Transforming How We Work, One Machine at a Time
New machines are becoming smarter as they blend mechanical and electronic technologies. This hybrid world is transforming manufacturing and how people work.
By helping to restore the global economy after the crisis of the Covid-19 pandemic and its related economic damage, Italian machine builders are on the leading edge of a revitalization, designing and building new machines that are helping manufacturers, particularly in North America, produce more products, of better quality, with less waste and using fewer resources.
Major challenges still lie ahead, particularly a shortage of skilled workers and a still fractious supply chain. Increased conflict between major regions of the world, and still-high energy prices and inflation, continue as significant barriers to any return to pre-Covid economic conditions.
Yet despite these challenges, Italian equipment makers continue to forge ahead, incorporating new technologies into their machines that benefit customers and their workers. The digitalization called for by Industry 4.0 is making real inroads into how companies structure their work processes. And remote monitoring and data analysis are becoming increasingly important to both manufacturers and OEMs. Machines are becoming easier to operate and maintain, alerting operators to equipment problems and indicating how to solve them. And training has become a real added value that machine builders can offer their customers to help them retain and educate workers with the technical skills required in manufacturing today. In fact, one Italian
company operates a foundation whose exclusive job is to share construction industry skills with new workers. Sustainability has become another key demand as users want to reduce their use of water, energy and raw materials. Making more healthful products is also critical for many customers, as a company making vegan products in Atlanta relies on an Italian maker of shrink-wrapping equipment to protect the nutritional value of its juices. Compostable food packaging is also expanding business opportunities for Italian packaging suppliers.
Fighting climate change by moving to batteries and away from fossil fuels is another area where Italian companies are taking a leadership role. This includes finding ways to create a circular economy where materials can be reused, and pollution can be reduced. Italian equipment builders are also working to recycle textiles. These two examples show how “Made in Italy” has come to signify quality and innovation.
Finally, this year’s issue of Machines Italia shows how the merger of electronic and mechanical technologies is bringing new levels of productivity and advanced capabilities to the Italian metalworking industry, and to the companies that use their innovative products around the world. It’s an exciting time to be in manufacturing. Benvenuti!
Sincerely,
Marco Verna Trade Commissioner—Chicago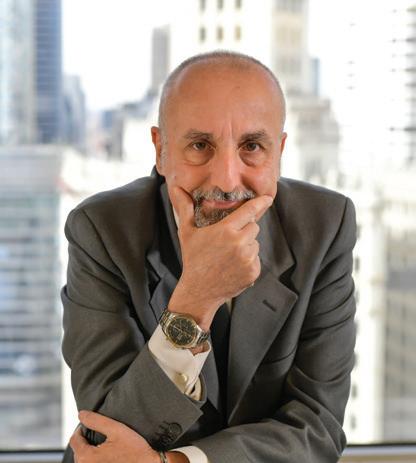

2 Transforming How We Work, One Machine at a Time New, smarter technologies are transforming the world.
4 Engineering the Future
Italian engineers are delivering new value to the manufacturing world.
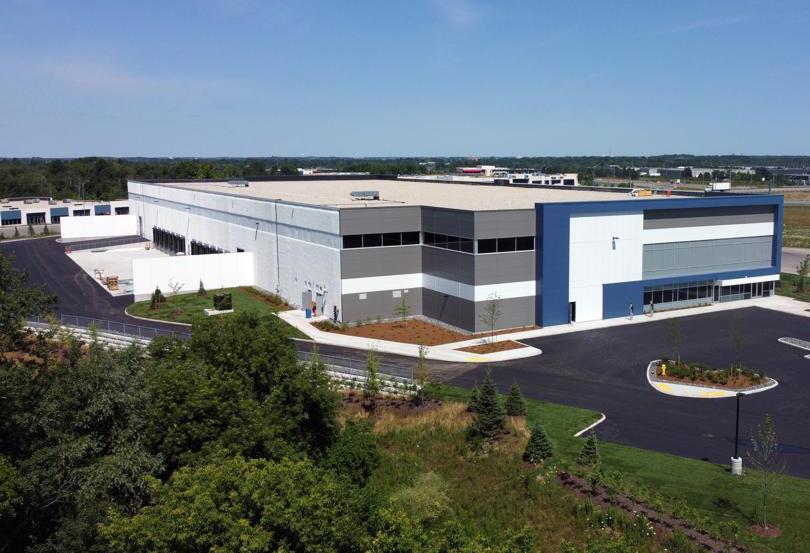
5 Manufacturing Embraces the Move to Smart Machinery Survey shows how technology is changing manufacturing.
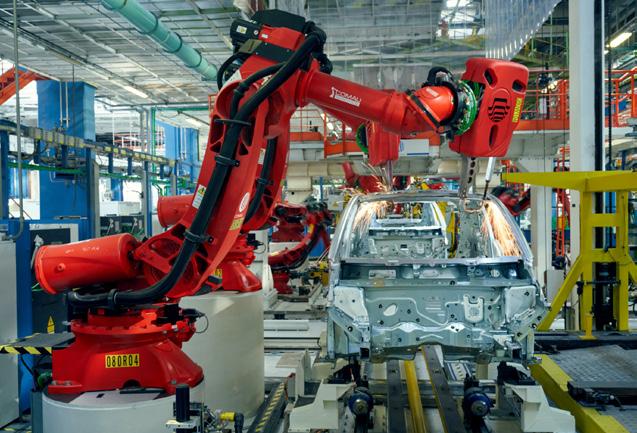
7 Merging Electronic and Mechanical Technologies Transform Machinery Smarter machines are revitalizing manufacturing and work.
11 From Farm to Table, Consumers Want Sustainable Food and Packaging Healthier food requires sustainable processes and packaging.
15 Creating New Ways to Build Products the World Needs Technology is transforming Italian machinery in every industry.
19 Training Matches Workforce Skills with Technology
Italian companies elevate the skills of their workers and customers.
23 Hybrid Systems Improve Metalworking Practices

The move to digital technologies is revitalizing metalworking.
27 Machines Italia News
News briefs from a selection of our 10,000 machinery manufacturers.
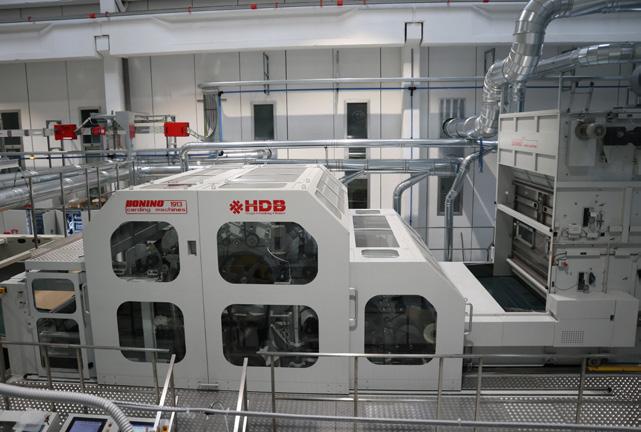
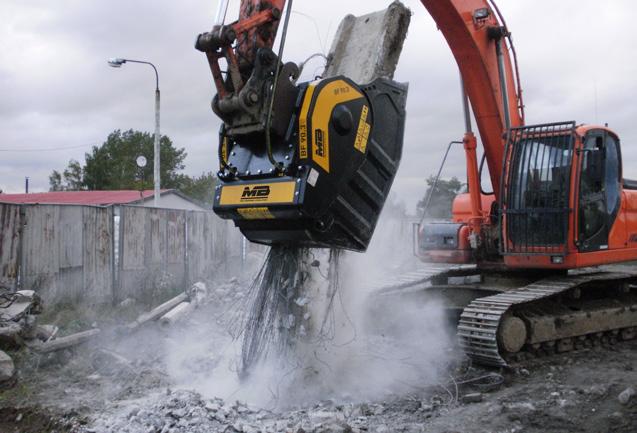
30 Italian Technology Award Programs
Connecting international students and faculty members with Italian companies and associations.
31 Italian Innovation in the Spotlight
From Chicago and Las Vegas to Mexico City and Ontario, Machines Italia is on the road to innovation.
32 Upcoming Trade Shows
Experience some of the industry’s best and brightest at these upcoming events.
34 Innovation at Work in Global Markets
A look at Machines Italia’s partner associations and industries.
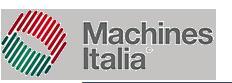
Italian Trade Agency—Chicago
ADDRESS TOLL-FREE TELEPHONE FAX E-MAIL WEBSITE
7
For a detailed interactive digital map on Italian Solution Providers in North America, please visit tinyurl.com/ItalianSolutionProviders.
11
15
19
23
401 N. Michigan Avenue, Suite 1720 | Chicago, Illinois 60611 1-888.ITALTRADE/482.5872 (U.S. and Canadian Callers) 312.670.4360 (Outside the U.S. and Canada) 312.670.5147 info@italtradeusa.com www.machinesitalia.org
The Italian Trade Agency’s North American offices in Chicago, Houston, Los Angeles, Toronto, and Mexico City are principally responsible for the machinery and technology sectors covered in this publication.
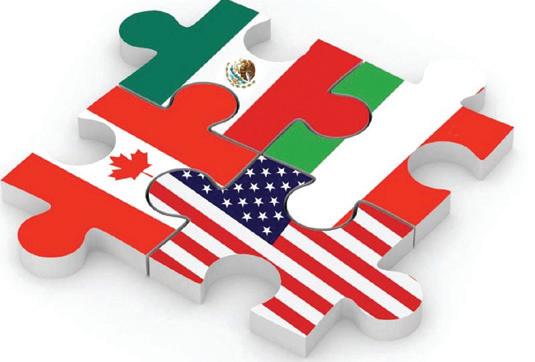
Engineering the future
Italian engineers are delivering new value to manufacturing, creating machines that are smarter and use resources more wisely.
Innovation is in the DNA of G&W Electric. Since our founding in 1905 we have created a number of electrical industry firsts, starting with the disconnecting porcelain pothead and much, much more. We’ve been a global enterprise for many years, working with customers based on our shared values of listening, expertise and service, on all seven continents, including Antarctica.
And as our company has discovered since 2019, when we began entering into a number of commercial engagements with family-owned Italian firms, it’s also in the DNA of Italian engineers. The technicians at these companies are world class and their engineering expertise is second to none. Many of them have earned PhDs from prestigious universities in Italy and elsewhere, and their credentials attest to the depth of their knowledge.

These engagements with Italian companies have allowed G&W Electric to take advantage of numerous advanced technologies that will help our customers succeed in this time of rapid change, including new resins and silicon rubber components that will be essential to building more reliable electric grids around the world. We expect to learn much more from them in the years ahead.
I share their optimism. I believe this is an exciting time to be working in manufacturing. Electronic technologies are changing what we do and how we work. It’s particularly awe-inspiring to see how eager our young engineers – from America, Italy and around the world – are to be working together to bring about this transformation.
Unlike in the US, where industries are usually dominated by two or three large corporations, Italian companies are often family owned and have a greater number of competitors. Employees see themselves as members of the family and manufacturing is a highly respected occupation. This has fostered a strong spirit of entrepreneurship, and Italian companies are recognized global leaders in many industries.
Conserving resources is a priority in Europe. Although their population matches that of Canada and the USA combined, their landmass is smaller, so they have fewer resources. It’s only natural they’ve been leaders in setting standards for sustainability.
Italian machine builders are putting those standards into practice in their equipment and making great progress in developing sustainable production processes that make wiser use of natural resources and produce less waste. These are values we share at G&W Electric. We went landfill-free six years ago and have installed our own microgrid at our Illinois factory.
Italian companies also share our respect for education and technical expertise. At G&W Electric, 20% of our employees are engineers; we provide college tuition assistance for employees and paid summer internships for college students. We also recruit engineers from all over the world.
As you’ll see in these pages, Italian equipment and component makers have always been known for quality and craftsmanship. They stay at the leading edge of technology by constantly researching and testing new ways to advance the capabilities of their products. It’s how they’re helping to transform the way we work, one machine at a time.
John H. Muller Chairman and CEO G&W Electric
Manufacturing Embraces the Move to Smart Machinery
Investments in technology are transforming machines and manufacturing, according to recent surveys by the National Association of Manufacturing, the largest group of manufacturers in the United States. It’s a finding affirmed by other research, including a joint readership survey conducted at the end of 1Q 2023 by the Italian Trade Agency’s Machines Italia program and Design World
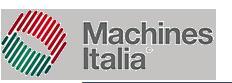
Smart devices, smarter machines
In the survey, approximately 200 respondents, primarily North American OEM design engineers and system integrators, shared their insights on smart machines, smart devices, innovations, workforce training and sustainability.
Approximately 49% of respondents currently embed smart devices in their machines, with 70% expected to do so within the next year. Motion control, safety devices, sensor operations, and motor control were the primary applications for these smart devices. Robotics (61.44%), AI (44.54%), simulation (42.86%), and smart machines/smart factories/ digitalization (38.66%) are the top areas for technology investments.
Smart devices, smarter machines
Machine builders are listening to their customers and their peers when it comes to designing and building new machinery. Remaining competitive (51%), improving manufacturing quality (50%), reducing downtime (38.28%,) digitalization strategy (35.16%) and increasing profitability (25%) were all important motivators for creating smarter machines.
Survey respondents also had a wish list for how vendors could improve their smart devices. These include global standards (57.03%) that would make products from multiple vendors compatible, easier network connectivity (48.44%), remote access and monitoring(41.41%), and easier OT/IT integration (30.47%)
Approximately 49% of respondents currently embed smart devices in their machines, with 70% expected to do so within the next year.
Insights from the Factory Floor
Tactics to add skilled workers
The shortage of skilled workers continues to be a barrier in manufacturing. Survey respondents said they’re attempting to solve this by adding robotics (50.86%), artificial intelligence (33.62%), remote monitoring and troubleshooting (38.79%), in-person (42.24%), online and phone training and technical support (20.69%), and by simplifying machine operations (35.34%) and offering remote work (41.38%). Significantly, few (18.10%) work with local colleges and high schools to recruit or train workers.
The results of this survey and other recent research show that the transition to smarter manufacturing processes is well underway in North America. It proves that a receptive audience now exists for the evolutionary equipment designs that Italian machine builders have been introducing so successfully to companies in the region
Tactics to add skilled workers
Opportunities to work from home, which increased during the pandemic, are still seen as valuable by workers who provide phone support for remote monitoring, tech support or troubleshooting. These support services are increasingly valued by customers of both machine builders and system integrators.

In this survey, 200 respondents, primarily North American OEM design engineers and system integrators, shared their insights on the state of the industry.
Merging Electronic and Mechanical Technologies Transform Machinery
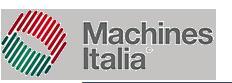
Redeploying waste on a construction site and turning it into a new resource, using digital technologies to create a new architectural material, or making textile dyeing and finishing more accurate are just some of the new processes that Italian companies are making possible using electronic technologies.
Recycling Waste
Conserving resources and reducing waste by reusing it is a priority for companies around the world. MB CRUSHER SpA (mbcrusher.com/us/us) has created machines that do the job in the construction industry, repurposing cement, debris and reinforced concrete in a cost-effective way on building sites.
Many experts consider this debris to be a “seventh resource” that can be of great value. Recycling is an opportunity not only for the environment, but for new revenue. By crushing debris and excavation materials on the site where they were produced, transportation costs, fees and pollution are reduced.
Attachments like the MB jaw crusher bucket travel with the excavator to any site and transform demolition waste into a resource. Debris can be used for filling foundations, pipe excavations, road surfacing or as decorative elements. It also becomes a commercial resource that can be sold to other companies.
Even those materials that some operators consider difficult, such as old light poles, columns, and concrete

pipes, railway sleepers or vineyard poles with spring steel, can be reduced easily. The bucket crusher’s geometry facilitates horizontal crushing, separating the concrete portion from the metal rebar. The iron comes out while the unit is crushing and can be separated from the processed material with an iron separator, which is installed on the MB unit and is controlled by the operator from the cabin. MB Crusher makes five lines of attachments suitable for any brand of excavator, loader or skid steer.
Digitizing Ceramics
Large slabs have taken the ceramics industry into a new dimension that goes beyond solutions for floors and wall coverings. System Ceramics SpA (systemceramics. com/it), part of Italy’s Coesia Group SpA (coesia.com/ en), is a leading operator in the sector’s production chain, contributing to the establishment of large formats.
The company offers a process solution for producing slabs with full-body veining. The resulting slabs stand out for a level of full-body definition, significantly superior resistance and durability, and a versatility of use that enables porcelain stoneware to become a composition element for the world of furnishing and design.
GENESIS is the company’s solution that starts from the ceramic material and traces a new path to countertops, worktops, kitchen tops and all those uses in the furnishing world that require a three-dimensional effect. Digitally managed, it is an extremely flexible and integrative concept that makes it possible to meet current slab production requirements and guarantees limitless aesthetic possibilities.
It’s based on a full-body, three-dimensional decoration process, with digital control of the discharge of the colored atomized powders – whether wet or dry colored, or possi-
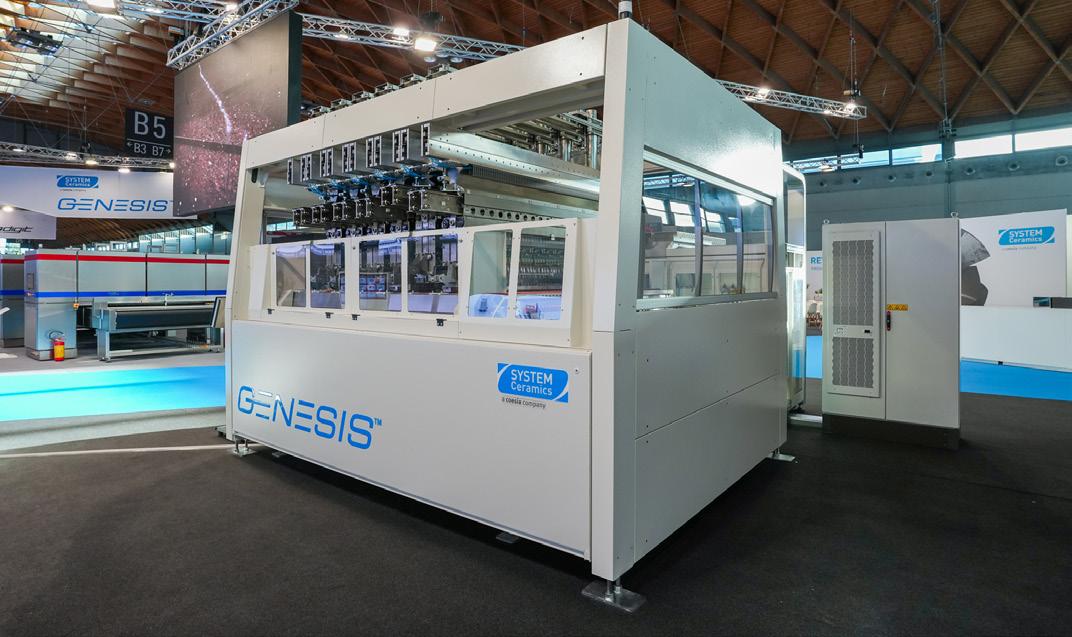
bly ‘salt and pepper’ mixes – in the different chosen points of the slab according to the graphics set-up. Its operation is based on the performance of the powder head which, since there are no moving elements, guarantees high levels of reliability and speed of response.
More Efficient Dyeing
A global leader in dosing and dispensing operations for powders and liquids, Lawer SpA (lawer.com) provides products, solutions and services to the textile industry to increase the reliability, safety and efficiency of their operations. With more than 50 years of industry experience, Lawer’s world-wide presence enables it to serve customers through the whole life cycle of its products.
The accurate monitoring of the dyeing process, the precision of the preparations, the repeatability of the recipes and the perfect traceability of the operations carried

