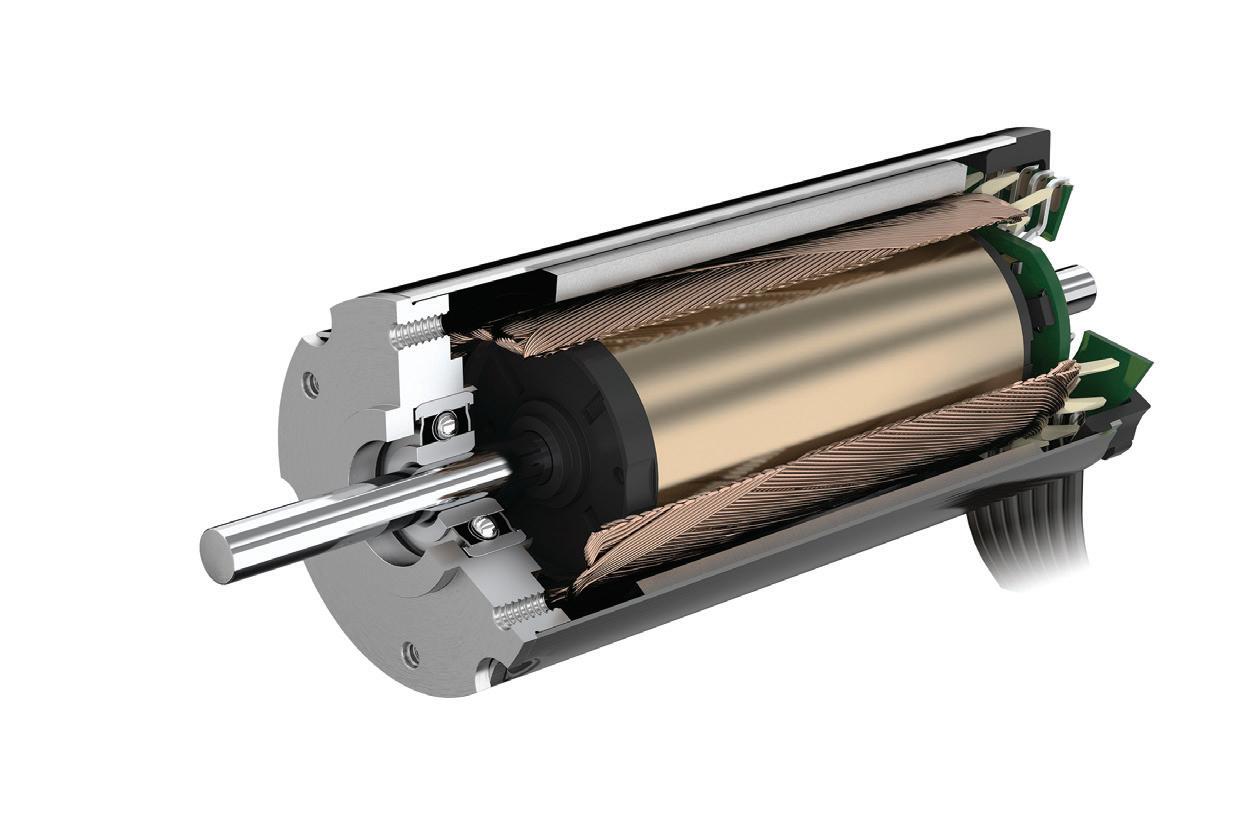
1 minute read
WAREHOUSE AUTOMATION
to “Intralogistics 4.0.” They are used for storage, removal, and dispatch preparation to optimize material flow, relieve employees, and replace conventional lift or pallet trucks.
For example, autonomous picking robots allow precise handling of individual objects. A typical picking robot comprises a lifting column, gripper, and a drive unit — perhaps a Faulhaber BX4 series brushless dc servomotor with an integrated motion controller and planetary gearhead. When used in the gripper, this combination ensures precise positioning during storage or retrieval, all during continuous operation with constant load changes. Yet the complete drive unit weighs only about 300 g and doesn’t require a counterweight even when the gripper fully extends.
cooperation with other robots and human workers. They need to be flexible and adapt to changing processes and the goods they handle,” said Kevin Moser, business development manager at Faulhaber.
Faulhaber engineers address challenges that modern warehouses face by evolving drive systems to match the industry’s shrinking need — the need for smaller, more powerful motion control components that reduce weight and improve speed.
Motion control for the modern robot Autonomously driving and selfcontained logistics robots are critical
The brushless dc servomotors are compact, with a diameter of only 32 mm and a length of 85.4 mm. This small size makes it possible to design a very flat gripper that can pick up packages stored just above the ground, making optimal use of expensive storage areas. With the brushless commutation system, the motors are long-lasting, deliver high torques, and run quietly with a balanced rotor. Integrated current control limits torque demands and protects the drive against overload.
“Robot design needs to be robust, lightweight, and very compact, resulting in low maintenance, low power consumption but high efficiency for extended battery life and minimum downtime,” said Moser. “Modularity is also important: As operations expand in a modular system, it is easy to add additional robots.”
Graphite-commutated dc micromotors of the CXR series combined with matched gearheads have also proven themselves in handling tasks. Their commutation system is well suited for dynamic, high-performance applications with fast start-stop operations required in many handling systems and automatic sorting, such as where switches are used to change routes on transport paths.
With their linear characteristics, the dc motors are easy to control. Combined with high-resolution encoders, they are ideal for precise positioning tasks. High-quality neodymium magnets and Faulhaber winding ensure high-power density in a compact design. The motors can be installed directly in handling elements and lift considerable weight despite their small size.
“As the degree of automation of intralogistics processes throughout the entire value chain increases, robots must be more autonomous, intelligent, and interconnected. Requirements regarding the speed and dynamics of the systems are increasing as well. This requires the robots to have reliable, safe, and smart