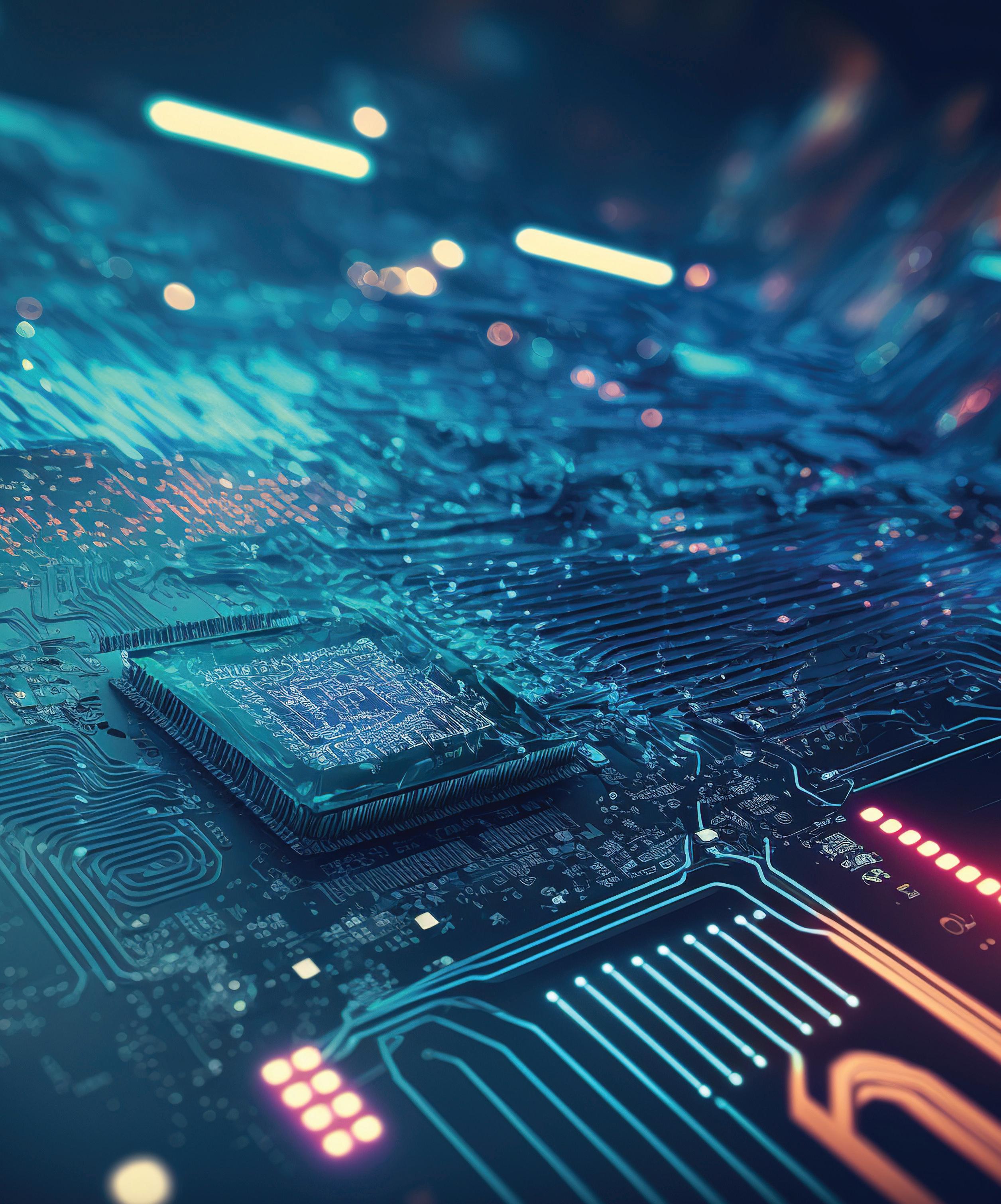
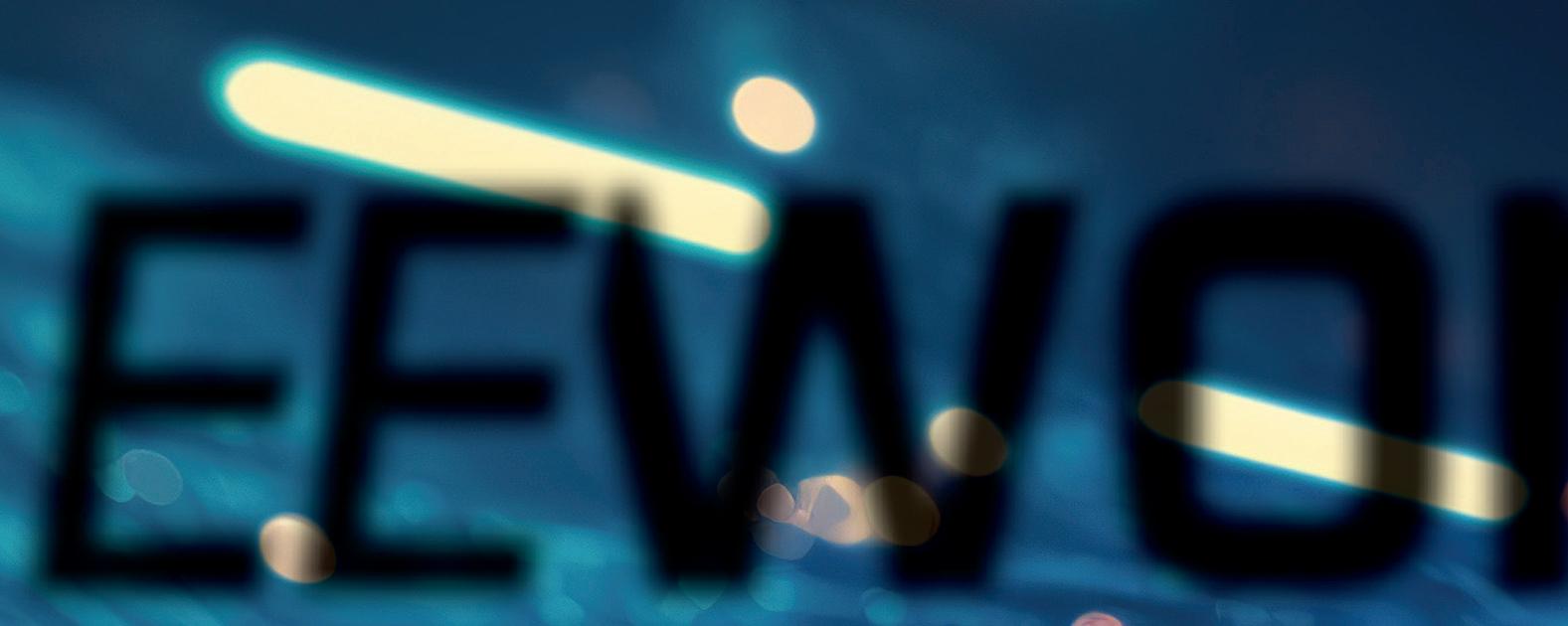
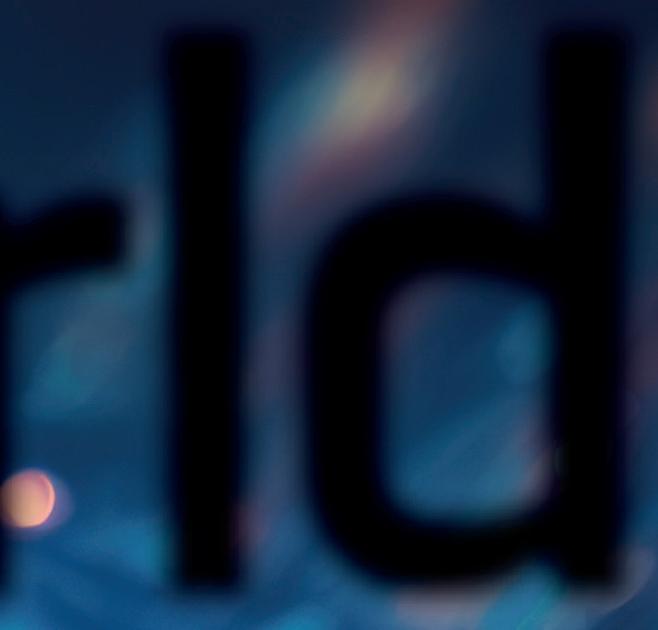
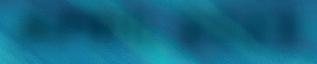
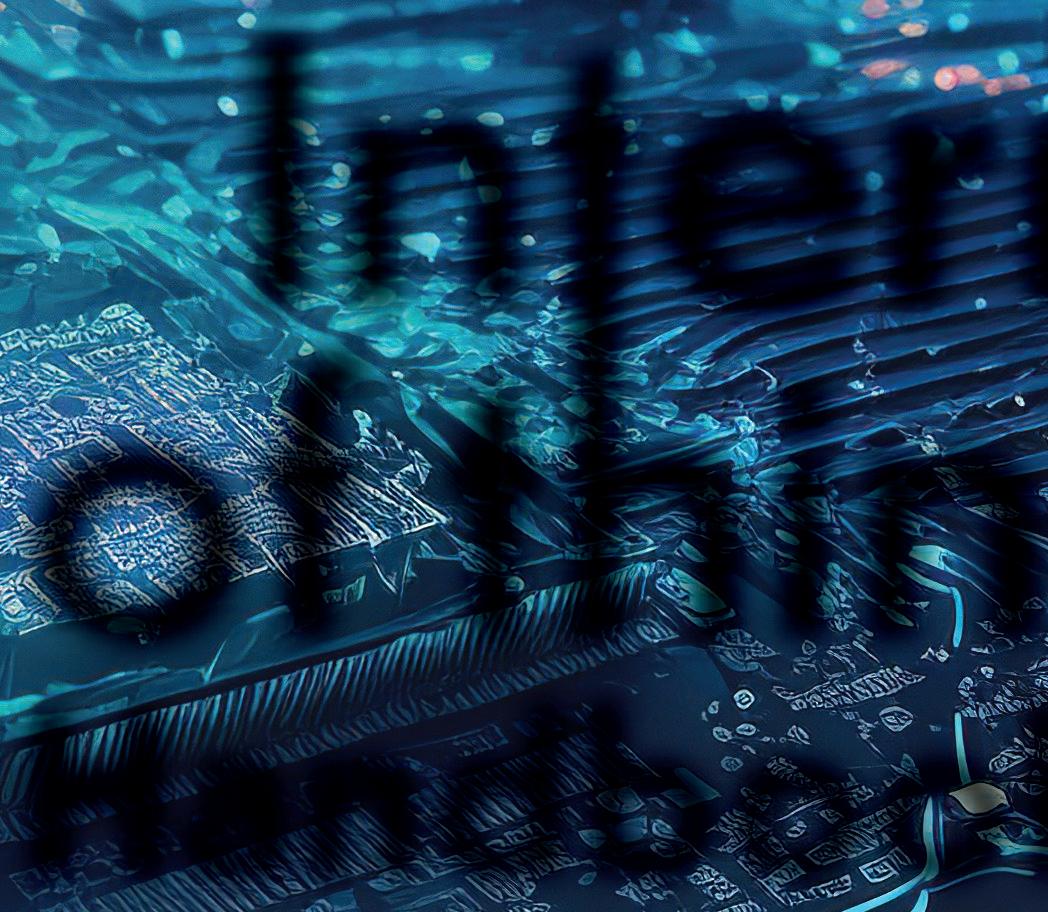
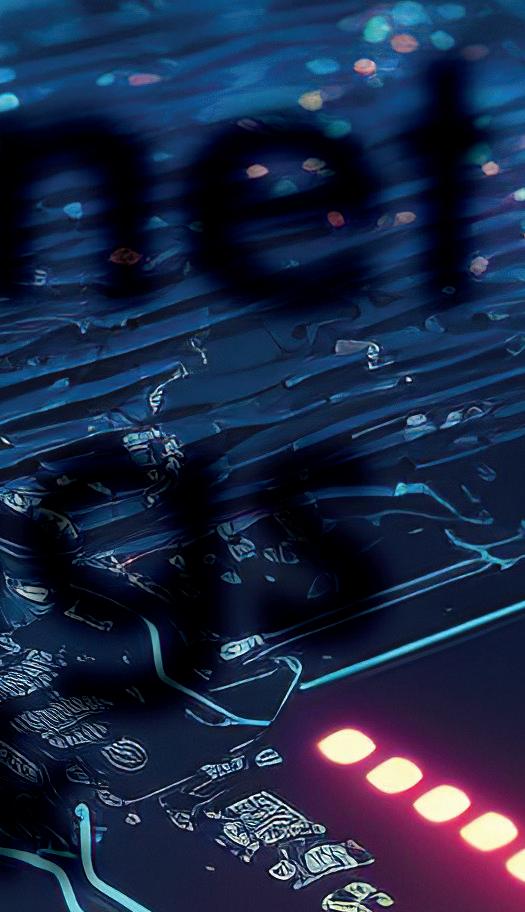
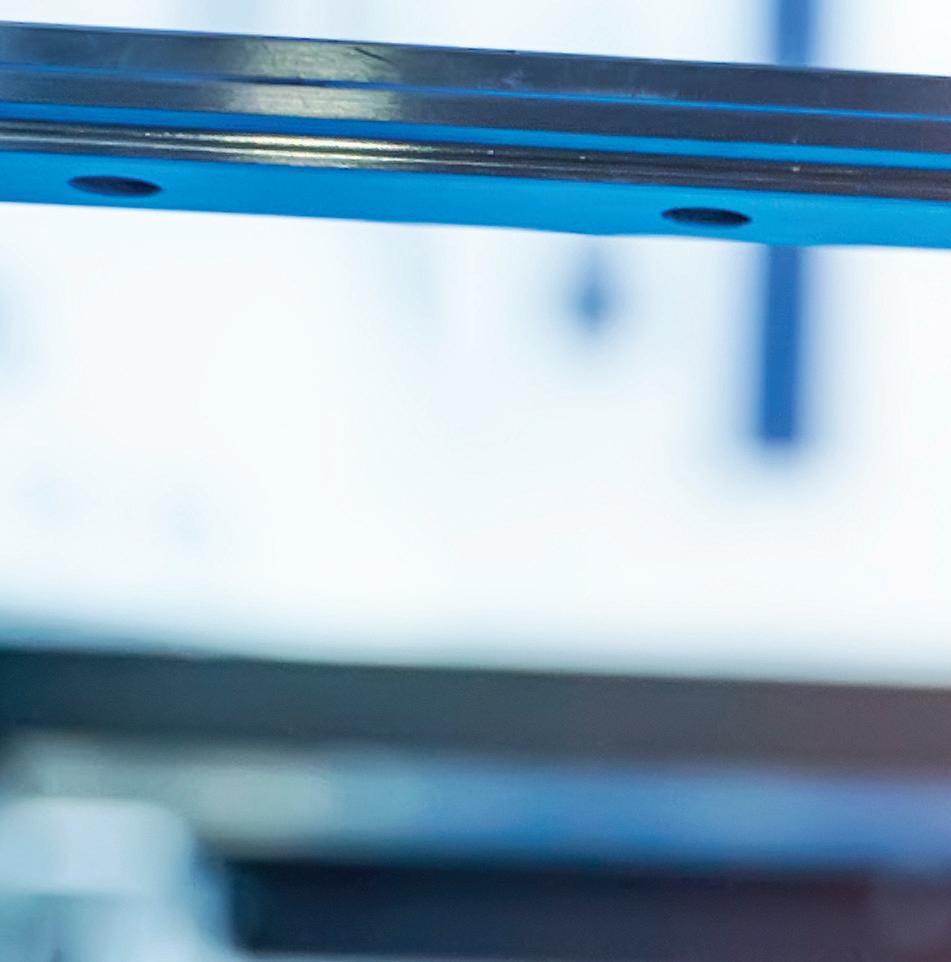
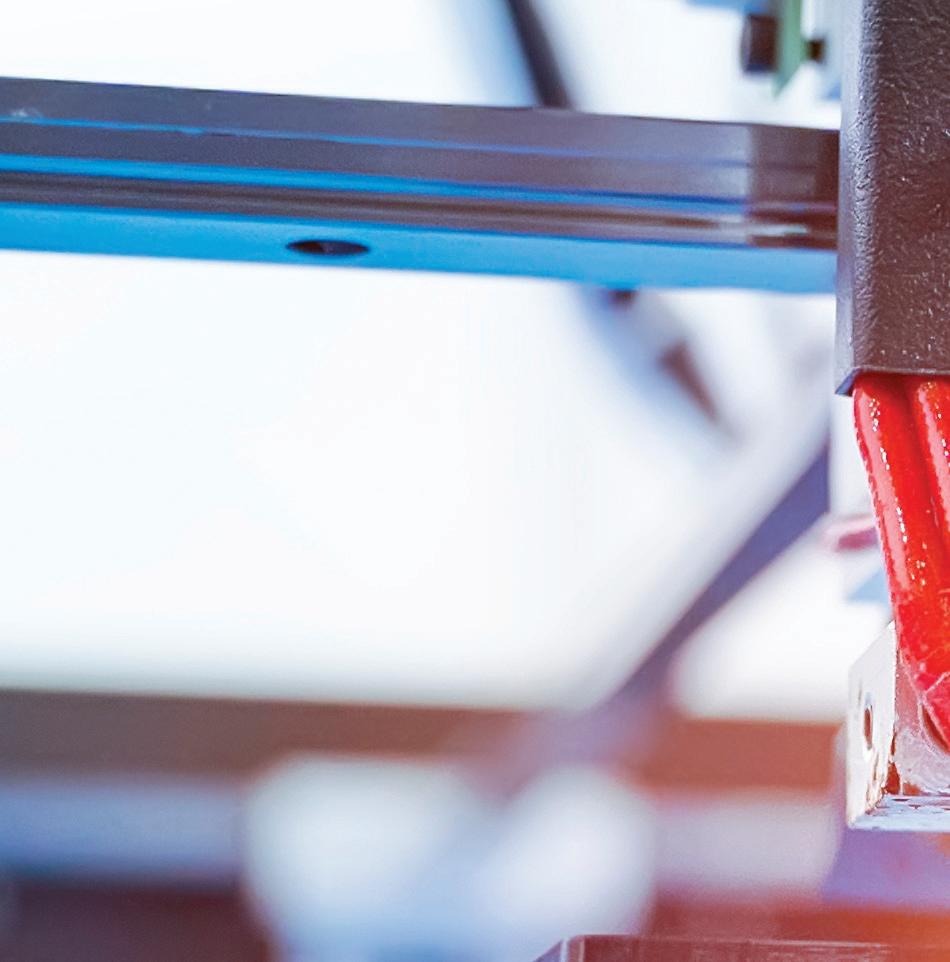
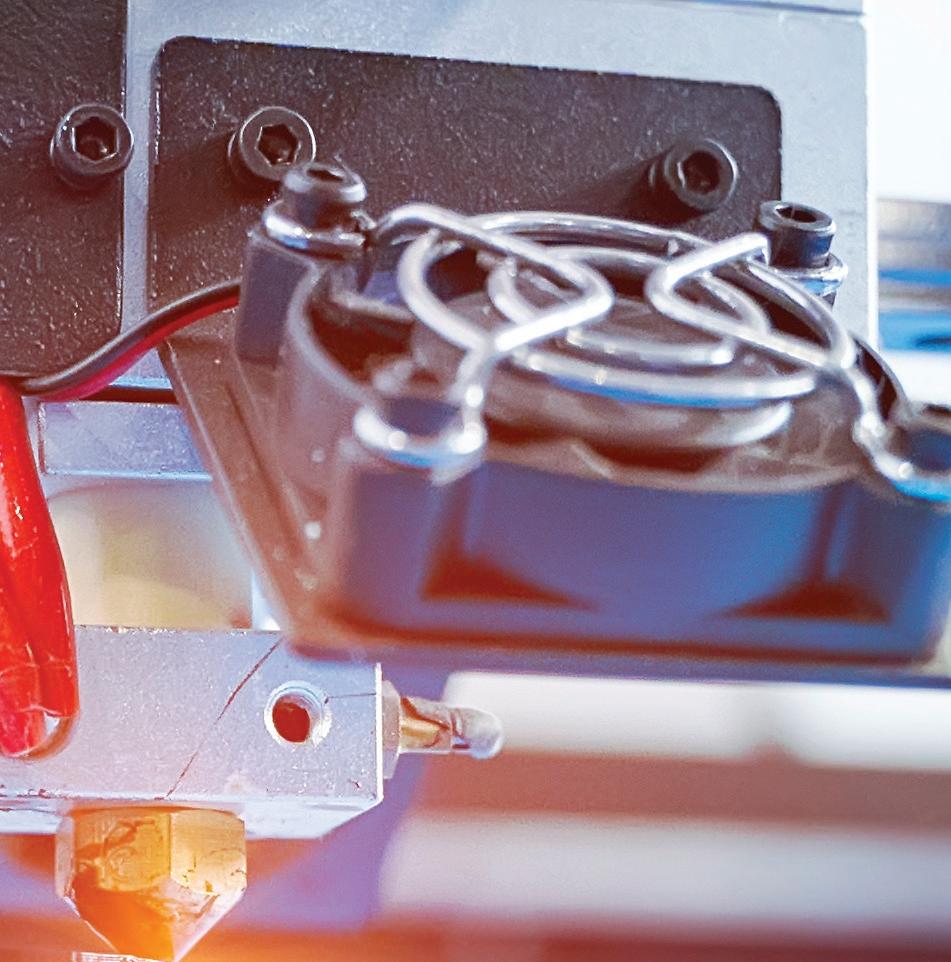
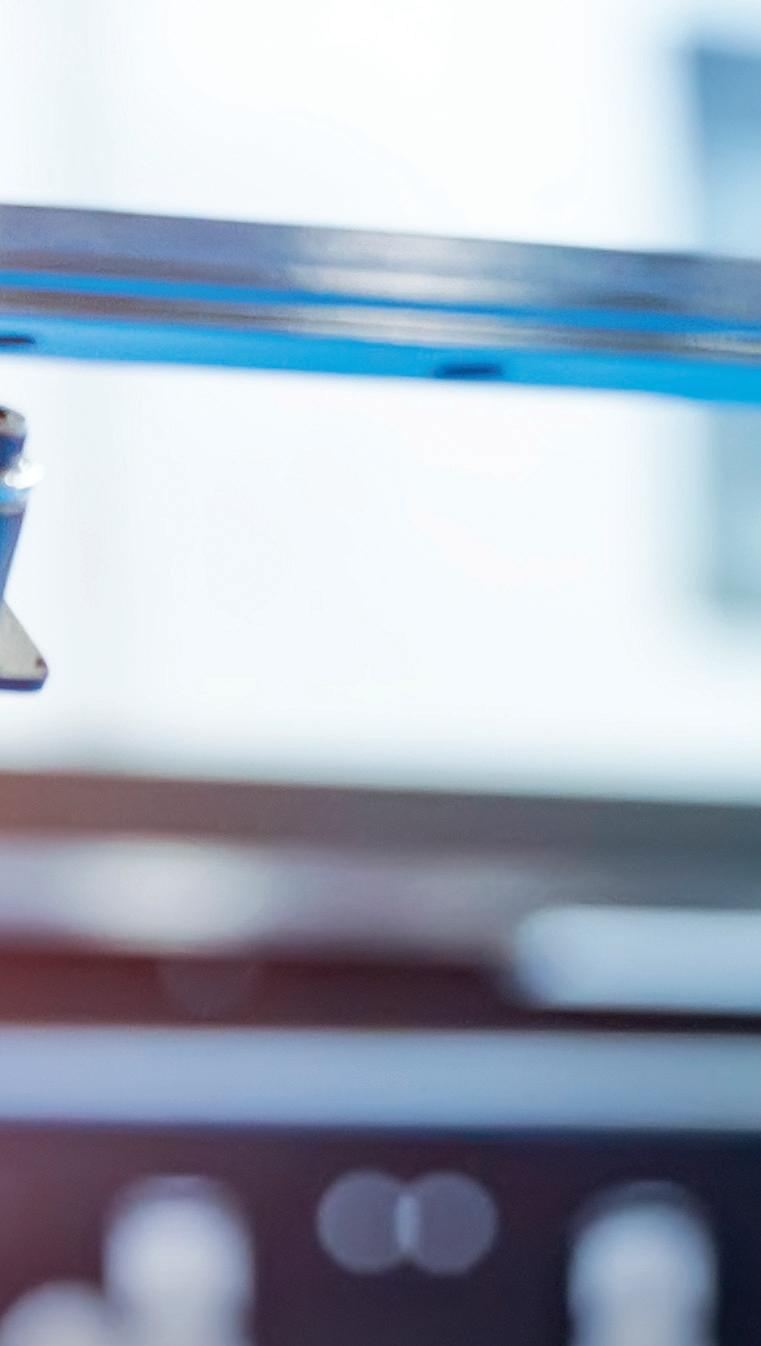
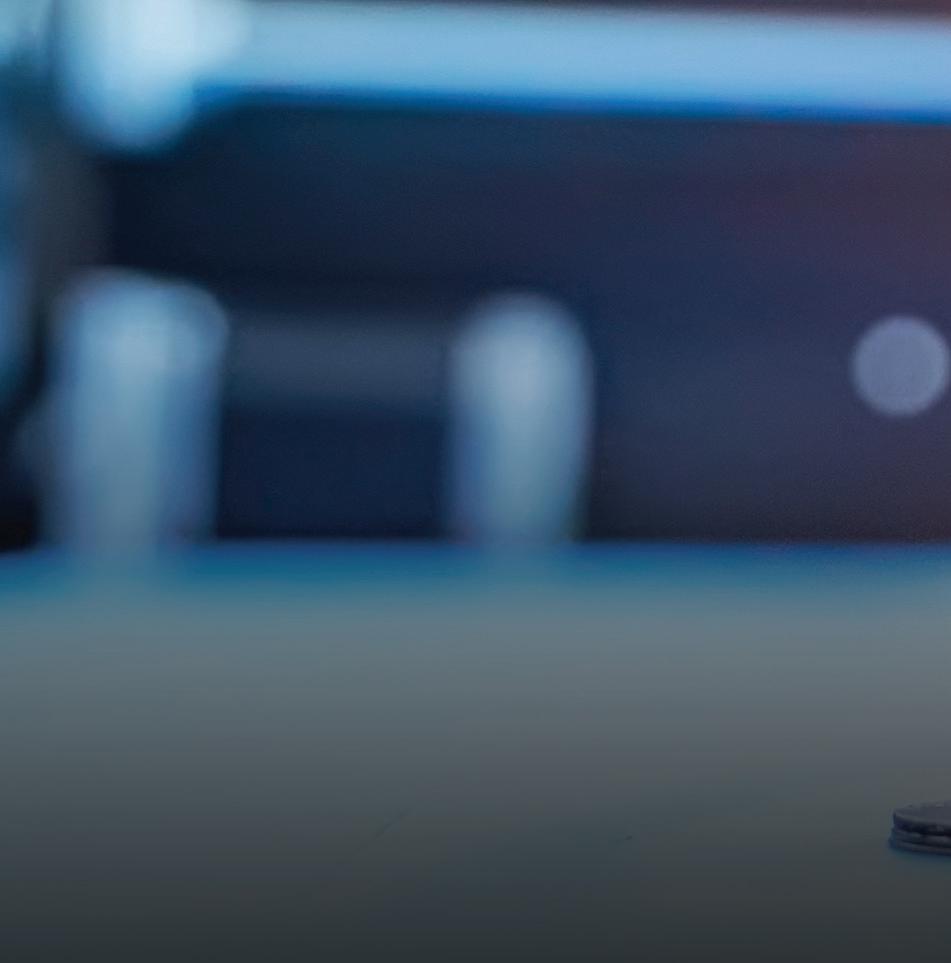
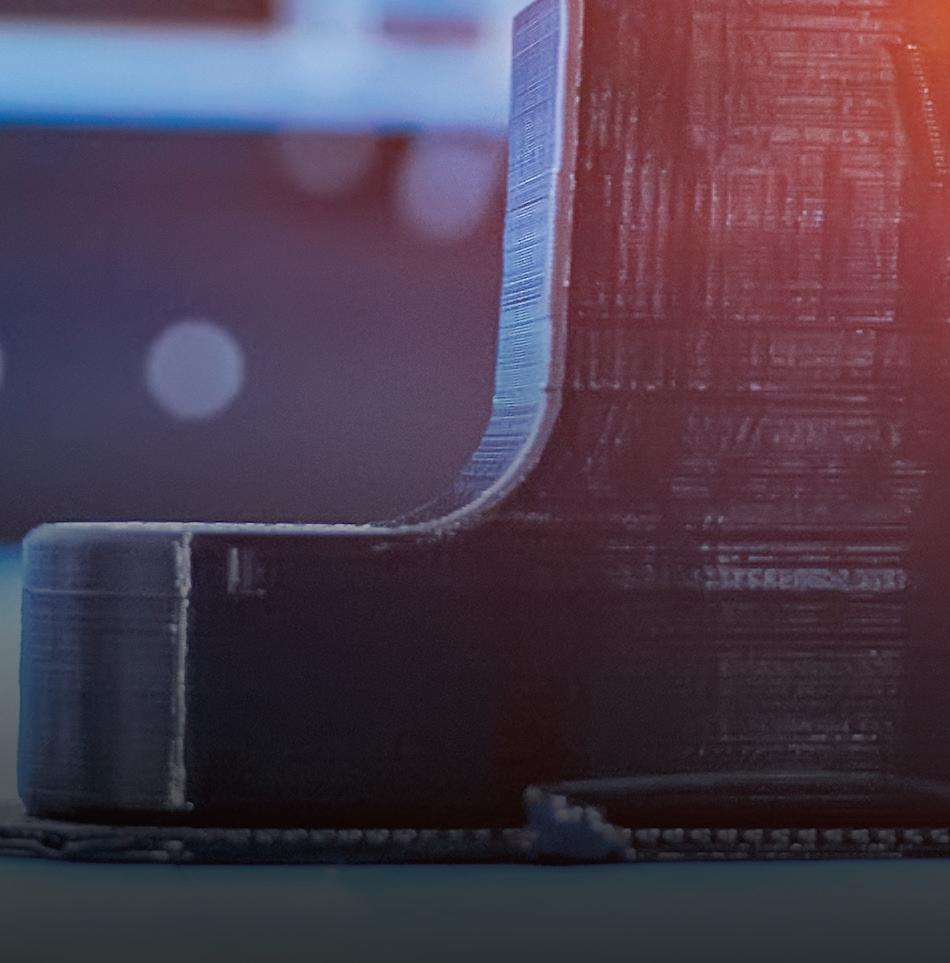
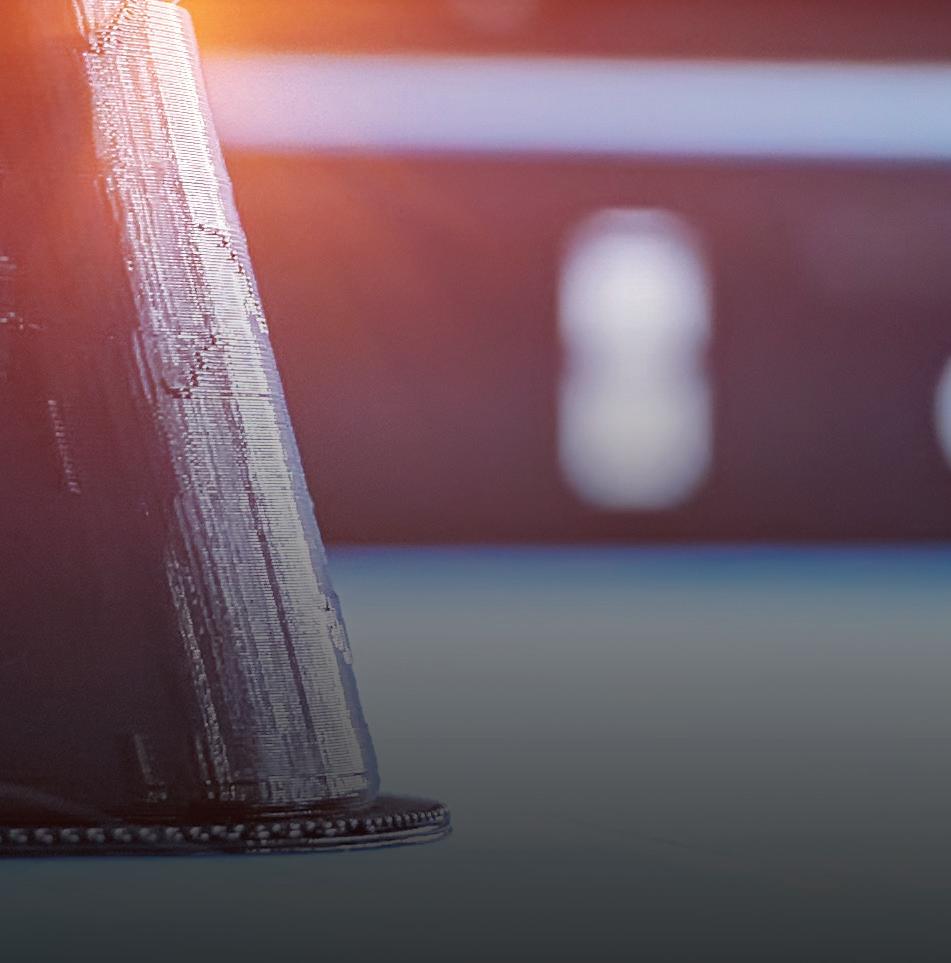
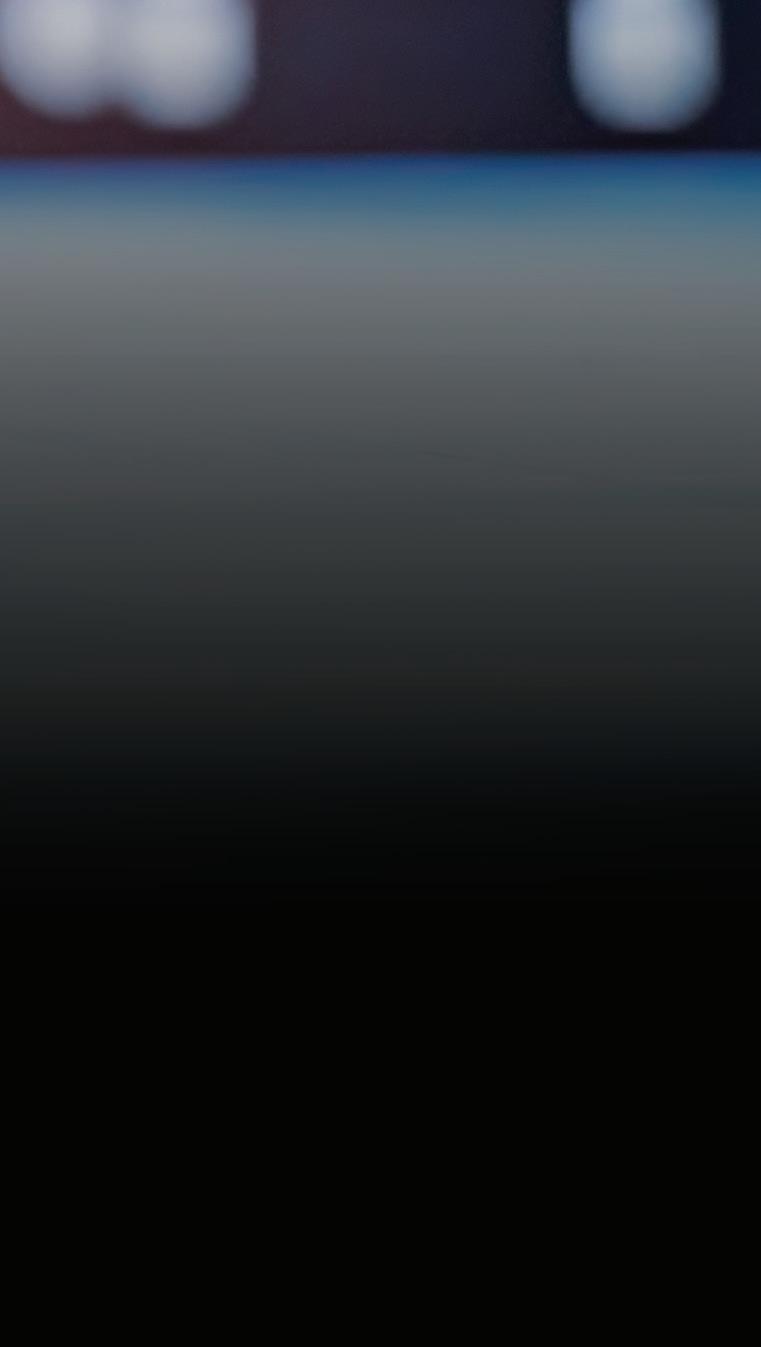
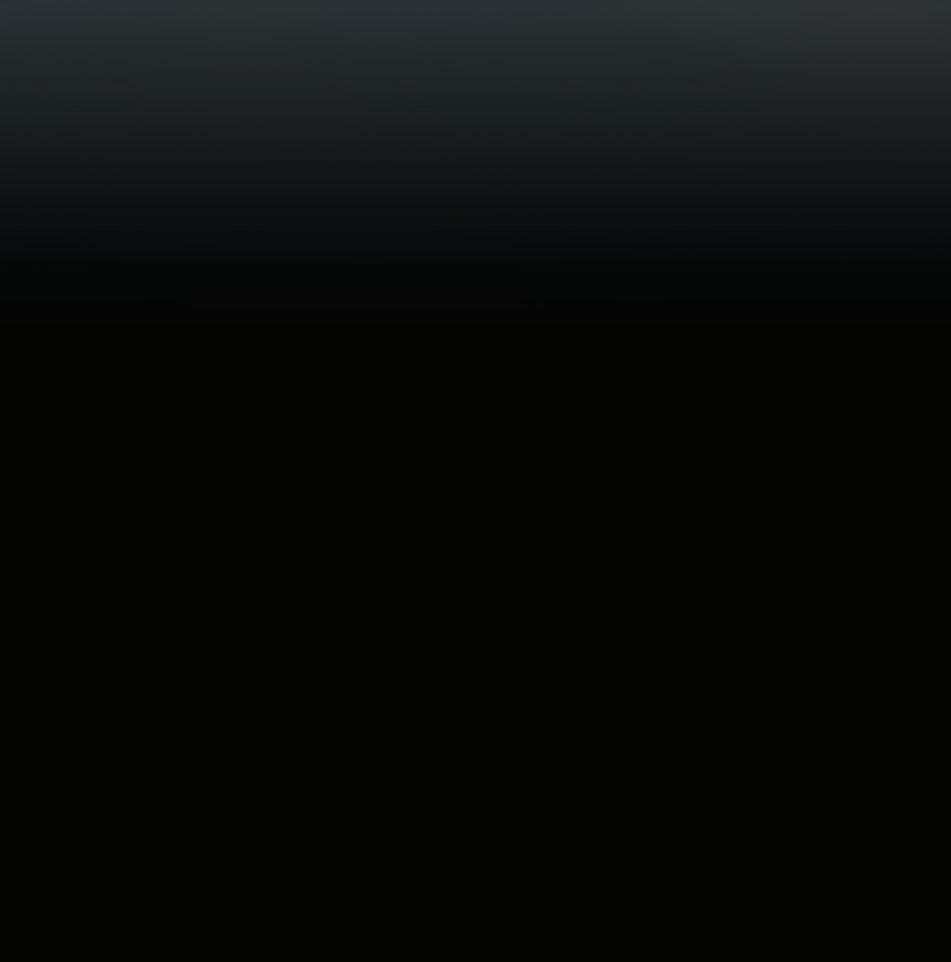
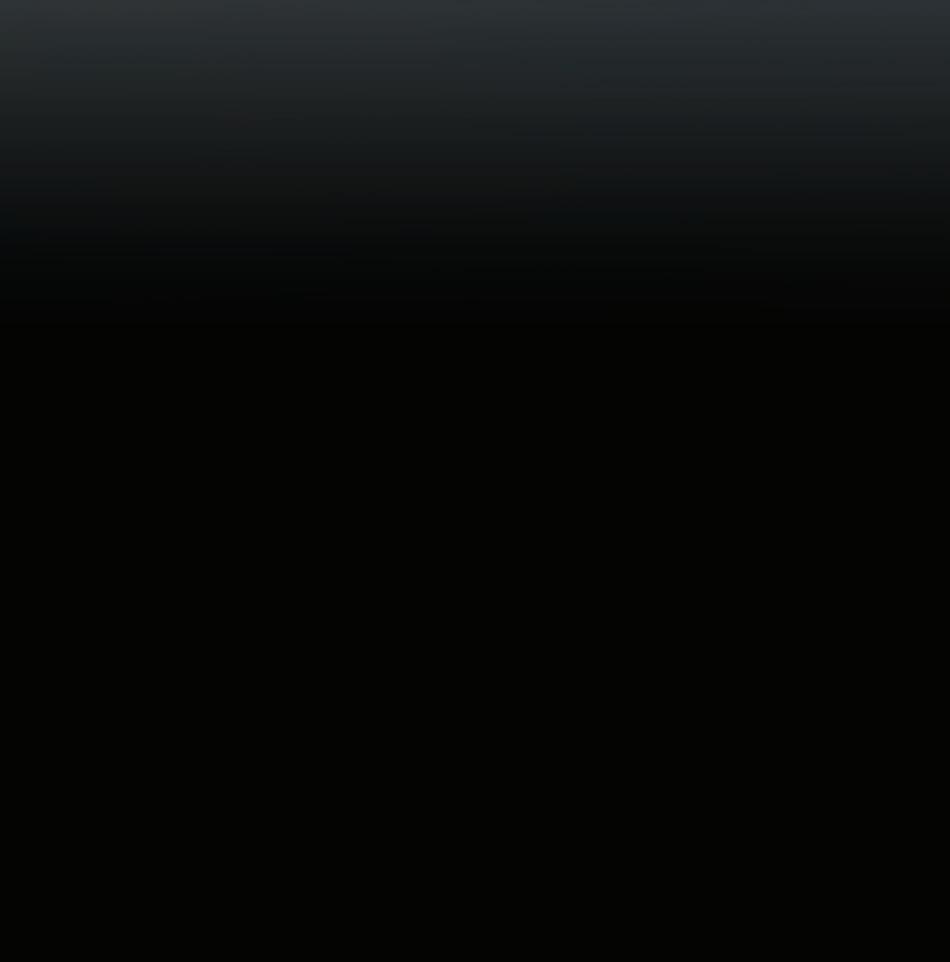
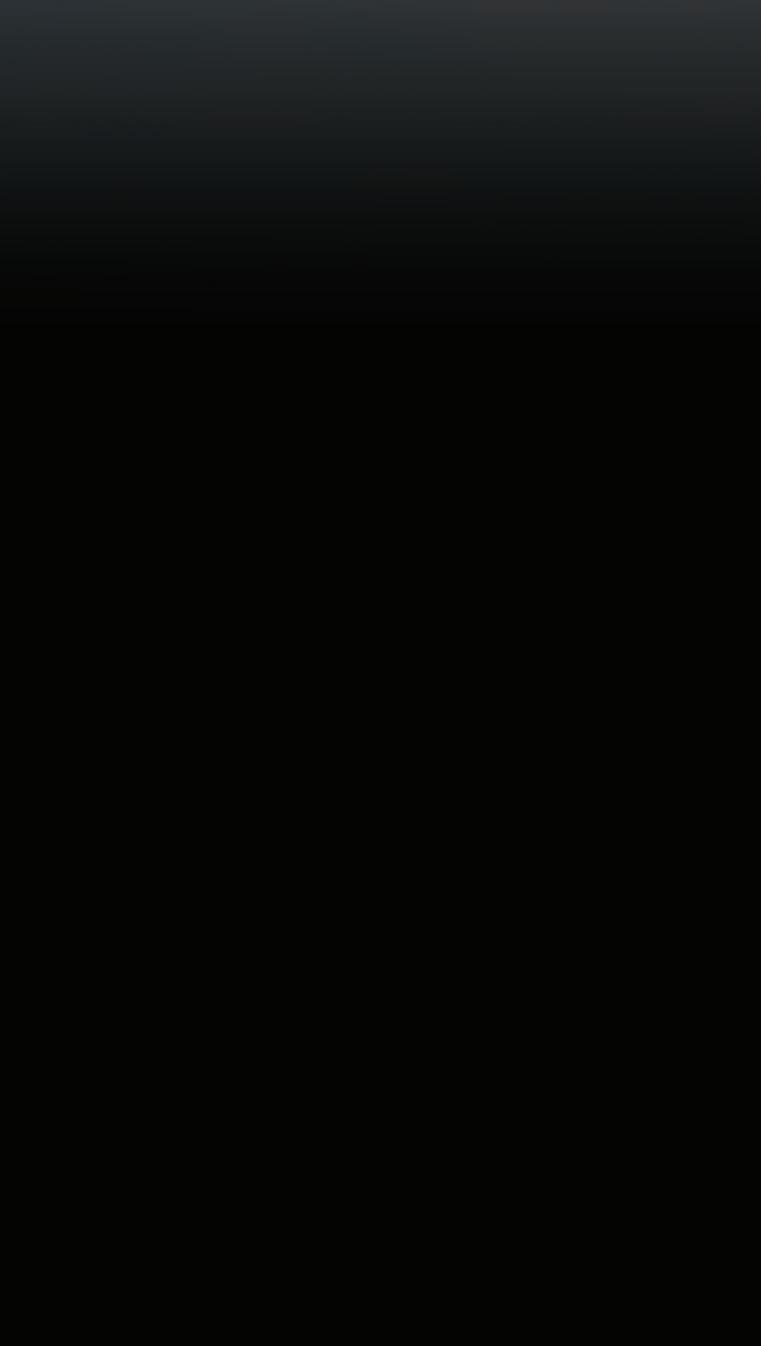
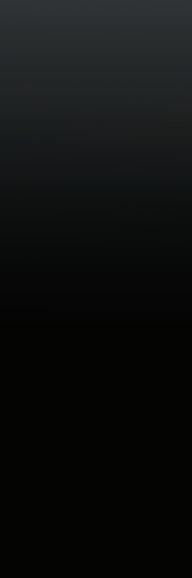
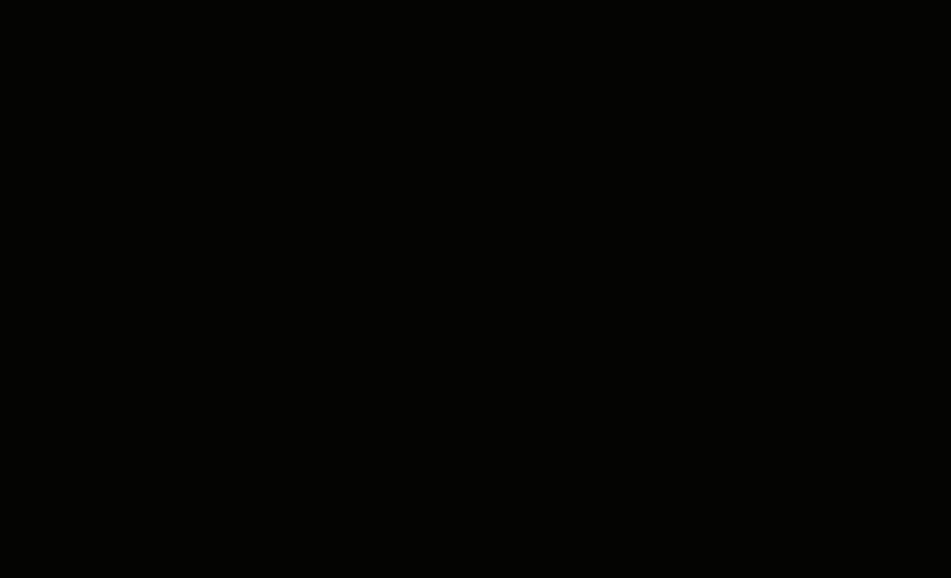
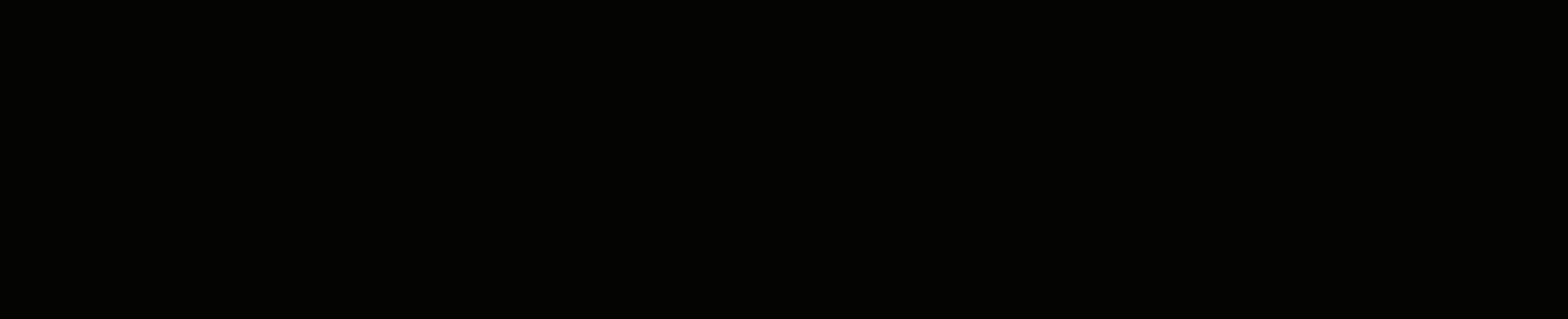
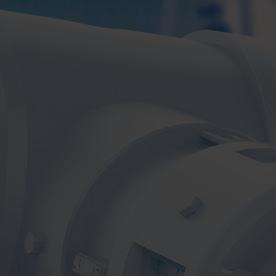