out are fundamental elements of an efficient working process, constant monitoring and cost reduction. The need for a healthy and hygienic working environment, where contaminations and product handling are minimized, are also essential elements for a modern process.
LAWER systems completely automate the preparation of dyestuffs and chemical products. Dosing systems automatically weigh and dose powders, liquid, and chemicals for textile dyeing and finishing. These systems are sold by agencies worldwide, installed and assisted from its Italian center and from after-sales offices located in China, Turkey and via Lawer USA in the United States.
Winding Expertise
Established in 1967, SIMET SpA (simet.it) is a leading manufacturer of winders, assembly winders, de-knitting
winders, winders with air jet, twisting machines for fancy yarns and single head TFO twisting machines. SIMET machines are used in spinning, weaving, warping, twisting, knitting, the socks industry and R&D laboratories.
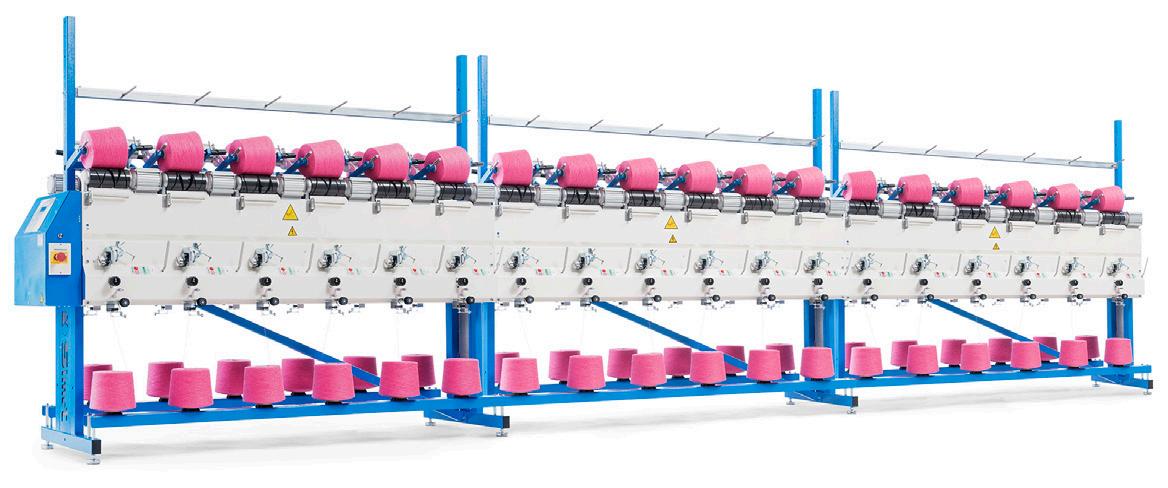
Besides standard machines, SIMET offers customized solutions and exports worldwide over 65% of its production. All products are developed and manufactured in Italy. A member of ACIMIT (Association of Italian Manufacturers of Machinery for the Textile Industry) (acimit.it/en) , SIMET cooperates actively with prestigious universities and research institutes.
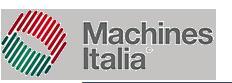
STALAM RF Dryer Eco+
Vega Group (vegagroup.it/en/) has been designing and selling machines for folding and gluing boxes in solid and corrugated cardboard since 1947, when Mario Nava founded the company near Milan. Vega operates in the packaging market and its products are designed for box makers and cardboard industries that need to fold and glue large quantities of blanks or glue different types of solid board sheets. Vega has structured itself through 2 business units - Vega Srl and Meccanica Magentina Srl – to achieve industrial synergies and economies of scale.
Optimizing dryers
STALAM SpA (www.stalam.com/eng/), established in 1978, is a world leader in RF equipment for the drying and thermal processing of raw materials, intermediates and finished industrial products. Its ongoing investments are designed to improve the performance and sustainability of its products, which has led to the development of its new RF ECO+ series dryers.
These efficient machines are designed for medium and large size dye-houses, to meet their high production capacity requirements. Having rated power values ranging from 125 kW to 150 kW, these dryers ensure savings in operating costs up to 20% compared to previous generation machines.
The RF power distribution electrodes have been adequately sized to maintain the lowest possible power density on the product being dried. The air circulation and evacuation systems also assist the evaporation process, maximizing moisture removal efficiency while avoiding all dew condensation problems inside the drying tunnels.
The system makes sure that all machine components and circuitry are in good and safe working order, promptly warning the operator of any problems and providing a detailed diagnosis and troubleshooting advice.
Vega produces reliable and well-known folder gluer machines plus end-line products and a high technology double feeder, strengthened by the acquisition of Revicart in 2018. It offers tailor-made solutions for all its machines, which are composed with standard and extra modules. Customers can add one or more extra modules over the years to improve production for changing needs.
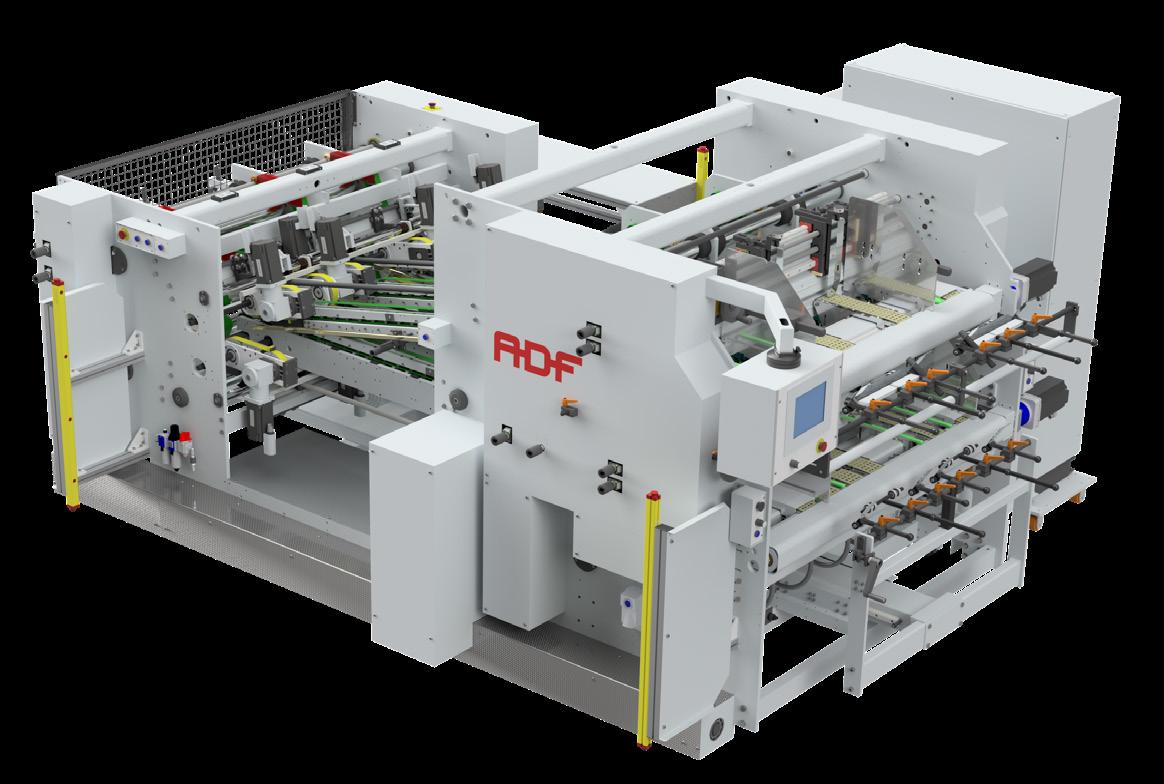
ALTAIR is a historical machine for Vega, developed and refined over a 20-year period but keeping the same name to identify a product that excels in corrugated box production. In 2023 it is releasing the new ALTAIR GT, an even higher performing machine. With up to 90% of its
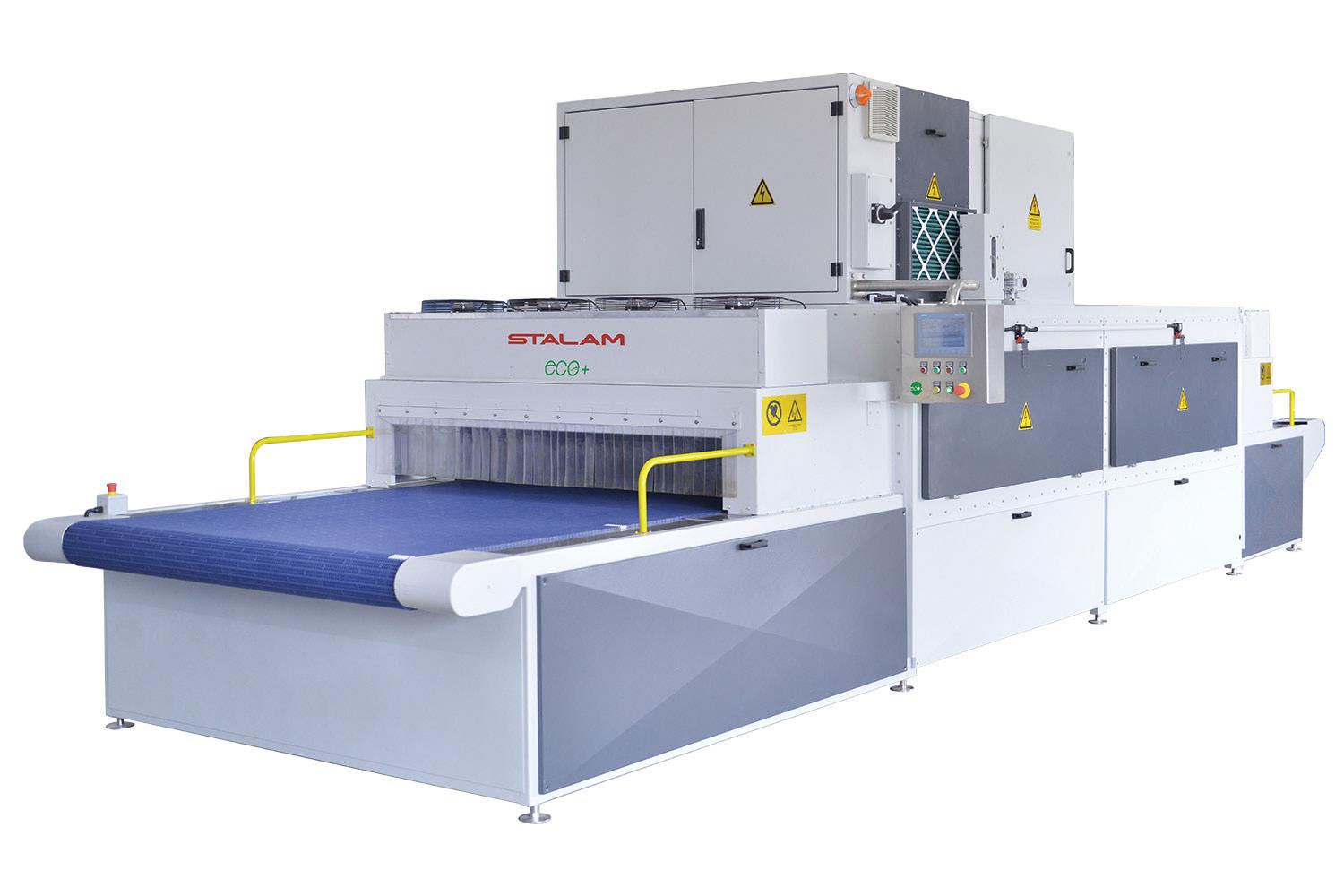
turnover from international sales, Vega has about 4,000 folder-gluers running around the world; the oldest one is still working after 45 years.
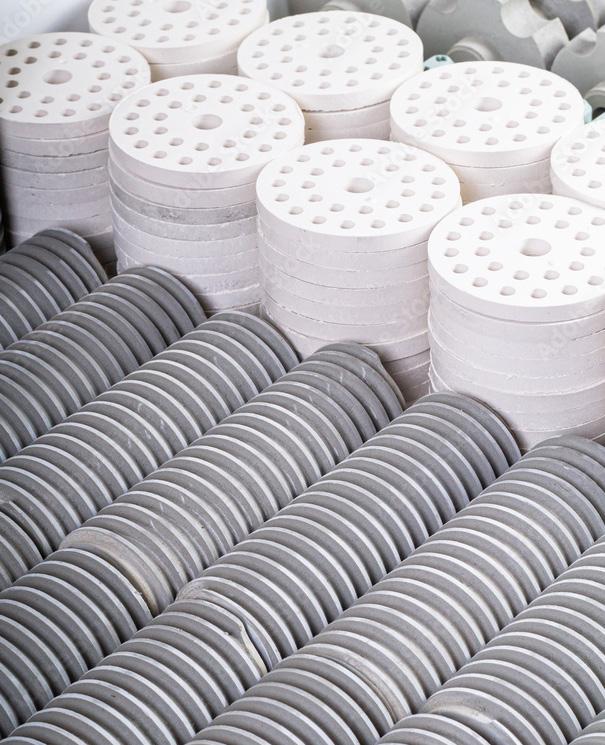
Working with Wood
ACIMALL, the Association of Italian Manufacturers of Woodworking Machines and Accessories, (acimall.com/ en) now represents more than 140 companies. Together they account for almost all the revenues and exports of the Italian woodworking machine industry.

Machines Get Smarter
Italian trade associations are on the front lines of the revolutionary changes happening with machines and manufacturing. While changes extend to every industry, these smart machines are being created even in traditional industries that used to rely almost exclusively on mechanical technologies.
In addition to the woodworking association ACIMALL, these groups include: ACIMAC (acimac.it), the Italian Manufacturers of Machinery and Equipment for the Ceramic Industry, ACIMIT (acimit.it/en), the Association of Italian Textile Machinery Manufacturers, Confindustria Marmomacchine (assomarmomacchine.com/en ), the Italian Association of Producers and Processors of Marbles, Granites and Natural Stones, and ASSOMAC (assomac.it/en), the National Association of Italian Manufacturers of Footwear, Leathergoods and Tanning Technologies.
Through its subsidiary CEPRA Srl, Acimall organizes Xylexpo, the biennial international exhibition of woodworking technology and furniture components. The association publishes the Xylon.it portal and two bimonthly industry-specific magazines, Xylon and Xylon International, distributed around the world. Finally, with Cepra Multimedia, Acimall is providing companies across several industries with communication services, mainly in the digital domain, including dedicated webinars, corporate videos, case studies and direct marketing campaigns.
While having deep roots in Italy, the industry is also active globally. In 2022, the Italian production of woodworking machines and tools amounted to an estimated 2.6 billion euros, up by 4.6 percent over 2021. Export was a key driver of this result, exceeding 1.8 billion euros with a 3.9 percent growth rate.
Italian companes are at the forefront of emerging electronic and mechanical technologies that will transform numerous global industries. From repurposing waste materials in construction sites to digitizing ceramics, improving textile dyeing and finishing, and advancing winding expertise in the textile industry, the smart machinery created by these companies is making it possible for North American manufacturers to produce more with fewer resources, fostering economic growth, creating new products and making production processes more accurate and efficient. The merger of electronic and mechanical systems is changing how people work, particularly here in North America.

Compostable Packaging
Italian companies have long been leaders in the crafting of equipment to make high-quality food products. Today they’ve taken a similar leadership role in making healthy and sustainable products and packaging for the food processing industry.
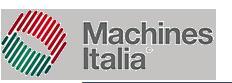
The new Canadian subsidiary of the family-owned Sunino Group SpA, (grupposunino.com/en), OMNIA Packaging Inc. (omniapackaging.ca), is a one-stop provider of innovative and sustainable packaging. This family-owned business is based in Castellamonte (province of Turin), Italy, and has been providing packaging solutions for many generations.
By leveraging the experience and expertise of the Sunino Group – which extends to several markets worldwide and counts a half-century of production – Omnia Packaging Inc. is poised to expertly serve the North American market packaging sector.
Omnia Packaging Inc. is the Sunino Group’s 11th industrial plant. Its 90,000 sq. ft. facility in Guelph, Ontario, was completed in September 2022. The company has two divisions for plastic and paper packaging solutions: Omnia Plastic and Mustang by Omnia Packaging
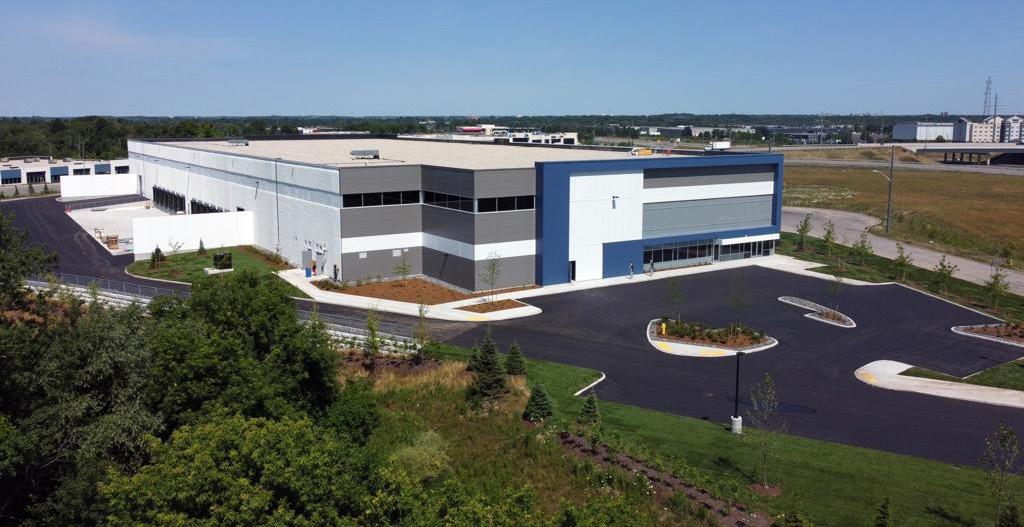
It is now essential to deliver a functional product that
is sustainable as well as cost effective. Omnia Packaging Inc. bridges that gap by offering sustainable, highly performing packaging solutions in paper and plastic through its brands. The Sunino Group had always prioritized sustainability; in Europe the company’s Italian parent company, Plastic Legno SpA (grupposunino.com/en/plastic-legno), received the ISCC Certification for recycled content in Q4 2022.
The Sunino family has specialized for more than half a century in injection plastic molding. It is the third largest worldwide supplier of the Ferrero Group and covers several sectors: food packaging, toys, sport accessories and gifting. Leveraging this expertise is providing Omnia Plastic with the same ability to produce high-precision, injection molded packaging solutions in plastic.
Through Omnia Plastic in Canada, the company will bring streamlined production, cost efficiency, highly repeatable and reliable processes, as well as design cus-
tomization. Omnia Plastic will start mass producing its first plastic tubs by end of July 2023, focusing on reduced plastic use, with lighter walls and no tamper-evident closure, only top sealable tubs and interchangeable lids in several sizes.

