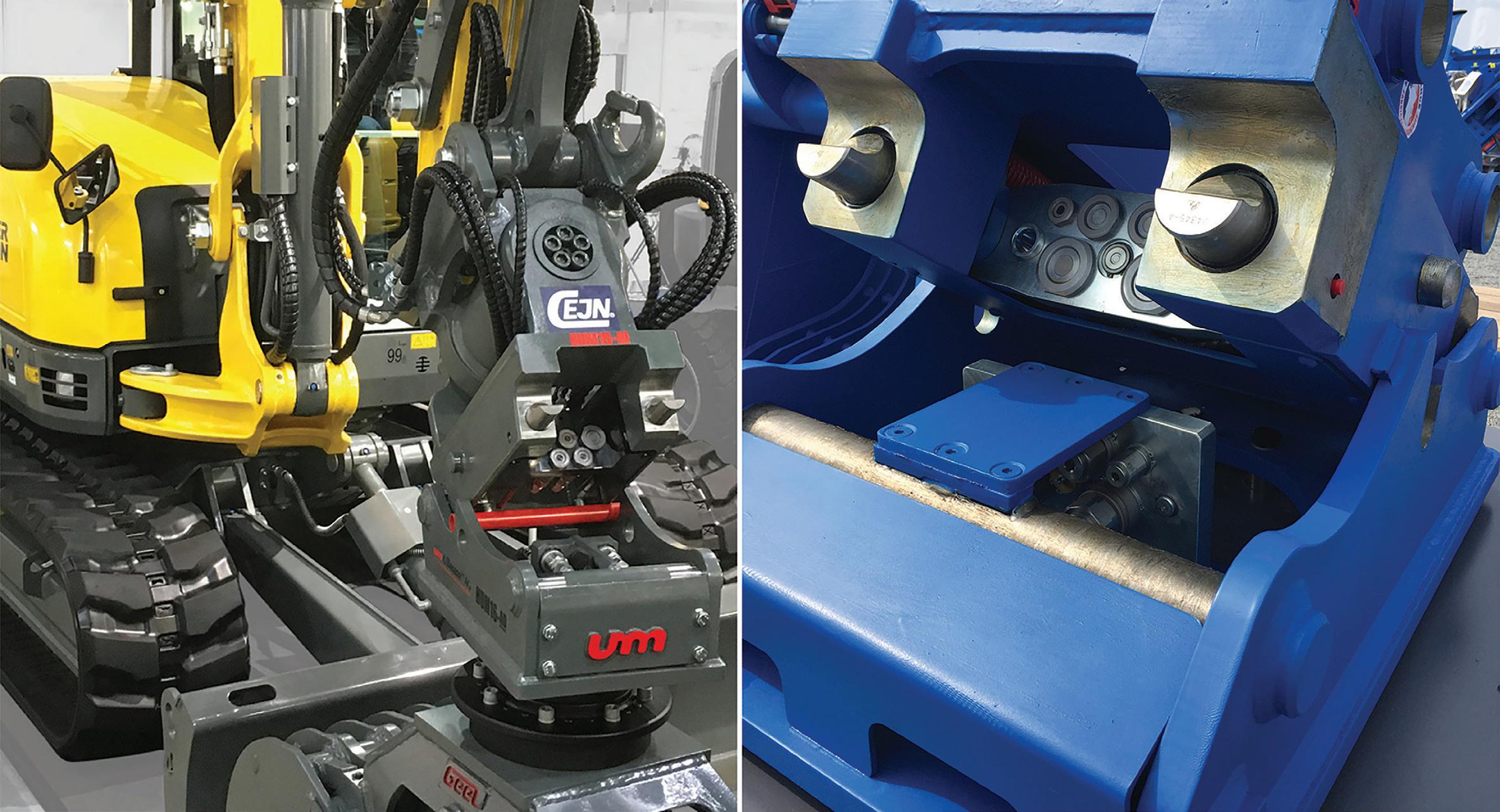
10 minute read
August 2020 Design Notes
Advances in hydraulic connection technology are again evolving within mobile machinery and tool attachment design while positively impacting professional use. The increased demands of worksite productivity and efficiency by the expert user have challenged manufacturers of machines, attachments, and component suppliers with technological improvements. After all, “time is money.” This article focuses on the advances of the autodock system — What is it, what is causing this demand, and how is it impacting manufacturers and professionals?
To better understand how auto-dock systems provide much-needed support, let’s review the evolution of hydraulic quick connects.

Center Auto-Dock
ISO A/B “poppet” quick connect coupling
Often termed the general-purpose quick connect, its basic design was only to offer an economical means to connect and disconnect hydraulic lines between machines and tools and attachments. This basic quick connect coupling has been in use for more than 50 years.
ISO 16028 “flat Face” quick connect coupling
Demand required the introduction of a no-spill/ non-drip quick disconnect and easier “one-handed” connection — to eliminate oil loss and reduce contamination to the hydraulic system. Eventually, a residual pressure elimination nipple was introduced to ease concerns with difficulty in connecting attachments from thermal expansion.
