


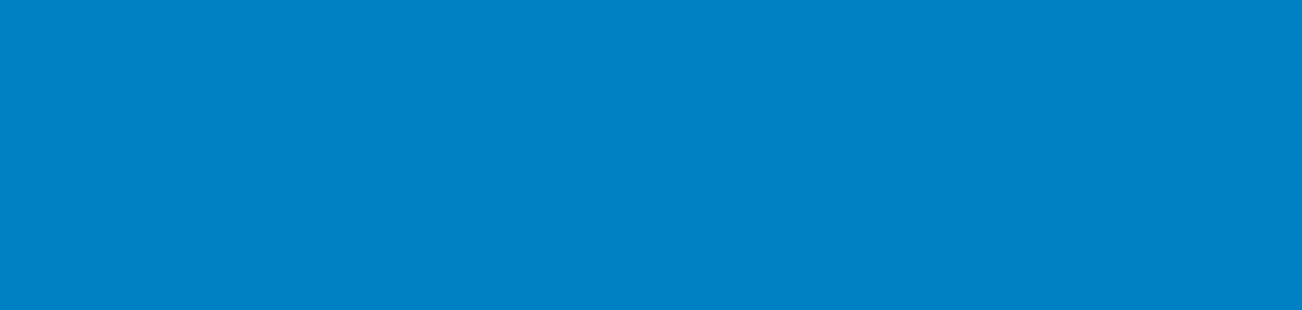
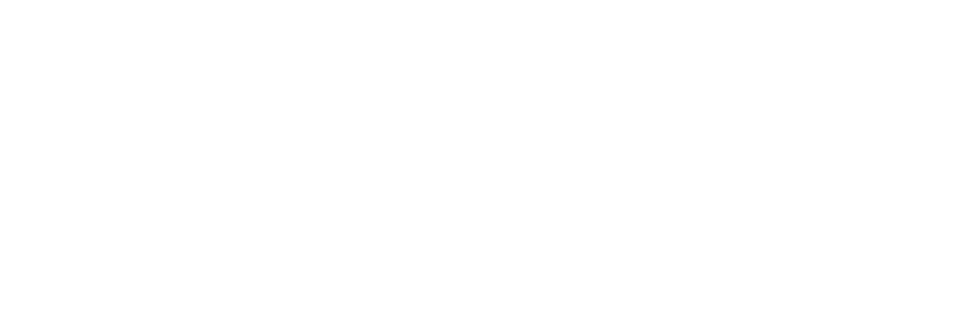



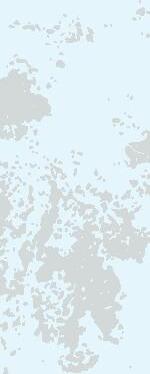
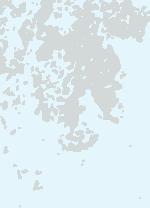



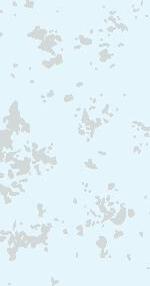
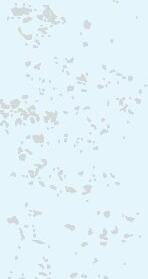






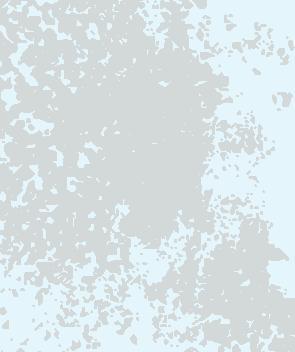
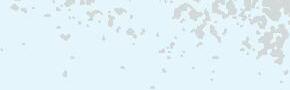



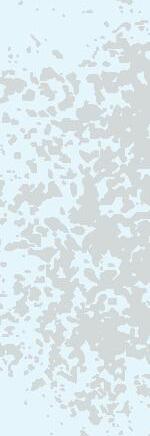
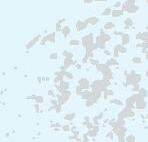
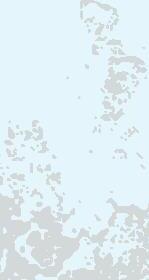



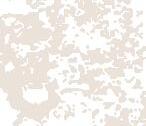
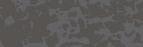

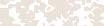
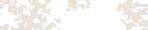


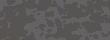



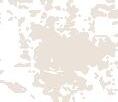











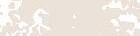
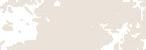




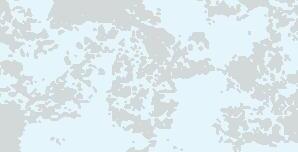


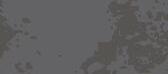





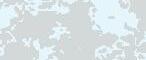
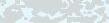






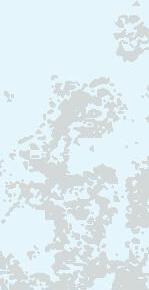
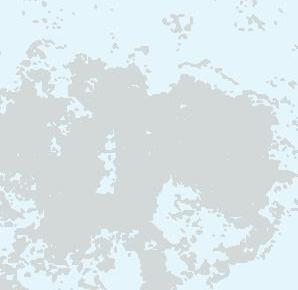
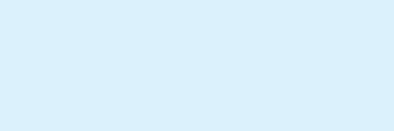



