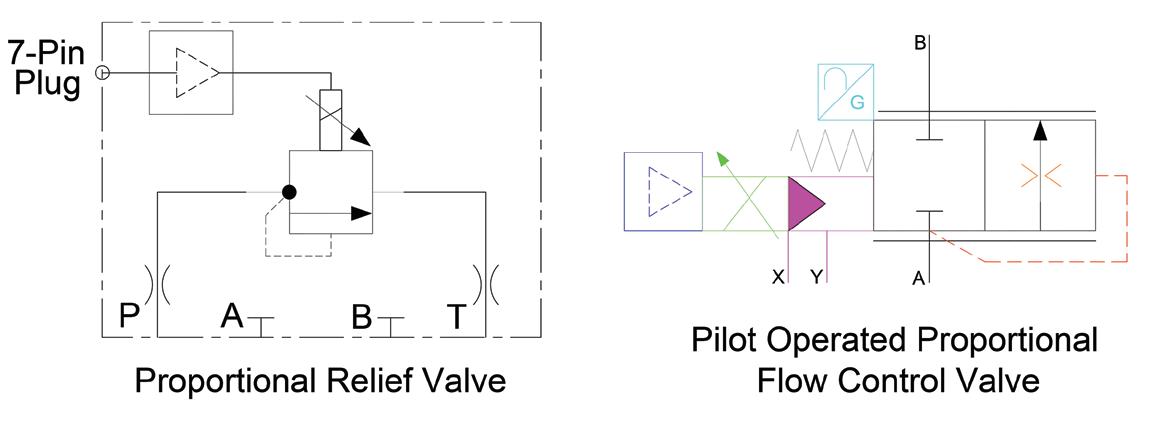
10 minute read
Hydraulic symbology 302 – high response valves
A “high response valve,” is a relatively new term used todescribe valves whose performance is variable, dynamic andpowerful. Previously only servovalves running technologies suchas a torque motor could be classified as high response, but withthe proliferation of contemporary electronics, feedback andprogramming, proportional valves have closed the gap. Now someproportional valves match the performance of servovalves, but forthe purpose of this discussion, I’ll call them all proportional valves.
I discussed proportional valve operators in Symbology 301 – Electrical and Electronic Symbols, which appeared in the August 2019 Fluid Power World magazine. However, only the electrical operators were discussed, leaving out any holistic explanation of a high response valve. In Symbology 302, I delve deeper to elucidate how electronic and hydraulic symbology intertwines to produce hybrid symbols reflecting the purpose of each valve. I should stipulate, electronic symbols in fluid power are not representative of electrical symbols, although anyone fluent in electronic symbology catches on quickly.
As mentioned in earlier articles in this series, there exists not only the ISO 1219 standard for drawing fluid power (and electrical) symbols but also a less relevant ANSI standard for drawing symbols. However, this does not stop individual manufacturers from drawing and detailing symbols as they see fit, either for clarity or narcissism, depending on who you ask. I’ve chosen actual catalog symbols from major manufacturers, so their depictions stray from explanations outlined by me previously. Bonus points if you can figure out who is who.

Figure 1. Proportional accessories valves
I’m starting with the symbols for proportional accessories valves – in this case, a proportional relief valve and a proportional flow control. I’ve sidestepped simple symbols because I know you’ve learned the basics by now, so you’ll see no bare-bones components made proportional by way of just a diagonal arrow. These are compound symbols using various individual symbols concomitantly performing a single hydraulic function.
In Figure 1 the proportional relief valve sits nested in the dash-dot boundary line, itself illustrating the encompassing nature of this symbol. In this case, the valve is an ISO 4401 D03 subplate mounted unit, which although nothing about the symbol tells us this, the functioning P (Pressure) and T (Tank) ports are being used while the A and B work ports are simply blocked due to obsolescence. The bottom of this valve may or may not exist with O-ring grooves for the work ports, and the optioning of them depends on the functioning of the proportional valve, which could also be constructed as a work port relief valve.