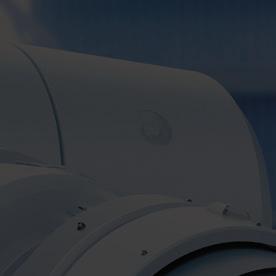
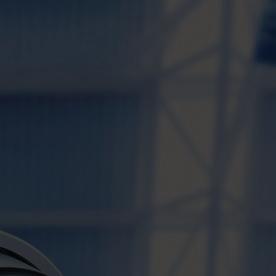
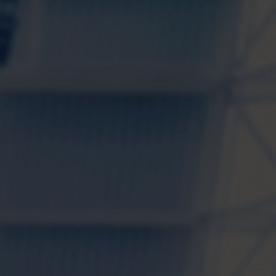
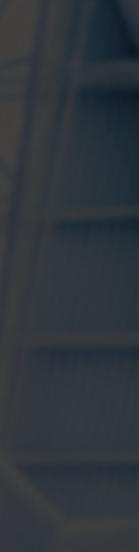
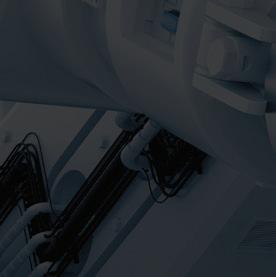
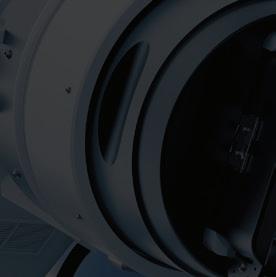
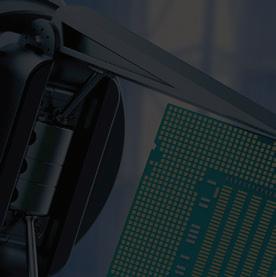
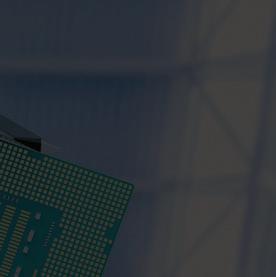
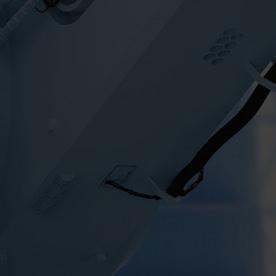
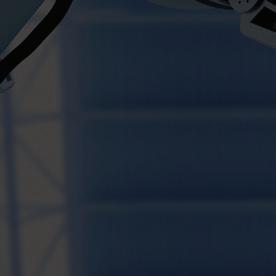
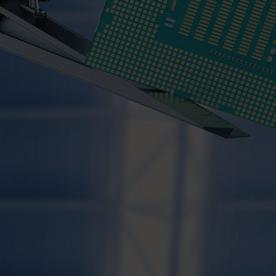
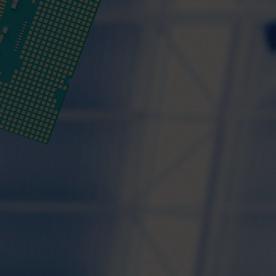
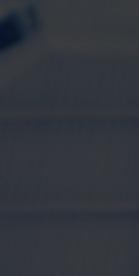
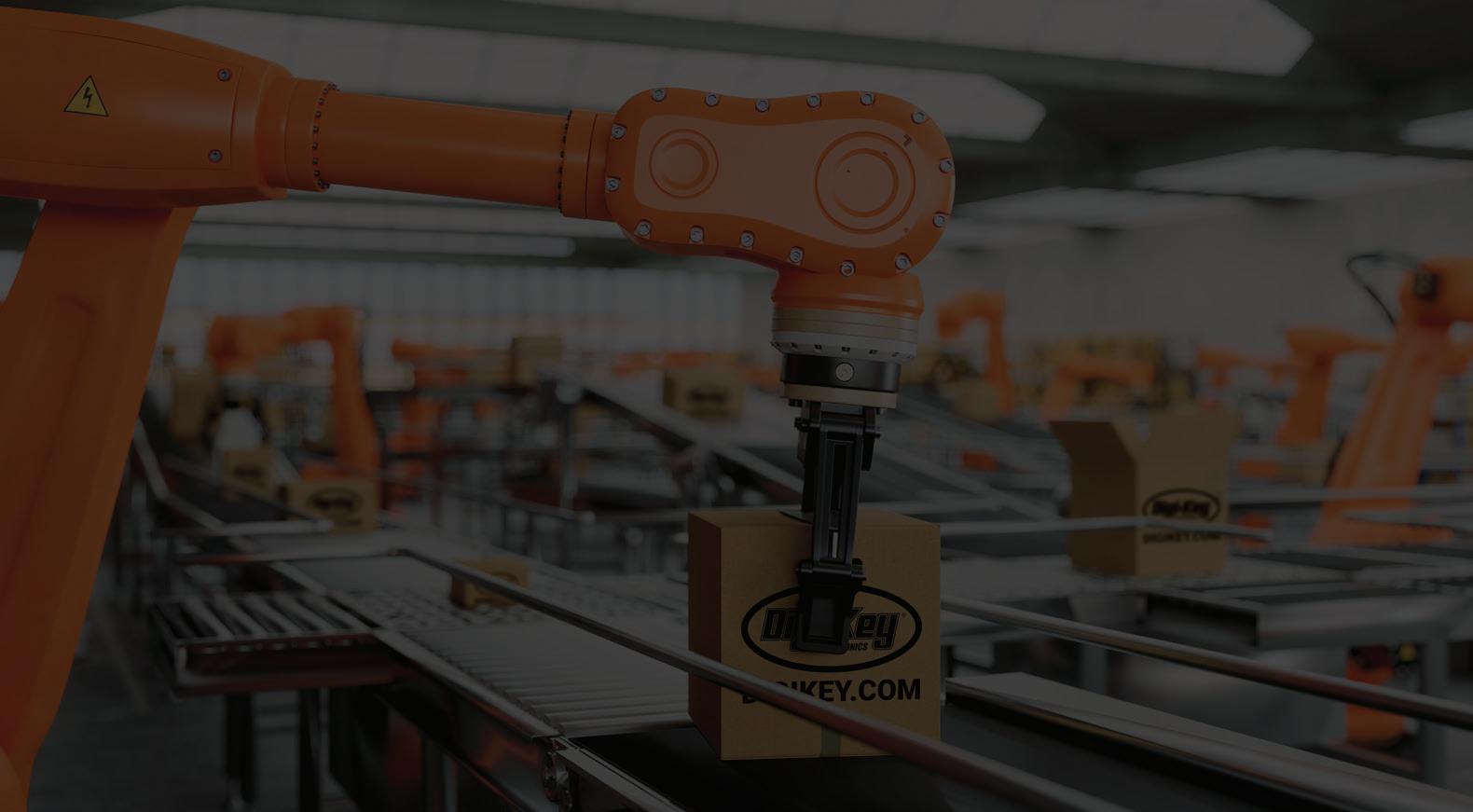

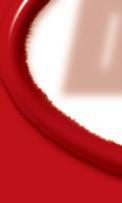
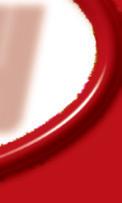
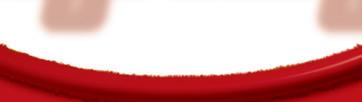
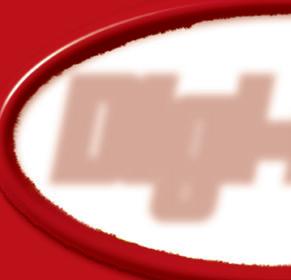
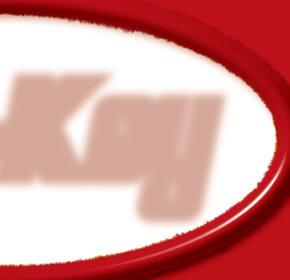
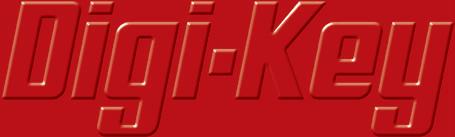
Today’s electronic engineers are challenged by multiple factors. Research over the years has illustrated common trends that you, as engineers, deal with including keeping your skills up-to-date, shrinking time-to-market windows, fewer engineers and smaller design teams for large projects and evolving technological trends. The bottom line is that you must continually update your engineering knowledge base to be successful in your work.
Throughout 2023, we are presenting a series of online educational days where you can learn how to address specific design challenges, learn about new techniques, or just brush up your engineering skills. We are o ering eight di erent Training Days. Each day will focus on a helping you address a specific design challenge or problem. These are not company sales pitches! The focus is on helping you with your work.