Omnia Packaging has also acquired exclusive rights to an innovative technology designed and patented in Italy, Mustang Machine, that thermoforms and heat seals paper trays without the use of any glue. Its paper trays are made of virgin paper; customers can also ask for FSC paper. Paper sheets are die cut and printed without using any oil or chemical derivatives, then thermo formed and heat sealed in paper trays used for fresh produce. This compostable, eco-friendly paper packaging will be used for fresh fruit and vegetables. The top-sealable trays guarantee freshness and shelf life for organic, conventional and greenhouse grown fresh produce. Virgin paper allows for the production of a sustainable packaging solution that is sturdy, clean, humidity-resistant and stackable.
The company will also produce IML in polypropylene using the same material for tubs, lids and labeling. The first available containers for local production will be applicable to the dairy sector, along with several open molds to provide sustainable packaging solutions for dips, sauces, soups and confectionary products. Omnia Packaging has exclusive rights for Canada and can support Canadian growers and packers operating in the Americas.
Preserving health through healthy eating
Arden Zinn always believed that you are what you eat, and that eating fresh and natural foods would make you feel better physically and mentally. When she founded Arden’s Garden, she was dedicated to producing juices and extracts from all types of fruit and vegetables.
She turned to SMI SpA (smigroup.it) the Italian maker of the ASW 50 F Ergon automatic shrink wrapper, to help realize her dream and protect her natural 100% cold-pressed juices, which are made without adding preservatives, water, dyes and sugars. But live juices must be extracted in the correct way, using extractors capable of keeping their properties active.
Arden’s Garden produces a wide range of coldpressed juices, a system that does not use heat, oxygen or other pasteurization methods that can damage the nutrients found in fruits and vegetables. The Atlanta-based company also makes other foods, such as raw, nutrient-rich vegan snacks made with nuts, rolled oats, kale, cashews, almonds, peanut butter and chocolate.
Since Arden’s death in 2020, her daughter, Leslie, has continued her mother’s legacy. Arden’s Garden is also focused on environmental sustainability. In the manufacture of smoothies, for example, straws are not required as the containers have lids with spouts. Plastic containers and bottles used by the company can be recycled.
To meet the needs of such a varied production, the company uses the latest generation SMI systems, which are flexible and adaptable to the needs of a constantly evolving market, using innovative technical solutions that allow simple, fast and economical format changes. The compact shrink wrapper installed at the Arden’s Garden plant easily adapts to end-of-line logistics conditions. It is equipped with a single lane infeed system and includes a film cutting unit with direct drive motorization that improves cutting precision and simplifies maintenance.
Atlanta is also home to SMI USA INC. (smiusa-co. com), the subsidiary of SMI SpA that since 1999 has been present in the United States to meet the needs of customers in North America.
Better Drying
RF Systems Srl (www.rfsystems.it) has introduced its ARIES radio frequency (RF) dryer for industrial bakery or confectionery applications. It has been specially developed to remove excess moisture from food substrates in minutes,
becoming superior technological solution for quality drying processes in many categories of food products
RF drying is particularly suitable for bakery products (biscuits, wafers, cream puffs, crackers, rusks, etc.), unlike drying with traditional ovens, which are difficult and not very effective due to the formation of a crust during baking, surface browning and high process costs. It guarantees perfect and totally uniform drying in a few minutes without causing browning or coloration of the product. It also increases shelf-life and reduces the risk of cracks and fractures in the products.
The introduction of Aries equipment in bakery production guarantees outstanding benefits compared to traditional ovens, including higher product quality and easy
integration into any production line. Aries also increases productivity, reduces operating costs and improves process control.
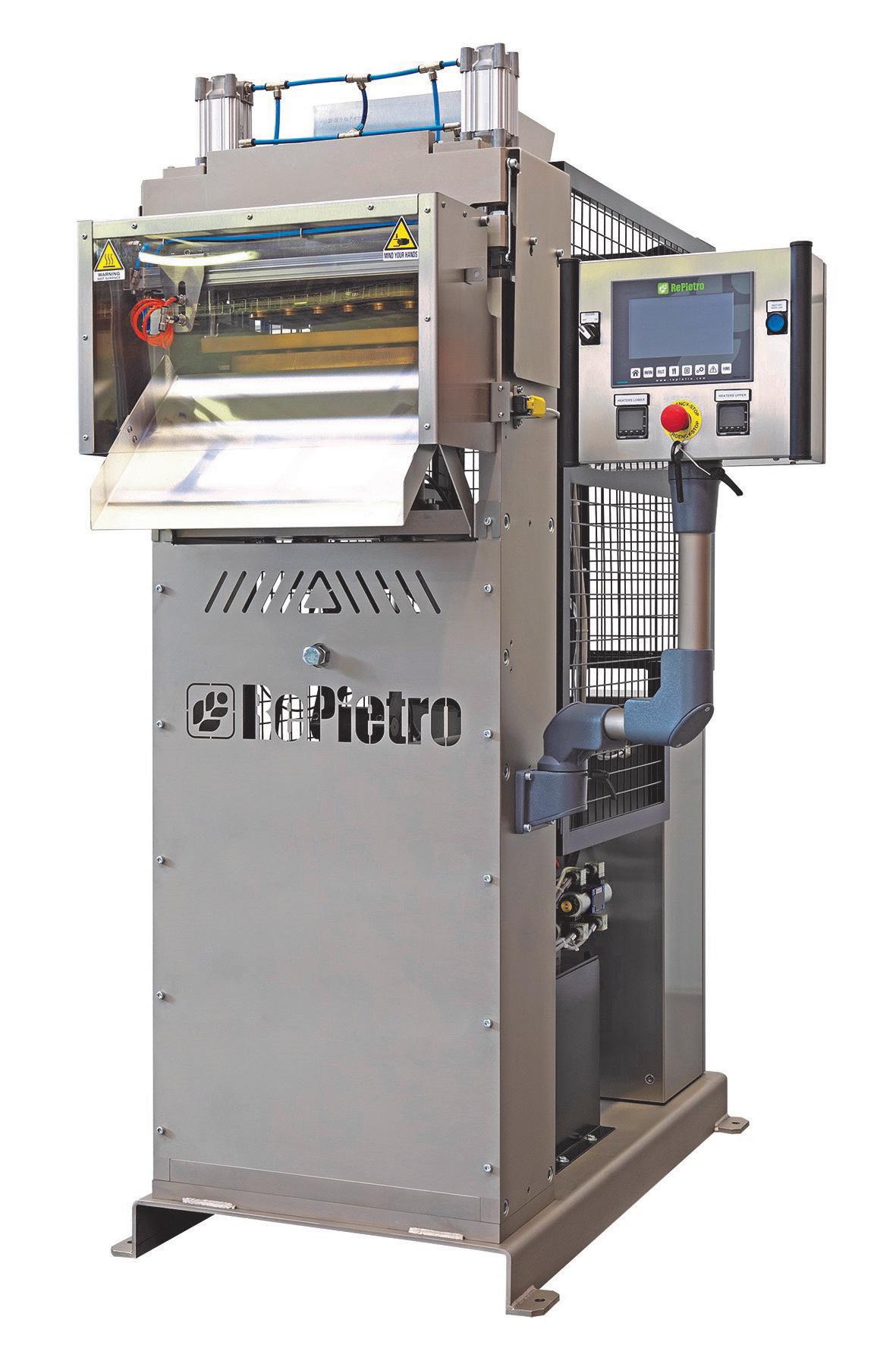
RF Systems has also introduced a food defroster for the rapid tempering and defrosting of meat, alternative proteins, seafood, vegetables and other food products. The compact Coldwave+ achieves defrosting in minutes rather than hours/days, even for large product blocks and, if necessary, directly inside packaging used for storage (carton boxes, polyethylene bags, etc.).
The process speed and uniformity minimize product degradation. There’s no deterioration of sensorial, chemical or physical properties. Defrosting is carried out continuously, with significant logistics advantages in product handling and production scheduling.
Transforming Grains
RE PIETRO Srl (repietro.com), founded in Milan over 90 years ago, has developed the Popping Machine RO-EVO to transform cereals (like rice, corn, wheat and buckwheat and legumes) into puffed cakes or very thin popped and no-fried snacks to meet growing consumption trends. Using the new popping machine adds value to the raw material, maintaining its taste and freshness, and also offers customers a product with a wide choice of flavors and shapes. As a healthy alternative to conventional bread, they provide a versatile carbohydrate supply during meals, a crunchy snack or a decoration for dishes and desserts. Once a mold has been chosen and installed, the popping machine consistently transforms cereals and/or micro-pellets into cakes or snacks. Its efficiency and flexibility allow it to produce a wide range of products as required, using only one press. The machine is equipped with a hydraulic system that produces the high pressure needed for expansion of the cereals or micro-pellets. From the HMI it is possible to set up each production phase, to save the recipes and check any malfunction using an efficient diagnostic system.
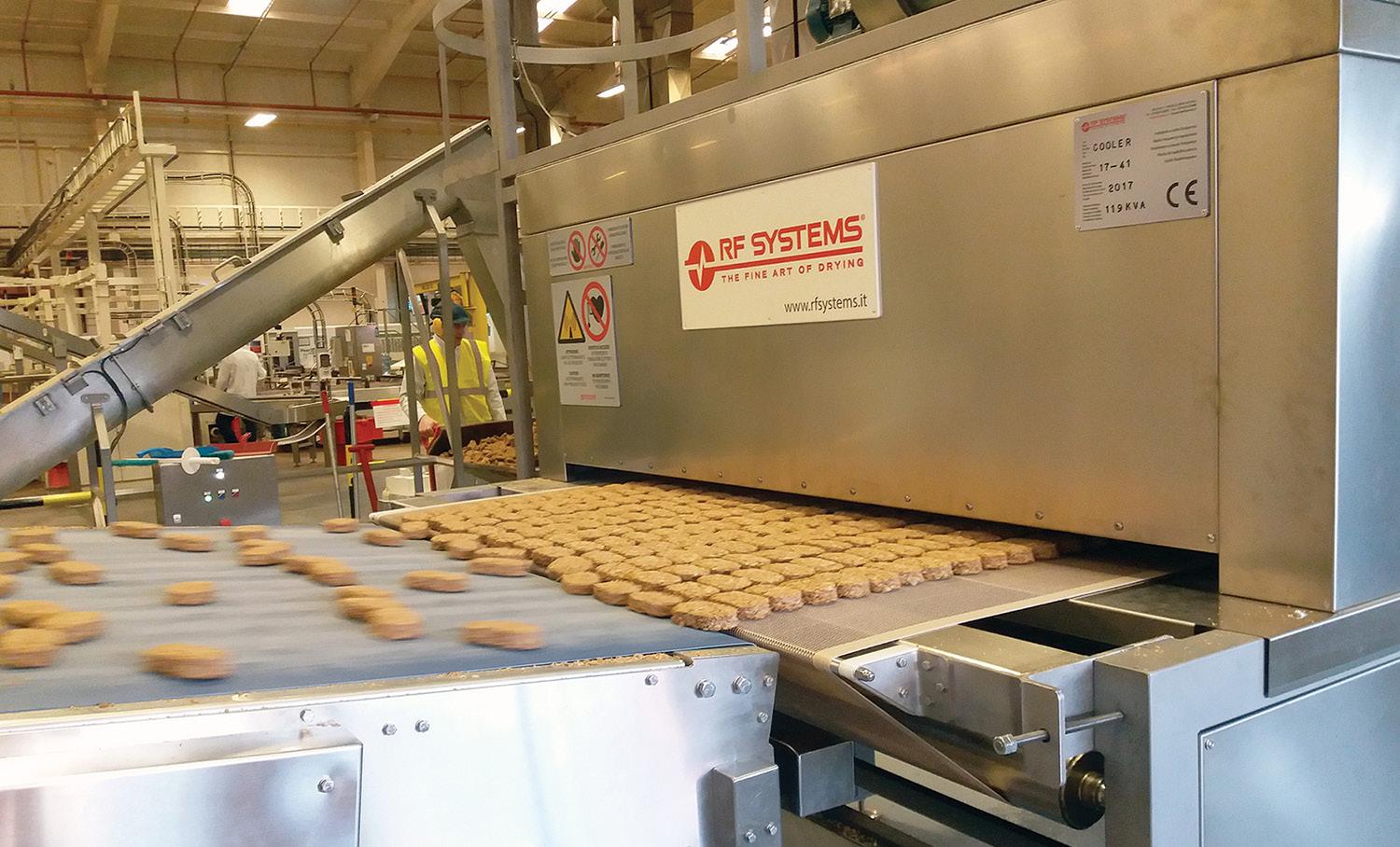
Supporting the Industry
A number of Italian trade associations provide guidance and support for the companies involved in creating equipment for the global food industry. These associations include: ASSOFOODTEC / UCMA (anima.it/associazioni/ elenco/assofoodtec), the Italian Association of Machinery and Plant Manufacturers for Food Production, Processing,
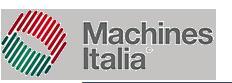
Preservation, and FederUnacoma (federunacoma.it/en/), the Italian Agricultural Machinery Manufacturers Federation. These associations and their member companies work to build awareness about the quality and productivity of Italian-made equipment in North American and global markets.
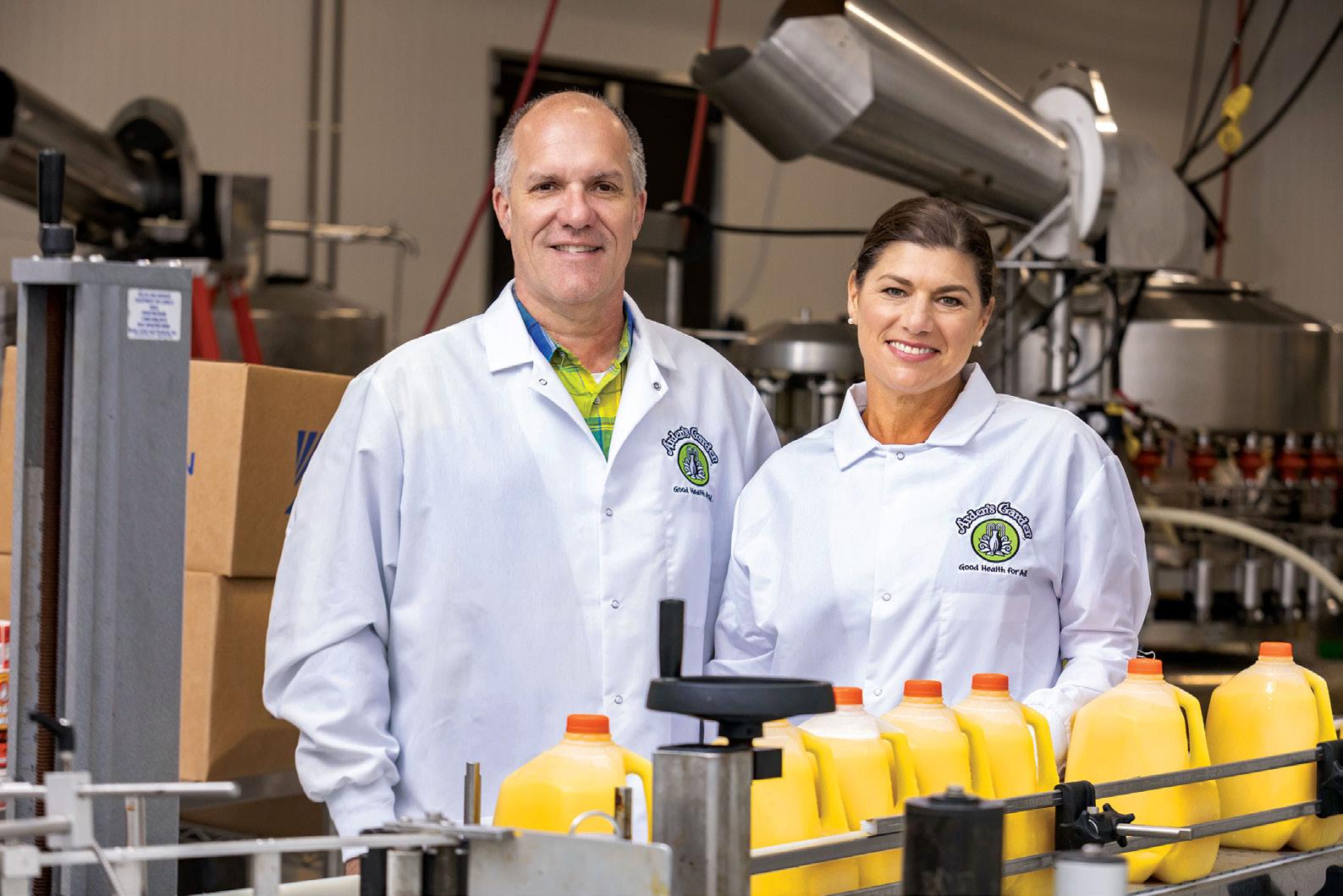

The continually evolving advance of electronic technologies into Italian agricultural and food processing equipment is improving the quality of the food we eat, the choices we have as consumers, the sustainability of the food processing and packaging machines the industry uses, and the productivity of food and beverage processors. More than 90 percent of the machines created by this Italian industry segment are now exported around the world.
The continually evolving advance of electronic technologies into Italian agricultural and food processing equipment is improving the quality of the food we eat, the choices we have as consumers, the sustainability of the food processing and packaging machines the industry uses, and the productivity of food and beverage processors. More than 90 percent of the machines created by this Italian industry segment are now exported around the world.