Both the P and T lines are shown with fixed orifices, a feature that protects the valve from saturation of flow. The valve is intended to operate in a pilot circuit, either by controlling system pilot pressure or as the singular control over a larger valve (like a slip-in cartridge element), so it flows very little.
Pressure energy flows directly into the left of the relief valve, where the pilot line can act upon the currently offset arrow to move it into the open flow path should upstream pressure overcome the solenoid’s active pressure setting. You’ll notice this manufacturer uses no spring in the symbol of the valve, although I assure you the spring exists in the physical part. They have simplified the operator as a simple solenoid rectangle bisected with the diagonal variable arrow. The diagonal arrow will be common to most, if not all, proportional valves, showing us that the current can be varied to adjust the position of a valve spool or poppet to achieve various ends.
The manufacturer embellishes the symbol with a 7-pin connector, which is a common connector used for proportional valves with onboard electronics. Those electronics will include an amplifier circuit to take the input power and control signal and turn it into a PWM output the valve can use. As discussed in the earlier article, the triangular amplifier symbol differs slightly in fluid power from electronic symbols by way of the dashed line, so as to not confuse it with a pneumatic pilot source. A final note on this symbol is that the manufacturer used the circular connection node at the pressure port of the relief valve, something not standard for an ISO symbol.
The next symbol in Figure 1 is also that from a major manufacturer, and at first glance appears to have a lot going on. It looks primarily like a 2/2 directional valve, and essentially it is. I’ve colorized this one to make explanations easy, but please note my color choices do not reflect any standard. It starts with a 2-way, 2-position valve symbol which is normally closed in neutral, with both A and B work ports blocked. The highly experienced among you will have noticed the dark red pilot line starting at the A port and working around to the right side positional envelope, and if you guessed this is a slip in cartridge valve, you’d be correct. This particular valve is a spool, however, rather than the traditional DIN poppet design.
The dark red pilot line tells us this valve can pilot itself open directly with pressure at port A because fluid acts upon the bottom of the spool directly and fights against only the spring force. As always, the parallel lines above and below the two operator boxes show infinitely variable positions between the two extremes.
The symbols to the left are stacked out quite wide, with three major components affecting performance. The first in magenta is the hydraulically operated pilot valve. The dark triangle (normally colored black) facing towards the operators differs from a pneumatic pilot source which would be a hollow triangle. The hydraulic pilot is required to overcome the flow forces at port A, which would prevent a direct operated valve from shifting.
The X line feeding into the bottom of the pilot triangle is the external pilot supply line, which for this valve must be equal to or higher than the work pressure at port A. The Y line is the pilot drain, which is needed to keep the spring chamber drained to allow both the pilot and main stage valves to perform predictably. Any pressure in the spring chamber of the valve can be additive to spring force, reducing valve performance or killing it altogether.
Attached to the left of the pilot actuator is the solenoid valve that operates the pilot valve, which is one and the same component — a screw-in cartridge valve in this case. This cartridge valve is actually a pressure reducing valve. The spring symbol above the pilot actuator shares a chamber with the external pilot supply coming from X. The pilot valve will reduce pressure as required to allow the valve to open, increasing flow; full pilot pressure means the valve is closed, while exhausted pilot pressure at Y will allow the valve to open fully.
The two dark orange orifice arrows pointing inward at the directional flow arrow are because this is an orifice spool, where fluid passes through the center from A to B to exert force upon the spool as a method to measure pressure drop. The force on the spool is measured by the linear transducer, the cyan symbol defined in the earlier article.
The dark blue attachment at the left is the amplifier card containing all the onboard electronics, and with the feedback from the linear transducer (which if you remember was measuring spool position and its movementrelated to pressure drop), will modify the signal at the pressure reducing valve as needed to match flow rate with the desired analog input from the PLC to the amplifier card. This valve operates on a closed-loop to provide accurate flow despite viscosity, pressure or temperature fluctuations.