Everything you need at great prices, in stock and ready to ship same day
AIR PREP COMPONENTS STARTING AT $24.00 (AF2-223)
SOLENOID VALVES STARTING AT $24.50 (AVS-3111-24D)
All pneumatic motion requires clean and dry air. The process of filtering, regulating and lubricating compressed air is known as air prep. The Norgren and NITRA family of air preparation components include:
• Particulate filters with 40 micron filter element (5 micron option), coalescing type and oil vapor removal in sizes from 1/8” to 1” NPT port sizes
• Regulators with adjustment from 4-58 PSI, 7-60 PSI, 7-130 PSI and 4-145 PSI
• Combination filter/regulators available with same options in one unit
• Lubricators in 1/8” to 1” port sizes
• Total air prep units that combine all air preparation functions in one compact unit
Solenoid valves are electrically controlled to direct air flow to sequence operations in pneumatic systems. Solenoid valves are used to control cylinders, rotary actuators, grippers and other pneumatic devices. Use a manifold to simplify plumbing for a bank of valves. Modular systems even allow networked control of valve group.
• Available as stand-alone units or as part of a compact modular valve system
• Stand-alone units can be used with optional manifolds to make system configuration simpler
• Available in 3-port/3-way, and 5-port/4-way styles
• 4-way valves come in 2-position or 3-position styles with center closed or center open
PNEUMATIC CYLINDERS STARTING AT $13.50 (A07005SN)
ALL COMPONENTS AS SHOWN TOGETHER $418.75
The most popular style of pneumatic actuator uses compressed air acting on a piston inside a cylinder to move a load along a linear path.
• Round body cylinders available in single-acting or double-acting styles, with up to an 18-inch stroke and 2-inch bore. Also available in stainless steel. Magnetic pistons are optional.
• NFPA tie rod air cylinders come in double-acting style, with up to a 32-inch stroke and 4-inch bore. All include a magnetic piston. Adjustable air cushions are an option.
• ISO 15552 air cylinders are double-acting cylinders with up to a 600mm stroke and 100mm bore. All include magnetic pistons and adjustable air cushions.
• Metric and Inch compact air cylinders as well as dual rod guided air cylinders also available.
As we gear up for IFPE 2023 and all that comes with it, it’s good to know we’ll still be riding a positive wave throughout this year. Although many economists have warned of a softening in the fluid power market, so far that softening has been just that — soft. According to the NFPA, the 12-month moving average of shipments for pneumatics, hydraulics, and total fluid power continue to grow. The year-to-date percent change for total fluid power shipments in December 2022 is 16.6%, down from 16.9% in November. As most experts predicted, the drop is minimal so far and our industry is still strong.
Despite inflation, threats of recession, and question marks on jobs (just today as I write this, we’ve seen record numbers!) IFPE and CONEXPO-CON/AGG are shaping up to be the biggest iterations of these shows yet.
But just big doesn’t necessarily mean better. What will be a key indicator of the health of our industry will be in the innovations one can expect to see there — major OEMs and small, niche component manufacturers’ takes on electrification, digitalization, and sustainability are all leading to reshape fluid power for the better.
Already, we’ve learned about:
• Danfoss’ Dextreme system, which is based on its Digital Displacement technology. It provides a pathway to 50% energy savings by tackling losses in the whole excavator hydraulic system.
• Hallite’s new products, featuring renewable or recyclable raw materials that have been tested to reduce environmental impact without compromising quality and performance.
• Volvo’s commitment to being fossil-free by 2040. Volvo will be highlighting its range of commercially available electric machines, related charging infrastructure, and sustainable power alternatives. Key here will be a redevelopment of the hydraulics on some of its electrified machinery to increase hydraulic efficiency and battery power.
• Elobau will highlights its new plug-and-play safety tested system with its 225MA midi armrest. It was designed with sustainability in mind, as 75% of the plastics used are bio-based materials made from castor oil (instead of petroleum).
• Bosch Rexroth will showcase a wide variety of technologies suited for mobile equipment, including the eLION electrification platform.
• Caterpillar will highlight its four new electric machines as well as prototype batteries.
As these examples indicate, anyone who says that the fluid power industry is stagnant or dying is dead wrong. We at Fluid Power World are committed to helping move the industry forward as well, by providing access to informative, educational content in many formats. Stop by our booth in the South Hall Lobby, where you can:
• Meet the folks from CD Industrial/Lunchbox Sessions. Our popular and longtime contributor Carl Dyke will be on hand and will have his schematics running in our booth — to show you a better and more visual way to learn fluid power circuit troubleshooting and design.
• Get hands-on with the five winning product technologies from our LEAP (Leadership in Engineering Achievement Program) Awards. Samples of DGD Fluid Power’s Cartridge Flow Transmitter (CFT), Danfoss’ shhark low-noise gear pump, Webtec’s RFS200 Run-time Meter, Norgren’s Excelon Plus Integrated Electronic Pressure Sensor (IEPS), and Emerson’s AV/ AES Valve System with integrated OPC UA, will be available in our booth for you to see why these technologies won the nods of our esteemed judges.
• Learn about our upcoming print and online content, including magazine issues, videos, online exclusives, and our NEW series of educational webinars slated for the Fall of this year.
Of course, I, Paul Heney, Rachael Pasini, and Ken Korane, as well as our video staff and publishing and sales team, will be on the show floor looking to connect with industry experts. Please stop by booth SL-80022 to say hello, talk shop, and learn more. We’re excited to discover all that will be new in fluid power in 2023 and beyond. More importantly, what we learn in Vegas, won’t stay in Vegas. You’ll see it all here on the pages and screens of Fluid Power World FPW
We’re all looking forward to the IFPE show next month, but the show’s operator, the Association of Equipment Manufacturers (AEM), has also been busy with other matters. This past October, the association surveyed 179 equipment manufacturing executives to find out their thoughts on supply chain disruptions and bottlenecks — and the impact it has had on production, lead times, and profits. The survey also asked about component availability and optimal inventory levels, as well as potential solutions.
AEM said that 98% of respondents still face supply chain issues, with 58% experiencing continuously worsening supply chain conditions. The two driving factors of current supply chain disruptions are workforce shortages and access to intermediate components for production.
“Far too many equipment manufacturers still feel the impact of the COVID-19 pandemic and supply chain disruptions on operations, lead times on components, labor force participation, and financial performance,” said Kip Eideberg, AEM’s SVP of government and industry relations. “The impact of this supply chain crunch is only worsened by nationwide workforce shortages seen across the country, which is particularly noticeable on our shop floors.”
“AEM continues to survey our member company executives to better understand how they are impacted by continued high inflation, strained supply chains, and global instability, and to provide elected officials with the data points they need to move legislation that will revitalize U.S. manufacturing and bolster U.S. global competitiveness,” said Eideberg. “Republicans and Democrats can take immediate action by extending R&D expensing, enacting meaningful permitting reform, removing tariffs on a range of critical components, and reaching a bipartisan agreement on the debt ceiling.”
Other findings include:
• Roughly 60% of equipment manufacturers are still having issues with workforce recruitment and retention.
• Year to date, equipment manufacturers were seeing an average of 12% production loss and were forecasting a slightly lower, but still significant, production loss of 8.2% in 2023. This production loss is especially critical when many manufacturers are fully sold out for 2023.
• Year to date, equipment manufacturers were seeing an average of 8.6% profit margin loss and were forecasting a 6.4% profit margin loss in 2023.
• Lead times continue to be an obstacle. While they understandably increased during the pandemic, lead times have only continued to grow as things stabilized, jumping from an average of 2.42 months in 2019 to 6.92 months in 2022.
• Certain parts remain difficult to acquire. In the agriculture sector, the most sought-after components are tracks (and their included components). Only 27% of inventory is available for components that manufacturers deem most optimal for their operations. In both agriculture and construction sectors, that means semiconductors and chips, with an average of 44% optimal inventory available across both sectors.
• There is no single solution to the ongoing supply chain disruptions. FPW
Paul J. Heney VP, Editorial Director pheney@wtwhmedia.com On Twitter @wtwh_paulheney Compact safety rotary encoders for position and speed measurement
Dynamically compensated inclination sensors for precise angle measurement
Position sensors for stroke measurement in hydraulic cylinders
STRONG – SAFE – EFFICIENT SENSORS FOR MOBILE AUTOMATION
IFPE COVERAGE
IFPE looks to up the ante in 2023
The triennial fluid power megashow returns to Las Vegas from March 14-18.
INDUSTRIAL HYDRAULICS
Preventing noise and vibration in industrial hydraulic systems
Learn how to reduce the damaging side effects of noise and vibration caused by hydraulic power units in industrial settings.
MOBILE HYDRAULICS
Why modern equipment can benefit from higher-performance hydraulic fluids Today’s hydraulic fluids are forced to operate in hotter environments. But the right formulation can help reliably moderate temperatures, creating significant operational benefits for end users.
SHOW PREVIEW
Hannover Fair 2023: Motion, drive, automation firms accelerate digital transformation
The every-year Hannover Messe is slated for April 17-21, with more than 2,000 exhibitors expected.
28 60 66 70
EDITORIAL
VP, Editorial Director Paul J. Heney pheney@wtwhmedia.com @wtwh_paulheney
Editor-in-Chief Mary Gannon mgannon@wtwhmedia.com @dw_marygannon
Technology Editor Ken Korane kkorane@wtwhmedia.com @fpw_kenkorane
Senior Editor Rachael Pasini rpasini@wtwhmedia.com
Associate Editor Heather Hall hhall@wtwhmedia.com @wtwh_heathhall
Contributing Editor Josh Cosford @FluidPowerTips
Contributing Editor Carl Dyke @carlindustry
Contributing Writer Robert Sheaf rjsheaf@cfc-solar.com
PRINT PRODUCTION
VP, Creative Services Mark Rook mrook@wtwhmedia.com @wtwh_graphics
Senior Art Director Matthew Claney mclaney@wtwhmedia.com @wtwh_designer
Senior Graphic Designer Allison Washko awashko@wtwhmedia.com @wtwh_allison
Graphic Designer Mariel Evans mevans@wtwhmedia.com @wtwh_mariel
Director, Audience Development Bruce Sprague bsprague@wtwhmedia.com
VIDEO SERVICES
Videographer Garrett McCa erty gmccafferty@wtwhmedia.com
Videographer Kara Singleton ksingleton@wtwhmedia.com
MARKETING
VP, Digital Marketing Virginia Goulding vgoulding@wtwhmedia.com @wtwh_virginia
Digital Marketing Manager Taylor Meade tmeade@wtwhmedia.com @wtwh_taylor
Digital Marketing Specialist Shannon Pipik spipik@wtwhmedia.com @WTWH_Shannon
Digital Production/ Marketing Designer Samantha King sking@wtwhmedia.com
Marketing Graphic Designer Hannah Bragg hbragg@wtwhmedia.com
Webinar Manager Matt Boblett mboblett@wtwhmedia.com
Webinar Coordinator Halle Kirsh hkirsh@wtwhmedia.com
Webinar Coordinator Kim Dorsey kdorsey@wtwhmedia.com
ONLINE DEVELOPMENT & PRODUCTION
Web Development Manager B. David Miyares dmiyares@wtwhmedia.com @wtwh_webdave
Senior Digital Media Manager Patrick Curran pcurran@wtwhmedia.com @wtwhseopatrick
Front End Developer Melissa Annand mannand@wtwhmedia.com
Software Engineer David Bozentka dbozentka@wtwhmedia.com
Digital Production Manager Reggie Hall rhall@wtwhmedia.com
Digital Production Specialist Nicole Lender nlender@wtwhmedia.com
Digital Production Specialist Elise Ondak eondak@wtwhmedia.com
Digital Production Specialist Nicole Johnson njohnson@wtwhmedia.com
VP, Strategic Initiatives Jay Hopper jhopper@wtwhmedia.com
PRODUCTION SERVICES
Customer Service Manager Stephanie Hulett shulett@wtwhmedia.com
Customer Service
Representative Tracy Powers tpowers@wtwhmedia.com
Customer Service
Representative JoAnn Martin jmartin@wtwhmedia.com
Customer Service
Representative Renee Massey-Linston renee@wtwhmedia.com
Customer Service
Representative Trinidy Longgood tlonggood@wtwhmedia.com
IN-PERSON EVENTS
Events Manager Jen Osborne jkolasky@wtwhmedia.com @wtwh_jen
Events Manager Brittany Belko bbelko@wtwhmedia.com
Event Marketing Specialist Olivia Zemanek ozemanek@wtwhmedia.com
FINANCE
Controller Brian Korsberg bkorsberg@wtwhmedia.com
Accounts Receivable Specialist Jamila Milton jmilton@wtwhmedia.com
SALES
Ryan Ashdown 216-316-6691 rashdown@wtwhmedia.com
Jami Brownlee 224.760.1055 jbrownlee@wtwhmedia.com
Mary Ann Cooke 781.710.4659 mcooke@wtwhmedia.com
Jim Powers 312.925.7793 jpowers@wtwhmedia.com @jpowers_media
Courtney Nagle 440.523.1685 cseel@wtwhmedia.com @wtwh_CSeel
www.nfpa.com
LLC
FLUID POWER WORLD does not pass judgment on subjects of controversy nor enter into dispute with or between any individuals or organizations. FLUID POWER WORLD is also an independent forum for the expression of opinions relevant to industry issues. Letters to the editor and by-lined articles express the views of the author and not necessarily of the publisher or the publication. Every effort is made to provide accurate information; however, publisher assumes no responsibility for accuracy of submitted advertising and editorial information. Noncommissioned articles and news releases cannot be acknowledged. Unsolicited materials cannot be returned nor will this organization assume responsibility for their care.
FLUID POWER WORLD does not endorse any products, programs or services of advertisers or editorial contributors. Copyright© 2023 by WTWH Media, LLC. No part of this publication may be reproduced in any form or by any means, electronic or mechanical, or by recording, or by any information storage or retrieval system, without written permission from the publisher.
SUBSCRIPTION RATES: Free and controlled circulation to qualified subscribers. Non-qualified persons may subscribe at the following rates: U.S. and possessions: 1 year: $125; 2 years: $200; 3 years: $275; Canadian and foreign, 1 year: $195; only US funds are accepted. Single copies $15 each. Subscriptions are prepaid, and check or money orders only.
SUBSCRIBER SERVICES: To order a subscription please visit our web site at www.fluidpowerworld.com FLUID
POSTMASTER:
As a new editor of Fluid Power World, I’m granted the privilege of meeting people and attending industry events with fresh eyes. I’ve heard stories of this tight-knit fluid power community and how passionate everyone is about the industry. Though I arrive with an open mind and eagerness to learn, my expectations continue to shatter with every interaction. The camaraderie among fluid power professionals is warming, and the dedication to strengthening the industry is inspiring.
Last November, I had the pleasure of attending the NFPA’s Fall Regional Meeting in Cleveland, where managers and engineers willingly exchanged knowledge. Chris Chidzik, Principal Economist at The Association For Manufacturing Technology (AMT), also spoke about economic trends and forecasts. In general, GDP is down, but consumption is up. Job growth is up, but so are job vacancies. Inflation is still rearing its ugly head, but consumer spending is up. With all the conflicting messages we hear, the big question everyone’s been asking is: Are we in a recession? Though the data suggests yes, it certainly hasn’t felt like one. Chidzik explained that this year’s GDP contraction was most likely due to supply issues, which all fluid power manufacturers experienced first-hand.
All this aligned with what I learned at the 2022 PTDA Industry Summit, where Alan Beaulieu of ITR Economics assured that manufacturers struggling to manage backorders may feel a sense of relief as the market eases. “We’re not looking at a recession. We’re looking at opportunities, just at a decelerated rate of rise,” said Beaulieu. But he cautioned against getting too comfortable because things aren’t returning to “normal” anytime soon. Though inflation is expected to take a break, it’ll creep back up again.
Within the first few months on the job, I also interviewed various fluid power professionals to learn about their latest products and innovations. Optimizing production, refining quality, and improving customer service were common themes. These days, customers don’t care if OEMs are innovative or flashy. They just want the exact part with the exact specifications within the needed time frame at the best cost. And they want to know that the OEM will be there to help when they call.
More than ever, each OEM is part manufacturer and part customer service provider. But that doesn’t mean they’re not innovating or thinking of the future. There’s a reason why products are still flying off the shelves, even at a decelerated rate.
Aside from products and economics, I’m looking forward to attending more fluid power events and connecting with this fun, hard-working community. I’ve already learned more than expected since I started at Fluid Power World. And the most important lesson that we can all take away is this: When considering parts for any fluid power system, don’t forget the most important part — the people. FPW
Rachael Pasini Senior Editor rpasini@wtwhmedia.comEditor’s Note: The December printed version of this Troubleshooting Challenge inadvertently featured the incorrect circuit drawing. We are reprinting the same problem from last month wtih the correct image for your troubleshooting pleasure.
The circuit shown here is used to open and close the cage doors on a zoo enclosure. The staff would start the hydraulic system when they needed to open and close the gates. They then would shut it down when all the gates were closed.
After having trouble opening one of the larger cage doors, they spent time making sure there wasn’t a mechanical obstruction and that the gate wheels rotated freely. A local repair shop told them to increase the pressure on the electric motor-driven pump, but it would not go any higher. They tried increasing the setting on the relief valve and it also would not increase the pressure.
They tried to start the gas engine stand-by system but could not get that up and running, either. They also noticed the oil temperature kept climbing the longer they allowed the power unit to run.
Can you identify what was the problem? We welcome responses of all kinds directly to Robert Sheaf at rjsheaf@cfc-solar.com or to mgannon@ wtwhmedia.com. The solution will be provided next month, in conjunction with our February 2023 issue. FPW
We understand that industrial needs can come in many shapes and forms. Our diverse line of hydraulic components are designed to fit any need you may have. When it comes to reliability, no other product on the market compares to what Yuken Hydraulics has to offer!
Our commitment to quality assurance will give you the confidence that your machinery is running safely and efficiently every time. So don’t settle for anything less.
Nominations are open for the Fluid Power Hall of Fame, hosted by the International Fluid Power Society. This special award was reestablished in 2019, to acknowledge those individuals who have dedicated their careers and have made significant contributions to fluid power technology.
Nominations are being accepted until April 15. Individuals who have dedicated their careers — innovators, researchers, application engineers, educators, as well as sales and service personnel — are the reason the fluid power industry has thrived throughout the years.
Any person can nominate an individual, living or deceased, who demonstrated excellence within their 25+ year fluid power career; however, an individual is only allowed to nominate for 1) living and 1) posthumous.
To be eligible for the award, individuals must have verifiable 25+ cumulative years in the fluid power industry. Those nominated are asked to complete a 15-question application.
