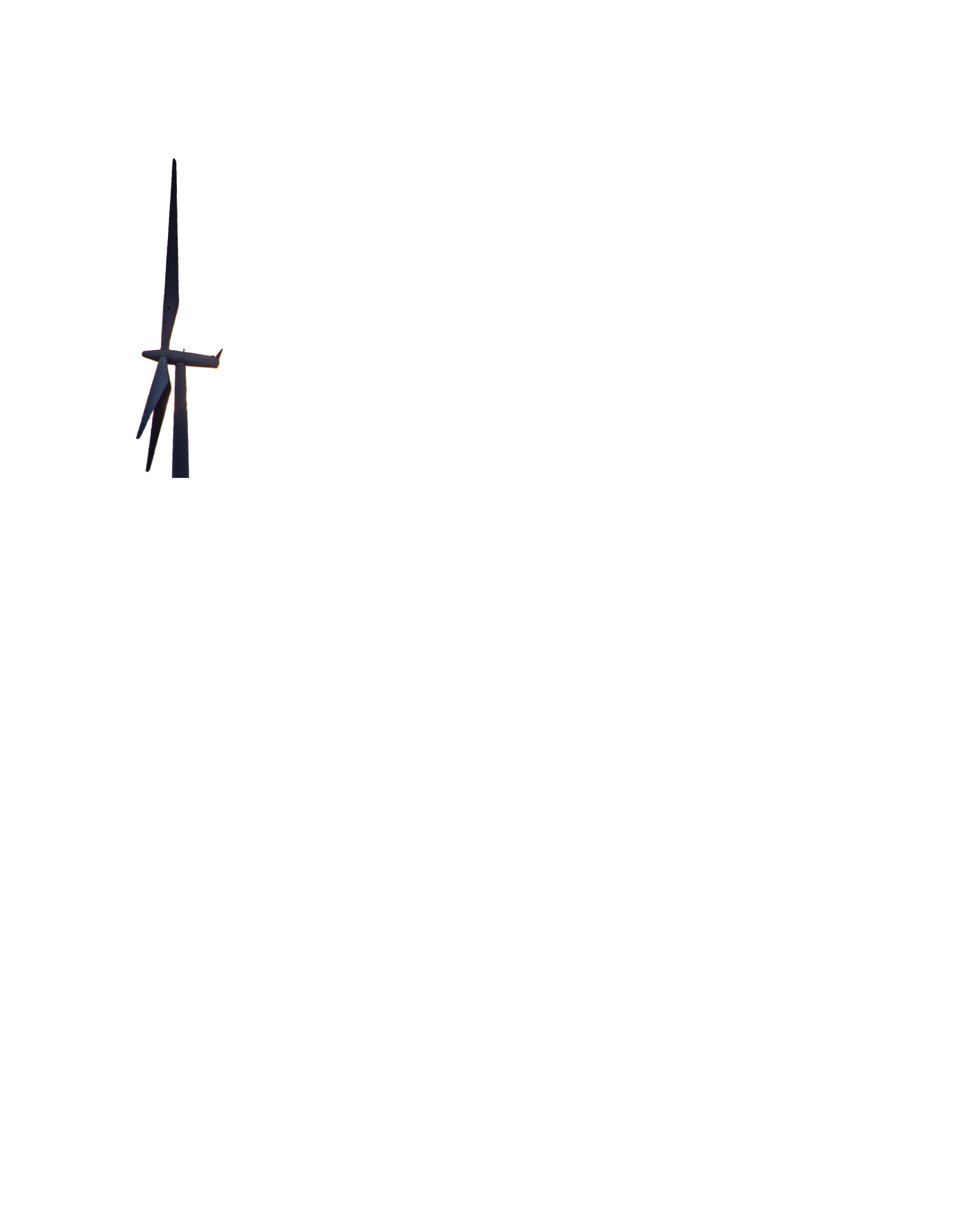
• Superior Pitch Control
• Multiple years of valve life
• 3-Year warranty
• Over 4,000 valves installed
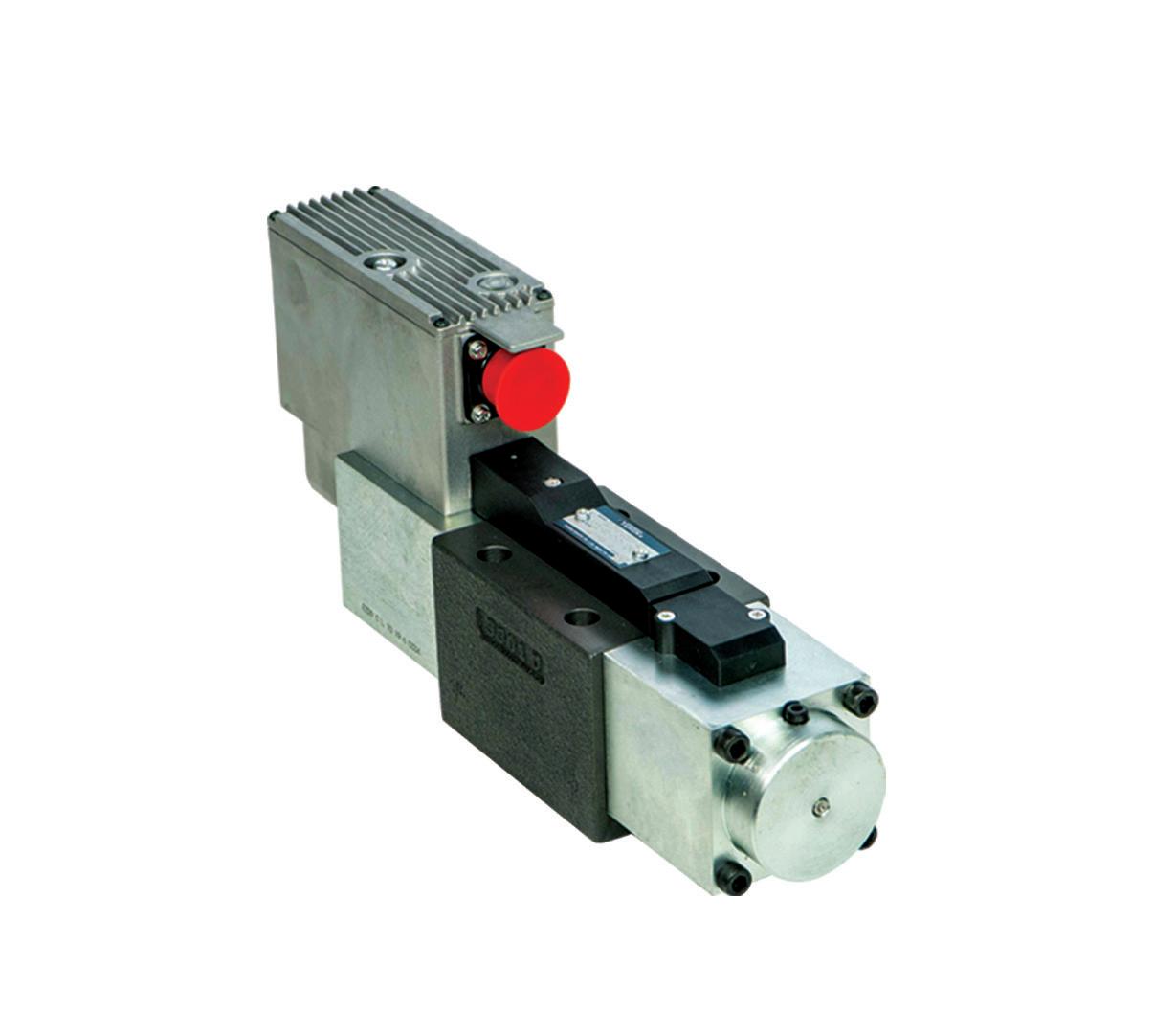
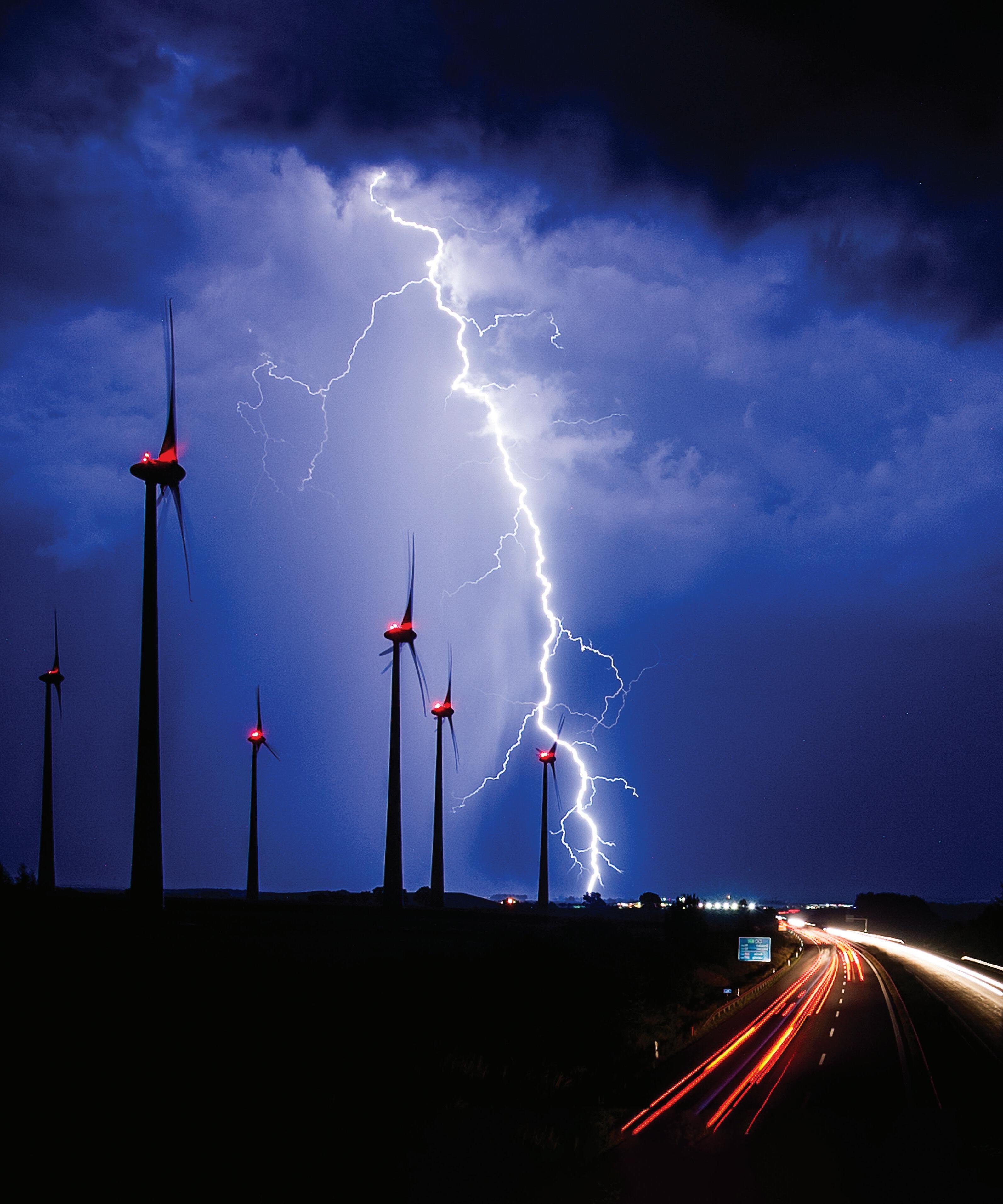
• Superior Pitch Control
• Multiple years of valve life
• 3-Year warranty
• Over 4,000 valves installed
Electrical transformers are central to the efficient operation of renewable energy systems, and they play a critical role in converting and managing the power generated. Protect your transformer by accurately assessing its degradation using Megger solutions and help prolong its life.
TRAX Multifunction transformer and substation test system for accurate condition assessment.
n Replaces the need for multiple test sets
n Powerful, portable and compact system
n Reduces user training and testing time
Renewable transformer bundle for every-day maintenance testing.
n Insulation resistance
n Winding resistance
n Turns ratio
PUBLISHER
Courtney Nagle cseel@wtwhmedia.com 440.523.1685
EDITORIAL
Editorial Director, Renewables Kelly Pickerel kpickerel@wtwhmedia.com
Senior Editor Billy Ludt bludt@wtwhmedia.com
CREATIVE SERVICES & PRINT PRODUCTION
VP of Creative Services Matthew Claney mclaney@wtwhmedia.com