Italian Machine Builders Are Creating New Ways to Build Products the World Needs
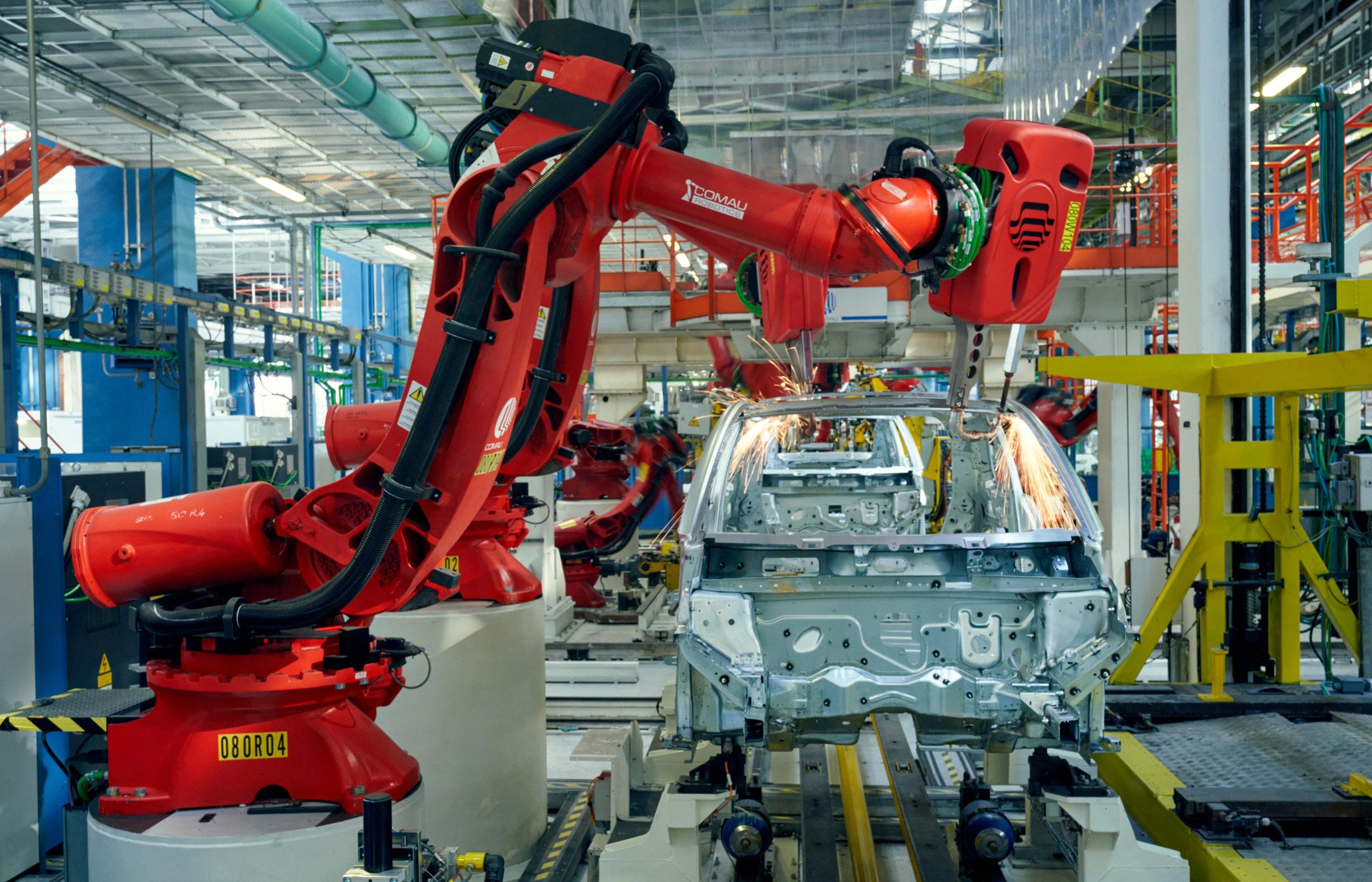
Italian companies are investing in creating more powerful and longer lasting batteries, 3D sensors and other quality control systems for developing new e-mobility motors, energy saving designs and advanced software for improving textile manufacturing and recycling. Explore how these technology advances are shaping the future of machines and manufacturing around the world.
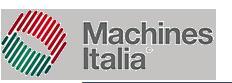
Green Power
To fully support international environmental goals, Comau SpA (comau.com) is developing cutting-edge
energy solutions that increase performance while lowering overall environmental impact. From high-performance battery manufacturing solutions for the naval, automotive and many other industries, to automating the production processes for wind, solar and hydrogen systems, Comau is helping empower green energy worldwide.
Comau’s history of solving challenging technical problems goes back almost 50 years. Founded in 1973 by a group of Italian engineers based in Torino, by the mid-1980s the company had already developed the first robotized automation system and the first hydraulic robot. Comau’s
Top Technologies
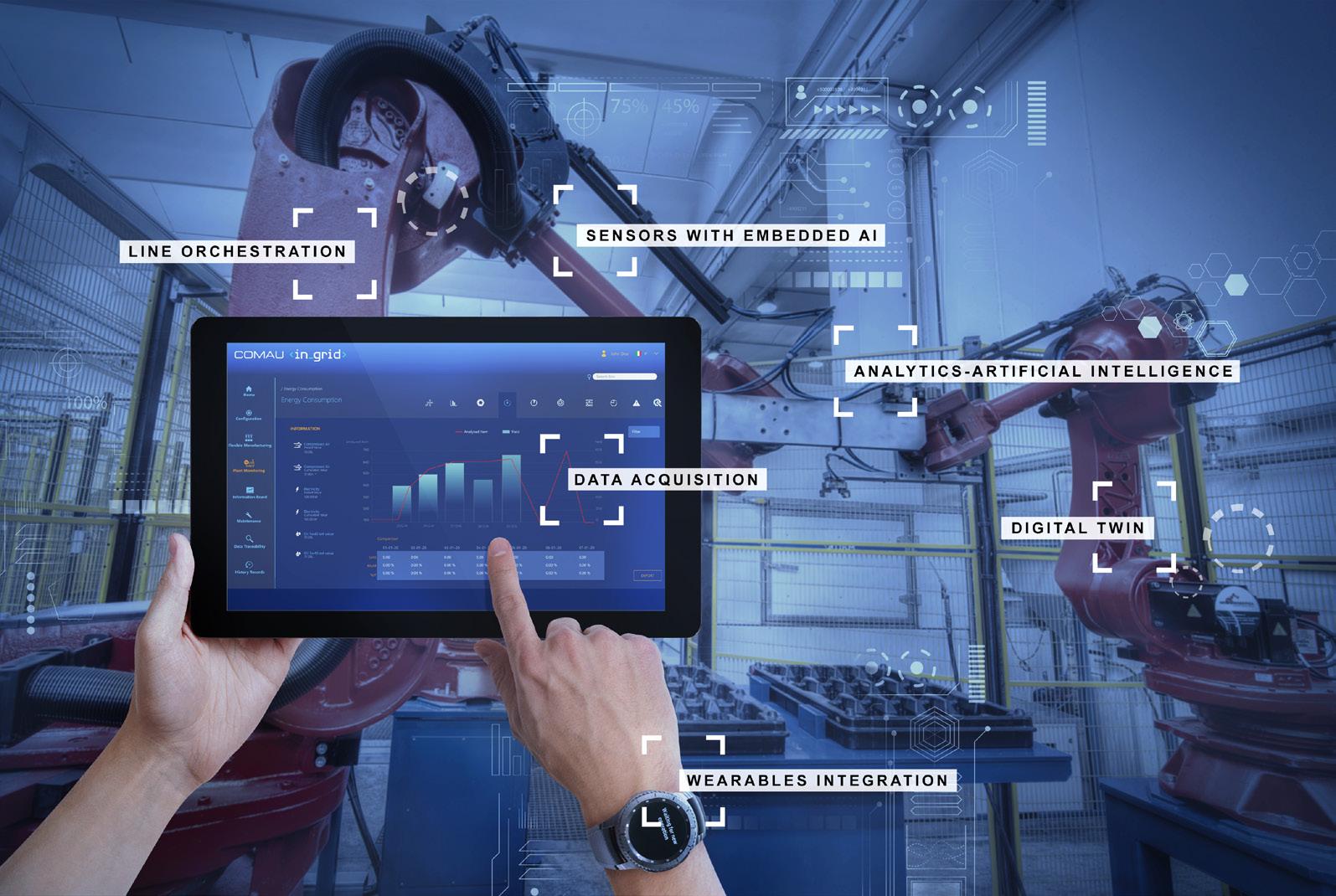
innovations in electrification, digital intelligence, advanced robotics, mobile technologies and smart factory enablers form the backbone of its commitment to empowering green energy supply, storage and transformation, helping promote and enable a cleaner, more sustainable future.
Leveraging its strong history of applying advanced research and innovation to manufacturing processes within mission-critical industries, Comau is also becoming a trusted point of reference for solar and wind energy, in addition to other renewables. Since wind and solar energy are expected to drive the renewable energy market over the next several years, automation can play a decisive role in operations and maintenance, as well as components manufacturing.
And when one of the top electricity companies asked Comau to help design a revolutionary approach to solar panel installation, its engineering team was quick to respond. Today, in addition to automating the outdoor installation of photovoltaic panels directly in the field, Comau has extended its focus on solar energy by developing a novel solution for the on-site production and assembly of solar blades.
Similarly, Comau developed an automated manufacturing system to produce 100+-meter-long wind turbine blades that helps reduce production costs and lead times, allowing wind power suppliers to better meet market demands. The project combines multiple articulated Comau robots with an overhead gantry system to automate the gel, glass fiber layup and gluing processes for the blades.
Comau has also begun developing automation solutions for the hydrogen sector to help facilitate the creation
of reliable, zero-emission power. Hydrogen use is expected to double over the next decade, largely driven by new applications in mobility and energy storage. This should also boost the demand for electrolyzers from an estimated 120 MW installed in 2020 to more than 20 GW expected in 2030. The market for fuel cells could grow from a few thousand fuel cell units deployed in 2020 to 1.2M units by 2030, equivalent to more than 100 GW of hydrogen energy.
To achieve this goal, Comau is working toward lowering the price point of fuel cells and electrolyzers by developing a proprietary solutions portfolio that automates key process steps, including cell preparation and stacking, leak testing and more. By industrializing the largely manual manufacturing environment, it can help fuel cell manufacturers scale-up production volumes and increase the quality of the high-precision process. Automation should also reduce operating costs by up to 20% due to increased precision and the reduced burden of cleanroom security measures.
Comau has also developed solutions for the automated production of lithium-ion battery modules for the naval sector that allow Leclanché, a company specializing in the production of lithium-ion cells and energy storage solutions, to increase its work capacity by up to six times. The solution both automates complex manual processes and reduces operating costs by up to 20%.
For energy transition to be truly sustainable, it is also necessary to manage the end-of-life environmental impact associated with batteries used to power ships, trucks, heavy rail and passenger vehicles. Comau has joined the “Battery regeneration project” and the Flexible Battery Dismantling (Flex-BD) project, working together with other partners to automate battery dismantling operations.
E-mobility motors
The transition to e-mobility is a major technological change for car manufacturers world-wide, who have to install new production lines and new quality control sys-
tems for electric motors. MARPOSS SpA (marposs.com/ eng) has a 70-year history in the field of quality control for the automotive industry.
Electric mobility has been a driving force behind the introduction of new measurement technologies, such as optical gauges, that are necessary to meet the changing needs of the industry. The traditional product lines are now complemented by new applications of optical technology for the components of the electric drive unit.
All vehicle manufacturers are accelerating their e-mobility development activities, according to UCIMU-SISTEMI PER PRODURRE (ucimu.it/en), the Italian Industry Association for Machine Tools, Robotics and Automation. As a result, the distance between R&D phases and a production launch is shrinking, which makes it increasingly necessary to control components in the phases where they are continuously revised and updated.
The flexibility of optical gauges is a crucial asset, as they can measure components of different shapes and sizes within very short cycle times. Optocloud 3D sensors from Marposs can perform more complex controls, such as in the case of electromobility, that are related to dimensional control and the inspection of the assembled stator, before or after the twisting operations and subsequent welding of the ends of the hairpins.
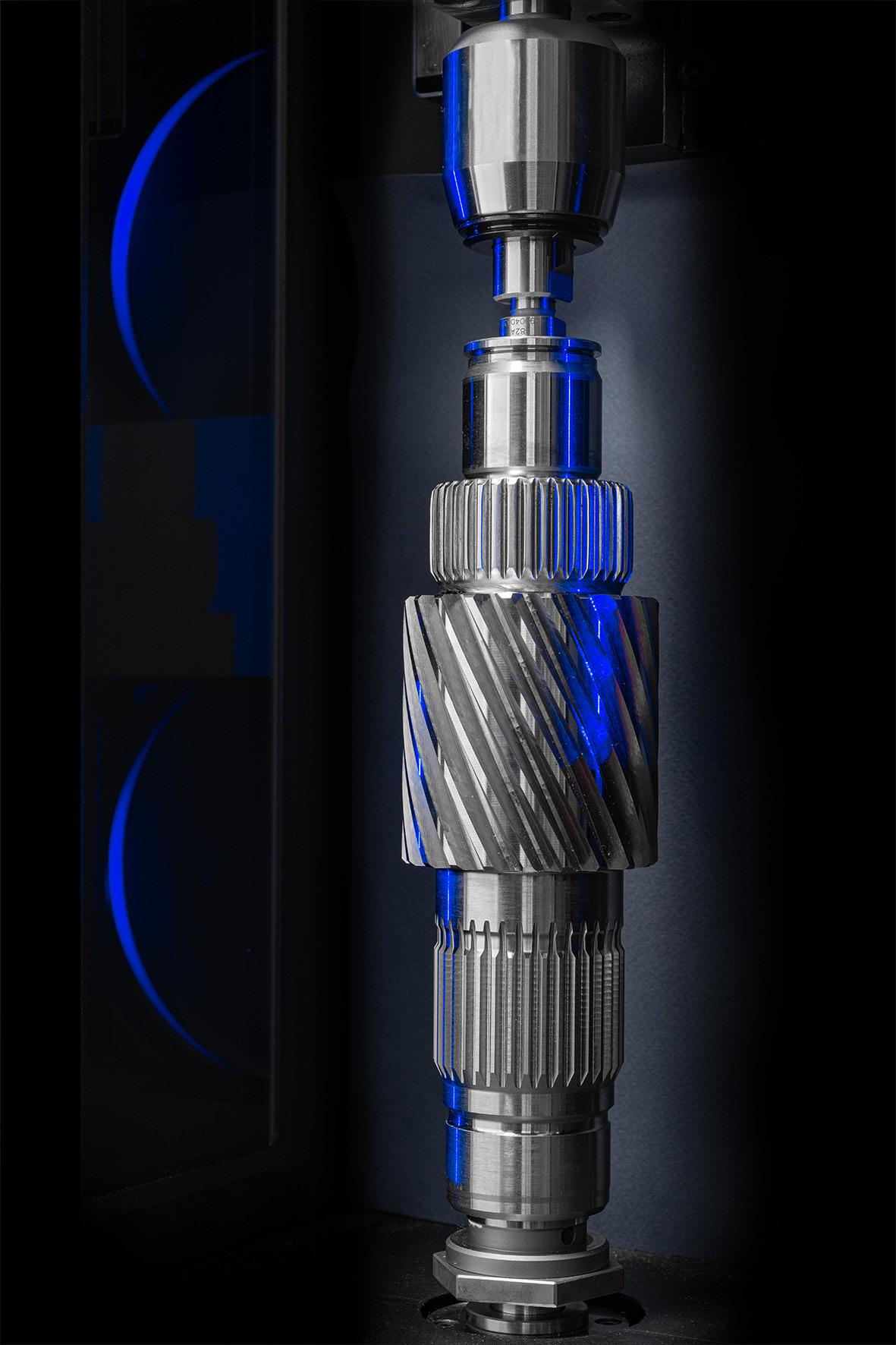
Innovating Fabrics
MARIO CROSTA Srl (mariocrosta.com) is a world leader in the production of textile finishing machinery. With the adoption of increasingly advanced technologies, textile machines are radically changing the way products are manufactured, enabling faster and more efficient production. The advent of the technological revolution has changed the company, reducing the manual workforce and increasing the research and development department, so that it remains a pioneer in developing machinery.
There are many advantages for textile manufacturers to this technology leadership, including the ability to produce customized and innovative fabrics. In 1981, Mario Crosta was the first company worldwide to apply newly released and updated inverters to its textile machines, guaranteeing a huge competitive advantage over others in the industry.

In 1993, a milestone was reached when Malden Mills, Ma. (later named Polartec) decided, after years of research, to rely on Mario Crosta to launch the revolutionary and never-before-seen Polar Fleece fabric into the market, which has marked the world of fashion for the last 30 years. Since then, many global companies have contributed to the widespread diffusion of these high-tech, high-performance fabrics, especially in the military and sports fields.
This collaborative model remains the cornerstone of the company’s new machine designs, enabling it to innovate in the fields of sustainability, digitalization and technology (S-D-T), also key themes of the Italian machinery
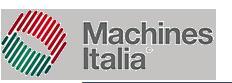
Top Technologies
association ACIMIT, Association of Italian Textile Machinery Manufacturers (acimit.com), where CEO Mario Crosta is a board member.

The company’s Energy Saving System (ESS) is an electronic configuration that allows energy savings of up to 35 to 55%. It enables energy sharing and recycling, using advanced software and state-of-the-art technologies to create machines whose electronic components are designed and built in-house.
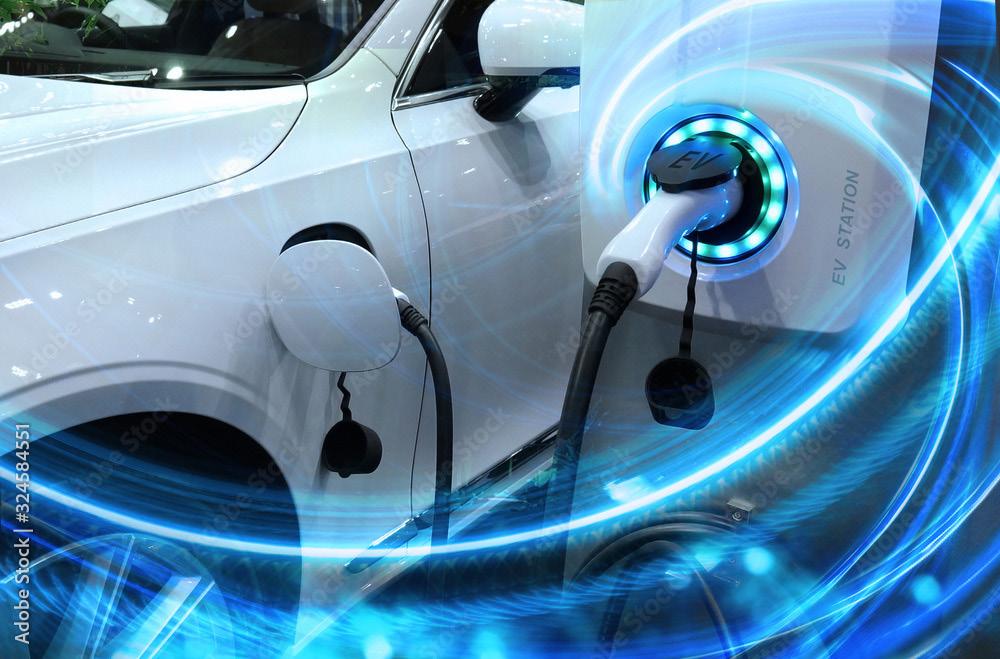
Recycling Textiles
A circular economy and recycling, as well as sustainability, are very important topics today in all industrial sectors globally, but particularly in the textile industry where Mesdan SpA (mesdan.com) has introduced new solutions to ubiquitous challenges.
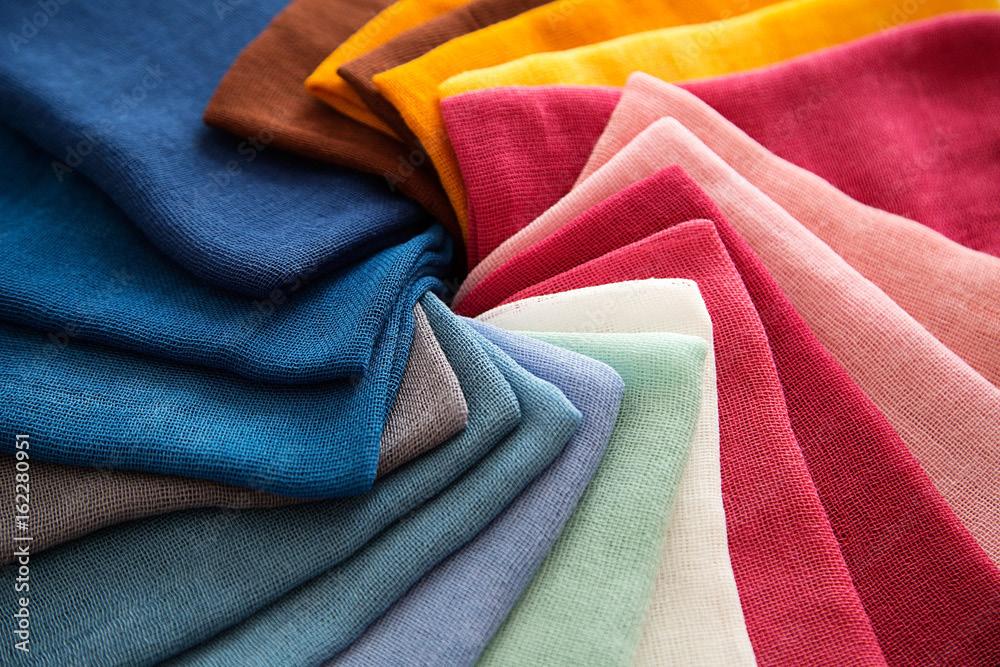
To reduce textile wastes and the consequent environmental pollution, international directives demand textile mills use a certain percentage of recycled fibers in their spinning process. But fabric shearing and shredding stresses the fibers, reduces their original length and makes it extremely difficult to spin a 100% recycled fiber composition.
For downstream processes, and particularly for ring spinning technology, it is necessary to blend in virgin fibers with a length that allows them to be spun in traditional machines. As well as the analysis of the recycled fiber features, an experimental study of the blending and testing of fibers with different technical characteristics, and blending them with different composition percentages, is required.
The Mesdan-Lab “Mini Spinning Line” can quickly perform those trials on a small scale by processing only 50 grams of fiber, with small machines occupying a compact space, consuming minimal power and raw materials. This permits different testing to identify the best blending approach, which is then reproduced in large scale production.
Mesdan equipment is frequently used to test the spinnability of new natural fibers of vegetable origin, like bamboo, ramie, abaca, kenaf, pineapple, milkweed, and fibers derived from birch bark or coconut palm leaves and other plants. Additionally, fabric wastes of expensive fibers like carbon or aramid can be recuperated and spun again, then blended with other spinnable fibers.
Small volumes of trashed garments and most textile production can also be processed to obtain additional fibers for lab scale recycling R&D projects.
These are just a few of the ways Italian companies are investing in developing cutting-edge energy solutions and advanced technology to improve the manufacturing process across multiple industries, including electric vehicles and textiles. These industries are also focused on developing circular economies, which will reduce levels of pollution and improve the health of millions of people around the world. In doing so, Italian companies will continue shaping the future of manufacturing by leading and empowering a cleaner, more sustainable future.
A Respect for Craftsmanship Matches Workforce Skills with Technology
Italian companies have long been admired for their craftsmanship and respect for the expertise of their workers. Workforce training is an integral part of their culture. Today, as electronic technologies transform how machines are designed and built, training is evolving to keep skills aligned with new machine capabilities.
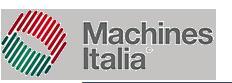
Merging Artistry, Technology
Since its birth in the early 1900s, when the Biella region of northern Italy was establishing itself among the most important textile districts worldwide, BONINO CARDING MACHINEs Srl (bonino1913.it) has developed a leadership position in the carding industry. This reflects its commitment to excellence, born of true artistry but equipped with the best electronic systems on the market.
The combination of mechanics and electronics results in increasingly automated and interconnected production models, with intelligent processes and communicating devices that allow greater performance in terms of productivity and energy savings.
Bonino’s philosophy of “tailor-made” equipment is aimed at making machines “speak” to aid their use by operators. In addition, the company also designs software that provides constantly updated production data that can be analysed in real time by the customer’s business units. This translates into leaner and more fluid work processes. Remote control and tele-assistance services play a crucial role in what Bonino means by the offer of not only superior technology, but also an eye of care for the customer, respecting what is the most human part of the company’s work.