A panel of judges from diverse segments of the industry reviews the applications and selects the Class of Inductees. The Hall of Fame Inductees will be announced on June 19 — Fluid Power Professionals’ Day. They are recognized in person at the IFPS Annual Meeting in the Fall.
Visit www.fluidpowerhalloffame.org to nominate now. FPW
The next virtual Quarterly Technology Conference from the NFPA and Fluid Power Industrial Consortium will be held March 2, with a focus on “New Components and System Architectures that Increase Energy
Efficiency.” Sessions will include:
• High VI Industrial Lubricants and Their Impact on Equipment Efficiency
—Ricardo Gomes, Technical Service Manager, Evonik Oil Additives USA Inc.
• Using Additive Manufacturing to Redesign Fluid Power Components for Greater Efficiency — Dan Bagley, B&B Management Labs
• Increasing System Efficiency with Servo-Driven Hydraulic Gear Pumps
— Thomas Afshari, Project Phoenix
Visit nfpa.com for more details and to register.
A recent study found that more than 68% of participants cited a lack of confidence as the biggest stumbling block to a student’s ability to succeed in math. The IFPS’ new online at-your-own-pace training module takes the IFPS Math Book and brings it to life.
Dan Helgerson, CFPAI, will teach fundamental fluid power math skills and build on that foundation to explain the calculation of more complex formulas. Each section includes step-by-step video instructions on how to solve complex fluid power math problems.
Attendees can expect to learn:
1. Welcome to the Fluid Power Math Workshop
2. Understanding the Order of Operations -PEMDAS
3. Units used in IFPS Fluid Power Math Equations
4. Math Basics
5. Circles
6. Various Math Equations
7. Fluid Power Formulae
8. Calculating, Volumetric, Mechanical and Overall Efficiency
9. How to Size and Select a Fluid Power Cylinder
10. Calculating Fluid Velocity
11. Detailed Explanation and the Importance Triangles in Fluid Power
12. Understanding Reaction Forces
13. Jib Boom Calculations
14. Understanding Toggles
15. Miscellaneous Reservoir Equations
16. Understanding Compressed Air
17. Coefficient of Velocity
18. Sizing Accumulators
19. Coefficient of Friction
20. Understanding Cartridge Elements
21. Electric Formulae -Ohm’s
Cost is $199, with multiple-user pricing for 5 or more.
E-mail sales@ifps.org for details. Visit
Our new thermal/pressure bypass valve option available for the brazed aluminum MAR and BOLR Series coolers allows you to have the lowest start up pressure in cold start situations to minimize pressure spikes in your hydraulic system.
Temperature bypass is activated (closes) when oil reaches a defined set point of 110° F and allows full oil flow through the heat exchanger. When the oil is cool, the valve is open to allow a partial flow bypass. 60 PSI pressure relieve protects the system from over pressurization.
Features and Benefits
Thermal Bypass and Pressure Relief in One Valve
Optional Feature for MAR and BOLR Series
Internal Design Helps to Bring the System Out of Bypass Sooner
Pressure Relief Protects Against Flow Surges
Eliminates the Need to Install External Components Saving Time and Money
CONTACT US TODAY TO LEARN MORE!
Piab has continued to evolve its piCOBOT program by adding a larger version, the piCOBOT L. Developed for customers who work with small industrial robots and cobots, its high payload and low building height enable maximum capacity usage.
The piCOBOT family consists of two pump units and a selection of grippers. Optionally, a tool changer with a respective docking station is available. The main differences between piCOBOT and piCOBOT L lie in payload and capacity. Both piCOBOT versions are compatible with a broad range of cobots and small industrial robots. They are equipped with specific software features to enable easy system installation and operation with Universal Robots (UR) and Fanuc industrial robots.
With a lifting capability of up to 35 lb, the piCOBOT L is beneficial for applications where gripping speed, high-vacuum flow, and heavy lifts are required. It builds on the same technology platform as the original version and consists of a vacuum pump unit and an optional gripper unit. The vacuum pump unit is scalable and can be equipped with up to four COAX cartridges. The ejector capability is targeted for applications such as e-commerce, logistics, warehouse, packaging, machine tending, part assembly, palletizing/de-palletizing, bin picking, and kitting, and for lifting heavier items in production.
The piCOBOT L’s high-vacuum flow facilitates the deployment of large Kenos foam grippers that can lift a wide variety of objects, from single large and heavy objects to a multitude of small objects simultaneously. Piab’s Custom Line specialists, the customer, or the system integrator can also develop customized end-effectors. Due to the vacuum connection at the bottom of the pump, no extra cabling is required when attaching a different gripper unit.
Design engineers can choose between two COAX ejector cartridge products depending on the application. The SX42 is designed for applications requiring higher vacuum flow to compensate for
piCOBOT L has a lifting capability of up to 35 lb, making it particularly useful for e-commerce, logistics, and warehouse applications and for lifting heavier items in production.
leakage when handling porous objects, such as corrugated boxes. The other choice, SX12, is designed for handling more solid nonporous surfaces, such as metal. Both products are multistage COAX Generation 2 ejector nozzles made of a fully dustproof design where flaps and check valves are separated. With the reduced outer dimension, the ejectors combine high vacuum flow and fast response times with high vacuum levels of 27 in.-Hg.
The piCOBOT L allows manual gripper changes and tool dissembling from the pump unit. It also has an optional automatic tool changer with a docking station to speed up tool changes, ensure continuous operations, and deploy one solution for many different tasks at the lowest possible cost.
The automatic tool changer is equipped with a lever to lock or unlock the adapter plate of the end-effector. The lever can be opened and closed automatically by the docking station to remove a gripping unit from the cobot and pick up and connect a different one without human
interference. Alternatively, the gripper switch at the tool changer can also take place manually.
The piCOBOT L was developed with easy access to parts that may require cleaning. Accordingly, the ejector cartridges can be extracted in portions, and the vacuum stages can be cleaned where needed. The integration of dust protection filters further maximizes machine uptime. Due to its IP65-compliant, robust pump body, long operation times are also realized in harsh environments. FPW
Users can customize the piCOBOT L with up to four COAX SX42 ejectors for handling porous objects, such as corrugated boxes, or SX12 ejectors for handling more solid nonporous surfaces, such as metal.
Forest machine manufacturer Ponsse is launching the new HH360 rotator, which lets the harvester head freely rotate 360° without limitations. The harvester head speeds up wood processing, makes the operator’s job easier, and reduces hose failures.
The product was developed in close cooperation with hydraulic motor and rotator manufacturer Black Bruin, and Ponsse has exclusive rights to the product for forest machine use.
“The HH360 is a combination of the well-known and durable radial piston technology of Black Bruin’s harvester rotators and Ponsse’s innovation,” said Tero Ylä-Mononen, Black Bruin’s R&D manager. “Thanks to the structure, the torque-transmitting components are wear-proof, and the rotator maintains a firm grip throughout the machine’s
service life. The rotator is extremely accurate in use and responds precisely and consistently to the user’s actions.”
Due to the radial piston rotator’s high efficiency, just 20 lpm of oil flow suffices to operate. Operating costs are low, and the rotator is easy to service if needed. This means that service life can be extended far into the future.
The powerful and exceptionally energy-efficient HH360 rotator is available for multiple Ponsse harvester heads when mounted as a loose-head installation.
The most important factor in choosing a rotator product is the application’s load capacity requirements. Black Bruin’s harvester rotator design is made for heavy-duty use and is based on its radial piston motor, giving the same highly efficient power as the motors. Black Bruin harvester rotators are rotary housing, which means the rotator shaft (cylinder block) remains in place while the rotator is running.
The rotation of the motor is achieved by feeding pressurized hydraulic fluid through the rotator distribution head to the distribution valve. The distribution valve directs the flow through the cylinder block to the pistons, which are on a power stroke. The pressure pushes the pistons, and the cams roll outwards against the cam ring on the housing (distribution head). The waveform of the cam ring transforms the force into torque. When the pistons reach the end of the power stroke, the distribution valve closes the flow to the pistons and switches the pistons to a return stroke. The cam ring
pushes the pistons back into the cylinder block, preparing them for the next outward power stroke.
Harvester rotators are used for cut-to-length and full-tree wheeled and tracked harvesters, while grapple rotators are for forwarders, timber trucks, and bulk material handling. Unlike harvester rotators, the radial piston grapple rotator housing remains in place, and the shaft (cylinder block) rotates.
A rotator connects to a boom or crane tip with a link and pin kit, and brakes can be installed to dampen the harvester head or grapple swinging. In harvester rotators, links enable the use of up to four brake kits, while links in grapple rotators enable up to two brake kits. Both rotators can also be used without brakes. FPW
Ponsse’s new HH360 rotator lets the harvester head freely rotate 360° without limitations.
Sometimes, a small change can make a big difference. In this case, small means a 1 x 1 in. sticker that holds hydraulic cylinder nameplate information.
Milwaukee Cylinder’s new self-adhesive Electronic Service Tag allows customers to download nameplate information, such as the serial number and cylinder properties, and request a seal kit or duplicate cylinder quote with a smartphone. Since nearly everyone has a smartphone, nearly
everyone can read a tag — no special tag readers are required.
Each Electronic Service Tag includes an NFC chip and a printed QR code. The QR code works with a smartphone camera, while NFC uses the phone’s electronic NFC reader. With the NFC chip, even if the tag is visually not readable, a smartphone can easily read the NFC chip to access the cylinder information.
“Having the correct cylinder information is absolutely critical and is required for ordering the correct cylinder seal kits,” said Douglas Lacina, president of Milwaukee Cylinder. “In industrial
Electronic Service Tags come standard on H, MH, LH, and A cylinder families. Milwaukee Cylinder can also retrofit and provide duplicate tags for existing cylinders for a nominal fee.
applications, most people rely on the cylinder’s nameplate to identify the cylinder. Unfortunately, the nameplate may not be accessible due to the cylinder’s placement, or the nameplate may have been painted over or damaged. Either of these issues makes ordering the correct cylinder parts difficult, time consuming, and aggravating. Our Electronic Service Tag makes life a lot simpler.”
Each Electronic Service Tag comes in a bag attached to the cylinder. The customer can place the tag in the most accessible location, such as on an accessible surface of the cylinder, on a machine nameplate or control station, or in a binder or machine manual. The tag is designed to work on metal surfaces in an industrial environment and can be placed on any surface with temperatures from -31 to 194° F.
To identify the cylinder, the customer simply scans the QR code with a smartphone or taps the phone on the NFC tag and downloads the information. Then, the customer can view the information on the phone and, if desired, request a quote for a seal kit or replacement cylinder.
The Electronic Service Tag comes standard on H, MH, LH, and A cylinder families at no charge. For a nominal fee, Milwaukee Cylinder will provide retrofit tags (or duplicate tags) for existing products. In addition to the tag, the company will continue to engrave nameplate information on the cylinder. FPW
Milwaukee Cylinder
milwaukeecylinder.com/nameplatetag
Low Pressure Suction Valves
ISO 9001 Certified
Medium - High Pressure Valves
Subsea & Gas Valves
Ball Valves
Check Valves
Flow Control Valves
Needle Valves
Flanges & Adapters
Bar & Custom Manifolds
Specialty Valves
Flow Control Needle Valves
Tank Accessories
Pressure Gauges & Snubbers
SSW Power Unit Systems
Transfer Pumps
Industries Served:
• Oil & Gas
Check Valves Bar & Custom Manifolds
SAE Port Flanges
• Industrial Hydraulics
• Mining
• Forestry
• Chemical & General Processing Plants
• Medical
• Aerospace
• Factories
• Mobile Equipment
• Defense
SSW Power Unit System
• Machine Tool
• Testing Equipment
• Ocean Depth Technology
• Automotive
• Food Processing
• Agriculture
• Industrial
• Aviation
• Petrochemical
• Marine
• Subsea
Made In America
Compressed air is one of the most expensive ways to supply energy to facility tools and equipment. This is due to the inherent inefficiencies in the process of compressing air — the biggest product is heat and the secondary output is compressed air. While this is disappointing, there are still things that can be done to keep your compressed air system costs as low as possible. Here are six key suggestions to improve your facility:
1. Baseline (measure) your system — Most people have no idea how much energy their air compressors are consuming and how much compressed air they are using. The
trick to managing a compressed air system is to measure it. This measurement can tell you the costs and point out some problems such as poor compressor control or high levels of leakage.
2. Fix your leaks — Leakage waste is one of the biggest costs in a compressed air system and something that can most easily be addressed by anyone that is handy with tools. But don’t try to hunt for leaks with your naked ears. There are readily available and affordable ultrasonic leak detection instruments that you can use to give yourself super-hearing. This way, you can locate even the smallest of leaks in noisy environments. But realize, you must control your compressors optimally to gain the most out of leak repair.
3. Eliminate wasteful end uses — Because compressed air is so expensive, about 7 to 8 horsepower goes into producing one horsepower of mechanical energy at the end use. Thus, it is a good idea to look for and eliminate wasteful items that can best be supplied by some other energy source such as direct drive electrical or hydraulic power. If the compressed air demand can’t be eliminated, then see what you can due to reduce the duty cycle. Control the demand by automatically turning it off with electrical switches (or manually) when it is not required — say, during evenings or weekends.
4. Lower your pressure — Reducing the pressure at the discharge of an air compressor will reduce its power
Installing a flow meter is a great way to find out how much compressed air you are using and how you are using it; this can help you understand how to improve.
consumption per unit output by about 1% for every 2-psi reduction. A secondary benefit is that the flow of compressed air to any unregulated compressed air use reduces by about 1% for every 1 psi of lower pressure. Use this fact to save yourself some energy costs.
5. Better control your compressors — Many ways exist to control compressed air systems, some more efficient than others. Old school compressor control methods operate using a very inefficient modulating mode that can make partially loaded compressors consume two or three times the energy needed. More efficient control modes use load/unload, variable displacement, start/stop, and variable frequency drive. If you don’t know how your compressors are being controlled, ask your service provider; there may be something that can be done to save costs.
6. Educate yourself on compressed air optimization, then take action — Many more processes and items can be improved in a compressed air system besides these six actions and the best way to find out is to take some great training. Have a look at the online training that is available from Compressed Air & Gas Institute (www.cagi.org) and the Compressed Air Challenge (www. compressedairchallenge.org) and sign up. Learn the steps required to improve your system then take action! FPW
Connect with thousands of engineering design professionals online.
John, the maintenance manager of a wood products company, was very proud of his Number 3 compressor. It had been operating for years, racking up more than 200,000 run hours — and was so trouble free, it was almost scary. Of course, John kept it maintained, changing oil and filters on a regular basis, fixing any leaks, and keeping it sparkling clean by cleaning up any collected dirt and oil.
He was particularly proud of the fact that it was the coolest compressor of his four units, never overheating once, even on the hottest days. From time to time, his compressor service company would stop by and try to sell him a new, more efficient replacement but he always put them off, because his existing Number 3 was a dream ... he wanted to keep it forever.
One day, the power utility offered to do a free checkup of John’s system. The inspector placed instruments on the air compressors, measuring pressure, power, and flow. He eagerly awaited the results, predicting his system would pass the inspection with flying colors. But the power company had bad news. His dream was about to turn into a nightmare: his compressors were running poorly. In fact, on average they were consuming about 2.5 times the energy than they should, and the worst of the bunch was the Number 3 compressor!
The power company report showed that the Number 3 compressor was running with its inlet valve almost totally closed, due to a mechanical malfunction. Thus, it was consuming about 70% power, but putting out very little air. Adding to this, the other three compressors were running in “modulation mode,” the absolute least efficient way to run lubricated screw compressors: loaded on average 40% and consuming twice as much energy as they needed.
The power company estimated, based on system loading, that the Number 3 compressor didn’t need to be running at all, and had wasted more than $50,000 per year in electricity costs, more than enough to pay for a new compressor many times over. Furthermore, two more of his four compressors were running unnecessarily. Big changes in John’s control strategy were required.
To soothe John’s disappointment, the power company offered to help John improve his compressors with a fat sixfigure incentive. First on John’s list to things to do is to call the compressor salesman back for a talk! FPW
Modulation mode is the least efficient way to operate compressors. If the inlet valve is only partially open, the energy use can be extreme.
fluid power industry’s biggest event returns to the Las Vegas Convention center this March, with 375 component manufactures expected on the show floor. Exhibitors will include those focused on electrical & mechanical power transmission, industrial hydraulics, mobile hydraulics, pneumatics, and water hydraulics.
The show, originally branded as the International Fluid Power Exposition, and run by the National Fluid Power Association, was a quadrennial show for decades until it was aligned with two large mobile machinery shows in 2002: CONEXPO and CON/AGG. In the years since, IFPE has been managed by AEM and runs every three years.
The last iteration, in March 2020, happened right at the onset of the COVID-19 pandemic, and featured many last-minute cancellations, both on the exhibitor and attendee sides, making for a strange experience. Now, the fluid power industry is primed to relaunch the event and start anew.
Pre-COVID attendance for the three combined shows always exceeded 100,000 visitors, and the hope is that the international audience — which has come from 130 countries in the past — is able to return in force. Once again, an International Trade Center area is planned, to