AVAILABLE ON DEMAND
THERMAL MANAGEMENT
MAY 3RD
EMI/RFI/EMC
JUNE 14TH
DESIGNING FOR SUSTAINABILITY
AUGUST 9TH
BATTERY MANAGEMENT
SEPTEMBER 13TH
MOTOR DRIVES DESIGN
OCTOBER 11TH
IOT DESIGN / WIRELESS
NOVEMBER 8TH
ELECTRIC VEHICLE DESIGN
DECEMBER 6TH 5G / RF DESIGN
For more information and to register for these webinars, go to:
Perhapsyou see the connection between origami and the IoT right away. It only occurred to me while watching a documentary the other night, opening my mind further to the symbiotic relationship between art and science.
The film “Between the Folds, The Science of Art, The Art of Science,” a 2008 documentary about origami, seems as far removed from 27 billion connected IoT devices (by 2025) as that 27 billion number appears to be from reality. The paper points connected the lines with such elegant purpose. While maybe not necessarily as elegant, I was reminded of the iconic graphic representations of the IoT — electrified lines moving from point to point around the globe.
In addition to the professional origami master artists profiled, the director also treated us to the several scientists and mathematicians who had taken up the art form. One hyperrealist walked away from a successful physics career to challenge the physics of a folded piece of paper. I read another profile of an advanced mathematician and scientist who received a MacArthur Genius Award for computational origami research. I was fascinated by the mathematical tools resulting in folds fashioned into elaborate sculptures. Additionally, origami’s physical structure has consistently inspired innovation in engineering, from better heart stents to foldable equipment at NASA to the Kresling-Inspired Mechanical Switch (KIMS) that has the potential to introduce a new class of memory devices.
After watching the film, I asked my Japanese friend, an executive with a company providing AI operations tools for IT and DevOps teams, what is it about those billions of connected devices of the IoT that makes me think about origami?
She took about two minutes to nail it.
“IoT made previously invisible and unmeasurable things datapoints, just like you create points with previously flat paper,” she said. “And these data points and paper points connect different dimensions, and something new emerges, whether a new insight or a new three-dimensional shape.”
It’s true. I learned that origami evolved and became more complex with more folds, points, and creases, elevating to an art form along the way. Rather than following instructions to create the same things, origami artists are creating new, one-of-a-kind pieces. Now think of how products are traditionally made — with uniform configurations, which the user then adapts to the design and intent of the product. We shaped ourselves into a pre-defined piece. With IoT and the added layer of AI, we can now create one-of-a-kind pieces, just like that art origami. We aren’t limited to the original intent of a product. We make it our own. Whether it is quantum computing giving artists a new way to envision the world or the origami of the Internet of Things, art and science are more innovative together than apart. Those billions of connected devices may indeed make every “thing” smarter. What we can create, envision, and dream of because of the massive amount of data communicated between the points is what will allow us to sculpt our world intelligently.
Aimee Kalnoskas Editor-in-Chief02 The Origami of the Internet of Things
06 What are emerging sensor technologies for Agriculture 4.0? Agriculture 4.0 is emerging and requires an expanded sensor suite.
09 Edge computing security: challenges and techniques
Addressing security for edge devices from the beginning must be an integral part of the design process.
12 How does the PICMG IoT.1 specification for smart IoT sensors work?
The recently released IoT.1 speci cation de nes a rmware interface and low-level data model providing vendorindependent con guration of smart sensors and e ectors.
17 Private 5G networks unlock IoT applications
As more industries rely on wireless devices, sensors, and arti cial intelligence to connect people and machines, private networks bring the potential to enable more advanced IoT applications while increasing security, bandwidth, and speed.
20 Flexible connectivity lets IoT flourish
Designers have choices when it comes to creating new IoT designs; connectivity choices depend on the design’s constraints. As with any engineering decision, the learning curve and time-to-market constraints can dictate OEMing an existing solution to the problem.
24 Single-Pair Ethernet: simplifying your Ethernet connectivity from sensor to cloud
A physical layer for Industrial Ethernet, Single-Pair Ethernet combines high data rates with a lightweight cable design, streamlining communication across automation levels.
28 Test tool simplifies and automates LoRaWAN certification
LoRaWAN certi cation is the solution for successfully scaling long-range, low-power end devices for IoT. The LoRaWAN certi cation test tool (LCTT) accelerates time to market through test automation.
32 The future of PCBs in the world driven by IoT
The traditional PCB design methods may not support the functionalities o ered by an IoT product.
34 How does Matter work as middlewarefor IoT devices?
Matter has been called an interoperable application layer solution. The Connectivity Standards Alliance, the same source that oversees the development of Matter, refers to it as a protocol.
37 IoT: how 5G differs from LTE
5G extends its scope beyond consumer to many new vertical and enterprise markets. Thanks to its exibility and improved performance, 5G opens the door to many industrial applications.
EDITORIAL
VP, Editorial Director
Paul J. Heney pheney@wtwhmedia.com @wtwh_paulheney
Editor-in-Chief
Aimee Kalnoskas akalnoskas@wtwhmedia.com @eeworld_aimee
Senior Technical Editor Martin Rowe mrowe@wtwhmedia.com @measurementblue
Associate Editor Emma Lutjen elutjen@wtwhmedia.com
Executive Editor Lisa Eitel leitel@wtwhmedia.com @dw_LisaEitel
Senior Editor Miles Budimir mbudimir@wtwhmedia.com @dw_Motion
Senior Editor Mary Gannon mgannon@wtwhmedia.com @dw_MaryGannon
Managing Editor Mike Santora msantora@wtwhmedia.com @dw_MikeSantora
VIDEOGRAPHY SERVICES
Videographer Garrett McCafferty gmccafferty@wtwhmedia.com
Videographer Kara Singleton ksingleton@wtwhmedia.com
CREATIVE SERVICES & PRINT PRODUCTION
VP, Creative Services Mark Rook mrook@wtwhmedia.com @wtwh_graphics
Senior Art Director Matthew Claney mclaney@wtwhmedia.com @wtwh_designer
Senior Graphic Designer Allison Washko awashko@wtwhmedia.com @wtwh_allison
Graphic Designer Mariel Evans mevans@wtwhmedia.com @wtwh_mariel
Director, Audience Development Bruce Sprague bsprague@wtwhmedia.com
PRODUCTION SERVICES
Customer Service Manager Stephanie Hulett shulett@wtwhmedia.com
Customer Service Representative Tracy Powers tpowers@wtwhmedia.com
Customer Service Representative JoAnn Martin jmartin@wtwhmedia.com
Customer Service Representative
Renee Massey-Linston renee@wtwhmedia.com
Customer Service Representative Trinidy Longgood tlonggood@wtwhmedia.com
MARKETING
VP, Digital Marketing Virginia Goulding vgoulding@wtwhmedia.com @wtwh_virginia
Digital Marketing Coordinator
Francesca Barrett fbarrett@wtwhmedia.com @Francesca_WTWH
Digital Design Manager Samantha King sking@wtwhmedia.com
Marketing Graphic Designer Hannah Bragg hbragg@wtwhmedia.com
Webinar Manager Matt Boblett mboblett@wtwhmedia.com
Webinar Coordinator
Halle Kirsh hkirsh@wtwhmedia.com
Events Manager
Jen Osborne jkolasky@wtwhmedia.com @wtwh_Jen
Events Manager
Brittany Belko bbelko@wtwhmedia.com
Event Marketing Specialist Olivia Zemanek ozemanek@wtwhmedia.com
Event Coordinator Alexis Ferenczy aferenczy@wtwhmedia.com
Web Development Manager B. David Miyares dmiyares@wtwhmedia.com @wtwh_WebDave
Senior Digital Media Manager Patrick Curran pcurran@wtwhmedia.com @wtwhseopatrick
Front End Developer Melissa Annand mannand@wtwhmedia.com
Software Engineer David Bozentka dbozentka@wtwhmedia.com
Digital Production Manager Reggie Hall rhall@wtwhmedia.com
Digital Production Specialist Nicole Lender nlender@wtwhmedia.com
Digital Production Specialist Elise Ondak eondak@wtwhmedia.com
Digital Production Specialist Nicole Johnson njohnson@wtwhmedia.com
FINANCE
Controller Brian Korsberg bkorsberg@wtwhmedia.com
Accounts Receivable Specialist Jamila Milton jmilton@wtwhmedia.com
WTWH Media, LLC
1111 Superior Ave., Suite 2600 Cleveland, OH 44114
Ph: 888.543.2447
FAX: 888.543.2447
DESIGN WORLD does not pass judgment on subjects of controversy nor enter into dispute with or between any individuals or organizations. DESIGN WORLD is also an independent forum for the expression of opinions relevant to industry issues. Letters to the editor and by-lined articles express the views of the author and not necessarily of the publisher or the publication. Every effort is made to provide accurate information; however, publisher assumes no responsibility for accuracy of submitted advertising and editorial information. Non-commissioned articles and news releases cannot be acknowledged. Unsolicited materials cannot be returned nor will this organization assume responsibility for their care.
DESIGN WORLD does not endorse any products, programs or services of advertisers or editorial contributors. Copyright© 2023 by WTWH Media, LLC. No part of this publication may be reproduced in any form or by any means, electronic or mechanical, or by recording, or by any information storage or retrieval system, without written permission from the publisher.
SUBSCRIPTION RATES: Free and controlled circulation to qualified subscribers. Non-qualified persons may subscribe at the following rates: U.S. and possessions: 1 year: $125; 2 years: $200; 3 years: $275; Canadian and foreign, 1 year: $195; only US funds are accepted. Single copies $15 each. Subscriptions are prepaid, and check or money orders only.
SUBSCRIBER SERVICES: To order a subscription or change your address, please email: designworld@omeda.com, or visit our web site at www.designworldonline.com
POSTMASTER: Send address changes to: Design World, 1111 Superior Ave., Suite 2600, Cleveland, OH 44114
refers to systems that employ drones, robotics, the Internet of Things (IoT), vertical farms, artificial intelligence (AI), renewable energy, and advanced sensor methodologies. Agriculture 4.0 is similar to Industry 4.0 in some ways: where Industry 4.0 is designed to support automation and mass customization of production processes, Agriculture 4.0 is expected to support autonomous operations and mass customization of farming practices across microenvironments.
Integrating digital technologies into farming, agricultural operations can target resources needed to increase yields, reduce costs, and minimize crop damage, water, fuel, and fertilizer usage. This FAQ looks at sensor technologies under development for Agriculture 4.0, including wearables for plants and hyperspectral imaging, the EU’s Agricultural Interoperability and Analysis System program, and the security challenges related to wireless sensor networks and the Internet of Things in Agriculture 4.0.
Graphene and fiber optics are two technologies used to develop wearable sensors for plants. Graphene sensors can measure the time it takes for different crops to move water from the roots to the lower and upper leaves. Initially, researchers are using these sensors to help develop plants that use water more efficiently. In the longer term, these graphene sensors on tape (also referred to as ‘plant tattoos’) are expected to support the design of inexpensive, high-performance sensors for Agriculture 4.0 applications (Figure 1) and help improve the efficiency of irrigation systems. The process used to make the sensors can produce devices that are several millimeters across with features as small as 5 μm. The small feature sizes increase the sensitivity of the sensors. The conductivity of the graphene oxide in these sensors changes in the presence of water vapor, enabling the measurement of transpiration (the release of water vapor) from a leaf.
Fiber Bragg grating (FBG) sensing technology is also being developed for agricultural applications. An FBG acts as a notch filter that reflects a narrow portion of light centered around the Bragg wavelength (λB) when illuminated by a broad light spectrum. It’s fabricated as a microstructure inscribed into the core of an optical fiber. Unlike graphene sensors, which are an emerging technology, FBG
sensors are already in use in several areas, including aerospace, civil engineering, and human health monitoring. FBG sensors can be fabricated with high sensitivities, small size, and lightweight. In the case of agricultural sensors, the intrinsic sensitivity to strain (ε) and temperature variations (ΔT) of FBG technology is being combined with a moisture-activated polymer to detect relative humidity changes (ΔRH) in the surrounding air. In addition, FBG sensors can be multiplexed to support the monitoring of both plant growth and environmental conditions in a single device. The FBG designed for agricultural applications consists of three segments, one for ε sensing, one for ΔRH monitoring, and a third optimized for ΔT measurements. It was fabricated using a commercial FBG with a grating length of 10 mm, λB of 1533 nm, with a stretchable acrylate coating. The coating protects the FBG and improves its adherence to the plant’s stem.
Multispectral imaging is an established agricultural sensing technology. It can detect subtle changes in plant health before visible symptoms are apparent. For example, a drop in a plant’s chlorophyll content can be detected before the leaves are visibly yellow. Multispectral sensors use the 712 to 722 nm wavelengths (the red edge band) where
indications of stress are most easily identified. Multispectral imaging can be implemented using fixed installations where the sensors travel back and forth on a track system in a greenhouse or across an open field. They are also well suited to be carried aloft on a drone. For example, in one configuration, a drone-based multispectral imaging system can scan a 100-acre field (at 400 feet above the found with a 70% overlap) in less than 30 minutes (Figure 2). Some of the benefits of multispectral imaging include:
• Early disease detection
• Improved irrigation and water management
• Quicker and more accurate plant counting to optimize fertilizer application and pest control
• Cost reductions from the automation of activities previously performed by walking the fields
The primary difference between today’s multispectral sensors and emerging hyperspectral sensors is the bandwidth (the number of bands and how narrow the bands are) used to represent the data of the electromagnetic spectrum. Multispectral imagery generally uses 3 to 10 bands to cover the relevant spectrum. Hyperspectral imagery consists of hundreds or thousands of narrower bands (10 to 20 nm), providing greater
resolution and covering a broader spectrum range. Spectral resolution, or the ability to capture a large number of narrow spectral bands, is an important feature of hyperspectral imaging compared with multispectral imaging.
Other advantages of hyperspectral imaging include:
• Higher spatial resolution and the ability to discriminate smaller features,
• Higher temporal resolution and the ability to quickly sense important environmental changes such as the need for irrigation
• Higher radiometric sensitivity and the ability to discern small differences in radiated energy
Hyperspectral imaging sensors provide a highly detailed electromagnetic spectrum of agricultural fields, making it a useful tool for detecting smaller and more localized variations in important soil attributes and degradation, as well as changes in crop health and fitness. The increasing use of sensors in Agriculture 4.0 and the addition of higher resolution sensors such as hyperspectral imaging is driving the use of big data, and raising concerns related to data security, data integrity, and privacy. Addressing those concerns is a major emphasis for the EU’s ATLAS program.
The EU-funded Agricultural Interoperability and Analysis System (ATLAS) project aims to develop an open platform to support innovation and Agriculture 4.0. ATLAS is one of the EU’s Horizon 2020 research and innovation programs. The Fraunhofer Society is managing the project. It addresses the current lack of data interoperability in agriculture by combining agricultural equipment with sensor systems and data analysis. The resulting platform is expected to support the integration of hardware and software interoperability from a wide variety of sensor systems and amplify the benefits of digital agriculture. ATLAS aims to develop an open interoperability network for agricultural applications and build a sustainable ecosystem for innovative datadriven agriculture (Figure 3). ATLAS is building on networks of in-the-field sensors and multisensor systems to provide the big data needed to realize Agriculture 4.0.
The ATLAS platform is expected to support the flexible combination of agricultural machinery, sensor systems, and data analysis tools to overcome the current lack of interoperability and enable farmers to sustainably increase their productivity by using the most advanced digital technology and data. ATLAS will also define layers of hardware and software to allow the acquisition and share data from a multitude of sensors, as well as the analysis of this data using a variety of dedicated analysis approaches. The program will demonstrate the benefits of Agriculture 4.0 through a series of pilot studies across the agricultural value chain and end by defining the next generation of standards needed to continue the growing adoption of data-driven architecture.
Wireless sensor networks and security Wireless Sensor Networks (WSNs) and Internet of Things (IoT) solutions are extensively used in Agriculture 4.0, providing numerous benefits to farmers. The interconnection among diverse sensors and network devices, however, can contain unpatched or outdated firmware or software, creates opportunities for network insecurities, and opens various attack vectors, including device attacks, data attacks, privacy attacks, network attacks, and so on.
The increasing use of automation and even autonomous operations to improve yields also raises safety concerns. Additionally to ATLAS, the European Union’s Horizon
2020 research and innovation programs focus on developing network traffic monitoring and classification tools for use in Agriculture 4.0 systems. Effective traffic monitoring is expected to play an essential role in protecting assistants and users from the impacts of network attacks. Network traffic analysis and classification tools are being developed for Agriculture 4.0 based on Machine Learning (ML) methodologies to help mitigate the threats to WSNs and other IoTconnected assets.
Summary
The deployment of Agriculture 4.0 relies on the increasing use of WSNs to improve yields and reduce costs for farmers. It also requires the development of new sensor modalities, such as plant wearables using graphenebased and FBG sensors, and the expansion of existing sensor modalities, such as the move from multispectral to hyperspectral imaging. The EU’s ATLAS program is designed to improve interoperability and realize the maximum benefit from the growing diversity of sensor and data analysis technologies. Improvements in network security will also be essential to ensure data security, integrity, and privacy in Agriculture 4.0.
References:
5 Ways to Use Multispectral Imagery in Agriculture, Coptrz. https://coptrz.com/14-waysto-use-multispectral-imagery-in-agriculture/
Advances in hyperspectral sensing in agriculture, Special Agriculture 4.0. https://www.scielo.br/j/rca/a/ vQYBDCJn5xz4BgQDVjyGMVf/?format =pdf&lang=en
Agriculture 4.0 and Smart Sensors. The Scientific Evolution of Digital Agriculture: Challenges and Opportunities, MDPI sensors. https://www.preprints.org/ manuscript/202105.0758/v1/download
ATLAS, Agricultural Interoperability and Analysis System, ATLAS. https://www. atlas-h2020.eu/objectives/
Engineers make wearable sensors for plants, enabling measurements of water use in crops, Iowa State University. https://www.news.iastate. edu/news/2018/01/03/planttattoosensors
Plant Wearable Sensors Based on FBG Technology for Growth and Microclimate Monitoring, MDPI sensors. https://www.ncbi. nlm.nih.gov/pmc/articles/PMC8512323/pdf/ sensors-21-06327.pdf
Precision Agriculture Technologies and Factors Affecting Their Adoption, US Department of Agriculture. https://www.ers. usda.gov/amber-waves/2016/december/ precision-agriculture-technologies-andfactors-affecting-their-adoption/
connected world, a growing number of applications depend on embedded devices; collecting and acting upon data from a wide range of physical processes. As the computing power of the Systems-on-Chip (SoC) at the heart of these devices continues to grow, more decision-making is devolved from the cloud to the edge, turning this rapidly increasing number of edge devices into attractive targets for attackers.
The vulnerability of the IoT is, therefore, a growing concern. Data transmitted to the cloud needs protection, and commands received from remote services need validation. Additionally, while services deployed in the cloud benefit from highsecurity data center infrastructure, edge devices are installed in many different locations, where physical protection methods can be limited.
Security is, consequently, a fundamental property of the edge device, and developers must design security from the outset. The fundamental network security concepts of data in transit, data at rest, and access control mechanisms apply equally to the security of edge devices. However, additional protection measures and a level of intrusion detection capability are required because of their physical locations. These requirements must be built into MCU designs by hardware capabilities such as root of trust (RoT), tamper detection, secure boot, and secure enclaves coupled with advanced software mitigation techniques.