Art Director Allison Washko awashko@wtwhmedia.com
Director, Audience Development Bruce Sprague bsprague@wtwhmedia.com
WTWH Media, LLC 1111 Superior Avenue, Suite 2600, Cleveland, OH 44114
Ph: 888.543.2447
Fax: 888.543.2447
Videographer Cole Kistler cole@wtwhmedia.com
VP of Digital Marketing Virginia Goulding vgoulding@wtwhmedia.com
Digital Marketing Manager Taylor Meade tmeade@wtwhmedia.com
Digital Marketing Coordinator Emily Gillespie egillespie@wtwhmedia.com
Digital Design Manager Samantha King sking@wtwhmedia.com
Marketing Graphic Designer Hannah Bragg hbragg@wtwhmedia.com
Webinar Coordinator
Halle Sibly hkirsh@wtwhmedia.com
ONLINE DEVELOPMENT & PRODUCTION
Web Development Manager B. David Miyares dmiyares@wtwhmedia.com
Digital Media Manager Patrick Curran pcurran@wtwhmedia.com
Digital Production Manager Reggie Hall rhall@wtwhmedia.com
Front End Developer Melissa Annand mannand@wtwhmedia.com
Digital Production Specialist Nicole Lender nlender@wtwhmedia.com
Digital Production Specialist Elise Ondak eondak@wtwhmedia.com
IN-PERSON EVENTS
Events Manager Jennifer Kolasky jkolasky@wtwhmedia.com
Events Manager Brittany Belko bbelko@wtwhmedia.com
Event Coordinator Alexis Ferenczy aferenczy@wtwhmedia.com
CUSTOMER SERVICE
Customer Service Manager Stephanie Hulett shulett@wtwhmedia.com
Customer Service Representative JoAnn Martin jmartin@wtwhmedia.com
Customer Service Representative Tracy Powers tpowers@wtwhmedia.com
Customer Service Representative Renee Massey-Linston renee@wtwhmedia.com
Customer Service Representative Trinidy Longgood tlonggood@wtwhmedia.com
FINANCE
Controller Brian Korsberg bkorsberg@wtwhmedia.com
Accounts Receivable Specialist Jamila Milton jmilton@wtwhmedia.com
HUMAN RESOURCES
VP of Human Resources Edith Tarter etarter@wtwhmedia.com
WINDPOWER ENGINEERING & DEVELOPMENT does not pass judgment on subjects of controversy nor enter into disputes with or between any individuals or organizations.
WINDPOWER ENGINEERING & DEVELOPMENT is also an independent forum for the expression of opinions relevant to industry issues. Letters to the editor and by-lined articles express the views of the author and not necessarily of the publisher or publication. Every effort is made to provide accurate information. However, the publisher assumes no responsibility for accuracy of submitted advertising and editorial information. Non-commissioned articles and news releases cannot be acknowledged. Unsolicited materials cannot be returned nor will this organization assume responsibility for their care.