help exhibitors and attendees connect across oceans and languages; it will feature the normal business center amenities, as well as interpretation services.
“The ITC is a really useful resource for international salespeople like me,” said Matt McCormick, Director of International Sales at Minnesota-based Cimline. “Having an area with translators on call in a quiet environment where we can offer an overseas visitor hospitality is valuable. I also find the input and presentations from the staff at the ITC to be useful.”
“In 2020, being able to present business opportunities about the Philippines at the International Lounge was a good ‘image building’ exercise for the country,” said Patrick Tan of Global-Link MP Events International, located near Manila. “There were plenty of inquiries thereafter specially on the presentation of the Philippine Construction Industry Roadmap that will be implemented over the next 30 years.”
Registration for the show opened in early August and show organizers said the largest groups of international registrations have been coming from Canada, Australia, the U.K., Mexico, and New Zealand.
“The international audience for IFPE is significant,” said John Rozum, show director for IFPE. “These are the engineers, the product planners, the executives from OEMs all over the world. The fluid power and motion control technology on display at IFPE is what makes the construction equipment you see at CONEXPO-CON/AGG work, and that doesn’t change regardless of where the product is made.”
Make sure to visit the Fluid Power World booth at the show, which will be one of the first you’ll see as you come up the escalators into the South Hall. Please stop by booth SL80022 in the lobby to see all that we will be spotlighting and to meet our editors.
Also, the popular Fluid Power Hour Networking Reception will be returning this year! The event will be held on Wednesday, March 15th from 4:00 to 6:00 p.m. on the second floor of the South Hall. The IFPE Fluid Power Hour reception will have drinks and live entertainment including showgirls, mirror ball walkers, Elvis stilt walkers, a solo guitarist, an uptown jazz duo, an electric guitarist and much more!
In addition to the exhibits, many fluid power professionals come to IFPE for the event’s wide array of educational seminars and conferences. Following is a complete rundown of the sessions, speakers, and descriptions (where available).
NOTE: Participation in educational sessions in the “Fluid Power Workshops” track requires a separate purchase and is not included in All Access Passes.
Presenter: Medhat Khalil
This presentation increases awareness of the fundamental concepts of fluid power technology. It will cover some rules of physics about fluid pressure and flow, as well as the generic structure of a hydraulic system, and construction and principal operation of the main components, e.g., pumps, motors, valves, cylinders, and rotary actuators. The course summarizes how to manage all these components in form of a system that works safely and efficiently. Topics covered will include: gauge versus absolute pressure, Pascal’s Law, laminar versus turbulent flow, basic construction of hydraulic systems, hydraulic pumps and motors overview, hydraulic valves overview, reciprocating actuators overview, hydraulic accumulators, actuators, and basic hydraulic circuits.
Presenter: Paul Michael
In this course, participants will learn about the composition of oils, the properties of lubricants and how hydraulic fluids can affect machine performance. Conventional, multigrade, synthetic and biodegradable fluids will be discussed. Research studies examining fluid efficiency effects in hydraulic motors, piston and gear pumps will be presented. The principles of oil analysis and filter selection will be outlined. The seminar concludes with case studies that demonstrate how filter debris analysis can be used to troubleshoot hydraulic system contamination control problems. Topics covered will include: hydraulic fluid base stocks and additives, multigrade and synthetic hydraulic fluids, fluid properties and hydraulic system efficiency, basics of inservice fluid analysis and filter selection, and in-service filter analysis case studies.
Contamination control and filtration
Presenter: Paul Michael
Contaminated fluids can cause damage to hydraulic equipment and reduce machine productivity. But keeping up on cleanliness requirements and understanding the options for filtration technology can be challenging. This session will discuss how to evaluate fluid cleanliness and implement strategies to ensure that hydraulic fluid starts out and stays clean.
Presenter: Lane Oltmanns
The purpose of this session is to present a simple, yet powerful, online engineering application that can calculate hydraulic system efficiencies from a pressure drop and piping system perspective. Attendees are encouraged to bring their pump output (gpm), hydraulic oil viscosity (cP) and specific gravity (g/ml) — and the presenter will run the numbers to get an idea of their piping system efficiencies and losses.
Presenter: Danny Richards
The presentation will begin with an overview of Global Data, its research capabilities, and offerings. This will be followed by a discussion of Global Data’s Economic Forecast and scenario analysis. Because Global Data’s economists judge that the outlook for growth is highly uncertain, especially in the United States and Europe, several U.S. outlook scenarios will be reviewed. It will conclude with examples of industry-specific forecasts and scenarios for the manufacturing sector in the U.S.
Presenter: Donna Pollander
The International Fluid Power Society certification tests provide an objective, third-party assessment of an individual’s technical skill level and are recognized industry-wide. The certification offerings keep pace with changing fluid power and motion control technologies. This session will review training resources and highlight updates taking place with the Society and certification.
Operator efficiency
Presenter: Jonathan Meyer
Electronic control on hydraulic equipment has been exponentially increasing over the past two decades. Previously electronic control has primarily focused on increasing the fuel efficiency while maintaining the same level of performance. As machine controllers become more powerful and new sensor technologies emerge, the focus is now switching to operator efficiency. Automation has already become part of our daily lives, with thermostats that can automatically adjust the temperature and devices that can order supplies when low. This automation is expanding into hydraulic machines by simplifying repetitive tasks, assisting when navigating crowded workspaces, and helping less experienced operators perform better and faster. This presentation will cover some of the latest technologies that are helping operators get more work done quicker and present what is coming in regard to fully automated machines.
Presenters: Eric Lanke, Jon Goreham, and Stephanie Scaccianoce Keeping the pool of fluid power professionals full is no easy task. The workforce shortage is one of the most challenging issues the industry is facing. This session will cover how critical partnerships with tech schools and engineering colleges are to educate and promote careers in the industry through hands-on laboratory experience and internship programs with major fluid power companies.
Presenter: Jon Jensen
A brief discussion of demand side targets for energy efficiency. Topics covered will include methods to improve energy intensive uses of compressed air, pressure control, leak remediation, flow monitoring, and general best practices. The focus will be on how to identify those low-cost projects and design improvements that will reduce demand for compressed air while maintaining productivity.
Wednesday, March 15th
What can you do to make your machine more efficient?
Presenter: Rance Herren
[No description was available at press time.]
An integrated electro-hydraulic unit for fluid power applications
Presenters: Andrea Vacca and Zifan Liu
This research demonstrates a novel design for an electrohydraulic unit made in collaboration between the Maha Fluid Power Research Center of Purdue University and Bosch Rexroth. In this unit, a permanent magnet (PM) electric motor with an internal gear pump are integrated in one housing, eliminating the shaft connection of traditional electric motor and hydraulic pump. When the unit is operating in pumping mode, the stator with electric windings is electrically inverted thus the rotor with permanent magnet is properly actuated and rotated at desired speed or torque). Therefore, the press-fit pump’s ring gear is driven, causing the meshing pinion gear to rotate. That provides pressurized fluid to the actuators. For cooling of the stator windings, a small portion of fluid is circulated around the stator windings, through a cartridge orifice between hydraulic pump and electric motor chambers.
In the design phase, both the hydraulic machine and electric machine have been through multi-objective optimization under typical Skid Steer Loader duty cycles. The profile of the involute gear set is optimized to achieve the Pareto front between total hydraulic efficiency and power density (W/L), with considerations on shaft/teeth endurance, hydraulic porting shape and fluid inlet velocity. The finalized ring gear outer radius is considered as a constraint in the electric machine optimization. An important design feature is compensation mechanisms to avoid leakage under high pressure operation. Radial and axial compensation mechanisms for the hydraulic unit
are designed to ensure appropriate operation with minimal leakage. A prototype of the unit has been manufactured and assembled and is currently under testing for efficiency mapping in the scope of different inlet fluid temperatures, rotation speeds, and loading pressures. It will undergo accelerated testing, evaluating its performance in conventional implement systems of common construction machineries. Another feature of this unit is modularity.
Presenter: Carl Dyke
Experiment wildly with hydraulic components and systems. Join Dyke (Industrial Mechanic & Chief Educational Officer at CD Industrial Group Inc.) for a unique fluid power educational experience and see the latest in teaching and learning technology. Carl will demonstrate the utility, effectiveness, and fun of online learning for the challenging topic of electrohydraulics using LunchBox Sessions. Every attendee will get free limited-time access. Dyke is the founder of CD Industrial Group Inc., and has made his mark as a sought-after on-site instructor, and hydraulics video presenter on YouTube.
How ecosystems are driving successful IoT deployments and delivering real ROI to the industry
Presenter: Adam Livesay
IoT 1.0 was a lot of buzz words with fancy dashboards and companies claiming to provide the complete end-toend solution to solve every problem. IoT 2.0 is comprised of ecosystems that have formed to deliver high-value solutions to the market. These ecosystems have evolved from the traditional fluid power and industrial supply chains to true IoT ecosystem partners that work together to deliver the right solution to the marketplace. We will examine use cases where industrial suppliers, OEMs, IoT providers, and customers work together to design, develop, and deliver the solution.
The industry-proven playbook for a successful IoT initiative, deployment, and ROI
Presenter: Adam Livesay
The MM-IoT playbook (Mobile Machine Industrial IoT playbook) has been used by hundreds of suppliers, distributors, and OEMs to develop an IoT strategy, manage a successful IoT project, and deliver industryleading solutions to the market that return real ROI and value to the OEM and their customers. This playbook was developed over several years by industry insiders. We will examine use cases for each phase of the playbook to allow you to leave with a framework to design, develop, and execute a successful IoT initiative.
Presenters: Austin Sowinski, Eric Lanke, and Tim Opperwall
Do you know the effect a single mA of error has on a final grade?
Traditionally, construction and agricultural machines have been designed and tuned for an expert operator. There is a closed loop relationship between operator and machine that is changing with the adoption of electrohydraulic controls, modern sensors, and computational power. Today’s job site requires a machine suited for operator augmentation and automation. This presentation walks through the challenges in enabling the controls transformation through a real-world system example and proposes how future hydraulic control architectures may look.
Presenter: Carl Dyke
New sensor technologies have allowed the machinery user, the machine purchaser, and the machinery operator to achieve higher degrees of energy efficiency, and safer, more accurate work. Sensors are devices that measure, detect, or respond to some type of input from the environment or changes to that environment over time. Sensor technologies can include ultrasound, hall effect, lasers, piezoelectric elements, a strain gauge, and magnetostrictive linear positioning to deliver data and signals that can be used in many applications for various purposes
Come to this highly visual session, featuring 2D and 3D from his company’s LunchBox Sessions website to learn about some of Dyke’s favorite sensors for hydraulics and motion control.
Presenter: Miguel Onandia
Compact mobile equipment, such as small loaders, compactors, or material handling machines, are experiencing important changes driven by increased environmental consciousness and focus on global warming. The goal is to reduce carbon dioxide emissions in every way possible, pushed in many countries by both governments and customers, so that machine manufacturers must be prepared to adapt.
To support this trend, Poclain’s teams have developed electrohydraulic transmission and data acquisition systems to optimize machine transmission. Last but not least, hydraulic wheel motors using radial piston technology, remain a keystone when it comes compact machinery’s drivetrain performance and optimization, especially for electrohydraulic machines, thanks to their superior power density and
efficiency, so they can match customer expectations for durability, cost, performance, machine autonomy, and range. This can be illustrated using application examples, such as compact wheel loader and asphalt roller.
Contamination standards prevent machine failure and boost cost savings
Presenters: Barry Verdegan, Eric Lanke, and Ivan Sheffield
Machine failures are costly. Contamination is the root cause of 80% of hydraulic failures. 90% of these failures are preventable. Standards, such as those created by ISO or national standards bodies, establish a level playing field to allow manufacturers, suppliers, and users to speak a common language and use best practices to develop and implement contamination control programs. Standards developed by ISO TC131/SC6 and other technical committees allow you to measure particulate contamination in fluids, set required cleanliness levels, choose appropriate filters for your application, compare products and identify false claims, and monitor the success of contamination control efforts. The speakers use real world examples to demonstrate the financial benefits of standard-based contamination control programs.
The value of telematics: featuring (live) use cases
Presenter: Chad Repp
Learn about telematics, specifically data logging and leveraging the data through analytics to set notifications for predictive maintenance, predetermined alerts for operator safety (collision avoidance), and how this all converts back to ROI for the OEM.
Functional safety requirements under the machinery directive 2006/42/EC
Presenter: Matthias Haynl
Functional safety standards can be a challenge to apply, particularly if they are not considered early in the life cycle. This session will discuss how to identify and apply the relevant Functional safety standards for construction/agriculture/mining machinery.
Advancing autonomy from operator assist to driverless vehicles
Presenter: Peter Bleday
In this session we will discuss the technical, social, and economic factors that are needed to advance vehicles in the construction industry from their current state to a state of high operator assistance and augmentation, and then to a state of driverless automation. This discussion will include some of the significant challenges OEMs and suppliers face with new technologies and edge case management around the vehicle and job site. During the discussion, we will also focus on how to overcome these challenges and the future of the construction autonomous vehicle industry.
Presenter: John McDonald CISSP & CRISC
Smart devices have infiltrated every aspect of our lives — and equipment, vehicle, and manufacturing environments aren’t exempt from the onslaught. Customers that used to be worried only about price and capabilities are now questioning manufacturers on the quality of the
cybersecurity in their devices, since a single hacker can take control of a vehicle and run rampant, resulting in significant vulnerability for the manufacturer. The industry has started to address these issues with standards such as IEC 62443, but many manufacturers are just starting to wonder how they can implement a cybersecurity program. This session will review the relevant cybersecurity standards in this space, the elements you need to consider when implementing a product cybersecurity program, and suggest an approach to help you get started.
Presenter: Cameron Guernsey
As the world is moving towards net zero goals, there’s a focus on electrifying all types of applications, especially mobile machinery. Danfoss acknowledges these trends and has invested in this zeroemission future through the addition of our Editron business. Our next step is to develop the eSolutions portfolio, which builds upon the existing PLUS+1 platform and applies the same machine application knowledge to now control electrified machines.
The eSolutions package is pre-developed application software that includes functional safety and interacts with our Editron hardware to provide optimal control and efficiency for the end user. The software is designed to be modular and scalable, so it can be used in most applications and span across all power ranges. Current PLUS+1 users will experience a much easier transition towards electrification, as eSolutions operates out of the same Guide & Service Tool screens currently being used. These solutions have been tested and demonstrated through our proof-of-concept machines, the first of which is our fully electric wheel loader in Nordborg, DE. Danfoss is excited to contribute to the world’s net zero goals by enabling faster development of electrified solutions and collaborating with the market to overcome the biggest obstacles still ahead.
Presenter: Dan Helgerson CFPS, CFPAI, CFPJPP, CFPAI, CFPSD
While a great deal of effort is being made to produce more efficient compressors, pumps, and motors, there has not been enough attention given to providing more efficient systems. The new Floating Cup pumps developed by INNAS DV have overall efficiencies of better than 95%, but when dumping flow across a relief valve, the system is 100% inefficient. Efficient components do not guarantee an efficient system.
An advantage of open loop fluid power systems is the ability to have a single power source supply multiple actuators, each with different flow and pressure requirements. However, there is an energy downside: the power source must be able to provide pressure to satisfy the most demanding actuator requirements. This means the power source will always be producing more power than can be used by the actuators. In its simplest form, a fixed displacement pump providing flow to a fixed displacement motor will always have a higher pressure at its outlet then what is required at the motor, even if there is no velocity control. Flow is always in the direction of lower pressure. So, to get flow from the pump to the motor, there must be some pressure differential to account for the line loss through the conductors. It is rightly accepted as the necessary cost of transferring power through a fluid.
When there is the need for velocity control of a variety of actuators operating at different pressures, the energy loss is compounded. The outlet of the pump will have to see a pressure that is greater than the highest-pressure demand of the actuators. If actuators with lower pressure requirements are exposed to this higher pressure, they will accelerate and go too fast. Some type of flow control is required to reduce the energy getting to the actuators. This presentation will explore some alternative methods of velocity and pressure control that cause fluid power motors and/or cylinders to draw only the energy needed for the work being done, regardless of the pressure at the pump outlet or the accumulator.