Both functional and platform security primitives are deployed in the security of edge devices. Functional security measures keep sensitive data secure and private. For example, by encrypting messages passed between two edge devices. Platform security primitives protect the implementation of functional security measures from remote or local attackers. The protection of the secret key used to encrypt and decrypt the messages passing between edge devices is an example of platform security.
Both types of security measures employ cryptographic features to provide one or more of the following capabilities in a system:
• Integrity — the data received is identical to the data sent
• Confidentiality — a third party cannot understand the message being communicated
• Authenticity — the authenticity of the message can be verified by the recipient
• Nonrepudiation — the sender cannot deny having sent the message
Cryptographic features and key management techniques enable the protection of in-transit and at-rest data, ensuring that the edge booting device is running authentic authorized firmware and software. A unique identity can also be created for the edge device, enabling a corrupt device to be identified and isolated.
The most commonly used cryptographic features and their applications are illustrated in Table 1.
Addressing security for edge devices from the beginning must be an integral part of the design process.
Advanced security measures require significant processing capabilities; SoC developers employ various hardware and software techniques to optimize chip performance while managing power consumption.
Microprocessor units (MPUs), with hardware acceleration, and hardware random number generation capabilities (figure 1.) offload the computational overheads of the security features, either to an extension of the main processor or to a purpose-built co-processor or core. NXP’s i.MX product family, as an example, includes specific hardware for cryptographic computation acceleration — the Cryptographic Accelerator and Assurance Module (CAAM). The CAAM also offers a unique key-wrapping mechanism protecting sensitive keys from being exposed to attackers.
As separate processors within the MPU, hardware accelerators are also effective isolation devices. The isolation of storage and processing of sensitive information is a common secure mitigation technique, and multicore MPUs offer effective isolation capabilities. With its own processing unit and local memory, the accelerator’s resources cannot be accessed by the other cores in the MPU, providing isolation capabilities to the system while not compromising the overall system performance.
The architectures of many modern edge devices enable the implementation of public key infrastructures (PKI) for edge computing. A third party certifies the binding between public keys, entities, individuals, and/ or organizations using a digital certificate in a PKI. The security features of the more advanced SoCs found in edge devices enable them to act as the third party in a PKI.
Other key security implementation techniques used in edge devices include:
Secure boot: chain of trust
A secure boot implementation guarantees that genuine, trusted binaries run on the system by starting from an
immutable memory within the SoC. The immutable part of the SoC and its features are also referred to as a root of trust (RoT), and specialized hardware security modules (HSMs) are often used to manage and protect the private key associated with RoT. An example of a secure boot implementation can be seen in many of the NXP i.MX range of applications processors, which use a mechanism called high assurance boot (HAB), shown in figure 2.
Trusted execution environment
A trusted execution environment (TEE) is a safe zone within an application processor, enabling separate execution of safe, trusted software from software with vulnerabilities such as large operating systems. Hardware vendors support TEE by including hardware extensions in their MPU designs, with examples including Intel SGX9, AMD Secure Encryption Virtualization (SEV)10, and Arm® TrustZone®11.
Virtualization clusters the applications performed by the edge device into virtual machines (VMs) executed by a hypervisor that also manages resource sharing among the virtual machines. If an attack compromises a VM, the other VMs will be unaffected, assuming that the hypervisor is not affected. There are several methods of implementing virtualization, including using a XEN hypervisor or a “docker” implementation. Additionally, modern SoCs provide hardware support for virtualization, the most common being memory management, which ensures secure memory partitioning.
Software architectures unlock the power of hardware in the implementation of security measures. Figure 3 shows an example of an edge device software stack that uses Arm TrustZone to provide two execution environments. The non-secure environment runs the rich Linux OS, while the
secure environment runs the open, portable OP-TEE software. Trusted applications in the open software offer cryptographic features to the Linux OS by using API access to core functionalities such as cryptographic, key, and storage operations. Those functions can be accelerated in hardware using the CAAM hardware on NXP i.MX devices.
Security should not be an afterthought
Security must be considered from day zero of an edge device’s development. Although the correct implementation of security is a complex and challenging task, the sooner it is addressed, the higher the chances that the end device will be fit for purpose — at a cost that does not threaten project viability.
The recently released IoT.1 specification defines a firmware interface and low-level data model providing vendor-independent configuration of smart sensors and effectors.
ThePCI Industrial Computer Manufacturer’s Group (PICMG) is developing a series of specifications to enable plug-and-play interoperability of smart sensors and effectors. The effort includes the large installed base of legacy non-IoT (not IP-enabled) devices and newer IoT-enabled smart sensors. The PICMG program includes the development of a family of three IoT specifications. PICMG IoT.1 is the second of those standards.
This FAQ presents an overview of PICMG IoT.1, looks at the previously released PICMG IoT.0 standard, and reviews the progress toward the third and final standard in the series, PICMG IoT.2.
IoT.1 supports sensing and motion
control needed in many emerging Industry 4.0 applications. It defines a firmware interface and low-level data model providing vendor-independent configuration of smart sensors and effectors, as well as plug-andplay interoperability with higher levels of the installation. Before IoT.1, PICMG addressed the lowest level of the hierarchy where the physical sensors and actuators of the factory equipment exist. Each of these devices may or may not be IoT-enabled, so PICMG developed IoT.0 (also called MicroSAM) to address the issue of hardware interoperability (Figure 1). The IoT.1 specification is a joint effort between PICMG and the Distributed Management Task Force (DMTF) organization. To more thoroughly address the needs of Industry 4.0, IoT.1 leverages and extends DFTF’s Platform Level Data Model (PLDM) specification. PLDM is a low-level messaging system that supports topologies, eventing, discovery, and runs over a variety of system-
level buses such as I2C/SMBus and PCIe Vendor-Defined Message (VDM) over Management Component Transport Protocol (MCTP) or Reduced Media Independent Interface (RMII) based transport (RBT) over Network Controller Sideband Interface (NC-SI), and others. Benefits of IoT.1 include:
• Enabling the production of smart sensors based on control circuits and software from PICMG-compliant suppliers.
• Enabling the interoperability of smart sensors and smart sensor components from various makers.
• Enabling integrators of sensors and smart effectors to use devices and controllers from multiple suppliers.
• Speeding the adoption of smart sensor technologies in Industry 4.0 through open specifications that ensure interoperability
The Micro Sensor Adapter Module (MicroSAM) is a compact computing module developed specifically to meet the needs of sensor-domain control in the Industrial Internet of Things (IIoT) and Industry 4.0. MicroSAM was the first IoT specification from PICMG; it was developed to solve the challenge of integrating non-IoT devices. MicroSAM is a 32 mm x 32 mm low-power microcontroller board that allows non-IIoTenabled devices to interact with an IIoT gateway in a plug-and-play manner. The introduction of MicroSAM filled a need not addressed by other PICMG specifications; a module designed for use with MCUs in the sensor domain. It’s optimized for processing performance and I/O connectivity for that purpose. Additionally, MicroSAM can be used with other PICMG devices such as MicroTCA, COM Express, or CompactPCI Serial, which provide higher layers of control, while MicroSAM provides sensor-optimized connectivity.
Figure 2. MicroSAM modules are designed to support the PICMG sensor domain data model and network architecture. Image courtesy of CNX Software
MicroSAM co-exists with and extends the existing ecosystem by offering a standards-based solution designed specifically for embedded use in Industry 4.0 applications. The basic features offered by MicroSAM are:
• Industrial operating temperature range from -40 to +85 °C
• Industrial-grade power filtering and signal conditioning for embedded installations
• RS422 communications
• Direct connectivity to analog voltage, analog current, and digital sensors
• Secure connectivity using latching connectors
• Pulse width modulation (PWM) output for motion control applications
• Synchronization using hardware interlock and trigger signals
• Compact (32 mm x 32 mm)
When combined with the PICMG sensor-domain data model and network architecture and data model, sensors connected to MicroSAM modules seamlessly integrate into the network with plug-and-play interoperability (Figure 2).
Coming soon: PICMG IoT.2
The PICMG IoT.2 network architecture specification is expected to be ratified later this year. It defines the integration of smart sensors and effectors, as well as their data, into larger Industry 4.0 systems of systems. IoT.2 is based on DMTF’s Redfish API and outlines an abstraction layer and transactional model so that sensor and effecter endpoints can be monitored and managed in the context of job models similar to those available from cloud service providers. When used together, IoT.1 and IoT.2 are intended to
support the analytics required for higher productivity levels and throughput across a factory environment (Figure 3).
• 1 provides low-level visibility of physical device parameters that can directly impact the quality and efficiency of your production line
• 2 provides an IT-like interface for managing both machines and jobs at a high level of abstraction.
To support collaboration, the PICMG IoT.2 standard will enable existing IoT communications protocols and models to be converted to maintain compliance with the new specification. The strategic alliance between PICMG and DMFT enables IoT.2 to use RedFish APIs. RedFish is a RESTful (Representational State Transfer) interface for the remote management of a platform. REST is simple, well-established, and easily facilitates client and server interactions. RedFish Framework benefits include:
• Easy for machines to parse and generate, and for people to use
• Scalable for use in Industry 4.0 systems of systems
• Re-uses established principles in well-organized formats
• Secure, extensible, and interoperable
The RedFish interface definition includes JavaScript Object Notation (JSON) and the Open Data Protocol (ODATS). ODATS is an ISO/IEC-approved OASIS standard that defines a set of best practices for building and consuming RESTful APIs. The RedFish interface leverages common Internet and web services standards, and its hardware management concept is very similar to PICMG’s Hardware Platform Management (HPM). Building on the RedFish communication protocol, PICMG
expects to add capabilities for motion control such as multicast capability and network time protocol (NTP) clocking. Additional security features will be included before the final release of the PICMG IoT.2 network architecture specification.
Summary
PICMG is developing a series of three specifications to enable plug-and-play interoperability of smart sensors and effectors. The specifications cover the large installed base of legacy non-IPenabled devices and newer IoTenabled smart sensors. The initial PICMG IoT.0 specification was developed to solve the challenge of integrating non-IoT devices. The recently released IoT.1 specification defines a firmware interface and low-level data model providing vendor-independent configuration of smart sensors and effectors designed to support sensing and profiled motion control needed in many emerging Industry 4.0 applications. The stillto-be-released PICMG IoT.2 will complete the effort and defines the integration of smart sensors and effectors, as well as their data, into larger Industry 4.0 systems of systems.
References:
Industrial IoT Overview, PICMG. https://www.picmg.org/industrialiot-overview/
MicroSAM System-on-Module
Standard Targets Microcontrollers, IIoT Sensors, CNX Software. https:// www.cnx-software.com/2020/10/14/ microsam-system-on-modulestandard-targets-microcontrollersiiot-sensors/
PICMG Ratifies IoT.1 Firmware
Specification for Smart IoT connected Sensors and Effecters, PICMG. https://www.picmg.org/ picmg-ratifies-iot-1-firmwarespecification-for-smart-iotconnected-sensors-and-effecters/
Our batteries offer a winning combination: a patented hybrid layer capacitor (HLC) that delivers the high pulses required for two-way wireless communications; the widest temperature range of all; and the lowest self-discharge rate (0.7% per year), enabling our cells to last up to 4 times longer than the competition.
Looking to have your remote wireless device complete a 40-year marathon? Then team up with Tadiran batteries that last a lifetime.
This article is based on an interview with Phil Ware and Sandro Sestan, u-blox.
By Martin Rowean IoT device using a cellular wireless module, there are many factors to consider in minimizing power consumption. Data sheets can provide guidance on power supply design, module placement, and connections. That will get you through the hardware design of your product, but it’s not the whole story. How you use the module makes a difference as well.
“How you use the module,” meaning that protocols make a difference in power consumption. Your goal is to keep the module operating at the lowest possible power level for the maximum amount of time while still achieving the desired performance.
The protocols you use and how you implement them at the application level make a difference in power use. Some power consumption is inevitable regardless of module or protocol because all modules must first connect to the cellular network; they all need to go through the cellular protocol stack. All modules have a boot time and must physically scan for a network in the bands of interest. That time is generally fixed. Once a module is registered on the network, you’re in the application space where your choices make a difference.
Suppose you’ve designed a module into a utility meter. You might use a “fire and forget” protocol that minimizes power consumption by simply sending a meter reading and shutting down the module. That’s the lowest power (and cost) way to send a message. If a reading gets lost, there’s always tomorrow. To accomplish this exchange, simply send a User Datagram Protocol (UDP), Message Queue Telemetry Transport for sensor networks (MQTT-SN), or Constrained Application Protocol (CoAP) message. The application can either shut down the module or use the 3GPP power-saving mode (PSM).
When the application requires an acknowledgment from a server, the module needs to wait for a downlink message. During this time, the radio is still connected, waiting for the ACK message. Some modules use NB-IoT because of low power, but then use “chatty” protocols that take time and use unnecessary power.
As an experiment, we tried using Cat-M1 and NB-IoT modules to send messages of 150 bytes. When sending that amount of data, the NB-IoT module used less power than the Cat-M1 module. Cat-M1 gets more efficient as the number of bytes increases. At 500 bytes and up, lowdata-rate protocols mean your transmitter is on for longer. Cat-M1 modules support ten times the data rate as NB-IoT, and thus are on for less time for a given amount of data.
With the NB-IoT protocol stack, when it re-attaches to the network, the attached message and the customer’s message are all part of the same transmission. Cat-M1 does not yet have these optimizations, and the application messages must travel over the User Data Plane. This is less efficient than sending messages over the Control Data Plane for shorter messages, say less than 200 bytes. The power efficiency crossover seems to occur somewhere between 150 and 200 bytes.
If you look at Lightweight M2M (LwM2M), you’ll see that its protocol is message heavy. Modules must negotiate lots of information with the host. The good news is it has lots of features. The dayto-day operation of an IoT device might not need LwM2M. It can use MQTT-SN or CoAP instead. Figure 1 shows the typical CoAP protocol sequence. Module users can change protocols depending on the application and should take advantage of that option. Keep that in mind when developing application software for your device. Protocol stack libraries are available for that purpose. Clients can be built into modules; you don’t need to develop your own client. There’s no cost in switching protocols. It’s just a matter of sending a few TCP or UDP packets.
3GPP power saving
3GPP specifies power-saving modes. For example, a module could go into listening mode for a specified amount of time before going back into sleep mode, called Extended Discontinuous Reception (eDRX). A module’s powersaving features depend on its chipset, although most implement Release 13/ Release 14 features. In listening mode, a chipset might only consume microamps of current. Some modules don’t need to fully boot when they wake up from sleep mode. Other modules need to boot, which can take four or five seconds when
the module is powered but not sending useful data.
The difference in power consumption from transmit to receive may depend on distance. A short distance to a base station means less transmit power. Receive current could be less than 100 mA but transmit current could be much higher. It depends on the distance to the base. The network defines the transmit power needed by the remote device. For the receiver, the network will determine how often (duty
cycle/C-DRX) the module will listen to the network’s signaling. Figure 2 compares a typical transmit and receive current for a wireless module.
As you can see, the protocols you use can make a difference in your IoT device’s power consumption. Choose your protocols based on data transfer rates and size. The right choices result in lower power use and lower power costs for the final device user.
consumption value depends on TX power and actual antenna load
Whilemajor U.S. telecom operators build their 5G networks, many organizations develop their own networks to take advantage of the next generation of connectivity. Private networks provide complete control of data and critical processes. Typically deployed in one or more specific locations owned or occupied by the end-user organization, private networks reside on premises. Only devices and users that the organization authorizes obtain network access. Figure 1 highlights what private networks can bring to organizations.
By Marco Contento, Telit and Xiaoxia Zhang, QualcommUnlike a public network, a private 5G network lets companies define the network’s capability, deployment timetable, and coverage quality. Configurations can vary by site, depending on the type of work undertaken in each venue, and customized to an organization’s specific location and operational needs. Elements include but are not limited to: Spectrum: organizations have the option to use either shared spectrum such as the general authorized access (GAA) tier of the Citizens Broadband Radio Service (CBRS) band, local-licensed spectrum dedicated to private networks in some countries, reuse licensed spectrum bands from mobile network operators, or use 5G NR in unlicensed bands as has already been standardized and pending commercialization. The GSMA expects mobile network operators (MNOs) to use spectrum from three principal ranges: (1) low-frequency bands (under 1 GHz), (2) mid frequency bands (in the core 3.3 GHz to 3.8 GHz range), and (3) high-frequency bands known as “millimeter wave” (in the 26 GHz, 28 GHz and 40 GHz range).
As more industries rely on wireless devices, sensors, and artificial intelligence to connect people and machines, private networks bring the potential to enable more advanced IoT applications while increasing security, bandwidth, and speed.Figure 1. Private 5G networks promise to connect people, sensors, and machines within factories, universities, ports, farms, and other facilitie. Image courtesy of Qualcomm
A rapidly growing number of countries in Asia, Europe, and North America have spectrum initiatives underway for private networks. Three examples are:
• Germany allocated 100 MHz in the 3.7 GHz to 3.8 GHz band for local and regional 5G networks that can be used for agriculture, forestry, and industrial applications.
• Japan set aside 28.2 GHz to 28.3 GHz for local 5G services and allows private LTE networks to use LTE Band 39 on a shared basis. It’s also considering private 5G allocations in the 4.6 GHz band and between 28.3 GHz to 29.1 GHz.
• The U.S. auctioned 70 MHz between 3.55 GHz and 3.65 GHz.
Core: in addition to spectrum, private 5G wireless networks will require a core, which includes software and hardware that can be acquired from a single or multiple vendor(s), or built with commodity hardware and open-source software. The core is responsible for a range of functions such as traffic shaping and rules for quality of service, billing, and data plans, as well as parameters for network monitoring.
Radios and antennas: private networks need radios and antennas for the CBRS spectrum in the US. These Citizens Broadband Radio Devices (CBSDs) need certification from a CBSD test lab.
Identity management: central to security, the core contains a database of subscribers and manages the subscriber identity module (SIM) cards activated for connection to the private network.
Enterprises can deploy a virtual private mobile network (dedicated network), which
typically uses 5G network slicing over the public mobile network. This affords the enterprise some of the advantages of a private network, minus the upfront cost and complexity involved in installing and operating an on-site wireless infrastructure (Figure 2).
Deloitte predicts that hundreds of thousands of companies in sectors such as retail, healthcare, education, utilities, manufacturing, and transportation will deploy private 5G networks over the next ten years. While these networks have been taking hold in Europe for some time, the 2020 Federal Communications Commission (FCC) auction finally freed up the necessary spectrum for U.S. enterprises, which can now build their own in-house and run it themselves, or outsource it to a mobile network operator (MNO) or systems integrator (SI).
In 2020, a wide range of organizations deployed these networks to address specific challenges and explore new opportunities:
• Germany-based Rohde & Schwarz partnered with Nokia to install a private 5G network at its plant in Teisnach, Germany to test new industrial applications and discover how to best optimize 5G for smart factories.
• Ford and Vodafone partnered to develop a private 5G network in the automaker’s new Electrified Powertrain in Manufacturing Engineering (E:PriME) facility located in Essex, England, with a goal to close the connectivity gap in critical automated processes on the factory floor — like welding, which is used extensively for parts that comprise an electric vehicle — and enable secure connectivity across the entire Ford campus.
British multinational energy and services company Centrica partnered with Vodafone to build the first 5G-ready mobile private network (MPN) for the oil and gas sector at its Easington facility, with a goal to create a digitized ecosystem that enables mission-critical monitoring, control, and communications in real time to improve environmental and worker safety among other things.