Screw-to-connect coupling
The development of heavier duty machines increased concerns with vibration damage and surge flow issues. A screw-to-connect coupling allowed a quick break for heavier duty equipment while withstanding the difficult application effects of vibration and surge flows (helping to reduce and eliminate failures when using previous quick-connect designs).
Hand-operated multi-connector system
As multiple hydraulic functions were incorporated into machinery, this increased the amount of hose routing connections. Challenges were made to reduce overall envelope size, eliminate cross-connection, residual pressure issues, and save overall connection and disconnection time. Handoperated multi-connectors achieved all of these goals and opened up acceptance towards auto-connectors.
Fast forward to 2020 — today’s auto-dock system
This latest technological advance, an auto-dock system, allows a professional machine operator to change tools and attachments without leaving their cab. This is achieved by incorporating fit plates and blocks, using hydraulic cylinders and locking mechanisms, guide assistance, and electrical cab controls into a single configuration at the point between machinery and tools and attachments.
During connection or disconnection, an auto-dock system completely connects or disconnects all hydraulic lines, all electrical connections, any water lines, air lines, etc., simultaneously. Using this type of system greatly reduces downtime between tool/attachment changes to about 10-20 sec overall when compared to the more traditional 5-10 min. An autodock system also helps eliminate issues related to cross-connection (user error of connecting/disconnecting all lines) and also helps eliminate “hanging components” that may be damaged in tight workplaces (like snagging a hose in close quarters on rebar or rubbing hoses against concrete).
Over the last 10-plus years, a couple of familiar companies have offered aftermarket auto-dock systems for small and medium-sized machinery, mainly geared for small business implementation. As mobile machinery and tool/attachment manufacturers have realized the values of an auto-dock system (by customer demand for improved overall savings), they are beginning to include them with new model introductions.
Several larger OEMs have also begun offering auto-dock systems bundled with standard tools/attachments. This provides professional users with a multi-function machine with greater capabilities and uses at each job site. Auto-dock systems are currently finding greater popularity in demolition and recycling industries (any site where cleanup is involved, and many tools/attachments are used). Still, the values can be gained in many mobile applications and industries.
As each manufacturer continues to develop capabilities using auto-dock systems, it will continue to revolutionize other mobile industries, similar to the influences caused by previous quick connect technologies. There are two common systems presently in use: horizontal and vertical connection. Thus far, the vertical connection system has been better received. It offers greater protection and improvements with the general lifespan on all auto-dock connections from dirt, debris, and other environmental conditions.
A key consideration for auto-dock systems is the frequency of tool/attachment changeouts. Suppose a professional machine operator has to frequently change out a specific group of tools/attachments each workday. In that case, this is a suitable target that should be evaluated for time loss reductions with implementation of an auto-dock system. An important question often asked by fleet and site managers (for each job site) is how much equipment and personnel are required to get each job done. If a machine typically uses the same 4-5 attachments or several machines share a group of tools/ attachments (depending on the size of the job), it’s possible to increase the overall productively with an auto-dock system. It can free up valuable inventory and personnel for additional work sites.
Another element to auto-dock systems is the consistency of design and usage. This is especially important when it comes to wear and tear on components used in mobile machinery. Logically, an auto-dock system allows operators more consistent conditions between connection and disconnection change out needs. Removing unnecessary variables (including user-inconsistencies), helps improve the overall life of components in this connection point system. The addition of sensors and other safety aspects also helps redirect from reactive towards proactive maintenance, including a desired predictive maintenance schedule.
This technology shift is quickly bringing value to the mobile machinery industries. Once the investment is made, the professional fleet can quickly identify their return on investment. It allows professional machine operators to work more effectively at each job site while allowing fleet or site managers to better plan and accommodate more jobs.
From a manufacturing standpoint, OEMs can capitalize on advancing technology while meeting customer demands for improved productivity and efficiency. As auto-dock systems are used more often in mobile machinery industries, this technology should provide additional business opportunities compared to companies reluctant to adopt new ideas and principles.
Should you consider an auto-dock system?
1. Does your team or your customers have machines that frequently change out tool/attachments during each workday?
2. Has your team or your customers experienced issues related to a forgotten connection (i.e., hydraulic, electrical, water, air, etc.) during tool/attachment change outs?
3. Does your team or your customers often deal with damaged hose assemblies from hanging hoses in more confined work areas?
4. Has your fleet or site manager or your customers complained about effectively sharing machinery between job sites? 5. Does your team or your customers often dedicate specific tools/attachments to specific machines?
6. Would your team or your customers be interested in reducing maintenance costs between machines and tool/attachments?
7. Is your team or your customers weighing additional machines and tool/ attachments purchases versus trying to find ways to maximize usage with their existing fleet?
If you answered “yes” to one or more of these questions, it’s time to learn more about auto-dock system technology.