Top Technologies
Training skilled workers
Construction is a highly competitive business that requires learning and implementing new customer solutions as fast as the industry is changing. SOILMEC SpA (soilmec.com) trains workers for the next generation of powerful machines and data-driven services, drawing on its 50-year global history in the deep foundations market.
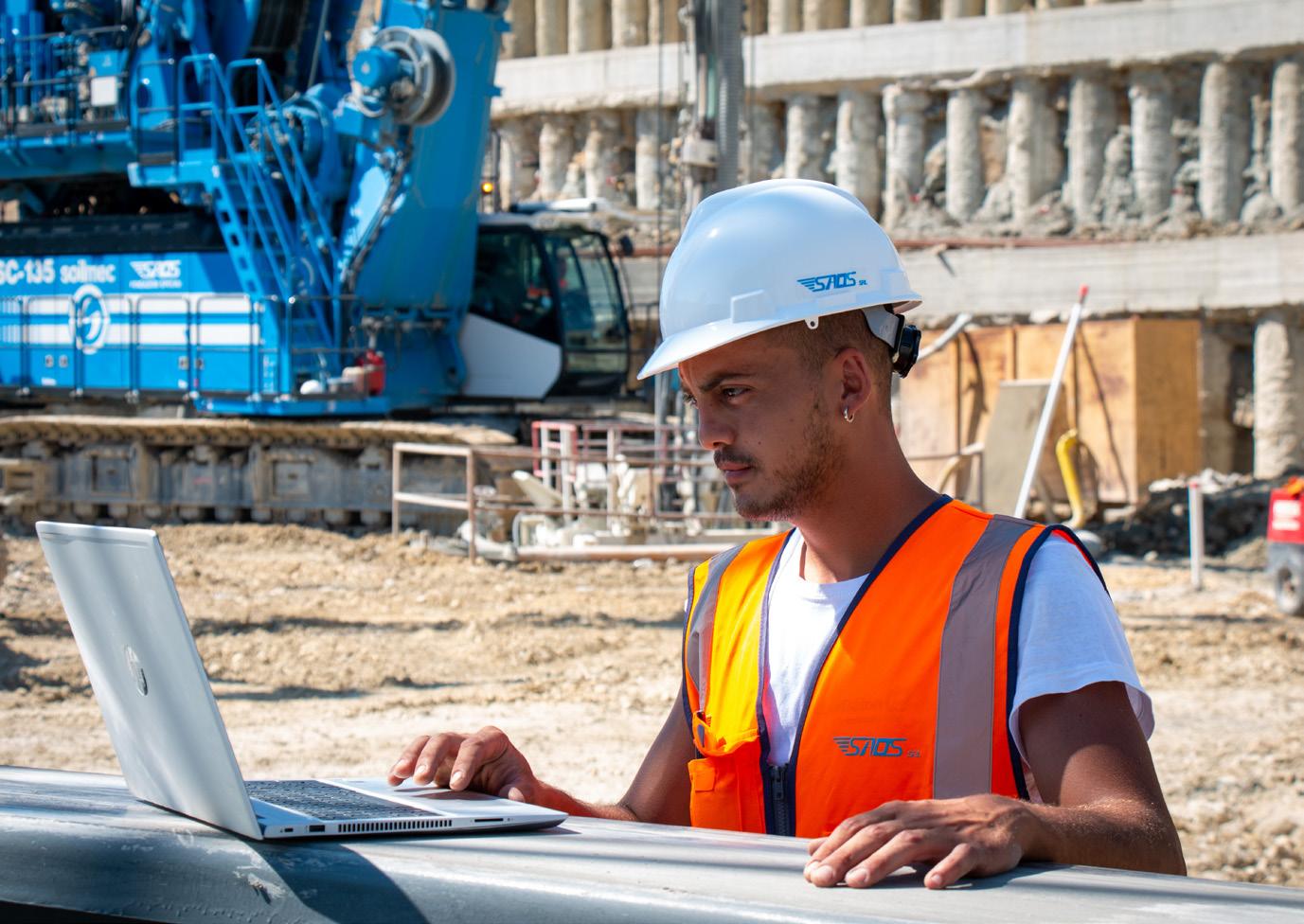
Promoting quality in education has always been a priority for the company. It supports training and skills
Smart tools
Ferrarini & Benelli Srl (ferben.com) is a leading Italian manufacturer of Corona surface treatment systems, in business since 1965 and based in Romanengo (Cremona), Italy. Corona treatment is aimed at improving the characteristics of adhesion and wettability on a wide range of substrates, including plastic and metallized films, plastic-coated paper, sheets, foil, laminates, labels, and every substrate used in flexible packaging or in special applications.
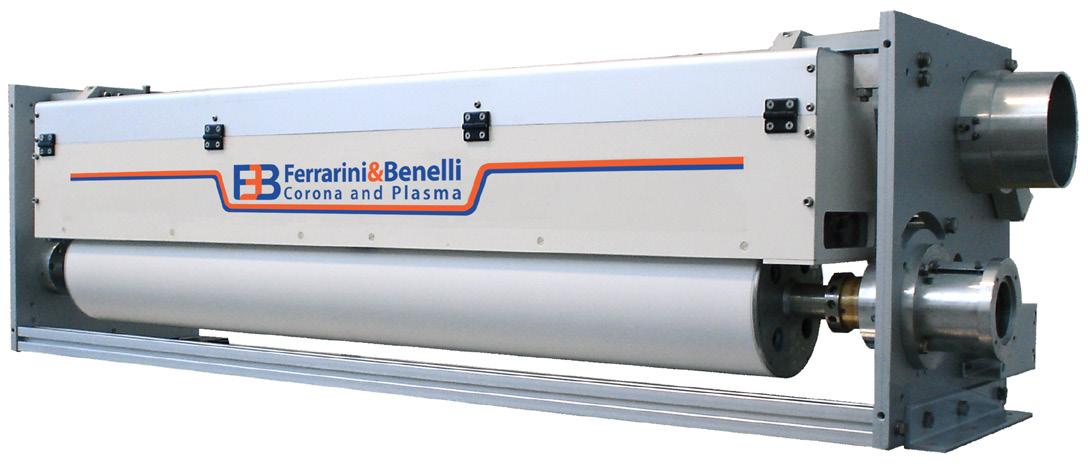
Corona treatment systems are formed for each application (extrusion, printing, converting, as well as any application of flexible packaging processing) and digital generators. Evo Smart, a new digital generator equipped with a touch screen HMI display and user-friendly interface, has been developed to reach the power needed to process any type of substrate at the highest line speeds.
development at all levels and job roles. The Foundations Technology Academy (FTA) started as an international training center for ground engineering professionals in 2006. Today FTA helps address construction challenges and piling needs through hybrid and simulation-based educational programs. This facilitates sharing best practices and encourages digital adoption to ensure safety, quality and sustainability in worksites around the world.
Courses are available in different formats to ensure accessibility and ease of use, including classroom teaching, e-learning, field practical training, simulation programs and coaching. By utilizing the data coming from on-board devices, FTA enables intelligent machine control to increase operational safety, equipment lifetime and availability.
The multilingual and easily browsable navigation system allows for immediate management of all working parameters and enables real-time monitoring of production data from many devices. Owing to the innovative characteristics of the system, data may be stored on SD cards for downloading to a computer via USB stick or be connected to the FB Cloud Platform, where customers and technicians can monitor production in real time and provide assistance and maintenance advice.
Evolving Glass
The glass industry is constantly evolving as the needs of customers, the imagination of architects and market requests change. One thing does not change, however: The processing of tempered glass is always very difficult to standardize because the dimensions, thicknesses and characteristics of the glass are always different. The recent energy crisis has also prompted many glassworks to look for machines with low energy consumption.
This evolution requires major efforts on the part of machinery manufacturers, who must constantly update
their products, the workers who design and build them, and the customers who buy them and use them in their daily work.
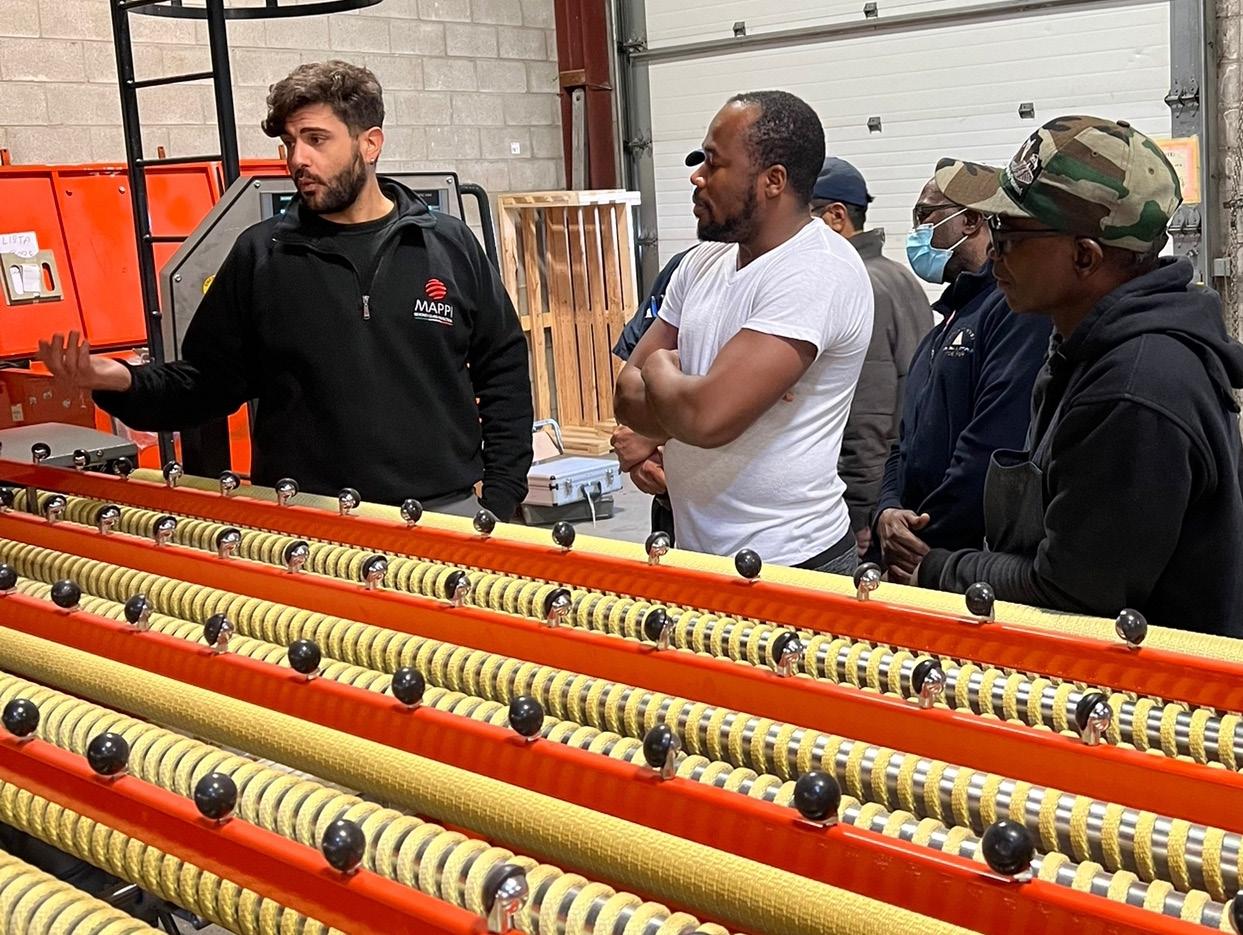
“Listening is the basis of all our work,” says Giulio Dalla Costa, chief designer at Mappi International Srl (mappi.us) “You cannot design an oven if you have not experienced the daily life of the glassworks from inside and if you have not fully understood the needs. When I add a new person to our staff, the first thing I look at is not the curriculum but the passion, the desire to understand, to learn, to innovate.”
The training of technicians and specialists who deal with the construction and maintenance of Mappi hardening furnaces is a daily activity. Specialist courses, study trips to glassworks to get to know every aspect of the work, sharing meetings and direct interaction with customers, are just some of the stages of a work that never ends, because the glassware system has many elements of variability and big areas for improvement,” explains Giulio.
Advancing Packaging
MOSS Srl (moss.it) specializes in printing and finishing equipment for primary rigid packaging. Established in 1967 in Reggio Emilia, in the heart of the Italian packaging valley, the company offers screen-printing and dry-offset machinery suitable to process a wide variety of plastic and aluminum items and containers.
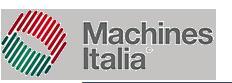
With more than 50 years in the global packaging market, MOSS has developed several solutions to respond with flexibility to the dynamics of vast and highly segmented markets, including beverages, luxury makeup, cosmetics, industrials, and pharmaceuticals. Its machines incorporate state-of-the-art technologies and the use of LED curing technology and efficient power management to reduce their environmental impact.
Advanced servo-controlled machines have CNC capabilities and motion control functions that help operators in the use and maintenance of the machine and expedite changeover operations. All MOSS machines have connectivity features that allow remote access, simplifying information management and reducing the time and cost of assistance and troubleshooting. Dedicated in-person training helps customers with the use of machines, inks, printing techniques and related technologies. The company’s remote education programs have proven to be an efficient mentoring tool.
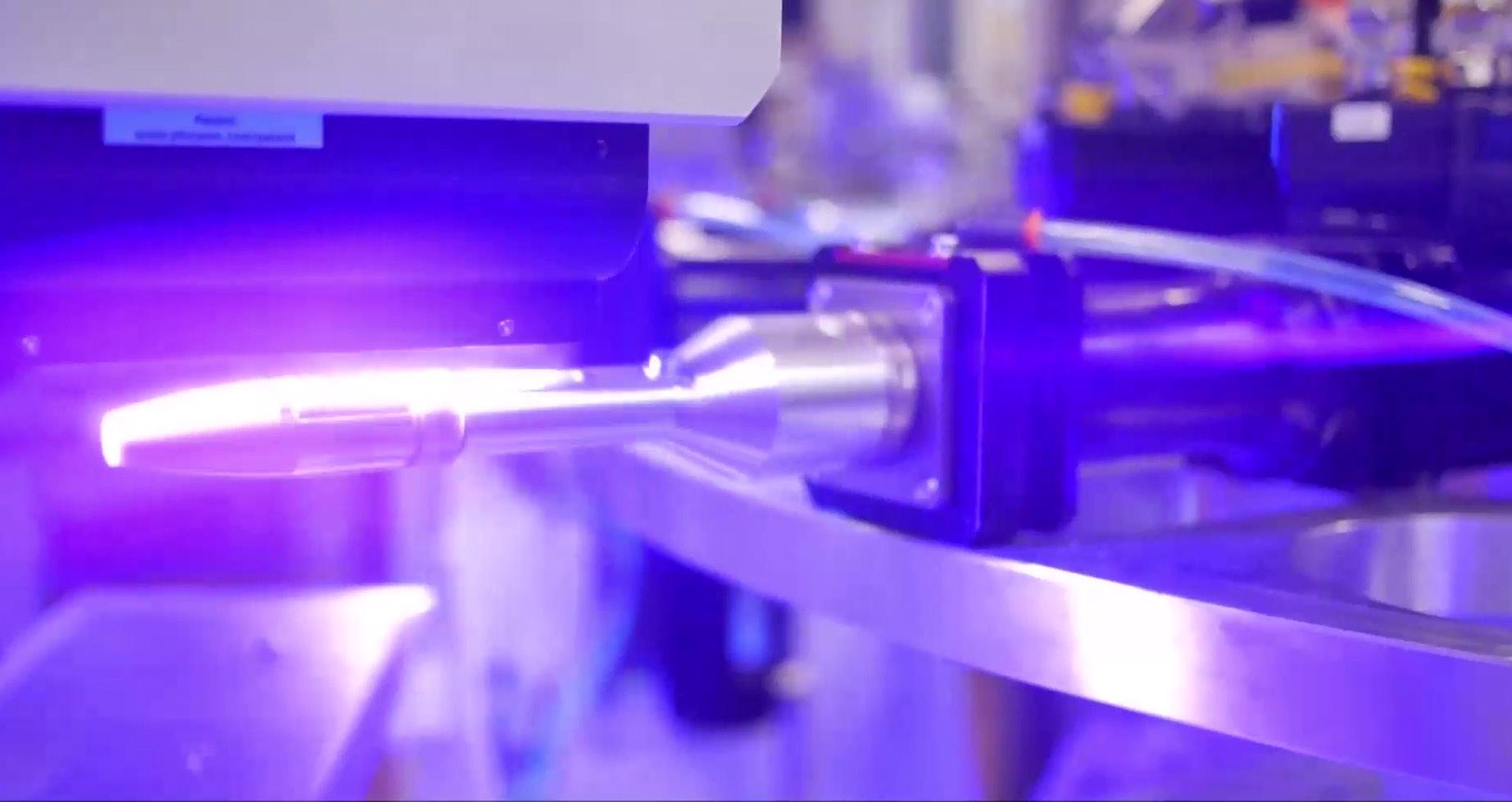
Top Technologies
The opening of a subsidiary branch, MOSS North America Inc. in Sunrise, FL, will enable focused customer support and spare parts service throughout North America.
Recent surveys by the Study Center within ASSOMAC, the National Association of Italian Manufacturers of Footwear, Leathergoods and Tanning Technologies, (assomac.it/en), reveal how manufacturing production processes are reconfiguring from the pandemic and recent economic crisis. This reconfiguration is being affected by a series of both macroeconomic and microeconomic factors. Disruptions between economic blocs, climate change, the fragility of supply chains, changing online consumer purchasing behavior, efforts to develop new ways to attract consumers and the Internet of Things (IoT) are all contributing to economic and social change.
The transition towards a sustainable, responsible, and transparent production model has already started in an irreversible way. Institutions and public opinion in developed countries have taken positions that are rapidly directing regulations, technological investments, and finally demand consistent with global objectives of environmental and social protection.
It is impossible to ignore the estimated data: the enlarged fashion and clothing sector is held responsible for the second largest contribution to CO2 production and the second largest consumption of fresh water in the world. It also employs about one-sixth of the world’s entire workforce, while accounting for a much smaller fraction of the global GDP.
Two considerations and two consequent economic and technological challenges can be deduced. The first
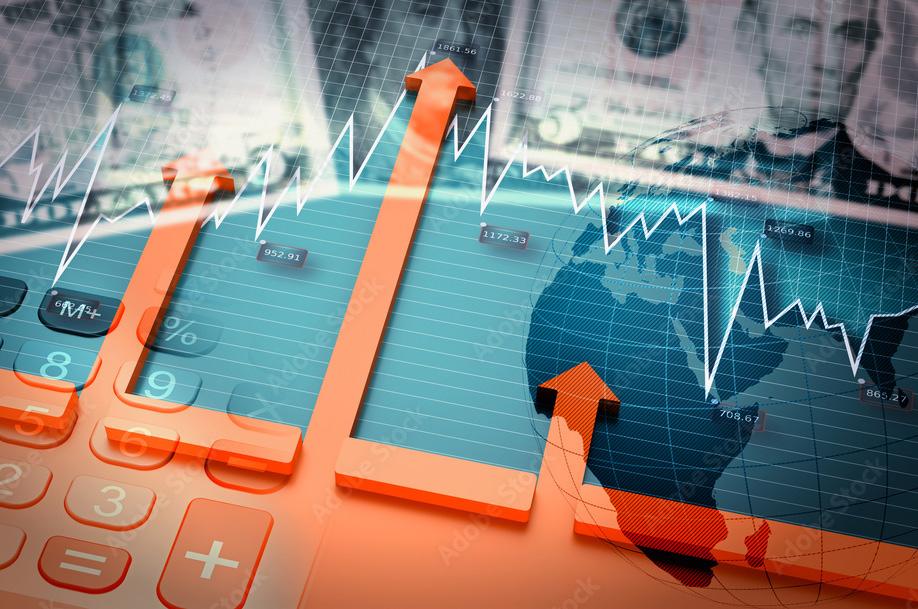

consideration is that labor productivity (80% made up of female workers) is much lower than the average of other sectors. The second is that the current model of production, distribution and consumption is environmentally unsustainable.
The resulting need is to progressively free hundreds of millions of workers from activities with low productivity, and often with a high risk of exposure to disease, through automation and artificial intelligence applied to all production and distribution processes.
The second challenge is to adopt recovery, recycling, and reuse systems with a view to the circular economy, for the entire supply chain. This will also require a massive use of new technologies, coordinated a cultural maturation of all the players in the sector.
Assomac represents Italian manufacturers of machineries and technologies for fashion, automotive, shoes, leather goods and upholstery manufacturing industries. Associated companies are aware of the difference they can make in terms of global challenges for sustainability because they are able to provide technological solutions helpful to direct production processes towards a lower environmental impact and better social development.
Training New Workers
Among the many Italian trade associations helping their member companies prepare for Industry 4.0 and the related worker training required for this shift are AMAPLAST (amaplast.org/en/), the Italian Plastics and Rubber Processing Machinery and Moulds Manufacturers Association, GIMAV (gimav.it/en/) , the Italian Association of Glass-Processing Machinery, and Unacea , (unacea.org/en) the Italian Construction Equipment Association.
In today’s manufacturing industry, technologies are transforming the design and build of machines, requiring workforce training to evolve and keep pace with the latest machine capabilities. From textile machinery to construction equipment, from the creation of packaging materials to glass, Italian companies are combining technology leadership with the human side of manufacturing. This respect for workers includes a focus on training them in their craft so they are updated on the knowledge, skills, and tools necessary for today’s market while helping them understand the tools that will make it easier to do their jobs with next-generation equipment.
Hybrid Systems Revitalize Metalworking Practices
The transition from traditional methods to the creation of hybrid systems that have been revitalized with electronic technologies is creating exciting new opportunities for Italian metalworking companies, proving that the possibilities for improving productivity, product quality, and creating better and safer jobs for workers are nearly limitless.
Modernizing Metalworking
Two industry trade associations – AMAFOND (amafond.it/en) , the Italian Association of Foundry Suppliers, and UCIMU-SISTEMI PER PRODURRE (ucimu.it/en), the Italian Industry Association for Machine Tools, Robotics and Automation— have been active in helping the metalworking industry embrace Industry 4.0 standards and achieve more sustainable production processes.
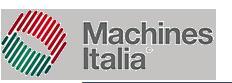
Workholding Innovation
Smart workholding creator SMW AUTOBLOK SpA (smwautoblok.com/us/en) was founded in Italy by two brothers in 1946. This family-owned machine tools company now has a global footprint, operating in more than 60 countries, and is a leader in using electronic technologies to transform metalworking practices.
SMW Autoblok provides a large, high-quality range of workholding solutions to a wide range of industries. The company combines stocked, standard products with a highly trained sales, service and engineering team to provide workholding solutions to customers.
Larry Robbins, president of the Commercial Division, points to the company’s work in developing electrically actuated products that enable the non-contact transfer of power without wires into base components. “Interconnectability between operations and information technologies

