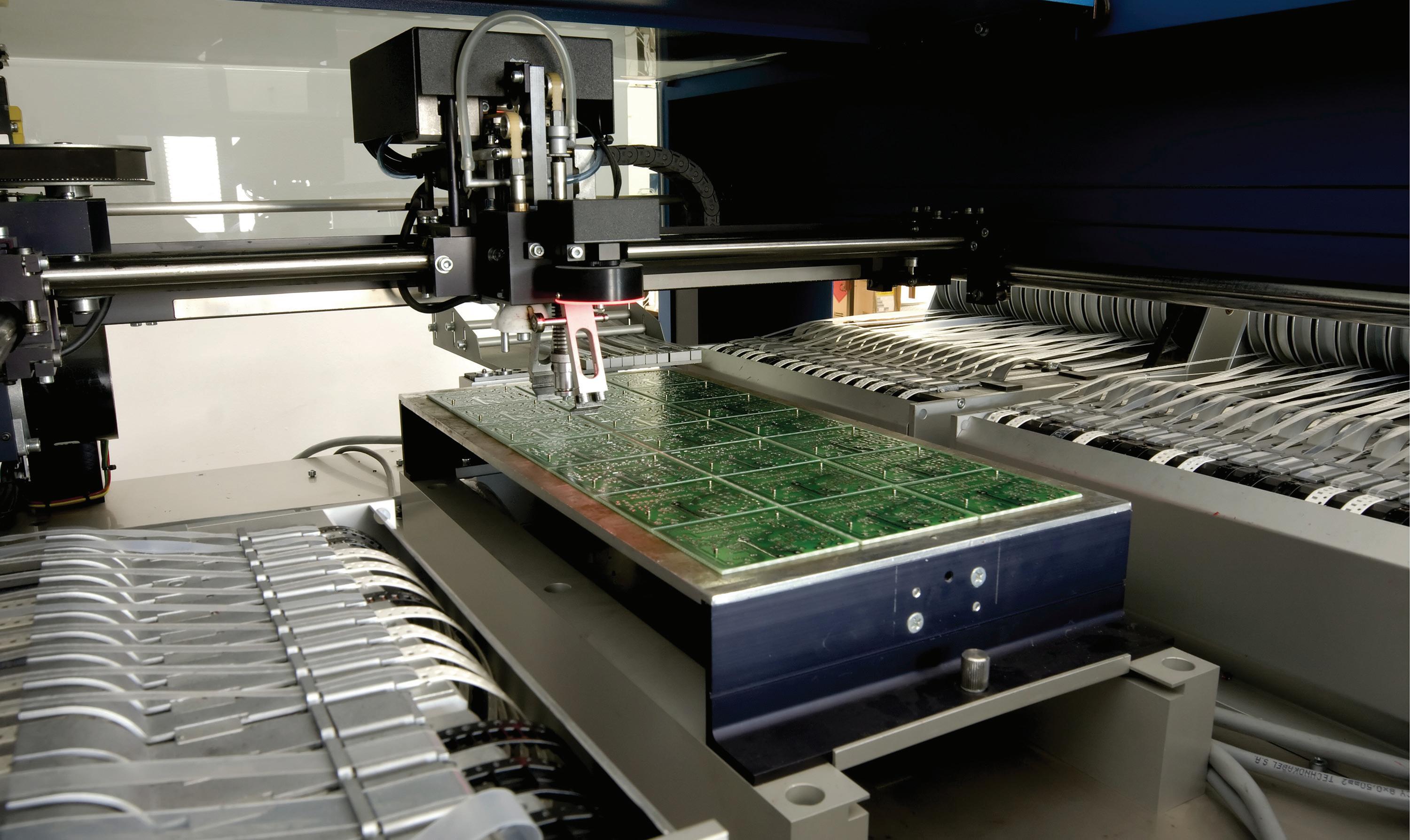
2 minute read
Common linear-motion options in 2020
Typical linear-motion arrangements consist of rails or shafts, carriages and runner blocks, and some type of moving element. Engineers differentiate these systems by the type of surface interaction (sliding or rolling) and the type of contact points — as well as how the design’s rolling-element recirculation works if applicable.
In fact, slides and rails are more advanced than ever, with advances in materials and lubrication setups (to help designs last longer in harsh applications), innovative rail geometries (to help designs withstand more misalignment and load than ever), and modular guide mounts (to boost load capacity and minimize deflection).
One word of warning here: The term linear guide can refer to any one of several different component types depending on the context. Unlike plain-bearing linear guide taxonomy (which is fairly consistent) the terminology for ball and roller linear guides is quite varied.

Shown here is a Cartesian gantry involved in the production of printed circuit boards (PCBs).
That said, the term linear guide often indicates a standalone rod assembly, rolling-element slide, or other mechanism for guiding loads. In contrast, many (though certainly not all) manufacturers use the terms linear slide and linear rail to indicate linear-motion guide elements in builds complete with some mechanical drive. The term linear stage generally implies a design with linear-guide elements, a reinforced frame, and actuation components of some type — with or without motor.
No matter the permutation, linear-motion rails, guides, and ways enable motion along an axis or rail either through sliding or rolling contact. Myriad moving elements can produce either sliding or rolling support. These include ball bearings, cam roller sliders, dovetail bearings, linear roller bearings, magnetic bearings, fluid bearings, X-Y tables, linear stages, and machine slides.
One classic rail with sliding contact is a dovetail slide, and one classic rail with rolling contact is a ball rail with a recirculating system. Sliding-contact bearings are the more straightforward type of linear-motion component. These consist of a carriage or slide that rides over a surface known as a rail, way or guide. Sliding contact occurs when the moving part directly contacts the rail section.
Older versions of these sliding-contact rails generated considerable friction during movement, so were only suitable for basic applications. However, newer versions have self-lubricating sleeves and other features to boost positioning accuracy and repeatability.
In contrast, rolling-element linear-motion systems are either recirculating or nonrecirculating. Non-recirculating types use rolling elements such as bearing balls, rollers and cam followers for movement. Recirculating types use some type of moving platform that houses a bearing block. This bearing block contains raceways with rolling elements that let the platform move along the rail with little friction. Recirculating types include linear guides and ballbushing bearings.
More specifically, rolling-element linear guides come in two basic versions — those with circular arc grooves and those with Gothic arc grooves. These groove choices are a result of industry evolution that’s enabled new geometries for better load handling.
Circular arc grooves contact bearing balls at two points. The Gothic arch contacts the balls at four points for bidirectional load capacity.
Another option for rolling-element linear motion is ball bushings that have a bushing nut lined with recirculating bearing balls. This nut rides along a round shaft to allow axial movement. History lesson: In 1946, ball bushings were introduced and established the basic mechanism of rolling-element linear-motion bearings. In today’s designs, the bushings may also have integral flanges to support axial loads.