CEJN | cejn.com
Rational speed sensors allow highly sensitive mobile machine control
Holmer Maschinenbau GmbH, a German-based agricultural company, developed the first self-propelled six-row sugar-beet harvester in 1974. Since that time, the Holmer machines have been in successful operation by customers in over 40 countries world-wide.
On its sugar beet harvesters, it requires a precise collection of actual values directly at the place of consumption (propulsion, toppers, and sugar beet transport systems). These data points are an absolute requirement for the optimum balancing of performance requirements of its high-performance harvesters for various consumers. The entire system must react precisely and quickly to the changing demands of the decentralized consumer.
For example, harvesting when the soil is looser requires less power for the harvesting module and driving through deep soil requires more propulsion power. These parameters can change during a harvesting process, making constant adjustments necessary.

Rheintacho’s FC-series rotational speed sensor
Decentralized collection of the actual, current performance needs allows a precise adjustment to the power production. Rotational speed sensors from Rheintacho are used to record one of the most important performance indicators, namely the rotational speed of the hydraulicallydriven operations, in a cost-effective way and without construction restrictions.
The sensor electronics of the fitted FC-series with asymmetric, one-eyed flange is constructed as a two-channel hall differential sensor. This sensor range complies with the standard DIN/EN 13309 (construction machines, agricultural technology). It is designed to withstand especially high temperatures (up to 160 °C) and pressures thanks to its special brass alloy. The brass sensor complies with protection type IP69K thanks to its intelligently designed sealing system.
The sensors of the FC-series have two frequency outputs. The extremely narrow tolerated phase shift of 20° in identifying the direction of rotation means that the sensor provides a highly precise signal and enables highly sensitive controlling.
The prompt, contact-free measurement of shaft speed in these modern mobile hydraulic control circuits from Rheintacho has become an essential part of the Holmer system to guarantee the best harvesting results with minimal influence from the soil environment.
Rheintacho | rheintacho.de
Mini factories in containers help reduce mask shortages
Disposable protective nasal-and-mouth masks are in short supply, but a manufacturing system from Swiss company Mikron could put masks within everyone’s reach. This scalable system produces 50-100 face masks per minute, depending on the version. With engineering support from Festo, Mikron developed the system in just six weeks.

Fits in a 20-ft shipping container: Mikron’s system for producing 50- 100 protective masks a minute.
Mini factories in containers
The beauty of Mikron’s system is that it fits in a 20-ft shipping container, which can also act as a cleanroom. The factory in a box could be located in front of a hospital, next to a shopping center, or near a school. The integrated air-conditioning system with air purification filters makes production possible even in places with a high risk of viral contamination. With adequate raw materials, the system can operate autonomously for more than two hours.
“This reduces the number of people required to operate the system, and as a result, lowers the risk of infection,” explains Nils Rödel, General Manager of Mikron Berlin. “The mini factory can produce protective masks in remote areas or even in crisis zones where meeting hygiene standards is most challenging.”
It would be possible to produce two million protective mouth-nose masks each month with just one system. The masks are based on meltblown, nonwoven fabric, which consists of many layers of fine fibers and thus filters out even the smallest particles such as bacteria and viruses from the air.
“Using official statistics, we calculated that medical personnel in Germany alone need at least 50 million disposable protective mouth-nose masks per month,” reports Rödel. “We could meet this demand with 25 containers.”
Eliminating the need for transport makes the end product less costly. Depending on how it’s configured, the system can make packs of ten masks or individual ones, shrink-wrapped for cleanliness, and packaged in printed bags and boxes if required. “Packaging masks involves docking an automated station developed by pi4_robotics GmbH, Berlin, a project partner,” says Rödel.
Reliable supply of system components
Electric and pneumatic components from Festo ensure the transport, clamping, unwinding, shaping, and folding for the non-woven fabric. An ultrasonic sealing station seals the edges. The servo drives CMMT from Festo are used for controlling the electric drives, EMMT are also used in the application because they can be easily connected to PLCs from major manufacturers, including Beckhoff, Siemens, and Rockwell.
The pneumatic components from the Festo core product range installed in the system — such as the compact cylinder ADN, the guided drive DFM, and the round cylinder DSNU —are in stock worldwide and available for shipment within 24 hours. Global availability enables quick and reliable manufacture of systems for producing masks within a condensed time frame. The pneumatic drives are actuated by MPA valves. The safety valve MS6-SV-E ensures that safetycritical system components are exhausted and de-energized as quickly as possible in the event of a sudden emergency stop.
Thanks to its international production and sales network, products from Festo are quickly available in 176 countries and enable systems to be built at locations worldwide. This is entirely in keeping with the global open-source approach of Project CAROLA, which provided the impetus for designing the mask production system in a shipping container.

Earloops added and done: Mikron’s scalable system produces 50-100 masks a minute, depending on the version.
Independent, decentralized, and virtual
“The current travel restrictions make it extremely difficult for commissioning technicians to go where the systems are to be built,” says Rödel. “Mikron came up with a digitized solution. We use Microsoft HoloLens, which enables commissioning to be done virtually using an interactive 3D projection.” FPW
FESTO | festo.us