Innovations in Metalworking
has also made it possible to achieve significant advances in condition monitoring in real time, so that manufacturers can observe their processes in detail and act quickly when they need to troubleshoot and fix production problems,” he explains.
The same technologies also make it possible to achieve predictable machine set-ups and quicker changeovers to process different products. “This saves manufacturers time and money, increases production volumes and predictability, and allows operators to adjust tolerances in finite detail,” he adds.
“The ability of everything to communicate with everything else is rapidly transforming machines and manufacturing. It’s an exciting time for everyone involved in industry, and soon electronics will outweigh the mechanical components required for metalworking.”
Among the dozens of recent product innovations introduced by SMW Autoblok are a round magnetic chuck, MillTec, for 5-axis machining. Working on 5 axes allows for the use of shorter tools to increase feeds and cutting speeds. This technology makes it easier to carry out complex operations, including complete profiling, the undercut working, through holes and the creation of pockets.
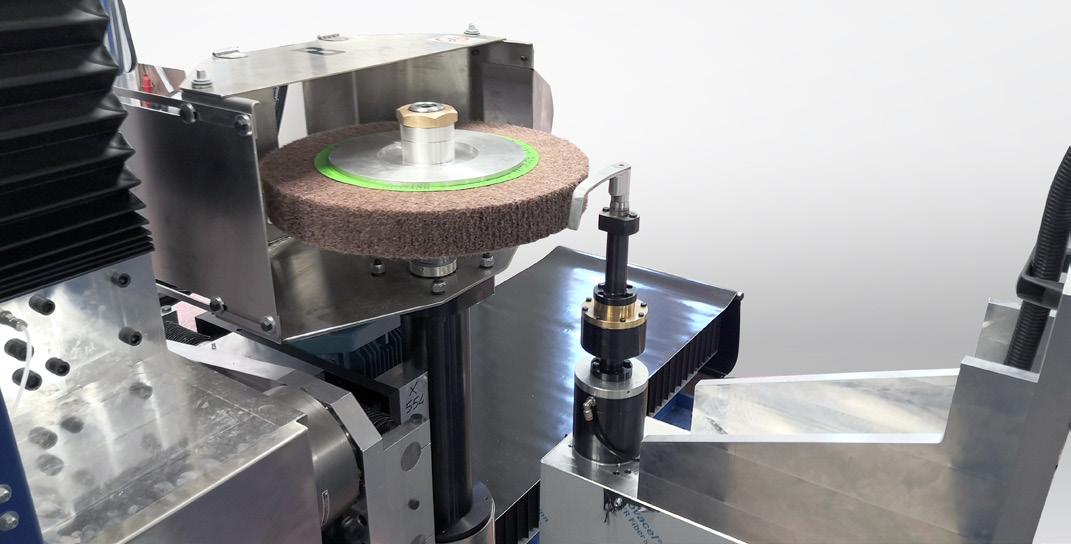
The best machine performance is achieved when all five faces of the workpiece are accessible. The processing area is limited by brackets used in traditional locking systems, which often requires multiple setups. With MillTec the workpiece is clamped from the base, without any obstacles to the tool.
The company’s Mag Autoblok division includes a full line of permanent electromagnetic chucking systems for quick and flexible workholding on horizontal and vertical milling machines, vertical turning centers, FMS systems, grinding machines, EDMs and other equipment. A full line of magnetic lifters for loading and unloading workpieces is also available.
Perfect Finishing
For more than 40 years, COSMAP Srl (cosmapsrl.it) has been manufacturing automatic robotic cell and rotary table machines for polishing and buffing metallic pieces. A recent project achieved perfect surface finishing thanks to a balanced polishing and buffing process for stainless steel handles created for Corbin Russwin, Berlin, CT.
The machine created by Cosmap is a metalworking innovation that allows it to carry out the polishing and buffing process automatically. With the Cosmap Automatic Balancing Compensation System, the interaction between the tool and the workpiece can be defined automatically for even complex shapes.
Thanks to the interpolation of the axes, the CNC2 unit can do simultaneous axis movement sequences at high speed. It can perform a complex cycle with no interruption or manual adjustments. And with a custom self-learning system, setting up the entire working cycle for each unit is simple and fast. The operator does not need to learn any specific programming language: just select a sequence of pre-set commands in the programming tab of the unit. Machine positioning is extremely fast with the auto-positioning of the unit taking place after each time a new program is loaded.
Advanced lubrication
Back in 1974, the DLS | DIE LUBRICATION SOLUTIONS (dls-italy.com) story started when Gianpaolo Bertotti built his first lubricator. Then, drawing on his many years of experience in hot forging lubrication, Gianpaolo and his son Fabio founded a company in 2018 dedicated to the lubrication of molds, mixing of release agents, and machinery retrofitting.
DLS provides a design and construction service for new, turnkey systems, or for the modernization of existing systems, specializing in the hot forging and metal blanking sector. Its LUBSYSTEM technology allows a uniform, homogeneous and nebulized distribution of the release

DLS systems allow a uniform, homogeneous and nebulized distribution of the release agent on all parts of the mold
agent on all parts of the mold. A touch screen panel makes it possible to manage every individual lubrication point. Each head is designed and engineered entirely by DLS.
The series has been specifically designed for dirty work environments such as stamping factories and forges. The machines are completely enclosed in metal panels that allow special covers to protect the moving metal parts from exposure to potentially harmful dust. It’s also possible to integrate the lubrication system with anthropomorphic robots.
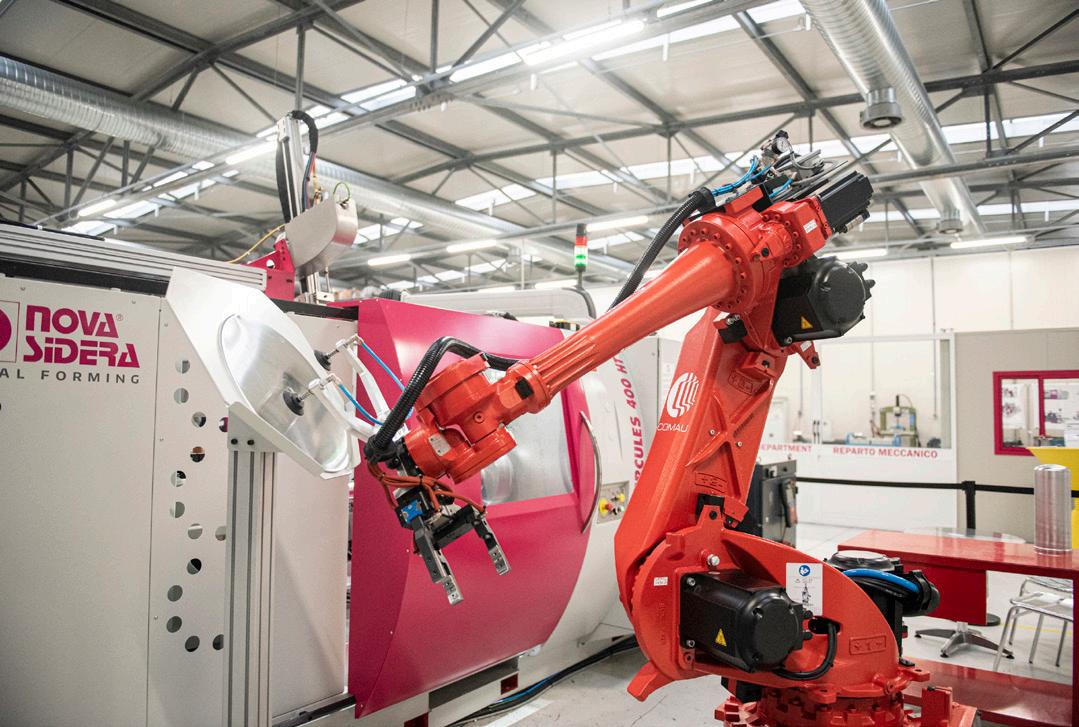
DLS is involved in the sheet metal cutting and shearing sector with spraying heads for the lubrication of sheet metal strips and mold parts, along with customized lubrication systems for precision metal stamping processes. They are equipped with spraying heads that can be adjusted and managed completely independent of each other. DLS also works in the field of cold stamping and blanking of metal sheets that are equipped with MG spray guns. Their small size limits lubrication to the places where it is needed and in the right quantity.
International Scope
NOVA SIDERA Metal Forming (novasidera.com), is based in Castell’Alfero in the northern region of Piedmont and is a member of UCIMU-SISTEMI PER PRODURRE, the Italian Machine Tools, Robots, and Automation Manufacturers’ Association. It has specialized for the past 30 years in the production of spinning lathes and special machinery for metal sheet forming.
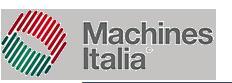
Managed today by the second generation of the Tasso family, Nova Sidera has focused on the internationalization and customization of its products, together with the aim of putting people at the center of its production. Nova Sidera’s international success started in the early 1990s and its growth in the North American market led to the opening of its US corporation in 2017, based in Miami, FL.
Nova Sidera’s teach and playback spinning lathes have been recognized globally for their reliability, customizations and after-sale service. The company has signed a strategic partnership agreement with Grotnes Inc., a Michigan-based company with more than a century’s experience in metal forming. This will allow them to closely cooperate on service, business development and joint projects for future machines.
In 2022 Nova Sidera installed its first model HERCULES 400 HT machine in the United States and received orders for 2 more that will be installed in 2023. The machine is characterized by a new heating system that is fully controlled by the CNC and helps keep parts at the right temperature during the different steps of the spinning process.
Until now, heat spinning has been performed using a hand torch independent of the machine, which has made this activity extremely dangerous, uncomfortable and created mixed results because it can’t precisely control the temperature of the part. This is crucial in a process like metal spinning, especially for a number of special alloys that have very specific ranges of temperature where it is possible to form the material.
A new version of the historic model Hercules 400, which already had hundreds of installations around the globe, has successfully installed the automated heating torch using propane and oxygen. Fully controlled by the machine’s numerical control system, it allows the operator to set all parameters, including the ones related to the temperature desired for the part, during all phases of the spinning process.
This technology will also help Nova Sidera train a new generation of professionals to tackle the ever more demanding requirements in precision and quality from disparate industrial sectors, both in the USA and internationally.
Inorganic Casting
PRIMAFOND Srl (primafond.com), is one of the leading Italian companies in the production of machines for foundry sand core production, and it continuously searches for simple and functional solutions for the forming of cores. Today it offers its core shooting machines and the necessary equipment for core forming with an inorganic process. Foundries and core-makers who are considering the use of the inorganic process are invited to consult with the company. Primafond is represented in the American market by EMI Inc. (emi-inc.com)
The choice of the right type of binding system and refractory material for core forming in the production of metal castings such as aluminum, cast iron, and steel is
Innovations in Metalworking
SAPORITI Srl (saporitimachines.com) has been an Italian manufacturer and world leader in making ball valve grinding machines since 1946. The demand is rising for next generation ball valves with higher requirements that can be worked precisely in severe conditions such as high pressures, extreme temperatures, high abrasives or dangerous fluids.
These machines require more hard material seats (metal to metal valve types) and very hard coating on the ball surface. Valve manufacturers also need machines suitable for obtaining high precision in roundness and roughness.
crucial to achieving a high-quality end-product. Silica sand is a common material for core production as it has good temperature resistance, thermal stability and a smooth surface. It is also important to choose a core with good dimensional stability at high temperatures and erosion resistance.
The choice of core depends on specific project requirements such as the need for mechanical strength or heat dissipation, and the ability to withstand thermal and current loads. In general, the choice of core is based on desired properties and the trade-off between weight, strength, thermal conductivity, and electrical conductivity.
Foundries are constantly attentive to design requirements and strict environmental and safety standards. In producing foundry cores, the greatest difficulties are represented by the combustion and thermal cracking of binders during casting, resulting in the loss of mechanical properties and the formation of gas, potential sources of porosity and cavities within the casting. Hazardous substance emissions, fumes and odors are produced in both the casting phase and the forming process.
Despite improvements in the overall process, attention is shifting towards the use of alternative binders, particularly inorganic binders. They use only water as a solvent, and their binding matrix is made up of a mixture of silicates, phosphates and borates in varying percentages.

Inorganic cores are widely used in foundries for the automotive industry because no combustion products are created during forming and casting (fumes, BTX, BTEX, amines, odors). Currently, in terms of total volumes, inorganic binders constitute a relatively low share of the binders used globally, but their use in foundries has been increasing in recent years.
SAPORITI’s experience helps customers find the best tool solutions for the coating material. Normally these coatings are carbide or a nickel - boron coating. This coating is particularly difficult to work on because the material doesn’t have a uniform texture and it is also powder welded on the rough metal ball and heated in a furnace. This makes its behavior strongly dependent on ball dimensions.
The SAPORITI PV grinding machines come in different sizes to cover a range of balls from 1” up to 98” OD (2500 mm). The models for balls up to 29.5” (750 mm) OD can be placed on good industrial floors with anti-vibration support included in the machine. All models save energy and generate less noise.
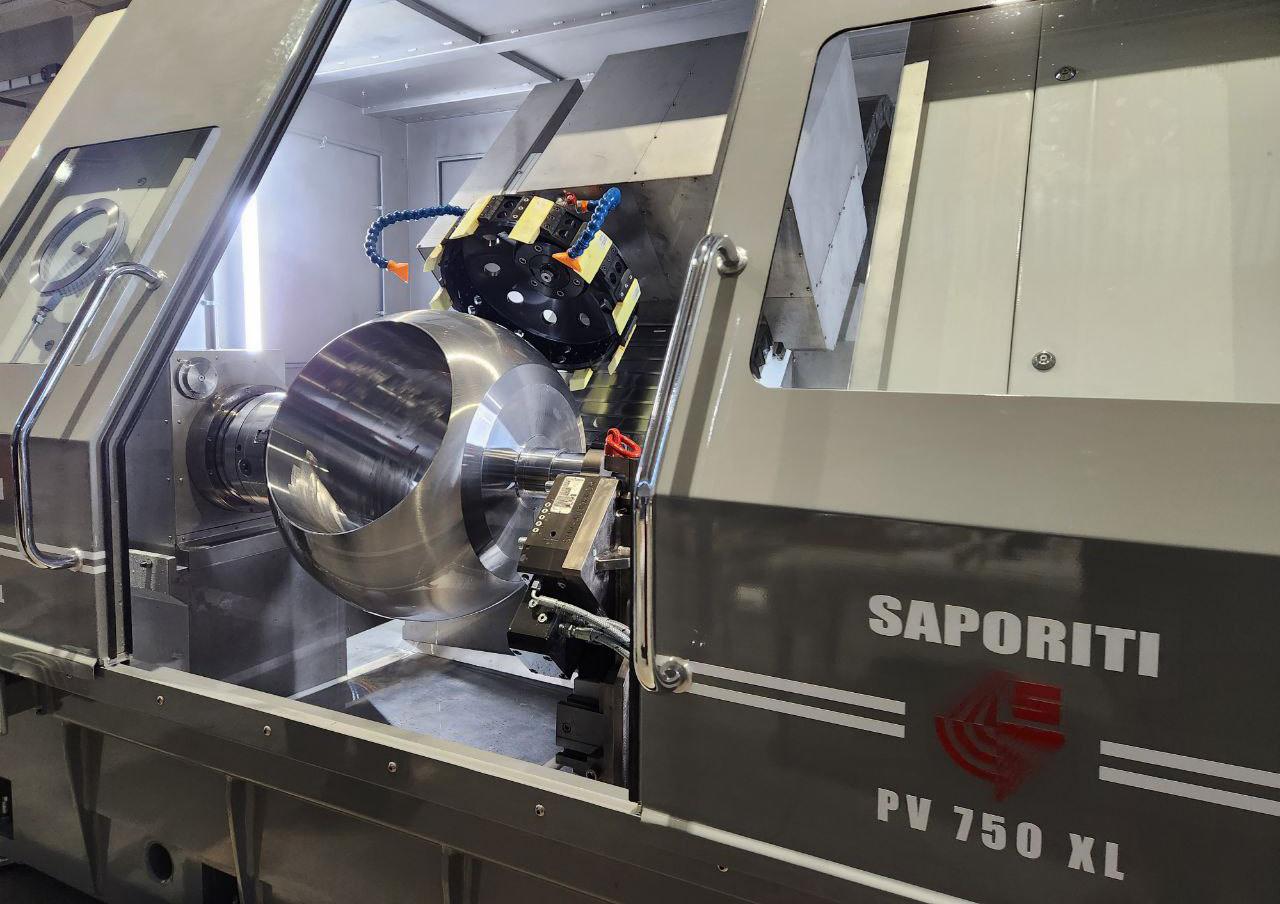
The development of hybrid metalworking solutions that combine the best of electronic and mechanical technologies is advancing rapidly. The industry in Italy has introduced a wide range of these new products over the past decade that have improved quality and manufacturing productivity, as well as modifications that have made it easier for North Americans to do their jobs.
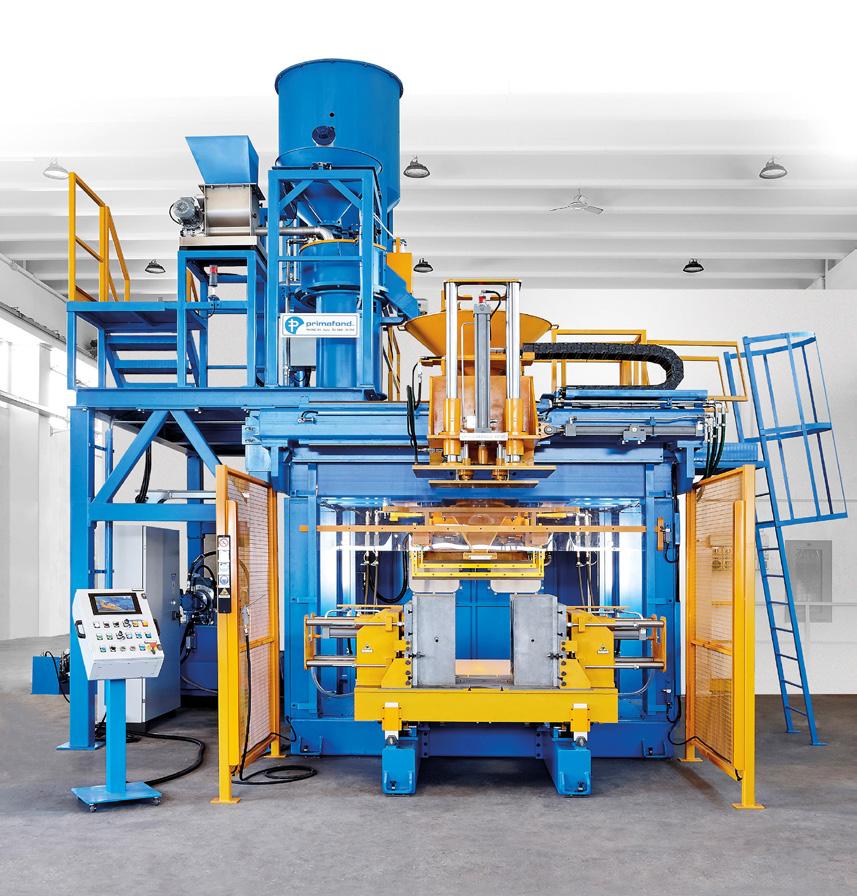
PASTA MANUFACTURER OPENS NORTH AMERICAN PRODUCTION FACILITY
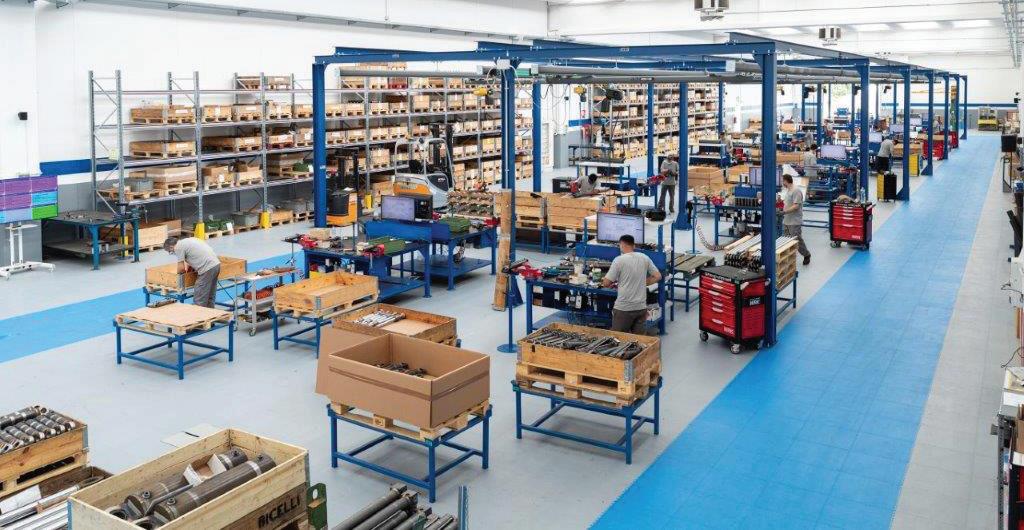
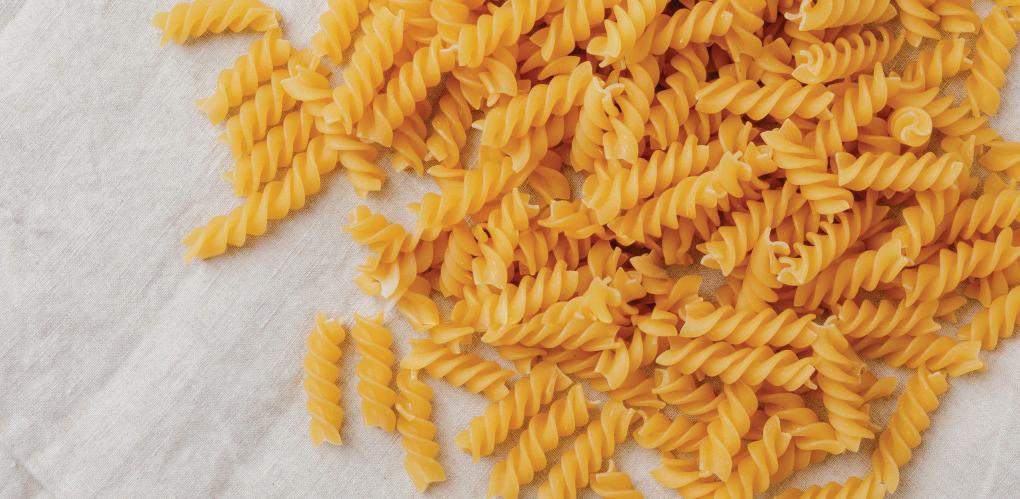
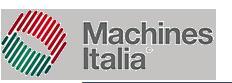
Italian food processor, Andriani SpA, recently announced that it is opening its first-ever North American allergen and gluten-free pasta production facility in London, Ontario. This new 50,000 sq. ft. facility will employ 50 people in the first phase and will allow the company to work closely with regional farms, which will supply access to raw materials and non-GMO brown rice, corn, quinoa, buckwheat, amaranth, lentils, peas, and more. While Andriani is already known for producing more than 40,000 tons of allergen and gluten-free pasta for more than 30 countries, the location will also help the company better support North American markets, including the U.S. and Canada. Website: andrianispa.com
COMPANY BOOSTS PRODUCTION WORKFLOW AND PLANS U.S. SUBSIDIARY





