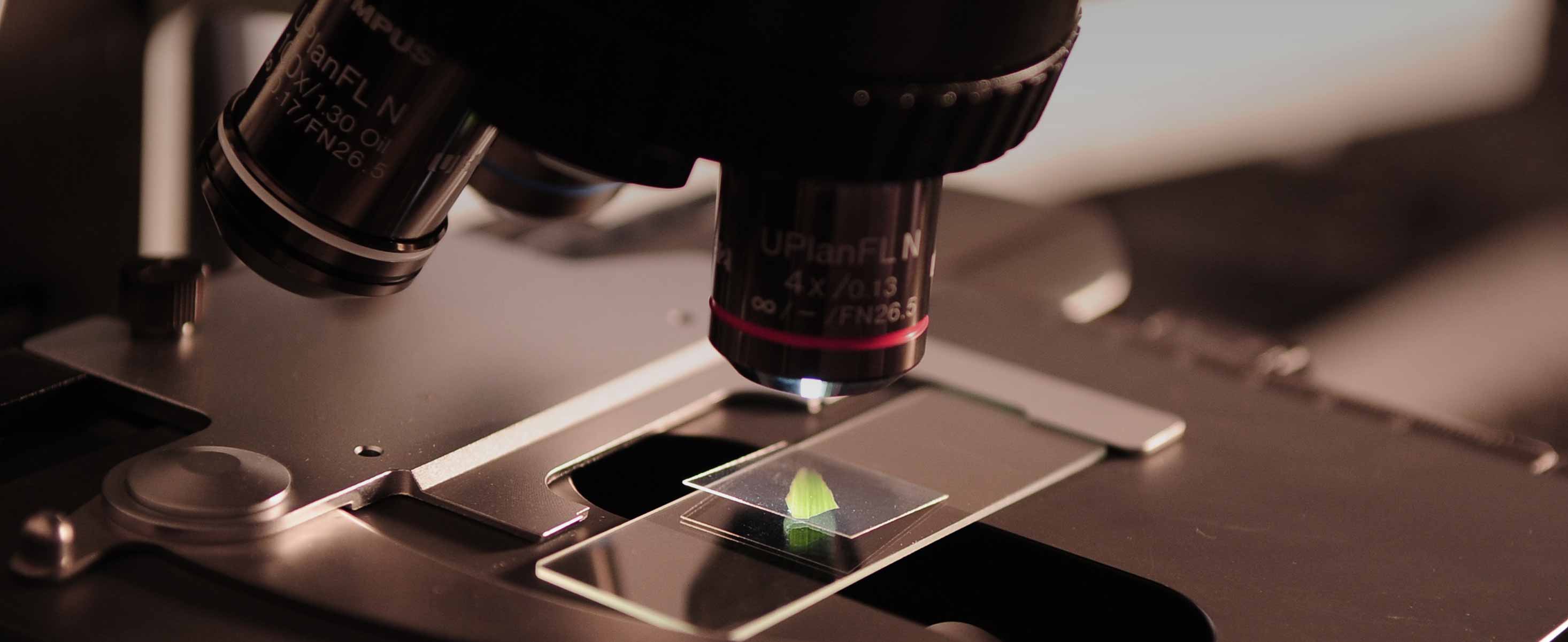
7 minute read
Brakes, clutches, and torque limiters
There are three types of electrical braking for motors —regenerative braking, dynamic braking, and plugging. Of the threemethods, plugging provides the fastest stop, but it can be harsh onboth the electrical and mechanical components. Because of this, it’sthe least commonly used method of braking … though appropriatefor some applications.
Plugging (called reverse current braking in some contexts) is possible on both dc motors and ac induction motors. For dc motors, plugging is via reversal of armature-voltage polarity. When this happens, back EMF voltage no longer opposes supply voltage. Instead, the back EMF and the supply voltage work in the same direction, opposing the motor’s rotation and causing it to come to a near-instant stop. The reverse current produced by the combined supply voltage and back EMF is extremely high, so resistance is placed in the circuit to limit the current.
One potential problem with plugging for braking (especially when braking time is short) is that it can be difficult to brake the motor at exactly zero speed. Another drawback to plugging is that it can induce high mechanical shock loads on the motor and connected equipment, due to the abrupt stop that it causes. Plugging is also very inefficient for stopping and generates significant heat.
