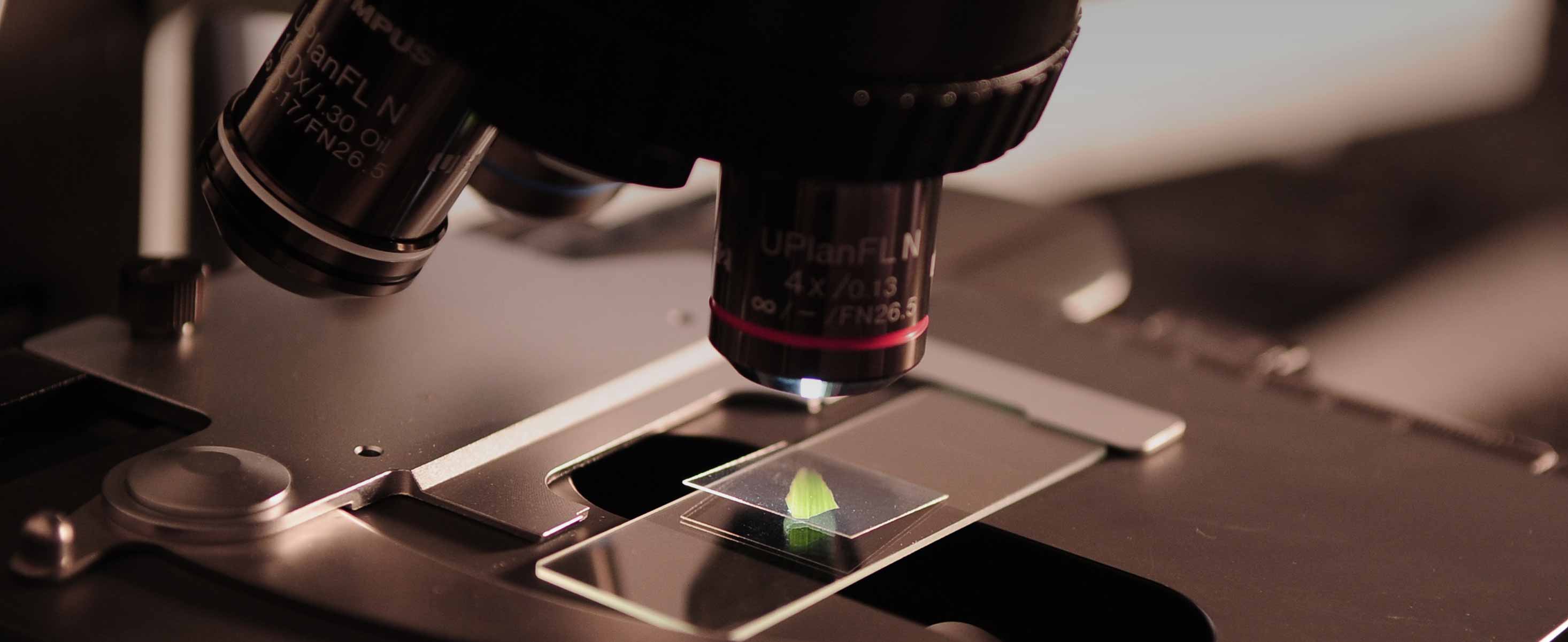
3 minute read
Fundamentals of dc motors

The EnduraMax 75i Series from Allied Motion Technologies is a 75-mm diameter brushless dc motor with an all-digital integrated drive. Command inputs to the motor can be ±10 Vdc, 4 to 20 mA, or via an optional CANopen or Modbus port.
Motors can be classified in a number of different ways, but one of the mostcommon is whether they are ac or dc motors. This division refers to the type of currentthat drives the motor with ac meaning alternating current and dc being direct current.
Specifically, dc motors operate using magnetic fields produced in the motor, either via electromagnetic windings or permanent magnets. There is also some type of mechanism that commutates or switches the current flow, using either electromechanical means or electronically.
Common dc motor types include brush, brushless, and permanent magnet (PM) motors. Brushed dc motors are sometimes referred to as wound-field motors, because a wound and lacquered coil of copper wire produces the electromagnetic field. There are permanent magnet, shunt, series, and compound-wound brushed dc motors.
Brush dc motors have commutators and brush contacts to pass current to the rotating rotor’s copper-wire windings. Designers can control speed by changing rotor voltage (and current with it) or by changing the magnetic flux between rotor and stator through adjustments of the field-winding current. Brush orientation to the rotor’s commutator bar segments mechanically controls the phase commutation.
The fact that dc brush motors let designers control field and rotor windings means they’re suitable for applications that need simple and cost-effective torque and speed control. However, increased functionality from electronics for PM motors means that this advantage is less pronounced than it once was. Moreover, current on both rotor and stator generate heat that limits the motors’ continuous-current ratings. The motors also present a spark hazard, so can’t go in explosive settings. At certain periods during the dc motor rotation, the commutator must reverse the current, reducing motor life with arcing and friction. So, brushed dc motors require more maintenance in the form of replacement of springs and brushes that carry the electrical current, and replacement or cleaning of the commutator. And because brush wear produces particles, designers shouldn’t use dc brush motors in cleanrooms. Same goes for applications that need high precision, as friction from brush-commutator engagement make for long position-settling times.
VOLTAGE AND SPEED RELATIONSHIPS
In a dc motor, the relationships between voltage and speed and between current and torque are straightforward.
When the load (torque) on the motor is constant, speed is proportional to the supply voltage. And when the supply voltage is constant, speed is inversely proportional to the load (torque) on the motor.
Specifications for dc motors include two voltage parameters: nominal voltage and a range of operating voltages. Nominal is the recommended voltage at which the motor should be operated, although the motor can be run with a voltage that falls anywhere within the specified range.
Nominal voltage is a key parameter for dc motors. In fact, a motor’s torque-speed curve is based on its nominal voltage. The slope of the torque-speed curve is determined by dividing the no-load speed of the motor by the stall torque. No-load speed is the speed at which the motor turns when running at nominal voltage and without a load. Stall torque is the maximum torque produced by the motor when running at nominal voltage. (The term “stall torque” is used because it occurs when the motor has zero velocity—i.e., when it is stalled.)
No-load speed: The speed at which the motor turns when running at nominal voltage and without a load (zero torque production).
Stall torque: The maximum torque produced by the motor when running at nominal voltage.
Other parameters that are given at nominal voltage include:
Nominal speed: The speed achieved when the motor operates at nominal voltage and nominal torque at ambient temperature (typically 20 to 25°C).
No-load current: The current the motor draws when operating at nominal voltage and with no load (zero torque production).
Operating a motor at a voltage below nominal generally has no detrimental effect on performance. In fact, running a motor at lower than nominal voltage (and, therefore, slower than nominal speed) can result in less brush and commutator wear (for brushed motors), lower current consumption, and longer motor life. On the other hand, running a motor at a voltage higher than nominal increases current draw and can cause the motor coils to overheat, decreasing motor life.