In Figure 2, we’ve kicked up the symbol a bit to show various primary symbols arranged in a compound symbol representing a pilot-operated proportional valve with onboard electronics and spool position feedback. Once again, I’m using the symbol as exists in the catalog of a major manufacturer, so my top students will note the differences between this and the standards I’ve covered thus far.
The pilot valve is a 4-way, 3-position proportional solenoid valve, spring-centerd with a “float” spool (P blocked with A and B to tank in neutral), which is sometimes called a motor spool. The parallel lines above and below the positional envelopes surrounded by proportional coils using diagonal arrows make it clear we’re dealing with a proportional valve.
The center condition is the basic form of a float center spool but has added to it an orifice symbol to each work port. Orifices are shown in the center condition of many proportional valves to describe the nature of the spool and body combination installed in the valve. Axially machined grooves called metering notches are added to the valve spool so that partial flow occurs even while the spool grooves are not fully extended past the internal ports of the body.
The orifices describe the metering notches, but also how it performs just off-center. The metering notches will allow a more gradual increase in flow rate as the valve shifts away from neutral, making this type of valve more desirable for applications accelerating smoothly from a stop. If the flow is regulated mostly while the machine is “at speed,” then more valve overlap can be used, but there tends to be a bit of a dead zone in the lower range of the command signal.
On the far right of the pilot valve is a familiar shape, although a previously undiscussed version of a symbol: the amplifier. The same triangular amplifier symbol is used, but rather than the dashed line to differentiate from a pneumatic pilot source, this valve employs three simple lines nearly trisecting the main triangle. This manufacturer came up with their own solution to prevent confusion, but I wonder if it caused more questions than answers.
The pressure and tank ports of the pilot valve are fed and drained respectively via pilot lines, which are both the same dashed line. Older versions of this example may have used the dotted drain line connecting the tank port to the tank line, but these days the dashed line represents both while allowing their obvious function to define the difference.
The work ports exit the lower valve with pilot lines crossing and then feeding into the pilot operators on either side of the main stage spool. You’ll notice the pilot operators are “floating” outside the valve, an interesting choice outside the ISO standard of a rectangular box attached to the a and b envelopes as is used on the proportional flow control symbol in Figure 1. You’ll have noticed the pilot lines cross using the obsolete semicircular jump I described as old school way back in Symbology 101, which is an odd choice in this symbol since other crossed lines simply cross as usual. My intuition tells me they didn’t feel the pilot lines crossing with the work lines would be confused as a junction, even though the appropriate nodes are used to join lines in other parts of the symbol.
The pilot lines need to cross each other to correctly direct flow from the pilot valve to the main stage valve. When the a envelope of the pilot starts to shift, it opens the P to B flow path, sending fluid to the a operator of the main stage spool. The opposite path exists when the b operator sends fluid from P to A across the pilot valve to shift the b operator of the main stage valve. Speaking of the b operator – it shows a symbol I’ve never seen used previously to this example.
The closed center neutral 0 position is typical, as is the a position showing P to B and A to T. The b envelope shows P flowing through an orifice to A and then A also flowing through an additional orifice to B. For any directional valve, connecting the pressure port simultaneously to both work ports creates a regeneration circuit. Regeneration is a counterintuitive function that allows a cylinder to extend rapidly but inversely proportional to a reduction in force. Usually, the symbol looks like the float spool of the pilot valve, but with P joined to A and B instead. However, I suppose this unique design was required to accurately represent the sequential metering of the two orifices.
As with most proportional valves, the main stage spool also shows the parallel lines above and below the main symbol to represent infinite variability between positions. As well, the transducer symbol perched at the top left measures the absolute position of the main stage spool to confirm the pilot signals are accurately positioning its larger spool. I would think that with proportional valve symbols using onboard electronics combined with spool position feedback, it would be helpful to draw an electrical line from the transducer to the amplifier to detail the concept of closed-loop control.