WINDPOWER ENGINEERING & DEVELOPMENT does not endorse any products, programs, or services of advertisers or editorial contributors. Copyright© 2023 by WTWH Media, LLC. No part of this publication may be reproduced in any form or by any means, electronic or mechanical, or by recording, or by any information storage or retrieval systems, without written permission from the publisher.
SUBSCRIPTION RATES: Free and controlled circulation to qualified subscribers. Non-qualified persons may subscribe at the following rates: U.S. and possessions, 1 year: $125; 2 years: $200; 3 years $275; Canadian and foreign, 1 year: $195; only U.S. funds are accepted. Single copies $15. Subscriptions are prepaid by check or money orders only.
SUBSCRIBER SERVICES: To order a subscription or change your address, please visit our web site at www.windpowerengineering.com
WINDPOWER ENGINEERING & DEVELOPMENT is published three times per year in April, September and a special issue in December by WTWH Media, LLC, 1111 Superior Avenue, Suite 2600, Cleveland, OH 44114.
The Gulf of Mexico, with its vast expanse and untapped potential, has become a focal point for wind energy development. However, the region’s susceptibility to hurricanes and extreme weather events poses significant challenges.
In wind turbine design, carbon fiber composites are indispensable due to their light weight and high-strength properties. However, the end-of-life management of carbon fiber waste poses a significant environmental challenge.
Connecticut, Massachusetts and Rhode Island signed a memorandum of understanding in 2023 to collaborate on offshore wind procurement. The MOU allows project developers to submit bids to multiple states at once, which could attract larger projects and drive down energy costs. What does the public think?
LS Greenlink USA, a subsidiary of South Korean cable manufacturer LS Cable, is constructing a $681 million subsea cable manufacturing facility in Chesapeake, Virginia. The facility will specialize in the production of advanced subsea cables used in offshore wind farms. Locating the facility at the Deep Water Terminal Site will allow LS GreenLink to utilize Chesapeake’s logistics network to easily access key markets and resources.
“This state-of-the-art facility represents our commitment to pushing the boundaries of technology and engineering,” said Bon-Kyu Koo, president and CEO of LS Cable & System. “This facility will not only enhance our capability to meet the growing global demands for submarine power cables but will also position us at the forefront of the industry.”
The factory will support 338 new jobs, and LS GreenLink will use 48C credits awarded via the Inflation Reduction Act to support construction.
California Community Power and developer CADEMO signed a MOU in May to develop a 60MW offshore wind project off the coast of California, the first for the state. The project is slated to be in state waters off the coast of Vandenberg Space Force Base near Lompoc. The wind farm is expected to start commercial operations in 2028.
The first monopile in the 2.6-GW Coastal Virginia Offshore Wind project was installed in May approximately 29 miles off the Virginia Coast. The 176-turbine project is expected to be complete in 2026. The monopile foundations are being staged at Portsmouth Marine Terminal and being installed into the sea floor to support the wind turbines.
Exus Renewables North America has invested $200 million to start repowering the 139-MW Twin Ridges Wind Farm in Somerset County, Pennsylvania. Nacelles and blades will be replaced, and the existing towers and foundations will remain in operation. With these upgrades, Twin Ridges will see a 30% increase in energy generation.
Equinor broke ground on the South Brooklyn Marine Terminal (SMBT) in June, starting the revitalization of a port facility to assist offshore wind development on the East Coast. SMBT will be a staging and preassembly site for turbine components on Empire Wind 1 and will be one of the largest offshore wind hubs in the United States.
Construction started on Ørsted’s 924-MW Sunrise Wind project off the New York coast in July. Sunrise Wind will create 800 union jobs during construction and will provide enough electricity to power 600,000 New York homes once completed. The offshore wind farm, a $700 million investment, is being built approximately 30 miles east of Montauk.
GEV, a wind turbine repair and maintenance company, has established the North American Wind Academy at its U.S. headquarters in Fort Worth, Texas. The company is certified to train technicians in blade repair courses and trade testing programs to meet the demand for almost 600,000 wind turbine technicians by 2027 to support industry growth.
Dr. Michael Gaultois is the Chief Scientific Officer of Fairmat, a deeptech startup that uses material science, AI and robotics to recycle carbon fiber composite and manufacture products. Before joining Fairmat in 2022, Michael led research at the interface of Materials Science and AI, developing novel methods and functional materials with applications in sustainability and energy.
Iulian Maciuca is Industry Sector Manager – Renewables for Celeros Flow Technology. He trained as a Mechanical Engineer with a specialization in Automotive Engineering – Vehicle Dynamics, in which he holds a bachelor’s degree. He has almost two decades of sales and business development experience, 14 years of which are at international level.
Rick Scott is a Senior Meteorologist and Industry Manager and has been with technology provider StormGeo for over 12 years. He has worked with a wide variety of industries, most notably with oil and gas and renewable energy. Rick received his master’s from Texas A&M University and bachelor’s from the University of Kansas.
