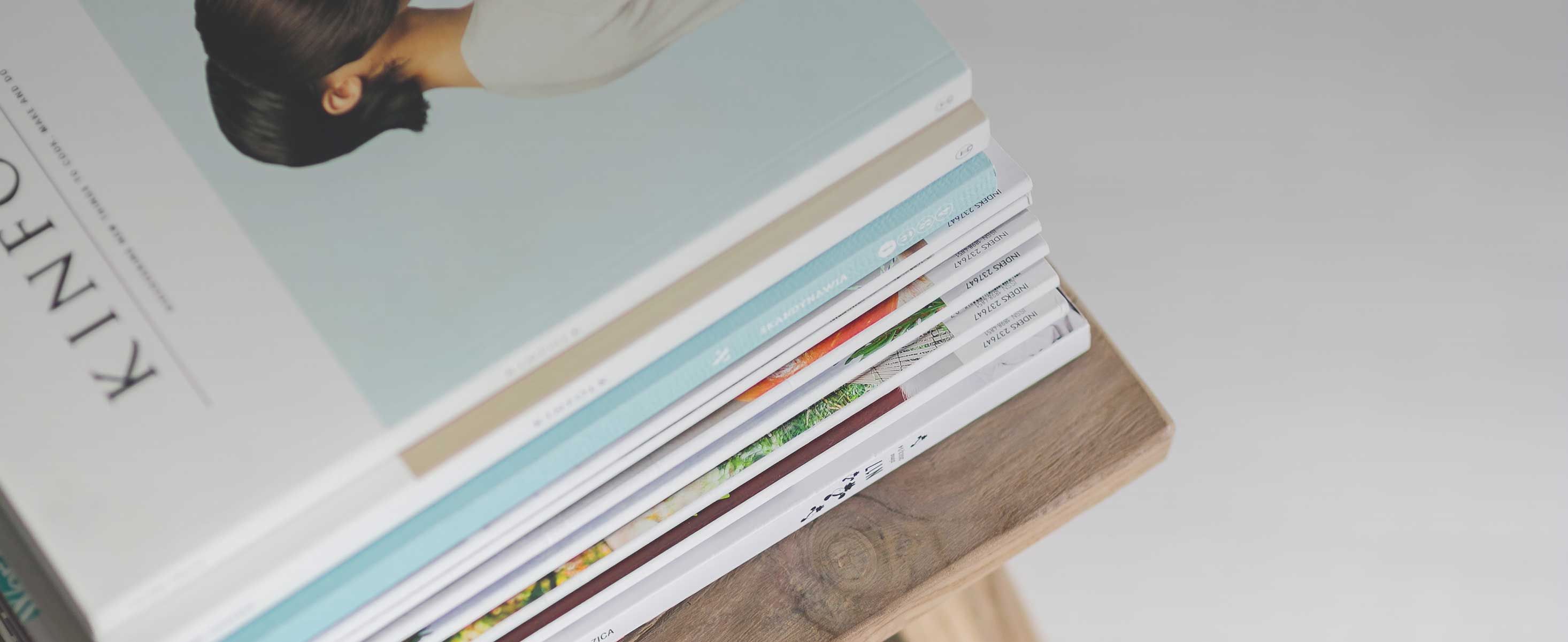
4 minute read
Comparing options for linear bearings, slides, and guides
Linear-motion devices incorporating ball and roller elements include plain bearings, ball bushings, recirculating roller bearings. Confusing matters is the fact thatindustry uses many linear-motion terms interchangeably … and many terms such as linear guides are so generic that they can refer to any one of several different products.
While the plain-bearing guide taxonomy has less variability in terminology and specification, ball and roller linear guides have quite a lot. So let’s review all these terms that are used to identify, describe, and specify them.
In many though not all cases, the term linear guide indicates a standalone guide rod, ball slide, or mechanism solely for guiding loads. In contrast, many manufacturers use the terms linear slide and linear rail to indicate a linear-motion guide element that is incorporated into an integrated build complete with mechanical drive. The term linear stage generally implies a design has guided elements as well as some mode of mechanical linear actuation and reinforced body — often sans inclusion of the motor.