So for most modern motion designs requiring high throughput — external brakes and clutches are required to get sufficiently quick stops or disengagement. This applies to conveyors, airport-baggage handlers, escalators, and elevators … as well as other axes that make frequent stops and starts — even as few as 10 cycles a minute in some cases. With stops and starts at much higher cycle rates, motor inertia may degrade the quickness with which starts and stops are possible. So here, clutch-brakes are often more suitable — as they disengage the driven load from the motor to allow the former to run even while the brake engages and stops the load. Of course, though we focus on responsiveness here, failsafe design features are another main driver of brake and clutch inclusion.
Mechanical, electric, fluidic, and selfactuated clutches and brakes are suitable for different applications. For example, springset brakes benefit motion designs that slow loads with the motor before the brake engages … and they’re suitable as holding mechanisms. Control of electric brakes is easy, and they can keep pace to a thousand cycles per minute. Most air-actuated brakes and clutches are cool-running and hold with minimal input. Friction brakes with drum, disc, and cone geometries deliver e-brake functionality with failsafe holding.
Brake or clutch size and type depend on whether the axis at hand will make emergency stops or softer stops that sacrifice the clutch or brake to protect systems and loads from shock. Or sometimes it’s more essential that the brake deliver soft stops to prevent shifting loads and misalignment. After that, other criteria — cycle rates, thermal capacity, machine envelope, and MRO schedules — dictate final selection.
Some tips: Size clutches and brakes to the machine axis’ motor torque. Where a brake must stop vertical loads, account for how motors can briefly draw current to output in excess of their rated torque. Consult performance curves in manufacturer PDFs for dynamic torque ratings at set speeds to match the brake or clutch to peak motor-output torque.
CLUTCH AND BRAKE ENGAGEMENT
Key parameters dictate which clutches and brakes are suitable for a given application: The first parameter is the mode of motion and whether the axis needs a brake or clutch. Clutches generally bridge moving machine sections to shape relative motion, while brakes’ main job is to stop and hold rotating elements. Several design variations exist, and a main differentiating factor is the way in which a brake or clutch engages. Some options include mechanical, electric, fluidic, or self-actuation.
Brakes and clutches using fluidpower actuation usually include a piston to physically engage friction discs for torque transmission from an input to an output. Hydraulically and pneumatically actuated clutches and brakes are quick-response units that act on fluid pressure and piston mass, so engagement speed follows control pressure.
Some air-actuated brake and clutch designs are specifically designed to run coolly … and maintain hold with minimal power.
Some caveats though: In many clutches, full piston force transmits through a bearing — effectively a wear point — to let the body rotate as the housing stays put. Here, the bearings and high loads also limit operating speed. Brakes using fluid-power actuation don’t need such bearings.
Brakes and clutches using mechanical actuation include a lever for mechanical advantage to trigger engagement and disengagement. This levering usually works to squeeze friction discs together for torque transmission. When the mechanism moves, the clutch or brake condition changes from engaged to disengaged or vice versa. Some such brakes and clutches have a locking mechanism to keep the unit as it is until repowering. Such clutches and brakes have no bearings to fail; are fairly speed tolerant; come in optional one-position setups; are unaffected by power failures; and offer automatic overload release during overtorqueing or locking. On the other hand, many mechanically actuated clutches and brakes don’t automatically disengage during power loss — and most need adjustments to compensate for wear.
Clutches and brakes that are electromagnetically engaged (or disengaged, depending on design) use a magnetic coil to generate a magnetic flux — either to move an armature from friction-disc contact or to move the armature for squeezing discs together. That’s because electromagnetic clutches and brakes are either electrically activated or spring-applied-electricallydeactivated setups. The latter does doubleduty as a failsafe during power loss.
Electromagnetic clutches and brakes are high-speed tolerant; exhibit long life; and come with self-adjustment mechanisms to compensate for friction-disc wear. But there are drawbacks with this technology too: They need bearings to support a stationary coil — and the bearings bear a light load from the radial flux-path use. What’s more, electromagnetic clutch or brake engagement time exceeds that of other designs due to the time needed to generate the coil’s magnetic field.
Clutches and brakes called wet-running units contain fluid to work by the effects of a transmission-fluid boundary layer. More specifically, fluid shears between friction discs and drive plates. As the parts come together, the fluid in shear transmits torque. This eliminates direct friction-disc contact during high-speed slip. Just note that oil shear generates heat even in neutral; there’s oil shear until the input and output are almost to equal rpm.
But in applications that must rapidly stop, start, reverse, and change speed, clutch brakes that use oil-shear technology excel. Heat from the friction dissipates as the fluid circulates to the housing. That’s useful on axes with start-stop cycles or cycle rates to highcycle setups (to 300 cycles per minute, as a rule of thumb). Here, oil-shear brakes last five to ten times longer than dry clutch-brake offerings. (Just review the application before specification to prevent heat from becoming an issue.)
