to ensure high performance — whether that be load, edge, or spacing performance. They also offer flexibility over mechanical anchors,” he explains.
However, there is one drawback to conventional adhesive anchors, particularly during a labor shortage.
“Ask any installer on a job site, and they’ll tell you adhesive anchors involve a complex and slow installation process.”
According to Beasley, anchoring involves drilling a hole, blowing out the debris with an air compressor, and
brushing out the surface. The hole must be cleaned until it’s completely free of dust fragments before dispensing the adhesive and waiting for it to cure. A standard adhesive anchor in normal temperature conditions could take up to 30 minutes or longer to cure, which is time-consuming.
“It’s a slow process but an important one because each step is critical for the adhesive anchor to bond properly,” he says. “This means there are opportunities for errors and improper installation, so our team began reassessing what could be done to simplify the anchoring process.”
Enter the Kwik-X Dual Action Anchor, the first anchor of its kind on the market
that uses a high-performance adhesive in combination with a screw anchor. According to Hilti, this dual-action anchor can reduce installation time by up to 70% and save up to 20% of the total cost of installation when compared to conventional adhesive anchoring systems.
“We developed this new anchoring technology with the aim of a better, simpler installation process, which eliminates several traditional steps,” shares Beasley. “For one, there’s no use for an air compressor or brushes because the drilled hole requires zero cleaning. Additionally, the adhesive comes in a pre-apportioned capsule that eliminates the need for dispensers.”
The anchor’s mechanical interlock cuts into the concrete when installed, offering additional holding properties. The special adhesive formulation uses debris from the drilled hole, mixing it
in, which results in an aggregate that supports the adhesive bond.
“This is why we call it a dual-action anchor…it uses a mechanical screw that’s drilled into the concrete and an adhesive,” he says. “The curing time is also reduced from 30 minutes or more for a standard formulation to just 30 seconds.”
Since the adhesive comes in a preapportioned capsule, it also reduces the risk of under or over-filling the hole with adhesive.
“It’s not uncommon for installers to add excessive adhesive to avoid underfilling the hole. This can lead to reduced performance of the anchor and up to 30% waste of the adhesive, which is far from inexpensive,” he says. “So, we wanted to ensure zero waste is associated with this product.”
Overall, Hilti found that the new anchoring system offers up to four times faster installation compared to standard adhesive anchors. It’s also possible to remove and reinstall the dual-action anchor in the same borehole once if necessary.
“By simplifying and speeding up the installation process, we’re eliminating critical points that can go wrong in an adhesive anchor installation process — and saving significant labor costs,” says Beasley. “And given today’s labor climate, that’s a major benefit.”
Currently, the anchor technology is primarily used for buildings to attach primary and secondary steel columns and beams, as well as ledger angles to concrete. It’s also finding use in handrails, platforms, balconies, and even racking applications.
The new dual-action anchor includes a screw anchor and an easy-to-use adhesive that comes in pre-measured capsules.
The anchor’s mechanical interlock cuts into the concrete when installed, offering additional holding properties. The special adhesive formulation uses debris from the drilled hole, mixing it in, which results in an aggregate that supports the adhesive bond.
However, the Kwik-X system took time to develop for the market. It was challenging to determine how to test an anchor that uses both chemical and mechanical anchoring against criteria solely built for one or the other.
“This was the first time a hybrid fastening system was reviewed by the governing bodies that be. Previously, there was no framework for developing or testing a mechanical and adhesive anchor to ensure it measured up to code,” he says. “So, it was an interesting and substantial process to get to the point of launching the Kwik-X in the market.”
Beasley adds: “It’s also very rewarding because we believe the dual-action adhesive anchor is a game-changer for the industry, especially as fewer people are going into the trades. Anything that can make these jobs faster, easier, and more efficient will be essential.” FE
Flat: Generally used for load disbursement
Tab/Lock: Designed to effectively lock an assembly into place
Finishing: Often found on consumer products
Adhesive anchors typically offer greater flexibility than mechanical anchors, ensuring high performance for heavy-duty applications.
Wave: For obtaining loads when the load is static or the working range is small
Belleville: Delivers the highest load capacity of all the spring washers
Fender: Distributes a load evenly across a large surface area
Shim Stacks: Ideal for simple AND complex applications
Boker’s Inc.
3104 Snelling Avenue
Minneapolis, MN 55406-1937
Phone: 612-729-9365
TOLL-FREE: 800-927-4377
(in the US & Canada)
bokers.com