Motorized rails (more commonly called linear actuators) abound — though the distinction here is that there are countless linear actuators sold sans any guided element. That’s useful for OEMs aiming to employ some specialized linear guide or omit it altogether.
Taxonomy variations don’t apply to just product descriptions: Design types and technical features are also called different names depending on the component manufacturer.
Plain bearings are the simplest type of linear guide, relying on sliding contact between two surfaces. Their construction can be boxway, dovetail, or shaft and bushing. Boxway bearings are able to carry the highest loads, while dovetail designs require less precise machining and assembly. Plain bearing bushings are simple to manufacture and install, but their unsupported shafts give them limited load capacities and make them vulnerable to deflection.
While metal surfaces provide the highest stiffness and load capacities, plain bearings can also be made of plastics or composites for high corrosion resistance and inherent lubricating properties. It’s important to note that sliding contact should always be between dissimilar materials, with one element being harder than the other. This allows wear to be concentrated in the softer element.
Plain bearings have a high coefficient of friction, typically 0.05 to 0.1, when compared to rolling-element bearings. But unlike rolling elements, they can withstand shock loads and vibrations without significant damage to the surfaces. Plain bearings are also less sensitive to contamination and rarely experience catastrophic failure.
In contrast, rolling-element linear guides add balls or rollers between the two bearing surfaces. Rolling-element bearings can be recirculating (profiled rail bearings or linear bushings or linear bearing guides) or non-recirculating linear bearings in the form of some cam roller guides or crossed-roller slides. Recirculating designs allow unlimited motion along the length of the guide rail or shaft, where non-recirculating designs are limited in stroke by bearing length.
PROFILED RAIL TRACK GEOMETRIES
A significant advantage of rolling-element linear guides is their low coefficient of friction, which is typically 0.005 to 0.01. Because they’re made of bearing steel, they have high load capacities and can be preloaded for very high rigidity. One caveat is that preload increases friction and must be taken into account when sizing rolling element linear guides.
While plain linear bearings can be made from a wide variety of materials, profile-rail rolling-element bearings come in the most diverse track geometries and raceway arrangements. Track geometry defines how the rolling elements make contact with the raceways. Profiled rail track geometries can be:
• Circular arc — which provides lower friction or
• Gothic arch — which gives higher moment capacities.
Circular arc geometry produces twopoint contact between the ball and the raceway. This gives the assembly a lower friction coefficient and smoother running characteristics.
Gothic arch geometry provides fourpoint contact between the ball and the raceways, resulting in higher moment load capacities … but also higher friction.
More specifically, the Gothic arch design provides two contact points on the ball and two contact points on the raceway.
Determining the life of rolling element linear guides is done by calculating the L10 bearing life — a theoretical but statistically formulated prediction of the distance the bearing can travel before it reaches its fatigue life. The L10 life is based on the type and magnitude of loading, although environmental factors such as shocks, vibrations, and contamination can reduce the life of rolling element bearings.
While the construction of linear bearings that employ balls for friction reduction isn’t a technical specification, it is typically referenced in manufacturer catalogs. That’s in part because various linear-bearing construction options have a significant effect on performance.
PROFILED RAIL ARRANGEMENTS
To review, raceway arrangement refers to where and how the load-bearing balls sit on the profiled rail. There are two raceway arrangements ... face-to-face and backto-back.
The face-to-face arrangement is often called the X arrangement because the contact lines between the balls and the raceways point inward, making an X inside the profiled rail. This arrangement gives the assembly equal load capacity in all directions but reduces its ability to handle moment loads.
The back-to-back arrangement is also called the O arrangement because the contact lines point outward — making an O around the rail. This design gives a longer moment arm and allows the bearing to withstand high moment loads.
Raceway geometry determines the number of contact points between the ball and raceway and affects the bearing block’s friction and load capacity.