RICK SCOTT, SENIOR INDUSTRY MANAGER AND METEOROLOGIST, STORMGEO
TheGulf of Mexico, with its vast expanse and untapped potential, has become a focal point for wind energy development. However, the region’s susceptibility to hurricanes and extreme weather events poses significant challenges to these renewable energy infrastructures. The devastating impacts of such events have underscored the urgent need for robust preparedness strategies to safeguard these valuable assets.
Interestingly, countries like Japan and Taiwan, frequently subjected to similar extreme weather conditions, have developed effective resilience strategies over the years. These strategies, honed by experience and innovation, offer valuable lessons that could be instrumental in fortifying the Gulf of Mexico’s wind farms. By integrating these proven strategies, we can enhance the resilience of wind farms in the Gulf, ensuring their longevity and reliability, even in the face of nature’s most formidable challenges. This not only secures our investment in renewable energy
but also contributes to a sustainable and resilient energy future.
The transition from El Niño to La Niña often signals a shift in weather patterns, including an increased likelihood of hurricane activity in the Gulf of Mexico. This heightened hurricane activity can have significant impacts on wind farms and turbines in the region. Hurricanes bring with them not only high-speed winds but also torrential rain and storm surges, all of which can cause substantial damage to wind turbines. The intense winds can exceed the operational limits of the turbines, leading to automatic shutdowns or, in extreme cases, structural failure.
Moreover, the increased frequency of these extreme weather events during the La Niña phase means that wind farms may face repeated disruptions and damages, leading to costly repairs and downtime. This not only affects the immediate energy output but can also have long-term implications for the overall viability and profitability of wind energy projects in the region. Therefore, it is crucial to factor in these climate phenomena and their potential impacts when planning and operating wind farms in the Gulf of Mexico.
Weather intelligence solutions can further enhance business mitigation
strategies. Advanced forecasting models can predict the path and intensity of hurricanes, allowing for strategic turbine operation to minimize any structural damage and ensure employees and assets safety. Sitespecific weather forecasting is a crucial tool for offshore wind farms, especially in hurricane-prone areas like the Gulf of Mexico. These forecasts provide detailed meteorological data tailored to the exact location of the wind farm, allowing operators to anticipate severe weather events such as hurricanes. With this information, they can adjust the operation of the turbines to minimize damage, for instance, by feathering the blades or shutting down the turbines entirely. This proactive
approach can significantly reduce the risk of costly damage and downtime. Moreover, site-specific weather forecasting can also help optimize the energy output of offshore wind farms. By predicting wind speeds and directions, these forecasts enable operators to adjust equipment and staffing. During a hurricane, while the primary concern is to protect the infrastructure, there may be periods where the wind speeds are within the operational range of the turbines. In such cases, the wind farm can harness the increased wind energy, contributing to the overall efficiency and productivity of the farm. Thus, site-specific weather forecasting is not only a protective measure but
also a strategy for enhancing the performance of offshore wind farms.
Taiwan and Japan, both prone to typhoons, have effectively utilized site-specific weather forecasting to safeguard their offshore wind farms.
In Taiwan, researchers have used the Weather Research and Forecasting model in conjunction with Wind Farm Parameterization to study the potential impact of offshore wind farms during Tropical Storm Haitang. This research has provided valuable insights into how wind farms interact with severe weather, helping to develop strategies to reduce damage. Similarly, Japan, with its advanced meteorological technology, has likely employed site-specific weather forecasting to protect its wind farms during typhoon conditions. These strategies not only ensure the safety and longevity of the wind farms but also contribute to the stability of the power supply during extreme weather events.
The Gulf of Mexico is known for its harsh weather conditions, particularly hurricanes. To harness wind energy in this region, turbines and other offshore structures are specially designed, certified and built to withstand these extreme conditions. These structures are robustly engineered to endure the high wind speeds and tumultuous
sea states that hurricanes bring. This resilience is crucial to ensure the safety of the structures, the continuity of energy production, and the overall viability of offshore wind farms in the Gulf of Mexico. Mitigating the risk of hurricanes in the Gulf of Mexico can be achieved by adopting and adapting strategies from Japan and Taiwan, countries that have long grappled with similar challenges. One such strategy is the design and implementation of typhoon-resistant wind turbines, which have been successfully deployed in Taiwan. Similarly, Japan’s rigorous maintenance protocols and advanced forecasting systems allow for early detection of potential threats, enabling timely turbine shutdowns and minimizing damage.
Looking toward the future, the Gulf of Mexico’s potential for wind energy development is vast, but the region’s susceptibility to hurricanes and extreme weather events presents significant challenges. The experiences of countries like Japan and Taiwan, which have developed effective resilience strategies for similar weather conditions, offer valuable lessons. By integrating these strategies, we can enhance the resilience of wind farms in the Gulf, ensuring their longevity and reliability. WPE
IULIAN MACIUCA • RENEWABLES INDUSTRY SECTOR MANAGER • CELEROS FLOW TECHNOLOGY
the global energy supply requires a renewable energy mix to replace more traditional power generation. Offshore wind is a key component of this energy transition. This article discusses the engineering challenges associated with offshore wind development and explains the role that flow control equipment can play in improving operations on wind turbine installation vessels (WTIVs) and submersible platforms.