MORE ON SIZING BRAKES AND CLUTCHES TO TORQUE AND SPEED AND CYCLES
The size and type of brake or clutch most suitable for a given design depends on whether the machine needs emergency stops or softer stops that sacrifice brakes to protect transported loads from shock. Then other application criteria (including the machine envelope, thermal capacity, cycle rates, and inspection and repair schedules) dictate final selection. In other machines, it’s more important that brakes prevent shifting loads and misalignment.
Expressed in lb/ft, N/m, or lb/in., static and dynamic torque values express clutch or brake output capability. Applications needing dynamic braking are those in which the brake controls rotating-axis motion by absorbing kinetic-energy changes. Dynamic clutching is that during which a clutch brings a stationary output to the input rpm by assuming the slower axis’ kinetic-energy delta.
Static-torque ratings (values that describe clutch and brake behavior when the units aren’t absorbing any kinetic energy) depend largely on torsional load. Reaching static torque operation with a clutch needs a clutch that must engage prior to rotating the input — so the clutch effectively functions as a coupling between in and output.
In contrast, reaching static torque operation with a brake just takes holding the output element stationary.
Static torque equals clutch holding torque when there’s no relative shaft rpm difference between input and output — or (in the case of a brake) when the shaft is stopped. The point at which a system exceeds a unit’s static torque is aptly called the breakaway torque. This is what a machine assembly must reach before relative motion arises between the shafts (in the case of a clutch) or before the shaft starts turning (in the case of brake).
Common clutches come in pulley and shaft-to-shaft variations. For the latter, the clutch output and input are inline.
Designers sometimes boost dynamic torque rating (and shorten response time) by selecting larger brakes and clutches — though keep in mind that this also increases torque and shear forces (due to torsion) on mounts to nonrotating machine-frame segments.
Dynamic torque depends on the rpm delta between in and output (for a clutch) and operating and zero rpm for a brake. Dynamic torque is usually about 50 to 80% of static torque. In friction-based designs, this value depends on the contact surfaces’ friction coefficient. Because that changes slightly (with the portion of operation the brake or clutch is delivering) designers usually employ an average coefficient for design calculations.
MORE ON DYNAMIC-TORQUE CALCULATIONS
The specifications of the electric motor driving the load partially dictates clutch or brake size. Dynamic torque in lb-ft = (5,250· hp/ rpm) · safety factor. Here rpm = Rotational shaft speed the brake must stop (or the speed difference between a clutch output and input). The safety factor adjusts for the motor type and its typical torsional output during operation. Electric motors have a safety factor near unity, as their output is quite consistent.
Note how a major consideration is time needed to change the axis speed. Another parameter is the duty cycle: If there are more than a few incidences of engagement per hour, duty cycle becomes an influencing design factor. Note that high-cycle applications running to 300 cycles per minute (as in indexing with a clutch brake) each clutch engagement transfers a torque spike to the connection between the motor shaft and input shaft of the clutch brake. High-cycle applications can cause severe hammering on the shaft connection of the motor to the clutch brake.
For convenience and ease of assembly, standard C-face connections are most common — but the loose fit can cause torque to transfer through the key and keyway, which hastens failure. Here, clutches and brakes that connect with shrink-fit or clamping couplings for a 360° connection perform better.
The dynamic-torque calculation presented above is based on time to stop the load or bring it to speed — not accounting for time needed for clutch or brake actuation. Consider clutch brakes that are electromagnetically engaged: Here a coil must build an electromagnetic field for armature activation and friction-disc engagement — a process that can take 10 to 500 msec depending on unit size.
Cycle rate is how many times per minute a brake or clutch must engage — and the amount of energy a brake dissipates or a clutch absorbs before the next cycle. Except for regenerative setups, energy dissipates as heat — with heat-load maximums published by manufacturers. But applications that run fast or hot or are extreme in some other way need extra evaluation …
• Machinery running beyond a few hundred cycles per minute may need clutches and brakes that are larger than performance curves indicate.
• Spring-set brakes benefit motion designs that slow loads with the motor before the brake engages; they’re also suitable as holding mechanisms.
• Brakes using permanent magnets automatically adjust for wear. Industrial designs operating in hot environments may benefit from friction brakes with specialty friction-surface geometries and phenolic resin or ceramic materials. Motion applications that won’t see a lot of maintenance also benefit from longer-life friction materials.