• The Belgian Port of Zeebrugge partnered with Nokia to deploy an end-to-end private 5G network to track, analyze and manage connected devices across multiple port-based applications in real time and support the use of autonomous vehicles, augmented reality, and drones.
• AT&T and Samsung deployed a 5G testbed at Samsung’s Austin, Texas manufacturing facility, providing a private 5G network that uses millimeter-wave (mmWave) spectrum and leverages LTE and Wi-Fi. The network also uses multiaccess edge computing (MEC) to keep data processing close to the end user.
• Lufthansa Technik and Vodafone Business built a standalone private 5G campus network at the Lufthansa base at Hamburg Airport in Germany to give the company the freedom to configure the network according to its needs. For example, technicians can now use high-resolution virtual and augmented reality technologies to work even more precisely and securely on the aircraft 24 fuselages.
According to an independent study from IHS Markit commissioned by Qualcomm, 5G will expand the mobile ecosystem to new industries that will result in a $13.1 trillion global economic value by 2035, powering the digital economy, with the support of dedicated private networks, fulfilling targeted needs of organizations in a range of sectors:
• $416B — Precision agriculture
• $984B — Construction and mining
• $264B — Digitized education
• $1,083B — Connected healthcare
• $2,224B — Richer mobile experiences
• $4,771B — Smart manufacturing
• 1,144B — Intelligent retail
• $2,213B — Connected smart cities
Private 5G networks for enterprises bring the potential to exploit new capabilities available in the latest phase of the 5G standard (3GPP Release 16), with enterprises likely to deploy in stages, and an initial focus on seamless mobility. Private 5G networks bring faster and safer operations, new capabilities, and efficiencies in industrial processes. Private networks will also require expertise in network design and management to meet industrial demands on network performance. Industry 4.0 applications have specific demands on communications technology concerning latency, reliability, and security. Thus, we suggest that you begin with test phases that can identify network infrastructure, coverage, and performance issues before a complete rollout.
According to Deloitte, 5G has the potential to become the world’s predominant local area network (LAN) and wide area network (WAN) technology over the next 10 to 20 years, especially in greenfield builds. For industrial users, the ability to design mobile networks to meet the coverage, performance, and security requirements of production-critical applications is fundamental to the new wave of cyber-physical systems ushering in Industry 4.0.
Industrial and enterprise operations will benefit from the rich capabilities of 5G, but cutting the data-collection wires, leading to more sensors for greater observability. By adding edge computing, 5G networks will process that data with low latency. Computeintensive machine learning will efficiently extract valuable insights, thereby reducing the Observe, Orient, Decide, and Act (OODA) loop for industrial processes. Industry 4.0 leaders stand to improve their operational efficiencies, improve their responsiveness to shifts in supply chains or customer demand, and their resilience to disruptive events, all to sharpen their competitive edge with the power of 5G.
• The industry’s lowest DCR and ultra-low AC losses across a wide frequency range
• Wide range of inductance values from 0.27 to 56 µH
• Current ratings up to 117 A with soft saturation
• Drop-in upgrade from our popular XAL1010 Series
Designengineers have choices on every level. Do we buy modules, or boards, or design the functions in-house? Do we use digital or analog signal processing? What microprocessor/microcontroller and architecture do we employ? Every decision has benefits and consequences.
Companies have core competencies in their specialty but often must make decisions regarding a device’s connectivity. As the technological players reshuffle the board, connectivity comes to the front, especially along the network edge. For example, do we use the newest 5G chipsets and go with 5G connectivity, or do we employ a lower-power wireless LAN technology capable of wide-area coverage that can reach all the devices at the edge?
Why all the focus on connectivity?
In a word: money. Wireless carriers charge a fee for every connected device, and the number of IoT devices is growing rapidly. Global wireless carriers needed three decades to reach the current 2.3 billion subscribers.
In the few years that IoT services have been available, more than 8.4 billion IoT devices have been connected. Now, at least 20 billion are connected. Even though not all IoT devices directly connect to the internet, 10 billion of them still create immense annual revenues for service providers. This influx of connectivity can be a huge revenue opportunity. IoT applications, however, have broad differences. The current capabilities of cellular-based and low-power wide-area network (LPWAN) applications differ such that no single standard will satisfy every need.
The choice of connectivity will depend on the constraints of the design. These include, but are not limited to:
• Cost
• Time to market
• Size
• Power
• Range
• Data rates
• Reliability
• Security
• Latency
• Ruggedness
• Expandability
Another factor is the cost burden to customers. If you require every IoT device in a small area to have a cellular connection, the cost of use can skyrocket. By the same token, if you need multiple aggregators and base stations to make your wide-area network function, that can also dissuade customers. Right off the bat, the constraints that your IoT-connected devices are sensitive to will steer your choices.
The cellular industry has unique advantages for IoT. Carriers already have almost ubiquitous LTE coverage in the US delivered by several hundred thousand macro base stations and perhaps three times that many small cells. In most cases, updating this infrastructure to accommodate communication with IoT devices requires just a software upgrade rather than a significant investment in hardware. In addition, even before IoT became the next big thing, wireless carriers provided connectivity to wireless-enabled sensors using 2G technology. Although 2G and 3G services are disappearing, 4G and 5G are available.
The industry has worked for years to accommodate IoT. 3GPP has included substantial specifications dedicated to IoT. Now at release 17, the protocols and standards under its umbrella include GSM 2G and 2.5G standards, UMTS 3G standards, LTE Advanced and LTE Pro 4G standards, 5G NR, and an evolving IP Multimedia Subsystem (IMS) as an access independent medium.
In contrast, low-power wide-area network (LPWAN) providers started with no such advantages. Because they were new entities, they needed to build every system in every area where coverage is desired. They have also had a limited time deploying these networks in key (typically urban) areas, as the cellular industry is rapidly rolling out its IoT-centric data plans. Fortunately, LPWAN systems are less expensive to build and deploy than cellular networks, do not always require leasing space on a tower, and cover wide geographical areas with fewer base stations. They also have the advantage of allowing proprietary solutions that can create the branding of function into the unlicensed RF bands.
Designers have choices when it comes to creating new IoT designs; connectivity choices depend on the design’s constraints. As with any engineering decision, the learning curve and time-to-market constraints can dictate OEMing an existing solution to the problem.Figure 1. The LPWAN standards vary from continent to continent and from country to country. In any case, aggregators and access points will allow internet connectivity regardless of the LPWAN standard used in a specific location. Image courtesy of GSMA
The question persists of whether LPWAN providers can survive in a cellular-dominated world. Most analysts believe they will offer similar capabilities to cellular networks, such as carrier-grade security and other mandatory features. They can become cost-competitive for customers as well. Analysts also suggest that at least half of IoT use cases can be served by LPWANs. It’s a relatively safe bet that, while the cellular industry will have a commanding presence in delivering IoT connectivity, LPWAN providers will still find room in what is likely to become a price war within individual markets.
Three standards seem to be emerging as viable choices for the engineering community at large. The market leaders so far are Long-Range Wide-Area Network (LoRaWAN), Narrowband Internet of Things (NB-IoT), and Long Term Evolution for Machines (LTE-M) standards. Others are, however, clawing their way into the visible ecosystem. LTE-M and NB-IoT have gained a foothold in North America, South America, parts of Europe, and Australia. NB-IoT has gained acceptance in Russia, China, and South Africa. LTE-M is establishing itself in Mexico and parts of Europe. But all are in play anywhere (Figure 1).
For large-scale deployment of relatively simple distributed sensor systems, LPWAN features low costs, long-range transfers, low power (coin cells can last for years), and sufficient throughput for simple and tokenized applications. For example, an array of wind speed, direction, temperature, and humidity sensors deployed over large continental areas might not have cellular coverage, especially in sparsely populated areas. This non-data-intensive information can be optimized to use time slots or polled operations. Each sensor can measure and log data at predetermined intervals. Because data values are simple short
numeric values, low data rates over long distances are desirable, with low-power operations, so batteries will last for years.
A lot will hinge on whether cellular coverage is available in a remote area. Although cellular services can provide longer ranges than Bluetooth, Bluetooth Low Energy (BLE), ZigBee, Wi-Fi, and other short-range protocols, LPWAN still has the advantage of the longest range in remote areas where there’s no cellular coverage.
A good choice for this application could be LoRaWAN. The narrow 125 kHz bandwidth supports 50 kb/sec data rates, which are sufficient to transfer low-power bursts of data over long distances. The 915 MHz frequency band offers many competitive component suppliers to help lower costs. Battery estimates of five to ten years are feasible. The Chirp Spread Spectrum (CSS) modulation technique is robust and relatively immune to noise, especially if channel selections can be made by measuring the best choices at specific locations. No cellular support is needed to implement this standard. LoRaWAN does not require license fees and uses an unlicensed spectrum.
Applications that need higher data rates can use LPWANs that link to cellular services if available at specific locations. NB-IoT and LTE-M LPWAN standards, which operate in a subset of the LTE bands, can have very long ranges because they link to cellular and
even cloud services. The NB-IoT features 100 kb/sec data rates using 180 kHz bandwidths because of QPSK and BPSK modulation. Battery life can potentially be ten or so years. The LTE-M standard increases the data rate to 370 Kb/ sec using a 1.08 MHz channel bandwidth and quadrature amplitude modulation (QAM). Note, LTE-M channels can support voice. This can be a nice feature when debugging a sensor in a remote area. Figure 2 shows an NB-IoT board that uses a module to add connectivity.
The cellular industry is developing technologies for IoT connectivity based on LTE. The industry’s overall roadmap is to build on LTE’s current versions and continue to refine them, including reducing their complexity and cost. As this process unfolds, cellular technology will become better suited to a wider variety of IoT applications, ultimately leading to the introduction of 5G, the fifth generation of cellular technology.
To achieve this goal, the industry consensus appears to be based on three standards primarily introduced in 3GPP release 13, ultimately resulting in what is included in the 5G standards. These solutions should ideally be implemented at frequencies below 1GHz where propagation conditions are more conducive to longer-range and building penetration:
• LTE-M: stands for long-term evolution for machines, also called enhanced machine type communication (eMTC). This is a cellular-based low-power wide-area network developed by 3GPP. Several releases are under this umbrella ranging from 1 Mb/sec to 10 Mb/sec download rates and 1 Mb/sec to 7 Mb/sec upload rates. Operating in half duplex or full duplex, the newer releases feature 10 ms to 15 ms of latency compared to 50 ms to 100 ms latency for older technology.
• NB-IoT: a narrowband version of LTE for IoT also developed by 3GPP. It used the same sub 6 GHz spectrum as 4G LTE and was designed with IoT in mind. It is claimed that IoT devices using the half-duplex NB-IoT can run for decades on battery power, but this will depend on your design. It does include power-saving features such as power-saving mode (PSM) and extended discontinuous reception (eDRX). It uses adaptive modulation, and an interesting repeater functionality called hybrid automatic repeat request (HARQ) to take advantage of narrowband transmission signaling. Up to 1 million NBIoT devices can connect within a square kilometer. Data rates are up to 127kb/sec download and 159 kb/sec upload.
• EC-GSM-IoT: extended Coverage-GSM for IoT is an extended coverage variation of Global System for Mobile Communications technology optimized for IoT in release 13 and can be deployed along with a GSM carrier. It can optimally achieve 2 Mb/sec upload and download rates but can drop to 474 kb/sec along the edge. The half-duplex protocol standards have long latencies, 700 ms to 2 sec, so real-time reporting and control are not recommended.
• 5G: chipsets for 5G are evolving now. Large-scale, high-volume manufacturers such as Samsung and Apple have grabbed these parts and will get application support and mindshare from device makers. Still, this technology will find its way to the bulk of the engineering community and onto PC boards designed for IoT functions. Although blazing speeds (peak 20 Gb/sec) and low latency (1 ms compared to 200 ms with 4G) are features of the 5G embedded designs, connectivity service charges are a part of this solution’s requirements. This adds up quickly as many 5G-based IoT devices come into service.
The unlicensed LPWAN technologies have an advantage over licensed versions, and the two leading the pack are LoRaWAN and Sigfox. Sigfox provides end-to-end connectivity using its proprietary architecture and ecosystem, but it lets endpoint devices use its technology for free if device manufacturers adhere to the Sigfox rules. Figure 3 shows a diagram of the Semtech SX1275 architecture. Figure 4 shows a Sigfox USB dongle.
It’s important to differentiate
LoRa, LoRaWAN, and offerings by Link Labs, as it can be a bit confusing. LoRa is the physical layer of the open standard administered by the LoRaWAN Alliance, while LoRaWAN is the Media Access Control (MAC) layer that provides networking functionality. LinkLabs is a member of the LoRaWAN Alliance that uses the Sematech LoRa chipset (Figure 5) and provides Symphony Link connectivity that has features unique to the company, such as operating without a network server. Symphony Link uses an eight-channel base station operating in the 433 MHz or 915 MHz industrial, scientific, and medical (ISM) bands, and the 868 MHz band used in Europe. It
can transmit over a range of at least 10 miles and backhauls data using Wi-Fi, a cellular network, or Ethernet through a cloud server to handle message routing, provisioning, and network management.
Newer players such as Symphony Link and Ingenu RPMA are overcoming some of the limitations of Sigfox and LoRaWAN. Expect to see more players in this space and cloud and infrastructure services emerging from cellular and non-cellular solutions.
An interesting anomaly in the IoT connectivity universe is Weightless. Weightless is an anomaly among IoT connectivity solutions; it was developed as a truly open standard managed by the Weightless Special Interest Group (SIG). It gets its name from its lightweight protocol that typically requires only a few bytes per transmission. This makes it an excellent choice for IoT devices that communicate very little information, such as some types of industrial and medical equipment, as well as electric and water meters.
Unlike many other standards, Weightless operates in the so-called T. white spaces below 1 GHz that were vacated by over-the-air broadcasters when they transitioned from analog to digital transmission. As these frequencies are in the sub-1 GHz spectrum, they have the advantages of wide coverage with low transmit power from the base station and the ability to penetrate buildings and other RF-challenged structures.
Weightless comes in two versions:
• Weightless-N is an ultra-narrowband, unidirectional technology.
• Weightless-P is the company’s flagship bidirectional offering that provides carrier-grade performance and security with extremely low power consumption and other features.
Another interesting player to watch is Nwave, an ultra-narrowband technology based on software-defined radio (SDR) techniques that can operate in licensed and unlicensed frequency bands. The base station can accommodate up to 1 million IoT devices over a range of 10 km with RF output power of 100 mW or less and a data rate of 100 b/sec. The company claims that battery-operated devices can operate for up to 10 years. When operating in bands below 1 GHz, it takes advantage of the desirable propagation characteristics in this region.
Also, be aware of Ingenu. Formerly called On-Ramp Wireless, Ingenu has developed a bidirectional solution based on many years of research that resulted in a proprietary direct-sequence spread spectrum modulation technique called random phase multiple access (RPMA). Designed to provide a secure wide-area footprint with high capacity, RPMA operates in the 2.4 GHz band.
A single RPMA access point covers 176 mi² in the US, significantly greater than either Sigfox or LoRa. It has minimal overhead, low latency, and a broadcast capability that allows it to send commands simultaneously to many devices. Hardware, software, and other capabilities are limited to those provided by the company, and the company builds its public and private networks dedicated to machineto-machine communications.
As more devices and services connect to the internet, refinements and enhancements will emerge. As with any engineering decision, the learning curve and time-to-market constraints can dictate OEMing an existing solution. As the number of nodes increases, the prices should drop.
A parallel approach allows OEMing a canned solution while developing your own. Already, antennas, filter networks, and assorted components for hardware are available. The sheer number of expected IoT connections makes this technology one that will be around for a long time. Climbing the learning curve can be desirable, even for smaller, narrowly focused companies.
We see ransom hackers disrupting normal operations of everything. So, think twice about how to manage security across the worldwide distribution of your IoT designs. Leave room for a backup plan.
Lastly, remember that various sources plan to put 262,000 Wi-Fi satellites around the globe. Although this might provide connectivity everywhere, it will still be a pay-per-connection technology.
A physical layer for Industrial Ethernet, Single-Pair Ethernet combines high data rates with a lightweight cable design, streamlining communication across automation levels.
By Sagar Patel, Product Manager at Lapp North Americathe Industrial Internet of Things (IIoT), the goal for many manufacturers is to connect all the machines, controls, actuators, and sensors in their plants. That’s easier said than done, however. There are many system inconsistencies at play, making communication between the field device, control, and enterprise levels anything but easy.
To reap the benefits of the IIoT, manufacturers need smooth, seamless communication across all automation levels. Although Ethernet has long been the communication standard at the control level, bus systems still dominate the field level, limiting potential data flow. The solution is to implement a cost-effective and space-saving infrastructure, enabling nonEthernet field devices to communicate with the Ethernet networks above it.
Single Pair Ethernet (SPE) has emerged as this critical bridge, making the field level smarter while ensuring consistent, reliable network communication across the entire automation pyramid. SPE is a cable design that uses a single pair of twisted copper wires to transmit data at speeds up to 1 gigabyte per second (Gbps), allowing real-time, continuous data transfer to and from the field level. Additionally, it offers the advantages of supporting cable lengths up to 1,000 meters (at 10 Mbps), minimizing space requirements, and easing installation.
The following white paper takes a deep dive into this cable construction; it looks at features, benefits, and standardization practices, empowering you to quickly and effectively use IIoT communication technology to improve your manufacturing facility.
Until now, manufacturers have typically relied on bus networks to enable the flow of data from field devices. One of the most widespread bus communication methods for automation technology is PROFIBUS, a serial fieldbus technology established over 30 years ago that uses one pair of cores in a BUS cable. Later, as the industry expanded from buses to Industrial Ethernet, particularly at the control and enterprise levels, PROFIBUS and PROFINET International (PI) developed PROFINET. This Industrial Ethernet protocol uses two pairs of cores to transmit Ethernet at a rate of 100 megabits per second (Mbps). Some manufacturing operations even use Gigabit (GB) Ethernet; a transmission technology that requires four pairs of cores and provides data rates up to 1 billion bits per second, or 1 GB.
With the rise of the connected factory, bus systems can no longer handle the large data transmission rates required by the ever-increasing number of sensors in production facilities. Despite the benefits of Industrial Ethernet solutions, Ethernet is not always suitable for connecting devices at the lowest field level. Cat.5 and Cat.7 cables can be too large to efficiently connect hundreds, possibly thousands, of individual sensors spread throughout production environments.
Another challenge is connection complexity. In order to bridge the communication gap between the field device level (bus) and everything above it (Ethernet), manufacturers must install translators and gateways. In addition to driving up system costs and complexity, the fieldwork required to install this additional hardware increases the risk of installation errors.
A streamlined cable solution, SPE simplifies Ethernet connectivity from the sensors up through the control and company levels, as well as with the cloud — opening new application areas for Industrial Ethernet. A lightweight, efficient cable design, SPE reduces the number of cores to two, enabling 1-Gb Ethernet communication over a single pair of cores. It also eliminates the need for costly gateways between Ethernet and bus networks, reducing installation work and minimizing the chance of errors. Because the cabling itself requires less space, SPE significantly reduces component costs.
In addition to high data transmission speeds via Ethernet, SPE can supply power to end devices via Power over Ethernet (PoE), a standard that specifies the power distribution method for use over a single twisted-pair link. PoE can provide 0.5 to 50 W of power over a twisted pair to power devices like cameras, sensors, and remote input/output (I/O). It further reduces costs by eliminating the need for additional cabling to power devices.
Benefits of SPE include the following:
• supports data rates up to 1 Gbps.
• cables can be deployed up to 1,000 m.
• SPE is more secure with end-to-end protection down to the edge.
