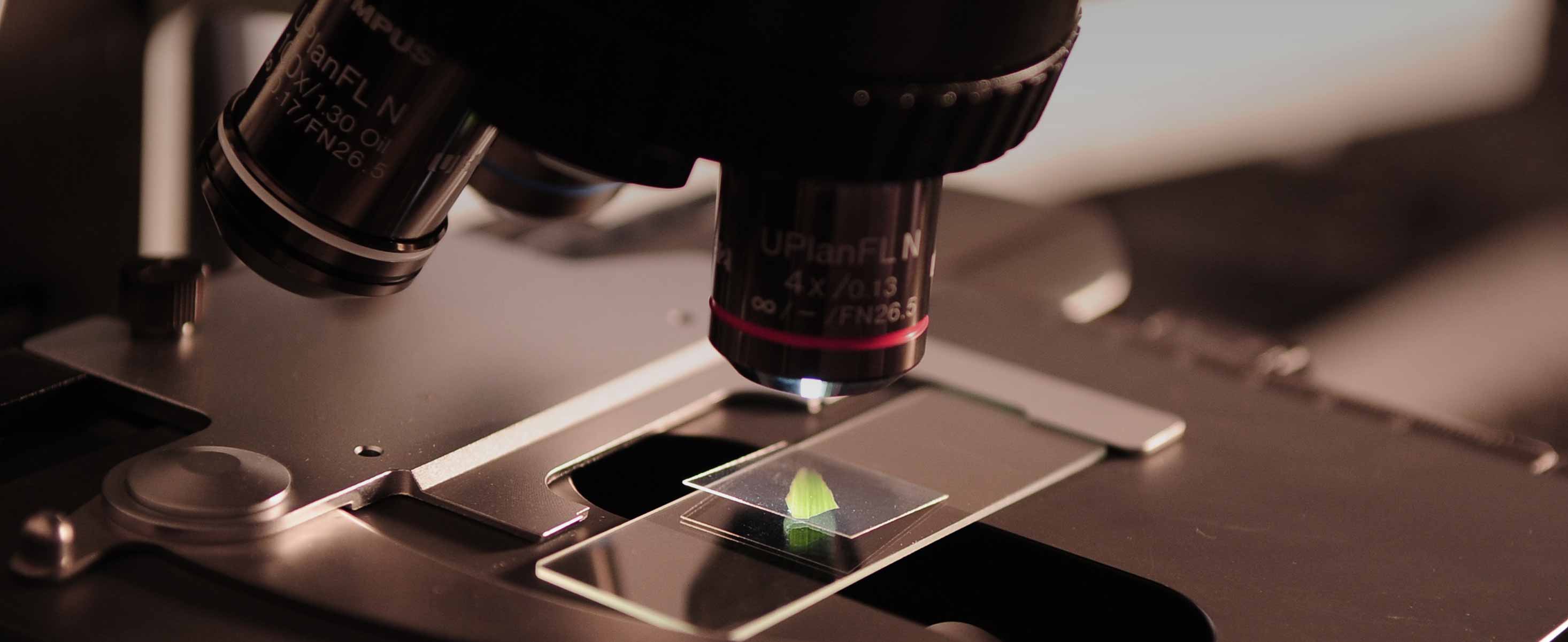
3 minute read
Basics of sprockets and chain drives

Image courtesy Martin Sprocket & Gear Inc.
Engineers have used chains in motion systems for more than a century. Theyare versatile and reliable components to drivemachinery and convey products. Now, advancesin precision and technology let designers usechains in more applications than ever. Remoteinstallations benefit from long-life chain thatrequires no lubrication, for example.Chain-based machinery abounds, but the most common industrial designs use roller chain. This type of chain consists of five basic components—pin, bushing, roller, pin link plate, and roller link plate. Manufacturers make and assemble each of these subcomponents to precise tolerances and heat treat them to optimize performance. More specifically, modern roller chains exhibit high wear resistance, fatigue strength, and tensile strength.
Roller-chain applications generally fall into two categories: Drives and conveyors.
Chain-drive applications: Most typical drive applications use an ASME/ANSI roller chain wrapped around a driver sprocket (connected directly to the motor or reducer) and the driven sprocket (often connected to a machine’s conveyor head-shaft). This portion of the drive lets the designer build a system that’s either faster or slower by simply changing the ratio of teeth between the drive and driven sprocket. The ratio of the teeth determines the reduction in rpm … so to reduce rpm, the driven sprocket must be larger than the driver sprocket. For example, if the driver sprocket has 15 teeth and the driven sprocket has 30 teeth, the ratio is 2:1, so the rpm is halved at the driven sprocket.
The easiest way to select a roller chain is using horsepower charts. First, obtain the motor horsepower and rpm of the small driver sprocket. From this, determine the chain size and number of teeth for the driver sprocket. Where roller chain must drive applications that need long life without contamination, pick chain with self-lubricating subcomponents. Where roller chain must drive applications than need high precision, pick chain with precision roller bearings at each link connection.
Conveyor applications: Conveyor chains come in myriad versions to move product horizontally, vertically, or even around curved radii. The most common conveyor chains are ASME-style (ANSI-style) attachment chains. These chains include extended pins or plates with tabs onto which parts or product-holding shoes can bolt. Common versions are single-pitch attachment chain, doublepitch attachment chain, hollow-pin chain, curved-attachment chain, and plastic-sleeve chain. The attachments let engineers put special fixtures or blocks onto the chain to serve specific conveyor functions.
One subtype of conveyor chain is the accumulating conveyor. These stop discrete products even while the chain is still moving, and they do so with minimal friction and wear. Accumulating conveyors are suitable for applications (such as assembly lines) that have products ride through several stations.
Tip: Select chain with top rollers or side rollers to let discrete products idle while the conveyor continues to run. Also pick custom attachments or work with manufacturers that make custom fixtures to handle specific parts. Many industries (including the automotive, food and beverage, and consumer-products industries) use custom attachments on their chain-based accumulator conveyors to economically and consistently move.

Morse inverted-tooth chain drives from Power Transmission Solutions of Regal-Beloit America comes in HV versions for high capacity at high speed. Silent chain is another option to make smooth, silent drives at slower speeds.
CHAINS ENDURE SUBOPTIMAL ENVIRONMENTS
The environments of many chain applications are less than ideal. Some require clean operation, without the lubrication that can contaminate products. Others expose chain-driven machinery to weather, water, or chemicals. So, chain manufacturers offer several products to meet these challenges.
Consider roller chain: One critical area where roller chains need lubrication is the pin-bushing contact zone. Self-lubricating chains stay cleaner because the exterior of the chain is free of excess lube. These chains also attract less dust and particulates than regular chains. Such roller chains are useful where oil contamination is a concern, including paper-product or woodprocessing industries.
Specialty coatings and stainless steel can delay or prevent corrosion.
Nickel-plated chains offer another alternative for chain coatings, providing some protection for mildly corrosive environments. Stainless steel chains offer superior corrosion resistance ... but designers must be aware that regular stainless steels cannot be hardened in the same manner as carbon steel. Therefore, the load carrying capacity of stainless steel is lower than carbon steel.
Proper chain maintenance requires periodic inspection. All chains must be checked for damage, wear, and chemical attack on a regular basis.
Another issue is elongation due to wear. Eventually roller chains wear to so much that they necessitate replacement—typically at 1.5% (12.180 in./ ft) to 2% (12.240 in./ft) elongation. Chains may work until they reach 3% elongation but are at increased risk for suboptimal performance.