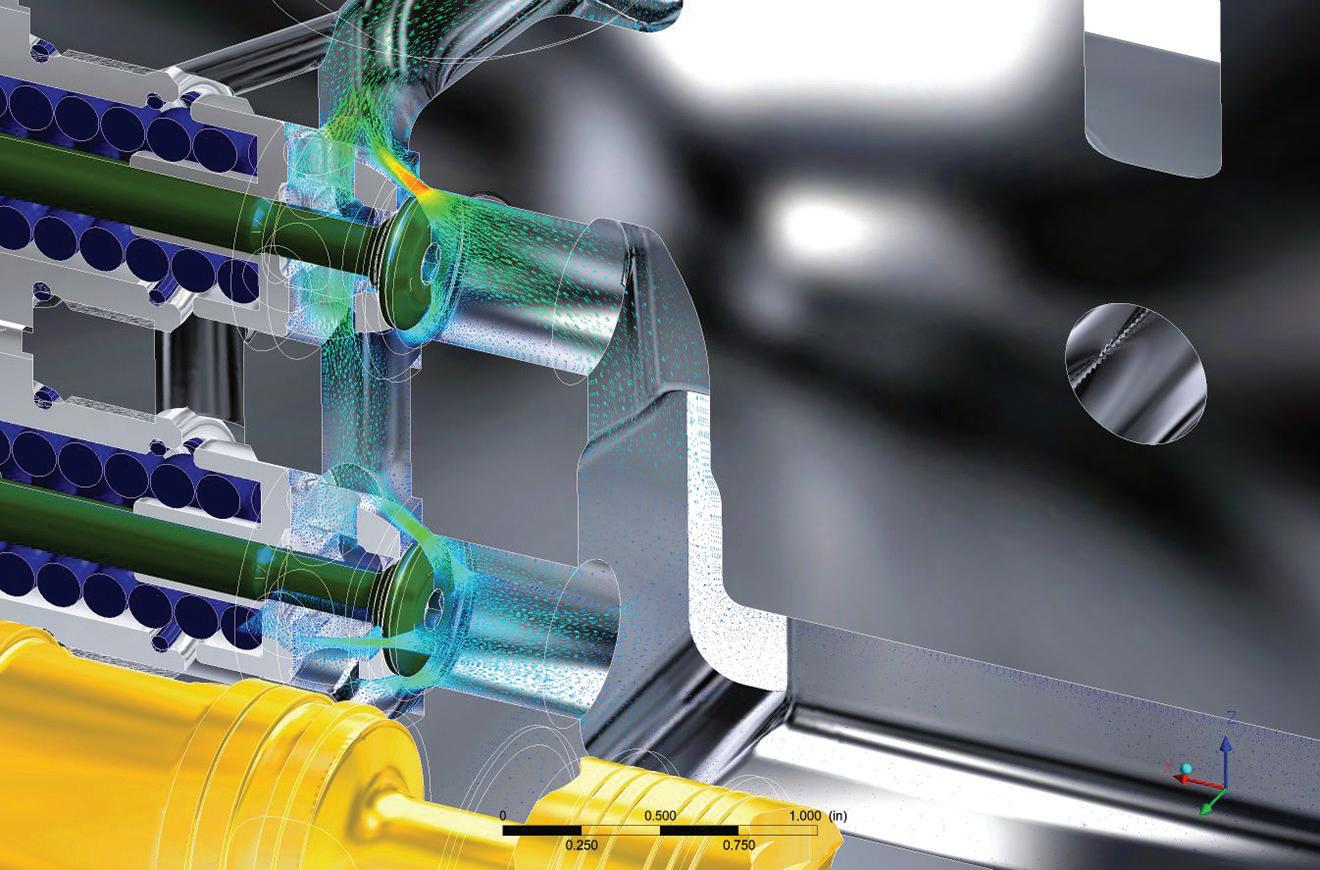
7 minute read
Part 1: Fast-tracking innovation through CAE simulation
This is the first in a two-part series on simulation in an economic downtown. Stay tuned for part 2 in our next issue, or find the complete article online at fluidpowerworld.com.
Economic slowdowns can hurt new business throughtightening budgets, order reductions or losses and breeding uncertaintyin the business. Because of this, many companies choose to putresearch and development departments in a slowdown in an effort tomaintain a semblance of normal operations. However, while focusingon survivability in these times is understandable, neglecting long-termgrowth will ultimately harm a business, causing design engineers tomake hasty decisions with limited information which can affect thequality of the products and the total product cost.
Innovation and R&D must always be an area of focus, especially during an economic slowdown, no matter how counterintuitive it may seem. To do this, engineering teams must harness the power of new technologies to drive innovation. Through computer-aided engineering (CAE), engineers can expedite R&D testing, bringing products to market faster, and developing higher quality products at lower development costs.
The power of simulation
Physical, real-world testing and prototyping have long been the backbone of R&D. However, with modern CAE, simulations are now an effective and reliable way to fast-track product innovation, offering shorter design cycle timeframes and reduced costs.
The power of CAE software centers around virtual prototyping. The advantages of virtual prototyping include:
• Lower costs
• Shorter time to market
• Higher-quality designs
• More competitive products
Before a wider adoption of simulation, the prototyping phase of a new product development project primarily involved creating a new physical prototype with each design change, leading to countless hours spent and piles of discarded castings, machined components and other hardware. Because parts made with permanent tooling, castings for example, can easily cost tens of thousands of dollars, the costs of design iterations can add up quickly. A cost-efficient prototyping process hinged upon getting the design right on the very first try, which, as any engineer would say, is about as likely to happen as winning the lottery. In engineering, it’s fairly easy to get it “right,” however it is not easy to barely get it right when it comes to perfectly optimizing for balanced performance and cost.
Now, through CAE-enabled virtual prototyping, engineers can create an analytical model of their design. These models allow a product to be tested in a virtual environment without the time and cost associated with making a physical test specimen. When simulation is an integral design tool, more time can be spent on product optimization instead of working to create products that merely achieve the minimum functional design requirements.