The first offshore wind farm comprised two 2-MW Vestas wind turbines with a rotor diameter of 66 m, sited less than 2 km from shore on monopile foundations in about 10-m water. Twenty years later, offshore wind turbines are typically rated at over 10-MW with rotor diameters of 150 to 164 m. It is predicted that by 2030 the industry will be deploying 20-MW turbines with rotors up to 300-m in diameter.
This growth in turbine size is, in part, a consequence of the "easy" sites — close to shore and with relatively shallow waters — being fully developed already. Offshore wind farms are therefore moving further off the coast, even though greater water depth can impact foundation size and vessel suitability. These nextgeneration turbines need a crane capacity of 2,500 to 3,500 tons to get them upright (compare this to 500 tons in 2005 when the first jack-up was deployed for offshore wind).
More than quadrupling tonnage requirements means that essential vessels such as jack-up rigs, selfelevating heavy lift crane barges and WTIVs must be able to cope with the additional strain of transporting and erecting these giant turbines.
Reliable flow control equipment plays a significant role in the successful deployment of offshore wind turbines and other deep-water structures. Raw water (seawater) in sufficient quantities is critical to various activities, including drilling, firewater duties and providing ballast on semi-submersible structures. Maximizing operational life and minimizing total cost of ownership of critical flow control systems is paramount. The electrical submersible pumps (ESPs) on which these systems depend need to be specifically engineered for seawater service. For example, the S&N Pumps range of ESPs from Celeros Flow Technology features high-grade construction using corrosion-resistant materials such as stainless steel. A Duplex material grade design is also available. These pumps can be oriented horizontally or vertically and are available in diameters of between 4 and 24 in. Equipped with powerful motors up to 750 hp, these pumps can achieve flow rates of up to 4,500 gpm.
In addition to constant exposure to harsh and corrosive conditions, ESPs can also be susceptible to blockages caused by marine growth, including seaweed and crustaceans. If left unchecked, such growths can create a thermal barrier around a pump motor and reduce the amount of heat that can be dissipated. Consequences include accelerated corrosion (such as erosion, pitting and cavitation), reduced fluid flow throughout the piping of the vessel or rig, and adverse increases or decreases in turbulence at pump intakes. These biological blockages are expensive and time consuming to remove, and, in severe cases, entire sections of pipework may need to be replaced.
Bio-fouling prevention systems such as the SNSAFE from Celeros Flow Technology provide a solution. This system comprises an anode cage
assembly which attaches to the motor housing of an electric submersible pump or the suction of a vertical turbine pump. The system delivers an impressed DC current from a power-converting control panel to strategically placed copper anodes in the seawater system. The passage of the DC current through the copper anode releases copper ions into the seawater flow at a predetermined rate to deter the entry and growth of fouling organisms. Deployed strategically, this comprehensive biofouling prevention system can significantly improve pump service life.
Reel benefits
ESPs may also form part of a preloading reel system that provides a means of storing, lowering and retrieving a hose to secure a reliable supply of raw water. A complete seawater lift system consists of a reel with the hose, power cable, safety cable and a submersible pump/motor with all necessary controls. The hose runs below the ocean surface to deliver seawater to an elevated offshore structure. Each system is designed to mount directly to the main deck with removable anchor pins or by welding. This is an improvement to the conventional approach of mounting the pump in the leg of the crane or platform and makes deployment quicker and easier. Hose reels also eliminate the need for removing
manifolding piping with the crane. However, these systems do have one weakness: the hoses can stretch, puncture or fracture, and this damage can lead to reel system snagging and related delays in deployment. In an industry that relies on specific time slots that are dictated by the limited availability of vessels and crew as well as weather patterns, failure of a hose system can be extremely expensive and cause major project delays.
Celeros Flow Technology offers a solution that minimizes this risk. The E-Z Fit Reel System from S&N Pumps features a hose with reinforcing wire along its entire length. This reinforced hose will support the combined weight of the pumps, shroud and full water columns, eliminating hose stretch and extending hose life. The reinforcement of the hose
is complemented by a custom engineered roller deployment system that intuitively maintains the radius bend of the hose throughout deployment and retraction.
The E-Z Fit systems are easily retrofitted to an existing vessel or supplied for new construction.
The economic viability of offshore wind is dependent on many complex factors, including continued political will, suitable construction sites and the ability to develop them economically. The trend toward ever larger wind turbines means that flow control equipment must continue to keep pace, in terms of performance and reliability, to ensure the global industry can deliver the energy transition. WPE
Dr. Michael Gaultois • Chief Scientific Officer • Fairmat
In various high-performance sectors like wind energy, carbon fiber composites are indispensable due to their light weight and high-strength properties. However, the end-of-life management of carbon fiber waste poses a significant environmental challenge. Traditional disposal methods, including incineration and landfilling, are not sustainable. Recent advancements in carbon fiber recycling have fostered sustainable solutions across multiple industries.
The importance of carbon fiber recycling
Carbon fiber reinforced polymers (CFRP) are crucial for industries that require materials with exceptional strength-to-weight ratios. However, their production and disposal are energy-intensive processes. Recycling carbon fiber helps conserve resources and reduce the carbon footprint associated with manufacturing new materials.