The presentation will include:
1. Explaining the terms Energy Unit (EU) and Power Unit (PU).
2. Analyzing the energy loss using accumulators, pressure compensated pumps, and load sensing pumps.
3. Redefine and explain flow control as power control.
4. Introduce methods of power control that transform the energy at the pump or accumulator outlet into what is required by the actuator. Including:
• Fixed Displacement Power Control (FDPC), Variable Displacement Power Control (VDPC), Pulse Frequency Modulation (PFM), Circuits diagrams using these methods, Energy comparisons, and compare the VDPC to the new electrohydraulic systems
Presenters: Jenny Tuertscher and Rob Johnson Often fluid power is overlooked when it comes to machinery safety. This presentation will provide understanding of the requirements for the control of hazardous energy using lockout, tagout, or alternative methods as they relate to fluid power. We will share the requirements from OSHA 29 CFR 1910.147 and ANSI/ASSP Z244.1 and the B11 series of standards for machinery safety.
The attendee will gain an understanding of the differences between hazardous energy, non-hazardous energy, and beneficial energy — and when alternative methods of energy control can be used. We will explain, using real-life application examples, how hazardous fluid power energy can be controlled using a variety of different methods. This will include enhancing traditional lockout procedures using trapped key interlocking to reduce the potential
for human error and applications using functional safety.
Attendees will gain an understanding of where to find more education, guidance, and support in using the ANSI B11 series of standards for machinery safety. This will be a valuable presentation for those new to or considering the profession, as well as those who have been in the industry for some time.
With construction technology around sustainability advancing in recent years, IFPE and CONEXPO-CON/AGG 2023 are set to have the biggest focus on sustainability ever. That means you’ll find sustainable technologies, products, and practices on display.
In addition to many OEMs highlighting efficient machines designed to reduce carbon emissions, there’s also a partnership with the Arbor Day Foundation. Exhibitors and attendees can contribute to the Arbor Day Foundation’s
funds, allowing the organization to further its goal of planting, nurturing, and celebrating trees around the globe. Each dollar contributed to the Arbor Day Foundation will result in one tree being planted in a forest in need.
Lastly, CONEXPO-CON/AGG has given sustainability its own educational track in its seminars, now with several sessions dedicated to the topic. Those sessions tackle subjects like reducing the carbon footprint of concrete, finding and managing electric construction equipment, asphalt and concrete recycling, carbon neutrality, and a “Sustainability 101” session for attendees just starting their journey towards sustainability. FPW
Visit
The Clean Seal System utilizes heat shrink technology to encapsulate the end of a hose or tube assembly with a Clean Seal Capsule, eliminating re-contamination that is problematic with traditional capping and plugging methods. Clean Seal Capsules leave your assemblies tightly sealed, tamper-proof, and 100% contamination free. They provide an easier, less costly, and more effective solution than traditional capping methods. You’ll never have to deal with an excessive cap and plug inventory again.
FESTIVAL GROUNDS
CENTRAL HALL
FESTIVALGROUNDS
Aggregates
Asphalt Concrete Safety
DIAMOND LOT
Business Operations
Concrete
Engines & Drivetrains
Hauling
Infrastructure Maint.
Jobsite Support
Land Clearing
Portable Power Safety Technology Solutions
Trucking
Underground
Earthmoving
NORTH HALL
Business Operations
Earthmoving
Hauling
Jobsite Support
Lifting
Land Clearing
Lifting Safety Technology Solutions
EDITOR’S NOTE: AT THE TIME OF PUBLISHING, SEVERAL EXHIBITORS WERE NOT ASSIGNED BOOTHS. THEY HAVE BEEN REMOVED FROM THE EXHIBITOR LIST FOR CLARITY.
ALSO, ALL ADVERTISERS IN THIS ISSUE ARE IN BOLD.
Technological advancement is accelerating at an exponential pace. Consider only fifty years ago how hydraulic cylinders were constructed much the same as they are today, yet how much has electronic, information and digital technology surpassed our venerable actuators? Hydraulic cylinders are simple and effective. They are so effective, in fact, one could consider them a perfect technology. What other component remains unchanged for decades yet remains superior to all other competitive technologies? Even we humans are soon to be obsoleted by artificial intelligence. Watch some recent videos on AI, and you’ll find yourself considering removing the wifi from your home.
Cylinders still contain, for the most part, the same components as always — namely, a piston, rod, barrel, head, cap, and seals. Most offer a bronze bushing to support the rod, but even those may be replaced by wear
strips if the application allows it. However, all the steel components offer little in the way of new technology — steel and chrome are the same as in 1965, with only marginal improvements to cylinder technology.
Seals, on the other hand, have provided much of the technology cylinders exploited to offer high pressure reliably. Today’s cylinders on mobile machinery with highpressure systems cresting 6,000 psi have seal technology to thank for their continued relevance. Advancements in synthetic rubbers, sophisticated fluid modelling and experience have led to manufacturers creating seal designs that provide highpressure operation for various applications. We’d like to think hydraulic technology will last well into the future, but other offerings (such as electric actuators) may displace our venerable cylinder. To help alleviate my fear of a hydraulic-less future, I asked Steve Cavera at Yates Industries for his opinion on the direction cylinders may take.
Cavera has been with Yates as National Sales Manager spanning more than fourteen years. His responsibilities include all sales operations for all of Yates’ facilities, where he oversees nationwide customers and distributors. Yates turned 50 just this year, spending those decades serving as many industries as there are using cylinders — paper/pulp, wood, plastics, automotive, government, steel/aluminum/metals, food, pharma, agriculture, oil & gas and shipbuilding. I asked Cavera what trends he sees with cylinder technology, to which he responded, “Smart sensors and the technology that they provide feedback-wise, and also quality-wise. Some (technology) emergent into electrical but
mainly in automation.”
Aside from seals, which have done much to improve hydraulic cylinders, sensory technology provides machine control systems with a method to intelligently operate what is essentially a “dumb” component. Using either discrete position sensors (proximity switches) or linear transducers (LDTs), machines know either when the cylinder is at the end of stroke or any position in between down to a fraction of an inch.
Although proximity switches installed into the head and cap of a cylinder provide just a trigger to the PLC that the cylinder has reached the end of stroke, this technology is excellent for process automation where we only need to know discrete positions. An LDT (Linear Differential Transducer) offers the machine controller precise cylinder position down to thousandths of an inch with rapid response time. Using the right valve technology to control directional flow, even huge cylinders may be positioned rapidly and precisely.
Even with the addition of technology, one might be curious if the cylinder’s days are numbered. I asked Cavera if electric actuators will ever replace hydraulic cylinders. “I don’t think so. Even if the technology one day exists, it would have to make cost-effective sense as well,” he said.
He raises a great point. Sure, linear electric actuators can be fast, and some offer high force. However, “high force” for an electric actuator is still only a fraction of what a high-pressure cylinder is capable of, and electric actuators aren’t so advanced yet to offer both high speed and high force in the same package. In fact, there may actually exist a power density limit to electric actuators. This is because electric motors (linear or otherwise) use the alignment of electromagnetic conductors to create the magnetic field to move the motor. Once all atoms of the conducting material are polarity aligned, there is no more capacity to increase the magnetic field.
Theoretically, there is no real limit to the number of oil atoms you can pack into a
hydraulic cylinder. Pressure may be increased exponentially so long as the materials containing that fluid remain intact.
However, just because there is no upper limit to pressure, does that mean we should strive to find out? Cavera disagrees. “I think more applications are trying to drive down the pressures because of the liability,” Cavera said. “Also, all components supplying the fluid to the cylinders have to be able to handle the increase in pressure. And at some point, those components also have limitations.”
Indeed, perhaps hyper-pressure applications will be few and far between in the decades to come. Even if cylinder construction remains primarily constant, manufacturing methods will surely improve. The days of a manual machinist turning rods and barrels while a colleague ports heads and caps using a heavy-duty drill pressure are no longer competitive tactics.
I asked Cavera how the manufacturing of cylinders has changed compared to fifty
years ago, and he responded, “It’s all about processes and efficiencies, really, just like any other manufacturing environment. We all want better quality, quicker, and at prices that people can afford.”
quality, We lathe and at
CNC technology ushered in a period of rapid, repeatable machining not previously possible. We can now load a piece of raw material into a lathe or mill and, minutes later, pull out a finished component looking and measuring precisely as the last part. Expect Industry 4.0 to usher in a new age of flexible manufacturing, where robots automatically select the correct raw material, CNC program, and tools to create finished components with no other input than what’s provided by the ERP software at sales order entry. FPW
The evolution of hydraulic filters from basic, pleated cellulose or paper into today’s synthetic depth media material has been slow but sure. This is because there are only so many ways to trap microscopic particles while offering little resistance to even smaller oil molecules. But engineers are continuing the advance towards high-efficiency filters capable of high dirt-holding capacity with little sacrifice in flow rate.
For ages, our filters were improved with ultra-fine media (5 microns or less), and we continue to improve the dirt-holding capacity of depth media elements. With that in mind, the advancements in filtration are not related to the filter micron rating but the ancillary technologies that improve user experience.
To help me elucidate the progression of trends in hydraulic filters, I asked MP Filtri Canada’s Stephanie Lamb to step in with her expertise on the subject. I asked her how the construction of modern filter assemblies and elements has changed from decades. “Filter housings have been continuously improved to be more compact and lower in weight, while offering equal or better performance.
“Filter elements have seen many improvements that provide lower pressure drop, increased dirt holding capacity and single pass efficiency by way of adding one or more additional layers of high-performance filtering media,” Lamb said. “Advancements in media construction specifically in microfiber elements allow for filtering to a lower micron rating resulting in cleaner oil. This has been critical as over the years hydraulic components have evolved to require a much higher performance than in the past to meet the cleanliness requirements of servo and proportional valves.”
Lamb also predicts further advancements in environmentally friendly fluid and filters. Likewise, changes in hydraulic fluid due to environmental concerns have introduced many fluids with lower conductivity. This increases the risk of electrostatic buildup and damaging
discharge within the filter. The higher the velocity of the oil moving through the filter element, the more likely this is to occur. Due to this aspect, we now see filters that dissipate these accumulated electrical charges by incorporating conductive material into their design.
The choice of fiber used to make the element’s fabric is not ignored by filter manufacturers pushing the boundaries of what’s possible in a filter. I asked Lamb about new media technology, and she added, “New proprietary media is always being developed and tested to offer the best performance versus cost. The structural design is always under continuous improvement for efficiency, for example, modifying the size of holes in the support tubes and adjusting the pleat design.”
One recent example is melt-blown fabric, a relatively new method of creating filtration media from melted polymers. The process involves the heated material extruded through a small nozzle by highvelocity gas, creating nanofibers that are wrapped onto a drum before processing like many other fabrics. This material provides your usual fine filtration (down to 3 microns) while offering high production capacity without using solvents.
Because the polymer recipes may be altered easily, some melt-blown media also offers water absorption capacity. The limitation of old, cellulose-based waterabsorbing filtration was the negative effect on pressure drop. As the water was absorbed into the filter media, it became more difficult for oil to pass, thereby increasing pressure drop. With the melt-blown media, water is absorbed with little effect on the flow rate. Moreover, old cellulose elements were terrible at removing particles, while the new melt-blown elements still enjoy the absolute filtration rating down below 5 microns.
Electrostatic discharge is a problem not often associated with hydraulics. Mineral oil has high electronegativity, which tends to readily attract and rob electrons from
Inline contamination monitor automatically measures hydraulic fluid particulate contamination, moisture and temperature. Courtesy of MP Filtri
other materials. In a nutshell, the movement of oil through the glass fibers of the filter element may create a static charge that could eventually dissipate dangerously. The result may lead to burned and damaged filters, increased oil varnish, or damage to electronic components.
Because of the increased proliferation of electronics in fluid conditioning, ensuring the simple process of oil filtration avoids potential pitfalls. Pressure transducers, temperature sensors, contamination sensors, and other sensitive equipment we use in our Industry 4.0 world must be protected from electrostatic discharge. To spend thousands on a particle counter to supplement your predictive maintenance
practices would be wasteful if you took steps to guarantee reliability.
Many high-end filter manufacturers now offer filter elements that reduce electrostatic charging. A combination of filter media and housing materials with neutral electronegativity makes sense when most top filter manufacturers also offer sophisticated electronics for fluid condition monitoring. With such a proliferation of electronics, one would hate to see the basic filter as the prime suspect in electronic failures.
Even with hydraulic machinery operating without electronic support, an electrostatic charge may still cause degradation to the oil itself. As a charge exceeds the fluid’s limit to contain electrons, a spark discharge from the oil to a grounded component creates a localized hot spot. These hot spots may burn or block filter elements but also increase the rate of fluid oxidation. Severe cases lead to varnish or sludge, possibly damaging other system components.
Modern environmentally friendly
hydraulic oils eschew conductive additives such as zinc, preventing the fluid itself from carrying away any charge. Unfortunately, ash-free oils also conduct electricity poorly, and the same static charge may occur.
The major filter manufacturers offer elements that do not encourage static buildup in oil. Made from materials that offer little or no charge potential, you no longer must worry about the destructive potential of electrostatic discharge. Electronics, oil, and filters themselves no longer risk spark damage. Such protection from potentially harmful electrons is necessary for the effort going into Industry 4.0 to be smooth. Lamb had plenty to offer because MP Filtri is a leader in filter-related electronics, adding, “Customers are recognizing that real-time contamination monitoring allows for proactive maintenance.
“For example, as a complement to hydraulic filtration in a system, MP Filtri offers contamination monitoring equipment which measures contamination, temperature and relative humidity in real time and
communicates real time data in a variety of communication protocols such as CANBUS and MODBUS, which can be easily adapted into both industrial and mobile equipment.
“Filter indicators, which used to be simple on-off differential pressure switches to advise when an element was at the end of life, are now being designed as transducers, and some are incorporating IoT technology. Customers can see the gradual increase in pressure drop across the filter and monitor on a PLC or even on an app to closely monitor the filter element as it progresses from clean to completely full. Filters in remote locations can be monitored and maintained easily.”
Although appearing simple at first glance, it’s clear that more goes into the design and manufacture of hydraulic filters than first meets the eye. Being such a critical element (pun intended) in any hydraulic system, filter assemblies will continue their path towards higher flow, and finer filtration while offering technology users need to stay relevant. FPW
Hydraulic fittings and couplings are often overlooked in mobile machinery design, yet they play a critical role in any fluid power system. In extremely high-pressure hydraulic applications, a leak or accidental disconnection can cause serious personal injury or damage to machinery. Therefore, machine builders must select fittings of the correct size, material, pressure and temperature rating, and application to ensure safety, functionality, and cost optimization.
Hydraulic hose safety can be ensured by using quick-connect fittings or quick couplings that make a repeated connection and disconnection between fluid lines and the equipment they are attached to. One of the most common designs is the flat face, which is available
as push-to-connect, threaded, or screw-in. Flat face couplings eliminate cavities where fluid or air can rest, thus removing the chance for trapped pressure and leakage. These couplings provide high flow and low pressure drop, and their sleeve-locking feature reduces the chance of accidental connection, removing leakage and spillage risks.
As mobile machinery requirements evolve, manufacturers are expanding their range of flat face couplings to meet demand. For example, Stauff recently released the new QRC-FG series of threaded flatface couplings that can be coupled under residual pressure on both sides. While the predecessor series could only be coupled on the plug side at up to 250 bar, the new series has a second valve so that the sleeve can now be easily coupled by hand under residual pressure. With these couplings, the flow rate is higher, and the coupling forces are lower.
Though flat face couplings are mainly used in large
Flat face hydraulic quick-release couplings make coupling and uncoupling hydraulic lines uncomplicated and safer for the user.
Courtesy of Stauffdemolition excavators, Stauff makes a case for use in other heavy-duty construction and agricultural machinery — basically any equipment exposed to high contamination levels. Solids and air cause hydraulic oil to age more quickly and be replaced more frequently, while humidity condenses and corrodes oil consistency. Dirt particles also promote abrasion on system components. As such, flat face screw couplings minimize drip quantities and prevent the entry of dirt particles and air into the hydraulic system.