CFD simulations. Images courtesy of Parker Hannifin.
No matter where a design team is in the design process, simulation can help. Common virtual tests include:
• Linear/non-linear static stress simulations to evaluate the strength of components based on how they will be loaded and constrained during operation,
• Thermal analysis and CFD simulations to gauge heat distribution through a model, and determine fluid flow in and around objects,
• Modal/vibration simulations to examine what happens to a part and how it performs when it undergoes vibration, and
• Fatigue simulation to identify the maximum stress, strain and deformations components will experience in use.
Simulations keep testing flexible and cost-effective, saving months or even years stuck in the design phase. That flexibility is key. Virtual prototyping allows an engineer to perform sensitivity and optimization studies where manufacturing tolerances are varied to determine acceptable and achievable tolerances from the very beginning of the project. This leads to fewer product iterations and less scrap during prototyping and production.
Simulation also makes it possible to benchmark designs against competitors by comparing a competitor’s product against the engineer’s own designs with virtual analysis tools. This way engineers can achieve better performance indicators and surpass the competition before finalizing the design.

This can help to build confidence in simulation modelling to accurately predict product performance. Economic downturns present an opportune time to focus engineering efforts on building simulationbased predictive models with confidence.
With virtual prototyping, design issues are often more apparent, allowing engineers to catch mistakes before they make it to final production. Late design changes and on-site modifications are risky and extremely costly; they delay project timelines and negatively impact customer confidence and growth, making it critical to identify errors as early on in a project as possible. Simulation coupled with tools like Design Failure Modes and Effect Analysis (DFMEA) can identify failures early in a development cycle so that engineers can create successful designs and not be forced to compete with mediocre products or limited resources.
Engineering simulation can also help to break into new markets. With up-front benchmarking against competitors and using virtual prototyping to mitigate design risks, Parker was able to develop the VO20, a new aluminum open center sectional valve. Parker was able to make the valve lighter and more reliable while increasing efficiency and product life, making it a good fit for mobile equipment applications in the trailer market. With the valve’s simulation-validated test data regarding fatigue life and hydraulic efficiency, Parker was able to break into the trailer equipment market and is now expanding the use of the product into other markets where weight reduction is critical. In the last decade, simulation has been key in the expansion Parker has achieved in these markets and in others, like oil and gas. By using simulation tools to combine proven valve technology already used in mobile and industrial applications with advanced subsea technology, Parker has been able to repeatedly create products greater than the sum of their parts.
Power beyond prototyping
Simulation enables the creation of better prototypes quickly and efficiently, but the power of simulation doesn’t end after a final design is chosen. Extensive virtual testing across multiphysics domains make it possible to account for scenarios that cannot be replicated in physical testing. It also enables design space exploration to drive innovation in ways that are simply not feasible in physical tests. Simulation also allows troubleshooting any issues in the field without having to perfectly recreate the physical environment. By analyzing the problem with CAE software, design engineers can easily identify potential problematic characteristics that are not otherwise observable.



How simulation can combat effects of a downturn
Part of what makes simulation so powerful is its ability to resist, and even reverse, the impact of economic downturns. Layoffs, facility shutdowns and other economic hardships that would normally prevent product development are less of an issue with virtual testing.
Design teams can use simulation to help identify and eliminate areas of high cost or inefficiency, leading to more cost-effective virtual solutions. Playing into Value Analysis and Value Engineering (VAVE), simulation allows the team to explore creative problem-solving strategies that can promote product development and improve processes. By creating internal communities of practice (CoPs), as Parker does between seemingly disparate technology groups including aerospace, filtration, and fluid power, it is possible to leverage a large engineering team to examine simulation and design best practices without increasing engineering headcounts or incurring large overhead costs.
Legacy product lines that were designed before the advent of simulation can be revisited for the team to identify the hidden potentials for cost savings. These could include:
• Material reductions
• Simplifying electrical and mechanical systems
• Using more modular components
• Avoiding large welds
However, don’t make the mistake of ignoring how important simulation can be outside of the niche role of engineering product development teams. Simulation can play a part in many cross-functional teams, bridging the gaps between departments.
Simulation can provide value through the new product development stage by forming a relationship with customers through exchanging simulation models to better understand their systems and desired outcomes. Beyond designing, virtual tools can also assist marketing and sales in identifying what the most marketable features of products are. CAE testing provides a good salesperson more data than ever before, so make sure to highlight any key features in the next marketing pitch.
The product quality team can step in to analyze analytical models as if they were physical products, then advise the design team on any problematic features. Make sure to then loop in supply chain as the teams work toward the final product so that they can provide further component-related feedback and quickly find suppliers and implement their design for manufacturing suggestions to drive down cost.
By using CAE tools at every stage in the design process, from initial conception to the delivery of the final product, engineers will be able to add even greater value and help protect the business, even when business opportunities are threatened by a sluggish economy.
Parker Hannifin | parkerhannifin.com
Industry Examples of Simulation
Engineering simulation testing has been a key performance differentiator for many markets. Examples include:
• Reduced time to market for automotive tires
• Optimized consumer container designs
• Reduced testing and development times for equipment power trains
• Reduced design cycles for golf equipment
http://www.acqnotes.com/Attachments/Federal%20Agency%20(NSF)%20View%20of%20Simulation-Based%20Engineering%20and%20Science,%209%20Nov%202010.pdf