Innovative recycling processes
Several innovative processes have emerged to address carbon fiber waste, turning it into valuable resources. Mechanical
recycling, thermal recycling and chemical recycling are key methods. Each process involves breaking down carbon fiber composites to recover fibers that can be reused in various applications:
Mechanical recycling: Mechanical recycling involves physically breaking down carbon fiber composites into smaller pieces using advanced machinery. This process is energy-efficient because it does not use high temperatures. However, traditional methods like grinding and crushing can shorten the fiber lengths, reducing their quality and strength. Deeptech startup Fairmat has developed an innovative robotic system that mechanically cuts the fibers while preserving their mechanical properties, making them suitable for reuse.
Thermal recycling known as pyrolysis:
Thermal recycling uses high temperatures to decompose the resin matrix in carbon fiber composites, leaving behind clean fibers. While effective, this method requires significant energy input and may release harmful emissions if not properly managed.
Chemical recycling known as solvolysis: Chemical recycling employs solvents to dissolve the resin matrix, separating the fibers without damaging their structure. This method is efficient and results in high-quality recycled fibers, although it involves complex chemical processes and significant chemical waste if not properly managed.
Broader industry impact
The impact of carbon fiber recycling extends beyond individual companies. Industrywide adoption of recycling technologies can significantly reduce the environmental impact of various sectors, including wind energy. This supports global sustainability goals and enhances the economic viability of using recycled materials by reducing costs.
Fairmat has made significant strides in developing mechanical recycling processes. Established in 2020 by Benjamin Saada, Fairmat has collaborated with partners such as Hexcel, Dassault Aviation, Exel Composites and Tarmac Aerospace. These partnerships drive Fairmat’s mission of closing the loop on carbon fiber waste and making significant strides in sustainability.
Fairmat’s recycling process begins with the collection and segregation of carbon fiber waste from various sources. The waste materials, which can include prepregs, offcuts and end-of-life (EOL) products, are carefully segregated to identify those suitable for recycling. Upon arrival at Fairmat's facilities, the collected waste undergoes further segregation and preprocessing. This step ensures
that the materials are in optimal condition for recycling. Preprocessing treatments, such as cleaning and cutting, are applied to prepare the carbon fiber waste for the next stage.
Mechanical recycling is the primary method used by Fairmat. This involves proprietary cutting technologies and the use of advanced machinery, robotics and artificial intelligence (AI). Importantly, unlike traditional grinding or crushing, Fairmat’s proprietary cutting technology mechanically breaks down the carbon fiber composites into smaller pieces while preserving the mechanical properties of the fibers, making them suitable for reuse in high-performance applications. Robotic tools and AI enhance the precision and efficiency of this process, converting the carbon fiber components into CFRP (carbon fiber reinforced polymer) building blocks. This is a unique and sustainable technology that combines material science, data informatics and robotics, permitting the recycling of a broad range of carbon feedstocks (uncured and EOL products). This innovative process creates recycled carbon fiber that can be used for applications such as interior structural reinforcements, impact surfaces and exterior design finishings. By seamlessly integrating advanced recycled material both inside and outside products poised to enhance electronics, sporting goods, mobility and beyond, Fairmat is not only redefining industries but also setting new benchmarks for innovation and environmental stewardship.
Partnerships driving sustainability
Fairmat's innovative recycling technology allows for the production of 100% recycled carbon composites that retain their strength and lightweight properties. By partnering with companies like Hexcel, Fairmat has
established a 10-year agreement to recycle carbon fiber composite materials from Hexcel’s Salt Lake City facility for reuse in various commercial markets. Additionally, the partnership with Exel Composites focuses on recycling carbon fiber composite scrap from Exel’s plants in Finland, transforming it into high-performance CFRP chips using the proprietary cutting technologies described above.
Despite the advancements, challenges remain in scaling up recycling processes and ensuring economic
feasibility. Research and development efforts are crucial in overcoming these hurdles and improving recycling efficiency. Future directions include enhancing the quality of recycled fibers and developing new applications for recycled materials. Collaboration within the industry ecosystem is essential to maximizing impact.
Recycling carbon fiber is a vital component of the sustainability strategy across multiple high-performance industries. By transforming waste into valuable resources, the industry can significantly reduce its environmental footprint and move closer to achieving a circular economy. WPE
In the fall of 2023, Connecticut, Massachusetts and Rhode Island signed a memorandum of understanding to collaborate on offshore wind procurement. The MOU allows project developers to submit bids to multiple states at once, which could attract larger projects and drive down energy costs. This past July, the Barr Foundation and Hart Research published views on findings from statewide surveys in the three states. The survey sought to understand voters’ perspectives on offshore wind and their feelings about collaboration between the three New England states on offshore wind.
Sam Schacht of the Clean Energy States Alliance (CESA) spoke to Kathryn Wright, senior program officer for clean energy at the Barr Foundation, and Jay Campbell, partner at Hart Research, about their motivations to undertake the research, key findings from the survey and what lessons we can learn from their work. Their conversation was shared with Windpower Engineering and Development
CESA: Why did you decide to pursue this research, and what went into creating it?