In addition to safety concerns, electrification continues to influence mobile machinery with an emphasis on electrohydraulic hybrid systems. However, hydraulic fitting manufacturers aren’t feeling the impact of electrification nearly as much as other component manufacturers.
From the fitting manufacturer position and their markets served, electrification has been used as a primary mover to drive hydraulic systems — think electric forklifts, scissor lifts, and material handling equipment. Those machines, in simplest form, use a battery or electric source to power an electric motor that drives the pumps and other system components. Moving away from fossil fuels and electrification of other vehicles, such as heavy haul semi-trucks, has changed little for many fittings companies, as customers continue to use traditional hydraulic adapters. However, this has opened some new doors for traditional hydraulics.
Aside from design, some hydraulic fitting and coupling
manufacturers are expanding their product offerings due to acquisitions and companies exiting the market. For example, Dayco North America is leaving the hydraulics category, and Kurt Hydraulics will take over the manufacture and supply directly to all Dayco distributors.
“As a long-time partner to Dayco’s hydraulic coupling business, our hose and couplings are interchangeable with Dayco’s product line and have a part match in the Kurt catalog and website,” said Scott Czupryna, national sales manager for Kurt Hydraulics. “Kurt Hydraulics has been manufacturing hydraulic fittings for Dayco for over 20 years, and has its own distribution network, so the transition is a natural one for us.”
Kurt Hydraulics is in the process of creating individual accounts for Dayco customers and providing notice to those customers. Additionally, Kurt is setting up a warehouse in Canada to better serve Canadian distributors. FPW
Ergonomics, safety, efficiency, and refined quality are key themes for hydraulic hose applications these days. Machine builders are looking for hoses that improve service life and fit their exact specifications. Therefore, manufacturers are designing more durable and flexible hose solutions for heavy-duty mobile machines and evolving electrohydraulic systems.
“A hose’s working pressure, flexibility, and lifetime are key selection criteria for original equipment manufacturers,” said Scott Bauman, product manager, rubber hydraulic hose and fittings, Danfoss Power Solutions.
Last year, Danfoss introduced a new two-wire braided hose that aims to extend service life and reduce maintenance time, costs, and waste. With higher pressure capabilities, the braided design can replace heavy, rigid four-wire spiral hose in certain applications, providing up to 30% direct cost savings. Braided hose is much more flexible than spiral hose, which may enable OEMs to reroute and reduce hose assembly lengths, contributing to further cost savings. Braided hose is also lighter in weight than spiral hose, which reduces the overall weight of the machine, improving fuel efficiency.
Jeff Berger, product sales manager, alternative fuels, Parker Hannifin Corp., noted that cleaner more sustainable energy solutions for off-road vehicles are gaining momentum versus traditional diesel-burning internal combustion engines (ICE). Two solutions under development are the battery electric vehicle (BEV) and hydrogen, either as a cleaner burning ICE or used in conjunction with a fuel cell electric vehicle (FCEV).
“When it comes to battery electric, the biggest changes we’re seeing are on the thermal management systems needed to regulate the temperature of the onboard batteries,” said Berger. “To increase the efficiency of the electric motors, inverters, and battery systems, the components are
cooled with media choices such as water/ glycol coolant solutions or direct refrigerant.”
Also, as the power source of equipment evolves from an ICE to battery technology, electrohydraulic systems are trending over straight electrical solutions due to the power density required to operate the equipment efficiently.
“An advantage of using a variable speed electric motor over a traditional ICE is that we expect the hose life to be extended with this technology,” said Mark Schoessler, VP of sales and marketing for Parker’s motion systems group. “You are able to slow the ramp rate of the pressure curve created when the pump turns on by slowing the ramp rate on the electric motors to minimize the pressure shock placed on the hose and connections. Though we are not yet seeing a wide adoption to changes to the linear work functions of equipment’s hydraulic circuits or requirements, we are heavily investing in our future with our engineering teams preparing for an increased demand of electromechanical actuators (EMA).”
Mitch Eichler, sales manager for Parker’s fluid connectors group, also noted that customers value hoses that are easy to route and install, withstand a demanding service life, and fit into more compact spaces on smaller and more efficient equipment.
“In response to these customer needs, Parker has continued to invest in our Compact Spiral technology which produces hoses with smaller ODs, reduced bend radii and force to flex, and reduced weight,” said Eichler. “These advantages support an evolving workforce and align with environmental, social, and governance (ESG) focuses towards reduction in material and weight, as well as a reduction in energy demands. The latest in this development is the 777 series hose, released in 2022, rated for 4,000 psi in accordance with ISO 18752.” Parker is also releasing a new solution for impact resistance in hydraulic and industrial hoses in IFPE booth S80229. FPW
Tank mounted return filter. Working pressure up to 116 PSI, flow rates up to 236 GPM.
In-line high pressure filter. Working pressure up to 6090 PSI bar, flow rates up to 79 GPM.
Filling caps and air breathers with 10 µm filter element. Flow rate up to 422 GPM. Replaceable filter element.
Visual oil level indicators available with 3”, 5” and 10” mounting sizes, to monitor the level of oil in the tank.
www.mpfiltriusa.com
(215) 529-1300
sales@mpfiltriusa.com
Sustainability continues to trend across the fluid power industry, as design engineers must develop more efficient products to meet the industry’s sustainability needs. Hydraulic seals, though relatively small in design, play a huge role in waste, emissions, efficiency, and overall environmental impact.
At IFPE, companies such as Hallite will introduce new products that demonstrate sustainable manufacturing by using nonpolluting processes, conserving energy and natural resources, and creating economically sound and safe products for employees, communities, and consumers. Innovations in hydraulic sealing product testing are also a major focus for Hallite at the show. The company will have dedicated space in its booth to demonstrate and discuss the value and impact of product testing.
The fluid power industry is also experiencing an uptake in custom sealing solutions to meet new and evolving design requirements.
“Customized seals, or at a minimum, ‘modified’ standard products, will see an increase in demand as manufacturers continue to innovate and increase application requirements,” said Michael Cook, global segment director, off-highway and marketing Americas segment manager, fluid power, Trelleborg Sealing Solutions.
Cook expects market demand to grow
for solutions differentiating performance, such as low friction, greater energy efficiency, and energy density (higher load in less space). It is critical for hydraulic seals to maintain existing performance expectations, as automation allows construction and agriculture equipment to operate for longer periods of time with potentially higher speeds, increased pressures, and wider operating temperatures. With renewable energy equipment, such as wind turbines, increased speeds and heat generation require further optimized sealing approaches to ensure consistent operation between maintenance cycles. Additionally, functional integration, higher speeds, and greater accuracy will drive advances in solutions.
However, exactly how sealing approaches will change with mobile electrification, efficiency, and other key trends is uncertain.
“Replacing an internal combustion engine with an electric motor/drive system will certainly change sealing requirements and likely reduce the number of hydraulic seals needed,” said Cook. “For linear applications, given the power density requirements in many mobile applications, we are likely to see more of an integration of electric technology with existing hydraulic infrastructure. In this case, we would expect to see the sealing approach stay mostly consistent. In smaller equipment that can be fully electrified, the linear sealing opportunities will likely be reduced as electromechanical actuators operate much differently than hydraulic cylinders. Also, electrified solutions will require protection against harsh environments.”
Cook also noted that material development will be critical to ensure materials compatible with new fuel sources,
such as hydrogen, are available. Seals that promote system efficiency, limit leakage, and facilitate extended equipment uptime and life will be essential to manage overall environmental impact. In the long term, seal materials will likely be reviewed to see where environmentally friendly or recyclable variations can be developed and production waste can be limited or repurposed.
Over the past couple of years, supply chain issues have forced design engineers to deepen their knowledge of materials and how components interact. Exploring alternative seal solutions to keep production and systems running without compromising quality and operation has become an ongoing task.
Since no one knows what to expect from supply chains moving forward, it’s best to be prepared and “think outside the traditional supply box,” as Corey Holloway, sales manager for anyseals North America, stated. Halloway recommends investigating compatible and better-performing alternatives made with different compounds. For example, it’s possible that certain seal properties aren’t necessary for a particular application and can therefore be substituted with more readily available sealing products.
Holloway also noted that since inventory management is critical for maintaining production during supply chain fluctuations, many customers are turning toward suppliers with virtual warehousing in case they need to make a product switch quickly. FPW
At IFPE, Hallite will exhibit several popular legacy products, including the 605 rod seal, shown here.
Trends in fluid power are less like consumer trends and more like glacial movement patterns. If we look back fifty years, hydraulic motors have changed less since the 70s than once fashionable bell bottoms. And although the electronic phone book appeared twenty years ago, it quickly died when cellular phones gained popularity, yet the radial piston motor is going nowhere soon. That being said, trends aren’t part of the everyday life of your average hydraulic component. Hydraulic hybrids may have had more hype than lasting proliferation in mobile machinery, but that’s probably the closest to a “trend” as you’ll see come and go in fluid power. A hydraulic trend acts more like an evolution, where venerable technologies adopt modern manufacturing or design concepts to improve user experience.
Two design trends common to hydraulic components that help keep the technology relevant in our green and connected world are common to most hydraulic systems — efficiency and IoT. First, in a world where we try to do more with less, it’s paramount that we waste little energy on the path towards achieving work in the factory, in the mine, and everywhere in between. This means our actuator’s output should closely match the energy
in the electrons or fuel input from our prime mover.
Of course, I’m not the last word on everything hydraulic, so I petitioned Danfoss Power Solutions’ Ismir Pekmic, their senior portfolio manager for hydrostatics. He agrees that efficiency wasn’t always top of mind, adding, “in the ‘70s, efficiency wasn’t a big concern. Now we drive towards more efficient motors and systems. The market has evolved towards the need [for efficiency]. “
The trend to move away from inefficient motor designs will continue as we reduce our carbon footprint and respect the limitations of fossil fuels to power our future. For mobile machinery, it could be some time before an all-electric future eschews diesel because remote work sights don’t have charging stations. But it will be essential to use as little fuel as possible.
Pekmic uses a great example of just how far we’ve come, “In the late 70s, the farm crisis and the number of combines that were manufactured reduced drastically due to efficiency improvements, and less need for a greater number of machines.”
You might be surprised at just how much we’ve advanced with efficiency and productivity.
Pekmic continued, “[The] world population is growing – but the number of machines is decreasing to serve almost two times the population since the late 70s to now.” In reality, many of the lowefficiency offenders were motors.
The offender taking the crown for least efficient is the gerotor motor. Also known as a low-speed high-torque motor,
even their name is misleading. Instead, they should be called low-speed some-torque motors because a good portion of the energy entering these beasts is wasted as pure heat, while some torque is created. Although it’s possible to run these motors within a narrow window of improved efficiency, that window exists over a limited pressure and flow range, so don’t expect much when your motor varies highly in speed and force output.
Although some versions of the low-speed high-torque offer improved efficiency, you’re still lucky to find them operating above 80% of input power. If you put 3,000 psi and 10 gpm into these motors, you may see only 8 gpm creating useful work, while the remainder is wasted as heat.
to the work ports of these motors just results in more waste flow as oil molecules work their way past clearances and gaps with more vigor.
We may blame the efficiency deficiency of LSHT motors on the size and quantity of internal clearances and gaps. Spool valves, plates and housings are rotating and sliding, each with a gap offering a path to leakage. Although compact and inexpensive, their days may be numbered.
To be fair, the gear motor provides little more advantage in the way of efficiency. Although much more straightforward in construction, they are also prone to high internal leakage. As discussed, any fluid lost before creating useful work is lost as heat, and you can expect only
80% efficiency from this design. Furthermore, although their efficiency is more stable over a wide range of pressures and flows, they are susceptible to contamination-induced wear, reducing efficiency over time.
The trend is toward more efficient motor designs, which, when broken down, leave pretty much only piston motors. Although vane motors are definitely a thing, they’re only marginally more efficient than gear motors and present you with a higher price of entry yet with reduced power density. The rising star in the motor world is the bent-axis piston design, which is robust, efficient and economical relative to their swashplate and radial piston motor kin.
The bent-axis piston motor (figure 1) has a unique, fixed-angle cylinder block relative to the input shaft. This design inherently allows both high pressure and high speed while taking up minimal real estate. Pekmic concurred. “The 70s were a shift in technology axial to bent-axis design, from 3:1 to 5:1 ratios or more,” he said. “Power density is continuing to increase.” The stroke ratio is the difference between the motor’s maximum and minimum piston displacement, with higher ratios offering both superior torque and speed. More torque and speed from the same package means more power density, and the bentaxis piston motor is king. Pekmic pointed out that Danfoss’ H1B model is the highest performing, most efficient motor capable of greater than 450 bar and offers zero-degree capability.
In any event, motors for advanced machinery must offer more than efficiency to be competitive. Half of what grants our old technology relevancy is
the adoption of post-modern electronics. The days of hydraulic joysticks are behind us, not only because they’re expensive but as Pekmic points out, “Control architectures have fundamentally changed with market and customer needs. [We have] more advanced controls, systems and software to regulate motor performance.”
Customers have high standards and expect more from their products, so we must also encourage the adoption of any and all technology so we may remain relevant. Pekmic said we must offer “technologies intrinsic to the motor: speed sensing, temperature sensing, condition monitoring the health of the motor.” The adoption must not only be electronic, but part of the manufacturing of the motor to improve performance and reliability. Pekmic added, “Tribology knowledge – surface finishes, coatings, material selection etc., is applicable to really any moving parts.”
We must allow the modern motor to integrate well with machinery applying Industry 4.0 practices, or the customer will look elsewhere at some other technology. I asked Pekmic where he thinks we’ll take motor technology in the coming decade, to which he responded, “Automation and robotics in our operations: bearing positioning etc., like [the] automotive approach [to manufacturing].”
Also, “Smart motors, [with] processing power on the motors themselves. Electrohydraulic motors into the future [will entail] hybridization of technology between electrics and hydraulics.”
Such hybrid technology exists, such as with electrohydraulic linear actuators
that use a self-contained power unit and cylinder combination. Using a compact, electric power unit attached to (or integrated with) the motor housing provides the power and flexibility to run the machine electrically while offering the actuator power of hydraulics. Electrohydraulic hybrid actuators installed on electrically motivated machinery will eventually replace the centralized hydraulic systems common to current mobile machinery.
How we use hydraulics has changed in the past five decades, but so too has how many manufacture them. Just as we strive to integrate Industry 4.0 into the customer experience, we also take advantage of IIoT, data and other next-generation technologies to help improve quality and productivity.
Pekmic clearly knows his subject matter and has plenty of input on how motors are manufactured. When I asked what has changed in how hydraulic motors are manufactured compared to fifty years ago, he provided a list of technologies and systems, “[We use] bar codes on parts to scan correct parts that are needed to minimize errors. We have technology today to specify and ensure quality specifications are met (such as bolt torques by material number that was produced), [offering] traceability.
“Technology into the design itself – speed sensors/controls we
single or back-to-back pump configurations.
motor is available in 41 and 49 cc displacements and has a builtin speed sensor port, making it easy to add a sensor to measure speed and direction.
are using, for example. Motors are digitally and electronically enabled (one portion of a system/design versus a single piece of hardware,” he said. Data is a hot topic, and Pekmic mentioned that Danfoss is all in. “Measure/test/retain data is much more sophisticated today and easier to manage, assess and iterate/adjust.”
With advanced manufacturing practices and intelligent computer design, hydraulic motors perform better with fewer manufacturing resources. Pekmic added, “[We] put less metal into the motor [yet] maintain durability/ reliability/ESG focus.”
If you’ve been on social media recently, you’ll see how quickly artificial intelligence has permeated the art and design kingdom. Expect AI to improve everything from design, manufacture and assembly. For example, with advanced 3D print technology, you can expect a trickle-down to hydraulics components that will be higher power, lower weight and use fewer resources to manufacture. FPW
There’snothing quite like the high-pitched racket emitting from a hydraulic power unit. The combination of noises originates primarily at the hydraulic pump, but secondary harmonics and reverberations contribute to a cacophony, unlike any other machine noise. The telltale hydraulic whine is the bane of machine operators forced to mentally block the press/shear/extruder noise, raising their neck hair.