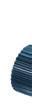

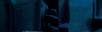




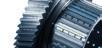




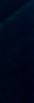
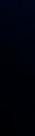





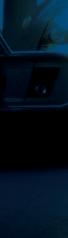



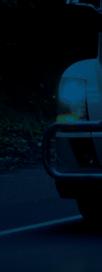
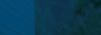
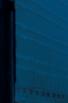
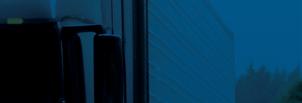



Family-owned Bicelli Hydraulics Srl is now investing in new CNC machines and welding robots, and, thanks to a state-of-the-art assembly process, is reorganizing its layout to simplify the production flow. With a new paintshop and self-learning robots, the company regularly guarantees top quality finishing of the products. The barcode traceability of the products’ manufacturing cycle allows a reliable tracking of each production phase and the observance of the confirmed delivery dates. For these reasons, and for its excellent customer service support, Bicelli prides itself on supplying renowned customers in the industry, agricultural, construction machinery, and automotive fields. The company also plans to set up a U.S.-based subsidiary to support the market with over 50 years domain expertise and the reliability of its quality products and services. Website: bicelli.it
GEARS FOR THE TOUGHEST MACHINES ON EARTH AVAILABLE IN NORTH AMERICA

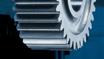
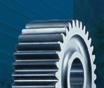
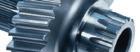
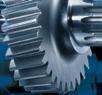

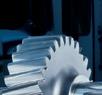
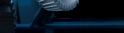
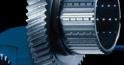






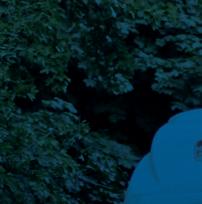
Cattini North America, a subsidiary of Cattini e Figlio SpA offers gears for the toughest machines on earth. The company also offers a wide variety of manufacturing capabilities covering almost all powertrain and driveline applications. Cattini North America makes available one of the widest production capability sets for custom gears for heavy duty vehicles for the entire industry, enabling OEM customers to focus on their projects. Website: cattinina.com


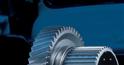
CHICANING SYSTEM FILLS 800 PIECES PER MINUTE
Cavanna Packaging USA Inc., a subsidiary of Cavanna SpA, a global, multi-site leader in automated flowpacking systems with three manufacturing sites and a US Sales and After-sales branch, recently provided a solution for the Enstrom Candy company. This chicaning system was able to put toffee in a single file at 800 pieces a minute, then automatically feed one Cavanna Zero5 flowpacker. This system helps the manufacturer of fine confectionery products to grow. Cavanna USA also offers machine control upgrades and a Rebuilding Service for crimper and fin wheel assemblies. While upgrading their system and installing new rebuilt cores, operators are able to continue production. Cavanna also offers turn-key primary and secondary packaging solutions, including handling, buffering, distribution, flowpacking, cartoning, and casepacking through vision systems and advanced robotic solutions.
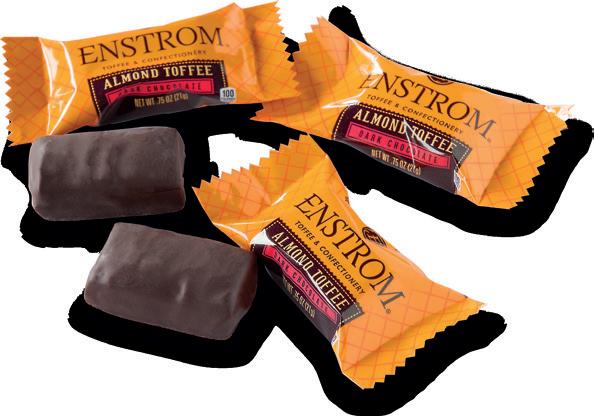
Website: cavanna-usa.com
NEW U.S.-BASED PLANT SUPPORTS NORTH AMERICAN TUBE FORMING
Though it already has 30 years of experience in serving the North American tube forming industry with benders and end forming equipment, Crippa USA, a subsidiary of Crippa SpA is now opening a new plant in Wixom, MI, to better support the North American market. The branch will be operated by highly experienced technical and commercial resources that will manage sales network development, spare parts management, and service with support from headquarters in Italy. Out of the building’s 14,250 sq. ft., 2,000 are dedicated to spare parts storage. The showroom will accommodate up to 10 machines, representing a wide range of the company’s abilities, while the office will serve as a hub for Crippa’s dedicated service
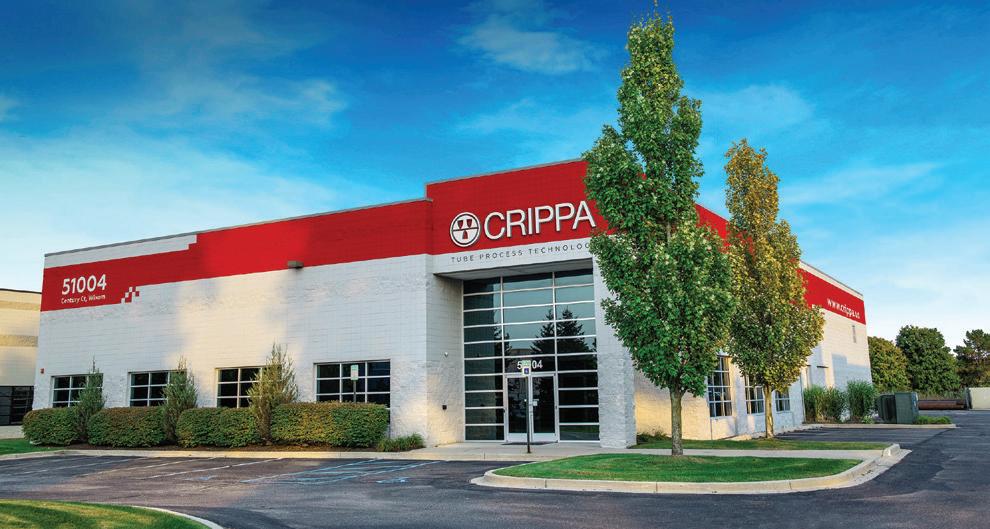
$38 MILLION INVESTMENT EARMARKED FOR U.S. EXPANSION
Ecopol SpA, an Italian company that produces biodegradable PVA film, announced that it will invest more than $38 million in the company’s first North American facility, which will be based south of Atlanta in Spalding County, Georgia. It will also create 130 new jobs. Founded in 2009, Ecopol’s mission was to reduce the use of plastics and carbon emissions by creating water-soluble and biodegradable film to wrap consumer goods. This new facility will help Ecopol expand the company’s vision throughout the U.S. while also strengthening trade between Italy and Georgia, as well as the nation. Website: ecopol.com
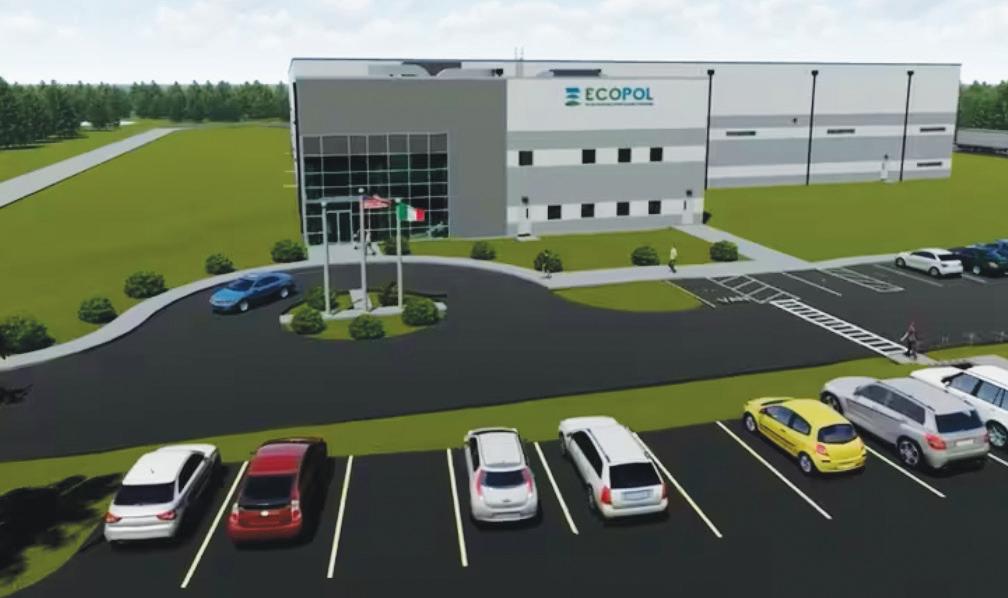
MANUFACTURER INVESTS $1.4 MILLION IN TENNESSEE PLANT EXPANSION
Officina Ferrari Carlo SpA, an Italian manufacturer of molds and die for ceramic tiles, announced that it will invest $1.4 million to expand its manufacturing operations at its U.S. headquarters in Clarksville, Tennessee. The news comes after the company decided to purchase Poligraph USA, which will give Ferrari Stampi more U.S.-based support for additional production lines. This investment will equip the Tennessee headquarters with the latest high-tech machinery and technology, while also doubling the company’s U.S. headcount by adding 30 jobs.
Website: ferraristampi.it
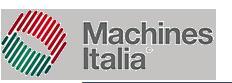
PARTNERSHIP PROVIDES COMPLETE METALFORMING SOLUTIONS CENTER
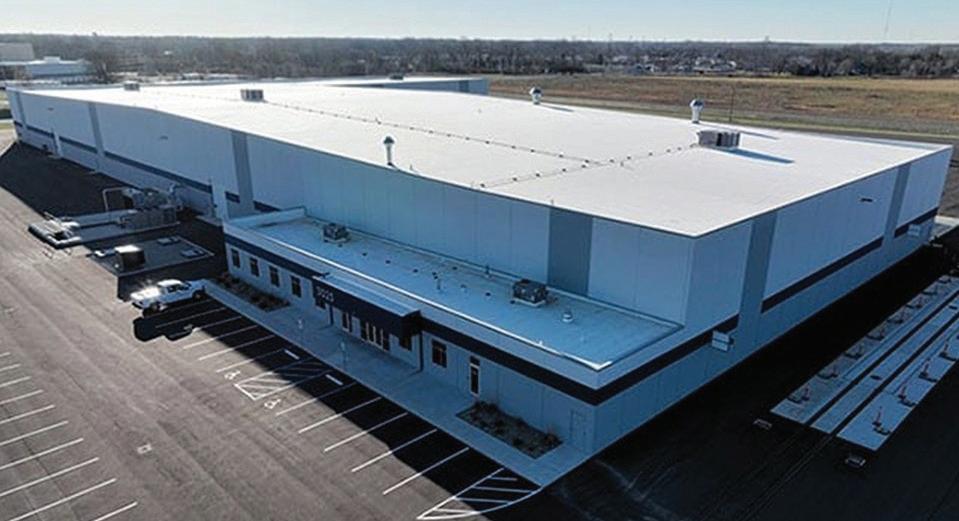
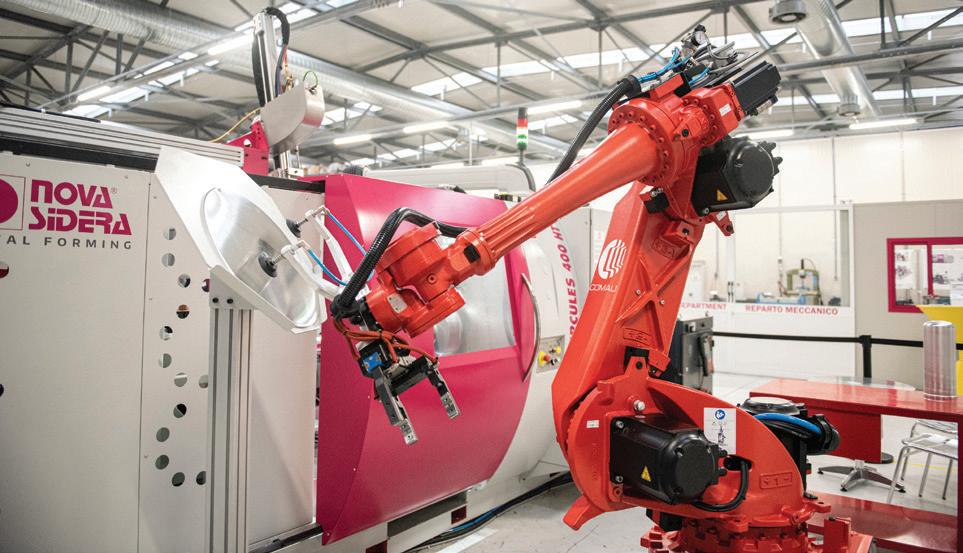
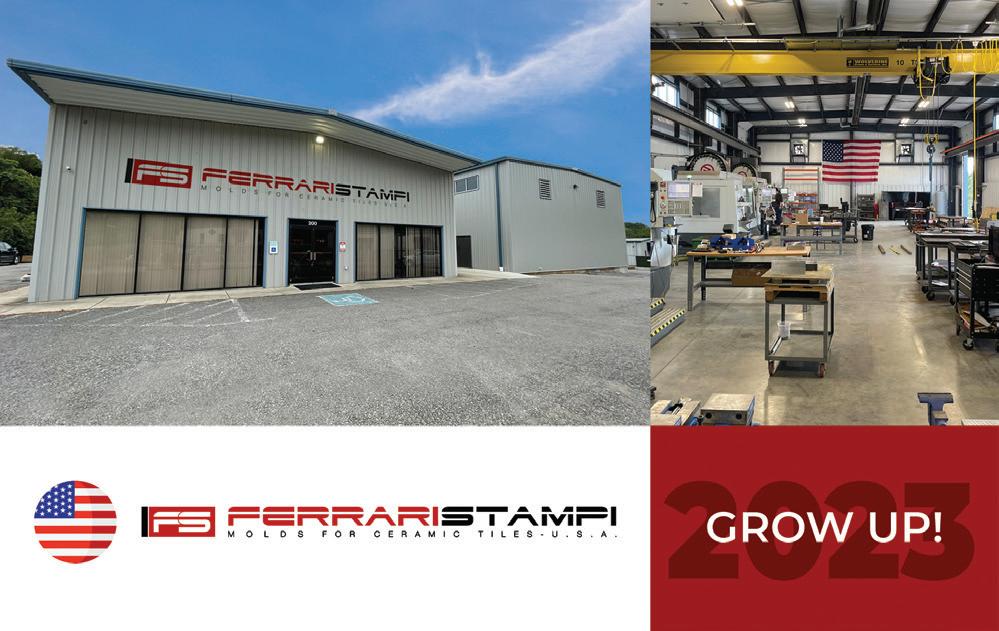
Nova Sidera Metal Forming Srl, based in Castell’Alfero, Italy, and its American subsidiary, Nova Sidera Metal Forming Corp. based in Miami, Florida, recently announced a strategic partnership with Michigan-based Grotnes, Inc. Both companies are known for a rich tradition of producing precision metal forming equipment, while Nova Sidera specializes in Metal Spinning Lathes and special machines for metal deformation, while Grotnes focuses on expanding, shrinking, spinning, and roll forming. The partnership will allow the companies to offer a complete metal forming solution center, stronger local support for customer service and spare parts in the U.S., and will allow both companies to explore new product development initiatives. Website: novasidera.com
SUSTAINABLE PLASTICS AND COMPOUNDS PRODUCER OPENS SECOND PLANT IN INDIANA
Sirmax SpA, a sustainable Italian producer of polypropylene compounds, engineering plastics, postconsumer compounds, and biocompounds, has invested $30 million to open a second plant in Anderson, Indiana. The new plant, called SER North America, is dedicated to producing recycled polypropylene from post-industrial waste and stands next to Sirmax North America, which was built in 2015 to select and regenerate post-industrial waste as well as Green Isoplen, a polymer made of 100-percent regenerated polypropylene. SER North America will employ 140 people and has a production capacity of 33 million pounds. Its recycled polypropylene will be used for industrial applications, as well as processed by Sirmax North America for its Green Isofil and Green Isoglass hybrid compounds. The combined output of both plants will reach 133 million pounds. Website: sirmax.com
Award Programs
Italian Technology Award Programs
Now in its second decade, the ITA - Italian Trade Agency (ICE-Agenzia, in Italian www.sitoeng. ice.it), along with several partners, has sponsored the Italian Technology Award. ITA and its partners have made it possible for groups of students and professors, not only from NAFTA but from around the world, to gain firsthand knowledge of Italian technology for the machinery manufacturing industries, including machine tools, textiles, plastic, foundry, ceramic, glass, leatherworking, marble and packaging. In January 2023, over 50 awarded students and faculty from six countries took part in educational programs at leading academic centers throughout northern Italy, along with visiting leading Italian machinery manufacturers within their respective industries of study.
Italian Machine Tool Technology
Sponsors: North American Offices — Chicago and Toronto
Countries: U.S. and Canada
Partner Association: UCIMU-SISTEMI PER PRODURRE
— Association of Italian Manufacturers of Machine Tools, Robots, Automation Systems, and Ancillary Products (ucimu.it)

Italian Leathergoods and Tanning Technologies
Sponsors: North American Offices — Chicago and Mexico City
Countries: U.S. and Mexico
Partner Association: ASSOMAC — Italian Footwear, Leathergoods, and Tanning Technologies Machinery Manufacturers Association (www.assomac.it)
Schools: University of Oregon and Tecnologico Nacional de Mexico, Campus Leon
Italian Packaging Technology
Sponsors: North American Offices — Chicago and Mexico City
Countries: U.S. and Mexico
Partner Association: UCIMA — Italian Packaging Machinery Manufacturers Association (www.ucima.it)
Italian Glassworking Technology
Sponsor: North American Office —Houston
Country: U.S.
Partner Association: GIMAV — the Association of Italian manufacturers and suppliers of machinery, equipment, and special products for glass processing (www.gimav.it)
Italian Plastic Technology
School: Italian Technological Center in Puebla
Country: Mexico
Partner Association: AMAPLAST — Italian Plastics and Rubber Processing Machinery and Moulds Manufacturers’ Association (www.amaplast.org)
Italian Ceramic Technology
School: Universidad Autónoma de Nuevo León
Country: Mexico
Partner Association: ACIMAC — Association of Italian Ceramic Machinery Manufacturers (www.acimac.it)
Italian Foundry Technology
Schools: Universidad Autónoma de Nuevo León, Universidad Autónoma de San Luis Potosí, Universidad Nacional Autónoma de México, and Instituto Politécnico Nacional
Country: Mexico
Other Italian Award Programs Beyond USMCA
In addition to the countries and programs listed above, the 2022 edition of the Italian Technology Award program included other sectors and operated this year in Iran, Uzbekistan, and Poland.
ITA program partners can now connect students, faculty members, and Italian companies and associations that have been part of the program since its inception by connecting with the agency’s website for the latest updates on each of the various programs at its website, machinesitalia.org/italian-technology-awards, and via its social media channels on Twitter, LinkedIn, and YouTube.
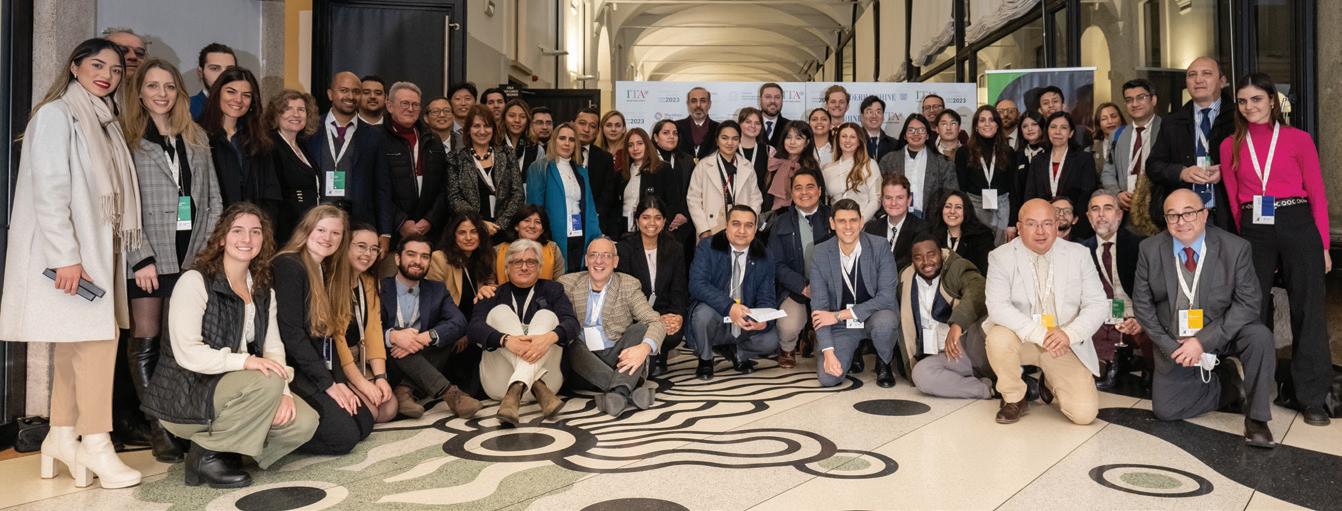
Italian Innovation in the spotlight
Machines Italia takes “Turning innovation into productivity” on the road to major North American events. Over the course of 2023–2024 Machines Italia, together with its partner associations, is proud to be a featured participant or sponsor of major industry events here in North America. We highlight some of the major ones here.
If you make the purchasing decisions for your company, you have an enormous responsibility. You must know the ins and outs of production in a way no one else does.
Italian machinery can make your decision easier, even in these uncertain times. That’s why Machines Italia, together with its partner associations, is proud to be a featured participant, supporter, and sponsor of major industry events. Over the course of 2023–2024, Machines Italia will promote the events where Italian companies participate, as listed here and at the end of this article.
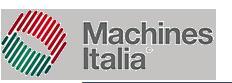
VITRUV 2023: The Forum for Resilient, Scalable and Secure Manufacturing
VITRUV 2023 will be held in Chicago, IL, on June 14th, 2023 at IllinoisTech / Kaplan Institute, where the Italian Trade Agency, via its Chicago Office, together with Italy’s UCIMU-SISTEMI PER PRODURRE (www.ucimu.it), and related governmental bodies and trade associations will be hosting a forum event spotlighting various technologies offered by 20 Italian machine tool builders, and concluding with a luncheon networking event. Amongst the guests, there will be representatives from leading Italian institutions and local partners. For more information and how to register go to www.machinesitalia.org/events

