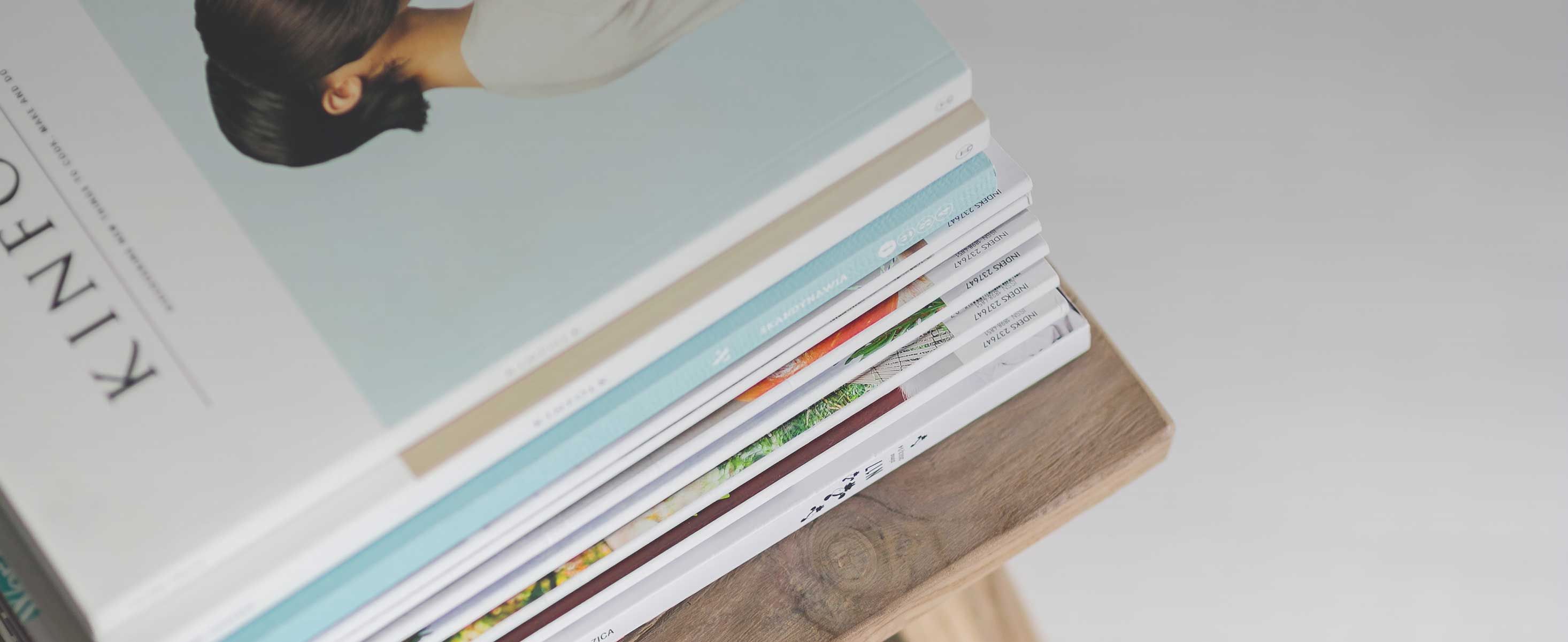
1 minute read
Image 22: Picture of a pump for illustration purpose
• Cold air should be directed so that it is blown where specifically needed (using the unit’s “flapper position”).
• Select an air conditioning unit and refrigeration system appropriate for the room size and temperature.
Advertisement
• Carry out an energy audit and develop a regular maintenance plan to maintain air conditioning and refrigeration devices according to the manufacturers’ recommendations.
Pumps
Many industrial processes, including those in the F&B industry, involve transportation of fluids, and a pump is the only mechanical means available to facilitate this transportation. Because a pump is incapable of transporting fluid on its own, it needs a “prime mover” in order to function. The prime mover can either be an electric motor, a diesel engine, or a steam/gas-powered turbine. To power a pump, all prime movers consume energy, either in the form of electric power or non-renewable petroleum products like diesel, oil or gas. Some best practices for saving energy in pumps are given below:
• Operate pumps near their best efficiency point (BEP).
• Minimize throttling and pump losses by modifying the pumping system to minimise pipe bends.
• Incorporate basic, key instruments in pumping systems, such as pressure gauges or flow meters.
• Using VSDs or sequenced control of multiple units, adapt the pumping system to a wide range of operational loads.
• Install and use booster pumps for smaller loads requiring higher pressures.
• Repair seals to minimize water lost in the pumping system through leaks/dripping.
• In a system with multiple pump operations, seek to carefully combine them to avoid throttling.
Image 22: Picture of a pump for illustration purpose