The hydraulic power unit noise problem isn’t lost on engineers and designers. As a result, manufacturers have designed components to be inherently smoother and quieter. Hydraulic designers may also select components less likely to contribute to the raucous sound. At the same time, technicians have options to ensure that as little of the vibrations as possible translate into annoying and potentially hazardous noise.
Much of the attention applied to noise and vibration reduction is rightfully aimed squarely at the hydraulic pump. Most hydraulic pumps transform incoming mechanical energy into hydraulic energy discretely. Rather than feed a continuous stream of hydraulic fluid into the circuit, a pump sends individual packets of pressurized fluid to the outlet. Each discrete bundle of compressed hydraulic fluid blasts forth into the pressure line with a tiny wave of pressure.
No pump perfectly transmits pressure without bumps, corners, or turbulence, and each impedance encourages vibration and noise. More often than not, lens plates, gears, vanes, ports, and pistons all contain sharp edges, abrupt turns, or choked flow paths. The movement of fluid through a pump is far from laminar. Even if every metal pump component were chamfered, bevelled and honed, the resulting reduction
Learn how to reduce the damaging side effects of noise and vibration caused by hydraulic power units in industrial settings.
in noise generation would likely be offset by the same reduction in efficiency.
From a design and installation perspective, the manufacturer holds responsibility for effort and ingenuity that must result in quieting solutions. In addition, a manufacturer must balance the varied demand asked of their pumps, which requires efficient operation across various pressure and flow outputs. A pump may be designed to limit pressure pulsations at 1,800 rpm and 3,000 psi but could do so poorly when run at 3,450 rpm and 1,000 psi, for example.
The pump pulsation is the primary NVH (Noise, Vibration & Harshness) driver. Each of those hydraulic energy bundles discharged from a pumping element (like a piston) or chamber (like vanes and gears) emits a pulse, and the frequency of those pulses dictates the timbre of the hydraulic noise. The frequency is a product of the prime mover rpm and the number of elements or chambers. A 9-piston pump running at 1,750 rpm results in 1,5750 pressure signals per minute. In acoustic terms, the pump’s fundamental frequency is 262.5 Hz (15,750 divided by 60 seconds in a minute) while also emitting high amplitude harmonics at 525 and 787.5 Hz.
By the same token, a pump may produce harmonics anywhere within the audible spectrum between 20 Hz and 20,000 Hz (or 11,500 Hz as tested for this author’s “old man ears” *see sidebar). Of course, we all know these harmonics combine to make annoying
sounds, especially the harmonics falling between 1,000 & 5,000 Hz, where people’s hearing is most sensitive.
Moreover, it’s essential to understand the rest of the hydraulic power unit’s contribution to amplifying noise. The prime mover and pump contribute most of the fundamental frequencies, but anything and everything attached to the power unit transmits and emits vibration and sound. An acoustic engineer could spend many times the cost of the power unit calculating and estimating how loud the power unit might be and at what frequencies. But sometimes, the particular sound and harmonics are unpredictable.
Let’s take the reservoir, for example. Its combination of welded plates, cut-outs, holes, and accessories sometimes augment the fundamental and harmonic frequencies emitted by the pump. Every physical body has a natural harmonic frequency, and sometimes those harmonics can overlap. When sound frequencies overlap with peaks atop peaks (Figure 1), the sound pressure level increases. Depending on the mass, size, shape, and elasticity of the object adding the resonance, the increase could range from barely audible to ear-splitting. When the dice fall against your favor, the reservoir may literally ring with resonance.
As much as possible should be done to isolate the pump from any possible harmonic
I’ve had my ears tested, and it appears that years of loud music in living rooms, cars and headphones have damaged my ears and lobbed off an entire octave of sound above 11,500 Hz. One of my hobbies is music production, so I’m slightly disadvantaged when mixing and mastering. However, there is one unexpected advantage to these old man ears – taking advantage of young ears. Tone generators downloaded on my phone make for a great prank to walk around blaring 15,000 Hz of piercing noise unheard by myself. It quickly clears the living room of teenagers lazing about on their electronics.
contributor. The most obvious point of shared vibration is where the pump/motor attaches to the reservoir. Two traditional methods are common — vertical (in-tank) and horizontal (tank top). The L-Shape and elevated tank make great choices, but the prior two choices far outnumber the latter.
With vertical motor power units, the pump resides below the oil level through a large hole in the top surface where the bell housing attaches using (typically) four bolts in its flange. Any vibration in the pump or motor transmits directly to that top plate and any other metal welded, clamped, or bolted to the tank. The horizontally mounted pump uses a C-Face motor that directly couples the pump using a similar bell housing. However, these units employ foot mounting via the motor, but the opportunity still exists for the pump’s vibrations to transmit through the bell housing and motor to the tank top surface as well.
Figure 1. A look at different types of noise wave interference. When sound frequencies overlap with peaks atop peaks, the sound pressure level increases. Depending on the mass, size, shape and elasticity of the object adding the resonance, the increase could range from barely audible to ear-splitting.
If you’ve designed or fabricated a hydraulic power unit, you know we don’t just weld or bolt the pump/motor group together and hope for the best. The damping of sound and vibration starts at the connection between the pump and motor. The drive couplers transfer the power from the motor to the pump and use a rubber insert tightly sandwiched between the couplers to reduce the vibration transfer from one to the other. The couplers and insert also help with shaft misalignment.
Any time you introduce elasticity to an interface, you reduce the natural frequency of the assembly. Elastomers (or actual springs) should be chosen with a natural frequency at least half that of the pump’s rotational frequency. For example, your 1,800 rpm motor’s 30 Hz frequency would best due with isolators offering 10 Hz or less. This theory applies not only to the coupler insert but the anti-vibration mounting feet (Figure 2) used to attach a horizontal pump/motor to the reservoir.
The individual mounting feet seen in Figure 2 are less prevalent in applications where the motor fully supports the pump via the bell housing. However, when foot-mounted pumps sit directly on the reservoir top and the motor is asked only to support its own weight, these act as a vibration buffer. For bell housing-mounted pumps, the solution is two-fold. First, rubber gaskets mounted between the motor C-Face and the bell housing provide a barrier for vibration and sound (and also work well in vertical pump power units).
The motor is best mounted using vibrationdamping bars as an additional isolation layer. Consisting of a thick rubber pad
sandwiched between two steel bars, the damping bars allow the technician to bolt the pump to the top bar while welding the bottom directly to the tank.
Of course, other components transmit sound and vibration besides the pump/motor group. You’d be surprised at how much sound energy transmits through plumbing, such as tubes and hoses. The steel of the tube or hose reinforcement vibrates readily in tune with specific harmonics, although the effect is mitigated by long lengths of plumbing, which have a lower natural frequency.
However, with long plumbing runs, using only tube or hose for the entire length
makes for an efficient radiator of sound energy, especially when harmonics overlap with its fundamental frequency. The ideal configuration for sound damping through conduits is to run the longest part of the plumbing with a tube and then each end terminating with short hose assemblies. The tube sandwich technique not only reduces cyclical radial expansion over a long hose but also isolates the tube from direct machine vibrations.
Sound emits not only from vibrating components but also through the hydraulic fluid itself. In fact, liquids transmit sound energy more efficiently than does air, so anywhere a conduit filled with oil goes, so too does pump noise. The creative use of pressure line accessories
helps to dampen and absorb noise as it leaves the pump. Hydropneumatic accumulators charged to around 1/3 operating pressure and teed into the pressure line provide a damper to absorb pressure waves, thereby reducing noise energy.
Noise may come from unexpected sources, as well. One application took our team days to discover and remedy the solution. It was a standard hydraulic power unit with a vertical pump motor mount attached to an 80-gal reservoir. Mounted atop was a kidney loop circuit for filtration and cooling, which included a liquid-to-air cooler. We narrowed the noise down to the cooler, which was constructed using bent sheet metal to shroud the heat exchanger. Our choice of pump,
along with steel tubing, created a harmonic resonance of the sheet metal.
Our fix was ad hoc, and through elimination, we changed to a different pump displacement, replaced the tube with hose, and then added two 90° elbows in series at the cooler inlet port. What previously gave the office workers headaches from the piercing noise morphed into your standard hydraulic whine. Even when all noise-reduction measures are heeded, sometimes the stars align to make a cacophony unintentionally with no way to predict the result. FPW
Mobileand stationary hydraulic systems have gone through major changes in recent years.
Widespread efforts toward higher efficiency and cost savings have spurred dramatic technological evolutions, and such developments have implications in every area of modern machinery.
Hydraulic fluids are one of those areas. Several increasingly common design choices have created increasingly severe operating conditions. Today’s fluids must contend with hotter temperatures and must provide high levels of performance in smaller volumes.
Traditional formulations may not be up to such tasks without contributing to costly downtime and abbreviated equipment life spans. Thoughtful fluid selection — taking into account new chemistries and polymers that provide high levels of performance —
can in fact reduce total cost of ownership for hydraulic equipment owners and operators. This article will explore why that is and what hydraulics professionals should consider into the future.
Hydraulic machinery OEMs have two driving imperatives when designing new equipment: cost control and higher efficiency. Often, those imperatives intersect in ways that can create new challenges for hydraulic fluids.
For example: Many new hydraulic machines are smaller and lighter than they have ever been. Certain components are downsized to reduce the total cost of materials required to manufacture the machine. Meanwhile, a smaller, lighter machine that can do the same work as a bigger, heavier machine is fundamentally more efficient, requiring less fuel to perform the same function.
One component that has been a primary target of downsizing is
Today’s hydraulic fluids are forced to operate in hotter environments. But the right formulation can help reliably moderate temperatures, creating significant operational benefits for end users.
Courtesy of Adobe Stock
the hydraulic fluid sump. And while this has been an effective weight-reducing strategy — oil sumps are traditionally a large and heavy component on such equipment — it also means that a smaller volume of hydraulic fluid is used in the machine. Less fluid being asked to provide the expected functionality creates more severe operating conditions. Fluids become hotter, and because there is less time for those fluids to cool between circulation routes throughout the machine, they stay hotter for longer periods of time.
This excessive heat can cause several issues for the hydraulic fluid, which not only protects equipment but provides the machine’s essential functionality. Some of the impacts include:
• Viscosity loss. The hotter conventional hydraulic fluids become, the greater their potential to lose viscosity. And as protective film layers become thinner and thinner due to this phenomenon, the fluid’s protective capabilities can become compromised.
• Premature oxidation. Sustained hotter temperatures can also cause the fluids to oxidize more quickly. This further reduces their protective and performance capabilities, which has the potential to damage parts.
And beyond the impact on the fluid’s capabilities, higher levels of heat in any part of a piece of hydraulic equipment will essentially cause the equipment to age more quickly. Given these circumstances, a hydraulic fluid’s ability to mitigate heat increases inherent to new designs can be of major benefit to operators of modern hydraulic equipment.
A reliable method for overcoming the challenges associated with more severe operational conditions is to select a hydraulic fluid formulation that includes performance polymer technology.
Performance polymers can enhance a wide range of performance attributes in many different fluids and oils that help modern equipment reach its full potential.
For example, Lubrizol has recently identified and thoroughly tested an energy-efficient ethylenepropylene copolymer (OCP), which has demonstrated significant improvements in viscosity retention and shear stability while helping to reduce operating temperatures. Our teams compared an ISO 46 formulation including OCP against a standard multigrade fluid containing polyalkyl methacrylate (PMA) additive and a conventional ISO 46 monograde baseline. Testing was performed in benchtop viscosity and tribology equipment, total hydraulic system test rigs, and in real-world mobile and stationary hydraulic equipment.
Our results were significant. In laboratory pump testing that evaluated the OCP fluid against the PMA fluid, thermal imagery cameras captured a difference in surface temperature of ~3 °C, suggesting significantly cooler operation within the pump using the OCP fluid. In a full-scale mobile hydraulic field trial, similar results were recorded. Hydraulic sump temperatures were reduced by an average of 4 °C over eight months of operation when using the OCP fluid, with even greater reductions in peak temperature spikes observed. The molecular structure of the performance polymer in the energy-efficient hydraulic fluid generates less heat-inducing fluid friction, or traction, throughout the hydraulic system resulting in cooler operation and, ultimately, longer fluid and equipment lifetimes.
This reduction in friction also allows the machine to perform its intended tasks more efficiently. In controlled experiments on-site and in climatecontrolled laboratory settings, our teams evaluated many different modes of off-highway hydraulic equipment. Compared to a conventional ISO 46 monograde, formulations including OCP demonstrated efficiency gains ranging
average sump temperatures by time of day ( synchronous operation )
from 1.4%-8.5% in a variety of applications, including laden lifts, front unladen lifts, backhoe loaders, wheel loaders, injection molding equipment, and more.
The ability of a high-performance hydraulic fluid to significantly decrease operating temperatures throughout the sump and hydraulic lines in critical equipment can translate to significant operational and maintenance benefits for end users.
More moderate temperatures over a sustained period of operation help mitigate the concerns around heat-related viscosity loss and premature oxidation as outlined earlier in this article. With these problems taken care of, a high-performance fluid will maintain its protective and performance properties over longer periods of time, helping to protect the equipment.
This durability and temperature reduction performance contribute to an extended oil drain interval, meaning that required fluid changeouts can be extended, thereby reducing the Operator’s Total Cost of Ownership. For end users, the potential here is significant. Fluid changeouts are one of the most time-consuming parts of regularly scheduled maintenance for many forms of hydraulic equipment, which in some instances requires flushing lines that may extend throughout the entire piece of equipment.
Consider a mobile excavator: Old fluid must be evacuated from lines that extend from the cab throughout the arm and the boom, and doing so can be a labor intensive process.
And taking any equipment out of service for any period of time in critical environments — commercial mining equipment, for example — can result in massive losses in productivity and profitability. In contrast, a higher-performing hydraulic fluid can help such equipment remain productive in the field for a significantly longer period of time on an annual basis.
Meanwhile, the energy efficiency gains provided by a higher-performing fluid can help any operation improve its productivity, profitability, and sustainability. Annually, our estimates suggest that such a formulation can help equipment move hundreds of thousands more tons; save tens of thousands of dollars on fuel and utility costs; and eliminate hundreds of tons of carbon dioxide generation. These can all be major bottomline impacts for any organization.
Modern hydraulic equipment has driven the need for higher-performing fluids, and it’s only reasonable to expect that such machinery will continue to evolve in the coming years. High-performing fluids that have been formulated with the right chemistry can help new equipment meet its full potential over the course of its lifetime. And by reducing the need for excessive, labor-intensive maintenance, these fluids have major potential to help operators significantly reduce their total cost of ownership. Work with your fluids supplier to identify and adopt such formulations — it can have a major impact. FPW
Lubrizol lubrizol.comMOTION, DRIVE, AUTOMATION FIRMS
ACCELERATE DIGITAL TRANSFORMATION
THE EVERY-YEAR HANNOVER MESSE IS SLATED FOR APRIL 17-21, WITH MORE THAN 2,000 EXHIBITORS EXPECTED.
WITHaround 2,000 exhibitors, HANNOVER MESSE will shine a spotlight on the way in which a number of different industrial ecosystems are intertwined to provide solutions for resource-efficient, climate-neutral and resilient production. The lead theme is “Industrial Transformation – Making the Difference” – a reference to how companies from the mechanical engineering, electrical and digital industries as well as the energy sector are driving change to tangibly reduce CO² emissions on a major scale.
High energy costs, broken supply chains, and rising raw material prices continue to pose new challenges to business. To remain competitive, companies need to take steps to increase their efficiency and contain energy costs, which in turn will lead to a reduction in their carbon footprint. High-tech solutions in this area will be presented at Hannover Fair — the world’s leading industrial trade fair, and the only event to centrally showcase the interaction of leading companies from the mechanical engineering, electrical and digital industries as well as the energy sector.
“At the upcoming Hannover Fair, we will be able to witness the new products and substantial innovations with which our exhibitors are tackling several different crises. In April, they will be presenting highly specific solutions for greater efficiency to counter climate change and enable CO²-neutral production. Digitization, artificial intelligence and hydrogen play a prominent role here,” said Dr. Jochen Köckler, Chairman of the Managing Board at Deutsche Messe. “Due to their high level of innovation, companies from the drive and fluid technology sectors have traditionally been among the biggest and most sustainable drivers of innovation at Hannover Fair.”