Machines Italia México - Expo Cihac 2023
Expo Cihac (https://www.expocihac.com/es/home.html), trade show dedicated to the construction, interior design and architectural sectors, will be held from October 11–13, 2023, at Centro Citibanamex, Mexico City. The Mexico City office will coordinate the Italian Pavilion which will host 25 producers of marble related technology.
Machines Italia Mexico @ Fundiexpo 2024
Monterrey hosts the 2024 edition of Fundiexpo (www.fundiexpo2024.com), the main Mexican exhibition for the foundry industry, to be held in the autumn of 2024. The trade show, in the CINTERMEX convention center, will showcase technology and innovation from Mexican and international providers. Given the importance of the foundry industry to the Mexican economy, Machines Italia, via its Mexico City Office, will be taking part by hosting Italian leading machinery and technology suppliers.
Calendar of North American Events
Fabtech Mexico 2023
May 16–18, 2023
Mexico City, Mexico https://mexico.fabtechexpo.com/
Expo Pack Guadalajara 2023
June 13–15, 2023
Guadalajara, Mexico www.expopackguadalajara.com.mx/en
FITMA 2023
June 20–22, 2023
Mexico City, Mexico https://www.fitma-la.com/
Glasstech Mexico 2023
July 19–21, 2023
Mexico City, Mexico https://www.glasstechmexico.com/
AWFS Fair 2023
July 25–28, 2023
Las Vegas, Nevada www.awfsfair.org
FESPA Mexico 2023
August 17–19, 2023
Mexico City, Mexico https://mexico.fespa.com/
GlassBuild America 2023
October 31–November 2, 2023
Las Vegas, Nevada www.glassbuildamerica.com
Pack Expo Las Vegas 2023
September 11–13, 2023
Las Vegas, Nevada www.packexpolasvegas.com
Fabtech Expo 2023
September 11–14, 2023
Chicago, Illinois www.fabtechexpo.com
Italian Exhibitions
ITMA 2023 The world’s largest international textile and garment technology exhibition, ITMA highlights innovations that will help textile and garment manufacturers transform and grow their business.
SIMAC TANNING TECH 2023
International exhibition of machines and technologies for footwear, leathergoods, and tanning
Textile Machinery Milan, Italy June 8-14 2023 https://itma.com/
Footwear, Leathergoods & Tanning Machinery
Milan, Italy
UITIC 21st International Technical Footwear Congress Footwear Milan and Vigevano, Italy
PLAST 2023
International exhibition for plastics and rubber industries
34.BI-MU Metal cutting, metal forming and additive machines, robots, digital manufacturing and automation, enabling technologies, subcontracting
LAMIERA Machines and equipment for the machining of sheet metal, pipes, sections, wire and metal structural work. Dies. Welding. Treatments and finishing. Subcontracting. Robots, automation and enabling technologies
MECFOR Mechanics for manufacturing & subcontracting
TECNA The International Exhibition of Technologies and Supplies for Surfaces
Plastics and rubber Milan, Italy
Machine Tools for Metalforming, Robots, Automation Systems, Components
Machine Tools for Metalforming, Robots, Automation Systems, Components
Mechanics for manufacturing & subcontracting
Milan, Italy
September 19-21 2023 https://www. simactanningtech.it
September 19-22 2023 https://uitic-italy2023.com
September 5-8 2023 www.plastonline.org
October 9-12 2024 www.bimu.it
Milan, Italy May 10-13 2023 www.lamiera.net
Parma, Italy
Ceramic Machinery Rimini, Italy
May 23-25 2023 www.mecforparma.it
June 13-14 2023 https://en.tecnaexpo.com/
IPACK IMA The fair specialized in food and non-food processing and packaging Processing & Packaging Milan, Italy May 27-30 2025 https://www.ipackima.com/
EIMA International Agricultural and Gardening Machinery Exhibition Agricultural Machinery Bologna, Italy
XYLEXPO Exhibition for woodworking technology and components for the furniture industry Woodworking Machinery Milan, Italy
6-10 2024 www.eima.it/en
12-15 2022 www.xylexpo.com
MARMOMACC International Exhibition of Stone Design & Technology Natural Stone, Machinery, Processing Technology Verona, Italy September 26-29 2023 www.marmomac.com
VITRUM "International Trade Show Specialized in Machinery, Equipment and Systems for Flat, Bent and Hollow Glass and in Glass and Processed Products for Industry”
Glass Milan, Italy
September 5-8 2023 www.vitrum-milano.com/en
HOSTMilano International Exhibition of the Hospitality Industry Food Technology: Catering & Restaurant Milan, Italy
SaMoTer International exhibition for construction equipment
Ecomondo International exhibition for circular economy
ITMA ASIA + CITME 2022 International exhibition of Textile Machinery
Construction and earthmoving Machinery
Construction and earthmoving Machinery
Verona, Italy
Rimini, Italy
Textile Machinery Shanghai, China
October 13-17 2023 www.host.fieramilano.it
May 3-7 2023 www.samoter.it/en
November 7-10 2023 www.en.ecomondo.com
November 19-23 2023 www.itmaasia.com
2501, Wing B, Dongyu (Disan Zhiye) Building No. Jia 1, Shuguang Xili, Chaoyang Dist.
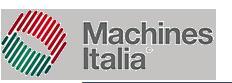
Innovations at work in global markets

AGRICULTURE, FARM, GARDENING MACHINERY, AND COMPONENTS

FEDERUNACOMA represents a broad sector of mechanics that brings together the following associations of producers: Agridigital, digital systems and technologies for agricultural machinery an farmer; Assoidrotech, irrigation systems; Assomao, agricultural implements; Assomase, self-propelled machines; Assotrattori tractors; Comacomp, components for agricultural machines and gardening; Comagarden, gardening machinery. The Federation acts as an umbrella organisation for seven industry associations representing various sectors of the agricultural, forestry and gardening machinery industry, with the aim of promoting mechanisation and technological innovation to meet the different needs in agriculture and green care.
Through FederUnacoma the Italian mechanisation enterprises are able to interface with institutions, promoting innovation, business culture and their presence in national and international markets. federunacoma.it
MACHINERY AND EQUIPMENTS FOR CERAMICS
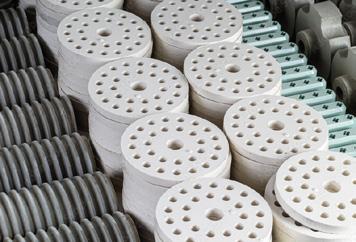
ACIMAC—the Italian Association of Manufacturers of Machinery and Equipment for the Ceramics Industry (ACIMAC) has earned a world-class reputation for providing solutions that meet a vast range of customer needs—from traditional ceramics to the latest design trends. Customers around the globe choose machinery produced by ACIMAC member companies, thanks in large part to their easy programmability and simplicity in maintenance. The Italian ceramic machinery manufacturing sector enjoys a world leadership position with an export share that now exceeds two-thirds of its total annual turnover, thanks to its unrivalled excellence and the fact that produces the most competitive plants that modern technology can offer. acimac.it
CONSTRUCTION EQUIPMENT
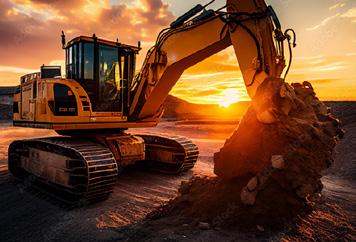
Created in 2010, UNACEA is the Italian construction equipment association with more than 70 members. UNACEA membership includes manufacturers of earth-moving machines, attachments, concrete equipment, tower cranes, road machines, and drilling machineries. UNACEA is the Italian member of Cece, the Committee for European Construction Equipment. unacea.org/en
FOOD TECHNOLOGY
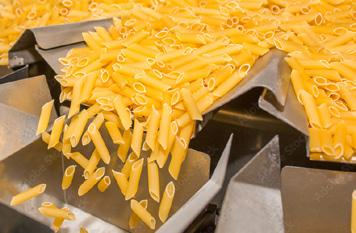
ASSOFOODTEC, the Italian Association of Machinery and Plant Manufacturers for Food Production, Processing, Preservation represents global leaders in the most important Italian association for technologies for the food industry, thanks to a diversified offer that ranges from relatively simple machines to extremely sophisticated production lines. Prestigious and qualified companies, a great wealth of experience and reliability, and an increasing technical development of products are what ASSOFOODTEC offers. ASSOFOODTEC cooperates in the activity of the most important bodies charged for the drawing up of European and world technical standards. ASSOFOODTEC operates within the Federation of Italian Mechanical and Engineering Association (ANIMA). assofoodtec.it
FOOTWARE, LEATHERGOODS, AND TANNING
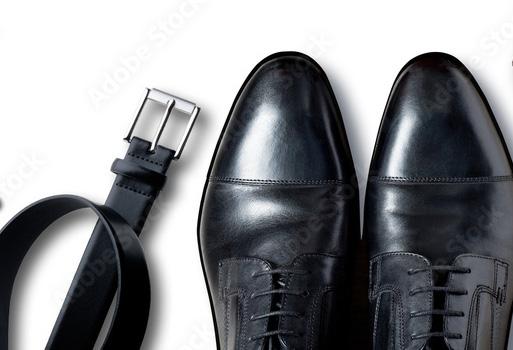
Assomac represents Italian manufacturers of machinery and technologies for fashion, automotive, shoes, leather goods, and upholstery manufacturing by unifying all the standards which make “Made with Italian Technology” a guarantee of high quality. Italian competence means product EXCELLENCY, processes EXPERTISE, and INNOVATION capabilities.
Assomac plays a key role in promoting the safety, welfare, and sustainability of the production environment model, central issues supported by Industry 4.0, and relative sustainability protocols represented by the voluntary third-party Green Label audits, and is able to point out the efficiency of technology for associate companies. Assomac represents its members worldwide, promoting and supporting a business culture focused on continuous research and development, reliability of aftersale services, and commitment to support efficient, sustainable processes. assomac.it
FOUNDRY AND METALLURGICAL MACHINERY AND PRODUCTS
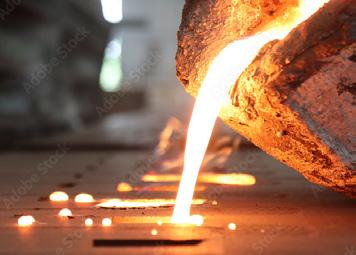
AMAFOND is the Italian association of companies producing machinery, plants, furnaces, products, and services for the foundry industry. It’s about 100 member companies provide machinery used in the manufacturing of everything from automobile engines and components to domestic appliances. AMAFOND credits the “Italian approach” to business — characterized by extra customer care and stronger personal relationships—as one of the reasons its member companies attract worldwide customers. amafond.com
GLASS
As an evolution of the Italian glass-making tradition, Gimav - the Italian Association of Glass-Processing Machinery and Accessory Suppliers - represents Italian excellence in glass-making machinery. This sector has expanded internationally by employing innovative technology that meets today’s marketplace needs. Gimav’s 70 members companies are known for customizing machines to meet end-users specifications from high-rise buildings to fine arts applications. gimav.it/en
MACHINERY AND EQUIPMENTS FOR MARBLE, GRANITE AND NATURAL STONE
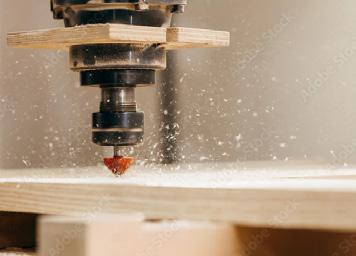
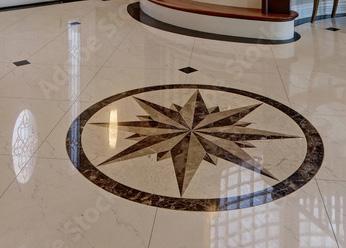
MARMOMACCHINE Association — CONFINDUSTRIA MARMOMACCHINE — is the Italian Association of Producers and Processors of Marbles, Granites, and Natural Stones, and of Manufacturers of Machinery, Complete Plants, Tools, and Complementary Products to quarry and process Natural Stones with more than 320 member companies and territorial consortia. This gives CONFINDUSTRIA MARMOMACCHINE broad Italian and gloabl representation. It acts as sole sector interlocutor with ministries, the Italian Trade Agency, Confindustria, standardization boards, labor unions, universities and polytechnics, Italian and foreign federations and associations, and tradefairs around the world. assomarmomacchine.com
MECHATRONIC SYSTEMS AND COMPONENTS FOR POWER TRANSMISSION
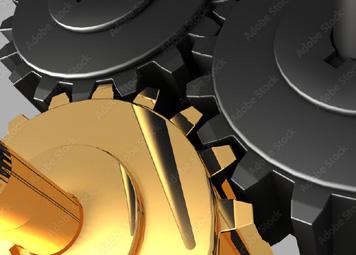
FEDERTEC — the Italian Association of Mechatronic Technologies and Components for Fluid Power, Power Transmission, Smart Automation and Control of Industrial Products and Processes — was established in 2019 after the merger of ASSIOT (Italian Transmission Elements and Gears Manufacturers Association) and ASSOFLUID (Italian Fluid Power Association), and, as of April 2022, FNDI (National Federation of Industrial Distribution). FEDERTEC has 280 member companies and represents a production of 12.5 billion euro (60% of which is exported) and 55,000 employees. federtec.it
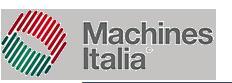
METALWORKING
UCIMU-SISTEMI PER PRODURRE is the Italian Machine Tools, Robots, and Automation Manufacturers’ Association. As an official representative of the industry, UCIMU-SISTEMI PER PRODURRE acts as a world-wide ambassador for some of the latest technology developed in Italy. With a constant interest in sector developments and a continuous trend monitoring, UCIMU provides associate member companies with specific consultancy and tangible services in the support of their activities. Over 240 member companies, who produce around 70% of the output for the sector, have won universal recognition for their quality, flexibility, reliability, and customization. ucimu.it/en/home
PACKAGING MACHINERY
UCIMA is the Italian Packaging Machinery Manufacturers’ Association. Its members represent 70% of the total Italian production and, on average, 80% of Italian exports. One packaging machine out of every four in the world bears the wording “Made in Italy.” And the United States is the industry’s main outlet market for the sector. The worldwide success of the Italian packaging and packaging industry is firmly rooted in a consolidated technologic tradition and in the ability to find customized packing solutions. www.ucima.it
PLASTICS AND RUBBER MACHINERY


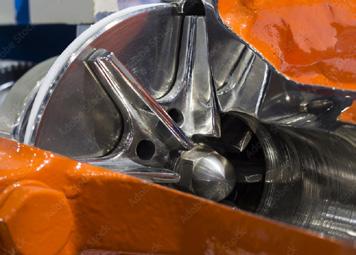
The companies of AMAPLAST, the Italian Plastics and Rubber Processing Machinery and Molds Manufacturers Association, are globally renowned for their “turnkey solutions” — addressing customer needs through sophisticated machines and engineering. As a result, the sector industry has seen steady growth since its inception in 1960. Italian machines are highly prized by the world’s most industrialized and economically advanced countries. amaplast.org/en
PRINTING, GRAPHIC, AND CONVERTING
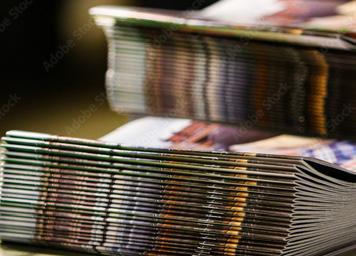
Acimga is the association of Italian manufacturers of machinery for the graphic, paper, and converting industry. Established in 1947, it plays a key role in representing “Made by Italy” production – that is, not just machinery produced in Italy, but the wealth of competence and expertise unique to the country which is the trademark of these technologies. Acimga represents all printing (roto, flexo, off set and digital) and converting technologies on all materials (paper, polycoupled and plastic) for applications on flexible, labels, corrugated cardboard, paper, tissue, aluminum. acimga.it/en
TEXTILE MACHINERY
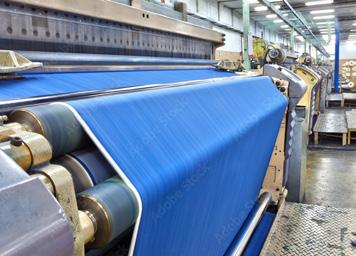
ACIMIT is the Association of Italian Textile Machinery whose production represents about 85% of the entire national textile machinery production. Its members meet the full spectrum of industry needs (spinning, weaving, knitting, and finishing machines). They are well appreciated for their commitment in the sustainable technologies and in the production of equipment for the most innovative niche markets (technical textiles, nonwovens). Leading American textile and clothing manufacturers rely on the quality of Italian high-tech machinery. acimit.it/en
WOOD
ACIMALL — Italian Woodworking Machinery and Tools Manufacturers’ Association, with over 220 of the most qualified companies in their fields, represents 90% of the entire industry in terms of employees and turnover. In every segment of woodworking, from sawmills to the industrial processing of solid wood and panel to finishing, the Italian industry is present with technological solutions capable of responding effectively to a multitude of user requirements. acimall.com/en
Thank You For Considering To Turn Our Innovation Into Your Productivity!
For more information on the companies cited within this publication or any of the other thousands of Italian manufacturers, you may either contact
directly, through our partner associations or via any of the Machines Italia offices listed here. Don’t
CHICAGO
c/o Italian Trade Agency 401 N. Michigan Avenue—Suite 1720
Chicago, Illinois 60511
TOLL FREE: 888-ITALTRADE
(482-5872)
TEL: 312-670-4380
FAX: 312-670-5147
E-MAIL: info@italtradeusa.com
HOUSTON
c/o Italian Trade Agency 777 Post Oak Boulevard—Suite 320 Houston, TX 77056
TOLL FREE: 888-ITALTRADE
(482-5872)
TEL: 281-888-4288
FAX: 281-974-3100
E-MAIL: houston@ice.it
LOS ANGELES
c/o Italian Trade Agency 1900 Ave. of the Stars—Suite 350 Los Angeles, CA 90067
TOLL FREE: 888-ITALTRADE
(482-5872)
TEL: 323-879-0950
FAX: 310-203-8335
E-MAIL: losangeles@ice.it
MEXICO CITY
y/o ICE — Agencia Italiana para el Comerica Exterior
Campos Eliseos N. 385, Torre B, 9o Piso Colonia Polanco-11560 México D.F.
TEL: (+52) 5552808425-5552813928
5552813957-5552813950-5552815010
TOLL FREE: 800.696.6032 (outside Mexico City)
E-MAIL: info@italtrademexico.com
TORONTO
c/o Italian Trade Agency 480 Univeristy Avenue #800 Toronto, Ontario
M5G 1V2 Canada
TOLL FREE: 888-ITALTRADE (482-5872)
TEL: 416-598-1566
FAX: 416-598-1610
E-MAIL: toronto@ice.it
Get Social with Machines Italia via the following: www.facebook.com/machinesitalia www.pinterest.com/machinesitalia
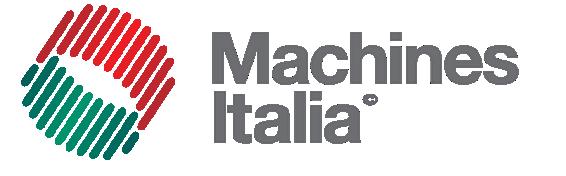
www.linkedin.com/machinesitalia www.twitter.com/ITAMachines
www.youtube.com/user/itcchicago