• it is an open communication tool — no dependence on one manufacturer or software
• SPE is a cleaner network topology, eliminating the need for costly, complex gateways
• the cables feature a small form factor.
• SPE offers a hybrid solution for data and power
By enabling continuous, long-length communication between the sensor level and cloud, as well as providing power supply via PoDL, SPE offers powerful applications in many industries.
SPE can bridge long distances in large chemical plants, where analog cables or
LAPP has contributed to SPE cable development with the introduction of our ETHERLINE T1 product family, consisting of SPE cables for use in industrial machinery and plants:
• ETHERLINE T1 FD P is a shielded 26AWG cable for use in cable chains.
• ETHERLINE T1 FLEX is an 22AWG cable for occasional movement.
• ETHERLINE T1 P FLEX is an 18AWG cable suitable for distances up to 1,000 m.
bus networks — some with data transmission rates of just 31.25 kilobits (kbit) — are still the norm. The Ethernet Advanced Physical Layer (Ethernet-APL), an offshoot of the IEEE 802.3cg (10BASE-T1L) standard, defines additional properties for these applications, taking into account the use of SPE cabling in explosive areas.
Transportation
SPE shines in electric transportation (e-transportation) applications because of its small, lightweight form factor, reducing weight and bend radii by up to 55 and 30%, respectively. Compared to a cable
with four wire pairs, which will weigh around 4.6 kilograms (kg) per 100 m, an SPE cable weighs only 3.0 kg. Specific use cases in the transportation sector include passenger
SPE can be used to network sensors in fire alarm systems, light or temperature sensors, access control systems, information boards and much more.
SPE is covered by several international standards, including the Institute of Electrical and Electronics Engineers (IEEE). In addition to specifying the primary transmission method, IEEE 802.3 stipulates the transmission channel, transmission length, and number of connectors. Other relevant standards organizations include the International Organization for Standardization (ISO), the International Electrotechnical Commission (IEC) and the Telecommunications Industry Association (TIA), all of which cooperate with IEEE 802.3.
When it comes to the cabling, several IEC 61156 standards are in progress, including IEC 61156-11 and IEC 61156-12 for 600-megahertz
information systems, seat reservation systems, passenger counting visual (PCV) systems, and closed-circuit television (CCTV).
(MHz) data cables in permanent and flexible installations, respectively. Others include IEC 61156-13 and IEC 61156-14 for 20-MHz data
The SPE Industrial Partner Network, of which LAPP is a member, consists of many electrical connection companies, including cable and connector manufacturers, as well as companies that specialize in advanced Single Pair Ethernet technology. The group expects SPE to replace the current fieldbus systems at the sensor and actuator level, providing the core infrastructure for intelligent sensors and actuators in modern smart factories. The goal of this partnership is to continue to create standardized interfaces and system components, all while working closely with various international committees.
• SPE benefits at a glance
• enables Networking with Transmission Control Protocol/Internet Protocol (TCP/IP) without system disruptions
• IP can address all field participants
• suitable for real-time critical applications thanks to time-sensitive networking (TSN)
• accommodates distances up to 1,000 m; more flexibility in cabling, and fewer switches
• can supply power to terminal devices via the same cable using PoDL
• sustainable, thanks to the elimination of batteries compared to wireless systems
• uses less material and lower weight over traditional 2- and 4-pair Ethernet
• offers flexibility and space savings in drag chain applications, conduits, etc.
• reduces installation errors and saves assembly time
• improves operational reliability
cables in permanent and flexible installations, respectively.
Regarding the SPE connectors, several IEC 63171 standards are in under-development. The first and only standard for connections in industrial applications that has been adopted by all major standards bodies is IEC 63171-6, which covers all versions from IP20 to IP 65/67. Published in 2020, IEC 63171-6 describes the T1 Industrial Style SPE plug-in face.
This T1 industrial connector has a very robust design, including stainless steel shield
plates, and a rugged core and cable gland. The interface also features a strong, stainlesssteel lock to maintain a secure connection — even in harsh production environments — and a stainless-steel jacket that encloses the entire connector, minimizing electromagnetic interference (EMI).
LAPP USA | lappusa.com
The demand for high data throughput, low power, and longer battery life is driving much of the breakthroughs and evolutions in connectivity technology.
In this Design Guide, we present the need-to-know basics, as well as the technology fine points aimed at helping you and your designs keep pace and stay competitive in the fast-changing world of connectivity.
BROUGHT TO YOU BY:
Tosuccessfully scale IoT over billions of devices, endusers need confidence that their devices will operate correctly. That’s where the need for industry standards comes in. The LoRa Alliance, which develops and maintains the LoRaWAN open standard, offers simple and inexpensive precertification testing reducing the time to certify end devices. Manufacturers can now perform this testing, which lets them debug prior to pursuing formal certification at an authorized test house.
Before diving into LoRaWAN certification and testing, we’ll explain the need to understand how LoRa, LoRaWAN, and the certification program relate to each other.
LoRa, the physical layer
LoRa is the chirp spread spectrum (CSS) modulation-based physical layer for wireless communication. It’s the basis of the physical radio and hardware that you need to enable longrange connectivity for massive IoT use cases.
LoRaWAN, end-to-end architecture and protocols
LoRaWAN is a low-power, wide-area networking (LPWAN) protocol family that wirelessly connects battery-operated “things” to the internet in local, regional, national, or global networks. LoRaWAN’s standard benefits include long battery life, deep signal penetration, choice of network type and business
model, full control of data and security, firmware updates over the air (FUOTA), and much more. LoRaWAN is now an official standard accepted by ITU-T, a global standards organization.
The LoRa Alliance offers the LoRaWAN Certification Program to ensure connectivity and interoperability between end devices to LoRaWAN networks. LoRaWAN-certified devices are tested for conformance, security, and interoperability.
As Figure 1 shows, according to the local ISM regulations using LoRa (the RF physical layer) with LoRaWAN (the L2 protocol layer) and the Alliance’s regional parameters allows for interoperability across networks making global networking possible.
Technology certification can be time-consuming, rife with mistakes, and may require more than one pass. The LoRaWAN certification test tool (LCTT) was designed for LoRa Alliance members to overcome these barriers to certification, thus significantly reducing time, cost, and mistakes.
The LCTT can be used at a device manufacturer’s facility, letting engineers fully test and regression test devices. Such testing lets engineers debug and make design tweaks before the formal certification process. Certification testing assures LoRaWAN network operators and end-users that devices attain the required quality and reliability to work on any LoRaWAN network out of the box. Figure 2 highlights the certification process. Recently, the LoRaWAN Alliance released a new version of the LCTT, which adds additional testing capabilities. Specifically, validation of:
• LoRaWAN Class A, B, and C end device functionality (Figure 3) selected based on the application requirements: all devices must support Class A communication, the lowest power bi-directional communication initiated by the end device, followed by two short downlink (i.e., reception) windows. Class B devices are bi-directional with deterministic downlink latency and are synchronized to the network using periodic beacons. The network can send downlink communications with a deterministic latency but use additional power consumption in the end device. Class C supports the lowest latency bi-directional end devices and keeps the receiver of the end device open. The network server can initiate a downlink transmission at any time, making class C suitable for applications with continuous power.
• Long-range frequency hopping spread spectrum (LR-FHSS) data rates for the EU868, US915, and AU915 regions: LR-FHSS data rates significantly increase network capacity in certain scenarios while maintaining LoRaWAN’s low power consumption. They are used for uplink only; standard data rates remain in use for the downlink.
• Back-off retransmissions prevent a radio network overload. Uplink frames require
an acknowledgment or answer from the network; if not received, messages are retransmitted by the end device. They can also be triggered by an external event causing synchronization across many devices (>100).
• Regional parameters: radio frequencies often have geographic region-specific restrictions including physical layer parameters such as frequency plans, mandatory channel frequencies, and data rates for join-request messages, as well as LoRaWAN layer parameters, including maximum payload size.
• End device activation: every end device must register with a network to send and receive messages. The LCTT tests: 1) over-the-air-activation (OTAA), which involves devices performing a join procedure with the network, during which the network assigns a dynamic device address. Cryptographic session keys are negotiated between the device and the network; and 2) activation by personalization (ABP), which involves hardcoding the device address and session keys.
• Adaptive data rates (ADRs): this feature is used by network servers to adapt and optimize the number of retransmissions, the data rate, and the transmission power of end devices. When ADR is enabled, end devices will be optimized
to use the fastest data rate and minimum possible transmission power.
• End-device is operating at the correct power level through transmit power control: this capability is region-specific and encoded in the LoRaWAN Regional Parameters document. The transmit output power indicated in the command is considered the maximum transmit power at which the end device may operate.
• Confirmed and unconfirmed frame functionality: LoRaWAN allows for unconfirmed or confirmed messages from end devices to the network and application servers and vice versa. Unconfirmed messages do not require an
acknowledgment from the server as where confirmed messages do.
• Proper opening of receive windows following each uplink transmission to allow bi-directional communications: when correctly implemented, an end device should open one or two receive windows following an uplink transmission to receive transmissions.
• Validating LoRaWAN security by verifying that advanced encryption standard (AES) encryption and message integrity code (MIC) algorithms are correctly implemented: multiple messages with varying length payloads are sent to the end device to
test the decryption of the message. If successfully received, the device generates messages with varying payloads and checks that they are encrypted correctly. The MIC frame signature is computed over the entire frame, which guarantees that the frame can’t be modified between the end device and the network server without compromising this signature.
• The ability to add/modify channels: the LCTT validates that a network server can create a new bidirectional channel and modify the parameters of an existing
one. The command sets the center frequency of the new channel and the range of uplink data rates that are usable on the channel.
• End device support for uplink retransmission of confirmed frames: if an end device sends a confirmed uplink frame containing important information that must get through, it will continue to resend it until the network server sends a downlink acknowledgment that it has been received.
LoRaWAN Certification also defines certification by similarity; a shorter and less expensive path
to certification that allows businesses to leverage the certified status of another end device, even if that end device is made by another manufacturer. The time to certify is a few workdays, reducing the time and cost of the testing cycle. The LCTT validates that the end device uses the same version of LoRaWAN and regional parameters.
Once installed, the latest technology package of the LCTT will automatically download to the tool to ensure that any precertification testing is done against the latest certification test specification.
The next step is to set up the test project (Figure 4).
Once the project is created, give the LCTT information about the device on the main management interface with the buttons on the left side. These give access to the most common actions and tests in the application. See Figure 5.
From here, actions to be performed include:
• Device under test (DUT) Setup Editor contains project name, DUT name, logged user, and role.
• DUT Extra Setup Editor allows modifying implementation extra information for testing (IXIT) and must be set up with the valid keys for OTAA and/or ABP device.
• General Parameters Editor includes details, values, and descriptions.
• Test cases show which test cases are applicable and allows the selection of one or several test cases to execute.
• Logs show the results of test case executions.
• Debug mode allows to send MAC commands directly to the DUT and can be used as a packet sniffer to see packet from the device.
• Test Report allows the creation of detailed test reports.
In certification pre-test mode, any or all the prepopulated certification tests can be selected and executed from the test case tab shown in Figure 6. Select the test cases, press the execute button and the test sequencer screen will appear (Figure 7).
The screen in Fig. 7 shows tests in the left-hand panel and results in the right-
hand panel. The middle panel displays all messages sent and received from the end device. If any part of the test fails, this is where the user can see the failure message. Then, by looking at the message sequence charts in the Certification Test Specification, you can identify what the aim of the test was and the expected response from the device. The best way to scale IoT devices is to use those certified to a standard. To quickly meet LoRaWAN specifications, achieve certification, and receive permission to apply the LoRaWAN Certified mark to a device, use the LCTT tool and accomplish much of the hard work by automating end device testing. This comprehensive and rigorous test suite ensures devices deliver the quality and performance expected by installers and end users alike. The path to LoRaWAN certification for an end device built from the ground up is a fairly short and low-cost process. It can be even shorter and less expensive using Certification-by-Similarity and leveraging the certified status of another certified end-device, even if that end-device
is made by another manufacturer.
The enhanced LCTT offers benefits for device manufacturers, network operators, and end customers. Device manufacturers will save time and expense by undergoing a single certification process that covers conformance, interoperability, and RF testing. Network operators no longer need to perform additional network testing on LoRaWAN Certified devices. When end users see the LoRaWAN Certified mark, they know a device will deliver the expected performance.
Special thanks to Derek Hunt, former Certification Committee Chair, for his contributions to this article.
The LoRa Alliance Certification Committee defines the policies, procedures, and execution of the LoRaWAN Certification Program. Its work is critical to ensuring that LoRaWAN devices are interoperable and perform as intended, which is a requirement to scale IoT. Participants come from LoRa Alliance member companies who have an interest and the background to support its work efforts.
mega tech trends revolutionizing today’s digital world is the ubiquitous Internet of Things (IoT).
By Suresh Patel, Sales Engineer, Mer-Mar ElectronicsThe significant factors pushing the IoT market are the decreased cost of CPU memory and storage, abundant availability of sensor devices, and accessibility of expandable repositories for storing data (like cloud services). The IoT devices can track, monitor, control, and optimize the information about a product’s features that are particularly useful in applications such as smart farming, connected vehicles, smart grids, and many more.
The design of an IoT device depends on the precise selection of the sensors, wireless connecting network, and power management. The traditional PCB design methods may not support the functionalities offered by an IoT product. Wearable IoT devices like fitness
The traditional PCB design methods may not support the functionalities offered by an IoT product.Image courtesy of Adobe Stock
trackers or smartwatches are supposed to be smaller in size but with maximum packed features. For example, a smartwatch includes a clear display, multiple sensors, a microcontroller, a Bluetooth chip for communication, and a battery. A PCB in such an application is expected to be very tiny yet reliable in operation.
In industrial IoT applications, the requirements are even more stringent as most of these devices are expected to be online and transmit information with no downtime. The PCB design in these applications should focus on effective power management.
Most IoT devices are designed to operate in a moving environment with resistance from the external setting. Conventional routing techniques are not suitable for this application. Flex and HDI PCB are used to develop tiny, lighter, and faster IoT devices.
Fabricating flex PCBs for IoT is quite different and demands accurate measurement of bend ratio, signal trace thickness, copper weight, heat generation of the components, and lifecycle repetitions. Thus, the PCB development and fabrication processes continuously upgrade to meet the IoT market requirements.
The substrate material of an IoT PCB should be flexible and lightweight. Flex PCBs and HDI PCBs are extensively used in this application. Flexible PCBs are best suited for wearable devices as more components can be placed in a small area. HDI PCBs simplify the wiring along with minimal mechanical stress.
The compact design requirements demand a thorough simulation and virtual prototyping to incorporate the design shape in the intended form of the IoT device. The necessity for miniaturized components has increased dramatically. Many latest sensors are manufactured using MEMS (microelectro-mechanical systems) technology to offer small footprints with high reliability. Future IoT designs may favor a new approach where mechanical and electrical circuit changes can be done concurrently.
IoT applications have eliminated the luxury of space for designers in component placement and routing. Multilayer PCBs are designed with strict EMC regulations. The peak component density and an increased count of vias in the circuit are achieved using HDI PCBs. The integrity of the sensor signals must be ensured by eliminating any possible coupling and interference issues in the design.
The component packages cannot be through-hole or surface-mount types in an IoT design, so there’s no possibility for through-hole or SMT PCB Assembly. The miniature gadget size has resulted in the development of new package technologies like multi-chip modules (MCM), system-in-package (SiP), and integrated three-dimensional circuits (3D-ICs).
One of the critical requirements of an IoT device is extended battery life. Designers should choose the right power management integrated circuits (PMIC) and calculate the power budget for each functional block. Power
consumption varies according to the device’s operating device’s state; hence, analyzing all corner cases is important during power estimation. The battery life drains faster in applications like healthcare monitoring devices, wireless transceivers, etc., which involve continuous activity. Techniques such as energy harvesting and design compliance with wireless standards can improve power efficiency and battery life.
As IoT devices are connected to a shared network, a security breach is an apparent possibility. There are applications involving sensitive data like medical details or financial information which can be misused. Along with software security updates, there is an increasing need for hardware protection in IoT devices.
Another vital feature required in IoT devices is their adaptability to end-user interaction. The human body temperature, moisture, and mobility can affect the performance of an IoT device, especially in wearable products. In an IoT PCB design, simulating these conditions and implementing suitable compensation circuits are important.
Manufacturing requirements for IoT PCB
Involving the contract manufacturer from the design stage is recommended for an effective PCB fabrication for your IoT device. Flexible PCBs and components in SiP packages can simplify the fabrication process. Preventing the usage of counterfeit components and adding identification codes in each layer of the PCB can improve the security of the IoT circuit.
It is necessary to consider the potential issues during the design to avoid failures after deployment. Generally, IoT devices are classified as consumer, industrial, and enterprise devices. The DFM requirements of a consumer IoT device (like smart TV, or wearable devices) are a balanced stackup, managing connector constraints, and selecting the PCB material with the required bend ratio.
Industrial IoT devices (like motors and construction vehicles) are supposed to have high board strength, thermal capacity, and high voltage. Including enough thermal relief during layout design is recommended for better PCB performance.
Enterprise IoT devices (like security systems and computing devices) demand high power reliability, high-frequency/RF connectivity, etc. The ease of depanelization and enough spacing for component rework can improve manufacturability.
We can collect data and use this information to build customized products with IoT devices. Combining IoT with 3D electronic printing technology has a tremendous potential to speed up the manufacturing process and can also build 3D PCBs. An optimized IoT PCB can be used in healthcare, aeronautics, defense, and more. The PCB design for IoT applications may become more specific as the business expands. New features can bring new challenges, but a common set of requirements indicate a possibility of using similar design procedures frequently.
Matter has been called an interoperable application layer solution. The Connectivity Standards Alliance, the same source that oversees the development of Matter, refers to it as a protocol.
By Jeff ShepardThisFAQ explores the definitions of communications interfaces and protocols. It compares those definitions with Matter, presenting the possibility that Matter is not a protocol but a new type of middleware for wireless Internet of Things (IoT) devices.
Interfaces like RS232, RS422, and RS485 provide physical links between systems, while human-machine interfaces (HMIs), like touch screens and link systems (including industrial systems, computers, and communications devices), link with operators and users (Figure 1). HMI specifications are generally related to ergonomics and psychology to support the needs of human users. HMIs are also called user interfaces (UIs) and can be made up of multiple physical devices like touch screens, keyboards, monitors, speakers, printers, etc. These various devices are called human interface devices (HIDs).
Machine-to-Machine interfaces
Just as there’s a wide variety of HIDs designed for specific purposes, there’s a wide range of machine-to-machine interfaces such as serial buses, fieldbuses, Ethernet, etc. Some serial buses use protocols like IO-Link to connect individual devices to a controller. The controller area network (CAN) serial bus can be implemented in a multi-master configuration with numerous devices sharing the bus.
Fieldbus profiles are standardized by the International Electrotechnical Commission (IEC), as IEC 61784 and 61158 can support various topologies like ring, branch, star, and daisy chains. In many industrial settings, fieldbuses have replaced RS-232 and RS422 serial communications. An important advantage of fieldbuses over other solutions is determinism. Communications can be received and acknowledged in real time, an
important feature in industrial process control systems.
Many fieldbus standards include RS-485 transceivers as an option for the physical layer. RS485 transceivers are inexpensive and have multiple speed ranges and other important features. Fieldbuses use a single bus to connect all devices on a network with a single controller. That arrangement reduces the amount of wiring needed and increases system modularity, both important considerations in industrial installations. A Fieldbus provides the physical layer and can be used with many communication protocols such as Foundation Fieldbus, EtherCAT, Profinet, Modbus, HART, etc.