And indeed, the transformation of drive technology and fluid power is running at full speed. Despite numerous global challenges, the two sectors are experiencing excellent economic results. Innovative and solutions competence are placing drive and fluid technology at the heart of Industrie 4.0. Added to this are the issues of climate protection and resource efficiency, which require cutting-edge technologies to provide lasting solutions. Here in particular, digitization offers new, efficient and sustainable solution approaches for customers in both industries. More than 130 key fluid power companies will exhibit at the event, including ATAM, Atos, Bosch Rexroth, Duplomatic,
Aventics, Festo, HAWE, Walter Hunger, Hydac, Intertraco, Lee Co., MHA Zentgraf, Mindman Industrial, Roth Hydraulics, SUCO, Ultra Clean Technologies, Uniflex-Hydraulik, Walter Staffenberg, Velgan, VIS Hydraulics, Vitillo, and more.
“Drive and fluid technology components are the central building blocks of machines, for power and motion, but also as a source of data for digital value-added services and crucial to the performance of customer products — this is what we will be showing at Hannover Fair,” said Hartmut Rauen, Deputy Executive Director of VDMA, who is responsible for power transmission engineering and fluid power at the association. Numerous VDMA member companies will be highlighting practical examples in the context of digitization and sustainability.
The companies grouped in drive technology and fluid power trade associations can look back on a successful 2022. Sustained high order volumes and even order backlogs have resulted in industry sales of around 9.5 billion euros in fluid power and just under 18 billion euros in drive technology, which are record figures. Despite challenging conditions, sales in hydraulics rose by more than 10% in nominal terms to around 6.5 billion euros compared with the already excellent previous year. In pneumatics, sales are a tad over 3 billion euros, which also represents a nominal increase of around 10% compared with 2021. Drive technology is recording a short-term nominal increase in sales of just under 12%.
It is difficult to forecast developments for 2023. Order intake weakened somewhat towards the end of last year, although the base effect of the very good previous year must also be taken into account, with some customers’ warehouses also being full. Overall, the Executive Board of the Fluid Power Association anticipates nominal sales growth of 2% for the industry this year (hydraulics and pneumatics both + 2%). The Executive Board for Drive Technology expects a nominal increase of 3%.
The supply of raw materials and energy, rising costs, inflation as well as supply chain problems and a shortage of skilled workers continue to be a burden. Even though the dramatic picture emerging from VDMA flash surveys seems to be gradually easing for upstream supply chains, it will remain a defining issue. In terms of challenges, this is only surpassed by the shortage of skilled workers, which more than 80% of companies see as an existential issue for the future. The VDMA is committed to this with initiatives such as the Young Talent Foundation, Talentmaschine (talentmaschine.de), the Tech Talents young talent fair, research projects (for example in the Fluid Power Research Fund or the Drive Technology Research Association) and numerous trade association-specific activities.
Due to a number of different global crises, many companies are currently focusing their strategy on China and ASEAN markets. This year’s partner country, Indonesia, has so far played a fairly minor role as a trading partner for the two sectors. In the fluid power sector, exports amount to 20 million euros (40th place in export rankings) and in drive technology 39 million euros (44th place in export rankings).
There is a great deal of potential here however, especially in view of the fact that Indonesia is the fourth most populous country in the world and rich in raw materials. Both industries are planning to open up new markets outside of China. This is mainly dependent on how Indonesia succeeds in the future in developing an independent mechanical engineering sector in addition to its agricultural industry, construction industry and raw materials market.
In terms of digitization, the Fluid Power Association is a pioneer, with the digital twin created in the management shell. Data and information over the entire life
cycle are available in a standardized, structured form that is compatible with other formats across all manufacturers. Sub-models containing data for specific use cases are driving new business models. The results, which have been published at fluidtechnik40.de, are the result of years of standardization activities, which continue to be facilitated by the staff of fluid power member companies with great commitment.
The Power Transmission Engineering Association, with the participation of leading drive technology manufacturers, is developing OPC UA Companion Specifications for the industry in an international Joint Working Group. The first OPC UA Specification 40400-1 describes a uniform information model for the vertical integration of drive systems with the application area of asset management. In addition, the contents of the second part of the OPC UA Companion Specification Powertrain (40400-2) have already been defined.
The fluid power and drive technology activities are flanked by several VDMA initiatives, for example one involving the OPC UA interface standard, the “Industrial Digital Twin Association” (IDTA) alliance co-initiated by VDMA, the “Wireless Communications for Machines” working group, and the “Industrial Security” Competence Center, which is also exhibiting at the show. With Manufacturing-X, the federative data room ecosystem for the manufacturing industry, the platform gap is now also closing. In this way, the
VDMA is helping to realize the interoperable system landscape of intelligently connected Industrie 4.0 production methods.
In a survey of VDMA members, the number of companies dealing with climate-related
issues tripled in 2022 compared with 2019. In addition, 71% of the companies surveyed said they are creating resources to address the challenge of climate change. Power transmission and fluid power companies are actively contributing to climate protection with performance
modules and smart, efficient components and systems. The sustainability activities of the trade associations, including on the topics of carbon footprints, digital product passports or the circular economy, will be flanked in Hannover by two new guides for member companies on circular economy and climate-neutral production. The aim is to provide members with assistance in analyzing and implementing the relevant issues at their companies. In addition, the VDMA’s “Carbon Busters Award” initiative — a competition in which young employees can submit ideas for reducing CO² consumption — will present and highlight the winning proposals at Hannover Fair.
Companies from the VDMA Drive Technology and Fluid Power Associations offer core components and systems to help their customers implement issues surrounding sustainability and digitization. The examples at the trade fair reveal that the supplier industry is an important source of data and offers services that make future-efficient and sustainable machines possible.
The structured and continuous generation and processing of data are essential in this context. Software and hardware go hand in hand. This is what makes automated and predictive maintenance and the efficient operation of machines and plants possible. Digitization is leading mechanical engineering into the future by promoting sustainability, and drive technology and fluid power — as supplier industries — are key enablers.
Eight companies from the power transmission and fluid power industry will present innovative products, innovations and solutions. FPW
IFPE Booth S-82641
SLP13 two-way two-position poppet-type solenoid valve is a low-power, low-pressuredrop solution for compact equipment. Cartridge valve significantly reduces power consumption from 29 W to less than 10 W, to extend run time in battery-operated vehicles. Reducing power consumption reduces the stabilized temperature of the valve’s new coil by nearly 50%, preventing coil burnout and enabling longer service life. Lower pressure drop than previous generation solenoid valves improves fuel efficiency and reduces emissions. It is available in size 10 with a nominal flow rate of 79 lpm (21 gpm) and pressure rating of up to 350 bar (5,000 psi).
Omni Powertrain Technologies has released a new range of gearboxes for high torque transfer marketed under its Omni Solutions brand. The product offering consists of planetary drives providing an extended range of torque outputs from 6,000 to 1,000,000 Nm. The design of these products offers the highest power density for transmissible torque “inside” the boundary volume of each gearbox. Moreover, the design methods are based on the latest calculation standards and incorporate state-of-the-art gear drive and transmission technology to provide the most suitable option for the market.
Ultra-compact ADN-S pneumatic cylinder performs small movements in tight quarters, helping keep projects as space-efficient as possible. Festo took the ISO standard ADN double-acting cylinder and shrank the housing length to create a significantly smaller, lighter weight, and attractively priced choice for space-critical applications. The ADN-S is also smaller than other compact double-acting cylinders.
ADN-S comes with multiple mounting options and a choice of fixed or no end-position cushioning. A proximity sensor can be added. The piston rod is available with internal or external threading, in diameters 6 to 60 mm and in standard strokes 5 to 50 mm.
IFPE Booth S-80541
SM helical rotary actuators for mobile machinery are designed to replace multiple components and function as a rotating device, mounting structure and bearing, all-in-one. They offer high power density with high drive and holding torque capabilities in a small, compact space claim. For leak and drift-free operation, load-holding (counterbalance valves) provide high holding torque to resist external loads. Exclusion sealing and regular greasing assures contamination resistance. Drop-in-ready installation is easy on existing or new applications. The SM82 and SM45 feature up to 180 rotation with drive torque of 8,200 and 4,500 in-lb., respectively.
CONEXPO-CON/AGG Booth N-11267
IFPE Booth S-81721
Newest generation of user interface displays are available in 5, 7, 12, and 15 in. sizes, featuring a 1000 nit IPS display with an optically bonded AR lens allowing for outstanding sunlight viewability. They are sealed to IP67, enabling both in-cab and externally mounted applications. In addition, the design features an edge-to-edge glass design that allows the displays to be flush-mounted seamlessly into the dash and other highly stylized applications in either a landscape or portrait configuration.
The displays feature a wide variety of interface options, including multiple video inputs, CAN, Ethernet, Bluetooth, and WiFi which enable the user to enable multiple applications and interfaces with different vehicle communications.
SMK-702 series swivel bracket accessory for the 100 series hose reels and the V-100 series vacuum reels is built of heavy gauge steel and features 360-degree rotation, with multiple locking positions via an easy to use ergonomic pin lock. It allows the user to point the reel in the direction where the hose is needed, improving the experience and function during payout and rewind. The SMK-702 comes in two sizes, SMK-702-8 and SMK-702-12.5. The SMK-702-8 is for use with 8 in. wide drum 100 series such as the 1123-100 and the 117-3-250. The SMK-702-12.5 follows the same logic for 12.5 in. wide drum reels like the 112-3-150, 117-3-400, 112-4-75, 117-4-225 and the 117-5-100 but will also work with all of the 100 Vacuum series V-112-730, V-117-835 and V-117-850 even though the drum with is actually 13.5 on some of those reels.
The new HED displays are designed with an open Linux-based operating system enabling users to select from a variety of programming tools, including Crank, Qt, and Codesys.
The CCS 5 mobile contamination control system is suitable for pressurized online operation and unpressurized sampling of fluids. It quickly and accurately determines solid contamination particle size distribution, water saturation, and temperature of hydraulic fluids in real-time. A 7-in. color touch screen works even while wearing latex gloves, ensuring operators hands remain clean. Compared to the previous generation, the CCS 5 has a 50% longer battery life in suction mode, meaning it can be used in the field for longer without requiring charging. It comes with all necessary accessories, including power adapter, high-pressure hydraulic hose, suction line, instruction manual, and a USB stick. The system can also store up to 100,000 measurement points, which can be downloaded onto a laptop via the USB stick for further analysis.
Tsunami Compressed Air Solutions released four new products — adding more capacity and customization to the Air Dryers product line. Tsunami’s new products expand on the existing Pure Series Dryer line and include the Pure-1, a 5-cfm dryer; the Pure-3, a 10-cfm dryer; the Pure-7, a 25-cfm dryer; and the Pure-30, a 120-cfm dryer. All of the dryers will also be available with pneumatic drains. These wide range capacity products will provide more flexibility in the Air Dryers product line.
IFPE Booth S-83725
The Merritt Evolve is designed to adapt and excel in virtually any mobile equipment application. It boasts a new performance-driven handle design with individually configurable front and rear faceplates so customers can tailor the joystick to fit their application’s needs. A range of standard faceplates are available to choose from, consisting of buttons, thumbwheels, and rocker switches while also offering completely custom comfort. Its vertical design enables flexibility for lefthand or right-hand mount installations. It offers spring return handle action in single or dual-axis operation with different tension options
IFPE Booth S-81907
Sharing the same technology as Rota’s field-proven, internal LA series, the LL series has been designed for ultra-robust environments where monitoring by standard, in-cylinder position transducers is undesirable or simply not an option. It may be mounted direct to the machine or mirror the pin-to-pin dimension of the cylinder which requires monitoring. The LL series is field-replaceable, reducing machine downtime, associated repair costs and loss of productivity.
Available to suit many stroke lengths, in current, voltage and digital output signals, key features of Rota’s LL series include:
• high vibration rating
• IP69K open face M12 and Deutsch connectors
• absolute signal
• -30 to 80°C operating temperature range
optimization and can be
integrated handrest for maximum operator for further application supplied with J1939, CANOpen, or a Hall Effect output.
Leighton Lee II was an innovator. He founded our company on that spirit, and it’s how we solve tough problems today. Every product you see here—from miniature check and relief valves to shuttle valves, flow controls, precision orifices and plugs—was developed to solve a customer’s fluid control challenge. Since 1948, we’ve been delivering engineered solutions for a wide variety of demanding applications. We have the experience, product breadth, and technical know-how to provide engineered performance, with zero risk. Don’t let an imitator ruin your day—or your design. Contact us today to put our knowledge to work for you. Learn more at theleeco.com/innovate
It would be easy to assume all cylinders fail in the same fashion — that hydraulic cylinders bypass and air cylinders experience bent rods. However, it’s a false assumption because the nature of their operation and intended application differ. Sure, a hydraulic cylinder can bypass but not as easily as a pneumatic cylinder. And indeed, an air cylinder may experience a bent rod, but rarely from its own force creation like with hydraulics.
The medium of compressed gas offers its own challenge to the linear actuator, which in turn results in unique modes of failure. A pneumatic cylinder, by and large, fails most frequently when its seals leak. Air cylinders leak past the rod seal, the piston seal(s) or the end seals. End-of-stroke cushions may also use soft seals, but because they are rarely adjusted after initial commissioning, they tend to be stable for many years.
With seal failure as the primary mode in mind, we must ask why pneumatic cylinder seals fail. When a seal no longer contains or isolates pressurized air, one of
many factors plays a part in the breach. Factors in seal failure include heat, extrusion, cracking, physical damage, and regular wear. Some factors, such as wear, are inevitable, while others are preventable through care or forethought.
When rubber heats up, the polymer becomes softer and more prone to wear and extrusion. The softer rubbers exhibit higher friction, so imagine a buna seal heated past its maximum rating and sliding across a steel rod. The higher friction from the soft rubber not only experiences wear across the friction surface as rubber molecules are ripped away, but the likelihood of extrusion increases as the rubber behaves more like a viscous liquid.
Seal extrusion occurs when the clearance or gap between the mating components opens too far, consequently allowing pressurized, semi-liquid rubber to escape. Suppose the extrusion gap (sometimes referred to as “E-Gap”) is large enough. In that case, the seal may catastrophically fail, but more likely, the effect slowly nibbles away at the edges, creating a ribbon of rubber material trailing into the low-pressure side. With enough extrusion-related ribbon removing material from the primary sealing location, the cylinder will slowly leak. A specific example occurs with barrel endseals when the rod is pulled with excessive force, stretching either the tie-rods or screws, which open an E-gap.
When a seal cracks, circumferentially radial (around the O-ring cross-section) gaps tend to open, thereby passing air. Seal cracking occurs through one of various
outside influences, such as chemical, heat, or UV exposure. When exposed to oxidizers such as fluorine or chlorine, rubber may quickly harden and crack as it no longer remains soft. Repeated heat cycles accelerate oxidization, even outside the presence of chemical contamination. Ultraviolet exposure may also result in cracking, especially in outdoor conditions subjected to heat and cold cycles.
Physical damage occurs more commonly than you think. For example, high-quality air cylinders employ rod wipers to clean the rod during every retraction stroke. However, should the wiper fail while working in contaminated environments, your first line of protection no longer prevents intrusion. Melted plastic, welding spatter, or industrial fallout may all wear or destroy a rod wiper, allowing subsequent contamination to walk right in to also damage the primary piston seal.
Of course, no seal lasts forever, and with regular use, any seal will need to be replaced eventually. However, one can still prevent premature wear by properly selecting seals to suit the application. High ambient heat requires suitable sealing technology, such as Viton, which remains stable where buna nitrile may fail. High-velocity applications should use appropriately selected seals, such as U-cups. High-friction seals, such as T-seals, are best suited for slow duty cycles because the interference-fit nature results in high friction. High friction results in high wear.
Outside of seal failures, pneumatic cylinders also fail when something careless or dangerous occurs. No matter how intelligently selected the seals are, backing up your live-bottom trailer into a wall and breaking a piston-rod on your tailgate cannot be prevented with even the best seals. FPW
As a leading manufacturer of precision-engineered fluid power products, Permco designs and builds the best-value solutions that uniquely fit their customers’ needs. With a decades-long tradition of exceptional customer service, Permco offers the highest quality product available to a wide customer base of OEM’s and distributors. Permco understands that the only success that matters is the success of their customers and are committed to reducing costs while continuing to make the process of doing business easy. With Permco, it’s personal.
Designing efficient systems involves much more than simply understanding a few basic principles. There is a true art to balancing the specific requirements of an application in order to achieve the desired goals in the best possible way. Help us understand the unique needs of your application and together, we’ll develop something that surpasses what any of us could have done alone.