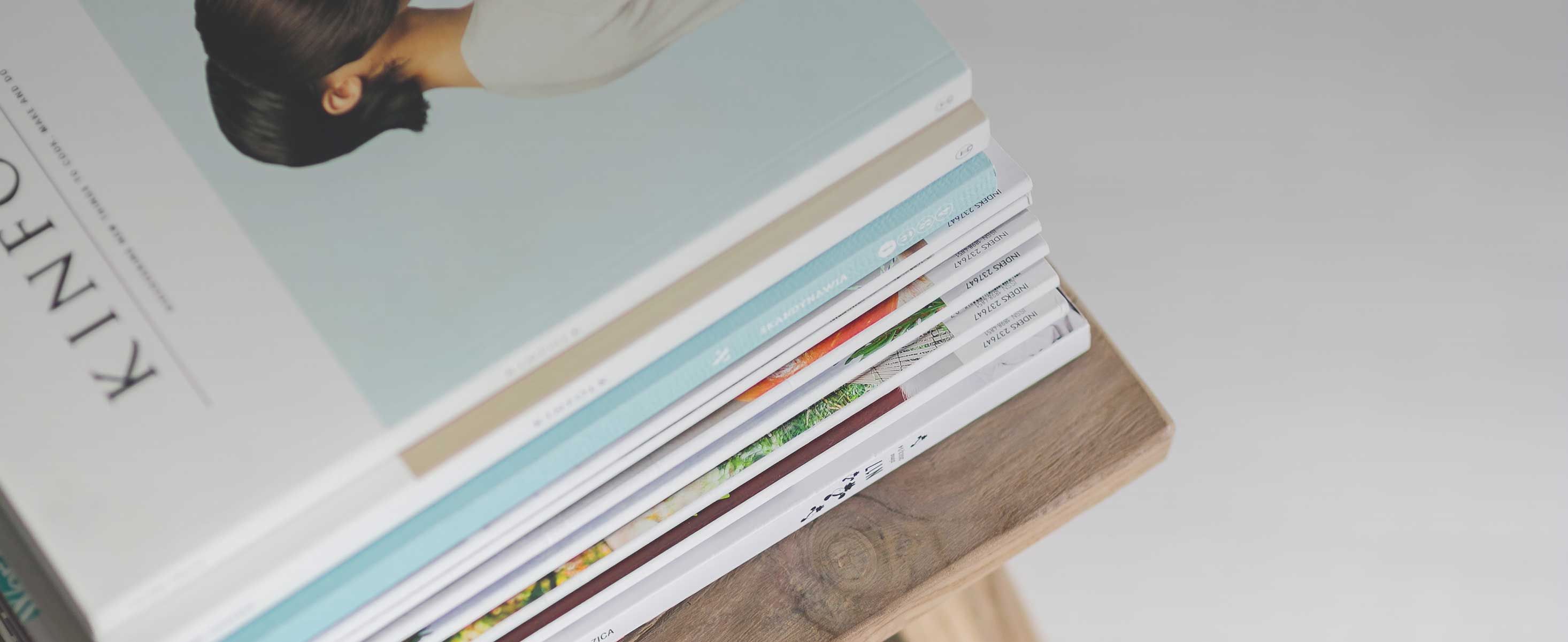
5 minute read
Using gears to change the inertia ratio of a motor-driven system
Any system using a motor to drive a load with precise positioning, velocity, or torque requires consideration of inertia. That’s because the ratio of load inertia to motor inertia significantly impacts a motor’s ability to effectively and efficiently control attached loads. That’s especially true during the acceleration and deceleration portions of the motion profile.
In this context, the inertia to which we’re referring is mass moment of inertia, sometimes called rotational inertia — an object’s resistance to change in rotational speed. An object’s mass moment of inertia depends on its mass and geometry … usually the radius defined by the object’s center of mass and the point around which the object rotates.
If the load’s inertia significantly exceeds the motor’s inertia, that load will essentially “try” to “drive” the motor … and the motor will struggle to get the load to its target position, speed, or torque. That in turn will prompt the motor to draw higher current … which decreases efficiency and increases wear on the motor and electrical components.