Kathryn Wright: For several years, the Barr Foundation has tried to do regular polling of New England states, mostly focusing on Massachusetts and Connecticut,
because that’s where we do the most work. One of the things we’ve always tried to track is how voters think about clean energy and our energy system.
Back in October, the three southern New England states of Massachusetts, Connecticut and Rhode Island signed an MOU saying they would work together on offshore wind to procure a lot more energy for the region. A request for proposals was released, and applications were submitted back in the spring. There’s also been quite a bit of press about offshore wind, because there’s active construction off the coast of New England. Both of those were opportunities for us to really get a sense of how people are feeling. These projects are now going from being concepts to being real.
For a project like this, we bring in the perspectives of the organizations we work with. We have a subset of organizations that receive grants from the Barr Foundation that are very focused on offshore wind from different perspectives. They provided feedback on some of the topics we were covering and helped to set the scope. They were part of the reason we ended up polling in all three states.
Jay Campbell: We interviewed 400 registered voters in each of those three Southern New England states. We reached them through a variety of methods, including some individuals who are part of a large national online
research panel. We augmented it with additional interviewing including live calls and directing people in all three states to our survey through text. We utilized all three modes of interviewing to get to 1,200 people. Through a series of conversations, using Barr’s expertise in offshore wind and Hart’s expertise in polling, we created a set of questions to help us understand where New Englanders are when it comes to offshore wind.
CESA: How do the results fit in with polls you’ve done in the past? Did anything surprise you about your findings?
Kathryn Wright: This poll is a little different than some of our previous work, which was more broadly about people’s perceptions of renewable energy, including states’ commitments to high-ambition renewable energy
and greenhouse gas targets, how reliable people think renewable energy is, and people’s opinions of the transition away from natural gas. I can tell you that generally, the trend we’ve seen from when we started polling to now is steady support for renewable energy and softening of support for a natural gas expansion and growing skepticism about gas safety.
Jay Campbell: One of my top-of-mind findings is this idea of cooperation among the states could potentially lead to better outcomes in this area. Whether that’s a perhaps decreased financial commitment for each individual state or the other types of benefits cooperation might bring, the idea of the states working together is actually a quite-high selling point in favor of the tri-state procurement idea. It’s not often in polling that respondents reflect on or are drawn
to those sorts of process-type elements. I think an important point is that three states in the same region are working together to tackle a very big problem. In my 28 years as a pollster one thing that I have learned is that people intuitively get a lot of things, and one of the things they get is that an individual state or an individual country cannot fix climate change.
CESA: How does this polling inform the way we ought to communicate the government’s role in offshore wind, especially considering people’s concerns about offshore wind and marine habitats?
Kathryn Wright: States and the offshore wind industry are taking a lot of precautions around marine life and whales throughout project development. Earlier this year, we
saw NOAA and the Bureau of Ocean Energy Management release new rules that were specific to whales and offshore wind development.
It’s something that’s being taken seriously, and we’re informed by the science that we know. Right now, a lot of the whale deaths we’ve seen are related to fishing line entanglements and ship collisions. There have been a lot of conversations on social media and misinformation around the connection between offshore wind and marine life. We have to take those concerns seriously, so perhaps there’s an opportunity to lift up some of the work that marine scientists are doing to really try to do some myth-busting where possible.
I think the survey results told us that there are a lot of positive benefits that people associate with offshore wind, including energy price reductions and energy independence.
I think the job we have as communicators is to lift up the positive story and not always play defense, but instead talk about the benefits of offshore wind, because they really resonated in the poll.
Jay Campbell: Whether it’s energy independence, jobs in the economy in the state, the effects of climate change, cleanliness of air and water, health or electric reliability — all of those factors come down very much on the positive side when people are asked to think about the potential effects of offshore wind. Upward of 75% of respondents said that they favored the idea of building these offshore wind operations off the coast of these states. It’s tough to get more than three-quarters of the electorate to be in favor of something. Addressing those concerns around marine life while also lifting up the
positives around the potential to bring down electricity prices and enhance energy independence for these states are all really important steps to take.
More broadly, the idea of working together to address this big problem of either air pollution, water pollution, climate change and being able to bring to bear the resources that three states have, that one state may not have on its own, to address big problems, I think is a really important way to think about this. For example, renewable energy is something that we know that young people care about a lot, and they tell us so in the poll. We can use the fact that something — the tri-state procurement — is going to address that as one way to illustrate the ability of government to affect change and take big steps to ultimately improve life for people in these states and the country as a whole into the future. WPE
Managing Director
Scott McCafferty
310.279.3844 smccafferty@wtwhmedia.com
EVP
Marshall Matheson
805.895.3609 mmatheson@wtwhmedia.com
Jami Brownlee
224.760.1055 jbrownlee@wtwhmedia.com
Ashley Burk
737.615.8452 aburk@wtwhmedia.com
Publisher
Courtney Nagle cseel@wtwhmedia.com 440.523.1685
CFO
Ken Gradman kgradman@wtwhmedia.com 773-680-5955
Jim Powers 312.925.7793 jpowers@wtwhmedia.com
See the latest wind power developments and U.S. project news on our website. Also find expert webinars and more from the leading wind power engineering magazine today.
BUILDING TODAY, POWERING TOMORROW.
LEARN MORE & REGISTER