Protocol suites and stacks
Communication protocols are composed of suites and stacks. A protocol suite is a general specification of how the protocol is structured and what elements are included. The protocol stack, known as the network stack, is a specific protocol suite implementation. Specialized protocol stacks can be developed from protocol suites to address specific communication and application needs. Each module in a protocol stack typically communicates with two other modules, hence the concept of being stacked on top of each other. The lowest layer in the stack links to the hardware interface, such as an HMI or a communications device like a radio. Moving up the stack adds functionality. At the top, the stack links with the application software. Examples of protocol suites include the open systems interconnection (OSI) model and the Internet protocol (IP) model.
The International Standards Organization (ISO) designed the OSI suite to provide an everyday basis for developing communications standards. The OSI suite and related standards partition the communications stack into seven abstraction layers beginning with the physical system interconnection
(interface) at the lowest level. The layers in the stack include physical, data link, network, transport, session, presentation, and application (Figure 2). Each intermediate layer in the OSI suite provides specific functionality to the layer above it and is supported with specific functionality from the layer below it.
An important aspect of a protocol stack is that each layer must have unique and welldefined functions, and the suite must define the interactions between adjacent layers. The OSI and IP communication protocol suites meet these requirements and can be used as the basis for multiple communication protocol implementations.
The IP suite is built using a very different model than the OSI. Instead of being built on ISO standards, the IP suite is built using a series of documents
individually called a ‘Request for Comments’ (RFC). Each RFC is a formal document from the Internet Engineering Task Force (IETF) that includes specifications and organizational notes about specific topics (layers) like routing, addressing, and transport technologies related to the Internet. According to the IETF, there are over 9,000 individual RFCs.
The lowest layer in computer communications, including the IP
suite, is called the link layer. It’s like the combination of the data link layer (layer 2) and the physical layer (layer 1) in the OSI stack, described in RFC 1122 and RFC 1123. The combination of RFC 1122 and RFC1123 is similar to, but not identical to, the combination of layers 1 and 2 in the OSI stack. RFC 1122 includes local area network protocols such as Ethernet, and other IEEE 802 networks like Wi-Fi and framing protocols such as Point-to-Point Protocol (PPP) that belong to the link, IP, and transport layers. RFC 1123 covers the application and support protocols. Matter provides an abstracted application layer on top of IP protocol stacks like WiFi, Ethernet, and Thread (Figure 3). Matter was developed to improve the interoperability and security of devices and simplify solution development across various IP connectivity protocols and technologies.
Trying to classify Matter as a type of software can be challenging. A significant difference between Matter and the protocol stacks and suites described above is that the lowest level of the Matter stack does not connect to a physical interface. The Matter specification “defines fundamental requirements to enable an interoperable application layer solution for smart home devices over the Internet Protocol.”
Confusion is easy: under the topic Connected Buildings, the Connectivity Standards Alliance site states, “Standard protocols like Zigbee and Matter enable buildings to be connected by design in a
Data Model Structure
Interaction Model Actions
Interaction Model Actions
Action Framing
Security (Encryption & Signing)
Message Framing & Routing
IP Framing & Transport Management
• Security: the Security Layer encrypts the encoded or ‘framed’ action to ensure that the data can be authenticated.
• Message Framing & Routing: the secure and framed action is formatted as needed with header fields, and other structures that describe the properties of the message and routing information are added.
• IP Framing & Transport Management: connects Matter with the underlying TCP/ UDP transport protocol layer for IP management of the message and connection to the communications protocol and interface layers.
Sub Layer
way that doesn’t require disparate or complex systems and allows fluid integration of devices and information over IP.” So, is Matter really a protocol? The truth may lie in the middle.
Matter in IoT devices can be likened to the middleware in an embedded MCU application. Middleware is the software in an embedded MCU that connects the OS with application software. Middleware (and Matter) simplify the development of embedded (and IoT) applications by:
• Handling the interactions of distributed applications
• Supporting seamless interactions between heterogeneous hardware, operating systems, and software protocols
• Making applications
interoperable, portable, and reusable through common and high-level interfaces.
• Eliminating duplication of effort and enhancing collaboration between applications by delivering a common group of services
In an embedded MCU, the application software uses services from the middleware. In a Matterenabled IoT device, the application software uses services from Matter (Figure 4):
• Data Model: data primitives and structures that describe device functions.
• Interaction Model: the set of actions that can be used to interact with the device, such as reading and writing, that operate on the structures described in the data model.
• Action Framing: actions constructed using the Interaction Model are framed or packaged into a binary format that can be communicated to other devices.
Summary Matter was developed to provide an intermediate application layer to support improved interoperability, security, and reliability on wireless IoT networks. Matter is not a communication protocol in the conventional sense; it sits between the IP protocol layers and the application in the device software stack, providing functionality and services analogous to the middleware in embedded MCU solutions.
References:
A FAQ about the Matter connectivity standard, Texas Instruments. https:// e2e.ti.com/blogs_/b/process/posts/ an-faq-about-the-matter-connectivitystandard-zigbee-alliance-project-chip
Connectivity Standards Alliance. https://csa-iot.org/all-solutions/matter/
HMI (Human Machine Interface), Microchip. https://www.microsemi. com/applications/industrial/hmi
Matter Architecture, Momoiot. https://momoiot.co.kr/matter/ overview/architecture/
Protocol stack, Wikipedia. https:// en.wikipedia.org/wiki/Protocol_stack
Whenresearchers and engineers started developing 5G in 2012, they began to look at use cases. The primary motivation for launching a new generation of wireless technology was an insufficient spectrum. Most industry analysts predicted an explosion of data traffic that would result in the saturation of existing spectrum resources.
Another motivation arose from the expected tremendous growth in the number of connected devices, including many new device types for machine-type communications (MTC) and Internet of Things (IoT) applications. This expansion gave rise to a variety of requirements that 4G missed. Here’s how 4G and 5G compare in relation to IoT.
5G’s definition took the shape of a now-famous triangular icon with three sides depicting the three main 5G components. The triangle was subsequently modified, reused, and adapted by many companies throughout the wireless industry. Figure 1 summarizes the three 5G use cases.
• eMBB: enhanced mobile broadband. Somewhat the same as 4G, but with faster speed and larger capacity. eMBB supports the accelerating growth in the number of consumer devices and mitigates the expected saturation of 4G networks.
• URLLC: ultra-reliable, low-latency communications. URLLC fulfills the requirements of vertical market segments such as industrial, health, transportation, and aviation that have high demands for low latency and high reliability. These new use cases came from stakeholders outside of the traditional telecommunications world, such as automotive and energy.
• mMTC: massive machine-type communications. mMTC supports a massive number of connected objects. While not necessarily requiring high data rates or low latency, these connected objects have other demanding requirements such as ultra-long battery life, small footprint, and simplicity needed to enable connections for almost any kind of object.
With so many use cases and requirements, 5G needed versatility and support for these generally non-compatible
requirements. These requirements were key in driving innovation in 5G design.
The new requirements imposed on 5G include not only a new radio (NR) interface; 5G adds an evolution in core network principles: convergence of wireless and wireline systems, new radio access networks (RANs), and new telecom network core architectures. These aspects are beyond the scope of this article.
To meet the three main use case requirements, 5G NR needed more flexibility and higher efficiency than 4G while providing more capacity, higher speed, and lower latency. To improve the capacity, concluded Shannon, one must either increase the bandwidth or improve the signal-tointerference-and-noise ratio (SINR).
4G and 5G differ in their use of spectrum [Ref. 1]. To increase the bandwidth for cellular, regulatory agencies look to repurpose spectrum from other uses. In the US, for example, frequencies formerly used for broadcast TV are now allocated for cellular. While 4G resides mainly below 3.8 GHz, 5G uses bands below 6 GHz (frequency range 1, FR1) and 24.25 GHz to 52.6 GHz (FR2).
In 4G, the use of unlicensed spectrum was introduced later in development with LTEassisted access (LAA) and LTE in unlicensed bands (LTE-U). In 5G, the use of unlicensed spectrum was considered early, under the NR-U (new radio unlicensed) name.
More efficient modulation schemes can increase spectral efficiency, resulting in the delivery of more bits per hertz. 5G uses 256 QAM and 1024 QAM, which provides greater spectral efficiency than lower-order modulations. New waveforms, generalization of multiple-input, multipleoutput (MIMO) antenna schemes, and the introduction of improved forward error correction (FEC) techniques help to improve SINR.
Many of 4G’s principles continue in 5G. For example, OFDM, OFDMA, and MIMO all came from 4G, and the protocols are almost identical [Ref. 2,3,4].
5G extends its scope beyond consumer to many new vertical and enterprise markets. Thanks to its flexibility and improved performance, 5G opens the door to many industrial applications.Figure 1. The original 5G triangle, from Recommendation ITU-R M.2083 [ITU-R, IMT Vision— Framework and overall objectives of the future development of IMT for 2020 and beyond].
Because flexibility was deemed necessary to meet the needs of a wide variety of new use cases, the time-frequency grid must accommodate different numerologies µ (from 0 to 4), corresponding to the subcarrier spacing (SCS) of OFDM symbols. Numerology 0 refers to a subcarrier spacing of 15 kHz (same as LTE). Numerology 1,2,3 and 4 correspond respectively to 30 kHz, 60 kHz, 120 kHz, and 240 kHz), resulting in different slot durations (the number of OFDM symbols in a slot is kept constant at 14). Table 1 summarizes the numerology. With this flexibility, the NR frame design can accommodate low latency traffic (using very short slot durations), as well as a variety of frequency bands (the higher the frequency, the higher the SCS).
4G LTE protocol has two main frame structures: FDD and TDD. In contrast, 5G NR has 56 slot formats currently defined that operate in either duplex mode, FDD, TDD, or even in self-contained slots that contain downlink and uplink symbols. Such self-contained slots enable fast communication on the air interface, minimizing the transmission time interval (TTI).
Beamforming shows another difference. In 5G NR, all signals are beamformed, which provides better reach and limits the overhead (pilots are transmitted only when needed). The pilot structure is flexible, allowing adaptation to the channel
characteristics. Front-loaded pilots let channel estimation occur first, and then demodulate received data symbols on the fly, for faster demodulation.
Additional innovations accommodate operation in mmWave bands. For instance, dedicated pilots such as phase reference symbols (PRS) counteract harmful phase noise.
5G also introduces low-density parity codes (LDPC) as forwarderror-correction codes for the data channels and polar codes for the control channels. Though polar codes are quite novel, LDPC were already being used in Wi-Fi. While NR design didn’t introduce anything revolutionary, it is a better version of 4G. It can deal with larger bandwidths and higher frequency bands than LTE.
The first definition of 5G NR in 3GPP was made in the context of release 15, completed in December 2017. For this release, the focus of standardization was on the eMBB use case, with some enablers for URLLC. 3GPP identified solutions for mMTC as LTE-M and NB-IoT, which were defined in release 13. This raises more general questions about support of IoT in 5G.
5G IoT support
4G LTE introduced MTC, which refers to two non-smartphone objects communicating with each other. MTC was originally considered only for low-datarate devices and applications,
generally known as IoT. 5G NR opens the door for communication of more sophisticated and higher data rate objects that must meet stricter latency and reliability requirements. This corresponds to the URLLC side of the ITU triangle (Figure 1). These more demanding objects are sometimes referred to as industrial IoT or critical IoT objects to distinguish them from low-profile IoT objects, mMTC.
3GPP defined 4G LTE in 2012 with release 8. It was then improved in subsequent releases, adding higher throughput and more features. Release 13 (2016) added two new flavors specifically defined to address IoT: category M (LTE-M) and narrowband IoT (NB-IoT, category NB). The former operates in regular LTE deployments, using the smallest possible channel size (1.4 MHz) and the latter operates in a 180 kHz channel. That lets it be deployed in standalone mode (typically reusing GSM channels), in regular LTE bands, or within LTE guard bands.
Think of LTE-M and NBIoT as stripped-down versions of regular LTE, with the design target being low cost, improved (indoor) coverage, and very long battery life. That’s needed for battery-powered IoT applications — utility meters, wearables, alarm panels, and asset trackers. Primary design objectives of LTE-M and NB-IoT include:
• Reduced cost, smaller footprint: LTE uses two antennas on the device side. LTE-M and NB-IoT use one, simplifying signal processing. Smaller channel sizes further simplify processing. Eliminating the duplexer (the specific filter that protects the receive path from the transmit signal) also simplifies the design in half-duplex FDD (HD-FDD), the mode used in LTE-M and NB-IoT. This simplified design lets a single hardware design operate globally.
• Improved coverage. Removing one antenna negatively impacts receiver sensitivity. To compensate for this loss and improve the coverage (as necessary for deep indoor deployments such as smart meters), coverage enhancement (CE) modes were introduced. CE modes are simply signal repetitions, a low-cost technique for improving SINR.
• Long battery life. New powersaving schemes and protocol optimizations let IoT devices enter deep sleep as fast and for as long as possible, resulting in reduced power consumption. LTE-M is richer in capability than NB-IoT. It supports mobility, VoLTE, and data rates up to 1 Mb/s while NB-IoT is limited to 30 kbps. NB-IoT achieves theoretically better coverage and lower power consumption.
In releases 14 and 15, 3GPP improved LTE-M and NB-IoT from their initial release. When 3GPP submitted its proposal to ITU for 5G, it submitted NR for eMBB and URLLC, while LTE-M and NB-IoT were accepted as already meeting the requirements for the mMTC aspects of IMT-2020.
3GPP introduced efficient solutions to connect classical objects. Depending on the application, the user can select the most appropriate cellular technology to connect objects, per application, as illustrated in Figure 2. LTE-M and NB-IoT are officially part of 5G.
How can we ensure that all deployed objects using LTE-M, NB-IoT, or even LTE Cat 1 have support going forward? In many applications, IoT-connected objects are expected to live in the field for many years (utility meters), and some were originally designed to operate with a 4G core network. The 5G core brings improvement, especially with respect to high-end quality of service, but does not
bring any specific benefit to lowend IoT (and more problematic, some power optimization features were not supported in the release 15 5G core network). There are three options for this problem: IoT devices can support both 4G and 5G core networks, which leads to additional cost and complexity, thus wiping out the low-cost advantages.
• Upgrade the devices over the air with new firmware when switching from a 4G to a 5G core, assuming an immediate transition on the network and the possibility to upload a complete firmware over the air despite a thin pipe.
• Network operators can continue to support 4G core functionalities within the 5G core, allowing easy support of legacy LTE devices.
Option three is the most realistic.
5G: Critical and industrial IoT 5G NR brings significant improvements in latency and data rate compared to 4G, and these improvements are key in meeting the strict requirements in vertical markets such as factory automation
(industry 4.0), transport, energy, or entertainment; including augmented and virtual reality. Most of these improvements are defined within the context of the URLLC side of the 5G triangle.
URLLC services are enabled by the flexible frame structure (allowing a very short TTI), preemptive scheduling, and anticipated retransmission for fast turn-around, grant-free transmission, etc.
Cellular connectivity, especially in harsh industrial environments, has an inherent advantage over Wi-Fi and even wired technologies. Wi-Fi is less secure and more susceptible to interference than cellular by design, and wired technologies are less flexible and more difficult to update or change in a factory layout. Thus, 5G will be a key technology for industrial applications, especially when deployed as a private network where the network owner has full network control.
In release 16, 3GPP introduced a dedicated working group to address Industrial IoT. The work item [5] introduced improved reliability thanks to enhanced packet data convergence protocol (PDCP, an upper layer of the
protocol stack) duplication, mechanisms to prioritize traffic between UEs and within a UE, and a means to support time-sensitive networking (TSN) [6].
TSN is a technique introduced by IEEE 802.1 group for an Ethernet wired network that provides deterministic transmissions by synchronizing various equipment components to a single master clock [7]. Mechanisms to ensure deterministic delays and synchronization were defined by IEEE and the objective of 3GPP was to adapt these mechanisms to the wireless and 5G world. Industrial IoT and its subsequent ongoing work item in release 17 called in 3GPP Enhanced IIoT complements URLLC and is expected to fully support the most stringent requirements of critical and industrially connected objects [8].
5G will not replace 4G. Both will coexist for a long time, especially for the LPWA side of IoT for which LTE-M and NB-IoT will remain the solution of choice. With 4G LTE and 5G NR, 3GPP defined a unified toolbox to support professional IoT and a wide range of applications from very simple,
low data rate types of connected objects to high-performance industrial and critical IoT.
References:
[1] Michelle Effros and H. Vincent Poor, “Claude Shannon: His Work and Its Legacy,” EMS Newsletter, March 2017, p.20. https://www.itsoc.org/ resources/Shannon-Centenary/ shannon-work-legacy-paper.
Bob Witte, “The basics of 5G’s modulation, OFDM,” 5G Technology World, April 16, 2020. https:// www.5gtechnologyworld.com/thebasics-of-5gs-modulation-ofdm/
Bob Witte, “OFDMA improves spectrum use in Wi-Fi 6,” 5G Technology World, June 4, 2020. https:// www.5gtechnologyworld.com/ofdmaimproves-spectrum-use-in-wi-fi-6/
Bob Witte, “More antennas, faster data transfer,” 5G Technology World, July 7, 2020. https:// www.5gtechnologyworld.com/ more-antennas-faster-data-transfer/
See RP-200797.zip available at: https://www.3gpp.org/ftp/ TSG_RAN/TSG_RAN/TSGR_88e/ Docs/RP-200797.zip
Packet Data Convergence Protocol (PDCP) specification (3GPP TS 38.323 version 15.2.0 Release 15), https://www.etsi.org/deliver/ etsi_ts/138300_138399/138323/15. 02.00_60/ts_138323v150200p.pdf.
Dave Cavalcanti, “Five reasons why TSN over 5G promises timely deliveries,” 5G Technology World, February 2, 2021. https:// www.5gtechnologyworld.com/fivereasons-why-tsn-over-5g-promisestimely-deliveries/
See RP-201310 available at https://www.3gpp.org/ftp/tsg_ ran/TSG_RAN/TSGR_88e/Docs/ RP-201310.zip
Stay tuned to the latest research & development news
The R&D World website is constantly updated with industry news, technology developments, case history stories, and all of the most current data about research budgets and future forecasts. From corporate to academic to government laboratories, the website — along with R&D World’s Twitter, Facebook, and LinkedIn pages — are your need-to-know information source for this industry!
Jami Brownlee jbrownlee@wtwhmedia.com 224.760.1055
Jim Dempsey jdempsey@wtwhmedia.com 216.387.1916
Mike Francesconi mfrancesconi@wtwhmedia.com 630.488.9029
Courtney Nagle cseel@wtwhmedia.com 440.523.1685
Jim Powers jpowers@wtwhmedia.com 312.925.7793 @jpowers_media
Publisher Mike Emich memich@wtwhmedia.com 508.446.1823 @wtwh_memich
CEO Scott McCafferty smccafferty@wtwhmedia.com 310.279.3844 @SMMcCafferty
EVP Marshall Matheson mmatheson@wtwhmedia.com 805.895.3609 @mmatheson
The world of IoT is linked by antennas. With the acquisition of Laird Connectivity's External Antennas business and Linx Technologies, TE Connectivity (TE) offers thousands of antenna solutions for a wide array of applications. From transportation and industrial applications to medical technology and data communications, and finally the home, TE is improving the capabilities of wireless connection on a global scale. Find out how our products and expertise can help take your projects from “concept” to “connected.”
Learn more at te.com/iot-brand
CONNECTORS
/ MICROWAVETANTALUMSUPERCAPACITORS
ANTENNAS ACTIVE + PASSIVE