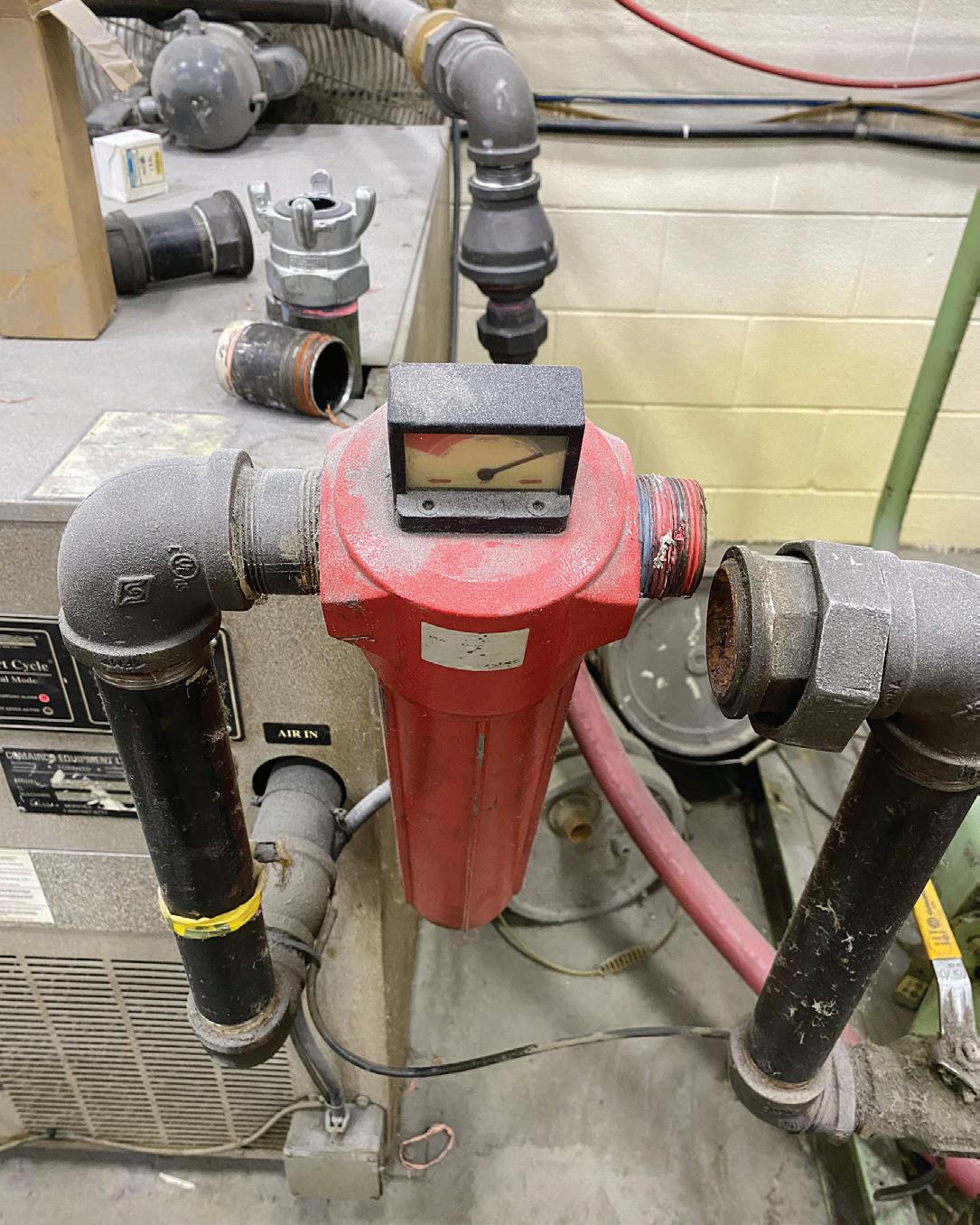
1 minute read
Compressed air fail: The spare dryer
A printing plant had two compressors — one main and one backup — each with refrigerated air dryers. Athird air dryer was on site as a backup, should the main dryer go down for any reason. The spare compressorwas too small for the plant but was used as emergency backup, in case the main compressor would fail.
An air auditor viewed the installation with the goal of reducing the system’s energy consumption. The auditor typically would measure the kW of each component to ensure things were working as they should. When he measured the air dryer, he was surprised to see the unit was consuming power but was not even hooked up to the compressed air system. The dryer does not have an “off” switch, so it must be deenergized at the disconnect switch.

This spare refrigerated dryer was not even hooked up, yet its refrigeration circuit continues to consume power.
Air dryers consume much less power than air compressors. In this case, the consumption was only about 1.5 kW, but the operating costs can certainly add up over time. This useless dryer was consuming about $900 per year in electrical costs — while doing absolutely nothing!
The same effect is often seen in other locations when non-cycling air dryers are used as spares or coupled with compressors that are not running (sometimes the offending dryer is inside the compressor enclosure). Non-cycling dryers usually consume near rated kW if left running, even when there is no compressed air flowing through them.
The key to avoiding this kind of energy waste is to turn the spare dryer off when not being used — and to purchase cycling air dryers for any situation where the dryer will not be processing air full time or will be partially loaded. Save yourself some money by attending to your air dryers!

Ron Marshall • Contributing Editor