On the other hand, if the motor’s inertia significantly exceeds the load’s inertia, it’s likely that the motor is oversized. That in turn has negative implications throughout the system — including higher initial cost, higher operating cost, larger footprint, and the need to oversize other components such as mounting hardware, couplings, and cables.
If the inertia ratio is too high, the load inertia is much higher than the motor inertia and will cause problems with positioning accuracy, settling time, or control of velocity or torque.
If this is the situation at hand, load inertia that is seen by (reflected to) the motor can be decreased by adding a gearset or gearbox between the motor and the load:

Where J L = Inertia of the load reflected to motor and J M = Inertia of the motor
Adding a gearset or a gearbox to a motor-driven system reduces the load inertia by the inverse square of the gear ratio, meaning that even a relatively low gear ratio can have a significant effect on the inertia ratio.

Where J L = Inertia of load reflected to motor; J D = Inertia of drive — whether ball screw, belt, or rack-and-pinion set; J E = Inertia of external (moved) load; J C = Inertia of the coupling; J G = Inertia of gearset or gearbox; and i = Gear ratio
Note that the inertia of the gearset or gearbox J G is added to the load inertia, but its effect is typically small compared to the reduction provided by the gear ratio.
In addition to optimizing the load-motor inertia ratio, gearboxes are often used in motion control applications to increase the torque delivered to the load from the motor, but they also decrease the rotational speed delivered to the driven component from the motor, by an amount equal to the gear ratio. This is why gearboxes are often called gear reducers or speed reducers.
In other words, if a motor running at 1,200 rpm is driving a load through a 3:1 gearbox, the rotational speed delivered to the load will be 1,200 ÷ 3 = 400 rpm. This reduction in speed can enable the system to operate at a more favorable location on the motor’s speed-torque curve.
Although it is possible to use a gearbox or gearset that is configured to reduce torque (and increase speed) in motion control applications, a more typical solution here is to choose a smaller motor.
Spur gear basics
Spur gears are a type of cylindrical gearing with shafts thatare parallel and coplanar ... and teeth that are straight and orientedparallel to the shafts. They’re arguably the simplest and mostcommon type of gear – easy to manufacture and suitable for a widerange of applications.
Spur gears are a type of cylindrical gearing with shafts that are parallel and coplanar ... and teeth that are straight and oriented parallel to the shafts. They’re arguably the simplest and most common type of gear – easy to manufacture and suitable for a wide range of applications.
The teeth of a spur gear have an involute profile and mesh one tooth at a time. The involute form means that spur gears only produce radial forces (no axial forces), but the method of tooth meshing causes high stress on the gear teeth and high noise production. Because of this, spur gears are typically used for lower speed applications, although they can be used at almost any speed.
Involute gear teeth have a profile that is the involute of a circle. So as two involute gears mesh, they contact at a single point where the involutes meet. This point moves along the tooth surfaces as the gears rotate ... and the line of force (known as the line of action) is tangent to the two base circles. In this way, the gears adhere to the fundamental law of gearing — that the ratio of meshing gears’ angular velocities must remain constant throughout the mesh.
Spur gears can be made from metals such as steel or brass or from plastics such as nylon or polycarbonate. Plastic gears are quiet but at the expense of strength and loading capability. Unlike other gear types, spur gears don’t experience high losses due to slippage, so they generally have high transmission efficiency. Multiple spur gears can work in series (referred to as a gear train) to achieve large reduction ratios.
The two types of spur gears are external and internal. External gears have teeth that are cut on the outside surfaceof the cylinder. Two external gears mesh together and rotate in opposite directions. In contrast, internal gears have teeth cut on the inside surface of the cylinder. An external gear sits inside the internal gear, and the gears rotate in the same direction. Because the shafts are positioned closer together, internal gear assemblies are more compact than external gear assemblies. Internal gears are primarily used for planetary gear drives.
Spur gears are generally best for applications needing moderate speed reduction and torque multiplication — such as ball mills and crushing equipment. High-speed applications that use spur gears (despite their high noise levels) include consumer appliances such as washing machines and blenders. Though noise limits the use of spur gears in automobiles, they’re common in aircraft engines, trains, and even bicycles.